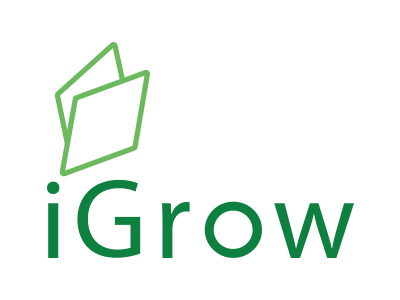
Welcome to iGrow News, Your Source for the World of Indoor Vertical Farming
Technology Is Shaping The Future of Food But Practices Rooted In Tradition Could Still Have A Role To Play
Its executive summary said the food we consume — and the way we produce it — was “doing terrible damage to our planet and to our health.”
By Anmar Frangoul
August 6, 2021
From oranges and lemons grown in Spain to fish caught in the wilds of the Atlantic, many are spoiled for choice when it comes to picking the ingredients that go on our plate.
Yet, as concerns about the environment and sustainability mount, discussions about how — and where — we grow our food have become increasingly pressing.
Last month, the debate made headlines in the U.K. when the second part of The National Food Strategy, an independent review commissioned by the U.K. government, was released.
The wide-ranging report was headed up by restaurateur and entrepreneur Henry Dimbleby and mainly focused on England’s food system. It came to some sobering conclusions.
Its executive summary said the food we consume — and the way we produce it — was “doing terrible damage to our planet and to our health.”
The publication said the global food system was “the single biggest contributor to biodiversity loss, deforestation, drought, freshwater pollution and the collapse of aquatic wildlife.” It was also, the report claimed, “the second-biggest contributor to climate change, after the energy industry.”
Dimbleby’s report is one example of how the alarm is being sounded when it comes to food systems, a term the Food and Agriculture Organization of the UN says encompasses everything from production and processing to distribution, consumption and disposal.
According to the FAO, food systems consume 30% of the planet’s available energy. It adds that “modern food systems are heavily dependent on fossil fuels.”
All the above certainly provides food for thought. Below, CNBC’s Sustainable Future takes a look at some of the ideas and concepts that could change the way we think about agriculture.
Growing in cities
Around the world, a number of interesting ideas and techniques related to urban food production are beginning to gain traction and generate interest, albeit on a far smaller scale compared to more established methods.
Take hydroponics, which the Royal Horticultural Society describes as “the science of growing plants without using soil, by feeding them on mineral nutrient salts dissolved in water.”
In London, firms like Growing Underground are using LED technology and hydroponic systems to produce greens 33-meters below the surface. The company says its crops are grown throughout the year in a pesticide free, controlled environment using renewable energy.
With a focus on the “hyper-local”, Growing Underground claims its leaves “can be in your kitchen within 4 hours of being picked and packed.”
Another business attempting to make its mark in the sector is Crate to Plate, whose operations are centered around growing lettuces, herbs and leafy greens vertically. The process takes place in containers that are 40 feet long, 8 feet wide and 8.5 feet tall.
Like Growing Underground, Crate to Plate’s facilities are based in London and use hydroponics. A key idea behind the business is that, by growing vertically, space can be maximized and resource use minimized.
On the tech front, everything from humidity and temperature to water delivery and air flow is monitored and regulated. Speed is also crucial to the company’s business model.
“We aim to deliver everything that we harvest in under 24 hours,” Sebastien Sainsbury, the company’s CEO, told CNBC recently.
“The restaurants tend to get it within 12, the retailers get it within 18 and the home delivery is guaranteed within 24 hours,” he said, explaining that deliveries were made using electric vehicles. “All the energy that the farms consume is renewable.”
Grow your own
While there is a sense of excitement regarding the potential of tech-driven, soilless operations such as the ones above, there’s also an argument to be had for going back to basics.
In the U.K., where a large chunk of the population have been working from home due to the coronavirus pandemic, the popularity of allotments — pockets of land that are leased out and used to grow plants, fruits and vegetables — appears to have increased.
In September 2020 the Association for Public Service Excellence carried out an online survey of local authorities in the U.K. Among other things it asked respondents if, as a result of Covid-19, they had “experienced a noticeable increase in demand” for allotment plots. Nearly 90% said they had.
“This alone shows the public value and desire to reconnect with nature through the ownership of an allotment plot,” the APSE said. “It may also reflect the renewed interest in the public being more self-sustainable, using allotments to grow their own fruit and vegetables.”
In comments sent to CNBC via email, a spokesperson for the National Allotment Society said renting an allotment offered plot holders “the opportunity to take healthy exercise, relax, have contact with nature, and grow their own seasonal food.”
The NAS was of the belief that British allotments supported “public health, enhance social cohesion and could make a significant contribution to food security,” the spokesperson said.
A broad church
Nicole Kennard is a PhD researcher at the University of Sheffield’s Grantham Centre for Sustainable Futures.
In a phone interview with CNBC, she noted how the term “urban agriculture” could refer to everything from allotments and home gardens to community gardens and urban farms.
“Obviously, not all food is going to be produced by urban agriculture, but it can play a big role in feeding local communities,” she said.
There were other positives, too, including flood and heat mitigation. “It’s … all those benefits that come with having green spaces in general but then there’s the added plus, [which] is that you’re producing food for local consumption.”
On urban farming specifically, Kennard said it provided “the opportunity to make a localized food system” that could be supported by consumers.
“You can support farms that you know, farmers that you know, that are also doing things that contribute to your community,” she said, acknowledging that these types of relationships could also be forged with other types of farms.
Looking ahead
Discussions about how and where we produce food are set to continue for a long time to come as businesses, governments and citizens try to find ways to create a sustainable system that meets the needs of everyone.
It’s perhaps no surprise then that some of the topics covered above are starting to generate interest among the investment community.
Speaking to CNBC’s “Squawk Box Europe” in June, Morgan Stanley’s global head of sustainability research, Jessica Alsford, highlighted this shift.
“There’s certainly an argument for looking beyond the most obvious … ways to play the green theme, as you say, further down the value and the supply chain,” she said.
“I would say as well though, you need to remember that sustainability covers a number of different topics,” Alsford said. “And we’ve been getting a lot of questions from investors that want to branch out beyond the pure green theme and look at connected topics like the future of food, for example, or biodiversity.”
For Crate to Plate’s Sainsbury, knowledge sharing and collaboration will most likely have a big role to play going forward. In his interview with CNBC, he emphasized the importance of “coexisting with existing farming traditions.”
“Oddly enough, we’ve had farmers come and visit the site because farmers are quite interested in installing this kind of technology … in their farm yards … because it can supplement their income.”
“We’re not here to compete with farmers, take business away from farmers. We want to supplement what farmers grow.”
Lead Photo: Fruit and vegetable allotments on the outskirts of Henley-on-Thames, England.
PinDuoDuo: Building A More Resilient Food System With Technology - July 14 -15
Join us virtually for our inaugural Food Systems Forum, which will convene experts from around the world to share their insights and spark further connections and potential collaborations
The pandemic has shone a light on how fragile and intertwined our global agri-food supply chain is, making it even more pressing to push for food systems innovation and change. Can we leverage technology to build a more resilient food system that feeds more people and feeds them better?
Join us virtually for our inaugural Food Systems Forum, which will convene experts from around the world to share their insights and spark further connections and potential collaborations.
Register To Join The Conversation
Affordable, Image-Based Crop Monitoring Using Smartphones and Microcontrollers
Dr. Krishna Nemali and his research group at Purdue University are tackling crop-monitoring challenges facing hydroponic and flower growers. Of the group’s many research foci, image-based crop monitoring using smartphones and microcontrollers has been at the forefront of Purdue’s technological advancements for the CEA industry.
Smart Sensors From Purdue University
With a mission to deliver easy-to-use, rapid and affordable technologies to the controlled environment agriculture (CEA) industry, Dr. Krishna Nemali and his research group at Purdue University are tackling crop-monitoring challenges facing hydroponic and flower growers. Of the group’s many research foci, image-based crop monitoring using smartphones and microcontrollers has been at the forefront of Purdue’s technological advancements for the CEA industry.
Image-based crop monitoring made practical and affordable
Image analysis is being used for monitoring plants in conventional, field-based agriculture through satellites, drones, and camera-mounted vehicles. However, these technologies are not practical for greenhouses and indoor farms due to the architecture of these facilities, which limits the movement of drones or camera-mounted vehicles over plants. Dr. Nemali and his research group are working to bring image-based crop monitoring on smartphones as handheld sensors. For installations where using cameras fixed to the growing systems is preferred (e.g. vertical farms with multi-tiered racking) or applications where continuous monitoring is useful, the research team is also building a system with a Raspberry Pi microcontroller and high-resolution camera, which sends the images to a central computer for processing and interpretation.
Left: Dr. Krishna Nemali. Right: smartphone sensor
Compared image-based monitoring to human evaluation
To test the efficacy of image-based crop monitoring, the research team grew lettuce and tomatoes under optimal and suboptimal conditions. In a blind trial, crop growth was visually evaluated daily by people (using a rating system) and by image-based sensors. As Dr. Nemali explains, the image-based system recorded statistically significant differences in crop growth between optimal and sub-optimal conditions 3-4 days before the human eye could detect differences.
“When you regularly take these photos and develop growth curves, you can monitor how your crop is measuring up against expected optimal growth. If these images indicate an issue, growers can resolve this before it is too late,” says Dr. Nemali.
The images can also be used to assess nitrogen status, germination percentage, and rate, and color progression, allowing the grower to monitor crop health, planting material, and estimate the time to harvest. Plant nitrogen status is usually measured in a laboratory, which is expensive and time-consuming or using expensive chlorophyll meters. Dr. Nemali’s research developed accurate algorithms using images captured by smartphones and microcontrollers to rapidly estimate plant nitrogen status.
Different plant measurements can be measured using images collected by a smartphone or microcontroller
Instantaneously assessing plant nitrogen
“Imaging the benefits of instantaneously assessing plant nitrogen status in CEA industry. Growers can supply fertilizers based on plant needs and avoid over or under application rates,” says Dr. Nemali
As these technologies are being developed at Purdue University, they will be made available to growers at a low cost, with any generated funds being poured back into further research and development. The smartphone app should be available in the spring of 2022, with a low purchase price and yearly license.
With photo-quality varying according to the camera, ambient light conditions, and distance from the crop, normalization processes have been incorporated into algorithms to ensure high-quality analyses. To account for differences in distance from the crop between imaging sessions, each photo is taken with a standard, measured object in the frame.
“Let’s say we have a red square with a known area of 25 cm2 and we place it beside the crop in each image. The computer will recognize that object, uses its area to determine the right pixel-area conversion and apply it to the plant. This creates a relative scale and eliminates height/distance altogether,” says Dr. Nemali.
To normalize for different light conditions, the technology considers different reflected wavelengths, both of which are affected by light intensity. By taking the ratio of two wavelengths, the setup can eliminate the effects of light intensity on the images altogether.
A demonstration of smartphone-based image technology can be viewed on Dr. Nemali’s website at this link.
Additional areas of research
Aside from image-based crop monitoring, Dr. Nemali’s research group is conducting extensive research on nitrogen management in hydroponically grown organic lettuce production.
“The yields of organic lettuce is usually lower compared to conventional production, because of challenges with nitrogen availability to plants in organic production. While organic lettuce does command a higher price, we still need to increase these yields to make it sustainable and organic produce more available to consumers,” explains Dr. Nemali.
Other areas of research include the use of ultraviolet radiation and ozone to reduce the risk of E. coli contamination in lettuce, and the optimization of production techniques to improve the nutritional density of leafy greens.
For more information on ongoing research in Dr. Nemali’s research group:
Dr. Krishna Nemali
Assistant Professor in Controlled Environment Agriculture
Purdue University
https://www.purdue.edu/hla/sites/cea/
24 June 2021
Author: Rose Seguin
© HortiDaily.com
PinDuoDuo: Building A More Resilient Food System With Technology - July 14 -15
Join us virtually for our inaugural Food Systems Forum, which will convene experts from around the world to share their insights and spark further connections and potential collaborations
The pandemic has shone a light on how fragile and intertwined our global agri-food supply chain is, making it even more pressing to push for food systems innovation and change. Can we leverage technology to build a more resilient food system that feeds more people and feeds them better?
Join us virtually for our inaugural Food Systems Forum, which will convene experts from around the world to share their insights and spark further connections and potential collaborations.
Register To Join The Conversation
“We Believe That The Time Has Come To Harness Innovative Technologies”
"The extreme African weather conditions make this market a perfect candidate for controlled environmental growth," says Francois Duvenage, R&D researcher at CAN Agri.
"The extreme African weather conditions make this market a perfect candidate for controlled environmental growth," says Francois Duvenage, R&D researcher at CAN Agri. “From wet tropical to extreme desert conditions, it especially means we can enable African countries to successfully grow their produce and sell a marketable product.”
Francois says the company has “two extremely exciting projects coming up, one project in Namibia starting in the next few months and the other is an international collaboration that we established and are strengthening.” According to him, the company is not only targeting Africa but also areas such as Eurasia and North America.
Value proposition
CAN-Agri has developed a multi-faceted solution to ensure our client’s overall support to successfully commission and sustain a CAN-Agri hybrid vertical-greenhouse. “We employ a six-phase approach where each phase is developed to ensure the client’s requirements are accommodated by detailed consultation agreements," says Francois.
“We believe that the time has come to harness innovative technologies to enable responsible and efficient food production, meeting the challenges and demands of the years to come,” says Francois. CAN-Agri’s operational procedure allows an advantage, that a farming unit is flexible in design and scalable to suit client needs. The vertical tower growing units allow for improved product quality and quantity through all seasons. Rows of fresh produce are harvested daily, opening space for new seedlings to be planted, forming a continuous daily production cycle.
Upcoming projects
As the travel restrictions are lifted, CAN Agri has encountered visitors both diplomats and private investors from several African countries. The interested parties are currently in negotiation processes and according to Francoise, the company foresees that its units will be established in these countries. “The earliest construction of a CAN-Agri greenhouse will probably start early August 2021, in our close desert neighboring country, Namibia.
This year, CAN-Agri has worked closely with a major retailer in the development of an additional market to amplify the supply and demand of its lettuce produce. Francois adds, “We have grown the sales of private markets to the extent that we are currently at full capacity. Our long shelf life, no-wash technique, and clean, great quality produce have been openly accepted by all of our clients, the demand keeps growing daily.”
Hybrid benefits
According to Francois, CAN-Agri’s patented technology allows providing an unmatched scalable, commercially viable farming solution that is grounded in both scientific research and credible data. The company has developed an innovative hybrid farming system. In this way, they can share the knowledge and technical support to allow their clients around the world to create a successful farm. “We continue to prove that our system provides better yields through our enhanced methods.”
As of now, the company does not make use of additional lighting. “We have done in-depth studies with regards to the implementation of lighting coupled with the installment and operation of additional lighting, mainly for use in other parts of the world with low solar radiation. Operating in sunny South Africa it is currently unnecessary to implement additional lighting as ample solar radiation is available to the plants,” says Francois.
In terms of cost-efficient production, the company identified common limiting factors and found solutions to the challenges of successful production in hybrid greenhouses. “Our extensive research and development on operation specifics are always ongoing. We have our commercial-scale testing facility CAN-AGRI Greenhouse RSA and continuously produce and record empirical data to support our model.”
For more information:
Francois Duvenage, R&D plant propagationist
CAN-Agri
info@can-agri.com
https://can-agri.com
3 May 2021
Author: Rebekka Boekhout
© HortiDaily.com
Lead photo: Francois Duvenage
VIDEO: Indoor Farming Powered By Robotics And Technology - Plenty
Indoor farming powered by robotics and technology is enabling one California company to grow 'Plenty' of flavorful nutrient-rich and pesticide-free produce
Author: abc10.com
April 6, 2021
How CubicFarms Is Feeding A Changing World With Its Automated Indoor Growing Technology
The global supply chain today is facing significant, costly disruptions. A shipping container crisis has upended the global food trade. Devastating winter weather has impacted the U.S., and ongoing labour shortages within the farming industry show no sign of relenting as border crossings remain shut
April 7, 2021
Mark Shelling, Market One Media
CubicFarms provides sustainable and profitable commercial-scale automated indoor growing systems for local produce and fresh livestock feed. , Image courtesy of Market One Media
Supply chain – CubicFarms Garden – Foodservice – HG cattle
In an already tumultuous year, agriculture is facing supply chain disruptions and unpredictable climate changes
To combat this, CubicFarms offers new automated indoor farming systems that could revolutionize global food supplies
With multiple patents in the ag-tech space, CubicFarms is poised for further expansion
The global supply chain today is facing significant, costly disruptions. A shipping container crisis has upended the global food trade. Devastating winter weather has impacted the U.S., and ongoing labour shortages within the farming industry show no sign of relenting as border crossings remain shut.
The ability to move people and goods across long distances will always be at risk of disruption because the longer the supply chain, the more chances there are for things to go wrong.
The farming industry was already in the midst of a labour crisis even before this year, with fewer and fewer workers available to tend to fields. Now with borders being shut, it's unclear how many foreign workers will be able to return to their jobs, despite some having been issued flight exemptions.
Because of this continued downward trend, Canada is currently projected to lose 123,000 workers within a decade, according to a report done by RBC. That represents a loss of $11 billion in GDP, if the labour gap continues to widen.
Couple this labour shortage with changing weather patterns like the devastating cold snap in Texas, the shipping container crisis, and the ongoing demand for fresh produce, and you’ve got a perfect storm against the food industry.
These stacked variables have revealed just how vulnerable the global food supply chain is. Farmers are now scrambling to find sustainable alternatives to what appears to be a crumbling framework.
"We believe long food supply chains are dangerous. As a technology company in the agriculture business, we’ve seen the challenges with growing outdoors. The solution is in using technology to make locally grown produce more widely accessible, 365 days a year, not just here, but anywhere in the world.”
— Dave Dinesen, CEO, CubicFarm® Systems Corp.
Innovative new agriculture technologies like indoor vertical farming are more attractive to farmers who want the stability and consistency that come from harvesting indoor crops. Innovators in the agriculture space have already anticipated this shift and are now offering ways to safeguard against further threats to cultivation.
The technology is improving rapidly with automated, commercial-scale indoor growing systems that grow fresh produce in a controlled environment. These crops can be harvested with less labour than traditional farming, addressing the need to do more during labour shortages.
By creating the ideal indoor environment onsite, growers use LED lighting, less land, significantly less water, and less energy. In Canada and the U.S., in particular, the ability to grow fresh produce during the winter months allows farmers to expand the growing season to 12-months a year.
Disruptions to the supply chain during the ongoing pandemic have sent food distribution centres searching for more local produce. We can expect that demand to rise as the number of growers using indoor vertical farming systems increases.
A new leader in agricultural automation
For a better look at these automated indoor growing systems, Canadian ag-tech company, CubicFarm® Systems Corp. (TSXV:CUB), offers insights into how this technology is the future of agriculture.
Different from other companies in the ag-tech space, CubicFarms began with the farmers themselves. Jack Benne and his son Leo Benne visited a farm in Puerto Rico after a hurricane when they had an idea for an automated indoor growing system that could grow produce in any weather.
Being the principles behind Bevo Farms, one of the largest propagation greenhouse systems in North America, they put their considerable expertise to work on this important problem.
CubicFarms’ produce is grown onsite in an indoor, controlled environment, for delicious greens harvested at the peak of freshness, bringing food production closer to home.
The automated systems they created are now at the forefront of solving the supply chain woes of countries that must rely on outside suppliers for their fresh produce. The potential for this shift is massive.
A local supply chain would reduce long distance shipping/flights, the indoor controlled environment is pesticide and herbicide-free so there would be fewer shortages due to recall (think of the recent romaine E. coli scares), and there would be less food waste, as produce is harvested at peak freshness instead of days or even weeks in advance.
Under traditional supply chains, there is an expected amount of rot, unnecessary waste of food and profits in each shipment, and it’s a wonder that’s considered tolerable.
The CubicFarm System technology is housed within modules that are 40 ft by 8 ft, standing 9.5 ft tall. The beauty of their structure is that farmers can buy as many modules as they need and place them together, creating indoor fields with the ideal controlled environment year-round.
A patented undulating path is used to move crops throughout the module. Plants are cycled through each module on suspended trays, which periodically pass an artificial LED light source along with regulated CO².
This is different than the typical ‘rack and stack’ vertical farming setups which need more space to allow people through to seed, monitor, and harvest plants. The CubicFarm System brings the plants in a full circle once every 90 minutes.
Each module is custom-built, stainless steel container. Trays move along a patented undulating path.
This allows for harvesting to easily take place at the front of the module, while sensors monitor the plants from the inside. This also prevents leaf burning, sometimes seen in vertical farms when the plants are too close to the light and heat source, or those suffering the ill-effects of their position too high or too low in the rack for the ideal amount of CO² necessary for healthy growth.
The CubicFarm System uses a propagator, which grows seeds into seedlings, and a cultivator that takes crops from seedlings to harvest.
This is all while being provided with the necessary nutrients and using up to 95 per cent less water than traditional farming. This line can replicate the exact growing conditions to yield the perfect leafy greens, herbs, and microgreens every time.
"When you provide the optimal environment every day for a crop, it won't only reward you by growing as fast as possible, but it will also be more delicious and nutritious," Dinesen notes.
Global food distribution giant, Sysco, recently announced on their Sysco Vancouver Facebook page that they’re purchasing fresh produce from growers using the CubicFarm System.
This significant relationship is appealing to anyone looking to get into the supply chain, which can be challenging for smaller farming operations.
A new division of CubicFarms is an expert brokerage called CubicFarms Garden. This expert team provides business consulting services for growers using the CubicFarm System onsite, helping them enter the local supply chain and fostering relationships with food distribution centres.
Farmers have long been at the forefront of technology when it comes to new machinery and systems. “Farmers are the most innovative people we know,” explains Dinesen. “In technology terms, this is the Tractor 2.0. After the invention of the tractor, no one would plow a field without one. With the automated, onsite, and commercial scale of the CubicFarm System, no one would want to grow indoors without us.”
While it might sound complex, farmers who use CubicFarm System will immediately notice its simplicity. When a new unit arrives on site, it's already 90 per cent ready to go, and the remaining set up is assisted by a hands-on customer experience team.
Farmers are trained on how to maximize each module's potential and are given resources for developing new crops. With the recently announced addition of Edoardo De Martin, former Microsoft Vancouver GM, to the executive team as Chief Technology Officer, we can expect the next generation of growing technologies to use more artificial intelligence and robotics to enhance their existing automations and efficiencies.
From fresh food to livestock feed
In January of 2020, the company's success and expertise led to the acquisition of a second farmer-founded innovative company called HydroGreen Inc. Another patented indoor farming system, the HydroGreen Grow System is focused solely on the production of fresh, nutritious livestock feed. Feed that would once be grown across acres of grazing land is now produced in a module that's a fraction of that size.
It is a necessary innovation for ranchers who are facing land and water scarcity issues. Dihl Grohs developed the technology for growing nutritious livestock feed for his ranches in South Dakota, Utah, and Missouri. The concept of low-maintenance feed growing was in direct response to the areas where his cattle had limited precipitation.
Recently published university research confirms greenhouse gas reductions using HydroGreen’s hydroponic fodder system. The university study results came from a HydroGreen Grow System operating in British Columbia, the latest market for the system in CubicFarms’ backyard.
At the EcoDairy in Abbotsford, British Columbia, where they produce milk and use agritourism to educate people about where their food comes from, owner Bill Vanderkooi is using HydroGreen for his dairy cattle.
In a video interview, Vanderkooi talks about incorporating HydroGreen livestock feed into the current mixture and replacing some grain and forage in the cattle diet, measuring against a control group for differences in performance, production, and health. “At the early stage of the trial we’re seeing some positive benefits on performance.” Ongoing research into the nutritional benefits will be combined with land, water, and energy usage as factors for farmers.
The HydroGreen Grow System uses 92 percent less water and less land than traditional farming, so it’s expected that this technology will be widely embraced by the livestock industry in the future.
The fresh livestock feed can be used for a variety of animals, but it’s mainly used for dairy and beef cattle. For those facing labour shortages, the HydroGreen module operates with the push of a button and is self-cleaning. Growing predictable amounts of fresh livestock feed indoors and onsite will allow farmers to reduce the unpredictability that can be costly and dangerous to their animals and livelihoods.
The HydroGreen Grow System’s automated seeder spreads half an inch of small grain seed on the growing surface, growing from seed to feed in six days, with less land, water, labour, and energy.
CEO Dave Dinesen considers the HydroGreen Grow System to be the most automated livestock feed growing technology on the planet.
He explains, "When it comes to animal health and nutrition, the HydroGreen Grow System is giving the most nutritious and delicious livestock feed to these animals. They’re healthier, the feed is more consistent, and ranchers can become more self-sufficient.”
“It’s also automated and scalable because we have the technology to make this possible and profitable,” he adds.
“At the end of the day, we’re a technology company, not a produce or livestock feed company, so we don’t compete with farmers. They become our farmer partners and it’s our job to advance the technologies that support their businesses.”
With a $5 million investment from a top ag-tech investor, Ospraie, and a 100-module sale (their largest yet) to a farm in Surrey, B.C., CubicFarms’ momentum is only growing. It's this momentum that will continue to cultivate new acquisitions, like HydroGreen, and propel the company into an expanding market.
CubicFarms also has an R&D Innovation Centre that is continuously creating new crops and streamlined growing practices to benefit the growers using their technologies, including the CubicFarm System and the HydroGreen Grow System. It's a hopeful progression in a time when there seems to be a new crisis emerging every month. With technology like this positioned to revolutionize global food supply and essentially end hunger, it's one fewer crisis we have to face in 2021.
Learn more about CubicFarms by visiting their website here.
For more information about the CubicFarm System, watch this overview video to see it in action.
Technology Is Key To Feeding The World - Celebrating National Ag Day On March 23: We've Come A Long Way From Plows To Agbots
High-Tech Farm Trends: A Glossary
March 18, 2021
By: Steve Foster
Extension Educator Pershing County, University of Nevada, Reno Extension
High-Tech Farm Trends: A Glossary
Over the years, I have listened to many speakers predict what the future of agriculture will look like. One of the biggest challenges for agriculture is to feed 9.6 billion people by 2050. To do so, food production must increase 70% by 2050.
One way to address these issues and increase the quality and quantity of agricultural production is to use sensing technology to make farms more intelligent and connected through so-called "precision agriculture," also known as “smart farming.”
I came across an article the other day, Five High-Tech Farming Trends, by JoAnn Alumbaugh, that shares British author and Labour Party politician Anthony Crosland’s most cited sentence: “What one generation sees as a luxury, the next sees as a necessity." History has shown this to be true – just look at the use of cell phones, televisions, hand-held devices, and computers. Then look at how living conditions and diets have changed as societies have become more affluent.
Below are technologies related to agricultural and natural manufacturing under four key areas of accelerating change, many of which are already in use today: sensors, food, automation, and engineering.
Sensors
Air & soil sensors: Enable a real-time understanding of current farm, forest or body of water conditions.
Equipment telematics: Allow mechanical devices, such as tractors, to warn mechanics that a failure is likely to occur soon.
Livestock biometrics: Collars with GPS, radio frequency identification systems (RFIDs), and biometrics identify and relay vital information about livestock in real-time. Also, farmers and ranchers are using virtual fencing to control the movement of livestock, similar to invisible fences for pets.
Crop sensors: Instead of prescribing field fertilization before application, high-resolution crop sensors inform application equipment of correct amounts needed. Drones or optical sensors, such as infrared light, identify crop health across the field.
Food
Genetically designed food: The creation of entirely new strains of food animals and plants to better address biological and physiological needs. A departure from genetically modified food, genetically designed food is engineered from the ground up.
In vitro meat: Also known as cultured meat, in vitro meat is muscle tissue grown in a lab and therefore never part of a live animal. These products have already entered the market, including the plant-based hamburgers sold by Burger King.
Automation
Agricultural robots: Also known as “agbots,” these are used to automate agricultural processes, including harvesting, fruit picking, plowing, soil maintenance, weeding, planting, and irrigation, among others.
Precision agriculture: Farming management based on observing and responding to intra-field variations. With satellite imagery and advanced sensors, farmers can optimize returns on crop resources, such as irrigation and fertilizer, while preserving natural resources at ever-larger scales. Further understanding of crop variability, geo-located weather data, and precise sensors should allow improved automated decision-making and complementary planting techniques.
Robotic farm swarms: The combination of dozens or hundreds of agbots with thousands of microscopic sensors that would monitor, predict, cultivate and extract crops from the land with practically no human intervention. Small-scale implementations are already on the horizon.
Variable-rate swath control: Building on existing geo-location technologies such as GPS, future swath control could save on seeds, minerals, fertilizer, and herbicides by reducing overlapping resources. By pre-computing the shape of the field where the resources are to be used, and by understanding the relative productivity of different areas of the field, tractors or “Agbots” can procedurally apply resources at variable rates throughout the field.
Engineering
Closed ecological systems: Ecosystems that do not rely on matter exchange outside the system. Such closed ecosystems would theoretically transform waste products into oxygen, food, and water to support life-forms inhabiting the system. Such systems already exist in small scales, but existing technological limitations prevent them from scaling.
Synthetic biology: Programming biology using standardized parts in the same way computers are programmed using standard libraries today. Includes the broad redefinition and expansion of biotechnology, with the ultimate goals of being able to design, build and remediate engineered biological systems that process information, manipulate chemicals, fabricate materials and structures, produce energy, provide food, and maintain and enhance human health and our environment.
Vertical farming: A natural extension of urban agriculture, vertical farms would cultivate plant or animal life within dedicated or mixed-use skyscrapers in urban settings. Using techniques similar to glass houses, vertical farms could augment natural light using energy-efficient lighting. The advantages are numerous, including year-round crop production, protection from the weather, support for urban food autonomy, and reduced transport costs.
The information revolution ties global and local producers and consumers together in ways not possible just a decade ago. As the speed and capacity of computers continue to increase, the ability to gather and use the information on all aspects of production agriculture will explode. Some of these technological advances have already been developed and are just waiting to become financially viable before they transition from a luxury to a necessity.
Sources:
“15 Emerging Agriculture Technologies That Will Change The World,” Michell Zappa, Policy Horizons Canada.
“Five High-Tech Farming Trends,” JoAnn Alumbaugh.
By: Steve Foster
Extension Educator Pershing County, University of Nevada, Reno Extension
Kosher Certification & Controlled Environment Agriculture
Kosher Certification Evolves With The Continuous Technological Changes in Food Production
February 25, 2021
Kosher Certification Evolves
With The Continuous Technological
Changes In Food Production
Since the OU’s first product certification of Heinz vegetarian baked beans in 1923, the OU’s processes for certification evolved with food production technology. A deep understanding of food production, technology, and science have made it possible to meet our customers where they are. The Controlled Environment Agriculture (CEA) Industry, an industry sector at the leading edge of agriculture has seen tremendous growth recently. It shows promise in the production of bug-free food vegetables which are in high demand by kosher consumers.
As background, most of us are familiar with pigs as not being Kosher as this is expressly forbidden for Kosher consumption in the Torah (bible). However, it is stated many more times that insects are forbidden to be eaten as well. As a result, the Kosher Consumer has to be very careful when preparing fresh produce because of the potential presence of insects such as Thrips and Aphids. This entails the consumer’s washing the produce at home, checking and, if clean (otherwise would have to restart the process) dry before consumption. Needless to say, this can be an arduous task when preparing any meal.
The Unique Nature of the Kosher Vegetable Market
This is where the Kosher Vegetable market is unique because kosher certified produce provides a critical convenience factor (often translating into higher premiums) for the consumer who is careful about not eating insects. Interestingly enough, consumers who do not keep the dietary restrictions of Kosher will nonetheless prefer kosher-certified produce because of the fear/perceived disgust of eating insects. A well-known resort was recently sued for serving lettuce wraps that contained Aphids by non-kosher consumers.
With many farms now going indoors, to allow control of humidity, lighting, and nutrients for the plants, there is a greater potential of being insect-free with the benefits of minimal to no pesticide use. This is in addition to the freshness of the product as many of these farms are more local since they are not bound by outdoor constraints. Some companies can deliver their produce within 24 hours of harvest. Due to this technology, the consumer can now have access to a greater variety of produce that can be insect-free and never has to be washed, a process that reduces the product’s quality.
This does not mean that indoor farms are automatically clean as it has been our experience that there are plenty of farms that have an insect infestation. Also, since many farms want to advertise that they are pesticide-free, this will translate into an Integrated Pest Management that requires the release of beneficial insects to consume the more detrimental ones.
The kosher certification of insect-prone vegetables is carefully supervised and navigated by the OU. Standard OU procedure will require an assessment of the facility. In addition, substantial samples of vegetables or final product are checked for insects prior to granting certification. The dynamic of OU certification of vegetables is undoubtedly highly involved but the OU has created a system of supervision to certify vegetables prone to insect infestation.
Through meeting many demands and developing an excellent working partnership with companies, the OU always strives to provide its certified companies with an unparalleled level of supervision.
Have any questions, comments, or want to explore Kosher Certification?
Please contact Rabbi Daniel Sharratt at: sharrattd@ou.org
Rabbi Daniel Sharratt
Rabbi Sharratt comes to the OU with experience working with many agencies across various industry sectors within the Food & Beverage Industry. Receiving a BS in Mechanical Engineering from the University of Notre Dame with a concentration in Industrial Design and receiving Rabbinic Ordination from Mesivta Torah Vodaath, he has become a valuable asset to the OU. As a Rabbinic Coordinator, he ensures that the Rabbis in the field are able to conduct their inspections, review formulas, manufacturing processes, and acts as the Accounts Executive. He currently specializes in Beverages and Produce (with a keen interest in Controlled Environment Agriculture). Rabbi Sharratt at one point even owned and operated a Kosher Fresh Vegetable company, developing a unique perspective into the Kosher Vegetable market. He is actively involved with ASK OU, where he provides classes for consumers on how to wash and check vegetables at home for kosher consumption. In addition, he works with many companies in Latin America due to his ability to speak Spanish.
This article originally appeared on OUkosher.org
US - SOUTH CAROLINA: VIDEO: Columbia Vertical Farm Uses Technology To Cut Plastic Pollution And Boost Sustainability
With the use of agricultural technology, Vertical Roots farm in West Columbia created a packaging system for its leafy greens that cut down the company’s plastic usage by 30% and extends the shelf life of the lettuce
FEBRUARY 01, 2021
Vertical Roots is the largest hydroponic container farm in the country. They grow and package lettuce varieties and have recently implemented a packaging process that reduces plastic with a resealable film. TRACY GLANTZ TGLANTZ@THESTATE.COM
With the use of agricultural technology, Vertical Roots farm in West Columbia created a packaging system for its leafy greens that cut down the company’s plastic usage by 30% and extends the shelf life of the lettuce.
In 2015, high school friends Andrew Hare and Matt Daniels created the idea for Vertical Roots, now the largest hydroponic container farm in the country. Hare is the general manager of the company and Daniels acts as the chief horticulturist.
The first Vertical Roots opened in Charleston and expanded with its second farm site in West Columbia in 2019. Vertical Roots parent company, AmplifiedAg, manufactures the container farms and farm technology of which Vertical Roots operates.
The farms are part of a growing industry called controlled environmental agriculture (CEA) that uses technology to ramp up nutrient-rich food production year-round.
Hydroponics helps the farm uses 98% less water than traditional farming, according to Hare. Their technology creates an indoor environment to grow lettuce on the East Coast. Most lettuce in the U.S. comes from California and Arizona, where temperatures do not fluctuate much throughout the year, traveling 2,000 miles from farm to table. Vertical Roots offers a solution for local lettuce.
“Our mission is to revolutionize the way communities grow, distribute and consume food,” said Hare. As populations grow, Hare said the ability to produce enough food is a global concern.
VERTICAL ROOTS AGRICULTURAL INNOVATION
As a company committed to sustainability, Vertical Roots had to address its plastic usage and the consumer demand for environmentally friendly products.
“I think everyone can agree that the amount of plastic that’s consumed and used globally is a bit of a problem,” said Hare.
If Vertical Roots were to completely opt-out of using plastics, as much as 40% of the lettuce would be damaged in transportation to the retailers, Hare said. So the company decided to still use plastic containers in order to cut out food waste, but it changed the amount and type of plastic used.
By replacing the conventional “clamshell” plastic lids that you see on a container of lettuce at the grocery store, Vertical Roots cut down more than 30% of plastic usage by creating a resealable film lid. The new packaging comes at no extra cost to the customer and will be cheaper in the long-run for Vertical Roots, according to Hare.
The farm also uses recycled plastic that can also be recycled again after use. Tiny perforations in the film lid of the packaging allows air to leave the lettuce container and extends the product’s freshness, making Vertical Roots lettuce last around 14 days on the shelf.
“We tested respiration and condensation with each lettuce variety, and ultimately found that we could extend the freshness and shelf life of our salad mixes even more,” said Hare.
GROWTH IN THE AGRICULTURAL TECHNOLOGY INDUSTRY
In the first three quarters of 2020, a record $754 million of venture capital was invested in the vertical farming industry, according to PitchBook data. This was a 34% increase from the entire previous year, Bloomberg reported in a January article.
A 2019 report from Global Market Insights showed that the vertical farming market size, or the number of potential customers or unit sales, surpassed $3 billion in 2018 and said it, “will exhibit a massive compound annual growth rate (CAGR) of over 27% from 2019 to 2026.”
In vertical farms, crops are harvested on several vertical layers indoors, where farmers can grow year-round by controlling light, temperature, water, and other factors, according to the U.S. Department of Agriculture.
Vertical agriculture is also seen as a growing industry because it “could help increase food production and expand agricultural operations as the world’s population is projected to exceed 9 billion by 2050,” according to the USDA.
However, some are skeptical about the future of vertical farming for several reasons. The farms use LED light bulbs to grow the crops, which require a lot of energy and money to operate.
Also, the farms mostly produce greens, which are low in calories because they take less water and light. The new farming technology is marketed as a way to combat world hunger, but in poorer countries, low-calorie greens are not as beneficial, according to Bloomberg.
THE FUTURE OF VERTICAL ROOTS
Despite a tough year due to COVID-19, Vertical Roots will open two more indoor, container farms in Georgia and Florida in 2021.
The company lost revenue from foodservice customers like restaurants, schools, and universities during the pandemic, said Hare.
Those food service customers accounted for about half of Vertical Roots’ business, Hare said. Grocery store business stayed steady and even grew during the pandemic. As schools and restaurants are slowly reopening, Vertical Roots is gaining business back.
The West Columbia farm location produces about $1.5 million pounds of produce per year, said Hare. Vertical Roots lettuce is in 1,200 different grocery stores in 11 states, including Lowes Foods stores, Publix, Harris Teeter, and Whole Foods Market chains.
Hare said the company is constantly working on sustainable initiatives, including figuring out a way to reduce light energy consumption by 20-25%, thinking about compostable packaging systems and finding ways to use less water at the farms.
In the future, Vertical Roots hopes to offer a larger variety of produce. The team is experimenting with growing foods like tomatoes, cucumbers, peppers, herbs and mushrooms to see if they could be viable products.
Advice For New Vertical Farmers: Grower Spotlight on Andrew Worrall
Andrew is LettUs Grow’s Farm Manager, he manages two of our sites across Bristol and has brought a wealth of knowledge into the company through his previous experience in indoor farming roles across the UK including at Grow Up, Raynor Foods & RootLabs. In this three part interview, we explore what it’s been like to move from animal husbandry to indoor farming, the lessons he’s learned along the way, what it’s like working at LettUs Grow and his advice for those new to indoor growing.
Last week we spoke about running a farm at LettUs Grow. What excites you about vertical farming?
It’s the future of the industry. Also, the amount of salad that these farms can produce for their local community. We want to be able to eat salad all year round and we import to make that happen. However, just a small farm can easily provide for its local community, very efficiently and all year round. The sustainability element is also exciting: with our salad there’s no food miles, it’s very minimalistic. You could use an electric van or bike to distribute this crop if you wanted to. It’s a step forward in terms of what we need to do to take care of our planet.
What do you think are the biggest downsides to vertical farming?
It’s still a new technology and it can be expensive. The biggest roadblock facing the industry is that we need more people and companies to collaborate together to make sure we can build these farms at a sensible rate, so we can provide farms to anyone. We want to be able to provide farms to people, communities and countries that don’t have a lot of money, so that they can provide affordable fresh produce to local people.
How has vertical farming impacted your life?
Massively! I wanted to find my passion, a job that I loved - that was very important to me. It’s satisfying to be in a position now where I’m very happy to be doing what I do and I look forward to going into work. I was happy to make the move from London to Bristol. I would have moved even further if it meant being able to continue working within this industry.
Image from: LettUs Grow
How do you see vertical farming playing a part in the future?
When indoor farming first came about, it had a reputation of being competition for outdoor farming, which just isn’t the case. There’s so much we can’t grow that outdoor farming can provide, such as cereal crops. I’m glad we’re at a stage where indoor and outdoor farms can start to work together to optimise both methods. With these new relationships, there should be a good increase in the amount of indoor farms you’ll be seeing. What LettUs Grow offers with DROP & GROW™ is an exciting project because that’s a 40ft shipping container which can be placed pretty much anywhere. It’s not that big - it could go in a car park or behind a restaurant, but actually provide quite a lot of salad to that area.
How much of our food should be grown this way?
Good question. If you had asked me a while back I would have just said salad, but now I’ve changed my mind. Indoor farming can have a massive impact on propagation, especially aeroponics, because of how we aerate and nourish our roots. We could start lettuce for greenhouse projects and we can also propagate tomatoes, strawberries and tree whips. Propagating trees in this way could potentially be hugely beneficial and it’s something we want to do more of.
We can also quickly grow large amounts of microgreens, baby leafs, herbs and we can grow fruiting crops like strawberries. We are slowly chipping away and it’s really exciting. I’m waiting to see if I can ever say I’ve grown or propagated every crop that can be grown in these farms!
What do you think are the biggest benefits of vertical farming?
How fast these crops can grow! The turnover can be as short as 5 days from seed, depending on the crop. Also how clean it can be - I’m very dedicated to making sure these farms are built to ensure they are easy to be maintained and clean. The most exciting part is the crop growth rate though - it’s incredible how fast our crop grows from seed to plate. In a very well maintained growing calendar, which Ostara® is great for supporting, you can optimise your beds so that the day you harvest can also be the day you germinate onto that same bed. Your farms can be forever providing salad at very fast rates.
Image from: LettUs Grow
What was the biggest change you encountered during your years indoor farming?
Moving from being a production grower to an R&D grower. It has been a great change! As a production grower I knew what I needed to know about growing the plant safely and getting it onto a plate so it was good for the consumer. Now I’m fully optimising, learning and understanding the plants completely, so that I can help the grower that I used to be. We spend a lot of time on crop recipes to make sure that whoever we sell our farms to can start up very quickly and they won’t have to spend months developing their crops. If they have the customers and clients behind them, they can buy DROP & GROW and start producing salad as soon as it's been commissioned.
What was the biggest change you encountered in the industry?
More and more people are speaking about what’s going on in the industry and getting involved. I get so many messages on LinkedIn with people who want to get into this career. It’s exciting to see that indoor growing is a career people can access now. When I was developing my skills I didn’t know I would end up in indoor farming. There are more opportunities than ever before. For example, our Crop Technician is doing a placement here for 2 years. The aim is that they can gain the skill sets and knowledge they need to then go off and do the same practice in any farm they want.
What advice do you have for people who are looking to start a career in growing?
Reach out to companies who are already out there. You could start off part-time or as an assistant. If you are patient and dedicated then it’s a journey I promise you won’t regret. It takes a lot of work, but the outcome is amazing - you’ll be learning so much about this new technology. You’ll also build great relationships: there are so many amazing people in this industry who are so interesting, with different backgrounds, who are willing to share their knowledge. You can always learn more and other people are a great source of that.
What about for those looking to start a vertical farming business?
Do your homework. There are people out there who you can reach out to and it’s very easy to get information. It’s very easy to get excited about the idea and jump straight into it, because it is exciting and can be very rewarding, but it’s really important to do it step by step. Know how to scale properly, learning the differences between a small and larger farm. Understand how many people you’ll need and the logistics. I’d also advise people to get some practical work experience before you buy. You want to start the company knowing the tricks of the trade.
Image from: LettUs Grow
LettUs Grow Blog: www.lettusgrow.com/blog/advice-for-vertical-farmers
The Mexican Tec Graduates Who Are Using Vertical Farming To Eradicate Hunger
Vertical farms use 90% less water than traditional agriculture and can meet the challenge of feeding more than 9 billion people
Vertical farms use 90% less water than traditional agriculture and can meet the challenge of feeding more than 9 billion people
Por Susan Irais
January 11, 2021
Not all fruit and vegetables can be grown using this technique, but a great variety can. (Photo: Courtesy of Verde Karma Fresh)
Every night, seven million people go to bed hungry in Mexico. It is estimated that the coronavirus pandemic will cause that figure to increase. According to the latest report by the United Nations Food and Agriculture Organization (FAO), 130 million people will be affected by chronic hunger worldwide by the end of 2020.
Unfortunately for Mexico, the traditional agricultural industry uses a lot of resources and wastes a large amount of what it takes from the land.
For example, 34% of total production ends up in landfills due to inefficiencies during processing, storage, and transportation. What’s more, 40 billion liters of water are wasted annually due to poor irrigation.
“Fresh” products travel 300 to 1,000 kilometers and have already lost 45% of their nutritional value by the time they hit the shelves. But there is a complementary option for agriculture: vertical gardens.
Vertical Farming
“Vertical farming –in controlled environments– is a method of growing in vertically stacked layers, optimizing growing conditions and soil-less cultivation techniques, such as hydroponics,” says Leo Lobato Kelly, CEO of Verde Karma Fresh, a vertical farming company from Monterrey, Nuevo León.
The modern concept of vertical farming was proposed in 1999 by Dickson Despommier, Professor of Public and Environmental Health at Columbia University in the United States.
Due to climate change, this method has become a real alternative for countries like Japan, Taiwan, Singapore, South Korea, Saudi Arabia, the Netherlands, Germany, France, the United Kingdom, the United States, Canada, and now, Mexico.
Karma Verde Fresh (KVF) has spent the last five years developing farming systems and growing a variety of vegetables, sprouts, and seedlings in Monterrey, Nuevo León. “This has been achieved through an association with two universities and Tec graduate agronomists, using natural substrates, in this case: tezontle (volcanic rock). This substrate can be washed without contaminating the soil. By substituting mineral products, you allow fields to regenerate themselves, which is highly beneficial to the soil,” says the CEO of Karma Verde Fresh.
Not all fruit and vegetables can be grown using this technique, but a great variety can be (Photo: courtesy of Karma Verde Fresh).
Vertical farming systems use 90% less water and 95% less space than traditional farming and are 100% herbicide and pesticide-free. “Our crops can be adapted to any space, which allows us to be closer to the consumer, reduce our carbon footprint, and promote local purchases that are fresher,” says Leo Lobato.
Vertical farms keep crops fresh for longer, so they don’t lose any nutrients, using state-of-the-art LEDs that are extremely energy efficient. Energy can also be generated from renewable sources and this creates job opportunities.
Traditional Agriculture Plus Vertical Farming
“Vertical farming is another option within the agricultural industry, though it is intended as a way of complementing rather than replacing traditional agriculture,” adds Tagino Lobato from KVF.
Not all fruit and vegetables can be grown using this technique, but a great variety can be, “enough to have a balanced diet,” according to Leo Lobato.
For example, KVF produces lettuce, microgreens (mustard), Ballerina lettuce, Alexandria lettuce, peas, beetroot, large-eared lettuce, radish, Italian lettuce, and sunflowers, as well as others such as astro arugula, rocket arugula, spinach, coriander, chard, strawberries, and tomato seedlings.
Vertical farms are very beneficial. For example, they use 90% less water than traditional agriculture and they can be built anywhere, which means many spaces could be repurposed. (Infographic: Karma Verde Fresh)
This type of initiative hopes to feed the 150 million people who will be living in Mexico by 2050, of whom approximately will be in 80% urban areas, according to FAO estimates.
Karma Verde Fresh saw a great entrepreneurial opportunity in vertical technology. “We need this in all communities because we all need to eat better without damaging the planet. Vertical farming in a controlled environment has many possibilities. We can take it to schools or food bank centers,” says the co-founder of Verde Karma Fresh.
The company wants to make this innovation in agriculture available to everyone, so they are looking to make the technology accessible. For example, “we already have one of these vertical farms in Dr. Adriana Elizondo’s house in the Linda Vista neighborhood of Guadalupe in Monterrey. She’s farming with this prototype from her bedroom,” says Leo.
Karma Verde Fresh has two versions of the growing system: one for crops (KVF-AG6) and one for seedlings (KVF-AG10). (Photo: Karma Verde Fresh)
Mexico, The Land of Opportunity
The Lobato technology has already made deals with 20 international universities to take their equipment and establish laboratories. “By involving universities, we are hoping to find Mexican ingenuity that will produce better technology and create more employment opportunities in all Spanish-speaking countries,” he says.
KVF doesn’t just want to sell the technology but also to lower the costs by using Mexican technology. Sources of financing are being set up for all of the entrepreneurs who wish to take vertical farms to different levels.
The end product from vertical farms promotes local purchases that are more nutritious (Photo: Courtesy)
Derby Vertical Farming Startup Gets £500K Funding to Develop ‘All In One’ Sensor
Derby-based Light Science Technologies delivers lighting, science and research-proven plant monitoring technology and software in partnership with world-leading university research teams
INVESTMENT NEWS / 13 JAN 2021
Derby-based Light Science Technologies delivers lighting, science and research-proven plant monitoring technology and software in partnership with world-leading university research teams. It delivers the right solution across multiple indoor applications such as vertical farming, medicinal plants, and greenhouses. Its full turnkey solution for Controlled Environment Agriculture (CEA) applications for next-generation scalable farming helps customers grow more with less.
Investment to boost agricultural productivity
Light Science Technologies just secured part of the £90M government investment to support the most innovative technology to boost agricultural productivity and set food production systems towards net zero emissions by 2040.
Furthermore, it is one of the 23 feasibility projects that has been awarded up to £500,000 from £4.3M funding that is meant for Science and Technology into Practice feasibility competition, as part of UKRI’s £90 million Transforming Food Production (TFP) program. Innovate UK drives productivity and economic growth by supporting businesses to develop and realize the potential of new ideas. Notably, Innovate UK is part of UK Research and Innovation.
Simon Deacon, CEO of Light Science Technologies added: “This is an especially important boost to our business. To be selected by Innovate UK is confirmation of the urgent need for more sustainable, productive, and cost-effective solutions in farming. Investment in UK technology and innovation in this sector is crucial in achieving a better approach to agricultural production and reducing emissions.”
Innovate UK Executive Chair Dr Ian Campbell said: “There are many innovative projects in our latest feasibility competition showcasing ideas for improving productivity and cutting emissions that range across the whole agricultural sector, from arable, to livestock, to sensor technology and to new biopesticides. Our funding and support for these projects is ongoing.”
Groundbreaking sensor technology
Along with partnership with Nottingham Trent University, the company will lead the project to develop a growing sensor and innovative transmission node for vertical farms over the next six months, which is in synergy with their light and science offering.
The IoT precision data solution for vertical farming will help in boosting 0roductivity and efficiency, thereby reflecting the government’s drive to help the agricultural sector grow economically with less environmental impact.
Light Science Technologies’ ‘all in one’ indoor farm sensor will let farms to monitor and control their environment by measuring key areas such as light, water, air, temperature, humidity, oxygen and soil, thereby ensuring optimal plant productivity and yield. Also, this sensor will form a vital part of its bespoke offering, reducing energy and saving costs using technology and real-time data.
Demand for CEA market!
Of late, there is a growing demand for the Controlled Environment Agricultural (CEA) market, which is growing fast at a CAGR of 21%. The demand is mainly from AgTech CEA farmers looking to install or replace existing indoor farms to achieve a maximum yield on crops for optimum profitability. However, the high startup costs attract investment from stakeholders eyeing the potentially significant ROI opportunity.
Light Science Technologies provides custom-made solution for the CEA market, and works with growers to provide an integrated, cost-effective and low maintenance solution that can be used across different crops to achieve maximum yield. Eventually, it creates the full growing recipe of lighting, nutrients, and the environment.
Notably, Light Science Technologies is focused on becoming a technology-driven trailblazer in vertical farming innovation and technology over the next four years as it eyes to shape up the future of the CEA market.
Japan: Operating Rate of 99% In Large-Scale Automated Farm
Stable production at a large-scale automated vertical farm, with a production capacity of 30,000 heads of lettuce per day, and running at full strength, is an achievement yet to be demonstrated at any other facility worldwide
Spread Reaches High Operating Rate At Techno Farm Keihanna
Spread Co., Ltd. has reached the operating rate of 99% at Techno Farm Keihanna, a large-scale automated vertical farm. This percentage is based on the number of harvested heads compared to the maximum capacity of the farm. Stable production at a large-scale automated vertical farm, with a production capacity of 30,000 heads of lettuce per day, and running at full strength, is an achievement yet to be demonstrated at any other facility worldwide. This will further support Spread’s expansion, as it strives to establish a model for sustainable agriculture.
The challenge of large-scale vertical farming
Stable production at a large-scale is considered one of the toughest challenges in vertical farming. Spread’s Kameoka Plant claims to achieve profitability and an operating rate of 97% within 6 years. Techno Farm Keihanna started operating in November 2018. It has now achieved a stable operating rate of 99% and has delivered a monthly average product weight of over 3 tons since October 2020.
Stable production and environmentally sustainable
Spread’s Technologies are implemented at the Techno Farm Keihanna, which is a high-level synergy of automated cultivation and human operations. Accordingly, Spread succeeded in automating most of the labor-intensive processes, to make the whole process inside the farm more efficient and cost-saving. Next to that, they make use of precise environmental control technology for large spaces Spread’s technology ensures there is little variation in temperature and humidity, even at a large scale. Analysis of the actual cultivation environment allows for stable production and consistent high quality.
Furthermore, the farm has a Techno Farm Cloud implemented. Meaning, a unified IoT-based management system for all farm operations. The visualization of cultivation data has brought efficiency improvements to farm management. Through analysis of the cultivation and post-harvest data, Spread maximizes cultivation efficiency and achieves truly smart agriculture.
The Techno Farm Keihanna
The environmentally sustainable factors used are water recycling technology and LED lights, optimized for vertical farming. Techno Farm Keihanna recycles over 90% of the water used in cultivation, allowing for savings of 16,000 liters/day. (This is equal to more than 10 million 500ml water bottles saved every year). Spread’s unique LED lights allow for a reduction in energy consumption by 30% compared to conventional LED lights. Implemented at both Kameoka Plant and Techno Farm Keihanna.
Sales performance
According to the Spread team, the demand for vertically farmed vegetables among consumers and the foodservice industry has been rising. Spread has been steadily increasing shipment volume since the start of operations at its Techno Farm Keihanna. Together with the utilization of an in-house logistics system, this has helped Spread to expand its presence among major Japanese retailers. At the moment, Spread supplies 3,600 stores across Japan.
Future developments
Using the validated technology of the Techno Farm TM, Spread is pursuing further business opportunities through technological innovation and collaboration with stakeholders, both in
Japan and overseas. Spread aims to provide solutions for the global problems of climate change and food security, and to deliver the SDGs through the creation of a truly sustainable society.
For more information:
Spread Co., Ltd.
www.spread.co.jp/en
Crop One Appoints Craig Ratajczyk New Chief Executive Officer
“I am thrilled to join Crop One and continue building on its existing success, bringing my global expertise and relationships to the company,”
MILLIS, Mass.--(BUSINESS WIRE)--Jan 13, 2021
Crop One, an industry-leader in technology-driven indoor vertical farming, today announced it has appointed Craig Ratajczyk as the company’s chief executive officer, effective immediately. Ratajczyk joins Crop One with extensive leadership experience in the agriculture industry and U.S. Navy. Ratajczyk succeeds Dr. Deane Falcone who has served as interim CEO since March 2020; Falcone will continue in his role as Crop One’s Chief Scientific Officer.
“I am thrilled to join Crop One and continue building on its existing success, bringing my global expertise and relationships to the company,” Ratajczyk said of his new position. “We have many exciting milestones ahead and I look forward to working closely with Crop One’s expert employees, stakeholders, and Board to continue growing our business, team, and a global network of partnerships.”
Ratajczyk’s agriculture career has focused on increasing stakeholder value, developing market opportunities, and building key relationships and alliances in the food, feed, and biofuels industries. His previous careers have taken him around the world, contributing tremendously to his leadership and industry expertise. He also brings global strategic acumen acquired from serving 28 years in the U.S. Navy Intelligence community.
“Craig’s energy and enthusiasm are assets that will help Crop One achieve its operational and strategic goals. The board welcomes him to the team,” said Scott Peters, Crop One Board of Directors.
“During this transformative time for Crop One, it’s important that we have not only an astute business leader at the helm, but also someone that understands the intricacies of the agriculture industry,” said Dr. Deane Falcone, Chief Scientific Officer at Crop One. “Craig brings both of those things to the table and we’re looking forward to executing on his vision for the company.”
Ratajczyk received his degree in International Business from Southern Illinois University, a Master of Business Administration from Thunderbird - American Graduate School of International Management and is an alumnus of the Harvard Business School’s Advanced Management Program (AMP). He is based out of the company’s Millis, Mass. headquarters.
To learn more about Crop One, visit cropone.ag.
About Crop One
Headquartered outside of Boston, Mass., Crop One is a technology-driven indoor vertical farming company on a mission to cultivate a sustainable future to meet global demand for fresh, local food. Through its Plants-First™ approach and industry-leading technology platform, Crop One grows fresh, delicious leafy greens using 95-99% less water than field-grown produce. Because it’s grown in an entirely sealed and controlled indoor environment, growing and harvesting can happen 365 days a year, regardless of the season. Crop One sells its fresh, local produce under the Fresh Box Farms label, available at a variety of retailers across southern New England. The company also has a joint venture with Emirates Flight Catering, a partnership that will result in the construction of the world’s largest vertical farm in Dubai. To learn more about Crop One, visit cropone.ag.
View source version on businesswire.com:https://www.businesswire.com/news/home/20210113005471/en/
CONTACT: Media
Bristol Rice
Inkhouse for Crop One
+1 617-631-0660
KEYWORD: UNITED STATES NORTH AMERICA MASSACHUSETTS
INDUSTRY KEYWORD: FOOD/BEVERAGE AGRICULTURE NATURAL RESOURCES RETAIL SUPERMARKET
SOURCE: Crop One
Copyright Business Wire 2021.
PUB: 01/13/2021 09:30 AM/DISC: 01/13/2021 09:30 AM
Vertical Indoor Farms Make Sense
Nate Storey, founder of a startup in the burgeoning agtech sector, which applies high-tech solutions to agriculture and farming, is convinced that the future of vegetable production is vertical and indoor cultivation, an approach that allows crops to be grown anywhere in the world to supply local markets
Enrique Dans Senior Contributor
Teaching and consulting in the innovation field since 1990
Nate Storey, founder of a startup in the burgeoning agtech sector, which applies high-tech solutions to agriculture and farming, is convinced that the future of vegetable production is vertical and indoor cultivation, an approach that allows crops to be grown anywhere in the world to supply local markets. His company, Plenty, has just demonstrated that about two acres laid out vertically and growing hydroponically, produces more than a conventional farm covering some 720 acres.
The company, which makes intensive use of robots and algorithms for watering and providing nutrients for fruit and vegetables, closed a $140 million funding round in October, bringing total investment to $500 million and reflecting the growing interest in this type of technology. Other companies also in the San Francisco area, such as Iron Ox Robotic Farms, also rely on robotization throughout the process, from planting to plant feeding and harvesting, and report similar yields.
High-density cultivation and control throughout the production cycle reduce the incidence of pests and diseases, along with reduced transportation costs, meaning the main expense is labor (hence the need for robotization), along with the initial installation investment and energy, which is increasingly cheaper and more efficient thanks to the development of solar energy and LED technology for lighting.
Another company, Finland’s iFarm, founded three years ago, , raised $4 million in an initial investment round in August. The company provides technology to about 50 projects in Europe and the Middle East covering a total of 11,000 square meters, and is capable of automating the care of about 120 varieties of plants, with the goal of reaching 500 by 2025 (the firm says it adds 10 new varieties each month).
Others, such as Rise Gardens, which raised $2.6 million in seed capital at the end of May, provide hardware and software kits for home hydroponics, which can be assembled in less than an hour and come in three different sizes, IKEA style, which also has a similar product. Others, such as Germany’s Infarm, offer these facilities to businesses such as stores and restaurants and have also attracted investors’ interest.
And there are many more: Eden Green, Bowery Farming, BrightFarms, Freight Farms, AeroFarms… a fast-growing sector that points to a future for vertical and indoor farming. A completely different model from that of conventional farms (which are also being heavily technologized), and that can be installed in any industrial building or even in containers (or in space, if need be), and that promises a transformation similar to that from growing crops under plastic. Will the vegetables we consume in the future come from this type of innovative farms?
Lead photo: (Brandon Wade/AP Images for Eden Green) ASSOCIATED PRESS
Never Forget The Horizontal In Vertical Farming
Vertical farming is all about how high you can go, how you can repurpose the space you have in ways you never thought possible before
Vertical farming is all about how high you can go, how you can repurpose the space you have in ways you never thought possible before.
But what sometimes gets lost in these conversations about vertical farming is the horizontal. To take advantage of all that high-density mobile grow rack systems like Montel’s GROW&ROLL have to offer, to truly maximize your space and your yield, always remember that it’s just as much about growing out as it is about growing up.
Whether you’re cultivating leafy greens, herbs, mushrooms, or cannabis, both the vertical and horizontal axes must work together to optimize space in grow rooms and reliably produce the healthiest crops month after month, year after year.
WHAT WE ALREADY KNOW ABOUT VERTICAL FARMING
We’ve spoken a lot about how multi-tier vertical farming benefits indoor growers, but it never hurts to go over the basics.
First and foremost, vertical farming capitalizes on the space you have, not the space you wish you had. Growing two, three, four times more plants without an inch of additional space is only limited by your imagination.
Montel’s mobile vertical farming racks can outfit your grow op with ventilation, lighting, and watering systems built right into each mobile carriage—no wasted power or resources, no plants missing out on what they need to thrive. And because of its collapsible design, mobile racking for indoor farms lower the risk of unauthorized handling, chemical contamination, or spreading disease.
HERE’S WHAT YOU MIGHT NOT KNOW ABOUT HORIZONTAL FARMING
We’ll take vertical farming out of the picture for a moment—how does horizontal farming contribute to the goals of high-density mobile racking for indoor grow ops?
Let’s look at rolling benches, another popular mobile racking option for indoor farmers. Traditional rolling benches leave about seven inches between each bench, enough room to slip a hand between to shift one bench open. Sure, that’s lost space, but it isn’t that much, right?
Actually, when the goal is to maximize canopy yield with only the space you have, it absolutely is.
Montel’s mobile benches were designed with special handles that don’t require the gap between benches. The result of this small change? You can fit sixteen Montel benches in the space needed for fourteen traditional benches. That’s two more benches of plants, two more benches of crop, and two more benches of profit.
Even when the conversation in agriculture focuses on the vertical in vertical farming, Montel always remembers the horizontal.
KUWAIT: "Up To 550 kg of Lettuce Per Day Thanks To Faster Growth Cycles"
Instead of traveling 5,000 kilometers between German growing areas and consumers, lettuce from vertical farming company &ever in Kuwait travels less than 100 kilometers
Hamburg-Based Start-Up &ever Makes Big Strides In Kuwait
Instead of traveling 5,000 kilometers between German growing areas and consumers, lettuce from vertical farming company &ever in Kuwait travels less than 100 kilometers. With its first commercial farm in the middle of the Kuwaiti desert, the Hamburg-based company supplies regionally grown leaf lettuce to local restaurants and grocers. These are grown on more than 3,000 m2 of cultivation area and taste like they were picked fresh from the field. "Thanks to faster-growing cycles, we can produce up to 550 kilograms of lettuce per day," Mark Korzilius, founder of &ever, told IT Zoom.de
Hypermodern cultivation technology / Image: &ever
"In the process, our newly developed Dryponics cultivation technology reduces water consumption by 90 percent and fertilizer use by 60 percent when compared to traditional cultivation methods." The company also eliminates the use of crop protection products.
For more information: https://and-ever.com
22 Dec 2020
Hort Innovation To Explore High-Tech Solutions
In a release, Hort Innovation said the use of technology, such as vertical farm systems and hydroponics, in food production and delivery systems have the potential to redefine horticulture by optimising yield, quality, and supply
17th December 2020, Melbourne
Six-month project to assess potential of emerging production technology and its uses in Australian urban landscape
A modular farm in Brisbane using high-tech horticulture.
Hort Innovation has announced it has teamed up with a consortium led by agricultural consultancy RMCG in partnership with University of Technology Sydney (UTS) and global urban agriculture consultancy Agritecture, to assess the potential of emerging production technology and its application in the Australian urban landscape as part of a six-month project.
In a release, Hort Innovation said the use of technology, such as vertical farm systems and hydroponics, in food production and delivery systems have the potential to redefine horticulture by optimising yield, quality, and supply.
“High-technology horticulture is being implemented in urban areas across the globe using vertical farm systems, hydroponics and aquaponic systems and nearly fully automated production as well as rooftop, underground and floating farms,” it said in a statement.
Hort Innovation chief executive Matt Brand said bringing the technology to Australia would help attract capital as well as new investment to the sector with new ideas, approaches and mindsets.
“It gives us the opportunity to grow more from less and to keep demonstrating the good work that Australian growers do, day in day out, providing food to families both here and overseas,” explained Brand.
“Urban also means regional areas and hubs. Growers will use the technology as part of the overall production mix. It’s another production system that will be part of the diversity and variety that is Aussie horticulture.
“High technology horticulture may have the potential to play a significant role in increasing Australia’s horticulture sector value and help achieve Australia’s target of a A$30bn industry by 2030,” he added.
The feasibility study aims to identify opportunities and challenges for high technology horticulture in urban Australia. It will identify a range of high technology systems and assess their suitability to urban Australia by considering four key areas.
This includes how the technology fits within current regulations and planning requirements, farm input and waste, supply chain logistics and social, environmental and economic requirements.
Hort Innovation said the project will include a high-level literature review, modelling of the social, economic and environmental impacts and detailed analysis of how the economics of high technology urban systems compare to traditional farming systems.
The outcomes of the study will identify future priorities for research, development and extension activities and investment into Australian high technology horticulture in urban areas.
The study is being guided by an industry-led reference group including growers and emerging commercial leaders engaged in urban high technology horticulture in Brisbane and Sydney, members of local city councils, and subject-matter experts in protected cropping.
Enjoyed this free article from Produce Plus Magazine and its team of editors? Don't miss out on even more in-depth analysis, plus all the latest news from the fresh produce business. Subscribe now to Produce Plus Magazine.
Autogrow Officially Launches European Office With The Appointment of James Croy
With over 15 years’ experience in the agricultural sector, James is looking forward to introducing cutting-edge technology to one of the largest exporting areas in the world
8 December 2020: Netherlands based James Croy has joined Autogrow to support the growth of their digital solutions, Folium, and FarmRoad, in the region. With over 15 years’ experience in the agricultural sector, James is looking forward to introducing cutting-edge technology to one of the largest exporting areas in the world.
“There’s a tangible shift in the mindset of growers here in Europe who understand the importance of capturing data and how it can be used for improving operations. It’s not just the younger generation but growers of all ages, crops and business sizes,” explains James.
“The way crops are managed today is through visual inspection and judgement based on varying degrees of grower knowledge and experience. Data allows for more advanced analytics and understanding of what is driving physiological responses in the plant.”
One of the unique things about James is he also happens to be a New Zealander.
“I left New Zealand in 2006 and was based in London for a time before moving to the Netherlands in 2009. 11 years and three children later, I am firmly embedded in the culture and the environment of the region and love being in such a historically significant and accessible location.”
“It’s ironic how I moved over 18,000 kilometers away from New Zealand and now find myself working for a New Zealand headquartered company again. It’s also great to be representing such great solutions and a business that invests in products that continuously develop in line with the evolving market.”
James will be the key contact for any customers based in Europe interested in FarmRoad and Folium. To contact James – james.croy@farmroad.io
For more information on Folium Network Sensor - https://autogrow.com/products/folium
For more information on FarmRoad - https://www.farmroad.io
MEDIA QUERIES
Kylie Horomia, Head of Brand & Communications
(e) Kylie.horomia@autogrow.com
(w) www.autogrow.com www.farmroad.io
Sales queries – sales@farmroad.io
About Autogrow
Autogrow leverages the power of technology, data science, and plant biology to provide indoor growers affordable, accessible, and easy-to-use innovation – 24/7, anywhere in the world.
Our hardware, software, and data solutions support growers and resellers in over 40 countries producing over 100 different crop types.
We are the experts in Controlled Environment Agriculture (CEA) and continue to stay ahead of a rapidly evolving landscape.
Autogrow, Building 3, Level 1, 61 Constellation Drive, Mairangi Bay, Auckland, Auckland 0632, New Zealand