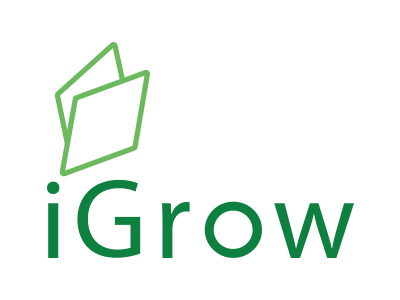
Welcome to iGrow News, Your Source for the World of Indoor Vertical Farming
SCOTLAND: Intelligent Growth Solutions (IGS) Vertical Farming Solutions
With vertical farming now starting to take off around the world, one Scottish company is rapidly becoming recognized as a world leader in providing the technology required to make vertical farms flourish
CLIMATE FOR CHANGE
IGS -produce grown in trays
With vertical farming now starting to take off around the world, one Scottish company is rapidly becoming recognized as a world leader in providing the technology required to make vertical farms flourish.
As David Farquhar, CEO at Intelligent Growth Solutions (IGS), explains, his company has patented several technologies that give IGS’s automated, human-free, vertical tower ‘farms’ a huge edge over the competition. There are at least three major challenges facing any company wanting to design ‘box’ systems for vertically farming plants, Farquhar explains.
“If you put plants into a sealed metal box you are putting a natural process into an unnatural housing, so you have to create the perfect weather and climate for them. This means solving three big problems,” he says.
David Farquhar, CEO at Intelligent Growth Solutions (IGS)
Most plants will tolerate 18 hours or so of sunlight a day, but as living, breathing organisms, they need a period of rest every 24 hours. Plus LED lighting, which replaces sunlight in these sealed structures, is very energy hungry. So the first challenge is how to devise and control the perfect lighting environment.
IGS solved this with several patented processes. “All the LED lights that you see around you have an inherent flicker,” Farquhar explains. This is because they use single-phase electricity. This is basically a sine wave and in the middle of each wave the current is off, so LEDs flicker 50 times a second,” he explains.
IGS’s process uses three-phase electricity and also clusters the LEDs into colours and wavelengths so that it can tune the lights to give the plants exactly, but only, what they need to optimise growth and minimise cost. “We have a worldwide patent on using all three phases of mains electricity at low voltage to power LEDs. This is a unique invention and gives us a huge advantage,” he comments.
Green light stresses plants, so the idea is not to simply deliver the equivalent of blanket sunlight throughout the growing life of the plant. By tuning the LEDs so the plants only get the wavelengths that really benefit them IGS maximises the growth potential and minimises climate impact.
“By being extremely precise and giving the plants only the parts of the spectrum they need, we can reduce the amount of power we need. So we only need 50 percent of the amount of energy that vertical farms generally require,” Farquhar says. That adds up to a very significant energy saving for the farmers.
The second big challenge comes from the fact that plants take in water, carbon and nutrients and as part of the transpiration process they ‘exhale’ warm, humid oxygen. That mix is deadly to other plants around them so the trick is to deliver the right amount of air at the right temperature and speed, while extracting the hot, humid oxygen, and then rebalancing everything in an environmentally efficient fashion.
IGS cools the oxygen and captures the condensed water vapour. Mixed with CO2 this cool air is then blown back into the tower at a temperature that offsets the unwanted heat generated by the LED lights. Because LEDs are not 100 percent efficient, only two-thirds of the energy they consume is released as light, the other third is released as heat. The sealed tower farms need to support multiple, precise microclimates so IGS’s algorithms and processes ensure that the tower farms stay at the perfect temperature for crops.
“That is our second really big invention, and that is all patented as well,” Farquhar says.
The third really big achievement in IGS’s approach is that its towers are completely automated. There are no humans in the loop. “The reason for eliminating humans from the loop is that humans can make mistakes. They can also accidentally bring pests, diseases and other contaminants into the tower environment and they add no value,” he says.
No humans mean no wages in the growth area (though some employment is needed outside), eliminating another massive cost to farmers. Bringing seed trays into the towers and removing trays of fully grown plants is done robotically.
“Our towers are powered by AI, using growth recipes, a full knowledge of the environment the plants require, the nutrients and water volumes required and so on. It knows what vegetables, root and fruit crops are on each tray, how old they are and when the tray is mature. Because of this, we do not need pesticides and we do not need to wash (and bruise) the finished crops. As a result, we virtually double the shelf life of the crops produced, which supermarkets love,” he comments.
IGS’s growth towers create zero emissions. “We have had SEPA visit our towers and they have confirmed this,” he notes.
Once the system has been installed for a vertical farm, the resulting produce is ready to be shipped as a first harvest to supermarkets in something between two and three weeks. So the system is generating cash in less than a month.
Click image to read the full report online
One tower system will create somewhere around 25 tonnes of food, depending on the crops being grown. Each tower is around nine metres tall with a 6x7m base. They are paired together which means that as a unit they will produce between 40 and 50 tonnes of food per annum.
There is a corridor between the pair for the robot to fetch and carry new and mature trays. The whole system is bio-secure with an airlock and positive air pressure inside to make it impossible for pests and diseases to contaminate the tower.
Farquhar says that IGS is already talking to property developers around Europe who are looking at erecting large multi-storey car park-like buildings to house multiple vertical towers. This will create some real scale to vertical farming and will help to give towns, cities and countries vastly improved food independence and nutritional security.
According to Farquhar, IGS’s towers are already producing several lines of seed and starter plants to populate other farms.
This in turn will go a long way towards making these local farmers independent of outside nurseries for new plantings.
Find out more at www.intelligentgrowthsolutions.com
This article appeared in The Herald COP26 report on the sustainable food sector in Scotland
Urban Crop Solutions Launches New "Modulex Plant Factory" on Sept. 9th, 2020
Launch Webinar hosted by Henry Gordon-Smith, CEO of Agritecture, on Sept 9th, 2020 (9 am EDT, 3 pm CEST, 9 pm SGT - 45 minutes)
Register And Get A Sneak Preview on The
New www.urbancropsolutions.com Website
Launch Webinar hosted by Henry Gordon-Smith, CEO of Agritecture,
on Sept 9th, 2020 (9 am EDT, 3 pm CEST, 9 pm SGT - 45 minutes)
Indoor Vertical Farming is a fast-emerging agriculture technology that provides compelling solutions to the United Nation’s Sustainable Development Goals: waste less food and support local farmers (Goal 2), avoid wasting water (Goal 6), and provide decent work (Goal 8).
However, few early adopters are making a profit.
Urban Crop Solutions has worked tirelessly to find a sensible solution to the open issues many investors and growers still face today. The initial Capex or investment cost is high and creates the need for a scalable solution. The unique freshness, taste, and shelf life of the crops go to niche markets with ever-changing needs, which requires a Plant Factory to be extremely adaptable. Also, high labor costs push Indoor Farms to implement more automation and become more efficient.
Based on the experiences and feedback of the customers on the 1st generation products, a new generation Plant Factory was designed from the ground up. The company believes it developed a concept that ‘simply makes sense’.
The ModuleX, the “Sensible Plant Factory” is Scalable, Adaptable, and Efficient.
The ModuleX can be configured between 2 to 64 Grow Modules, which means that the Plant Factory is scalable. One Grow Module contains 86 m² (925 sq.ft) of growing surface, yielding about 6.000 kg/year (13.228 lbs/year) of fresh vegetables. Each separate module features an independent climate and nutrient system, allowing the mix of crops to be adaptable to customers’ needs.
The base price is an industry-low Capex of 1.800 EUR per m² growing surface ex-works (199 USD/sq.ft). The labor costs are reduced by the automated crop-to-person ‘BenchCarousel’. For example, the ModuleX-8 has 8 Grow Modules for a total of 688 m² (7.403 sq.ft). The base price is 1.238.400 EUR (approx. 1.47 mm USD) for an output of 44 ton/year of romaine lettuce (97.000 lbs/year). For mid-sized solutions under 5500 m² growing surface, this is probably the most efficient solution on the market today.
To help people in the long and confusing journey into indoor vertical farming, the company also initiates an end-to-end support program, with a free feasibility calculator, technical support, biological consulting, and contract research. Urban Crop Solutions also developed a Corona-proof support system for training, set-up, startup, and first harvest support of any ModuleX Grow Module, which all can now happen remotely.
Tom Debusschere, CEO of Urban Crop Solutions: “We’ve been listening closely to the feedback of our customers and we found improvements just about everywhere. But the breakthrough invention is the automated BenchCarousel. This new crop-to-person carousel brings any bench of your choice to you within 90 seconds. It also allows us to fit a growing surface of 86m² (925sq.ft) within a 40ft insulated freight container, which we believe is an industry record.
What you really pay for is growing surface, labor, and electricity, and the ModuleX Plant Factory offers a step-change improvement in each. We invite you to take a look at our new website, with the investment cost in full transparency, so you can quickly see which solution is the best fit for you.”
Urban Crop Solutions is an agtech pioneer in the fast-emerging world of ‘Indoor Vertical Farming’. Throughout years of research, 220+ ‘plant growth recipes’ were developed for efficient indoor growing. All drivers for healthy plant growth, such as optimal LED spectrum and intensity, nutrient mix, irrigation strategy, and climate settings are tested and validated daily in the company’s own Indoor Biology Research Center.
To date, Urban Crop Solutions has manufactured container Farms and a Plant Factory for clients throughout Europe, North America, and Asia. Urban Crop Solutions’ commercial farms are being operated for vegetables, herbs, and micro-greens for food retail, foodservice, and industrial applications. Research institutions operate the growing infrastructure of Urban Crop Solutions for scientific research on banana seedlings, flowers, hemp, and many more.
Visit www.urbancropsolutions.com for a full virtual tour.
For more information: www.urbancropsolutions.com
Brecht Stubbe, Sales Director brst@urbancropsolutions.com
Maarten Vandecruys, CTO mava@urbancropsolutions.com
Tom Debusschere, CEO tode@urbancropsolutions.com
European headquarters: Regional headquarters:
Grote Heerweg 67 800 Brickell Avenue, 1100 Suite
8791 Beveren-Leie (Waregem) Miami (FL 33131)
Belgium Florida
(+32) 56 96 03 06 +1 (727) 601 7158
Facebook: www.facebook.com/urbancropsolutions
Twitter: www.twitter.com/U_C_Solutions
LinkedIn: www.linkedin.com/company/urbancropsolutions
YouTube channel: http://www.youtube.com/c/UrbanCropSolutions
Instagram: https://www.instagram.com/urbancropsolutions/?hl=en