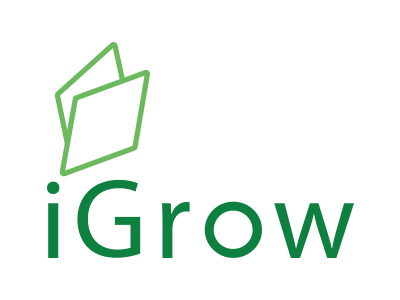
Welcome to iGrow News, Your Source for the World of Indoor Vertical Farming
Robotic Warehouse Farms Will Save The World
The theory behind CEA is that by controlling the environment in which it grows, we can control everything about a plant and what it grows into by micro-tweaking one of a thousand different characteristics―including temperature, humidity, light duration, light wavelength, dissolved oxygen in the water, and carbon dioxide saturation in the air
by Elle Griffin
Four years ago, Ritch Wood was looking for a better way to grow plants. As the CEO of global skincare company Nu Skin, he ran into ingredient shortages every winter when fields went dormant―and when he moved grow operations to the equator he ran into water and land shortages, along with a host of quality control issues.
Nu Skin needed reliable, quality ingredients for their skincare products. But farming was too unpredictable an industry. “If there was a way to grow indoors,” he thought, “and be able to do that 24 hours a day, 365 days a year―if we could guarantee that it was grown without any herbicides or pesticides and in a sustainable way that uses less water and land―that would be really helpful.”
At the time, controlled-environment agriculture (CEA) was in its infancy and grow-light technology had yet to take a turn for the more affordable. When he learned of an agricultural system that promised to use a fraction of the land and water used by traditional agriculture methods and had the potential to make it more affordable, Wood made an investment.
Nu Skin paid $3 million for 70 percent of the company and rights to its IP―and Grōv Technologies was born.
Grōv grass grown in the Olympus machine at the Bateman Mosida Farms. Photo from Grōv Technologies
Controlled-environment agriculture is on the rise
The theory behind CEA is that by controlling the environment in which it grows, we can control everything about a plant and what it grows into by micro-tweaking one of a thousand different characteristics―including temperature, humidity, light duration, light wavelength, dissolved oxygen in the water, and carbon dioxide saturation in the air. By tweaking the growing cycle, we can control the caloric content as well as the nutrient content and density of the plant.
“What we’ve learned through controlled-environment agriculture,” Benjamin Swan, co-founder and CEO at Sustenir in Singapore, once told National Geographic, “[is] we can actually emphasize certain characteristics of the plants. So, without using GMO, we can make our kale softer, we can actually make it sweet.”
The theoretical use cases for this technology are endless―from being able to grow in places where water is scarce (like in much of Africa), or where water is overly abundant (like Hawaii), or in places where labor is scarce (like in parts of Asia), or even in places that have long winters (like Northern Europe). Theoretically, we could have grow towers in every town and feed the whole of it no matter its natural environment.
We could even grow those foods to those cities’ exact nutritional needs―more vitamin D-rich foods in wintery places, for example. Dr. Lee Mun Wei, a senior manager at the Food Innovation and Resource Centre (FIRC) in Singapore aims to predict and prevent illness in a given population by tracking their biometric data using Apple watch-like wearables, then 3D printing nutrient-specific foods that could mitigate imbalances.
Though these technologies exist, they are still in their infancy. Singapore leads much of the research and development out of necessity. With limited land and water resources, the county is forced to import 90 percent of their food and 40 percent of their water from outside the country. As a result, they have no option but to grow vertically and desalinate water from the ocean.
Elsewhere, the industry has been slow to catch on, largely due to exorbitant startup costs, low returns, and lack of urgent need. According to a 2017 State of Farming report by L.E.K., only 27 percent of indoor, vertical farms are profitable compared with 50 percent of container farms and 75 percent of greenhouses. But one thing has spurred the industry on in recent years: cannabis.
Legalized in 39 states, demand for cannabis has created a $13.6 billion industry and enough capital to fund CEA-enabled grow operations. “When you have a crop that fetches up to $2,400 or $2,500 a pound, you need to be able to dial everything in and make it consistent and repeatable,” says Dashiel Kulander, co-founder and CEO at Boojum Group. “If the temperature swings five to 10 degrees on a cannabis plant, that will change the plant’s various cannabinoids. The goal is to create a medicine that is consistent batch after batch.”
It’s only recently that there has been some financial incentive to use CEA technologies for food use―largely driven by Big Ag players hoping to hedge out the competition. Berry farming giant Driscoll’s, for one, led a $500 million round to fund Plenty, a 2.2-acre vertical farm in California they hope will help them fulfill a contract with Albertsons. The Ingka Group, for another, led a $100 million round to fund AeroFarms, a 2.4-acre vertical farm in New Jersey that will help them fulfill a contract with Singapore Airlines.
Grōv tent at the Bateman Mosida Farms. Photo from Grōv Technologies
Grōv Tech is building CEA prototypes in Utah
By investing in Grōv Tech, Nu Skin hopes to do something similar, getting ahead of the supply chain that fuels their skincare products before the competition can beat them to it, or before climate change makes traditional methods more difficult, all while shoring up technology that could provide a farming model that is more sustainable―if only it were more economical.
“The purpose was always, can we build a better product for Nu Skin?” Wood says. “We think there’s a huge story around the ingredient sustainability, and there were a lot of ingredients we felt we could grow, but the challenge was: could we do it in an economical way?”
Grōv Tech started out with a prototype: a tower that pairs hydroponic growing technology with grow lights. But like all CEA startups, a lot of the growing process was manual and the technology was prohibitively expensive. To make something that was scalable and profitable the whole thing needed to be automated and it needed to be cheap.
With this goal in mind, Wood decided they would start by growing animal feed for Bateman’s Dairy farm. Having grown up on a dairy farm himself, Wood figured this would allow the company to scale the product while refining and automating the technology to the point that it could be replicated. And all of this would have a fortuitous effect on Nu Skin’s bottom line.
“One of our bestselling products is a weight-loss protein powder which uses whey protein,” Wood says. “So again, a very nice connection there is if the animal is eating a more sustainable product and producing better milk with better protein and it’s being done in a sustainable way―certainly that can be a benefit to Nu Skin down the road.”
One year into feeding the 20,000 animals at Bateman, the company has learned a lot. For instance: cows need a lot of magnesium, but they don’t like eating it. Now, Grōv Tech puts magnesium in the water so it’s directly absorbed into the plant and then becomes bioavailable to the cow upon eating it. And because the growing process only takes seven days, data scientists can analyze the results in real-time and adjust the components to optimize production for the next batch of feed.
According to Grōv Tech president Steven Lindsley, it’s not far off that we’ll be looking at milk production (butter, fats, and proteins) and optimizing a herd’s diet for taste, quality, and nutritional value―not to mention the wellbeing of the animal. We’ll be able to look at how many trips from the veterinarian an animal gets when they’re fed certain nutrients in their diet, and whether they can have more calves and produce the same amount of dairy on less, better quality feed. (So far, the answer to this last question is yes. When animals are fed better quality food they need less of it―just like humans.)
And if we hook all of the cows up to robotic milking equipment and connect everything to artificial intelligence, machine learning, and the Internet of Things―Lindsley’s far-flung goal―then we might be able to collect enough data to not only feed cows to their optimum health and performance ability, but humans too. And that could have ramifications not only for feeding the world, but nourishing it― just like Dr. Wei hopes to do in Singapore.
“Last year was about starting to feed animals and get data and prove out the hypothesis we have while continuing to perfect the technology and get confidence there,” Wood says. “And now we’re really to a point where we’ve got data that proves that it works and that financially it’ll be a good thing for a farmer. So now we can really take that proposition to farmers and start to scale.”
Olympus Tower Farm at Bateman Farms in Mosida, UT. Photo from Grōv Technologies
CEA technology could feed the world
Right now, Grōv Tech is focused on refining its technology right here in our own backyard. But once they do that, the plan is to expand internationally.
“Saudi Arabia has actually passed a law where you cannot use water to grow fodder or feed for animals, so all of that now has to be imported. China imports one-third of their alfalfa feed for their dairy animals because they don’t have the capability of growing it,” Wood says. “So there are countries that will probably benefit more than the US would. But we’ve got to refine the technology and get that built to where it’s ready to scale before we start spreading ourselves all around the globe.”
CEA technology is just getting started. Like the Tesla Cybertruck, we have a working concept that promises a more-than-Jetson’s-level future many of us can see the benefits of and actively want―it’s just not quite available to the masses yet. But with more than a billion dollars invested in the technology in just the past few years alone―we’re getting there. And the “there” we are heading toward is rosy indeed.
“To put it in perspective, one tower that is about 875 square feet on the ground will replace 35 to 50 acres of land,” says Lindsley. “And that will feed the animals on roughly five percent of the amount of water. The UN says that that the world will add about 2.5 billion people in the next 30 years. And we have to find a way to feed them on arguably less arable land and water. The good news is the technology is coming along to help solve that equation.”
If COVID-19 taught us anything, it’s that our food supply chain is fragile. But that’s only because our supply chain was built to grow food in California, refrigerate it so it stays fresh, then transport it 1,500 miles so we can eat a salad in the winter in Chicago. In the future, that might not be a thing. “We’re having a dry year now,” Lindsley tells me in February. “But a year ago we were in a blizzard, and even in the middle of a blizzard in February in Utah, we’re pumping out fresh, beautiful, safe green grass for animals. It’s a paradigm shift.”
“Four years ago it was a good idea,” Wood tells me of his company’s investment in CEA technology, “But four years from now it’s going to be required.”
Elle is the editor-in-chief of Utah Business and a freelance writer for Forbes, The Muse, and The Startup. She is also a literary novelist and the author of a weekly newsletter called The Novelist.
Learn more at ellegriffin.com.
How Indoor Vertical Farms Use Big Data And Robotics To Grow Animal Feed
"Grov focuses on producing feed for animals to produce the other foods we depend on," said Lindsey. "Climate change, droughts, foods, etc., are reducing the water and arable land needed
These indoor vertical farms are designed to help farmers grow animal feed with less water and land.
GROV TECHNOLOGIES
PitchBook's December Q3 2020 Agtech analyst report highlighted a 14% decline in venture capital deals from Q2, 2020, but according to Alex Frederic, senior analyst of emerging technology at PitchBook, despite the declining overall AgTech investment, Animal Ag was up in Q3 2020 and estimated to reach $9.56 billion by 2025.
Frederic says Animal Ag companies are developing technology solutions to monitor, analyze, and optimize animal health and production in two primary categories: livestock and aquaculture.
"COVID-19 has highlighted the vulnerability of agriculture systems and the importance of maximizing animal health and nutrition," said Frederic. "We expect investment in animal ag hardware, such as robotics and wearables, to pick up in the near term given the rising concern over food security and animal supply chains."
Indoor vertical farming for animal feed
Animal Ag vertical farming newcomer Grov Technologies, which was acquired by Nu Skin Enterprises (NYSE:NUS) in 2016, announced in December 2020, the company was collaborating with Amazon Web Services (AWS) to apply cloud-based machine learning capabilities to their vertical robotic farming indoor platform to grow high-density nutrient (HDN) animal feed.
According to Steve Lindsey, president of Grov Technologies, most indoor farming around the world is focused on the production of vegetables and greens for human consumption.
"Grov focuses on producing feed for animals to produce the other foods we depend on," said Lindsey. "Climate change, droughts, foods, etc., are reducing the water and arable land needed. Highly digestible feed has the potential to reduce animal emissions. Farmers will need to produce more with less under more challenging conditions. Indoor vertical farming help mitigate some of these issues."
Less water, less land
Lindsey adds that the most striking change of using a vertical farm is producing feed using less water, a fraction of the land, and reducing the cost and carbon emissions from transportation by placing indoor feed centers next to the cattle they feed.
"Many locations around the world are struggling to feed their populations, let alone their animals, [..] we put the farmer in a better position to control his future while mitigating the effects of weather," added Lindsey.
Grov's Olympus Tower can produce 5,000 to 6,000 pounds of sprouted wheat or barley grass per day using less than five percent of the water and replacing between 35 to 50 acres compared to traditional farming. Lindsey says that the Olympus Tower requires minimal labor because it uses robotic seed-to-harvest technology.
Lindsey says that since consumers are demanding greater visibility and traceability to proven sustainability practices, they want to know that animals are fed highly digestible and pesticide-free diets while using less water and land.
"Consumers are awakening to a greater understanding of how fragile food and feed supply chains are," added Lindsey.
Sensors, robotics, and machine learning
Grov's indoor vertical farms are equipped with micro-sensors that capture temperature, humidity, water flow, and growth rates from each growing tray in the tower. That data is correlated to calibrate the trays' rotation, the watering, lighting spectrum, and the robotic seeding ad harvesting.
"Our technology fuses the Internet of Things (IoT), cloud, robotics, machine learning with lighting and spectrum management [..] to maximize potential yield and nutrition of a variety of crops," said Lindsey.
Lindsey believes that controlled environment agriculture is emerging as an impactful technology that can help address global climate change issues and sustainability for food and feed production.
"Covid 19 has alerted us that food and feed security is one of the most pressing issues of our day," said Lindsey. "The world is simply using too much land and water to feed animals. Increasing the use of efficient and sustainable technology can potentially make a difference."
Utah Farm Using Robotic Vertical Farming To Feed Their Animals For Less
"The key is you can eliminate the weather challenges and it can give you a predictable optimized crop every time," said Steve Lindsley, the president of Grōv Technologies
The Future of Farming Is Here In Utah, All Thanks To Something Called
Robotic Vertical Farming
By: Jordan Hogan
Posted at 8:19 AM, Nov 29, 2020
and last updated 7:08 AM, Nov 30, 2020
MOSIDA, Utah — A Utah tech company, Grōv Technologies, is working with a local farm, Bateman and Mosida Farms, to produce food for their cows more efficiently.
It's being done in towers that handle the whole growing process from start to finish.
The farm produces milk and meat from their cows, but raising them takes a lot of feed and a lot of time.
Now, technology is making part of the process easier.
Olympus Tower farms made by Grōv are a form of robotic vertical farming.
"The key is you can eliminate the weather challenges and it can give you a predictable optimized crop every time," said Steve Lindsley, the president of Grōv Technologies.
It starts with wheat seeds being loaded into trays. Then, they're wheeled up to the top of the tower to start a six-day journey back down to the bottom of the tower for harvest.
Along the way, they're watered with precision and given light from special LEDs that don't give off any heat.
The whole process is automated too, meaning it can run without the help of many traditional farmhands.
Grōv says each one of the towers produces 6,000 lbs of food each time it goes through its cycle. That saves money, time, water and energy. The benefits don’t stop there either — they are then passed on to the consumer.
"Each of these machines represents between 35 and 50 acres of land, so in this case here, it's the same as 50 acres of land but it's only covering 875 square feet of the ground and it uses 95% less water to grow the crops," said Lindsley.
Saving water and space is something that's becoming increasingly important as the demand for more homes increases and climate change increases the chances for extreme drought in the summer months.
"One of the biggest challenges farmers have around the world is how do they deal with the weather, the climate, and the uncertainties that come with that," Lindsley said.
The new technology couldn't have come at a better time for the farm either.
"In the first weeks and the first month of the COVID-19 Pandemic things started to go a little bit crazy," said Brad Bateman, a farming operations partner at Bateman Mosida Farms.
He said the farm wasn't able to order in a lot of their feed at the beginning of the pandemic, threatening the cows' food supply.
Now they can rely on their own production of feed, and this model of farming could be adopted beyond farms in the future.
"The vision that I see is there’s probably one of these in the back of every supermarket growing fresh food right in the store," said Bateman.
Grōv Technologies told FOX 13 they plan on rolling out this technology worldwide once they reach agreements with other farms.
CubicFarms Systems Corp. Announces C$3.8 Million Sale of Commercial Scale Systems to Farming Customer in Indiana
The Company’s commercial agreement with Vertical Acres is for the sale of 21 CubicFarms machines, including 17 cultivators, three propagators, and one fertigator, for a complete CubicFarm installation
VANCOUVER, B.C., NOVEMBER 25, 2020 – CubicFarm® Systems Corp. (TSXV:CUB) (“CubicFarms” or the “Company”), a technology company developing and deploying technology to feed a changing world, announced today that its automated, controlled-environment growing technology has been selected by Vertical Acres Farm LLC (“Vertical Acres”), an Indiana-based produce company, to grow commercial quantities of fresh produce for the region.
The Company’s commercial agreement with Vertical Acres is for the sale of 21 CubicFarms machines, including 17 cultivators, three propagators, and one fertigator, for a complete CubicFarm installation.
The agreement, which includes a deposit received from Vertical Acres, represents approximately C$3.8 million in anticipated revenue to the Company. The technology is expected to be installed in Indiana in the first half of 2021.
The Company’s patented CubicFarms technology will enable Vertical Acres to grow high-quality foods, with predictable crop yields indoors, all year round.
CubicFarms CEO Dave Dinesen, commented: “We are looking forward to our partnership with Vertical Acres to help them successfully grow high-quality, great tasting, local produce in Indiana, and for the neighbouring regions. Our patented technology should enable them to maximize their production per cubic foot, while greatly reducing the physical footprint of their traditional farming operations.”
Vertical Acres owner Fred Schakel, said: “We evaluated a large number of indoor growing systems and chose CubicFarms as the optimal commercial-scale fresh produce system solution. We love the idea of the perfect growing environment, the fraction of water it takes to grow our greens, and the freedom from contaminants that the Cubic system affords. We are excited that we will be able to supply our local community with fresh, perfect greens every day of the year without the influence of bad weather always weighing on our production model. With CubicFarms’ excellent technology, we are truly looking forward to this partnership.”
Private Placement
The Company also announced that pursuant to a non-brokered private placement (the “Offering”), the owners of Vertical Acres have agreed to purchase 225,500 common shares of the Company at a purchase price of C$0.78 per common share for gross proceeds of C$175,500.
The Company intends to use the proceeds of the Offering for general working capital purposes.
Closing of the Offering is subject to approval of the TSX Venture Exchange.
Mr. Schakel commented, “After performing significant due diligence on the Company’s technology, we are excited to further demonstrate our conviction in CubicFarms through this investment in its business.”
Neither the TSX Venture Exchange nor its Regulation Services Provider (as that term is defined in the policies of the TSX Venture Exchange) accepts responsibility for the adequacy or accuracy of this release.
About CubicFarm® Systems Corp.
CubicFarm Systems Corp. (“CubicFarms”) is a technology company developing and deploying technology to feed a changing world. Its proprietary technologies enable growers around the world to produce high quality, predictable crop yields. CubicFarms has two distinct technologies that address two distinct markets. The first technology is its CubicFarms™ system, which contains patented technology for growing leafy greens and other crops indoors, all year round. Using its unique, undulating-path growing system, the Company addresses the main challenges within the indoor farming industry by significantly reducing the need for physical labour and energy, and maximizing yield per cubic foot. CubicFarms leverages its patented technology by operating its own R&D facility in Pitt Meadows, British Columbia, selling the system to growers, licensing its technology and providing vertical farming expertise to its customers.
The second technology is CubicFarms’ HydroGreen system for growing nutritious livestock feed. This system utilizes a unique process to sprout grains, such as barley and wheat, in a controlled environment with minimal use of land, labour and water. The HydroGreen system is fully automated and performs all growing functions including seeding, watering, lighting, harvesting, and re-seeding – all with the push of a button – to deliver nutritious livestock feed without the typical investment in fertilizer, chemicals, fuel, field equipment and transportation. The HydroGreen system not only provides superior nutritious feed to benefit the animal, but also enables significant environmental benefits to the farm.
For more information, please visit www.cubicfarms.com
Cautionary Statement on Forward-looking Information
Certain statements in this release constitute "forward-looking statements" or "forward-looking information" within the meaning of applicable securities laws, including, without limitation, statements with respect to CubicFarms’ expected revenue recognition, and the completion of the sale and installation of the system by the customer. Such statements involve known and unknown risks, uncertainties, and other factors which may cause the actual results, performance, or achievements of CubicFarm Systems Corp., or industry results, to be materially different from any future results, performance, or achievements expressed or implied by such forward-looking statements or information including the Company obtaining the approval of the Offering from the TSX Venture Exchange. Such statements can be identified by the use of words such as "may", "would", "could", "will", "intend", "expect", "believe", "plan", "anticipate", "estimate", "scheduled", "forecast", "predict", and other similar terminology, or state that certain actions, events, or results "may", "could", "would", "might", or "will" be taken, occur, or be achieved.
These statements reflect the Company's current expectations regarding future events, performance, and results and speak only as of the date of this news release. Consequently, there can be no assurances that such statements will prove to be accurate and actual results and future events could differ materially from those anticipated in such statements. Except as required by securities disclosure laws and regulations applicable to the Company, the Company undertakes no obligation to update these forward-looking statements if the Company's expectations regarding future events, performance, or results change.
VIDEO: We Use An Exceptional Amount of Land To Grow Food For Sows. Vertical Farms Could Change That If We Used Them To Grow Cow Feed
While most other vertical farms focus on growing salad greens for city dwellers, the new system is designed to tackle another challenge: the environmental footprint of growing feed for livestock
[Photo: Grōv Technologies]
Inside a new tent-like building on a large dairy farm west of Provo, Utah, tall towers stacked with trays of wheatgrass grow food for the cows outside. While most other vertical farms focus on growing salad greens for city dwellers, the new system is designed to tackle another challenge: the environmental footprint of growing feed for livestock.
A single tower in the growing system, from a startup called Grōv Technologies, takes up a little more than 850 square feet on the ground. But it can grow as much wheat or barley grass as 35 to 50 acres of farmland, the company says. Right now, an inordinate amount of land in the contiguous U.S.—around 780 million acres, or 41% of the total area—is used to grow feed for farm animals, either on pastures or through growing crops. And the demand continues to grow. “The availability of arable land, especially for animal feed, is shrinking,” says Steve Lindsley, president of Grōv Technologies.
[Photo: Grōv Technologies]
In some areas, that means forests are being cut or burned down to make room for crops to feed cows or chickens. “There’s clearly an environmental benefit that we think can be profound when you think about deforestation around the world,” Lindsley says. Grōv’s technology also significantly saves water, using around 5% of what is used in conventional farming. Additionally, it can reduce the distance to transport animal feed—China, for example, which has been buying agricultural land all over the world to grow food for its own animals, including in the U.S., is one of the startup’s key markets. The company plans to sell its systems to farms raising dairy and beef cattle to grow feed directly for their own animals.
[Photo: Grōv Technologies]
The farm in Utah, called Bateman’s Dairy Farm, is the first to test the new technology. Inside the new building, 10 towers, each around 25 feet tall, are filled with wheatgrass. Everything is automated: A robot plants four pounds of seeds in each tray and then sends it into the system, where sensors monitor conditions to give the crop the light and water it needs until it’s harvested automatically. “In an average of six and a half days, we have the crop,” Lindsley says.
Grōv provides support, but the system is designed to operate on its own, without any additional labor needed from the farmer. The system is also designed to minimize operating costs. The startup’s custom lights, for example, don’t put out heat, avoiding the large air-conditioning bills that are necessary in some other indoor farms. (The company says that the system can also run on renewable energy, and it plans to reach net-zero emissions by 2025.)
In early tests with hundreds of cows in 2019, the dairy found that the feed was more nutritious than its standard feed; the cows ate less, helping save money while producing the same amount of milk. Grōv estimates that farmers can break even on their investment in the technology in three years. As climate change progresses, growing indoors can also help mitigate risk from increasing droughts, heatwaves, floods, wind storms, and other extreme weather conditions.
The technology isn’t intended to fully replace conventional farming, but to provide one portion of the mix of food that cattle eat. At the farm in Utah, the new pilot system will provide 15% of the food for around 2,000 cows. But even replacing a fraction of conventional farming has the potential to make a meaningful difference. (That’s especially true if some farmland could be reforested, helping suck up excess carbon from the atmosphere to fight climate change.)
Lindsley argues that the environmental benefits could help dairy and beef farmers compete in a world where an increasing number of consumers are turning to plant-based foods. “The industry can utilize this technology as a counterpunch, really, to some of the lab-based protein efforts or the competitive efforts that are trying to pull people away from beef and/or dairy products,” he says.
ABOUT THE AUTHOR
Adele Peters is a staff writer at Fast Company who focuses on solutions to some of the world's largest problems, from climate change to homelessness. Previously, she worked with GOOD, BioLite, and the Sustainable Products and Solutions program at UC Berkeley, and contributed to the second edition of the bestselling book "Worldchanging: A User's Guide for the 21st Century."