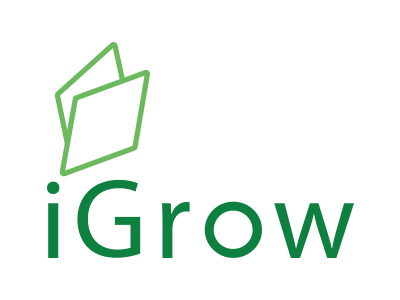
Welcome to iGrow News, Your Source for the World of Indoor Vertical Farming
Light Science Technologies Launches Sustainable nurturGROW LED Lighting Range
Leading UK AgTech company Light Science Technologies (LST) has launched nurturGROW to the market, its new sustainable grow lighting product range, offering an innovative, high-performance and cost-effective solution for indoor farming, covering greenhouses, vertical farming, polytunnels and medicinal plants.
July 21, 2021
90% recyclable and interchangeable design enables growers to simply upgrade and replace
Leading UK AgTech company Light Science Technologies (LST) has launched nurturGROW to the market, its new sustainable grow lighting product range, offering an innovative, high-performance and cost-effective solution for indoor farming, covering greenhouses, vertical farming, polytunnels and medicinal plants.
Created with four core component parts, the patent-pending nurturGROW range is made of high-quality, durable materials to give growers the ideal balance between strength and optimal performance. 90% of the components are recyclable, minimizing the amount of materials needed to drastically cut down on waste and reduce carbon footprint. Thanks to its sustainable, future-proof design, 85% of nurturGROW is also reusable, allowing growers to easily upgrade components, cost-effectively and with no downtime, making nurturGROW easy to maintain. Backed by a 25-year product lifecycle, it ensures indoor farmers maximize the use of every element over a longer lifespan to generate maximum yields and save them a third on future costs.
Built for scale and sustainability
Thanks to its modular structure, the nurturGROW range consists of more than 30 different options with variable lengths of up to 2.78m, making it the longest luminaire on the market. It provides the scale needed to commercialize the right recipe and cut down on waste with both energy and space. With a high efficacy of up to 3.0 umol/J and up to 30-degree variance, growers can choose from 1000s of different light recipes to improve plant performance, from one of the widest ranges of recipes available on the market.
What’s more, nurturGROW enables you to give back to the environment. As proud reforestation partners of One Tree Planted, they plant one tree for every LST product sold, as part of a mutual commitment to champion global reforestation efforts and raise awareness of the importance of ecosystem restoration.
In-house UK scientific and manufacturing expertise
nurturGROW features industry-leading, high performing LED lighting innovation by drawing on its own in-house manufacturing capabilities, assuring growers of nothing
less than high quality and high performance grow lighting. This is supported by a successful tried and tested approach in real environments to prove nurturGROW’s long-lasting lighting technology.
Backed by science, LST works with growers to create the perfect recipe for crop growth. Using light testing equipment and data gathered from LST’s purpose-built laboratory, its in-house team of scientists can help identify the right spectral waveforms and PPFD levels by recreating various environment scenarios in one of its accredited grow chambers.
Grow more, with less
Founded in 2019, LST’s approach from the beginning was to create a bespoke, fully integrated lighting solution that met key criteria for CEA farmers and growers: sustainability, cost-effectiveness, and high performance. Knowing that each growing environment has its own set of unique requirements, nurturGROW gives growers optimum control over their crops with the potential to deliver optimal yield and minimize both CAPEX and OPEX costs.
Craig Price, Operations Director at Light Science Technologies, said: “Being customer-focused by design means that as an experienced LED grow light partner, we understand every variable and can help indoor growers to design a sustainable solution that fits their unique growing parameters.
“This extends to adjusting the light recipe for growers, as nurturGROW will allow you to increase, decrease or change the recipe depending on preference, thanks to an interchangeable luminaire body.
“The unique aspect of our design also means that we have already allowed for future integration of sensor technologies, offering significant added value. By choosing to add in our new sensor technology, which is under development, indoor growers and farmers can look to control their environment in much more granular detail. This will enable them to reduce any sub-optimal performances, whether that be in any environmental controls or from the light itself.”
LettUs Grow, GrowStack, Digital Farming & Farm Urban Collaborating To Deliver Four Social-Impact Vertical Farming Projects In Wales
Vertical farming, a way of growing crops indoors on stacked shelves, can be beneficial for people, plants and the planet. It allows growers to provide fresh, healthy produce to their local area 365 days of the year and can help to supplement outdoor growing
Source: LettUs Grow
07/12/21
Four major UK vertical farming companies, LettUs Grow, Digital Farming, Farm Urban and GrowStack, are collaborating to bring the benefits of controlled environment agriculture (CEA) to Welsh communities. This is one of the widest collaborations between leading CEA tech providers in the UK to date, with a focus on delivering vertical farms across different locations in Wales as part of a social impact and community-focused project called Crop Cycle.
Vertical farming, a way of growing crops indoors on stacked shelves, can be beneficial for people, plants and the planet. It allows growers to provide fresh, healthy produce to their local area 365 days of the year and can help to supplement outdoor growing. It diversifies our supply chains and boosts local food security. It also has a long stream of environmental benefits, such as using fewer resources including land or water, removing the use of chemical pesticides and reducing the need to transport food across seas. However, a common criticism of vertical farming is that it’s not always accessible or affordable to areas under-served by our food networks.
Crop Cycle is looking to bring the benefits of vertical farming directly to communities that could benefit most and is being funded by the Welsh Government through the Foundational Economy Challenge Fund. The project is being led by Social Farms and Gardens, supported by Welsh Government's NutriWales CEA Special Interest Group and BIC Innovation.
The project enables multiple different CEA systems to be tailored to fit different community settings, whilst also allowing them to be assessed in coordination across the pilot sites. This approach is unique, facilitating the testing of new socially focused business models, the engagement of the local communities and businesses with CEA and the development of new technical solutions. LettUs Grow, Digital Farming, GrowStack and Farm Urban are working together to share their specialisms and apply different technologies to where they are best suited within four sites in Wales, two of which are in the Valleys.
This project will introduce year-round food growing right into the heart of Welsh communities, where they’ll be connected to the particular dynamics of the local area. Activities will test new community-based engagement models, focusing on social well-being, local entrepreneurship and environmental impact. In this way, the project will be bringing together community, businesses and local public sector organisations.
Gary Mitchell, the Wales Manager for Social Farms and Gardens who is leading the project team stated, "we are excited to be running the pilot project across a diverse set of sites to gain insight and further knowledge into how new agricultural systems can successfully support communities in delivering local, fresh and nutritious foods as well as important social benefits in a sustainable manner."
Welcome To Our Woods
Welcome To Our Woods in Treherbert is nestled in the heart of the Rhondda Valleys, where LettUs Grow and GrowStack will be delivering an aeroponic and hydroponic vertical container farm. This proactive community group has been actively engaging with its communities through partnerships with the Green Valleys CIC and their joint ‘Skyline’ project. This partnership has led to several funding investments in the region, exploring community ownership of land and the benefits of allowing the community to utilise their surrounding natural green assets.
Chris Nelson, director of GrowStack said: “Growstack are delighted to be working alongside LettUs Grow and Digital Farming as part of this important social enterprise. It is always fantastic to be part of a project that champions vertical farming and really shares in the values of what this approach to food production can offer, including the benefits to the local community. Working in partnership with innovative farming companies is always a pleasure, as together we can combine our expertise to deliver outstanding results.”
Ian Thomas from Welcome To Our Woods said, “We are excited to be bringing such an innovative and progressive project to our local high street. We have already been engaging with the Upper Rhondda community to explore the projects that actively use our woodlands for the benefit of those they surround, and initiatives such as this help give local people an idea of what can be achieved."
Cultivate
Two linked sites will be in Newtown, one within the established community growing space attached to the Newtown Campus of the Neath Port Talbot College Group, and one within a new town centre ‘Circular Economy’ shop. The two CEA systems, provided by LettUs Grow and Digital Farming, are being integrated into an active college site and managed by a community group, with a cafe and kitchen, shop, deli and veg box scheme in place. The site is supported by Cultivate, which is a membership cooperative linking food and community. Cultivate aims to address many of the issues associated with the modern food system, and focus on creating sustainable local food solutions.
Charlie Guy, co-founder and CEO of LettUs Grow said this about the collaborations: “LettUs Grow is delighted to be working alongside these leaders of the UK vertical farming ecosystem and inspiring community projects. The UN Sustainable Development Goals (SDGs) were implemented the same year as our foundation and have never been far from our minds. SDG 17 ‘Partnerships for the Goals’ rings especially true for us. We believe a brighter future can only be realised with inclusive partnerships and strong cooperation, built on shared values and a vision which places people and the planet at its epicentre.”
Greenmeadow Community Farm
Greenmeadow Community Farm in Cwmbran is being delivered by Digital Farming. It is one of only two ‘city farms’ in Wales and one which connects people to food and farming in a very public way. It is owned and operated by Torfaen County Borough Council, bringing with it a high-level partnership. The farm already welcomes thousands of visitors through its gates and connects locally through a number of schools and college partnerships – making it an ideal ‘showcase’ location for this pilot. Digital Farming were commissioned to deliver the Digital Farm in a container for pilot production of high nutrition greens and herbs. The system uses V-Farm patented growing systems linked to Digital Farming’s smart digital management system powered by solar PV.
Dr Gareth Jones, CEO of Digital Farming, said, “we were delighted to be awarded this project and have been enjoying working with the team at Social Farms and Gardens and Greenmeadow to bring together a new concept to explore the business of growing locally using controlled environment agriculture to enhance nutrition for communities.”
Xplore! Science Discovery Centre
The final site is in Xplore! Science Discovery Centre, situated in the centre of Wrexham: a brand new science centre that will support the promotion of urban agriculture in north Wales’ largest urban area. The vertical farming system is provided by Farm Urban. It will reach out to all generations, showcasing new technology and modern horticulture methods, blended with traditional growing experience. Xplore! welcomes public visitors, school groups and provides a range of educational workshops.
Paul Myers, Managing Director of Farm Urban said: “We are thrilled to be able to offer our hydroponic Edible Wall systems, Produce Pod aquaponic systems and learning programmes across all four sites involved in the Crop Cycle project. The team at Farm Urban have loved working alongside the four community organisations, they are all so enthusiastic and engaged which is exactly what we need for the social and environmental benefits of CEA to be shared across the UK and beyond. It has been a privilege to work alongside industry leaders GrowStack, LettUs Grow and Digital Farming learning more about their systems and approach. One of the many highlights of this project has been the openness and willingness to share and collaborate between all partners which is so important to drive the industry forward.”
To follow the progress of the community grow sites, you can follow Crop Cycle on social media, and technology providers LettUs Grow, Digital Farming, GrowStack and Farm Urban.
Tags: Indoor & Vertical Farming, Processing & Supply Chain | AgTech
Bucolic Kailash, An Agritech Startup, Brings “Computerized Farms” From The Future!
At the futuristic and smart agritech start-up “Bucolic Kailash”, a mission is becoming more real every day; the vision that soon in the very near future, starting and running farms profitably, will be as easy as downloading an app
July 6, 2021
At the futuristic and smart agritech start-up “Bucolic Kailash”, a mission is becoming more real every day; the vision that soon in the very near future, starting and running farms profitably, will be as easy as downloading an app.
Bucolic Kailash researches, manufactures and markets user-friendly life-growing computers. These computers are meant to enable economic and nutritional autonomy for its users. For example, one of the patented life-growing computers at Bucolic testing labs grows as much as Rs. 25 lakh worth of healthy produce annually in just 100 sq ft space with operational expenses of under Rs. 50,000/month for the user. Systems like these can be started with as low as 3 sq ft of space and scaled up with time.
Bucolic Kailash’s Vertical Garden and Vertical Farm System series are made to deliver super intensive and sustainable cultivation that is 100% organic, without soil and achieves more than 90% of water and energy saving. The smart agritech company has developed and acquired multiple patents on products and technologies that have shown promising results in the scope of personal, organized, and organic aquaponics farms. Their hydroponics computers grow up to 84 plants, vegetables, and salads in 1 sq ft. Their mushroom farming computers grow 50 Kgs of mushrooms in 3 sq ft every 45 days. Their fish-farming computer designs yield up to 800 Kgs of shrimps in just 10 sq mt every 150 days. All of this is achieved with IT, IoT and their custom developed life-growing AI. The Systems are engineered by closely working with its early customers and focusing on ease of use, AI & IoT powered automation and distribution. Engineering, Manufacturing, and IT has been the most guiding product shaper for the company’s early success.
Bucolic Kailash has unlocked a huge market for vertical farming, fish farming and hydroponic personal gardens.Their use of technological intervention empowers people to cultivate and harvest every day and in the comfort of their own homes through most efficient and effective ways. The company’s new offering under Vertical Garden system series ‘Tree of Wisdom – Eleganté’ is by far the most groundbreaking vertical hydroponics system the world has ever seen before. The product complies with ISO 9001:2015 for best in grade Quality Management and has been tested to meet the required hydroponics system parameter controls, as well as the state-of-art features. Tree of Wisdom - Eleganté has been doing well since its launch on 11th May 2021 at amazon.in.
The Company was founded by Mr. Utkarsh Sinha in March 2020 and now the company is a community of 18 carefully selected and nurtured members. During our interview with the founder, we found him very engaged and excited about the road ahead. Utkarsh graduated in MCIT-Computing from The University of Melbourne and B. Tech from MIT, Manipal. According to him, having worked with Godrej's R&D, Honeywell Aero HTS, Fagerhult OR Tech teams in India and Australia, helped him manage the company’s departments, processes, and make shipments possible from concept-to-product, even during the pandemic. The company runs its fully functional aquaponic devices manufacturing facility in Manipal on lean manufacturing and quality control principles.
On further talking with the founder, we found that the company’s mission with its life-growing computers is to ultimately enable community empowerment and economic development. The company believes that such life-changing science and technology should be available as user-friendly products. In the founder’s words, “It was a contrasting journey that I took back home to India in 2019 while having employment opportunities from companies in Australia that made me reflect upon my priorities and self-actualization needs. I wish to make communities exchange value through healthy food and money that can make coexistence wholesome.” We believe that Bucolic Kailash is a futuristic company that understands the needs of today's communities and a fast-changing world. They develop and market environmentally friendly agritech computers. The company has raised partial seed-funding after a year of setting up its manufacturing factory and distribution channels and they plan to expand their life-growing computers reach to a wider niche and the tap global market in the next 6 months.
Visit www.bucolic.ltd for more inspiration and information
A Primer On Vertical Farming As The Industry Gains Steam
Nearly $1.9 billion of global venture capital was invested in indoor farming in 2020, nearly tripling investment in 2019. And just this week, New York-based vertical farming startup Bowery Farming raised $300 million in its latest funding round, valuing the company at $2.3 billion.
Rich Alternman
May 28, 2021
The modern concept of vertical farming was put forth in 1999 by Columbia University microbiologist Dickson Despommier, who along with his students, came up with a design of a skyscraper farm that could feed 50,000 people.
Since then, vertical farming has become a multi-billion-dollar industry. And it’s growing rapidly.
According to PitchBook data, nearly $1.9 billion of global venture capital was invested in indoor farming in 2020, nearly tripling investment in 2019. And just this week, New York-based vertical farming startup Bowery Farming raised $300 million in its latest funding round, valuing the company at $2.3 billion.
Vertical farming growth may be accelerating at the ideal time, as concerns about population growth and climate change push the food industry to innovate to meet tomorrow’s challenges.
By 2050, around 68% of the world population is expected to live in urban areas, and this growth will lead to an increased demand for food. The use of vertical farming could play a role in preparing for such a challenge. At the same time, it could help restore forests depleted by commercialized agriculture and curb planet-warming emissions caused by farming and transportation. Agriculture and forestry alone account for about a quarter of the world’s greenhouse gases.
What is it?
Vertical farming is the practice of growing crops in vertically stacked layers as opposed to a single level, like a field or greenhouse.
Through the artificial control of temperature, light, humidity, and gases, food can be produced indoors in a way that optimizes plant growth and soilless farming techniques such as hydroponics, aquaponics, and aeroponics. The benefits of which are reliable, environmentally friendly, year-round crop production, significantly reduced water usage (by some estimates up to 95% less), efficient land use, and less exposure to chemicals and disease.
Among its downsides, vertical farms are costly to set up and operate and are too dependent on technologies that have yet to reach full maturity. Further, with its heavy reliance on electricity for lighting and climate control, it uses more energy than traditional farming methods and contributes to greenhouse gas emissions.
With that, the sector continues to innovate. And with vertical farming merely in its infancy, it’s reasonable to expect big things in the coming decades.
Investors certainly think so.
In fact, the global vertical farming market is projected to reach $12.77 billion by 2026, growing at a CAGR of 24.6%, according to Allied Market Research.
Some recent examples of vertical farming going mainstream include:
Newark, N.J.-based AeroFarms planning to double its product offering at Whole Foods and, for Amazon Fresh, expanding from one to five distribution centers, increasing availability throughout the New York metropolitan area.
Albertsons Cos. rolling out indoor-farmed produce from Bowery Farming to 275 Acme and Safeway stores in the Northeast and Mid-Atlantic.
The Kroger Co. rolling out produce from vertical farm 80 Acres Farms to more than 300 stores in Ohio, Indiana and Kentucky.
Giant Eagle introducing more packaged greens products from vertical- and robotic-farming specialist Fifth Season to supermarkets in Pennsylvania and Ohio.
Cost barriers
While investors and environmentalists alike are excited by the prospects of vertical farms, the cost barriers are significant, around 20% to 30% higher than traditional farms.
With that, investors may not be able to live up to the hype they’ve created around the industry, and see their bubble burst before they have a chance to prove themselves, said IDTechEx analyst Michael Dent, in a Bloomberg News article. “If people are expecting world-changing progress and they don’t see it in the first two or three years — and what they see is high-quality salad — there’s a chance they might pull out their investment on the field and move on to the next thing.”
Vertical Farming Startup Oishii Raises $50m In Series A Funding
“We aim to be the largest strawberry producer in the world, and this capital allows us to bring the best-tasting, healthiest berry to everyone.”
By Sian Yates
03/11/2021
Oishii, a vertical farming startup based in New Jersey, has raised $50 million during a Series A funding round led by Sparx Group’s Mirai Creation Fund II.
The funds will enable Oishii to open vertical strawberry farms in new markets, expand its flagship farm outside of Manhattan, and accelerate its investment in R&D.
“Our mission is to change the way we grow food. We set out to deliver exceptionally delicious and sustainable produce,” said Oishii CEO Hiroki Koga. “We started with the strawberry – a fruit that routinely tops the dirty dozen of most pesticide-riddled crops – as it has long been considered the ‘holy grail’ of vertical farming.”
“We aim to be the largest strawberry producer in the world, and this capital allows us to bring the best-tasting, healthiest berry to everyone. From there, we’ll quickly expand into new fruits and produce,” he added.
Oishii is already known for its innovative farming techniques that have enabled the company to “perfect the strawberry,” while its proprietary and first-of-its-kind pollination method is conducted naturally with bees.
The company’s vertical farms feature zero pesticides and produce ripe fruit all year round, using less water and land than traditional agricultural methods.
“Oishii is the farm of the future,” said Sparx Group president and Group CEO Shuhei Abe. “The cultivation and pollination techniques the company has developed set them well apart from the industry, positioning Oishii to quickly revolutionise agriculture as we know it.”
The company has raised a total of $55 million since its founding in 2016.
VIDEO: Device Communicates With Plants Using Electric Signals
Researchers envision a future where farmers can take preventive steps to protect their crops, using the plant ‘communication’ device they have developed
24 March 2021
Researchers envision a future where farmers can take preventive steps to protect their crops, using the plant ‘communication’ device they have developed.
A team of scientists led by Nanyang Technological University, Singapore (NTU Singapore) has developed a device that can deliver electrical signals to and from plants, opening the door to new technologies that make use of plants.
The NTU team developed their plant ‘communication’ device by attaching a conformable electrode (a piece of conductive material) on the surface of a Venus flytrap plant using a soft and sticky adhesive known as hydrogel.
Pick up and transmit electric signals
With the electrode attached to the surface of the flytrap, researchers can achieve two things: pick up electrical signals to monitor how the plant responds to its environment, and transmit electrical signals to the plant, to cause it to close its leaves.
According to the scientists, the ability to measure the electrical signals of plants could create opportunities for a range of useful applications, such as plant-based robots that can help to pick up fragile objects or to help enhance food security by detecting diseases in crops early.
Text continues underneath the video
Monitor crop health
The research team envisions a future where farmers can take preventive steps to protect their crops, using the plant ‘communication’ device they have developed.
Lead author of the study, Chen Xiaodong, President’s Chair Professor in Materials Science and Engineering at NTU Singapore said: “Climate change is threatening food security around the world. By monitoring the plants’ electrical signals, we may be able to detect possible distress signals and abnormalities. When used for agriculture purpose, farmers may find out when a disease is in progress, even before full‑blown symptoms appear on the crops, such as yellowed leaves. This may provide us the opportunity to act quickly to maximise crop yield for the population.”
Smartphone
The device has a diameter of 3 mm and is harmless to the plant. The researchers say it does not affect the plant’s ability to perform photosynthesis while successfully detecting electrical signals from the plant. Using a smartphone to transmit electric pulses to the device at a specific frequency, the team elicited the Venus flytrap to close its leaves on demand, in 1.3 seconds.
The researchers have also attached the Venus flytrap to a robotic arm and, through the smartphone and the ‘communication’ device, stimulated its leaf to close and pick up a piece of wire half a millimetre in diameter.
Is All White Light the Same - Webinar
In this free webinar, we break down the differences among different types of white horticultural lighting. We will present the results of comparative plant trials we conducted using a variety of our own and other LED providers’ luminaires
More and more LEDs are going from purple to white. Is there any difference among the countless white LED light options on the market, in addition to fluorescent? Cool white, warm white, full-spectrum white, fluorescent, white with UV and far red, etc. How to evaluate these choices?
In this free webinar, we break down the differences among different types of white horticultural lighting. We will present the results of comparative plant trials we conducted using a variety of our own and other LED providers’ luminaires.
Spectra appearing white to human eyes contain a variety of spectrum colors, including green. Humans can distinguish them in terms of their temperature (e.g. warm white and cool white) and CRI (color rendering index) which determines how realistic objects appear under them.
Plants however can have dramatically different reactions to light that appear nearly the same to us. The example here shows the difference in biomass accumulation from three light sources that look exactly the same!
This webinar is aimed at growers and researchers trying to understand which kind of light to illuminate their growth chambers, indoor farms, and greenhouse compartments with.
Register for the webinar here.
Contact Valoya sales here - sales@valoya.com
About Valoya
Valoya is a provider of high-end, energy-efficient LED grow lights for use in crop science, vertical farming, and medicinal plant cultivation. Valoya LED grow lights have been developed using Valoya's proprietary LED technology and extensive plant photobiology research. Valoya's customer base includes numerous vertical farms, greenhouses, and research institutions all over the world (including 8 out of 10 world’s largest agricultural companies).
Additional information:
Valoya Ltd, Finland
Tel: +358 10 2350300
Email: sales@valoya.com
Web: www.valoya.com
Facebook: https://www.facebook.com/valoyafi/
Twitter: https://twitter.com/valoya
Hydroponics Greenhouse Provides Hands-On Learning At Hudson High School
A $20,000 grant was given by The Kiwanis Club of Hudson to support the project, and this money was used to purchase greenhouse equipment.
Yeji Kim
Special to the Hudson Hub-Times
A Jan. 15 tour led by HHS AP Environmental Science teacher Matthew Kearns offered members of The Kiwanis Club of Hudson insight into the hydroponic greenhouse. The club donated a $20,000 grant to help fund the project. Submitted Photo
Project-based learning is a learning model where students work together to engage in real-world questions and problems, and the Hudson High School hydroponics greenhouse centres around this approach to education.
The hydroponics greenhouse started roughly two years ago, and Phillip Herman, Superintendent of the Hudson City School District, and Christina Wooley, HCSD Curriculum Coordinator, are credited with most of the original idea.
Herman first learned about hydroponics gardening and greenhouses from a community member and thought there may be a way to better utilize the HHS greenhouse space to create learning opportunities for students. He began by discussing the idea with teachers, visiting an operating hydroponics greenhouse and exploring areas of the curriculum that could be enhanced.
The first year consisted largely of planning, strategizing and raising money, and this past year was when equipment started to come in and crops began to grow.
A hydroponics greenhouse differs from a traditional greenhouse in that no soil is required. Instead, the plants draw up nutrient-rich water. Less water is used since the water is recycled, and because of the absence of soil, hydroponics greenhouses take up less space — the plants can be stacked vertically. The HHS hydroponics greenhouse also includes a monitoring computer system that measures what is currently in the water and what will be needed.
A $20,000 grant was given by The Kiwanis Club of Hudson to support the project, and this money was used to purchase greenhouse equipment.
CropKing, an Ohio-based hydroponics equipment company, was the supplier for the equipment, seeds and fertilizer, and the firm also aided in setting up the equipment and trained those involved with the greenhouse.
Two other grants, an ADAR grant and a grant from the Hudson Parent-Teacher Organization supplemented the Kiwanis grant money. The greenhouse itself is located off of HHS biology classes and has been there before the hydroponics greenhouse was started.
Students are faced with real-world questions, such as how to sustain crops in regions without sufficient access to water, ways to use the land effectively and properly, impacts on the environment and how to grow sustainably and locally.
Science teacher Matthew Kearns said students have been seeing the benefit of this project, which includes those in the AP Environmental Science class he teaches, special education students who work with Intervention Specialist Kristin Stonestreet and biology classes taught by Ron Wright. Students visit at least once a week to monitor the crops.
Currently, the greenhouse is growing its first round of crops, which includes lettuce, tomatoes and cucumbers.
Stonestreet and Kearns are considering adding cilantro, basil and peppers as well. The diversification would enhance the project-based learning aspect, as students will need to work together to figure out how much additional lighting and heat every crop needs.
The long term goal is to get involved with the community; through connecting with the business department and forming a club, students plan to sell produce from the greenhouse at the Hudson Farmers Market in the summertime and sell to HCSD faculty and staff when school is in session, engaging aspects of science, business and team-work. Several potential products for sale in the future include a salsa kit, tomato sauce and fresh herbs.
Herman notes how this greenhouse works to enhance classroom activity and curriculum.
“Over recent years, we have continued to learn more about and explore opportunities for project-based learning. Project-based learning enables students to learn course content and develop other essential success skills by beginning with a challenging problem or question and conducting a sustained inquiry to explore solutions to the problem and answers to their questions. Together, Christina Wooley, Mr Kearns and Mrs Stonestreet dug in and worked collaboratively to do the hard work to bring an idea to implementation.”
BRITISH COLUMBIA: Agri-Tech To Anchor New Okanagan Falls Industrial Park
“This really is the future of agriculture,” said Monique Janower, senior marketing and strategy director for Avery Group.
JOE FRIES
A vertical farming operation similar to this is planned for an Okanagan Falls industrial park.
USDA/Special to The Herald
Vertical farming could be what finally helps a light-industrial park take root in Okanagan Falls.
Avery Group purchased the 110-acre former Weyerhaeuser mill site for $3.2 million in July 2020, and this week received tentative rezoning approval from the board of the Regional District of Okanagan-Similkameen.
The application, which would down-zone the site from its current heavy-industrial rating, is now set for a public hearing March 18.
At the heart of the redevelopment plan is a 30-acre lot on which Avery Group wants to build a vertical farming facility, in which rows of crops would be stacked on top of one another in a warehouse-like environment.
“This really is the future of agriculture,” said Monique Janower, senior marketing and strategy director for Avery Group.
Potential crops include lettuce and leafy greens that vertical farming operations around the world had parlayed into a $2-billion industry as of 2018, according to Forbes Business Insights, which projects the market will expand to $12 billion by 2026.
The rest of the land at 1655 Maple St. would then be subdivided into lots ranging from 2.5 to 15 acres for a variety of uses, ranging from storage and food packaging to beverage processing and light manufacturing.
Janower, who cautioned there are still many regulatory hurdles to be cleared, said there has nonetheless been “tremendous interest” from potential buyers due to the relative rarity of new industrial land and the site’s central proximity to Alberta and the Lower Mainland.
Avery Group is owned by Garry Peters, who has deep ties to the area, according to Janower, so the company appreciates the site’s context within the community.
“We understand we’re not just creating bricks and mortar,” said Janower. “It’s very much tied to regional economic development of the area.”
The rezoning application already has the support of RDOS staff and a key community group.
“Rezoning of the property could potentially bring an influx of new and growing industrial businesses to Okanagan Falls,” Matt Taylor, president of the Okanagan Falls Community Association, wrote in a letter to the RDOS board.
“This in turn could lead to additional employment, a need for more residences and even more tourism. These factors would all contribute to and support the community.”
Since the 2007 closure of Weyerhaeuser, the site has been the subject of multiple development proposals, including an industrial park, residential development and, most recently, a cannabis production facility.
If rezoning is granted, Avery Group will then apply for the RDOS development permit required for the vertical farming operation. At the same time, it will apply to the B.C. government for subdivision. If all goes well, the company expects the park to be open for business in 2022.
Little Leaf Farms Raises $90M to Grow Its Greenhouse Network
Massachusetts-based Little Leaf Farms has raised $90 million in a debt and equity financing round to expand its network of hydroponic greenhouses on the East Coast. The round was led by Equilibrium Capital as well as founding investors Bill Helman and Pilot House Associates. Bank of America also participated.
by Jennifer Marston
Image from: Little Leaf Farms
Massachusetts-based Little Leaf Farms has raised $90 million in a debt and equity financing round to expand its network of hydroponic greenhouses on the East Coast. The round was led by Equilibrium Capital as well as founding investors Bill Helman and Pilot House Associates. Bank of America also participated.
Little Leaf Farms says the capital is “earmarked” to build new greenhouse sites along the East Coast, where its lettuce is currently available in about 2,500 stores.
The company already operates one 10-acre greenhouse in Devins, Massachusetts. Its facility grows leafy greens using hydroponics and a mixture of sunlight supplemented by LED-powered grow lights. Rainwater captured from the facility’s roof provides most of the water used on the farm.
According to a press release, Little Leaf Farms has doubled its retail sales to $38 million since 2019. And last year, the company bought180 acres of land in Pennsylvania on which to build an additional facility. Still another greenhouse, slated for North Carolina, will serve the Southeast region of the U.S.
Little Leaf Farms joins the likes of Revol Greens, Gotham Greens, AppHarvest, and others in bringing local(ish) greens to a greater percentage of the population. These facilities generally pack and ship their greens on the day of or day after harvesting, and only supply retailers within a certain radius. Little Leaf Farms, for example, currently servers only parts of Massachusetts, Pennsylvania, New York, and New Jersey.
The list of regions the company serves will no doubt lengthen as the company builds up its greenhouse network in the coming months.
Agritech: Precision Farming With AI, IoT and 5G
For a company that grows and delivers vegetables, Boomgrow Productions Sdn Bhd’s office is nothing like a farm, or even a vertical farm. Where farms are bedecked with wheelbarrows, spades and hoes, Boomgrow’s floor plan is akin to a co-working space with a communal island table, several cubicles, comfortable armchairs, a cosy hanging rattan chair and a glass-walled conference room in the middle
Image from: Photo by Mohd Izwan Mohd Nazam/The Edge
For a company that grows and delivers vegetables, Boomgrow Productions Sdn Bhd’s office is nothing like a farm, or even a vertical farm.
Where farms are bedecked with wheelbarrows, spades and hoes, Boomgrow’s floor plan is akin to a co-working space with a communal island table, several cubicles, comfortable armchairs, a cosy hanging rattan chair and a glass-walled conference room in the middle.
At a corner, propped up along a walkway leading to a rectangular chamber fitted with grow lights, are rows of support stilts with hydroponic planters developed in-house and an agricultural technologist perched on a chair, perusing data. “This is where some of the R&D work happens,” says Jay Dasen, co-founder of the agritech start-up.
But there is a larger farm where most of the work behind this high-tech initiative is executed. Located a stone’s throw from the city centre in Ampang is a 40ft repurposed shipping container outfitted with perception technologies and artificial intelligence (AI) capabilities that mimic the ideal environment to produce more than 50,000kg of vegetables a year.
Stacked in vertical layers, Boomgrow’s vegetables are grown under artificial lights with Internet of Things (IoT) sensors to detect everything from leaf discolouration to nitrate composition. This is coupled with AI and machine learning algorithms.
Boomgrow is the country’s first 5G-connected vertical farm. With the low latency and larger bandwidth technology, the start-up is able to monitor production in real time as well as maintain key parameters, such as temperature and humidity, to ensure optimal growth conditions.
When Jay and her co-founders, K Muralidesan and Shan Palani, embarked on this initiative six years ago, Boomgrow was nowhere near what it is today.
The three founders got together hoping to do their part in building a more sustainable future. “I’ve spent years advising small and large companies on sustainability, environmental and social governance disclosures. I even embarked on a doctorate in sustainability disclosure and governance,” says Jay.
“But I felt a deep sense of disconnect because while I saw companies evolving in terms of policies, processes and procedures towards sustainability, the people in those organisations were not transforming. Sustainability is almost like this white noise in the background. We know it’s important and we know it needs to be done, but we don’t really know how to integrate it into our lives.
“That disconnect really troubled me. When we started Boomgrow, it wasn’t a linear journey. Boomgrow is something that came out of meaningful conversations and many years of research.”
Shan, on the other hand, was an architect who developed a taste for sustainable designs when he was designing modular structures with minimal impact on their surroundings between regular projects. “It was great doing that kind of work. But I was getting very dissatisfied because the projects were customer-driven, which meant I would end up having debates about trivial stuff such as the colour of wall tiles,” he says.
As for Murali, the impetus to start Boomgrow came from having lived overseas — while working in capital markets and financial services — where quality and nutritious produce was easily available.
Ultimately, they concluded that the best way to work towards their shared sustainability goals was to address the imminent problem of food shortage.
“By 2050, the world’s population is expected to grow to 9.7 billion people, two-thirds of whom will be in Asia-Pacific. Feeding all those people will definitely be a huge challenge,” says Jay.
“The current agricultural practice is not built for resilience, but efficiency. So, when you think of farming, you think of vast tracts of land located far away from where you live or shop.
“The only way we could reimagine or rethink that was to make sure the food is located closer to consumers, with a hyperlocal strategy that is traceable and transparent, and also free of pesticides.”
Having little experience in growing anything, it took them a while to figure out the best mechanism to achieve their goal. “After we started working on prototypes, we realised that the tropics are not designed for certain types of farming,” says Jay.
“And then, there is the problem of harmful chemicals and pesticides everywhere, which has become a necessity for farmers to protect their crops because of the unpredictable climate. We went through many iterations … when we started, we used to farm in little boxes, but that didn’t quite work out.”
They explored different methodologies, from hydroponics to aquaponics, and even started growing outdoors. But they lost a lot of crops when a heat wave struck.
That was when they started exploring more effective ways to farm. “How can we protect the farm from terrible torrential rains, plant 365 days a year and keep prices affordable? It took us five years to answer these questions,” says Jay.
Even though farmers all over the world currently produce more than enough food to feed everyone, 820 million people — roughly 11% of the global population — did not have enough to eat in 2018, according to the World Health Organization. Concurrently, food safety and quality concerns are rising, with more consumers opting for organically produced food as well as safe foods, out of fear of harmful synthetic fertilisers, pesticides, herbicides and fungicides.
According to ResearchAndMarkets.com, consumer demand for global organic fruit and vegetables was valued at US$19.16 billion in 2019 and is anticipated to expand at a compound annual growth rate (CAGR) of 6.5% by 2026.
Meanwhile, the precision farming market was estimated to be US$7 billion in 2020 and is projected to reach US$12.8 billion by 2025, at a CAGR of 12.7% between 2020 and 2025, states MarketsandMarkets Research Pte Ltd.
Malaysia currently imports RM1 billion worth of leafy vegetables from countries such as Australia, China and Japan. Sourcing good and safe food from local suppliers not only benefits the country from a food security standpoint but also improves Malaysia’s competitive advantage, says Jay.
Unlike organic farming — which is still a soil-based method — tech-enabled precision farming has the advantage of catering for increasing demand and optimum crop production with the limited resources available. Moreover, changing weather patterns due to global warming encourage the adoption of advanced farming technologies to enhance farm productivity and crop yield.
Boomgrow’s model does not require the acres of land that traditional farms need, Jay emphasises. With indoor farms, the company promises a year-round harvest, undisturbed by climate and which uses 95% less water, land and fuel to operate.
Traditional farming is back-breaking labour. But with precision technology, farmers can spend less time on the farm and more on doing other things to develop their business, she says.
Boomgrow has secured more than RM300,000 in funding via technology and innovation grants from SME Corporation Malaysia, PlaTCOM Ventures and Malaysia Digital Economy Corporation, and is on track to build the country’s largest indoor farms.
Image from: Boomgrow
The company got its chance to showcase the strength of its smart technology when Telekom Malaysia Bhd (TM) approached it to be a part of the telco’s Smart Agriculture cluster in Langkawi last October.
“5G makes it faster for us to process the multiple data streams that we need because we collect data for machine learning, and then AI helps us to make decisions faster,” Jay explains.
“We manage the farm using machines to study inputs like water and electricity and even measure humidity. All the farm’s produce is lab-tested and we can keep our promise that there are no pesticides, herbicides or any preserving chemicals. We follow the food safety standards set by the EU, where nitrate accumulation in plant tissues is a big issue.”
With TM’s 5G technology and Boomgrow’s patent-pending technology, the latter is able to grow vegetables like the staple Asian greens and highland crops such as butterhead and romaine lettuce as well as kale and mint. While the company is able to grow more than 30 varieties of leafy greens, it has decided to stick to a selection of crops that is most in demand to reduce waste, says Jay.
As it stands, shipping containers are the best fit for the company’s current endeavour as containerised modular farms are the simplest means of bringing better food to local communities. However, it is also developing a blueprint to house farms in buildings, she says.
Since the showcase, Boomgrow has started to supply its crops to various hotels in Langkawi. It rolled out its e-commerce platform last year after the Movement Control Order was imposed.
“On our website, we promise to deliver the greens within six hours of harvest. But actually, you could get them way earlier. We harvest the morning after the orders come in and the vegetables are delivered on the same day,” says Jay.
Being mindful of Boomgrow’s carbon footprint, orders are organised and scheduled according to consumers’ localities, she points out. “We don’t want our delivery partners zipping everywhere, so we stagger the orders based on where consumers live.
“For example, all deliveries to Petaling Jaya happen on Thursdays, but the vegetables are harvested that morning. They are not harvested a week before, three days before or the night before. This is what it means to be hyperlocal. We want to deliver produce at its freshest and most nutritious state.”
Plans to expand regionally are also underway, once Boomgrow’s fundraising exercise is complete, says Jay. “Most probably, this will only happen when the Covid-19 pandemic ends.”
To gain the knowledge they have today, the team had to “unlearn” everything they knew and take up new skills to figure what would work best for their business, says Jay. “All this wouldn’t have been possible if we had not experimented with smart cameras to monitor the condition of our produce,” she laughs.
Bowery’s Founder, Irving Fain, On The Future of Vertical Farming
At one point in the not-so-distant past, vertical farming’s role in our future agricultural system was far from certain. Growing leafy greens in warehouse-like environments controlled by tech seemed like a compelling business, but one that had yet to prove itself either economically or as an important source of food for a growing world population
Image from: The Spoon
At one point in the not-so-distant past, vertical farming’s role in our future agricultural system was far from certain. Growing leafy greens in warehouse-like environments controlled by tech seemed like a compelling business, but one that had yet to prove itself either economically or as an important source of food for a growing world population.
That, at least, was a common sentiment Irving Fain, CEO and founder of Bowery, met with when he started his vertical farming company five years ago. “There was a bit of skepticism around it,” he told me over a call recently, suggesting that five years ago, there were a lot more “ifs” than “whens” in terms of vertical farming’s future.
Fain, Bowery, and the entire vertical farming industry get a much warmer reception nowadays. Investment dollars are pouring into the space. Around the world, companies, scientists, and food producers are using the method to not just supply upscale grocery stores with greens but experiment with breeds of produce, feed underserved populations, and grow food in non-arable regions. As Fain suggested when we spoke, the last 12 months seem to have turned those “ifs” into definite “whens.”
Bowery’s last 12 months also illustrate this change. Fain said that Bowery went from under 100 retail locations about a year ago to nearly 700 right now, and will be in more than 1,000 “in the coming months.” Its produce is in a number of food retailers around the Mid-Atlantic and Northeast, including Whole Foods Market, Giant Food, Stop & Shop, Walmart, and Weis Markets. And in 2020, the company experienced “more than 4x growth” with e-commerce partners.
While the pandemic is responsible for some of this popularity, Fain insists it is not the only reason for the eventful year. “It’s definitely bigger than the pandemic,” he said. “What you’re seeing is a food system that’s evolving and [people have a desire] to see transparency and traceability in the food system.” These, he says, are issues the traditional food supply chain isn’t really able to address right now, hence the opportunity for companies like Bowery, which effectively cut multiple steps out of the supply chain.
Bowery grows its greens (lettuces, herbs, and some custom blends) inside industrial spaces where crops are stacked vertically in trays and fed nutrients and water via a hydroponic system. Technology controls all elements of the farm, from the temperature inside to how much light each plants get. The company currently operates two farms, one in New Jersey and the other in Maryland. A third is planned for Pennsylvania.
Technology, in particular, is something Bowery has big plans for. On top of a retail expansion, Bowery also added some notable personnel to its staff, including Injong Rhee, formerly the Internet of Things VP at Google as well a chief technologist at Samsung. Having such technology chops onboard will be vital in order for Bowery to realize many of its ambitions around advanced automation, which has the potential to optimize many parts of the seed-to-store process for vertically grown greens.
For example, Bowery’s farms are equipped with sensors and cameras that are constantly collecting data — “billions” of points, according to the company — that can be used to not just observe the current state of plant health but also predict the most optimal growing conditions for each crop. Elements like temperature, humidity levels, nutrient levels, and light intensity can all be adjusted, via the BoweryOS software, to create those optimal conditions. The end result is more consistent crop production, better yields, more flavorful food, and, ideally, a better nutritional profile for the greens compared to what conventional produce offers.
The system can also, through automation and AI, detect problems with plants. In a recent interview with Venture Beat, Bowery Chief Science Officer Henry Sztul used the example of butterhead lettuce yellowing at the edges during growth. Bowery’s system is technologically advanced enough at this point that it is starting to understand the conditions that create those yellowing edges. That foreknowledge, in turn, will allow growers to adjust the crop “recipe” (see above mixture of lights, temperature, etc.) to avoid the problem.
It took Bowery years to get to this point in terms of what its technology is capable of doing. “The system [for] indoor farming that you choose has a direct impact on the crops you’ll be able to grow, on the margins you’ll be able to generate, and on the return profile of the business itself,” said Fain. “And so being incredibly intentional and thoughtful about what technology you use is something we spent a lot of time on because it has an extraordinarily important economic impact.”
On a less technically complex note, controlled ag from Bowery and others also goes some way towards reinventing the supply food chain. Rather than greens being harvested in, say, Mexico and shipped via a complex distribution process all the way to Baltimore, they are packaged up at the farm and distributed to nearby retailers, usually those within a day’s drive “It is much more sustainable. It is much more efficient, and it’s more reliable, and those things have been important to consumers long before COVID,” said Fain.
Bowery will continue to innovate on both the technology and supply side of its business, as well as with the food itself. The company just launched a new specialty product line that will experiment with different flavors of greens and change frequently.
In terms of tech, Bowery’s latest farm, currently being built in Bethlehem, Pennsylvania, will incorporate even more automation than the company’s two existing farms. That location is slated to open later in 2021. When it does, Bowery will be capable of serving nearly 50 million people within a 200-mile radius.
The company hopes to expand its geographic reach much wider some day, building farms near most major U.S. cities and beyond. Given the increased confidence in the vertical farming sector as a whole, now looks to be the optimal time to move towards those ambitions.
by Jennifer Marston, The Spoon
Yasai To Establish First Zürich Vertical Farm, Strategic Partnership Announced
iFarm with Yasai AG (Switzerland) and Logiqs B.V. (Netherlands) are proud to announce the beginning of a long-term cooperation. With the launch of the first vertical farm project in Zurich, Yasai AG announced the signing of a strategic agreement with equipment and tech suppliers
Image from: Urban Ag News
iFarm with Yasai AG (Switzerland) and Logiqs B.V. (Netherlands) are proud to announce the beginning of a long-term cooperation.
With the launch of the first vertical farm project in Zurich, Yasai AG announced the signing of a strategic agreement with equipment and tech suppliers. The company involved Logiqs and iFarm as technology partners in the construction of a pilot facility, with 673 sq. m of growing area and with a design capacity of 20 tons of fresh herbs per year.
The Dutch company Logiqs will act as a supplier of automated shelving systems and grow lights. iFarm will supply the nutrient solution management system, climate control equipment, and the Growtune software platform which enables flow chart implementation and control over production conditions and processes. Going forward, the partners plan to scale up the experience of rapidly constructing an automated, compact, high-performance vertical farm, gained in a Swiss project, across the globe.
Image from: Urban Ag News
Mark Essam Zahran (co-founder Yasai):
The project will not just be limited to the testing and fine-tuning of state-of-the-art innovative solutions. We expect to lay the groundwork for large-scale industrial vertical farming in smart cities and showcase the incredible benefits of a circular economy. A plantation in the largest Swiss city, one of the most expensive cities in the world, will help us assess the economic prospects and give other European cities an example of how to produce an abundant yield without harming the planet, plants, and people.
Gert-Jan van Staalduinen (owner Logiqs):
The Swiss project opens up interesting prospects for us. We expect a fruitful collaboration with Yasai experts and a beneficial exchange of best practices with iFarm. With our vast experience in implementing automation and logistics systems on farms, we will be able to build a technologically advanced farm in the very heart of Europe.
Kirill Zelenski (CEO iFarm Europe):
We appreciate how meticulous and scrupulous Yasai is and are impressed by their passion and drive. We are just as inspired by the prospect of working with seasoned professionals from Logiqs. We hope that our software technologies will perfectly complement their hardware and the project as a whole will become a lasting benchmark for the industry and will serve as the beginning of a long-term cooperation.
These 2 Companies Are Putting Big Money Into Hawaii’s Agricultural Future. Will Their Bets Pay Off?
A pair of companies backed by a billionaire and a pension fund are trying to revitalize fallow farmland in the state
A pair of companies backed by a billionaire and a pension fund are trying to revitalize fallow farmland in the state.
02-15-21
On Lanai, where shreds of black plastic in the soil are the last vestiges of the island’s defunct pineapple fields, a sliver of long-abandoned farmland is getting an encore — and a reinvention.
In six high-tech greenhouses, a futuristic vision of food-growing is underway — one in which nutrient density and flavor are automated.
It doesn’t matter that the red dirt below the greenhouse is eroded or peppered with plastic that once served as Dole pineapple plantation’s weed control. In fact, the hydroponic tomatoes and leafy greens grown here by Sensei Ag don’t depend on soil at all.
The ag-tech company founded by Larry Ellison, the Oracle founder who owns nearly all of Lanai’s acreage, and Dr. David Agus, a physician, and medical researcher, is pioneering tools to produce affordable food in places like Lanai that — despite its history as an agricultural plantation — lack traditional farming essentials like water and fertile soil.
Sensei Farms Lanai, a two-acre indoor farming pilot project by Larry Ellison’s Sensei Ag, produced 35,000 pounds of produce in less than three months last year. Sensei Ag
In doing so, the company is redeploying a scrap of neglected farmland into active agriculture in an attempt to buck an unsettling trend: Hawaii imports more than 85% of its food.
Hawaii has tens of thousands of acres of fallow former sugar and pineapple plantation lands. There are many reasons why this land isn’t being used for farming — inadequate infrastructure, soil erosion, the sky-high price of agricultural real estate. All of these challenges and more make growing food on old plantation acreage unaffordable for most farming operations.
Putting more of this stagnant acreage into food production, however, is a worthwhile goal, experts say, because it could help the state wean itself off of a reliance on the cargo ships and planes that deliver food supplies to the islands.
“When you bring up Hawaii to anyone anywhere on earth, what they think of is paradise on earth,” said Vincent Mina, president of the Maui Farmers Union United. “But what paradise do you know of that brings in 85% of its food?”
State Efforts Have Fallen Short
Re-fashioning former sugar and pineapple plantations into viable food farms is what the Hawaii Agribusiness Development Corp. was designed to do.
However, a scathing state audit in January said that the 25-year-old state agency has so far failed its mission because “the economic void created when plantations ceased production remains mostly unfilled.”
Larry Jefts, one of the state’s largest produce producers, recently expanded his farm footprint with access to ADC lands in Central Oahu that had lain fallow since Del Monte stopped pineapple production nearly two decades ago.
The problem, according to Jefts, is not that the ADC is inert. It’s the state’s poor land use policy that has allowed some farmland to be developed, as well as society’s lack of commitment to local agriculture.
The Agribusiness Development Corp. has failed in its mission to reinvent Hawaii’s agricultural sector, two recent reports say. Office of the Auditor
“The problem is there’s no will here,” Jefts said. “Good farm ground is coming out to go into solar energy farms because the people who own it can make more money in solar. If they charged that much money to the farmers, the farmers would fail and imported foods would take over.”
Yet while Jefts is farming on a portion of the 1,200-acre Whitmore Project — land left vacant by Del Monte in 2004 and then acquired by the ADC for local agriculture in 2012 — hundreds of acres attached to the project remain fallow almost 10 years later.
That’s in part due to the time-intensive, bureaucratic process of securing money, permits, and contracts to build and repair the infrastructure required to make more of the acreage farmable, said Sen. Donovan Dela Cruz, a champion of the project.
It’s one thing to acquire the land, he said. But it’s another challenge entirely to ready it for farmers who need water, roads, electricity for refrigeration, and food safety-compliant facilities in order to make their businesses financially viable.
“With our state, there’s so many good intentions but just no money to put through to implementation,” said Kirsten Oleson, associate professor of ecological economics at the University of Hawaii College of Tropical Agriculture and Human Resources.
“If we’re serious about doubling production of food that is grown and eaten here, it would take some time to rethink policy and some pretty large and potentially risky investment that the state’s coffers don’t have.”
While state efforts flounder, a pair of new agriculture companies backed by a billionaire and a pension fund are stepping in with lofty goals to revitalize fallow farmland with diversified agriculture operations that aim to help Hawaii wean itself off of imported foods.
A Billionaire’s Bid To Boost Food Security
On Lanai, Sensei Ag is sidestepping many of the traditional high-yield farming requirements: lots of land, lots of water, lots of hard manual labor.
Founded by Oracle billionaire Larry Ellison, left, and medical researcher David Agus, Sensei Ag’s goal is to grow food that is more sustainable and nourishing than if it were farmed traditionally.
Sensei Ag
Although the company’s two-acre greenhouse farm is just a scrap of the 20,000 farmed acres that earned Lanai the moniker of the world’s largest pineapple plantation, yields from hydroponics can be far greater than those from conventional soil farming.
Sensei Ag CEO Sonia Lo projects the company will harvest 500,000 pounds of food for statewide consumption in 2021, including Swiss chard, basil, tomatoes, cucumber and eggplant.
“What we’re doing is we’re competing against the likes of Organic Girl that’s coming in from California or Earthbound Farms,” Lo said. “It’s pretty straightforward given that our stuff is a day old or two days old by the time it gets on a shelf as opposed to two weeks or three weeks old.”
Hydroponic growing is capital-intensive, however. Sensei Ag’s approach benefits from the fact that it’s bankrolled by Ellison, one of the richest people in the world.
Lo declined to reveal the amount of financial investment it took for the Lanai pilot project to achieve its inaugural harvest last October, but she acknowledged the role of Ellison’s wealth.
Yet while the cost to build a state-of-the-art greenhouse is out-of-reach for most farmers, indoor farming offers growers a chance to capture significant long-term financial savings since producing food this way requires significantly less land and water than traditional outdoor farming.
According to Lo, Sensei Farms Lanai requires about 10% of the amount of water it would take to produce a similar harvest in the dirt.
With this in mind, Sensei Ag’s mission includes efforts to make greenhouse farming more accessible. The company is aggregating risk assessment data in hopes that it will encourage banks to finance indoor growing mechanisms such as greenhouses and vertical farms. The company is also writing a playbook for people who want to build a successful indoor farm business, Lo said.
The rise of this kind of high-tech, high-yield farming could be a key to making Hawaii-farmed foods more competitive, according to Jesse Cooke, vice president of investments and analytics at the Ulupono Initiative.
“Using a hydroponic system, you could guarantee that every week you would have the same amount of quantity and the same quality (of produce) — and that’s what you need to sell to a large grocer,” Cooke said. “A lot of outdoor operations can’t guarantee that because they’re at the whim of nature itself.”
Brian Miyamoto, executive director of the Hawaii Farm Bureau Federation, agrees that indoor farming could be a game-changer — if Hawaii farmers can figure out how to raise enough capital to build the infrastructure without sabotaging future profits.
“We can grow a lot of things here in Hawaii as far as food products,” Miyamoto said. “What we struggle with is doing it competitively — that’s why we import so much.”
Hawaii can’t rely on billionaires to make the upfront investment in high-tech indoor farming, Oleson said. Rather, the state needs to follow in the footsteps of other countries that enacted public policies to encourage this kind of agriculture.
In places like Israel and the Netherlands, high-tech greenhouses are important food production tools, Oleson said.
Beyond policy and economics, Oleson said there are aesthetic and cultural considerations associated with scaling up indoor farming in the islands.
“You’re not looking across rolling green landscapes, you’re looking at lands with big infrastructure on it so there’s sometimes social pushback,” Oleson said. “I’m not a Native Hawaiian, but I would be very curious to know the response of the local community to that kind of agriculture because it’s very divorced from the earth.”
Will Mahi Pono’s ‘Serious Amount Of Money’ Pay Off?
On Maui, a partnership between a California farm management company and a Canadian pension fund is producing food on fallow land resulting from the 2016 closure of the state’s last sugar grower.
Since Mahi Pono bought 41,000 acres of Hawaiian Commercial & Sugar Co.’s former sugar cane fields in 2019, the company has begun growing some of Hawaii’s top food imports — potatoes and onions — in hopes of winning over some of that market share.
Mahi Pono’s mission to produce foods that Hawaii imports heavily and that are agriculturally possible to grow here is a smart one, according to Oleson. But she said it could be difficult for the company to compete with the price point for potatoes and onions imported from the mainland.
In 2016, Hawaii’s last remaining sugar grower shut down an operation that had run for 146 years. Now the 40,000 acres are owned by Mahi Pono, the marriage of a California farm management company and a Canadian pension fund. The company is growing produce with plans to reduce the state’s reliance on imports. Courtesy: Mahi Pono
It might also prove hard to convince consumers to pay more for locally grown potatoes and onions as opposed to more perishable produce.
“Potatoes and onions can sit on a boat and the quality doesn’t decline quite as fast, but all of us know what happens when you buy a box of spinach from Costco and if you don’t eat it that night it turns to slime,” Oleson said. “So the concern is growing foods locally where the freshness really matters.”
But Mahi Pono is growing more than just root vegetables. The company planted over a half million avocado and breadfruit trees, as well as rows of trees to shelter crops from the wind. The company plans to plant its 1 millionth tree by the end of June, according to community relations director Tiare Lawrence.
The company is also growing produce ranging from tangelos and finger limes to broccoli and eggplants, and it’s leasing affordable land and water to small farmers for an annual fee of $150 per acre.
Ultimately, Mahi Pono’s staple crops will be citrus, papaya, macadamia nuts, and coffee, Lawrence said.
And while the company is exporting papayas to Canada, and eventually plans to export coffee, macadamia nuts, and citrus to markets outside the state, the majority of the food produced by Mahi Pono will feed Hawaii’s people, Lawrence said.
“I personally think these lands can be brought into production,” Lawrence said. “We’ve seen it across Hawaii where farmers have been able to take former sugar and pineapple lands and turn it into a thriving farm and I refuse to entertain doomsday scenarios.”
Mahi Pono is growing red, yellow, and white potatoes with the goal of stealing away some of the Hawaii market share from mainland-grown potatoes. Courtesy: Mahi Pono
But the farm enterprise faces many challenges.
With an average wind speed of 30 miles per hour in the Central Maui plains, there are erosion issues, as well as crop damage from pests, deer, and pigs.
“We really can’t plant a field unless we fence it in, so that adds to our costs,” Lawrence said.
There’s also the problem of the former plantation’s aging, outdated infrastructure.
“Mahi Pono has spent a serious amount of money in updating the irrigation systems and making repairs to wells,” Lawrence said.
If Mahi Pono can surmount these challenges and find success, Cooke of Ulupono said the operation will be an example to follow.
“If they can get it up and running, that could be one of the hugest transformations that Hawaii has seen, especially going towards local food for local consumption,” Cooke said. “The worry is that it doesn’t work and somehow the land gets zoned residential and a housing development goes up.”
“Hawaii Grown” is funded in part by grants from the Ulupono Fund at the Hawaii Community Foundation, the Marisla Fund at the Hawaii Community Foundation, and the Frost Family Foundation.
Brittany Lyte is a reporter for Civil Beat. You can reach her by email at blyte@civilbeat.org or follow on Twitter at @blyte
Use the RSS feed to subscribe to Brittany Lyte's posts today
Pontus Submits Building Permit Application for Surrey Aquaponics Facility
The Company has submitted a construction application to the City of Surrey for its 20,570 square foot aquaponics facility. The approval process is estimated to be completed within 6 weeks and is expected to be followed by the immediate commencement of construction of the Facility's leasehold improvements. Accordingly, the leasehold improvements are to consist of a complete retrofit of the Facility to establish Pontus' solar-powered, water recycling CEVASTM aquaponic system
VANCOUVER, BC, Feb. 3, 2021 /CNW/ - Pontus Protein Ltd. ("Pontus" or the "Company"), is pleased to announce it has made significant progress towards the development of its state of the art, integrated aquaponics facility located in Surrey, British Columbia, Canada (the "Facility").
Image from: CNW Group/Pontus Protein Ltd
The Company has submitted a construction application to the City of Surrey for its 20,570 square foot aquaponics facility. The approval process is estimated to be completed within 6 weeks and is expected to be followed by the immediate commencement of construction of the Facility's leasehold improvements. Accordingly, the leasehold improvements are to consist of a complete retrofit of the Facility to establish Pontus' solar-powered, water recycling CEVASTM aquaponic system.
The installation of all required equipment for the growth and production is forecasted to take between four and six months to complete. Upon completion, the Facility will be approximately 20 times the size of Pontus' prior prototype facility. The prototype facility has been used to test and develop the technology for the Company's proprietary growing process.
The Facility, as seen in the image above and video below, will utilize an array of additional technologies to create a clean and sustainable aquaponics ecosystem. Solar energy panels will be installed to capture renewable energy and power the closed-loop water system, which recycles up to 95% of all water inputs. The implementation of the Facility's unique, sustainable technology in conjunction with Pontus' proprietary CEVAS™ automated growth technology will allow the Company to emphasize biosecurity in its agricultural production processes, removing the need for additional chemicals, pesticides, and other non-native components.
Pontus CEO, Conner Yuen states: "Entering the construction application process is a major milestone for the Company as we move toward the commissioning of the Facility. Our aim is to create a state of the art process that will incorporate the latest in sustainable agriculture technology. The ability to implement this highly efficient technology solves many issues we see with current methods of food production such as land scarcity and low yields and contamination.
Pontus' biosecurity and renewable food sources are intended to create a proactive solution to these issues by reducing the potential for contamination and the need for pesticides. Pontus hopes the Facility will revolutionize how traditional agriculture is conducted and show the power of technological food advancements."
Plant-based Protein Powder Market
The Company's plant-based protein powder is a premium entry into the global protein and supplements market, which is currently valued at USD$15 Billion and is expected to grow to USD$20 Billion by 2025 according to Grand View Research. This growth is expected to be fuelled by many North Americans reducing or eliminating the regular consumption of animal products. The North American plant-based protein market is also anticipated to grow at a compound annual growth rate of 14% from 2019 through 2025.
About Pontus Protein Ltd
Pontus Protein Ltd. makes pure plant-based protein powder sourced from nutritious water lentils, farm-grown in Vancouver, BC, with development plans to expand to Surrey, B.C.. Not only does Pontus Protein Powder exceed certified organic standards, but it's also gluten-free, pure and allergen safe. It's jam-packed full of antioxidants, minerals, vitamins and ALL the essential amino acids.
This is not your average lentil, these are water lentils; a crop that can be harvested every 24 hours in an indoor aquaponic farm that uses 95% less water than traditional agriculture, using Pontus' proprietary Closed Environment Vertical Aquaponics System (or CEVAS™) aquaponic agritech technology. This is wonderful news for a planet populated with us hungry and health-conscious humans.
Nanobubble Tech Could Revolutionize Aquaculture & Aquaponics
“There is a pressing need to develop an alternative to the current highly energy-intensive conventional aeration,” said Khanal. “Nanobubble technology has a potential to revolutionize aquaculture and aquaponic systems, with higher productivity and resource recovery.” Khanal was initially awarded CTAHR’s Team Science grant, which was critically important to obtaining preliminary data for his grant proposal to NIFA
Image from: University of Hawai’i News
The burgeoning fields of aquaculture and aquaponics hold vast potential for growing food. Yet, the efficacy of these microbial-mediated processes is governed by the availability of dissolved oxygen in water. Generally, oxygen has poor solubility in water, which has a negative effect on fish growth and plant yields.
Almost $200,000 in new funding from the USDA-National Institute of Food and Agriculture’s (NIFA) Water Quantity and Quality Program may expand researchers’ understanding of how nanobubbles could improve aeration and oxygen supplies.
Under the grant, Samir Khanal of the University of Hawaiʻi at Mānoa’s College of Tropical Agriculture and Human Resources (CTAHR ) Department of Molecular Biosciences and Bioengineering, will apply the technology to these aqueous systems. His goal is to uncover new opportunities for improving fish and plant yields—with concomitant improvements in water quality.
Image from: University of Hawai’i News
“There is a pressing need to develop an alternative to the current highly energy-intensive conventional aeration,” said Khanal. “Nanobubble technology has a potential to revolutionize aquaculture and aquaponic systems, with higher productivity and resource recovery.”
Khanal was initially awarded CTAHR’s Team Science grant, which was critically important to obtaining preliminary data for his grant proposal to NIFA.
“Thanks to the CTAHR and NIFA grants, we hope our findings will benefit existing Hawaiʻi businesses, as well as a new generation of growers, across the state and beyond,” Khanal added.
Ensuring Singapore's Food Security Despite the Odds
As with most issues that impact national security in Singapore, it often seems that the odds are stacked against us. Food security — access to safe and nutritious food — is a challenge on several fronts. Singapore is a small city-state with limited resources, with only 1 per cent of land available for food production, and over 90 per cent of food is imported from an increasingly disrupted world. The Covid-19 pandemic has further amplified the gravity of safeguarding food security
Image from: Reuters
As with most issues that impact national security in Singapore, it often seems that the odds are stacked against us. Food security — access to safe and nutritious food — is a challenge on several fronts.
Singapore is a small city-state with limited resources, with only 1 per cent of land available for food production, and over 90 per cent of food is imported from an increasingly disrupted world. The Covid-19 pandemic has further amplified the gravity of safeguarding food security. The city-state has been proactively planning for long-term food security through the Singapore Food Agency’s (SFA) strategy of “three food baskets” — diversifying food sources, growing locally and growing overseas. This approach has served the Republic well in securing a supply of safe food.
DIVERSIFIED SOURCING IS KEY
Singapore’s food importers leverage the nation’s connectivity and the global free trade environment to import from multiple sources in about 170 countries and regions worldwide. Should there be a disruption to any one source, importers are able to tap alternative food sources and ensure supply remains stable. Lockdown measures brought about by Covid-19 underscored Singapore’s vulnerabilities to supply disruptions in food.
It was not by luck that the Republic’s food supply remained stable and market shelves continued to be promptly restocked — it was the result of a deliberate whole-of-government strategy to diversify food sources. To keep the nation’’s diversified food supply lines intact amid the Covid-19 global pandemic, SFA worked closely with the Ministry of Trade and Industry and Enterprise Singapore (ESG) to monitor Singapore’s food supply situation. Together with the Ministry of Foreign Affairs, these economic agencies worked with like-minded countries to maintain open trade links.
LOCAL PRODUCTION AN IMPORTANT BUFFER
SFA drives innovation in local farms with the ambitious goal of producing 30 per cent of Singapore’s nutritional needs by 2030 as part of our “30 by 30” plan. To meet this goal, we need a holistic and long-term approach to space-planning, boosting agri-food technology and developing local agri-specialists. To facilitate and support the establishment of high-technology and productive farms in Singapore, SFA tenders out land based on qualitative criteria such as production capability, production track record, relevant experience and qualifications, innovation and sustainability.
In addition, a masterplan for the greater Lim Chu Kang (LCK) region, spanning about 390ha of land, will be undertaken in consultation with stakeholders over the next two to three years. The redeveloped LCK agri-food cluster will produce more than three times its current food production.
Building on the above efforts to grow Singapore’s high-tech agri-tech sector, SFA will continue to partner with the Economic Development Board and ESG to attract best-in-class global agri-tech companies, as well as to nurture promising homegrown agri-tech companies into local champions and help them to expand overseas.
EXPLORING ALTERNATIVE, UNDERUTILISED SPACES
Urban food solutions are expected to play a key role in global food security. While there are progressive enterprises operating out of farmlands and industrial estates, some agricultural game-changers are also taking root in unconventional areas — indoors, on rooftops and in underutilised spaces.
SFA worked with the Singapore Land Authority to introduce an urban farm at the former Henderson Secondary School site, which was transformed into Singapore’s first integrated space comprising an urban farm, childcare centre and nursing home within a state property. The farm space within the site was awarded in May 2019 to social enterprise City Sprouts, and it has become a vibrant destination for the young and old to learn about urban farming and enjoy a relaxing day out.
Citiponics, the first commercial farm located on a multi-storey car park in a residential neighbourhood, harvested its first yield of vegetables in April 2019. In September 2020, another nine sites atop multi-storey car parks were awarded for urban farming.
The successful bidders included proposals for hydroponic and vertical farming systems with a variety of innovative features, such as the Internet of Things (IoT), blockchain technology and automated climate control. These sites have the potential to collectively produce around 1,600 tonnes of vegetables annually.
Image from: Ciitiponics
TAPPING TECH
The Agriculture Productivity Fund (APF) supports local farms in their capability development and drive towards higher productivity. Through APF, SFA co-funds the adoption of farming systems to better control environmental variables, test-bed technologies and boost production capabilities. Between October 2014 and September 2020, a total of almost S$42 million has been committed to 115 farms.
The Covid-19 pandemic presented greater impetus to speed up local food production capacities. In September 2020, SFA awarded S$39.4 million to nine companies under the 30x30 Express Grant to quickly ramp up food-farm outputs over the next six months to two years. With advanced robotic and digital systems increasingly being used in farming, Singapore’s vegetables farmers have also become innovative agri-engineers and specialists in their own right.
With support from the 30x30 Express Grant, urban farming engineering solutions firm Indoor Farm Factory Innovation will set up an indoor vegetable farm with a vertical integration growth system up to 8m in height in a fully controlled and pesticide-free environment. The farm will leverage artificial intelligence farming systems integrated with IoT monitoring, dosing irrigation and an advanced environmental control system to achieve optimum growing conditions all year round.
Seng Choon, a chicken egg farm that has been in business for more than 30 years, has also proved itself a modernist in its operations. The company uses a computer that scans eggs to ascertain if they are clean; while feeding systems, temperature controls and waste cleaning systems have been automated with SFA’s support. Singapore’s efforts at ensuring food security would not be complete without support from consumers. To boost recognition of local produce among consumers, SFA brought the industry and public together to create a new “SG Fresh Produce” logo.
Farmers have been using this emblem on their packaging since August 2020. A website was also launched to provide a trove of information on locally farmed food. While the Covid-19 pandemic has led to import restrictions, it also helped to accelerate support for local produce. With public support for local farmers and other key measures, Singapore can beat the odds in ensuring food security in this ever-evolving, ever-disrupted world.
The Future of the Food Supply Chain Lives on a Rooftop in Montreal
The world’s biggest commercial rooftop greenhouse sits atop a former Sears warehouse in a semi-industrial northwestern quarter of Montreal. Early every morning, staff pick fresh vegetables, then bring them downstairs, where they get packed into heavy-duty plastic totes along with the rest of the day’s grocery orders.
Image from: Lufa Farms
The world’s biggest commercial rooftop greenhouse sits atop a former Sears warehouse in a semi-industrial northwestern quarter of Montreal. Early every morning, staff pick fresh vegetables, then bring them downstairs, where they get packed into heavy-duty plastic totes along with the rest of the day’s grocery orders.
Tablets loaded with custom pick-and-pack software tell them where to put what: This basket has lettuce, tomatoes, and cucumbers, plus some chicken, eggs, and milk. The next one has eggplant, cashew Parmesan, tomato sauce, fresh pasta, and vegan ground round crumble. Whatever Luca doesn’t grow in its four greenhouses comes from local farms and producers, mostly from within 100 miles.
This is a modern foodie’s dream: a tech-forward online shop full of locally grown, pesticide-free, ethically-sourced products at reasonable price points, delivered once a week to either your doorstep or a local pickup point in your neighborhood.
It’s stunning to think Lufa was founded by two people who’d never even grown a tomato before, let alone sold one. “We said, ‘Instead of learning how the food world works, let’s just come up with what we feel the food world should be,’” says Mohamed Hage, 39, who cofounded Lufa with Lauren Rathmell in 2009.
To them, it looked like this: rooftop greenhouses that bring agriculture into cities. No pesticides, herbicides, or fungicides. Composting their green waste. Selling direct-to-consumer the same day the food is harvested. Capturing and reusing rainwater. Reusable packaging.
That’s exactly what they now have—and they feed a portion of Montreal, the second-biggest city in Canada, with it.
Image from: Lufa Farms
Back in the warehouse, workers poke at their tablets, checking off items as they’re packed into the boxes.
Customers—Lufavores, as the company calls them—typically place their orders a few days before delivery through the online store, dubbed “the Marketplace,” which Lufa built from scratch in 2012. That’s how Lufa’s suppliers know how much product to provide: They get forecasts first, then final order numbers, through their Lufa software. Some items, like frozen meat, can be delivered to the warehouse once a week. Others, like bread, arrive fresh every day.
Artisanal Montreal bakery la Fabrique Arhoma started supplying Lufa with bread and pastries about six years ago, co-owner Ariane Beaumont tells Fortune. Today, they hand-make 6,000 individual items a day for Lufa. Beaumont said Lufa now accounts for between 30% to 40% of her commercial sales; since pandemic shutdowns, a lot of the product destined for restaurants got redirected to Lufa. “They’re an exceptional company. I don’t know how they do it,” Beaumont says. “And they pay the fastest, too.”
Technology is the underpinning of Lufa’s success, and the owners know it.
“We see ourselves as a technology company, in the sense that we solve with software,” Rathmell, 32, says. They didn’t really have any other choice. To fulfill that dream they had back in 2009—years before COVID-19 forced most grocery stores to enable online shopping—they had to do it themselves.
“Nothing off-the-shelf can be applied to what we do, because it’s so complex,” Rathmell notes. “We harvest food ourselves; we gather from farmers and food makers throughout the province; most of it’s arriving just in time throughout the night to be packed in baskets for that day, and every order is fully unique.”
Lufa now has a team of eight programmers working on software and systems that manage e-commerce, warehouse management, routing, customer relationships, supplier fulfillment, pick-and-pack, vendor payments, delivery ETAs, and more.
Those technologies were tested on that fateful Friday the 13th last March, when Quebec and Canada each announced their first waves of COVID-19 lockdowns. People panicked, rushing to the grocery store to stock up on flour and toilet paper.
Online, new sign-ups for Lufa’s weekly grocery baskets exploded, and existing subscribers began ordering more than they’d ever ordered before—all while Lufa’s pickup points were shutting down. “We essentially doubled overnight,” Rathmell recalls. Lufa was forced beyond its operational capacity, and the cracks started showing in the systems and software that had, until that point, done a fine job getting the company by.
Lufa temporarily closed the website and opened a wait list. The staff analyzed the pandemic’s trajectory and how they had to adapt at each step; reconfigured their warehouse floor to station workers further apart; then relaunched at the capacity they could handle, gradually scaling each week until they hit their usual stride. Today, they’re humming along at 25,000 baskets a week.
Leading with tech helped make them nimble and strategic during those hairy early pandemic days, said Hage and Rathmell. After some recalibrations and new developments, their software and processes can now handle more customers, vendors, and processes—critical elements as the company continues to scale its greenhouse operations. In August of 2020, Lufa opened its fourth greenhouse, doubling its square footage. The four greenhouses combined produce 57,000 pounds of food a week. A fifth is planned for this year.
“Our objective at Lufa is to get to the point where we’re feeding everyone in the city,” Hage says.
And after Montreal? They’re planning on a yet to be determined second site in the northeastern pocket of North America, ideally this year. “Our vision is to grow food closer to where people live, and grow it more sustainably,” Rathmell says.
Image from: Lufa Farms
Bringing high-yield crop production into cities is a smart answer to many modern challenges in environmental and human health.
Mark Lefsrud, an associate professor of agricultural and environmental sciences at McGill University, points out that embracing technologies like LEDs and automation to grow indoors and in urban greenhouses means shorter supply chains, better nutritional integrity, less food waste, and reduced vulnerability to climate swings. In cities fed primarily by low-carbon energy (hydroelectricity in Montreal’s case), indoor growing versus importation becomes even more of a no-brainer.
“I’ve been working in the controlled environment and greenhouse industry for 20-some years, and having a company like Lufa has brought a lot of attention to not just urban agriculture, but also the need for greenhouse production,” Lefsrud says, adding that Lufa’s success has prompted more government investment in the sector overall.
“The Quebec government now takes this as a serious venture system, which then means that the students that I’m training, and research we’re doing here at the university, now have employment and have the possibility of setting up their own system,” says the McGill professor.
That idea, of developing more vertically integrated food systems, is a passion of Hage’s—not only for the idea of cutting out production and transformation middlemen to improve profit margins, but also to improve quality, traceability, and ultimately the ethics of food production.
“You know, every time we talk to someone about it, we feel like it’s the ’80s, and we’re holding a big solar panel trying to convince the room that this is the future,” Hage says.
As the larger agricultural industry catches on to vertical integration, it seems Hage and Rathmell are no longer mad scientists with a crazy dream. Instead, they are the voice of reason—and a new generation of food.
As the larger agricultural industry catches on to vertical integration, it seems Hage and Rathmell are no longer mad scientists with a crazy dream. Instead, they are the voice of reason—and a new generation of food.
As the larger agricultural industry catches on to vertical integration, it seems Hage and Rathmell are no longer mad scientists with a crazy dream. Instead, they are the voice of reason—and a new generation of food.
NASA's Challenge To Grow Food In Space Can Win You Up To $500,000
There are thousands of bizarre challenges doing the rounds on the internet. These unique challenges soon go viral on the internet, with countless participants hopping on board. A number of these challenges also involve some form of food. If you're a food innovator who's looking for the next interesting challenge to take up, NASA (National Aeronautics and Space Administration) may have something for you. The NASA, in collaboration with Canada's CSA (Central Space Agency), has launched a 'Deep Space Food Challenge'. The one-of-a-kind competition seeks to find food production technologies which are sustainable in long duration missions to outer space.
NASA has launched a 'Deep Space Food Challenge' to prompt innovation of food production techniques and technologies viable in outer space.
Image from: Deep Space Food
There are thousands of bizarre challenges doing the rounds on the internet. These unique challenges soon go viral on the internet, with countless participants hopping on board. A number of these challenges also involve some form of food. If you're a food innovator who's looking for the next interesting challenge to take up, NASA (National Aeronautics and Space Administration) may have something for you.
The NASA, in collaboration with Canada's CSA (Central Space Agency), has launched a 'Deep Space Food Challenge'. The one-of-a-kind competition seeks to find food production technologies which are sustainable in long duration missions to outer space.
Our cargo resupply missions can only go so far! That's why we need your help to design a food system to keep our astronauts feed during long duration space exploration.
— NASA Wallops (@NASA_Wallops) January 30, 2021
Check out the @NASAPrize Deep Space Food Challenge: https://t.co/9mxtZXbwaC pic.twitter.com/izU8nSqPDc
A short video explaining the purpose behind the challenge was shared by the official handle. The 56-second clip elaborated on how astronauts embarking on lunar space exploration missions usually rely on pre-packaged meals or resupply of food through shuttles from Earth.
Thus, creating a brand, new food production system with minimal input and nutritious output with minimal wastage can go a long way in fuelling longer duration space explorations. The challenge's focus is on identifying food production technologies that can help feed a crew of four astronauts and help fill food gaps for a three-year round-trip mission with no resupply required from Earth.
These innovative food production methods may also help communities on Earth living in harsh conditions and extreme climates. This could also help tackle food insecurity in the future, which is one of the biggest issues that loom large today. "Solutions identified through this Challenge could support these harsh environments, and also support greater food production in other milder environments, including major urban centres where vertical farming, urban agriculture and other novel food production techniques can play a more significant role," stated the Deep Space Food Challenge's official website.
.@NASA & @csa_asc are launching a Deep Space Food Challenge to develop food production tech in space.
— NASA STI Program (@NASA_STI) January 28, 2021
Hey @GuyFieri, how about Diners, Drive-Ins, Dives & Deep Space? #STIdocs #Flavortown 🚀🥘
Read about it: https://t.co/fnz80uwpJT
See research: https://t.co/18q6RG3L2G pic.twitter.com/lSRTiiAFes
Registrations for the challenge close on 28th May, and submissions are due 30th July, 2021. Winners of Phase 1 of the challenge will be announced in the month of September this year. The prize money for winners of Phase 1 can go up to USD 500,000 (Rs. 3.64 crores approximately). So, if you have an exciting idea to produce food which could help future space missions - you know what to do!
Is AppHarvest the Future of Farming?
In this video from Motley Fool Live, recorded on Jan. 28, Industry Focus host Nick Sciple and Motley Fool contributor Lou Whiteman discuss AppHarvest, one such SPAC that is looking to disrupt the agriculture industry. Here are the details on what AppHarvest wants to do, and a look at whether the company represents the future of farming.
Special purpose acquisition companies, or SPACs, are red-hot right now, with investors clamoring to get into promising young companies.
In this video from Motley Fool Live, recorded on Jan. 28, Industry Focus host Nick Sciple and Motley Fool contributor Lou Whiteman discuss AppHarvest, one such SPAC that is looking to disrupt the agriculture industry. Here are the details on what AppHarvest wants to do, and a look at whether the company represents the future of farming.
Nick Sciple: One last company I wanted to talk about, Lou, and this is one I think it's -- you pay attention to, but not one I'm super excited to run in and buy. It was a company called AppHarvest. It's coming public via a [SPAC] this year. This vertical farming space. We talked about Gladstone Land buying traditional farmland. AppHarvest is taking a very different approach, trying to lean into some of the ESG-type movements.
Lou Whiteman: Yeah. Let's look at this. It probably wouldn't surprise you that the U.S. is the biggest global farm exporter as we said, but it might surprise you that the Netherlands, the tiny little country, is No. 2. The way they do that is tech: Greenhouse farm structure. AppHarvest has taken that model and brought it to the U.S. They have, I believe, three farms in Appalachia. The pitches can produce 30x the yields using 90% less water. Right now, it's mostly tomatoes and it is early-stage. I don't own this stock either. I love this idea. There's some reasons that I'm not buying in right now that we can get into. But this is fascinating to me. We talked about making the world a better place. This is the company that we need to be successful to make the world a better place. The warning on it is that it is a SPAC. So it's not public yet. Right now, I believe N-O-V-S. That deal should close soon. [Editor's note: The deal has since closed.] I'm not the only one excited about it. I tend not to like to buy IPOs and new companies anyway. I think the caution around buying into the excitement applies here. There is a Martha Stewart video on their website talking up the company, which I love Martha Stewart, but that's a hype level that makes me want to just watch and see what they produce. This is just three little farms in Appalachia right now and a great idea. This was all over my watchlist. I would imagine I would love to hold it at some point, but just be careful because this is, as we saw SPACs last year in other areas, people are very excited about this.
Sciple: Yeah. I think, like we've said, for a lot of these companies, the prospects are great. I think when you look at the reduced water usage, better, environmentally friendly, all those sorts of things. I like that they are in Appalachia. As someone who is from the South, I like it when more rural areas get some people actually investing money there. But again, there's a lot of execution between now and really getting to a place where this is the future of farming and they're going to reach scale and all those sorts of things. But this is a company I'm definitely going to have my radar on and pay attention to as they continue to report earnings. Because you can tell yourself a story about how this type of vertical farming, indoor farming disrupts this traditional model, can be more efficient, cleaner, etc. Something to continue paying attention to as we have more information, because this company, like you said, Lou, isn't all the way public yet. We still got to have this SPAC deal finalized and then we get all our fun SEC filings and quarterly calls and all those sorts of things. Once we have that, I will be very much looking forward to seeing what the company has to say.
Whiteman: Right. Just to finish up along too, the interesting thing here is that it is a proven concept because it has worked elsewhere. The downside of that is that it needed to work there. Netherlands just doesn't have -- and this is an expensive proposition to get started, to get going. There's potential there, but in a country blessed with almost seemingly unlimited farmland for now, for long term it makes sense. But in the short term, it could be a hard thing to really get up and running. I think you're right, just one to watch.