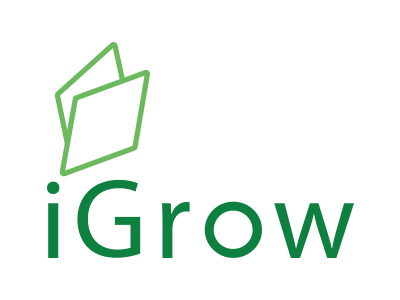
Welcome to iGrow News, Your Source for the World of Indoor Vertical Farming
Dickson Despommier, Professor Emeritus - Contributor To The New Book "The Economics of Sustainable Food: Smart Policies For Health And The Planet "
In The Economics of Sustainable Food, co-authored by Dr. Charles Knirsch, I discuss, as agrotechnology advances rapidly, consumers will no longer have their produce shipped months in advance and from thousands of miles away
I contributed to the new book The Economics of Sustainable Food: Smart Policies for Health and the Planet , Co-Authored by Dr. Charles Knirsch, and am excited to say that it is now available!
In The Economics of Sustainable Food, I discuss, as agrotechnology advances rapidly, consumers will no longer have their produce shipped months in advance and from thousands of miles away. Vertical farming uses a fraction of the resources of conventional farming and allows farmers to grow locally and bring fresh produce to the mass market within days or even hours, reducing the carbon footprint associated with transporting food. Additionally, as climate change brings dramatic weather changes, CEA allows constant conditions regardless of weather patterns. VF thus promises substantial environmental and economic gains, and policy should incentivize vertical farms to grow increasing shares of produce both domestically and across the world.
If you’d like to purchase a copy from Island Press, which ships worldwide, use the code BATINI, which is good for a 20% discount. You can also order the book from Amazon, Barnes and Noble, and your local independent bookseller.
I hope you will consider sharing the book with your own networks.
You can help in a few ways:
Forward this message to your own contacts or
share the news on your social media networks.
Feel Free To Include The Discount Code, BATINI.
· If you’d like to review it for a publication or website, you can request a review copy from press@islandpress.org.
· If you’d like to use it in a class, you can request an exam copy
at www.islandpress.org/request-exam-copy.
· Encourage your organization to contact info@islandpress.org
for details about a discounted bulk purchase.
· Review the book on Amazon, Goodreads, or another review site.
If you have any questions or ideas for how to use the book in your own work, please don’t hesitate to get in touch. I hope you enjoy the book.
All the best,
Dickson
Purdue Study Addresses Environmental, Economic Impacts of Hydroponic, Aquaponics Systems
Hydroponics and aquaponics offer promise for growing produce and raising fish. But some may be wary of entering the industries because of perceptions about high capital and operational costs and environmental impacts
October 22, 2020
Story by Brian Wallheimer
Hydroponics and aquaponics offer promise for growing produce and raising fish. But some may be wary of entering the industries because of perceptions about high capital and operational costs and environmental impacts.
Purdue University scientists compared the environmental performances of both systems and calculated their economic efficiencies in Indiana. Their findings, published in the Journal of Cleaner Production, inform those interested in entering hydroponic or aquaponic industries on how to get the most for their investment with the least environmental footprint.
Hydroponics and aquaponics are soilless systems. Hydroponic plants are grown in water containing chemical fertilizers as nutrients. Aquaponics adds the raising of fish and uses fish waste to replace chemical fertilizers. These indoor operations come with upfront capital costs and require use of significant amounts of energy for lighting, heating and water pumping, as well as fish feed and fertilizers.
For one month, graduate students Peng Chen and Gaotian Zhu raised six vegetables in a hydroponic system and those same vegetables with tilapia in an aquaponic system. Experiments were conducted in the lab of Hye-Ji Kim, a Purdue assistant professor of horticulture and landscape architecture, and in collaboration with Paul Brown, a Purdue professor of forestry and natural resources. Jen-Yi Huang, a Purdue assistant professor of food science and the leader of the project, worked with the students to conduct a life cycle assessment using the data they collected.
Purdue University researchers conducted a life cycle assessment of hydroponic and aquaponic growing systems in Indiana to measure their environmental and economic impacts. (Photo provided by Peng Chen)
The researchers found that the aquaponic system led to 45 percent less environmental impact when considering fossil fuel use, global warming, water acidification and eutrophication created by resources used as well as waste and emissions released. Twice as much food is grown in the aquaponic systems with little added environmental cost.
“The aquaponic system is more environmentally friendly when you look at the total environmental footprint per US dollar of economic value of the products,” Huang said. “But that is based on using Indiana’s current energy mix. If we consider using more renewable energy sources, things start to change.”
Indiana currently gets almost 60 percent of its energy from coal-fired power plants, according to the U.S. Energy Information Administration, with about one-third coming from natural gas. The less electricity hydroponic and aquaponic growers source from fossil fuels, the more environmentally friendly their operations become.
Chen said that changing the mix and getting one-third of power from coal, natural gas and wind would reduce the environmental impacts of hydroponics by up to 48 percent. If an operation sourced its electricity solely from wind energy, hydroponic operations would be considered slightly more environmentally friendly than aquaponics.
“By using wind energy, which is largely produced in Indiana, farmers can reduce their environmental footprint enough to make these two systems essentially equal in terms of the economic output gained for the environmental cost,” Chen said. “By choosing more plant-based fish feed, the environmental impacts can be further reduced in aquaponic systems.”
GreenFactory Emirates: The Largest Indoor Farm In The World To Be Developed In Abu Dhabi
GreenFactory Emirates will develop an innovative indoor farming with the world's most advanced indoor growing system from The Netherlands
Barendrecht (The Netherlands) and Abu Dhabi (UAE)
September 22, 2020
A joint venture between GrowGroup IFS from Barendrecht (The Netherlands) and RainMakers Capital Investment LLC from Abu Dhabi (UAE) will build the largest indoor farm in the world in the desert of Abu Dhabi. The GreenFactory Emirates will produce 10,000 tons of fresh produce per year on a plot of 17.5 hectares and a cultivation area of 160,000 square meters.
GreenFactory Emirates will develop an innovative indoor farming with the world's most advanced indoor growing system from The Netherlands. It is a combination of vertical and flat farming and solves the normal cultivation restrictions due to extreme climates in regions as the UAE. The facility will involve numerous leading agro-technological companies in its construction as best of breed for each component will be sourced through top-tier Dutch companies. It is now possible to cultivate high-quality vegetables 100% pesticide-free, all year round and anywhere on the planet: “Quality of Holland – Local Grown.” From seeding, harvesting, processing to "ready to eat" products will take place under one roof.
The joint venture also plans to build other indoor farms in other regions of the world where extreme climates are a challenge to normal cultivation.
Water, Co2, and waste
The GreenFactory will be saving 95% of water consumption as opposed to standard methods of cultivation as well as reducing its Co2 footprint up to 40%. By growing fresh produce locally, GreenFactory Emirates will also contribute to reducing waste in various other areas. Its contribution to slowly reducing reliance on fresh foods imports will in turn reduce waste of produce occurring during the transport process while reducing logistical traffic.
Research and development
GreenFactory Emirates will include a built-in research and development component that will help ramp up the production beyond the 56 current varieties of lettuces, leafy greens, herbs, and kale. It will also optimize its production by collecting real-time data to inform future global expansion of indoor farming. With confirmed partnerships with GAAS Wageningen and Delphy in The Netherlands, GreenFactory will benefit from live feedback provided by some of the best students and Academia in the field.
Food security
Food security is high on the UAE’s agenda. The country aims to be number 1 on the Global Food Security Index by 2051. In 2019, the UAE ranked on the 21st place on the Index, jumping an impressive 10 places from number 31 in 2018. Boosting local production and creating an enabling environment for agri-tech is a top priority for the government. The UAE strives to become a knowledge hub with regards to food production in heat, high humidity, and high salinity soil. The private sector (supermarket chains and the hospitality industry) has also set ambitious targets for itself in order to sell more local produce.
Partnership
The partnership between GrowGroup and rainMKRS is initiated and a result of an introduction made by the Embassy of the Kingdom of The Netherlands in the United Arab Emirates and the Monarch Group which has played an instrumental role in seeking opportunities and nurturing relationships.
Expo 2020 Dubai
The total project amounting to 650M AED (150M EURO) is planned in different phases in 3 years. Phase 1 will be operational before Expo 2020 Dubai in October 2021, so GreenFactory Emirates can show the world its innovations. A kick-off for more similar projects and innovations worldwide.
GrowGroup IFS
GrowGroup IFS (Innovative Farming Solutions), founded by CEO John Breedveld in Barendrecht in The Netherlands, is specialized in developing indoor farming based on the most advanced Dutch innovative farming solutions, especially in regions where normal cultivation is restricted by extreme climate and or limited space.
rainMKRS Capital Investment LLC
With offices in Abu Dhabi (UAE) and Montreal (Canada), rainMKRS is an entrepreneurial catalyst co-founded by a group of Emirati and Canadian entrepreneurs. Led by Mohamed Jouan Al-Dhaheri, Sultan Al-Nassour, Sebastien Leblond, and Jonathan Mérineau Gosselin, rainMKRS brings together the world’s most impactful companies and projects in the food and agriculture sector and UAE’s economic, educational, and investment stakeholders. rainMKRS’ objective is to help bridge the gap between these stakeholders in order to accelerate the progress on critical and strategic components in support of the UAE desire to achieve food security.
GreenFactory Emirates is its first of many initiatives in the field.
The Second Generation of Vertical Farming Is Approaching. Here’s Why It’s Important
Current market prices for 1 kg of leafy greens are around $33 for vertically-grown produce and $23 for organic produce. As vertical farms invest and employ higher levels of technology, they will be able to increase their competitive advantage by driving down costs and prices
November 4, 2019
Editor’s Note: Boaz Toledano is a business consultant specializing in vertical farming and other agtech markets. His website is: www.EconoMind.co. Here he writes about how vertical farming is progressing into its next stage. Disclosure: Toledano independently included mention of one of the AgFunder’s portfolio companies IGS (Intelligent Growth Solutions).
Vertical farming practitioners claim to be pioneering the third agricultural revolution.
Vertical farming is the practice of growing produce in vertical stacks using soil, hydroponics or aeroponics to deliver water and nutrients to the plants.
With seemingly higher-quality produce that is grown efficiently, locally and with a potentially lower environmental footprint, the industry appears to be a promising answer to the rising need for sustainable farming methods.
The market was valued at $2.3 billion in 2018 and investments grew significantly from $60 million in 2015 & 2016 to $414 million in 2017 & 2018. What’s less commonly known, however, are the challenges vertical farming companies face and the prospects of overcoming them in order to establish the viability of this industry.
Want to invest in the foodtech and agtech revolution?
Join Us! Sign up for our Asia fund here.
Not surprisingly, capital expenditure (CAPEX) is high. A smallscale, low-tech vertical farm employing 1st generation technology (more on this later) can cost around $280 thousand to start. However, when we consider the more complex operations, those that employ 2nd generation technologies, the setup costs may surpass $15 million.
In order to understand why these figures are so high, we must first understand the difference between the two generations of vertical farming technologies, and why the transition between the 1st and the 2nd is the most important process in this industry’s short history.
First-generation technology enables the basic functions of a vertical farm to occur without the constant intervention of human operators. Second-generation technology enables the growing process to not only be automated but also be continuously optimized to the requirements of the plants being grown. These two generations can be further divided into five levels, detailed below. Generally, the more a company has advanced down these levels, the better its competitive advantage.
When vertical farms were being established around the world about a decade ago, they employed 1st generation technology. These operations showed it was possible to grow food — and other plants — in vertical structures, thus enabling a more efficient use of land. On average, 2nd generation vertical farms yield 55 times more produce per unit of area compared with conventional farms. For the first time in modern history, food could be grown in cities, where it is eaten.
It has also become possible to remove problematic sections of our food supply chain, for instance, transportation and the pollution that goes with it, excessive packaging and preservatives. Also, we could finally reconnect to the source of (some) of our food, a privilege that was removed from our lives around the 17th century, when the Second Agricultural Revolution — also known as the British Agricultural Revolution — sparked the industrial revolution that led to mass urbanization.
Next, vertical farms had to prove their economic viability. Virtually the only way companies were able to become profitable is by using technology to cut down on the high operating expenses (OPEX), which mainly consist of lighting and labor (~30% of OPEX each).
Enter 2nd generation technology.
In a vertical farm, LEDs (light-emitting diodes), which provide light to the plants, are more efficient than other forms of artificial lighting that were used in the past (fluorescent and incandescent), resulting in lower operating costs. According to the International Energy Agency (IEA), LED lighting efficiency is expected to increase by an extra 70% by 2030. The pricepoint also continues to drop.
Labor expenses will be tackled by automation. Many startups and some capital-backed growers are developing technologies to help vertical farms reduce their dependence on human labor, with remarkable achievements. A noteworthy example is IGS (Intelligent Growth Solutions), which has developed an automated system that enables highly efficient production using modular structures. The company claims to have reduced labor by up to 80% and power by up to 50%. Its plan is to sell its technology to companies that want to improve the efficiency of their vertical farms’ operations.
Another example is Plenty, an industry leader and one of the best-funded vertical farming groups globally, which was able to improve the energetic efficiency of its newest facility, Tigris Farm, fivefold, compared with its previous facility. Though quite secretive, we now know that the company uses plant management automation to transfer its growing towers around the warehouse, as well as harvesting automation.
These are examples of the OPEX reduction trends the industry is seeing. Lighting improvements should reduce OPEX by 12%, and automation should cut OPEX by a further 20%+.
Since vertical farms have thus far introduced mediocre returns on investment (ROIs), these reductions in OPEX are crucial for the industry to prove itself to investors, governments, and companies considering entering the market. Although CAPEX will remain high compared with conventional and organic farming, the 30%+ expected reduction in OPEX makes a compelling case for vertical farming.
Current market prices for 1 kg of leafy greens are around $33 for vertically-grown produce and $23 for organic produce. As vertical farms invest and employ higher levels of technology, they will be able to increase their competitive advantage by driving down costs and prices. Eventually, I believe, they will be able to compete with organic producers, who last year operated in a $100 billion market.
Can Vertical Farms Be Profitable?
“There are both small and large leafy greens vertical farms,” Hernandez said. “Some of them are going out of business and some new ones are opening up. All of them have similar challenges
By David Kuack, UrbanAgNews.com
March 15, 2019
Although vertical farms producing leafy greens are receiving most of the press coverage, there are a variety of other crops being being grown and innovative growers are finding these crops to be profitable.
When you think about a vertical farm what picture comes to mind? Ricardo Hernandez, horticulture professor at North Carolina State University, said most people think of vertical farms as indoor growing operations that produce leafy greens, primarily lettuce.
“There are both small and large leafy greens vertical farms,” Hernandez said. “Some of them are going out of business and some new ones are opening up. All of them have similar challenges.
“The main challenge is that even though they can produce a lot of leafy greens because they are able to stack the plants, there is a bottleneck in terms of how fast they can produce the crops. The bottleneck is tied to the plant genetics. With the current plant genetics and cultivars that most vertical farm entrepreneurs are using, it is very hard to outperform the lettuce crops coming out of the field. This is especially the case if the field conditions are suitable to grow lettuce such as in California and the southern part of Arizona during the winter.”
For many of the cultivars being grown in the field, including butterhead, red leaf lettuce and baby greens, the same seed is being used in vertical farms.
“In order for the leafy greens produced in vertical farms to actually gain significant market share, the genetics have to be changed in those plants,” Hernandez said. “This can come through conventional breeding or gene editing or through targeted breeding using molecular tools. A new set of cultivars is needed, a new set of genetics that are specific for indoor farms. Right now we are using the genetics that are good for field production. These field cultivars have high plant uniformity in terms of growth under a large variability of environmental conditions. The field genetics enable plants to look the same even if there is a lot of variability in the environment.”
Ricardo Hernandez, horticulture professor at North Carolina State University, said one of the biggest challenges facing vertical farms growing leafy greens is the lack of cultivars bred specifically for these production facilities. Photos courtesy of Ricardo Hernandez, N.C. St. Univ.
Because vertical farms provide a stable environment, Hernandez said the types of genetics that are needed are specifically for an environment that can be controlled. The genetics for field crops of maintaining high uniformity and minimizing large variability are not a concern with vertical farms.
“Unfortunately, the market for breeding companies to develop varieties specifically for vertical farms is small,” Hernandez said. “There is not an established market for vertical farm growers. There hasn’t been a significant effort by established breeding companies to start developing cultivars specifically for vertical farms. Maybe some startups will be able to develop new cultivars or university researchers may be able to give those efforts a boost.”
Cost of production
One of the major hurdles with vertical farms is cost of production.
“There is a lot of technology and utilities associated with producing leafy greens in vertical farms,” Hernandez said. “That cost of production is very high compared to the leafy greens grown on the West Coast even when the shipping costs are added on.
“There actually are some vertical farms making money. Some of those are in boutique markets. These growers are able to get more money for a head of lettuce than the competing product that comes from the field. However, it is going to be difficult for growers who are selling to boutique markets and who receive a premium price for a head of lettuce to break into the mass market. Most consumers are not willing to pay the higher boutique prices.”
Hernandez said in order for vertical farms to acquire a significant share of the market, they are going to have to bring down the price of lettuce so more people will be willing to pay for the product.
Making money with transplants
One area of vertical farm production that Hernandez said growers can be profitable is producing transplants or starter plants.
“I’m convinced based on economic studies that we have done in my lab, using vertical farms or indoor growing is economically viable for growing transplants or starter plants,” he said. “Growing transplants is a very economical way to successfully adopt vertical farm production. These starter plants are a high value product and they can be grown under very high density in vertical farms, even higher than they can be grown in a greenhouse. These transplants are inserted into the current supply chain and will be sold to greenhouse and field growers who will produce the end products.”
Hernandez has started a transplant vertical farm, Grafted Growers, with his business partner John Jackson. Hernandez said growers looking to produce transplants in vertical farms should choose crops considered to have the highest value.
“These would be transplants that benefit the most from being grown indoors,” he said. “The clean controlled environment of a vertical farm can ensure a very high germination rate and a lot of plants can be produced in a small area. The controlled environment of vertical farms also provides a desirable outcome including finished plants that flower sooner or plants that have more dry mass.”
The controlled environment of a vertical farm used to produce transplants can ensure a high germination rate and can produce a lot of transplants in a small area.
Hernandez said the uniformity and quality of transplants grown in a greenhouse may not always match transplants grown in vertical farms.
“If there is good solar radiation levels, greenhouse growers can produce very good transplants,” he said. “If growers are trying to produce those transplants in greenhouses during the fall or winter, they may have to supplement the natural light levels or the quality of the transplants may not be as good. There may be a difference in quality and uniformity between seasons.
“Growing transplants in a vertical farm the quality of the transplants is consistent no matter what the outdoor conditions are. Comparing transplants grown in a vertical farm with transplants grown in a greenhouse during the winter, which is when many transplants are grown, the vertical farm transplants usually have a higher dry mass and are more uniform.”
Hernandez said a grower producing transplants during the winter may be able to match the quality of vertical farm transplants if a lot of supplemental light is used.
“It’s not only the amount of light that is important, but also the quality of light,” he said. “Even though transplants grown in a greenhouse may be receiving enough light with the use of supplemental light, depending on the light spectrum the transplants could end up stretching because they are planted at a high density.
“In a vertical farm the transplants can be kept from stretching by controlling the light spectrum so that they can be grown compact in a very high density. By taking the sun out of the equation and controlling the plant growth with artificial light eliminates the potential for stretching.”
Having the right vertical farm setup
Hernandez is quick to caution growers considering starting a vertical farm that different crops require different production setups.
Different crops require different vertical farm setups. The production setup that is optimum for for transplants may not work for leafy greens.
“Growers can create a lot of microclimates and have poor uniformity when they have the wrong vertical farm setup,” he said. “The vertical farm that works for leafy greens may not work for transplants because the requirements for transplants uniformity are different from those for leafy greens. If growers don’t have the right vertical farm to grow transplants, it’s not going to be easy and it could become a bigger problem.
“Growers need to listen to the plants and know what the plants need. Growers can incorporate a lot of technology, including robotics and sensor control, but if they are not listening to what the plants need, the technology will only deliver marginal improvements. The most important thing in a vertical farm is the plants. Everything else is just details.”
For more: Ricardo Hernandez, North Carolina State University, Department of Horticultural Science, Raleigh, NC 27695-7609; rhernan4@ncsu.edu; https://hortenergy.cals.ncsu.edu.
This article is property of Urban Ag News and was written by David Kuack, a freelance technical writer from Fort Worth, TX.