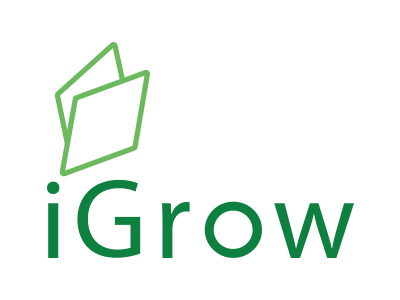
Welcome to iGrow News, Your Source for the World of Indoor Vertical Farming
A Vertical Farm In New Jersey May Be Transforming The Farm-to-Store Supply Chain
Bowery Farming in Kearny, New Jersey, is reimagining the farm-to-store supply chain. Bowery is the largest vertical farm in the United States, growing leafy greens, herbs, fruits, and vegetables inside a climate-controlled warehouse where crops grow in stacked trays under lights that mimic natural sunlight.
August 5, 2021
Bowery Farming in Kearny, New Jersey, is reimagining the farm-to-store supply chain. Bowery is the largest vertical farm in the United States, growing leafy greens, herbs, fruits, and vegetables inside a climate-controlled warehouse where crops grow in stacked trays under lights that mimic natural sunlight. “Marketplace” host Kai Ryssdal recently toured the research and development part of the farm, where Bowery fine-tunes the flavor of new produce such as radishes and strawberries with fewer threats of pests, water scarcity, or other challenges associated with traditional outdoor farming. Bowery also grows wasabi arugula and other hard-to-find vegetables that are difficult to cultivate using conventional growing methods.Because Bowery’s business model is based on growing crops in indoor sites near the cities they sell in, most products that would normally take two or three weeks to reach stores make it to market a day or two from harvest. Bowery Farming’s CEO Irving Fain sees vertical farming as nothing short of revolutionary, stating that it can “democratize access to high-quality fresh food” in cities. Bowery is growing in other ways: It has a second farm in Nottingham, Maryland, and a third is under construction in Bethlehem, Pennsylvania.
Vertical Farming Modules Take Hyperlocal To New Heights
One of the largest and fastest-growing vertical farming platforms in the world, Infarm’s smart farming modules are bringing a whole new meaning to the word “hyperlocal.”
Cultivating by Artificial intelligence,
These Vertical Farming Modules Are
Bringing Fresh Herbs And Leafy Greens Straight To The Consumer
December 7, 2020
By Greta Chiu
Infarm modules grow fresh herbs and leafy greens by automation, partnering with grocery retailers worldwide.
One of the largest and fastest-growing vertical farming platforms in the world, Infarm’s smart farming modules are bringing a whole new meaning to the word “hyperlocal.”
Best recognized for their grocery store installations that have appeared all over the globe, shoppers are able to watch the growing process and pick from fresh herbs and leafy greens immediately after harvest. Maintained by machine learning and AI technology, each standalone vertical farming unit is continuously monitored and tweaked to ensure optimal growing conditions.
“We control our farms remotely using sensors and a centralized, cloud-based platform that adjusts and improves itself continuously, so each plant grows better than the one before – providing plant seedlings with an ideal combination of light spectrums, temperature, pH, and nutrients for optimal growth,” explains Emmanuel Evita, global communications director for Infarm.
Using machine learning, big data and IoT technologies, the Berlin, Germany-based company is able to collect large amounts of data from their farms around the world in real-time, amounting to more than 50,000 data points within a plant’s lifetime. And the modules aren’t just for grocery stores. Infarm says their easily scalable and rapidly deployable technology has been set up in distribution centres, restaurants and other urban spaces to match local needs.
“With more than 1,000 farms in stores and distribution centers, we’re able to use the data on each one of more than 500,000 plants we grow every month to understand their unique growth patterns and offer the highest quality product to consumers,” says Evita.
The company is deeply committed to improving the safety, quality and environmental footprint of food production. Offering an ever-expanding catalogue with over 65 different combinations of herbs, microgreens and leafy greens, the range of products includes cooking staples like Italian basil to specialty varieties such as wasabi rucola. Infarm’s plants are also grown without the use of chemical pesticides and are locally germinated in their nursery farms. The seedlings are then cultivated in-store for another three to four weeks to maturity before being offered to consumers. The vertical farming units are said to require 95 per cent less water, 90 per cent less transportation and 75 per cent less fertilizer compared to conventional soil-based agriculture. 90 per cent of electricity used by the Infarm network is sourced from renewable energy, and the company has set a target to reach zero-emission food production next year.
“We save thousands of food kilometres by not shipping from abroad, removing trucks from the road, and increasing the resilience of the global food system with every farm we install. Our approach supports biodiversity by reducing and almost eliminating the supply chain of food,” says Evita.
Landing in Canada
Infarm partnered with Empire Company Ltd. and begin rolling out installations in select Sobeys, Safeway and Thrifty Foods in British Columbia earlier this year.
“Our partnership with Infarm is unique in Canada and offers our customers a world-leading urban farming solution,” says Niluka Kottegoda, vice president of customer experience at Sobeys. “By the end of September, we will have fully functional vertical farming units in 28 of our Safeway and Thrifty Foods stores in the Vancouver and Victoria areas with several additional stores carrying the harvested herbs and lettuce.”
Kottegoda says their customers have been responding very well to this urban farming solution. “Not only do they appreciate the sustainable nature of the farms, but they certainly love having access to the freshest possible leafy greens and herbs all year long.” Empire expects to bring Infarm installations into Toronto soon, with a national rollout on the horizon.
Taking the world by storm
First established in 2013 by Osnat Michaeli and brothers Erez and Guy Galonska to help cities become self-sufficient in food production, Berlin-based Infarm now has operations in 10 countries and 30 cities worldwide. Over the past year, they’ve partnered with 30 of the largest retailers in the world, including Albert Heijn (Netherlands), Aldi Süd (Germany), Amazon Fresh, COOP/Irma (Denmark), Empire Company Ltd (Canada), Kaufland (Germany), Kinokuniya (Japan), Kroger (United States), Marks & Spencer (United Kingdom), Selfridges (United Kingdom) as well as others in France, Luxembourg, and Switzerland.
In September, Infarm announced another $170 million in the first close of a funding round expected to reach $200 million. That will bring in over $300 million of funding to date.
By investing this capital into infrastructure, research and development, the company expects to grow their installations by 10 per cent, reaching over 5,000,000 sq. ft. in the next five years.
“The coronavirus pandemic has put a global spotlight on the urgent agricultural and ecological challenges of our time,” says Erez Galonska, co-founder and CEO of Infarm. “As we scale to 5,000,000 sq. ft. in farming facilities across Europe, North America and Asia by 2025, this investment will help us make a truly global impact through our network, preserving the thousands of acres of land, millions of liters of water and ultimately change the way people grow, eat and think about food.”
Topics: Handling Systems Retail Vegetables
Mushroom Company Execs Join Crop One Advisory Board
Crop One Holdings, whose vertical farms company FreshBox Farms grows leafy greens, has added executives from The Giorgi Cos. Inc., parent of mushroom grower Giorgio Fresh, to its advisory board.
October 28, 2018
Crop One Holdings, whose vertical farms company FreshBox Farms grows leafy greens, has added executives from The Giorgi Cos. Inc., parent of mushroom grower Giorgio Fresh, to its advisory board.
Joe Caldwell, president of Giorgi Mushroom Co. and Giorgio Fresh, said the company is “very interested in the potential of vertical farming to transform the fresh produce industry,” in a news release.
Caldwell joined Giorgi Mushroom in 2017, after more than three decades at Monterey Mushrooms.
Brian Loiseau, senior vice president of sales, marking and research and development for Giorgio Foods Inc., also has joined Crop One’s advisory board. He has more than two decades of consumer packaged goods marketing experience, and was involved in the recent launch of Giorgio’s Savory Wild Portabella Jerky.
“We look forward to leveraging our own go-to-market experiences to help Crop One bring exceptional quality produce to everyone’s kitchen tables,” Loiseau said in the release.
ScottsMiracle-Gro to Acquire Sunlight Supply Inc.
The Scotts Miracle-Gro Company a marketer of branded consumer lawn and garden as well as hydroponic growing products, has announced it has entered into a definitive agreement to acquire the assets of Sunlight Supply Inc., in a transaction that will greatly enhance the ability of SMG’s wholly-owned subsidiary,
ScottsMiracle-Gro to Acquire Sunlight Supply Inc.
The pending acquisition of the hydroponic distributor will benefit customers while driving growth and synergies that enhance shareholder value.
April 18, 2018
MARYSVILLE, Ohio, April 17, 2018 (GLOBE NEWSWIRE) -- PRESS RELEASE --
The Scotts Miracle-Gro Company a marketer of branded consumer lawn and garden as well as hydroponic growing products, has announced it has entered into a definitive agreement to acquire the assets of Sunlight Supply Inc., in a transaction that will greatly enhance the ability of SMG’s wholly-owned subsidiary, The Hawthorne Gardening Company, to meet the needs of the rapidly evolving hydroponic products marketplace, according to a press release.
The transaction will create a direct distribution model for Hawthorne that will service more than 1,800 hydroponic retail customers throughout the United States.
Hawthorne, which had 2017 sales of approximately $290 million, owns leading hydroponic brands such as Gavita, Botanicare, Can-Filters and General Hydroponics. Sunlight Supply is the largest distributor of hydroponic products in the United States. Within the last year, Sunlight opened a state-of-the-art 350,000-square-foot distribution center in Vancouver, Wash., and has eight other distribution facilities across North America.
Among the many benefits of the transaction, Hawthorne will possess the most technologically advanced supply chain in the hydroponic supply industry. By being able to ship directly, Hawthorne will have greatly enhanced relationships with hydroponic retailers, giving it greater visibility into current market trends, retail inventory levels and point-of-sale data that will allow it to operate more effectively.
“We are creating a game-changing moment for ScottsMiracle-Gro, for Hawthorne, the hydroponic products industry and the users of our products,” said Jim Hagedorn, chairman, and CEO of ScottsMiracle-Gro. “Combining Hawthorne’s industry-leading product portfolio with Sunlight’s unparalleled distribution capabilities and complementary portfolio will benefit consumers and all stakeholders in the hydroponic marketplace. It reinforces our confidence in the future of this industry and takes Hawthorne to a new level as a business with unique competitive advantages.”
Transaction details and financial implications
In fiscal 2017, Sunlight Supply recorded sales of approximately $460 million and earnings before interest, taxes, depreciation, and amortization (EBITDA) of approximately $55 million. On a combined basis, Hawthorne and Sunlight Supply are expected to have combined annualized sales of approximately $600 million. About 20 percent of Sunlight’s current sales come from distributing Hawthorne’s products and are therefore excluded from the annualized estimate. Additionally, both businesses are expected to see unit volume declines in 2018 due to a temporary disruption to the California marketplace.
In fiscal 2018, the transaction is expected to be dilutive by $0.30 to $0.40 per share on a non-GAAP adjusted basis. The dilution is attributable to the timing of the expected close of the deal, non-cash purchase accounting adjustments including amortization, increased deal costs, and increased interest expense.
Upon completion of the transaction, which is expected by June 1, the Company is launching an initiative it is calling ‘Project Catalyst,’ which calls for Hawthorne to achieve no less than $35 million in financial synergies by the end of fiscal 2019. The company expects to incur approximately $15-20 million in restructuring charges to achieve those synergies. Benefits from the transaction are expected to improve year-over-year non-GAAP adjusted earnings by $0.60 to $0.80 per share in fiscal 2019.
The company has set a goal for Hawthorne to achieve segment profit of approximately $120 million and operating profit margin of 17 to 18 percent by the end of fiscal 2020.
“We have been deliberate in the steps we’ve taken thus far in creating the Hawthorne portfolio and made sure not to disrupt the marketplace as we’ve grown,” Hagedorn said. “The pending acquisition of Sunlight Supply now gives us the green light to aggressively optimize the businesses we’ve acquired and create a more efficient business that better serves the needs of consumers and our customers and drives value for our shareholders.”
Terms of the transaction call for ScottsMiracle-Gro to pay $425 million in cash and $25 million in SMG equity to Sunlight Supply upon completion of the deal. The transaction, which is subject to regulatory approval, will be financed using the Company’s existing credit facility. ScottsMiracle-Gro expects to have a debt-to-adjusted EBITDA ratio slightly above 4.0 times at the completion of the transaction.
“We are extremely pleased with the financial terms of the transaction,” said Randy Coleman, chief financial officer for ScottsMiracle-Gro. “The synergies from combining the businesses makes the transaction even more financially attractive. However, purchase accounting adjustments, deal costs, and financing costs from the deal will trigger a leverage ratio higher than our previously stated goals. Because we believe a leverage ratio of 3.5 times is appropriate for our business, we will focus on returning to that level by the end of fiscal 2019. This will likely slow our share repurchase efforts for the next several quarters, although we have not changed our long-term commitment to return cash to shareholders.”
ScottsMiracle-Gro will release complete financial results for its fiscal second quarter on May 1 and expects to provide a detailed overview of the expected impact of the Sunlight Supply transaction on its 2018 financial guidance. The company currently expects it will announce that Hawthorne segment sales declined approximately 30 percent in the second quarter, including the impact of past acquisitions. The Company also anticipates reporting a 5 percent decline in second-quarter sales for its U.S. Consumer segment as extremely unseasonable weather has delayed the start of the lawn and garden season in many key U.S. markets.
“The entire hydroponic industry continues to see pressure on sales due to the recent regulatory changes in California,” Hagedorn said. “We now expect the challenges in California to continue throughout the balance of fiscal 2018. Because our long-term optimism about this category is unchanged, however, we see no reason for these near-term challenges to delay the implementation of our strategy.”
Combination creates benefits for the hydroponic growing supply industry
The combination of Hawthorne and Sunlight Supply will create immediate benefits for consumers, retailers, and vendors throughout the hydroponic products industry. Upon completion of the acquisition, Hawthorne will have a fully vertically integrated operating model that will ship directly to retailers, providing unmatched capabilities in the industry. The Company believes the transaction will make Hawthorne the preferred distributor for the majority of other manufacturers in this space.
Synergies from the transaction will allow Hawthorne to invest in improved service, more attractive promotional programs for its retail partners, as well as benefit consumers with unique R&D efforts to improve the effectiveness of hydroponic growing products.
“In deciding to join forces with Hawthorne we were seeking a partner who shared our long-term optimism for this industry and was focused on further improving the experience for our retail dealers and current vendors,” said Craig Hargreaves, founder, and CEO of Sunlight Supply. “This is an innovative and smart combination that allows our industry to take a giant step forward and benefits consumers and all of Sunlight’s current stakeholders. We are truly excited to become part of the ScottsMiracle-Gro family and to partner with Hawthorne in creating the most important company in the hydroponic products industry.”
Business operations and leadership team
Hawthorne Gardening Co. will remain based in New York although significant operations will be consolidated in Vancouver, Washington, where Sunlight Supply is based and recently opened a world-class and fully automated manufacturing and distribution facility. Chris Hagedorn will continue to serve as general manager of Hawthorne. Doug Hargreaves, currently executive vice president at Sunlight Supply, is expected to be the lead of operations at Hawthorne upon completion of the deal. Craig Hargreaves is also expected to join ScottsMiracle-Gro in a highly visible capacity upon completion of the deal that allows him to influence Hawthorne’s long-term strategy.
“Craig and Doug Hargreaves are not just seasoned business operators, but are among the most respected people in the U.S. hydroponic industry today,” Hagedorn said. “Completing this deal was contingent on both of them joining our team. I welcome them and the entire Sunlight team as we begin this exciting new chapter.”
Wells Fargo Securities acted as financial advisor to ScottsMiracle-Gro in connection with this transaction.