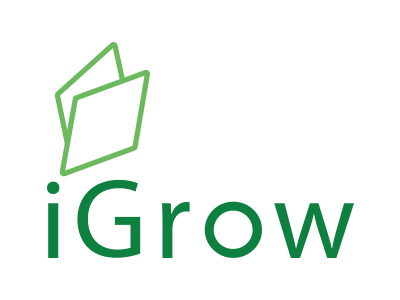
Welcome to iGrow News, Your Source for the World of Indoor Vertical Farming
SINGAPORE - VIDEOS: How IoT And Machine Learning Are Automating Agriculture
A new generation of farmers is tapping the internet of things and machine learning to operate self-sustaining urban farms with minimal supervision
A New Generation of Farmers Is Tapping The internet of Things And Machine Learning To Operate Self-Sustaining Urban Farms With Minimal Supervision
By Aaron Tan, TechTarget
21 Jul 2021
A new generation of farmers is turning to technologies such as the internet of things (IoT) and machine learning to automate agricultural production, alleviating the need to toil on the land while keeping a watchful eye on their crops.
Joining their ranks is Phoebe Xie, director, and co-founder of Singapore-based agrotechnology startup AbyFarm. Teaming up with technology service provider SPTel, Xie is building a smart hydroponics farm in a greenhouse that uses a plethora of IoT sensors, including video cameras, to keep the farm humming around the clock.
“To run a self-regulating farm at the optimal temperature with optimal water and nutrient supply, and to control the quality and taste of vegetables and fruits, we need IoT sensors,” she said, adding that the farm and its sensors collect and monitor thousands of data points, including humidity and temperature.
With the data and in certain environmental conditions, processes and actions are automatically triggered to protect crops from the elements. For instance, if the temperature or humidity gets too high, fans, water curtains, and roof shades are activated in the greenhouse.
Xie said the smart farm, located at a rooftop carpark in Singapore, is also equipped with sensors that monitor the pH and electrical conductivity levels of water. Among the sensors, which are connected to a Lora low-power wide area network, is a dozer that automatically releases acidic or alkaline nutrients to maintain optimal pH levels.
Whereas the farmers of old had to physically inspect their crops, AbyFarm’s agronomists and farmers can do so remotely using video cameras and image recognition technology to identify crops that might be succumbing to disease.
“If the image recognition finds that a plant is likely to be sick, the farmer will be alerted to go onsite to check how the plant is right now,” said Xie, adding that agronomists will also advise farmers on taking corrective actions to prevent disease or restore the health of their crops.
Like any machine learning system, AbyFarm’s algorithms get smarter over time. Each time a crop is affected by disease, data about the occurrence and corrective action is fed into the system, enabling its algorithms to formulate solutions for other farmers with similar crop issues – without consulting an agronomist.
With that, said Xie, even those who are new to the field can use the system to guide them on treating diseased crops, which can be isolated from other crops to prevent cross-infections.
AbyFarm’s automated farming system, which is hosted on SPTel’s private cloud, can also advise farmers on the best time to transplant their crops after germination and harvest them later for sale, said Xie.
Heng Kwee Tong, vice-president for engineering and customer solutions at SPTel, said the company has built up a software-defined platform to help companies like AbyFarm overcome the challenges of deploying applications such as IoT.
“The common struggle that companies like AbyFarm face with building an IoT solution is that it is quite intensive in terms of ICT infrastructure,” said Heng. “You’ve got to find the radio connectivity like Lora, subscribe to a service provider, and connect your sensors to a sensor collector.
“We make it easy by investing in a platform and because we are a service provider with edge hub assets for deploying radio connectivity, all AbyFarm needs to do is to bring their sensors onboard.”
Going forward, Heng said SPTel is looking to support next-generation video analytics capabilities through edge cloud services that can be used to crunch workloads closer to where they reside, reducing latency.
AbyFarm was one of six companies to win contracts from the Singapore Food Agency last year to build urban farms at nine rooftop carparks in public housing estates across Singapore.
The goal is to collectively produce about 1,600 tonnes of vegetables a year in a bid by the city-state – where less than 1% of the land is used for agriculture – to become more self-sufficient in meeting the nutritional needs of its people.
That could well be achievable with technology that makes farming more efficient, scalable, and less labor-intensive than before. “We are willing to train and educate the next generation in agrotechnology because now you don’t need 10 farmers to take care of one farm,” said Xie. “It’s just looking at the dashboard and, with the alerts, doing what is required.”
Large-Scale Automated Vertical Farm Near Tokyo by Spread And ENEOS Partnership
Techno Farm Narita is Spread’s first partnership project and the first to be located in Eastern Japan
July 14, 2021, Spread Co., Ltd. (HQ: Kyoto, Japan; CEO: Shinji Inada, hereinafter “Spread”)’s partner, and a member of ENEOS Group, J Leaf Corporation (HQ: Chiba, Japan; President: Jun Uehara, hereinafter “J Leaf”) started operating the automated vertical farm “Techno Farm Narita” (Chiba, Japan) on 30th of June.
Spread’s Large-Scale Vertical Farming Partnership with ENEOS Group’s J Leaf Starts Operations near Tokyo
Spread owns and operates two vertical farms in Western Japan (Kyoto), the Kameoka Plant and Techno Farm Keihanna. Techno Farm Narita is Spread’s first partnership project, and the first to be located in Eastern Japan. The most significant feature of Techno Farm Narita is the increased efficiency in the use of land. This has been achieved by increasing the number of cultivation racks levels to 28, double that of Techno Farm Keihanna. Techno Farm Narita will produce 30,000 heads of lettuce daily, building on the know-how accumulated through the operation of Techno Farm Keihanna to deliver increasingly sustainable food production.
Unique Features of Techno Farm Narita
Even more efficient land saving through 28-level cultivation rack system (roughly 2 times more efficient than Techno Farm Keihanna)
Located in the Greater Tokyo Area, allowing for local production and consumption
Transforming idle land to efficient and sustainable agriculture ・
The utilization of renewable energy generated from solar panels
Techno Farm Narita also retains other features of Spread’s next-generation food production system, Techno Farm™, including pesticide-free, stable cultivation, integrated automation, specialized LED lighting, and Spread’s proprietary IoT-based cultivation management system, Techno Farm Cloud.
Techno Farm Narita’s Cultivation Room Opening Ceremony
About the Partners
ENEOS Group is one of Japan's leading corporate groups, with revenue in excess of 10 trillion yen. *1
The Group has the largest market share in oil refinery and petrochemicals distribution in Japan and is centered around ENEOS Holdings.
Spread’s vision is to create a sustainable society where future generations can live with peace of mind. On the way to this objective, Spread plans to reach a total production capacity of 100 tons per day domestically by 2030, through the expansion of its Techno Farm™. With the collaboration at Techno Farm Narita as a foundation, both parties are considering further partnership projects. The green business market is expected to continue growing, and Spread strives to become a leading vertical farming company globally.
Spread will continue to pursue further business opportunities through technological innovation both in Japan and overseas. Spread aims to provide solutions for the global problems of climate change and food security and the delivery of a truly sustainable society.
*1 FY2019 results (announced on May 20, 2020)
*2 ENEOS Techno Materials Corporation is a member of ENEOS Group
Applying Automated Warehouse Systems To Indoor Farming
“At Swisslog, we don’t have standard solutions in place for vertical farms yet. But due to our long-lasting expertise both in the food industry and in the distribution of fresh products to the point of sale, we understand the supply chain processes and linked to that shelf life considerations.”
“History is written in circles as we observe similar drive for automation in indoor farming, as we saw years ago in the intralogistics sector. There are yet few important differences,” says Timo Landener, product innovator at Swisslog.
Swisslog, with the vision to shape the future of intralogistics, not only develops warehouse automation and software solutions to reduce costs and introduce flexibility to warehouse-based operations but also looks into innovative future-proof approaches. In March 2021, Swisslog announced its foray into the vertical farming market. While Swisslog has not specifically designed systems for vertical farming, its vast portfolio of automation solutions can be adapted to vertical farms, whether pre-existing or purpose-built.
Timo Landener
“At Swisslog, we don’t have standard solutions in place for vertical farms yet. But due to our long-lasting expertise both in the food industry and in the distribution of fresh products to the point of sale, we understand the supply chain processes and linked to that shelf life considerations. Moreover, our portfolio can be easily adapted to indoor farming since the payload is fairly light, the throughput is not critical and the automation operations demand low power compared to the needs of the intralogistics automation,” explains Timo. “Nevertheless, we already learned, that we can't just adopt the same requirements, because plants are living organisms. And we have to respect that.”
Although unable to reveal their clients, Swisslog has reportedly demonstrated its technologies in the vertical farming industry with success to allow growers to reduce operational costs and increase scalability. Examples of innovative systems applicable to vertical farming include the PowerStore high-density storage system, the AGV based good-to-person order fulfillment solution CarryPick, the Tornado mini-load crane and the Vectura stacker crane.
When does automation become economically feasible?
Automation can be applied to multiple processes in an indoor farm including seeding, harvesting, packaging, tray manipulation, etc. However, Timo explains that automation is capital-intensive and best suited for large-scale indoor farms. A higher production level introduces more opportunities to increase operational efficiency and reduce labor requirements.
“Even Amazon began in a small space with little automation. Then, they reached a level where automation made sense. In the vertical farming industry, we need to discuss with clients where the tipping point is for needing automation,” says Timo.
To determine which automation solutions are right for the grower, Swisslog’s automation experts work directly with clients to identify opportunities for increased operational efficiency and customize solutions according to the farm’s architecture. Additionally, the close relation with KUKA as the parental company allows collaboration opportunities to automate and incorporate the sub-processes in an Indoor Farm to a more turnkey solution.
Harvest-on-demand
Timo explains that despite the relatively short distance between urban indoor farms and retailers, a major challenge to indoor farming is the logistics of transporting farm-grown products to retailers while maintaining crop quality.
“After the plants have grown in a perfect environment, they are cut and immediately begin to lose quality. The current challenge is to speed up the process of getting the products to the retailer. Pursuing the innovative approach of harvesting-on-demand, we can make sure that the end customer receives fresh and rich nutrition vegetables. With a palette of automated solutions this is finally possible,” says Timo.
Swisslog’s ties with global retailers started long ago as the Swiss Company delivered solutions for huge automated projects (distribution centers) as well as smaller, more local applications, known as Micro-Fulfillment Centers. Harvesting-on-demand differs from mainstream distribution models by supplying retailers with living plants, which can continue growing until they are purchased.
This process can be carried out in retailers’ “back shops” and would support additionally retailers to fulfill three major sales channels: in-store sales, home delivery and BOPIS (buy online, pick up in-store). Swisslog is certain that we are at the edge of a revolution in food the supply chain: There will be the need for Indoor Farms at the point of sales: a “fresh food on the demand-supply grid”. We see automation as a means for leveraging the indoor farms and help them deliver efficiency that will lower the entry threshold for further investments.
Retailers are a fundamental part of this revolution. “Many indoor farms are currently selling to retailers. Due to the fact, that the retailers sell the crops, they determine how the supply chain will look like. Thus, the power of re-designing the process of the supply chain and ensuring consistency in the circular economy lies in their hands. As for today, the complexity and ramifications of the matter inspire us to join forces with retailers and find out how to react in the best way to changing needs of the customers and the industry. We are on the verge of something new and powerful. Swisslog, an intralogistics automation leader, together with retailers and farming experts, we can deliver a great added value for consumers” explains Timo.
For more information:
Timo Landener, product innovator
Swisslog
timo.landener@swisslog.com
www.swisslog.com
Publication date: Thu 3 Jun 2021
Author: Rebekka Boekhout
© VerticalFarmDaily.com
Pontus Files International Patent Application For Automated Vertical Farm Harvesting Robot
Pontus' initial crop, water lentils, is the fastest-growing leafed plant.* Pontus' CEVAS helps accelerate the growth of Pontus' water lentils, requiring the plant to be harvested every 24 hours
NEWS PROVIDED BY
Jun 09, 2021, VANCOUVER, BC, June 9, 2021 /CNW/ - Pontus Protein Ltd. (TSXV: HULK) (OTCQB: HLKKF) (FSE: 8YC) ("Pontus" or the "Company"), is pleased to announce that it has filed an international patent application through the Patent Coordination Treaty with the World Intellectual Property Organization for Pontus' proprietary Harvesting Automated Robotic Vehicle or "HARV" for short. HARV is a vertical farm rack system and automated plant tending and harvesting robot designed to work alongside and assist Pontus' Closed Environment Vertical Aquaponics System or CEVAS system.
Pontus' Harvesting Automated Robotic Vehicle or “HARV” for short. HARV is a vertical farm rack system and automated plant tending and harvesting robot (CNW Group/Pontus Protein Ltd.)
Pontus' initial crop, water lentils, is the fastest-growing leafed plant.* Pontus' CEVAS helps accelerate the growth of Pontus' water lentils, requiring the plant to be harvested every 24 hours. Pontus developed the HARV technology to allow the crop to be automatically harvested daily. In addition, due to its low profile, HARV will enable Pontus to stack nine levels of vertical farming at its Surrey, British Columbia production facility.
Steve McArthur, Chief Technology Officer, Pontus, stated, "Talking with the experienced team at Automation Experts (an automation and innovation company based in Calgary, Canada), we were able to identify that there was no robot out there that handled everything we needed it to do. By harvesting the crop in situ, using HARV, we will reduce the space between the water beds and increase the number of levels, increasing efficiency and the yield. We are beyond excited about pairing HARV with our CEVAS system, as we see CEVAS as a greener, more ecologically sustainable way of producing high nutrition food products."
Stephen Bruce Wong, CEO, Automation Experts, added, "HARV is more than a mechanical tool for harvesting. It will manage the farm and give us critical insight and data regarding the optimization of the growing environment. The robotics in HARV will allow Pontus to eliminate moving parts from the structure thus lowering the cost to build Pontus' vertical farms as the water beds can be dumb and do not need the technology built into them. It also uses machine learning and artificial intelligence to support all aspects of the growing process."
The patent filing is part of the technology leadership in the aquaponic space that Pontus continues to secure.
About Pontus Protein Ltd.
Pontus Protein Ltd. is a Vancouver, B.C. based technology company that grows water lentil protein for commercial use. Pontus is reinventing agriculture with their proprietary Closed Environment Vertical Aquaponic System (CEVAS) – the farming of the future. Pontus specializes in the indoor vertical farming of water lentils that use 95% less water than traditional agriculture and no pesticides or chemicals. Pontus is committed to solving the global food crisis by providing access to sustainable indoor biosecure pure plant-based proteins. Pontus' water lentils can be harvested every 24 hours, exceed organic certification, and can be grown in any climate in a relatively small area. Our water lentil protein is filled with antioxidants, minerals, vitamins, and all the amino acids, making a complete protein food source. Pontus aims to revolutionize the plant-based sector as the entire sector is currently based on two main protein sources: soy and pea. Water lentil protein is far superior to pea and soy protein. It contains over 40% protein vs. 5-36% protein*, and Pontus aims to be the base protein for nutrition-rich plant-based food products and nutraceuticals to support the movement transitioning the world from meat-based to plant-based proteins.
To learn more, please visit pontuswaterlentils.com.
*https://www.infood.net/visitor/collection/75?portion_size=100
*https://www.zmescience.com/science/fastest-growing-plant-02022021/
On behalf of the Board of Directors
"Connor Yuen"
Connor Yuen, CEO
Pontus Protein Ltd.
Contact Information
For more information, please contact:
Connor Yuen
Chief Executive Officer
https://pontuswaterlentils.com/company/#contact
Forward-Looking Information
Certain statements in this release are forward-looking statements, which reflect the expectations of management regarding the Company. Forward-looking statements consist of statements that are not purely historical, including any statements regarding beliefs, plans, expectations or intentions regarding the future, including but not limited to Pontus' ability to revolutionize the plant based sector. Such statements are subject to risks and uncertainties that may cause actual results, performance or developments to differ materially from those contained in the statements, including risks related to factors beyond the control of the Company. These risks include, but are not limited to, the following: the unknown magnitude and duration of the effects of the COVID-19 pandemic, the failure of Pontus to receive the necessary approvals from the Canadian Food Inspection Agency for its products and facilities, the inability to complete Pontus' Surrey-based production facility, as well as other general business, economic, or market related risks beyond the director control of the Company and which may affect the Company's business, operations, or products. No assurance can be given that any of the events anticipated by the forward-looking statements will occur or, if they do occur, what benefits the Company will obtain from them. The Company undertakes no obligation to update forward-looking information if circumstances or management's estimates or opinions should change, unless required by law. The reader is cautioned not to place undue reliance on forward-looking information.
Neither the TSX Venture Exchange nor its Regulation Services Provider (as that term is defined in policies of the TSX Venture Exchange) accepts responsibility for the adequacy or accuracy of this release.
SOURCE Pontus Protein Ltd.
For further information: Investor Relations or Media enquiries: invest@pontuswaterlentils.com, (403) 589-7992
Organization Profile
Pontus Protein Ltd.
'Automation Is Needed To Reduce Costs And Improve Efficiency'
“We believe that automation can play a decisive role in delivering fresh produce for the most diverse uses and make agriculture accessible to many," says Giuseppe
There is so much to win regarding safety and workforce availability that traditional farming won’t help us with,” says Prof. Dr. Giuseppe Pasciuti, Marketing Strategist and Board Member at ONO Exponential Farming. For this particular reason, automation is the key to agricultural acceleration.
“We believe that automation can play a decisive role in delivering fresh produce for the most diverse uses and make agriculture accessible to many," says Giuseppe. He continues, "automation can also limit low labor availability in the agricultural sector. It could even, as we have experienced during the pandemic, restrict the access of pathogens or viruses in food production. We at ONO/EF believe that automation is the key to match the new era for indoor farming ”
Full automation
ONO/EF Farms allows growers to remotely control all growing operations. Through automation, ONO/EF Farm is continuously generating new growing conditions for plants, in terms of climate conditions and the right mix of nutrients according to each crop type and its growth stage. Giuseppe says that automation allows them to reduce CapEx and operation costs dramatically.
ONO E/F's idea of vertical farming does not require Giga farms to make the investment sustainable. Giuseppe says that "the company isn't keen to build the largest farm in the world, but a distributed network of connected farms close to consumers. Because in this industry, collaboration is key.”
According to Giuseppe, the vertical farming industry needs profitability in combination with sustainability. “For that reason, we have developed ONO Exponential Farming. Our advanced technological platform, which is completely robotized, supported by AI and our algorithms,” he says.
ONO / EF provides 100% of the production infrastructure, from seeding to finished product packaging.“We are redefining the concept of farming by constantly update and improve our algorithms and AI. In this way, we can make farm operations more effective and efficient.
Experience
ONO/EF has been a technology provider in industrial automation for 20 years. The vertical farming industry is known for its rapid development in terms of techniques and automation.
“Our company is already witnessing the introduction of automated elements that we consider outdated. Functional automation is linked to complete processes that allow human intelligence to concentrate on value-added activities. Activities such as studying plant physiology and identifying cause-effect relationships in growth processes," Giuseppe says.
For more information:
Giuseppe Pasciuti, Marketing Strategist and Board Member
ONO Exponential Farming
giuseppe.pasciuti@onoef.com
https://onoexponentialfarming.com
26 May 2021
Author: Rebekka Boekhout
© VerticalFarmDaily.com
Blue Radix & Ecoation Join Forces With The World's 1st Autonomous Find & Fix Solution
May 19, 2021, Rotterdam, Netherlands and North Vancouver, Canada
Blue Radix, an independent Dutch AI-tech specialist for the international greenhouse industry, and Ecoation Innovative Solutions Inc. (ecoation), a Canadian developer of automated greenhouse management and crop health monitoring technologies, have signed an agreement.
The collaboration aims to identify new ways to automate decision-making and action in the greenhouse, using vision technology and algorithms. ecoation and Blue Radix are using the data collected by ecoation’s OKO and platform to enhance the impact of Blue Radix’ algorithms for autonomous growing. By combining data sets, algorithms, and analytical efforts the companies are able to create new insights and applications that help growers worldwide to improve their crop strategy, quality and yield.
Blue Radix and ecoation look forward to ongoing collaborative efforts where the duo explores the multitude of innovation opportunities that become available when you combine ecoation’s OKO and platform with Blue Radix’ Crop Controller. Collaborating across data and algorithms has the potential to create value across many avenues, including optimizing crop strategy, autonomous steering, IPM enhancement, and understanding spatial climate distribution.
The World’s 1st Autonomous Find & Fix Solution
The first project the duo is working on is enhanced autonomous growing with crop data visualization. ecoation’s OKO collects sensory data and information about climate, integrated pest management, and crop work at every row and post to an SqM granularity. These insights greatly contribute to a complete and accurate view on the state of the crop. The broad range of data points, including fruit count, fruit colouring, and stem density, will be combined with the smart steering algorithms of Blue Radix’ Crop Controller. Crop Controller will actively, continuously and autonomously control the greenhouse conditions with the grower’s crop strategy as its starting point and the optimal crop status as its goal. E.g. by optimizing the plant load, plant stress is reduced avoiding weak plants that are vulnerable to pests and diseases. In this way ecoation and Blue Radix find and fix imperfections before they impact yield or crop quality.
Support growers
“Collaborating with Blue Radix means pioneering the future of ag more effectively, at a pace that would be difficult to reach if we carried on separately,” shared ecoation CEO Dr. Saber Miresmailli. “Both teams are committed to the same goal: to support growers in making the best possible decisions. Working together means unlocking new ways to get the most from the data and providing better insights to our customers that inform their decisions.”
“Ecoation offers solutions which are important components in a fully autonomous greenhouse. Optimization and steering with algorithms depends on high quality data and a robust crop strategy. Vision technology and enhanced analytics from ecoation provides this data and the necessary input to improve the grower’s crop strategy even further,” emphasizes Blue Radix CEO Ronald Hoek. “We strive for open collaboration and partnerships. Growers should always be able to choose freely what they want to do with their data and benefit from the best combination of services & products for their greenhouse.”
The duo will only work with greenhouse data retrieved from the customers of ecoation and Blue Radix who provide full consent. Transparency and data security is paramount, and this collaboration will rely on growers who are looking to optimize their greenhouse operations with autonomous processes and are interested in contributing to the future of ag with their facility data and insights.
About Blue Radix
Blue Radix is an independent Dutch AI-tech specialist for the international greenhouse industry. Blue Radix creates solutions with artificial intelligence for daily decisions and actions in greenhouses. Greenhouses offer an efficient way to produce food and flowers in a sustainable manner. But the number of skilled people with expertise of growing crops in greenhouses is declining every year. This has a direct and negative impact on yield, costs, continuity, and product quality. Blue Radix offers solutions for these challenges: smart algorithms which optimize and steer climate, irrigation, and energy continuously and autonomously, supported by off-site
Autonomous Greenhouse Managers. Blue Radix offers growers a digital brain for their greenhouse. More information at blue-radix.com. Find Blue Radix on LinkedIn, Twitter, and Instagram.
About ecoation
ecoation is an award-winning grower-centric platform that combines Human knowledge and experience with Machine precision and automation to increase operational visibility, assist growers, and enhance their decisions. Commercially available since September 2019, ecoation products can be found in greenhouses across the United States, Canada, Mexico, and Europe. With an experienced team of 60+ growers, scientists, engineers, and business professionals from all over the globe, ecoation is passionate about enabling a cleaner future and supporting growers in making the best possible decisions. At ecoation, we are on a mission to empower growers because we believe in doing so, we win together.
More information at ecoation.com. Find ecoation on LinkedIn, Twitter, and Instagram.
For media inquiries, please contact:
Blue Radix
Marijke van Rongen
Manager Global Marketing & Communications
marijke.vanrongen@blue-radix.com
+31 6 53 43 38 39
ecoation
Marketing and Media Contact
Cameron Lust
Taking Indoor Farming Operations To New Heights
Conveyor systems technology can help indoor farming operations grow to new heights while improving productivity, efficiency and ergonomics, according to Ultimation Industries LLC, a leader in conveyor technology and automation for over 30 years
Conveyor Systems Technology From Ultimation Industries
Conveyor systems technology can help indoor farming operations grow to new heights while improving productivity, efficiency and ergonomics, according to Ultimation Industries LLC, a leader in conveyor technology and automation for over 30 years.
“Harnessing unused vertical space through the use of motorized and overhead conveyors helps indoor farmers maximize their footprint while achieving greater efficiencies in food production and improved ergonomics,” said Richard Canny, president of Ultimation Industries.
Customized and automated
Ultimation is a provider of customized conveyor and automation solutions for indoor agriculture. They design and build systems for vertical farms of all sizes, including a major system for a West Coast-based vertical farming system which is among the world’s largest.
In a typical indoor agriculture facility, workers move through the growing area to plant, monitor and harvest crops. Multi-tier operations may use time-consuming and potentially dangerous lifts to take employees up and down as they perform their daily tasks. Conveyor technology can move plants through automated systems as they grow, bringing them down to the operator level when needed for more efficient, and ergonomically friendly, handling.
Multiple choice
The conveyors and industrial automation equipment used in vertical farming include many of the traditional conveyor types such as gravity roller, belt, and skate wheel or flow rail conveyors. These conveyors are among the most versatile because they help reduce the manual labor of carrying items by hand.
Larger systems use vertical elevators or Power and Free conveyors. Power and Free conveyors are the ultimate in space and volume optimization for vertical farming systems as they enable tight concentration of product in some areas while also enabling separation of the products for movement to processing areas.
Reducing costs
More recently, the technology used in larger vertical farming systems is including motorized and overhead conveyors. These systems take advantage of unused vertical space above a working area and bring plants down to an operator level when needed.
“Using robotics and conveyors has been shown to help vertical farms maximize their growing operations and reduce costs. We believe that indoor farming systems are best optimized through a balanced use of low-cost material handling systems for slow-growing areas. They are complemented by more sophisticated conveyors and other devices for faster moving material handling tasks,” said Canny.
Ultimation’s indoor agriculture solutions range from simple flow rail systems up to more comprehensive systems for larger indoor vertical farming facilities. The company's systems meet food-safe requirements for lubricants, oils, and greases.
“As indoor farmers work to achieve greater efficiencies in food production, conveyor systems technology is likely to be part of any economically viable and scalable solution,” said Canny.
For more information:
Kali Cresent, Sales, and Marketing Manager
Ultimation Industries, LLC
kcresent@ultimation.net
+1 586-771-1881
www.ultimation.net
9 Apr 2021
The World’s First Autonomous Greenhouse Manager
Geert van der Wel started in the role of Autonomous Greenhouse Manager at Blue Radix. He represents the human support side of the Crop Controller service in addition to the smart algorithms that control greenhouses
07-04-2021 | Goedemorgen
Early February, Geert van der Wel started in the role of Autonomous Greenhouse Manager at Blue Radix. He represents the human support side of the Crop Controller service in addition to the smart algorithms that control greenhouses. Read more about how Geert helps customers and about his background. As he says himself: "I was almost literally born among tomatoes in De Lier, where my parents had a tomato greenhouse."
Name: Geert van der Wel
Home: I’ve been married to Tessa for 16 years and we have two children. We have lived in Burgundian West Brabant since 1998.
Childhood: Almost literally, I was born among the tomatoes in De Lier, where my parents had a tomato greenhouse.
Study: I completed Secondary Horticultural School in De Lier, and also undertook several (horticultural) studies.
Work experience: I worked in my parents’ tomato greenhouse right from my childhood. After finishing my studies my partner and I became owners of Kwekerij Polderwel for ten years, growing tomatoes on 2.5 hectares. We wound up this undertaking because of the construction of the A4 highway between Antwerp and Rotterdam. Then I did three years as a manager at the Nuijten plant nursery, and when this firm ceased trading I ended up at Nickerson-Zwaan in Made; it later became known as Hazera Seeds. For the first four years, I worked in the Planning & Control department, moving on to become Product Manager High-Tech Tomatoes for the final five years.
What can you do for growers as an Autonomous Greenhouse Manager?
“Blue Radix offers autonomous growing as a service. So alongside our smart algorithms controlling the greenhouse, our Crop Controller service also has a ‘human side’, and customers get daily support from an off-site Autonomous Greenhouse Manager (AGM). So as that AGM I’m constantly looking over the customer’s shoulder, and I’m their first point of contact. Right from the start, I guide clients intensively in taking their first steps into the world of algorithms. They are given an extensive onboarding program where they get explanations on the steps to autonomous growing, the operation of the algorithms, and the Crop Controller portal. I also monitor the management of the greenhouse continuously and discuss the progress on a regular basis, including through reports. My work experience has taken me through all the processes involved, from seed to the final product. This is what enables me to support our customers fully as AGM, to advise them, and to help them to realize their crop strategies.”
Blue Radix offers autonomous growing as a service; why is this important?
“Cultivation is the core business of every greenhouse company. To leave this completely to autonomous control requires a lot of trust from the customer. We are very aware that autonomous growing is still quite new and innovative. Providing good service with the support of the AGM lets us guide growers fully in working with algorithms. Our experience shows that customers are more likely to abandon their own processes and working methods step by step because there’s always someone monitoring the entire process.”
Describe your day. How do you monitor greenhouses worldwide?
“Every day I open the Crop Controller portal to see how the algorithms are behaving in terms of our various customers’ crop strategies. I contact the grower if any anomalies appear, or if there’s a technical issue I get in touch with the Blue Radix product developers. This also applies to feedback I receive from customers on how we can optimize Crop Controller still further.”
What do you like about your job? And what are your views on autonomous greenhouse management?
“In the horticultural world, it’s great to see that there’s a continuous search for innovations, and specifically for autonomous growing. I used sensors and digital tools on a small scale when I was a grower myself. But at that time I got very little guidance on how they worked and how to interpret it all. Now I use this experience to give our customers good information so that ultimately they’ll be able to grow autonomously in the best possible way!”
Got a question for Geert, or about autonomous growing generally?
Send us a message, and we’ll be happy to help you.
Vertical Farming Startup Oishii Raises $50m In Series A Funding
“We aim to be the largest strawberry producer in the world, and this capital allows us to bring the best-tasting, healthiest berry to everyone.”
By Sian Yates
03/11/2021
Oishii, a vertical farming startup based in New Jersey, has raised $50 million during a Series A funding round led by Sparx Group’s Mirai Creation Fund II.
The funds will enable Oishii to open vertical strawberry farms in new markets, expand its flagship farm outside of Manhattan, and accelerate its investment in R&D.
“Our mission is to change the way we grow food. We set out to deliver exceptionally delicious and sustainable produce,” said Oishii CEO Hiroki Koga. “We started with the strawberry – a fruit that routinely tops the dirty dozen of most pesticide-riddled crops – as it has long been considered the ‘holy grail’ of vertical farming.”
“We aim to be the largest strawberry producer in the world, and this capital allows us to bring the best-tasting, healthiest berry to everyone. From there, we’ll quickly expand into new fruits and produce,” he added.
Oishii is already known for its innovative farming techniques that have enabled the company to “perfect the strawberry,” while its proprietary and first-of-its-kind pollination method is conducted naturally with bees.
The company’s vertical farms feature zero pesticides and produce ripe fruit all year round, using less water and land than traditional agricultural methods.
“Oishii is the farm of the future,” said Sparx Group president and Group CEO Shuhei Abe. “The cultivation and pollination techniques the company has developed set them well apart from the industry, positioning Oishii to quickly revolutionise agriculture as we know it.”
The company has raised a total of $55 million since its founding in 2016.
Is All White Light the Same - Webinar
In this free webinar, we break down the differences among different types of white horticultural lighting. We will present the results of comparative plant trials we conducted using a variety of our own and other LED providers’ luminaires
More and more LEDs are going from purple to white. Is there any difference among the countless white LED light options on the market, in addition to fluorescent? Cool white, warm white, full-spectrum white, fluorescent, white with UV and far red, etc. How to evaluate these choices?
In this free webinar, we break down the differences among different types of white horticultural lighting. We will present the results of comparative plant trials we conducted using a variety of our own and other LED providers’ luminaires.
Spectra appearing white to human eyes contain a variety of spectrum colors, including green. Humans can distinguish them in terms of their temperature (e.g. warm white and cool white) and CRI (color rendering index) which determines how realistic objects appear under them.
Plants however can have dramatically different reactions to light that appear nearly the same to us. The example here shows the difference in biomass accumulation from three light sources that look exactly the same!
This webinar is aimed at growers and researchers trying to understand which kind of light to illuminate their growth chambers, indoor farms, and greenhouse compartments with.
Register for the webinar here.
Contact Valoya sales here - sales@valoya.com
About Valoya
Valoya is a provider of high-end, energy-efficient LED grow lights for use in crop science, vertical farming, and medicinal plant cultivation. Valoya LED grow lights have been developed using Valoya's proprietary LED technology and extensive plant photobiology research. Valoya's customer base includes numerous vertical farms, greenhouses, and research institutions all over the world (including 8 out of 10 world’s largest agricultural companies).
Additional information:
Valoya Ltd, Finland
Tel: +358 10 2350300
Email: sales@valoya.com
Web: www.valoya.com
Facebook: https://www.facebook.com/valoyafi/
Twitter: https://twitter.com/valoya
"We’re Retrofitting With The Variables We Have In Place"
Planted Detroit introduces new 20.000 sq. ft. growing facility
“The Square Room is a big block of pink lights with eight levels, where all our growing is done. Everything after germination is done in the same room, both harvesting of our baby greens and microgreens. Because we’re almost done with our PARS (Planted Automated Racking System), which is the big automation,” says Megan Burritt, Managing partner at Planted Detroit.
From a mix-fused downtown neighborhood in Detroit, daily deliveries of ready-to-eat salads and fresh greens are transported to local retailers and restaurants. Planted Detroit makes a large contribution to the city’s share of fresh produce.
New facility
Planted Detroit has been in the middle of the construction of its new 20.000 sq. ft growing facility. The growing space has been a massive update to the company compared to its previous 6-level growing facility which was between 1500-2000 sq. ft. The same room was used for processing, packaging, harvesting, and so on. “It was rather crowded, says Megan, but the main goal was to keep everything tight for the construction to continue in the near surrounding. We’re very serious about biosecurity and we have a daily procedure for everyone who sets foot in our grow room to go through. Making sure our greens don’t come into contact with pathogens is our top priority.
The new growing room
The Square Room, one of our growing rooms, is highly automated, including an automatic harvester to ensure work-efficiency. Once everything is big enough to be transplanted out of their plug trays, PARS (Planted Automated Racking System) will be transplanted with gutters and then go into harvesting. On the other side of PARS, the gutters are taken down and harvested through Planted’s new automatic harvester.
Delivering directly to consumers
The company wants to reach a higher volume of customers as it’s aiming to obtain a consumer brand status. Next to that, the company is always on the lookout for finding more customers through other venues. “We want to go directly to consumers via our web-store to shorten food miles as much as possible, delivering the freshest and most delicious greens,” Megan says. In order to do that the company needed to have a bit more scale, trying to maximize the space they already had.
She adds: “Our farm maybe isn’t the square footage which we could have built from scratch, but we’re retrofitting with the variables we have in place. That is why we have done a combination of a microgreen vertical nursery and PARS for baby greens. Our direct customers wanted meal solutions and we’ve been able to deliver them that. We’ve been doing everything from seed to plate basically.”
Megan Burritt, Managing partner
New projects coming up
On the same campus, 10 meters away, a new farm will be constructed, under the company's office space. In this farm herbs and edible flowers will be grown in response to different customers' demands. Megan says that Planted Detroit’s wholesale customers got them to this point as they were very interested in herbs and edible flowers. “However we weren’t able to perfect these as well in the systems that our baby greens were in perfectly. That’s why we’ve been leaning into R&D lately because once finishing the construction of Farm 2 it will have excellent growing conditions that are better than they have been for those crops.”
Edible flowers are an interesting thing, says Megan, but the company has gotten so much interest in it. According to Megan there aren’t many farms in the US that are growing them. “They’re high priced at this point. It sort of sticks to our original innovation, namely what exists here in the food system and what does not. Where can we fill the ‘does not exist niche’ and satisfy the needs of our customers.”
The company is rolling out a subscription program sometime this year and figuring out where it fits into the fresh food subscription system and how they can partner with other parties in order to get produce closer to society. “It’s great to have this ag job, applied science to be able to do. In all the things we’ve been doing is hiring these Detroiters and showing that we can really create a really great culture of work. It’s really great to see we’re contributing to a better Detroit and a better tomorrow,” Megan states.
Team expansion
During 2020 most of the team stayed on by moving around working hours, so the farm could come back in full force. By the time all equipment was in place, 10 to 12 people were added to the team to have them fully trained before the system would be functioning. “It has been really wonderful to expand the team to see what our capacity is,” says Megan.
“Luckily we’ve been able to develop systems that have been resilient. We’ve seen so many different patterns in consumer behavior but they seem to have fallen in our favor. People are eating more at home, shopping for groceries more, and that triggered our pivot focusing on direct consumers. But now, it’s perfectly in line with our strategy on how we go to market. As long as we can supply our customer needs we’ll be on the right path. Nothing but bright hopes for the future right now,” Megan affirms.
For more information:
Planted Detroit
Megan Burritt, Managing partner
megan@planteddetroit.com
www.planteddetroit.com
Author: Rebekka Boekhout
© VerticalFarmDaily.com
A Fully Automated Three-Dimensional Vertical Farm Comes Into Operation
Eponic Agriculture Co. Ltd is a supplier of indoor farming equipment. Alice, the company's director, introduced the recently fully automated production system of a stereochemical vertical farm
Eponic Agriculture Co. Ltd is a supplier of indoor farming equipment. Alice, the company's director, introduced the recently fully automated production system of a stereochemical vertical farm.
"The current three-dimensional indoor farms on the market are based on semi-automated workflow, with some links requiring additional equipment configuration and no continuity in the whole planting system. In order to solve this problem, we developed and designed a complete automated planting system, including the processes from sowing to planting, full-spectrum planting light control, fertilization, harvesting, and cleaning. Which are all done by automated equipment. Whereas all procedures can be controlled by intelligent software with real-time monitoring, data collection, and many other functions."
Benefits of an automated farm
When talking about the advantages of the automated equipment, Alice said, "Take our recently built 20-layer vertical farm as an example. First of all, the mechanical sowing time is 10 times-30 times faster than manual sowing. And on top of that, the use of automated equipment can realize precise planting and efficient communication of multi-layer planting surfaces. The 20-layer vegetable trays are automatically transferred to the ground for uniform watering, harvesting, and cleaning. This greatly improves productivity.
Secondly, the use of lift trucks is required when handling high-level crops. There are certain safety hazards in using lift trucks in a small space. While operating the automated equipment, only a tablet computer is needed to control the whole planting process, which is much safer and more convenient."
Although automated vertical farm systems have many advantages, their application in China is not yet popular. "In terms of production design, we have gone through countless experiments to design the most suitable software program. As well as hardware equipment for practical planting applications. Luckily after a long period of research, we finally chose the most cost-effective and suitable materials. The R&D investment is large and time-consuming.”
From a cost point of view, according to Alice, a fully automatic system is 2-3 times higher in costs than the semi-automatic system which is currently used more often. Most traditional agricultural companies find it difficult to accept such high initial costs. Thirdly, the automated system requires high technical requirements for farm managers. Managers need to have an understanding of both planting technology and software. Alice adds: “It is for these three reasons that the application of fully automated stereoscopic systems is not very common in China and other countries."
Automated planting
"Although the application is not yet widespread, I think fully automated stereoscopic planting is a trend. Urbanization has led to a reduction in arable land and soil pollution has triggered problems with pests and pesticide residues in fruits and vegetables, and the development of three-dimensional agriculture is the only way to maximize and optimize output in a limited area. Currently, stereoscopic planting plants still require a lot of manual labor to operate. As labor costs rise and planting techniques require more precision, the use of automated equipment will be a future trend," Alice notes.
"Automated systems are a trend, not only in China but also globally. Urbanization has been moving forward, in the face of soil pollution, pesticides and pests, etc. The planting area is gradually reduced and three-dimensional agriculture must be developed in order to quantify planting. Three-dimensional agriculture can be located near the city, and reduce the transport distance, people can eat the freshest vegetables, to achieve local supply. Therefore it is necessary to promote automated, intelligent planting systems in order to achieve efficient planting and sustainable development." Alice said.
Industry experience
Eponic Agriculture Co. Ltd's head office, Dahua Intelligent Electronics, has a twenty-five-year history division. The team has been focusing on the development and production of intelligent control systems and industrial lighting. Alice said that based on years of technical foundation, we developed full-spectrum LED planting lights which have been approved and applied by the USDA. Over the years, we have received technical support and affirmation from several agricultural doctors from Europe and the United States, focusing on the development and production of automated stereoscopic planting equipment.
According to Alice, the company has laboratories and showrooms in the US, Australia and Africa. This year, the company is planning on opening new showrooms and laboratories in Europe. “We are expanding our global reach and continue to optimize our growing systems to be a better supplier of fully automated growing equipment."
For more information:
Eponic Agriculture Co. Ltd
Alice Ou, Director
aliceou@eponicagriculture.com
www.eponicagriculture.com
Author: Rebekka Boekhout
© VerticalFarmDaily.com
Bringing The Future To life In Abu Dhabi
A cluster of shipping containers in a city centre is about the last place you’d expect to find salad growing. Yet for the past year, vertical farming startup Madar Farms has been using this site in Masdar City, Abu Dhabi, to grow leafy green vegetables using 95 per cent less water than traditional agriculture
Amid the deserts of Abu Dhabi, a new wave of entrepreneurs and innovators are sowing the seeds of a more sustainable future.
Image from: Wired
A cluster of shipping containers in a city centre is about the last place you’d expect to find salad growing. Yet for the past year, vertical farming startup Madar Farms has been using this site in Masdar City, Abu Dhabi, to grow leafy green vegetables using 95 per cent less water than traditional agriculture.
Madar Farms is one of a number of agtech startups benefitting from a package of incentives from the Abu Dhabi Investment Office (ADIO) aimed at spurring the development of innovative solutions for sustainable desert farming. The partnership is part of ADIO’s $545 million Innovation Programme dedicated to supporting companies in high-growth areas.
“Abu Dhabi is pressing ahead with our mission to ‘turn the desert green’,” explained H.E. Dr. Tariq Bin Hendi, Director General of ADIO, in November 2020. “We have created an environment where innovative ideas can flourish and the companies we partnered with earlier this year are already propelling the growth of Abu Dhabi’s 24,000 farms.”
The pandemic has made food supply a critical concern across the entire world, combined with the effects of population growth and climate change, which are stretching the capacity of less efficient traditional farming methods. Abu Dhabi’s pioneering efforts to drive agricultural innovation have been gathering pace and look set to produce cutting-edge solutions addressing food security challenges.
Beyond work supporting the application of novel agricultural technologies, Abu Dhabi is also investing in foundational research and development to tackle this growing problem.
In December, the emirate’s recently created Advanced Technology Research Council [ATRC], responsible for defining Abu Dhabi’s R&D strategy and establishing the emirate and the wider UAE as a desired home for advanced technology talent, announced a four-year competition with a $15 million prize for food security research. Launched through ATRC’s project management arm, ASPIRE, in partnership with the XPRIZE Foundation, the award will support the development of environmentally-friendly protein alternatives with the aim to "feed the next billion".
Image from: Madar Farms
Global Challenges, Local Solutions
Food security is far from the only global challenge on the emirate’s R&D menu. In November 2020, the ATRC announced the launch of the Technology Innovation Institute (TII), created to support applied research on the key priorities of quantum research, autonomous robotics, cryptography, advanced materials, digital security, directed energy and secure systems.
“The technologies under development at TII are not randomly selected,” explains the centre’s secretary general Faisal Al Bannai. “This research will complement fields that are of national importance. Quantum technologies and cryptography are crucial for protecting critical infrastructure, for example, while directed energy research has use-cases in healthcare. But beyond this, the technologies and research of TII will have global impact.”
Future research directions will be developed by the ATRC’s ASPIRE pillar, in collaboration with stakeholders from across a diverse range of industry sectors.
“ASPIRE defines the problem, sets milestones, and monitors the progress of the projects,” Al Bannai says. “It will also make impactful decisions related to the selection of research partners and the allocation of funding, to ensure that their R&D priorities align with Abu Dhabi and the UAE's broader development goals.”
Image from: Agritecture
Nurturing Next-Generation Talent
To address these challenges, ATRC’s first initiative is a talent development programme, NexTech, which has begun the recruitment of 125 local researchers, who will work across 31 projects in collaboration with 23 world-leading research centres.
Alongside universities and research institutes from across the US, the UK, Europe and South America, these partners include Abu Dhabi’s own Khalifa University, and Mohamed bin Zayed University of Artificial Intelligence, the world’s first graduate-level institute focused on artificial intelligence.
“Our aim is to up skill the researchers by allowing them to work across various disciplines in collaboration with world-renowned experts,” Al Bannai says.
Beyond academic collaborators, TII is also working with a number of industry partners, such as hyperloop technology company, Virgin Hyperloop. Such industry collaborations, Al Bannai points out, are essential to ensuring that TII research directly tackles relevant problems and has a smooth path to commercial impact in order to fuel job creation across the UAE.
“By engaging with top global talent, universities and research institutions and industry players, TII connects an intellectual community,” he says. “This reinforces Abu Dhabi and the UAE’s status as a global hub for innovation and contributes to the broader development of the knowledge-based economy.”
Ensuring Singapore's Food Security Despite the Odds
As with most issues that impact national security in Singapore, it often seems that the odds are stacked against us. Food security — access to safe and nutritious food — is a challenge on several fronts. Singapore is a small city-state with limited resources, with only 1 per cent of land available for food production, and over 90 per cent of food is imported from an increasingly disrupted world. The Covid-19 pandemic has further amplified the gravity of safeguarding food security
Image from: Reuters
As with most issues that impact national security in Singapore, it often seems that the odds are stacked against us. Food security — access to safe and nutritious food — is a challenge on several fronts.
Singapore is a small city-state with limited resources, with only 1 per cent of land available for food production, and over 90 per cent of food is imported from an increasingly disrupted world. The Covid-19 pandemic has further amplified the gravity of safeguarding food security. The city-state has been proactively planning for long-term food security through the Singapore Food Agency’s (SFA) strategy of “three food baskets” — diversifying food sources, growing locally and growing overseas. This approach has served the Republic well in securing a supply of safe food.
DIVERSIFIED SOURCING IS KEY
Singapore’s food importers leverage the nation’s connectivity and the global free trade environment to import from multiple sources in about 170 countries and regions worldwide. Should there be a disruption to any one source, importers are able to tap alternative food sources and ensure supply remains stable. Lockdown measures brought about by Covid-19 underscored Singapore’s vulnerabilities to supply disruptions in food.
It was not by luck that the Republic’s food supply remained stable and market shelves continued to be promptly restocked — it was the result of a deliberate whole-of-government strategy to diversify food sources. To keep the nation’’s diversified food supply lines intact amid the Covid-19 global pandemic, SFA worked closely with the Ministry of Trade and Industry and Enterprise Singapore (ESG) to monitor Singapore’s food supply situation. Together with the Ministry of Foreign Affairs, these economic agencies worked with like-minded countries to maintain open trade links.
LOCAL PRODUCTION AN IMPORTANT BUFFER
SFA drives innovation in local farms with the ambitious goal of producing 30 per cent of Singapore’s nutritional needs by 2030 as part of our “30 by 30” plan. To meet this goal, we need a holistic and long-term approach to space-planning, boosting agri-food technology and developing local agri-specialists. To facilitate and support the establishment of high-technology and productive farms in Singapore, SFA tenders out land based on qualitative criteria such as production capability, production track record, relevant experience and qualifications, innovation and sustainability.
In addition, a masterplan for the greater Lim Chu Kang (LCK) region, spanning about 390ha of land, will be undertaken in consultation with stakeholders over the next two to three years. The redeveloped LCK agri-food cluster will produce more than three times its current food production.
Building on the above efforts to grow Singapore’s high-tech agri-tech sector, SFA will continue to partner with the Economic Development Board and ESG to attract best-in-class global agri-tech companies, as well as to nurture promising homegrown agri-tech companies into local champions and help them to expand overseas.
EXPLORING ALTERNATIVE, UNDERUTILISED SPACES
Urban food solutions are expected to play a key role in global food security. While there are progressive enterprises operating out of farmlands and industrial estates, some agricultural game-changers are also taking root in unconventional areas — indoors, on rooftops and in underutilised spaces.
SFA worked with the Singapore Land Authority to introduce an urban farm at the former Henderson Secondary School site, which was transformed into Singapore’s first integrated space comprising an urban farm, childcare centre and nursing home within a state property. The farm space within the site was awarded in May 2019 to social enterprise City Sprouts, and it has become a vibrant destination for the young and old to learn about urban farming and enjoy a relaxing day out.
Citiponics, the first commercial farm located on a multi-storey car park in a residential neighbourhood, harvested its first yield of vegetables in April 2019. In September 2020, another nine sites atop multi-storey car parks were awarded for urban farming.
The successful bidders included proposals for hydroponic and vertical farming systems with a variety of innovative features, such as the Internet of Things (IoT), blockchain technology and automated climate control. These sites have the potential to collectively produce around 1,600 tonnes of vegetables annually.
Image from: Ciitiponics
TAPPING TECH
The Agriculture Productivity Fund (APF) supports local farms in their capability development and drive towards higher productivity. Through APF, SFA co-funds the adoption of farming systems to better control environmental variables, test-bed technologies and boost production capabilities. Between October 2014 and September 2020, a total of almost S$42 million has been committed to 115 farms.
The Covid-19 pandemic presented greater impetus to speed up local food production capacities. In September 2020, SFA awarded S$39.4 million to nine companies under the 30x30 Express Grant to quickly ramp up food-farm outputs over the next six months to two years. With advanced robotic and digital systems increasingly being used in farming, Singapore’s vegetables farmers have also become innovative agri-engineers and specialists in their own right.
With support from the 30x30 Express Grant, urban farming engineering solutions firm Indoor Farm Factory Innovation will set up an indoor vegetable farm with a vertical integration growth system up to 8m in height in a fully controlled and pesticide-free environment. The farm will leverage artificial intelligence farming systems integrated with IoT monitoring, dosing irrigation and an advanced environmental control system to achieve optimum growing conditions all year round.
Seng Choon, a chicken egg farm that has been in business for more than 30 years, has also proved itself a modernist in its operations. The company uses a computer that scans eggs to ascertain if they are clean; while feeding systems, temperature controls and waste cleaning systems have been automated with SFA’s support. Singapore’s efforts at ensuring food security would not be complete without support from consumers. To boost recognition of local produce among consumers, SFA brought the industry and public together to create a new “SG Fresh Produce” logo.
Farmers have been using this emblem on their packaging since August 2020. A website was also launched to provide a trove of information on locally farmed food. While the Covid-19 pandemic has led to import restrictions, it also helped to accelerate support for local produce. With public support for local farmers and other key measures, Singapore can beat the odds in ensuring food security in this ever-evolving, ever-disrupted world.
Farming Fish in the Sky
Sometime soon, Apollo Aquaculture Group will have one of the world’s largest vertical fish farms up and running in Singapore. Though construction has been delayed by COVID-19, the farm, once complete, will scale eight stories. Crucially, says the company, it won’t only be the farm’s height that sets it apart from the competition
Image from: Hakai Magazine
Sometime soon, Apollo Aquaculture Group will have one of the world’s largest vertical fish farms up and running in Singapore. Though construction has been delayed by COVID-19, the farm, once complete, will scale eight stories. Crucially, says the company, it won’t only be the farm’s height that sets it apart from the competition.
The high-tech facility will produce up to 3,000 tonnes of hybridized grouper, coral trout, and shrimp each year—with an efficiency, measured in fish per tonne of water, that is six times higher than established aquaculture operations in the Southeast Asian city-state, says spokesperson Crono Lee.
In doing so, the company hopes to become a major contributor to an ambitious plan to boost the food security of the small island city-state, which currently imports 90 percent of its food.
According to Ethan Chong Yih Tng, an engineer at the Singapore Institute of Technology who is not involved with the company, this stacking of fish farms is one of the key initiatives that geographically small Singapore is looking at to achieve its ambitious “30 by 30” target for food security—to produce 30 percent of its nutritional needs locally by 2030.
Founded in 1969, Apollo isn’t a new arrival to aquaculture in Singapore. Since the 1970s, it has been breeding ornamental fish across its 300-odd farms in the region. But when Eric Ng took over the family business in 2009, he was quick to diversify into producing marine fish as food, borrowing methods from operations in Germany, Japan, and Israel, says Lee. The outcome was a three-story farm in Lim Chu Kang, a rare green spot on the outskirts of Singapore. That aquaculture facility has been in operation for nearly a decade.
Each level of the Lim Chu Kang operation has two 135-square-meter tanks supplied with seawater by a system that filters, purifies, monitors, and recirculates water through the farm. As a result, only around five percent of the water needs to be replaced when contaminated by effluent from the fish—though Lee says the goal at both the new and existing facilities is to reduce that to zero using aquatic plants that clean and treat water naturally. That’s in contrast to significant levels of waste at Singapore’s traditional onshore pond farms, where farmers routinely clean out and replace entire tanks.
Image from: Apollo Aquaculture Group
In nearly 10 years of operating the Lim Chu Kang farm, which produces up to 200 tonnes of fish per year, the company has built up meticulous data sets on how to increase yields, says Lee—data they will apply to the new, larger facility.
“We understand the amount of water required, the condition of the water, and the amount of feed—measured down to a single gram per cubic meter of water. As a result, we’re able to produce fish in a much shorter time frame, at the right size for the market,” says Lee.
The decision to build this system up, rather than out, is a response to the lack of space in the Asian city-state. “We’re a very small country, and it’s very difficult to secure land,” says Lee. “So rather than building sideways, and expanding horizontally, why not expand vertically?”
Ever larger onshore fish farms is not the only approach the city-state is using to reach its 30 by 30 goal, however. In late 2019, for example, an offshore fish farm opened about five kilometers off Singapore’s Changi Point Ferry Terminal. Using a closed-containment system, it produces around 166 tonnes of barramundi, red snapper, and grouper each year across four tanks. The system “effectively isolates the fishes from the seawater when the quality of the surrounding water turns poor,” says Yih Tng. The self-contained system offers the control of Apollo’s vertical farm without the initial outlay on expensive land, or the high power costs.
Though Lee insists Apollo’s new eight-story farm will be economically competitive with traditional fish farms, high operating costs remain one of the primary reasons that commercial vertical closed loop fish farms remain limited globally.
In the United States, the majority of farms represented by the Recirculating Farms Coalition are outdoors, and much smaller than the Singapore operation, says founder and executive director Marianne Cufone. “That means we’re not as dependent on artificial inputs, such as temperature controls,” she explains.
“A lot of the larger systems sacrifice some of the natural benefits of [recirculating] systems in that they use a lot of energy for cooling, for heating, and for the circulating pumps. That’s not to say these outweigh the benefits, but a smaller, well-designed system can be extremely eco-efficient versus some of the larger-scale ones.”
The increased operational costs of a large facility translate to the price of the product: a 150-gram pack of Apollo’s ready-to-cook hybridised grouper fillet will set a customer back around US $12—roughly double the price of a frozen red grouper on sale at Singapore’s biggest grocer, Fair Price.
However, Cufone adds, large enclosed fish farms are becoming more prevalent in North America and the rest of the world. Few places is that growth more urgent than in Singapore—a fact only exacerbated by the spread of COVID-19.
“COVID-19 has exploded the awareness of [food insecurity] exponentially to local Singaporeans, and right now there’s a big shift in thinking toward local production,” says Lee. A shift that Apollo plans to take full advantage of.
Is AppHarvest the Future of Farming?
In this video from Motley Fool Live, recorded on Jan. 28, Industry Focus host Nick Sciple and Motley Fool contributor Lou Whiteman discuss AppHarvest, one such SPAC that is looking to disrupt the agriculture industry. Here are the details on what AppHarvest wants to do, and a look at whether the company represents the future of farming.
Special purpose acquisition companies, or SPACs, are red-hot right now, with investors clamoring to get into promising young companies.
In this video from Motley Fool Live, recorded on Jan. 28, Industry Focus host Nick Sciple and Motley Fool contributor Lou Whiteman discuss AppHarvest, one such SPAC that is looking to disrupt the agriculture industry. Here are the details on what AppHarvest wants to do, and a look at whether the company represents the future of farming.
Nick Sciple: One last company I wanted to talk about, Lou, and this is one I think it's -- you pay attention to, but not one I'm super excited to run in and buy. It was a company called AppHarvest. It's coming public via a [SPAC] this year. This vertical farming space. We talked about Gladstone Land buying traditional farmland. AppHarvest is taking a very different approach, trying to lean into some of the ESG-type movements.
Lou Whiteman: Yeah. Let's look at this. It probably wouldn't surprise you that the U.S. is the biggest global farm exporter as we said, but it might surprise you that the Netherlands, the tiny little country, is No. 2. The way they do that is tech: Greenhouse farm structure. AppHarvest has taken that model and brought it to the U.S. They have, I believe, three farms in Appalachia. The pitches can produce 30x the yields using 90% less water. Right now, it's mostly tomatoes and it is early-stage. I don't own this stock either. I love this idea. There's some reasons that I'm not buying in right now that we can get into. But this is fascinating to me. We talked about making the world a better place. This is the company that we need to be successful to make the world a better place. The warning on it is that it is a SPAC. So it's not public yet. Right now, I believe N-O-V-S. That deal should close soon. [Editor's note: The deal has since closed.] I'm not the only one excited about it. I tend not to like to buy IPOs and new companies anyway. I think the caution around buying into the excitement applies here. There is a Martha Stewart video on their website talking up the company, which I love Martha Stewart, but that's a hype level that makes me want to just watch and see what they produce. This is just three little farms in Appalachia right now and a great idea. This was all over my watchlist. I would imagine I would love to hold it at some point, but just be careful because this is, as we saw SPACs last year in other areas, people are very excited about this.
Sciple: Yeah. I think, like we've said, for a lot of these companies, the prospects are great. I think when you look at the reduced water usage, better, environmentally friendly, all those sorts of things. I like that they are in Appalachia. As someone who is from the South, I like it when more rural areas get some people actually investing money there. But again, there's a lot of execution between now and really getting to a place where this is the future of farming and they're going to reach scale and all those sorts of things. But this is a company I'm definitely going to have my radar on and pay attention to as they continue to report earnings. Because you can tell yourself a story about how this type of vertical farming, indoor farming disrupts this traditional model, can be more efficient, cleaner, etc. Something to continue paying attention to as we have more information, because this company, like you said, Lou, isn't all the way public yet. We still got to have this SPAC deal finalized and then we get all our fun SEC filings and quarterly calls and all those sorts of things. Once we have that, I will be very much looking forward to seeing what the company has to say.
Whiteman: Right. Just to finish up along too, the interesting thing here is that it is a proven concept because it has worked elsewhere. The downside of that is that it needed to work there. Netherlands just doesn't have -- and this is an expensive proposition to get started, to get going. There's potential there, but in a country blessed with almost seemingly unlimited farmland for now, for long term it makes sense. But in the short term, it could be a hard thing to really get up and running. I think you're right, just one to watch.
This Startup Wants Vertical Farmers To Hire A Robot Gardener
“By automating the production with robotics and remote monitoring, we can lower labor costs and offer solutions for food producers that are economically viable and environmentally sustainable,” the company claims on their website.
Arugula micro greens are grown at AeroFarms on February 19, 2019, in Newark, New Jersey.
Photo: Photo by Angela Weiss (Getty Images)
In recent years, vertical farming has emerged as a futurist’s solution to the world’s agricultural problems. The growing trend seeks to use controlled environments to boost food production, leveraging indoor labs where temperature, light, and nutrients can be mechanically controlled.
Yet while vertical farms have gained in popularity, they are also still very expensive. When compared to conventional farming, these farms necessitate the purchase of pricey equipment to aid human labor—a fact that, when paired with other economic pressures, has apparently led to an industry “littered with bankruptcies.”
One company hopes to change this dire picture. Enter Watney the robot.
Watney was designed by start-up Seasony. The company, which was featured today at this year’s Alchemist Accelerator’s Demo Day, has sought to make the tech-farming trend more accessible by automating away some of the more difficult labor involved.
Image: Screenshot: Youtube/TV2LORRY
“By automating the production with robotics and remote monitoring, we can lower labor costs and offer solutions for food producers that is economically viable and environmentally sustainable,” the company claims on their website.
Indeed, Watney is designed to augment (and, in many ways, replace) a human labor force—currently one of the biggest expenditures for vertical farms. Essentially an intelligent, automated cart, the robot was designed to “move and transport plant trays” within a farming hub. In techno-jargon, it is an autonomous mobile manipulation robot (AMMR), a type of machine known for moving and manipulating items on its own. It is also equipped with a camera that captures image data and sends it back to farm management software for human analysis. Watney also gathers valuable horticultural data to help farmers optimize yields, said Christopher Weis Thomasen, Seasony’s CEO and Co-Founder, in an email.
From left to right: Erkan Tosti Taskiran, Servet Coskun and Christopher Weis Thomasen.
Photo: Photo from Seasony.
“We are doing for vertical farming what the integration of autonomous mobile robots did to amazon. We are able to decrease the costs of growing food in a vertical farm by alleviating the logistics pains of working from scissor lifts,” said Thomasen.
Thomasen, a mechanical engineer, and his two co-founders electrical engineer Servet Coskun and business specialist Erkan Tosti Taskiran, were inspired to create the business while brainstorming what it would take to sustain life in outer space (Watney the robot is named after Mark Watney, the astronaut in the movie The Martian, who, after being stranded on the Red Planet, fertilizes potatoes with his own poop to survive).
“It quickly evolved to Seasony setting up a vertical farming lab and exploring the technical challenges facing the new industry. Reducing the costs related to labor is key in order to scale vertical farming and make agriculture more sustainable,” Thomasen said.
There is, of course, some debate in the farming community about the social costs incurred through the large-scale displacement of human labor.
Presumably, we will have to wait to see what that cost-saving process looks like. Seasony, which is still getting off the ground, plans to do a pilot trial with the largest vertical farm in Europe in April. It has plans to conduct further testing with several smaller vertical farms, as well, Thomasen said.
Lucas Ropek
Staff writer at Gizmodo
Plants Talk: Creating The Perfect Environment For Growth
There’s more to growing the greatest greens on the planet than just using less water.
Nate Klingler
It is well known that plants grow best when the weather is just right. Traditional farming methods have developed ways to combat mother nature by using an abundance of water, pesticides, herbicides, and chemical fertilizers. Crops are also transported, typically from California to Arizona, in the Fall and Winter months due to the changes in climate at that time of year. While these methods can help us adapt and grow crops in less than ideal conditions, they present potential problems, from resource consumption to introducing bacteria and disease into the crop. At Living Greens Farm, we have developed the perfect environment for our plants.
Hi, I’m Michelle Keller, Head Grower at Living Greens Farm. If you’ve been following along, you’ve seen how our non-GMO seeds grow into seedlings and eventually move from the nursery into our grow rooms. We recently showed you how we use 95% less water with our trolly mist system. But there’s more to growing the greatest greens on the planet than just using less water. Things like temperature, light, and air affect the plant’s growth.
Temperature is an easy element to control when you grow indoors. As the world’s largest indoor aeroponic farm, we have the responsibility to ensure that our grow rooms are highly regulated. That is why we continually monitor the temperature, not just for the health of our plants, but to make sure our energy consumption is at a responsible level.
Creating the Perfect Taste
We grow indoors to regulate the perfect amount of light given to the plants at just the right time. Our technology utilizes low energy LED lights that simulate sunlight and allow the plants to perform photosynthesis without being overwhelmed. This is one of the reasons our plants are known for their color and flavor. We’ve harnessed the energy of the sun and we give it to our plants right when they need the energy.
And we wouldn’t be an aeroponic farm without harnessing the power of the air. Our plants are grown in vertical grow racks and are challenged with the force of air which makes them stronger. When people eat Living Greens Farm salads for the first time, we are often asked how our greens are so crisp. Well, it’s because we grow our plants to be the strongest they can be.
Bringing Mother Nature Indoors
Controlling mother nature will always be a losing battle for traditional farmers. As the next generation of farming, we’ve brought mother nature indoors and can control the elements to grow the tastiest, healthiest greens on the planet.
Signify’s Expanded GrowWise Control System Helps Growers Boost Operational Efficiencies
Signify has expanded its GrowWise Control System, allowing for higher levels of automation and reducing manual labor and operational costs
Signify has expanded its GrowWise Control System, allowing for higher levels of automation and reducing manual labor and operational costs. This can be achieved by automating the lighting planning for their crop’s full growth cycle, up to one year ahead. The software tool brings dynamic lighting to greenhouses and vertical farms and fits seamlessly with modern climate computers and greenhouse management systems. This enables growers to automatically adjust light levels to maintain consistent levels on cloudy days, save energy on sunny days and simulate sunrise and sunset throughout the day or season.
Growers, like the Italian vertical farm, Planet Farms, and the Belgium greenhouse, De Glastuin, are already using the expanded system providing additional value within their growing facility.
“Using the GrowWise Control System is ideal for us,” says Luca Travaglini, co-founder of Planet Farms. “We want to automate as many aspects of our operations as possible to become more cost efficient. Now we can easily create custom light recipes and set them to run year-round to provide the right light recipe with the right light intensity at the right time throughout the crop’s growth cycle. By automating our full light strategy during the growth cycle, for the whole year, we can run our operations very efficiently and keep our manual labor costs low. That makes it easier for us to maintain consistent quality as we scale up our production.”
The demand for the GrowWise Control System is increasing for greenhouse applications as well. “The lighting can be used much more efficient, since it gives us the flexibility to reduce light levels at any moment we need to,” says Wouter de Bruyn, owner at De Glastuin. Lettuce grower De Glastuin is using the GrowWise Control System to control the Philips GreenPower LED toplighting compact grow lights via its climate control system. “The climate computer is equipped with a daylight sensor that sends actual light measurements to the GrowWise Control System so we can adapt our light levels automatically to ensure an even light level throughout the day and season. This results in a continuous high-quality crop. In case the electricity is the limiting factor, we are still able to use the LEDs evenly for the whole greenhouse in a lesser intensity.”
“Dynamic lighting in a greenhouse is the next step in improving the cost-efficiency and quality for the cultivation process,” says Udo van Slooten, Business leader Horticulture LED solutions at Signify. “It allows growers to effortlessly maintain a consistent level of light throughout the day to produce the best possible crops. The system compensates for cloudy weather and creates a more controlled growing environment for your crop.”
For more information about the GrowWise Control System and our Philips-banded horticulture lighting, visit our horticulture pages.
Or please contact:
Global Marcom Manager Horticulture at Signify
Daniela Damoiseaux
Tel: +31 6 31 65 29 69
E-mail: daniela.damoiseaux@signify.com
About Signify
Signify (Euronext: LIGHT) is the world leader in lighting for professionals and consumers and lighting for the Internet of Things. Our Philips products, Interact connected lighting systems and data-enabled services, deliver business value and transform life in homes, buildings and public spaces. With 2019 sales of EUR 6.2 billion, we have approximately 37,000 employees and are present in over 70 countries. We unlock the extraordinary potential of light for brighter lives and a better world. We achieved carbon neutrality in 2020, have been in the Dow Jones Sustainability World Index since our IPO for four consecutive years and were named Industry Leader in 2017, 2018 and 2019. News from Signify is located at the Newsroom, Twitter, LinkedIn and Instagram. Information for investors can be found on the Investor Relations page.
VIDEO: Common Mistakes When Setting Up Hydroponics
Even if you have a lot of guidance in setting up your grow space, you may make mistakes in the initial development stages
January 4, 2021 | By Joy King
Starting a hydroponics garden is thrilling. It's an exciting project where you can enjoy the progress your plants make over time. However, producing perfect plants requires some skill and attention to detail that take time to develop. Even if you have a lot of guidance in setting up your grow space, you may make mistakes in the initial development stages.
What is hydroponics?
Wikipedia describes hydroponics as "a type of horticulture as a method of growing plants, usually crops, without soil. It's become popular in vertical and indoor farming. Let's examine some common errors to avoid when setting up a hydroponics grow:
Ignoring plants
New growers may not devote the amount of time necessary to grow hydroponically. Some mistakenly believe that they can check in on plants on the weekend. But, a lot can go wrong if you're not regularly checking on them. Even if your system is fully automated through a grow controller, it's essential to check on your plants daily to ensure that everything is going smoothly.
Check that your automation system isn't clogged or failed in some other way. Once you are a more experienced grower, it will become easier for you to identify failures in your systems and problems with your plants since you're dedicating time to their wellbeing.
Going overboard
More is not always better, particularly in regards to plant growth. Often, problems arise in the grow room from a lack of experience in tending to plants grown hydroponically. It usually takes time to understand how to irrigate and fertilize plants properly. Overwatering is often detrimental to plants, and beginners often do not realize they are overwatering before it is too late. Excessive nutrients, or nutrient burn as it's referred to, is also a common problem for beginners.
Overcrowding plants
It is common for beginners to overestimate how many plants will fit in their grow space. When you first plant them, it may seem that your plants have a lot of room, but once they grow up, they will need that extra space to maintain growth. Be vigilant about removing excess plants and pruning if overcrowding seems like it will be a problem. When in doubt, err on the side of caution and plant fewer plants.
Sudden changes to the environment
You need to give your plants time to adjust when you make changes. One of the most common problems that beginners face is when they suddenly change the grow room's light levels or room temperature. Any sudden increase in light may cause leaf bleaching and burning. It's better that you make changes gradually, giving your plants time to adjust.
Final thoughts
There are many scholarly books on starting hydroponics grow room or space. Do your research and enjoy your hydroponic garden! It's a rewarding way to grow food, cannabis, or flowers.
Source: Growlink
Tags: Hydroponics, Nutrient Dosing System, Wireless Automation, Automated Grow System, Customer Service, Automated Grow Systems, Nutrient Delivery System, nutrients, automation