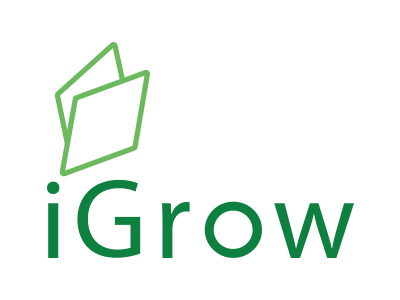
Welcome to iGrow News, Your Source for the World of Indoor Vertical Farming
Kroger Expands Partnership With 80 Acres Farms To 316 Stores
80 Acres Farms latest farm in Hamilton, OH grows10 million servings of fresh, pesticide-free produce annually
80 Acres Farms latest farm in Hamilton, OH grows10 million servings of fresh, pesticide-free produce annually
CINCINNATI - March 8, 2021 - ( Newswire.com )
The Kroger Co. (NYSE: KR) and 80 Acres Farms bring farm-fresh produce to customers across Ohio. Today, the companies are growing their partnership to reach more shoppers in the Midwest - both in-store and online.
“Everyone deserves easy access to fresh, affordable, delicious food,” said Dan De La Rosa, Group Vice President Fresh Merchandising, Kroger. “This newly expanded partnership means more communities will have just-picked produce at their fingertips 365 days a year. We’re proud to partner with 80 Acres Farms as we work together to create a world with Zero Hunger | Zero Waste.”
80 Acres Farms’ breakthrough technology means the company can grow pesticide-free produce all year long. With locations closer to customers, the farm-to-table carbon footprint and overall food waste are low.
“Kroger leads with their commitment to fresh by providing customers access to fresher and more nutritious produce,” said Mike Zelkind, CEO and Co-founder of 80 Acres Farms. “Consumers are looking for more nutrition from their diet and want to trust that their food is safe and chemical-free and it will last longer in their refrigerators. The 80 Acres Farms brand delivers against all those promises.”
Today, 80 Acres Farms has four locations in Greater Cincinnati. Its latest state-of-the-art farm will support the new Kroger partnership, bringing 10 million fresh produce servings to communities across the Midwest.
Beginning March 15, 80 Acres will serve 316 Kroger locations across Ohio, Indiana, and Kentucky.
For further information, please contact us at:
Rebecca Haders
rebecca.haders@eafarms.com / +1 513-910-9089
Related Links
New funding sets up 80 Acres Farms for ‘rapid’ expansion
‘The future of food’: 80 Acres debuts world’s first-of-its-kind indoor farm: PHOTOS
Press Release Service by Newswire.com
Original Source: Kroger Expands Partnership With 80 Acres Farms to 316 Stores
USA: Living Greens Farm’s Salads To Sell In 80 Cub Stores In Midwest
Starting December 2020, LGF’s ready-to-eat bagged salad products (Caesar Salad Kit, Southwest Salad Kit, Harvest Salad Kit, Chopped Romaine, and Chopped Butter Lettuce) will be carried in 80 high-volume CUB Foods stores in Minnesota and Illinois. CUB is known for its focus on food quality and commitment to offering the best produce, period
January 27, 2021
FARIBAULT, Minn., Jan. 26, 2021 (GLOBE NEWSWIRE) — via InvestorWire – Living Greens Farm (LGF), the largest vertical, indoor aeroponic farm in the U.S. that provides year-round fresh salads, salad kits, microgreens, and herbs, announced the addition of significant new retail distribution of its products in the upper Midwest.
Starting December 2020, LGF’s ready-to-eat bagged salad products (Caesar Salad Kit, Southwest Salad Kit, Harvest Salad Kit, Chopped Romaine, and Chopped Butter Lettuce) will be carried in 80 high-volume CUB Foods stores in Minnesota and Illinois. CUB is known for its focus on food quality and commitment to offering the best produce, period.
CUB will receive LGF’s products from UNFI BB #:158953, which distributes food products to thousands of stores nationwide. UNFI’s Hopkins, Minn., distribution center makes LGF products available to the CUB stores along with 100+ additional independent retail stores within their service area. This represents a significant amount of growth in the distribution of LGF products in 2021, continuing an impressive expansion trend for the company. LGF boasted a record sales year in 2020 with 190 new stores serviced and revenues more than doubling 2019’s figures.
LGF’s proprietary vertical indoor farming method yields the highest quality and freshest produce available. This is because there are no pesticides or chemicals used in the growing process. And because LGF’s growing, cleaning, and bagging process significantly reduces handling and time to the retail shelf, consumers enjoy the freshest product on the market. These benefits continue to attract new users and new retail distribution and could possibly lead to even more from UNFI.
For more information on why Living Greens Farm products are the cleanest, freshest, and healthiest farm salads and greens available, go to www.livinggreensfarm.com.
ABOUT LIVING GREENS FARM
Headquartered in Minnesota, Living Greens Farm is the world’s largest vertical plane aeroponic farm. Living Greens Farm produce requires 95% less water and 99% less land to grow year-round and all products are grown without pesticides or GMOs. Living Greens Farm has a full product line that includes salads, microgreens and herbs available throughout the Midwest. For more information, please visit http://www.livinggreensfarm.com.
Contact:
Jarrod Holland
910.431.3322
jarrod@fireworksbydesign.com
Tagged greenhouse, salads
Infarm Raises $200 Million To Add “Farm” to Cities
heir environment-controlled and automated growing chambers grow food such as leafy greens inside the supermarket, so it’s fresh, without your food accumulating food miles
Infarm’s Israeli founders take on Berlin and the farm to table movement with high-tech farms.
Infarm, a company that grows fresh produce inside supermarkets, has recently announced a $170 million USD funding round to help the company expand across Europe. Their environment-controlled and automated growing chambers grow food such as leafy greens inside the supermarket, so it’s fresh, without your food accumulating food miles.
The company was founded by three Israelis in Berlin in 2013, and they announced this astounding investment achievement despite the Covid plague destroying global markets. Food, we understood, is something that must stay constant. The need for food which is grown locally, and available fresh now resonates at a time of uncertainty and the basic need for survival.
The company has raised $200 million USD total in their Series C round funding which was by LGT Lightstone, Hanaco, Bonnier, Haniel, and Latitude, Atomico, TriplePoint Capital, Mons Capital, and Astanor Ventures.
With a mix of equity and debt financing, the fresh capital brings Infarm’s total funding to date to more than $300 million, underscoring consumer and retailer appetite for Infarm’s approach to fresh, sustainable, and local food production in the wake of this year’s pandemic.
By 2025, Infarm’s farming fridge network is expected to reach more than 5,000,000 square feet to become the largest distributed hydroponic network in the world as it builds towards helping cities become self-sufficient in their food production. Competition includes Freight Farms in the US, and BrightFarms, also American.
“The coronavirus pandemic has put a global spotlight on the urgent agricultural and ecological challenges of our time,” says Erez Galonska, Co-founder and CEO of Infarm. His brother Guy Galonska is also a founder: “At Infarm, we believe there’s a better, healthier way to feed our cities: increasing access to fresh, pure, sustainable produce, grown as close as possible to people,” adds Erez.
The investment will be used to deepen the regional and local penetration of Infarm’s global farming network and complete development of Infarm’s new generation of vertical cloud-connected farms, capable of generating the crop-equivalent of acres of farmland and amplifying the diversity of produce currently available through vertical farming. Vertical farming is also known as hydroponic farming or controlled environment agriculture.
The technology has become developed and well-known over the years thanks to cannabis growers who used this energy-intensive and “stealth” mode of farming to grow cannabis with high concentrations of the active ingredient THC. When it was illegal to grow in Canada, young entrepreneurs were inspired by early blueprints from NASA and farming in space and found ways to set up a soil-less system in basements and closets. To their surprise, they could grow better quality cannabis, faster as inputs such as lighting, humidity, and nutrients could be tightly controlled.
And growing food became the next natural step for people who wanted to grow fresh food year-round even though it’s usually not cost-effective to grow tomatoes or lettuce this way unless you do it at scale.
Hydroponics and variations of it, using just water, a semi-solid coir medium or Styrofoam and/or with fish added, has become the promise for growing food in far-flung locations like Antarctica and food deserts where chocolate bars are available at bodegas, but fresh greens are not. This is according to mothers I have met in Harlem, New York. The hydroponic method is not that complicated at all in theory but in practice, it is hard to achieve good results without know-how in chemistry, engineering, and biology.
An integration of advanced engineering, software, and farming technology, the Infarm farms will save labour, land, water, energy, and food-miles, while contributing to a more sustainable food system, the company proposes.
Partnering with Aldi, Marks & Spencer, Sobeys
While companies like Farmigo founded in New York (also by an Israeli) wanted to put supermarkets out of business, in the past year Infarm has been working to keep them relevant and formed new partnerships with the world’s largest retailers, including Albert Heijn (Netherlands), Aldi Süd (Germany), COOP/Irma (Denmark), Empire Company Ltd (Sobeys, Safeway, Thrifty Foods – Canada), Kinokuniya (Japan), Kroger (United States), Marks & Spencer (United Kingdom) and Selfridges (United Kingdom).
With operations across 10 countries and 30 cities worldwide, Infarm harvests 500,000+ plants monthly, while using 99.5% less space than soil-based agriculture, some 95% less water, 90% less transport, and zero chemical pesticides. Today, 90% of the electricity use throughout the Infarm network is from renewable energy and the company has set a target to reach zero emissions from their production next year.
With the cost of lighting typically very high in hydroponics systems, I’d be curious to know how they will do that without buying carbon credits. Consider this Stanford research paper that mentioned the cost of hydroponic lettuce to be about 8KG of carbon compared to 150g if grown conventionally. The research is a few years old and certainly, there can be ways to improve energy efficiencies.
What organic farmers think?
Proponents of organic farming, regenerative agriculture, and permaculture don’t love hydroponics farming because it relies on petroleum-based fertilizers and nutrients as additives, and while there may be no or few bugs in the grow chambers, there is a risk of fungus and bacteria; in nature, there is always free natural sun (unless you are in Finland in the winter) and natural interactions between plant, soil; and even among small biota like mycorrhizal fungi which play a role in the uptake of micronutrients to the roots and the overall essence of what we call a plant. There is one school of thought that says the “organic” label can only be applied to soil-based farming. Lawyers are debating the issue now.
The answer will be somewhere in the middle. Like most things in life the middle way will help us. The dream is many one-acre regenerative farms to feed us healthily and to feed the planet too but meanwhile there is a gap. How do we feed everyone else who can’t afford to buy at Whole Foods?
We need to improve our local supply chain for food. When you live in a country like Israel, Egypt or Jordan with ample sun, growing food inside a supermarket fridge makes no sense, although hydroponics does. See this project in Jordan, funded by the USAID. Or the one that has changed lives in Harlem.
I had a hydroponics robotics venture (see this article on Bloomberg) and I took it to New York a few years ago and found myself running in circles trying to explain why eating local is good for the planet, it’s good for a circular economy that might one day be about survival. Venture Capitalists laughed at me. They said my technology and vision was a vitamin and not a bandaid –– “a nice to have” but not “a necessary to have”, especially in cities like New York. Then Covid thinking happened.
Here is what investors in Infarm say now (and kudos to the team who worked hard building physical farms and maintaining the pilots):
“We are excited to partner with the Infarm team to accelerate their urban vertical farm vision, ultimately creating a more sustainable food system for a growing population,” says Dharmash Mistry, Partner of LGT Lightstone: “With over $1bn of customer demand, partnerships with 17 of the top 50 global grocers, Infarm is set to revolutionise the market behind a unique ‘demand led’ modular business model.”
Let’s hope. Another Israeli called Benzi Ronen came from Silicon Valley and started a farm-to-table venture in New York and was on top of the world. He had just raised $26 million to grow Farmigo into the Amazon for fresh food and I spoke with him at one point when he warned me to stay in Israel and work there locally for a couple of years before moving stateside. That’s me in the biodome below, growing bok choy for future Martians on my roof in Tel Aviv. I didn’t listen.
I had a venture in robotics to help cannabis farmers (even Mars farmers grow cannabis in space – see this article in Fast Company) and city hydroponic farmers. Farmigo was trying to eliminate supermarkets, by connecting farmers to consumers at drop off points throughout the city. The model was valorous –– who doesn’t want the freshest farm picked veggies every morning? The modern CSA? And it supported local farming, just like what Michael Pollan wants us to do. And to compete with Amazon? Yes. Yes. Yes.
Farmigo raised millions and then the company’s vision to be the Amazon of fresh food could not compete with Amazon. Farmigo changed its business model and now sells software.
I saw the challenges of the business in supplying fresh food. The mechanics of the machines, the lack of willing labor, software needed, the logistics, the importance of food safety. The fungus, the bacteria. The good bacteria. The bad. The responsibility. The chemicals needed to feed the plants, to keep the systems “clean” and safe. So much is hard to control when you are talking about living things.
I always said that if hydroponics or farmers that come from Microsoft want to make city farming work the model will look like the cellphone industry: different players supplying various parts like Qualcomm, Verizon, 3M, Broadcom, and Texas Instruments does. Even to make iPhones work.
Can and will Infarm do it all?
“We see a massive demand in the market for sustainable, environment-friendly, and healthy food – and Infarm has just the right team in place to make this happen,” says Pasha Romanovski, Co-founding Partner of Hanaco Ventures.
More about Infarm
Founded in Berlin in 2013 by Osnat Michaeli and the brothers Erez and Guy Galonska, Infarm is dedicated to creating a future where local super fresh produce is available for everyone. The farms are placed in various locations in the city, like supermarkets, restaurants, and distribution centers, so that vegetables grow and are harvested close to the moment of purchase or consumption. People like Elon Musk’s brother Kimbal Musk has been doing this in New York with a project called Square Roots. They train young entrepreneurs to dream up all sorts of business models inside the shipping container farms built by Freight Farms.
Some in the VC world I have talked with question the viability of the business model of these containers. While it’s a nice idea it’s hard to get the return on the upfront investment.
But when it comes to specialty products and “farms” you can find the Infarm service model in all sorts of permutations in the United States. I got to spend some ample time in meetups with a pile of entrepreneurs building an urban farming project in New York. There I met Andrew Carter, now growing mushrooms in a warehouse in Williamsburg. There is also Farm.One which grows papalo, minutina and all the boutique and hipster greens any chef could dream up in the center of New York City. They deliver.
Lastly and most easily is to try out growing fresh greens at home without the supermarket, or less of the supermarket. I met the founder of Hamama when she was in Israel via MIT helping kids in Israel grow their own food using hydroponics at The Greenhouse. (After I wrote this story in 2008 <— kids from the US were writing me about how to donate their Bar Mitzva money to Noam Geva).
Over at The Greenhouse Camille had her head inside an aeroponics system she’d rigged up last time I saw her. She brought a few of her MIT geek friends over to my house in Jaffa and we talked about hydroponics changing the world. And now she helps people in the easiest way to grow microgreens at home. That’s a hyper simplified way to do hydroponics. She was one of the most inspiring people I met in hydroponics and urban farming.
In fact many in the business are. They are people who want to change the world. Have you met Henry?
Go out and meet someone, start a farm. Grow something. That’s how we change the world.
Now over to Infarm: good luck!
Expert Input Can Boost Yields For Vertical Farming
Designing, constructing and integrating new facilities that live up to vertical farming’s many promises calls for the right kind of knowhow, says Ian Hart, business development director at adi Projects
3rd September 2020
Designing, constructing, and integrating new facilities that live up to vertical farming’s many promises calls for the right kind of know-how, says Ian Hart, business development director at adi Projects.
For almost 12,000 years, humankind has found increasingly ingenious ways to convert the natural forces at play on Planet Earth into an ever more bountiful, diverse and predictable source of sustenance.
And, as global and national populations have grown historically and in particular, in recent decades, the issue of food security has always hovered somewhere in the background. Today, although we’re by no means on the brink of a Malthusian catastrophe, the idea that the UK might at some stage struggle to feed itself has taken on a new relevance.
We’ve always been used to the supermarket shelves being full. But the early stages of lockdown betrayed the reality that supply chains are highly sensitive not only to the onset of a pandemic but to economic and environmental shocks.
Imperfect storm
Putting COVID to one side, the UK is staring those other two factors square in the face. We currently import approximately 80% of our food, including real basics, such as carrots, but, in Brexit, we are on the verge of a significant dislocation between ourselves and our biggest and closest trading partners who also happen to supply 30% of the total.
And, while Brexit may cause short-to-medium term disruptions, presupposing an eventual agreement on future trade, the risks posed by the environment seem baked in for decades to come.
High hopes for UK vertical farming startup
Scottish vertical farming startup harvests £5.4m in funding
Extreme weather events, such as significant flooding which has quadrupled since 1980, can harm livestock and spoil crops. On the other side of the coin, water inefficiency and scarcity are issues in many parts of the world, as agriculture competes increasingly with industry and domestic use.
Rising temperatures are playing havoc with growing seasons and sparking ever more wildfires that can devastate farms, even when the flames don’t actually reach them.
So, the commercial risks are there for producers. Supply chains are fragile, meaning that businesses dependent on imported produce may be unable to meet the service levels demanded by the supermarkets – even in the short-term – and then scramble for unsustainable and often very costly workarounds.
Removing risk
Vertical farming facilities are the subject of increased interest in the industry. Climate-controlled facilities enable producers to regulate the variables of the environment and avoid pollution to grow produce of a consistently high standard and at predictably higher yields.
The vertical farm projects we have worked on are very hygienic, removing fungal and bacterial risks and the threat from all manner of pests. And, run on LEDs and recycling very high proportions of the water they use back into their processes, energy costs can be minimized, there is no need for water to be chemically treated and producers can extricate themselves from any sense that the taps might one day dry up.
Locally sited facilities mean the vagaries of geopolitics and international trade agreements are no longer an issue. And, as importantly, locating one close to a waste-to-energy plant would enable you to harness its heat and CO2 to aid the growing process.
The UK currently imports around 80% of its food
So, vertical farming has a real role to play in helping create circular economies at the local level.
While no means a silver bullet, in our experience vertical farms do solve many of the problems of contemporary food production and have the potential to help brands forge solid reputations as innovators and on sustainability.
But, so great are its potential upsides, one might quite reasonably ask why the shift to vertical farming isn’t gathering pace at a steadier rate. The answer, I believe, lies in a perceived lack of expertise in this country at getting such projects off the ground.
A specialist business
For all the simple answers the technology offers, the processes involved are highly sophisticated and capital intensive. Often it is only businesses with the means who go beyond the initial feasibility stages but, even then, they require specialist assistance.
The design and construction of the facilities themselves are highly complex. Different vegetable, fruits, and greens each require their own zoning and specific climatic conditions, and each of the different vertical levels – up to nine in some cases – has to create and sustain its own unique characteristics.
The electrical and robotic systems running the lighting and hydroponics are as innovative as anything in the sector and that’s before one overcomes the challenges of integrating the entire operation.
So, I’d advise companies exploring their options on vertical farming to go back to basics. If you can get those right from the outset and ensure you have continuity throughout the project, you can not only remove risk during planning and construction and for the duration of the facility’s lifecycle but also enjoy certainty on cost and program during the set-up phases.
Ian Hart is business development director at adi Projects
Visit the UK’s dedicated jobsite for engineering professionals. Each month, we’ll bring you hundreds of the latest roles from across the industry.