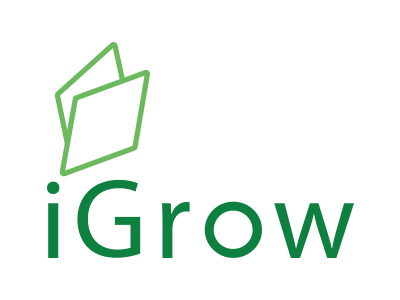
Welcome to iGrow News, Your Source for the World of Indoor Vertical Farming
AI Is Learning To Understand How Vegetables Taste
With the global demand for food escalating, vertical farms are becoming a critical component of agriculture's future. They use robotics, machine learning and artificial intelligence (AI) to automate farming and perfect the growing of greens and vegetables.
By Jennifer Kite-Powell
July 20, 2021
With the global demand for food escalating, vertical farms are becoming a critical component of agriculture's future. They use robotics, machine learning and artificial intelligence (AI) to automate farming and perfect the growing of greens and vegetables. With steady growth, the vertical farming market was had an estimated value of $4.4 billion in 2019 and is expected to reach $15.7 billion by 2025.
Fifth Season is a vertical farm in Pittsburgh that uses super-stack software and robotics to run their fully automated farming systems. And, by combining big data and AI, they have created the optimal grow recipe that determines the best flavor for the plants they grow.
"The role of AI in determining flavor is to leverage big data and AI to ensure you achieve the target flavor — sweetness, spiciness, bitterness, total degree of flavor and texture," said Austin Webb, CEO of Fifth Season.
"Our plant's individualized grow recipe is the unique mix of the different LED lights," said Webb. "The plants go through the grow room with a QR code that communicates that plant's route and tells the automated system where each plant needs to be throughout the process."
Webb says their super stack system, which serves as 'the brain' of the vertical farm maps, maps out each plant's route through the grow room based on its grow recipe and then moves the plants where they need to go.
"We use AI and data to find improvements in all aspects of crop quality, even beyond what humans think they know about flavor profiles. We call this proactive, deterministic growing compared to traditional farming, including greenhouse growing, where you have to be reactive based on weather and sunlight conditions," said Webb. "We then leverage human/chef feedback on what tastes the best and what texture is best and [..] combine that qualitative data with the 26K quantitative data points for every tray of greens per lifecycle."
"From there, we tweak our grow recipes to build the best flavor. For some vegetables, like tomatoes, experts have leveraged Brix scores, but [..] we measure flavor quality based on these factors: sweetness, spiciness, bitterness, the total degree of flavor, texture and color," said Webb. "Humans don't need to guess what iron content or Brix score is best; the brain in our farms can do that. Humans tell the grain what tastes best, and the brain will compute and tweak the grow recipes from there."
Darryn Keiller, CEO and founder of WayBeyond, says that to impact flavor, you either have to change the genetics of the crop or alter the existing biochemical profile.
"For example, growers can impact flavor by adjusting light and nutrients, which can then enhance the texture (crunch, thickness) or flavor (increased sweetness or bitterness)," said Keiller. "Once you determine the key characteristics you want in a crop, you then use machine learning or AI to automate and optimize the production process for consistent growth and be responsive to changing consumer preferences."
"Currently, vertical farms utilize seed stock bred for outdoor farming. Using AI technology, they can create their breeding stock (or lines) better suited for indoor environments. It's about refining your research and development and creating genetics perfect for your environment and management practices while ensuring continuous improvement of commercial production. The potential is huge."
Webb adds that many indoor growers sought to build an outdoor farming system that can thrive indoors; however, Fifth Season chose to apply smart manufacturing principles to agriculture that would enable them to grow food in a new way.
"We grow more than 15K pounds a week of fresh food with 90% less water than what would be required to grow that amount of fresh food on a traditional outdoor farm - and that is done on a footprint of just 25,000 square feet," added Webb.
Webb believes that scaling viable vertical farming operations that can crack code on both the technology and the consumer experience to deliver consistently fresh, nutritious and clean produce changes the consumer shopping significantly.
"It changes our entire definition of what fresh can and should taste like; it changes the ease of access and availability and convenience to fresh food, which brings so much value to consumers," said Webb. "It's another avenue for shoppers to access the freshest, highest-quality food at retail with produce that has a much longer shelf life than we're accustomed.”
Lead Photo: Greens leaving the grow environment on route to harvesting and packaging in Fifth Season's vertical farm in Pittsburgh.
Robots Take Vertical Farming To New Heights
Braddock, Pa., is where Andrew Carnegie first mass-produced steel. The city, now one-tenth its former size, is home to a new kind of industry: robotic farms that grow greens inside buildings
Braddock, Pa., Is Where Andrew Carnegie First Mass-Produced Steel. The City, Now One-Tenth Its Former size, Is Home To A New Kind Of Industry: Robotic Farms That Grow Greens Inside Buildings.
June 28, 2021
A decades-long decline of industry in Braddock has left the western Pennsylvania town in ruins. Ten miles upriver from Pittsburgh in the Mon (Monongahela) Valley, most of the city’s factories, businesses and homes were abandoned long ago and leveled. Among the ruins, a sprawling steel mill, built by Andrew Carnegie in 1874, is still producing slabs of steel, 24 hours a day, seven days a week. It’s stained blue walls and maze of giant, rust-colored pipes and vents stand in contrast to the brand-new, block-long, gleaming white structure directly across the street. The mill’s neighbor is Fifth Season, a vertical farm growing greens indoors by stacking racks of plants on top of each other.
Fifth Season is the brainchild of brothers Austin and Brac Webb, and co-founder Austin Lawrence. “We view vertical farming as really a smart manufacturing system,” says Austin Webb. “We just happen to manufacture living organisms.”
The partners consider their fledgling enterprise as more than a means to feed people, but also a chance to work with a community in need. Almost none of the old steel plant’s employees live in Braddock. Conversely, everyone hired to work at Fifth Season lives close by and in the surrounding communities. “We’re creating a workforce of the future,” Webb says. “It’s an entirely new ag-manufacturing job that hasn’t existed before.”
Since the collapse of the steel industry in Braddock, the borough has struggled to attract new business and residents.(David Kidd/Governing)
Automated City Farming
Two shifts of 20 people oversee operations at the vertical farm. And like the steel maker across the road, the work never stops. Dressed in blue scrubs and lab coats, with heads covered and gloves on their hands, workers inside the plant look more like medical research professionals than farmers. The entire process, from seed to harvest, is controlled robotically. “What we have built is the industry first, and industry only, end-to-end automated platform,” says Webb.
Fifth Season’s proprietary software allows efficiencies otherwise not attainable. Spinach, arugula and other greens move around the 60,000-square-foot facility in plastic trays, each with its own unique ID. Sensors are constantly monitoring everything from nutrient mix, carbon dioxide levels and light spectrum, in order to ensure that the greens follow their prescribed grow recipe. Every plant can be traced from any point in the process, at any time.
Webb is quick to tout the advantages of vertical farming. Fifth Season uses up to 95 percent less water and 98 percent less land than conventional farming. Water from the municipal system is filtered and proprietary nutrients added before getting to the plants directly through their roots. “It means you can replicate any form of soil environment,” he says. Whatever water is not used by the plants is retreated and recirculated, with nutrients added as needed. A peat mix is used to support the roots, but all the nutrients are in the water, not the “soil.”
“We use no herbicides and no pesticides,” Webb says. “And that’s because we have hermetically sealed environments.” The possibility of contamination is all but eliminated. Fifth Season recently received a perfect score from the Safe Quality Food (SQF) program, an international, independent body that certifies food safety management. “The second time in 25 years they gave 100 percent,” he says.
With only their faces exposed, employees work among the various conveyor belts that crisscross the high, white-walled rooms of Fifth Season’s production floor. But there are no humans in the adjacent grow room, where tightly spaced racks, supporting trays of plants, are stacked 30 feet high, bathed in an otherworldly purple-magenta glow. The dramatic color comes from the LEDs that replicate the most useful parts of the spectrum of sunlight. “You can’t control the sun,” Says Webb. “But what you can control are LEDs.”
Fifth Season’s proprietary systems allow more plants to be grown in less space. The purple-magenta LED lighting replicates the most useful parts of the spectrum of sunlight, improving growth of the greens.(Fifth Season)
Every few minutes, a robot glides forward and back along a raised guideway that runs down the center of the room, dividing the stacks in half. The machine is not much more than a plain box, just a few feet tall. A metal beam rises from its back, extending to the ceiling. Its task is to place and remove trays of plants, taking its instructions from the all-knowing software. Because they are so tightly spaced, more trays can be stacked on top of each other, resulting in greater production.
“Compared to some other vertical farms out there, we have a lot more density,” says Webb. “We’re able to have more racks that grow inside the same space.” Moving trays is a task well-suited to a machine. Not only does the robot fit into places no human could, it always knows where every tray of greens should be, and for how long.
Vertical Farming Comes to Braddock
After a five-year career in finance, Austin Webb enrolled in an MBA program at Carnegie Mellon University in Pittsburgh. “I believe that robotics will possibly disrupt every industry in the world,” he says. “And so I went to C.M.U., specifically because it’s the No. 1 school in computers, science and robotics.”
There he met Austin Lawrence, who shared his interest in controlled environment agriculture. Together they visited a few vertical farms, coming to the conclusion that what was needed was an entire robotic platform, something the two of them could not accomplish on their own. Webb’s brother Brac, a self-described engineer and entrepreneur, was soon recruited to help. Their new business was incorporated in 2016, initially as RoBotany, which later morphed into Fifth Season.
With financial backing in hand, the partners looked for a place to build, quickly settling on nearby Braddock. They broke ground in May of 2019, were installing equipment less than a year later and were at full production before the end of 2020. “I think there’s a lot of opportunity for resurgence in a place like this,” says Webb. “A lot of folks that stayed are passionate around Braddock being able to grow and thrive and we want to be a part of that.”
In the foreground, Fifth Season’s new structure stands in contrast to the steel plant behind it that still dominates the town.(David KIDD/Governing)
Andrew Carnegie’s mill was the first of many that would proliferate in the Mon Valley, making it the nation’s steel capital. The churches, schools, stores and restaurants that served the town’s 20,000 inhabitants are mostly gone now. Shops and services are few and far between for the 2,000 that remain. “The nearest grocery store is up the hill, two towns over,” says Braddock Mayor Chardae Jones. “And most people don’t have cars.” It’s a hot day in June when a few of the locals gather in a brand-new park along Braddock Avenue. Everyone agrees the park is nice, but it’s no consolation for the hospital that used to stand on the site.
Many years ago, steelworkers and their families lived close to the mill.(David Kidd/Governing)
A few blocks away, an ever-present din still emanates from Carnegie’s steel mill, and a parade of trucks continues to roll past the boarded-up stores and empty lots that line the borough’s main thoroughfare. “We have a lot of vacant buildings,” says Mayor Jones. “That’s our biggest issue.” But there are signs of a revival among the ruins.
Present Day Braddock
Against the backdrop of empty and dilapidated storefronts, “The Ohringer,” a former furniture store built in the streamline moderne style of the 1940s, has recently been completely rebuilt and modernized as apartments and studio space for artists. Applicants are expected to present their work for review and answer a few questions, one of which is “why are you interested in becoming part of Braddock’s resurgence?”
Not only does Braddock lay claim to Andrew Carnegie’s first steel mill, but also the first Carnegie library, dedicated in 1889. Narrowly escaping demolition in the 1970s, the impressive stone structure is today undergoing a comprehensive restoration and modernization. Bright yellow notices of this year’s street sweeping schedule are affixed to telephone poles near the library and all over town, an indication that the local government is still functioning.
A repurposed furniture store now provides updated living and studio space to area artists.(David Kidd/Governing)
Further up the avenue, more official-looking signs are attached to random telephone poles. “NOTICE, WRITE MORE LOVE LETTERS” says one. “NOTICE, LOVE IS FREE,” says another. The signs were placed there, unofficially, by Gisele Fetterman, wife of former mayor and current Lt. Governor John Fetterman. Among her many initiatives to improve the lives of people in Braddock, she founded the Free Store nine years ago, a place where “surplus and donated goods are received and redistributed to neighbors in need.”
Fifth Season is a regular contributor to the Free Store, having recently given them a new refrigerator and donating 100 pre-packaged salads every Thursday. “We’re treated like we’re a customer,” says Gisele Fetterman. “We’re not getting things that didn’t sell, or surplus. Our families get to come in and choose. They can feel like they are at a grocery store. There is great dignity in the process of being able to choose.”
Offering “produce grown in soil by humans in Braddock,” workers at Braddock Farms do it the old-fashioned way.(David Kidd/Governing)
There are more signs along Braddock Avenue. “BE ALERT: VEGETABLES AHEAD.” Another simply says “TURNIPS.” Back in 2007, when John Fetterman was the mayor, he encouraged a nonprofit group of community gardeners to establish a farm in Braddock. Bisected by a side street, the organic farm has expanded to a little less than an acre in size, growing greens, tomatoes, onions, peppers and eggplant. This is Nick Lubecki’s fourth year as manager of the farm. “We’re here in Braddock, so the people in Braddock are our main focus,” he says. “We want to be useful.”
At best, the little farm on Braddock Avenue can produce 13 plantings of greens in a year. It is entirely different from the computer-controlled, machine-driven, non-stop production that takes place a few blocks away at Fifth Season, where a half-acre indoors can produce the equivalent of nearly 100 acres of farmland. But higher yields don’t matter as much if a significant portion is ultimately lost in transit to the table.
Serving a Market
Localized food production means less spoilage and waste. “If it takes anywhere from five to eight days to go from California to Pittsburgh, you’ve just lost five to eight days of shelf life,” says Austin Webb. Most of what Fifth Season produces is consumed in the Pittsburgh area. “The day after it was cut, not 10 days later.” Their ready-to-eat salads can be purchased at a local supermarket chain, or delivered directly to the consumer at home, a direct response to the pandemic. Local restaurants, hospitals and universities are also customers.
Convinced they have successfully demonstrated the viability of their proprietary technology, the three partners are looking to expand beyond western Pennsylvania. “We can build these anywhere… even larger than what we have here today,” says Austin Webb. “And we don’t have to re-create the wheel. It’s not like it would take us another five years.”
Conversations are already taking place about licensing the technology, proceeding in partnership with someone else, or going it alone. “That will allow us to build a facility just like we built in Braddock, in other parts of the U.S., and other parts of the world, even faster.”
A Job You Can Walk to
Andrew Carnegie built his steel mill in the Mon Valley because he needed the river, the raw materials, and access to labor. His plant was expressly designed to use the Bessemer Process, the first method to inexpensively mass-produce steel. Nearly 150 years later, the Webb brothers and their partner Austin Lawrence chose the exact same location to showcase their own new manufacturing technology and to fill a need in the community. “Knowing that we could build these anywhere, we wanted to build in Braddock because we knew that we could create jobs,” says Austin Webb. “That we could create this new workforce of the future.”
Employed since January, John Davis lives less than a block away from Fifth Season. “I have family in Braddock. They’re very happy I’ve got a job.”(David Kidd/Governing)
Braddock resident John Davis may or may not think of himself as part of the workforce of the future. But he’s happy to have a good job. Covered head to toe in his surgical outfit, he works in the seeding department at Fifth Season, a job he’s held since January. He’s lived here for 20 years, and this is the first job he’s had that didn’t involve a commute. He walks to work from his house, half a block away.
Davis is 32 years old and anxious to put the past behind him. “To have a job that you like, where you live, it’s comfortable,” he says. “And you can see that this is going to change Braddock for the better because it gives the residents jobs and new innovations. It’s going to bring life.”
While awaiting their fate, many of Braddock’s empty buildings provide space for murals and artwork.(David Kidd/Governing)
Lead photo: Greens leave the grow room at robot farm Fifth Season, ready for harvest. (Fifth Season)
Tags: Economic DevelopmentFood AssistanceTechnology
David Kidd is a photojournalist and storyteller for Governing. He can be reached at dkidd@governing.com.
Farm Tech Startup Iron Ox Appoints Impossible Foods and Tesla Veteran Rachel Konrad as First Independent Board Member
Iron Ox growing facilities use advanced robotics to precisely cultivate perfect, nutritious produce by giving each plant the specific attention it needs, and then getting it on a store shelf nearby within about a day of harvest
-- Konrad, who spent the past five years at Impossible Foods, joins the board of Iron Ox during a period of rapid manufacturing scale-up and retail expansion.
-- Iron Ox growing facilities use advanced robotics to precisely cultivate perfect, nutritious produce by giving each plant the specific attention it needs, and then getting it on a store shelf nearby within about a day of harvest.
-- The Series B-stage company, whose products are already a breakout seller in California, is also hiring plant scientists, engineers, greenhouse operators, and roboticists.
SAN CARLOS, Calif., June 10, 2021 /PRNewswire/ -- Iron Ox, a farming innovation company with deep expertise in robotics and artificial intelligence, has appointed former Impossible Foods and Tesla executive Rachel Konrad as its first independent board member. This appointment further demonstrates the food tech startup's growth trajectory as they scale up operations and expand their commercial footprint.
Iron Ox, which launched the world's first autonomous farm, has an industry-leading intellectual property portfolio to automate farming and produce that's fresher, cleaner, and locally grown. Thanks to the company's groundbreaking robotics, Iron Ox farms require 90% less water than traditional farms — generating 30 times more produce per acre of land.
Konrad joins Iron Ox after spending the past five years as Chief Communications Officer and a member of the senior leadership team at Impossible Foods, reporting directly to CEO Pat Brown. She previously held senior management roles at Renault-Nissan-Mitsubishi and Tesla, where she reported directly to Elon Musk as the company scaled up operations.
"We can't solve our planet's climate crisis without radical changes to the way we make food," said Konrad, who lives in the San Francisco Bay Area and enjoys cooking for her family and hiking with her rescue German Shepherd. "Iron Ox's intellectual property portfolio can usher in a new era of farming that produces food sustainably and ethically. But honestly, I was sold after my first whiff of Iron Ox basil."
"Rachel understands the unique power of disruptive startups to shift entire industries and force even the most entrenched incumbents to do the right thing for people and the planet," said Brandon Alexander, Iron Ox CEO and Co-Founder. "Her unique perspective will help Iron Ox refine and execute our ambitious strategy. As our first independent board member, we expect Rachel to help us set a new standard for inclusive governance in corporate America."
The Series B-stage company operates farms in Northern California and recently broke ground on a new 535,000 sq. ft. indoor farm in Lockhart, Texas. Today, California consumers can buy Iron Ox food throughout California at Whole Foods and at San Francisco Bay Area's upscale Biancchini's markets. Sales in Texas are expected to begin in late 2021.
The company is also hiring plant scientists, engineers, greenhouse operators and roboticists who are passionate about solving food insecurity, which is at the root of our environmental and public health crises.
For more information, and to view the job openings, visit the Iron Ox jobs page.
About Iron Ox:
Iron Ox is a farming innovation company with deep expertise in robotics and artificial intelligence, and a vision to solve global climate through food. Their approach redesigns every step of the farming process, achieving levels of precision that are impossible through traditional farming. Iron Ox produce is both local and sustainable by design, greatly reducing systemic food waste and minimizing the ecological impact of farming. For more information, visit www.ironox.com.
SOURCE: Iron Ox
Robotic Warehouse Farms Will Save The World
CEA technology is just getting started. Like the Tesla Cybertruck, we have a working concept that promises a more-than-Jetson’s-level future many of us can see the benefits of and actively want―it’s just not quite available to the masses yet
by Elle Griffin
Four years ago, Ritch Wood was looking for a better way to grow plants. As the CEO of global skincare company Nu Skin, he ran into ingredient shortages every winter when fields went dormant―and when he moved grow operations to the equator he ran into water and land shortages, along with a host of quality control issues.
Nu Skin needed reliable, quality ingredients for their skincare products. But farming was too unpredictable an industry. “If there was a way to grow indoors,” he thought, “and be able to do that 24 hours a day, 365 days a year―if we could guarantee that it was grown without any herbicides or pesticides and in a sustainable way that uses less water and land―that would be really helpful.”
At the time, controlled-environment agriculture (CEA) was in its infancy and grow-light technology had yet to take a turn for the more affordable. When he learned of an agricultural system that promised to use a fraction of the land and water used by traditional agriculture methods and had the potential to make it more affordable, Wood made an investment.
Nu Skin paid $3 million for 70 percent of the company and rights to its IP―and Grōv Technologies was born.
Grōv grass grown in the Olympus machine at the Bateman Mosida Farms. Photo from Grōv Technologies
Controlled-environment agriculture is on the rise
The theory behind CEA is that by controlling the environment in which it grows, we can control everything about a plant and what it grows into by micro-tweaking one of a thousand different characteristics―including temperature, humidity, light duration, light wavelength, dissolved oxygen in the water, and carbon dioxide saturation in the air. By tweaking the growing cycle, we can control the caloric content as well as the nutrient content and density of the plant.
“What we’ve learned through controlled-environment agriculture,” Benjamin Swan, co-founder and CEO at Sustenir in Singapore, once told National Geographic, “[is] we can actually emphasize certain characteristics of the plants. So, without using GMO, we can make our kale softer, we can actually make it sweet.”
The theoretical use cases for this technology are endless―from being able to grow in places where water is scarce (like in much of Africa), or where water is overly abundant (like Hawaii), or in places where labor is scarce (like in parts of Asia), or even in places that have long winters (like Northern Europe). Theoretically, we could have grow towers in every town and feed the whole of it no matter its natural environment.
We could even grow those foods to those cities’ exact nutritional needs―more vitamin D-rich foods in wintery places, for example. Dr. Lee Mun Wei, a senior manager at the Food Innovation and Resource Centre (FIRC) in Singapore aims to predict and prevent illness in a given population by tracking their biometric data using Apple watch-like wearables, then 3D printing nutrient-specific foods that could mitigate imbalances.
Though these technologies exist, they are still in their infancy. Singapore leads much of the research and development out of necessity. With limited land and water resources, the county is forced to import 90 percent of their food and 40 percent of their water from outside the country. As a result, they have no option but to grow vertically and desalinate water from the ocean.
Elsewhere, the industry has been slow to catch on, largely due to exorbitant startup costs, low returns, and lack of urgent need. According to a 2017 State of Farming report by L.E.K., only 27 percent of indoor, vertical farms are profitable compared with 50 percent of container farms and 75 percent of greenhouses. But one thing has spurred the industry on in recent years: cannabis.
Legalized in 39 states, demand for cannabis has created a $13.6 billion industry and enough capital to fund CEA-enabled grow operations. “When you have a crop that fetches up to $2,400 or $2,500 a pound, you need to be able to dial everything in and make it consistent and repeatable,” says Dashiel Kulander, co-founder and CEO at Boojum Group. “If the temperature swings five to 10 degrees on a cannabis plant, that will change the plant’s various cannabinoids. The goal is to create a medicine that is consistent batch after batch.”
It’s only recently that there has been some financial incentive to use CEA technologies for food use―largely driven by Big Ag players hoping to hedge out the competition. Berry farming giant Driscoll’s, for one, led a $500 million round to fund Plenty, a 2.2-acre vertical farm in California they hope will help them fulfill a contract with Albertsons. The Ingka Group, for another, led a $100 million round to fund AeroFarms, a 2.4-acre vertical farm in New Jersey that will help them fulfill a contract with Singapore Airlines.
Grōv tent at the Bateman Mosida Farms. Photo from Grōv Technologies
Grōv Tech is building CEA prototypes in Utah
By investing in Grōv Tech, Nu Skin hopes to do something similar, getting ahead of the supply chain that fuels their skincare products before the competition can beat them to it, or before climate change makes traditional methods more difficult, all while shoring up technology that could provide a farming model that is more sustainable―if only it were more economical.
“The purpose was always, can we build a better product for Nu Skin?” Wood says. “We think there’s a huge story around the ingredient sustainability, and there were a lot of ingredients we felt we could grow, but the challenge was: could we do it in an economical way?”
Grōv Tech started out with a prototype: a tower that pairs hydroponic growing technology with grow lights. But like all CEA startups, a lot of the growing process was manual and the technology was prohibitively expensive. To make something that was scalable and profitable the whole thing needed to be automated and it needed to be cheap.
With this goal in mind, Wood decided they would start by growing animal feed for Bateman’s Dairy farm. Having grown up on a dairy farm himself, Wood figured this would allow the company to scale the product while refining and automating the technology to the point that it could be replicated. And all of this would have a fortuitous effect on Nu Skin’s bottom line.
“One of our bestselling products is a weight-loss protein powder which uses whey protein,” Wood says. “So again, a very nice connection there is if the animal is eating a more sustainable product and producing better milk with better protein and it’s being done in a sustainable way―certainly that can be a benefit to Nu Skin down the road.”
One year into feeding the 20,000 animals at Bateman, the company has learned a lot. For instance: cows need a lot of magnesium, but they don’t like eating it. Now, Grōv Tech puts magnesium in the water so it’s directly absorbed into the plant and then becomes bioavailable to the cow upon eating it. And because the growing process only takes seven days, data scientists can analyze the results in real-time and adjust the components to optimize production for the next batch of feed.
According to Grōv Tech president Steven Lindsley, it’s not far off that we’ll be looking at milk production (butter, fats, and proteins) and optimizing a herd’s diet for taste, quality, and nutritional value―not to mention the wellbeing of the animal. We’ll be able to look at how many trips from the veterinarian an animal gets when they’re fed certain nutrients in their diet, and whether they can have more calves and produce the same amount of dairy on less, better quality feed. (So far, the answer to this last question is yes. When animals are fed better quality food they need less of it―just like humans.)
And if we hook all of the cows up to robotic milking equipment and connect everything to artificial intelligence, machine learning, and the Internet of Things―Lindsley’s far-flung goal―then we might be able to collect enough data to not only feed cows to their optimum health and performance ability, but humans too. And that could have ramifications not only for feeding the world, but nourishing it― just like Dr. Wei hopes to do in Singapore.
“Last year was about starting to feed animals and get data and prove out the hypothesis we have while continuing to perfect the technology and get confidence there,” Wood says. “And now we’re really to a point where we’ve got data that proves that it works and that financially it’ll be a good thing for a farmer. So now we can really take that proposition to farmers and start to scale.”
Olympus Tower Farm at Bateman Farms in Mosida, UT. Photo from Grōv Technologies
CEA technology could feed the world
Right now, Grōv Tech is focused on refining its technology right here in our own backyard. But once they do that, the plan is to expand internationally.
“Saudi Arabia has actually passed a law where you cannot use water to grow fodder or feed for animals, so all of that now has to be imported. China imports one-third of their alfalfa feed for their dairy animals because they don’t have the capability of growing it,” Wood says. “So there are countries that will probably benefit more than the US would. But we’ve got to refine the technology and get that built to where it’s ready to scale before we start spreading ourselves all around the globe.”
CEA technology is just getting started. Like the Tesla Cybertruck, we have a working concept that promises a more-than-Jetson’s-level future many of us can see the benefits of and actively want―it’s just not quite available to the masses yet. But with more than a billion dollars invested in the technology in just the past few years alone―we’re getting there. And the “there” we are heading toward is rosy indeed.
“To put it in perspective, one tower that is about 875 square feet on the ground will replace 35 to 50 acres of land,” says Lindsley. “And that will feed the animals on roughly five percent of the amount of water. The UN says that that the world will add about 2.5 billion people in the next 30 years. And we have to find a way to feed them on arguably less arable land and water. The good news is the technology is coming along to help solve that equation.”
If COVID-19 taught us anything, it’s that our food supply chain is fragile. But that’s only because our supply chain was built to grow food in California, refrigerate it so it stays fresh, then transport it 1,500 miles so we can eat a salad in the winter in Chicago. In the future, that might not be a thing. “We’re having a dry year now,” Lindsley tells me in February. “But a year ago we were in a blizzard, and even in the middle of a blizzard in February in Utah, we’re pumping out fresh, beautiful, safe green grass for animals. It’s a paradigm shift.”
“Four years ago it was a good idea,” Wood tells me of his company’s investment in CEA technology, “But four years from now it’s going to be required.”
Elle Griffin
Elle is the editor-in-chief of Utah Business and a freelance writer for Forbes, The Muse, and The Startup. She is also a literary novelist and the author of a weekly newsletter called The Novelleist. Learn more at ellegriffin.com.
UNFI Picks Up Living Greens Farm Products in Midwest Expansion
Living Greens Farm (LGF), the largest vertical, indoor aeroponic farm in the US that provides year-round fresh salads, salad kits, microgreens and herbs, announced the addition of significant new retail distribution of its products in the upper Midwest to independent, specialty, and co-op retailers
I|mage from: Living Green Farms
Living Greens Farm (LGF), the largest vertical, indoor aeroponic farm in the US that provides year-round fresh salads, salad kits, microgreens and herbs, announced the addition of significant new retail distribution of its products in the upper Midwest to independent, specialty, and co-op retailers.
Starting February 2021, LGF’s full line of products featuring ready-to-eat bagged salad products (Caesar Salad Kit, Southwest Salad Kit, Harvest Salad Kit, Chopped Romaine, and Chopped Butter Lettuce) will be carried by UNFI Produce Prescott (formerly Alberts Fresh Produce). UNFI Produce Prescott is a division of UNFI, which distributes food products to thousands of stores nationwide. Their focus is on independent, specialty and co-op retailers.
UNFI has eight warehouses nationwide. LGF’s products will be carried by their upper Midwest location, located just across the river from the Twin Cities in Prescott, WI. This distribution center services hundreds of retailers throughout Minnesota, Wisconsin, Illinois, North Dakota, South Dakota, Missouri, Iowa and Nebraska. UNFI is the first national Certified Organic distributor, something they take a lot of pride in. Their produce and floral businesses are rooted in local farms and seasonal import growers.
LGF’s proprietary vertical indoor farming method yields the highest quality and freshest produce available. This is because there are no pesticides or chemicals used in the growing process. And because LGF’s growing, cleaning and bagging process significantly reduces handling and time to the retail shelf, consumers enjoy the freshest product on the market. These benefits continue to attract new users and new retail distribution as UNFI Produce Prescott is the second UNFI location to carry LGF. In December, UNFI’s Hopkins, MN location began offering LGF products.
For more information on why Living Greens Farm products are the cleanest, freshest and healthiest farm salads and greens available, go to www.livinggreensfarm.com.
Vertical Farming Robot Wins Design Challenge
The winners of the 2018 Valtra Design Challenge were announced at the EIMA Show in Bologna, Italy. The competition which started in April and ended on September 23rd was targeted globally to designers, academic design students, design studios and automotive suppliers. This year’s challenge was to design the multi-purpose vehicle of the future: a machine that can handle multiple tasks to meet future needs and that is more efficient than today’s highly specialized machines.
The first place of the competition was awarded to the work “VERTICAL” by Austrian design team Benjamin Miller, Jack Morris, and Alireza Saeedi. The jury praised the concept as being a very creative interpretation of the challenge theme. “At first glance it looks very specialized, but if you judge the complete system instead of only the tractor, a versatile and holistic concept for the future emerges. The concept takes care of everything from seeding to distribution of food”, comments member of the jury Hans Philip Zachau.
“Valtra has been widely recognized for ground-breaking and visionary industrial design. We started the Design Challenge in order to raise awareness of future challenges in the agricultural community and society at large. It is also a platform for designers to showcase their innovations.” comments head of the jury and industrial design & user experience manager at Valtra, Kimmo Wihinen. “The Valtra Design Challenge is the world´s largest design contest in agricultural machinery and one of the biggest in the off-road vehicle industry. The high number of innovative and high-class entries shows us that there is a demand for this type of competition, and we are already working on the theme for the next edition”, he adds.
The Valtra Design Challenge 2018 Jury members were Kimmo Wihinen from Valtra, Brandon Montgomery and Sam Freesmeyer from AGCO, Hans Philip Zachau from Lighthouse Industrial Design and Paolo Grazioli Frozen Design Tokyo.
The Valtra Design Challenge was organised for the second time in 2018. This year the competition has received 107 entries from 32 different countries and six continents. The first prize of the Valtra Design Challenge is a €10,000 cheque.
For more information:
www.valtra.com/designchallenge
Q&A: Driscoll’s Head of Emerging Technology On Harvesting Robotics and Open Innovation
Q&A: Driscoll’s Head of Emerging Technology On Harvesting Robotics and Open Innovation
FEBRUARY 7, 2018 EMMA COSGROVE
As head of R&D strategy and emerging technology at Driscoll’s, Nolan Paul has a unique view of the agtech startups in the specialty crop space.
The global berry seller has become known for its technological innovation in breeding and genetics, but the company’s focus on robotics is less well-known. Paul told AgFunderNews that Driscoll’s wants to support the development of automated strawberry harvest and is in contact with many if not all of the startups working in this area of robotics. That interest has led to investments in Harvest CROO and Agrobot and field trials with more.
Strawberry growing is long overdue for a shake-up and stakeholders know it. Robotic harvesting technologies are not quite ready for wide use. Labor is becoming more scarce as immigration uncertainty in the US continues and also because strawberry picking at ground level is a particularly grueling task. Some growers, inside and out, are raising up growing surfaces to waist-height to mitigate these issues and Driscoll’s is in the position to help and encourage its growers to keep up with the times.
We caught up with Paul ahead of the World Agri-Tech Innovation Summit, where he’ll play the shark in several startup pitch presentations, to discuss how Driscoll’s works with startups and lessons learned while trying to determine the future of strawberry growing.
Driscoll’s is constantly testing and verifying technologies, but can growers afford to make major investments in technology right now?
Nolan Paul
It depends on what we’re talking about. The startups are recognizing that this is an issue and moving to a service model where you de-risk the technology for the grower base. They’re not going to have to pay a half a million dollars for a piece of equipment. But at some point, we come in. I think it’s not going to be as simple as just the robotics, let’s say, for harvest. It’s a combination of the robotics and the growing system and actually the genetics too. In that combination of all three is where you’ll really see the success. So Driscoll’s will come in, certainly on the breeding, on the genetics side, we’ll optimize for traits like mechanization. But on the growing system too, we’re supporting our growers with that, we help them out. And of course, we’re dedicated to investing in the development of ag technologies on behalf of our growers.
What is your assessment of the harvesting robotics field? Are outdoor growers transitioning to waist-height tables as well as indoor growers? And does that mean that harvesting machinery could work indoors and outdoors?
The good news is that the last couple years have seen a crop of harvesting startups pop up. Honestly, I doubted that would happen so quickly but I’m glad I was wrong. So today Driscoll’s is currently in active conversations with six automated strawberry harvesting startups. And they’re all taking a unique approach, which is great.
The challenges are certainly different. I think when you look at the visioning systems, that will be the same, but the robustness, the durability, and the scale will be different. And I think that’s what we’re seeing — some startups perhaps don’t appreciate the scale that will be required for outdoor farms in the US. If you’re growing in a greenhouse or a glasshouse, you know that’s one thing. But when you need to be out on a 100-acre ranch, those robots, those harvesters need to cover a lot of space and it’s probably not a reasonable thing to assume that you can just have a bunch of these robots going through a field. It’s hard for a grower to manage that. So I think there is a certain fleet size that can only be so big.
I think that’s something we’ve found that perhaps some of the startups haven’t looked at. And I don’t think you’ll just see one winner, I think you’ll see different solutions going into indoor farming whether that’s greenhouse or glasshouse or vertical farm and solutions for outdoors. I think the ones that are successful have the vision to scale from strawberries to other crops and perhaps indoors that’s easier to do. I think that’s a big deal. I’m still skeptical that harvesting robots are going to be successful if you just focus on one crop. And that’s really where we want to work with the startups, to help them understand that narrative, so they’re able to raise VC money.
That’s fascinating coming from you. It seems like Driscoll’s has done a pretty good job of making a big market for strawberry technology.
Yeah, it’s an interesting space. We’ve certainly recognized in the last three years how we engage with startups has to change because there are a lot of people who give them lip service. But what we’ve realized is you have to really be structured the right way. It’s not even about the money — there’s plenty of money. You need people who can work alongside these startups and move at the same speed.
It’s easy to go pitch ideas to a CEO, but to actually execute on them is really tough. And certainly we’re learning and getting better at it. Some of these large companies almost want to own what the startup is doing – to have a competitive edge. A lot of times, unless you’re really big, it just doesn’t work and you almost end up killing the startup.
Why doesn’t it work?
Well, I think most of the companies aren’t big enough to justify exclusivity — certainly not in the specialty crop space. It’s a very high, high-value space, but we’re fragmented. There are a lot of one to five billion dollar crops in the US across grapes, strawberries, nuts, and vegetables. But in and of itself it’s not big enough for a startup to scale. It’s important for folks to focus. But you have to have the vision of how you’re going to scale. The right strategic corporate can be a good partner for startups. But they need to recognize that, if you’re working with a startup it’s great that you’re an anchor customer, but you want the startup to be around in two, four, six, 10 years. And the only way they’re going to be around in six to 10 years is if they’ve been able to scale up and either be acquired or maybe, they have to create that scale themselves. I think people are too short-term when they interact with startups.
Canon Electronics Plans Full Automation At Vegetable Factory
The Canon unit will convert empty space at a Gunma Prefecture facility into an indoor farm initially dedicated to growing lettuce and other green, leafy vegetables friendly to hydroponics.
December 28, 2017
Canon Electronics Plans Full Automation At Vegetable Factory
Robots may bring lower costs crucial to profit in growing but finicky sector
At this Gunma Prefecture plant, Canon aims to turn empty space into a roboticized indoor farm.
TOKYO -- Canon Electronics plans to open an entirely automated vegetable factory in 2019, seeking to lower costs by applying homegrown robotics technology to a burgeoning industry where stable profits remain tough to cultivate.
The Canon unit will convert empty space at a Gunma Prefecture facility into an indoor farm initially dedicated to growing lettuce and other green, leafy vegetables friendly to hydroponics. Robots will handle everything from planting seeds and transplanting seedlings to harvesting and packaging crops for shipment. Details such as annual production scale and sales targets will be settled later.
The company will partner with other businesses for know-how on managing the factory and building sales networks. Canon Electronics is also considering building a second such factory in western Japan.
The unit makes some of the manufacturing machinery on the automated production lines in Canon's domestic camera business. Its delicate automation technology from that precision machinery will be put to use developing green-thumbed robots for the company's new factory plan.
Japan had 197 plant factories using artificial light as of February, roughly triple the count in 2011, a survey by the Japan Greenhouse Horticulture Association shows. But production costs run high at such factories, driving up retail prices and making it hard to turn steady profits. In 2016, 37% of the factories operated in the red, the association reported.
Those losses recently led some companies to back out. At the end of 2016, Toshiba closed one such facility in Kanagawa Prefecture. And in 2015, an agricultural startup and plant factory manager based in Miyagi Prefecture went bankrupt under a debt burden of 1 billion yen ($8.81 million at present rates).
Canon Electronics intends to wield its automated production to make operations profitable. Some domestic plant factories automate seed-planting or other processes, but virtually none are automated start to finish. Agricultural startup Spread is building a fully automated plant factory in Kyoto Prefecture, set to begin operations in summer 2018.
(Nikkei)
This Robot Handles The Entire Process Of Growing Lettuce By Itself
This Robot Handles The Entire Process Of Growing Lettuce By Itself
By Adele Peters/ Nov 30, 2017
A new indoor farming startup called Iron Ox wants to staff its greenhouses with only automated workers.
[Photo: Iron Ox]
Inside a warehouse in the middle of the suburban office sprawl of San Carlos, a Silicon Valley town south of San Francisco, hundreds of heads of lettuce and herbs grow next to a mobile robot designed to move the plants as they get bigger. In a lab next door, engineers tweak robots that can handle every part of the growing process, from planting seeds to packaging harvested heads of lettuce for a grocery store.
By early 2018, Iron Ox, the startup behind the R&D farm, plans to open an 8,000 square foot production farm nearby–all fully automated, in a system that the company says can make local, pesticide-free food production as cheap as traditional agriculture in the field.
[Photo: Iron Ox]
When the co-founders decided to launch the startup, one was working on delivery drones at Alphabet’s X, and the other was building room service robots for hotels. They liked the work but wanted to do more with the available technology. “Robotics has come so far in the past few years–sensors have gotten cheaper, software has become more robust,” says co-founder and CEO Brandon Alexander. “We felt that we could be doing something with more impact.”
[Photo: Iron Ox]
They saw an opportunity in food production, where traditional farming faces multiple challenges. Most lettuce, for example, is grown in California and Arizona, two states that face an increasing risk of water shortages and stress from heat as the climate changes. A head of lettuce may be treated with nine different pesticides before it’s harvested and then shipped hundreds or thousands of miles across the country to consumers. As fewer people want to work on farms, producers also struggle with labor shortages.
Indoor farming, which uses a tiny fraction of the water and space, doesn’t require pesticides, and can happen within cities or suburbs, is often billed as a solution. But as Alexander and co-founder Jon Binney researched the market, they realized that cost was a challenge. “We loved the idea [of greenhouses],” Alexander says. “But our question was, if this is so much better, why is most produce grown outdoors? The biggest thing we found was that it costs significantly more–at least twice as much–to grow a head of lettuce indoors than outdoors.”
Other companies, such as Plenty–another farming startup based in Silicon Valley, which grows greens in vertical towers and recently raised $200 million in funding–say that it can produce lettuce at a cost that is competitive with traditional farms. Plenty uses a layout that maximizes yield in small spaces, and notes that the cost of key components for growing, like LED lights, have dropped dramatically. But Iron Ox’s approach is to focus on removing another cost: labor, which for some growers, can account for 50% of the cost of production.
Some greenhouse-grown lettuce might cost $3.99 now, versus $1.99 for the same head of lettuce from the field. “At the end of the day, if you’re always going to have to cost more, then you’re going to be this niche product,” says Alexander. “For the impact that we’re after, one of the biggest things for us is we need to make this produce accessible. Accessible doesn’t just mean affordable–that’s part of it–but it’s affordable and available. Ideally to everybody.”
In the company’s system, a robotic arm plants seeds in a tightly-packed tray, where the seeds germinate in nutrient-filled water. As the plants get bigger, the arm can transplant them to a tray with more space, and then transplant them again a couple of weeks later. Moving the plants maximizes the number of plants that can grow in a tight space.
The robotic arm also uses a camera to scan each plant and note any problems. “We can actually observe is it the right size, is it the right color, does it have any pest pressure or mildew or anything like that,” he says. Plants with mildew, which can easily spread, can be automatically removed. The robots can use machine learning over time to optimize how the plants are grown.
[Photo: Iron Ox]
The new production farm won’t be the first to grow lettuce with an automated system; a massive new factory in Japan uses robots to grow millions of heads of lettuce a year. But the new system in Silicon Valley is less like a traditional factory, and more flexible.
“That [Japanese farm] works well for a set process: ‘we’re going to grow this type of lettuce in this way, and we’re going to do that for the next 20 years,'” Alexander says. “We try to go with as little infrastructure as possible. All we really need is a concrete floor, at the end of the day. All of our modules, these hydroponic pallets, are portable. We have a mobile robot.” If the company later wants to use a slightly more efficient layout, or change its operation, it can make those changes through software.
As the first production farm in San Carlos scales up, the startup will sell to local chefs with an interest in the company’s sustainability; once output is high enough, it will sell to grocery stores. Ultimately, the company envisions building farms near consumers across the country, so someone shopping at a grocery store in Atlanta no longer buys week-old greens from California. It also plans to expand to other crops.
“We don’t want to be just a leafy green farm, at the end of the day,” says Alexander. “That is our initial focus–we want to nail that, we think that’s important to solve– but with our approach, this robotic system, we would like to be a fresh produce farm.”
Startup Iron Ox Mixes Robotics and Hydroponics to Futurize Farming
Silicon Valley-based startup Iron Ox is utilizing autonomous robotics to fundamentally change the nature of greenhouse-based agriculture. While the exterior of the Iron Ox greenhouse in San Carlos, California is far from remarkable, the cost-cutting integration of hydroponics, solar energy, robotics, and space-conscious farming is more than noteworthy.
Startup Iron Ox Mixes Robotics and Hydroponics to Futurize Farming
Photo Credit: Jirakan Jiherb/123RF
Silicon Valley-based startup Iron Ox is utilizing autonomous robotics to fundamentally change the nature of greenhouse-based agriculture. While the exterior of the Iron Ox greenhouse in San Carlos, California is far from remarkable, the cost-cutting integration of hydroponics, solar energy, robotics, and space-conscious farming is more than noteworthy.
Iron Ox
By using autonomous robots to plant, seed, water, and even harvest their hydroponically grown crops, Iron Ox’s system provides uniformity and rapidity which conventional, human-centric farming methods can’t match. Iron Ox greenhouses’ daily harvesting and proximity to urban centers, grocery stores and produce suppliers diminishes the nutrient loss and often bland taste which results from produce being shipped hundreds or thousands of miles from farm to store.
Founders Brandon Alexander, a former Google X engineer and John Binney, who holds a PhD in robotics, check all the boxes when it comes to consumer demand for non-GMO, pesticide-free produce. Alexander, Iron Ox’s CEO, is uniquely qualified as the leader of this farming revolution. His work on Google’s Project Wing included exploring and implementing ways for autonomous robots to work in combination. With the proper technology in place, Alexander estimates that set-up of one of Iron Ox’s urban greenhouses takes only three to four months, on average.
Luiz Ribeiro Ribeiro/123RF
The master plan is to expand Iron Ox greenhouses manned by autonomous robot-farmers to as many American cities as possible, providing a fresher, potentially cheaper source of produce that traditional farms located far from these cities would be hard-pressed to compete with. Consider that, according to Alexander, a single square-acre Iron Ox greenhouse can match the annual yield of 30 acres of traditional farmland. It also stands to reason that the products created in these robotic greenhouses are less vulnerable to insects and parasites, eliminating the need to use harmful chemicals used to protect outdoor-grown crops.
Like so many industries that have long been a staple of the American and world economies, the application of robotic technology in agriculture will likely mean a drastic shift away from dependence on human labor. The proliferation of companies like Iron Ox carries clear benefits, but it will almost certainly mean structural unemployment for those who depend on traditional means of agriculture as a livelihood. That said, it’s not a matter of if, but a matter of when we see this shift toward autonomous greenhouse farming on a mass scale.
Your Next Head of Lettuce, Grown By A Robot
Your Next Head of Lettuce, Grown By A Robot
You could drive past and never see the only farm in San Carlos, California. The tiny city of 30,000 that sits between San Francisco and Silicon Valley has all the charms of suburbia—sprawling office parks and single-story homes—but doesn’t seem a likely suspect for agriculture.
The farm, run by startup Iron Ox, is nestled between three stonemasons and a plumber in a nondescript office park building; there’s no greenhouse, no rows of freshly-tilled soil, or tractor parked outside. Only peeking in the large bay door reveals the building’s tenants: a few hundred plants and two brightly-colored robot farmers.
Iron Ox looks a lot like a tech company. One of its co-founder is an ex-Google engineer and it raised $1.5 million in pre-seed venture capital from Y Combinator, Pathbreaker, and Cherubic Ventures in April 2016. Instead of fake food, or plant-based meat meals, or even a food delivery service tethered to an app, Iron Ox is reinventing farming, raising real, not faux, food. Think hydroponically raised lettuce and basil, like what you’d get at an ordinary farmers market.
Iron Ox plans to build a network of autonomous, robot-run greenhouses near major US cities, complete with a fleet of trucks to ensure same-day delivery. Traditional outdoor farms don’t mesh with suburban sprawl, but the planned square-acre greenhouses have a small footprint that can easily fit into dense urban or suburban areas. The robots plant, raise, and harvest the crops.
Iron Ox founders Jon Binney, left, and Brandon Alexander. (Iron Ox)
Pod lettuce
Co-founder and CEO Brandon Alexander, who worked on Google’s Project Wing, figuring out how to make multiple robots work together, says it takes just three or four months to set up one of its farms. Plants take six weeks to mature. One of these modular, square-acre farms could provide the same yearly yield as 30 acres of traditional farmland, Alexander says.
“We want to have the most efficient farm out there,” says Alexander. “In some ways this is just the natural evolution of [farming].” Growing up, Alexander spent summers working on his grandfather’s peanut, potato, and cotton farm that straddles Texas and Oklahoma. He’s seen his grandfather adopt self-guided tractors and other new technologies, giving the ability to scale the family farm from 40 to 5,000 acres in one generation.
While raising crops has evolved from the time of small family farms, it’s still inefficient, Alexander says. Vegetables waste a large portion of their shelf lives traveling 2000 miles to get from farm to store. In addition, the pool of labor for existing centralized farms is aging and diminishing. The average US farmer is 55 years old, and the average crop worker is 33. “There’s just not enough labor to go around,” Alexander says.
Iron Ox isn’t the only company trying to revolutionize food production. Plenty, another Bay area startup, recently received $200 million from the Softbank Vision fund with a similar mission of distributed farms near metropolitan areas. Plenty’s buzzword isn’t automation, but vertical farming: growing crops up walls to save space. AeroFarmswants to disrupt hydroponics with nutrient-filled mist. Freight Farmswill grow crops in shipping containers.
The robots
Iron Ox plans to use three robots powered by artificial intelligence to work each square-acre of greenhouse. Two robots, without official names but referred to as transporters, will lift and ferry trays of plants over to the third robot, a robotic arm. The robotic arm will plant seeds, cycle juvenile plants into larger growing plots, image the plants to check for disease, and harvest the crop. Iron Ox plans to grow leafy greens like the lettuce and basil varieties it is testing now. Large-field crops like corn aren’t on the roadmap.
Iron Ox is using a hydroponic system called deep water culture; the plants, seated in plastic cones, float on a raft in a tray of water, their roots submerged in nutrient-rich water.
These trays are the key to Iron Ox’s indoor farm; while many deep water culture systems are built around large, stationary pools of water, these trays allow the plants to be moved to and from the robotic arm. The company developing the three components—robotic arm movement, transporter robot, and automated hydroponic system—separately. Humans now do the work slated for the robots, but the pre-robot farming provides a valuable runway of data for Iron Ox about optimal growing conditions.
Half a dozen data points are collected from each water tray per second, plus air temperature and quality, ambient light, humidity. The brains of the system are in the robotic arm. If it knows certain plants need more space, the transporter can be summoned to collect them for transplanting. If it’s time for harvest, the trays come to the arm.
The arm, which stands between two trays, moves with serpentine ease only occasionally interrupted by a mechanical lurch. As I watch, it’s controlled by CTO Jon Binney, but can be set to autonomously shuffle plants around from tray to tray. The goal is to only have one robot arm per acre of greenhouse, able to switch out its end effector, or hand, for specialized tools based on the task. Universal Robots is the arm’s manufacturer, but it runs custom code for motion planning. The stereoscopic cameras used to image the produce are installed and integrated by Iron Ox, and the end effectors used to inject and transplant are built custom-built by the company as well.
The transporter’s job is to hulk over a tray of plants, tuck the tray into its belly, and carefully transport it to a space next to the arm. It glides around the warehouse with a precise, mechanical grace, seemingly able to drift in any direction on its Mecanum wheels. These specialized wheels mean the trays can be just inches apart on the entirety of the greenhouse floor, since the transporter doesn’t need space to turn.
The process
The plants start as seeds, which are injected by the robotic arm into small, foam-like cubes seated in a plastic cone. The plastic cone protects the base of the plant from the robotic arm’s grippers, which giving each plant a standardized place to grip the plant while moving it around.
When the seeds have sprouted and grown for about two weeks, they are brought to the arm by the transporter. The robotic arm then picks up the plants and transplants them to a tray with more room between each plant. Each tray is outfitted with augmented reality tags (that allow the arm to recognize which tray it’s working with, and the bounds of where it can and can’t put plants.)
Two weeks later, the transplant process occurs again, and then again two weeks after that. Each time a plant is moved, two cameras on the arm build a 3D model of it, which is analyzed to check for disease and to ensure it’s growing normally. After the plant is fully grown, the arm pulls it—roots and all—from its plastic cone, and places it in a plastic clamshell container to be shipped.
The company has yet to launch its first fully-functioning greenhouse, and it currently donates its hydroponically-grown produce at a local San Carlos food bank in addition to supplying the company salad bar. IronOx wants to build the first greenhouse by the end of 2017, sell to local chefs in the Bay Area, and then scale to grocery stores in early 2018.