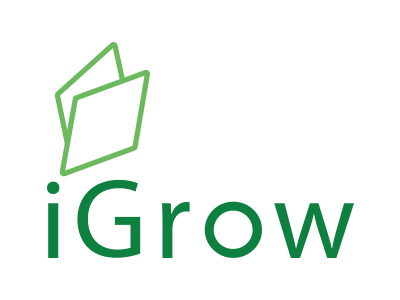
Welcome to iGrow News, Your Source for the World of Indoor Vertical Farming
Ushio Germany Presents Horturion HPS 1000W de el Supra Plus "The Highest Light Output Ever Achieved By A 1,000 W Lamp"
With the Horturion HPS 1000W de el Supra Plus lamp, Ushio Germany GmbH presents another innovation in the field of plant growth lamps. "The Horturion Supra Plus is a 1,000 W lamp with a light output of 2180 µmol/s and therefore the most efficient 1,000 W lamp ever introduced in the market", the Ushio Germany team says.
July 5, 2021
With the Horturion HPS 1000W de el Supra Plus lamp, Ushio Germany GmbH presents another innovation in the field of plant growth lamps. "The Horturion Supra Plus is a 1,000 W lamp with a light output of 2180 µmol/s and therefore the most efficient 1,000 W lamp ever introduced in the market", the Ushio Germany team says. "It offers 3.8 % more light output compared to the standard Horturion 1000 W lamp and enables growers to achieve a noticeable increase in yield and thus higher income with the same energy input."
"The Horturion Supra Plus is the answer to the demand for a 1,000 W lamp with significantly increased light output, a result of many years of exchange and closest cooperation with our customers, especially in the Netherlands, the pioneer in horticulture in Europe, if not worldwide", they continue.
The Horturion Supra Plus is compatible with all standard 1,000 W luminaires for double-ended lamps on the market and will be available as early as August 2021.
More micromoles per square meter
At 2180 µmol per second, the Horturion Supra Plus offers 3.8 % more light output compared to its 1,000 W equivalent at 2100 µmol/s.
In-house labs for the highest quality HPS lamps
Just at the end of last year, Ushio Germany, formerly BLV Licht- und Vakuumtechnik GmbH, made a clear and bold statement by discontinuing its horticulture LED lighting solutions division and clearly focusing on the development, production, and distribution of HPS lamps for this sector.
Consistently following this strategic orientation, the company has further expanded its development capacities at the Steinhöring site. Ushio’s own laboratories, equipped with the latest technology and sophisticated equipment for precise measurements and tests, have for years provided ideal conditions for innovations and world premieres. All prototypes of the legendary BLV Horturion HPS series were developed here, including the Horturion Supra Plus.
Expanded production capacities
In order to meet the increasing demand, even for high volumes, a new production facility with a total area of almost 6,000 m² was inaugurated at the Ushio Poland site back in 2017. At full capacity, one million lamps for professional greenhouse lighting can be produced here per year. With this capacity, Ushio is not only a trusted partner for lamps of the highest quality but is also able to reliably produce and deliver orders with very high quantities for large projects.
The Horturion® Supra Plus will be available from August 2021. Pre-orders are accepted as of now.
For more information:
Ushio
info@ushio.eu
www.ushio.eu
BLV
Muenchener Strasse 10
85643 Steinhoering
Germany
www.blv-licht.de
VIDEO: Vertical Farms Could Take Over The World
As the global population continues to increase, vertical farming is becoming a more widely recognized and viable solution to our food production problem
By JACK BERNING
May 22, 2021
Vertical Farming Offers Better Tasting,
More Sustainable Produce.
Will It Take Over Farming
As We Know It?
As the global population continues to increase, vertical farming is becoming a more widely recognized and viable solution to our food production problem. Vertical farming is a type of indoor farming where crops are grown in stacked layers, rather than spread out across large plots of land.
To View The Video, Please Click Here
These futuristic farms aren't just going to have an impact on how we survive here on Earth; they could also enable us to create a food source beyond our planet, without a dependence on the outdoor climate or arable land.
Although the task sounds unimaginable, developments in controlled environment agriculture are proving that it is very much possible. Adopting these sustainable farming practices could lead to a monumental shift in how we produce food, both for today and the future of humanity.
Vertical Farming Advantages
Vertical farms offer many benefits over traditional farming practices — an increased crop yield with a smaller land requirement, more control over the resulting flavor and cleanliness of crops, and the prospect of better access to healthy foods in underserved communities, to name a few.
Because these farms are constructed completely indoors using LED lights, their output isn't subject to the natural elements that typically affect plant production such as adverse weather, insects, and seasons.
Vertical farms offer more control over the resulting flavor and cleanliness of crops, and the prospect of better access to healthy foods in underserved communities.
They're better for the environment because they require less energy and put out less pollution, without a need for heavy machinery, pesticides, or fertilizers. Vertical farms often use soil-less farming methods like aquaponics, hydroponics, and aeroponics, which requires just 10% of the amount of water consumed by conventional outdoor farms.
Think of a vertical farm as a plant factory — one that enables farmers to predictably grow anything, anywhere, from strawberries to kale. The idea was first introduced in 1999 by Dickson Despommier, a professor at Columbia University. Despommier and his students came up with designs for a "skyscraper farm" that could feed 50,000 people. Though the structure has yet to be built, they successfully managed to popularize the ideology behind vertical farming systems.
Output isn't subject to the natural elements that typically affect plant production such as adverse weather and insects.
So, why wasn't the skyscraper farm ever built? The answer sheds light on one of the most prominent vertical farming disadvantages — cost. A single farm can cost a hundred million dollars to construct, and a lack of data surrounding the long-term economic feasibility of vertical farms has caused some investors to shy away.
However, this hasn't stopped vertical farmers from persisting to disrupt the food production industry. Vertical farming has already been adopted in countries like China, Japan, and other parts of Asia. In fact, the market for vertical farming in that region is expected to increase 24% by 2026. And in the U.S., some vertical farming companies are already selling their produce in stores.
More Produce With Less Resources
One of those companies is Plenty, headquartered in San Francisco, California. Plenty was founded in 2014 by Matt Barnard and Nate Storey with a simple yet powerful mission to improve the lives of plants, people, and the planet.
Plenty already has established vertical farms in the San Francisco Bay Area, Wyoming, and Washington. These farms supply fresh produce including kale, arugula, and lettuce to major grocery stores like Whole Foods and Safeway.
The team at Plenty recently began construction on a new farm in the Bay Area that they call Tigris. Tigris will be its largest and most efficient farm yet, capable of growing a million plants at a time.
With Plenty's vertical farming technology, 700 acres of farmland can be condensed into a structure the size of a big-box store. Plenty's farms harvest 365 days per year and shrink growth cycles to about 10 days for many of their products.
This results in a yield increase of about 700% as compared to traditional farming, all while saving about a million gallons of water per week and using just one percent of the land that traditional farms use.
The secret to this astronomical efficiency lies in the technology. Plenty's farms are equipped with air handling units that capture transpired water, allowing them to recirculate 99% of the water back into the system. They also use LED light bulbs and, seeking to be as efficient as possible, the bulbs are designed in a grid format that maximizes the amount of energy absorbed by the plants.
These systems allow farm operators to have more control over their crop yield — all the way down to a plant's flavor profile. Blue LED lighting, for example, can create a crispier crunch in kale leaves. Additionally, without a need for pesticides, their products are completely organic.
Plenty's farm saves about a million gallons of water per week and uses just 1% of the land that traditional farms use.
"When you grow things outside, the elements are much more unpredictable," Shireen Santosham, the head of strategic initiatives for Plenty, explains. "If you grow indoors, you can control a lot of those factors in ways that are accessible to outdoor growers. And the result is that our produce can be hundreds of times cleaner."
Not only is the produce cleaner, it's also higher quality. Because Plenty's products are grown in urban areas and don't have to be shipped across the country, the brand doesn't have to prioritize shelf life. Less transportation needs also reduces their carbon footprint.
What could all of this mean for the future? That every place in the world, regardless of climate, could sustainably grow the same nutrient-rich and flavorful crops. And it could someday result in the colonization of other planets, as well.
"We can give the world back — a lot," says Storey. "We can give the world back land. We can give back the jungles of Borneo to the orangutans. We can give back the Amazon to the planet. We can give back the midwest to the buffalo. We can give back the things that we've taken. And we can be a lot less extractive."
Vertical Farming Startup Oishii Raises $50m In Series A Funding
“We aim to be the largest strawberry producer in the world, and this capital allows us to bring the best-tasting, healthiest berry to everyone.”
By Sian Yates
03/11/2021
Oishii, a vertical farming startup based in New Jersey, has raised $50 million during a Series A funding round led by Sparx Group’s Mirai Creation Fund II.
The funds will enable Oishii to open vertical strawberry farms in new markets, expand its flagship farm outside of Manhattan, and accelerate its investment in R&D.
“Our mission is to change the way we grow food. We set out to deliver exceptionally delicious and sustainable produce,” said Oishii CEO Hiroki Koga. “We started with the strawberry – a fruit that routinely tops the dirty dozen of most pesticide-riddled crops – as it has long been considered the ‘holy grail’ of vertical farming.”
“We aim to be the largest strawberry producer in the world, and this capital allows us to bring the best-tasting, healthiest berry to everyone. From there, we’ll quickly expand into new fruits and produce,” he added.
Oishii is already known for its innovative farming techniques that have enabled the company to “perfect the strawberry,” while its proprietary and first-of-its-kind pollination method is conducted naturally with bees.
The company’s vertical farms feature zero pesticides and produce ripe fruit all year round, using less water and land than traditional agricultural methods.
“Oishii is the farm of the future,” said Sparx Group president and Group CEO Shuhei Abe. “The cultivation and pollination techniques the company has developed set them well apart from the industry, positioning Oishii to quickly revolutionise agriculture as we know it.”
The company has raised a total of $55 million since its founding in 2016.
UNFI Picks Up Living Greens Farm Products in Midwest Expansion
Living Greens Farm (LGF), the largest vertical, indoor aeroponic farm in the US that provides year-round fresh salads, salad kits, microgreens and herbs, announced the addition of significant new retail distribution of its products in the upper Midwest to independent, specialty, and co-op retailers
I|mage from: Living Green Farms
Living Greens Farm (LGF), the largest vertical, indoor aeroponic farm in the US that provides year-round fresh salads, salad kits, microgreens and herbs, announced the addition of significant new retail distribution of its products in the upper Midwest to independent, specialty, and co-op retailers.
Starting February 2021, LGF’s full line of products featuring ready-to-eat bagged salad products (Caesar Salad Kit, Southwest Salad Kit, Harvest Salad Kit, Chopped Romaine, and Chopped Butter Lettuce) will be carried by UNFI Produce Prescott (formerly Alberts Fresh Produce). UNFI Produce Prescott is a division of UNFI, which distributes food products to thousands of stores nationwide. Their focus is on independent, specialty and co-op retailers.
UNFI has eight warehouses nationwide. LGF’s products will be carried by their upper Midwest location, located just across the river from the Twin Cities in Prescott, WI. This distribution center services hundreds of retailers throughout Minnesota, Wisconsin, Illinois, North Dakota, South Dakota, Missouri, Iowa and Nebraska. UNFI is the first national Certified Organic distributor, something they take a lot of pride in. Their produce and floral businesses are rooted in local farms and seasonal import growers.
LGF’s proprietary vertical indoor farming method yields the highest quality and freshest produce available. This is because there are no pesticides or chemicals used in the growing process. And because LGF’s growing, cleaning and bagging process significantly reduces handling and time to the retail shelf, consumers enjoy the freshest product on the market. These benefits continue to attract new users and new retail distribution as UNFI Produce Prescott is the second UNFI location to carry LGF. In December, UNFI’s Hopkins, MN location began offering LGF products.
For more information on why Living Greens Farm products are the cleanest, freshest and healthiest farm salads and greens available, go to www.livinggreensfarm.com.
Fifth Season Takes Vertical Farming to a Whole New Level
Fifth Season’s verdant baby spinach screams farm fresh even though it’s grown nowhere near traditional farmland. The sweet and slightly crunchy greens are grown in a Braddock warehouse on racks stacked 30 feet high. Located just a stone’s throw from U.S. Steel’s Mon Valley Works Edgar Thomson Plant, it is urban farming at its core
Image from: Pittsburgh Post-Gazzette
Fifth Season’s verdant baby spinach screams farm fresh even though it’s grown nowhere near traditional farmland. The sweet and slightly crunchy greens are grown in a Braddock warehouse on racks stacked 30 feet high. Located just a stone’s throw from U.S. Steel’s Mon Valley Works Edgar Thomson Plant, it is urban farming at its core.
What makes the vertical farming operation especially unique is that it is automated and robots call the shots. About 40 to 60 machines are involved in every step of the life of the spinach and other leafy greens, from planting the seed to providing nutrients to the final packing.
Fifth Season does employ local “farm workers” to assist the robots in seeding, harvesting, packaging, quality assurance and control using computer software, but there is no human touch involved through it all.
“The first time someone ever touches the spinach leaf with a finger is when the package is opened,” says Grant Vandenbussche, chief category officer.
Co-founded by brothers Austin and Brac Webb and Austin Lawrence, Fifth Season started a year ago. Within months it was rolling out its baby spinach, leafy greens and salad kits.
“We wanted a name that represents what we are doing,” says Austin Webb, 32, who also is the CEO. “It is a call to the fact we have created an entirely new season. It is 24/7, 365 with the technology we have built.”
None of them planned to become modern farmers, says the Carnegie Mellon University grad, but they turned to vertical farming because it was an efficient, economically sustainable way to solve land and water woes.
Image from: thespoon.tech
‘Fields’ of Greens
Fifth Season grows an equivalent production of 200 acres in 25,000 square feet of grow space. Its “fields” are stacked on top of one another in vertical shelves. When you add up all that surface area of grow space, it is more like 126,000 square feet.
“We also quickly turn crops at the farm,” Mr. Vandenbussche says.
While spinach takes about 40 days to grow outdoors and can be harvested only twice during its peak season, it takes the crop only three or four weeks to grow in the controlled environment and is harvested 19 times. Once the plants are harvested, a new cycle of reseeding begins with fresh media, seeds and nutrients.
“That’s why we get so much more productivity,” he says. “We are immediately reseeding our ‘land.’”
This controlled environment yields quality produce because it is always peak season at Fifth Season, says Chris Cerveny, who heads the Grow R&D division. Greens are grown in the same conditions year-round, getting the exact amount of nutrients and water they need. Because pests and airborne toxins also are kept at bay, crops can be produced without pesticides.
All that TLC comes through in the slightly curled baby spinach, which is sweet and not grassy. The leaf doesn’t wilt or get slimy or lose its slight crunch even after two weeks of refrigeration.
A lot of thought was given even for the curl, which gives the spinach a stronger volume, making it look full and bountiful. The curl also makes the spinach more forkable unlike its flat-leaf counterpart that is hard to stab on a plate.
Other leafy greens such as kale, mustard, Chinese cabbage, green tatsoi and purple pac choi are featured in two blends — Bridge City and Three Rivers. Fifth Season plans to roll out its Romaine lettuce in spring.
The greens also are found in four types of salad kits — Sweet Grains (blended greens, quinoa, chickpeas, corn, feta and poppy seed dressing), Crunchy Sesame (blended greens, farro, sesame sticks, dried cranberries and ginger-mandarin dressing), Toasted Tuscan (spinach, lentils, sun-dried tomatoes, bagel chips and vinaigrette), and Spiced Southwest (blended greens, black beans, pepitas, cotija cheese, corn-salsa sticks and chipotle ranch dressing) — which are available online and in Giant Eagle stores. A fifth salad kit is in the works and is being called “a shakeup of one of the most classic salads.”
While machines are a big part of what Fifth Season does, it seeks to keep human connection alive. It recently launched a recipe blog for those who have an appetite for cooking and writing, The Green Room is devoted to cataloging personal memories, dream meals and recipes via short stories.
Fifth Season also has partnered with the Penguins and is providing greens for the team’s pregame meals for the 2020-21 season.
“We want people in Pittsburgh to be able to eat the exact same delicious blend of greens that Sidney Crosby and company are eating,” Mr. Webb says. “We want people to know that there’s a new way to grow food and to eat and experience it.”
Image from: Next Pittsburgh
It’s All Under Control
Everything from seeding to packaging is done in four rooms. The process starts in the seeding and processing room, where seeds and growing media are placed inside black planter-like boxes called inserts. Each has a unique code that’s traced by a software system. The inserts go on white trays that pass through a photo station, feeding information to the computer system, and then glide into the bio dome.
There are two rooms in the bio dome, each with a grow space of 12,500 square feet. They’re lit up with a pinkish-purplish glow from high-efficiency LED light bulbs that mimic the different seasons of the year.
“They are positioned over the plants at different heights depending on stage of growth,” Mr. Cerveny says. “This is partly how we can provide consistently ideal growing conditions.”
As the plants grow, they are moved by a robot to optimize their growth cycle. Full-grown crops are transferred to the harvesting room by another robot.
“Harvesting is where it becomes like a Willy Wonka factory,” Mr. Vandenbussche says.
Long rows of trays filled with tiny plants are sent on a conveyor system to a station where workers inspect them for quality with surgical tools. After inspection, the plants are harvested by a robot and then immediately ride up a tall conveyor to be packaged and sealed in a 34- to 36-degree room so they remain fresh.
“Every crop we grow gets evaluated for maximum flavor, volume, crunch and color,” he says.
The plants’ intense, dark color is controlled by LED light bulbs, which are dialed up or down to get the correct hue. Although they never see the sun, the greens don’t get into a funk as humans might.
“What humans see in terms of light and how chlorophyll responds during photosynthesis are two different things,” Mr. Cerveny says. “Plants really only need red and blue light to grow effectively. We include some additional colors to help bring out other quality aspects of our crops, but providing the full sunlight spectrum is effectively a waste of energy, especially indoors.
“To the human eye, it looks like the plants live in a land of purple and pink lights, but they are perfectly happy there.”
Even though the environment is controlled and the software system is constantly updated, no two plants are exactly the same. Some fight for light more than others. Some might fail the quality control test and end up in a compost waste facility if their flavor is off or their color is not right.
“That is what is so amazing. We have more control than any other farmer, and yet we have limitations. Every seed is different,” Mr. Vandenbussche says. “They are plants. They are real living organisms.”
Feeding Leeds: A Fair and Self-Sustaining Food System for the City
A bold vision for feeding the population of Leeds would transform the city into a far more food secure, fair and sustainable place to live. Analysts from the University of Leeds’ Global Food and Environment Institute studied the city’s food system to assess its resilience in the face of supply chain and delivery disruptions caused by severe weather, climate change and events such as the COVID-19 pandemic and Brexit
Image from: University of Leeds
A bold vision for feeding the population of Leeds would transform the city into a far more food secure, fair and sustainable place to live.
Analysts from the University of Leeds’ Global Food and Environment Institute studied the city’s food system to assess its resilience in the face of supply chain and delivery disruptions caused by severe weather, climate change and events such as the COVID-19 pandemic and Brexit.
The urban food system includes all the activities involved in the production, distribution and consumption of food within a city.
They mapped and analysed publicly available data relating to agricultural production and human health in the metropolitan district and discovered that 48.4% of the city’s total calorific demand can be met by current commercial food production activities.
This is relatively high for such an urbanised space, but there is little diversity in what is being produced. Three cereal crops (wheat, barley, oats) dominate the Leeds production system, reflecting a post-war food system that focused on energy supply. This means that most of the fruits and vegetables consumed in the city are transported in from elsewhere.
The researchers’ findings also show that the most deprived areas of the district, which have higher rates of obesity, diabetes, and cardiovascular disease, are also likely to be the first to be impacted by supply disruptions. The resulting food shortages can increase prices, and people on low incomes may not have the option to travel to larger supermarkets or afford to bulk buy.
The researchers say there are no quick and easy options for significantly increasing the security, fairness, or sustainability of the food system supplying Leeds.
But they say the metropolitan district’s sizeable number of farmers, manufacturers, suppliers, and food services could all contribute to improving its food resilience by creating a system which provides easy access to healthy foods, shares energy, reuses water and nutrients and repurposes local infrastructure and resources.
Caroline Orfila, who led the study, published today in the journal Food Security, is Professor of Plant Biochemistry and Nutrition in the School of Food Science and Nutrition. She said: “Our work demonstrates the inequalities in food production and dietary health.
“The local food production system can only provide around 50% of the calories needed by the population, highlighting that ‘eating local’ is not currently possible for everyone. In particular, the local food system would not provide sufficient protein or fats. The lack of food diversity suggests current food production is also unlikely to meet vitamin and mineral requirements.
“Any disruptions to food production, distribution or retail, from flooding, longer term climate change, COVID-19 or Brexit, is likely to impact those in deprived areas the most.
“Disruptions tend to cause shortages in some food categories, which then increase food prices. People on low incomes spend more of their income on food; any increases in food prices will limit what they can afford to buy.
“People in deprived areas have limited choice of where to buy foods, they may not have private transport to access larger supermarkets or access to online shopping. They may also not have the cash flow or storage space to buy items in bulk, relying on what is available.
“Interventions are needed to level up those areas.”
Researchers identified more than 1,000km2 of warehousing, derelict land, and unused floor space in abandoned buildings, with direct or possible connections to renewable energy and water.
Half of this land lay near food banks, community centres and numerous food processors and outlets.
The land could potentially be used for no waste innovative farming techniques, including vertical food farms, where crops are grown in vertically stacked layers; green walls, where plants grow on vertical surfaces, and rooftop agriculture, where fresh produce is grown on top of buildings.
The study found that within the metropolitan district of Leeds there is substantial food activity with more than 5,500 businesses and charities supplying fresh and prepared food, including fast food providers, restaurants, and supermarkets. Some 23 food banks are located within the inner-city area.
There are almost 100 hectares of allotment controlled by Leeds City Council, and approximately 39 hectares of private allotment and community growing areas in the Leeds Metropolitan District.
Lead author Dr Paul Jensen, also from Leeds' School of Food Science and Nutrition at the University of Leeds, said: “We found there are numerous underutilised city assets that could be incorporated into a resource efficient urban food ecosystem, which could include a mix of vertical farming, hydroponics, or more conventional growing methods.
“Most notably, many of these areas are within those suffering most from food poverty, diet related health issues and a limited intake of fruit and vegetables - those who are usually the first to suffer during a crisis situation.”
The research identified locations for ‘food hubs’ that connect producers to consumers and discuss the need for a coordinated approach between producers, government, charitable groups and consumers in creating a more sustainable food system.
The research was carried out with FoodWise Leeds, a not-for-profit campaign by Leeds City Council, the University of Leeds, businesses and charities to address food health and sustainability issues.
FoodWise Leeds co-ordinator Sonja Woodcock, said: “This past year has highlighted how vulnerable the local food system is. Taking a coordinated approach and implementing available policy levers, such as including local food within public procurement contracts, increasing access to land for both commercial and community food growing, as well as investing in cooking and food skills will help to create a more resilient and fair local food system.”
Professor Orfila added: “These findings are significant because it shows the vulnerability and inequality of UK cities and urban food systems. The situation in Leeds mirrors the situation in many other cities worldwide.”
Professor Steve Banwart, Global Food and Environment Institute Director said: “The results of this study provide essential evidence to guide access to nutrition for the entire population. The project dramatically changes our view of what is a city and what is a farm and catalyses our partnerships to build a more resilient community.”
Further Information
‘Mapping the Production-Consumption Gap of an Urban Food System: An Empirical Case Study of Food Security and Resilience’ and is published on 8 February in the journal Food Security. It is available online here:https://link.springer.com/article/10.1007/s12571-021-01142-2.
For media enquiries, contact University of Leeds press office via pressoffice@leeds.ac.uk.
Plants Have A Body Clock As Well Research Shows
This research highlights a single letter change in their DNA code can potentially decide whether a plant is a lark or a night owl
This research highlights a single letter change in their DNA code can potentially decide whether a plant is a lark or a night owl. The findings may help farmers and crop breeders to select plants with clocks that are best suited to their location, helping to boost yield and even the ability to withstand climate change.
The circadian clock is the molecular metronome that guides organisms through day and night -- cockadoodledooing the arrival of morning and drawing the curtains closed at night. In plants, it regulates a wide range of processes, from priming photosynthesis at dawn through to regulating flowering time.
These rhythmic patterns can vary depending on geography, latitude, climate, and seasons -- with plant clocks having to adapt to cope best with the local conditions.
Researchers at the Earlham Institute and John Innes Centre in Norwich wanted to better understand how much circadian variation exists naturally, with the ultimate goal of breeding crops that are more resilient to local changes in the environment -- a pressing threat with climate change.
To investigate the genetic basis of these local differences, the team examined varying circadian rhythms in Swedish Arabidopsis plants to identify and validate genes linked to the changing tick of the clock.
Click here to access the complete research.
21 Dec 2020
Published by Dani Kliegerman for iGrow.News
Valoya Announces Its Spectrum Technology Licensing Program
Valoya’s extensive patent portfolio in the field of horticultural LED lighting is a result of significant innovation and investments into R&D over the past 11 years
Valoya, the research-driven LED grow light manufacturer has today announced a licensing program making their patented technology available to LED manufacturers and horticultural LED fixture providers.
Valoya’s extensive patent portfolio in the field of horticultural LED lighting is a result of significant innovation and investments into R&D over the past 11 years. The patents are in the field of light spectra for plant cultivation and lighting applications. At the moment, the portfolio consists of over 100 patents, all of which can be reviewed at valoya.com/patents.
'We have always been curious about the possibilities of light and how its potential could be pushed further to make cultivation of crops we use for food or medicine production more efficient. When we started in 2009, LED meant piercing purple light produced by red and blue chips. We were the first to apply wide spectrum LED light to plants in our experiments and to introduce wide spectrum light to the market. We are now in a business phase where we can extend this intellectual property and know-how to other companies wishing to produce premium quality horticultural LED luminaires through our licensing program' comments Lars Aikala, the CEO and Co-Founder of Valoya.
The research and development at Valoya does not stop. ‘After having conducted over 600 plant trials on over 300 plant varieties/species, we have an understanding of plant response to light, unmatched by other LED companies in the market. The focus remains on advancing horticulture through developing even better spectra and helping our customers grow. We are happy we get to share this expertise with other companies now’, comments Nemanja Rodic, Marketing Director of Valoya.
To learn more about Valoya's patent licensing program,
please click here.
About Valoya
Valoya is a provider of high end, energy-efficient LED grow lights for use in crop science, vertical farming, and medicinal plants cultivation. Valoya LED grow lights have been developed using Valoya's proprietary LED technology and extensive plant photobiology research. Valoya's customer base includes numerous vertical farms, greenhouses, and research institutions all over the world (including 8 out of 10 world’s largest agricultural companies).
Additional information:f
Valoya Oy, Finland
Tel: +358 10 2350300
Email: sales@valoya.com
Web: www.valoya.com
Facebook: https://www.facebook.com/valoyafi/
Twitter: https://twitter.com/valoya