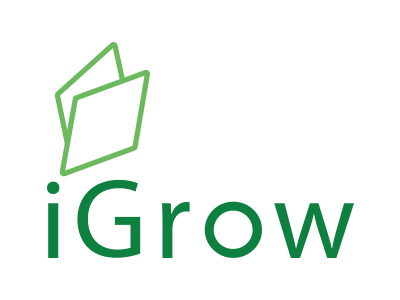
Welcome to iGrow News, Your Source for the World of Indoor Vertical Farming
Design Firms Eye Efficiency, Speed To Market And Turnkey Design Solutions
Many of these transactions have included product and technology firms, but there is one acquisition, in particular, that is going to have quite a significant impact not only on the cannabis industry but on the larger indoor Controlled Environment Agriculture sector
By Andrea Di Pastena
July 13, 2021
Recently, consolidation within the cannabis industry has been seen through several mergers and acquisitions. Many of these transactions have included product and technology firms, but there is one acquisition, in particular, that is going to have quite a significant impact not only on the cannabis industry but on the larger indoor Controlled Environment Agriculture sector.
urban-gro has agreed to acquire the architecture firm MJ12 Design Studio in a move that makes urban-gro a one-stop company supporting growers with full-building turnkey design solutions including architecture, engineering, and cultivation systems integration. “Our role as an Architecture and Engineering firm truly sets us apart from the rest of the industry,” says Sam Andras, AIA, senior principal and partner at MJ12 Design Studio. “This acquisition has created a company that truly integrates turnkey design solutions under one roof.”
MJ12 Started Early in Cannabis Facility Design
The story of MJ12 Design Studio goes back to the very inception of the cannabis industry. “MJ12 Design Studio’s parent company of 2WR,” Andras recounts. “For 20 years, we had offices in the deep south, and we were working on federal projects. Then, we saw a tremendous opportunity with the legalization of cannabis in Colorado. So, we had to come up with a different brand for our cannabis design services. If you dig back in history, President Harry Truman had a group whose mission was to investigate alien activity. This secret group was called The Majestic 12, and the acronym was MJ12. So, since we were going to be a ‘secret’ architectural firm, MJ12 was the perfect name. From that moment on, we have designed over 100 cultivation facilities, with projects across North America and beyond - including Gibraltar, North Macedonia, and New Zealand.”
Read the rest of the article here
For more information:
urban-gro
720-390-3880
marketing@urban-gro.com
urban-gro.com
“When You Start Growing Upwards, There’s More To Consider Than Verticality”
The Massachusetts-based company manufactures the Agrify Vertical Farming Unit (VFU), a stackable, multi-tiered cultivation chamber designed to increase yields while improving harvest consistency and quality
“Vertical farming technology has really focused on the utilization of the vertical space," says David Kessler, Chief Science Officer at Agrify. "To that end, the environmental management is left to the operator who needs to choose a system and integrate it cohesively; this is a major undertaking. Agrify has a systems-engineered solution to enable vertical growing without needing to figure out all the other obstacles."
The Massachusetts-based company manufactures the Agrify Vertical Farming Unit (VFU), a stackable, multi-tiered cultivation chamber designed to increase yields while improving harvest consistency and quality. Also delivering on improved biosecurity and environmental control over the crop, a single unit has two tiers, and three units can be stacked for six total levels of canopy.
According to David, the transition towards taller vertical farms has made environmental control difficult as the high planting density increases total transpiration and the height of the building results in air temperature stratification. The Agrify VFU is an enclosed cultivation chamber and is monitored and controlled remotely using Agrify’s software. This enclosed climate-controlled design affords operators enhanced environmental management, and is one of the key features distinguishing the Agrify VFU from other vertical racking systems, according to David.
While the VFU was specifically designed for cannabis and hemp production, Agrify first began by producing leafy greens, which David says allowed the company to accrue significant experience in optimizing the environment to increase production.
“When you’re growing leafy greens as opposed to high-value medicinal herbs, the profit margins are quite slim. This form of economics sharpened our swords and forced us to become experts at controlling cultivation environments, with a keen eye towards production costs,” says David.
Smart design for grower safety
Occupational safety is an increasingly important subject in vertical farming, specifically in tall installations relying on manual labor. Scissor lifts are common in the horticultural industry but can be precarious when used in tight spaces at full extension. With vertical farming pushing the boundaries on height, it is important that employees’ safety be prioritized. According to David, Agrify has designed its farming units with employees in mind by incorporating an integrated catwalk into the system’s design and ensuring that its units can be solidly connected.
“When you start growing upwards, moving all of that biomass is cumbersome and can reduce workflow efficiency while increasing risk to employees. Our cultivation chambers are roughly 4’ by 8’ by 9.5’ tall and can be stacked side-by-side with a catwalk in between. This gives employees more safety and flexibility to work standing or sitting,” says David.
Automation in the Agrify VFU
According to David, the Agrify VFU is automated to control irrigation, fertigation, sanitation processes, lighting, humidity control, etc. The VFU control system also allows growers to collect roughly 100 data points per chamber per hour and a minimum of 850,000 data points per year. Features in the software then allow the grower to run daily analyses both within and between chambers. David explains that having enclosed chambers also facilitate this data collection and use as growers can implement different growing conditions in different chambers then compare the resulting outcomes to determine the best production conditions.
Moving forward, Agrify is looking to integrate cameras, artificial intelligence and machine learning into its systems to enable the consistent recreation of precise environmental conditions and proactive crop management.
“We believe that the future will not necessarily be in autonomous production but in computer-aided production. Machine vision will allow 24/7 crop monitoring rather than the typical weekly pest scouting, as an example. With our software, we’re capturing the data as well as providing the tools to analyze it and act on it.
For more information:
David Kessler, CSO
Agrify Corp.
David.kessler@agrify.com
www.agrify.com
23 Apr 2021
Author: Rebekka Boekhout
© VerticalFarmDaily.com
Affinor Growers To Enter Aruban Market With Circular Farming Systems
Affinor Growers Inc. is nearly ready to plant its first seedlings and begin showcasing its vision of sustainable agriculture for a ten-year period
Green Cash Crop Funds
Leafy Greens Growth
Affinor Growers Inc. is nearly ready to plant its first seedlings and begin showcasing its vision of sustainable agriculture for a ten-year period. The company recently announced its lease agreement for a 15,000-square foot greenhouse.
The land is located in Abbotsford, British Columbia, and is reportedly divided between a 15,000-square foot greenhouse operation and a 12,000-square foot composting facility. With the Canadian spring beginning its transition into summer, Affinor Growers Inc. is looking forward to planting its first crops in the greenhouse by July 2021.
The new greenhouse site
Cannabis cuts profit margins differences
According to CEO and founder Nick Brusatore, the greenhouse will use vertical production techniques to maximize space efficiency in the greenhouse. The company currently plans to grow strawberries under one greenhouse bay, romaine lettuce under another bay, and eventually have a craft cannabis operation in another section. Affinor Growers is currently building out and getting ready to submit its craft cannabis license application to Health Canada but is content to begin with food crops for the time being. As Nick explains, his main goal in growing cannabis is to showcase sustainable production techniques and to increase the profitability of the entire system.
“We want to sustain our strawberry and romaine production, but food crops typically have lower margins. The high price of cannabis will allow us to grow even more strawberries and romaine lettuce by washing out the differences between profit margins. That way, we can deliver our products to the market at a good price and high quality.”
Greenhouse features
Continuing in its systems approach to agriculture, Affinor Growers Inc. also plans to reduce waste by composting organic materials and remediating its growing material. Altogether, the greenhouse and composting operation will allow the company to pursue its vision of high-quality, low-cost food production in a circular manner.
The greenhouse will also be completely automated, allowing the company to reduce labor costs by eliminating the need to move plants and materials manually. As Nick explains, the time between removing a crop from the greenhouse and replacing it with a new one takes a few minutes, as the plants are cut in the cooler and the soil replanted with new seedlings before being sent back into the greenhouse.
Vertically stacked cannabis
Entering Aruban market
While the 15,000-square foot greenhouse is located in British Columbia, the company is planning to take its vision into new markets and will begin with Aruba, according to Nick.
Nick explained that after having worked with the people and incorporating Vertical Designs Aruba VBA along with understanding the Country and Government needs after six years learning what is needed to mass-produce plant tissue, he has become attached to the country and has seen the need for circular farming systems. Affinor Growers Inc. will reportedly be building a farm near San Nicholas, in the southern region of Aruba.
Affinor Growers Inc. wants to work with Arubans to provide good jobs and economic benefits to the area. If all goes as Nick hopes, this project and others like it could increase tourism on Aruba’s southern side. Nick also explained that cannabis production is a possibility pending success in licensing application once the country’s laws and licensing are complete, this strategic move that will benefit agricultural capabilities in the long-term through the construction of infrastructure.
“We figured we would grow cannabis because the demand s high, so we can easily build-out. As the cannabis demand settles down globally over the next 5-10 years, the industry will have paid for massive food infrastructure without the government or taxpayers paying for it. In Aruba, we’re going to take a lot of that profit to create food infrastructure,” says Nick.
For more information:
Nick Brusatore, Founder and CEO
Affinor Growers
Publication date: Thu 22 Apr 2021
Author: Rebekka Boekhout
© VerticalFarmDaily.com
Agrify (AGFY) Enters Into Binding Letter of Intent For An Additional $3M Contract With Hannah Industries For Facility Build-Out And Installation of 179 Vertical Farming Units
Agrify Corporation (NasdaqCM: AGFY) (“Agrify” or the “Company”), a developer of highly advanced and proprietary precision hardware and software grow solutions for the indoor agriculture marketplace
February 19, 2021
Agrify Corporation (NasdaqCM: AGFY) (“Agrify” or the “Company”), a developer of highly advanced and proprietary precision hardware and software grow solutions for the indoor agriculture marketplace, today announced it has entered into a binding letter of intent, which sets forth the principal terms of a contract currently being negotiated with Hannah Industries (“Hannah”), a leading Tier 2 producer and distributor of cannabis in Washington State, for the design and build-out of an approximately 30,000 square foot facility. The contract will include facility build-out services in total of $3 million and annual SaaS revenue of approximately $285,000. Such payments will be financed by Agrify, are to be made monthly over a two-year period commencing upon the first successful harvest, and will reflect an APR of 25%. The agreement for this design and build-out will be in addition to the previously purchased 179 Vertical Farming Units (“VFUs”) and is part of Agrify’s turnkey solution to its customers. The work is expected to be completed by early Q4 2021, subject to entry into a definitive agreement.
Small-cap stocks have been on the upswing since March—but not all small caps are created equal. For the long term, small caps that have grown their dividends consistently may be a more attractive investment opportunity. Find out why. Read More
“We are especially proud to be selected by Hannah Industries, a leading producer and distributor in the State of Washington. Their decision to upgrade from the traditional grow methodology to Agrify’s integrated vertical farming solution is the strongest testimony of our joint belief that Agrify’s solution will help Hannah Industries to produce the highest quality cannabis flowers consistently. We’re thrilled to have been chosen again by Hannah for the facility design, construction, and installation of our proprietary and advanced grow solutions,” said Raymond Chang, Chief Executive Officer of Agrify. “Agrify VFUs and Agrify Insights software should also help Hannah realize increased levels of automation, control, transparency, and repeatability. We expect this will be a great win for our team, and we look forward to working with Hannah to successfully implement it.”
“The current market is very competitive, and consumers have lots of options. One of the most important things to our business is being able to deliver a consistent, high-quality supply of cannabis to our retail partners,” said Jason Whitney, Chief Executive Officer of Hannah. “The Agrify grow system and software allow us to have an extremely high level of control over the grow, helping us meet our customers’ needs. In addition, the information Agrify Insights software provides will allow our team to make real-time decisions on supply chain management based on feedback from our customers. This evolution in the industry is one of the reasons we are extremely pleased to be implementing the Agrify solution for our cultivation facility.”
WEBINAR: Learning Transfer From The Cannabis Industry To The Vertical Farming Industry
We are thrilled to organize a Webinar focusing on the technical aspects and experience of these experts
MARCH 3, 2021
AT 16:00 Central European Time
ONLINE
Register
Critical Lessons: Learning Transfer from the Cannabis Industry to the Vertical Farming Industry
We are thrilled to organize a Webinar focusing on the technical aspects and experience of these experts:
Our speaker Emil Breza is Co-Founder, President, and CEO of AgricUltra™ Advancements Inc. Bringing together his interdisciplinary technical expertise and many years of product development and innovation he introduced to AgricUltra a PlantFirst™ design approach to create one of the industries most advanced Turn-Key Vertical solutions for Controlled Environment Agriculture applications.
Prior to founding AgricUltra, Emil had years of experience in Process Engineering, the Automotive Industry, Professional consulting, and the Military where he honed his ability to identify the root cause of problems and develop solutions that are outside the box.
Our speaker Buck Young is co-founder and Executive Director at CannTx Life Sciences Inc, a Canadian LP focused on leveraging innovation and science to produce exceptional cannabis products and provide solutions to the industry. He is also the CEO of Saed Technologies Ltd, which develops and licenses technologies related to plant propagation, a Board member of Mary Agrotechnologies, and sits on the management committee for a cannabis botanical drug strategic alliance with Devonian Health Group. He is passionate about translating research findings into commercial outcomes, advancing the adoption of precision agriculture, and understanding nature’s pharmacopeia.
Emil Breza
Buck Young
Dr. Joel Cuello
Please register here, there is only a limited number of tickets available.
Register
TAGS: ADVANTAGES OF VERTICAL FARMING AFRICA AGRITECHNICA AGROSPACE AVF WORKSHOP BRAINSTORM THE ECOSYSTEM DESIGNING THE ECOSYSTEM DLG ECOLOGICALLY ECONOMICALLY EVENT FOOD SAFETY FOOD SECURITY FOOD SYSTEM FOODSYSTEM FOOD TRACEABILITY FRAUNHOFER FRAUNHOFER IME HOW VERTICAL FARMING WORKS HUNGER INFARM INFOGRAPHICS INSPIRATIONAL ITALY MOTIVATION OPPORTUNITIES OPPPORTUNITIES PARTNER EVENT REGIONAL DEVELOPMENT RETAIL ROME RZ SOCIALLY SOUTHAFRICA STORYTELLING SUBMISSION SUMMIT SUPERMARKET SUPPLYCHAIN SUSTAINABILITY THE SIX SESSIONS URBAN AG VERTICAL FARMING WORKSHOP WORKSHOP WARM UP
Emerging Needs In Vertical Farming And Cannabis Cultivation
The development of vertical farming will continue considerably in the coming years, according to Montel Inc.. With the company’s Vertical Farming Systems Montel expects a very high volume of new projects in both food and cannabis. “COVID-19 has only increased the need to grow locally and inside cities”, says Yves Bélanger, VP Sales Vertical Farming Market International
15 January 2021
Jacco Strating
Yves Bélanger of Montel Inc. believes that COVID-19 has only increased the need to grow locally and inside cities. He speaks about why the development of vertical farming will continue considerably in the coming years.
The development of vertical farming will continue considerably in the coming years, according to Montel Inc.. With the company’s Vertical Farming Systems Montel expects a very high volume of new projects in both food and cannabis. “COVID-19 has only increased the need to grow locally and inside cities”, says Yves Bélanger, VP Sales Vertical Farming Market International.
Established in 1924, Montel pioneered high-density mobile storage systems providing cost-efficient storage solutions using less space and established a global network of authorized Montel distributors. Montel's achievements include some of the most prestigious projects in North America and around the world. “Prior to becoming North America's leading manufacturer of mobile systems, we had acquired nearly 40 years' experience in the electrical industry, including extensive involvement in the construction of generating stations and power grids for major world-leading hydroelectricity plants. This explains our expertise and the exceptional quality of our electrical mobile systems”, says Bélanger.
Inventive ways to feed the world
Before the crisis, it was already accepted as a general consensus that we are facing a complex challenge: we will need inventive ways to feed to growing population but the potential and land availability for cultivation has almost reached its maximum capacity. Also rising before the crisis was the global trend of growing locally due to a variety of factors or needs: in regions in which climate is a challenge, in remote areas, where there is water or soil rarity, aiming at lowering the carbon footprint, increasing product short shelf life, cutting down on transportation, etc. “In the long term, we feel that the current crisis will accelerate tremendously and definitely crystallize the need to grow locally and/or inside cities and the need to grow in a controlled cleanroom environment which will result in a higher demand for our product and a growth in our sector”, says Bélanger. “With its mobile carriages, the Greenrak Integrated Vertical Indoor Farming Solution is the ideal response to the current situation allowing both to increase yield while reducing the required surface by eliminating space wasting.
Customers increasingly have groceries delivered directly to their homes seems to be also an underlying trend rising from this crisis and in the long term, this may also play a role in creating a higher demand for our high-density cold storage solutions.”
Montel’s Greenrak and Grow&Roll systems were developed specifically for growing applications. Greenrak mobile system is lightweight, rust-resistant, and simple in design which allows for easy installation, use, and maintenance. Grow&Roll mobile system is the heavy-duty version of Greenrak and can withstand a weight of 3630 kg. Growrak was engineered to free up space between frames at each level providing plenty of clearance for better airflow, ventilation system ducts, lighting fixtures, and enough spacing for oversize trays to pass through between frames.
High yield hydroponic vertical farms
“Given the fact that Montel's Vertical Farming systems have been implemented in numerous indoor high yield hydroponic vertical farms that utilize cleanroom technologies and automation as well as many medical or recreational cannabis facilities around the world, we feel our expertise will benefit this growing sector. We are expecting a very high volume of projects that will require Integrated Vertical Farming Solutions. Our experience and knowledge allows us to rapidly assist the emerging needs in vertical farming and medical or recreational cannabis cultivation. By extension, we also foresee an increasing demand in the Cannabis Dispensaries market for our Light-duty drawer cabinet. We also expect a possible higher demand for our High-Density Cold Storage Solutions for the grocery delivery market and Buy Online, Pickup In-Store (BOPIS) market.”
Tags: Vegetables, Medicinal cannabis
VIDEOS: The Technologies Helping Move Agriculture Indoors
As more agriculture moves indoors, Israeli technologies are moving in with them to optimize lighting, watering, temperature, and other factors for an efficient and effective operation. Greenhouses and urban farm factories are expensive to set up but pay off in higher yield, quality, and market value, growing all through the seasons.
Greenhouses and urban farm factories are expensive to set up but pay off in higher yield, quality, and market value, growing all through the seasons.
A pick-yourself strawberry farm in China built inside an Azrom greenhouse. Photo courtesy of Azrom
Grain crops will always need large fields. But tomatoes, leafy greens, peppers, and strawberries are some of the many fruits and veggies that thrive indoors under precisely controlled conditions.
Though it costs more to raise produce in greenhouses or urban “farm factories,” the payoff is higher yield, quality, and market value. The plants can grow year-round with less fertilizer and pesticide.
As more agriculture moves indoors, Israeli technologies are moving in with them to optimize lighting, watering, temperature, and other factors for an efficient and effective operation.
Sarai Kemp, vice president of deal flow at Trendlines AgriFood. Photo: courtesy
“There is a growing trend for traditional greenhouse farming and indoor hydroponic and vertical farming for certain types of crops,” says Sarai Kemp, vice president of deal flow at Trendlines AgriFood based in Israel with branches in China and Singapore.
Kemp tells ISRAEL21c that most greenhouse-grown tomatoes go straight to consumers while most field-grown tomatoes go into items like ketchup.
“Growing indoors helps you produce more in a better environment than in open fields,” she says. “Farmers invest in technology for greenhouses because they can control the growing environment and sell the produce at a higher value.”
Kemp says a lot of indoor farming technology originated in Israel. “We have the experience, capability, and technology to provide monitoring solutions.”
Europe is the main market for Israeli indoor farming technology, and Kemp notes that a new market has opened closer to home.
“The United Arab Emirates is very interested in indoor farming because of the desert conditions that make it difficult to grow in open fields there.”
Let’s look at a few Israeli solutions for indoor farming.
Greenhouse experts
This 5.5-acre medical cannabis greenhouse complex in Greece is covered with f-CLEAN, a durable polymer offering exceptional light transmission and energy savings. Photo courtesy of Azrom
One of the oldest market leaders in the greenhouse farming business is Azrom, a family company that has specialized in designing, building, and installing fully customized greenhouse systems since 1979.
“That’s all we do,” says Zviki Porat, Azrom’s international marketing manager. “We started exporting in 1979 to Greece and since then we have done about 1,500 projects in more than 70 countries.”
In the old days, technology meant simple drip irrigation. Today, Azrom partners with Israeli research institutes and ag-tech companies to stay a step ahead of the greenhouse technologies curve.
“Now it’s a whole package of high-tech systems that lead to much higher yields and monitor processes better, including weather and topography, planning, designing, engineering, and remote controls,” says Porat.
Also in the early days, greenhouse crops were raised in the ground. Today, most farmers opt for hydroponics – growing in soil-free mediums.
“There are 10 kinds of platforms to choose from in hydroponics, so it’s much more complicated today to plan and price a greenhouse system,” says Porat.
Four kinds of crops growing under one greenhouse roof in Belarus. Photo courtesy of Azrom
“And every year more crops are being grown in greenhouses because land is in short supply. The main crops are vegetables, strawberries, ornamental flowers, and medical cannabis. But you can even grow watermelon, pineapple, and mango indoors where they stay warm and are exposed to fewer pests.”
In addition to Asia and Europe, Azrom has projects planned in Louisiana (US) and Dubai (UAE).
“Greenhouse growing requires a high investment. But you pollute less because you don’t spray as much, and you can collect and reuse water and even fertilizer,” Porat says. “So we have a lot to contribute to desert agriculture.”
Hydroponic greenhouse factories
A British-Israeli venture formed from a merger of two established companies about eight years ago, Growponics designs and builds automated hydroponic greenhouse factories in urban settings.
“You can grow vegetables all year round in greenhouses in many places, like in California’s Salinas Valley. But that is not where the population is,” says founder Lior Hessel.
Hessel says shipping costs today account for more than 80% of the landed cost of vegetables – that is, the total expense to get a product to its destination.
“Local greenhouse farming is expensive, but it pays off compared to shipping costs,” Hessel tells ISRAEL21c. “In the last 10 years, a new trend is local production with a lower landed price and lower carbon footprint.”
Still, for a massive greenhouse factory to be profitable, its steep capital and operating expenses must be offset by maximizing yield per square meter, Hessel explains.
“In Growponics we do this by using automation. The plants move on conveyers. We eliminate aisles, which normally take up 15 to 20% of greenhouse space; and we adjust the spacing between plants in different parts of the growth cycle. That alone can increase yield by more than 40% on top of the savings from eliminating aisles. It’s a gamechanger when you put them together.”
With funding in part from the Israel Innovation Authority, Growponics invests heavily in R&D in cooperation with institutes in Israel, the UK, and continental Europe.
One innovation is a data collection robot that supplements the data collection done by sensors in the greenhouses. Another is organic fertilizer produced via atmospheric nitrogen fixation, which uses bacteria to make nitrogen in the air available to plants. This technology won Growponics the European Union’s Seal of Excellence and €2.5 million in funding to implement it in Europe.
Growponics has three sites in Israel, accounting for more than 70% of domestic hydroponics.
“In Europe, we registered a new company in Greece to do more than $4 million in projects,” says Hessel, “and we are going to the UAE as part of an Israeli business delegation before the end of the year.”
Three years ago, Growponics established a two-acre greenhouse factory in Connecticut that sells its produce to New England supermarket chains. Further US expansion is planned with local partners as owner-operators to handle marketing and distribution.
Lighting and growing system
“Indoor growing demands scientific knowledge of what each plant needs and when,” says Daniel Levin, founder of Tel Aviv-headquartered Growor, whose indoor agriculture system can reduce overall costs up to 40 percent (up to 70% electricity saving alone) while increasing yield by about 30%.
The business started five years ago with a light-bulb idea, literally.
Pharma-grade cannabis thriving under Growor’s lighting system. Photo: courtesy
The smart LED light, which can manipulate outcomes such as tomato color and juiciness, was developed by Levin’s business partner Michael Naich, now CEO of Growor and its companion R&D company Group 1607 (so named because both their birthdays are on July 16).
But lighting alone wasn’t enough. Indoor farmers must control and monitor a variety of inputs such as water, nutrients, temperature, and humidity.
“Because we had so much data from our lighting system, we were able to develop a full dynamic protocol for any kind of indoor growing,” says Levin. “The protocols adapt to help each plant feel it is in the best conditions at any time and location.”
Energy-efficient LED lighting retains a starring role in the Growor system, which includes sensors, AI software, and a mobile app to manage cultivation remotely.
“We adjust the rest of the parameters to the light parameters because only light can manipulate the plant’s behavior drastically. More or less water, or more or less fertilizer, won’t change a tomato’s color.”
Growor has pilot projects in Israel, North America, Europe, and Asia for growing flowers, tomatoes, cucumbers, and pharma-grade cannabis. The latter crop, says Levin, is raised in clean rooms and must be reliably stable and consistent because “there’s no room for surprises.”
Robotic indoor harvesting
The higher yield in indoor agriculture requires more farmhands, and that’s a problem.
“One of most the urgent issues today is a labor shortage because most activities are done manually,” says MetoMotion CEO Adi Nir.
MetoMotion is developing a robotic system that automates labor-intensive greenhouse tasks and simultaneously gathers actionable data to improve yield and quality.
MetoMotion’s GRoW robot picks tomatoes and performs other labor-intensive tasks in greenhouses. Photo: courtesy
This portfolio company of The Trendlines Group has been testing its unique GRoW robotic tomato harvester in Israel and in The Netherlands in partnership with Bayer Crop Science.
“Since March we haven’t been able to travel from our offices in Yokne’am,” says Nir. “Our team there works with the robot and the software is operated mainly from here. This reduces the amount of staff needed at the greenhouse.
“You always need people too, but the robots work autonomously and from the office, you can see yield and yield forecast and other actionable data collected and transmitted to the cloud.”
The first commercial GRoW units will be shipped to a few farmers in Europe for evaluation in the next eight months.
“We are currently focused on tomatoes, but the platform can be adapted to different vegetables,” says Nir. GRoW also can be adapted to perform pruning, pollination, and de-leafing.
Wall to fork
As ISRAEL21c previously reported, “green walls” can provide insulation, air purification, and aesthetic landscaping to the interior or exterior of buildings.
They can also produce salad greens, mushrooms, and strawberries in an urban space-saving way.
However, vertical farming is still quite limited because to be profitable “you have to either grow more or save on costs of labor or resources such as electricity,” Sarai Kemp from Trendlines tells ISRAEL21c.
Among several Israeli vertical farming startups working to make this model viable are Verticanna and Vertical Field.
Verticanna, in the seed investment stage with two medical cannabis pilots running in Israel, aims to revolutionize vertical hydroponic growing systems for crops including, uniquely, citrus fruit.
Vertical Field of Ra’anana makes the Vertical Farm, a modular, moveable soil-based platform that can grow 200 types of organic, pesticide-free crops and requires no special training to operate.
The Vertical Farm can grow hundreds of types of crops indoors or outdoors at a supermarket, restaurant or another retail outlet. Photo courtesy of Vertical Field
Vertical Farm can be placed in a 20-foot or 40-foot standalone container equipped with advanced sensors that monitor, irrigate, and fertilize crops throughout every growth stage.
Vertical Farms are up and running at some Israeli supermarkets and at Farmers & Chefs restaurant in Poughkeepsie, NY, and at Evergreen Kosher Market in Monsey, NY. Expansion across other US cities is planned.
“We offer an easy-to-use real alternative to traditional agriculture,” CEO Guy Elitzur said. “Our urban farms give new meaning to the term ‘farm-to-table,’ because one can pick their own pesticide-free greens and herbs at supermarkets, restaurants, or other retail sites.”
The Israeli startup was cited by Silicon Review as one of “50 Innovative Companies to Watch in 2019” and named by World Smart City in 2019 as “Best Startup.”
Abigail Klein Leichman is a writer and associate editor at ISRAEL21c. Prior to moving to Israel in 2007, she was a specialty writer and copy editor at a major daily newspaper in New Jersey and has freelanced for a variety of newspapers and periodicals since 1984.
CubicFarm Systems Announces Its First Operational Growing Machine For Hemp and Cannabis
The ZenCube project leverages CubicFarms' patented, undulating-path growing technology to allow hemp and cannabis growers to cultivate significant amounts of product in a smaller footprint by doing so in a completely climate-controlled environment
October 28, 2019
License Agreement with Zenabis to Expand Sales of CubicFarms Systems in New Vertical
VANCOUVER, BC / ACCESSWIRE / October 28, 2019,/ CubicFarm� Systems Corp. (TSXV:CUB) ("CubicFarms" or the "Company") is pleased to announce that ZenCube, its vertical-farming machine for growing hemp and cannabis, is fully operational at a showcase and R&D facility in Langley, Canada.
The ZenCube project leverages CubicFarms' patented, undulating-path growing technology to allow hemp and cannabis growers to cultivate significant amounts of product in a smaller footprint by doing so in a completely climate-controlled environment. The ZenCube helps to address challenges faced by traditional growing methods, by providing a solution that requires less space, labour, water and energy, and is expected to result in a more consistent, higher quality product for farmers and end-users alike.
CubicFarms has developed a pipeline of sales opportunities for its ZenCube-branded growing machines that is expected to be augmented by an exclusive License Agreement signed with Zenabis Ltd. ("Zenabis"), a subsidiary of Zenabis Global, a leading Canadian licensed cannabis cultivator of medical and recreational cannabis, and propagator and cultivator of floral and vegetable products. Under terms of the agreement, Zenabis shall fulfill a minimum sales threshold of 150 ZenCube machines by year 2024 to maintain its exclusive license to operate, sell and sublicense ZenCube machines globally.
The License Agreement supersedes the Joint Venture Agreement between CubicFarms and Zenabis, announced in a Bevo Agro press release dated October 9, 2018. Bevo Agro now is Zenabis Global.
CubicFarms and Zenabis are conducting ongoing R&D on crop growth and quality at the Zenabis-owned-and-licensed Langley facility.
Dave Dinesen, Chief Executive Officer of CubicFarms, commented: "CubicFarms is excited to bring online its first growing machine for the purposes of facilitating yet another vertical in the hemp and cannabis space, and to help farmers grow more produce reliably, 12 months a year, wherever they are on earth. CubicFarms has received numerous enquiries to utilize our technology in this space and we are thrilled to serve this market, in addition to our other verticals, namely fresh produce, animal feed and nutraceuticals."
Leo Benne, Chief Growing Officer of Zenabis, added: "The Zenabis and CubicFarms partnership on the ZenCube project is a culmination of our joint vision of bringing a robust and reliable solution to the global hemp and cannabis market, to ensure we meet consistency and quality in our crop yields."
Neither the TSX Venture Exchange nor its Regulation Services Provider (as that term is defined in the policies of the TSX Venture Exchange) accepts responsibility for the adequacy or accuracy of this release.
About CubicFarm� Systems Corp.
CubicFarm� Systems Corp. ("CubicFarms") is an ag-tech company commercializing large scale, vertical farming solutions for global industrial markets. Founded in 2015, the Company's mission is to provide industries around the world with efficient growing systems capable of producing predictable crop yields. CubicFarms offers turnkey, commercial scale, hydroponic, automated vertical farm growing systems that can grow predictably and sustainably for 12 months of the year virtually anywhere on earth. CubicFarms enables its customers in the fresh produce, animal feed, nutraceutical, and hemp/cannabis industries to grow locally and to provide their markets with safe, sustainable, secure and fresh ingredients that are consistent in colour, size, taste, nutrition and allows for a longer shelf life. Further support and value is provided to customers through the Company's patent-pending germination technology and proprietary auto harvesting and processing methods.
Using its unique, undulating growing system, the Company addresses the main challenges within the indoor farming industry by significantly reducing the need for physical labour and energy, and maximizing yield per cubic foot. The Company has sold and installed systems in Canada and the US, and is currently negotiating with a global pipeline of prospective customers. It also operates one wholly owned facility in Pitt Meadows, British Columbia, and sells its produce in the province to retail and wholesale customers under the brand name Thriiv Local Garden".
Information contact
Kimberly Lim
kimberly@cubicfarms.com
Phone: +1-236-858-6491
www.cubicfarms.com
Cautionary statement on forward-looking information
Certain statements in this release constitute "forward-looking statements" or "forward-looking information" within the meaning of applicable securities laws, including, without limitation, statements with respect to the ZenCube is expected to result in a more consistent, higher quality product for farmers and end-users alike; and CubicFarms' sales pipeline is expected to be augmented by the License Agreement. Such statements involve known and unknown risks, uncertainties, and other factors which may cause the actual results, performance, or achievements of CubicFarm Systems Corp., or industry results, to be materially different from any future results, performance, or achievements expressed or implied by such forward-looking statements or information. Such statements can be identified by the use of words such as "may", "would", "could", "will", "intend", "expect", "believe", "plan", "anticipate", "estimate", "scheduled", "forecast", "predict", and other similar terminology, or state that certain actions, events, or results "may", "could", "would", "might", or "will" be taken, occur, or be achieved.
These statements reflect the company's current expectations regarding future events, performance, and results and speak only as of the date of this news release. Consequently, there can be no assurances that such statements will prove to be accurate and actual results and future events could differ materially from those anticipated in such statements. Except as required by securities disclosure laws and regulations applicable to the company, the company undertakes no obligation to update these forward-looking statements if the company's expectations regarding future events, performance, or results change.
SOURCE: CubicFarm Systems Corp
Exploring Cannabis Vertical Cultivation
Conceptually, vertical cultivation is not really easy to visualize. Simply put, vertical farming is the practice of growing cannabis in vertically stacked layers. This growing practice could either use conventional soil, hydroponic or aeroponic growing methods. Vertical farms can help produce cannabis in otherwise challenging environments
Conceptually, vertical cultivation is not really easy to visualize. Simply put, vertical farming is the practice of growing cannabis in vertically stacked layers. This growing practice could either use conventional soil, hydroponic or aeroponic growing methods. Vertical farms can help produce cannabis in otherwise challenging environments.
As some growers have come to know, cultivating cannabis indoors can be a costly affair. Real estate costs coupled with energy bills, significant staffing requirements, and a host of different elements needing to come together in precise tandem are required for an indoor grow to be operational. It then becomes crucial to be consistently profitable. And that can only be achieved by increasing plant yields. Maximizing the grow space is one way to reach this goal and that’s what brings us to the many aspects of vertical growing; the practice of producing plants in vertically stacked or inclined surfaces.
Primarily vertical farming can be done in one of two ways.
Stacked Vertical
The most common method of vertical farming is a stacked vertical setup. Here levels of plant racks have LED lights above each rack. Plants are topped and defoliated to keep them short and bud-heavy. This may lead to growers stacking in the flower stage - despite the plants being large and top heavy.
True Vertical
In true vertical growing, plants are grown out of the side of a column, with water and nutrients dripping down from the top.
The LED and the Ramp
Cannabis cultivation is going vertical in a big way and the primary reason for that is the vastly improved performance of indoor LED lighting systems. This is resulting in more and more cannabis growers investing in powerful multi-tier (or ‘vertical farm’) lighting systems. With fully functional LED system in place one can expect reducing production time on both the retail flower market as well as for oil extraction. More associated benefits include decreased energy consumption, reduced ventilation, air conditioning and heating needs, decreased cycle time, doubled production because of increased crop yield and of course, the overall reduction of the cost per pound of the finished product. It is also known to significantly reduce water and fertilizer usage. Most growers swear by it for the consistent, year-round flower quality and chemotype with denser trichome development in buds.
Environmental Conditions Get Complex Quickly
Maintaining optimum temperature, humidity, and air circulation is tough for all cannabis grows. But in vertical growing there are more variables in macro and micro environmental conditions because there are more plants, making absolute control more difficult. For the atmospheric variability, the use of sensors to detect data points like moisture changes is recommended. Generally, commercial growers use a single temperature/humidity sensor to monitor a room - even for grow areas spanning over 20,000 feet. In such cases, it is prudent to recommend air circulation systems that push air right in between the racks above the plants, usually with small ducts that take air from the edges of the room to the center of the racks.
Expensive to Set Up and Maintain
While growing plants vertically provides several fundamental advantages for cultivators, it also stands to reason that the increased yield comes with some added costs. This may include increased energy usage from artificial lighting, the upkeep and maintenance of state-of-the-art climate control systems, extra infrastructure required to facilitate a logistical equilibrium and of course, paying high-skilled technicians to constant upgrade and modify the equipment.
Certain Cultivars Work Better Than Others
The most successful cannabis cultivars for vertical growing are those that are short but have big buds. They will also need to have fewer leaves, so less defoliation is necessary. But if you are a confident defoliator, you can broaden the range and diversity of the cultivars used.
For more information:
Frontier Botanics
Lindsay Gayman BScN, Medical Cannabis Educator
+44 (0) 203 993 8250
info@frontierbotanics.com
frontierbotanics.com
Publication date: Wed 30 Oct 2019
© MMJDaily.com / Contact
Is Vertical Growing The Future of Cannabis?
In the food sector, vertical growing companies like Plenty, Aerofarms, Gotham Greens, and many more, are revolutionizing agriculture. But in the cannabis industry, which practically invented sunless growing, there has been notably less activity
(Daniel Berman for Leafly)
August 2, 2019
Indoor cannabis grows are expensive operations. Given the real estate costs, massive energy bills, and significant staffing requirements, it’s crucial to find a way to increase profits. Maximizing your grow space is one way to do this and that could mean vertical growing—the practice of producing plants in vertically stacked layers or vertically inclined surfaces.
In the food sector, vertical growing companies like Plenty, Aerofarms, Gotham Greens, and many more, are revolutionizing agriculture. But in the cannabis industry, which practically invented sunless growing, there has been notably less activity.
This is partly because high-pressure sodium lights (HPS), one of the most common lights used to grow cannabis for decades, run so hot that plants have to be many feet away to stay unharmed.
How to Top Cannabis Plants for Bigger Yields
But LEDs run at much lower temperatures, so you can install them inches from the plant canopy. Their decreasing price and increasing ability to equal or exceed HPS yields are making LEDs the standard, finally opening the door to vertical growing for cannabis.
“The main catalyst behind cannabis cultivation going vertical is the improved performance of LED lighting,” says Thomas Rogers, LED engineer of Exact Lux. “Cannabis growers are approaching us wanting the most powerful multi-tier or ‘vertical farm’ lighting systems possible.”
Two Types of Vertical Farming
Stacked vertical (left) and true vertical (right) cannabis grows with LEDs. (Sean Walling/Leafly)
Stacked Vertical
The most common method of vertical farming is a stacked vertical setup—levels of plant racks with LED lights above each rack. Plants are topped and defoliated to keep them short and bud-heavy.
Growers even stack in the flower stage, despite plants being large and top-heavy.
True Vertical
With true vertical growing, plants grow out the side of a column, and water and nutrients drip down from the top—see these examples from ZipGrowand Tower Garden.
Within the column, a hybrid method combines nutrient film technique (NFT), where nutrient water is passed directly over the roots, and aeroponics, a soilless grow method where roots hang in the air.
How to Prune Cannabis Plants for Maximum Yields
Pros and Cons of Vertical Growing
So why don’t all cannabis operations grow vertically, especially in this competitive new industry? Here we’ll look at some of the benefits and drawbacks.
Environmental Conditions Get Complex
Maintaining optimum temperature, humidity, and air circulation is tough for all cannabis grows. But in vertical growing there is even more variability in macro and micro environmental conditions because there are more plants, making control more difficult.
Because of this atmospheric variability, Hugh Gaasch, engineer at STEM Cultivation, recommends sensors to detect data points like moisture changes. “Shockingly, the majority of commercial growers I’ve seen to date use a single temperature/humidity sensor to monitor a room, even large spaces, over 20,000 feet.”
Grow Room Humidity Control: 5 Tips for Indoor Growers
In contrast, STEM Cultivation uses one temperature sensor per 100 cubic feet. STEM collects data on: temperature, humidity, air pressure, CO2 levels, lighting levels, lighting power (kW) and energy (kWh), system air circulation rates, localized air circulation, VOC (volatile organic compounds), and HVAC power and energy, to name a few.
Mike Zartarian, from Zartarian Engineering, builds circulation systems for vegetable and cannabis growers. To decrease chances of mold and fungi, he says: “I recommend systems that push air right in between the racks above the plants, usually with small ducts that take air from the edges of the room to the center of the racks.”
Expensive to Set Up and Maintain
Although vertical growing of any kind will increase yield by maximizing space, when you add up the increased energy usage from more artificial lighting, an upgraded climate control system, the extra infrastructure required (ladders, racks, sensors, and more), and paying high-skilled agro-technicians, it is very costly for many.
Zartarian says: “It’s by no means impossible, but the jury is very much out on whether it’s cost effective long-term. If veggie growers prove it to be a dominant technique, I would expect to see more experimentation on the cannabis side.”
How to Train Your Cannabis Plants for Better Yields and Potency
As it is, licensed operators he works with are struggling to meet demand and prefer to stick to more traditional techniques they know will produce.
Dangerous Conditions
Vertically grown cannabis needs a lot of hands-on attention during the flowering cycle as compared to, say, vertical lettuce crops which are more set-and-forget. The height of a plant must be closely controlled, which requires grow technicians to get up on step stools or scaffolding to reach into the plant canopy. These high-tier tasks may not be OSHA-compliant.
Certain Cultivars Work Better Than Others
The most successful cultivars for vertical growing are short, have big buds, and fewer leaves, so less defoliation is necessary. But if you’re a confident defoliator, the diversity of cultivars you can grow will broaden.
Arthur Brownsey, cannabis cultivation consultant at Four Trees, thinks most strains can grow vertically. “If you have a tight production schedule, group like-cultivars together, and plan accordingly, there are no restrictions to what you can grow.”
Factors That Impact Your Cannabis Strain: Part 3, Growing Techniques
Agro-engineer Aja Atwood of Trella sees value in vertical growing, but the limited cultivars it serves made her determined to find another option. “There is a wide variety of strains out there that prefer longer vegetation periods and have a taller growth structure. In order to diversify, you need to train or trellis those taller varieties to stay within the space.”
To allow for vertical growing with a diversity of strains, she and her partner Andres Chamorro invented a grow unit, TrellaGro LST, that trains plants to grow horizontally. Each unit is vertically stackable and equipped with LED lights that follow it as it grows sideways, allowing for taller strains and less energy use.
Stay Tuned
In these early days, vertical growing has yet to revolutionize the industry, and some operations, focused on supplying a high-demand market, are sticking with traditional growing methods.
However, most operations already know the price of cannabis will likely drop as competition grows. In that climate, the future of cannabis could move up, not out.
Christine Giraud, a freelance writer in Boston, has been writing about cannabis for publications like The Boston Globe, Overture Global Magazine, Dig Boston, Civilized, Her(b) Life, and Foottraffik.
Cannabis Sales Could Hit $41B By 2025, Nielsen Predicts
The market for all legalized cannabis, including CBD, is expected to quintuple from $8 billion in 2018 to $41 billion by 2025, according to new data from Nielsen
AUTHOR Jessi Devenyns
July 30, 2019
Dive Brief:
The market for all legalized cannabis, including CBD, is expected to quintuple from $8 billion in 2018 to $41 billion by 2025, according to new data from Nielsen.
Since the Farm Bill legalized hemp last December, Nielsen found interest in alternative forms of ingesting CBD has increased.
In the last four years, the variety of CBD edibles and other products has grown significantly. In 2014, there were only two states where marijuana was legalized and 166 brands of products. By 2018, that number jumped to 2,600 marijuana brands across four legalized states.
Dive Insight:
Despite cannabis remaining illegal at a federal level, the sentiment regarding the substance is changing. Last year, President Trump signed the Farm Bill, which made it legal to cultivate hemp. That move helped consumers and retailers feel more comfortable giving it a try.
Although there are still FDA restrictions on hemp-derived CBD as an additive in food, several retailers are now selling health and beauty products with it, according to Nielsen. A study by A.T. Kearney last year found four in 10 U.S. consumers said they would be willing to try food made with cannabis. This open sentiment has pushed more food and beverage companies to want to introduce cannabis products — a major reason for the high predicted growth rate in the next five years.
Beer companies have already seen success investing in the space. The Nielsen report shows that cannabis-interested adults are 41% more likely to drink beer. Lagunitas Brewing, part of Netherlands-based Heineken, sells its SuperCritical IPA made with aromatic marijuana terpenes in California. Ceria, helmed by former Blue Moon brewmaster Keith Villa, launched THC brew Grainwave in Colorado. Two Roots Brewing unveiled its nonalcoholic "cannabier" in Nevada. Meanwhile, Constellation and Molson Coors are still working on their brews.
Big companies in the food space have been more hesitant. Typically, CPG giants are slow to pick up on trends and introduce popular functional ingredients into their products, and the case is no different in with cannabis.
But companies are starting to promise to put the ingredient in products if the FDA legalizes it. Ben & Jerry’s said it will offer a CBD-infused ice cream to consumers. Bloomberg reported that Coca-Cola was in talks with Aurora Cannabis for a CBD-infused soda, though the soda company demurred and said it doesn't "have any plans at this stage" to enter the market.
Nielsen's numbers account for both marijuana and CBD-infused products. The firm also assumes 75% of the U.S. adult population will have consistent access to legal marijuana by 2025. The full legalization of the ingredient and its $35 billion effect on CPG sales, according to Nielsen, depends on several unknowns. But BDS Analytics is also projecting full U.S. legalization of all forms of cannabis by 2021 — based on public opinion through state legalization issues, federal government sentiment and momentum elsewhere.
Although the FDA held its first public hearing on cannabis and CBD this year, analysts still say it could be years before there is a path for products to get to market. While these big predictions on sales growth could entice more companies to get involved, others might remain cautious and wait before developing products. The increasing confidence and predicted growth from market research firms may inspire companies waiting on the sidelines to get into the market or it may push those companies that are already on the edge to take action.
Lead Photo: (Credit: Jennifer Martin )
Recommended Reading:
Micro Lab Farms New California Cultivation Complex Approved by City of Needles
The unique facility features Gen3 GrowPods, designed to outperform other methods of cultivation, and provide rapid growth in a multi-billion dollar market
July 29, 2019
The unique facility features Gen3 GrowPods, designed to outperform other methods of cultivation, and provide rapid growth in a multi-billion dollar market
CORONA, Calif., July 29, 2019 /PRNewswire/ -- Micro Lab Farms, a premier provider of automated indoor micro-farms for rapid production of legal cannabis, announced that it has been granted a Conditional Use Permit for a two phase cultivation facility in the city of Needles, California.
The resolution was passed by the Needles City Council, and allows Micro Lab Farms to develop its California Cannabis Cultivation Complex, which will feature over 100 state-of-the-art GrowPods.
The pods, designed by GP Solutions GWPD, +0.00%, are automated, transportable, scalable micro farms that have been shown to grow cannabis at a faster rate than conventional means of agriculture.
GrowPods allow cultivation to take place year-round, and eliminate pathogens, contaminants, pesticides and chemicals, to produce clean and robust crops. The Pods also provide a sealed environment for excellent isolation of specific strains and clones.
The GrowPods will also utilize GP Solutions proprietary soil mixture, which contains no animal products. This is critical in the cannabis industry because many other soils and additives can contain harmful pathogens and bacteria that have the potential to contaminate crops and cause testing failures.
The California Cannabis Cultivation Complex also provides investment opportunities to experienced growers, entrepreneurs, and qualified individuals seeking to add the cannabis sector to their portfolios. This passive investment allows stakeholders to participate in the rapid growth of the cannabis sector, with mitigated risk.
The Conditional Use Permit allows Micro Lab Farms to develop over 35,000 square feet of cultivation space.
For more information on Micro Lab Farms, or for information on GrowPods, or for details on investing in the California Cannabis Cultivation Complex, contact Micro Lab Farms at: (951) 266-6096, or visit: www.microlabfarms.com
About Micro Lab Farms
Micro Lab Farms has made it possible to rapidly and affordably enter or expand in the legal cannabis industry with its "GrowPod" cultivation systems.
GrowPods are modular, indoor micro-farms that feature a controlled environment, state-of-the-art air and water filtration, proprietary pathogen-free living soils, and automation systems that far outperform other methods of cultivation, and produce clean, robust crops without pathogens, contaminants, pesticides or chemicals.
For information on Micro Lab Farms, call: (951) 266-6096, or visit: www.microlabfarms.com
Connect:
Website: www.microlabfarms.com
Facebook: facebook.com/MicroLabFarms
Twitter: @MicroLabFarms
View original content:http://www.prnewswire.com/news-releases/micro-lab-farms-new-california-cultivation-complex-approved-by-city-of-needles-300892124.html
SOURCE Micro Lab Farms
Copyright (C) 2019 PR Newswire. All rights reserved
“LitHouse Uses AmHydro EPIC Nutrient To Capture 4 Cannabis Cup Awards”
LitHouse took 4 awards (including a 1st place in the Sungrown Flower category) at the High Times 2019 NorCal Cannabis Cup on June 1st-2nd
July 9, 2019
AmHydro, industry-leading provider of hydroponic growing systems, crop consulting, grower training, and crop-specific nutrients, is proud to announce the recent Cannabis Cup® victory by grower LitHouse Farm® of Mendocino Coast CA.
LitHouse took 4 awards (including a 1st place in the Sungrown Flower category) at the High Times 2019 NorCal Cannabis Cup on June 1st-2nd . A family run operation since 2002, Lit House has cultivated their crops using the AmHydro EPIC® Cannabis nutrient line. AmHydro EPIC, a 5- stage cannabis nutrient program, is available at https://shop.amhydro.com/collections/epic-nutrients
Congratulations to LitHouse for a job well done!
They will be competing next at the Bay Area Cannabis Cup June 22nd-23rd.
Visit LitHouse at: http://www.lithouse.farm/ and on Instagram : https://www.instagram.com/lit_house_farm/?hl=en
US (MA): Hydroponic Growing Graduates Learned With Lettuce, Seek Jobs in Cannabis
"The skills they learn in the (shipping containers) are transferable to the cannabis industry," Morse said.
Ernesto Hernandez Martin graduated Thursday from the Freight Farms Hydroponic Growing apprenticeship program at Holyoke Community College, having learned how to grow lettuce in the controlled environment of two shipping containers. But that’s not all he can grow.
“I’m looking forward to getting a job in the new industries, either in marijuana or in growing vegetables,” Hernandez Martin said while leading a tour of Freight Farms on Race Street in the city’s industrial Flats neighborhood and adjacent to the HCC MGM Culinary Arts Institute.
Neither college officials or Holyoke Mayor Alex Morse were shy Thursday about linking the hydroponic program with the city’s new marijuana industry and its need for skilled labor. They also said the program has the potential to help feed Holyokers who have trouble affording healthy meals.
"The skills they learn in the (shipping containers) are transferable to the cannabis industry," Morse said.
The college has no plans to grow anything but vegetables. The city, though, has embraced the newly legal cannabis industry.
Just this month, seed-to-sale marijuana company Trulieve Cannabis Corp., formerly Life Essence, bought a 150-year-old mill building at 56 Canal St. for $3.2 million with plans to build a 126,000-square-foot growing, processing, testing and retail operation there.
Source: MassLive (Jim Kinney)
Publication date: 7/1/2019
Micro Lab Farms in Needles, CA Helps Individuals Get Started With Modular Farming With Shipping Container Greenhouses
America’s medical cannabis industry is growing at a steady pace, with marijuana sales expected to amount to $50 billion in the upcoming decade
America’s medical cannabis industry is growing at a steady pace, with marijuana sales expected to amount to $50 billion in the upcoming decade. Micro Lab Farms is a California based company that empowers anyone to efficiently launch or expand a high-quality marijuana operation.
Needles, CA - America’s medical cannabis industry is growing at a steady pace, with marijuana sales expected to amount to $50 billion in the upcoming decade. This explosive growth has been driven largely in part due to all the legislative changes around the herb that have taken place recently. Entrepreneurs looking to capitalize on the numerous business opportunities can jump into the “green rush” and get started almost immediately with today’s technology. Micro Lab Farms is a California based company that empowers anyone to efficiently launch or expand a high-quality marijuana operation.
Micro Lab Farms is known for their cutting-edge, eco-friendly growing systems which are optimized for productivity and profitability. Entrepreneurs from all backgrounds are looking into container farms from Micro Lab Farms to streamline the start-up process. Micro Lab Farms in California has gained recognition for their turnkey solutions that provide a full-featured environment to grow in any climate and any season.
These plug and grow systems are designed for automation and easy operation, allowing users to begin generating revenue almost immediately. Micro Lab Farms retrofits shipping containers and specifically modifies them to provide a controlled environment that allows for year-round production. A spokesperson for their company said, “Our grow lab is an affordable, scalable, efficient, and automated system. As a full turnkey solution, a grower can be up and running in a short amount of time. The return on investment can be achieved in as little as 6 months.”
Micro Lab Farms has developed ecological grow labs that utilize 90% less water and 80% less fertilizer. Since these are food-grade containers, no pesticides or pollutants are required to harvest high-grade medicinal cannabis. The California company offers soil, soilless, and hydroponic high yield and low impact solutions. Their 20’ and 40' shipping container greenhouses come equipped with an LED expert series lighting system, a rolling table system, a reverse osmosis water purification system, an HVAC system, a steel man door, and both, a dehumidifier and humidifier. Micro Lab Farms can develop a personalized solution to fit each individual’s growing needs, as they can include additional features such as clean rooms, shelving systems, prep stations, additional sensors and controls, as well as flower, clone and drying labs. Their grow labs are modular, stackable, and can be self-contained with solar and natural gas energy solutions.
Each grow lab is a completely secure and monitored environment. They are equipped with a mobile device compatible cloud-based control system, allowing users to seamlessly oversee their product from seed to harvest, through Micro Lab Farms’ remote monitoring and controlling app. The app provides real-time data of all the key components of the farm including the air, water, humidity, nutrients, and plant growth. Giving users clear visibility and maximum control over every aspect of their grow operation and eliminating all surprises.
Micro Lab Farms is located at 3353 Needles Hwy, Needles, CA 92363. For inquiries, contact their team via phone at (951) 266-6096 or via email at info@microlabfarms.com. Visit their website for additional information regarding their services.
Micro Lab Farms Offers The Fastest, Most Efficient Pathway to Cultivate Cannabis
The company’s modular automated micro-farms can be fitted for
cultivation, drying, cloning or custom uses
Corona, CA – June 6, 2019 – Micro Lab Farms, a premier provider of fully automated turnkey systems for rapid production of legal cannabis, announced that it is offering four different units designed for specific applications.
The Micro Lab “FlowerPod” is designed for cannabis cultivation, and is an affordable, scalable, efficient and automated system that allows a grower to be quickly up and running. The Pod features a soil-based platform and proprietary air and water filtration, along with complete environmental control. The Pod outperforms other methods of cultivation, and return on investment can be achieved in as little as 6 to 9 months.
The “ClonePod” is the perfect solution to ensure consistent growth and exact replicas of favored plants and preferred cannabinoid profiles. As a sealed eco-system, worries about plant cross pollination and contamination are eliminated. The ClonePod offers an economical and consistent method to reproduce plants in a clean, contaminant-free environment.
The “DryingPod” provides the perfect space for finishing a harvest in a humidity-controlled environment. With a clean, temperature controlled room, growers are now able to dry and cure with a precision never before available.
The “CustomPod” is designed with a grower’s specific needs in mind. The team of botanists and scientists at Micro Lab Farms can develop the perfect environment for any particular crop, or to meet any goal.
The GrowPods allow cultivation to take place year-round, any place and any time, and have been shown to produce higher yields with greater consistency than other methods of cultivation.
GrowPods are environmentally friendly, use less water, and eliminate pathogens and pesticides.
Micro Lab Farms offers financing options with a minimum down payment. With reduced labor costs and no TI’s or construction needed, Micro Lab Farms provides a quick and cost-effective method to help a business get established and rapidly start growing.
To learn more about the GrowPods from Micro Lab Farms, call: 800-320-0761, or visit: www.microlabfarms.com
CONNECT:
Website: www.microlabfarms.com
Facebook: facebook.com/MicroLabFarms
Twitter: @MicroLabFarms
How Cannabis Cultivation Has Advanced Farming Technologies
Those same technologies and practices are being brought to other agricultural products in a phenomenon called vertical farming
May 27, 2019
Canada’s newly legal cannabis industry might still be in its infancy but the legacy of illicit growers continues to contribute to greener agricultural practices across the globe.
The once covert operations—meant to keep cannabis cultivation under police radar—can be credited with creating innovative farming techniques that curb agricultural waste and save on natural resources like space and water.
See how cannabis has already helped in making the future a little greener.
Sustainable, environmentally-friendly farming practices may not have been the initial goal, but are among the unintended side effects of cannabis prohibition in this country.
Looking back to the 1970s when cannabis consumption was skyrocketing in Canada, supply simply could not keep up with demand and prices rose accordingly.
The problem was the supply chain. Most cannabis was brought into Canada by tourists, or people posing as them, returning from tropical nations like Jamaica, Mexico or the Bahamas. Law enforcement seized a big chunk of that illicit supply, causing numerous dry periods.
The solution to the problem was for cannabis enthusiasts to grow their own. That was easy for people living in California, but not so much for those in Nova Scotia.
Canadian cannabis consumers, however, persevered.
Growing indoors, they constantly improved their technology to include hydroponics, aeroponics, grow-lights and other devices to promote growth.
Sean Berrigan/Leafly
They selectively bred strains that were not just hardier, more bountiful, and increasingly potent, but used the same care that vintners take with fine wine to ensure traits they desired.
In just more than a generation, Canada went from having virtually no cannabis crop to becoming the No. 8 producer in the world, according to the UN, and a net exporter of what many consider among the world’s best varieties.
How Canada’s West Coast Became World Renowned for Cannabis Cultivation
And now, those same technologies and practices are being brought to other agricultural products in a phenomenon called vertical farming.
Essentially, the legacy concepts pioneered by cannabis growers have been adopted by people and companies growing other produce indoors with outstanding results. Although most of the biggest producers are in Japan, Taiwan and large American cities—where they can take up whole high-rises and warehouses—it’s quickly becoming big business in Canada too.
According to the Food and Agriculture Organization of the United Nations, as much as 20% of the world’s food supply is grown in urban situations. And Allied Market Research predicted in a White Paper that vertical farming will take in nearly six times as much revenue in 2023 as it did in 2016.
It makes perfect sense. More efficient land use, less water used, few if any pesticides, lower fertilizer use, year-round harvests, and availability where people live without refrigeration or trucking are all cost reducers and environment helpers. And because the process is cleaner than traditional farming, yields are huge and even taste can be improved.
Chemical-Free Cannabis: Canadian Growers Turn to Biological Pesticides
“When you do a side-by-side test of the flavour,” said Rob Wing, executive chef for the Eataly gourmet market chain, “the taste isn’t even comparable.”
Leafly spoke with Ricky (not his real name), a veteran Abbotsford grower who started with a single plant in 1985 and 20 years later, was cultivating dozens. “People talk about it like it’s a new idea,” he said. “But we’ve been doing it since forever.”
He explained that cannabis growing was forced inside as much by law enforcement as climate; but acknowledged that by being able to control the farm’s temperature, he could harvest year-round.
Growing Cannabis Indoors vs. Outdoors: 3 Key Differences
Of course, such covert indoor cultivation requires artificial light. “That’s when the cops started looking at everyone’s utility bills,” he told us. Residences that used an inordinate amount of electricity were flagged as potential grow-ops. So, growers like Ricky switched to more efficient LED lights, reducing their electricity use. Business began to boom, and Ricky made cannabis cultivation his full-time job.
To keep up with demand without moving to a bigger, more conspicuous location, he had to become more efficient—and that required serious technology. “I tried hydroponics, but didn’t like all the water usage,” he said. “So, I switched to aeroponics.” That not only increased his output, but allowed him to grow far more potent cannabis.
Sensing legalization over the horizon, Ricky sold his plants and equipment and went into real estate. “I might have made a mistake, though,” he said, after reading some articles about successful urban farmers and noting how similar they are to his old operation. “I just should have switched to tomatoes or something.”
Even now that cannabis cultivation has gone big-scale and corporate, the innovations aren’t stopping. Hamilton’s Green Relief has embarked on an entirely new way to grow cannabis. Called aquaponics, the cannabis plants are grown alongside tanks of tilapia. The fish produce waste that is processed into fertilizer and the plants filter and clean the water for the tilapia.
Introduction to Growing Cannabis With Aquaponics
“Hydroponic cultivators have to drain their tanks every couple of weeks and refill them, starting the process all over again,” said Allan Glanfield, Green Relief’s marketing director. “Ours is closed circuit, from plants to fish to plants again.” The yield, the company says, is ten times as high as traditional methods and requires 90% less water. He likens the process to how lily pads grow in a natural setting.
While Green Relief could turn the tilapia it raises into a revenue stream, Glanfield said that the company donates them to Second Harvest to help feed the needy in the Hamilton area.
Although Green Relief is the only large-scale aquaponics farm in North America, Glanfield said that he is aware of several others in the startup process, and not all for cannabis.
“We’ve worked out the kinks and have an effective system, so it’s no surprise to see others adopt it,” he said. “We don’t feel threatened by them, we just like being reminded that it’s a great idea.”
Green Relief founders Warren and Lyn Bravo are so dedicated to the cause that they are building a smaller version of their farm for their backyard to provide them with fresh vegetables and fish.
Farms are moving indoors not just because they are cleaner, more efficient, and offer better products, but also because of the profit incentive. And it’s not just cannabis.
In many vertical farms, according to a study conducted by Agrilyst, Cornell University, Urban Ag News, foodshed.io, the Association for Vertical Farming, and FarmersWeb, it was determined that similar profits can be made by growing flowers, greens, microgreens, and herbs. And you don’t have to go through an arduous, years-long process to get a license to grow flowers.
So, when your future self is enjoying a big fat salmon steak along with fine fruits and vegetables all grown a few blocks away and harvested fresh that day, raise a glass to the pioneering cannabis growers who made it all possible.
Jerry Langton is a political reporter and author who splits his time between Canada and NYC.
Lead photo: Green Relief
Micro Lab Farms Adds Kyle Kushman to Board as Company Expands in Cannabis Industry
The company’s modular indoor farms allow growers, entrepreneurs and investors to enter or expand in the legal cannabis industry through a variety of options
Corona, CA – May 29, 2019 – Micro Lab Farms, a premier provider of fully automated turnkey systems for rapid production of legal cannabis, announced that noted cultivator, Kyle Kushman, has joined the company’s Advisory Board. Kushman is an internationally renowned legal cannabis cultivator who has earned 13 Cannabis Cups Awards.
Micro Lab Farms has made it possible for farmers, businesses, entrepreneurs and investors to enter or expand in the legal cannabis industry with its “GrowPod” cultivation systems.
GrowPods are modular, indoor micro-farms that utilize a clean, controlled environment to grow robust, fast-turn, healthy crops. The system uses state-of-the-art air and water filtration, proprietary pathogen-free living soils, and automation controls that together provides a highly advanced environment that outperforms other methods of cultivation.
The system eliminates pathogens, contaminants, pesticides and chemicals, and gives growers the ability to harvest clean crops with fast harvest times.
The system can be easily transported, allowing cultivation to take place virtually anywhere.
The GrowPod system from Micro Lab Farms is ideal for growers that want to keep genetics separated, add new strains, expand their operation, or enter the market.
Kushman says that Micro Lab Farms is providing several pathways to get involved in the legal cannabis industry.
“An existing business or farmer can have a Pod shipped to their location and it can be up and running in just days,” he said. “Or for a more hands-off approach, an investor or entrepreneur can have Pods delivered to the new California Cultivation Complex and have the entire process managed by our world-class experts.”
Further details on the California Cultivation Complex are available upon request.
For information on Micro Lab Farms, call: 800-320-0761, or visit: www.microlabfarms.com
Connect:
Website: www.microlabfarms.com
Facebook: facebook.com/MicroLabFarms
Twitter: @MicroLabFarms
Many Unanswered Questions, Concerns About CBD Products, Says FDA Acting Chief At First Public Hearing
The acting head of the Food and Drug Administration launched the agency’s first hearing on CBD products Friday with a laundry of list of questions about cannabidiol, better known as CBD, which is already being sold in pills, tinctures, skin lotions, sodas and dog food
You can buy CBD in oils, supplements, soda, even dog food. But most of them violates federal food and drug regulations, prompting concerns over safety and deceptive marketing.
A jar of CBD gummy candies at The Cannabis World Congress & Business Exposition trade show in New York City. REUTERS/Mike Segar (Mike Segar/Reuters)
By William Wan
May 31, 2019
The acting head of the Food and Drug Administration launched the agency’s first hearing on CBD products Friday with a laundry of list of questions about cannabidiol, better known as CBD, which is already being sold in pills, tinctures, skin lotions, sodas and dog food.
How much of the cannabis extract is safe to consume daily, he asked at the jam-packed, all-day hearing at FDA headquarters in Silver Spring. How will it interact with other drugs? What if a consumer is pregnant? What is CBD’s effect on children? What happens if someone takes it over the course of years?
Acting Commissioner Norman “Ned” Sharpless said answers to most of those questions are still unknown despite the popularity of many CBD products.
“There are important reasons to generally prohibit putting drugs in the food supply,” Sharpless said. And cannabis extracts like CBD “are no exception.”
During the 10 hours of testimony that followed, hemp growers, start-up businesses, academic researchers and consumer advocates argued about how FDA should regulate the already booming CBD industry. Some demanded strict oversight. Others — especially companies with millions at stake — lobbied for looser regulation.
But the common theme among them all: FDA needs to figure out its rules sooner, rather than later.
Even though FDA’s regulations make adding CBD to food and supplements illegal, the CBD industry has exploded in recent years with thousands of unproven products flooding the market. Companies have trumpeted the compound’s alleged health benefits — claiming it can reduce anxiety, pain and insomnia and treat conditions from Parkinson’s disease to cancer. But almost all such claims lack rigorous scientific proof, prompting concern among health officials and scientists about safety and deceptive marketing.
Without clearly defined regulations, no one knows for sure how much CBD is in products available on the market, or how safely the chemical compound is being manufactured and incorporated into them.
“It’s a wild West kind of environment right now,” said Yasmin Hurd, a psychiatry professor at the Icahn School of Medicine at Mount Sinai in New York City, who has researched CBD for almost 10 years. “I’m inundated every day with patients wanting to know how much CBD they should take, which ones to buy. But we don’t know what’s in the stuff now being sold. . . . We’ve had this explosion without guidance to the public or regulation.”
How the FDA will choose to regulate the industry and how long it will need to figure that out remain unclear. Those prospective regulations have become a fierce battleground: More than 400 people and groups applied for a chance to speak at Friday’s hearing, with roughly 120 speaking slots parsed out.
CBD can be derived from the marijuana plant or hemp. Congress in December legalized hemp as part of the Farm Bill, clearing the way for industrial production of the nonintoxicating compound from that plant. But the FDA quickly made it clear to companies that while hemp was legal, CBD extract remained under government regulation. In recent months, the agency has sent warning letters to some companies that it said were “illegally selling CBD products that claimed to prevent, diagnose, treat, or cure serious diseases, such as cancer.”
Billions are at stake in how the FDA decides to regulate the compound, with business analysts projecting the industry could grow to be worth as much as $22 billion in the next five years.
Market research firm New Frontier Data estimated that sales of CBD products in the United States more than tripled between 2014 and 2017, to $367 million.
Retailers like CVS and Walgreens have announced plans to sell CBD lotions and creams. Food and beverage companies have eagerly jumped in, too, with burger chain Carl’s Jr. selling CBD-infused burgers.
At Friday’s hearing, hemp growers argued that the CBD market represented thousands of jobs and a booming source of growth for the economy. CBD retailers relayed anecdotal evidence of patients who found relief to longstanding medical problems in their products.
Health advocates spoke equally passionately about the dangers posed by an unfettered CBD market.
So far, the agency has approved only one CBD-based drug, Epidiolex, which treats severe forms of childhood epilepsy.
In a phone interview, Orrin Devinsky, a New York University researcher who helped develop the drug, said the government’s haphazard approach has been frustrating to scientists trying to help suffering patients.
“You have researchers having to struggle through enormous expense and obstacles to study CBD,” he said. “At the same time, you can walk down to your neighborhood bodega and buy a CBD soda off the shelf. The nation and marketplace are in a horribly confused state.”
So far, treating epilepsy is the only application for CBD supported by rigorous scientific data, Devinsky said. Though less rigorous, some promising findings have emerged for CBD’s possible effect on anxiety and inflammation.
“The thing we worry about is someone with cancer forgoing real treatment like chemo and taking CBD instead,” said Devinsky, a neurology professor at NYU.
At Friday’s hearing, scientists and consumer advocates also warned that for the thousands of CBD products being sold, there is little data to guide dosage levels, expiration dates, and manufacturing protocols to make sure they don’t also contain other elements like tetrahydrocannabinol, or THC, the main psychoactive component in marijuana, which has been found in some CBD products.
Whatever the FDA decides, many in the industry are pressing for it to move quickly.
“I’ve talked to beverage companies and they want to get into this space, but they are not interested in just throwing themselves headlong into an area without science and engagement with regulators,” said Coleen Klasmeier, a former FDA staff lawyer and now partner at law firm Sidley Austin.
“For years now, the agency’s position has been just to throw up their hands and say it’s a confusing issue,” said Daniel Fabricant, a former FDA official overseeing dietary supplements, who is now chief executive of the Natural Products Association representing the supplement industry.
In addition to Friday’s hearing, the FDA has set a deadline of July 2 for written comments on the issue. It also convened a working group led by Deputy Commissioner Amy Abernethy to explore ways CBD products might be sold legally, the impact of such products on public health, and whether new FDA rules or congressional legislation may be needed.
In a string of tweets on Friday, Abernerthy summed up main points she and FDA officials were hearing over and over at the meeting: “Key questions about product safety need to be addressed. Data are needed to determine safety thresholds for CBD...There are both positive supporters of cannabis-cannabis derived products including CBD and also concerned citizens worried that widely available products can be harmful.”
Vertical Farming For Cannabis Gets Trial Run in Langley
Leo Benne, chief growing officer of Zenabis, with the converted shipping container that will become a testbed for a vertical cannabis farm. (Matthew Claxton/Langley Advance Times)
Grower Zenabis Will Start With Industrial Hemp And May Move to
Commercial Marijuana
Jun. 6, 2019
Zenabis, which merged with longtime Langley greenhouse firm Bevo last year, has received a hemp cultivation license from Health Canada, with growing to take place in Langley, Pitt Meadows, and Aldergrove facilities.
“We expect the seed to come in this week,” said Leo Benne, chief growing officer for Zenabis.
A small portion of that seed will be planted not in one of the greenhouses facilities, but in a converted shipping container, as a test on whether cannabis can be vertically farmed.
Bevo has already helped develop a vertical farming system through CubicFarms, a Pitt Meadows-based spin off.
Vertical farming involves growing large amounts of crops on small amounts of space, indoors, and usually without any soil.
Plants are reared in racks, stacked as high as the building or container can accommodate, and grown either hydroponically or aeroponically.
Energy efficient LED lights allow the plants to grow 24 hours, seven days a week, in any weather.
In theory, the cost of the equipment and intensive rearing is offset by the ability to grow non-stop and to place the growing site much closer to the end-consumer. Rather than trucking lettuce from California or Mexico, it could be grown just a few miles outside of Canadian cities and shipped just a few kilometres.
The hemp vertical farm is just a test at this point, said Benne. A single converted shipping crate has been hauled into one of the Zenabis greenhouses in Langley and will be ready for its test run at about the same time as 20 acres of industrial hemp is planted in the three facilities, from Langley to Pitt Meadows.
While most crops planted in vertical farms are extremely low-growing, allowing for many racks close together, cannabis is usually a tall-growing crop.
Benne said that a combination of the plants chosen and growing practices is expected to keep the plants shorter for the vertical farm project.
If the project goes well, vertical farming facilities could be used for growing commercial marijuana, said Zenabis CEO Andrew Grieve.
The industrial hemp isn’t being grown for commercial marijuana sales. Instead, the hemp will be processed into CBD oil, fibre, or other derivatives. The project is separate from Zenabis’s plans for growing commercial cannabis in Langley.
While Langley’s other large cannabis cultivator has caused controversy in Aldergrove over smell issues, Benne doesn’t believe that will be an issue for Zenabis.
“We’re doing things a lot differently,” he said. “First of all, we’re constructing a closed greenhouse facility. We’re able to keep most of the air inside the greenhouse.”
There are to be no roof vents, which should not only control odour, it helps the growers control humidity and other issues.
“Because we don’t have that exchange of air with the outside, we don’t have a lot of pest issues,” he said.
Air exhaust is to be controlled through carbon filters, and if those aren’t sufficient, biofiltration. That means basically pumping all the air exhaust through a big box full of bark and cedar chips to absorb the smell.