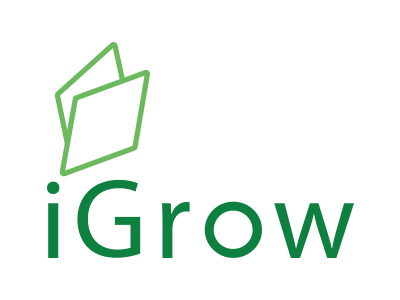
Welcome to iGrow News, Your Source for the World of Indoor Vertical Farming
Underground Agriculture In London Is Gearing Up
By 2022, Growing Underground aims to produce 60 metric tons of vegetables across an area of 528 square meters. That should be enough for 10,000 households and is 12x more than what is produced on a regular farm
Growing Underground In London Is One
of The Largest Underground Vertical Farms
In the World That is Controlled Entirely
By A Digital Twin At The University of Cambridge.
29 March 2021
All the good things an old World War II bunker can bring, right? Thirty meters below ground, near the London New Covent Garden food market, two entrepreneurs have been working together for several years with the British University of Cambridge on an underground farm that has great ambitions.
Their intention is not only to significantly increase production on-site over the coming years. The project also serves as an example for the whole world, according to co-founder Richard Ballard,
By 2022, Growing Underground aims to produce 60 metric tons of vegetables across an area of 528 square meters. That should be enough for 10,000 households and is 12x more than what is produced on a regular farm.
Energy and water
Vegetable cultivation takes place without soil, as the plants thrive on a kind of ‘woolen carpet’ that uses very little water. “70% less than on a conventional farm,” claims Growing Underground. Energy consumption is also low due to the great depth – which ensures few temperature fluctuations – and thanks to the energy-efficient LED lighting.
Nevertheless, energy is the one thing that still stands in the way of a global breakthrough. Ballard: “Vertical agriculture is on the verge of exponential growth due to ever-improving LED technology, the Internet of Things, cloud computing, and wireless sensors. But the really big breakthrough will come once more and cheaper renewable energy becomes available that can also be stored.”
Ballard believes vertical agriculture can make a significant contribution to the food problem we undoubtedly have in store as a result of an ever- growing global population. For a techie, the fun part is that it also requires a lot of high-end sensor technology.
Melanie Jans-Singh
A digital twin
There are 25 sensors in the underground farm that constantly track how the plants are doing. E.g., whether something needs to be done with the amount of CO2 in the air, nutrients, temperature, humidity and light. In total, 89 variables are involved. Even the speed at which the plants grow is measured, says researcher Melanie Jans-Singh from the University of Cambridge.
Jans-Singh: “The digital twin provides us with a 3D representation of the situation in London here in Cambridge. That image is even better than if you were there on site yourself. The digital twin can do much more than a human being. It can monitor, learn, give feedback and make predictions. All factors that will help increase productivity.”
A great deal of research into vertical farming is also being done in the Netherlands, such as by the company Plantlab.
ABOUT THE AUTHOR
Maurits Kuypers graduated as a macroeconomist from the University of Amsterdam, specializing in international work. He has been active as a journalist since 1997, first for 10 years on the editorial staff of Het Financieele Dagblad in Amsterdam, then as a freelance correspondent in Berlin and Central Europe. When it comes to technological innovations, he always has an eye for the financial feasibility of a project.
UNITED KINGDOM: Sheffield Underground Farm Is 'Green And Sustainable'
Luke Ellis, from Sheffield, grows his produce at Kelham Island using organic soil and food created from waste products and without natural light
03-18-21
A Former Builder Has Transformed Unused Cellar Space
Into An Underground Farm To Produce
Fresh Herbs And Vegetables
Luke Ellis, from Sheffield, grows his produce at Kelham Island using organic soil and food created from waste products and without natural light.
He said it might sound like science fiction, but the unusual farming method has the potential to address food shortages and climate change.
The business already sells produce to restaurants and direct to customers.
Mr. Ellis first became interested in hydroponics technology six years ago but felt it was not as sustainable as it could be with most companies using high-tech, state-of-the-art equipment with a high start-up cost.
To address that he decided to create a bioponic farm, an organic form of hydroponics.
"Bioponic vertical farming may sound like something straight out of the world of science fiction, but it is a sector which holds a lot of potential for growth," he said.
The produce is grown in soil created from waste food, paper, used coffee, and ash
COPYRIGHT LUKE ELLIS
The plants are fed with an organic food packed with nutrients | COPYRIGHT LUKE ELLIS
The company uses waste materials, such as paper, card and food scraps, to create its own soil and the run-off from those systems is not wasted either.
"We make our own plant food, which means we don't ever pour anything away," said Mr Ellis.
The plants are grown under electric lights which, he added, offer advantages.
"Artificial light can be better than natural light because we can control the flavour of the food and control the growth rate."
Electric lighting helps control the growth rate of the plants. COPYRIGHT LUKE ELLIS
The produce is sold to both restaurants and individual customers. COPYRIGHT LUKE ELLIS
Mr. Ellis said he hoped the business, which opened in December 2020, would inspire others to help build a "greener, more sustainable society".
"It's super fast to grow, we use recyclable materials, it's 100% organic and it's very efficient," he added.
Follow BBC Yorkshire on Facebook, Twitter and Instagram. Send your story ideas to yorkslincs.news@bbc.co.uk or send video here.
Lead photo: Luke Ellis supplies residents and restaurants with herbs and greens. COPYRIGHT LUKE ELLIS
Indoor Farming Gains Ground Amid Pandemic, Climate Challenges
Investors used to brush off Amin Jadavji’s pitch to buy Elevate Farms’ vertical growing technology and produce stacks of leafy greens indoors with artificial light. Now, indoor farms are positioning themselves as one of the solutions to coronavirus pandemic-induced disruptions to the harvesting, shipping, and sale of food
Investors say urban farming can boost food security despite rising inflation, trade tensions and global food shortages.
Image from: Reuters via AppHarvest
Investors used to brush off Amin Jadavji’s pitch to buy Elevate Farms’ vertical growing technology and produce stacks of leafy greens indoors with artificial light.
“They would say, ‘This is great, but it sounds like a science experiment,'” said Jadavji, CEO of Toronto, Canada-based Elevate.
Now, indoor farms are positioning themselves as one of the solutions to coronavirus pandemic-induced disruptions to the harvesting, shipping, and sale of food.
“It’s helped us change the narrative,” said Jadavji, whose company runs a vertical farm in Ontario, and is building others in New York and New Zealand.
Proponents, including the US Department of Agriculture (USDA), say urban farming increases food security at a time of rising inflation and limited global supplies. North American produce output is concentrated in Mexico and the US southwest, including California, which is prone to wildfires and other severe weather.
Climate-change concerns are also accelerating investments, including by agribusiness giant Bayer AG, into multi-storey vertical farms or greenhouses the size of 50 football fields.
They are enabling small North American companies like Elevate to bolster indoor production and compete with established players BrightFarms, AeroFarms and Plenty, backed by Amazon.com Inc founder Jeff Bezos.
But critics question the environmental cost of indoor farms’ high power requirements.
Vertical farms grow leafy greens indoors in stacked layers or on walls of foliage inside of warehouses or shipping containers. They rely on artificial light, temperature control and growing systems with minimal soil that involve water or mist, instead of the vast tracts of land in traditional agriculture.
Image from: Reuters via AppHarvest
Greenhouses can harness the sun’s rays and have lower power requirements. Well-established in Asia and Europe, greenhouses are expanding in North America, using greater automation.
Investments in global indoor farms totalled a record-high $500m in 2020, AgFunder research head Louisa Burwood-Taylor said.
The average investment last year rose sharply, as large players including BrightFarms and Plenty raised fresh capital, she said.
A big funding acceleration lies ahead, after pandemic food disruptions – such as infections among migrant workers that harvest North American produce – raised concerns about supply disruptions, said Joe Crotty, director of corporate finance at accounting firm KPMG, which advises vertical farms and provides investment banking services.
“The real ramp-up is the next three to five years,” Crotty said.
Vegetables grown in vertical farms or greenhouses are still just a fraction of overall production. US sales of food crops grown under cover, including tomatoes, cucumbers and lettuce, amounted to 358 million kilogrammes (790 million pounds) in 2019, up 50 percent from 2014, according to the USDA.
California’s outdoor head lettuce production alone was nearly four times larger, at 1.3 billion kg (2.9 billion pounds).
Image from: Reuters via AppHarvest
The USDA is seeking members for a new urban agriculture advisory committee to encourage indoor and other emerging farm practices.
Plant Breeding Moves Indoors
Bayer, one of the world’s biggest seed developers, aims to provide the plant technology to expand vertical agriculture. In August, it teamed with Singapore sovereign fund Temasek to create Unfold, a California-based company, with $30m in seed money.
Unfold says it is the first company focused on designing seeds for indoor lettuce, tomatoes, peppers, spinach and cucumbers, using Bayer germplasm, a plant’s genetic material, said Chief Executive John Purcell.
Their advances may include, for example, more compact plants and an increased breeding focus on quality, Purcell said.
Unfold hopes to make its first sales by early 2022, targeting existing farms, and startups in Singapore and the United Kingdom.
Greenhouses are also expanding, touting higher yields than open-field farming.
AppHarvest, which grows tomatoes in a 60-acre greenhouse in Morehead, Kentucky, broke ground on two more in the state last year. The company aims to operate 12 facilities by 2025.
Its greenhouses are positioned to reach 70 percent of the US population within a day’s drive, giving them a transportation edge over the southwest produce industry, said Chief Executive Jonathan Webb.
“We’re looking to rip the produce industry out of California and Mexico and bring it over here,” Webb said.
Projected global population growth will require a large increase in food production, a tough proposition outdoors given frequent disasters and severe weather, he said.
Image from: Reuters via AppHarvest
New York-based BrightFarms, which runs four greenhouses, positions them near major US cities, said Chief Executive Steve Platt. The company, whose customers include grocers Kroger and Walmart, plans to open its two largest farms this year, in North Carolina and Massachusetts.
Platt expects that within a decade, half of all leafy greens in the US will come from indoor farms, up from less than 10 percent currently.
“It’s a whole wave moving in this direction because the system we have today isn’t set up to feed people across the country,” he said.
‘Crazy, Crazy Things’
But Stan Cox, research scholar for non-profit The Land Institute, is sceptical of vertical farms. They depend on grocery store premiums to offset higher electricity costs for lighting and temperature control, he said.
“The whole reason we have agriculture is to harvest sunlight that’s hitting the earth every day,” he said. “We can get it for free.”
Bruce Bugbee, a professor of environmental plant physiology at Utah State University, has studied space farming for NASA. But he finds power-intensive vertical farming on Earth far-fetched.
“Venture capital goes into all kinds of crazy, crazy things and this is another thing on the list.”
Bugbee estimates that vertical farms use 10 times the energy to produce food as outdoor farms, even factoring in the fuel to truck conventional produce across the country from California.
AeroFarms, operator of one of the world’s largest vertical farms, based in a former New Jersey steel mill, says comparing energy use with outdoor agriculture is not straightforward. Produce that ships long distances has a higher spoilage rate and many outdoor produce farms use irrigated water and pesticides, said Chief Executive Officer David Rosenberg.
Vertical farmers tout other environmental benefits.
Elevate uses a closed-loop system to water plants automatically, collect moisture that plants emit and then re-water them with it. Such a system requires two percent of the water used on an outdoor romaine lettuce operation, Jadavji said. The company uses no pesticides.
“I think we’re solving a problem,” he said.
Bringing The Future To life In Abu Dhabi
A cluster of shipping containers in a city centre is about the last place you’d expect to find salad growing. Yet for the past year, vertical farming startup Madar Farms has been using this site in Masdar City, Abu Dhabi, to grow leafy green vegetables using 95 per cent less water than traditional agriculture
Amid the deserts of Abu Dhabi, a new wave of entrepreneurs and innovators are sowing the seeds of a more sustainable future.
Image from: Wired
A cluster of shipping containers in a city centre is about the last place you’d expect to find salad growing. Yet for the past year, vertical farming startup Madar Farms has been using this site in Masdar City, Abu Dhabi, to grow leafy green vegetables using 95 per cent less water than traditional agriculture.
Madar Farms is one of a number of agtech startups benefitting from a package of incentives from the Abu Dhabi Investment Office (ADIO) aimed at spurring the development of innovative solutions for sustainable desert farming. The partnership is part of ADIO’s $545 million Innovation Programme dedicated to supporting companies in high-growth areas.
“Abu Dhabi is pressing ahead with our mission to ‘turn the desert green’,” explained H.E. Dr. Tariq Bin Hendi, Director General of ADIO, in November 2020. “We have created an environment where innovative ideas can flourish and the companies we partnered with earlier this year are already propelling the growth of Abu Dhabi’s 24,000 farms.”
The pandemic has made food supply a critical concern across the entire world, combined with the effects of population growth and climate change, which are stretching the capacity of less efficient traditional farming methods. Abu Dhabi’s pioneering efforts to drive agricultural innovation have been gathering pace and look set to produce cutting-edge solutions addressing food security challenges.
Beyond work supporting the application of novel agricultural technologies, Abu Dhabi is also investing in foundational research and development to tackle this growing problem.
In December, the emirate’s recently created Advanced Technology Research Council [ATRC], responsible for defining Abu Dhabi’s R&D strategy and establishing the emirate and the wider UAE as a desired home for advanced technology talent, announced a four-year competition with a $15 million prize for food security research. Launched through ATRC’s project management arm, ASPIRE, in partnership with the XPRIZE Foundation, the award will support the development of environmentally-friendly protein alternatives with the aim to "feed the next billion".
Image from: Madar Farms
Global Challenges, Local Solutions
Food security is far from the only global challenge on the emirate’s R&D menu. In November 2020, the ATRC announced the launch of the Technology Innovation Institute (TII), created to support applied research on the key priorities of quantum research, autonomous robotics, cryptography, advanced materials, digital security, directed energy and secure systems.
“The technologies under development at TII are not randomly selected,” explains the centre’s secretary general Faisal Al Bannai. “This research will complement fields that are of national importance. Quantum technologies and cryptography are crucial for protecting critical infrastructure, for example, while directed energy research has use-cases in healthcare. But beyond this, the technologies and research of TII will have global impact.”
Future research directions will be developed by the ATRC’s ASPIRE pillar, in collaboration with stakeholders from across a diverse range of industry sectors.
“ASPIRE defines the problem, sets milestones, and monitors the progress of the projects,” Al Bannai says. “It will also make impactful decisions related to the selection of research partners and the allocation of funding, to ensure that their R&D priorities align with Abu Dhabi and the UAE's broader development goals.”
Image from: Agritecture
Nurturing Next-Generation Talent
To address these challenges, ATRC’s first initiative is a talent development programme, NexTech, which has begun the recruitment of 125 local researchers, who will work across 31 projects in collaboration with 23 world-leading research centres.
Alongside universities and research institutes from across the US, the UK, Europe and South America, these partners include Abu Dhabi’s own Khalifa University, and Mohamed bin Zayed University of Artificial Intelligence, the world’s first graduate-level institute focused on artificial intelligence.
“Our aim is to up skill the researchers by allowing them to work across various disciplines in collaboration with world-renowned experts,” Al Bannai says.
Beyond academic collaborators, TII is also working with a number of industry partners, such as hyperloop technology company, Virgin Hyperloop. Such industry collaborations, Al Bannai points out, are essential to ensuring that TII research directly tackles relevant problems and has a smooth path to commercial impact in order to fuel job creation across the UAE.
“By engaging with top global talent, universities and research institutions and industry players, TII connects an intellectual community,” he says. “This reinforces Abu Dhabi and the UAE’s status as a global hub for innovation and contributes to the broader development of the knowledge-based economy.”
UNFI Picks Up Living Greens Farm Products in Midwest Expansion
Living Greens Farm (LGF), the largest vertical, indoor aeroponic farm in the US that provides year-round fresh salads, salad kits, microgreens and herbs, announced the addition of significant new retail distribution of its products in the upper Midwest to independent, specialty, and co-op retailers
I|mage from: Living Green Farms
Living Greens Farm (LGF), the largest vertical, indoor aeroponic farm in the US that provides year-round fresh salads, salad kits, microgreens and herbs, announced the addition of significant new retail distribution of its products in the upper Midwest to independent, specialty, and co-op retailers.
Starting February 2021, LGF’s full line of products featuring ready-to-eat bagged salad products (Caesar Salad Kit, Southwest Salad Kit, Harvest Salad Kit, Chopped Romaine, and Chopped Butter Lettuce) will be carried by UNFI Produce Prescott (formerly Alberts Fresh Produce). UNFI Produce Prescott is a division of UNFI, which distributes food products to thousands of stores nationwide. Their focus is on independent, specialty and co-op retailers.
UNFI has eight warehouses nationwide. LGF’s products will be carried by their upper Midwest location, located just across the river from the Twin Cities in Prescott, WI. This distribution center services hundreds of retailers throughout Minnesota, Wisconsin, Illinois, North Dakota, South Dakota, Missouri, Iowa and Nebraska. UNFI is the first national Certified Organic distributor, something they take a lot of pride in. Their produce and floral businesses are rooted in local farms and seasonal import growers.
LGF’s proprietary vertical indoor farming method yields the highest quality and freshest produce available. This is because there are no pesticides or chemicals used in the growing process. And because LGF’s growing, cleaning and bagging process significantly reduces handling and time to the retail shelf, consumers enjoy the freshest product on the market. These benefits continue to attract new users and new retail distribution as UNFI Produce Prescott is the second UNFI location to carry LGF. In December, UNFI’s Hopkins, MN location began offering LGF products.
For more information on why Living Greens Farm products are the cleanest, freshest and healthiest farm salads and greens available, go to www.livinggreensfarm.com.
Future of Agriculture Grows Under Seoul’s Subway Stations
The Seoul Metropolitan Government, Seoul Metro, and the agriculture company Farm8 have come together for this project
Experts introduce the facility during the opening showcase of Metro Farm at Sangdo Station in September 2019. (Farm8)
Walking down the stairs from exit No. 2 of Sangdo Station in southwestern Seoul, its not easy to miss a white and green signboard that reads “METRO Farm.”
A method of what‘s known as “smart farming,” Metro Farms can create nature-friendly environments while being located inside urban subway stations, using AI and Internet of Things (IoT) technologies.
Sangdo Station’s exit No. 2 was originally left unattended, merely serving its purpose as a meet-up plaza. Since September 2019, the space is now a farm full of sprouts and herbs.
The 394-square-meter cultivation facility is a complex space consisting of an “Auto-Farm,“ where robots manage basic sowing and harvesting, a “Farm Cafe,” which sells fresh salad and juice, made from crops harvested on the same day, and “FarmX,” a zone where visitors can learn about the future of agriculture.
The Seoul Metropolitan Government, Seoul Metro, and the agriculture company Farm8 have come together for this project. In 2004, Farm8 started out as a firm that produced and distributed vegetable salads. Over time, the company shifted gears to conduct research on indoor farming as a method of sustainable agriculture that can operate regardless of weather conditions and has succeeded in developing high-tech distribution centers.
The three organizations worked together to enhance the ecological sensitivity of Seoul as a city, and allow young people living in urban districts to experience agriculture with their own eyes.
Children line up in front of a Metro Farm to experience and learn about agriculture in January 2020.(Farm8)
“We tried our best to make Metro Farms a lively experience, where visitors can get a grasp of its possibilities and to be recognized a place where technology meets nature,” senior manager of Farm8 Yeo Chan-dong told The Korea Herald.
Since the very first showcase of Metro Farm at Dapsimni Station in eastern Seoul in May 2019, Yeo explained that they have made progress in creating urban agricultural jobs and expanded Metro Farms across the city.
An average of 7.5 million people take the subway each day in Seoul, according to Seoul Metro. This means that passersby will naturally encounter Metro Farms on their way to work, home or to meet family and friends.
“Our assignment for the new year is to make Metro Farms more popular and sustainable,” Yeo spoke with confidence, “In other words, not only presenting the experience but eventually making a system for the crops grown to be made a competitive quality to suit the needs of the public.”
By Kim Hae-yeon (hykim@heraldcorp.com)
The Future of Farming Is Inside This Bomb Shelter
The farm is known as Growing Underground (GU), and it’s located 108 feet below the main street in Clapham, a south London suburb
Ten Stories Underneath London,
Thousands of Plants Are growing
BY ROB KEMP
PHOTOGRAPHY BY KATE PETERS
NOV 12, 2020
Deep beneath the streets of London, in a complex of bomb shelters left abandoned since World War II, something is growing. Thousands of green sprouts burst from their hydroponic trays, stretching toward glowing pink lights that line the arched ceilings. These plants, along with tens of thousands of other salad crops, are being grown from seed without soil or sunlight, in tunnels transformed into a high-tech commercial farm.
The farm is known as Growing Underground (GU), and it’s located 108 feet below the main street in Clapham, a south London suburb. Every year, in 6,000 square feet of old bomb shelter, more than 100 tons of pea shoots, garlic chives, cilantro, broccoli, wasabi mustard, arugula, fennel, red mustard, pink stem radishes, watercress, sunflower shoots, and salad leaves are sown, grown, and prepared for dispatch.
London’s unique move toward re-localizing agriculture—feeding its growing population while cutting the environmental impact of producing and transporting crops—is the brain-child of entrepreneur Richard Ballard and his business partner Steve Dring.
The tunnels consist of two portions - a larger upper level, where growing and processing takes place, and a smaller lower level, shown here, which is used for storage. KATE PETERS
“The United Nations predicts that we need 70 percent more food by 2050,” says Ballard. “But how are we going to achieve this when only 10 percent of the Earth’s surface is suitable for agriculture and we use a third of that to grow livestock feed?”
Ballard’s journey to becoming a pioneering subterranean farmer is an unusual one. After his ethical garden furniture business went bust in 2008, he moved closer to his old friend, Dring, and the pair would regularly sit in the pub and discuss ideas for start-ups. Both men were intrigued by the idea of vertical farming as an efficient way to feed people, especially in urban areas.
These farms are not susceptible to weather, and crops can be protected from food contamination and grown without herbicides and pesticides. Transport costs are minimal, harvesting is often automated, and much of the water used to grow crops can be recycled.
But the question of how to build it in a city where living space is at such a high premium presented their first major challenge.
At that time, London’s Crossrail line was in its construction stages. The excavations for the 73-mile-long high-speed railway across the city regularly featured on the TV news—especially as secrets to the city’s past were being unearthed, including plague pits, Roman artifacts, and unexploded World War II bombs. It led Ballard and Dring to consider going underground.
Cilantro sprouts under the pink growing lights. KATE PETERS
They worked with the management company for the city’s underground railway network, Transport for London (TfL), to find the Clapham site. “As long as we weren’t building an underground nightclub, they were happy for us to trial a small farm to see if a tunnel could work as a growing environment,” Dring says.
A crowdfunded campaign raised more than $900,000 to develop the site. After a successful trial in one small section of the shelters, Ballard and Dring negotiated a nearly 20-year lease from TfL and began operating in 2015.
The entrance to GU is within an unassuming brick office at street level. In here sit four of the site’s seven aboveground staff; they work at computers taking orders from retailers and arranging deliveries. It’s also the spot where visitors are asked to remove any jewelry and sign a consent form confirming that they are in good health, have never carried typhoid, and are not bringing any nuts onto the site.
From there, it’s a trip into a cramped elevator with barely enough room for two people. It descends slowly, 10 stories belowground, to where visitors step out into a tunnel of whitewashed corrugated arches that contrast brightly with the eerie elevator shaft. Through a row of rubber strips hanging from a tunnel entrance, the kind you see in an industrial refrigerator, a bright pink light glows. Coupled with a sound of hard-core punk music coming from another passageway, this farm has the feel of the illicit nightclub their landlords had feared.
The working farm currently occupies an eighth of its potential 45,000 square feet of growing space. The entire site is two parallel tunnels, each 1,640 feet in length. Built at the height of the Blitz between 1940 and 1942 and capable of accommodating 8,000 people, the space was already connected to electricity and the London water supply before Growing Underground moved in.
Pea shoots are planted in the recycled growing medium. KATE PETERS
Belowground the next set of safety precautions sees visitors putting on white rubber boots, disposable hair nets, another net to cover any facial hair, and white lab coats.
“It’s a controlled environment. We don’t need pesticides but we can’t afford contamination,” says Jess Moseley, GU’s operations coordinator and tour guide. “We ask visitors to remove their jewelry to prevent any possibility of any foreign body contamination. We don’t want tiny gemstones in our salad.” Visitors wash their hands thoroughly with soap and use an alcohol-based sanitizer on them, and then are free to enter the farm.
Moseley works alongside a team of growers, all wearing the same hair net and rubber boots combo. Four of them, dressed in blue, stand in a line at polished-metal weighing scales picking bunches of harvested herbs and packing them for distribution.
“There are 16 production staff and two growers who organize the sowing,” Moseley explains, as the electronic scales beep and another box of fresh herbs is sealed and stacked. These micro greens are the intensely flavored early stages of plants that are usually harvested later in their life cycle. They’re especially popular with restaurants that serve dishes with very little on the plate. “We switched pea shoots to tendril pea shoots, which are frillier, because the chefs prefer them,” says Moseley.
The trays in the foreground hold crops that are ready for the harvest, while those under the lights are still growing. KATE PETERS
Most of GU’s crops are micro herbs—there are only two larger crops, pea shoots and sunflower shoots. Most full-size produce such as carrots or bok choy could be grown here, but they take too long to grow to make them profitable. However, more research into alternative lighting spectrums may make these a possibility, says GU operations manager Alex Hamilton-Jones.
"OUR PEA SHOOTS CAN BE HARVESTED UP TO 60 TIMES IN A YEAR. OUTDOORS YOU GET THREE OR FOUR HARVESTS A YEAR; IN A GREENHOUSE, AROUND 30."
“Larger crops require a change to the growing equipment, like the height of the stacks and light intensity,” Moseley says. “This is going to be a part of the next iteration of the farm.”
Within its short existence, Growing Underground’s team has expanded its variety and reduced turnaround time on crops. That’s due in no small part to a number of technological innovations that optimize growing conditions on the farm.
“Our pea shoots can be harvested up to 60 times in a year,” Ballard says. “Outdoors you get three or four harvests of those in a year; in a greenhouse, around 30.”
To help plants grow quickly, the correct lights are key. Ballard and Dring tried seven different LEDs during their R&D and found that the system they settled on—spectrum AP673L LEDs from Valoya of Finland—produced the best yield and greatest flavors.
These LEDs utilize a red:far-red (R:Fr) spectrum ratio that targets the red and far-red light-absorbing photoreceptors on the plant leaf. The light resembles sunlight at its peak level, which delays the flowering of herbs and allows the plant to focus its energy into fast biomass development.
The result is a compact, intensely flavored product grown in a short time in conditions that not only suit the plant but meet the needs of the growers, too. “The cycle for growing coriander has gone from 21 to 14 days,” explains Riley Anderson, the site’s team leader. “Some plants can be harvested after just six days in the growing tunnel, which beats anything a farm aboveground can achieve consistently through the year.” They toyed with duller tones than the vivid pink that now illuminates the growing tunnel, but found that the reduction in visibility meant having to lift each plant tray out off of its bench to do quality checks. It slowed the process and didn’t enhance the crop.
Jess Moseley, GU’s operations coordinator and tour guide, checks on some of the crops. KATE PETERS
“We wanted to source the lowest energy-consuming lighting system we could find,” explains Ballard. “The LEDs do not use the same amount of energy nor do they create the high direct heat that conventional (high-pressure sodium) lights do, which means we’re able to grow the plants in shelves closer together.”
The power comes from Good Energy, which only uses renewable sources. “As it’s a closed-loop system of farming, anything that’s added—nutrients or fertilizers—stays within the circuit,” says Ballard. The only farm waste—the substrate recycled carpet leftover from harvesting the herbs—is sent to SELCHP, a waste-to-energy converter in southeast London. “Zero carbon output has been the Key Performance Indicator we chose to work to from the very start because any business starting today needs to think about its impact on the environment,” says Ballard.
This 700-recipe cookbook will have you eating every last bit of your bounty. This is an actual problem at our house. Cooking everything takes creativity.
In addition to high-tech lighting, there are several other adaptations that allow plants in the tunnels to grow so quickly. It starts when the seeds are sown, without the aid of conventional soil: Workers place two-inch-thick rectangular growing mats—called Growfelt and made from pulped floor carpet—into shallow trays. The mats are sprinkled with seeds by hand.
Once sown, the seed trays are stacked onto carts and left in a dark section of the same tunnel for propagation. For a short time, they sit in complete darkness, covered with plastic wrap. This “fools” the seeds into thinking they’re beneath the earth. This is where germination begins. Within a day or two, the seed shoots appear. By the fourth day, the trays are transferred to shelves known as benches under the banks of LEDs in the crop-growing tunnel.
Garlic chive seeds are sewn into the recycled carpet seed bed. KATE PETERS
There’s no music playing in the growing area—workers seldom spend much time in here, as the plants are doing all the work on their own. Instead, the only noise in this long, flamingo-pink chamber is the whirring of the axial fans dangling from the ceiling. Although the fans help keep the farm at a settled temperature of around 59°F, the plants beneath the glare of the LEDs feel the warmth of up to 77°F.
“There’s a slight variance throughout the farm,” says Anderson. “We place the crops strategically to optimize growth. Our radishes prefer to be right at the front of the farm, where it is coolest. Our most robust crop, the pea shoot, grows well wherever it is positioned within the farm.”
On either side of the tunnel are trays bristling with herbs at different stages of growth. In each tray, a handwritten sign identifies the type of crop, along with a P date of propagation, an L for the day it was put under the lights (when transferred to the farm from propagation), and B for the bench the tray is assigned to.
The warming glow provides “sunlight” for 18 hours a day. Rain comes in the form of hydroponics. A faucet fills each tray of plants with a water-and-nutrient mix five times a day. The roots in the trays grow down through the matting to absorb the mix and then water is filtered through tanks beneath the benches. “We use 70 percent less water than conventional field farming,” says Moseley.
The garlic chive crop is harvested and ready for packing. KATE PETERS
The night before a harvest, workers put the plants on carts in the middle of the farm, which has the best airflow, Anderson says. That dries them overnight to the point of being packable without them breaking down quicker.
CROPS HERE CAN BE HARVESTED, PACKED, DELIVERED, AND SERVED ON A PLATE ALL WITHIN FOUR HOURS.
To harvest, fresh herbs are sliced from their roots, shaken off of the matting that served as their soil bed, and placed into a blue bowl. From there the crop is weighed and packed into transparent tubs made from rPET—recycled plastic—and labeled with the GU logo and contents.
Above each growing bench is a round, yellow sensor the size of a large coin that records temperature, humidity, and illumination, and sends the data to the University of Cambridge’s engineering department. The results are fed back to GU, which compares them with the crop yields to determine which conditions are working best for growth.
“We monitor yields every day when we cut,” says Ballard. “A platform with machine learning capability collects the data from all the sensors and alerts you to any anomalies. It gives us access to the sort of technology being used in big agricultural projects, but that would be too expensive for us to put together.”
Crops here can be harvested, packed, delivered, and served on a plate all within four hours. The reduced time spent in transit means GU products have a longer shelf life than those grown outside of the capital. As a result, they’re sold in some of the U.K.’s major food retailers and wholesalers.
A number of renowned London chefs use GU produce, too, including Michelin-starred Michel Roux Jr. He not only uses their herbs in his dishes at Le Gavroche, a French restaurant in the Mayfair area of London, but he also came on board as a founding supporter. He describes the shoots and leaves that it provides as “mind-blowingly good.”
For distribution to smaller restaurants, GU goes underground as well. “We send our delivery guys off with all these bags of orders onto the subway trains,” says Anderson. “Food that’s been grown in a Tube tunnel is delivered through one as well, further reducing the carbon footprint.”
Tours of the tunnels take place outside of the production cycle, with chefs, students, and potential investors visiting during the week and members of the public shown around on Saturday afternoons. “We’ve had farmers from Scotland, mainland Europe, and as far as America come and visit us,” adds Anderson. In the past five years that the farm has been operating, technology has improved a lot—more efficient LED lighting, water recycling, and air management systems, Anderson says. “But the principle of what we’re doing is remarkably simple, giving crops the nutrients they need and a medium to grow in.”
Ballard is now busy sourcing funding to expand farther into the tunnels while investigating sites for other controlled-environment farms in other parts of the world and in different structures.
“When we started, the plan was to produce a supply for London,” Ballard says. “But as the retailers have taken an interest, we’re now looking to serve their distribution centers beyond the M25 [London’s encircling motorway].”
As GU grows, it looks to similar farms for inspiration. In South Korea, subterranean vegetable farms are cropping up at underground stations on the Seoul metro, thanks to a start-up called Farm8, while in Tokyo, abandoned utility tunnels built to service a skyscraper city that never materialized have also been converted into GU-style farms. In Hamburg, Germany, a vertical farm called &ever uses methods similar to GU’s to harvest salad crop using just 5,920 square feet of indoor growing space. Producing an equivalent yield outdoors would require 161,458 square feet of open field.
Increasingly crowded cities are getting imaginative when it comes to farmland. “But these farms don’t have to be underground at all,” says Ballard. “It can be in an abandoned factory or disused warehouse aboveground. The model is simply redundant space.” Even so, with at least six more abandoned tunnels beneath London alone, GU’s subterranean farm may not be the only game of its type in town, or underneath it, for much longer.
VIDEOS: Vertical Farming Goes High-Tech And Underground
Vertical Farms Are Evolving Into A Major
Food Industry Powered by Sophisticated
Technologies And Production Methods
Growing fresh produce in underground areas
Transforming a tunnel into a vertical farming operation
Infarm allows customers to pick the produce themselves
Vertical farming companies are facing an array of challenges
Technology and lower costs are critical for the industry’s sustainability
Innovation is vital to solving the world’s greatest challenges
Farmers around the world are heading towards an uncertain future. Apart from the prospect of feeding the global population that’s set to reach around 10.9 billion by 2100, they are also facing climate change-induced floods, droughts, and heatwaves. Fertile land is in ever shorter supply as soil erosion intensifies. Farming is also to blame for some of these problems as the CO2 footprint of food accounts for 17 percent of total global emissions. And by the time plants get transported to supermarkets, they lose 45 percent of their nutrients. As it becomes increasingly apparent that traditional agriculture is unsustainable, growing food in an artificial environment is emerging as a potentially better way forward.
Instead of plowing fields, farmers would produce food in vertically stacked trays. Soil would be replaced by nutrient-rich water, while LED lights would act as the sun to ensure plants photosynthesize. This practice, known as vertical farming, offers many benefits. The indoor environment protects crops from extreme weather events and pests, which means that food grows fast and there’s no need for pesticides. Also, food is grown close to cities, which not only reduces food miles and the related carbon footprint but also provides consumers with fresh and tasty crops.
However, vertical farming faces certain challenges as well. Companies have to constantly innovate to cut production costs and turn a profit, which is vital for the survival of this industry. But entrepreneurs remain optimistic. The global vertical farming market is forecasted to reach $12.77 billion by 2026 and people are becoming increasingly aware that there’s a better way to feed the populGrowing fresh produce in underground areas
High rents and the lack of space have prompted some modern urban farmers to go underground. In London, for instance, a farm called Growing Underground operates from a World War II bomb shelter located 33 metres below Clapham High Street. Owned by Stephen Dring and Richard Ballard, the vertical farming facility produces an array of herb and salad mixes, including parsley, red mustard, coriander, and pea shoots. Fresh produce is then sold through Marks & Spencer, Waitrose, Ocado, and several other retailers. Some restaurants have also expressed interest in buying fresh produce, says Ballard.
He also points to many advantages of vertical farming. For instance, his farm delivers 60 harvests a year, compared with around seven that can be achieved in traditional agriculture. Furthermore, Growing Underground is carbon neutral and uses 70 percent less water than typical farms. The only major cost he’s trying to reduce is the electricity that powers the lights. And his ambitions are global. “The UK is the hardest market for growing salad. We’ve got very low prices in the supermarket, so if we can make it work here we can make it work anywhere,” says Ballard.
Underground vertical farming is thriving in other British cities as well. The Liverpool-based social enterprise Farm Urban, for example, provides customers with a weekly box of living salad leaves, edible flowers, and fragrant herbs. Jens Thomas, the company’s technical director, says that the product is pesticide-free and “it’s grown using 90% less water than if it was grown in a field; it’s zero-waste; and it’s hyper-local.” Farm Urban is trying to promote healthy and sustainable living. For each box of greens customers buy, the company delivers a box of greens to a local school. This activity is part of the Greens for Good campaign that aims to reconnect people with locally-grown food.
In New York, the vertical farming business Farm. One is also growing. Its underground farms produce over 500 different herbs, edible flowers, and microgreens year-round, using specialized software to manage multiple operations, such as seed, harvest, and flavor optimization. Founded by Rob Laing, the company supplies fresh produce to various New York-based restaurants, including Atera, Ai Fiori, Benno, and Flora Bar. All deliveries are made by bike and subway. Also, visitors can book a tour of the farm or take a class in hydroponics to learn how to grow vegetables in a soil-free environment.
Transforming a tunnel into a vertical farming operation
Successful vertical farming businesses can also be launched outside of cities. NEXTON, a South Korea-based startup, has built vertical farms in a former highway tunnel, located 190 kilometres south of the capital city of Seoul. Growing salads, leafy greens, and strawberries beneath mountains has many advantages. For one, the 6,500-square-metre facility naturally maintains a temperature that ranges between 10 to 20 degrees Celsius, which translates into lower energy spend for cooling or heating. Furthermore, labor costs are reduced by automating various operations. And as farming is done without pesticide or herbicide, with sensors monitoring humidity and CO2 concentrations, customers receive both healthy and affordable products.
Choi Jae-bin, the CEO of NextOn, also uses non-tech tactics to boost production. For instance, the music of Beethoven and Schubert is played in the 600-metre-long tunnel as Jae-bin believes it will help plants to grow faster. And his plan is to build more farms in urban areas. “Plants easily grow at home, at nearby stores, at hamburger restaurants, or even at metro stations. I think the system to grow crops far away from a city and transporting it will disappear,” he says.
Infarm allows customers to pick produce themselves
Infarm, a Berlin-based startup, has already achieved in several European countries what Jae-bin plans to do in South Korea. The German company builds modular farms that are placed in customer-facing locations, such as schools, grocery stores, restaurants, and shopping malls, enabling customers to pick the produce themselves. Clients can also add more modules if they want to increase the farming output, while the production is monitored and controlled through a cloud-based platform. Essentially, the whole thing functions as a ‘farming as a service’ operation that combines the IoT, Big Data, and cloud analytics.
The company is working with 25 major food retailers in Germany, France, and Switzerland, including Migros, Casino, Intermarche, Auchan, Selgros, and AmazonFresh. Furthermore, it has installed more than 200 in-store farms, as well as 150 farms in distribution centres. And in 2019, Infarm raised $100 million in Series B investment round. The funding will be used to expand research and development, sales, and operation teams. Also, the startup plans to increase its presence in the UK and negotiate partnerships with retailers in the US and Japan.
Vertical farming companies are facing an array of challenges
While the rise of vertical farming companies has been impressive, the industry is facing many challenges and its survival depends on reducing costs and increasing productivity. Take, for example, the fact that deploying even a small, low-tech vertical farm with the 1st generation technology costs around $280,000. On the other hand, the cost of setting up more complex farms with advanced tech can go over $15 million. There are also operating expenses such as lighting and labour that can further pressure companies’ bottom line, making it hard to compete with organic and traditional producers.
So it comes as no surprise that return on investment (ROI) in vertical farming projects is mediocre at best. The current market prices don’t make the situation any easier either. A kilogram of vertically-grown leafy greens is around $33, while organic produce costs $23. To gain a competitive edge, vertical farming startups need to take several measures.
Technology and lower costs are critical for the industry’s sustainability
The first step in ensuring the long-term profitability of vertical farms is transitioning to 2nd generation technology. This means that in addition to automatic control of irrigation, humidity, lighting, CO2, and other relevant parameters, farms should also be capable of autonomously collecting data and optimizing growing processes. They also need to implement cutting-edge machines that will autonomously run planting and weeding operations in the facility, and harvest sort and package produce for shipping. These improvements can enable the second generation of vertical farms to yield 55 times more produce than conventional farms.
Increased automation will also cut labour expenses. Intelligent Growth Solutions, a UK-based agritech business, has reportedly developed an automated farming system that uses modular structures to reduce labour needs by up to 80 percent. Furthermore, LED lighting efficiency is likely to improve by an additional 70 percent by 2030, reducing the energy spend. Boaz Toledano, a business consultant specializing in vertical farming, says that “lighting improvements should reduce OPEX [operating expenses] by 12%, and automation should cut OPEX by a further 20%+”.
Companies can also reduce costs by setting up farming operations underground. This would not only help them avoid the high cost of renting in urban centres but also enable them to enjoy the benefits of having a steady temperature. Underground facilities also offer better protection against natural disasters and can be more easily adapted to producers’ needs.
Innovation is vital to solving the world’s greatest challenges
New technologies are moving the food industry forward. Vertical farming, though still gaining traction, could help solve some of the world’s greatest challenges, such as food shortage. Tasked with feeding the growing global population, today’s agriculture producers still primarily rely on farming practices that hurt the environment. As it becomes clear that traditional farming is unsustainable, innovative entrepreneurs and scientists have come up with a potential solution. Vertical farming is increasingly hailed as an alternative food production method that can provide people with healthy and fresh produce. Thriving in undergrounds, stores, and restaurants around the world, vertical farms are becoming a major industry. But their survival depends on the ability of businesses to lower food production costs and increase productivity.
This article is written by Richard van Hooijdonk
Trendwatcher, futurist, and international keynote speaker Richard van Hooijdonk takes you to an inspiring future that will dramatically change the way we live, work, and do business. All lectures
From Bomb Shelter To farm: The Latest Food Revolution
When you think of growing anything ‘underground’, the first thing you may envisage is some kind of criminal activity. But, there’s a food innovation gaining traction around the world, specially in London, and while it might be coming from beneath the streets, it’s all above board
14 Nov 2019
Sponsored by KETTO
Food for thought
When you think of growing anything ‘underground’, the first thing you may envisage is some kind of criminal activity. But, there’s a food innovation gaining traction around the world, specially in London, and while it might be coming from beneath the streets, it’s all above board.
Here's what you need to know about the latest underground food revolution...
Growing Underground
The fully-working Growing Underground farm is located 33 metres beneath the busy streets of Clapham, in the abandoned tunnels of a former World War II air-raid shelter.
The urban farm covering 65,000 square feet lie 120 feet under Clapham High street and are home to 'Growing Underground', the UK’s first underground farm. The farms produce includes pea shoots, rocket, wasabi mustard, red basil and red amaranth, pink stem radish, garlic chives, fennel and coriander, and supply to restaurants across London.
Salad without soil?
Urban farmers, Richard Ballard and Steven Dring are using the latest hydroponic systems and LED technology to grow fresh microgreens and salad leaves, in a stable, sustainable and pesticide-free environment.
A spigot supplies nutrients and water to the roots of the plants and artificial light and warmth is provided by LED lighting. The site is powered with renewable energy.
Instead of using soil, seeds are planted into mats made out of old carpet offcuts. Once the seeds germinate, they are put under lights to mimic sunlight.
Science behind the sprouts
So what is hydroponics? According to the Royal Horticultural Society, it is “the science of growing plants without using soil, by feeding them on mineral nutrient salts dissolved in water.”
Hydroponics does not use soil, instead, the root system is supported using an inert medium such as perlite, Rockwool, clay pellets, peat moss, or vermiculite.
Location, location, location
Its central London location is convenient to distribute the vegetables to hotels, restaurants and shops, reducing the food miles for businesses and consumers. The farm also boasts using 77% less water than conventional agricultural methods.
The system is completely unaffected by the weather and seasonal changes, which means they can be grown 356 days a year.
All photos: Getty Images
These Tech Start-Ups Are Changing What It Means To Farm
Feeding a rapidly expanding population without depleting the Earth’s finite resources, is one of the major challenges of the 21st century
The future of farming? Image: REUTERS/Ilya Naymushin
01 Jul 2019
Briony Harris Senior Writer, Formative Content
This article is part of the Annual Meeting of the New Champions
Feeding a rapidly expanding population without depleting the Earth’s finite resources, is one of the major challenges of the 21st century.
These four entrepreneurs - who have all been selected as the World Economic Forum’s Technology Pioneers for 2019 - have a vision to transform the way we farm in order to help feed the world.
Mini-farms in underground parking lots
In an abandoned car park in downtown Beijing, trays and trays of planting beds are stacked on top of each other.
This is a mini-farm, right in the heart of the city, and it supplies nearby hotels with lettuce, celery, herbs, kale and other green vegetables.
“It’s no longer impossible to grow food where people work and live”, says Stuart Oda, who co-founded the agriculture start-up Alesca Life in 2013, referring to the amount of disused urban infrastructure available, including things such as old shipping containers.
LEDs provide the light, and mineral nutrients are added to water instead of soil. Internet-linked devices monitor humidity, acidity levels and the amount of dissolved oxygen in the water, allowing such variables to be adjusted to increase yields.
“Our system allows us to automate all of the major points of human error that could lead to a loss of crop,” Oda says.
Stuart Oda shows his container farms to the UAE’s minister for food security . | Image: Stuart Oda
The proximity of the mini-farms to the customers means that the produce is fresh, and reduces transport and packaging.
Alesca Life has signed an agreement to distribute 1,000 container farms across the Middle East, Africa, China, and North America.
Oda’s decision to launch his company was prompted by the change he could see happening all around him in China, including rapid urbanization, population growth and land degradation of traditional farms.
“There’s a real sense of urgency to dealing with these challenges and I want to dedicate all my productive years, including my passion and my youth, to addressing them,” he says.
2. Finding a market for ugly fruit and veg
Christine Moseley has witnessed massive food waste at first hand.
During the harvest of romaine lettuce, Moseley watched as 25% of each plant was put into uniform packaging, while the rest was discarded.
“I knew then we had a broken food system. It was my ‘aha’ moment and I vowed not to stop until I found a way for that produce to be utilized for consumption,” she told Forbes.
That was when she decided to start Full Harvest, a B2B platform to sell rather than waste unsightly or unwanted fruit and veg.
Roughly one-third of the food produced in the world for human consumption every year — approximately 1.3 billion tonnes — gets lost or wasted, according to the Food and Agricultural Organization of the UN.
In the US alone, 9 billion kilos of ‘ugly’ and surplus produce are wasted each year simply due to the cosmetic standards of grocery stores.
Supermarkets often only buy perfect produce
Image: Reuters/Ngwyen Huy Khan
Full Harvest connects food companies with trucking firms and farms so that they can make use of the imperfect and surplus produce.
This not only makes good use of the food, it also stops water being wasted and limits carbon dioxide emissions from agriculture.
3. Preventing waste with NASA’s hyperspectral imaging
Hyperspectral imaging sees information on parts of the electromagnetic spectrum that human eyes cannot. That means it can test the freshness of food - from beef steaks to avocados - without even touching it.
The technology - first developed by NASA for aerial imaging - detects the internal quality and chemical composition of food products.
ImpactVision then uses machine-learning techniques to assess the quality of the product, providing food companies with real-time information about their stock.
With an avocado, for example, the images can determine the fruit’s ripeness and reject any rotten ones. Previous systems have depended on sampling - and then wasting - fruits.
“Using advanced imaging and machine learning, we help food companies learn about the quality of their food products non-invasively, providing real-time continuous data,” says ImpactVision’s CFO Rachael Gan.
“That leads to optimized decision-making during processing that in turn reduces waste.”
Can you tell which avocado is ripe without touching . Image: REUTERS/Siphiwe Sibeko
ImpactVision is now working with several leading food producers and supermarkets in the US and believes the data it gathers has the power to transform food supply chains in the same way as GPS transformed navigation.
As food quality control is digitized, this new technique could also help spot contamination and prevent costly food recalls at a later date.
Have you read?
4. More productive seeds
“Seeds are the heroes of modern agriculture. If we improve seeds, then we determine how much land, how much water, how much fertilizer will be used,” says Ponsi Trivisvavet, CEO of Inari Agriculture. “We can solve these major environmental problems by going back to the root cause - the seed.”
Image: FAO
Inari operates a seed foundry where a plant’s genes are edited - some genes may be knocked out, others inserted and others fine-tuned. "Everything we do would probably happen naturally over the next 1,000 years or so,” says Trivisvavet. “We’re just speeding up that process.”
Three changes were simultaneously carried out on tomato plant seeds in order to grow the size of the branch, increase the number of flowers and expand the size of the fruit. This led to an increase of productivity of more than 90%, something which has never happened before in the history of crop development, according to Trivisvavet.
The same technology is being used for soybeans, where the genes of the seed are being edited to increase the number of pods per node, and the number of seeds per pod.
Inari’s seed foundry uses AI-powered computuational crop design to understand the genomes of the crop and how they interact with each other.
“The gene editing itself is easier than identifying where the changes need to be made,” Trivisvavet says. “AI tells us where the changes need to be.”
Among the areas being worked on is making crops more drought-resistant and less dependent on fertilizer.
“We’re working out how to feed the world without starving the planet,” Trivisvavet says.
“If we can grow food with less inputs, then we can return land to nature and lighten the ecological footprint of farming.”
Written by Briony Harris, Senior Writer, Formative Content
The views expressed in this article are those of the author alone and not the World Economic Forum.
Old Coal Mines Can Be 'Perfect' Underground Food Farms
By Matt Lloyd BBC Wales
December 2, 2018
Experts say former mine shafts could be used to grow food |GETTY IMAGES
Abandoned coal mines across the UK could be brought back to life as huge underground farms, according to academics.
Mine shafts and tunnels are seen as "the perfect environment" for growing food such as vegetables and herbs.
The initiative is seen as a way of providing large-scale crop production for a growing global population.
Advocates say subterranean farms could yield up to ten times as much as farms above ground.
President of the World Society of Sustainable Energy Technology, Prof Saffa Riffat, believes the scheme would be a cost-effective way of meeting the growing need for food.
It could also breath new life into many mines that have been closed since the decline of the UK coal industry in the late 1980s and a cheaper alternative to vertical farming in giant greenhouses.
NOTTINGHAM UNIVERSITY How it would work
The idea has already gained support from mine owners, including the Land Trust and Coal Authority, while the Chinese government has also expressed an interest.
There are an estimated 150,000 abandoned shafts and 25,000km-sq of disused mines and tunnels in the UK.
"I'm very excited about the enormous potential. Rather than import so much food by air, rail and sea, we could grow a lot of it here and in huge quantities," said Prof Raffat.
"I wish I had thought of this idea when they were making all the miners redundant. We may have been able to offer them an alternative job."
So what are underground farms, and how would they work?
A problem solved?
By all predictions, global population will continue to grow with the figure in the UK set to reach 80 million before the end of the century, according to the United Nations.
Increasingly, people are opting to live in cities rather than rural areas, putting a strain on food production and land space.
"We have a major issue with food production and supply with the world's population expected to reach nine billion by 2050," said Prof Raffat, of Nottingham University.
"We need to do this for our future. We have a growing demand for food, especially in the cities, but less space to grow it."
ZERO CARBON FOOD | Richard Ballard (left) and Steven Dring grow food in a former air-raid tunnel in London
Why tunnels?
A former World War Two air-raid shelter 100ft (30.5m) under Clapham Common, London, is already being used to grow greens for local supermarkets and restaurants.
Unlike current agriculture, farming underground is unaffected by irregular seasons, climate change and the extreme weather witness throughout 2018.
Almost all the ingredients needed for growing crops such as lettuces, carrots, mushrooms and strawberries are already in place.
The air temperature and humidity levels are generally temperate and constant while there is a ready water supply as well as carbon dioxide.
"Tunnels and shafts would need less energy with heating, so are very attractive for food production. They're almost perfect," said Prof Raffat.
Skip Twitter post by @GrownUnderView image on Twitter
Growing Underground@GrownUnder
THROWBACK THURSDAY! Remembering a very special visit down on the farm earlier this year from @MONKEY_47 Looking forward to celebrating something very special with these guys soon. Stay tuned! #minesagin #undergroundfarm
See Growing Underground's other TweetsTwitter Ads info and privacyReport
End of Twitter post by @GrownUnder
How would it work?
Crops would either be grown in water or suspended in the air and sprayed with water and nutrients.
Lighting would either be from LED lights which are now "extremely cheap to buy and run" or fibre-optic technology which can tunnel sunlight up to 40 metres into the ground.
Carbon-capture technology would capitalise on the naturally occurring CO2.
NOTTINGHAM UNIVERSITY
Is it viable?
Currently, mass-producing crops requires large areas of land.
However one 7m-sq shaft can produce 80 tonnes of food per year, according to Prof Riffat, approximately eight to 10 times the amount of food grown on the same area of land above ground.
"You're looking at about £30,000 to set up one shaft and the running costs are very low - less than the energy consumed by three houses each year. With natural sunlight, the costs are even less."
What has been the reaction?
The Land Trust owns and manages many former colliery sites that have been converted into public spaces.
"It's a great idea and one that we have previously considered ourselves," said chief executive Euan Hall.
"There are obvious challenges, not least that many shafts have been capped or have been built on, but there are lots of coalfields where there's no community around them, where this is clearly something worth looking at.
"A lot of hill farmers in Wales are living hand to mouth so anything that helps diversity and brings a new form of income would be very welcome."
A spokesperson for the Coal Authority said it was "open to considering new ideas" as part of its innovation strategy.
He added: "As an organisation, we constantly review new ways to develop our mining legacy in an effort to minimise remediation costs, generate income from by products and create a future for these important and unique areas.
"Any schemes involving former coal mines would inevitably throw up many technical, legal and financial challenges that would need to be overcome."
NOTTINGHAM UNIVERSITY | Shafts close to cities to provide a steady supply of fresh food.