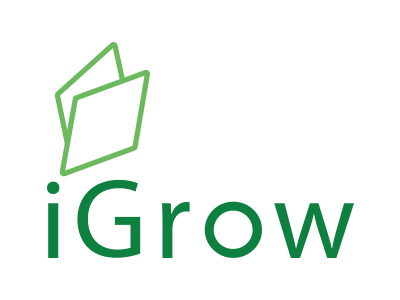
Welcome to iGrow News, Your Source for the World of Indoor Vertical Farming
Step Away From That Screen And On To Our Expanded Expo Floor
There's nothing like an in-person event for getting a first-hand look at the latest product innovations. So step away from that computer screen, step onto our expo floor and see live product demonstrations...Touch new products...Ask questions and gather feedback from company execs and peers in the booth
BIGGER, BETTER EXPO FLOOR OFFERS PERFECT ZOOM FATIGUE FIX!
(And some pretty great solutions for your business, too)
There's nothing like an in-person event for getting a first-hand look at the latest product innovations. So step away from that computer screen, step on to our expo floor and see live product demonstrations...Touch new products...Ask questions and gather feedback from company execs and peers in the booth.
We've significantly expanded our expo floor to bring you even more top names, established best-sellers and promising start-ups. See the latest in lighting, operating, automation and control systems, growth chambers, seed treatments, plant nutrition, greenhouse & hydroponic supplies, substrates, pest control, irrigation, equipment & design resources and so much more from companies like:
LEARN MORE
YOUR TWO-DAY INDOOR AG-CON EXPERIENCE PACKAGE
Indoor Ag-Con is so much more than an event. It's an experience! And one you don't want to miss. Hear from 70+ speakers, network with industry peers, see the latest product innovations. Then, head back to your operation armed with actionable ideas and profitable strategies that promise to grow your business!
Register before our Early Bird Rates end on August 16, 2021 to save up to $300 on our full access pass. And if your plans change, no worries! Passes are completely refundable prior to September 27, 2021, and include:
All Keynotes, Morning Conference Sessions, Afternoon Panels
Expo Floor Access
Welcome Gift Bag
Complimentary On-Demand Access to In-Depth, 2-Day "Financing Indoor Ag Seed To Scale" webinar
White Paper From The Packer & PMG presenting the latest research on indoor growing & sustainability
Lunch Daily
Show Floor Cocktail Receptions
Event App
Access to Indoor Ag-Con Library
REGISTER NOW & SAVE UP TO $300
OUR SAFETY PROMISE
Your health and safety are priority one at Indoor Ag-Con Orlando.
Rest assured that the Indoor Ag-Con team is closely monitoring the
guidelines issued by the CDC, state and local officials. We're working with our venue partner, Hilton Orlando, to provide you with a safe and
productive environment to conduct business.
SPECIAL THANKS TO OUR INDOOR AG-CON SPONSORS,
MEDIA & MARKETING ALLIES
Indoor Ag-Con, 3834 Silvestri Lane, Las Vegas, NV 89120, United States
Optimizing Resource Use Efficiency In CEA System
An important factor affecting the profitability of vertical farming is a grower’s ability to consistently deliver a predictable product
Date: July 29, 2021
Time: 2 p.m. - 3 p.m. EDT
Presented by: Murat Kacira (The University of Arizona)
Click Here To Register
Webinar Description
An important factor affecting the profitability of vertical farming is a grower’s ability to consistently deliver a predictable product. To achieve this, growers must create an environment that supplies all the crop’s needs over its entire growth cycle by identifying and co-optimizing environmental variables such as CO2, light, humidity, airflow, and other parameters. This presentation will focus on real-time sensing, monitoring, and climate control strategies with system designs for environmental uniformity leading to enhanced resource use efficiency in CEA system.
Dr. Murat Kacira (Professor)
Murat Kacira is director of the Controlled Environment Agriculture Center and he is a professor in the Biosystems Engineering Department at the University of Arizona. He received his B.S. degree in Agricultural Engineering in Cukurova University in Turkey and M.Sc. and Ph.D. degrees from Food, Agricultural and Biological Engineering from The Ohio State University in USA. His research involves automation, environmental control, alternative energy integrated CEA systems and resource use optimization in controlled environment agriculture systems including greenhouses and vertical farming-based plant factories with artificial lighting. He is a member of American Society of Agricultural and Biological Engineers (ASABE), American Society of Horticultural Sciences (ASHS), and International Society for Horticultural Science (ISHS). He serves as Chair of the Division Precision Horticulture Engineering under ISHS.
Special thanks to our Industry partners
Join Today
If you have any questions or would like to know more about GLASE, please contact its executive director Erico Mattos at em796@cornell.edu
CEA Producers Join To Support Data-Driven USDA Project
AppHarvest (Ky.) and Revol Greens (Texas) are vanguards of modern greenhouse cultivation, while Elevate Farms (N.J.) and Fifth Season (Penn.) are pioneers in vertical farming
Four agricultural producers have joined with nonprofit Resource Innovation Institute (RII) under the banner of its USDA Conservation Innovation Grant-funded project: Data-Driven Market Transformation for Efficient, Sustainable Controlled Environment Agriculture.
AppHarvest (Ky.) and Revol Greens (Texas) are vanguards of modern greenhouse cultivation, while Elevate Farms (N.J.) and Fifth Season (Penn.) are pioneers in vertical farming. The producers will serve as initial pilot partners in support of the USDA-funded project that aims to transform the controlled environment agriculture (CEA) market sector toward more efficient production through coordinated research on energy and water practices spearheaded by RII and the American Council for an Energy-Efficient Economy (ACEEE).
“We are thrilled to unite with these categories in the name of innovation and agricultural resilience,” said Derek Smith, Executive Director of RII. “Working together with these initial pilot partners and others to follow, we can unlock basic knowledge about performance metrics that will serve as beacons of efficiency and productivity for CEA producers globally.” In addition to geographic diversity, the producers represent an expanding global market growing a range of crops in indoor environments, from microgreens to tomatoes to berries.
Resource Innovation Institute’s PowerScore resource benchmarking platform enables CEA producers to confidentially validate their innovative practices. Using standardized key performance indicators, PowerScore helps producers gain powerful insights into their operational performance while protecting strategic business interests.
“RII is trusted throughout the supply chain to provide data analysis and peer-reviewed guidance to producers, vendors, governments and utilities. Our consortium of members and partners are committed to collaboratively study the most sustainable horticultural practices across climate zones, building types, technologies and techniques to guide decision-makers on how to advance agricultural resilience,” said RII’s Smith.
To ensure the highest level of PowerScore data protection, RII has engaged Management Science Associates (MSA), global companies in data security and analytics, with expertise in HIPAA compliance and benchmarking for associations across industries. Together with producers, investors, and supply chain partners, RII continues to develop protocols that clearly define access, use, and ownership of data.
“We believe that the only way to fundamentally build an industry starts with data capture and accountability,” said Travis Kanellos, Chief Strategy Officer, Elevate Farms. “Our approach from day one has been to drive yields and profitability through metrics and KPIs. We believe RII will validate our approach."
For more information:
Resource Innovation Center
www.resourceinnovation.org
23 June 2021
Can Vertical Farms Be Profitable?
Basically, we’re skeptical of both the economics and the save-the-world ethos that many companies preach. We enlisted an industry insider to help us separate the wheat from the chaff
Earlier this year, we covered a couple of indoor farming companies going public through mergers with special purpose acquisition companies (SPACs). Neither seemed very appetizing for retail investors, with negligible revenues to date. As we predicted, more indoor farming startups (referring to both large-scale greenhouses and vertical farming operations) are jumping on the SPAC crazy train. The latest is a Montana company called Local Bounti that had generated little buzz until this month’s announcement, which included news that Cargill is providing $200 million in debt financing in the deal.
In this article, we want to take a step back and look a little more closely at the indoor farming industry, sometimes referred to as controlled environment agriculture (CEA), particularly on the vertical farming side of things. Basically, we’re skeptical of both the economics and the save-the-world ethos that many companies preach. We enlisted an industry insider to help us separate the wheat from the chaff.
Saving the World from BS
Mark Korzilius
Mark Korzilius is the founder and chief strategy officer of &ever, a vertical farming startup based in Germany, with its first mega-farm located in the desert of Kuwait. Korzilius was also the co-founder in 2002 of a chain of fast-casual Italian restaurants, Vapiano, with more than 200 locations in about 30 countries. He reached out to us, as founders sometimes do after reading a story that didn’t include them, to tell us about all of the cool things their company is doing. In the case of Korzilius, he also wanted to set the record straight on all of the things that competitors like AeroFarms and other indoor vertical farming companies aren’t doing despite claims to the contrary.
Obviously, Mr. Korzilius is biased, but he also confirmed one of our chief suspicions: Many indoor farming companies claim they are on a mission to help feed the world, which seems incongruous with the fact that most are growing leafy greens, herbs, berries, and maybe tomatoes. Hardly the sorts of staples that are going to keep the estimated 800 million people in the world from going hungry at the end of the day. He also argues that claims of automation using artificial intelligence and sensor-rich environments are also overblown.
“We truly believe to become farmers and to be successful farmers for some crops, we can prove that [vertical farming] is, in the end, a way forward,” he says. “Hopefully, we can find some technologies to really overcome some issues that have been created by others … that will help solve problems that have been the result of technologies that have been created 50 years ago.”
In the second half of that comment, Korzilius is obviously referring to the modern industrial farming system, with its reliance on pesticides, herbicides, and fertilizers that deplete and poison soils and water supplies. That’s why you see so many companies developing natural fertilizers using microbes or biomanufacturing solutions for non-chemical pesticides. Outdoor agriculture is also water intensive, especially for products like almonds, which require one gallon of water per nut. Various technologies are in development to use water more efficiently, from soil sensors to aerial imagery from drones and satellites. Vertical farming gets at the root of the problem by moving the growing operation indoors, employing LED lights and hydroponics to deliver nutrients using only water rather than soil. That eliminates both pesticides and many traditional fertilizers, and reportedly cuts down on water usage by as much as 95%. Let’s take a look at the specific technology behind Korzilius’ company.
Creating the Right Climate for Vertical Farms
Founded in 2015, &ever (formerly known as Farmers Cut) has raised an undisclosed amount of money, originally through bootstrapping and Seed funding, before raising a Series A from partners in Kuwait for its mega-farm, a joint venture with a local investment company called NOX Management. Korzilius said &ever is currently raising a Series B but declined to offer any details.
There are two key parts to the company’s technology, as we understand it: Dryponics and climate cells.
Dryponics is a new riff on hydroponics, which involves growing plants without soil. The company uses a proprietary growth substrate to keep the roots dry. In effect, the root system stays on top of the substrate, while absorbing the nutrients in the water. This setup reportedly has several advantages, including using 68% less water than common hydroponic systems and 37% less water than aeroponic systems, which grow plants in the air using a mist environment or similar system. Less water means the basins underneath the substrates are flatter, allowing more compact layering of crops.
Each crop requires different growing conditions, Korzilius explains, so his team developed climate cells – microenvironments optimized for temperature, light, humidity, and CO2, among other factors. Controlling the environment also helps control energy costs, especially in the large structures that house many of today’s vertical farms, including the company’s flagship facility in Kuwait.
Credit: &ever
“Within the same premises, we can create different climates. In our Kuwait farm, we have four climate cells next to each other. So, we could potentially create California climate next to Denmark climate next to Singapore climate,” he explains. “By creating climate cells within one premise, we save energy [and] only climatize what needs to be climatized.”
Take spinach, a notoriously difficult plant to grow indoors that took the company two years to figure out the right combination of substrate and climate. But that work has paid off by reducing the amount of growth time by 15%, which translates into 18 grow cycles a year, which is good enough for Popeye to be an investor (if only he hadn’t blown his retirement on canned spinach).
Betting the Farm on Indoor Farming
The value proposition is that products from &ever leave the farm as living plants with the roots intact, continuing to grow while staying fresh and retaining maximum freshness, according to Korzilius. The Kuwait farm is the first large-scale effort to prove the business model, though the company also has smaller grow towers for on-site retail locations like grocery stores, including one in Munich. A second mega-farm is in development in Singapore.
A &ever grow tower. Credit: &ever
The Kuwait farm, which went live shortly before the Rona hit, is designed to grow up to 250 varieties of greens and herbs. The 30,000-square-foot facility can reportedly produce up to 1,200 pounds of green stuff. Korzilius says the pandemic continues to hinder full-scale operations of the farm, which is overseen by just six employees. However, he claims the vertical farm is profitable from an operations standpoint (in other words, without accounting for the original capital expenditure). “So, we are not selling below cost. Yes, it’s a prototype, but it’s working nicely.”
Tasty greens from a vertical farm in Kuwait. Credit: &ever
However, there is a reason why the mega-farm is located in Kuwait and not in Munich or elsewhere in Europe. Energy is simply cheaper in the Middle East, so it was a no-brainer to plug into the grid there. In Singapore, where electricity doesn’t come as cheaply, the local government has stepped in with grant money to subsidize the project. Currently, Singapore imports more than 90% of its food, so the government is motivated to find ways to be more self-sufficient, especially in the wake of the pandemic.
The bigger implication is that vertical farms will require cheap sources of energy to be economically viable. That goes against the current narrative of locating large-scale operations in the middle of big urban centers where electricity is usually pretty expensive. Of course, there are other economics to consider: Centrally located growing facilities will incur lower shipping costs and can theoretically deliver fresher, tastier products to consumers, who may be willing to pay the premium for what Korzilius calls harvest on demand.
“I strongly believe in consumers being at the center of all activities,” he says. “The consumer, in the end, has to pay for this. And, if he doesn’t, then all of this is just a stupid bubble.”
Conclusion
The bubble is certainly ballooning. The three indoor farming companies that are going (or have gone) public that we are aware of are valued at nearly $4 billion. Last year, the top three indoor farming startups in 2020 funding brought in more than $400 million between them, according to AgFunder News. These companies claim to be building a sustainable food system, but it seems unlikely that a business built on microgreens can be sustainable at that scale and cost. As always, the market will decide which model will succeed.
Tech investing is extremely risky. Minimize your risk with our stock research, investment tools, and portfolios, and find out which tech stocks you should avoid. Become a Nanalyze Premium member and find out today!
What Is Driving The UK’s CEA boom?
The main findings of the panel were that the UK has been lucky with its well-established greenhouse industry which offers a great foundation for vertical farmers to understand the CEA space
“In the UK, fruits and vegetables are quite cheap in comparison to other European countries and other parts of the world. In the UK, the market has been squeezed by supermarkets that squeeze out the margins of the supply chain,” said Andrew Lloud, COO at Intelligent Growth Solutions, during a panel at the Indoor AgTech Innovation Summit.
During the session, three UK-supplier panelists elaborated on the topic. Joining were, Andrew Lloud, COO at IGS, Ben Crowther, Co-founder and CTO at LettUs Grow, Jen Bromley, Head of Plant R&D at Vertical Future, and Oscar Brennecke with Rethink Events who led the conversation.
The main findings of the panel were that the UK has been lucky with its well-established greenhouse industry which offers a great foundation for vertical farmers to understand the CEA space.
However, at the same time, it's quite costly to produce indoors given the high electricity and transport costs. This might change over time, due to several renewable energies coming into the market that will allow for cheaper production. Later on, the panelists will elaborate on the differences between the US and Europe, being monocropping whereas EU farmers grow more different varieties at the same time.
What makes the UK CEA space unique?
Andrew noted that UK consumers are willing to pay a certain price for fruits and vegetables. However, indoor ag bring along high electricity costs, whereas UK transport costs are high as well. Next to that, the economic and political dynamic being post-Brexit and currently battling the pandemic has highlighted its challenges. “Technology can economically viable grow a wide variety of crops, forming part of the food mix in the UK and in other parts of the world.”
73% of the surface area available for farming, said Ben Crowther, Co-Founder and CTO at LettUs Grow, a UK-vertical farming supplier, however, the UK still imports half of the produce.” He claimed that there’s an opportunity to make things more sustainable and efficient. Jen Bromley, Head of Plant R&D at Vertical Future, said that it’s not always about growing at a large scale, but that it differs per crop. “It’s always about pushing boundaries to see where the economics can work for the crop.”
Opportunities
More renewables and power generation are coming in, so there’s the opportunity to drop in things like vertical farms according to Andrew. “The real trick is to see if you can get a tariff from the energy provider so that the price per kw/h consumed is optimized to grow plants in the cheapest way.
Jen added that there are some obvious low-hanging fruits that can be taken within the market. Such as leafy greens, herbs, and fruits, given they work really well with the infrastructure. “However, there are also markets we can go deeper into, such as proteins, high-care products that can all be managed very well in the vertical farming space.”
Andrew added that a wide variety of crops will eventually be important, depending on your location. The difference in the US is that it’s a lot about monocropping, but they don’t tend to have the same diversity as seen in the UK or other European countries. I’ve seen it here, but I expect it to come to America as well.”
UK greenhouse- vs vertical farming market
Ben notes that “because of the well-established UK greenhouse industry, we can better understand the vertical farming market.” Berries are a great example, in the UK there has been a 10% market growth. It drives how people are looking for rootstock in these markets, specifically in greenhouses. As well as looking into year-round growing to complement their off-season. The idea translates into more traditional farmers, looking for a more consistent, lower-risk way to make their business more resilient.
Jen said that a traditional farm is a long-term play as they’re handed down by generations. In a vertical farming system, it’s an infrastructure that has to last. Whereas, Andrew claimed that the seasonal variation will be smoothed out by multi-tenant farmers using the same facility for different crops for different points in the year.
Consumer perception
“On the whole, there’s a growing understanding I think,” says Ben. He explains that there are some products available at various retailers already. Jen noted that branding is far more developed in the US, given the produce brands they have. Whereas Andrew affirmed that the elephant in the room in the UK and Europe is the use of the word organic. In the US, vertically farmed produce can be labeled as organic, however, in Europe, we’re still looking at what post-organic looks like. It’s confusing for the consumers, however, we’re at the beginning of educating people, starting with kids.
Other topics discussed were subsidies and barriers in vertical farming in the UK.
For more information:
Intelligent Growth Solutions
www.intelligentgrowthsolutions.com
For more information:
Vertical Future
info@verticalfuture.co.uk
www.verticalfuture.co.uk
For more information:
LettUs Grow
info@lettusgrow.com
lettusgrow.com
For more information:
Indoor AgTech Innovation Summit
www.indooragtechnyc.com
29 Jun 2021
Author: Rebekka Boekhout
© HortiDaily.com
Designing Future-Proof Substrate for CEA
“I believe that Horticubes® AeroMax will be the most relevant substrate in the industry,” says Dr. Vijay Rapaka, global research manager at OASIS® Grower Solutions, a division of Smithers-Oasis Company, about Horticubes AeroMax. This substrate is engineered for the precision growing of young plants for hydroponic farming of leafy greens and compact plants.
OASIS Grower Solutions Launches Horticubes AeroMax
“I believe that Horticubes® AeroMax will be the most relevant substrate in the industry,” says Dr. Vijay Rapaka, global research manager at OASIS® Grower Solutions, a division of Smithers-Oasis Company, about Horticubes AeroMax. This substrate is engineered for the precision growing of young plants for hydroponic farming of leafy greens and compact plants.
OASIS Grower Solutions was established in the mid-1950s and began with the development of ornamental growing media. Fast forward to the present day and the company has expanded its product offering to meet the demands of the ever-developing horticultural industry, which now includes vertical farms and highly automated greenhouses. OASIS Grower Solutions currently has manufacturing locations in 20 countries and develops new products through in-house research and customer feedback. The company introduced its Horticubes line in the 1980s, then added Horticubes XL in 2011. Now, OASIS Grower Solutions introduces Horticubes AeroMax for the hydroponic production of leafy greens.
The benefits
When designing the Horticubes AeroMax substrate, OASIS Grower Solutions focused on what they consider to be the three cardinal rules of horticultural substrate development. Firstly, a substrate should allow the grower to propagate healthy, uniform, and vigorous young plants. The second rule is that a substrate should support growers in modulating crop growth by facilitating the acceleration or deceleration of growth, or the use of wet and dry cycles. Finally, substrates should be able to withstand automated processes. This, according to Vijay, is especially important in controlled environment agriculture as automation is becoming increasingly used.
“With more LEDs, IoT, and automated processes, we knew that we needed a substrate that allowed us to precise control of young plant growth. We needed a smart substrate exclusively designed for precision hydroponic farming,” says Vijay.
The Horticubes AeroMax is engineered according to these cardinal rules and is unique from other substrates in five main ways. As denoted in its name, AeroMax is a very porous media that enhances the oxygenation of the root zone so that seeds can germinate quickly and uniformly. According to Vijay, more air in the root zone also increases root health and root branching. AeroMax is also different in that the substrate is low-density, low-strength which makes the substrate light and airy. As a result, roots can easily penetrate the substrate and express their full potential without expending much energy.
“With hydroponics, we need the roots to get to the nutrients as soon as possible. We don’t want the substrate to be a barrier,” explains Vijay.
The third advantage of Horticubes AeroMax is the good drainage which virtually eliminates any chance of overwatering because the excess water easily drains out. This also means that growers can achieve maximum nutrient refreshment rates. Fourthly, OASIS Grower Solutions tested multiple substrate colors but eventually selected black as this allows growers to increase the surface temperature of the substrate by a few degrees, thereby accelerating crop growth. A final benefit of Horticubes AeroMax is the reduction in algae growth on the substrate surface as the high drainage rate ensures that the top surface is dry.
According to Vijay, “these five key features weren’t present in our previous substrates. Overall, we achieved in making a substrate that will respond well to controlled growing environments, allowing the precision production of plants.”
The target market for Oasis Horticubes AeroMax
Horticubes AeroMax was primarily developed for leafy green production in vertical farms and was engineered to be future-proof, according to Vijay.
“This industry is progressing with LEDs, IoT, automation, etc. We developed Horticubes AeroMax with all of this in mind and believe it will be the most relevant substrate in the industry.”
OASIS Grower Solutions is currently developing Horticubes AeroMax applications for high-wire products and has another product coming to the floriculture industry.
For more information:
Vijay Rapaka, Global Research Manager
OASIS Grower Solutions
https://oasisgrowersolutions.com/aeromax
Publication date: Wed 16 Jun 2021
Author: Rebekka Boekhout
© HortiDaily.com
Pure Harvest Aims To Change The Face of Fresh Food
Having secured $60 million in funding, Pure Harvest Smart Farms is looking to expand its operations into Saudi Arabia and Kuwait, using advanced technology to bring food security to the arid Middle Eastern climate.
Having secured $60 million in funding, Pure Harvest Smart Farms is looking to expand its operations into Saudi Arabia and Kuwait, using advanced technology to bring food security to the arid Middle Eastern climate.
7 June 2021
Year-round Local Fresh Food
Pure Harvest is a farming startup using hi-tech, fully climate-controlled greenhouses and a coconut shaving hydroponic solution. Their aim is to provide year-round fresh food in a region where nearly 90% of food is imported. Having secured $60 million in funding, with a further $100 million earmarked by Kuwait’s International Investment Company (Wafra), Pure Harvest Smart Farms is looking to expand its operations into Saudi Arabia and Kuwait, using advanced technology to bring food security to the arid Middle Eastern climate. CEO and co-founder Sky Kurtz described their pilot project in Abu Dhabi as showing promising results with the “potential for year-round local production at very high quality and at a very good cost structure.”
Taming the Desert with High Tech Solutions
Farming consumes huge amounts of water, leading to water scarcity even in temperate regions such as Europe and America. In the arid, dry desert wasting even a drop of water is inconceivable, and Pure Harvest Smart Farms claims their self-contained greenhouses offer a level of efficiency 30 times greater than traditional field farms.
This model of controlled-environment agriculture (CEA) uses greenhouses that go far beyond glass walls to isolate plants. A climate chamber removes heat and humidity from the outside air; this humidity is condensed and fed to the plants inside. There is no soil as plants are grown inside a nutrient rich solution and monitored by sensors to keep the plants healthy. Triple-paned smart glass windows and over-pressurized airflow help manage temperatures to within a 1 degree Celsius margin and carbon dioxide is added to optimize plant growth.
Kurtz claims that Pure Harvest is expecting a yield of six to eight times more food per meter than other greenhouse farms, while using only one-seventh the amount of water. It will produce 17 to 23 times more food per meter than a traditional field farm.
A Large Market but Pure Harvest struggles to Gain Funding
Despite the success of the pilot, Pure Harvest has a long way to go. According to Kurtz, once they are producing at a scale of 30,000 square meters the produce should be 20-40% cheaper than imported fresh food giving them a very promising market.
But even with the investment of $60 million, and the $100 million soon to follow, Pure Harvest has struggled to secure the funding to expand. The industry is extremely capital intensive, and the Middle East venture capital market is less developed than in other countries. The company has managed to raise $50 million through bonds known as “Sukuk,” Shariah law compliant Islamic bonds, with a further $10 million investment from a January fundraising round led by Sancta Capital.
With the additional $100 million from Wafra, the total sum might appear to be significant, but compared to comparable ventures it is low. Recently a vertical farming firm in the U.S., Plenty, raised more than $500 million in funding.
A Promising Future for Local Food
With global supply chains heavily disrupted by the Covid-19 pandemic and further shaken by the blockage of the Suez Canal by the Ever Given in March 2021, the UAE region has become increasingly concerned about securing a food supply. If Pure Harvest can deliver on their promises, they stand to benefit handsomely. At the moment there is no reason to suspect otherwise as the company moves forward with expansion plans. Already the Pure Harvest has reached a $35 million agreement with The Sultan Centre in Kuwait to build a farm stretching across 80,000 square meters that can produce millions of kilograms of fresh fruit and vegetables, well past the size that Kurtz marks for profitability.
Photos: findwonder.abudhabi / agfstorage.blob.core.windows.net
USDA Funds Composition of New CEA Market Characterization Report
. “This is the first such supply chain assessment in CEA. We appreciate these leaders for stepping forward to support this important effort.”
Resource Innovation Institute (RII) has assembled a senior level of its Technical Advisory Council to support its USDA-funded project titled Data-driven Market Transformation for Efficient, Sustainable Controlled Environment Agriculture. The new Controlled Environment Agriculture (CEA) Leadership Committee, composed of a range of subject matter experts in CEA, will advise the development of a Market Characterization Report that will analyze the emerging “controlled environment” horticultural supply chain to determine opportunities to increase energy and water efficiency in cultivation.
“Market characterization is a critical first step in a coordinated effort to transform an economic sector toward efficient production,” said Derek Smith, Executive Director of Resource Innovation Institute. “This is the first such supply chain assessment in CEA. We appreciate these leaders for stepping forward to support this important effort.”
The Market Characterization Report represents the first publication that RII will deliver as part of its work on a three-year USDA Conservation Innovation Grant designed to advance resource efficiency in CEA, a diverse, expanding market that includes greenhouses and vertical farms growing a range of crops, from microgreens to tomatoes to berries. RII is partnering with the American Council for an Energy-Efficient Economy (ACEEE) to deploy the grant.
The CEA Leadership Committee is providing input on key market characterization issues such as supply chain: describing key market actors, barriers to energy efficiency and the best leverage points for market interventions; energy use: describing the energy used by producers (including on-site renewable energy, microgrids, and back-up generation); advantages of efficiency; describing the energy and non-energy benefits realized through implementation of efficiency projects; and baseline identification: describing key market baselines to be used in evaluating the impact of the market transformation initiative over time.
The organizations represented on RII’s CEA Leadership Committee include:
American Society of Agricultural and Biological Engineers
American Society of Heating, Refrigerating and Air-Conditioning Engineers
CEA Consultancy
Ceres Greenhouses
Energy Solutions
Fifth Season
Fluence by OSRAM
Grodan
Midwest Energy Efficiency Alliance
Oregon Association of Nurseries
Priva
Resource Innovations
Schneider Electric
Signify
UVM Extension Services
Zartarian Engineering
For a complete roster, see www.ResourceInnovation.org/TAC.
For more information:
Resource Innovation Center
www.resourceinnovation.org
7 June 2021
Controlled Environment Agriculture (CEA) 4.0 - Conference & Exhibition Day 2 - Friday 4th June - Attendee Tickets Still Available - 522 Attendees Registered
By purchasing a ticket for Conference Day 2 you will receive access and instructions on how you can view recording of the below presentations from Conference Day 1
Controlled Environment Agriculture (CEA) 4.0
Day 2 Conference & Exhibition (Virtual)
Friday 4th June 2021
CEA 4.0 Conference & Exhibition Day 2 is this Friday the 4th of June. With 522 industry attendees officially registered, we still have a small number of attendee tickets that have been made available for Conference Day 2 on Friday
Attendee tickets range from £14.99 - £19.99 per attendee.
Day 2 Conference Presenters
Advanced Plant Growth Centre (APGC) - Derek Stewart, Director
Algal Tech - Armando Leon, Founder & CEO
AmplifiedAg - Don Taylor, CEO & Founder
DAG Facilities - Mark Gemignani, CEO
FarmTech Society (FTS) - Nicole Thorpe, Vice-Chair
GlobalG.A.P. - Kristian Moeller, Managing Director
Greens for Good by Farm Urban - Jens Thomas, Technical Director
GroenLeven - Willem de Vries, Business Innovation Manager
Growfoam - Niels Steenvoorden, Chief Commercial Officer
Intelligent Growth Solutions - David Farquhar, CEO
Jungle - Nicolas Seguy, Managing Director
Mycelium - Eric Dargent, Managing Partner
Mycelium - Yishai Nissan, Managing Partner
Natural Resources Institute Finland - Titta Kotilainen, Senior Scientist
Planet Farms - Daniele Benatoff, Co-Founder & Co-CEO
Red Sea Farms - Ryan Lefers, CEO
SolarPower Europe - Miguel Herrero, Policy Advisor
UK Urban AgriTech (UKUAT) - Katia Zacharaki, Communications Director
Urban-Gro - Mark Doherty, Executive Vice President of Operations
Urban Crop Solutions - Tom Debusschere, CEO
Urban Harvest - Alexandre Van Deun, Co-Founder
Urban Harvest - Olivier Paulus, Engineering & Co-Founder
Valoya - Mika Linden, VP Sales
Valoya - Satu Karjalainen, Research Coordinator
Vertical Farm Institute - Daniel Podmirseg, Director
Vertical Future - Jen Bromley, Head of Plant Research & Development
Vertical Harvest - Nona Yehia, Co-Founder & CEO
Würth Elektronik eiSos - Johann Waldherr, Business Development Manager
Day 1 Conference Presenters
By purchasing a ticket for Conference Day 2 you will receive access and instructions on how you can view the recording of the below presentations from Conference Day 1.
AeroFarms - Roger Buelow, Chief Technology Officer
BrightFarms - Paul Lightfoot, President & Founder
CEA Food Safety Coalition - Marni Karlin, Executive Director
Certhon - Martin Veenstra, Consulting Engineer Indoor Farming Systems
Cultinova - Jim Thorpe, Chief Technology Officer (CTO)
Department for Environment, Food and Rural Affairs (Defra) - Caroline Povey, Team Leader – Agri-Innovation Policy
Finnish Glasshouse Growers' Association - Jyrki Jalkanen, CEO
GE Current - Dr. Hans Spalholz, Senior Plant Scientist
Graines Voltz - Solène Voltz, Vertical Farm Sales
Graines Voltz - Wolfgang Fishcer, International Product & Sales Specialist
Heliospectra - Fei Jia, Technical Solutions Manager
HerbanLeaf Farms - Myrianthi Oxtoby, Founder & CEO
Jones Food Company - James Lloyd-Jones, Founder & CEO
LEAF (Linking Environment & Farming) - Caroline Drummond, Chief Executive
Netled - Niko Kurumaa, COO
North Carolina State University - Dr. Ricardo Hernández, Professor
ONO Exponential Farming - Thomas Ambrosi, Director
Planet Farms - Daniele Benatoff, Co-Founder & Co-CEO
Real Leaf Farms - Karen Hennessy, CEO
Signify - Tom Könisser, Business Development Manager City Farming
Singapore Food Agency (SFA) - Poh Bee Ling, Director, Horticulture Technology Department Agri-Food
UK Research & Innovation – Innovate UK - Ian Cox, Innovation Lead
UK Research & Innovation – Innovate UK - Tom Jenkins, Deputy Challenge Director – Transforming Food Production
Urban Crop Solutions - Tom Debusschere, CEO
VEK Adviesgroep - Reinier Donkersloot, Director Business Consultancy
Vertical Future - Jen Bromley, Head of Plant Research & Development
Vitabeam - James Millichap-Merrick, CEO
Wageningen University & Research - Luuk Graamans, Scientist Vertical Farming
CLICK HERE TO BOOK YOUR ATTENDEE TICKET
Click Here To Meet The Current CEA 4.0 Sponsors,
Presenters, Exhibitors & Attendees
VIP Attendee Ticket Includes
Full event access provided to the conference, workshops, exhibition, etc
Personal event attendee profile
Company profile
Ability to arrange up to 36 one-to-one meetings with any attendee during the event
Ability to message and video chat with any attendee
Access to the presentation recordings from Conference Day 1
Company branding on the event website & at the event
CLICK HERE TO BOOK YOUR ATTENDEE TICKET NOW
BEFORE THEY ARE SOLD OUT
TECH 4.0 Ltd
info@tech40.net
https://www.tech40.net/
Polygreens Podcast Episode 28 Jake Emling
Beginning in July 2018 he joined CropKing, Inc. based out of Lodi, Ohio. His experience with hydroponics, aquaculture, and aquaponics was instrumental to his desire to start Root 42 Harvests with his wife Katie
Jake attended Michigan State University where he earned both undergraduate and graduate degrees in horticulture. He has nine years of experience across a variety of specialties including agriculture, agronomy, entomology, and viticulture.
During his early career in Michigan, he worked for Michigan State University, AgroLiquid, and the U.S. Department of Agriculture.
Beginning in July 2018 he joined CropKing, Inc. based out of Lodi, Ohio. His experience with hydroponics, aquaculture, and aquaponics was instrumental to his desire to start Root 42 Harvests with his wife Katie.
Latest Episode
Vertical Farming: Sustainable Food Never Tasted So Good
Vertical farming enables the ability to grow food closer to large population centers and also reduces the “food miles” associated with distribution thus reducing the carbon footprint
Richard Howells | Brand Contributor
May 5, 2021
There’s a lot of good press these days about the potential of vertical farming to help address climate change. The idea is to use hydroponics and other techniques to grow food “soil-lessly” (if that’s a word) in vertically stacked layers.
Vertical farming enables the ability to grow food closer to large population centers and also reduces the “food miles” associated with distribution thus reducing the carbon footprint.
But not so fast.
Mark Korzilius from &ever GmbH – a vertical farming startup with a farm in Kuwait and one coming in Singapore – disagrees with the food miles argument. Here’s why.
Quality first: Iceberg no more!
In a recent interview on the Climate21 podcast with Tom Raftery, Korzilius urges us to “forget about transportation in order to justify vertical farming.” Instead, the focus needs to be on bringing the best product to the consumer. Quality, in this case, means healthy, leafy greens.
“You want to have high nutrients, high in secondary metabolites, everything that is extremely valuable for your body,” said Korzilius.
To most of us, the antithesis of healthy leafy greens is iceberg lettuce. However, as Korzilius explained, it tends to be cut, bagged, and refrigerated for distribution.
“This is where a lot of the carbon footprint comes from,” said Korzilius. “And let’s be honest, iceberg in foul-smelling bags is less than appetizing.”
Instead, &ever follows a “harvest on demand” process. It distributes its leafy greens as potted plants – like you might see with basil or other herbs in your grocery store. Korzilius claims that the customer receives the best-tasting, locally grown leafy greens available, without plastic or refrigeration needed. The chef at the Four Seasons in Kuwait, reportedly, thinks the coriander is the best he’s ever tasted!
Greater control and higher yield, too
&ever’s operations are entirely indoors, where the climate is controlled. This is crucial for successful yields. Growing spinach, for example, is notoriously difficult with vertical farming. But by experimenting with the right seeds, lighting, and temperature, &ever has found the right recipe.
One key advantage is that &ever can grow without pesticides – which, in the end, is just another form of energy. It can also optimize light spectrums to achieve desired results. Many of its crops run on 18 hours of light and six hours of darkness.
The result is higher yields over the course of a year. &ever can grow 18 cycles a year, compared to maybe seven for a traditional greenhouse. And, says Korzilius, it can do it with 85% less water.
Complexity managed
Korzilius also makes the point that tracking all the variables – such as light, temperature, water, production cycles, energy costs, growing recipes, and more – makes for a lot of complexity. SAP is working with &ever to help manage it all. Vertical farming is a high-tech endeavor where control is the key to success. We’re proud to help be part of the solution. Hopefully, this approach to growing food will help minimize carbon output while also delivering delicious food – from (vertical) farm to table.
Listen to the podcast here and be sure to check out the latest research from Oxford Economics on how to “Build a Resilient and Sustainable Supply Chain.”
I've been working in the supply chain management and manufacturing space for over 25 years, and I'm responsible for driving the market direction and positioning of SAP’s Supply Chain Management and IOT solutions. Prior to joining SAP in 2004, I spent 15 years with Marcam Solutions where I was VP of Marketing for the companies Process ERP solutions. I have also implemented ERP and SCM systems at companies such as Nestle, Gillette, Colgate Palmolive, Rohm & Haas, Wyeth, Royal Worcester Spode and Dairy Crest. I hold a Bachelor of Science degree in Computer Science from the University of Mid Glamorgan in the UK. Follow me @howellsrichard
Lead photo: Vertical farm and its employees taking care of plant growth. Plant food production in vertically stacked layers. GETTY
Widespread Investment In CEA Is An Important Piece of The Food Security Puzzle
It has become increasingly clear that traditional agriculture is simply not meeting the food demands of the future
Sky Kurtz, CEO, and Co-Founder, Pure Harvest Smart Farms
There is a commonly quoted statistic estimating that by 2050, we will have nearly 10 billion people on the planet and, in turn, 10 billion hungry mouths to feed. Aside from population factors, the world’s climate is changing in ways human beings have never seen before. Across the globe, our water sources are being diminished and arable landmasses are shrinking. Food security and sustainability is becoming an ever-more pressing issue. There are a number of pioneering companies worldwide working hard to address these critical issues.
The Problem with Traditional Agriculture
It has become increasingly clear that traditional agriculture is simply not meeting the food demands of the future. Food production is heavily driven by significant freshwater consumption and can be both labour intensive and inefficient. Alongside this, changes in climate are negatively impacting yields. This is being witnessed across the board by the food production industry, investors, and governments alike.
The Power of the Consumer
Increased awareness of these issues has led to changes in consumer demands. Consumers have become more discerning about the quality of the products they buy, specifically when it comes to pesticide use, sustainability, freshness, food safety, variety, and brands. They are ever more interested in having knowledge of and creating a relationship with the foods they consume. This is evidenced by the huge organic growth rates of organics over the past 10 years. People care about quality and are voting strongly with their wallets.
Cultural and socio-economic demographics heavily influence what can and should be grown. Some crops such as premium quality leafy greens tend to target more affluent demographics and palates, whereas tomatoes, cucumbers, and a number of other greenhouse vegetables are staples of many diets and can be produced affordably in most places in the world.
The Promise of Controlled-Environment Agriculture
Controlled-Environment Agriculture (CEA) facilitates the growth of sustainable, high-quality produce but not at the expense of the consumer. CEA allows for consistent, high quality production by eliminating the environmental impacts on food production, allowing for more localized production, and reducing, or even eliminating, the use of pesticides.
Reducing Risk
Since early 2020, COVID-19 has woken the world to the risks and fragility of global fresh fruit and vegetable supply chains. Given perishability, the fruit & vegetable market is uniquely vulnerable vs. other crops e.g. the likes of corn, wheat, rice which can be stored & siloed. Controlled-environment agriculture is a solution that addresses these issues facilitating more localized production and supply, offering high output, resource-efficient production capabilities, while meeting the consumer’s changing demands.
In March, the world’s gaze turned to the Suez Canal where a container ship, the Ever Given, became lodged, blocking the canal. On a daily basis, the Suez Canal carries 12% of global trade, around one million barrels of oil and roughly 8% of liquefied natural gas. The cost of the blockage was reportedly $14m-$15m every day!
The Local Promise
The local unique selling point (USP) is now possible pretty much anywhere. Solutions like ours at Pure Harvest Smart Farms have made it possible to affordably produce year-round, even in the harshest climates in the world for example, the UAE, Kuwait, and Malaysia serving Singapore.
Large-scale solutions are necessary for the food to be economic, due to economies of scale in what is ultimately a manufacturing process. Large-scale greenhouses are particularly suitable for dense urban populations, as just 1 or 2 large production sites within 100 – 500 kilometers of the city or town can serve a large group of people affordably.
Unfortunately for more distributed, rural populations, this becomes more challenging. If you scale-down the solutions to hyper-localize, you often lose efficiency (in terms of both capital expenditure/ m2 and operational expenditure/ m2 for production. With more of the world’s population urbanizing, this is another trend that supports widespread investment in CEA as an important piece of the puzzle to serve future food demands.
The Future
The challenge of feeding nearly 10 billion people by 2050 MUST be solved on both the supply side and demand side. From the supply side, adopting technologies that augment output and resource-efficient growing methods. From the demand side, via changing what we consume, reducing waste, and environmental consciousness. Addressing these issues means we can produce more food with less and less resources.
High-tech agriculture presents a multi-decade investment opportunity to contribute to food security, water conservation, economic diversification, and a more sustainable future for all.
Join Sky at the virtual Indoor AgTech Innovation Summit on June 24 and tune into his live panel discussion on ‘Scaling at Speed: Delivering the Promises of a Mission-Led Industry’ at 16.50 EST.
For more information about Pure Harvest Smart Farms, follow them on Facebook, LinkedIn, Instagram and Twitter.
Recent Posts
Indoor AgTech Investment Landscape
Widespread Investment in CEA is an Important Piece of the Food Security Puzzle
Workshop: Food for the Next Frontier
Connecting Retailers, Buyers, and Growers Across Indoor Farming
IGS enters UAE market, signing deal with Madar Farms to enhance food security in the GCC region
Archive
Twitter: @IndoorAgTech
LinkedIn: Indoor AgTech
Hashtag: #IndoorAgTech
AeroFarms CEO Rosenberg Kicks Off Indoor Ag-Con 2021 Keynote Address
“We are thrilled to have an industry leader like David Rosenberg join us as we kick off our return to the live event format,” says Brian Sullivan, co-owner, Indoor Ag-Con LLC
Rosenberg Headlines Full Roster of Keynotes, Panels, Networking & Expo Floor Innovations For In-Person October 4-5, 2021 Edition In Orlando
MAY 6, 2021 -- AeroFarms CEO David Rosenberg will lead the opening morning keynote address for the 8th annual edition of Indoor Ag-Con, scheduled for October 4-5, 2021 at the Hilton Orlando, Florida.
Themed “Growing Your Business,” the premier trade show and conference for the indoor |vertical farming industry will give attendees the opportunity to explore new resources on the expo floor and hear from Rosenberg, other CEOs, thought leaders and industry experts from today’s cutting-edge farms and other innovative companies.
“We are thrilled to have an industry leader like David Rosenberg join us as we kick off our return to the live event format,” says Brian Sullivan, co-owner, Indoor Ag-Con LLC along with other event industry veterans Nancy Hallberg and Kris Sieradzki. “We look forward to gathering with our industry colleagues again and are working hard to bring the best possible combination of networking, education and exhibition opportunities together in Orlando.”
Scheduled for opening morning, October 4, Rosenberg’s address will be held from 8:30 am – 9:20 am. Rosenberg co-founded and leads AeroFarms. AeroFarms has been leading the way for indoor vertical farming and championing transformational innovation for agriculture overall. On a mission to grow the best plants possible for the betterment of humanity, AeroFarms is a Certified B Corp Company with global headquarters in Newark, New Jersey, United States. Named one of the World’s Most Innovative Companies by Fast Company three years in a row and one of TIME's Best Inventions, AeroFarms patented, award-winning indoor vertical farming technology provides the perfect conditions for healthy plants to thrive, taking agriculture to a new level of precision, food safety, and productivity while using up to 95% less water and no pesticides vs. traditional field farming. Grown for flavor first, AeroFarms enables local production to safely grow flavorful baby greens and microgreens all year round.
ROBUST 2021 CONFERENCE SCHEDULE NOW IN DEVELOPMENT
In addition to Rosenberg’s keynote, look for additional announcements coming soon on other CEO keynote presentations planned for the October event. The 2021 conference will also include a full roster of panel discussions, fireside chats and presentations offering a deep dive into three core tracks – Business & Marketing, Science & Technology and Alternative Crops.
In addition to the extensive educational component, attendees will find more new initiatives and show highlights to explore, including:
NEW LOCATION: HILTON ORLANDO – DISCOUNTED HOTEL RATES, TOO
Indoor Ag-Con’s Hilton Orlando venue makes it the perfect opportunity for a business vacation. Centrally located to all major theme parks and attractions, it is just minutes from the eclectic dining scene and entertainment of International Drive. What’s more, the Hilton Orlando resort sits on more than 26 acres of lush landscaping and tropical inspirations making it a true destination of its own. Indoor Ag-Con has arranged for discounted hotel rates for attendees and exhibitors starting as low as $129/night. Complete details are available on the show website.
NEW ASSOCIATION ALLIANCES
Indoor Ag-Con is also forging new alliances with other events, industry associations/groups that will play an integral role in its marketing outreach and conference programming. Look for partnership announcements coming soon.
EXPANDED EXHIBIT FLOOR & NETWORKING OPPORTUNITIES
The Indoor Ag-Con team is working to bring even more resources for farmers/growers to explore across all sectors – everything from IT, energy, AI and lighting solutions to substrates, vertical farming solutions, business services and much more. Attendees and exhibitors alike will also have even more networking opportunities with daily luncheon sessions and receptions on the show floor.
QUICK FACTS:
WHEN: Monday, October 4 – Tuesday, October 5
WHERE: Hilton Orlando, 6001 Destination Pkwy, Orlando, FL 32819
INFO: For information on exhibiting or attending visit www.indoor.ag
ABOUT INDOOR AG-CON LLC
Founded in 2013, Indoor Ag-Con has emerged as the premier trade event for vertical farming | indoor agriculture, the practice of growing crops in indoor systems, using hydroponic, aquaponic and aeroponic techniques. Its events are crop-agnostic and touch all sectors of the business, covering produce, legal cannabis |hemp, alternate protein, and non-food crops. In December 2018, three event industry professionals – Nancy Hallberg, Kris Sieradzki, and Brian Sullivan – acquired Indoor Ag-Con LLC, setting the stage for further expansion of the events globally. More information: https://indoor.ag
“When You Start Growing Upwards, There’s More To Consider Than Verticality”
The Massachusetts-based company manufactures the Agrify Vertical Farming Unit (VFU), a stackable, multi-tiered cultivation chamber designed to increase yields while improving harvest consistency and quality
“Vertical farming technology has really focused on the utilization of the vertical space," says David Kessler, Chief Science Officer at Agrify. "To that end, the environmental management is left to the operator who needs to choose a system and integrate it cohesively; this is a major undertaking. Agrify has a systems-engineered solution to enable vertical growing without needing to figure out all the other obstacles."
The Massachusetts-based company manufactures the Agrify Vertical Farming Unit (VFU), a stackable, multi-tiered cultivation chamber designed to increase yields while improving harvest consistency and quality. Also delivering on improved biosecurity and environmental control over the crop, a single unit has two tiers, and three units can be stacked for six total levels of canopy.
According to David, the transition towards taller vertical farms has made environmental control difficult as the high planting density increases total transpiration and the height of the building results in air temperature stratification. The Agrify VFU is an enclosed cultivation chamber and is monitored and controlled remotely using Agrify’s software. This enclosed climate-controlled design affords operators enhanced environmental management, and is one of the key features distinguishing the Agrify VFU from other vertical racking systems, according to David.
While the VFU was specifically designed for cannabis and hemp production, Agrify first began by producing leafy greens, which David says allowed the company to accrue significant experience in optimizing the environment to increase production.
“When you’re growing leafy greens as opposed to high-value medicinal herbs, the profit margins are quite slim. This form of economics sharpened our swords and forced us to become experts at controlling cultivation environments, with a keen eye towards production costs,” says David.
Smart design for grower safety
Occupational safety is an increasingly important subject in vertical farming, specifically in tall installations relying on manual labor. Scissor lifts are common in the horticultural industry but can be precarious when used in tight spaces at full extension. With vertical farming pushing the boundaries on height, it is important that employees’ safety be prioritized. According to David, Agrify has designed its farming units with employees in mind by incorporating an integrated catwalk into the system’s design and ensuring that its units can be solidly connected.
“When you start growing upwards, moving all of that biomass is cumbersome and can reduce workflow efficiency while increasing risk to employees. Our cultivation chambers are roughly 4’ by 8’ by 9.5’ tall and can be stacked side-by-side with a catwalk in between. This gives employees more safety and flexibility to work standing or sitting,” says David.
Automation in the Agrify VFU
According to David, the Agrify VFU is automated to control irrigation, fertigation, sanitation processes, lighting, humidity control, etc. The VFU control system also allows growers to collect roughly 100 data points per chamber per hour and a minimum of 850,000 data points per year. Features in the software then allow the grower to run daily analyses both within and between chambers. David explains that having enclosed chambers also facilitate this data collection and use as growers can implement different growing conditions in different chambers then compare the resulting outcomes to determine the best production conditions.
Moving forward, Agrify is looking to integrate cameras, artificial intelligence and machine learning into its systems to enable the consistent recreation of precise environmental conditions and proactive crop management.
“We believe that the future will not necessarily be in autonomous production but in computer-aided production. Machine vision will allow 24/7 crop monitoring rather than the typical weekly pest scouting, as an example. With our software, we’re capturing the data as well as providing the tools to analyze it and act on it.
For more information:
David Kessler, CSO
Agrify Corp.
David.kessler@agrify.com
www.agrify.com
23 Apr 2021
Author: Rebekka Boekhout
© VerticalFarmDaily.com
May 18th, 9 am EST - Webinar On How To Invest In CEA With Confidence
Agritecture is hosting a series of webinars, starting with How to invest in CEA with confidence
Agritecture is hosting a series of webinars, starting with How to invest in CEA with confidence. The CEA sector is heating up and is expected to grow 5x over the next 10 years. Investment in CEA has surpassed $2.0B across North America and Europe. Join Henry Gordon-Smith, Founder & CEO at Agritecture, for this 1-hour live webinar to learn more about how to invest confidently in the CEA industry.
How To invest In Controlled
Environment Agriculture With
Confidence
May 18 - 9 am EST
The lineup of speakers include:
Louisa Burwood Taylor, Head of Media & Research at AgFunder
Robert Glanville, Senior Advisor at REG Consulting LLC
Andrew Carter, Co-Founder & CEO at Smallhold
Darren Thompson, CFO at Bowery Farming
Djavid Amidi Abraham, Director Of Consulting at Agritecture
Click Here To Register!
For more information, you can check out our events listing here.
Agritecture
www.agritecture.com
Taking Indoor Farming Operations To New Heights
Conveyor systems technology can help indoor farming operations grow to new heights while improving productivity, efficiency and ergonomics, according to Ultimation Industries LLC, a leader in conveyor technology and automation for over 30 years
Conveyor Systems Technology From Ultimation Industries
Conveyor systems technology can help indoor farming operations grow to new heights while improving productivity, efficiency and ergonomics, according to Ultimation Industries LLC, a leader in conveyor technology and automation for over 30 years.
“Harnessing unused vertical space through the use of motorized and overhead conveyors helps indoor farmers maximize their footprint while achieving greater efficiencies in food production and improved ergonomics,” said Richard Canny, president of Ultimation Industries.
Customized and automated
Ultimation is a provider of customized conveyor and automation solutions for indoor agriculture. They design and build systems for vertical farms of all sizes, including a major system for a West Coast-based vertical farming system which is among the world’s largest.
In a typical indoor agriculture facility, workers move through the growing area to plant, monitor and harvest crops. Multi-tier operations may use time-consuming and potentially dangerous lifts to take employees up and down as they perform their daily tasks. Conveyor technology can move plants through automated systems as they grow, bringing them down to the operator level when needed for more efficient, and ergonomically friendly, handling.
Multiple choice
The conveyors and industrial automation equipment used in vertical farming include many of the traditional conveyor types such as gravity roller, belt, and skate wheel or flow rail conveyors. These conveyors are among the most versatile because they help reduce the manual labor of carrying items by hand.
Larger systems use vertical elevators or Power and Free conveyors. Power and Free conveyors are the ultimate in space and volume optimization for vertical farming systems as they enable tight concentration of product in some areas while also enabling separation of the products for movement to processing areas.
Reducing costs
More recently, the technology used in larger vertical farming systems is including motorized and overhead conveyors. These systems take advantage of unused vertical space above a working area and bring plants down to an operator level when needed.
“Using robotics and conveyors has been shown to help vertical farms maximize their growing operations and reduce costs. We believe that indoor farming systems are best optimized through a balanced use of low-cost material handling systems for slow-growing areas. They are complemented by more sophisticated conveyors and other devices for faster moving material handling tasks,” said Canny.
Ultimation’s indoor agriculture solutions range from simple flow rail systems up to more comprehensive systems for larger indoor vertical farming facilities. The company's systems meet food-safe requirements for lubricants, oils, and greases.
“As indoor farmers work to achieve greater efficiencies in food production, conveyor systems technology is likely to be part of any economically viable and scalable solution,” said Canny.
For more information:
Kali Cresent, Sales, and Marketing Manager
Ultimation Industries, LLC
kcresent@ultimation.net
+1 586-771-1881
www.ultimation.net
9 Apr 2021
Can Vertical Farming Be A Viable Method Of Controlled Environment Production?
Fifth Season is using its fully integrated, automated operating system to crack the economics code for vertical farming with the potential to integrate with greenhouse operations.
Fifth Season is using its fully integrated, automated operating system to crack the economics code for vertical farming with the potential to integrate with greenhouse operations.
To say that controlled environment agriculture is drawing a lot of interest and dollars from the investment world would be an understatement. Austin Webb, co-founder, and CEO at Fifth Season, a vertical farm operation in Pittsburgh, Pa., estimates that over $3 billion has been invested in the CEA industry during the last four years alone, excluding debt and merger and accusations activities for greenhouse operations.
“For indoor ag overall, including both vertical farming and greenhouse, about half that equity investment has been for vertical farming,” Webb said. “There were a lot of dollars that came into this space early on. The unfortunate piece to that is there was a lot of overhype and false promises made in this space. A lot of those dollars came in too early for some of these companies and overall were wasted.
“There has been an industry-wide struggle to make the economics of vertical farming work. All of these companies talk about what they are going to do in the future, but the issue is they have negative unit economics. They lose money for every pound of produce they sell. In many cases, they will say that they will make the economics work in the future, but only after they build more production facilities.”
Webb said negative economics has had a major impact on the vertical farm industry.
“The false promises and the negative economics have held the industry back, overshadowed companies that are building substantial vertical farming solutions that work and pushed additional dollars to incremental greenhouse solutions,” he said. “Moving forward we will continue to see more dollars come into CEA and into vertical farming specifically. This will include public markets and SPAC (special purpose acquisition company) activity.
“Overall, there will be more money invested in CEA. This will include investments that are mediocre. The important element will be investments made into tech platforms designed for scalability and repeatability. This is the only way that volume requirements for wholesale buyers can be met to unlock indoor ag as a material participant in overall market share.”
Need for a mindset change
Even with additional investment dollars coming into the CEA industry, Webb doesn’t expect it to be enough to make traditional vertical farming companies a success.
“Unfortunately, even though significant dollars have been invested in vertical farming, much of it has been wasted,” he said. “The incremental mindset a lot of people in this industry have had is to simply convert farming from outdoors to indoors. In doing so, all they inevitably did was bring people from outdoors and put them indoors. The mindset was to create a growing platform to produce leafy greens and then sprinkle on some technology. The technology was sort of an afterthought.
“There were a lot of companies throwing out buzz words without having actual practicality in regards to robotics, artificial intelligence, and automation. All the money that has been invested has been going toward continued R&D, but at a level which has companies creating technical debt.”
The thing that has helped Fifth Season avoid the technology issues other vertical farms have encountered is the way the company developed and designed its operating system.
Fifth Season has created a manufacturing platform that is fully automated from end-to-end including growing, processing, and packaging.
“We had a completely different mindset,” Webb said. “We took a blank slate to really design this holistically from beginning to end. We think of this as manufacturing a living organism. As a result, we’ve created an IoT–connected smart manufacturing platform that is an industry-first, industry-only, fully end-to-end automated platform—not just growing, but also processing and packaging. There are other operations that have automation here or there, but nothing else truly automated from beginning to end.
“More importantly, we have integrated the system so it is completely run by our proprietary software platform. We don’t have a bunch of automated equipment that runs on its own controls. Instead, we have a combination of our own proprietary tech and some off-the-shelf equipment such as conveyors. All of the electromechanical systems sit within our software skin and are run by our in-house built firmware and software brain. We have a pathfinding algorithm where when we receive an order from a customer, our system is sequencing out the schedule completely on a daily, weekly and monthly basis.”
Fifth Season worked with Hort Americas and GE Current, a Daintree company, to develop its automated grow room.
“Partnering together on our solution helped us validate that there was a path for our vertical farm to have favorable economics,” Webb said. “Being able to bounce ideas and technologies off of the Hort Americas team allowed us to push the boundaries of innovative thinking in terms of our approach and how we wanted to use technology to solve the complex issues that are limiting vertical farming. We were able to think differently, knowing we had the Hort Americas team as both a check and enabler, which ultimately created a successful collaboration.”
Partnering with Hort Americas also gave Fifth Season the opportunity to incorporate Current’s LED technology into its unique growing platform.
“We did a lot of things differently with our proprietary design and in so doing there were certain things that we couldn’t necessarily handle ourselves,” Webb said. “Working with Hort Americas and Current enabled us to move very quickly while making smart, capital-efficient decisions, as opposed to designing the LEDs ourselves or over-paying for unnecessary functionality.
“We worked with Current in key areas that made big differences related to the integration of our design. We leveraged Current’s significant expertise in regards to light spectrum strategy and the corresponding impact on plant science and quality.”
Creating an economic advantage
Webb said Fifth Season’s unique platform has allowed the company to unlock positive unit economics where it can offer a market price that works for wholesalers and consumers.
“We have been able to make money per pound and make vertical farming economically sustainable,” he said. “Our platform has enabled us to make a stepwise function change in labor costs and efficiency and in energy costs. For labor, we have 2x+ less labor costs than other companies in this space. We also measure and track energy down to every individual bot. We have over 60 bots that are all integrated into one robotics system. We measure and track how to optimize energy utilization to all of those bots.
Fifth Season’s unique operating platform has allowed the company to unlock positive unit economics enabling it to offer a market price that works for wholesalers and consumers.
“Finally we have made a stepwise function change in pounds to fixed costs ratio. That’s because we have been able to remove large aisle ways and manual inefficient storage and retrieval. We have created a patent-pending solution around our automated storage retrieval, which ties to the rest of our system. In the end, we are able to remove all human involvement from the grow room and are able to achieve 2x+ the growing capacity.”
Another advantage of the platform Fifth Season has created is the need for raising additional capital compared to some other vertical farms.
“We have raised just over $40 million to date,” Webb said. “There are multiple vertical farm companies that have raised $200 to $400 million+. The reason we haven’t had to raise that much capital is because of our mindset about engineering, grow science, and operations in the same R&D pipeline. It has allowed us to catch up and to surpass the rest of the industry in a fraction of the time with a fraction of the capital.
“As we move forward and look at raising additional capital, what’s different is we don’t have to use our equity capital to build more farms for all the hard costs associated with real estate, equipment and building facilities. We can if we want to and if it makes sense for our equity partners, but it is not required. We have been able to unlock positive unit economics which means we have been able to unlock non-dilutive capital to build additional facilities more capital efficiently. Overall, we have built a scalable, repeatable platform, which is what investors need to see.”
What’s ahead for vertical farming?
Webb said there will be a few select companies that have approached indoor ag and vertical farming with a solution that works and will thrive. There will also be a number of companies that are large and excessive that will eventually disappear.
“There will be some consolidation in this industry,” he said. “Some companies won’t be consolidated because they don’t have a tech platform that is investable in terms of the synergies of wanting to acquire that footprint. Consolidation will be selective in some cases.
“There is a lot of production regardless of footprint and money going into leafy greens. There are companies in this space that have no intention of doing anything different than that. I think that focus will run them into a leafy greens race to the bottom. It all comes down to no sustainable competitive advantage.”
Webb also sees the potential for synergy between vertical farms and greenhouses.
“We have built a scalable system that allows us to do a number of crops and then do asset management across different applications,” he said. “We also have the technology that is applicable from an asset management production operations standpoint that works for greenhouses as well.
“We will be able to unlock with this technology what many others won’t necessarily be able to do. Fifth Season will not only be a company that has vertical farm and greenhouse footprints but also is one that uses those footprints in a collaborative way for specific crops. For example, a crop could be in a vertical farm environment for part of its life and in a greenhouse for another part of its life. This will create cross-category and cross footprint combinations.”
For more: Fifth Season, (412) 899-2268; hello@fifthseasonfresh.com; https://www.fifthseasonfresh.com/
Lead photo: Austin Webb, co-founder, and CEO at Fifth Season, said even though significant dollars have been invested in vertical farming, much of it has been wasted. Photos courtesy of Fifth Season
This article is property of Urban Ag News and was written by David Kuack, a freelance technical writer in Fort Worth, Texas.
Oishii Sees Itself As ‘The Tesla of Vertical Farming.’ Here’s How It’s Cracking CEA Strawberries
“Strawberries are the hardest crop to grow in a vertical system and it’s been every vertical farmer’s dream to grow them. Conquering strawberries allows us to grow into other crops very quickly.”
March 31, 2021
Indoor farming is best known for leafy greens and micro-herbs. But New York’s Oishii is hoping to blaze a new trail and sweeten up the segment.
“A lot of people call strawberries the holy grail of vertical farming,” Oishii founder Hiroki Koga tells AFN. “Strawberries are the hardest crop to grow in a vertical system and it’s been every vertical farmer’s dream to grow them. Conquering strawberries allows us to grow into other crops very quickly.”
The startup announced a $50 million funding round this month led by Mirai Creation Fund, part of Tokyo-based SPARX Group. Additional investors included Sony Innovation Fund — the corporate venture arm of Japanese tech giant Sony — Tokyo-based AI company PKSHA Technology, and San Francisco-based VC Social Starts.
“We’ve had multiple offers from different funds but we ultimately decided to go with SPARX because they have a very strategically aligned mandate. They’re backed by Toyota, one of the largest manufacturing companies in the world [and] vertical farming is the intersection of agriculture and manufacturing,” Koga says.
Although it may seem odd for Toyota to be interested in agrifood tech, the carmaker is working on its Woven City project located at the base of Japan’s Mount Fuji. It’s a so-called “living laboratory” where researchers live and work full-time to imagine what future cities may look like through technological innovation.
Koga is no stranger to controlled environment ag (CEA). Six years ago, he was working as a CEA consultant in Japan, helping large corporations enter the space. While Koga views Japan as the birthplace of vertical farming, he moved to the US in 2015 – around the time that the method was becoming popular in the country.
Alongside the allure of being the first to crack indoor strawberry cultivation, Koga sees the fruit as a way to address what he calls the “unit economics problem” in indoor farming. He sees strawberries as providing a very strong revenue and profit model, as well as a crop that can further “democratize” vertical farming.
“In order to democratize it, I wanted to start with something that’s truly impactful — not products that people will buy because they are sustainable — [but] something that is superior compared to what is on the market, and that would completely change people’s experience,” Koga says.
He leveraged his personal network in Japan to collaborate with farmers and research institutions on the details of indoor strawberry cultivation – from seeding all the way to harvesting. It took “countless” iterations to get the formula right, he says.
“There’s probably 20 or 30 different things that you can tweak in a given cycle of the plant. So, let’s say there are five or six different stages of the plant life cycle – if you multiply all of those, there are millions of different combinations,” he explains.
“It’s a matter of tweaking those on a daily basis to figure out what the perfect mix is.”
However, this know-how isn’t what Koga considers to be Oishii’s “secret sauce.” Rather, that’s the bees that the startup’s using handle pollination.
While Koga won’t spill the ‘bees’ about how all this works in Oishii’s context, he claims to have found a way to replicate a natural environment within an indoor vertical farm that convinces the critters they’re outside.
“They live in harmony with our farmers and robots,” is all Koga will add.
The Tesla of vertical farming
With the initial R&D under its belt, Oishii is now turning its focus to consistency and quality of the product. Its current New Jersey facility spans a few tennis courts, Koga says; but its next one will be the size of an American football field. It currently sells direct-to-consumer through its website, and through traditional retail channels like supermarkets.
But its strawberries may be out of some consumers’ grocery budgets, retailing between $15 and $50 per pack depending on the size and the number of fruits. This price point puts Oishii’s berries in the luxury food category – for now, at least.
“If you think about how Tesla started with a Roadster or Nissan started with the LEAF, we like to think we are in the Roadster camp,” Koga says.
“Our current Omakase berry is our Roadster right now, but we already have developed multiple strawberry cultivars that we can produce much more cost-efficiently. Our Model S and Model 3 will be on the market soon,” he says, referring to the latter-day models now being sold by Elon Musk’s company.
Another US vertical farming startup, Plenty, is also trying to solve the strawberry equation. It recently added Driscoll’s to its list of backers and is collaborating with the major berry producer on indoor strawberry cultivation.
Koga welcomes competition in the space, particularly if it means branching beyond leafy greens.
“It’s generally a good thing that people are following in our footsteps and expanding out of the leafy green space. The more berries the better,” he says.
“Ten years ago, we only had Tesla, maybe a few other companies. But Tesla was the one who proved that it can be done, and now there are dozens and dozens of electric car manufacturers. [The electric car] become much more widely available.”
Expanding Controlled Environment Agriculture Beyond 'The Big 4'
Greenhouses, vertical farms, and hybrid systems (collectively known as controlled environment agriculture or CEA) continue to attract investment at a much greater scale than in previous decades
By PETER TASGAL
March 29, 2021
Greenhouses, vertical farms, and hybrid systems (collectively known as controlled environment agriculture or CEA) continue to attract investment at a much greater scale than in previous decades. In each of the past five years, there have been multiple nine-figure capital raises. Capital has been deployed across farm types:
Large-scale greenhouses (e.g., AppHarvest, Mastronardi Produce),
Regional greenhouses (e.g., Gotham Greens, Bright Farms),
Localized vertical farms (e.g., InFarm – Berlin, Kalera).
Sources of funding have expanded from almost exclusively highly-specialized private equity investors to include public equity, mezzanine debt and even commercial banks. Within these funding sources, the breadth of investors has expanded beyond agriculture-focused investors to more mainstream investors, especially those with an interest in Environmental, Social and Corporate Governance (ESG) investing.
More from The Packer: Deep dive on the economics of greenhouse growing
Despite all of the investment, the vast majority of produce grown in CEA’s across North America consists of tomatoes, cucumbers, peppers, and lettuce, and leafy greens (“The Big 4”). Most of the lettuce and leafy greens are coming from CEA’s in the U.S. In Canada, The Ontario Greenhouse Vegetable Growers include 220 members producing tomatoes, cucumbers, and peppers on over 3,000 acres of greenhouse.
In my opinion, the next leap for the industry will be expanding the breadth of products. Specifically, focusing on products the taste of which is highly important to the consumer. A strawberry, for example, is a more important purchasing decision to the average consumer compared to lettuce. Lettuce is much more likely to be eaten as part of a salad along with a variety of other ingredients. Today, you can buy at mainstream retail locations a greenhouse-grown strawberry likely grown by Mucci Farms in Ontario or Mastronardi’s Green Empire Farms in New York.
Consumer demand will continue to drive product expansion. Meeting that demand will be possible through further investment in the CEA space. Although investment has been growing, it has not met the levels of other industries where many billions of dollars have been invested on an annual basis. Investment levels in CEA are likely to become far greater over the near future as some of the largest investors in the world are focused on investments that meet and exceed ESG standards.
More from The Packer: On tour with AeroFarms
Efficient vertical farms and greenhouses meet and exceed ESG standards. The farms are closed-loop systems where everything that goes into the farm is contained and recycled. Additionally, as the environment is fully controlled, only the precise amounts of inputs are added so as to limit excess waste. Lastly, a controlled environment allows for plants to grow without chemicals and pesticides.
Combining consumers’ desire for more locally-grown produce throughout all seasons of the year with increased investor appetite should drive great growth across the industry for years to come. I believe the biggest leap will be new and exciting products coming from indoor farms. This will all be enhanced with incremental improvements in product taste, farm efficiency, and additional varieties within The Big 4 and other products to come.
Peter Tasgal is a Boston-area food agriculture consultant focused on controlled environment agriculture.
Vertical Farming Startup Oishii Raises $50m In Series A Funding
“We aim to be the largest strawberry producer in the world, and this capital allows us to bring the best-tasting, healthiest berry to everyone.”
By Sian Yates
03/11/2021
Oishii, a vertical farming startup based in New Jersey, has raised $50 million during a Series A funding round led by Sparx Group’s Mirai Creation Fund II.
The funds will enable Oishii to open vertical strawberry farms in new markets, expand its flagship farm outside of Manhattan, and accelerate its investment in R&D.
“Our mission is to change the way we grow food. We set out to deliver exceptionally delicious and sustainable produce,” said Oishii CEO Hiroki Koga. “We started with the strawberry – a fruit that routinely tops the dirty dozen of most pesticide-riddled crops – as it has long been considered the ‘holy grail’ of vertical farming.”
“We aim to be the largest strawberry producer in the world, and this capital allows us to bring the best-tasting, healthiest berry to everyone. From there, we’ll quickly expand into new fruits and produce,” he added.
Oishii is already known for its innovative farming techniques that have enabled the company to “perfect the strawberry,” while its proprietary and first-of-its-kind pollination method is conducted naturally with bees.
The company’s vertical farms feature zero pesticides and produce ripe fruit all year round, using less water and land than traditional agricultural methods.
“Oishii is the farm of the future,” said Sparx Group president and Group CEO Shuhei Abe. “The cultivation and pollination techniques the company has developed set them well apart from the industry, positioning Oishii to quickly revolutionise agriculture as we know it.”
The company has raised a total of $55 million since its founding in 2016.