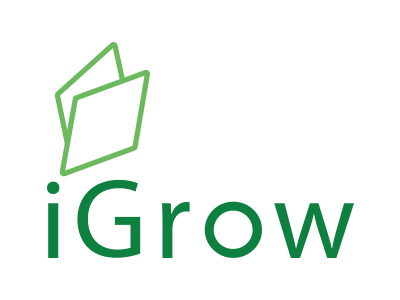
Welcome to iGrow News, Your Source for the World of Indoor Vertical Farming
Bringing Energy Management And Automation Opportunities To Indoor Farming
“We can’t be the most sustainable company in the world if we don’t work on the world’s biggest sustainability challenges,” says Travis Graham, international account manager at Schneider Electric. Schneider provides a vast array of digital technologies to multiple sectors, including horticulture
By Rebekka Boekhout
July 14, 2021
“We can’t be the most sustainable company in the world if we don’t work on the world’s biggest sustainability challenges,” says Travis Graham, international account manager at Schneider Electric. Schneider provides a vast array of digital technologies to multiple sectors, including horticulture. However, the company recently decided to strategically address the indoor farming segment and partner with growers to improve energy efficiencies within the sector.
As a global specialist in energy management and automation, Schneider’s goal is to empower the global population to improve their energy and resource use efficiency. This purpose, coined “Life is On”, aligns strongly with the spirit of indoor agriculture whose goal is to produce food and medicinal crops in an environmentally sustainable manner.
Named the world’s most sustainable company in 2021 by Corporate Knights, Schneider holds sustainability at its core and uses its century-long experience in energy management to help growers improve the energy efficiency of their facilities.
Read the rest of the article here
For more information:
Schneider Electric
www.se.com
Nature Fresh Farms And The University of Windsor Looks To Bring Clean Transportation In New Partnership
Nature Fresh Farms joins the University of Windsor in their long-haul vehicle transportation sustainability project to help achieve new advancements in energy efficient shipping.
July 5, 2021
Leamington, ON – Nature Fresh Farms joins the University of Windsor in their long-haul vehicle transportation sustainability project to help achieve new advancements in energy efficient shipping.
The purpose of this $160,000 project is to determine the impact of long-haul electric vehicles (LHEV) on Ontario’s electric grid. They will create an archetypal routing network by determining the most frequently traveled routes and then overlay the electric grid which will help determine how it will perform when managing a fleet of electric trucks. Being battery operated the trucks will look, haul, and perform similarly to diesel trucks but with zero emissions. By drawing power from the electric grid, the transport trucks would not only be able to sustainably deliver goods but also allow for the transferring of electrons back to the grid at strategic locations and times.
The project is spearheaded by Dr. Rupp Carriveau, of the Environmental Energy Institute, and his associate Dr. Hanna Maoh, of the Cross Border Institute, with the assistance of several graduate students. In addition, they are developing various industry related partnerships that will assist in different facets of their project, including Nature Fresh Farms.
“We needed a partner to help pilot our project and potentially test and Nature Fresh Farms came to mind. They are a very progressive company and are calculated risk takers that push boundaries with new technologies.” – Rupp Carriveau
The analytics and case studies are where Nature Fresh Farms comes in. The company will be able to send information from its operations which will include shipping schedules, power use, and utility costs to provide the research team with data that will determine the strengths and weaknesses of converting its fleet to electric vehicles. This information will help to examine the opportunities of electric trucks in the greenhouse industry.
“As an innovative company we are always thinking ‘what is next?’, whether its developments in product varieties, technology, or sustainability. Green transportation is the next big focus,” shared Nature Fresh Farms CEO, Peter Quiring. “We were given the opportunity to work closely on this project and offer our operations as a case study to see how we can find feasible alternatives, not only for Nature Fresh Farms or even for companies in agriculture, but for every industry that relies on the transportation of their goods.”
With the first step of the project working towards establishing an electrical grid that will manage a fleet of electric vehicles, phase two is the potential pilot study of developing and using electric long-haul vehicles for that grid. Nature Fresh Farms looks forward to the continued partnership and progression of their project with the University of Windsor and the future in the sustainable shipping of goods.
About Nature Fresh Farms - Continuously expanding, Nature Fresh Farms has become one of the largest independent, vertically integrated greenhouse vegetable farms in North America. As a year-round grower with farms in Leamington, ON, Delta, OH, and Mexico, Nature Fresh Farms prides itself on consistently delivering exceptional flavor and quality to key retailers throughout North America, while continuing to innovate and introduce more viable and sustainable growing and packaging solutions.
SOURCE: Nature Fresh Farms | info@naturefresh.ca
T: 519 326 1111 | www.naturefresh.ca
Lead Photo: CEO, Peter Quiring (Left) & Dr. Rupp Carriveau (Right)
CANADA - QUEBEC: Billionaire Project In Saint-Bruno
This project is extremely interesting because it combines data centers with greenhouses. As you may know, data centers produce huge amounts of heat
Editor’s Note: This project is extremely interesting because it combines data centers with greenhouses. As you may know, data centers produce huge amounts of heat. In the cold climate of Quebec, greenhouses could use some more heat. It will be interesting to watch this project develop, and see if this new model for using waste heat to help grow food year-round is viable!
Martin Bouchard, the founder of the Copernic search engine and the 4Degrés data centers, wants to eventually build at least three high-intensity data processing complexes including the recovery of thermal waste. The total estimated bill will be around 5 billion.
Is the plan complicated? To put this into words: artificial intelligence, innovation, circular economy, high capacity computing servers, clean energy, greenhouse production, food autonomy; stir calmly and you will obtain the successful project on which Mr. Bouchard and his associates Vincent Thibault and Dany Perron have been working for three years.
The Quebec government is receptive to this project, La Presse has learned. The role of the monopoly of electricity distribution is essential since such a data center dedicated to artificial intelligence consumes twice as much energy in a year when compared to a city the size of Drummondville.
Construction has started on the first campus located in Lévis. Completion is scheduled for November 2022. The daily Le Soleil described the main features recently. QScale is planning a second branch in the Ecoparc de Saint-Bruno-de-Montarville, on the South Shore of Montreal, just behind the commuter train station.
“Saint-Bruno would be half the size of that of Lévis, our flagship. Ultimately, our vision is to be present in the main regions of Quebec.”
— MARTIN BOUCHARD
The unveiling of financial and strategic partners will be done soon. “We would like to make an announcement in the next few months, if not the next few weeks. We are going to announce our plan to become the world's top 3 in computing. We must have our food autonomy, but also our calculation autonomy, ”emphasizes Mr. Bouchard.
The serial entrepreneur, along with private investors, invested 30 million to start the project. The rest of the financial package will be revealed at the time of the official announcement. "We are working very hard to ensure that the ownership of the company remains entirely in Quebec. "
We are talking about big bucks: from 2 to 3 billion for the Lévis complex, 1 billion for the Saint-Bruno complex.
What is it about?
QScale aims to be a data processing campus with high computational density. Campuses seek to meet the needs of machine learning, the demand for which is growing with the arrival of artificial intelligence in enterprises. Consider the data calculations required to safely move autonomous vehicles forward. Mr. Bouchard cites Tesla, Volkswagen, Pfizer, and Goldman Sachs as potential customers.
“Compared to what you would find in a conventional data center, our fridge-sized server cabinets will have five times the processing capacity. It's going to heat up even more, ” notes the 48-year-old entrepreneur. Quebec has the advantage of having clean and cheap energy.
This type of infrastructure is only just beginning to emerge in the world.
“There is not yet a leader in high density processing. Americans like Colovore, in Santa Clara, and ScaleMatrix, in San Diego, are powered by fossil fuels, without heat recovery, and with high electricity costs. We will be at least 10 times bigger than them only with Lévis.”
— MARTIN BOUCHARD
The business plan provides for the recovery of heat released by servers to heat agricultural greenhouses.
"We want to contribute to the food self-sufficiency of the province with a potential of 400 hectares of greenhouses just for the first campus," he insists. However, all greenhouse vegetable production is currently grown on 123 hectares. "For this component, we are in discussion with several players," says Mr. Bouchard. Consultant for Savoura, André Michaud confides that he has never been contacted by QScale. He said he was puzzled when he learned about the outline of the project.
"We have a greenhouse robotization project using artificial intelligence to potentially automate physically demanding jobs," retorts Mr. Bouchard. In Lévis, we have adjacent farmland which is equivalent to the equivalent of 80 football fields, enough to produce 2,880 tonnes of raspberries and 83,200 tonnes of tomatoes. "
That's not all. Mr. Bouchard wants to add to these complexes an innovation zone specializing in artificial intelligence. “The AI Zone is the missing link between basic AI research and its application in manufacturing companies. "
IQ analyzes the file
The pharaonic project has appeared on the radar screen of the Legault government. "We heard about it," said an unnamed government source. It’s an interesting file that is being looked at.
It is at Investissement Québec (IQ) that the file is analyzed. The state's financial arm was on the list of organizations QScale wanted to solicit, after being listed in the Quebec Lobbyists Registry.
As for electricity, "we already have agreements with Hydro-Quebec. Everything is in order. They are very happy. I cannot disclose anything, it will be announced. It’s very large, ”says Mr. Bouchard.
It is the user-pays principle that applies when the promoter of a project wants to have access to the Hydro-Québec network. QScale's land is conveniently located near high-power substations.
For data centers, hydro rates typically start at 4.04 cents per kilowatt-hour (kWh) when the economic development rate applies. If applicable, the price is 5.05 ¢ / kWh.
CONTENT AND IMAGE SOURCED FROM LA PRESSE
Lead photo: QScale has started construction of the first high-intensity data processing complex in Lévis. Completion is scheduled for November 2022; Image sourced from QScale
June 3, 2021
WRITTEN BY:
ANDRÉ DUBUC, AND
JULIEN ARSENAULT
MIT Engineers Have Discovered A Completely New Way of Generating Electricity
A new material made from carbon nanotubes can generate electricity by scavenging energy from its environment
By ANNE TRAFTON
MASSACHUSETTS INSTITUTE OF TECHNOLOGY
JUNE 7, 2021
MIT engineers have discovered a way to generate electricity using tiny carbon particles that can create an electric current simply by interacting with an organic solvent in which they’re floating. The particles are made from crushed carbon nanotubes (blue) coated with a Teflon-like polymer (green). Credit: Jose-Luis Olivares, MIT. Based on a figure courtesy of the researchers.
Tiny Particles Power Chemical Reactions
A new material made from carbon nanotubes can generate electricity by scavenging energy from its environment.
MIT engineers have discovered a new way of generating electricity using tiny carbon particles that can create a current simply by interacting with liquid surrounding them.
The liquid, an organic solvent, draws electrons out of the particles, generating a current that could be used to drive chemical reactions or to power micro- or nanoscale robots, the researchers say.
“This mechanism is new, and this way of generating energy is completely new,” says Michael Strano, the Carbon P. Dubbs Professor of Chemical Engineering at MIT. “This technology is intriguing because all you have to do is flow a solvent through a bed of these particles. This allows you to do electrochemistry, but with no wires.”
In a new study describing this phenomenon, the researchers showed that they could use this electric current to drive a reaction known as alcohol oxidation — an organic chemical reaction that is important in the chemical industry.
Strano is the senior author of the paper, which appears today (June 7, 2021) in Nature Communications. The lead authors of the study are MIT graduate student Albert Tianxiang Liu and former MIT researcher Yuichiro Kunai. Other authors include former graduate student Anton Cottrill, postdocs Amir Kaplan and Hyunah Kim, graduate student Ge Zhang, and recent MIT graduates Rafid Mollah and Yannick Eatmon.
Unique properties
The new discovery grew out of Strano’s research on carbon nanotubes — hollow tubes made of a lattice of carbon atoms, which have unique electrical properties. In 2010, Strano demonstrated, for the first time, that carbon nanotubes can generate “thermopower waves.” When a carbon nanotube is coated with layer of fuel, moving pulses of heat, or thermopower waves, travel along the tube, creating an electrical current.
That work led Strano and his students to uncover a related feature of carbon nanotubes. They found that when part of a nanotube is coated with a Teflon-like polymer, it creates an asymmetry that makes it possible for electrons to flow from the coated to the uncoated part of the tube, generating an electrical current. Those electrons can be drawn out by submerging the particles in a solvent that is hungry for electrons.
To harness this special capability, the researchers created electricity-generating particles by grinding up carbon nanotubes and forming them into a sheet of paper-like material. One side of each sheet was coated with a Teflon-like polymer, and the researchers then cut out small particles, which can be any shape or size. For this study, they made particles that were 250 microns by 250 microns.
When these particles are submerged in an organic solvent such as acetonitrile, the solvent adheres to the uncoated surface of the particles and begins pulling electrons out of them.
“The solvent takes electrons away, and the system tries to equilibrate by moving electrons,” Strano says. “There’s no sophisticated battery chemistry inside. It’s just a particle and you put it into solvent and it starts generating an electric field.”
“This research cleverly shows how to extract the ubiquitous (and often unnoticed) electric energy stored in an electronic material for on-site electrochemical synthesis,” says Jun Yao, an assistant professor of electrical and computer engineering at the University of Massachusetts at Amherst, who was not involved in the study. “The beauty is that it points to a generic methodology that can be readily expanded to the use of different materials and applications in different synthetic systems.”
Particle power
The current version of the particles can generate about 0.7 volts of electricity per particle. In this study, the researchers also showed that they can form arrays of hundreds of particles in a small test tube. This “packed bed” reactor generates enough energy to power a chemical reaction called an alcohol oxidation, in which alcohol is converted to an aldehyde or a ketone. Usually, this reaction is not performed using electrochemistry because it would require too much external current.
“Because the packed bed reactor is compact, it has more flexibility in terms of applications than a large electrochemical reactor,” Zhang says. “The particles can be made very small, and they don’t require any external wires in order to drive the electrochemical reaction.”
In future work, Strano hopes to use this kind of energy generation to build polymers using only carbon dioxide as a starting material. In a related project, he has already created polymers that can regenerate themselves using carbon dioxide as a building material, in a process powered by solar energy. This work is inspired by carbon fixation, the set of chemical reactions that plants use to build sugars from carbon dioxide, using energy from the sun.
In the longer term, this approach could also be used to power micro- or nanoscale robots. Strano’s lab has already begun building robots at that scale, which could one day be used as diagnostic or environmental sensors. The idea of being able to scavenge energy from the environment to power these kinds of robots is appealing, he says.
“It means you don’t have to put the energy storage onboard,” he says. “What we like about this mechanism is that you can take the energy, at least in part, from the environment.”
Reference: “Solvent-induced electrochemistry at an electrically asymmetric carbon Janus particle” by Albert Tianxiang Liu, Yuichiro Kunai, Anton L. Cottrill, Amir Kaplan, Ge Zhang, Hyunah Kim, Rafid S. Mollah, Yannick L. Eatmon, and Michael S. Strano, 7 June 2021, Nature Communications.
DOI: 10.1038/s41467-021-23038-7
The research was funded by the U.S. Department of Energy and a seed grant from the MIT Energy Initiative.
Ontario Greenhouse Installs Combined Heat Power
"We look forward to expanding our energy-efficient and sustainable system"
With the demand for greenhouse-grown produce continuing to increase, DelFrescoPure is consistently looking for ways to become more sustainable. "Ensuring high-quality produce is available year-round. Implementing a Cogeneration power plant is the most efficient way to achieve that goal," they say. As of fall 2021, DelFrescoPure will be increasing their pre-existing Cogen system by 6.5 MW, for a total of 10+ MW across their facilities.
Cogeneration or combined heat and power (CHP) is the onsite generation of electricity from the use of natural gas. The byproducts of CHP are the heat that can be stored and used to create the desired microclimate within the greenhouse and CO2 that is used to fertilize the crops. The CHP units will additionally produce the electricity required to power the grow lights as well as the mechanical load of the facility. While electricity generation alone is typically 40% efficient in converting fuel to power, adding heat recovery to the equation can bring that efficiency to 90%, a reality that suits greenhouses well.
Year-round production
DelFrescoPure intends to use the electricity to power the lights at Via Verde Hydroponics. These grow lights allow for an extended growing season, making produce that would originally be grown in the summer available all year round. The heat harnessed by CHP will also be recycled to heat the greenhouses and meet all daily power needs. Being able to produce electricity more cost-effectively onsite also means DelFrescoPure does not have to worry about voltage fluctuation from the area maxing out the local grid. With electricity no longer being a concern DelFrescoPure is primed and ready for the 25-acre expansion currently underway.
“DelFrescoPure is excited to increase our Cogeneration Power units. We are very pleased to be working with Martin Energy again to install the new CHP technology and solutions they offer. The results from using the Cogeneration technology over the past three years have been great. We look forward to expanding the system so we can continue to provide fresh produce all year long.” said Carl Mastronardi, President of Del Fresco Produce.
Along with the financial benefits, CHP power is better for the environment. This method ensures that fewer resources are wasted and required to produce electricity. The extended growing season also reduces our carbon footprint by decreasing the need for local retailers to import high milage commodities. DelFrescoPure is taking a sustainable approach to providing consumers with the freshest items possible. CHP is perfectly suited for the greenhouse environment since it is able to harness all three attributes of the technology (electricity, heat & CO2). DelFrescoPure® will never have to worry about where their energy is coming from and can continue to expand as market demand increases.
For more information:
DelFresco Pure
www.delfrescopure.com
Biggest Energy Uses When Shopping In-Store Vs Online
Competition for the title of ‘most sustainable model’ has been hotting up as online shops and traditional bricks & mortar stores try to prove their worth to environmentally conscious consumers
By George Nott
4 June 202
A delivery fleet can produce 73% of an online-only grocer’s total emissions, and the energy consumption of physical stores constitutes 60% of emissions for a traditional retailer, but which is greener?
Competition for the title of ‘most sustainable model’ has been hotting up as online shops and traditional bricks & mortar stores try to prove their worth to environmentally conscious consumers.
Retailers in both spaces have been innovating to cut emissions, implement sustainable alternatives and switch to renewable energy sources without compromising the customer experience.
Here, we compare the biggest emitters of each model.
Energy use in the store model
Lighting
A 2018 study by UCL and Brunel University found UK supermarkets had “significantly improved” and reduced energy intensity in recent years. Reductions of up to 32% have been won in lighting, much of it through the use of LED lights. Iceland ploughed £8m into sales floor LED lighting in 2015, which has delivered a 50% cut in its lighting-related emissions. More recently, it has installed automatic light controls so only half are used when stores are closed to the public and none when security alarms are activated.
Refrigeration
Supermarkets use vast amount of energy on keeping everything chilled. But that energy use is falling, thanks to the advent of new technology. A 2018 analysis of 565 supermarket stores from one retailer in the UK found the amount of energy used by refrigeration had fallen by as much as 20% in the five years to 2017. Simple solutions work. M&S is using ‘aerofoils’ on open-fronted fridges, which guide cold air down more efficiently, thereby using potentially 30% less energy.
HVAC
To keep customers comfortable, supermarkets typically maintain an in-store temperature of between 18°C and 24°C. Air-con systems have to work against bakery ovens, open chillers, customer body heat, opening entry doors, and the weather. Improvements are harder fought, with energy usage by supermarket HVAC systems falling only 8% in recent years. Tesco is using AI to fine-tune its systems. “This will optimize our heating and air conditioning through predictive algorithms,” the supermarket says.
Energy used by refrigeration fell by about 20% in the five years to 2017
Customer vehicles
Close to a third of offline retail’s carbon emissions are a result of customers individually driving from their homes to shops. The impact is more than double that of delivery vans, which make multiple deliveries, fulfilling the same amount of shopping. There are significant variables – like distance travelled. If they take public transport, walk or cycle, the emissions drop. But carrying a full basket is hardly desirable. Promisingly, Oliver Wyman predicts vehicle emissions will fall 30% by 2030.
Alternative energy
Many supermarkets are prioritizing renewable energy sources. Some have gone all out on solar energy, in particular. Aldi has around 100,000 solar panels across 400 of its UK stores and all 11 distribution centres. On average, panels power around 10% of a store’s electricity consumption each year, the discounter says. Meanwhile, M&S boasts one of the UK’s largest panel arrays at its Castle Donington DC, while Tesco recently signed a deal for 15,000 solar panels to be installed on 17 of its stores.
Energy use in the online model
Delivery vans
Vehicle emissions are responsible for the most emissions in online operations. In Ocado’s case, its fleet produces 73% of the company’s total emissions (followed by electricity at 20%).
Ocado’s proposed new Islington depot will use electric vans for customer deliveries as it works towards “operating the largest fleet of electric vans of any grocery retailer in the UK”. Restocking the site will be done using only natural gas-powered LGVs, which are up to 65% lower in emissions than diesel LGVs.
Route optimizing
The rise of online grocery has led to efficiencies thanks to the density of drop-offs that can be made by a single van. “The innovation that needs to happen, but won’t,” says Andy Needham, MD of online surplus retailer Approved Food, “is that supermarkets amalgamate deliveries so there is just one van visiting a street at any one time, instead of the current procession of an Asda van at one house, Sainsbury’s two doors down at the same time and then Tesco turning up 20 minutes later.”
’Over-packaging’ of online orders represents 23% of total parcel weight in fashion
Packaging
Oliver Wyman found “over-packaging” of online orders represents 23% of total parcel weight in fashion, 10% in books, and 18% in consumer electronics. For online grocery, above product-level packaging is minimal. While the analysis considered the impact of carrier bags “marginal”, online grocers have been confronting the problem. In April, Tesco removed the option for plastic bags and tray liners online. Meanwhile, Ocado operates a buy-back and recycling scheme for plastic carrier bags.
IT systems
The automated picking and packing systems used by online pure-players comes at a considerable energy cost. According to Oliver Wyman, IT energy consumption amounts to 178g of CO2 equivalent emissions per product for e-commerce, totaling around a fifth of total emissions. Here physical retail – despite all the checkouts, scanners, and control systems used in the space – is undoubtedly less impactful. In stores, IT emissions stand at 115g per product or 35% less than online.
CFCs
While huge grocery CFCs or ‘dark stores’ use less energy than stores, there are still improvements to be made. Major operators are joining the supermarkets in pursuing net-zero carbon targets. Logistics company Wincanton – which operates a CFC on behalf of Waitrose – this month launched a new environmental strategy that “will achieve its target to be net zero by 2040 across transport, property and waste”. Under its plans, home deliveries will be net-zero carbon throughout its network by April 2022.
Tags: Carbon Emissions Online Packaging Store design Supermarkets Sustainability & environment
CANADA: Quebec AI Processing Centers To Heat Gigantic Greenhouse Complex
A Quebec City entrepreneur, well known in the field of technology, is piloting a pharaonic project. Workers are working quietly on a large plot of land in Saint-Nicolas. The value of the total investment is in the billions of dollars
A Quebec City entrepreneur, well known in the field of technology, is piloting a pharaonic project. Workers are working quietly on a large plot of land in Saint-Nicolas. The value of the total investment is in the billions of dollars. And it would be only the first of a series of "campuses" at the cutting edge to be built on Quebec soil. And, there's greenhouses in it.
Developer Martin Bouchard, founder of the Copernic search engine and then of the 4Degree data centers, wants to build at least three high-intensity data processing complexes with thermal waste recovery, to which would be added a pole of applied innovation in artificial intelligence. The total estimated cost is close to 5 billion euros. Why that could be relevant for the horticultural industry? The business plan calls for the recovered heat being used to heat greenhouses. "We want to contribute to the province's food autonomy with a potential of 400 hectares of greenhouses for the first campus alone," he tells in an article on LaPresse.
Put the words artificial intelligence, innovation, circular economy, high-capacity computer servers, clean energy, greenhouse production, food autonomy; stir calmly and you will obtain the "Baiejamésienne" project on which Mr. Bouchard and his associates Vincent Thibault and Dany Perron have been working for three years on the QScale project.
QScale is a high-density data processing campus. The campuses seek to meet the needs of machine learning, which is in growing demand with the arrival of artificial intelligence in businesses. Consider the data calculations required to safely drive autonomous vehicles. Bouchard cites Tesla, Volkswagen, Pfizer and Goldman Sachs as potential clients.
The serial entrepreneur, along with private investors, has invested $30 million to start the project. The rest of the financial package will be revealed at the time of the official announcement. "We are working very hard to ensure that the ownership of the company remains entirely Quebec-based. "
The Quebec government is receptive to the project, La Presse has learned. Hydro-Quebec would have already said yes, assures Mr. Bouchard. The imprimatur of the monopoly of electricity distribution is essential because such a data center dedicated to artificial intelligence consumes twice as much power in a year as a city the size of Drummondville.
Construction has begun on the first campus located in Levis. Delivery is scheduled for November 2022. The daily newspaper Le Soleil recently outlined the project. QScale is planning a second branch in the Écoparc de Saint-Bruno-de-Montarville, on Montreal's South Shore, just behind the commuter train station.
With the heat, greenhouses are to be heated. "We want to contribute to the province's food autonomy with a potential of 400 hectares of greenhouses for the first campus alone," he insists. However, all the vegetable production in greenhouses is currently grown on 123 hectares. "We are in discussion with several players for this part of the project," says Bouchard. André Michaud, a consultant for Savoura, says he has never been contacted by QScale. He said he was puzzled when he saw the project outline.
We have a greenhouse robotization project using artificial intelligence to eventually automate physically demanding jobs," says Mr. Bouchard. In Levis, we have the adjacent farmland that corresponds to the equivalent of 80 soccer fields, enough to produce 2880 tons of raspberries and 83,200 tons of tomatoes. "
4 Jun 2021
VIDEOS: A Made-In-Canada Clean Energy Solution Wins Multiple Awards For Innovation
The Eavor-Loop is a closed system within which a proprietary working fluid is contained and circulated
Eavor’s technology consists of several Patent Pending innovations. The Eavor-Loop is a closed system within which a proprietary working fluid is contained and circulated. The working fluid is not fluid from a reservoir flowing into our wells, it is a fluid added to the closed-loop Eavor-Loop™ to create an efficient radiator, much like a vehicle radiator circulates fluid in a closed-loop to remove heat from a gasoline engine.
Eavor-Loop™ harvests heat from deep in the earth to be used for commercial heating applications (ex: greenhouses or district heating) or to be used to generate electricity using conventional heat to power engines. Eavor-Loop™ is an industrial-scale geothermal system that mitigates many of the issues with traditional geothermal systems, which rely upon using wells to produce brine from a subsurface aquifer.
The closed-loop is the key difference between Eavor-Loop™ and all traditional industrial-scale geothermal systems. Eavor-Loop™ is a buried-pipe system, which acts as a radiator or heat exchanger. It consists of connecting two vertical wells several kilometers deep with many horizontal multilateral wellbores several kilometers long. As these wellbores are sealed, a benign, environmentally friendly, working fluid is added to the closed-loop as a circulating fluid. This working fluid is contained within the system and isolated from the earth in the Eavor-Loop™. The wellbores act as pipes, not wells producing fluid from the earth.
The working fluid naturally circulates without requiring an external pump due to the thermosiphon effect of a hot fluid rising in the outlet well and a cool fluid falling in the inlet well. The working fluid contained in this closed-loop pipe system brings thermal energy to the surface where it is harvested for use in a commercial direct heat application or converted to electricity with a power generation module (heat engine).
Unlike heat pumps (or “geo-exchange”), which convert electricity to heat using very shallow wells, Eavor-Loop generates industrial-scale electricity or produces enough heat for the equivalent of 16,000 homes with a single installation.
An excellent new video by CNBC entitled 'How Geothermal Energy Could Power The Future' features Eavor CEO, John Redfern and several others in the modern geothermal industry such as Catherine Hickson of Geothermal Canada, Tim Latimer of Fervo Energy, Cindy Taff of Sage Geosystems and Joe Scherer of GreenFire Energy.
The video covers topics such as:
- What is Geothermal energy?
- Geothermal startups gain traction
- Major opportunity for oil and gas
- The future of geothermal
"Miles below the Earth’s surface, there’s enough thermal energy to power all of humanity for the foreseeable future. It’s called geothermal energy, and it’s poised to play an increasingly large role as a source of always available, renewable power. Now, there are a number of startups in the geothermal space, working to figure out how to access this heat in difficult-to-reach geographies, at a price point that makes sense. And it’s even gotten the attention of oil and gas industry giants, who are interested in greening their portfolios while sticking to their core competencies - extracting energy resources from deep within the Earth."
Strategic Partnership Between Oreon And Enersavings, Inc.
The energy savings possibilities of Oreon’s LED grow lights made EnerSavings recognize the advantages of the sustainable water-cooling technology
IJsselstein, 4 May 2021. Oreon and the Canadian company EnerSavings Inc. have come to an agreement for a strategic partnership. EnerSavings is a leader in customized lighting retrofits throughout Canada with a presence in 7 provinces. As a lighting engineering firm, they continuously work on improvement and innovation. EnerSavings expertise in providing the most sustainable and energy-saving solutions to its customers, fits perfectly with the sustainable water-cooling technology of Oreon’s LED grow lights.
Energy saving solutions
In EnerSavings, Oreon sees a strong partner for the Canadian market. EnerSavings is based in Toronto, Ontario, and has over a decade of experience in the ever-increasing market demand for efficient lighting technologies. The energy savings possibilities of Oreon’s LED grow lights made EnerSavings recognize the advantages of the sustainable water-cooling technology. They see lots of opportunity for growers in the fixture’s high efficiency and the ability to reuse the gained heat and save on cooling costs. The active water-cooling makes it possible for the LED fixtures to efficiently produce a large amount of light without heating up the greenhouse or grow facility. Revenues are increased by lowering operating costs, and growers get full control over the climate in their facility. This results in high-quality yields year-round.
"EnerSavings is excited to partner with Oreon and expand its presence in the North American LED plant grow light market. The Oreon water-cooled fixture is by far the best grow light in the market today, bringing the highest value proposition to growers. Oreon was the first to bring an LED grow light to market in 2009 and its fixtures are the best built, and cheapest per micromole. The water-cooling ensures productive longevity second to none. The first install over a decade ago still has over 90 percent light output today!" – Jason Beer, Business Development Director of EnerSavings.
“With EnerSavings Inc. as a new dealer, Oreon creates a better connection to the Canadian market. Both Oreon and EnerSavings share the fact that we are both committed to providing sustainable LED solutions and tailored energy-saving solutions, so customers can reduce operating expenses and increase profits. With the expertise of EnerSavings in commercial horticulture projects, we see a promising future in this rapidly growing market,” says Bill Whittaker (North-American Sales Manager) of Oreon.
Joined Up Thinking: Food & Energy Grids
This article, written by our CEO and co-founder Charlie Guy, about the connection between our energy grid and food networks, originally appeared in Volume 35 of the Journal for Food Science and Technology.
It may not always feel like it at this time of year, but on our planet we are blessed to bathe in a constant and abundant stream of energy and warmth. Effectively, all of this energy comes from the sun before being transformed, stored or used in some way. From the organic matter that once formed our fossil fuel sources, to the climatic differences that drive our weather systems and the solar panels you might have on your roof.
Food is our fundamental energy source as individuals - it powers everything that we do in our daily lives. For almost all food types, the energy used to produce it is derived from the sun (ok, mushroom-heads may argue against this, but they are still feeding on organic matter). Because of this simple concept, our food and energy systems are intrinsically intertwined. Bizarrely though, this fact is often overlooked in the food supply chain, from producers, all the way through the distribution and cold chain, right up to ourselves, the end consumers. Our current food system separates out different energy types. Heat, electricity, fuel and light often end up as mere balance sheet inputs to the production of food and many energy inputs don’t get recorded at all.
This simplified way of thinking leads to us cutting corners for the sake of cost and not considering the absolute energy impact of our food production. There are no individuals at fault here, our economic system has lined us up to think in a linear fashion for the past few centuries and this has muddied the long-held practices of stewardship for the land. Effectively, our understanding of what we give and take from nature and the sun to produce our food is no longer in balance.
If we look at the inputs and flows of energy that make up global food production, we see many areas that we may not consider when we buy food products in our local supermarkets or greengrocers. Berners-Lee et al (2018) produced a high-level analysis of the global energy flows in food production, shown in Figure 1, ultimately showing that we grow enough calories to feed everyone on our planet, but we do not use or distribute them efficiently.
Figure SEQ Figure \* ARABIC 1 - The flows of global food energy (kcal/person/day) from the amount grown to the amount eaten. For crops fed to animals, the units are based on the global human population, not animal population. The left-hand bar divides the crops grown into those that are directly edible by humans and the grass, pasture & stover that is only edible by animals. The right-hand bar divides the nutrients eaten into that required for healthy human living and net excess consumption. Animal losses include all the losses inherent in animal husbandry, such as energy used for respiration, growth, movement, and reproduction and the wastage of animal parts not used as food. DOI: https://doi.org/10.1525/elementa.310.f1
When you consider the journey of a simple soil-grown lettuce, you must consider the following energy inputs and flows as a minimum:
- Preparation – soil, seed production, transportation of seeds, drying and storage of seeds, farming infrastructure, fertilizer/pesticide production
- Growing - the sun, soil, fertilizer/pesticide application, and waste, machinery, human labor, energy use if in a greenhouse/vertical farm
- Harvesting and storage – farm machinery, fuel, refrigeration and spoilage
- Processing and packaging – transforming raw materials into products
- Transportation - cold chain refrigeration, freight by lorry, boat or long haul air travel
- Consumption - home energy usage including storage and cooking
- Waste - throughout the chain and in the home
Through each of these processes, we are either adding energy to our food on its journey to our plates or we’re losing energy through losses along the way. This is why the impact of wasting food in the home is so severe, as we are not only wasting the energy that went into producing the food, but we are also wasting the energy that was used in the supply chain along the way too. Each of these losses, even if they seem small at each stage, adds up. Taking Berners-Lee’s analysis and comparing this to electrical energy usage, the average food wasted per person is equivalent to all 7.8 billion people on our planet leaving a reasonably-sized LED TV (64W) on for 24 hours a day, 365 days a year.
Ever more work is being done in the field of lifecycle analyses to understand and bring to light the impact of our foods. These individual losses need to be understood, quantified and then reduced in our vision of a more efficient combined food and energy system.
There is a clear comparison that can be made between our current food systems and the journey that our energy systems have been on over the last few centuries. Through the various energy revolutions, we have transitioned from distributed to centralized energy and food systems. Centuries ago, we were required to balance the use of wood and food, to heat and fuel ourselves, to sustain our communities, and avoid overconsumption of either energy source. Food and fuel tended to be distributed locally to fulfill the energy needs of the community and we had a better understanding of the link between the sun, our food, our energy and the need to prevent over-consumption to remain in balance.
Fast-forward to the 21st Century and the current paradigm of large power stations that distribute electricity through grids to people, whose only connection is the vibration of their phone when they plug it in to charge. There is zero connection to how or where the energy was produced. The equivalent analogy in food production sees swathes of industrialized monocropping, focused in certain areas of the globe. Products and ingredients are shipped halfway around the world and our only connection is to open the packet and experience their flavors. Arguably there are substantial “efficiencies” and economies of scale in this kind of production model, but at what cost? Is this what we want the next chapter of our food and energy systems to look like?
Renewable energy has a huge opportunity to bring us back to a more decentralized system. In simplistic terms, the fact that the wind and sun are well distributed around the world gives the potential for much more equitable access to energy production. Renewables also bring us much closer to the only real source of energy that we have, the sun, whilst revealing our true reliance upon it as well. There are some known issues regarding renewable energy storage, but the humble chloroplasts in plants long-ago worked out how to capture this energy and store it for use later on. We can learn from this and begin to look forward with a more joined-up view of our food and energy systems. Putting our farmers and stewards at the heart of this system, ensures that links can be rebuilt between food and energy production.
So how do we link our food and energy systems back together in a way that can provide enough food for all of us in the most sustainable way? Firstly, this challenge needs to be undertaken with the concepts of sustainable intensification and circular economy principles in mind. If these are new to you, do check out the Ellen Macarthur Foundation. Secondly, we need a diversity of thinking and solutions, including both technical and business innovations. There is no silver bullet here for such a complex problem.
Many solutions in both energy and food supply are coming to the fore already, albeit independently at the moment – local energy schemes and community-supported agriculture schemes (CSAs) both enable communities to benefit from locally produced energy and food. Can we imagine a future where we bring these together into combined food and energy schemes?
Controlled environment agriculture (CEA) is one emerging practice that allows us to do things in ways that previously we have not been able to do in open-field agriculture. Using CEA, indoor farms such as greenhouses and vertical farms, enable the inputs to the growth of fresh produce to be understood, controlled and optimised. Water, nutrients, light energy and environmental conditions can all be tweaked to optimise the output of the crop and to reduce the use of resources.
These farms allow us to understand the system of growing without impacting the local environment, by ensuring efficient energy and resource flows along with recapture technologies. They enable us to build farms anywhere in the world, to grow produce in a more decentralized, resource-efficient way that can help build resilience into our food system.
Opponents of CEA will point to the increased use of energy, but this is offset by the reduced energy requirements in transportation, processing, storage, fertiliser and pesticide usage. If you understand and match your local energy and food production, this is no longer such an issue. There are still challenges for the CEA industry, but the winds are blowing in the right direction.
Increasing the renewable energy mix on the grid will reduce the cost of energy over time and is the perfect power source for indoor farms. Spiky supply and storage may appear to present an issue, but the energy profile of an indoor farm can be tuned to the supply of the grid. Plants are great at storing energy and have inherent redundancy too, hence the possibility of using plants as a new form of battery becomes very real when we see our food and energy systems as one.
There are numerous flagship examples of CEA projects implementing many of these principles worldwide. From the advanced Dutch greenhouse networks, to Sundrop Farms in Australia, to new combined heat, power and greenhouse projects in the UK such as Beeswax Dyson’s new strawberry growing facility. From Growing Underground’s vision of circular farms, to LettUs Grow’s partnership with Octopus Energy and the many projects in the pipeline with farmers around the UK looking to incorporate indoor vertical farms with existing anaerobic digestion plants. These projects show that things are moving rapidly in the right direction to bring our food and energy systems back together again.
There are still big questions to answer and challenges ahead when looking at the sustainable future of our combined food and energy systems, but we are on a very exciting journey as part of a new industry and a whole new way to look at food and energy. Joined up thinking is needed and bridges need to be rebuilt - energy and food producers will be working much closer together. To address climate change we know that we need to seriously address our energy system. And to address our energy system in full, we need to include food as a fundamental part of it.
Charlie is co-founder & Chief Executive Officer at LettUs Grow. With a background in renewable energy consultancy & engineering design, Charlie is a proponent of tech for good & passionate about all manners of sustainability, whether in food, energy, resource efficiency or waste valorisation. Charlie is also on the UKUAT (UK Urban AgriTech collective) advisory board.
Vertical Farms vs Greenhouses: Energy and LED Costs And Differences [Part 2 of 5]
Lighting is one of the biggest expenses for a vertical farm, for obvious reasons – each layer in the farm needs its own LED “suns.” Agritecture Designer, a consulting software created by Gordon-Smith’s company, estimates the need at roughly 10 LEDs per square meter
Part 2 of 5] This is the second post in a 5-part series on the differences between vertical farms and greenhouses, and the considerations that will help farming entrepreneurs decide which is right for their situation.
Last week, in the first article of this series, we discussed the basic differences between vertical farms and greenhouses, including why location is such an important factor in the decision. In short: The location of a farm governs how much space will be available for it, and the source of the energy it will use.
That last part is what you might call “the elephant in the room” when it comes to indoor farming: Energy demand, and the main reason we care about it – carbon emissions. So let’s talk about that today.
Carbon Footprint Factors: Electricity (But Not Only)
One of the leading critiques of vertical farming is that replacing natural sunlight and open-air with LED bulbs and climate control requires electricity – lots of it.
“If the source of the energy is not renewable,” points out Henry Gordon-Smith, the CEO of Agritecture, an independent consultancy that helps clients decide between vertical farms and greenhouses, “Then vertical farms have enormously more carbon footprint than greenhouses.”
But the opposite is also true – where renewables are available, vertical farming can greatly reduce the carbon footprint of foods that are normally trucked long distances, or flown in from overseas.
For example, “Norway could be huge for vertical farming, because they just have so much cheap, renewable energy,” Gordon-Smith suggested.
When you tally the emissions reductions from shorter transport distances, the reduction in fertilizer use (fertilizer production is highly carbon-intense, and Controlled Environment Agriculture uses it much more efficiently than outdoor farms), plus the reduction in food waste, it’s clear that artificial light and conditioned air inside vertical farms are not the only carbon footprint factors to consider.
Bringing the Sun Indoors: Changing Electricity Costs for Farms
Lighting is one of the biggest expenses for a vertical farm, for obvious reasons – each layer in the farm needs its own LED “suns.” Agritecture Designer, a consulting software created by Gordon-Smith’s company, estimates the need at roughly 10 LEDs per square meter.
That’s a useful figure to get started, but given the variability between types of LEDs, a more precise estimate would be about 100 watts of LED power per square meter, according to Gus van der Feltz, another CEA industry expert. Van der Feltz is a co-founder and Board Member of Farmtech Society in Belgium, and project leader for Fieldlab Vertical Farming in the Netherlands.
With these lamps operating 12 to 18 hours a day in most vertical farms, the power usage from LEDs accounts for 50 to 65% of the electricity bill.
The exact amount depends on several factors: The relative efficiency of the LEDs used, compared with the efficiency of other systems in the farm (such as climate control), as well as the light requirements of each individual crop. (For example, the total electricity required for growing light-loving strawberries in an iFarm, for example, is about 117 kWh per month for each square meter of growing space, while arugula needs only about 52 kWh.)
But whether you opt for a greenhouse or a vertical farm, you’ll be growing local produce, which means your farm may be eligible for subsidies or another form of reduced electricity rate. Be sure to check with your local government and electricity providers.
It’s also important to note that greenhouses increasingly rely on LEDs as well, especially during winter in northern climates.
This may be only supplemental light, and it will vary with the location, seasonality, and how much light each crop requires – but greenhouses are still not as energy-intensive as vertical farms.
“It takes a lot of energy to produce food (with vertical farms),” says Ramin Ebrahimnejad, vice-chair of the Association for Vertical Farming, and an expert on multiple types of urban farming.
“But,” he adds, “most vertical farms in the developed world already use renewable energy. In the long term, that’s not going to be a challenge for the industry”.
As our electricity sources become more renewable (and as LED technology improves, as we’ll discuss below) energy-intense vertical farming will become both more sustainable – less carbon-intense – and more affordable.
And we can see this evolution happening in real-time: In 2020, Europe produced more electricity from renewables than from fossil fuels for the first time.
The Cost of LEDs for Vertical Farms vs Greenhouses
LEDs themselves are another major OpEx factor in vertical farming. And even though the cost per bulb varies widely, along with the efficiency, the LEDs in a vertical farm generally have to be replaced every five to 10 years, according to the Agritecture Designer software.
However, just as the cost and carbon footprint of electricity are becoming less of a hurdle for indoor farms, the LED situation is also evolving quickly.
An idea that’s become a modern certainty is that technology gets cheaper over time. As the environmental economist William Nordhaus studied in the 1990s, the declining cost of light over the centuries – from candles, to oil lamps, to ever-more-efficient light bulbs – has been changing the world and fueling innovation for millennia.
Something similar is happening with LEDs – up to a point. Moore’s Law famously predicted computing power doubling every year, and Haitz’s Law now forecasts that the cost per lumen for LED light will fall by a factor of 10 each decade, while the light produced increases 20-fold.
However, as Van der Feltz points out, this cannot continue forever and is more limited by the laws of physics than Moore’s Law. Currently, a well-designed horticultural LED system can be up to about 55% efficient – meaning 55% of the energy put in becomes photons, which plants use to grow, and 45% becomes heat. Fifty-five percent efficiency is already impressive when compared with incandescent light bulbs, for example, where energy input produces 5% light and 95% heat.
But still, for the purpose of CEA and especially in vertical farms, the remaining 45% of the energy that becomes heat is often – though not always – useless.
“In greenhouses,” Van der Feltz explains, “the additional heat is typically not all bad. Especially since auxiliary greenhouse lighting is mostly used in the darker and cooler winter months, and there are usually plenty of options for ventilation in case it gets too warm.”
But vertical farms heat up quickly, and as closed systems where opening a window is not an option, any extra heat from LEDs must be balanced with air conditioning or creatively repurposed. Van der Feltz says some indoor farms have been designed to divert excess heat to warm an adjacent building, for example.
So LED performance can still improve marginally, but not exponentially. Van der Feltz says experts estimate that another 25% efficiency improvement is possible, but LEDs will never be able to produce light energy out of thin air.
Whatever the limits of Haitz’s Law, it’s still true that while electricity and LED light bulbs are the most expensive part of a vertical farm today, they’re also the area where improvement is most imminent. (Innovation, and the laws of supply and demand, are constantly bringing down the costs of both, regardless of how much efficiency improvement is still technologically possible.) So operating a vertical farm should still become increasingly affordable over time.
Improved technology and reduced costs for LEDs are especially good news for the potential to grow even more crops in vertical farms, as different plants use different parts of the light spectrum.
iFarm is already a leader in the industry when it comes to research and development for expanding the crop selection available to vertical farmers. As LED technology improves, we’ll be able to take those efforts even further.
Other Energy Costs: Climate Control Needs in Vertical Farms vs. Greenhouses
The high energy costs of lighting a vertical farm are obvious, but the demands of climate control are often not as clear.
Since vertical farms are closed systems, with little to no air exchanged with the outside, they must be constantly cooled and dehumidified. About 20% of the electricity used on a vertical farm is for air conditioning, while dehumidifiers account for 10%.
The need for both of these increases with each layer added to a vertical farm, in order to counter the effects of plants transpiring and increasing the heat and humidity of the system.
In temperate regions, greenhouses can save energy by using natural ventilation, as the Agritecture Designer program explains: Sidewalls can roll up to allow cool air in, while hot air escapes through vents at the top of the greenhouse. Greenhouses can also opt for an evaporative cooling system, which is still more energy efficient than a fully climate-controlled system but does add humidity – another element to be controlled.
But it’s also important to remember that greenhouses are more sensitive to outside temperatures, and therefore, the operational expenses of climate control and/or the time needed for crops to mature will vary more than they will with vertical farms – especially in cold, Northern climates.
Next, in Part 3, we’ll discuss additional cost considerations for vertical farms and greenhouses, beyond electricity.
To learn more about starting a profitable vertical farming business, reach out to our friendly team at iFarm today!
Learn more
09.03.2021
A New FEZ "Karakalpak-Agro" Established In Uzbekistan
“….increasing the production of agricultural products, expanding its deep processing and increasing exports, effectively using the production potential of the region…”
Tashkent, Uzbekistan (UzDaily.com) - The Cabinet of Ministers adopted a resolution”On measures to organize the activities of the free economic zone “Karakalpak-Agro”.
In accordance with the decree of the President “On measures for the comprehensive socio-economic development of the Republic of Karakalpakstan in 2020–2023” on an area of 875.4 hectares in Amu Darya, Buzatausky, Kegeili, Konlikul, Kushgirot, Muynak, Nukus , Takhiatash, Turtkul, Khodjeyli, Shumanai and Ellikala districts, the SEZ "Karakalpak-agro" was created.
The functions of managing the activities of the FEZ "Karakalpak-Agro" are assigned to the State Unitary Enterprise "Directorate of the free economic zone" Nukus ".
The main tasks and directions of the SEZ "Karakalpak-Agro":
- attracting direct foreign and domestic investments for organizing modern greenhouses on a cluster basis, including hydroponic ones, as well as organizing the production of structures, equipment and other components for the construction of modern energy-efficient greenhouses;
- increasing the production of agricultural products, expanding its deep processing and increasing exports, effectively using the production potential of the region;
- encouraging the organization of the complete process of agricultural production from seeds to delivery to the market;
- introduction of effective mechanisms for providing greenhouses with seeds and seedlings of high-yielding crops demanded by the market, by creating conditions for organizing nurseries, as well as seed production;
- formation of a modern infrastructure for the provision of logistics services, assistance to agricultural producers in organizing the export of their products;
- widespread introduction of modern resource-saving technologies, the use of alternative sources of thermal energy in the organization of greenhouses;
- creation of research and production centers to assess the compliance of products with international standards.
The Council of Ministers of Karakalpakstan, together with the Ministry of Investments and Foreign Trade, the Chamber of Commerce and Industry and commercial banks, was instructed to develop a targeted program of facilities for the production of structures for greenhouses on the territory of Karakalpak-Agro within two months, with the allocation of vacant non-agricultural land.
Hydroponics Greenhouse Provides Hands-On Learning At Hudson High School
A $20,000 grant was given by The Kiwanis Club of Hudson to support the project, and this money was used to purchase greenhouse equipment.
Yeji Kim
Special to the Hudson Hub-Times
A Jan. 15 tour led by HHS AP Environmental Science teacher Matthew Kearns offered members of The Kiwanis Club of Hudson insight into the hydroponic greenhouse. The club donated a $20,000 grant to help fund the project. Submitted Photo
Project-based learning is a learning model where students work together to engage in real-world questions and problems, and the Hudson High School hydroponics greenhouse centres around this approach to education.
The hydroponics greenhouse started roughly two years ago, and Phillip Herman, Superintendent of the Hudson City School District, and Christina Wooley, HCSD Curriculum Coordinator, are credited with most of the original idea.
Herman first learned about hydroponics gardening and greenhouses from a community member and thought there may be a way to better utilize the HHS greenhouse space to create learning opportunities for students. He began by discussing the idea with teachers, visiting an operating hydroponics greenhouse and exploring areas of the curriculum that could be enhanced.
The first year consisted largely of planning, strategizing and raising money, and this past year was when equipment started to come in and crops began to grow.
A hydroponics greenhouse differs from a traditional greenhouse in that no soil is required. Instead, the plants draw up nutrient-rich water. Less water is used since the water is recycled, and because of the absence of soil, hydroponics greenhouses take up less space — the plants can be stacked vertically. The HHS hydroponics greenhouse also includes a monitoring computer system that measures what is currently in the water and what will be needed.
A $20,000 grant was given by The Kiwanis Club of Hudson to support the project, and this money was used to purchase greenhouse equipment.
CropKing, an Ohio-based hydroponics equipment company, was the supplier for the equipment, seeds and fertilizer, and the firm also aided in setting up the equipment and trained those involved with the greenhouse.
Two other grants, an ADAR grant and a grant from the Hudson Parent-Teacher Organization supplemented the Kiwanis grant money. The greenhouse itself is located off of HHS biology classes and has been there before the hydroponics greenhouse was started.
Students are faced with real-world questions, such as how to sustain crops in regions without sufficient access to water, ways to use the land effectively and properly, impacts on the environment and how to grow sustainably and locally.
Science teacher Matthew Kearns said students have been seeing the benefit of this project, which includes those in the AP Environmental Science class he teaches, special education students who work with Intervention Specialist Kristin Stonestreet and biology classes taught by Ron Wright. Students visit at least once a week to monitor the crops.
Currently, the greenhouse is growing its first round of crops, which includes lettuce, tomatoes and cucumbers.
Stonestreet and Kearns are considering adding cilantro, basil and peppers as well. The diversification would enhance the project-based learning aspect, as students will need to work together to figure out how much additional lighting and heat every crop needs.
The long term goal is to get involved with the community; through connecting with the business department and forming a club, students plan to sell produce from the greenhouse at the Hudson Farmers Market in the summertime and sell to HCSD faculty and staff when school is in session, engaging aspects of science, business and team-work. Several potential products for sale in the future include a salsa kit, tomato sauce and fresh herbs.
Herman notes how this greenhouse works to enhance classroom activity and curriculum.
“Over recent years, we have continued to learn more about and explore opportunities for project-based learning. Project-based learning enables students to learn course content and develop other essential success skills by beginning with a challenging problem or question and conducting a sustained inquiry to explore solutions to the problem and answers to their questions. Together, Christina Wooley, Mr Kearns and Mrs Stonestreet dug in and worked collaboratively to do the hard work to bring an idea to implementation.”
Belgian Bio-Planet Now Sells Vertically-Farmed Coriander Too
For us, the story didn't end with sustainable basil.
Just under a year ago, Bio-Planet first introduced its basil to the market. This came from this Belgian store's self-developed vertical farm. "This cultivation method differs from conventional farming. It requires less water and space and fewer nutrients. That results in herbs with tiny ecological footprints. For us, the story didn't end with sustainable basil. We now have the technique down for coriander. We've been selling this second vertically-farmed herb since 19 February. That's in the Bio-Planet webshop and 31 stores", says a representative from this supermarket chain.
"Consistent, year-round quality"
"The Colruyt Group is the only retailer in Belgium with its a self-developed vertical farm. It grew basil plants for Bio-Planet last year. That was in a closed system, in two rows, one above the other. The group could, therefore, test out its vertical farm for a year. That was in all aspects, from production through logistics to sales. And the results are impressive. In a challenging year, we managed to guarantee a stable production of quality basil plants," says Jan Van Holsbeke, Bio-Planet's Manager.
"The global pandemic ensured it wasn't the easiest test year. We had to scale up our vertical farm. That's was due to the increased sales in our stores. At the same time, this demonstrates the power of indoor multilayer cultivation. We can create the perfect growing conditions, regardless of the weather. That means the herbs have consistent, year-round quality. And we can match production to demand." And demand there certainly was. More people bought fresh basil from Bio-Planet last year than the previous year.
"Coriander with a tiny environmental footprint"
Bio-Planet sees potential in this new farming method. They can grow herbs with a minimal ecological footprint. "Up to 20 times less space is needed the same number of plants. They also need 50% fewer nutrients and 90% less water. The herbs are 100% pure too because no pesticides are used," adds the company spokesperson.
"We integrated the farm into one of the group's distribution centres. So, transportation was cut five-fold. The farm uses purified rainwater that's collected on the DC's roof. It has self-developed, energy-efficient LED lighting and an innovative ventilation system. These make the farm very energy efficient. Moreover, the system runs on 100% green electricity. This is generated by wind turbines and solar panels."
“All these factors make the farm and its herbs very sustainable. That's crucial for Bio-Planet. We want to offer our shoppers sustainable, local, innovative products. We think other herbs and even leafy green vegetables can be vertically-farmed too. This, however, requires more research and investment. Also, the technology has to be further developed," concludes Jan.
Bringing The Future To life In Abu Dhabi
A cluster of shipping containers in a city centre is about the last place you’d expect to find salad growing. Yet for the past year, vertical farming startup Madar Farms has been using this site in Masdar City, Abu Dhabi, to grow leafy green vegetables using 95 per cent less water than traditional agriculture
Amid the deserts of Abu Dhabi, a new wave of entrepreneurs and innovators are sowing the seeds of a more sustainable future.
Image from: Wired
A cluster of shipping containers in a city centre is about the last place you’d expect to find salad growing. Yet for the past year, vertical farming startup Madar Farms has been using this site in Masdar City, Abu Dhabi, to grow leafy green vegetables using 95 per cent less water than traditional agriculture.
Madar Farms is one of a number of agtech startups benefitting from a package of incentives from the Abu Dhabi Investment Office (ADIO) aimed at spurring the development of innovative solutions for sustainable desert farming. The partnership is part of ADIO’s $545 million Innovation Programme dedicated to supporting companies in high-growth areas.
“Abu Dhabi is pressing ahead with our mission to ‘turn the desert green’,” explained H.E. Dr. Tariq Bin Hendi, Director General of ADIO, in November 2020. “We have created an environment where innovative ideas can flourish and the companies we partnered with earlier this year are already propelling the growth of Abu Dhabi’s 24,000 farms.”
The pandemic has made food supply a critical concern across the entire world, combined with the effects of population growth and climate change, which are stretching the capacity of less efficient traditional farming methods. Abu Dhabi’s pioneering efforts to drive agricultural innovation have been gathering pace and look set to produce cutting-edge solutions addressing food security challenges.
Beyond work supporting the application of novel agricultural technologies, Abu Dhabi is also investing in foundational research and development to tackle this growing problem.
In December, the emirate’s recently created Advanced Technology Research Council [ATRC], responsible for defining Abu Dhabi’s R&D strategy and establishing the emirate and the wider UAE as a desired home for advanced technology talent, announced a four-year competition with a $15 million prize for food security research. Launched through ATRC’s project management arm, ASPIRE, in partnership with the XPRIZE Foundation, the award will support the development of environmentally-friendly protein alternatives with the aim to "feed the next billion".
Image from: Madar Farms
Global Challenges, Local Solutions
Food security is far from the only global challenge on the emirate’s R&D menu. In November 2020, the ATRC announced the launch of the Technology Innovation Institute (TII), created to support applied research on the key priorities of quantum research, autonomous robotics, cryptography, advanced materials, digital security, directed energy and secure systems.
“The technologies under development at TII are not randomly selected,” explains the centre’s secretary general Faisal Al Bannai. “This research will complement fields that are of national importance. Quantum technologies and cryptography are crucial for protecting critical infrastructure, for example, while directed energy research has use-cases in healthcare. But beyond this, the technologies and research of TII will have global impact.”
Future research directions will be developed by the ATRC’s ASPIRE pillar, in collaboration with stakeholders from across a diverse range of industry sectors.
“ASPIRE defines the problem, sets milestones, and monitors the progress of the projects,” Al Bannai says. “It will also make impactful decisions related to the selection of research partners and the allocation of funding, to ensure that their R&D priorities align with Abu Dhabi and the UAE's broader development goals.”
Image from: Agritecture
Nurturing Next-Generation Talent
To address these challenges, ATRC’s first initiative is a talent development programme, NexTech, which has begun the recruitment of 125 local researchers, who will work across 31 projects in collaboration with 23 world-leading research centres.
Alongside universities and research institutes from across the US, the UK, Europe and South America, these partners include Abu Dhabi’s own Khalifa University, and Mohamed bin Zayed University of Artificial Intelligence, the world’s first graduate-level institute focused on artificial intelligence.
“Our aim is to up skill the researchers by allowing them to work across various disciplines in collaboration with world-renowned experts,” Al Bannai says.
Beyond academic collaborators, TII is also working with a number of industry partners, such as hyperloop technology company, Virgin Hyperloop. Such industry collaborations, Al Bannai points out, are essential to ensuring that TII research directly tackles relevant problems and has a smooth path to commercial impact in order to fuel job creation across the UAE.
“By engaging with top global talent, universities and research institutions and industry players, TII connects an intellectual community,” he says. “This reinforces Abu Dhabi and the UAE’s status as a global hub for innovation and contributes to the broader development of the knowledge-based economy.”
Signify Adds Automatic Intensity Adjustment Plus Year-Long Recipe Modulations To Horticultural Controls
There’s something for both the greenhouse and the vertical farm in the GrowWise tweaks, which in some cases rely on tying to other systems’ sensors.
The Signify toplights at Belgium’s De Glastuin lettuce greenhouse automatically dim or brighten as daylight levels changes. (Photo credit: All images courtesy of Signify.)
Signify has enhanced the control system for its greenhouse LED lighting so that toplights can react immediately to changes in daylight conditions and adjust brightness accordingly. The company has also added year-long control settings intended to allow vertical farmers — but not greenhouses — to program seasonal variations in LED spectral content over a 365-day period.
Both upgrades are intended to reduce manual labor and improve overall cost efficiencies, Signify said.
Until now, greenhouse farmers could dim or brighten their Signify toplights by instructing the lights to do so via the control system, called GrowWise. Signify has now modified GrowWise software so that it can take readings from daylight sensors that are part of separate systems. GrowWise then instantly and automatically adjusts artificial light intensity emitted by the toplights, called Philips GreenPower LED.
“The lighting can be used much more efficiently since it gives us the flexibility to reduce light levels at any moment we need to,” said Wouter de Bruyn, the owner of Belgian lettuce grower De Glastuin, an early user of the new automatic feature.
Whereas Signify is known in office settings to build sensors into its smart luminaires, the GrowWise controls make use of sensors that are part of climate control systems and greenhouse management systems from companies such as Priva, Hoogendern Growth Management, and Ridder, all based in Holland.
Planet Farms’ Luca Travaglini backs up Signify’s point that prescribing a year of spectral content improves efficiency and helps keep down manual labor costs in controlled environment agriculture (CEA) operations such as vertical farms.
“The climate computer is equipped with a daylight sensor that sends actual light measurements to the GrowWise Control System so we can adapt our light levels automatically to ensure an even light level throughout the day and season,” de Bruyn said at De Glastuin, based in Kontich.
“Dynamic lighting in a greenhouse is the next step in improving the cost efficiency and quality for the cultivation process,” said Udo van Slooten, business leader, horticulture LED solutions at Signify. “It allows growers to effortlessly maintain a consistent level of light throughout the day to produce the best possible crops. The system compensates for cloudy weather and creates a more controlled growing environment for your crop.”
In another upgrade to GrowWise, vertical farmers who want to prescribe modulations in spectral content are no longer limited to 24 hours of looped recipe cycles. Rather, they can order up a year’s worth of shifts for controlled environment agriculture (CEA) operations.
The year-long programming feature is aimed at vertical farmers rather than at greenhouses because the lights that Signify provides for vertical farms support controllable spectral changes, whereas the greenhouse toplights do not. Signify refers to its GreenPower LED vertical farm lights as “production modules” rather than as “toplights.” Toplights and production modules can both be programmed for intensity over a year, but the intention of the year-long feature is oriented toward spectral content.
Compared to greenhouses, vertical farms tend to make much less, if any, use of natural light. In vertical farms, the lights are mounted much closer to the crop in stacked shelves.
One of the first users of the year-round feature is Italy’s greens and lettuce grower Planet Farms.
“Now we can easily create custom light recipes and set them to run year-round to provide the right light recipe with the right light intensity at the right time throughout the crop’s growth cycle,” said Planet Farms co-founder Luca Travaglini. “By automating our full light strategy during the growth cycle, for the whole year, we can run our operations very efficiently and keep our manual labor costs low. That makes it easier for us to maintain consistent quality as we scale up our production.”
The horticultural market is a key growth sector for Signify, especially as it maps out a strategy to maintain profits in the pandemic economy, in which last week it reported a yearly rise amid rigorous cost controls that now include a small number of layoffs. CEO Eric Rondolat is targeting a big chunk of what he has quantified as a $2 billion general horticultural lighting market by 2023.
MARK HALPER is a contributing editor for LEDs Magazine, and an energy, technology, and business journalist (markhalper@aol.com).
IPO Planned To Improve Revenues Indoors
Light Science Technologies has gained the funding from Intuitive Investments Group plc (IIG), ahead of going public on the London Stock Exchange in the next six months.
8-01-2021| Business Live
“We believe that there is no better time to be involved in both agritech and medtech." A company which makes technology to improve indoor crop yields has received a £1 million investment ahead of a planned IPO.
Light Science Technologies has gained the funding from Intuitive Investments Group plc (IIG), ahead of going public on the London Stock Exchange in the next six months.
The business, based on the Hilton Business Park, Derby, provides lighting and plant growing and monitoring technology for agriculture in partnership with university research teams.
Its agricultural tech can be used in three main indoor settings – vertical farming (where crops such as tomatoes are grown in vertically stacked layers), greenhouses and medicinal plants.
Its patent-pending, sustainable light unit combines interchangeable LEDs, power and technology to help reduce costs and generate maximum yields over 25 years.
Its real-time monitoring and control technology can also be used to link technicians, farmers, and facility managers with their crops to provide instant production data.
Management said that with better light quality and energy savings, its light, science and technology products increase cycles.
It also supplies technology to clients in the electronics, audio, automotive, AI technology and pest control sectors.
The move to become a publicly listed company follows significant investment in its team and operations over the past few years which, the business said, has “brought to market a fully updateable, bespoke and intelligent lighting solution that provides optimal yield”.
The company is also due to launch its own in-house growth and laboratory service in the spring, focusing on plant growth and performance to help farmers with their crops.
Chief executive Simon Deacon said: “We believe that there is no better time to be involved in both agritech and medtech as two rapidly expanding sectors which are going to be responsible for spearheading some of the most significant global developments over the coming decade and beyond.
“IIG’s investment is not just a reflection of its commitment to LSTH as a fast-growing business backed by almost 30 years’ expertise in light technology but also of its awareness of the importance in achieving a better, more sustainable approach to agricultural production as well as pioneering potential life-saving solutions in digital health innovation.”
Light Science Technologies is IIG’s first investment following its own successful IPO and admission to AIM in December, as it seeks to attract investors with its life sciences portfolio.
IIG chairman David Evans said: “LSTH has the key ingredients for success; it has an excellent management team, a deep knowledge of the light spectrum and the application of that knowledge to areas where substantial growth can be obtained.
“I am personally excited about the potential diagnostic applications in the digital health sector, such as non-invasive haemoglobin measurement, as well as the developments in vertical farming technology that will underpin the long-term growth of LSTH.”
The investment follows recent funding for Light Science Technologies from Innovate UK which will see it work over the next six months with Nottingham Trent University to develop a growing sensor and transmission node for vertical farms.
Photo: Light Science Technologies designs lighting, science and plant monitoring technology.
Source and Photo Courtesy of BusinessLive
Combining Hydroponic And Aeroponic In Vertical Farming
Growers are finding new ways to drive the efficiency up and the cost down, and one of these solutions is vertical farming.
Generally speaking, horticulture operations can be quite expensive to operate; yet, growers can rely on hundreds of years of knowledge to improve the efficiency, so that those costs go down. At the same time, indoor farming cannot rely on such knowledge, and it is not uncommon to see cultivation facilities with huge bills at the end of the month. As the industry matures, growers are finding new ways to drive the efficiency up and the cost down, and one of these solutions is vertical farming.
LED technology
Nowadays, LED technology has made a huge leap forward, and Alvis Ma, the CEO of GrowSpec claims they are the industry standard. “Growers generally make the switch from HPS to LED for three reasons: increased yield, improved cannabinoid, and terpene content, and energy efficiency,” he explains. Thus, LEDs allow for vertical cultivation, which has a host of benefits, especially when it comes to space optimization.
“The VetriAero Planter system uses a mobile planting rack that reduces the ‘required’ indoor grow space area and extends the plant cultivation space by multiple tiers, maximizing growth space, increasing the yield and thus the profit,” Alvis Ma points out. “And if a grower wants to use one rack only initially, other tiers can be added later on: the helves can be connected to one another so that growers can modify the VetriAero Planter system length according to the size of the room.”
A very peculiar feature of this system is the integration of both aeroponic and hydroponic methods. “Instead of growing in soil, the roots are suspended in mid-air and surrounded by oxygen,” he adds. “The plant roots get misted directly with a nutrient-dense solution that gets sprayed to the roots every 3-5 minutes. At the same time, the remaining liquid at the bottom of our container ensures that, in the event of an emergency, there is still enough nutrient-dense liquid to sustain your plants for up to 48 hours.”
“Commercial indoor cultivation operations can be very expensive,” says Alvis Ma with GrowSpec. “And if you look at the cost of the real estate, added on top of substantial
power bills and staffing requirements, it becomes critical to find a way to increase profit and reduce overhead costs.” Exactly to respond to such a demand, GrowSpec has developed the VertiAero Planter system, a new vertical growing system. “One of the primary reasons why vertical farming is so attractive for growers is the improved performance of current LEDs,” Alvis Ma continues. “This is something that could not happen back in the day, as HPS has been the go-to lights for decades, and they produce a lot of heat; generally speaking, the plants have to be placed a couple of feet away from light to stay safe and healthy.”
Controlling the environment
Indoor growing, especially vertical growing, requires a particularly efficient airflow system to guarantee healthy growth for the plants. This has direct consequences on the growing environment. “Maintaining optimum temperature, humidity, and air circulation is challenging for all cannabis operations,” Alvis Ma remarks. “But in vertical growing, there is even more variability in macro and micro environmental conditions, because more plants make control more difficult.
That’s why the GrowSpec VertiAero’s multi-layer airflow solution improves the airflow rate in the micro-environment of the plant canopy by maintaining consistent plant canopy temperature and humidity, reducing the cultivation potential of harmful pathogens, and increasing the rate of photosynthesis by evenly distributing CO2 over the plant canopy. The system utilizes various sensors to detect crucial data points such as moisture change, for instance.”
Although such a system might sound complicated to use, user-friendliness and easiness of use are very well implemented. “The VertiAero Planter system integrates intelligent control and touchscreen control system so that your business can save up exponentially on overhead costs,” Alvis Ma points out. “At our core, we operate according to the highest standard, combining this with technology that respects our planet.”
For more information:
GrowSpec
Yuxin Industry Zone, Shishan Town, Nanhai, Foshan, Guangdong, China
+86-15914220731
Pilot Project To Recycle Crypto Mining Farm Energy Waste Into Energy For Greenhouses
The pilot project's objective is to address concerns about the excess energy waste generated by crypto mining facilities while also supporting the government's objective to become more self-sufficient in food production, rather than relying on imports
Genesis Mining has announced the launch of a new pilot project that will focus on recycling excess energy waste from crypto mining facilities into sustainable heat and energy to power greenhouses.
The pilot project's objective is to address concerns about the excess energy waste generated by crypto mining facilities while also supporting the government's objective to become more self-sufficient in food production, rather than relying on imports.
Commenting on this potential, Mattias Vesterlund, Senior Researcher at RISE (Research Institutes of Sweden), said, "A 1 MW data center would have the ability to strengthen the local self-sufficiency up to 8% with products that are competitive on the market."
The project is a private-public partnership between Systemair, Lulea Technical University, RISE (Research Institutes of Sweden), Boden Business Agency, the local Boden municipality, and Genesis Mining's philanthropic arm, Hashpower For Science. It's located in Boden, Sweden, and has been in development for over one year.
Boden Business Agency's Nils Lindh, said, "This project is exciting because there is an opportunity to contribute in scaling up the food industry and at the same time meet the national energy efficiency targets. It's the first of many projects within the Energy Symbiosis, and hopefully, the results will show that it's very possible to scale up into large commercial production."
For the initial pilot project, one of Genesis Mining's custom-built crypto mining storage containers will be placed near the greenhouse. The greenhouse and container are connected via a custom-built air duct system that carries the excess energy directly from the crypto mining storage container into the greenhouse.
Andreas Johansson, a Senior Lecturer from Lulea Technical University, who is making the calculations for designing the system for air flow from the datacenter to the greenhouse, said, "For the cold climate in the north of Sweden, our calculations show that a 300 m2 greenhouse can easily be heated with a 550 kW container, even with outdoor temperatures reaching almost -30℃. But the potential is much bigger than that. The temperature difference over the greenhouse is in this calculation only 10 degrees since we assume a DC output temp of 35℃ and a GH temp of 25℃. If the DC output is increased to 55℃, then the GH area can be tripled to 900 m2."
Genesis Mining's CEO and co-founder Marco Streng said, "Crypto mining is the backbone that makes decentralized cryptocurrencies and applications possible, and we strongly believe the benefits of this decentralization will transform the world, but all those benefits can't come at the cost of the environment."
As one of the world's largest crypto mining companies with over a dozen data centers spread across the globe, Genesis Mining's R&D team has been actively working on different solutions and collaborations to enable more sustainable crypto mining facilities.
"Genesis Mining has always preferred locations that offered 100% renewable energy sources, that's why we've focused so much on the Nordics. But as the industry leader, we view it as our moral and ethical responsibility to push the industry forward, and finding a way to convert our excess energy has been a major priority. We look forward to scaling this project and bringing it to not only more of our own datacenters — but to others as well."
A Monster Wind Turbine Is Upending An Industry
Twirling above a strip of land at the mouth of Rotterdam’s harbor is a wind turbine so large it is difficult to photograph. The turning diameter of its rotor is longer than two American football fields end to end
G.E.’s Giant Machine, Which
Can Light Up A Small Town,
Is Stoking A Renewable-Energy Arms Race
By Stanley Reed
January 1, 2021
Twirling above a strip of land at the mouth of Rotterdam’s harbor is a wind turbine so large it is difficult to photograph. The turning diameter of its rotor is longer than two American football fields end to end. Later models will be taller than any building on the mainland of Western Europe.
Packed with sensors gathering data on wind speeds, electricity output and stresses on its components, the giant whirling machine in the Netherlands is a test model for a new series of giant offshore wind turbines planned by General Electric. When assembled in arrays, the wind machines have the potential to power cities, supplanting the emissions-spewing coal- or natural gas-fired plants that form the backbones of many electric systems today.
G.E. has yet to install one of these machines in ocean water. As a relative newcomer to the offshore wind business, the company faces questions about how quickly and efficiently it can scale up production to build and install hundreds of the turbines.
But already the giant turbines have turned heads in the industry. A top executive at the world’s leading wind farm developer called it a “bit of a leapfrog over the latest technology.” And an analyst said the machine’s size and advance sales had “shaken the industry.”
A New Generation of Wind Turbines
General Electric’s prototype for a new offshore wind turbine, the Haliade-X, is the largest ever built.
London Eye - Ferris wheel GE Haliade-X 13MW - wind turbine Empire State Building
HEIGHT: 443 feet HEIGHT: 853 feet HEIGHT: 1,050 feet
Source: General Electric
The prototype is the first of a generation of new machines that are about a third more powerful than the largest already in commercial service. As such, it is changing the business calculations of wind equipment makers, developers, and investors.
The turning diameter of the Haliade-X’s rotor is longer than two American football fields.Credit...Ilvy Njiokiktjien for The New York Times
The G.E. machines will have a generating capacity that would have been almost unimaginable a decade ago. A single one will be able to turn out 13 megawatts of power, enough to light up a town of roughly 12,000 homes.
The turbine, which is capable of producing as much thrust as the four engines of a Boeing 747 jet, according to G.E., will be deployed at sea, where developers have learned that they can plant larger and more numerous turbines than on land to capture breezes that are stronger and more reliable.
The race to build bigger turbines has moved faster than many industry figures foresaw. G.E.’s Haliade-X generates almost 30 times more electricity than the first offshore machines installed off Denmark in 1991.
In coming years, customers are likely to demand even bigger machines, industry executives say. On the other hand, they predict that, just as commercial airliners peaked with the Airbus A380, turbines will reach a point where greater size no longer makes economic sense.
“We will also reach a plateau; we just don’t know where it is yet,” said Morten Pilgaard Rasmussen, chief technology officer of the offshore wind unit of Siemens Gamesa Renewable Energy, the leading maker of offshore turbines.
The turbine is so large that it will be able to generate enough power to light up a town of 12,000 homes. Credit...Ilvy Njiokiktjien for The New York Times
Although offshore turbines now account for only about 5 percent of the generating capacity of the overall wind industry, this part of the business has taken on an identity of its own and is expected to grow faster in the coming years than land-based wind.
Offshore technology took hold in Northern Europe in the last three decades and is now spreading to the East Coast of the United States as well as Asia, including Taiwan, China and South Korea. The big-ticket projects costing billions of dollars that are possible at sea are attracting large investors, including oil companies like BP and Royal Dutch Shell, that want to quickly enhance their green energy offerings. Capital investment in offshore wind has more than tripled over the last decade to $26 billion, according to the International Energy Agency, the Paris-based forecasting group.
G.E. began making inroads in wind power in 2002 when it bought Enron’s land-based turbine business — a successful unit in a company brought down in a spectacular accounting scandal — at a bankruptcy auction. It was a marginal force in the offshore industry when its executives decided to try to crack it about four years ago. They saw a growing market with only a couple of serious Western competitors.
Still, G.E.’s bosses figured that to become a leader in the more challenging marine environment, they needed to be audacious. They proceeded to more than double the size of their existing offshore machine, which came to G.E. through its acquisition of the power business of France’s Alstom in 2015. The idea was to gain a lead on key competitors like Siemens Gamesa and Vestas Wind Systems, the Danish-based turbine maker.
A larger turbine produces more electricity and, thus, more revenue than a smaller machine. Size also helps reduce the costs of building and maintaining a wind farm because fewer turbines are required to produce a given amount of power.
These qualities create a powerful incentive for developers to go for the largest machine available to aid their efforts to win the auctions for offshore power supply deals that many countries have adopted. These auctions vary in format, but developers compete to provide power over a number of years for the lowest price.
The prototype is on a piece of land in Rotterdam Harbor, but the Haliade-X is designed as an offshore turbine, to be planted in relatively shallow sea water. Credit...Ilvy Njiokiktjien for The New York Times
“What they are looking for is a turbine that allows them to win these auctions,” said Vincent Schellings, who has headed design and production of the G.E. turbine. “That is where turbine size plays a very important role.”
Among the early customers is Orsted, a Danish company that is the world’s largest developer of offshore wind farms. It has a preliminary agreement to buy about 90 of the Haliade-X machines for a project called Ocean Wind off Atlantic City, N.J.
“I think they surprised everybody when they came out with that machine,” said David Hardy, chief executive of Orsted’s offshore business in North America.
As a huge buyer of turbines, Orsted wants to help “establish this new platform and create some volume for G.E.” so as to promote competition and innovation, Mr. Hardy said.
The G.E. turbine is selling better than its competitors may have expected, analysts say.
On Dec. 1, G.E. reached another preliminary agreement to provide turbines for Vineyard Wind, a large wind farm off Massachusetts, and it has deals to supply 276 turbines to what is likely to be the world’s largest wind farm at Dogger Bank off Britain.
One day turbines will reach a size limit, but “we just don’t know where it is yet,” said Morten Pilgaard Rasmussen of Siemens Gamesa Renewable Energy. Credit...Carsten Snejbjerg for The New York Times
These deals, with accompanying maintenance contracts, could add up to $13 billion, estimates Shashi Barla, principal wind analyst at Wood Mackenzie, a market research firm.
The waves made by the G.E. machine have pushed Siemens Gamesa to announce a series of competing turbines. Vestas, which until recently had the industry’s biggest machine in its stable, is also expected to unveil a new entry soon.
“We didn’t move as the first one, and that of course we have to address today,” said Henrik Andersen, the chief executive of Vestas.
To pull off its gambit, G.E. had to start “pretty much from scratch,” Mr. Schellings said. The business unit called G.E. Renewable Energy is spending about $400 million on design, hiring engineers and retooling factories at St. Nazaire and Cherbourg in France.
To make a blade of such extraordinary length that doesn’t buckle from its own weight, G.E. called on designers at LM Wind Power, a blade maker in Denmark that the company bought in 2016 for $1.7 billion. Among their innovations: a material combining carbon fiber and glass fiber that is lightweight yet strong and flexible.
Offshore turbines account for only about 5 percent of the generating capacity of the overall wind industry, but that number is expected to grow. Credit...Ilvy Njiokiktjien for The New York Times
G.E. still must work out how to manufacture large numbers of the machines efficiently, initially at the plants in France and, possibly later, in Britain and the United States. With a skimpy offshore track record, G.E. also needs to show that it can reliably install and maintain the big machines at sea, using specialized ships and dealing with rough weather.
“G.E. has to prove a lot to asset owners for them to procure G.E. turbines,” Mr. Barla said.
Bringing out bigger machines has been easier and cheaper for Siemens Gamesa, G.E.’s key rival, which is already building a prototype for a new and more powerful machine at its offshore complex at Brande on Denmark’s Jutland peninsula. The secret: The company’s ever-larger new models have not strayed far from a decade-old template.
“The fundamentals of the machine and how it works remain the same,” said Mr. Rasmussen, the unit’s chief technology officer, leading to a “starting point that was a little better” than G.E.’s.
There seems to be plenty of room for competition. John Lavelle, the chief executive of G.E.’s offshore business, said the outlook for the market “gets bigger each year.”
Stanley Reed has been writing from London for The Times since 2012 on energy, the environment and the Middle East. Prior to that, he was London bureau chief for BusinessWeek magazine. @stanleyreed12 • Facebook
A version of this article appears in print on Jan. 2, 2021, Section B, Page 1 of the New York edition with the headline: A Monster Wind Turbine Is Upending an Industry. Order Reprints | Today’s Paper | Subscribe