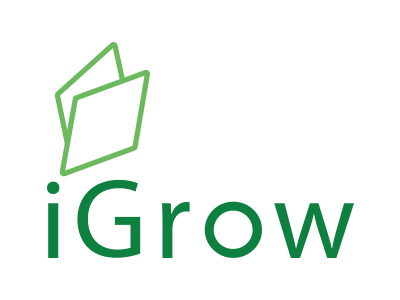
Welcome to iGrow News, Your Source for the World of Indoor Vertical Farming
5 Ways Vertical Farming Is Improving Nutrition
Vertical farming has taken cities by storm, enabling urbanites to grow produce within their own homes and entrepreneurs to meet the growing demand for fresher and higher quantities of locally-grown produce
August 3, 2021
Vertical farming has taken cities by storm, enabling urbanites to grow produce within their own homes and entrepreneurs to meet the growing demand for fresher and higher quantities of locally-grown produce.
We often hear about vertical farms using water sustainably, 95% less than traditional open field harvesting, to provide superior tasting crops.
But, how is this soilless farming technique impacting human health?
#1: Harvesting On Demand At Peak Freshness
&ever’s Grow Tower; image sourced from &ever
With the power to farm vertically within one’s own home, consumers can now harvest their crops only moments before consumption, resulting in a higher nutritional value, better-tasting greens, and significantly less food waste.
&ever’s Grow Box is a one-stop-shop system for leafy greens and can even be operated by untrained staff, according to &ever. The proprietary technology of the climate cell creates a steady microenvironment to allow plants to grow independently of weather, seasons, and pests, plus the use of “dryponics” helps keep the plants alive until the consumer is ready to harvest.
The key here is the freshness of the crops. Produce no longer has to travel miles and miles through countries or states to get to your kitchen table. This time saved in travel is also nutritional value preserved in the crops. Another benefit is that no artificial preservatives, like wax coatings, are needed to keep the produce consumer-ready.
#2: Growing Under Perfect Conditions
Vertical farms generally use hydroponics or aeroponics to grow their plants in nutrient-enriched water that can be carefully monitored through digital sensors. This degree of control over plant nutrient supply means that the fertilization strategies are designed to match the plant needs for all 14 essential plant nutrients throughout the growth period.
Control mechanisms are also utilized to balance temperature, humidity, and carbon dioxide levels in the grow facility and deliver the optimal combination of these factors for the specific crop or crops being grown. With climatic conditions playing no part in the crop’s success, growers have reliable year-round production of greater quantity and the highest quality.
In this sense, vertical farms are able to spend more time enhancing nutritional value and less time worrying about the success of their harvest. The SKY HIGH program led by Dr. Leo Marcelis of Wageningen University in the Netherlands, is one such program exploring factors that increase crop nutrients.
#3: Tailoring The Development Of Genetic Varieties
Vindara argues that the difference is in the seeds.
By designing seeds specifically for indoor vertical farms - “entirely through analytics, not gene-editing or GMOs” - this company claims to amplify crop yield, appearance, nutrition, and flavor.
Their seed-design system takes a data-driven approach to deliver any kind of genetic variety, tailored to each customer’s needs. According to Vindara, each property is individually editable.
Today’s seeds are still being bred for resistance to disease and pests, designed for long storage and transportation that isn’t as relevant for indoor vertical farming operations. This results in genetic tradeoffs that reduce nutritional value. Vindara removes these limitations that traditional seeds impose by delivering nutrient-dense seeds to growers.
#4: Growing Foods Adapted To Dietary Needs
Alongside fresh and flavorful food, there has been a growing demand and need for foods adapted to specific dietary needs.
Prime Delica, for example, has conducted research with Tamagawa University, CCS, and Signify to determine the optimal light recipe to increase the vitamin levels and nutritional value of lettuce. Dr. Céline Nicole from the Philips Lighting Research team has similarly studied the effects of the daily light integral (DLI) and light quality on the nitrate levels of arugula and spinach, alongside the vitamin C levels of arugula and tomatoes.
Through vertical farming, the Korea Institute of Science and Technology (KIST) has also successfully produced low potassium kale with increased glucosinolate content as a novel dietary option for renal dysfunction patients.
Growing foods with adapted dietary needs could thus make a world of difference in ensuring that we receive greater control over our diets, and allow us to design food-as-medicine alternatives to conventional produce.
#5: Food Safety
In using controlled growing environments, vertical farms are intrinsically free of harmful pesticides. Because of implementing biological controls, there is no need to contaminate crops with potentially toxic chemicals.
According to the CEA Food Safety Coalition, “traditional food safety risk profiles associated with conventional farming include examining the physical hazards and microbial hazards from water use, herbicide, and pesticide use, and impact from animals and animal byproducts. These do not impact CEA growers in the same way, if at all.” Even though the risk of contamination isn’t zero within CEA facilities (as seen in this recent news), CEA-grown produce has a reduced risk of such occurrences.
Compared to traditional field-grown crops, we find that the EPA regulates pesticides individually and not collectively, meaning that the pesticides can have a cumulative toxic loading effect on human health.
Studies have shown that pesticides most impact farmworkers and pesticide applicators with symptoms like nausea, abdominal cramps, diarrhea, dizziness, anxiety, and confusion. This long list of side effects tells us that pesticides are not to be taken lightly. As a result, it’s best to avoid them at all costs. Fortunately, vertical farms help us do precisely this.
Click here for more information.
Source and Photo Courtesy of Agritecture
80 Acres Farms CEO Mike Zelkind Joins CEO Keynote Line-Up For In-Person Indoor Ag-Con In Orlando Oct. 4-5, 2021
80 Acres Farms CEO Mike Zelkind will lead the Day Two CEO Keynote Address for the in-person October 4-5, 2021 edition of Indoor Ag-Con at the Hilton Orlando.
July 23, 2021
80 Acres Farms CEO Mike Zelkind will lead the Day Two CEO Keynote Address for the in-person October 4-5, 2021 edition of Indoor Ag-Con at the Hilton Orlando. Themed “Growing Your Business,” the trade show and conference for indoor |vertical farming | controlled environment agriculture will give attendees the opportunity to explore new resources on the expo floor and hear from Zelkind, other CEOs, thought leaders and industry experts from today’s cutting-edge farms and innovative companies.
“80 Acres has been making headlines this year in a number of areas – from plans to expand its produce offerings to new research initiatives. We are so excited to be returning to our live, in-person format in October and offering a platform for forward-thinking industry leaders like Mike Zelkind to share the indoor farming innovations he and the 80 Acres team are working on,” says Brian Sullivan, co-owner, Indoor Ag-Con LLC.
Scheduled for day two, October 5, 2021, Mike Zelkind’s address will be held from 11:30 am – 12:20 pm. In addition to his CEO role with 80 Acres Farms, Mike is also Board Member of Infinite Acres (est. 2019), a vertical farming leader providing customers with fresh, nutritious fruits and vegetables at affordable prices.
Utilizing world-class technology and analytics, 80 Acres Farms offers customers pesticide-free food with a longer shelf-life and the highest food safety standards while using fewer natural resources to produce over 300x more food on less than 1% of the footprint. Winner of Fast Company’s eighth “Most Innovative Company in North America,” 80 Acres was also a finalist for Red Herring’s Top 100 North America award, featured two years in a row on Forbes “Best Start-up List,” and awarded the eleventh spot on the “FoodTech 500” list.
For more than 25 years, Mike has been working with top-tier food companies such as General Mills, Del Monte, Bumble Bee, and ConAgra Foods and top-tier consultancies and start-ups AT Kearney and ICG Commerce, focusing on the food industry. Over the last 15 years, he has worked with Private Equity (such as Oaktree Capital and Bain Capital’s Sankaty) to drive over $2.5B of shareholder value.
In addition to headliner keynote sessions from leaders like Mike Zelkind, other 2021 event highlights include:
ROBUST 2021 CONFERENCE SCHEDULE NOW IN DEVELOPMENT
The 2021 conference will include a full roster of keynote sessions, panel discussions, fireside chats and presentations offering a deep dive into three core tracks – Business & Marketing, Science & Technology and Alternative Crops. Other keynotes will be led by David Rosenberg, CEO, AeroFarms and Sonia Lo, CEO, Sensei Ag.
The extensive educational conference will be joined by other new initiatives and show highlights, including:
NEW LOCATION: HILTON ORLANDO – DISCOUNTED HOTEL RATES, TOO
Indoor Ag-Con’s Hilton Orlando venue makes it the perfect opportunity for a business vacation. Centrally located to all major theme parks and attractions, it is just minutes from the eclectic dining scene and entertainment of International Drive. What’s more, the Hilton Orlando resort sits on more than 26 acres of lush landscaping and tropical inspirations making it a true destination of its own. Indoor Ag-Con has arranged for discounted hotel rates for attendees and exhibitors starting as low as $129/night. Complete details are available on the show website.
EXPANDED EXHIBIT FLOOR & NETWORKING OPPORTUNITIES
The Indoor Ag-Con team is working to bring even more resources for farmers/growers to explore across all sectors – everything from IT, energy, AI and lighting solutions to substrates, vertical farming solutions, business services and much more. Attendees and exhibitors alike will also have even more networking opportunities with daily luncheon sessions and receptions on the show floor.
QUICK FACTS:
WHEN: Monday, October 4 – Tuesday, October 5 , 2021
WHERE: Hilton Orlando, 6001 Destination Pkwy, Orlando, FL 32819
INFO: For information on exhibiting or attending www.indoor.ag or e: suzanne@indoor.ag
ABOUT INDOOR AG-CON LLC
Founded in 2013, Indoor Ag-Con has emerged as the premier trade event for vertical farming | indoor agriculture, the practice of growing crops in indoor systems, using hydroponic, aquaponic and aeroponic techniques. Its events are crop-agnostic and touch all sectors of the business, covering produce, legal cannabis |hemp, alternate protein and non-food crops. In December 2018, three event industry professionals – Nancy Hallberg, Kris Sieradzki and Brian Sullivan – acquired Indoor Ag-Con LLC, setting the stage for further expansion of the events globally. More information:www.indoor.ag
ABOUT 80 ACRES FARMS
80 Acres Farms is a vertical farming leader providing customers with the freshest and most nutritious fruits and vegetables at affordable prices. Utilizing world-class technology and analytics, the Company offers customers a wide variety of pesticide-free food with a longer shelf life that exceeds the highest food safety standards. More information: www.eafarms.com
Highlighting The Potential of Dutch Horticulture In Vertical Farming
Indoor Farming Holland aims to bring companies together to see where their knowledge can be developed and applied in the vertical farming space. “We’re focusing on the combination of technical solutions with plant science, where Holland has a great proposition.”
“The Dutch are falling behind when it comes to vertical farming,” says Judith van Heck, Community Builder at Indoor Farming Nederland. “As we’re so tremendously good at greenhouse growing there is relatively less interest in building vertical farms in the Netherlands. In comparison to countries such as the US, this has resulted in lower investments. That’s why we started the initiative Indoor Farming Nederland. We want to help the Dutch horticulture sector to develop the potentially very interesting sector, and we also want to highlight the international potential of Dutch horticulture in vertical farming.”
Indoor Farming Holland aims to bring companies together to see where their knowledge can be developed and applied in the vertical farming space. “We’re focusing on the combination of technical solutions with plant science, where Holland has a great proposition. We, therefore, believe that we can obtain optimal results from vertical farms and take the lead on that,” Judith notes.
“Due to many things happening around vertical farming and innovative solutions that are brought to market, we’ve created a government-backed organization to stimulate indoor farming amongst Dutch horticultural companies,” says Gus van der Feltz, project leader for the Fieldlab Vertical Farming. In the Fieldlab Vertical Farming, an important collaboration is established between South Holland knowledge institutions and companies that are engaged in the production of vertically grown products, the sale of vertically grown products, and suppliers of technologies for vertical farms.
Gus van der Feltz and Judith van Heck
Increasing awareness
The Fieldlab is supported by the European Fund for Regional Development of the European Union and the Province of South Holland. Now, the organization’s activities consist of four different ‘packages’ which they’d like to elaborate on throughout the Dutch horticulture industry. Vertical Farming Zuid-Holland received a subsidy to develop a foundation for potential market entrants that consists of four different packages.
The Fieldlab, working together with Indoor Farming Nederland, wants to increase awareness of the added value of vertical farming. Firstly, by using market research to understand consumers, growers, retailers, and the supply chain’s perspective on vertical farming. “Through market research, we want to highlight the benefits and processes that could be improved,” says Gus. Secondly, the organization will do research and testing to generate knowledge on vertical farming and recipes through development and innovations by Dutch horticulture companies.
Thirdly, “we want to educate and train people,” says Gus. “We’re working on developing training programs specifically focusing on vertical farming. From the technical side of things to running a farm and selling your produce successfully.” Last but not least, a sector-related platform is to be constructed to create a long-term and sustainable network the industry can fall back to. In collaboration with Vertical Farming Fieldlab, for the industry to further develop knowledge in Dutch horticulture, the organization consists of multiple companies, such as Own Greens, Delphy, Signify, WUR Bleiswijk, Vertify, Logiqs, Proeftuin Westland, InHolland, WUR Wageningen, Future Crops (Poeldijk).
Judith explains that the community works with jointly formulated ambitions. “We help this cluster of companies to obtain as much knowledge as needed. We stimulate them to co-create on several challenges. One of the ambitions is to communicate the potential of the cluster and indoor farming products to various target groups. Amongst other things, we are creating a white paper regarding the general statements about vertical farming and the complex reality of it.” Next to that, the organization is exploring the feasibility of a collective market intelligence tool to see where vertical farming can add value internationally. However, the community aims to not only help Dutch entrepreneurs but the collective market. One of the ambitions, for instance, is to communicate the potential of the cluster to various target groups within, but especially also outside, the Netherlands.
Amongst other things, Indoor Farming Nederland will create a whitepaper that states all facts concerning vertical farming. Next to that, the organization is exploring the feasibility of a collective market intelligence tool to see where vertical farming can add value internationally. They’re doing so by looking at climate, population density, food patterns, availability of water, and energy. Also by analyzing where the most potential is for vertical farming, or hybrid solutions even, in combination with greenhouses.
For more information:
Indoor Farming Nederland
Gus van der Feltz, Project leader
gus@feltzwerk.nl
Judith van Heck, Community Builder
judith@imagro.nl
Publication date: Wed 16 Jun 2021
Author: Rebekka Boekhout
© HortiDaily.com
Certhon Wraps Up 7th Raspberry Trial Successfully
After successfully growing strawberries in the Certhon Innovation Centre (CIC), the company has decided to take on another trial of growing fruits indoors.
“Raspberry isn’t the first crop that comes to mind when figuring out which crops to grow indoors,” Andrea Huegler, R&D Engineer and Agronomist at Certhon said. “However, we accepted the challenge and decided to go for it as there are a lot of benefits to growing it in a controlled environment.”
After successfully growing strawberries in the Certhon Innovation Centre (CIC), the company has decided to take on another trial of growing fruits indoors. Certhon has been doing lots of research on indoor farming for a long time now. This has allowed them to investigate how to grow more complex crops in a controlled environment without daylight.
Andrea Huegler
Trial results
The main advantage of growing this crop indoors is having higher yields and consistent quality year-round. Certhon sees great opportunities ahead for the crop, due to its premium status and short shelf life. “It makes it a perfect candidate to be grown indoors.” During this trial, common raspberry cultivars were chosen. Certhon used chilled raspberry canes from a propagator, pollination by bumblebees and top and interlighting was used to flourish the crops. The harvesting period comprises 10 weeks, out of a total cultivation cycle of 21 weeks and is expected to end in July 2021.
Cultivation risks
The research was mainly about investigating the right transition of the vegetative state of the crop to the generative state. Andrea says that balancing the climate and light with energy consumption is the trickiest part here. “Ever since the first raspberry trial we’ve been trying to balance out the reduction of energy use, having an X amount of yield at a great quality and extending the harvesting period. Throughout the trials, we have obtained nearly twice as much yield compared to the traditional Dutch polytunnel producers in the summer,” Andrea notes.
However, raspberry cultivation isn’t without challenges. “One of the risks that could come up is growing grey mold,” explains Andrea. “If nectar isn’t removed well from the flower, the fruit can grow mold or have a grey undertone. However, if you manage your humidity wisely, the incidence is severely reduced. That’s the idea behind the CIC, optimizing growing recipes and eventually expanding the product portfolio because we want to provide a wide selection of product options to our clients.”
Greenhouse application
The knowledge that is generated in the CIC can also be applied to the cultivation of raspberries in greenhouses. Growing these crops indoors allows Certhon to generate ideal growing conditions and maximum potential for raspberry cultivation. With this knowledge, Certhon generates a blueprint that growers can follow in greenhouse cultivation as well.
Andrea explains, “For instance, the blueprint can be followed when growers want to know when to: provide extra lighting, shading, or adjust the humidity. In this way, ideal growing conditions can be mimicked to achieve the highest quality and yield possible in a greenhouse.”
Cane risk
Another, very important aspect is the quality of the raspberry canes. In order to have good production, your raspberry canes need to be of good quality and pest-free. “This cannot always be guaranteed, '' says Andrea, “since they are propagated outdoors and therefore bound to the pressures of external influences, such as climate. Although we have not tried it ourselves yet, we think the next step is to also propagate raspberry canes in a controlled environment without daylight.”
For more information:
Andrea Huegler, R&D Engineer and Agronomist
Certhon
andrea.huegler@certhon.com
ABC Westland 555
P.O. Box 90
2685 ZH Poeldijk
The Netherlands
Tel: +31 174 22 50 80
www.certhon.com
Publication date: Mon 7 Jun 2021
Author: Rebekka Boekhout
© HortiDaily.com
Vertical Farming Startup Oishii Raises $50m In Series A Funding
“We aim to be the largest strawberry producer in the world, and this capital allows us to bring the best-tasting, healthiest berry to everyone.”
By Sian Yates
03/11/2021
Oishii, a vertical farming startup based in New Jersey, has raised $50 million during a Series A funding round led by Sparx Group’s Mirai Creation Fund II.
The funds will enable Oishii to open vertical strawberry farms in new markets, expand its flagship farm outside of Manhattan, and accelerate its investment in R&D.
“Our mission is to change the way we grow food. We set out to deliver exceptionally delicious and sustainable produce,” said Oishii CEO Hiroki Koga. “We started with the strawberry – a fruit that routinely tops the dirty dozen of most pesticide-riddled crops – as it has long been considered the ‘holy grail’ of vertical farming.”
“We aim to be the largest strawberry producer in the world, and this capital allows us to bring the best-tasting, healthiest berry to everyone. From there, we’ll quickly expand into new fruits and produce,” he added.
Oishii is already known for its innovative farming techniques that have enabled the company to “perfect the strawberry,” while its proprietary and first-of-its-kind pollination method is conducted naturally with bees.
The company’s vertical farms feature zero pesticides and produce ripe fruit all year round, using less water and land than traditional agricultural methods.
“Oishii is the farm of the future,” said Sparx Group president and Group CEO Shuhei Abe. “The cultivation and pollination techniques the company has developed set them well apart from the industry, positioning Oishii to quickly revolutionise agriculture as we know it.”
The company has raised a total of $55 million since its founding in 2016.
Would You Like To Host A Strategic HQ In Decentralized Agriculture And Food Supply Systems
Our vision is to strengthen community resiliency and reduce food insecurity on a global scale over time
We would appreciate a city location in Central Europe in order to facilitate our EU-labelled strategy.
Our vision is to strengthen community resiliency and reduce food insecurity on a global scale over time.
For questions and tentative interest please contact:
thomas.tapio@gmail.com
Strasbourg 27th February, 2021 🇫🇷🇪🇺
Little Leaf Farms Raises $90M to Grow Its Greenhouse Network
Massachusetts-based Little Leaf Farms has raised $90 million in a debt and equity financing round to expand its network of hydroponic greenhouses on the East Coast. The round was led by Equilibrium Capital as well as founding investors Bill Helman and Pilot House Associates. Bank of America also participated.
by Jennifer Marston
Image from: Little Leaf Farms
Massachusetts-based Little Leaf Farms has raised $90 million in a debt and equity financing round to expand its network of hydroponic greenhouses on the East Coast. The round was led by Equilibrium Capital as well as founding investors Bill Helman and Pilot House Associates. Bank of America also participated.
Little Leaf Farms says the capital is “earmarked” to build new greenhouse sites along the East Coast, where its lettuce is currently available in about 2,500 stores.
The company already operates one 10-acre greenhouse in Devins, Massachusetts. Its facility grows leafy greens using hydroponics and a mixture of sunlight supplemented by LED-powered grow lights. Rainwater captured from the facility’s roof provides most of the water used on the farm.
According to a press release, Little Leaf Farms has doubled its retail sales to $38 million since 2019. And last year, the company bought180 acres of land in Pennsylvania on which to build an additional facility. Still another greenhouse, slated for North Carolina, will serve the Southeast region of the U.S.
Little Leaf Farms joins the likes of Revol Greens, Gotham Greens, AppHarvest, and others in bringing local(ish) greens to a greater percentage of the population. These facilities generally pack and ship their greens on the day of or day after harvesting, and only supply retailers within a certain radius. Little Leaf Farms, for example, currently servers only parts of Massachusetts, Pennsylvania, New York, and New Jersey.
The list of regions the company serves will no doubt lengthen as the company builds up its greenhouse network in the coming months.
Agritech: Precision Farming With AI, IoT and 5G
For a company that grows and delivers vegetables, Boomgrow Productions Sdn Bhd’s office is nothing like a farm, or even a vertical farm. Where farms are bedecked with wheelbarrows, spades and hoes, Boomgrow’s floor plan is akin to a co-working space with a communal island table, several cubicles, comfortable armchairs, a cosy hanging rattan chair and a glass-walled conference room in the middle
Image from: Photo by Mohd Izwan Mohd Nazam/The Edge
For a company that grows and delivers vegetables, Boomgrow Productions Sdn Bhd’s office is nothing like a farm, or even a vertical farm.
Where farms are bedecked with wheelbarrows, spades and hoes, Boomgrow’s floor plan is akin to a co-working space with a communal island table, several cubicles, comfortable armchairs, a cosy hanging rattan chair and a glass-walled conference room in the middle.
At a corner, propped up along a walkway leading to a rectangular chamber fitted with grow lights, are rows of support stilts with hydroponic planters developed in-house and an agricultural technologist perched on a chair, perusing data. “This is where some of the R&D work happens,” says Jay Dasen, co-founder of the agritech start-up.
But there is a larger farm where most of the work behind this high-tech initiative is executed. Located a stone’s throw from the city centre in Ampang is a 40ft repurposed shipping container outfitted with perception technologies and artificial intelligence (AI) capabilities that mimic the ideal environment to produce more than 50,000kg of vegetables a year.
Stacked in vertical layers, Boomgrow’s vegetables are grown under artificial lights with Internet of Things (IoT) sensors to detect everything from leaf discolouration to nitrate composition. This is coupled with AI and machine learning algorithms.
Boomgrow is the country’s first 5G-connected vertical farm. With the low latency and larger bandwidth technology, the start-up is able to monitor production in real time as well as maintain key parameters, such as temperature and humidity, to ensure optimal growth conditions.
When Jay and her co-founders, K Muralidesan and Shan Palani, embarked on this initiative six years ago, Boomgrow was nowhere near what it is today.
The three founders got together hoping to do their part in building a more sustainable future. “I’ve spent years advising small and large companies on sustainability, environmental and social governance disclosures. I even embarked on a doctorate in sustainability disclosure and governance,” says Jay.
“But I felt a deep sense of disconnect because while I saw companies evolving in terms of policies, processes and procedures towards sustainability, the people in those organisations were not transforming. Sustainability is almost like this white noise in the background. We know it’s important and we know it needs to be done, but we don’t really know how to integrate it into our lives.
“That disconnect really troubled me. When we started Boomgrow, it wasn’t a linear journey. Boomgrow is something that came out of meaningful conversations and many years of research.”
Shan, on the other hand, was an architect who developed a taste for sustainable designs when he was designing modular structures with minimal impact on their surroundings between regular projects. “It was great doing that kind of work. But I was getting very dissatisfied because the projects were customer-driven, which meant I would end up having debates about trivial stuff such as the colour of wall tiles,” he says.
As for Murali, the impetus to start Boomgrow came from having lived overseas — while working in capital markets and financial services — where quality and nutritious produce was easily available.
Ultimately, they concluded that the best way to work towards their shared sustainability goals was to address the imminent problem of food shortage.
“By 2050, the world’s population is expected to grow to 9.7 billion people, two-thirds of whom will be in Asia-Pacific. Feeding all those people will definitely be a huge challenge,” says Jay.
“The current agricultural practice is not built for resilience, but efficiency. So, when you think of farming, you think of vast tracts of land located far away from where you live or shop.
“The only way we could reimagine or rethink that was to make sure the food is located closer to consumers, with a hyperlocal strategy that is traceable and transparent, and also free of pesticides.”
Having little experience in growing anything, it took them a while to figure out the best mechanism to achieve their goal. “After we started working on prototypes, we realised that the tropics are not designed for certain types of farming,” says Jay.
“And then, there is the problem of harmful chemicals and pesticides everywhere, which has become a necessity for farmers to protect their crops because of the unpredictable climate. We went through many iterations … when we started, we used to farm in little boxes, but that didn’t quite work out.”
They explored different methodologies, from hydroponics to aquaponics, and even started growing outdoors. But they lost a lot of crops when a heat wave struck.
That was when they started exploring more effective ways to farm. “How can we protect the farm from terrible torrential rains, plant 365 days a year and keep prices affordable? It took us five years to answer these questions,” says Jay.
Even though farmers all over the world currently produce more than enough food to feed everyone, 820 million people — roughly 11% of the global population — did not have enough to eat in 2018, according to the World Health Organization. Concurrently, food safety and quality concerns are rising, with more consumers opting for organically produced food as well as safe foods, out of fear of harmful synthetic fertilisers, pesticides, herbicides and fungicides.
According to ResearchAndMarkets.com, consumer demand for global organic fruit and vegetables was valued at US$19.16 billion in 2019 and is anticipated to expand at a compound annual growth rate (CAGR) of 6.5% by 2026.
Meanwhile, the precision farming market was estimated to be US$7 billion in 2020 and is projected to reach US$12.8 billion by 2025, at a CAGR of 12.7% between 2020 and 2025, states MarketsandMarkets Research Pte Ltd.
Malaysia currently imports RM1 billion worth of leafy vegetables from countries such as Australia, China and Japan. Sourcing good and safe food from local suppliers not only benefits the country from a food security standpoint but also improves Malaysia’s competitive advantage, says Jay.
Unlike organic farming — which is still a soil-based method — tech-enabled precision farming has the advantage of catering for increasing demand and optimum crop production with the limited resources available. Moreover, changing weather patterns due to global warming encourage the adoption of advanced farming technologies to enhance farm productivity and crop yield.
Boomgrow’s model does not require the acres of land that traditional farms need, Jay emphasises. With indoor farms, the company promises a year-round harvest, undisturbed by climate and which uses 95% less water, land and fuel to operate.
Traditional farming is back-breaking labour. But with precision technology, farmers can spend less time on the farm and more on doing other things to develop their business, she says.
Boomgrow has secured more than RM300,000 in funding via technology and innovation grants from SME Corporation Malaysia, PlaTCOM Ventures and Malaysia Digital Economy Corporation, and is on track to build the country’s largest indoor farms.
Image from: Boomgrow
The company got its chance to showcase the strength of its smart technology when Telekom Malaysia Bhd (TM) approached it to be a part of the telco’s Smart Agriculture cluster in Langkawi last October.
“5G makes it faster for us to process the multiple data streams that we need because we collect data for machine learning, and then AI helps us to make decisions faster,” Jay explains.
“We manage the farm using machines to study inputs like water and electricity and even measure humidity. All the farm’s produce is lab-tested and we can keep our promise that there are no pesticides, herbicides or any preserving chemicals. We follow the food safety standards set by the EU, where nitrate accumulation in plant tissues is a big issue.”
With TM’s 5G technology and Boomgrow’s patent-pending technology, the latter is able to grow vegetables like the staple Asian greens and highland crops such as butterhead and romaine lettuce as well as kale and mint. While the company is able to grow more than 30 varieties of leafy greens, it has decided to stick to a selection of crops that is most in demand to reduce waste, says Jay.
As it stands, shipping containers are the best fit for the company’s current endeavour as containerised modular farms are the simplest means of bringing better food to local communities. However, it is also developing a blueprint to house farms in buildings, she says.
Since the showcase, Boomgrow has started to supply its crops to various hotels in Langkawi. It rolled out its e-commerce platform last year after the Movement Control Order was imposed.
“On our website, we promise to deliver the greens within six hours of harvest. But actually, you could get them way earlier. We harvest the morning after the orders come in and the vegetables are delivered on the same day,” says Jay.
Being mindful of Boomgrow’s carbon footprint, orders are organised and scheduled according to consumers’ localities, she points out. “We don’t want our delivery partners zipping everywhere, so we stagger the orders based on where consumers live.
“For example, all deliveries to Petaling Jaya happen on Thursdays, but the vegetables are harvested that morning. They are not harvested a week before, three days before or the night before. This is what it means to be hyperlocal. We want to deliver produce at its freshest and most nutritious state.”
Plans to expand regionally are also underway, once Boomgrow’s fundraising exercise is complete, says Jay. “Most probably, this will only happen when the Covid-19 pandemic ends.”
To gain the knowledge they have today, the team had to “unlearn” everything they knew and take up new skills to figure what would work best for their business, says Jay. “All this wouldn’t have been possible if we had not experimented with smart cameras to monitor the condition of our produce,” she laughs.
How This Vertical Farm Grows 80,000 Pounds of Produce per Week
To some, the pristine growing conditions and perceived mechanical interference of a vertical farm can seem unnatural, but at Bowery Farming “interference” is actually not the goal at all. “We don’t really think about how people are involved in the growing process, but how to take people out of the growing process”
Bowery Farming uses technology to prioritize accessibility and sustainability in their produce growing operations
To some, the pristine growing conditions and perceived mechanical interference of a vertical farm can seem unnatural, but at Bowery Farming “interference” is actually not the goal at all. “We don’t really think about how people are involved in the growing process, but how to take people out of the growing process” says chief science officer Henry Sztul. “Our goal is actually to have as few people walking around our plants as possible.”
Bowery Farming is a network of vertical farms working to reengineer the growing process. Using a system of light and watering technology, Bowery is able to use 95 percent less water than a traditional outdoor farm, zero pesticides and chemicals, and grow food that tastes as good as anyone else’s.
Bowery Farming uses vertical farm-specific seeds that are optimized for flavor instead of insect resistance and durability. Seeds are mechanically pressed into trays of soil, and sent out into growing positions, or racks within the building that have their own lighting and watering systems. Each tray gets its own QR code so that they can be monitored and assigned a customized plan for water and light until they’re ready to be harvested.
Irving Fain, Bowery Farming’s founder and CEO contemplates the prediction from the United Nations that 70 to 80 percent of the world’s population will be living in and around cities in the next 30 years. “Figuring out ‘how do you feed and how do you provide fresh food to urban environments both more efficiently as well as more sustainably?’ is a very important question today, and an even more important question in the years to come.”
Bringing The Future To life In Abu Dhabi
A cluster of shipping containers in a city centre is about the last place you’d expect to find salad growing. Yet for the past year, vertical farming startup Madar Farms has been using this site in Masdar City, Abu Dhabi, to grow leafy green vegetables using 95 per cent less water than traditional agriculture
Amid the deserts of Abu Dhabi, a new wave of entrepreneurs and innovators are sowing the seeds of a more sustainable future.
Image from: Wired
A cluster of shipping containers in a city centre is about the last place you’d expect to find salad growing. Yet for the past year, vertical farming startup Madar Farms has been using this site in Masdar City, Abu Dhabi, to grow leafy green vegetables using 95 per cent less water than traditional agriculture.
Madar Farms is one of a number of agtech startups benefitting from a package of incentives from the Abu Dhabi Investment Office (ADIO) aimed at spurring the development of innovative solutions for sustainable desert farming. The partnership is part of ADIO’s $545 million Innovation Programme dedicated to supporting companies in high-growth areas.
“Abu Dhabi is pressing ahead with our mission to ‘turn the desert green’,” explained H.E. Dr. Tariq Bin Hendi, Director General of ADIO, in November 2020. “We have created an environment where innovative ideas can flourish and the companies we partnered with earlier this year are already propelling the growth of Abu Dhabi’s 24,000 farms.”
The pandemic has made food supply a critical concern across the entire world, combined with the effects of population growth and climate change, which are stretching the capacity of less efficient traditional farming methods. Abu Dhabi’s pioneering efforts to drive agricultural innovation have been gathering pace and look set to produce cutting-edge solutions addressing food security challenges.
Beyond work supporting the application of novel agricultural technologies, Abu Dhabi is also investing in foundational research and development to tackle this growing problem.
In December, the emirate’s recently created Advanced Technology Research Council [ATRC], responsible for defining Abu Dhabi’s R&D strategy and establishing the emirate and the wider UAE as a desired home for advanced technology talent, announced a four-year competition with a $15 million prize for food security research. Launched through ATRC’s project management arm, ASPIRE, in partnership with the XPRIZE Foundation, the award will support the development of environmentally-friendly protein alternatives with the aim to "feed the next billion".
Image from: Madar Farms
Global Challenges, Local Solutions
Food security is far from the only global challenge on the emirate’s R&D menu. In November 2020, the ATRC announced the launch of the Technology Innovation Institute (TII), created to support applied research on the key priorities of quantum research, autonomous robotics, cryptography, advanced materials, digital security, directed energy and secure systems.
“The technologies under development at TII are not randomly selected,” explains the centre’s secretary general Faisal Al Bannai. “This research will complement fields that are of national importance. Quantum technologies and cryptography are crucial for protecting critical infrastructure, for example, while directed energy research has use-cases in healthcare. But beyond this, the technologies and research of TII will have global impact.”
Future research directions will be developed by the ATRC’s ASPIRE pillar, in collaboration with stakeholders from across a diverse range of industry sectors.
“ASPIRE defines the problem, sets milestones, and monitors the progress of the projects,” Al Bannai says. “It will also make impactful decisions related to the selection of research partners and the allocation of funding, to ensure that their R&D priorities align with Abu Dhabi and the UAE's broader development goals.”
Image from: Agritecture
Nurturing Next-Generation Talent
To address these challenges, ATRC’s first initiative is a talent development programme, NexTech, which has begun the recruitment of 125 local researchers, who will work across 31 projects in collaboration with 23 world-leading research centres.
Alongside universities and research institutes from across the US, the UK, Europe and South America, these partners include Abu Dhabi’s own Khalifa University, and Mohamed bin Zayed University of Artificial Intelligence, the world’s first graduate-level institute focused on artificial intelligence.
“Our aim is to up skill the researchers by allowing them to work across various disciplines in collaboration with world-renowned experts,” Al Bannai says.
Beyond academic collaborators, TII is also working with a number of industry partners, such as hyperloop technology company, Virgin Hyperloop. Such industry collaborations, Al Bannai points out, are essential to ensuring that TII research directly tackles relevant problems and has a smooth path to commercial impact in order to fuel job creation across the UAE.
“By engaging with top global talent, universities and research institutions and industry players, TII connects an intellectual community,” he says. “This reinforces Abu Dhabi and the UAE’s status as a global hub for innovation and contributes to the broader development of the knowledge-based economy.”
Warehouse Becoming Vertical Farms — And They’re Feeding New Jersey
New Jersey's vertical farms are transforming agriculture by helping farmers meet growing food demand. New Jersey Agriculture Secretary Doug Fisher said that while conventional farming in outdoor fields remains critical, vertical farming has its advantages because of its efficiency and resistance to pests and thus less need for chemicals
Image from: New Jersey 101.5
New Jersey's vertical farms are transforming agriculture by helping farmers meet growing food demand.
New Jersey Agriculture Secretary Doug Fisher said that while conventional farming in outdoor fields remains critical, vertical farming has its advantages because of its efficiency and resistance to pests and thus less need for chemicals.
Vertical farming is the process of growing food vertically in stacked layers indoors under artificial light and temperature, mainly in buildings. These plants receive the same nutrients and all the elements needed to grow plants for food.
Vertical farms are also versatile. Plants may be growing in containers, in old warehouses, in shipping containers, in abandoned buildings.
"That's one of the great advantages — that we can put agriculture in the midst of many landscapes that have lost their vitality," said Fisher.
ResearchandMarkets.com says the U.S. vertical farming market is projected to reach values of around $3 billion by the year 2024.
The one drawback is that its operational and labor costs make it expensive to get up and running.
Image from: AeroFarms
In the past decade, however, vertical farming has become more popular, creating significant crop yields all over the state.
AeroFarms in Newark is the world's largest indoor vertical farm. The farm converted a 75-year-old 70,000-square-foot steel mill into a vertical farming operation. AeroFarms' key products include Dream Greens, its retail brand of baby and micro-greens, available year-round in several ShopRite supermarkets.
Kula Urban Farm in Asbury Park opened in 2014. Vacant lots are transformed into urban farms and there's a hydroponic greenhouse on site. That produce is sold to local restaurants.
Beyond Organic Growers in Freehold uses no pesticides and all seeds and nutrients are organic. There's a minimum of 12,000 plants growing on 144 vertical towers. On its website, it says the greenhouse utilizes a new growing technique called aeroponics, which involves vertical towers where the plant roots hang in the air while a nutrient solution is delivered with a fine mist. It also boasts that by using this method, plants can grow with less land and water while yielding up to 30% more three times faster than traditional soil farming.
Vertical farms in New Jersey help feed local communities. Many are in urban areas and are a form of urban farming.
Fisher predicts that vertical farms will be operational in stores and supermarkets around the state.
"It's continued to expand. There's going to be many, many ways and almost any area in the state has the opportunity to have a vertical farm," Fisher said.
Is AppHarvest the Future of Farming?
In this video from Motley Fool Live, recorded on Jan. 28, Industry Focus host Nick Sciple and Motley Fool contributor Lou Whiteman discuss AppHarvest, one such SPAC that is looking to disrupt the agriculture industry. Here are the details on what AppHarvest wants to do, and a look at whether the company represents the future of farming.
Special purpose acquisition companies, or SPACs, are red-hot right now, with investors clamoring to get into promising young companies.
In this video from Motley Fool Live, recorded on Jan. 28, Industry Focus host Nick Sciple and Motley Fool contributor Lou Whiteman discuss AppHarvest, one such SPAC that is looking to disrupt the agriculture industry. Here are the details on what AppHarvest wants to do, and a look at whether the company represents the future of farming.
Nick Sciple: One last company I wanted to talk about, Lou, and this is one I think it's -- you pay attention to, but not one I'm super excited to run in and buy. It was a company called AppHarvest. It's coming public via a [SPAC] this year. This vertical farming space. We talked about Gladstone Land buying traditional farmland. AppHarvest is taking a very different approach, trying to lean into some of the ESG-type movements.
Lou Whiteman: Yeah. Let's look at this. It probably wouldn't surprise you that the U.S. is the biggest global farm exporter as we said, but it might surprise you that the Netherlands, the tiny little country, is No. 2. The way they do that is tech: Greenhouse farm structure. AppHarvest has taken that model and brought it to the U.S. They have, I believe, three farms in Appalachia. The pitches can produce 30x the yields using 90% less water. Right now, it's mostly tomatoes and it is early-stage. I don't own this stock either. I love this idea. There's some reasons that I'm not buying in right now that we can get into. But this is fascinating to me. We talked about making the world a better place. This is the company that we need to be successful to make the world a better place. The warning on it is that it is a SPAC. So it's not public yet. Right now, I believe N-O-V-S. That deal should close soon. [Editor's note: The deal has since closed.] I'm not the only one excited about it. I tend not to like to buy IPOs and new companies anyway. I think the caution around buying into the excitement applies here. There is a Martha Stewart video on their website talking up the company, which I love Martha Stewart, but that's a hype level that makes me want to just watch and see what they produce. This is just three little farms in Appalachia right now and a great idea. This was all over my watchlist. I would imagine I would love to hold it at some point, but just be careful because this is, as we saw SPACs last year in other areas, people are very excited about this.
Sciple: Yeah. I think, like we've said, for a lot of these companies, the prospects are great. I think when you look at the reduced water usage, better, environmentally friendly, all those sorts of things. I like that they are in Appalachia. As someone who is from the South, I like it when more rural areas get some people actually investing money there. But again, there's a lot of execution between now and really getting to a place where this is the future of farming and they're going to reach scale and all those sorts of things. But this is a company I'm definitely going to have my radar on and pay attention to as they continue to report earnings. Because you can tell yourself a story about how this type of vertical farming, indoor farming disrupts this traditional model, can be more efficient, cleaner, etc. Something to continue paying attention to as we have more information, because this company, like you said, Lou, isn't all the way public yet. We still got to have this SPAC deal finalized and then we get all our fun SEC filings and quarterly calls and all those sorts of things. Once we have that, I will be very much looking forward to seeing what the company has to say.
Whiteman: Right. Just to finish up along too, the interesting thing here is that it is a proven concept because it has worked elsewhere. The downside of that is that it needed to work there. Netherlands just doesn't have -- and this is an expensive proposition to get started, to get going. There's potential there, but in a country blessed with almost seemingly unlimited farmland for now, for long term it makes sense. But in the short term, it could be a hard thing to really get up and running. I think you're right, just one to watch.
Advice For New Vertical Farmers: Grower Spotlight on Andrew Worrall
Andrew is LettUs Grow’s Farm Manager, he manages two of our sites across Bristol and has brought a wealth of knowledge into the company through his previous experience in indoor farming roles across the UK including at Grow Up, Raynor Foods & RootLabs. In this three part interview, we explore what it’s been like to move from animal husbandry to indoor farming, the lessons he’s learned along the way, what it’s like working at LettUs Grow and his advice for those new to indoor growing.
Last week we spoke about running a farm at LettUs Grow. What excites you about vertical farming?
It’s the future of the industry. Also, the amount of salad that these farms can produce for their local community. We want to be able to eat salad all year round and we import to make that happen. However, just a small farm can easily provide for its local community, very efficiently and all year round. The sustainability element is also exciting: with our salad there’s no food miles, it’s very minimalistic. You could use an electric van or bike to distribute this crop if you wanted to. It’s a step forward in terms of what we need to do to take care of our planet.
What do you think are the biggest downsides to vertical farming?
It’s still a new technology and it can be expensive. The biggest roadblock facing the industry is that we need more people and companies to collaborate together to make sure we can build these farms at a sensible rate, so we can provide farms to anyone. We want to be able to provide farms to people, communities and countries that don’t have a lot of money, so that they can provide affordable fresh produce to local people.
How has vertical farming impacted your life?
Massively! I wanted to find my passion, a job that I loved - that was very important to me. It’s satisfying to be in a position now where I’m very happy to be doing what I do and I look forward to going into work. I was happy to make the move from London to Bristol. I would have moved even further if it meant being able to continue working within this industry.
Image from: LettUs Grow
How do you see vertical farming playing a part in the future?
When indoor farming first came about, it had a reputation of being competition for outdoor farming, which just isn’t the case. There’s so much we can’t grow that outdoor farming can provide, such as cereal crops. I’m glad we’re at a stage where indoor and outdoor farms can start to work together to optimise both methods. With these new relationships, there should be a good increase in the amount of indoor farms you’ll be seeing. What LettUs Grow offers with DROP & GROW™ is an exciting project because that’s a 40ft shipping container which can be placed pretty much anywhere. It’s not that big - it could go in a car park or behind a restaurant, but actually provide quite a lot of salad to that area.
How much of our food should be grown this way?
Good question. If you had asked me a while back I would have just said salad, but now I’ve changed my mind. Indoor farming can have a massive impact on propagation, especially aeroponics, because of how we aerate and nourish our roots. We could start lettuce for greenhouse projects and we can also propagate tomatoes, strawberries and tree whips. Propagating trees in this way could potentially be hugely beneficial and it’s something we want to do more of.
We can also quickly grow large amounts of microgreens, baby leafs, herbs and we can grow fruiting crops like strawberries. We are slowly chipping away and it’s really exciting. I’m waiting to see if I can ever say I’ve grown or propagated every crop that can be grown in these farms!
What do you think are the biggest benefits of vertical farming?
How fast these crops can grow! The turnover can be as short as 5 days from seed, depending on the crop. Also how clean it can be - I’m very dedicated to making sure these farms are built to ensure they are easy to be maintained and clean. The most exciting part is the crop growth rate though - it’s incredible how fast our crop grows from seed to plate. In a very well maintained growing calendar, which Ostara® is great for supporting, you can optimise your beds so that the day you harvest can also be the day you germinate onto that same bed. Your farms can be forever providing salad at very fast rates.
Image from: LettUs Grow
What was the biggest change you encountered during your years indoor farming?
Moving from being a production grower to an R&D grower. It has been a great change! As a production grower I knew what I needed to know about growing the plant safely and getting it onto a plate so it was good for the consumer. Now I’m fully optimising, learning and understanding the plants completely, so that I can help the grower that I used to be. We spend a lot of time on crop recipes to make sure that whoever we sell our farms to can start up very quickly and they won’t have to spend months developing their crops. If they have the customers and clients behind them, they can buy DROP & GROW and start producing salad as soon as it's been commissioned.
What was the biggest change you encountered in the industry?
More and more people are speaking about what’s going on in the industry and getting involved. I get so many messages on LinkedIn with people who want to get into this career. It’s exciting to see that indoor growing is a career people can access now. When I was developing my skills I didn’t know I would end up in indoor farming. There are more opportunities than ever before. For example, our Crop Technician is doing a placement here for 2 years. The aim is that they can gain the skill sets and knowledge they need to then go off and do the same practice in any farm they want.
What advice do you have for people who are looking to start a career in growing?
Reach out to companies who are already out there. You could start off part-time or as an assistant. If you are patient and dedicated then it’s a journey I promise you won’t regret. It takes a lot of work, but the outcome is amazing - you’ll be learning so much about this new technology. You’ll also build great relationships: there are so many amazing people in this industry who are so interesting, with different backgrounds, who are willing to share their knowledge. You can always learn more and other people are a great source of that.
What about for those looking to start a vertical farming business?
Do your homework. There are people out there who you can reach out to and it’s very easy to get information. It’s very easy to get excited about the idea and jump straight into it, because it is exciting and can be very rewarding, but it’s really important to do it step by step. Know how to scale properly, learning the differences between a small and larger farm. Understand how many people you’ll need and the logistics. I’d also advise people to get some practical work experience before you buy. You want to start the company knowing the tricks of the trade.
Image from: LettUs Grow
LettUs Grow Blog: www.lettusgrow.com/blog/advice-for-vertical-farmers
SINGAPORE: High-Five: Developing “The World’s First Vertical Aquaculture Farm”
Singapore-based entrepreneur John Diener is committed to developing a series of urban aquaculture facilities that are able to produce shrimp, whitefish and seaweeds in high tech five-story farming systems
by Rob Fletcher
24 November 2020
Singapore-based entrepreneur John Diener is committed to developing a series of urban aquaculture facilities that are able to produce shrimp, whitefish, and seaweeds in high tech five-story farming systems.
John Diener aims to produce shrimp, tilapia, and seaweeds in five-tier facilities that can be fitted into the footprint of a standard warehouse. © Akualogix
The last decade of Diener’s career has seen him involved in a number of aquaculture-related ventures, as well as agritech startups, and the concept of a completely novel farming system came to him in 2016 when he was researching how machine learning could benefit aquaculture during a part-time MSc in aquaculture at St Andrews University.
“I have a lot of experience in data science and I wanted to find out what would happen if you reassessed the whole concept of aquaculture,” he explains.
Diener’s research led him to believe that vertical farms using cutting-edge technologies had the capacity to produce – for their footprint – an impressive amount of seafood, making them suitable for urban settings.
Three pillars
Diener describes the development of the system as resting on three pillars – biological, mechanical and digital. The biological side relates to investigating the most productive integrated-multitrophic (IMTA) system, with vannamei shrimp as the primary species.
“The business plan has been developed around shrimp – they’re a unique product in terms of their flavour profile, much like salmon are, which makes it very hard to produce substitutes. And they can also be raised at high densities,” Diener notes.
“We’ve also incorporated a filter-feeding fish – we’re currently using tilapia because they’re very robust, but will probably trial milkfish too,” he adds.
The bottom of the IMTA pyramid is taken up by sea grapes – called umibudo in Japan, where they are considered something of a delicacy.
“These are known as ‘the green caviar’ in parts of Asia, so have the potential to be sold as food. They can also be used as an ingredient in shrimp feeds, as we’re aiming to produce our own, sustainable feeds, while they also help to remove nitrates and phosphates from the water,” says Diener.
Technology
The second pillar consists of the engineering, and Diener intends to develop raceway systems four or five levels high, which are equipped with modular autonomous devices to optimise factors such as measuring water quality. The third pillar relates to the digital side of operations.
“We’re investing time and effort to develop advanced technology to manage feeding – both in terms of studying shrimp behaviour so we know when to feed and in terms of measuring the biomass in the systems, so we know how much to feed. We will also be looking to manage the water quality by feeding information into a deep learning algorithm that can control factors like pump speeds and the addition of minerals to the water,” he says.
The digital side also covers the farm’s “Aqua OS” [operational systems], ensuring all the technology works together, to simplify the management of all the tanks, Diener explains.
Launch
John Diener, founder of Akualogix
Four years after coming up with the concept Diener launched his own company, called Akualogix, in August, after finding a suitable site for a pilot-scale facility, in a building owned by the Marine Aquaculture Centre, on St John’s island in Singapore. This will, he notes, be perfect for securing proof-of-concept, before he looks to expand into a commercial-scale facility.
Initially self-funded, by Diener and the company’s co-founder, they are now looking into securing pre-series A funding in order to build a larger scale production unit.
Funding opportunities have remained robust in the agri-food sector, despite the outbreak of Covid. And as our systems are designed for an urban environment, and food security is increasingly important in Singapore and other cities around the world, we see strong investor interest
“Funding opportunities have remained robust in the agri-food sector, despite the outbreak of Covid. And as our systems are designed for an urban environment, and food security is increasingly important in Singapore and other cities around the world, we see strong investor interest,” Diener reflects.
The current farm has – he predicts – the capacity to produce 500-600 kg of shrimp per cycle, but he’s not yet sure what the yields of the tilapia or sea grapes will be – pointing out that no one has undertaken a mass balance study in such a system.
A juvenile shrimp at the pilot facility in Singapore. © Akualogix
“Our business economics is based on shrimp – making any money from the tilapia would be the icing on the cake – but the main reason we have the fish is part of the multi-trophic system and benefit the overall environment, they’re part of the filtration system,” he explains.
We will be looking at establishing commercial farms that can produce in the region of 1,000 to 1,500 tonnes of shrimp a year. It might not sound like much compared to some of the commercial salmon RAS that are now being established, but if we’re operating 20 or 30 farms that would make us one of the biggest shrimp producers in the world
Next steps
Once the pilot facility has fulfilled its potential Diener aims to establish a farm – and ultimately a network of farms – that use Akualogix’s design and equipment, establishing partnerships in a range of countries, primarily in Asia, as the concept takes off.
“We will be looking at establishing commercial farms that can produce in the region of 1,000 to 1,500 tonnes of shrimp a year. It might not sound like much compared to some of the commercial salmon RAS that are now being established, but if we’re operating 20 or 30 farms that would make us one of the biggest shrimp producers in the world,” he points out.
Diener is also looking to develop a unique, sustainable feed that’s designed specifically for producing shrimp in RAS facilities.
“The current range of commercial shrimp feeds are not great for use in RAS, and we’re looking to produce a next generation shrimp feed using sustainable ingredients. And we’re looking for a flavour enhancing additive as a finishing diet – potentially one that comes from algae,” he says.
Given the technology involved and the emphasis on sustainable feed ingredients Diener is aware that production costs are going to be considerably higher than conventional shrimp farms.
“We estimate that our cost of production will be 40-50 percent higher than shrimp produced in a pond in, say, India. But we’re close to market and can charge a premium for a fresh product that’s so sustainably produced,” he says.
Operational experience
The pilot facility holds 30,000 shrimp per cohort and 1,000 tilapia. The former are housed in a two-stage grow-out system and he aims to take them from the end of the nursery stage to harvest in 60 days, while achieving survival rates of roughly 90 percent.
However, as Diener admits, the design concepts of the system are still evolving, and there are other issues that have caused setbacks.
“It turned out that our first batch of PL [post-larvae] had pathogenic vibrio and we started seeing mortalities related to vibriosis,” he explains.
It was an unfortunate start, but a useful reminder of the importance of biosecurity.
“We decided to implement a full biosecurity package [once operating commercially], which will include our own hatcheries to prevent the introduction of pathogens,” he says.
Should the pilot facility prove productive, and investment forthcoming, Diener then aims to roll out the concept across some of Asia’s most populous coastal cities.
“There’s currently a lot of investment in salmon RAS and I think shrimp are the next species to go in that direction. If we can be a pioneer of shrimp RAS it will be a game-changer,” he concludes.
Miele Commitment To Vertical Agriculture At Home
Miele continues with its commitment to acquire or participate in new projects to diversify its business and redefine the experience in the field of cooking, with the purchase of Agrilution assets
02/14/2020
Miele continues with its commitment to acquire or participate in new projects to diversify its business and redefine the experience in the field of cooking, with the purchase of Agrilution assets . This young company of German origin has opted to offer vertical agriculture solutions, which many experts have defined as the future of greenhouses, in the home itself.
This type of agriculture, which is based on aeroponics (a technology that does not require land, sun, or water) makes plants grow based on the humidity and heat of artificial light. Its domestic use means having a kind of standard refrigerator, which offers the perfect growing conditions, with minimal care and an extra design contribution both in the kitchen and in the living room.
In the words of Maximilian Lössl, founder of Agrilution together with Philipp Wagner, "our domestic greenhouse provides fresher lettuce, herbs, and micro vegetables directly on the table."
Agrilution's home greenhouses allow fresh, aromatic and nutrient-rich sprouts, herbs and micro vegetables to be enjoyed at home throughout the year, through a self-contained ecosystem with simple seed coatings, regulated lighting, and a controlled microclimate, as well as automatic irrigation.
The first crop can be harvested one to three weeks after commissioning.
To establish a comparison that clearly illustrates its effectiveness, a lettuce grown in the field requires up to 120 liters of water to grow and that volume is sufficient to supply an entire Plantcube throughout the year.
United Fresh 2020 Launches Controlled Environment Pavilion
According to a press release, the CEA Food Safety Coalition is a new independent and member-governed coalition whose mission is to develop credible, strong, and appropriate food safety standards; educate consumers and regulators on controlled environment growing; and communicate the value of controlled environment agriculture
Dec. 23rd, 2019
WASHINGTON, DC - Right about now, everybody is experiencing the full swing of the holiday season, but that’s not slowing United Fresh down. The organization announced that it has teamed up with the Controlled Environment Agriculture Food Safety Coalition (CEA Food Safety Coalition) to launch a new Controlled Environment Pavilion at the United Fresh Convention & Expo. This new Pavilion was made to support the growing category of indoor growers and the commitment to drive innovation in fresh produce.
Tom Stenzel, President and CEO, United Fresh Produce Association
“From first-generation indoor farms growing tomatoes and cukes to today’s innovators growing berries, leafy greens, microgreens, herbs, and more, the Controlled Environment Pavilion is the place to meet with potential customers and service providers, and learn from experts in every phase of the business,” said United Fresh President and CEO Tom Stenzel.
According to a press release, the CEA Food Safety Coalition is a new independent and member-governed coalition whose mission is to develop credible, strong, and appropriate food safety standards; educate consumers and regulators on controlled environment growing, and communicate the value of controlled environment agriculture.
This year’s United Fresh Convention & Expo will feature a Controlled Environment Pavilion, sponsored by the Controlled Environmental Agricultural Food Safety Coalition (CEA Food Safety Coalition)
Marni Karlin, Executive Director of the CEA Food Safety Coalition
“We’re pleased to collaborate with United Fresh in hosting this new pavilion,” said Marni Karlin, Executive Director of the CEA Food Safety Coalition. “Our members are pioneering new production models in fresh produce, and we look forward to the opportunity to engage with participants at the United Fresh event—to share perspectives and create an opportunity for conversation across the entire supply chain.”
Members of the CEA Food Safety Coalition include BrightFarms, AeroFarms, Plenty, Little Leaf Farms, Revol Greens, and Bowery. The Pavilion will feature a discussion area where thought leaders will share perspectives on current issues and growth opportunities for indoor ag, hydroponics, vertical farms, and rapidly expanding greenhouse production. Retail and foodservice buyers can visit the pavilion to learn more about the category and meet with potential suppliers.
For more innovative opportunities happening in the produce world, keep reading ANUK.
Trade Association United Fresh Produce Association Controlled Environment Agriculture Food Safety Coalition Innovation Launch Partnership Expo Feature New Feature Discussion Trade Show Event New Partner Marni Karlin Tom Stenzel
The Farms of The Future Were Built For Outer Space. Will They Work On Earth?
It will be years until NASA is ready for a journey to the red planet, but if Earth continues to suffer from climate change, Mars could come to us.
It will be years until NASA is ready for a journey to the red planet, but if Earth continues to suffer from climate change, Mars could come to us.
August 13, 2019
Visitors look at vegetables growing under artificial light on a vertical farm, in the IKEA: Gardening Will Save the World garden, in London on May 20th, 2019. (Photo: Daniel Leal-Olivas/AFP/Getty Images)
On Mars, we'll all farm underground. Our crops will grow in a greenhouse, where large, parabolic mirrors focus the sun's weak rays and transmit them through fiber optic cables. We'll harvest vegetables to eat—but also the purified water that evaporates from their leaves. We'll all be vegan, because raising animals for food will be too expensive. And, most importantly, the plants will give us oxygen.
"That's the starting point to a whole civilization right there," says Utah State University researcher Bruce Bugbee. This is Bugbee's vision, one he's been dreaming of and testing and revising for years as a plant engineer with NASA.
Astronauts going to Mars can eat all the freeze-dried food they're able to ship, but if humans are going to survive on the planet they'll need to plants to produce oxygen. Not just any photosynthesizer will do: Mars is a difficult environment, with many challenges for farmers. Crops will need to be able to thrive in a small area, retain their nutrient content, and still taste good. Structures where they grow on the surface will need to withstand basketball-sized meteorites. The technology used to grow the plants will take massive amounts of energy. Mars also presents the ultimate recycling challenge, since astronauts can't pack all the water and nutrients they need on a two-and-a-half-year space flight.
Bugbee and his colleagues have been working on all these problems for decades, in a sometimes fantastical bid to support life on Mars (and, in the meantime, on space shuttles). Decades ago, NASA researchers ruled out some of the easiest plants to grow indoors, like algae: not enough sustenance, Bugbee says. Very tall crops like corn and sugarcane were also nixed because they wouldn't fit easily into the plant habitats.
What the astronauts really wanted was something green. "They say that having the texture and flavor and color and aromas of fresh foods apparently—and I believe it—really does add to the experience of eating," says NASA plant physiologist Raymond Wheeler.
Scientists started looking at traditional field crops like lettuce, tomatoes, and broccoli. Right now, astronauts are growing mixed greens 250 miles above Earth on the International Space Station, using two small, sealed greenhouse units called Veggie. NASA researchers have planned and adjusted and measured for everything—including which types of lettuce tastes best in space. Astronauts' clogged sinuses already make it so they "can't taste much of anything," according to Canadian astronaut Chris Hadfield, but the researchers are also curious to see whether the space environment affects a plant's flavor compounds and nutrient levels. Panels of specialists at NASA's Johnson Space Center in Houston typically conduct formal taste tests, but sometimes the researchers sample a leaf or two themselves.
What Bugbee and his team didn't expect is that the technology they created for this grandiose, futuristic mission would become somewhat eclipsed by those using it to farm on more familiar terrain.
In 2017, NASA commissioned a space farming project to figure out how to grow food on Mars, but they were also hoping to make some discoveries that could improve crop yields overall. The problems that space farmers of the future will face are similar to those already plaguing earthbound agriculture as climate change grows worse, including a dwindling water supply and poor soil. Now, researchers in Utah and three California universities—NASA's partners with the Center for the Utilization of Biological Engineering in Space—are working on projects that can sustain life not just on Mars, but on Earth.
"I think the reason NASA funds us is a powerful human fascination with being able to go inside a closed system and grow your own food," Bugbee says. "What if the atmosphere went bad and we had to build a big dome ... and go inside and live in it?"
In 1988, Wheeler built the first working vertical farm—growing plants on shelves, typically in a warehouse or storage container—at the agency's Kennedy Space Center. Wheeler's farm was 25 feet high and equipped with a hydroponic system for growing plants in water and high-pressure sodium lamps, the type commonly used for street lighting. All together, it was 20 square meters of growing space—almost 90,000 times less than the size of the average outdoor United States farm. According to Wheeler's calculations, it would take 50 square meters of plants to provide enough food and oxygen—and remove enough carbon dioxide—for one human in space. (Astronauts won't be using sodium lamps, though: A few years after Wheeler's innovation, a different group of NASA-funded researchers patented another significant piece of technology to indoor farmers: LEDs, which require much less electricity than sodium lights and are now used to power most greenhouses.)
Wheeler was focused on optimizing the area inside a chamber aboard a NASA space shuttle—and up seemed like the best way to go. "One of the things you have to think about in space is volume efficiency," he says. "You're vertically and dimensionally constrained." The team had to pick shorter crops: wheat, soybeans, potatoes, lettuce, and tomatoes.
In space, resources are limited: NASA scientists have to extract and reuse the nutrients from excess plant material and human waste; they collect water from the condensation that collects in the closed chambers. Here on Earth, water is also growing increasingly precious—climate change will make droughts more frequent and severe, devastating crop yields and making some staple crops like corn and soybeans obsolete. Every day, Earth looks a little more desolate, a little more like Mars.
When Wheeler started, the term "vertical farming" didn't exist yet. Today it's a $10 billion industry attracting interest from Silicon Valley and start-ups all over the world. Its acolytes believe the technology will one day completely replace conventional field agriculture, allowing businesses to grow crops year-round and indoors, insulated from the next drought or flood and the effects of climate change. "People imagine that we'll grow everything indoors, in skyscrapers in the middle of Manhattan," Bugbee says. "It's a wildly popular idea."
Sonio Lo, the chief executive officer of the biggest vertical farming company in the world, Crop One Holdings, says she believes vertical farming can "liberate agriculture from climate change and geography."
Crop One broke ground on the world's largest vertical farm last November in Dubai: a five-story, 130,000-square-feet warehouse, capable of producing three tons of leafy greens a day. The company is also growing chard, arugula, and other greens in large, sealed rooms—year-round. "I made my whole management team stand in the supermarket and give out samples of what we were growing in the middle of the Boston winter," Lo says.
Soon people across the U.S. can try it too. Crop One is building new farms in the northeast, southwest, and California, where it will grow food to sell through its FreshBox Farms brand.
While researchers have been quick to condemn vertical farming's promises as over-hyped, even the industry's greatest critics acknowledge that this approach eliminates some of the challenges with conventional agriculture: Since vertical farms are located in compact warehouses, they're often located much closer to their markets than, say, the corn belt is to a city, allowing producers to cut down on food waste and save on transportation costs—a major contributor to U.S. greenhouse gas emissions.
The lettuce grows in a controlled environment, free of pests and pathogens, meaning farmers can grow food without pesticides or herbicides, which have a massive environmental and human-health cost. Vertical farmers can also recycle their nutrients—like astronauts do in space—preventing phosphorus or nitrogen from flooding into the world's waterways and wreaking havoc with algal blooms. And indoor growth systems can be very productive: When all the conditions are right, researchers have surpassed record crop yields in the field by as much as six times.
Lo says that a vertical farm using 100 percent renewables has one-tenth of the carbon impact of a conventional farm. But few companies have reached this goal; most are still moving toward a combination of renewable energy and non-renewables to power the electric lights used to grow the plants. It takes a lot of land to generate that much solar—about five acres of solar panels to supply the light for just one acre of indoor farm, Bugbee estimates. That's why many have resorted to fossil fuels, breaking one of vertical farming's great promises. "It takes massive amounts of fossil fuel energy, so, environmentally, it's really a disaster," Bugbee says. "Those people have used many of the principles that we've developed through NASA."
Bugbee's current project could help with that. His lab at Utah State is using LEDs and fiber optics to grow plants under different types of lights, with different ratios of colors—ultra violet, blue, green, red, far red (out of the limit of human vision)—to manipulate both photosynthesis and plant shape. The goal, he says, is to find "the most efficient system possible." Right now, the technology is too expensive: millions of dollars to light one building. But eventually, he believes fiber optics will replace electric lights for good.
But there are other qualms with vertical farming: Instead of helping to colonize space—the future that Mars researchers envision for their technology—vertical farms might take over city real estate, at a time when housing costs are extremely high. In some countries and some industries, it already has: Japan has had flourishing plant factories for the last 10 years. The fledgling cannabis industry has also started to ramp up its indoor production, poised to become even more profitable.
Lo says it won't be long until greens grown indoors cost the same as those in the field. "Field-grown food will continue to rise in cost, and course the climate is also changing," she says. "From a cost perspective, vertical farming will become competitive very quickly."
Others are more skeptical: "Economically, will they succeed? That question is still ongoing, because they always have to compete with field agriculture," Wheeler says. "What's their cost to pay for electric power? What are their labor costs? Are these operations sustainable? All of this is sort of a living experiment right now."
Technology for farming in climate change may be a by-product of NASA's research, but it has helped the agency ensure funding for its work in space. In response to the skeptic who doubts whether it's worth figuring out how to farm for a Mars mission we might never see, one only has to point to vertical farms in Boston or Seattle that already use some of NASA's innovations.
But Bugbee believes these earthly pursuits can be just as futuristic (or deluded) as those meant for space. "People that do it say they're going to save the planet ... but they have to have a lot of fossil fuels," he says. "It'll tell you all kinds of rosy pictures about it—that it saves water, it saves fertilizer."
He's not quite comfortable with his research being used to prop up this industry, now flooded with billions of dollars of venture capital. "I'm not doing it to make this more possible on Earth," he says. "We get asked all the time about the spinoffs: Could you do this, could you do that."
We may never make it to Mars. It will be years until NASA is ready for a journey to the red planet, and many more until Bugbee would be able to build his greenhouse underground, tucked away from meteorites. But if Earth continues on this collision course, Mars could come to us.
TAGS CLIMATE CHANGE VERTICAL FARMING NASA OUTER SPACE PLANTS AGRICULTURE
BY EMILY MOON
Emily Moon is a staff writer at Pacific Standard. Previously she worked at the Chicago Sun-Times and the Herald-Times in Bloomington, Indiana. She is a graduate of Northwestern University.
Climate Heat Mapping For Indoor Growing Environments
A lot goes into designing a good indoor agriculture environment, from selecting the right lights, to ensuring proper irrigation, optimizing airflow, and more. But while the big four – light, water, nutrients, and air – are the major keys to plant growth, the size and quality of a crop is highly dependent on a number of other factors as well. Environmental factors like humidity and temperature have a major impact on plant growth and, as a result, precision climate control has become an increasingly important part of successful indoor growing.
by Ted Tanner, Growlink CEO and Co-Founder
The importance of the perfect climate
As with all living things, plants thrive in some climates and struggle – or die – in others. The impacts of that are obvious out in nature where frigid winter temperatures or scorching desert heat render the landscape all but barren, but even in the relative comforts of an indoor grow space, small swings in temperature and humidity can have big impacts on growth, affecting both quality and yield.
Ideal growth climate
Different types of plants have different preferred climates in which to grow. Those preferred ranges aren’t necessarily static either, and while some plants will grow happily in one climate throughout their entire life cycle, others grow best in one climate during the vegetative stage and another during the flowering stage. Lettuce, for instance, grows best at around 60°F – much too cold for cannabis plants, which prefer temperatures of around 70-80°F in the vegetative stage with a bit of a cool-down when they flower.
Nighttime cooling
In nature, plants get a chance to cool off when the sun goes down, and in an indoor environment, the lights-off period provides the same opportunity. The problem is that just as with day-time temperatures, plants have ideal “lights out” temperatures. The risk of cooling down too much is very real, especially in places where the outdoor nighttime temperature drop is significant. In addition to the growth problems that overly cold temperatures present, colder air also increases the risk of condensation forming on the plants – a haven for damaging molds and fungi. That makes it extremely important for growers to carefully control the temperature drop that comes along with shutting off the lights.
Canopy overheating
Most of the lights used in indoor growing give off a huge amount of heat. As a result, the risk of overheating a crop’s canopy exists even in rooms that are otherwise set to the correct ambient temperature. An overheated canopy leads to all kinds of problems, including sucking moisture out of the plants and reducing their ability to perform photosynthesis – both of which could kill a crop outright in extreme instances. Canopy overheating can be fixed by simply increasing the distance between lights and plants, or by employing LED lighting which gives off very little heat.
Heat mapping – A game-changing climate control tool
As with all indoor climate control, the first step to getting things properly dialed-in is monitoring. Traditional thermostats, while fine for setting a comfortable temperature in a home or office, have major limitations that make them generally unsuitable for serious indoor growing.
The primary drawback is that most thermostat systems only measure part of the room. Dialing in a perfect climate for a grow operation is pointless if that climate isn’t even across the entire environment. Likewise, a simple thermostat only takes into account ambient temperatures – it can’t pinpoint specific trouble areas, like a partially overheated canopy, for instance.
The solution is heat mapping. Heat mapping employs an array of thermal imaging sensors placed across an environment to accurately measure the temperature of not just the ambient air, but of all the surfaces including the canopy. The result is a clear picture of all the hot and cold areas of a room and the gradients in between them – either in the form of a color visual image or as a set of raw data points.
From a growing perspective, the benefit of heat mapping is an unparalleled level of insight into the temperature and other climate variables not just in the room as a whole, but on a plant-by-plant basis (depending on the number of sensors employed). For instance, if bad air flow in a growing environment is causing overheating in one portion of the canopy, a thermostat won’t provide that information, but a heat-map will. That kind of intelligence is invaluable when it comes to maximizing crop health.
The advanced data provided by Growlink's real-time and historical playback heat-map tool can be used to make manual adjustments or, in the case of larger operations, to control an automated climate control system that can automatically adjust room heating, lighting intensity, and humidity as necessary to keep the growing environment at an optimal setting 24-hours a day.
One of the primary goals of growing indoors is maximizing control over the many factors that go into producing the best crop possible. Of those factors, the climate is both one of the most important and the most controllable. However, it’s impossible to tightly control something that can’t be accurately measured, and measurement has long been the weak point in climate control. Thanks to high density sensors and visual heat mapping, indoor growers can now access a real-time picture of the exact profile of their growing environment, allowing them to fine-tune their systems to a level never before possible. The result is perfectly tuned growing environments that boost productivity by increasing yields, reducing losses and cutting down input costs.
For more information:
Growlink
875 Kalamath
Denver, CO 80204
+800-432-0160
info@growlink.com
growlink.com
Gordon Food Service and Square Roots to Bring Local Food to Cities Across North America
The strategic partnership will see new campuses of Square Roots’ indoor farms built on or near Gordon Food Service distribution centers and retail stores across the continent, enabling year-round growing of premium quality herbs, greens, and more, which will then be available to Gordon Food Service customers.
March 6, 2019
BROOKLYN, NY
Gordon Food Service has linked up with Square Roots, a leader in urban indoor farming, to provide customers across North America with locally-grown food. The strategic partnership will see new campuses of Square Roots’ indoor farms built on or near Gordon Food Service distribution centers and retail stores across the continent, enabling year-round growing of premium quality herbs, greens, and more, which will then be available to Gordon Food Service customers.
Rich Wolowski, CEO, Gordon Food Service
“Customers want an assortment of fresh, locally-grown food all year round,” stated Rich Wolowski, CEO of Gordon Food Service, in a recent press release. “We are on a path to do that at scale with Square Roots and are excited to be the first in the industry to offer this unique solution to our customers.”
Gordon Food Service has linked up with Square Roots, a leader in urban indoor farming, to provide customers across North America with locally-grown food
The press release noted that this partnership enables Gordon Food Service to bring a modern offering to meet growing customer demand for local food across North America. It also signifies the first significant expansionto new locations for Square Roots.
Tobias Peggs, Co-Founder and CEO, Square Roots“
This partnership means we will grow delicious, local real food at huge scale,” said Tobias Peggs, Co-Founder and CEO of Square Roots. “We’re so happy to be working with a mission-aligned partner in Gordon Food Service—leveraging technology to bring real food to a huge number of people across the country, while delivering real social impact by empowering thousands of young people to become our country’s future farmers.”
Customers can scan a QR code on packaging to trace how their food was grown and who grew it
Square Roots utilizes a high-tech farming platform with its Next-Gen Farmer Training Program to train young people to become future leaders in the food industry. In addition to this tech, the company's Transparency Timeline enables customers to trace exactly how their food was grown and who grew it, simply by scanning a QR code on its packaging. Two winning tech solutions, if you ask me!
Stick with us here at AndNowUKnow for the latest in new partnerships.
Gordon Food Service Square Roots
Distribution Gordon Food Service New Partnership Square Roots Locally-Grown Rich Wolowski Tobias Peggs
COMPANIES IN THIS STORY
Gordon Food Service
Gordon Food Service is the largest privately-held, family-managed broadline foodservice distributor in North America-and...
Key Leadership Additions at Fluence Bioengineering to Accelerate Global Growth
Austin, Texas – March 5, 2019 – To further scale its solutions and services, Fluence Bioengineering announces key hires underscoring the company’s commitment to support the global horticulture industry. These appointments of industry veterans include professionals outside of the horticulture industry, enabling Fluence to expand its portfolio and commit the company to an aggressive growth trajectory.
“Innovations pioneered by Fluence are enabling growers to produce more and virtually eliminate seasonality. These appointments ensure our solutions and support teams are immediately accessible to a global audience,” said Dave Cohen, chief executive officer, Fluence Bioengineering.
Lorrie Schultz, senior vice president of marketing. In this role, Lorrie will lead global marketing efforts across Fluence to elevate the global brand, enhance customer engagement and extend demographic reach. Lorrie was formerly senior vice president of marketing at Q2 Software where she enabled the marketing department to scale and develop their brand. She is a tech veteran from Dell, where she held numerous global marketing roles in consumer, retail, small business, enterprise and customer experience.
“I am keen on collaborating with our growers to discuss the challenges they face today, as I believe communities are built around how they source and consume food and medicine,” said Lorrie Schultz. “Our mission is to enable growers to cultivate better plants and I am deeply interested in conveying this message to the global marketplace and I am excited to be a part of this team.”
Timo Bongartz, general manager, EMEA. Timo has led the development of global horticulture strategy at OSRAM, since 2015. He will be responsible for the expansion of Fluence in Europe, the Middle East and Africa. He will manage leadership as well as sales goals for each country.
Greg Hovagim, global director of controllers, dimmers, and IoT solutions. Greg brings experience encompassing work from across the commercial and defense sectors. Previously, he oversaw rapid prototype development projects as well as large-scale defense projects. At Fluence, he will manage the dimming & controls technologies for Fluence LED lighting solutions and development of innovative customer solutions.
###
About Fluence Bioengineering
Fluence Bioengineering Inc., a wholly-owned subsidiary of OSRAM, creates the most powerful and energy-efficient LED lighting solutions for commercial crop production and research applications. Fluence is the leading LED lighting supplier in the global cannabis market and is committed to solving the looming food crisis by enabling more efficient crop production with the world’s top vertical farms and greenhouse produce growers. All Fluence lighting solutions are designed and built at the company’s
Headquarters in Austin, Texas, U.S.A., with European sales and support based in Amsterdam, Netherlands. https://fluence.science