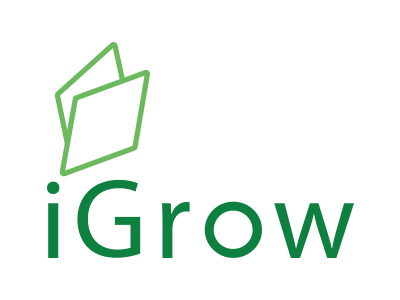
Welcome to iGrow News, Your Source for the World of Indoor Vertical Farming
SCOTLAND: Intelligent Growth Solutions (IGS) Vertical Farming Solutions
With vertical farming now starting to take off around the world, one Scottish company is rapidly becoming recognized as a world leader in providing the technology required to make vertical farms flourish
CLIMATE FOR CHANGE
IGS -produce grown in trays
With vertical farming now starting to take off around the world, one Scottish company is rapidly becoming recognized as a world leader in providing the technology required to make vertical farms flourish.
As David Farquhar, CEO at Intelligent Growth Solutions (IGS), explains, his company has patented several technologies that give IGS’s automated, human-free, vertical tower ‘farms’ a huge edge over the competition. There are at least three major challenges facing any company wanting to design ‘box’ systems for vertically farming plants, Farquhar explains.
“If you put plants into a sealed metal box you are putting a natural process into an unnatural housing, so you have to create the perfect weather and climate for them. This means solving three big problems,” he says.
David Farquhar, CEO at Intelligent Growth Solutions (IGS)
Most plants will tolerate 18 hours or so of sunlight a day, but as living, breathing organisms, they need a period of rest every 24 hours. Plus LED lighting, which replaces sunlight in these sealed structures, is very energy hungry. So the first challenge is how to devise and control the perfect lighting environment.
IGS solved this with several patented processes. “All the LED lights that you see around you have an inherent flicker,” Farquhar explains. This is because they use single-phase electricity. This is basically a sine wave and in the middle of each wave the current is off, so LEDs flicker 50 times a second,” he explains.
IGS’s process uses three-phase electricity and also clusters the LEDs into colours and wavelengths so that it can tune the lights to give the plants exactly, but only, what they need to optimise growth and minimise cost. “We have a worldwide patent on using all three phases of mains electricity at low voltage to power LEDs. This is a unique invention and gives us a huge advantage,” he comments.
Green light stresses plants, so the idea is not to simply deliver the equivalent of blanket sunlight throughout the growing life of the plant. By tuning the LEDs so the plants only get the wavelengths that really benefit them IGS maximises the growth potential and minimises climate impact.
“By being extremely precise and giving the plants only the parts of the spectrum they need, we can reduce the amount of power we need. So we only need 50 percent of the amount of energy that vertical farms generally require,” Farquhar says. That adds up to a very significant energy saving for the farmers.
The second big challenge comes from the fact that plants take in water, carbon and nutrients and as part of the transpiration process they ‘exhale’ warm, humid oxygen. That mix is deadly to other plants around them so the trick is to deliver the right amount of air at the right temperature and speed, while extracting the hot, humid oxygen, and then rebalancing everything in an environmentally efficient fashion.
IGS cools the oxygen and captures the condensed water vapour. Mixed with CO2 this cool air is then blown back into the tower at a temperature that offsets the unwanted heat generated by the LED lights. Because LEDs are not 100 percent efficient, only two-thirds of the energy they consume is released as light, the other third is released as heat. The sealed tower farms need to support multiple, precise microclimates so IGS’s algorithms and processes ensure that the tower farms stay at the perfect temperature for crops.
“That is our second really big invention, and that is all patented as well,” Farquhar says.
The third really big achievement in IGS’s approach is that its towers are completely automated. There are no humans in the loop. “The reason for eliminating humans from the loop is that humans can make mistakes. They can also accidentally bring pests, diseases and other contaminants into the tower environment and they add no value,” he says.
No humans mean no wages in the growth area (though some employment is needed outside), eliminating another massive cost to farmers. Bringing seed trays into the towers and removing trays of fully grown plants is done robotically.
“Our towers are powered by AI, using growth recipes, a full knowledge of the environment the plants require, the nutrients and water volumes required and so on. It knows what vegetables, root and fruit crops are on each tray, how old they are and when the tray is mature. Because of this, we do not need pesticides and we do not need to wash (and bruise) the finished crops. As a result, we virtually double the shelf life of the crops produced, which supermarkets love,” he comments.
IGS’s growth towers create zero emissions. “We have had SEPA visit our towers and they have confirmed this,” he notes.
Once the system has been installed for a vertical farm, the resulting produce is ready to be shipped as a first harvest to supermarkets in something between two and three weeks. So the system is generating cash in less than a month.
Click image to read the full report online
One tower system will create somewhere around 25 tonnes of food, depending on the crops being grown. Each tower is around nine metres tall with a 6x7m base. They are paired together which means that as a unit they will produce between 40 and 50 tonnes of food per annum.
There is a corridor between the pair for the robot to fetch and carry new and mature trays. The whole system is bio-secure with an airlock and positive air pressure inside to make it impossible for pests and diseases to contaminate the tower.
Farquhar says that IGS is already talking to property developers around Europe who are looking at erecting large multi-storey car park-like buildings to house multiple vertical towers. This will create some real scale to vertical farming and will help to give towns, cities and countries vastly improved food independence and nutritional security.
According to Farquhar, IGS’s towers are already producing several lines of seed and starter plants to populate other farms.
This in turn will go a long way towards making these local farmers independent of outside nurseries for new plantings.
Find out more at www.intelligentgrowthsolutions.com
This article appeared in The Herald COP26 report on the sustainable food sector in Scotland
Three Way To Maximize A Vertical Farm's Potential
Population growth and urbanization are forcing global food production to a crossroads
17 March 2021
By Abhay Thosar, Ph.D., director of horticulture services for Fluence by OSRAM
Previously published in the February 2021 issue of Inside Grower.
Population growth and urbanization are forcing global food production to a crossroads. Overall, migration to high-density areas increases access to health care, higher-paying jobs, education, and other socio-economic opportunities. But it also places more strain on existing infrastructure and demand for resources, leading to greater water scarcity, energy consumption, waste, and, perhaps most importantly, threats to the food supply, prices, and quality.
The economically disadvantaged will be the first to pay the price of increased urbanization. As prices increase and access to quality food sources decreases, the nutritional health of poor populations will decline. Over the next several years, the responsibility of bridging the gap between projected food supply and demand in urban areas will largely fall on vertical farms, an industry that is expected to nearly quadruple by 2025 to about $16 billion. The COVID-19 pandemic could accelerate that growth rate even further.
The vertical farming industry still has challenges to overcome. Production costs remain relatively high and, as a young market, knowledge gaps in operational best practices in critical areas like facility design and environmental conditions threaten long-term sustainability and profitability. The evolving economic dynamic with supermarkets is forcing vertical farms to scale quickly as they attempt to grow and supply a wider variety of crops while maintaining the buyer’s standards around produce size, quality, and nutritional value.
And, as we look to the future, new innovations in lighting strategies, facility design, cultivation best practices, and automation mean that vertical farming operations have to be constantly adapting and seeking new operational advantages. This is just as true for new market entrants and relatively established players alike, and each will be critical to not only maintaining profitability, but ensuring that food production in urban areas can increase with demand.
With that in mind, here are three critical factors vertical farmers need to consider to meet market expectations, improve efficiency and ultimately grow, cultivate and distribute larger quantities of quality food to more people in a smaller area.
Facility design as a function of market demand
The history and growth of the vertical farming market are largely driven by two trends at the consumer and buyer levels. A decade ago, consumers asking questions about how, where, and when their food was grown was practically unheard of. Things are different today. People want to know the provenance behind the food they buy and ensure it is chemical-free and safe to eat. Every product has become more than a label, it’s become a story that consumers want to hear, and one that has an equally significant impact in where they shop and what they buy.
Supermarkets have taken notice. Beyond that, though, vertical farming operations have given supermarkets one more option in addition to the existing supply chains on which they’ve relied for food production and distribution. Vertical farms play an even more important role during large-scale disruption events like the COVID-19 pandemic or massive recalls. As a result, supermarkets—which value the consistent supply of produce above all—are turning to their local vertical farming operations and, in some cases, even investing in them directly. The increased attention, however, comes at a cost (literally and metaphorically). Supermarkets are demanding that the vertical farms supplying them grow a wider variety of crops—lettuce, tomatoes, cucumbers, leafy greens, microgreens, herbs—more consistently while also meeting unique specifications around weight, aesthetic, nutritional value and a variety of other factors that are ultimately dictated by the vertical farm’s environment and the grower’s expertise.
Vertical farmers are quickly realizing they need to expand their portfolio from potentially a handful of crops to a few dozen or more, raising a range of questions on how to design or retrofit their facilities and adjust environmental conditions that favor any given crop.
The first decision many vertical farmers face is the growing technique that will be most scalable and viable for their operation. Hydroponics, aeroponics and aquaponics have all emerged as viable options with varying degrees of success, but they’re far from interchangeable.
In the end, there is no universal solution for every vertical farm. Cultivators should closely consider their buyers’ expectations, and how those expectations might change over time. Then, cultivators must assess the full range of their crops’ needs and how each might respond differently to various environmental factors and lighting strategies.
Strike a balance between environmental factors
The next set of factors governing facility design, investment and day-to-day operations should always be the environmental conditions themselves.
How air flows into and across each rack of a vertical farm is one of the most unique and important challenges vertical farms have to solve. Ignoring or failing to closely monitor airflow is often a death blow to entire sections of crops and to profitability, yield, and consistency as a result. Air movement helps to maintain temperature, humidity, and transpiration at each rack, and lack of it creates wide temperature swings or large gaps between crops at the bottom and crops at the top. It’s an incredibly fragile balance to strike. Everything from the number of access points into a warehouse—there should only be one access point—to HVAC and circulation systems affect air movement.
As a best practice, the maximum difference between the temperature at the top-most rack and the bottom-most rack should be no more than two degrees Fahrenheit. In practical scenarios, cultivators facing large temperature fluctuations can also consider placing crops that prefer relatively warmer temperatures—such as basil, oregano, chives, sage or thyme—at the top and simply let the laws of thermodynamics do the rest.
Carbon dioxide enrichment is a slightly easier condition to manage but no less important and changes based on temperature and lighting strategy. CO2 enrichment, too, can fluctuate based on the number of access points into a warehouse (again, there should only be one). Enriching a cultivation environment with carbon dioxide stimulates photosynthesis and plant growth, the rate of which is critically dependent on the difference between CO2 concentrations in the air and in the leaf cells.
The law of diminishing returns puts a cap on the amount of carbon dioxide cultivators should be introducing. CO2 is by no means the only factor governing plant growth, but vertical farms have the advantage of being able to closely monitor and control CO2 levels. To do so properly, however, they shouldn’t shy away from significant investments in both handheld devices—which allow cultivators to measure carbon dioxide levels at each rack, each plant, and each leaf—but also large-scale control systems that can measure and track CO2 throughout the entire warehouse.
Humidity levels govern a plant’s transpiration rate and the aperture sizes of its stomata, ultimately affecting how much water it moves from its root zone to release back into the warehouse. When a plant’s stomata open, they release water while also collecting carbon dioxide, making the balance of humidity, temperature, and carbon dioxide all the more crucial. Different plant types in different growth stages have different transpiration rates, adding even more complexity to how a vertical farm is designed and managed. The most common way to express humidity is relative humidity, the percentage of water vapor in the air at a given temperature compared to the total amount of water the air can hold at that temperature. In vertical farming, however, vapor pressure deficit (VPD) is the more accurate way to gauge humidity’s effect on plant growth. VPD remains an interesting discussion among researchers as the industry seeks to understand the differences between VPDs for air and leaves as well as exact VPD calculations.
Every environmental factor in a vertical farm affects the others to some degree. Nearly everything can be controlled; it’s both the advantage and the challenge native to the market. No factor, however, is more important to photosynthesis than its primary driver: light. Each factor—CO2, temperature, airflow, humidity, fertilizer, irrigation, VPD—need to be fine-tuned with changes to light quantity and quality to optimize plant performance and response.
Designing an effective lighting strategy
The design and implementation of an effective lighting strategy is and always will be the primary driver of your vertical farm’s success. In environments as complex as vertical farms, identifying the correct light intensity, spectra, photoperiod, and configuration will determine how other environmental factors work together to optimize a facility for plant yield and quality.
The first of these, the fixtures themselves, carry more implications for vertical farms than other cultivation spaces; in a vertical farm, plants receive no other source of light. The sun isn’t the safety blanket that it is for greenhouses. This simple and obvious fact means that vertical farmers have to find efficiencies in ways others don’t, which can manifest across a variety of operational metrics. Light efficacy, for instance, becomes more important. Most vertical farms are located in urban areas and are likely paying a premium for electricity. Maximizing micromoles per watt and reducing energy waste becomes more than a sustainability initiative, it’s critical to overall profitability.
Similarly, vertical farms operating warehouses measuring in the tens of thousands of square feet need fixtures with a good form factor without sacrificing light intensity. The right configuration means vertical farms can squeeze more racks into their facilities while also putting the lights closer to the plants for better results.
Beyond the hardware specifications, lighting design and strategy consist of several key factors: light intensity, light quality (or spectra), and light bar configuration. Each should be rooted in a facility’s overarching goals—typically defined by the consumer or buyer. Lighting strategies can be customized by crop, yielding specific plant chemistries or changes in biomass. Differences in spectra and light intensity can affect a crop’s coloration, shelf life, taste, and smell. Desired crop characteristics should be determined upfront in conjunction with the prospective buyer, therefore guiding a lighting designer to identify the optimal strategy to accomplish a facility’s goals.
Light quantity is the first and foremost aspect when it comes to optimizing the productivity of the crop. It is important to target the correct mols/day for each crop. Light quality (or spectra) is defined by measuring light’s wavelength in nanometers (nm). Wavelengths of light that drive photosynthesis are primarily found within 400 to 700nm—a range identified as photosynthetically active radiation (PAR). In a vertical farming environment, broad, white light has proven effective for tissue culture, propagation, and vegetative growth—while also serving the more practical function of making it easier for human eyes to diagnose and observe crops day in and day out. As the body of research into LED applications has expanded, it’s become clear that lighting strategies need to shift based on the growth stage. The days of bombarding plants with the same intensity and spectra are quickly fading. More and more research is showing that different cultivars respond to different lighting strategies at different stages of their maturation. More nuanced, customized lighting strategies are increasingly leading to tangible business outcomes for cultivators: longer shelf life, improved aesthetic, enhanced nutritional value, faster cycle times, and higher yields.
LED improvements will continue to drive costs down, while more in-depth research will discover and confirm a new set of lighting strategies and operational best practices to help vertical farmers meet future market demand for increased food production while also improving profitability. Overall, the future for vertical farms is bright and ripe for even broader innovation. Automation—the final frontier of food production—will mean even greater control of agricultural environments. That future is on the horizon. For now, though, vertical farms just need to stick to what they can control, which is pretty much everything else.
About Abhay
Abhay Thosar is the director of horticulture services at Fluence by OSRAM, where he is responsible for managing a team of horticulture specialists that enhances how cultivators grow their crops, optimize their lighting strategies and increase profitability in their operations. He holds a Ph.D. in plant physiology from Gujarat Agricultural University and spent more than a decade at leading greenhouses and nurseries throughout the U.S.
Have A Look Inside Large Plant Factory on JPFA Training Course
Plant factories, or vertical farms, are grabbing the headlines lately. Learn about them on our science-based practical online course--anytime at your convenience and anywhere in the world during the course period
Have you ever visited a plant factory with artificial lighting (PFAL)? The Japan Plant Factory Association is now receiving applications for its 2021 Online Training Course on PFALs scheduled for Feb. 18-March 11. The course gives you the privilege of taking an exclusive look inside a large-scale, commercial PFAL in central Japan.
Plant factories, or vertical farms, are grabbing the headlines lately. Learn about them on our science-based practical online course--anytime at your convenience and anywhere in the world during the course period.
Besides introductory classes on the basics of PFALs, the course has the just mentioned PFAL virtual tour and the following other special content:
A lecture on phenomics and the potential of phenotyping
Hands-on technical training on PFAL business management
Tailored, further explanations on previous-course lectures,
Operational and hygiene management, future of PFALs in COVID-19 times (2020 Workshop)
Its introductory classes cover not only PFAL principles and the basics like photosynthesis, respiration, transpiration, light environment and plant growth, nutrient solution and hydroponic cultivation, but also forthcoming technologies and PFAL business management.
The JPFA oversees a plant factory hub on the Chiba University Kashiwanoha campus in Kashiwa, northeast of Tokyo. The nonprofit organization has shifted from on-site to online training due to the coronavirus pandemic.
The first-rate lecturers of the coming course include Toyoki Kozai, professor emeritus and former president of Chiba University, who is known as the father of plant factories, and Chieri Kubota, professor at the Ohio State University.
Along with lectures, the training course, run on a specified platform, encourages participants to interact each other and gives them a chance to join an online live question-and-answer session.
The course is available for anybody interested in PFALs--not only JPFA members but nonmembers as well. If you are curious, check here and apply now.
Apply Now
For more information
Japan Plant Factory Association
https://npoplantfactory.org/en/
https://npoplantfactory.org/information/news/2120/
https://npoplantfactory.org/wp-content/uploads/2020/12/Renewed-Information-for-JPFA-2021-Online-Training-Course-on-Plant-Factories-with-Artificial-Lighting-PFALs-2021.1.20.pdf
Japan Plant Factory Association
The Japan Plant Factory Association, a nonprofit organization founded in 2010, is devoted to advancing the plant factory industry and controlled-environment agriculture in and outside Japan through academia-industry collaborations.
Its mission is to develop and disseminate sustainable plant factory systems in a bid to address issues concerning food, the environment, energy and natural resources.
The JPFA oversees plant factories on the Chiba University Kashiwanoha campus in Kashiwa, northeast of Tokyo. Also, it works on about 20 R&D projects and runs workshops and training courses.
How to Become a JPFA Member
Apply for JPFA membership here. For more information, visit the JPFA website or email us at training@npoplantfactory.org. We welcome your inquiries.
Price List for JPFA 2021 Online Training Course on PFALs
Want more online educational options?
Elevated Vertical Farming: Vaisala Sensors And The Story of Fifth Season
“When you don’t have to worry about outdoor conditions, you have the benefit of going vertical. We can grow plants year-round in urban areas close to the dense part of a city,” said Fifth Season Cofounder and CTO/COO Brac Webb
Vertical farming is looking up – quite literally. No sun, no soil, no vast expanse of land? No problem. At least not for indoor vertical farming company Fifth Season.
“When you don’t have to worry about outdoor conditions, you have the benefit of going vertical. We can grow plants year-round in urban areas close to the dense part of a city,” said Fifth Season Co-founder and CTO/COO Brac Webb
Every minute, we’re collecting Vaisala sensor data to measure and maintain the conditions most important for plant growth and using that information to build something special.
-Brac Webb, Fifth SeasonUsing a sophisticated mix of artificial intelligence (AI), sensors, data modeling and robotics, Fifth Season’s technology tends to each plant’s individual needs at high levels of efficiency and precision. But sensors and their data play the most pivotal role. “The plants are telling us exactly what they want. We just have to adjust to that,’ said Webb. “Every minute, we’re collecting Vaisala sensor data to measure and maintain the conditions most important for plant growth and using that information to build something special.”
Background
The story of Fifth Season is very much the story of the American Dream.
The startup began with three friends and entrepreneurs: cofounders Brac Webb, Austin Webb, and Austin Lawrence. Originally founded in 2016 as RoBotany Ltd., the company was incubated at Carnegie Mellon University’s (CMU) Swartz Center for Entrepreneurship.
“We really started as a tech company and looked at the vertical farming problem at first and wondered what we can do to help solve some tech problems there,” Webb said. “Much of our evolution is due to the advances of HVAC sensors and LED lights. We already had the programming. So, we said, heck, let’s just do the whole thing.”
Fifth Season is now a 60,000-square-foot, solar-powered vertical farm in the Pittsburgh borough of Braddock, PA. The company’s 25,000 square-foot grow room is equipped with 40 different robots and has 12 levels with more than 125,000 square feet of production capacity. Compared to conventional produce, which can travel thousands of miles by truck or plane, fresh produce grown in local vertical farms need only travel a few miles to reach consumers. The company produces an assortment of leafy greens, arugula, and spinach as well as ready-to-eat salads that are sold to a local clientele including Giant Eagle and numerous other retailers. They have also launched a Direct-To-Consumer model on their website.
The company uses its small army of 40 robots to streamline almost every aspect of the vertical growing operation, including storage, retrieval, harvesting, integrated pest, and disease management, scouting, seeding, media packaging, and more, according to Webb. Humans are minimally involved in the process, mostly to coordinate the robotic army to execute specific growing recipes or other tasks – which also cuts labor costs from 40% in traditional farms to just 20%.
“We have cutting-edge technology - not using traditional methods, using more of a robotics approach - and a ton of data collection with Vaisala sensors, not only for closed-loop control but also for alerting us to changes in plant growth or the environment,” Webb said.
Industry Overview
Total control of the growing environment – 24/7/365 – in small spaces governed by known and emerging technologies are farming’s oft-cited competitive advantages over other types of farming. Vertical farming also is known for efficient resource management. For example, with its hydroponics approach, growing plants in a solution of water and nutrients, Fifth Season uses 97% less land and up to 95% less water than traditional farming.
Vertical farming attempts to take the uncertainties of agriculture – pests, sunlight, soil, etc. – and makes them controllable through various combinations of AI, artificial light, sensor monitoring, climate control systems, etc. Crops are stacked in layers or rows sometimes 20 to 30 feet high. LED lights are used by all vertical farms to create a specific light recipe for each plant, giving the greens the exact spectrum, intensity, and frequency needed for photosynthesis. LEDs offer several benefits, such as: exceptional color range, longevity, low radiated heat, and energy-efficiency. They can also be recycled and don’t contain any toxic compounds or elements like mercury. Different types of crops prefer different types of lighting. For example, leafy greens and vegetative crops prefer light towards the blue side of the spectrum; whereas fruiting and flowering crops may need something more along the red spectrum.
Vaisala Sensors
The peace of mind factor is huge. You get that from Vaisala.... I never once questioned the reading that I’m getting, or that it will be just as consistent tomorrow.
-Brac Webb, Fifth Season
So, why Vaisala? “The peace of mind factor is huge. You get that from Vaisala. If we have issues with our growing environments, all our plants can die. I mean, it could kill our business,” Webb said. “I never once questioned the reading that I’m getting, or that it will be just as consistent tomorrow. But, more than that, it was also the support we received to quickly integrate your technology into our engineering and get everything up and running fast,” Webb added. In fact, tightly controlling and monitoring light, humidity, CO2, and the temperature is critically important to Fifth Season. So, data, data, data….
“We have, gosh, probably 360 of Vaisala’s HMP110 humidity and temperature probes and 36 GMP252 CO2 probes distributed throughout the entire growing environment. It’s not just about gathering data in real-time. With post-analysis of big data, we can review the growth history of those plants and learn something about them. We may learn, for example, what we thought was the best growing environment for those plants to achieve optimal conditions for taste, quality, and yield isn’t the best after all,” Webb said. “And we can course-correct.”
Future
As the world’s population expands, projected to reach 9 billion by 2050, so too does the amount of fruits and vegetables needed to sustain it. There is only so much farmland to accommodate the increase in fresh food required for life. The U.S. Department of Agriculture, investors, and entrepreneurs alike are acknowledging vertical farming as having the potential to strengthen the global food system. And startups like Fifth Season, backed by significant venture capital, are paving the way to deliver new solutions that efficiently deliver fresh and healthy food to people.
“The more we learn, the more we can improve vertical farming,” Webb said, jokingly adding: “If only we can get to the point that the computer could taste the plant.”
The story of Fifth Season is just beginning.
“We’d like to replicate these hyper-local farms. So, it isn’t just about solving the problems of having fresh produce available in Pittsburgh and making sure we can run it here. This farm is a product that we want to be able to deploy in multiple locations all over the United States, all over the world at some point, you know. That’s our grand vision.”
For Fifth Season and Webb, there’s also an underlying humanitarian goal of vertical farming that transcends business.
“As a person and an engineer, I always like reading about how (US President) Thomas Jefferson thought agriculture and engineering are intertwined: that agriculture is humanity’s first and foremost engineering problem to solve. You’re helping create jobs in that local area and we have seen how important that is to the economy. Thanks to the technology from Vaisala, you can create an environment that is perfect for the plants and help people too.”
For more information, please Contact Us.
Download the complete Customer Story below.
Elevated vertical farming: Vaisala sensors and the story of Fifth Season
Certhon's First Results of Indoor Strawberries Trial
Martin Veenstra, Indoor Farming specialist at Certhon: “This way of growing strawberries is unique because all grow parameters can be precisely controlled during the entire growth cycle
Martin Veenstra, Indoor Farming specialist at Certhon: “This way of growing strawberries is unique because all grow parameters can be precisely controlled during the entire growth cycle. From start to finish. This ensures optimum quality, yield, and fruit sizes, independent of the growing season. All grown without any pesticides and with a choice of both traditional as well as organic nutrients.”
The Certhon Innovation Centre consists of multiple indoor farms equipped with state of the art systems for LED lighting, climate control, CO2 dosing and irrigation systems which are all managed by Certhon's farm control system. In these farms, many crop trials are conducted for the indoor growing of a wide variety of plants, ranging from leafy greens to many vegetables and soft fruit. We would like to share exciting results of our trials with growing strawberries in our indoor farming system.
Results
Yields vary off course per strawberry variety, but at least a minimum of 26 up to 30 kg per m² per year with a consistent BRIX of 8 or higher is now available to every grower. Also, fruit sizes are much more consistent compared to open field or even greenhouse growing.
"At Certhon, we focus on the consistent and uniform top quality of the produce with an improved shelf life. In addition to optimizing the yield, we also put a strong emphasis on minimizing the power consumption for lighting and climate control. Also reducing water consumption is a strong focus point."
Martin: “We are continuously improving our trials and see even more potential in the very near future. Besides strawberries, we are also testing with tomatoes, lettuce, and raspberries.”
For more information:
Certhon
ABC Westland 555
P.O. Box 90
2685 ZH Poeldijk
The Netherlands
Tel: +31 174 22 50 80
Fax: +31 174 22 50 81
www.certhon.com
5 Jan 2021
Challenges With Airflow Strategies In Vertical Applications
As the industry continues to search for ways to maximize efficiencies, the utilization of LED lighting is becoming increasingly common. Aside from energy efficiency gains, one of the many benefits of migrating to LED’s is the ability to also maximize space utilization
As the industry continues to search for ways to maximize efficiencies, the utilization of LED lighting is becoming increasingly common. Aside from energy efficiency gains, one of the many benefits of migrating to LED’s is the ability to also maximize space utilization.
With less radiant heat and more consistent PPFD, cultivators are able to move lighting much closer to the plant canopy (in some cases less than 6”), which makes vertical, or multi-tier, cultivation far more feasible than with HID lighting.
The obvious benefit to tiered applications is the ability to increase canopy square footage without additional building square footage. Although there are some drawbacks to multi-tier growing, there can also be great reward, and so we’re seeing more and more of our clients choose to go this route in their facilities.
From an HVAC perspective
The challenge with multi-tier cultivation is twofold: first, we must ensure homogeneity to the entire canopy at multiple heights (that all plants at all levels are seeing the same conditions), and second, we must ensure that the HVAC system is getting adequate access to the hot, humid canopy air to ensure that it operates at full capacity.
When standalone dehumidifiers are in use (as opposed to integrated dehumidification systems), it’s doubly important. Dehumidifiers are typically ceiling-mounted and getting the humidity from the lower tier all the way to the ceiling is both difficult and absolutely vital to the proper operation of the dehumidification system. These requirements can be challenging even in single tier applications, so when the complication of airflow obstructions associated with multiple tiers of canopy are added into the mix, the need for specialized expertise becomes even more evident.
Unfortunately, it can be exceptionally difficult for cultivators to find and incorporate a well-designed airflow system for their racking design. While something is certainly better than nothing, one-size-fits-all strategies without the proper engineering can be difficult to dial in, often resulting in improper air speed over the canopy, uneven temperatures, higher than necessary cost or higher than necessary energy use in both HVAC and the air distribution system itself.
The variables must be considered
Various lengths of ductwork, various canopy heights, and various distances from the lighting source will all result in variances in airflow requirements. The speed of the airflow, the diffusion of the airflow, and the temperature of the air will all impact VPD and plant transpiration. As even LED lights vary in wattage and sensible heat output, so should the amount of air being displaced over the canopy to ensure that temperature goals are met.
While certain components of racking airflow systems can be utilized in multiple applications, some care must be taken in each application to ensure that the components being applied are appropriate—from duct diameter to static pressure and fan selection to diffusion strategies. And this is only contemplating what is required to deliver cooler, dryer air to the canopy. Delivering the hot, humid air to the air conditioning and dehumidification system must also be considered. Luckily, these are all challenges that can be addressed with the right experience and engineering expertise, and it doesn’t have to cost an arm and a leg.
The racking airflow design should be an integral part of the HVAC design
We are very happy to help any cultivator retrofit their existing racking systems with a well-designed airflow system, regardless of the HVAC system in use. With the proper engineering behind them, these retrofits can solve homogeneity and airflow challenges quite nicely and at a reasonable cost.
By the same token, what we find is that the most cost-effective and energy efficient multi-tier airflow strategies are those incorporated from the get-go as part of the HVAC design. Looking at it objectively, of course these systems should be incorporated at the HVAC design level when possible. Incorporating airflow over the canopy is a natural extension of the HVAC system. However, historically the industry has seen it as a separate challenge, or as a component of the racking systems themselves, and has largely considered only canopy air movement without considering how to ensure the HVAC system impacts the design.
Consistent airflow is achievable if designed right
The fact of the matter is, integrating the airflow systems with the racking systems is the easiest part. The hard part is making sure the airflow systems themselves are correctly designed to achieve their actual purpose: helping provide a cultivation environment that is consistently perfect.
When the multi-tiered airflow strategies within a room are considered as part of the HVAC design, all of the various airflow systems in the room are working in harmony instead of competing and interfering with each other, ensuring that everything operates as it was intended. This approach also minimizes the amount of equipment being utilized to achieve air distribution goals, which minimizes capital costs, overall connected electrical load, and energy use. It can even boost the energy efficiency of the HVAC system itself, by ensuring that air handlers have greater access to the hot, humid air at the canopy.
In any multi-tier application, a well-engineered racking airflow system design is an absolute requirement. However, we must stop thinking of these systems as components of racking, or as a design afterthought, and start thinking of them as an important part of the overall HVAC strategy.
Whether designing the system at the beginning of the room HVAC design or incorporating it after the fact, engineering and expertise that implements the racking airflow system as a vital component of the overall HVAC strategy will always yield the best results.
For more information:
Surna
Tel. +1 303 993 5271
www.surna.com
Valoya Launches Two New Greenhouse LED Grow Lights
Valoya, the research-driven manufacturer of horticultural LED grow lights has expanded its RX-Series line of greenhouse LEDs with two new models – RX500 and RX600
Valoya, the research-driven manufacturer of horticultural LED grow lights has expanded its RX-Series line of greenhouse LEDs with two new models – RX500 and RX600. The new models are higher power, higher efficiency versions of the existing RX400 model, and can be used as true 1-to-1 HPS replacements. RX500 and RX600 produce up to the staggering 1700 µmol/s of uniform light output. They have been designed to be robust and compact, producing minimal shading over the canopy. With an Ingress Protection rating of IP65 (wet location) these luminaires are completely dust tight and can withstand spraying with water jets from any direction. The high light intensity they produce enables them to be positioned high above the canopy, as much as 4 meters above it.
Valoya’s LED technology is proprietary and great efforts have been taken to create LED luminaires that last long and sustain the same light spectrum over their entire lifetime. RX500 and RX600 typically last 50000 hours whereby the intensity drops to 90% after about the 36000-hour mark. The spectrum decays evenly ensuring the grower will be getting the same plant performance and will not have to change the growth protocol over time.
In transitioning from HPS to LED, growers have to develop new growth protocols quickly. This is where Valoya’s team of biologists will provide support and expertise based on over 600 plant trials conducted in over 10 years. This means growers will hit the ground running after their LED upgrade and will see improvements in their plant performance right after it.
The new models are available with most of Valoya’s patented spectra such as SolrayÒ (sunlight replica) and AP673L (vegetative growth). All of Valoya’s spectra can be used as sole source lighting in no sunlight environments as well as together with sunlight. They have been tested on over 300 plant species/varieties and we will gladly share this data with growers to help them get the most out of their plants.
RX500 and RX600 are heavy-duty, greenhouse luminaires designed to produce high and uniform light output over a long period of time. Combined with Valoya’s patented spectra and the support of a team of photobiologists, RX-Series is the way to upgrade to LEDs in your greenhouse.
Contact Valoya today to get your free light plan - sales@valoya.com
To learn more about the RX-Series, please download the brochure.
About Valoya
Valoya is a provider of high end, energy-efficient LED grow lights for use in crop science, vertical farming, and medicinal plants cultivation. Valoya LED grow lights have been developed using Valoya's proprietary LED technology and extensive plant photobiology research. Valoya's customer base includes numerous vertical farms, greenhouses, and research institutions all over the world (including 8 out of 10 world’s largest agricultural companies).
Additional information:
Valoya Ltd, Finland
Tel: +358 10 2350300
Email: sales@valoya.com
Web: www.valoya.com
Facebook: https://www.facebook.com/valoyafi/
Twitter: https://twitter.com/valoya
VeggiTech Builds and Operates Digital Smart Farms For Customers
In conversation with Hemant Julka, Chief Operating Officer, VeggiTech
By GN Focus | May 28, 2020 | Gulf News
In conversation with Hemant Julka, Chief Operating Officer, VeggiTech
Could you tell us about VeggiTech and its operations in the UAE?
VeggiTech is an agro-tech organisation focused on disrupting the agriculture industry to create sustainable and eco-friendly farms. We focus on LED-assisted hydroponics for indoor vertical farms and protected hydroponics to farm sustainably even in the UAE’s challenging conditions, where soil, temperature and water are not conducive to traditional farming. Our farming landscape has grown to over 60 acres of protected hydroponic farms and more than 45,000 sq ft of indoor vertical farms, with a team of over 150 qualified agronomists, engineers and farmers.
How could you help traditional farms in the country incorporate hydroponic farming practices?
VeggiTech’s business model is to build and operate digital smart farms for our customers. We drive the transformation of farms with these innovative technologies in a cost-effective manner. The year 2019 saw more than 35 acres of traditional farms converted into protected hydroponics and the introduction of 45,000 sq ft of indoor vertical farms in Sharjah alone.
Given our expertise, we ensure the latest innovation in farming technology is delivered with optimal return on investment for our customers.
Could you talk about a couple of key projects that you have handled recently?
Some of our recent successes were the conversion of a traditional farms (640,000 sq ft) into modern protected hydroponic farms and the commissioning of the indoor vertical farm of 25,000 sq ft grow area. Our protected hydroponics technologies provide a harvest of 40-45kg per sq m per annum, while our indoor vertical farms provide a harvest of 85-90kg per sq m per annum using less than 5 percent of the water used in traditional farming.
What initiatives have you taken to create more awareness on hydroponics and other innovative farming technologies for a sustainable agricultural ecosystem in the UAE?
Education is key for long term sustainable impact. We work closely with the Ministry of Climate Change and Environment (MOCCAE). Our Chief Agronomy Officer, Bhaskar Rao, leads our Learning Hub platform that hosts the Urban Grower’s programme for students, parents and teachers. We have had more than 50 graduate participants from the programme.
VIDEO: VeggiTech - Vegetation Technology Redefined
VeggiTech is an Agro technology start up with the sole aim of disrupting the agriculture industry
VeggiTech is an Agro technology start up with the sole aim of disrupting the agriculture industry. VeggiTech obsesses on addressing the key challenges of traditional farming – soil, temperature and water through its design of protected Hydroponics and Grow Lights assisted Hydroponics.
VeggiTech stands for Vegetation technology redefined and has currently chosen the harsh conditions of UAE to demonstrate these technologies in farms that are open for Investors, Students and Consumers to experience. The Leadership team firmly believes in moving beyond presentations and demonstrating technology that provides the Return on Investment in a live functional environment.
Lead Image Credit: Supplied
UAE Farm Tech To The Fore
New technologies are helping the country make more of its own produce
New technologies are helping the country make more of its own produce
Over a span of just six months, Covid-19 has not only changed the way we work, celebrate occasions and stay healthy but also forced countries to take a hard look at how they feed their residents. “I believe the current pandemic has provided us the opportunity to completely reimagine the global food system,” says Tony Hunter, a global food futurist.
Going urban
One of the factors pushing the global agri-tech agenda is the growth and increasing density of cities. “By 2050, more than two thirds of the world’s population is forecasted to live in cities,” explains Smitha Paresh, Executive Director of Greenoponics, a UAE-based retailer of commercial and consumer hydroponics systems, adding that urban agriculture will be crucial for feeding burgeoning urban populations.
“On a macro level, we will see a rise in urban farming, mostly using high-tech farming methods such as hydroponics, aeroponics or aquaponics.” Paresh cites Singapore’s conversion of car parks into urban farm centres as an example. “In the UAE, as per the national food security strategy for 2017-2021, we have already witnessed a huge increase in climate-controlled greenhouses all over the country.”
Arable environments
For Hunter, who spoke about potential silver linings of Covid-19 at a recent Gulfood webinar, new technologies present the best means of achieving domestic self-sufficiency. “They can release countries from the tyrannies of arable land and water stress.” He singles out algal products that rely on low rainfall and can use seawater; cultivated meat and biomass products; cell-based products such as milk proteins; and synthetic biology that can manufacture a range of food products.
Over the long term, Ravindra Shirotriya, CEO, VeggiTech, believes there are three critical areas for sustainable farming in the UAE. The first is precision agriculture, which focuses on growing conditions for plants using hyperbaric chambers and nanotechnology-based organic nutrition. Photo bio-reactors, meanwhile, can cultivate food-grade algae such as spirulina. Finally, Shirotriya cites smart farms, which work with smart cities to create harvest plans based on real-time data on food demand and consumption within communities. “This will address our current broken food ecosystem, where we waste 35 percent of food while 15 percent of the world population goes to sleep hungry.”
VeggiTech’s primary focus is on setting up LED-assisted hydroponics for indoor vertical farms and protected hydroponics for sustainable farming in the UAE.
In terms of crop production, Avinash Vora, Co-founder of Aranya Farms, says new technologies aim to boost yields, reduce waste and grow produce entirely. “Technology is being applied at every stage, whether for plant seeding, monitoring growth, managing water, energy conservation, harvesting and packaging. “We are making huge strides adapting all of them here in the UAE; the interest and investments in agriculture prove that.”
For Philippe Peguilhan, Country Manager of Carrefour UAE at Majid Al Futtaim Retail, the UAE had already been seeking self-reliance in food production, but coronavirus amped up its importance. “The disruption that Covid-19 caused to the supply chain highlighted the importance of local produce and presented an excellent opportunity for local farmers to grab a greater share of the market.” Majid Al Futtaim recently made headlines for opening the UAE’s third, and Dubai’s first, in-store hydroponics farm.
Hydroponic hope
Hydroponics is one agri-tech that’s attracting keen investor interest. “As an indicator, Madar Farms’ 7,000-sq-m factory will produce 365 tons of tomatoes a year, and about 14,000 tons of cherry vine tomatoes were consumed in the UAE in 2019,” says Hunter. “There’s therefore the market opportunity for 38 Madar farms in the UAE for tomatoes alone. Add in other nutrient-dense crops such as cucumbers, peppers and leafy greens. Depending upon their size, we could be looking at several hundred businesses.”
On an individual level, more people are leaning towards home farming, especially towards soil-less cultivation since it is simple and easy, according to Paresh. “It guarantees a certain amount of yield. Home farming will be on the rise, considering the disruption we may face in trying times like this.”
As with most technologies, Hunter says the biggest challenge of hydroponics is profitability. “Fortunately, the costs of technology inputs required to optimise hydroponic production efficiencies are falling rapidly. This drop, together with simultaneous increases in performance, is driving down the costs of hydroponics, making acceptable ROIs much easier to achieve.” He adds that economies of scale can help achieve good ROIs. “Currently most farms are in the 1-2 ton per day range but farms of 50 tons per day are being projected by as early as 2025.”
Sustainability challenges
“Challenges in building our own farm were access to sufficient and cost-effective electricity; renewable sources of water; and the availability of locally made raw materials, specifically growing media, nutrients and seeds. With seeds we are adapting — we have been growing our own seeds but having a library of seeds to choose from that are suitable for our climate and environment would be a huge boon to all farmers.”
— Avinash Vora, Co-founder of Aranya Farms
By Riaz Naqvi, Staff Writer | Gulf News | May 28, 2020
Lettuce Scare Spurs Sales At Superior's Bay Produce
Recent outbreaks of foodborne illnesses have generally been bad news for lettuce growers nationwide, but one greenhouse operation in snowy Superior reports its sales actually have been bolstered as consumers search for healthy alternatives to field-grown greens
Written By: Peter Passi | Dec 21st, 2019
Greenhouse with a mission delivers safe greens to the local market.
Rich Fisher, Bay Produce's head grower, checks the pH level of the water in flats growing butterhead lettuce at Bay Produce in Superior. (Clint Austin / caustin@duluthnews.com)
Recent outbreaks of foodborne illnesses have generally been bad news for lettuce growers nationwide, but one greenhouse operation in snowy Superior reports its sales actually have been bolstered as consumers search for healthy alternatives to field-grown greens.
Bay Produce, located next door to the Mariner Retail and Business Center, has found a strong market for the red and green butterhead lettuces it grows in the wake of a national lettuce scare.
"It seems like any time there's a lettuce recall, our sales go up," said Don Gitz, a specialist for Bay Produce.
Most recently, the U.S. Food and Drug Administration warned consumers to avoid eating romaine lettuce harvested in California's Salinas Valley — a prolific agricultural region often referred to as the nation's salad bowl. This latest E. coli outbreak resulted in more than 100 reported cases of illness in 23 states. But regulators advised people that there was no reason to avoid hydroponic and greenhouse-grown lettuce.
8 / 8
The silver tube at the center of the photo houses a high-intensity ultraviolet light used to kill pathogens in the water at Bay Produce in Superior. (Clint Austin / caustin@duluthnews.com)
Bay Produce fits that bill to a T. It grows lettuce, basil, tomatoes, cucumbers, peppers and eggplant inside a 1 1/2-acre greenhouse equipped with hydroponics.
Rich Fisher, Bay Produce's head grower, said the greenhouse uses Superior city water that has been treated with ultraviolet light, rendering it "99.9% microbe-free."
He contrasted the sterile greenhouse setting at Bay Produce to farm fields where lettuce is often grown on plots adjacent to livestock "where they really have almost no control over runoff."
In addition to producing a consistently safe and tasty product, Bay Produce also has a story to sell. The greenhouse is operated by Challenge Center Inc., an organization established by Catholic Charities 50 years ago to serve children and adults with developmental disabilities. The greenhouse is staffed with 10 Challenge Center staff members and up to about 40 clients at any given time.
Challenge Center Director Mark Kroll said the greenhouse provides a sheltered work setting that can accommodate clients' unique needs, whether that's a short two-hour shift or one accompanied by a job coach.
"We provide sheltered employment for folks with disabilities," Kroll said. "It's an amazing program we have here. So, we already have a lot of local folks looking for our projects anyway, because they support our mission. But this provides a little extra push for us. It's one more reason for folks to look for Bay Produce products."
Bay Produce has enjoyed a safety edge over larger growers in regard to other products, too. For instance, earlier this summer people across the nation were sickened with cyclosporiasis from contaminated basil grown in Mexico. Again, Bay Produce offered a safe alternative.
"It's amazing how things that happen on a national scale that make the national news can really affect local growers," Kroll said.
Bay Produce distributes its products exclusively in the Northland through grocers and restaurants as far north as Grand Marais and as far east as Ashland. Because its produce isn't traveling great distances, Kroll said they are able to deliver a product that's ripe and ready to eat the moment it hits the shelves or lands on a restaurant's sandwich.
US, OHIO: Great Lakes Ag Tech Summit - September 23, 2019
Join Urban Ag News, Hort Americas and Current, powered by GE, for the inaugural Great Lakes Ag Tech Summit on September 23. The summit will be held at at the historic Nela Park campus in Cleveland, Ohio
By urbanagnews
August 14, 2019
Join Urban Ag News, Hort Americas and Current, powered by GE, for the inaugural Great Lakes Ag Tech Summit on September 23. The summit will be held at at the historic Nela Park campus in Cleveland, Ohio.
The one-day event features keynote presentations and panel discussions from leading researchers and innovative growers in the Great Lakes region. Attendees will be able to connect with growers, scientists, researchers and entrepreneurs as we shape the future of food and move controlled environment agriculture forward.
Keynotes
Optimizing Plant Production Under a Controlled Environment – Research and Education Programs at the Ohio State University
Dr. Chieri Kubota – The Ohio State University
Dr. Kubota’s research mission is to serve in the development of science and technology in the area of controlled environment agriculture (CEA). Her projects are in an interdisciplinary area that encompasses plant physiology and horticultural engineering to enhance understanding and efficiency of CEA plant production systems such as greenhouses, warehouses (vertical farms), and growth chambers.
Are Consumers and Growers Putting Dollars in the Local Food Industry? Insights on Technologies and Preferences
Dr. Ariana Torres – Purdue University
Dr. Torres’ background combines field experience in agriculture with theoretical and applied research on agricultural economics. She has worked on projects looking at the impact of marketing choices on technology adoption for fruit and vegetable growers; the economic implications of social capital on entrepreneurship; and the role of community support on the resilience of small business after disasters.
Dr. Torres uses economic analysis to support the economic viability of the horticulture industry. Her research focuses on the intersection between the horticulture industry and marketing decisions. Her goal is to conduct innovative outreach and applied research in specialty crops marketing, with the end of promoting economic sustainability for horticultural businesses.
Dr. Torres is currently working on a project evaluating the market, economics, and potential barriers to produce export-quality dried apricots from smallholders of southern Tajikistan. She is also working on evaluating the adoption of a solar dehydrator for selected dried specialty crops in Indiana and Georgia. Lastly, she is collecting foundational data and establishing long-term pricing reports for Indiana farmers markets.
Vertical Farm Production of Young Plants, From Hemp to Tomatoes
John Jackson – Sustainable Indoor Growing Systems, Inc.
John is the CEO of Sustainable Indoor Growing Systems, Inc. (SIGS) born from an USDA funded industry-academic partnership with Grafted Growers, the University of Arizona, and North Carolina State University. John is an award-winning entrepreneur and University of Arizona alum with an MBA from the Eller College of Management. John has successfully launched investor and grant funded businesses and operated tech based companies to early stage revenue. Born in Compton, California, John continues his grandfather’s legacy as a sharecropper of tomatoes in rural Texas.
SIGS gives plants what they need to express the features that the market wants.
Sustainable Indoor Growing Systems, Inc. (SIGS) is a clean agricultural technology company that uses controlled environment agriculture to induce young generic plants to express enhanced physiological traits customers want – while increasing the economics of propagation. This is made possible by scientific discovery and development of unique growing recipes which are learned and enabled only by the SIGS multi-layered growing platform and architecture.
Click Here to Register Now! Seats Are Limited!
Location
1975 Noble Rd. Cleveland, OH 44112
Date & Time
Monday, September 23, 2019
9 am to 4pm
Registration
Early bird admission price is $30 if registration occurs before Sept. 16.
Regular admission: $50
Hotel
Hyatt Legacy Village
24665 Cedar Rd
Lyndhurst, OH 44124
The rate is $129 for the night of 9/22/19.
• Call the toll-free number at 1-888-492-8847 for Hyatt Place Reservations and ask for the “Great Lakes Ag Tech Summit” or code G-GLGT
• OR use this link https://www.hyatt.com/en-US/hotel/ohio/hyatt-place-cleveland-lyndhurst-legacy-village/clezl?corp_id=G-GLGT
Click Here to Register Now!
About Urban Ag News
The mission of Urban Ag News is to be the leading science communicator for the commercial hydroponics, greenhouse vegetable, vertical farming and urban agriculture industries. Urban Ag News educates readers and provide an understanding of the industry’s latest technologies and luminaries.
About Current, powered by GE
Current, powered by GE, offers cutting-edge innovations in horticultural lighting. We’ve spent years perfecting our lighting technology and working with growers, systems integrators and plant scientists to establish the specific needs of the horticulture industry. The result? LED grow systems that maximize the potential of greenhouses and indoor farms by enabling efficient growth at an industrial scale.
TAGS Ariana Torres Chieri Kubota Conference GE Lighting Greenhouse Greenhouse Technology Hort Americas Indoor Ag Technology LED Grow Lights Ohio State University
Grow Lights Are Major Focus of Cultivate’19 Educational Sessions
If you are contemplating installing supplemental grow lights in your controlled environment production facility, then Cultivate’19 was the place to learn how the lights are being used. Both growers and university researchers presented information on the results they have gotten with grow lights, particularly light-emitting diodes (LEDs)
Growers and researchers discuss the benefits of using grow lights when it comes to growing controlled environment crops.
If you are contemplating installing supplemental grow lights in your controlled environment production facility, then Cultivate’19 was the place to learn how the lights are being used. Both growers and university researchers presented information on the results they have gotten with grow lights, particularly light-emitting diodes (LEDs).
Grow lights a must for producing greenhouse strawberries
Sarah Gunn, head grower at De Jong Greenhouses in Pella, Iowa, discussed how she has been using LEDs to produce greenhouse strawberries from November through January. The company, which grows primarily ornamental plants, has been trialing greenhouse strawberries for eight years. For the last three years the company has been selling its strawberries through a produce distributor to local grocery stores. Gunn said the price point during the months the company produces the berries has been good enough to justify the costs associated with growing the crop.
Gunn said the strawberries which are grown in 12-inch containers can hold three to four plants. She advised growers to start with certified bare root plants. Greenhouse strawberries are a labor intensive crop requiring removal of runners (stolons), old leaves and harvesting fruit every two to three days.
Gunn said that two-thirds of the United States doesn’t have sufficient light levels during the winter months to grow greenhouse strawberries. The optimum daily light integral (DLI) for strawberries is 15-25 moles per square meter per day (mol·m-2·d-1). Gunn is using LEDs to deliver a DLI of 12 mol·m-2·d-1. Extending the day length to 13-16 hours can help boost fruit yields. Plants should not be lit for longer than 16 hours.
The company purchases bumblebees to pollinate the strawberry plants. Because different light spectrum can affect bumblebees, Gunn advises growers to find out how grow lights can impact the bees behavior.
Growers in two-thirds of the United States don’t have sufficient light levels during the winter months to produce greenhouse strawberries.
Photo courtesy of Chieri Kubota, Ohio St. Univ.
De Jong uses a template for berry size and color to determine when the berries are ready to harvest. Since strawberries were the first food crop the company had grown, a consultant was hired to implement food safety protocols.
Gunn said cultural practices and biocontrols are being used for greenhouse pests and diseases. Pests include two-spotted spider mite, aphids and thrips. Prior to growing greenhouse strawberries Gunn said she never had to deal with lygus bugs, commonly referred to tarnished plant bugs. Diseases issues include powdery mildew, Botrytis and leather rot (Phytophthora cactorum).
Multiple crops grow well under LEDs
A panel of growers and a university researcher discussed the experiences they have had growing under LEDs.
John Bonner, owner and CEO at Great Lakes Growers in Burton, Ohio, has been hydroponically growing leafy greens and herbs since 2011 when he started with 300 square feet of greenhouse production. His operation has expanded to 160,000 square feet. Bonner who started with high pressure sodium (HPS) lamps has replaced most of those fixtures with LEDs. Once the company’s current expansion is completed Bonner expects to be able to annually produce 6 million heads of lettuce.
James Darrow, general manager at Jolly Farmer in New Brunswick, Canada, began research with LEDs in 2012. He said Jolly Farmer provides at least 25 moles of light per day by LEDs during the winter. After installing LEDs Darrow said adjustments had to be made in how often crops were irrigated, fertilizer applications and crop timing. Many of the bedding crops, especially begonias, needed to be fertilized more often when grown under LEDs.
The economics of using grow lights
Horticultural researchers Neil Mattson from Cornell University and Marc van Iersel from the University of Georgia discussed the Lighting Approaches to Maximize Profits (LAMP) project. Funded by the USDA National Institute for Food and Agriculture Specialty Crop Research Initiative, LAMP aims to determine how growers can maximize their return on investment when considering installing grow lights.
Researchers involved with the Lighting Approaches to Maximize Profits (LAMP) project are working to help growers maximize their return on investment in grow lights while optimizing plant growth.
Photo courtesy of Marc van Iersel, Univ. of Georgia
The team of researchers involved in this $5 million, four-year project is studying the best way to optimize crop growth and quality in cost-effective ways. The research includes simulation of different lighting scenarios and the use of sensors to monitor crop growth and physiology. Researchers are studying how much light crops require and assessing supplemental lighting needs and options.
This article is property of Hort Americas and was written by David Kuack, a freelance technical writer in Fort Worth, TX.
IHS ‘Ready to Grow’ Horticultural LED Grow Lights Named As Innovative New Product Winner at HTA National Plant Show
Intelligent Horticultural Solutions (IHS) was thrilled to be announced the Innovation winner in the New Product Showcase at the HTA National Plant Show, which took place on 18-19 June 2019 at Stoneleigh Park, Coventry.
Intelligent Horticultural Solutions (IHS) was thrilled to be announced the Innovation winner in the New Product Showcase at the HTA National Plant Show, which took place on 18-19 June 2019 at Stoneleigh Park, Coventry.
New HTA members IHS received the accolade for their ‘Ready to Grow’ range of Florence horticultural LED grow lights. The annual event was a great success with a wide variety of British suppliers to the horticultural market exhibiting their wares. Attendees, were mainly suppliers to the green-fingered public such as garden centres, landscape gardeners, etc., voted the IHS lighting solution as the most inspiring, Innovative New Product showcased at the show.
IHS’s Florence LED grow lights are designed specifically for low and no sunlight applications, maximising growth potential whilst minimising both initial purchase costs and on-going running costs. The Florence unit is no deeper than a standard fluorescent tube fitting, allowing an easy switch to LED lighting without losing growing space.
The modular design enables a smooth, effortless installation, which paired with the standard 100-240V AC mains input, allows for a quick and easy electrical installation, saving further time and cost. LED recipes are available for a wide range of standard horticultural applications, as well as fully customisable solutions.
The Florence range is proving to be a success within the sector having already won the Award for Best Innovation 2018 at the GroSouth Show held last November in Chichester. This was an important day for IHS, being the official launch and showcasing of the new Florence LED grow light modules into the fast-growing horticultural market.
There are currently eight different standard Florence LED recipes to choose from including; Biomass, Seeding, Flowering, and Fruiting” (available for applications both with or without existing daylight). Three different lens options are available, per recipe – narrow, wide and oval to direct the light onto the target areas.
These recipes were devised in conjunction with experts from LED manufacturer Osram Opto Semiconductors, who are market leaders in the supply of quality LEDs for the horticultural lighting sector.
IHS’s ‘Ready to Grow’ LED lights enable a longer growing season and also increase the speed of growth for plants, when under the correct recipe.
The Florence product range is currently available for purchase through RS Components.
LED Recipe IHS Part Number RS Article (Buy Here)
Biomass FLORENCE-BIO-WIDE-CASED-1CH-01. (187-4965)
Seeding FLORENCE-SEED-WIDE-CASED-1CH-01. (187-4970)
Flowering FLORENCE-FLOWER-WIDE-CASED-1CH-01. (187-4967)
Fruiting FLORENCE-FRUIT-WIDE-CASED-1CH-01. (187-4968)
Quality LED horticultural lighting from IHS is a cost-effective and viable solution for both backyard gardeners and large commercial growers alike. Ideal markets for these grow lights include polytunnels, environmental chambers, propagators, vertical farms and indoor farms, as well as schools, universities and research institutes.
IHS is a LED Light for You (LLFY) Partner, which draws on world-leading quality LEDs from Osram Opto Semiconductors and combines them with other quality components, materials and in-house expertise to provide the LED solution you need.
More horticultural LED Grow Light product families are being introduced from IHS in the near future, watch this space!
All our horticultural LED Grow Lights will be on show at our 2019 Horticultural LED seminars. - Sign up now
For enquiries or further information, please contact +44 (0) 1635 294606 or info@i-hled.co.uk
Or alternatively, refer to our website www.i-hled.co.uk
ILS is a division of Intelligent Group Solutions Ltd (IGS) a well-established and respected industry leading display and opto-electronics solutions provider. IGS’ provides semi-custom or custom products both in component and sub-assembly form. All the senior staff have been involved with the opto-electronics industry for at least 20 years and are dedicated to ensuring that ILS is an innovative and highly successful operation.
4 July 2019
Rensselaer Polytechnic Institute Lighting Research Center Releases New Report on LED Horticultural Lighting Systems
The Lighting Research Center (LRC) at Rensselaer Polytechnic Institute has published a new report on the energy and economic performance of LED horticultural luminaires.
Rensselaer Polytechnic Institute Lighting Research Center Releases New Report on LED Horticultural Lighting Systems
By urbanagnews
May 16, 2018
The Lighting Research Center (LRC) at Rensselaer Polytechnic Institute has published a new report on the energy and economic performance of LED horticultural luminaires. The LRC evaluated key factors such as power demand, life-cycle cost, luminaire intensity distribution, and luminaire shading. Of particular importance is the fact that the LRC considered the effectiveness of the entire lighting system for a controlled growing environment.
The research team found that for a given growing area, energy savings were possible with some of the tested LED horticultural luminaires compared to the tested high-pressure sodium (HPS) and metal halide (MH) horticultural luminaires, when meeting the same photosynthetic photon flux density (PPFD) criterion, but there was remarkably wide variation among products.
The LRC chose PPFD as the primary metric for the evaluation because, for plants, PPFD is analogous to photopic illuminance on a work surface in an architectural application. Just as it is only valid to compare the power densities of alternate lighting systems at equal illuminance levels on the work plane, the power densities of alternate horticultural luminaires should only be compared when they provide the same PPFD on the plant canopy. The LRC found that, on average, approximately three times as many LED horticultural luminaires would be needed to provide the same PPFD as a typical 1000-watt HPS horticultural luminaire layout.
For this project, the LRC developed an equal-PPFD-based framework for evaluating and comparing horticultural luminaires, which includes 11 luminaire-specific metrics and 5 application-specific metrics to provide growers with the most accurate information regarding any given horticultural luminaire’s performance. The LRC used this framework to evaluate a total of 14 horticultural luminaires, including 10 LED products. The evaluation included photometric testing, application simulations, and life-cycle cost analysis.
The results of the evaluation show that stakeholders can be misled by considering luminaire efficacy alone. Rather, the luminaire intensity distribution and layout to reach a criterion PPFD are necessary for an accurate life-cycle cost analysis. The LRC report provides a technology-neutral framework that stakeholders can use to evaluate lighting systems.
“Upon analyzing our data, we were intrigued by how intensity distribution and layout emerged as key factors in system performance,” said LRC Research Scientist Leora Radetsky, who authored the report.
When choosing a lighting system for a greenhouse, growers should consider the size and number of luminaires needed, because luminaires block the daylight from reaching the plants. The LRC shading analysis found an increase in shading from LED luminaires compared with HPS luminaires due to the size of the luminaires and the fact that more are needed to provide the same PPFD. The shading from LED luminaires reduces daylight in a greenhouse by up to 55% compared with a 5% reduction in daylight from HPS luminaires, thus more electric energy could be needed for lighting with the LED systems, depending upon the available daylight.
In a recent LRC survey, 75% of growers identified the cost of LED horticultural lighting to be a barrier to adoption, therefore it was important to include a life-cycle cost analysis in the report. The LRC found that three of the tested LED horticultural luminaire lighting systems had lower life-cycle costs and the remaining seven had higher life-cycle costs than either of the two 1000-watt HPS lighting systems that were tested.
“Energy use and life-cycle costs vary widely among LED and HPS lighting systems used in controlled environment horticulture,” said Radetsky. “It has been the standard approach for many years in the field of architectural lighting, and is becoming readily apparent in horticultural lighting, that we must conduct complete system energy and life-cycle cost analyses to generate an accurate picture of which technology would work best for each particular application.”
The project was funded by the Lighting Energy Alliance and Natural Resources Canada. Members of the Lighting Energy Alliance include Efficiency Vermont, Energize Connecticut, National Grid, and the Northwest Energy Efficiency Alliance.
View the LED and HID Horticultural Luminaire Testing Report.
About the Lighting Energy Alliance
The Lighting Energy Alliance (LEA) at Rensselaer Polytechnic Institute’s Lighting Research Center is a collaboration of members who pool their funds to advance lighting research and education that is of common interest. Since launching in 2014, LEA has worked to identify effective new ways to save energy, quantify the savings, and support its members in implementation.
About the Lighting Research Center
The Lighting Research Center (LRC) at Rensselaer Polytechnic Institute is the world’s leading center for lighting research and education. Established in 1988 by the New York State Energy Research and Development Authority (NYSERDA), the LRC has been pioneering research in solid-state lighting, light and health, transportation lighting and safety, and energy efficiency for more than 30 years.
LRC lighting scientists with multidisciplinary expertise in research, technology, design, and human factors collaborate with a global network of leading manufacturers and government agencies, developing innovative lighting solutions for projects that range from the Boeing 787 Dreamliner to U.S. Navy submarines to hospital neonatal intensive-care units. LRC researchers conduct independent, third-party testing of lighting products in the LRC’s state of the art photometric laboratories, the only university lighting laboratories accredited by the National Voluntary Laboratory Accreditation Program (NVLAP Lab Code: 200480-0).
In 1990, the LRC became the first university research center to offer graduate degrees in lighting and today, offers an M.S. in lighting and a Ph.D. to educate future leaders in lighting. With 35 full-time faculties and staff, 15 graduate students, and a 30,000 sq. ft. laboratory space, the LRC is the largest university-based lighting research and education organization in the world.
About Rensselaer Polytechnic Institute
Rensselaer Polytechnic Institute, founded in 1824, is America’s first technological research university. The university offers bachelor’s, master’s, and doctoral degrees in engineering; the sciences; information technology and web sciences; architecture; management; and the arts, humanities, and social sciences.
Rensselaer faculty advance research in a wide range of fields, with an emphasis on biotechnology, nanotechnology, computational science and engineering, data science, and the media arts and technology. The Institute has an established record of success in the transfer of technology from the laboratory to the marketplace, fulfilling its founding mission of applying science “to the common purposes of life.”