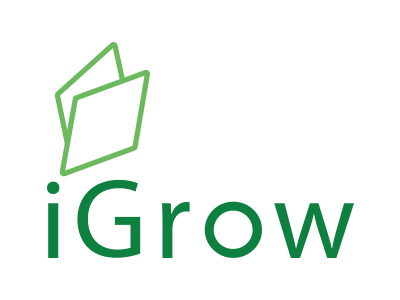
Welcome to iGrow News, Your Source for the World of Indoor Vertical Farming
Little Leaf Farms Raises $90M to Grow Its Greenhouse Network
Massachusetts-based Little Leaf Farms has raised $90 million in a debt and equity financing round to expand its network of hydroponic greenhouses on the East Coast. The round was led by Equilibrium Capital as well as founding investors Bill Helman and Pilot House Associates. Bank of America also participated.
by Jennifer Marston
Image from: Little Leaf Farms
Massachusetts-based Little Leaf Farms has raised $90 million in a debt and equity financing round to expand its network of hydroponic greenhouses on the East Coast. The round was led by Equilibrium Capital as well as founding investors Bill Helman and Pilot House Associates. Bank of America also participated.
Little Leaf Farms says the capital is “earmarked” to build new greenhouse sites along the East Coast, where its lettuce is currently available in about 2,500 stores.
The company already operates one 10-acre greenhouse in Devins, Massachusetts. Its facility grows leafy greens using hydroponics and a mixture of sunlight supplemented by LED-powered grow lights. Rainwater captured from the facility’s roof provides most of the water used on the farm.
According to a press release, Little Leaf Farms has doubled its retail sales to $38 million since 2019. And last year, the company bought180 acres of land in Pennsylvania on which to build an additional facility. Still another greenhouse, slated for North Carolina, will serve the Southeast region of the U.S.
Little Leaf Farms joins the likes of Revol Greens, Gotham Greens, AppHarvest, and others in bringing local(ish) greens to a greater percentage of the population. These facilities generally pack and ship their greens on the day of or day after harvesting, and only supply retailers within a certain radius. Little Leaf Farms, for example, currently servers only parts of Massachusetts, Pennsylvania, New York, and New Jersey.
The list of regions the company serves will no doubt lengthen as the company builds up its greenhouse network in the coming months.
Agritech: Precision Farming With AI, IoT and 5G
For a company that grows and delivers vegetables, Boomgrow Productions Sdn Bhd’s office is nothing like a farm, or even a vertical farm. Where farms are bedecked with wheelbarrows, spades and hoes, Boomgrow’s floor plan is akin to a co-working space with a communal island table, several cubicles, comfortable armchairs, a cosy hanging rattan chair and a glass-walled conference room in the middle
Image from: Photo by Mohd Izwan Mohd Nazam/The Edge
For a company that grows and delivers vegetables, Boomgrow Productions Sdn Bhd’s office is nothing like a farm, or even a vertical farm.
Where farms are bedecked with wheelbarrows, spades and hoes, Boomgrow’s floor plan is akin to a co-working space with a communal island table, several cubicles, comfortable armchairs, a cosy hanging rattan chair and a glass-walled conference room in the middle.
At a corner, propped up along a walkway leading to a rectangular chamber fitted with grow lights, are rows of support stilts with hydroponic planters developed in-house and an agricultural technologist perched on a chair, perusing data. “This is where some of the R&D work happens,” says Jay Dasen, co-founder of the agritech start-up.
But there is a larger farm where most of the work behind this high-tech initiative is executed. Located a stone’s throw from the city centre in Ampang is a 40ft repurposed shipping container outfitted with perception technologies and artificial intelligence (AI) capabilities that mimic the ideal environment to produce more than 50,000kg of vegetables a year.
Stacked in vertical layers, Boomgrow’s vegetables are grown under artificial lights with Internet of Things (IoT) sensors to detect everything from leaf discolouration to nitrate composition. This is coupled with AI and machine learning algorithms.
Boomgrow is the country’s first 5G-connected vertical farm. With the low latency and larger bandwidth technology, the start-up is able to monitor production in real time as well as maintain key parameters, such as temperature and humidity, to ensure optimal growth conditions.
When Jay and her co-founders, K Muralidesan and Shan Palani, embarked on this initiative six years ago, Boomgrow was nowhere near what it is today.
The three founders got together hoping to do their part in building a more sustainable future. “I’ve spent years advising small and large companies on sustainability, environmental and social governance disclosures. I even embarked on a doctorate in sustainability disclosure and governance,” says Jay.
“But I felt a deep sense of disconnect because while I saw companies evolving in terms of policies, processes and procedures towards sustainability, the people in those organisations were not transforming. Sustainability is almost like this white noise in the background. We know it’s important and we know it needs to be done, but we don’t really know how to integrate it into our lives.
“That disconnect really troubled me. When we started Boomgrow, it wasn’t a linear journey. Boomgrow is something that came out of meaningful conversations and many years of research.”
Shan, on the other hand, was an architect who developed a taste for sustainable designs when he was designing modular structures with minimal impact on their surroundings between regular projects. “It was great doing that kind of work. But I was getting very dissatisfied because the projects were customer-driven, which meant I would end up having debates about trivial stuff such as the colour of wall tiles,” he says.
As for Murali, the impetus to start Boomgrow came from having lived overseas — while working in capital markets and financial services — where quality and nutritious produce was easily available.
Ultimately, they concluded that the best way to work towards their shared sustainability goals was to address the imminent problem of food shortage.
“By 2050, the world’s population is expected to grow to 9.7 billion people, two-thirds of whom will be in Asia-Pacific. Feeding all those people will definitely be a huge challenge,” says Jay.
“The current agricultural practice is not built for resilience, but efficiency. So, when you think of farming, you think of vast tracts of land located far away from where you live or shop.
“The only way we could reimagine or rethink that was to make sure the food is located closer to consumers, with a hyperlocal strategy that is traceable and transparent, and also free of pesticides.”
Having little experience in growing anything, it took them a while to figure out the best mechanism to achieve their goal. “After we started working on prototypes, we realised that the tropics are not designed for certain types of farming,” says Jay.
“And then, there is the problem of harmful chemicals and pesticides everywhere, which has become a necessity for farmers to protect their crops because of the unpredictable climate. We went through many iterations … when we started, we used to farm in little boxes, but that didn’t quite work out.”
They explored different methodologies, from hydroponics to aquaponics, and even started growing outdoors. But they lost a lot of crops when a heat wave struck.
That was when they started exploring more effective ways to farm. “How can we protect the farm from terrible torrential rains, plant 365 days a year and keep prices affordable? It took us five years to answer these questions,” says Jay.
Even though farmers all over the world currently produce more than enough food to feed everyone, 820 million people — roughly 11% of the global population — did not have enough to eat in 2018, according to the World Health Organization. Concurrently, food safety and quality concerns are rising, with more consumers opting for organically produced food as well as safe foods, out of fear of harmful synthetic fertilisers, pesticides, herbicides and fungicides.
According to ResearchAndMarkets.com, consumer demand for global organic fruit and vegetables was valued at US$19.16 billion in 2019 and is anticipated to expand at a compound annual growth rate (CAGR) of 6.5% by 2026.
Meanwhile, the precision farming market was estimated to be US$7 billion in 2020 and is projected to reach US$12.8 billion by 2025, at a CAGR of 12.7% between 2020 and 2025, states MarketsandMarkets Research Pte Ltd.
Malaysia currently imports RM1 billion worth of leafy vegetables from countries such as Australia, China and Japan. Sourcing good and safe food from local suppliers not only benefits the country from a food security standpoint but also improves Malaysia’s competitive advantage, says Jay.
Unlike organic farming — which is still a soil-based method — tech-enabled precision farming has the advantage of catering for increasing demand and optimum crop production with the limited resources available. Moreover, changing weather patterns due to global warming encourage the adoption of advanced farming technologies to enhance farm productivity and crop yield.
Boomgrow’s model does not require the acres of land that traditional farms need, Jay emphasises. With indoor farms, the company promises a year-round harvest, undisturbed by climate and which uses 95% less water, land and fuel to operate.
Traditional farming is back-breaking labour. But with precision technology, farmers can spend less time on the farm and more on doing other things to develop their business, she says.
Boomgrow has secured more than RM300,000 in funding via technology and innovation grants from SME Corporation Malaysia, PlaTCOM Ventures and Malaysia Digital Economy Corporation, and is on track to build the country’s largest indoor farms.
Image from: Boomgrow
The company got its chance to showcase the strength of its smart technology when Telekom Malaysia Bhd (TM) approached it to be a part of the telco’s Smart Agriculture cluster in Langkawi last October.
“5G makes it faster for us to process the multiple data streams that we need because we collect data for machine learning, and then AI helps us to make decisions faster,” Jay explains.
“We manage the farm using machines to study inputs like water and electricity and even measure humidity. All the farm’s produce is lab-tested and we can keep our promise that there are no pesticides, herbicides or any preserving chemicals. We follow the food safety standards set by the EU, where nitrate accumulation in plant tissues is a big issue.”
With TM’s 5G technology and Boomgrow’s patent-pending technology, the latter is able to grow vegetables like the staple Asian greens and highland crops such as butterhead and romaine lettuce as well as kale and mint. While the company is able to grow more than 30 varieties of leafy greens, it has decided to stick to a selection of crops that is most in demand to reduce waste, says Jay.
As it stands, shipping containers are the best fit for the company’s current endeavour as containerised modular farms are the simplest means of bringing better food to local communities. However, it is also developing a blueprint to house farms in buildings, she says.
Since the showcase, Boomgrow has started to supply its crops to various hotels in Langkawi. It rolled out its e-commerce platform last year after the Movement Control Order was imposed.
“On our website, we promise to deliver the greens within six hours of harvest. But actually, you could get them way earlier. We harvest the morning after the orders come in and the vegetables are delivered on the same day,” says Jay.
Being mindful of Boomgrow’s carbon footprint, orders are organised and scheduled according to consumers’ localities, she points out. “We don’t want our delivery partners zipping everywhere, so we stagger the orders based on where consumers live.
“For example, all deliveries to Petaling Jaya happen on Thursdays, but the vegetables are harvested that morning. They are not harvested a week before, three days before or the night before. This is what it means to be hyperlocal. We want to deliver produce at its freshest and most nutritious state.”
Plans to expand regionally are also underway, once Boomgrow’s fundraising exercise is complete, says Jay. “Most probably, this will only happen when the Covid-19 pandemic ends.”
To gain the knowledge they have today, the team had to “unlearn” everything they knew and take up new skills to figure what would work best for their business, says Jay. “All this wouldn’t have been possible if we had not experimented with smart cameras to monitor the condition of our produce,” she laughs.
How This Vertical Farm Grows 80,000 Pounds of Produce per Week
To some, the pristine growing conditions and perceived mechanical interference of a vertical farm can seem unnatural, but at Bowery Farming “interference” is actually not the goal at all. “We don’t really think about how people are involved in the growing process, but how to take people out of the growing process”
Bowery Farming uses technology to prioritize accessibility and sustainability in their produce growing operations
To some, the pristine growing conditions and perceived mechanical interference of a vertical farm can seem unnatural, but at Bowery Farming “interference” is actually not the goal at all. “We don’t really think about how people are involved in the growing process, but how to take people out of the growing process” says chief science officer Henry Sztul. “Our goal is actually to have as few people walking around our plants as possible.”
Bowery Farming is a network of vertical farms working to reengineer the growing process. Using a system of light and watering technology, Bowery is able to use 95 percent less water than a traditional outdoor farm, zero pesticides and chemicals, and grow food that tastes as good as anyone else’s.
Bowery Farming uses vertical farm-specific seeds that are optimized for flavor instead of insect resistance and durability. Seeds are mechanically pressed into trays of soil, and sent out into growing positions, or racks within the building that have their own lighting and watering systems. Each tray gets its own QR code so that they can be monitored and assigned a customized plan for water and light until they’re ready to be harvested.
Irving Fain, Bowery Farming’s founder and CEO contemplates the prediction from the United Nations that 70 to 80 percent of the world’s population will be living in and around cities in the next 30 years. “Figuring out ‘how do you feed and how do you provide fresh food to urban environments both more efficiently as well as more sustainably?’ is a very important question today, and an even more important question in the years to come.”
Indoor Farming Company With Backing From Ubben Aims to Solve The Problems With America’s Produce
The agriculture technology company focuses on building an indoor farm in Appalachia. The company combines agricultural techniques with cutting-edge technology and including access for all to nutritious food, farming, and building a homegrown food supply. The company operates a 60-acre controlled environment, agriculture facility in Morehead, Kentucky, which grows juicy beefsteak tomatoes and tomatoes on the vine
Image from: AppHarvest
Company: AppHarvest Inc. (APPH)
The agriculture technology company focuses on building an indoor farm in Appalachia. The company combines agricultural techniques with cutting-edge technology and including access for all to nutritious food, farming, and building a homegrown food supply. The company operates a 60-acre controlled environment, agriculture facility in Morehead, Kentucky, which grows juicy beefsteak tomatoes and tomatoes on the vine. It also operates a 60-acre indoor farm, outside Richmond, Kentucky, where it cultivates fresh fruits and veggies.
The company’s technological systems monitor the pollination across all 68 bays and 684 rows of plants. AppHarvest is only the fourth U.S. public Certified B corporation. A B corporation is a company that has (1) achieved a high standard of social and environmental performance as measured by the B Impact Assessment, (2) verified their scores through transparency requirements, and (3) made a legal commitment to consider all stakeholders, not just shareholders. Any company can apply to be one.
Stock Market Value: $3.3 billion ($33.26 per share)
Image from: CNBC
Activist:
Inclusive Capital
Percentage Ownership:
12.05%
Average Cost:
n/a
Activist Commentary:
Inclusive Capital Partners was formed in 2020 by ValueAct founder Jeff Ubben, to leverage capitalism and governance in pursuit of a healthy planet and the health of its inhabitants. The firm seeks long-term shareholder value through active partnership with companies whose core businesses contribute solutions to this pursuit. Inclusive is a returns driven fund with a focus on environmental and social investing.
Their primary focus is on environmental and social value creation, which leads to shareholder value creation. It is the successor to the ValueAct Spring Fund, which was launched in January 2018 and merged into Inclusive in 2020.
Inclusive is building a huge network and has accessed experts in industries such as energy, electrification, water, agriculture, food production, particulates, education and human rights. Just like ValueAct’s constructive, patient investment style, Inclusive will seek to earn the trust of managers, board members and institutional investors.
Jeff Ubben serves as the portfolio manager and Eva Zlotnicka serves as vice president. Eva has a pre-existing relationship with ValueAct through their interactions with Morgan Stanley, where she served as a VP and U.S. lead for the Global Sustainability Research Team. At Morgan Stanley, she worked to help address and raise awareness of environmental and social issues both inside and outside of corporations.
What’s Happening:
Jeff Ubben was appointed to the company’s Board in connection with the company’s business combination with Novus Capital.
Behind the Scenes:
This was initially an investment of ValueAct Spring Fund, which was converted into Inclusive Capital in 2020. Jeff Ubben first met AppHarvest founder Jonathan Webb in 2017 and has been involved with the company since the 2018 Series A round, working with Webb to put the management team together and develop a strong balance sheet. The company went public on February 1, 2021 through a $100 million SPAC transaction and a $375 million PIPE investment. Jeff Ubben is on the board where he can continue to help the company execute.
AppHarvest plans on having 12 facilities by 2025. The goal here is to make Kentucky the Netherlands of North America. The Netherlands (at 16,000 square miles) is the second largest agricultural exporter in the world, using greenhouse technology to feed two-thirds of all of Europe. In comparison, the state of Kentucky is 40,000 square miles and the US is 3.8 million square miles. AppHarvest’s motivation is first and foremost to benefit society, but if successful would have extraordinary financial returns as well.
As of 2018, 69% of fresh vine crops in the U.S. were imported, mostly from Mexico. These crops are pesticide-laden and grown using labor practices not up to U.S. standards. Moreover, they sit at the border for days and are driven 2,000+ miles to their destination, using tons of diesel fuel and resulting in less fresh produce. AppHarvest produces crops with no pesticides with greater nutrient density, and from their central location can reach 70% of the U.S. population in one day resulting in 80% less diesel fuel and much lower emissions. However, the larger environmental and economic benefit is in how the crops are grown — using 90% less water and yielding thirty times more per acre.
Moreover, AppHarvest’s resources are nature based – the greenhouse structure allows them to use 12 hours of sunlight per day and they collect the heavy Kentucky rainfall for their system resulting in a much less adverse effect on the water supply while greatly decreasing their cost of production by not having to pay for water. The greenhouse system also eliminates any weather or seasonal constraints, allowing the company to grow more efficiently 365 days per year.
While the company has no historic revenue, they just made their first delivery of beefsteak tomatoes on January 19, 2021, to customers that include Walmart, Kroger and Publix
US - OHIO: Thinking And Growing Inside The Box
A brother-sister team has taken the mechanics of farming out of the field and into a freight container. “We are growing beautiful plants without the sun; there’s no soil, and so it’s all a closed-loop water system,” Britt Decker, co-owner of Fifth Season FARM, said
A brother-sister team has taken the mechanics of farming out of the field and into a freight container.
“We are growing beautiful plants without the sun; there’s no soil, and so it’s all a closed-loop water system,” Britt Decker, co-owner of Fifth Season FARM, said. “We use non-GMO seeds, completely free of herbicides and pesticides, so the product is really, really clean. In fact, we recommend people don’t even wash it, because there’s no reason to.”
Fifth Season FARM is unique in many ways; the 3-acre hydroponic farm is contained in a 320-square-foot freight container that sits along 120 S. Main St. in Piqua, with everything from varying varities of lettuce, to radishes, to kale and even flowers in a climate-controlled smart farm that allows Decker and his sister, Laura Jackson, to turn crops in a six- to eight-week cycle. The crops spend 18 hours in “daytime” every day, and the farm uses 90% less water than traditional farming.
“It’s tricky because we’re completely controlling the environment in here. It’s kind of a laboratory more than a farm,” Decker said. “I think there’s about 50 of them around the world right now. These are really international, and they’re perfect for places that are food deserts where they can’t grow food because of climate or other reasons. It gives them a way to grow food in the middle of nowhere.”
Image from: Sidney Daily News
Decker and Jackson, along with their brother Bill Decker, also do traditional farming and grow corn, wheat and soybeans, but Decker said they were looking for a new venture that would help lead them to a healthier lifestyle and learn something new.
“Just with the whole local food movement becoming more and more important and food traceability, we just thought it would be a great thing to bring to our community to help everyone have a healthier lifestyle,” Decker said. “People love food that’s grown right in their hometown and the shelf-life on it, when you get it home, is remarkable. It’ll keep for two weeks.”
Image from: AgFunder News
Currently, Decker and Jackson are growing a half-dozen variety of specialty lettuces that include arugula, butterhead and romaine, as well as specialty greens like kale and Swiss chard, and even radishes and flowers. They received their freight container at the end of July and set up their indoor farm over two weeks; while the farm has been in operation for less than six months, Decker says that they’re growing beautiful product.
They have also started growing micro-greens, said Decker. Micro-greens are immature plants which are 1 to 3 inches tall and are in a 5-inch by 5-inch container.
“People will use them as garnishments and in smoothies,” said Decker. “Since they are immature plants, they have an intense flavor.”
Decker said they are growing wheat germ, broccoli and spicy salad mixes.
They’ve also started moving forward with sales and marketing. Fifth Season FARM has partnered with the Miami County Locally Grown Virtual Market to sell their products to the community. They also take orders through their website, customers can opt to pick up their orders between 4 and 6 p.m. on Wednesdays, or Decker and Jackson will deliver products up to five miles from the farm. Decker said that Fifth Season FARM is also in discussions with three restaurants in the area about including their specialty greens on their menus.
Decker said they also plan to attend the Sidney Farmers Market when it opens for the spring/summer season.
“We’re really just getting going,” Decker said. “While we were learning to grow products, we didn’t want to overcommit to a restaurant or grocery store before we knew we could really grow beautiful product, so we’ve been donating product every week to the food pantry at the Presbyterian Church. It feels good to plant the seeds and watch them grow, and it feels good to make sure that people who aren’t getting the proper nutrition are getting some.”
UNFI Picks Up Living Greens Farm Products in Midwest Expansion
Living Greens Farm (LGF), the largest vertical, indoor aeroponic farm in the US that provides year-round fresh salads, salad kits, microgreens and herbs, announced the addition of significant new retail distribution of its products in the upper Midwest to independent, specialty, and co-op retailers
I|mage from: Living Green Farms
Living Greens Farm (LGF), the largest vertical, indoor aeroponic farm in the US that provides year-round fresh salads, salad kits, microgreens and herbs, announced the addition of significant new retail distribution of its products in the upper Midwest to independent, specialty, and co-op retailers.
Starting February 2021, LGF’s full line of products featuring ready-to-eat bagged salad products (Caesar Salad Kit, Southwest Salad Kit, Harvest Salad Kit, Chopped Romaine, and Chopped Butter Lettuce) will be carried by UNFI Produce Prescott (formerly Alberts Fresh Produce). UNFI Produce Prescott is a division of UNFI, which distributes food products to thousands of stores nationwide. Their focus is on independent, specialty and co-op retailers.
UNFI has eight warehouses nationwide. LGF’s products will be carried by their upper Midwest location, located just across the river from the Twin Cities in Prescott, WI. This distribution center services hundreds of retailers throughout Minnesota, Wisconsin, Illinois, North Dakota, South Dakota, Missouri, Iowa and Nebraska. UNFI is the first national Certified Organic distributor, something they take a lot of pride in. Their produce and floral businesses are rooted in local farms and seasonal import growers.
LGF’s proprietary vertical indoor farming method yields the highest quality and freshest produce available. This is because there are no pesticides or chemicals used in the growing process. And because LGF’s growing, cleaning and bagging process significantly reduces handling and time to the retail shelf, consumers enjoy the freshest product on the market. These benefits continue to attract new users and new retail distribution as UNFI Produce Prescott is the second UNFI location to carry LGF. In December, UNFI’s Hopkins, MN location began offering LGF products.
For more information on why Living Greens Farm products are the cleanest, freshest and healthiest farm salads and greens available, go to www.livinggreensfarm.com.
Fifth Season Takes Vertical Farming to a Whole New Level
Fifth Season’s verdant baby spinach screams farm fresh even though it’s grown nowhere near traditional farmland. The sweet and slightly crunchy greens are grown in a Braddock warehouse on racks stacked 30 feet high. Located just a stone’s throw from U.S. Steel’s Mon Valley Works Edgar Thomson Plant, it is urban farming at its core
Image from: Pittsburgh Post-Gazzette
Fifth Season’s verdant baby spinach screams farm fresh even though it’s grown nowhere near traditional farmland. The sweet and slightly crunchy greens are grown in a Braddock warehouse on racks stacked 30 feet high. Located just a stone’s throw from U.S. Steel’s Mon Valley Works Edgar Thomson Plant, it is urban farming at its core.
What makes the vertical farming operation especially unique is that it is automated and robots call the shots. About 40 to 60 machines are involved in every step of the life of the spinach and other leafy greens, from planting the seed to providing nutrients to the final packing.
Fifth Season does employ local “farm workers” to assist the robots in seeding, harvesting, packaging, quality assurance and control using computer software, but there is no human touch involved through it all.
“The first time someone ever touches the spinach leaf with a finger is when the package is opened,” says Grant Vandenbussche, chief category officer.
Co-founded by brothers Austin and Brac Webb and Austin Lawrence, Fifth Season started a year ago. Within months it was rolling out its baby spinach, leafy greens and salad kits.
“We wanted a name that represents what we are doing,” says Austin Webb, 32, who also is the CEO. “It is a call to the fact we have created an entirely new season. It is 24/7, 365 with the technology we have built.”
None of them planned to become modern farmers, says the Carnegie Mellon University grad, but they turned to vertical farming because it was an efficient, economically sustainable way to solve land and water woes.
Image from: thespoon.tech
‘Fields’ of Greens
Fifth Season grows an equivalent production of 200 acres in 25,000 square feet of grow space. Its “fields” are stacked on top of one another in vertical shelves. When you add up all that surface area of grow space, it is more like 126,000 square feet.
“We also quickly turn crops at the farm,” Mr. Vandenbussche says.
While spinach takes about 40 days to grow outdoors and can be harvested only twice during its peak season, it takes the crop only three or four weeks to grow in the controlled environment and is harvested 19 times. Once the plants are harvested, a new cycle of reseeding begins with fresh media, seeds and nutrients.
“That’s why we get so much more productivity,” he says. “We are immediately reseeding our ‘land.’”
This controlled environment yields quality produce because it is always peak season at Fifth Season, says Chris Cerveny, who heads the Grow R&D division. Greens are grown in the same conditions year-round, getting the exact amount of nutrients and water they need. Because pests and airborne toxins also are kept at bay, crops can be produced without pesticides.
All that TLC comes through in the slightly curled baby spinach, which is sweet and not grassy. The leaf doesn’t wilt or get slimy or lose its slight crunch even after two weeks of refrigeration.
A lot of thought was given even for the curl, which gives the spinach a stronger volume, making it look full and bountiful. The curl also makes the spinach more forkable unlike its flat-leaf counterpart that is hard to stab on a plate.
Other leafy greens such as kale, mustard, Chinese cabbage, green tatsoi and purple pac choi are featured in two blends — Bridge City and Three Rivers. Fifth Season plans to roll out its Romaine lettuce in spring.
The greens also are found in four types of salad kits — Sweet Grains (blended greens, quinoa, chickpeas, corn, feta and poppy seed dressing), Crunchy Sesame (blended greens, farro, sesame sticks, dried cranberries and ginger-mandarin dressing), Toasted Tuscan (spinach, lentils, sun-dried tomatoes, bagel chips and vinaigrette), and Spiced Southwest (blended greens, black beans, pepitas, cotija cheese, corn-salsa sticks and chipotle ranch dressing) — which are available online and in Giant Eagle stores. A fifth salad kit is in the works and is being called “a shakeup of one of the most classic salads.”
While machines are a big part of what Fifth Season does, it seeks to keep human connection alive. It recently launched a recipe blog for those who have an appetite for cooking and writing, The Green Room is devoted to cataloging personal memories, dream meals and recipes via short stories.
Fifth Season also has partnered with the Penguins and is providing greens for the team’s pregame meals for the 2020-21 season.
“We want people in Pittsburgh to be able to eat the exact same delicious blend of greens that Sidney Crosby and company are eating,” Mr. Webb says. “We want people to know that there’s a new way to grow food and to eat and experience it.”
Image from: Next Pittsburgh
It’s All Under Control
Everything from seeding to packaging is done in four rooms. The process starts in the seeding and processing room, where seeds and growing media are placed inside black planter-like boxes called inserts. Each has a unique code that’s traced by a software system. The inserts go on white trays that pass through a photo station, feeding information to the computer system, and then glide into the bio dome.
There are two rooms in the bio dome, each with a grow space of 12,500 square feet. They’re lit up with a pinkish-purplish glow from high-efficiency LED light bulbs that mimic the different seasons of the year.
“They are positioned over the plants at different heights depending on stage of growth,” Mr. Cerveny says. “This is partly how we can provide consistently ideal growing conditions.”
As the plants grow, they are moved by a robot to optimize their growth cycle. Full-grown crops are transferred to the harvesting room by another robot.
“Harvesting is where it becomes like a Willy Wonka factory,” Mr. Vandenbussche says.
Long rows of trays filled with tiny plants are sent on a conveyor system to a station where workers inspect them for quality with surgical tools. After inspection, the plants are harvested by a robot and then immediately ride up a tall conveyor to be packaged and sealed in a 34- to 36-degree room so they remain fresh.
“Every crop we grow gets evaluated for maximum flavor, volume, crunch and color,” he says.
The plants’ intense, dark color is controlled by LED light bulbs, which are dialed up or down to get the correct hue. Although they never see the sun, the greens don’t get into a funk as humans might.
“What humans see in terms of light and how chlorophyll responds during photosynthesis are two different things,” Mr. Cerveny says. “Plants really only need red and blue light to grow effectively. We include some additional colors to help bring out other quality aspects of our crops, but providing the full sunlight spectrum is effectively a waste of energy, especially indoors.
“To the human eye, it looks like the plants live in a land of purple and pink lights, but they are perfectly happy there.”
Even though the environment is controlled and the software system is constantly updated, no two plants are exactly the same. Some fight for light more than others. Some might fail the quality control test and end up in a compost waste facility if their flavor is off or their color is not right.
“That is what is so amazing. We have more control than any other farmer, and yet we have limitations. Every seed is different,” Mr. Vandenbussche says. “They are plants. They are real living organisms.”
“Autonomy Will Not Happen Until We Start Sharing Data”
In an emerging industry with companies eager to prove their technologies’ worth, Sensei Ag remains form-factor agnostic, meaning that the agtech company remains unbiased towards different farm hardware solutions – focusing more on software and plant biology. Sensei Ag is a market-changing agtech company that develops agile growing solutions through a highly iterative approach to farming, focused on improving the nutritional quality of fruits and vegetables while also reducing production costs. The company combines plant science, computer vision, machine learning, automation and artificial intelligence into its growing systems
In an emerging industry with companies eager to prove their technologies’ worth, Sensei Ag remains form-factor agnostic, meaning that the agtech company remains unbiased towards different farm hardware solutions – focusing more on software and plant biology.
Sensei Ag is a market-changing agtech company that develops agile growing solutions through a highly iterative approach to farming, focused on improving the nutritional quality of fruits and vegetables while also reducing production costs. The company combines plant science, computer vision, machine learning, automation and artificial intelligence into its growing systems.
According to Sensei Ag CEO Sonia Lo, remaining form factor agnostic is key to the company’s mission of providing hyper-nutritious food to as large a consumer base as possible, which it achieves through both vertical farms and greenhouses.
Image from: Sensei Ag
“We believe that the most robust data comes from operating farms of multiple types. So, not just vertical farms, but also low-tech and high-tech greenhouses. And with vertical farms, we are looking at a number of form factors. Our end goal is to be a grower’s resource and know more about growing at scale with different form factors than anyone else.”
The company is also a strong advocate for open data in the vertical farming industry, which is currently lacking, as evidenced by the siloed development of multiple systems and products, some of which cannot be easily integrated into third-party systems.
“There are lots of data flows and increasingly inexpensive farm management systems. The question, then, is the organization of data into intelligence. Intelligence facilitates autonomy, and as we manage data flows, more farms can become autonomous. But I don’t think autonomy will happen until we start sharing data. For example, we saw an automation supplier with a great robot.
The problem was the robot only works in their ecosystem, so you have to buy the whole farming solution in order for the one robot to work. Ideally, that robot would be plug and play and be able to work in greenhouses and vertical farms,” says Sonia.
Image from: Sensei Ag
According to Sonia, open data in the vertical farming industry may currently be restricted by the dominance of venture financing, which has its own return mandates to fulfill and sometimes wants a “winner takes it all” mentality for the ventures it chooses to back. While such financing has allowed the vertical farming industry to emerge, it may ultimately hinder the industry’s scalability and information sharing.
“There is definitely a capital model in Silicon Valley and in venture capital world in general which is not focused on profitability but is focused on technological achievement and market penetration. We saw this in solar and in the renewables industry when multiple venture capital funds invested in solar assets. Then, the bottom fell out because government subsidies fell away in certain jurisdictions.
I hope that agricultural infrastructure currently financed by venture capital will not necessarily follow the same pathway as solar, but will instead find a public-private partnership model. At some point, these farms need to demonstrate a profit for the debt capital markets to allow scale to occur.”
Image from: Sensei Ag
By embracing open data and transparency, Sonia explains that the vertical farming industry can further mature and iterate with technology to continue lowering costs. By continuously collecting and sharing data from different farm forms, the vertical farming industry would have better insights into the true costs which, according to Sonia, “helps drive scale because it enables the finance community to understand how the farms can be risk assessed and financed.”
Looking ahead, Sensei Ag hopes to form partnerships around the world to bring its innovative, data-driven growing systems across the globe. Taking the Middle East, China and Japan as examples, Sonia explained that the goal would be to choose strategic partners in each region whose local knowledge and business prowess would allow Sensei Ag to iterate its technologies appropriately and serve local markets, bringing cost-competitive farming techniques and nutritious, local produce around the world.
VIDEO: SANANBIO Announces the Availability of its Unmanned Vertical Farming System UPLIFT to Global Growers
“Pour your seeds in the seeder and do nothing but expect fresh veggies to be harvested in a matter of days,” said Zhan Zhuo, co-founder, and CEO of SANANBIO. UPLIFT has been under tests in the last two years and proves to be commercially feasible and ready to be established as turnkey projects for worldwide growers
XIAMEN, CHINA, July 16, 2020--SANANBIO, one of the world’s largest indoor farming technology providers announces the availability of its unmanned vertical farming system, a.k.a. UPLIFT, to growers globally.
“Pour your seeds in the seeder and do nothing but expect fresh veggies to be harvested in a matter of days,” said Zhan Zhuo, co-founder, and CEO of SANANBIO. UPLIFT has been under tests in the last two years and proves to be commercially feasible and ready to be established as turnkey projects for worldwide growers. “It can produce 6-8 tons of fresh leafy greens every day on a farm of only 5,000 sqm. By stacking up layers higher than a traditional vertical farm, we can best utilize the space to increase the yields. With the same farm size, UPLIFT’s productivity is 6 times of a 6-layered vertical farm.
The increased yield means a lowered cost, which in turn makes our produce affordable to more people. We’ve also upgraded our water circulation system so that 60% of the water can be absorbed by plants and the remaining 40% recycled. This fact is especially meaningful for the regions of the world that struggle with water shortages and harsh agricultural conditions.” said Zhan.
UPLIFT uses PlantKeeper, a proprietary indoor farming management system, to control and monitor environmental factors so farm operators can be updated with real-time growing conditions throughout the farm. By using simple and proven robotics and conveyor systems, UPLIFT automates seeding, transplanting, harvesting, plant transporting, and system cleaning, reducing labor intensity to its lowest.
“We’re phasing out manpower to make our produces available for more people. So we can say that UPLIFT is unmanned for humanity,” said Zhan.
About SANANBIO
SANANBIO is a joint-venture by Sanan Optoelectronics, one of the world’s largest LED manufacturers, and the Institute of Botany of Chinese Academy of Sciences, China’s leading institute in plant science. Comprised of LED experts and plant scientists, SANANBIO is able to provide simple indoor farming solutions for global growers. The RADIX, a patented vertical hydroponic system, has been widely endorsed by growers in more than twenty countries.
“We’re phasing out manpower to make our produces available for more people. So we can say that UPLIFT is unmanned for humanity,” said Zhan.
To learn more about UPLIFT, please contact SANANBIO at global@sananbio.com or visit its LinkedIn page https://www.linkedin.com/company/fujiansanansinosciencephotobiotechcoltd.