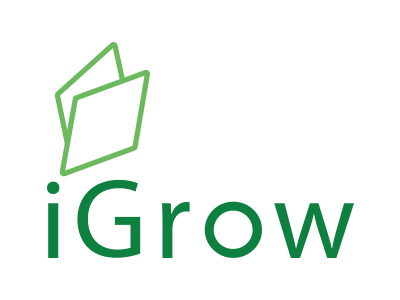
Welcome to iGrow News, Your Source for the World of Indoor Vertical Farming
Vertical Farming and the Future of Automation in Agriculture
Vertical farming is by no means a new idea. However, recent supply chain disruptions coupled with the falling price of produce, is opening new doors for a farming method previously deemed unviable by many.
August 10, 2021
Vertical farming is by no means a new idea. However, recent supply chain disruptions coupled with the falling price of produce, is opening new doors for a farming method previously deemed unviable by many. Here, John Young, APAC country manager at automation parts supplier EU Automation, highlights the renewed interest in vertical farming among a new generation of farmers, and explores the advantages it offers in tackling some of the biggest challenges facing the sector.
Turn the clock back approximately 1000 years, and less than four per cent of the world's habitable land was used for farming — that is the equivalent of four million square kilometres. Today, farmland takes up more than half of the world's habitable land, which equates to a landmass larger than South America.
Our World in Data reports the alarming facts associated with industrialized livestock farming, involving climate change, extinction of species, widespread destruction of habitat, and 80 per cent of cropland grown to feed livestock. With the population of the Asia Pacific region expected to reach 5 billion by 2050, the responsibility to supply food to an ever-growing population is becoming difficult.
A new generation of farmers are rising to the sustainability challenge. This agricultural revolution presents the transition from traditional farming to futuristic high-tech artificial intelligence (AI) and robotics. Whether it's weed-killing robots, harvesting and picking robots, or autonomous tractors, the farming landscape is evolving. In this age of robotic farming, producers believe incorporating automation and data will enable farmers to produce more, while damaging the environment less.
One major process change that is currently on the rise is the shift to vertical farming. Currently, 16.55 million square feet (sq ft) of indoor farms operate across the globe. However, the State of Indoor Farming report suggests this figure will increase to 22 million sq ft by 2022. The demand is high, and the AI journey is only getting started.
Why are farmers suddenly interested in vertical farming?
Vertical farming is the practice of producing food in vertically stacked layers. The climate-controlled indoor farms contain rows of plants situated next to each other, growing vertically, and hanging from the ceiling. Robotics help manoeuvre the products around, and AI can monitor the different parameters that are required for the crops to grow, such as the levels of water, temperature, and light.
Indoor agriculture is at an exciting point in its development. Key technologies used in farming systems today range from perception technologies which use cameras and sensors to detect and monitor various factors of the lifecycle. AI processes the data from sensors and provides solutions, while automated and autonomous mechatronics that use robotics and automated machines collect products when ready to dispatch to the market and recover the crops from ailments during the growing cycle.
Right now, the focus is to take vertical farming to the next level by developing smart robots which can increase precision and productivity, while minimizing environmental impact and risk. Agriculture, one of humankind’s oldest inventions, is merging with the latest technology, and farmers will soon be looking to pair with a reliable automation parts supplier to make the step up to vertical farming.
Vertical farming offers a unique set of advantages. Farmers understand there are many urgent and practical reasons to grow upwards rather than outwards. This farming method has huge potential for sustainability and food security, while protecting the environment, economy, and ecosystems.
In addition, the inclusion of AI and robotics ensures high-quality growth of products all year round, while preserving water, nutrients, and land consumption by 95 per cent. The controlled process of indoor farming with the help of AI and robotics also protects crops against pest invasions, and ensures they are well insulated — this is an aspect field farming cannot guarantee since it requires amenable weather conditions and labour.
Vertical farms can operate anywhere with no geographical constraints and are not subject to the limitations presented in outdoor farming, such as extreme conditions. This not only protects the crops, but also provides a safer working environment for labourers. What’s more, labour costs can be significantly reduced due to the automated indoor growing systems; thus, there is no longer a need for manual labour all year long.
In addition, energy consumption can be drastically reduced in vertical farming by implementing LED lighting to mimic the sun as a light source. A minor change like this can limit heat waste while increasing energy efficiency and cutting energy costs. Not only can LED lighting be used as an alternative, but renewable energy generated from wind turbines can be paired with vertical farming to ensure 100 per cent of its energy is produced from renewable sources. It is a win-win situation.
How will it boost the economy?
This sector is expecting a huge boom in investment and interest and manufacturers, suppliers and retailers are therefore preparing for this shift through early adoption. In the past, vertical farming was viewed as theoretical, but now the vertical farming market in the APAC region is expected to grow at a compound annual growth rate (CAGR) of 29 percent, rising from its current value of $0.78 billion to $2.77 billion by 2026. This is largely due to the advancement in technology such as sensors and smart energy systems that have improved the efficiency of growing products.
Although vertical farms will not replace traditional ways of farming, they hold great potential to revamp the future of agriculture in the APAC region by pushing towards a sustainable, environmentally conscious, tech savvy, economically rational, and health-sensitive world.
Source and Photo Courtesy of Agritech Tomorrow
Large-Scale Automated Vertical Farm Near Tokyo by Spread And ENEOS Partnership
Techno Farm Narita is Spread’s first partnership project and the first to be located in Eastern Japan
July 14, 2021, Spread Co., Ltd. (HQ: Kyoto, Japan; CEO: Shinji Inada, hereinafter “Spread”)’s partner, and a member of ENEOS Group, J Leaf Corporation (HQ: Chiba, Japan; President: Jun Uehara, hereinafter “J Leaf”) started operating the automated vertical farm “Techno Farm Narita” (Chiba, Japan) on 30th of June.
Spread’s Large-Scale Vertical Farming Partnership with ENEOS Group’s J Leaf Starts Operations near Tokyo
Spread owns and operates two vertical farms in Western Japan (Kyoto), the Kameoka Plant and Techno Farm Keihanna. Techno Farm Narita is Spread’s first partnership project, and the first to be located in Eastern Japan. The most significant feature of Techno Farm Narita is the increased efficiency in the use of land. This has been achieved by increasing the number of cultivation racks levels to 28, double that of Techno Farm Keihanna. Techno Farm Narita will produce 30,000 heads of lettuce daily, building on the know-how accumulated through the operation of Techno Farm Keihanna to deliver increasingly sustainable food production.
Unique Features of Techno Farm Narita
Even more efficient land saving through 28-level cultivation rack system (roughly 2 times more efficient than Techno Farm Keihanna)
Located in the Greater Tokyo Area, allowing for local production and consumption
Transforming idle land to efficient and sustainable agriculture ・
The utilization of renewable energy generated from solar panels
Techno Farm Narita also retains other features of Spread’s next-generation food production system, Techno Farm™, including pesticide-free, stable cultivation, integrated automation, specialized LED lighting, and Spread’s proprietary IoT-based cultivation management system, Techno Farm Cloud.
Techno Farm Narita’s Cultivation Room Opening Ceremony
About the Partners
ENEOS Group is one of Japan's leading corporate groups, with revenue in excess of 10 trillion yen. *1
The Group has the largest market share in oil refinery and petrochemicals distribution in Japan and is centered around ENEOS Holdings.
Spread’s vision is to create a sustainable society where future generations can live with peace of mind. On the way to this objective, Spread plans to reach a total production capacity of 100 tons per day domestically by 2030, through the expansion of its Techno Farm™. With the collaboration at Techno Farm Narita as a foundation, both parties are considering further partnership projects. The green business market is expected to continue growing, and Spread strives to become a leading vertical farming company globally.
Spread will continue to pursue further business opportunities through technological innovation both in Japan and overseas. Spread aims to provide solutions for the global problems of climate change and food security and the delivery of a truly sustainable society.
*1 FY2019 results (announced on May 20, 2020)
*2 ENEOS Techno Materials Corporation is a member of ENEOS Group
VIDEO: Ohio Company Redefines Farming By Going Indoors
Farm Manager Noah Zelkind was working on Wall Street before making the switch to 80 Acres, which houses 20 different growing rooms
The Hamilton company 80 Acres Farm will now have produce in Kroger stores across the state.
BY OLIVIA WILE
June 24, 2021
CINCINNATI — The future of farming is right here in Ohio, and it’s happening indoors.
What You Need To Know
The company 80 Acres Farms has the ability to control and change the environment of each of the rooms where produce is growing
The farm doesn't see itself as competition with other conventional farms, but instead aims to help feed a growing population
Its produce is now being sold in Kroger locations in Ohio
The company 80 Acres Farms in Hamilton, 20 miles north of Cincinnati, is one of just a handful of “vertical farms” in the world. Farm Manager Noah Zelkind was working on Wall Street before making the switch to 80 Acres, which houses 20 different growing rooms.
“We have 10 levels stacked on top of each other, 10 rows long, and 10 tables inside of each row,” said Zelkind.
The company is able to control and change the environment of each of the rooms where produce is growing. It’s technology that’s years in the making.
“We went through and tried to study nature and replicate everything that’s important about it and really make sure we’re giving the plant exactly what it needs but in the most efficient way possible.”
It's a method Zelkind said gives the company ultimate control.
"This really is the next generation of farming," he said. "We have a completely different level over the control of the entire process of growing than anything anyone has done before.”
“You're going to get the same healthy fresh lettuce whether you're in the middle of winter and it's snowing outside or you’re in the middle of the summer.”
But he said the company is not trying to compete with conventional farmers.
"We don’t see ourselves competing with farmers at all,” said Zelkind. “If you look, we’re supposed to have 10 billion people in the world in the next 20 to 30 years, and in order to feed the population, we’re going to need 70% more arable land.”
The farm's produce is now available in Kroger stores across the state.
Applying Automated Warehouse Systems To Indoor Farming
“At Swisslog, we don’t have standard solutions in place for vertical farms yet. But due to our long-lasting expertise both in the food industry and in the distribution of fresh products to the point of sale, we understand the supply chain processes and linked to that shelf life considerations.”
“History is written in circles as we observe similar drive for automation in indoor farming, as we saw years ago in the intralogistics sector. There are yet few important differences,” says Timo Landener, product innovator at Swisslog.
Swisslog, with the vision to shape the future of intralogistics, not only develops warehouse automation and software solutions to reduce costs and introduce flexibility to warehouse-based operations but also looks into innovative future-proof approaches. In March 2021, Swisslog announced its foray into the vertical farming market. While Swisslog has not specifically designed systems for vertical farming, its vast portfolio of automation solutions can be adapted to vertical farms, whether pre-existing or purpose-built.
Timo Landener
“At Swisslog, we don’t have standard solutions in place for vertical farms yet. But due to our long-lasting expertise both in the food industry and in the distribution of fresh products to the point of sale, we understand the supply chain processes and linked to that shelf life considerations. Moreover, our portfolio can be easily adapted to indoor farming since the payload is fairly light, the throughput is not critical and the automation operations demand low power compared to the needs of the intralogistics automation,” explains Timo. “Nevertheless, we already learned, that we can't just adopt the same requirements, because plants are living organisms. And we have to respect that.”
Although unable to reveal their clients, Swisslog has reportedly demonstrated its technologies in the vertical farming industry with success to allow growers to reduce operational costs and increase scalability. Examples of innovative systems applicable to vertical farming include the PowerStore high-density storage system, the AGV based good-to-person order fulfillment solution CarryPick, the Tornado mini-load crane and the Vectura stacker crane.
When does automation become economically feasible?
Automation can be applied to multiple processes in an indoor farm including seeding, harvesting, packaging, tray manipulation, etc. However, Timo explains that automation is capital-intensive and best suited for large-scale indoor farms. A higher production level introduces more opportunities to increase operational efficiency and reduce labor requirements.
“Even Amazon began in a small space with little automation. Then, they reached a level where automation made sense. In the vertical farming industry, we need to discuss with clients where the tipping point is for needing automation,” says Timo.
To determine which automation solutions are right for the grower, Swisslog’s automation experts work directly with clients to identify opportunities for increased operational efficiency and customize solutions according to the farm’s architecture. Additionally, the close relation with KUKA as the parental company allows collaboration opportunities to automate and incorporate the sub-processes in an Indoor Farm to a more turnkey solution.
Harvest-on-demand
Timo explains that despite the relatively short distance between urban indoor farms and retailers, a major challenge to indoor farming is the logistics of transporting farm-grown products to retailers while maintaining crop quality.
“After the plants have grown in a perfect environment, they are cut and immediately begin to lose quality. The current challenge is to speed up the process of getting the products to the retailer. Pursuing the innovative approach of harvesting-on-demand, we can make sure that the end customer receives fresh and rich nutrition vegetables. With a palette of automated solutions this is finally possible,” says Timo.
Swisslog’s ties with global retailers started long ago as the Swiss Company delivered solutions for huge automated projects (distribution centers) as well as smaller, more local applications, known as Micro-Fulfillment Centers. Harvesting-on-demand differs from mainstream distribution models by supplying retailers with living plants, which can continue growing until they are purchased.
This process can be carried out in retailers’ “back shops” and would support additionally retailers to fulfill three major sales channels: in-store sales, home delivery and BOPIS (buy online, pick up in-store). Swisslog is certain that we are at the edge of a revolution in food the supply chain: There will be the need for Indoor Farms at the point of sales: a “fresh food on the demand-supply grid”. We see automation as a means for leveraging the indoor farms and help them deliver efficiency that will lower the entry threshold for further investments.
Retailers are a fundamental part of this revolution. “Many indoor farms are currently selling to retailers. Due to the fact, that the retailers sell the crops, they determine how the supply chain will look like. Thus, the power of re-designing the process of the supply chain and ensuring consistency in the circular economy lies in their hands. As for today, the complexity and ramifications of the matter inspire us to join forces with retailers and find out how to react in the best way to changing needs of the customers and the industry. We are on the verge of something new and powerful. Swisslog, an intralogistics automation leader, together with retailers and farming experts, we can deliver a great added value for consumers” explains Timo.
For more information:
Timo Landener, product innovator
Swisslog
timo.landener@swisslog.com
www.swisslog.com
Publication date: Thu 3 Jun 2021
Author: Rebekka Boekhout
© VerticalFarmDaily.com
Pontus Files International Patent Application For Automated Vertical Farm Harvesting Robot
Pontus' initial crop, water lentils, is the fastest-growing leafed plant.* Pontus' CEVAS helps accelerate the growth of Pontus' water lentils, requiring the plant to be harvested every 24 hours
NEWS PROVIDED BY
Jun 09, 2021, VANCOUVER, BC, June 9, 2021 /CNW/ - Pontus Protein Ltd. (TSXV: HULK) (OTCQB: HLKKF) (FSE: 8YC) ("Pontus" or the "Company"), is pleased to announce that it has filed an international patent application through the Patent Coordination Treaty with the World Intellectual Property Organization for Pontus' proprietary Harvesting Automated Robotic Vehicle or "HARV" for short. HARV is a vertical farm rack system and automated plant tending and harvesting robot designed to work alongside and assist Pontus' Closed Environment Vertical Aquaponics System or CEVAS system.
Pontus' Harvesting Automated Robotic Vehicle or “HARV” for short. HARV is a vertical farm rack system and automated plant tending and harvesting robot (CNW Group/Pontus Protein Ltd.)
Pontus' initial crop, water lentils, is the fastest-growing leafed plant.* Pontus' CEVAS helps accelerate the growth of Pontus' water lentils, requiring the plant to be harvested every 24 hours. Pontus developed the HARV technology to allow the crop to be automatically harvested daily. In addition, due to its low profile, HARV will enable Pontus to stack nine levels of vertical farming at its Surrey, British Columbia production facility.
Steve McArthur, Chief Technology Officer, Pontus, stated, "Talking with the experienced team at Automation Experts (an automation and innovation company based in Calgary, Canada), we were able to identify that there was no robot out there that handled everything we needed it to do. By harvesting the crop in situ, using HARV, we will reduce the space between the water beds and increase the number of levels, increasing efficiency and the yield. We are beyond excited about pairing HARV with our CEVAS system, as we see CEVAS as a greener, more ecologically sustainable way of producing high nutrition food products."
Stephen Bruce Wong, CEO, Automation Experts, added, "HARV is more than a mechanical tool for harvesting. It will manage the farm and give us critical insight and data regarding the optimization of the growing environment. The robotics in HARV will allow Pontus to eliminate moving parts from the structure thus lowering the cost to build Pontus' vertical farms as the water beds can be dumb and do not need the technology built into them. It also uses machine learning and artificial intelligence to support all aspects of the growing process."
The patent filing is part of the technology leadership in the aquaponic space that Pontus continues to secure.
About Pontus Protein Ltd.
Pontus Protein Ltd. is a Vancouver, B.C. based technology company that grows water lentil protein for commercial use. Pontus is reinventing agriculture with their proprietary Closed Environment Vertical Aquaponic System (CEVAS) – the farming of the future. Pontus specializes in the indoor vertical farming of water lentils that use 95% less water than traditional agriculture and no pesticides or chemicals. Pontus is committed to solving the global food crisis by providing access to sustainable indoor biosecure pure plant-based proteins. Pontus' water lentils can be harvested every 24 hours, exceed organic certification, and can be grown in any climate in a relatively small area. Our water lentil protein is filled with antioxidants, minerals, vitamins, and all the amino acids, making a complete protein food source. Pontus aims to revolutionize the plant-based sector as the entire sector is currently based on two main protein sources: soy and pea. Water lentil protein is far superior to pea and soy protein. It contains over 40% protein vs. 5-36% protein*, and Pontus aims to be the base protein for nutrition-rich plant-based food products and nutraceuticals to support the movement transitioning the world from meat-based to plant-based proteins.
To learn more, please visit pontuswaterlentils.com.
*https://www.infood.net/visitor/collection/75?portion_size=100
*https://www.zmescience.com/science/fastest-growing-plant-02022021/
On behalf of the Board of Directors
"Connor Yuen"
Connor Yuen, CEO
Pontus Protein Ltd.
Contact Information
For more information, please contact:
Connor Yuen
Chief Executive Officer
https://pontuswaterlentils.com/company/#contact
Forward-Looking Information
Certain statements in this release are forward-looking statements, which reflect the expectations of management regarding the Company. Forward-looking statements consist of statements that are not purely historical, including any statements regarding beliefs, plans, expectations or intentions regarding the future, including but not limited to Pontus' ability to revolutionize the plant based sector. Such statements are subject to risks and uncertainties that may cause actual results, performance or developments to differ materially from those contained in the statements, including risks related to factors beyond the control of the Company. These risks include, but are not limited to, the following: the unknown magnitude and duration of the effects of the COVID-19 pandemic, the failure of Pontus to receive the necessary approvals from the Canadian Food Inspection Agency for its products and facilities, the inability to complete Pontus' Surrey-based production facility, as well as other general business, economic, or market related risks beyond the director control of the Company and which may affect the Company's business, operations, or products. No assurance can be given that any of the events anticipated by the forward-looking statements will occur or, if they do occur, what benefits the Company will obtain from them. The Company undertakes no obligation to update forward-looking information if circumstances or management's estimates or opinions should change, unless required by law. The reader is cautioned not to place undue reliance on forward-looking information.
Neither the TSX Venture Exchange nor its Regulation Services Provider (as that term is defined in policies of the TSX Venture Exchange) accepts responsibility for the adequacy or accuracy of this release.
SOURCE Pontus Protein Ltd.
For further information: Investor Relations or Media enquiries: invest@pontuswaterlentils.com, (403) 589-7992
Organization Profile
Pontus Protein Ltd.
'Automation Is Needed To Reduce Costs And Improve Efficiency'
“We believe that automation can play a decisive role in delivering fresh produce for the most diverse uses and make agriculture accessible to many," says Giuseppe
There is so much to win regarding safety and workforce availability that traditional farming won’t help us with,” says Prof. Dr. Giuseppe Pasciuti, Marketing Strategist and Board Member at ONO Exponential Farming. For this particular reason, automation is the key to agricultural acceleration.
“We believe that automation can play a decisive role in delivering fresh produce for the most diverse uses and make agriculture accessible to many," says Giuseppe. He continues, "automation can also limit low labor availability in the agricultural sector. It could even, as we have experienced during the pandemic, restrict the access of pathogens or viruses in food production. We at ONO/EF believe that automation is the key to match the new era for indoor farming ”
Full automation
ONO/EF Farms allows growers to remotely control all growing operations. Through automation, ONO/EF Farm is continuously generating new growing conditions for plants, in terms of climate conditions and the right mix of nutrients according to each crop type and its growth stage. Giuseppe says that automation allows them to reduce CapEx and operation costs dramatically.
ONO E/F's idea of vertical farming does not require Giga farms to make the investment sustainable. Giuseppe says that "the company isn't keen to build the largest farm in the world, but a distributed network of connected farms close to consumers. Because in this industry, collaboration is key.”
According to Giuseppe, the vertical farming industry needs profitability in combination with sustainability. “For that reason, we have developed ONO Exponential Farming. Our advanced technological platform, which is completely robotized, supported by AI and our algorithms,” he says.
ONO / EF provides 100% of the production infrastructure, from seeding to finished product packaging.“We are redefining the concept of farming by constantly update and improve our algorithms and AI. In this way, we can make farm operations more effective and efficient.
Experience
ONO/EF has been a technology provider in industrial automation for 20 years. The vertical farming industry is known for its rapid development in terms of techniques and automation.
“Our company is already witnessing the introduction of automated elements that we consider outdated. Functional automation is linked to complete processes that allow human intelligence to concentrate on value-added activities. Activities such as studying plant physiology and identifying cause-effect relationships in growth processes," Giuseppe says.
For more information:
Giuseppe Pasciuti, Marketing Strategist and Board Member
ONO Exponential Farming
giuseppe.pasciuti@onoef.com
https://onoexponentialfarming.com
26 May 2021
Author: Rebekka Boekhout
© VerticalFarmDaily.com
Blue Radix & Ecoation Join Forces With The World's 1st Autonomous Find & Fix Solution
May 19, 2021, Rotterdam, Netherlands and North Vancouver, Canada
Blue Radix, an independent Dutch AI-tech specialist for the international greenhouse industry, and Ecoation Innovative Solutions Inc. (ecoation), a Canadian developer of automated greenhouse management and crop health monitoring technologies, have signed an agreement.
The collaboration aims to identify new ways to automate decision-making and action in the greenhouse, using vision technology and algorithms. ecoation and Blue Radix are using the data collected by ecoation’s OKO and platform to enhance the impact of Blue Radix’ algorithms for autonomous growing. By combining data sets, algorithms, and analytical efforts the companies are able to create new insights and applications that help growers worldwide to improve their crop strategy, quality and yield.
Blue Radix and ecoation look forward to ongoing collaborative efforts where the duo explores the multitude of innovation opportunities that become available when you combine ecoation’s OKO and platform with Blue Radix’ Crop Controller. Collaborating across data and algorithms has the potential to create value across many avenues, including optimizing crop strategy, autonomous steering, IPM enhancement, and understanding spatial climate distribution.
The World’s 1st Autonomous Find & Fix Solution
The first project the duo is working on is enhanced autonomous growing with crop data visualization. ecoation’s OKO collects sensory data and information about climate, integrated pest management, and crop work at every row and post to an SqM granularity. These insights greatly contribute to a complete and accurate view on the state of the crop. The broad range of data points, including fruit count, fruit colouring, and stem density, will be combined with the smart steering algorithms of Blue Radix’ Crop Controller. Crop Controller will actively, continuously and autonomously control the greenhouse conditions with the grower’s crop strategy as its starting point and the optimal crop status as its goal. E.g. by optimizing the plant load, plant stress is reduced avoiding weak plants that are vulnerable to pests and diseases. In this way ecoation and Blue Radix find and fix imperfections before they impact yield or crop quality.
Support growers
“Collaborating with Blue Radix means pioneering the future of ag more effectively, at a pace that would be difficult to reach if we carried on separately,” shared ecoation CEO Dr. Saber Miresmailli. “Both teams are committed to the same goal: to support growers in making the best possible decisions. Working together means unlocking new ways to get the most from the data and providing better insights to our customers that inform their decisions.”
“Ecoation offers solutions which are important components in a fully autonomous greenhouse. Optimization and steering with algorithms depends on high quality data and a robust crop strategy. Vision technology and enhanced analytics from ecoation provides this data and the necessary input to improve the grower’s crop strategy even further,” emphasizes Blue Radix CEO Ronald Hoek. “We strive for open collaboration and partnerships. Growers should always be able to choose freely what they want to do with their data and benefit from the best combination of services & products for their greenhouse.”
The duo will only work with greenhouse data retrieved from the customers of ecoation and Blue Radix who provide full consent. Transparency and data security is paramount, and this collaboration will rely on growers who are looking to optimize their greenhouse operations with autonomous processes and are interested in contributing to the future of ag with their facility data and insights.
About Blue Radix
Blue Radix is an independent Dutch AI-tech specialist for the international greenhouse industry. Blue Radix creates solutions with artificial intelligence for daily decisions and actions in greenhouses. Greenhouses offer an efficient way to produce food and flowers in a sustainable manner. But the number of skilled people with expertise of growing crops in greenhouses is declining every year. This has a direct and negative impact on yield, costs, continuity, and product quality. Blue Radix offers solutions for these challenges: smart algorithms which optimize and steer climate, irrigation, and energy continuously and autonomously, supported by off-site
Autonomous Greenhouse Managers. Blue Radix offers growers a digital brain for their greenhouse. More information at blue-radix.com. Find Blue Radix on LinkedIn, Twitter, and Instagram.
About ecoation
ecoation is an award-winning grower-centric platform that combines Human knowledge and experience with Machine precision and automation to increase operational visibility, assist growers, and enhance their decisions. Commercially available since September 2019, ecoation products can be found in greenhouses across the United States, Canada, Mexico, and Europe. With an experienced team of 60+ growers, scientists, engineers, and business professionals from all over the globe, ecoation is passionate about enabling a cleaner future and supporting growers in making the best possible decisions. At ecoation, we are on a mission to empower growers because we believe in doing so, we win together.
More information at ecoation.com. Find ecoation on LinkedIn, Twitter, and Instagram.
For media inquiries, please contact:
Blue Radix
Marijke van Rongen
Manager Global Marketing & Communications
marijke.vanrongen@blue-radix.com
+31 6 53 43 38 39
ecoation
Marketing and Media Contact
Cameron Lust
The World’s First Autonomous Greenhouse Manager
Geert van der Wel started in the role of Autonomous Greenhouse Manager at Blue Radix. He represents the human support side of the Crop Controller service in addition to the smart algorithms that control greenhouses
07-04-2021 | Goedemorgen
Early February, Geert van der Wel started in the role of Autonomous Greenhouse Manager at Blue Radix. He represents the human support side of the Crop Controller service in addition to the smart algorithms that control greenhouses. Read more about how Geert helps customers and about his background. As he says himself: "I was almost literally born among tomatoes in De Lier, where my parents had a tomato greenhouse."
Name: Geert van der Wel
Home: I’ve been married to Tessa for 16 years and we have two children. We have lived in Burgundian West Brabant since 1998.
Childhood: Almost literally, I was born among the tomatoes in De Lier, where my parents had a tomato greenhouse.
Study: I completed Secondary Horticultural School in De Lier, and also undertook several (horticultural) studies.
Work experience: I worked in my parents’ tomato greenhouse right from my childhood. After finishing my studies my partner and I became owners of Kwekerij Polderwel for ten years, growing tomatoes on 2.5 hectares. We wound up this undertaking because of the construction of the A4 highway between Antwerp and Rotterdam. Then I did three years as a manager at the Nuijten plant nursery, and when this firm ceased trading I ended up at Nickerson-Zwaan in Made; it later became known as Hazera Seeds. For the first four years, I worked in the Planning & Control department, moving on to become Product Manager High-Tech Tomatoes for the final five years.
What can you do for growers as an Autonomous Greenhouse Manager?
“Blue Radix offers autonomous growing as a service. So alongside our smart algorithms controlling the greenhouse, our Crop Controller service also has a ‘human side’, and customers get daily support from an off-site Autonomous Greenhouse Manager (AGM). So as that AGM I’m constantly looking over the customer’s shoulder, and I’m their first point of contact. Right from the start, I guide clients intensively in taking their first steps into the world of algorithms. They are given an extensive onboarding program where they get explanations on the steps to autonomous growing, the operation of the algorithms, and the Crop Controller portal. I also monitor the management of the greenhouse continuously and discuss the progress on a regular basis, including through reports. My work experience has taken me through all the processes involved, from seed to the final product. This is what enables me to support our customers fully as AGM, to advise them, and to help them to realize their crop strategies.”
Blue Radix offers autonomous growing as a service; why is this important?
“Cultivation is the core business of every greenhouse company. To leave this completely to autonomous control requires a lot of trust from the customer. We are very aware that autonomous growing is still quite new and innovative. Providing good service with the support of the AGM lets us guide growers fully in working with algorithms. Our experience shows that customers are more likely to abandon their own processes and working methods step by step because there’s always someone monitoring the entire process.”
Describe your day. How do you monitor greenhouses worldwide?
“Every day I open the Crop Controller portal to see how the algorithms are behaving in terms of our various customers’ crop strategies. I contact the grower if any anomalies appear, or if there’s a technical issue I get in touch with the Blue Radix product developers. This also applies to feedback I receive from customers on how we can optimize Crop Controller still further.”
What do you like about your job? And what are your views on autonomous greenhouse management?
“In the horticultural world, it’s great to see that there’s a continuous search for innovations, and specifically for autonomous growing. I used sensors and digital tools on a small scale when I was a grower myself. But at that time I got very little guidance on how they worked and how to interpret it all. Now I use this experience to give our customers good information so that ultimately they’ll be able to grow autonomously in the best possible way!”
Got a question for Geert, or about autonomous growing generally?
Send us a message, and we’ll be happy to help you.
Vertical Farming Startup Oishii Raises $50m In Series A Funding
“We aim to be the largest strawberry producer in the world, and this capital allows us to bring the best-tasting, healthiest berry to everyone.”
By Sian Yates
03/11/2021
Oishii, a vertical farming startup based in New Jersey, has raised $50 million during a Series A funding round led by Sparx Group’s Mirai Creation Fund II.
The funds will enable Oishii to open vertical strawberry farms in new markets, expand its flagship farm outside of Manhattan, and accelerate its investment in R&D.
“Our mission is to change the way we grow food. We set out to deliver exceptionally delicious and sustainable produce,” said Oishii CEO Hiroki Koga. “We started with the strawberry – a fruit that routinely tops the dirty dozen of most pesticide-riddled crops – as it has long been considered the ‘holy grail’ of vertical farming.”
“We aim to be the largest strawberry producer in the world, and this capital allows us to bring the best-tasting, healthiest berry to everyone. From there, we’ll quickly expand into new fruits and produce,” he added.
Oishii is already known for its innovative farming techniques that have enabled the company to “perfect the strawberry,” while its proprietary and first-of-its-kind pollination method is conducted naturally with bees.
The company’s vertical farms feature zero pesticides and produce ripe fruit all year round, using less water and land than traditional agricultural methods.
“Oishii is the farm of the future,” said Sparx Group president and Group CEO Shuhei Abe. “The cultivation and pollination techniques the company has developed set them well apart from the industry, positioning Oishii to quickly revolutionise agriculture as we know it.”
The company has raised a total of $55 million since its founding in 2016.
Bringing The Future To life In Abu Dhabi
A cluster of shipping containers in a city centre is about the last place you’d expect to find salad growing. Yet for the past year, vertical farming startup Madar Farms has been using this site in Masdar City, Abu Dhabi, to grow leafy green vegetables using 95 per cent less water than traditional agriculture
Amid the deserts of Abu Dhabi, a new wave of entrepreneurs and innovators are sowing the seeds of a more sustainable future.
Image from: Wired
A cluster of shipping containers in a city centre is about the last place you’d expect to find salad growing. Yet for the past year, vertical farming startup Madar Farms has been using this site in Masdar City, Abu Dhabi, to grow leafy green vegetables using 95 per cent less water than traditional agriculture.
Madar Farms is one of a number of agtech startups benefitting from a package of incentives from the Abu Dhabi Investment Office (ADIO) aimed at spurring the development of innovative solutions for sustainable desert farming. The partnership is part of ADIO’s $545 million Innovation Programme dedicated to supporting companies in high-growth areas.
“Abu Dhabi is pressing ahead with our mission to ‘turn the desert green’,” explained H.E. Dr. Tariq Bin Hendi, Director General of ADIO, in November 2020. “We have created an environment where innovative ideas can flourish and the companies we partnered with earlier this year are already propelling the growth of Abu Dhabi’s 24,000 farms.”
The pandemic has made food supply a critical concern across the entire world, combined with the effects of population growth and climate change, which are stretching the capacity of less efficient traditional farming methods. Abu Dhabi’s pioneering efforts to drive agricultural innovation have been gathering pace and look set to produce cutting-edge solutions addressing food security challenges.
Beyond work supporting the application of novel agricultural technologies, Abu Dhabi is also investing in foundational research and development to tackle this growing problem.
In December, the emirate’s recently created Advanced Technology Research Council [ATRC], responsible for defining Abu Dhabi’s R&D strategy and establishing the emirate and the wider UAE as a desired home for advanced technology talent, announced a four-year competition with a $15 million prize for food security research. Launched through ATRC’s project management arm, ASPIRE, in partnership with the XPRIZE Foundation, the award will support the development of environmentally-friendly protein alternatives with the aim to "feed the next billion".
Image from: Madar Farms
Global Challenges, Local Solutions
Food security is far from the only global challenge on the emirate’s R&D menu. In November 2020, the ATRC announced the launch of the Technology Innovation Institute (TII), created to support applied research on the key priorities of quantum research, autonomous robotics, cryptography, advanced materials, digital security, directed energy and secure systems.
“The technologies under development at TII are not randomly selected,” explains the centre’s secretary general Faisal Al Bannai. “This research will complement fields that are of national importance. Quantum technologies and cryptography are crucial for protecting critical infrastructure, for example, while directed energy research has use-cases in healthcare. But beyond this, the technologies and research of TII will have global impact.”
Future research directions will be developed by the ATRC’s ASPIRE pillar, in collaboration with stakeholders from across a diverse range of industry sectors.
“ASPIRE defines the problem, sets milestones, and monitors the progress of the projects,” Al Bannai says. “It will also make impactful decisions related to the selection of research partners and the allocation of funding, to ensure that their R&D priorities align with Abu Dhabi and the UAE's broader development goals.”
Image from: Agritecture
Nurturing Next-Generation Talent
To address these challenges, ATRC’s first initiative is a talent development programme, NexTech, which has begun the recruitment of 125 local researchers, who will work across 31 projects in collaboration with 23 world-leading research centres.
Alongside universities and research institutes from across the US, the UK, Europe and South America, these partners include Abu Dhabi’s own Khalifa University, and Mohamed bin Zayed University of Artificial Intelligence, the world’s first graduate-level institute focused on artificial intelligence.
“Our aim is to up skill the researchers by allowing them to work across various disciplines in collaboration with world-renowned experts,” Al Bannai says.
Beyond academic collaborators, TII is also working with a number of industry partners, such as hyperloop technology company, Virgin Hyperloop. Such industry collaborations, Al Bannai points out, are essential to ensuring that TII research directly tackles relevant problems and has a smooth path to commercial impact in order to fuel job creation across the UAE.
“By engaging with top global talent, universities and research institutions and industry players, TII connects an intellectual community,” he says. “This reinforces Abu Dhabi and the UAE’s status as a global hub for innovation and contributes to the broader development of the knowledge-based economy.”
In Malahide, Two Friends Raise A Vertical Farm
When salesman Jack Hussey finishes his work day, he closes the laptop, leaves his home in Malahide and walks 10 minutes down the road. At the bottom of his friend’s farm sits an outhouse with a coldroom which now hosts his side business, Upfarm. A farm that goes upwards
Image from: Dublin Inquirer
When salesman Jack Hussey finishes his work day, he closes the laptop, leaves his home in Malahide and walks 10 minutes down the road. At the bottom of his friend’s farm sits an outhouse with a coldroom which now hosts his side business, Upfarm. A farm that goes upwards.
Imagine a shelf rack, says Hussey. “We’ve kitted the roofs of each shelf with an LED grow light. It’s to replicate the sunlight basically.”
A photo of the farm shows purple light beaming down on thick heads of lemongrass and basil, stacked on shelves. Yields from vertical farming are far more efficient than in-the-ground farming, Hussey said, on the phone last Friday.
He likens it to real estate. “You can have houses that are populated side by side or you can start going upwards with apartments.”
From Podcast to Table
Hussey always had an interest in food, he says. Last year he and a school friend, Bill Abbott, began to look into urban farming.
“But we were saying, is farming in the ground actually the best route to go?” Hussey says.
It’s labour intensive, which didn’t suit the two guys, who work other full-time jobs. Then, in March 2020, Hussey heard a podcast with American urban farmer Curtis Stone. He had an urban farm where he was using a spin-farming method, says Hussey. “It’s what they call it. You rotate crops out of the ground in a much more efficient way.”
“Essentially he was able to capitalise on a third acre of land. He was able to take in 80k a year,” he says.
Hussey was inspired by that, by somebody making the most of a small bit of land. So in June last year, in the middle of a pandemic and juggling working from home, Hussey and Abbot set about doing the same, albeit with a different model, and launched their vertical farm.
Image from: Farmony
How It Works
Farmony, which specialises in tech for vertical farming, sold Upfarm with the tools to get up and running – shelves, special LED lighting, a watering system and humidifiers. It is the ideal conditions for growing produce, says Framony co-founder John Paul Prior. Nutrients, hours of light, humidity and temperature are controlled in vertical farming, Prior says.
But Farmony is also a data company, Prior says. “So we capture data at all stages of the growing cycle. And we feed that back to the grower.”
This helps the grower to establish the optimum conditions, he says. “That’s not just in terms of plant growth, that’s in terms of workflow management.”
The size of an operation can be the small coldroom in Malahide that uses one Farmony module, and produces microgreens and wheatgrass for sale. Or it can be like a farm in Tipperary with 60 modules, he says. A module is 1 metre wide, 1.3 metres long and 2.5 metres tall, Prior says. Hussey says it is labour-intensive looking after a vertical farm module.
After work last Thursday, he and his dad replanted his microgreen crops into 30 different trays. “It took about two hours,” he says.
What Is the Benefit?
“So as long as you can control your temperature, your humidity, and your nutrient levels in the water, you can basically grow all year round,” says Prior. Vertical farming also means better conditions for workers, Prior says.
“If you’re working in a controlled environment, like a vertical farm, you’re working in a clean environment,” Prior says.
“You work between 18 to 22 degrees. There’s no harsh frost. There’s no extreme cold winters, equally there’s no burning-hot summers.,” says Prior.
The crop is consistent too, says Prior, thanks to the controlled environment.
“Let’s say I’m someone who loves basil and who makes a lot of pesto at home,” he says.
Getting basil of consistent quality from the supermarket can be difficult when it comes from different countries, or may have been sitting on a shelf for days after travelling thousands of miles, he says.
Image from: Farmony
Why Is this Important?
Soil quality is dropping, Hussey says. “What does that mean for outdoor growing?”
The answer, Hussey says, is vertical farming. It uses mineral-rich water so it doesn’t rely on nutrients from the ground, Hussey says.
Says Prior: “Vertical farming uses about 10 percent of the water of traditional farming.”
Prior says it takes less energy to get food from a nearby vertical farm than to ship it from afar. It was not always the case until a breakthrough in another industry, he says.
“Billions of dollars have been invested in the cannabis industry globally. It’s meant that the investment in grow-lighting technology has been huge,” he says.
“As a result, the price, the efficiency and most importantly, the energy efficiency of the lighting is really amazing” he says.
Says Hussey: “It’s not easy work but it is nice work. It’s good work.”
Ensuring Singapore's Food Security Despite the Odds
As with most issues that impact national security in Singapore, it often seems that the odds are stacked against us. Food security — access to safe and nutritious food — is a challenge on several fronts. Singapore is a small city-state with limited resources, with only 1 per cent of land available for food production, and over 90 per cent of food is imported from an increasingly disrupted world. The Covid-19 pandemic has further amplified the gravity of safeguarding food security
Image from: Reuters
As with most issues that impact national security in Singapore, it often seems that the odds are stacked against us. Food security — access to safe and nutritious food — is a challenge on several fronts.
Singapore is a small city-state with limited resources, with only 1 per cent of land available for food production, and over 90 per cent of food is imported from an increasingly disrupted world. The Covid-19 pandemic has further amplified the gravity of safeguarding food security. The city-state has been proactively planning for long-term food security through the Singapore Food Agency’s (SFA) strategy of “three food baskets” — diversifying food sources, growing locally and growing overseas. This approach has served the Republic well in securing a supply of safe food.
DIVERSIFIED SOURCING IS KEY
Singapore’s food importers leverage the nation’s connectivity and the global free trade environment to import from multiple sources in about 170 countries and regions worldwide. Should there be a disruption to any one source, importers are able to tap alternative food sources and ensure supply remains stable. Lockdown measures brought about by Covid-19 underscored Singapore’s vulnerabilities to supply disruptions in food.
It was not by luck that the Republic’s food supply remained stable and market shelves continued to be promptly restocked — it was the result of a deliberate whole-of-government strategy to diversify food sources. To keep the nation’’s diversified food supply lines intact amid the Covid-19 global pandemic, SFA worked closely with the Ministry of Trade and Industry and Enterprise Singapore (ESG) to monitor Singapore’s food supply situation. Together with the Ministry of Foreign Affairs, these economic agencies worked with like-minded countries to maintain open trade links.
LOCAL PRODUCTION AN IMPORTANT BUFFER
SFA drives innovation in local farms with the ambitious goal of producing 30 per cent of Singapore’s nutritional needs by 2030 as part of our “30 by 30” plan. To meet this goal, we need a holistic and long-term approach to space-planning, boosting agri-food technology and developing local agri-specialists. To facilitate and support the establishment of high-technology and productive farms in Singapore, SFA tenders out land based on qualitative criteria such as production capability, production track record, relevant experience and qualifications, innovation and sustainability.
In addition, a masterplan for the greater Lim Chu Kang (LCK) region, spanning about 390ha of land, will be undertaken in consultation with stakeholders over the next two to three years. The redeveloped LCK agri-food cluster will produce more than three times its current food production.
Building on the above efforts to grow Singapore’s high-tech agri-tech sector, SFA will continue to partner with the Economic Development Board and ESG to attract best-in-class global agri-tech companies, as well as to nurture promising homegrown agri-tech companies into local champions and help them to expand overseas.
EXPLORING ALTERNATIVE, UNDERUTILISED SPACES
Urban food solutions are expected to play a key role in global food security. While there are progressive enterprises operating out of farmlands and industrial estates, some agricultural game-changers are also taking root in unconventional areas — indoors, on rooftops and in underutilised spaces.
SFA worked with the Singapore Land Authority to introduce an urban farm at the former Henderson Secondary School site, which was transformed into Singapore’s first integrated space comprising an urban farm, childcare centre and nursing home within a state property. The farm space within the site was awarded in May 2019 to social enterprise City Sprouts, and it has become a vibrant destination for the young and old to learn about urban farming and enjoy a relaxing day out.
Citiponics, the first commercial farm located on a multi-storey car park in a residential neighbourhood, harvested its first yield of vegetables in April 2019. In September 2020, another nine sites atop multi-storey car parks were awarded for urban farming.
The successful bidders included proposals for hydroponic and vertical farming systems with a variety of innovative features, such as the Internet of Things (IoT), blockchain technology and automated climate control. These sites have the potential to collectively produce around 1,600 tonnes of vegetables annually.
Image from: Ciitiponics
TAPPING TECH
The Agriculture Productivity Fund (APF) supports local farms in their capability development and drive towards higher productivity. Through APF, SFA co-funds the adoption of farming systems to better control environmental variables, test-bed technologies and boost production capabilities. Between October 2014 and September 2020, a total of almost S$42 million has been committed to 115 farms.
The Covid-19 pandemic presented greater impetus to speed up local food production capacities. In September 2020, SFA awarded S$39.4 million to nine companies under the 30x30 Express Grant to quickly ramp up food-farm outputs over the next six months to two years. With advanced robotic and digital systems increasingly being used in farming, Singapore’s vegetables farmers have also become innovative agri-engineers and specialists in their own right.
With support from the 30x30 Express Grant, urban farming engineering solutions firm Indoor Farm Factory Innovation will set up an indoor vegetable farm with a vertical integration growth system up to 8m in height in a fully controlled and pesticide-free environment. The farm will leverage artificial intelligence farming systems integrated with IoT monitoring, dosing irrigation and an advanced environmental control system to achieve optimum growing conditions all year round.
Seng Choon, a chicken egg farm that has been in business for more than 30 years, has also proved itself a modernist in its operations. The company uses a computer that scans eggs to ascertain if they are clean; while feeding systems, temperature controls and waste cleaning systems have been automated with SFA’s support. Singapore’s efforts at ensuring food security would not be complete without support from consumers. To boost recognition of local produce among consumers, SFA brought the industry and public together to create a new “SG Fresh Produce” logo.
Farmers have been using this emblem on their packaging since August 2020. A website was also launched to provide a trove of information on locally farmed food. While the Covid-19 pandemic has led to import restrictions, it also helped to accelerate support for local produce. With public support for local farmers and other key measures, Singapore can beat the odds in ensuring food security in this ever-evolving, ever-disrupted world.
Is AppHarvest the Future of Farming?
In this video from Motley Fool Live, recorded on Jan. 28, Industry Focus host Nick Sciple and Motley Fool contributor Lou Whiteman discuss AppHarvest, one such SPAC that is looking to disrupt the agriculture industry. Here are the details on what AppHarvest wants to do, and a look at whether the company represents the future of farming.
Special purpose acquisition companies, or SPACs, are red-hot right now, with investors clamoring to get into promising young companies.
In this video from Motley Fool Live, recorded on Jan. 28, Industry Focus host Nick Sciple and Motley Fool contributor Lou Whiteman discuss AppHarvest, one such SPAC that is looking to disrupt the agriculture industry. Here are the details on what AppHarvest wants to do, and a look at whether the company represents the future of farming.
Nick Sciple: One last company I wanted to talk about, Lou, and this is one I think it's -- you pay attention to, but not one I'm super excited to run in and buy. It was a company called AppHarvest. It's coming public via a [SPAC] this year. This vertical farming space. We talked about Gladstone Land buying traditional farmland. AppHarvest is taking a very different approach, trying to lean into some of the ESG-type movements.
Lou Whiteman: Yeah. Let's look at this. It probably wouldn't surprise you that the U.S. is the biggest global farm exporter as we said, but it might surprise you that the Netherlands, the tiny little country, is No. 2. The way they do that is tech: Greenhouse farm structure. AppHarvest has taken that model and brought it to the U.S. They have, I believe, three farms in Appalachia. The pitches can produce 30x the yields using 90% less water. Right now, it's mostly tomatoes and it is early-stage. I don't own this stock either. I love this idea. There's some reasons that I'm not buying in right now that we can get into. But this is fascinating to me. We talked about making the world a better place. This is the company that we need to be successful to make the world a better place. The warning on it is that it is a SPAC. So it's not public yet. Right now, I believe N-O-V-S. That deal should close soon. [Editor's note: The deal has since closed.] I'm not the only one excited about it. I tend not to like to buy IPOs and new companies anyway. I think the caution around buying into the excitement applies here. There is a Martha Stewart video on their website talking up the company, which I love Martha Stewart, but that's a hype level that makes me want to just watch and see what they produce. This is just three little farms in Appalachia right now and a great idea. This was all over my watchlist. I would imagine I would love to hold it at some point, but just be careful because this is, as we saw SPACs last year in other areas, people are very excited about this.
Sciple: Yeah. I think, like we've said, for a lot of these companies, the prospects are great. I think when you look at the reduced water usage, better, environmentally friendly, all those sorts of things. I like that they are in Appalachia. As someone who is from the South, I like it when more rural areas get some people actually investing money there. But again, there's a lot of execution between now and really getting to a place where this is the future of farming and they're going to reach scale and all those sorts of things. But this is a company I'm definitely going to have my radar on and pay attention to as they continue to report earnings. Because you can tell yourself a story about how this type of vertical farming, indoor farming disrupts this traditional model, can be more efficient, cleaner, etc. Something to continue paying attention to as we have more information, because this company, like you said, Lou, isn't all the way public yet. We still got to have this SPAC deal finalized and then we get all our fun SEC filings and quarterly calls and all those sorts of things. Once we have that, I will be very much looking forward to seeing what the company has to say.
Whiteman: Right. Just to finish up along too, the interesting thing here is that it is a proven concept because it has worked elsewhere. The downside of that is that it needed to work there. Netherlands just doesn't have -- and this is an expensive proposition to get started, to get going. There's potential there, but in a country blessed with almost seemingly unlimited farmland for now, for long term it makes sense. But in the short term, it could be a hard thing to really get up and running. I think you're right, just one to watch.
Signify Adds Automatic Intensity Adjustment Plus Year-Long Recipe Modulations To Horticultural Controls
There’s something for both the greenhouse and the vertical farm in the GrowWise tweaks, which in some cases rely on tying to other systems’ sensors.
The Signify toplights at Belgium’s De Glastuin lettuce greenhouse automatically dim or brighten as daylight levels changes. (Photo credit: All images courtesy of Signify.)
Signify has enhanced the control system for its greenhouse LED lighting so that toplights can react immediately to changes in daylight conditions and adjust brightness accordingly. The company has also added year-long control settings intended to allow vertical farmers — but not greenhouses — to program seasonal variations in LED spectral content over a 365-day period.
Both upgrades are intended to reduce manual labor and improve overall cost efficiencies, Signify said.
Until now, greenhouse farmers could dim or brighten their Signify toplights by instructing the lights to do so via the control system, called GrowWise. Signify has now modified GrowWise software so that it can take readings from daylight sensors that are part of separate systems. GrowWise then instantly and automatically adjusts artificial light intensity emitted by the toplights, called Philips GreenPower LED.
“The lighting can be used much more efficiently since it gives us the flexibility to reduce light levels at any moment we need to,” said Wouter de Bruyn, the owner of Belgian lettuce grower De Glastuin, an early user of the new automatic feature.
Whereas Signify is known in office settings to build sensors into its smart luminaires, the GrowWise controls make use of sensors that are part of climate control systems and greenhouse management systems from companies such as Priva, Hoogendern Growth Management, and Ridder, all based in Holland.
Planet Farms’ Luca Travaglini backs up Signify’s point that prescribing a year of spectral content improves efficiency and helps keep down manual labor costs in controlled environment agriculture (CEA) operations such as vertical farms.
“The climate computer is equipped with a daylight sensor that sends actual light measurements to the GrowWise Control System so we can adapt our light levels automatically to ensure an even light level throughout the day and season,” de Bruyn said at De Glastuin, based in Kontich.
“Dynamic lighting in a greenhouse is the next step in improving the cost efficiency and quality for the cultivation process,” said Udo van Slooten, business leader, horticulture LED solutions at Signify. “It allows growers to effortlessly maintain a consistent level of light throughout the day to produce the best possible crops. The system compensates for cloudy weather and creates a more controlled growing environment for your crop.”
In another upgrade to GrowWise, vertical farmers who want to prescribe modulations in spectral content are no longer limited to 24 hours of looped recipe cycles. Rather, they can order up a year’s worth of shifts for controlled environment agriculture (CEA) operations.
The year-long programming feature is aimed at vertical farmers rather than at greenhouses because the lights that Signify provides for vertical farms support controllable spectral changes, whereas the greenhouse toplights do not. Signify refers to its GreenPower LED vertical farm lights as “production modules” rather than as “toplights.” Toplights and production modules can both be programmed for intensity over a year, but the intention of the year-long feature is oriented toward spectral content.
Compared to greenhouses, vertical farms tend to make much less, if any, use of natural light. In vertical farms, the lights are mounted much closer to the crop in stacked shelves.
One of the first users of the year-round feature is Italy’s greens and lettuce grower Planet Farms.
“Now we can easily create custom light recipes and set them to run year-round to provide the right light recipe with the right light intensity at the right time throughout the crop’s growth cycle,” said Planet Farms co-founder Luca Travaglini. “By automating our full light strategy during the growth cycle, for the whole year, we can run our operations very efficiently and keep our manual labor costs low. That makes it easier for us to maintain consistent quality as we scale up our production.”
The horticultural market is a key growth sector for Signify, especially as it maps out a strategy to maintain profits in the pandemic economy, in which last week it reported a yearly rise amid rigorous cost controls that now include a small number of layoffs. CEO Eric Rondolat is targeting a big chunk of what he has quantified as a $2 billion general horticultural lighting market by 2023.
MARK HALPER is a contributing editor for LEDs Magazine, and an energy, technology, and business journalist (markhalper@aol.com).
Abandoned Spaces And Automation: What To Expect For Indoor Farming in 2021
Controlled-environment agriculture — also simply known as indoor farming — had a big year both in terms of activity and investment dollars
Controlled-environment agriculture — also simply known as indoor farming — had a big year both in terms of activity and investment dollars. While once we might have questioned the sector’s economic viability and ability to actually feed a growing global population, a lot of those doubts have diminished and indoor ag in its many forms now has an important role in our future food system.
What that role is, however, will continue to evolve over time. Here are a few thoughts on how that will happen over the next 12 months.
More automation.
Automation isn’t new to controlled-environment agriculture, but its presence as a part of indoor farming operations has increased over the last several months and will continue to in the next year.
In the context of controlled-environment farming, automation can refer to any kind of technology that removes manual human labor from the growing process. In some cases that includes robots that plant and harvest greens or move trays of produce around the farm. More often, though, automation refers to software that can calculate the optimal environmental temperature for each plant, know when plants need to be fed and harvested, and handle many other calculations that would otherwise require a person to have horticultural and technological (hardware and software) expertise.
Moving into 2021, we’ll definitely see a few more robots buzzing around the indoor farm. But the bulk of automation will be about software.
More grocery store partnerships.
Many large-scale indoor farms started out selling their leafy green wares to restaurants and hotels. The pandemic, of course, put a hold on that in 2020, and controlled-environment agriculture operations had to look elsewhere for customers.
Enter the grocery store. From container farms at local markets to Kalera’s partnership with Publix stores across the U.S., more indoor farming companies are growing their greens either onsite at grocery stores or within throwing distance of them.
This could in turn help bring the cost of greens grown on high-tech farms down, since the shipping and distribution steps will be less resource intensive in many cases and nonexistent in others.
More underutilized space.
One of my favorite stories from 2020 was this one, about a company called Wilder Fields that turned an abandoned Target store in south Chicago into a massive indoor farm.
Many companies are constructing their own facilities from the ground up, while others stick to smaller scale container farms that are a bit more mobile. Finding existing space, such as an abandoned big box retailer, seems a logical middle ground, and one we’ll likely see more of as companies work to lower costs and keep their environmental footprint down.
Predictions pieces, of course, are always a bit of a crapshoot, and even if the above forecasts turn out to be true, they’ll be but a smattering of the activity that will happen for controlled-environment ag in 2021.
FILED UNDER: AG TECH BUSINESS OF FOOD DELIVERY & COMMERCE FEATURED FOODTECH
Marcel Koolen, Codema; "Food Safety, Automation And Reliability Are More Critical Than Ever"
“In this changing market, it is crucial that we provide the investor and what we call the 'corporate horticulturist' with the right information, knowledge and the proper perspective
Since 2017, Marcel Koolen has been at the head of Codema as CEO. He took over from founder Maarten de Jager, who meticulously merged various horticultural specialists into the Netherlands' leading supplier of horticultural solutions. It is his task to realize the international ambitions and at the same time, realize his own vision.
Market for horticultural solutions is changing
“We come from a world in which our customers, experienced growers who took over the company from their parents, know all about the technology. They exactly know what they need. These people choose the best solution for each individual aspect of their operation, for example, a logistics system from Hawe or a water solution from B-E De Lier. These critical cultivation systems can now be found under one roof: at Codema. This fits in well with the changing market. An increasing part of the market requires a conversation partner who comes up with a total solution.”
In recent years, horticulture has been a popular destination for the money of investors who want to invest on a large scale in, for example, medicinal cannabis, food production, and vertical farming. Floriculture and traditional growers also continue to develop and grow. Partly due to size, technical innovation must ensure higher efficiency or yield.
Conversation partner from the start
“In this changing market, it is crucial that we provide the investor and what we call the 'corporate horticulturist' with the right information, knowledge and the proper perspective. After which, we arrive at the delivery of critical cultivation systems. In the first place, this means that, from the beginning of their trajectory, we are a full conversation partner for these organizations. Our organization is now geared up for this.
Secondly, this requires an international presence. We are always building projects in America, Europe and the Asia-Pacific region with a particular emphasis on China. This goes beyond a simple sales organization, our "license to operate" depends on our ability to provide after-sales service and maintenance."
Due to these developments and continuing growth, the organization of Codema has grown strongly. "From the Netherlands, we serve and supply all over the world and on location we work as much as possible with local workers. Many beliefs converge in the latter; cost control from the customer and the influence of Nordian Capital. For example, on sustainability." However, Koolen's personal motives also make their mark:
“That does not mean that I make many difficult considerations or want to impose these on my customers. By applying new technological developments and continuing to work on both design and engineering, we already are more economical with raw materials.
Of course, it starts by considering if we can make better decisions in everything we think about and everything we do. Think about choosing green energy, solar panels, limiting flight movements, a hybrid fleet, and so on. Good business decisions that are simply better for our planet. It is no coincidence that this is also essential for our investor, Nordian Capital. Nordian’s entire investment portfolio compensates for all of its emissions through certified contracts with Land Life Company. This foundation is committed to the reforestation of around 2 billion hectares of land around the world.’’
A shared vision for the future
Originally, Marcel Koolen was an Electrical Engineer. However, he soon discovered that a wider field of vision suits him better. That theme had been a common thread in his entire career. Paired with his passion for what he calls ‘public interest’. With every step, his playing field grew larger.
‘The first time that it actually connected was with an electrical family business. There I quickly built up a department whose turnover was equal to that of the parent company and was allowed to slim it down a few years later. I have been able to face these kinds of challenges at an increasingly higher level. First at VolkerRail, during the privatization of the railways, and then at Spitzke and ABB.
When I started at Codema, significant changes were to come and therefore was an excellent fit. However, the main reason for my choice is our shared vision for the future. When I worked on the mobility of the Netherlands at VolkerRail, I noticed that serving the ‘public interest’ motivates me enormously. And at Codema we go further: we help feed the world. A good and efficient food production not only ensures that everyone has food but also makes it a lot less harmful to the environment. That is a challenge, which I would like to put my efforts into.’
Future and strategy Codema: food production
The herb cultivation market has boomed in recent years, and the legalization of the cultivation of medicinal cannabis has created a large capital inflow, which also benefited Codema. Codema realized critical cultivation systems in the largest, most advanced cannabis greenhouses in the world. These are greenhouses in which food safety and reliability, as well as automation, are more critical than ever. Codema also works in the floriculture with large cultivation organizations to apply the latest technology in areas such as software, water, lighting, and logistics. This provides knowledge and experience that Codema can directly apply to food cultivation.
“Investing in food production is a good business decision. The world population is growing, and with it, the demand for food. There are many challenges in this area that require a technical solution and where Codema can make the difference. That makes it a good investment for both investors and Codema. Since we are now active in the three major time zones, we reduce the risk of economic volatility further. That makes us future-proof.”
Cooperation in the chain
“That does not mean that Codema can do that alone. We work together with greenhouse builders and engineering -and consultancy firms, such as scientific researchers, educational institutions and market researchers. Partly because of this, Codema is able to present the final solution to the customer. This means that we go further than ever in our services. That is also what the market demands.”
When asked whether he is satisfied if, in Codema 2024 anchored her international position as a food production specialist, Koolen replies:
“We should always keep growing, but that doesn't mean it's always about financial growth. This could, for instance, be growth in the impact you have on the world. Or growth in knowledge and skills, the development of new technologies. We need to keep moving and ensure that Codema can continue to offer its customers the best proposition in the future.”
For more information:
Codema Systems Group
Oosteindsepad 8
2661 EP Bergschenhoek
The Netherlands
+31105212755
info@codemasystemsgroup.com
www.codemasystemsgroup.com
Publication date: Wed 8 Apr 2020
Green Automation Is Bringing Automation And Efficiency To New Greenhouse Operation In Texas
Green Automation Group is proud to announce the latest project realization in the North American market – hydroponic lettuce producer TrueHarvest Farms in Belton, Texas. The 50,000 square feet greenhouse is equipped with growing automation technology from Green Automation
October 24, 2019, Wellington, FL, USA
Green Automation Group is proud to announce the latest project realization in the North American market – hydroponic lettuce producer TrueHarvest Farms in Belton, Texas. The 50,000 square feet greenhouse is equipped with growing automation technology from Green Automation. Riding on the steadily increasing demand for locally grown produce, TrueHarvest Farms will grow fresh and pesticide-free head lettuce locally in the controlled environment of a greenhouse 365 days a year. The farm is strategically located in the “Texaplex Triangle”, which is formed between the cities, Dallas-Fort Worth, Houston, San Antonio, and Austin. With a population of around 20 million people and having 80% of the state’s population growth since 2000 as well as generating up to 70% of the Texas economy, this area is the ideal location for new, innovative and sustainable production of leafy greens.
“The climate here in Texas makes year-round field growing of leafy greens impossible and the area has so far, as the rest of the USA, relied heavily on having lettuce trucked into the state from California and Arizona for a substantial part of the year”, says Marshall McDaniel, Managing Member at TrueHarvest Farms. “We will be distributing truly fresh, nutritious, safe and locally grown lettuce to stores within a 250 miles radius of our operations. The lettuce will be available to the customer in less than 24 hours of harvesting”.
TrueHarvest Farms, rooted in Belton, TX, is ready to supply fresh, nutritious and safe leafy greens to the Texaplex Triangle.
Recent food safety scares in the lettuce industry has led to an increased interest in and call for safe and clean lettuce produced in a controlled environment. The greenhouse is a closed system, controlling what comes into the greenhouse, making it possible to not only keep the lettuce clean but also to grow them without using any chemical pesticides. The irrigation water, the air, and the growing medium are controlled, monitored and clean - keeping consumers safe and the environment protected.
“There is an enormous demand for locally grown and safe lettuce today”, confirms Jason Maks, Managing Member, and Grower at TrueHarvest Farms. “Our facility is in the final stage of obtaining PrimusGFS certification and we are dedicated to meeting the highest safety standards in the food industry. TrueHarvest Farms will be a reliable source for locally grown and safe produce for the Texas markets. We are ramping up our production right now and expect to reach full capacity in January 2020. At the moment we are growing Butterhead, Crisp and Romaine varieties”, explains Maks.
TrueHarvest Farms is using the automated growing system optimized for head lettuce production. “When growing leafy greens in tough climates it is imperative to operate the greenhouse with the highest efficiency and to generate the highest yields per square foot, therefore TrueHarvest Farms decided to use the automated growing system from Green Automation”, says Patrik Borenius, CEO, Green Automation Americas. “Throughout the entire growing process maximal space efficiency is achieved through automatic movement and adjustment of gutters, giving the plants as much space as needed, but as little as possible”.
In addition to maximizing yield through space efficiency, labor efficiency is an essential key component in a profitable operation. The system has a highly automated and versatile medium filling and seeding line arrangement using stackable trays and supporting both net pots as well as Ellepots. After seeding and germination, the plants are placed onto the automatic growing system, featuring adjustable and movable growing lines, where they will soak up the natural sunlight. As the plants grow, they are moved automatically through the greenhouse toward the harvesting station.
TrueHarvest Farms did multiple trips to reference operators in Europe, including to such remote locations as Joensuu, Finland, before making a decision. “It is a proven system and on par with our earth-conscious commitment. We are looking forward to growing and providing the Texas market with the highest quality lettuce”, says Marshall McDaniel. “This is only the beginning, we have room to grow and our head house as well as the irrigation system are designed for future expansions,” McDaniel explains.
Contact:
Patrik J. Borenius
Green Automation Americas LLC
13833 Wellington Trace, Suite #E4-203
Wellington, Florida 33414
About Green Automation Group
Green Automation Group Ltd, headquartered in Finland, and it’s subsidiary Green Automation Americas LLC, based in Florida, develop, manufacture and market the most advanced greenhouse automation systems for lettuce and herb production. The systems are designed for commercial greenhouse operations with a growing area of 1 acre / 0.4 hectares and above. www.greenautomation.com
About TrueHarvest Farms
TrueHarvest Farms, LLC is a controlled environment hydroponic farm specializing in leafy greens. Founded in 2017, the company is focused on rapid growth through the production and distribution of high-quality lettuce and other leafy greens. TrueHarvest Farms is the evolution of a family hay and pecan farm now 40 years old. So, whether it is the “family roots” or the “plant roots,” we are truly “Rooted in Belton, Texas”.
https://www.facebook.com/trueharvestfarms
Indoor Farming Technology Leader SANANBIO (R) Debuts UPLIFT (TM) Vertical Farming System
SANANBIO firmly believes that agriculture technology should be based on science paired with input from farmers
10/02/19
SANANBIO®, a leading provider in LED horticulture lighting and vertical farm technology, announces the commercial release of its fully automated vertical farming system: UPLIFT™ (Unmanned Platform of Lean and Intelligent Farming Technology). Decades of manufacturing and automation experience, combined with successful multi-year vertical farm operations through parent company Sanan Optoelectronics, have given SANANBIO the expertise necessary to design and prove the concept of UPLIFT.
SANANBIO firmly believes that agriculture technology should be based on science paired with input from farmers. Michael Yates, Sananbio VP of Sales, said, "With over one million square feet of commercial vertical farms currently using RADIX, farmers and investors in more than 10 countries believe in our company's highly engineered grow technology. The proof is in the plants as our customers like to say."
Sananbio UPLIFT
Fully automated vertical farming system
UPLIFT is based on RADIX™, SANANBIO's highly successful manual vertical grow system being used in farms today. "Farmers and investors in more than 10 countries and a combined one million square feet of commercial space believe in our company's highly engineered grow technology. The proof is in the plants as our customers like to say," said Yates.
UPLIFT offers a full suite of automation for growing vertically. From seeding and germination to transplanting and harvesting, the high-stack, high-cube configuration offers the latest advancements in vertical farming solutions that reduce labor while achieving higher yields. The UPLIFT farming platform also benefits from an industry-standard production and inventory management system facilitating crop management, farm production planning, and crop traceability.
"Labor costs continue to be a major challenge for vertical farm operators while also maintaining profitability," stated Dr. Charlie Wang, Sananbio U.S. CEO. "The UPLIFT system will help operators significantly reduce labor costs so they can sell more fresh and healthy produce and, therefore, receive better returns on their investment. The system also provides an open platform to integrate technology that enables farms with more intelligence and controls, allowing for maximized yields and profitability."
SANANBIO's is prepared to work with leading farmers and investors in the industry who share the same passion to build ground-breaking projects in controlled environment agriculture using this cutting-edge technology.
ABOUT SANANBIO®
SANANBIO^® is a trademark carried and backed by Sanan Sino-science Photobiotech, a company invested in by Sanan Optoelectronics, one of the world's largest LED chip manufacturers. Supported by an elite R&D team comprised of plant scientists, researchers, and engineers, SANANBIO utilizes state-of-the-art technology that enables growers in the horticulture industry to increase the quality and quantity of their yields. Years of extensive research and real-world deployment and operations allow SANANBIO to offer its customers proven, scalable, efficient and cost-effective solutions in LED horticulture lighting and Controlled Environment Agriculture (CEA) vertical farming grow systems. SANANBIO empowers growers with the technology and knowledge to achieve unprecedented results in farming operations. Learn more at https://sananbious.com/.
This Startup Is Building A Massive Indoor Farm In A Rust Belt Steel Town
The farm, from a startup called Fifth Season, will begin selling spinach, lettuce, and other leafy greens early next year, using a robot-based system that the founders say is cost-competitive with growing and transporting the same crops from a traditional farm
Fifth Season will begin selling spinach, lettuce, and other leafy greens—all grown inside with the help of robots—early next year.
[Photo: courtesy Fifth Season]
10.22.19
In a vacant lot next to one of the last remaining steel mills in Braddock, Pennsylvania, a town just south of Pittsburgh, a massive new indoor farm is taking shape. The farm, from a startup called Fifth Season, will begin selling spinach, lettuce, and other leafy greens early next year, using a robot-based system that the founders say is cost-competitive with growing and transporting the same crops from a traditional farm.
It’s more affordable, they argue than some others in the vertical farming industry. “We looked at vertical farming and realized that the industrywide struggle to make the economics work was a huge factor, and something that would really prevent the industry from truly taking off,” says Austin Webb, co-founder, and CEO of Fifth Season, which incubated its first farm at Carnegie Mellon University. “The per-unit economics don’t work. Companies are losing money for every pound that they sell. And that obviously needs to change.”
[Photo: courtesy Fifth Season]
Like others in the space, the startup touts the advantages of growing indoors. It’s possible to use only a tiny fraction of the water that’s used to grow greens in fields; most lettuce is currently grown in drought-prone California and Arizona. (In Arizona, farmers will also soon start losing access to water from the Colorado River.) Growing indoors eliminates the need for pesticides. It eliminates food safety hazards like E. coli contamination. And if crops are grown close to end markets—in this case, restaurants and stores in Pittsburgh—it also eliminates the emissions from trucks traveling thousands of miles and the problem of less-than-fresh produce that may be more likely to be thrown out because it’s already starting to wilt. “When we look at the food distribution system, we looked at it and saw an overly complicated broken system, where no one’s connected to their food, and there’s a lot of food waste,” Webb says.
[Photo: courtesy Fifth Season]
Some past efforts at indoor farming have failed because of high costs, such as FarmedHere, near Chicago, which shut down in 2017 in part because of the cost of labor. “When you look at vertical farms and labor is 40% to 60% of their cost—labor for them is actually more than the all-in delivered cost of Western-grown field produce—it’s just not going to work,” he says. The company’s system, which it has running now at another location and which it’s recreating at the new location, uses around 40 robots. “Together, they’re completely integrated so that our facility is, in a sense, one robotic system.”
Robots plant seeds in trays and deliver trays to grow rooms, where automated systems control everything from the amount of nutrients the plants receive to the schedule of lighting and the amount of carbon dioxide in the air. When a crop is ready, it goes into an automated harvesting system, and then to an automated packaging system, and the trays are sent back to be automatically cleaned and sanitized and then replanted. “We essentially looked at it and said that we should create an automated fulfillment center,” says Webb. “The difference being that instead of pallets of boxes, it should be trays of plants.” Solar panels on the roof and a battery backup system means that the facility can continue operating even if extreme weather takes out the electric grid.
[Photo: courtesy Fifth Season]
Other companies in the industry are also developing automated systems, including Plenty, a Softbank-funded Silicon Valley startup that now has a suite of state-of-the-art custom robotics. Plenty hasn’t shared the details of the cost of its system. But Fifth Season estimates, as an example, that its own robot used for storing and retrieving plants may cost two to three times less. It also uses space more efficiently than some other companies; because everything is automated and humans don’t need to access rows of produce on scissor-lift equipment, the aisles between plants can shrink, growing more produce in the same amount of space. (The new farm is 60,000 square feet, a little smaller than the 69,000-square-foot farm run by another company called Aerofarms.) During its first full year of operation, it expects to grow half a million pounds of greens and herbs, with prices in line with organically grown produce. At that price point, the payback period of the full system will be less than two years.
[Photo: courtesy Fifth Season]
In Braddock, where the population has shrunk more than 90% since its high point in the 1920s to around 2,000 people today, the new farm can provide some new jobs, despite the automation. Three shifts a day will employ 20 workers each. “These are manufacturing-like jobs where we’ve got folks that are helping us operate our machinery,” Webb says. “We’ve got folks that are monitoring the health of the equipment. All of that is something where someone can come from a previous job and you’re not necessarily saying you’re going to do something that’s totally completely different, such as sit at a computer and write code.” As the company expands, it will also hire more engineers and plant scientists.
The startup hopes to replicate the new facility, designed as a modular system, throughout the country. “We’re able to take what we’re building in Braddock and take those blueprints and really hit the repeat button quickly,” he says.
ABOUT THE AUTHOR
Adele Peters is a staff writer at Fast Company who focuses on solutions to some of the world's largest problems, from climate change to homelessness. Previously, she worked with GOOD, BioLite, and the Sustainable Products and Solutions program at UC Berkeley, and contributed to the second edition of the bestselling book "Worldchanging: A User's Guide for the 21st Century."
You Might Also Like:
Robots are already farming crops inside this Silicon Valley warehouse
Live in your own farm in the sky in this plant-covered apartment building
Video: The most crucial advice Patreon CEO Jack Conte has for any struggling creator
SPONSORED: OLD DOMINION
How Old Dominion is using technology to better serve its customers
Shenandoah Growers Opens Next Generation USDA Certified Indoor Biofarms In Virginia
The new BioFarms will solve persistent problems in the fresh product supply chain – delivering peak freshness, longer shelf life, enhanced food safety, reduced food miles, and year-round organic supply.
ROCKINGHAM, Va. — Shenandoah Growers, Inc., the US leader in indoor USDA certified organic agriculture, has begun harvests at its next generation BioFarm facilities in Rockingham and Elkwood, Virginia. The company will now grow, pack and ship locally grown, premium quality organic produce from its sustainable indoor farms to its customers in the Mid-Atlantic region 365 days a year.
Shenandoah Growers BioFarm Basil Plants
The new BioFarms will solve persistent problems in the fresh product supply chain – delivering peak freshness, longer shelf life, enhanced food safety, reduced food miles, and year-round organic supply. Shenandoah’s sustainable growing technology uses bioactive soil and fresh water, just like in nature, producing healthy organic plants and delivering on the company’s mission to reduce its carbon footprint and lead in environmental stewardship.
The Rockingham BioFarm will supply 100% of Shenandoah’s basil in the Mid-Atlantic region, marking the transition away from traditional field production. Basil is not only the best-selling herb, but it is also the most difficult to grow and ship nationally due to its vulnerability to weather volatility, disease and temperature damage. The Elkwood BioFarm will supply the company’s new line of local organic lettuces to Mid-Atlantic customers.
“Being able to grow the totality of our basil demand inside our pack house and not fly or truck hundreds or thousands of miles from the field was inconceivable when I entered the business over 20 years ago,” says Tim Heydon, CEO.
While Shenandoah Growers are pioneers in indoor organic agriculture, they are quick to emphasize that the company has been farming and operating in the industry for over 30 years. Chief Customer Officer Steven Wright intoned, “It’s one thing to be able to grow indoors, it’s quite another to harvest, pack and deliver with consistent quality 7 days a week, 52 weeks a year while meeting demand during peak seasons.”
The company points out that its indoor production units, many of which have been in operation for over 4 years, are proven efficient. According to company President, Phillip Karp, “Fundamentally we are about the democratization of sustainably grown organic produce, and for the promise of indoor agriculture to truly unlock its great potential, it must achieve cost parity with traditional farming. Anything we launch from our indoor farms will be scalable and profitable for us and our customers and affordable for the shopper.”
The company is in the process of accelerating its indoor farming capacity with a clearly defined plan to deploy additional next generation USDA certified organic Biofarms across its entire national platform of operating locations.
About Shenandoah Growers, Inc.
Founded in 1989, Shenandoah Growers is the leading grower and marketer of fresh organic culinary herbs in the United States, providing sustainable, USDA certified organic, regionally grown produce to retailers coast-to-coast. The Rockingham, Virginia-based company has developed the nation’s largest commercial indoor organic growing systems and continues to redefine how to bring fresh, organic, and sustainably farmed produce to market—operating across a nationally integrated platform of farms, production, and logistics facilities. For more information, please visit www.shenandoahgrowers.com.
Under the THAT’S TASTY® BRAND, Shenandoah Growers provides USDA organic, non-GMO, regionally grown, and sustainably farmed fresh culinary herbs and greens. Launched in 2017, the THAT’S TASTY BRAND offers consumers ways to add Pure Organic Flavor™ to their everyday cooking by offering a full line of products including living organic herb plants, fresh cut herbs, herb purees, lettuces and microgreens. www.thatstasty.com