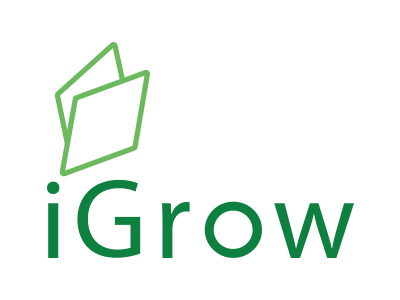
Welcome to iGrow News, Your Source for the World of Indoor Vertical Farming
Pontus Submits Building Permit Application for Surrey Aquaponics Facility
The Company has submitted a construction application to the City of Surrey for its 20,570 square foot aquaponics facility. The approval process is estimated to be completed within 6 weeks and is expected to be followed by the immediate commencement of construction of the Facility's leasehold improvements. Accordingly, the leasehold improvements are to consist of a complete retrofit of the Facility to establish Pontus' solar-powered, water recycling CEVASTM aquaponic system
VANCOUVER, BC, Feb. 3, 2021 /CNW/ - Pontus Protein Ltd. ("Pontus" or the "Company"), is pleased to announce it has made significant progress towards the development of its state of the art, integrated aquaponics facility located in Surrey, British Columbia, Canada (the "Facility").
Image from: CNW Group/Pontus Protein Ltd
The Company has submitted a construction application to the City of Surrey for its 20,570 square foot aquaponics facility. The approval process is estimated to be completed within 6 weeks and is expected to be followed by the immediate commencement of construction of the Facility's leasehold improvements. Accordingly, the leasehold improvements are to consist of a complete retrofit of the Facility to establish Pontus' solar-powered, water recycling CEVASTM aquaponic system.
The installation of all required equipment for the growth and production is forecasted to take between four and six months to complete. Upon completion, the Facility will be approximately 20 times the size of Pontus' prior prototype facility. The prototype facility has been used to test and develop the technology for the Company's proprietary growing process.
The Facility, as seen in the image above and video below, will utilize an array of additional technologies to create a clean and sustainable aquaponics ecosystem. Solar energy panels will be installed to capture renewable energy and power the closed-loop water system, which recycles up to 95% of all water inputs. The implementation of the Facility's unique, sustainable technology in conjunction with Pontus' proprietary CEVAS™ automated growth technology will allow the Company to emphasize biosecurity in its agricultural production processes, removing the need for additional chemicals, pesticides, and other non-native components.
Pontus CEO, Conner Yuen states: "Entering the construction application process is a major milestone for the Company as we move toward the commissioning of the Facility. Our aim is to create a state of the art process that will incorporate the latest in sustainable agriculture technology. The ability to implement this highly efficient technology solves many issues we see with current methods of food production such as land scarcity and low yields and contamination.
Pontus' biosecurity and renewable food sources are intended to create a proactive solution to these issues by reducing the potential for contamination and the need for pesticides. Pontus hopes the Facility will revolutionize how traditional agriculture is conducted and show the power of technological food advancements."
Plant-based Protein Powder Market
The Company's plant-based protein powder is a premium entry into the global protein and supplements market, which is currently valued at USD$15 Billion and is expected to grow to USD$20 Billion by 2025 according to Grand View Research. This growth is expected to be fuelled by many North Americans reducing or eliminating the regular consumption of animal products. The North American plant-based protein market is also anticipated to grow at a compound annual growth rate of 14% from 2019 through 2025.
About Pontus Protein Ltd
Pontus Protein Ltd. makes pure plant-based protein powder sourced from nutritious water lentils, farm-grown in Vancouver, BC, with development plans to expand to Surrey, B.C.. Not only does Pontus Protein Powder exceed certified organic standards, but it's also gluten-free, pure and allergen safe. It's jam-packed full of antioxidants, minerals, vitamins and ALL the essential amino acids.
This is not your average lentil, these are water lentils; a crop that can be harvested every 24 hours in an indoor aquaponic farm that uses 95% less water than traditional agriculture, using Pontus' proprietary Closed Environment Vertical Aquaponics System (or CEVAS™) aquaponic agritech technology. This is wonderful news for a planet populated with us hungry and health-conscious humans.
The Future of the Food Supply Chain Lives on a Rooftop in Montreal
The world’s biggest commercial rooftop greenhouse sits atop a former Sears warehouse in a semi-industrial northwestern quarter of Montreal. Early every morning, staff pick fresh vegetables, then bring them downstairs, where they get packed into heavy-duty plastic totes along with the rest of the day’s grocery orders.
Image from: Lufa Farms
The world’s biggest commercial rooftop greenhouse sits atop a former Sears warehouse in a semi-industrial northwestern quarter of Montreal. Early every morning, staff pick fresh vegetables, then bring them downstairs, where they get packed into heavy-duty plastic totes along with the rest of the day’s grocery orders.
Tablets loaded with custom pick-and-pack software tell them where to put what: This basket has lettuce, tomatoes, and cucumbers, plus some chicken, eggs, and milk. The next one has eggplant, cashew Parmesan, tomato sauce, fresh pasta, and vegan ground round crumble. Whatever Luca doesn’t grow in its four greenhouses comes from local farms and producers, mostly from within 100 miles.
This is a modern foodie’s dream: a tech-forward online shop full of locally grown, pesticide-free, ethically-sourced products at reasonable price points, delivered once a week to either your doorstep or a local pickup point in your neighborhood.
It’s stunning to think Lufa was founded by two people who’d never even grown a tomato before, let alone sold one. “We said, ‘Instead of learning how the food world works, let’s just come up with what we feel the food world should be,’” says Mohamed Hage, 39, who cofounded Lufa with Lauren Rathmell in 2009.
To them, it looked like this: rooftop greenhouses that bring agriculture into cities. No pesticides, herbicides, or fungicides. Composting their green waste. Selling direct-to-consumer the same day the food is harvested. Capturing and reusing rainwater. Reusable packaging.
That’s exactly what they now have—and they feed a portion of Montreal, the second-biggest city in Canada, with it.
Image from: Lufa Farms
Back in the warehouse, workers poke at their tablets, checking off items as they’re packed into the boxes.
Customers—Lufavores, as the company calls them—typically place their orders a few days before delivery through the online store, dubbed “the Marketplace,” which Lufa built from scratch in 2012. That’s how Lufa’s suppliers know how much product to provide: They get forecasts first, then final order numbers, through their Lufa software. Some items, like frozen meat, can be delivered to the warehouse once a week. Others, like bread, arrive fresh every day.
Artisanal Montreal bakery la Fabrique Arhoma started supplying Lufa with bread and pastries about six years ago, co-owner Ariane Beaumont tells Fortune. Today, they hand-make 6,000 individual items a day for Lufa. Beaumont said Lufa now accounts for between 30% to 40% of her commercial sales; since pandemic shutdowns, a lot of the product destined for restaurants got redirected to Lufa. “They’re an exceptional company. I don’t know how they do it,” Beaumont says. “And they pay the fastest, too.”
Technology is the underpinning of Lufa’s success, and the owners know it.
“We see ourselves as a technology company, in the sense that we solve with software,” Rathmell, 32, says. They didn’t really have any other choice. To fulfill that dream they had back in 2009—years before COVID-19 forced most grocery stores to enable online shopping—they had to do it themselves.
“Nothing off-the-shelf can be applied to what we do, because it’s so complex,” Rathmell notes. “We harvest food ourselves; we gather from farmers and food makers throughout the province; most of it’s arriving just in time throughout the night to be packed in baskets for that day, and every order is fully unique.”
Lufa now has a team of eight programmers working on software and systems that manage e-commerce, warehouse management, routing, customer relationships, supplier fulfillment, pick-and-pack, vendor payments, delivery ETAs, and more.
Those technologies were tested on that fateful Friday the 13th last March, when Quebec and Canada each announced their first waves of COVID-19 lockdowns. People panicked, rushing to the grocery store to stock up on flour and toilet paper.
Online, new sign-ups for Lufa’s weekly grocery baskets exploded, and existing subscribers began ordering more than they’d ever ordered before—all while Lufa’s pickup points were shutting down. “We essentially doubled overnight,” Rathmell recalls. Lufa was forced beyond its operational capacity, and the cracks started showing in the systems and software that had, until that point, done a fine job getting the company by.
Lufa temporarily closed the website and opened a wait list. The staff analyzed the pandemic’s trajectory and how they had to adapt at each step; reconfigured their warehouse floor to station workers further apart; then relaunched at the capacity they could handle, gradually scaling each week until they hit their usual stride. Today, they’re humming along at 25,000 baskets a week.
Leading with tech helped make them nimble and strategic during those hairy early pandemic days, said Hage and Rathmell. After some recalibrations and new developments, their software and processes can now handle more customers, vendors, and processes—critical elements as the company continues to scale its greenhouse operations. In August of 2020, Lufa opened its fourth greenhouse, doubling its square footage. The four greenhouses combined produce 57,000 pounds of food a week. A fifth is planned for this year.
“Our objective at Lufa is to get to the point where we’re feeding everyone in the city,” Hage says.
And after Montreal? They’re planning on a yet to be determined second site in the northeastern pocket of North America, ideally this year. “Our vision is to grow food closer to where people live, and grow it more sustainably,” Rathmell says.
Image from: Lufa Farms
Bringing high-yield crop production into cities is a smart answer to many modern challenges in environmental and human health.
Mark Lefsrud, an associate professor of agricultural and environmental sciences at McGill University, points out that embracing technologies like LEDs and automation to grow indoors and in urban greenhouses means shorter supply chains, better nutritional integrity, less food waste, and reduced vulnerability to climate swings. In cities fed primarily by low-carbon energy (hydroelectricity in Montreal’s case), indoor growing versus importation becomes even more of a no-brainer.
“I’ve been working in the controlled environment and greenhouse industry for 20-some years, and having a company like Lufa has brought a lot of attention to not just urban agriculture, but also the need for greenhouse production,” Lefsrud says, adding that Lufa’s success has prompted more government investment in the sector overall.
“The Quebec government now takes this as a serious venture system, which then means that the students that I’m training, and research we’re doing here at the university, now have employment and have the possibility of setting up their own system,” says the McGill professor.
That idea, of developing more vertically integrated food systems, is a passion of Hage’s—not only for the idea of cutting out production and transformation middlemen to improve profit margins, but also to improve quality, traceability, and ultimately the ethics of food production.
“You know, every time we talk to someone about it, we feel like it’s the ’80s, and we’re holding a big solar panel trying to convince the room that this is the future,” Hage says.
As the larger agricultural industry catches on to vertical integration, it seems Hage and Rathmell are no longer mad scientists with a crazy dream. Instead, they are the voice of reason—and a new generation of food.
As the larger agricultural industry catches on to vertical integration, it seems Hage and Rathmell are no longer mad scientists with a crazy dream. Instead, they are the voice of reason—and a new generation of food.
As the larger agricultural industry catches on to vertical integration, it seems Hage and Rathmell are no longer mad scientists with a crazy dream. Instead, they are the voice of reason—and a new generation of food.
NASA's Challenge To Grow Food In Space Can Win You Up To $500,000
There are thousands of bizarre challenges doing the rounds on the internet. These unique challenges soon go viral on the internet, with countless participants hopping on board. A number of these challenges also involve some form of food. If you're a food innovator who's looking for the next interesting challenge to take up, NASA (National Aeronautics and Space Administration) may have something for you. The NASA, in collaboration with Canada's CSA (Central Space Agency), has launched a 'Deep Space Food Challenge'. The one-of-a-kind competition seeks to find food production technologies which are sustainable in long duration missions to outer space.
NASA has launched a 'Deep Space Food Challenge' to prompt innovation of food production techniques and technologies viable in outer space.
Image from: Deep Space Food
There are thousands of bizarre challenges doing the rounds on the internet. These unique challenges soon go viral on the internet, with countless participants hopping on board. A number of these challenges also involve some form of food. If you're a food innovator who's looking for the next interesting challenge to take up, NASA (National Aeronautics and Space Administration) may have something for you.
The NASA, in collaboration with Canada's CSA (Central Space Agency), has launched a 'Deep Space Food Challenge'. The one-of-a-kind competition seeks to find food production technologies which are sustainable in long duration missions to outer space.
Our cargo resupply missions can only go so far! That's why we need your help to design a food system to keep our astronauts feed during long duration space exploration.
— NASA Wallops (@NASA_Wallops) January 30, 2021
Check out the @NASAPrize Deep Space Food Challenge: https://t.co/9mxtZXbwaC pic.twitter.com/izU8nSqPDc
A short video explaining the purpose behind the challenge was shared by the official handle. The 56-second clip elaborated on how astronauts embarking on lunar space exploration missions usually rely on pre-packaged meals or resupply of food through shuttles from Earth.
Thus, creating a brand, new food production system with minimal input and nutritious output with minimal wastage can go a long way in fuelling longer duration space explorations. The challenge's focus is on identifying food production technologies that can help feed a crew of four astronauts and help fill food gaps for a three-year round-trip mission with no resupply required from Earth.
These innovative food production methods may also help communities on Earth living in harsh conditions and extreme climates. This could also help tackle food insecurity in the future, which is one of the biggest issues that loom large today. "Solutions identified through this Challenge could support these harsh environments, and also support greater food production in other milder environments, including major urban centres where vertical farming, urban agriculture and other novel food production techniques can play a more significant role," stated the Deep Space Food Challenge's official website.
.@NASA & @csa_asc are launching a Deep Space Food Challenge to develop food production tech in space.
— NASA STI Program (@NASA_STI) January 28, 2021
Hey @GuyFieri, how about Diners, Drive-Ins, Dives & Deep Space? #STIdocs #Flavortown 🚀🥘
Read about it: https://t.co/fnz80uwpJT
See research: https://t.co/18q6RG3L2G pic.twitter.com/lSRTiiAFes
Registrations for the challenge close on 28th May, and submissions are due 30th July, 2021. Winners of Phase 1 of the challenge will be announced in the month of September this year. The prize money for winners of Phase 1 can go up to USD 500,000 (Rs. 3.64 crores approximately). So, if you have an exciting idea to produce food which could help future space missions - you know what to do!
Cover Crop Powers First Transatlantic Flight Using Sustainable Biojet
A United Airlines plane powered by biojet fuel made a landmark non-stop voyage from San Francisco to Zurich.
SEPTEMBER 24, 2018 LAUREN MANNING
On Monday, a United Airlines plane powered by biojet fuel made a landmark non-stop voyage from San Francisco to Zurich. Agrisoma Biosciences, a Canadian agtech company that develops Carinata seeds to produce aviation biojet fuel, partnered with United Airlines and French oil and proteins sector company Avril Group to accomplish the second international commercial flight using the company’s seed oil.
As with any startup, proof of concept is a key milestone.
“We are creating a new industry,” Hank Krakowski, Agrisoma’s Director of Sustainable Aviation, told AgFunderNews. “The question was whether the fuel is ready, and it is. Until we got through the approval process, we couldn’t talk to people about investing in contracts with us to create the feedstock for the biojet fuel.” Krakowski has deep ties to the aviation industry after working as a commercial pilot for United Airlines for 30 years. After hanging up his wings, he served as chief operating officer of the Federal Aviation Administration’s Air Traffic Organization for a few years before transitioning into aerospace investment banking. It was through this endeavor that biojet fuel and a sustainable future for aviation captured his focus.
Earlier this year, Agrisoma and Australia’s Qantas Airways partnered on a transpacific flight from Los Angeles to Melbourne that used biojet fuel produced from Carinata, which is a member of the mustard seed family.
“Qantas came to us over a year ago curious about whether we could be the source for their biofuel needs in Australia,” Krakowski explains. “Something happened that surprised us in a wonderful way: when the flight ended, over the next few months Australian farmers called us and Qantas to see how they could work with us.”
Since launching in 2001, Agrisoma has captured over $27 million in venture capital from Canadian investors, with its most recent Series C in March 2018 raising roughly $12 million. Its four investors – fund manager DesJardins Capital, impact investors Cycle Capital, Quebec-focused funders LuneRouge, and multi-stage investor BDC – all hail from Canada and seek out sustainable technologies. Krakowski hints at more financing activity for Agrisoma in the near future, but could not share more details at this time.
A Seed Company at Heart
While many might assume that Agrisoma brands itself as a biofuel company, it’s better categorized as a seed company. Agrisoma’s proprietary Carinata seed, currently being cultivated by growers in both the Americas and Australia, is a non-food, mustard-like oilseed that produces a grain that is roughly 50% oil and 50% protein. Carinata biojet fuel is made by harvesting tons of Carinata crop, crushing the grain to recover the oil, and refining that oil into jet fuel by the same process used for petroleum-derived jet fuel.
Agrisoma sells its Carinata seeds to farmers or agricultural cooperatives who then grow the seed as a cover crop and sell it back to Agrisoma. It has developed 20,000 lines of germplasm so that it can select the precise variation for different geographical locations and holds numerous patents for the germplasms.
“We have to go into different locations, do trials, sort out the right seed varieties and germplasms for that area, and then we put a two-to-five-year scale-up plan in place where we increase the acreage every year. We have to get farmers to plant and grow the seed and to harvest it correctly,” he explains. The company currently reports 50,000 acres of commercial crop growing across the Americas and Europe with the hope of doubling this acreage every year. It’s started the trial process for Carinata cultivation in Australia, New Zealand, and France.
While biojet fuel is a relatively new product in the jet fuel market, Agrisoma has found a way to slip into the existing supply chain: the company sells directly to existing refineries with biofuel production capabilities, aiming to avoid adding additional layers of complexity to the process and the existing supply chain, says Krakowski.
The biojet fuel typically replaces 10% to 30% of the petroleum jet fuel needed for a flight, making for a cleaner fuel blend that reduces greenhouse gas emissions, according to Agrisoma. Carinata is the first oilseed to be certified as sustainable by the Roundtable on Sustainable Biomaterials, an independent global standard, and certification program for sustainable biomaterials.
Competing with Conventional Jet Fuel
When it comes to industry acceptance, Agrisoma is banking on recent agreements from United Nations International Civil Aviation Organization (ICAO) encouraging airlines to achieve carbon neutral status by 2021 with the goal of claiming a 50% reduction of CO2 emissions by 2050. Carinata and the way in which the company goes about cultivating the crop offers certain environmental benefits that play directly into the ICAO’s aims.
“When you grow it, it sequesters carbon out of the atmosphere like any plant and puts it into the ground. Then, you harvest the plant, and you have a biomass that you leave behind on the ground that does a number of things: it prevents carbon from escaping and provides nutrients for the next crop growing.”
Farmers have been largely receptive to cultivating Carinata, which is used as a cover crop. This means that it doesn’t compete with traditional food growing cycles. And while other cover crops commonly don’t have a dollar value, Carinata cultivation offers farmers an additional stream of income during the off-season.
As an added bonus, Agrisoma sells the spent meal that’s leftover after the seed-crushing process for livestock feed. Because Carinata is a non-GMO seed, the meal sells at a premium to dairies producing organic products.
With some estimates suggesting that airline travel will double from current demand levels by 2040, Krakowski thinks that airlines will have no choice but to seek out sustainable fuel sources that allow them to keep pace with demand while satisfying the ICAO agreement. In fact, Agrisoma is in active discussions with a handful of oil companies about using its oil as a feedstock for biofuel production, says Krakowski.
The Sky’s the Limit
With a few successful flights under its belt, the company is focusing on increasing its acres of production and scaling up in the Americas and France, as well as Australia, New Zealand and perhaps Asia. Most startups keep a close eye on the competition, but for Agrisoma and Krakowski there is plenty of room in the biojet fuel space for additional players.
“If you look at the numbers the industry needs to meet a doubling of air commerce against biofuel availability, they will need every drop they can get from anybody who can produce biofuel regardless of where it comes from.”