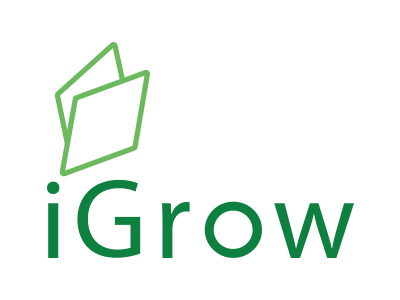
Welcome to iGrow News, Your Source for the World of Indoor Vertical Farming
"New Tabletop Growing System Requires Much Lower Capital Investment"
Plantlogic is focused on developing and producing containers and growing systems for substrate agriculture
Introducing "Plantlogic’s hi-grow system"
Plantlogic is focused on developing and producing containers and growing systems for substrate agriculture.
"The benefits of tabletop strawberry production are well known – boosting yields using substrate techniques and reducing labor costs. However, the capital investment needed for the most common system, metal gutters, can be a major barrier to the expansion of this growing system," they have seen.
"Furthermore, the substrate in slabs compromises many of the benefits of substrate production. Still, other tabletop systems compromise plant health by creating continuous troughs of the substrate with uneven drainage or sealing roots into a closed space."
For the past four years, Plantlogic has been developing a totally new tabletop growing system that seeks to reduce the capital investment while continuing to create optional conditions for roots to thrive. The result of these years of testing, design failures, and successes is the “Hi-Grow System”.
"Available in a variety of configurations including for troughs/pots, for slabs, with and without drainage collection. Now growers can enjoy the benefits of substrate tabletop production without compromising benefits with a much lower capital investment," they say.
Specific advantages of using Plantlogic’s Hi-Grow system are first, that it benefits from tabletop production at a lower cost. "Secondly, it supports troughs/pots, as the pots provide the best conditions for root development with a fixed volume, carefully controlled drainage, and oxygen uptake holes, making irrigation easier."
"Besides, it enables growers to do develop plants in the same container in a high-density nursery environment then move tabletops for fruit production. Growers can save money by using bulk substrate or enable the use of the blended substrate. Finally, growers can avoid labor for removal or pollution from the plastic film around slabs, and the truss support is included in the pots," they continue.
This solution supports the use of traditional substrate slabs. Also, drainage is collected into a narrow gutter. Growers can reduce risks by separating plants from drainage and other containers, as the trough is not continuous.
For more information:
Plantlogic
sales@getplantlogic.com
www.getplantlogic.com
17 Jun 2021
China Introduces Farm Display with Air Purifier
In a shopping mall in Urumqi City, people were attracted by an indoor growing display. While bringing fun to people who are growing, the product can also play a role in purifying the air.
In a shopping mall in Urumqi City, people were attracted by an indoor growing display. "It doesn't only allow you to eat fresh vegetables but it also purifies the air," said the representer.
The indoor farm cabinet is as big as a refrigerator, divided into four layers with LED lights installed on every level. Regardless of the vegetable planting machine occupies less than one square meter, it can grow seven or eight kinds of vegetables at the same time. There's a seedling area for the young plants to grow up, whereas the plants later can be transplanted for the final growing stage. When moved, they can be picked and eaten after 10 days.
The product allows to grow cherry tomatoes, coriander, Chinese cabbage, spinach, and strawberries. While bringing fun to people who are growing, it can also play a role in purifying the air. Especially for families with children, kids can observe the process of seed germination and vegetable growth, and follow the complete growing cycle.
The farm has already formed large-scale planting in the mainlands because of its multi-product growth and quick-growing cycles.
Source: k.sina.com.cn (In Chinese)
Publication date: Wed 9 Jun 2021
Sweden: Opening of New In-Store Vertical Farm At ICA Maxi
The opening event of the in-store vertical farm, a service provided and managed by Swedish technology company Swegreen, gained lots of traction from surprised and sometimes confused shoppers.
“We are actually making a difference here, because we grow next to the consumer, literally,” says Andreas Dahlin, CEO of Swegreen. “There are still many vertical farms that claim to produce sustainable, located close to the consumer, but they don’t mention the last mile. If logistics are needed to get the product to the consumer, they can still make a much bigger difference. That’s why we think this hyper-local model really makes an impact in the supply chain.”
It was all laughs and surprised faces during the opening at the ICA Maxi supermarket in Linköping this week. The opening event of the in-store vertical farm, a service provided and managed by Swedish technology company Swegreen, gained lots of traction from surprised and sometimes confused shoppers. Andreas opened the event by giving a toast to invitees. After explaining the concept, the crowd was allowed a visit to the farm.
Andreas leading the tour. Photo credit: Vertical farm daily.
Click here to view the photo report.
Biggest in Sweden
After successfully launching an in-store farm at ICA Focus, Gothenburg late 2020, the Swedish, fast-growing vertical farming enterprise Swegreen is now rolling out its Farming-as-a-Service concept in Scandinavia. First to get the installation in place is Ica Maxi in Linköping. The 60m2 farm supplies 10 different lettuces and herbs to the store – and more sorts are coming up – which makes this in-store growing facility the biggest in Sweden. Another share of the crops will be used in the store's own kitchen. Every day, several hundreds of crops are harvested that will end up on the shelves very soon after that.
Andreas adds, “The excessive heat from the farm is brought into the supermarket to optimally use all energy of the farm. We’re constantly looking at how we can optimize the cultivation processes up to energy use.”
Andreas explaining on vertical technologies. Photo credit: Verticalfarmdaily.
Full control
All technology is supplied and developed by Swegreen, such as the cultivation room and the AI-based control system which controls and optimizes the environment remotely. The farm is fully equipped with sensors, taking a huge relief off the farm operator who normally visits the facility 3-4 hours a day. Robot arms enable the gutters to be automatically moved from the beginning to the end-stage.
All processes are done on the farm, from seeding, breeding, cultivation and harvesting to packing the products. Everything in the farm is visible to the naked eye of store visitors.
Sepehr Mousavi, Chief Innovation Officer, and Innovation Lead at Swegreen explains that all technology is automated. “We can prevent any kind of error in the farm because the sensors will notify our technical services team immediately if something goes wrong to prevent any downtime.”
Click here to view the photo report.
Lead photo: Photo report: Swegreen launches event to celebrate project launch
For more information:
Swegreen
Andreas Dahlin, CEO of Swegreen
andreas.dahlin@swegreen.se
www.swegreen.se
Publication date: Wed 16 Jun 2021
Author: Rebekka Boekhout
© FreshPlaza.com
Vertical Farming Startup Oishii Raises $50m In Series A Funding
“We aim to be the largest strawberry producer in the world, and this capital allows us to bring the best-tasting, healthiest berry to everyone.”
By Sian Yates
03/11/2021
Oishii, a vertical farming startup based in New Jersey, has raised $50 million during a Series A funding round led by Sparx Group’s Mirai Creation Fund II.
The funds will enable Oishii to open vertical strawberry farms in new markets, expand its flagship farm outside of Manhattan, and accelerate its investment in R&D.
“Our mission is to change the way we grow food. We set out to deliver exceptionally delicious and sustainable produce,” said Oishii CEO Hiroki Koga. “We started with the strawberry – a fruit that routinely tops the dirty dozen of most pesticide-riddled crops – as it has long been considered the ‘holy grail’ of vertical farming.”
“We aim to be the largest strawberry producer in the world, and this capital allows us to bring the best-tasting, healthiest berry to everyone. From there, we’ll quickly expand into new fruits and produce,” he added.
Oishii is already known for its innovative farming techniques that have enabled the company to “perfect the strawberry,” while its proprietary and first-of-its-kind pollination method is conducted naturally with bees.
The company’s vertical farms feature zero pesticides and produce ripe fruit all year round, using less water and land than traditional agricultural methods.
“Oishii is the farm of the future,” said Sparx Group president and Group CEO Shuhei Abe. “The cultivation and pollination techniques the company has developed set them well apart from the industry, positioning Oishii to quickly revolutionise agriculture as we know it.”
The company has raised a total of $55 million since its founding in 2016.
Little Leaf Farms Raises $90M to Grow Its Greenhouse Network
Massachusetts-based Little Leaf Farms has raised $90 million in a debt and equity financing round to expand its network of hydroponic greenhouses on the East Coast. The round was led by Equilibrium Capital as well as founding investors Bill Helman and Pilot House Associates. Bank of America also participated.
by Jennifer Marston
Image from: Little Leaf Farms
Massachusetts-based Little Leaf Farms has raised $90 million in a debt and equity financing round to expand its network of hydroponic greenhouses on the East Coast. The round was led by Equilibrium Capital as well as founding investors Bill Helman and Pilot House Associates. Bank of America also participated.
Little Leaf Farms says the capital is “earmarked” to build new greenhouse sites along the East Coast, where its lettuce is currently available in about 2,500 stores.
The company already operates one 10-acre greenhouse in Devins, Massachusetts. Its facility grows leafy greens using hydroponics and a mixture of sunlight supplemented by LED-powered grow lights. Rainwater captured from the facility’s roof provides most of the water used on the farm.
According to a press release, Little Leaf Farms has doubled its retail sales to $38 million since 2019. And last year, the company bought180 acres of land in Pennsylvania on which to build an additional facility. Still another greenhouse, slated for North Carolina, will serve the Southeast region of the U.S.
Little Leaf Farms joins the likes of Revol Greens, Gotham Greens, AppHarvest, and others in bringing local(ish) greens to a greater percentage of the population. These facilities generally pack and ship their greens on the day of or day after harvesting, and only supply retailers within a certain radius. Little Leaf Farms, for example, currently servers only parts of Massachusetts, Pennsylvania, New York, and New Jersey.
The list of regions the company serves will no doubt lengthen as the company builds up its greenhouse network in the coming months.
Agritech: Precision Farming With AI, IoT and 5G
For a company that grows and delivers vegetables, Boomgrow Productions Sdn Bhd’s office is nothing like a farm, or even a vertical farm. Where farms are bedecked with wheelbarrows, spades and hoes, Boomgrow’s floor plan is akin to a co-working space with a communal island table, several cubicles, comfortable armchairs, a cosy hanging rattan chair and a glass-walled conference room in the middle
Image from: Photo by Mohd Izwan Mohd Nazam/The Edge
For a company that grows and delivers vegetables, Boomgrow Productions Sdn Bhd’s office is nothing like a farm, or even a vertical farm.
Where farms are bedecked with wheelbarrows, spades and hoes, Boomgrow’s floor plan is akin to a co-working space with a communal island table, several cubicles, comfortable armchairs, a cosy hanging rattan chair and a glass-walled conference room in the middle.
At a corner, propped up along a walkway leading to a rectangular chamber fitted with grow lights, are rows of support stilts with hydroponic planters developed in-house and an agricultural technologist perched on a chair, perusing data. “This is where some of the R&D work happens,” says Jay Dasen, co-founder of the agritech start-up.
But there is a larger farm where most of the work behind this high-tech initiative is executed. Located a stone’s throw from the city centre in Ampang is a 40ft repurposed shipping container outfitted with perception technologies and artificial intelligence (AI) capabilities that mimic the ideal environment to produce more than 50,000kg of vegetables a year.
Stacked in vertical layers, Boomgrow’s vegetables are grown under artificial lights with Internet of Things (IoT) sensors to detect everything from leaf discolouration to nitrate composition. This is coupled with AI and machine learning algorithms.
Boomgrow is the country’s first 5G-connected vertical farm. With the low latency and larger bandwidth technology, the start-up is able to monitor production in real time as well as maintain key parameters, such as temperature and humidity, to ensure optimal growth conditions.
When Jay and her co-founders, K Muralidesan and Shan Palani, embarked on this initiative six years ago, Boomgrow was nowhere near what it is today.
The three founders got together hoping to do their part in building a more sustainable future. “I’ve spent years advising small and large companies on sustainability, environmental and social governance disclosures. I even embarked on a doctorate in sustainability disclosure and governance,” says Jay.
“But I felt a deep sense of disconnect because while I saw companies evolving in terms of policies, processes and procedures towards sustainability, the people in those organisations were not transforming. Sustainability is almost like this white noise in the background. We know it’s important and we know it needs to be done, but we don’t really know how to integrate it into our lives.
“That disconnect really troubled me. When we started Boomgrow, it wasn’t a linear journey. Boomgrow is something that came out of meaningful conversations and many years of research.”
Shan, on the other hand, was an architect who developed a taste for sustainable designs when he was designing modular structures with minimal impact on their surroundings between regular projects. “It was great doing that kind of work. But I was getting very dissatisfied because the projects were customer-driven, which meant I would end up having debates about trivial stuff such as the colour of wall tiles,” he says.
As for Murali, the impetus to start Boomgrow came from having lived overseas — while working in capital markets and financial services — where quality and nutritious produce was easily available.
Ultimately, they concluded that the best way to work towards their shared sustainability goals was to address the imminent problem of food shortage.
“By 2050, the world’s population is expected to grow to 9.7 billion people, two-thirds of whom will be in Asia-Pacific. Feeding all those people will definitely be a huge challenge,” says Jay.
“The current agricultural practice is not built for resilience, but efficiency. So, when you think of farming, you think of vast tracts of land located far away from where you live or shop.
“The only way we could reimagine or rethink that was to make sure the food is located closer to consumers, with a hyperlocal strategy that is traceable and transparent, and also free of pesticides.”
Having little experience in growing anything, it took them a while to figure out the best mechanism to achieve their goal. “After we started working on prototypes, we realised that the tropics are not designed for certain types of farming,” says Jay.
“And then, there is the problem of harmful chemicals and pesticides everywhere, which has become a necessity for farmers to protect their crops because of the unpredictable climate. We went through many iterations … when we started, we used to farm in little boxes, but that didn’t quite work out.”
They explored different methodologies, from hydroponics to aquaponics, and even started growing outdoors. But they lost a lot of crops when a heat wave struck.
That was when they started exploring more effective ways to farm. “How can we protect the farm from terrible torrential rains, plant 365 days a year and keep prices affordable? It took us five years to answer these questions,” says Jay.
Even though farmers all over the world currently produce more than enough food to feed everyone, 820 million people — roughly 11% of the global population — did not have enough to eat in 2018, according to the World Health Organization. Concurrently, food safety and quality concerns are rising, with more consumers opting for organically produced food as well as safe foods, out of fear of harmful synthetic fertilisers, pesticides, herbicides and fungicides.
According to ResearchAndMarkets.com, consumer demand for global organic fruit and vegetables was valued at US$19.16 billion in 2019 and is anticipated to expand at a compound annual growth rate (CAGR) of 6.5% by 2026.
Meanwhile, the precision farming market was estimated to be US$7 billion in 2020 and is projected to reach US$12.8 billion by 2025, at a CAGR of 12.7% between 2020 and 2025, states MarketsandMarkets Research Pte Ltd.
Malaysia currently imports RM1 billion worth of leafy vegetables from countries such as Australia, China and Japan. Sourcing good and safe food from local suppliers not only benefits the country from a food security standpoint but also improves Malaysia’s competitive advantage, says Jay.
Unlike organic farming — which is still a soil-based method — tech-enabled precision farming has the advantage of catering for increasing demand and optimum crop production with the limited resources available. Moreover, changing weather patterns due to global warming encourage the adoption of advanced farming technologies to enhance farm productivity and crop yield.
Boomgrow’s model does not require the acres of land that traditional farms need, Jay emphasises. With indoor farms, the company promises a year-round harvest, undisturbed by climate and which uses 95% less water, land and fuel to operate.
Traditional farming is back-breaking labour. But with precision technology, farmers can spend less time on the farm and more on doing other things to develop their business, she says.
Boomgrow has secured more than RM300,000 in funding via technology and innovation grants from SME Corporation Malaysia, PlaTCOM Ventures and Malaysia Digital Economy Corporation, and is on track to build the country’s largest indoor farms.
Image from: Boomgrow
The company got its chance to showcase the strength of its smart technology when Telekom Malaysia Bhd (TM) approached it to be a part of the telco’s Smart Agriculture cluster in Langkawi last October.
“5G makes it faster for us to process the multiple data streams that we need because we collect data for machine learning, and then AI helps us to make decisions faster,” Jay explains.
“We manage the farm using machines to study inputs like water and electricity and even measure humidity. All the farm’s produce is lab-tested and we can keep our promise that there are no pesticides, herbicides or any preserving chemicals. We follow the food safety standards set by the EU, where nitrate accumulation in plant tissues is a big issue.”
With TM’s 5G technology and Boomgrow’s patent-pending technology, the latter is able to grow vegetables like the staple Asian greens and highland crops such as butterhead and romaine lettuce as well as kale and mint. While the company is able to grow more than 30 varieties of leafy greens, it has decided to stick to a selection of crops that is most in demand to reduce waste, says Jay.
As it stands, shipping containers are the best fit for the company’s current endeavour as containerised modular farms are the simplest means of bringing better food to local communities. However, it is also developing a blueprint to house farms in buildings, she says.
Since the showcase, Boomgrow has started to supply its crops to various hotels in Langkawi. It rolled out its e-commerce platform last year after the Movement Control Order was imposed.
“On our website, we promise to deliver the greens within six hours of harvest. But actually, you could get them way earlier. We harvest the morning after the orders come in and the vegetables are delivered on the same day,” says Jay.
Being mindful of Boomgrow’s carbon footprint, orders are organised and scheduled according to consumers’ localities, she points out. “We don’t want our delivery partners zipping everywhere, so we stagger the orders based on where consumers live.
“For example, all deliveries to Petaling Jaya happen on Thursdays, but the vegetables are harvested that morning. They are not harvested a week before, three days before or the night before. This is what it means to be hyperlocal. We want to deliver produce at its freshest and most nutritious state.”
Plans to expand regionally are also underway, once Boomgrow’s fundraising exercise is complete, says Jay. “Most probably, this will only happen when the Covid-19 pandemic ends.”
To gain the knowledge they have today, the team had to “unlearn” everything they knew and take up new skills to figure what would work best for their business, says Jay. “All this wouldn’t have been possible if we had not experimented with smart cameras to monitor the condition of our produce,” she laughs.
How This Vertical Farm Grows 80,000 Pounds of Produce per Week
To some, the pristine growing conditions and perceived mechanical interference of a vertical farm can seem unnatural, but at Bowery Farming “interference” is actually not the goal at all. “We don’t really think about how people are involved in the growing process, but how to take people out of the growing process”
Bowery Farming uses technology to prioritize accessibility and sustainability in their produce growing operations
To some, the pristine growing conditions and perceived mechanical interference of a vertical farm can seem unnatural, but at Bowery Farming “interference” is actually not the goal at all. “We don’t really think about how people are involved in the growing process, but how to take people out of the growing process” says chief science officer Henry Sztul. “Our goal is actually to have as few people walking around our plants as possible.”
Bowery Farming is a network of vertical farms working to reengineer the growing process. Using a system of light and watering technology, Bowery is able to use 95 percent less water than a traditional outdoor farm, zero pesticides and chemicals, and grow food that tastes as good as anyone else’s.
Bowery Farming uses vertical farm-specific seeds that are optimized for flavor instead of insect resistance and durability. Seeds are mechanically pressed into trays of soil, and sent out into growing positions, or racks within the building that have their own lighting and watering systems. Each tray gets its own QR code so that they can be monitored and assigned a customized plan for water and light until they’re ready to be harvested.
Irving Fain, Bowery Farming’s founder and CEO contemplates the prediction from the United Nations that 70 to 80 percent of the world’s population will be living in and around cities in the next 30 years. “Figuring out ‘how do you feed and how do you provide fresh food to urban environments both more efficiently as well as more sustainably?’ is a very important question today, and an even more important question in the years to come.”
10 Ways Square Roots’ Farm-Tech Platform Empowers The Next Generation of Farmers
Square Roots’ scalable “farmer-first” platform brings fresh, healthy food to urban areas all year-round, while simultaneously training future generations of farmers to maintain sustainability in the future.
Square Roots is building a distributed network of indoor, modular farms, farmed by a new generation of farmers, to grow local food for people in cities all over the world. Here’s why it’s working.
Square Roots Super Farms are scalable, resilient and smart, and can be built fast. (Image: Via Chicago Architects + Diseñadores)
Square Roots’ scalable “farmer-first” platform brings fresh, healthy food to urban areas year-round, while simultaneously training future generations of farmers. With production farms in Brooklyn, New York, and Grand Rapids, Michigan (with more to come in 2020!), Square Roots has a mission to bring local, real food to people in cities across the world while empowering the next generation of leaders in urban farming.
Whether we’re in the farms tweaking CO2 levels, or in a board meeting plotting a pathway for what the company looks like in 2050, every decision we make is guided to help us achieve our mission faster, smarter, and with as much impact as possible.
Choices we’ve made around our technology platform are a good illustration of that. Our platform needs to bring fresh, healthy food to urban areas year-round, consistently, sustainability, and on any continent in the world. At the same time, it must also be a welcoming environment, conducive to training future generations of farmers to be productive, fast.
Central to our platform is the decision we made very early in the company’s life to build a distributed network of modular Climate Containers, as opposed to following the plant factory template.
Inside a Square Roots Climate Container, data-empowered farmers work with optimum growing conditions, all year round.
There are a lot of smart people in this industry, many with different visions for the optimum architecture and model for indoor farming (e.g. plant factories). But all working hard to bring better food to market — which, given our wider vision to bring real food to everyone, is wonderful to see. The more of us working on the real food revolution the better — and we want all of these systems to flourish. But here are 10 reasons why we think container farming rocks:
1. Speed to Market
Today we can enter a new market and open a Square Roots “Super Farm” — with 25 Climate Containers, cold storage, biosecurity infrastructure, and everything else you need to run a food-safe farm at scale — in less than three months, like we did in partnership with Gordon Food Service last Fall. That time period is only coming down. In comparison, building a plant factory can cost tens of millions of dollars, as well as take years to construct. We want to get real food to more people, and fast!
2. Easy to Scale
To meet increasing market demand, we simply add Climate Containers to any existing deployment. This means just-in-time capital deployment, and also just-in-time technology deployment. This is really important in an industry where the technology is improving fast. You don’t want to spend years and millions to open a big farm full of old tech that immediately needs a refresh.
3. Climate Control
I was an early investor in Chicago’s Farmed Here, one of the first and largest plant factories in the US. There, I saw first-hand how much the team struggled to control the climate in a building that size. Plants don’t like it when you get it wrong. And neither do landlords — the humidity can wreak havoc with the underlying infrastructure. In our programmable Climate Containers, each one built inside a 320 square foot shipping container, optimum conditions for a variety of crops can easily be maintained. The perfect climate for each variety can be seamlessly replicated — in any market — to ensure consistent quality every time, at every harvest.
Alyssa Patton, Square Roots Next-Gen Farmer, harvesting fresh, local basil inside a Climate Container in Grand Rapids, Michigan.
4. Diversity of Products
Multiple containers on our Super Farms allow for multiple climates, which lets us grow multiple crops at the same time to satisfy local market demands. For example, basil requires a completely different climate than chives to grow well, so it’s practically impossible to grow these two products together in a way that tastes good if you have a giant farm with one mono climate. The ability to grow multiple quality SKUs is particularly important in the retail market, where product variety is key to getting shelf real estate. Having multiple climates also means we can tackle many niches in any local market (e.g. using one container on a Super Farm to grow something exotic like Shiso or Mustard Greens), giving us a lot of business flexibility while keeping things interesting for our teams of farmers.
5. Sustainable Systems
As with most hydroponic growers, Square Roots uses zero pesticides, and 90% less water than outdoor farms. We can also be clever about energy usage. For example, we make it “daytime” in the farm by turning on our grow lights overnight when there is excess energy in the grid, and the cost per kilowatt-hour is lower. However, if for some reason we need to be in the farms during “daytime,” we can put a Climate Container into “harvest mode” — which dims the lights, and configures the climate to be optimum conditions for people at work — before seamlessly switching back to plant growing mode once we’re done.
6. Location
Our modular architecture means we can be very creative in repurposing existing city infrastructure when we look for locations to build a farm. We can pop up on an empty parking lot like we did in Brooklyn, New York, or build a campus on the headquarters of a major distribution company like we did with Gordon Food Service, or even build into a new development. This flexibility means we can build our Super Farms literally in the same zip code as the end consumer. This means fresher and tastier products for the customer, fewer food miles (most industrial food is shipped in from the other side of the world!), and less food waste. It also helps to get consumers more connected to their food and the people who grow it — they can simply jump on a subway or in their car, and come visit one of our farms!
7. Food Safety and System Resilience
All indoor farms need to be prepared for bad things to happen. While there is way less risk in a controlled environment versus an outdoor farm, it’s inevitable that you will get some sort of pest outbreak, powdery mildew, or some other issue at some point while you’re managing a complex ecosystem full of living, breathing plants. If that ever should happen in one of our Climate Containers, we can quickly shut it down and reboot that single node while the rest of the network keeps going strong. I’ve seen this happen in a plant factory, with one big mono climate, and you lose all your crops.
8. Faster Learning
Our farms are cloud-connected, and we collect millions of data points that we analyze to determine how changes in certain environmental parameters can impact factors like yield, taste, and texture of the final product. More climates in more containers means more feedback loops, which means faster learning. To systematize this learning, we’ve built The Square Roots Farmer Toolbelt — a software which is now the OS for the whole company as we all learn faster together.
9. The Network Gets Smarter as it Scales
Square Roots’ cloud-connected farms and data-empowered farmers learn from each other, enabling us to replicate success from one location to another, seamlessly. Working with Gordon Food Service to build farms across their network of distribution centers and retail stores brings us closer to the vision of a distributed network of indoor farms, bringing local, real food to people in cities across the world—while empowering thousands of next-gen leaders in urban farming through our unique training program.
10. Sense of Responsibility
Perhaps this is unique to Square Roots and our Next-Gen Farmer Training Program, but because we grow in modular Climate Containers, we’re able to give all our young farmers a personalized understanding of their individual impact on the overall business. The Square Roots Farmer Toolbelt provides day-to-day instructions on a per-farmer and per-crop basis, as well as a means for data capture, and real time analysis of both plant health and business metrics. All this information is accessible from the tablets that everyone on our farm team carries everyday. This system also ensures that we track every aspect of production — who does what, when, and how, from seed to sales. This is a goldmine of data, that not only helps us improve operations, but also implicitly provides traceability. In December 2018, we started exposing this data to consumers in the form of our Transparency Timeline. On every package of Square Roots produce, you can simply scan a QR code and get a complete story of where your food comes from — seed to shelf.
Simply scan the QR code on every Square Roots package to see where your food comes from.
Our Super Farm platform is exciting in terms of scalability, resilience, and efficiency, and it’s a really wonderful environment for our farmers to farm in. For urban consumers it means local farmers growing your food with love — which is why it tastes absolutely delicious. And technology enables us to grow a ton of food in a very small area, in ways that make a lot of business sense too. It’s a classic example of “doing well by doing good”.
It has been an exciting journey to our Super Farm platform. When we launched Square Roots back in 2016, we were very focused on figuring out the Farmer Training Program model — as we knew that farmers bring love to the food, the program would create enormous impact over time, and it would also be a long term engine of growth. So we partnered with a number of 3rd parties who could provide parts of the growing system for us, while we got the training program right. (In many ways, that was like Tesla sourcing our chassis from Lotus for the first Roadster). After that initial phase, and finding out what the urban farming world needs — i.e. higher quality yields with much lower costs to drive scalable unit economics, and ultra-high standards of biosecurity to support operations that are first class in food safety—we have developed our own technology specifically tailored to our model. This enables us to grow local food at incredible scale in ways that make sense for people, planet, and profits.
Our partnership with Gordon Food Service was announced at the end of March 2019, and our first co-located farm opened just six months later in Grand Rapids, Michigan — marking our next step of bringing local food to people in cities all across North America while training thousands of future farmers. Which, in a neat and circular way, brings us right back to the mission statement we started this post with.
Of course, we still have lots of work to do and we have a lot of exciting announcements coming this year as we grow! And, we’re always looking to talk with great people — from hardware and software engineers to farmers and plant scientists. So feel free to check our website and get in touch.
This article was originally published on the Indoor Ag-Con blog by Kimbal Musk on March 4, 2020.
Published by Dani Kliegerman for iGrow News
Ikea Just Shared Its Garden Sphere Design For Free
Blueprints for IKEA’s Garden Sphere are available for free download, distribution, and reuse. The product design allows any users to feed an entire street, block, or even neighborhood, depending on population
IKEA's idea lab Space 10 created a sustainable, spherical garden for urban environments called The Growroom with open-source blueprint and instructions.
IKEA is making its garden sphere design free to access.
May 12, 2020
Blueprints for IKEA’s Garden Sphere are available for free download, distribution, and reuse. The product design allows any users to feed an entire street, block, or even neighborhood, depending on population.
The Growroom gardening sphere design makes it easy to grow fresh produce in dense urban areas. The multi-tiered, spherical design mimic some forms of verticle gardening by maximizing airspace. The structure’s designers, architects Sine Lindholm and Mads-Ulrik Husumtoin are part of Space 10—IKEA’s innovative idea lab.
The entire Growroom frame can be constructed with just a few supplies: plywood, screws, a hammer, and access to a local fab lab. Experts suggest small workshops offering digital fabrication are increasingly commonplace. “This means most people — in theory — could produce almost anything themselves,” the company press release read.
Community-grown food minimizes the distance traveled and other contributing factors in food production’s carbon footprint. Many people do not have ready access to fresh produce and outdoor space. The Growroom can help facilitate shared access to both.
“Local food represents a serious alternative to the global food model. It reduces food miles and our pressure on the environment and educates our children about where food actually comes from,” Space 10 noted on its website. “The challenge is that traditional farming takes up a lot of space — and space is a scarce resource in our urban environments.”
The Growroom could increase access to fresh produce in urban areas. | Image/bellinghammakers
IKEA And Sustainability
IKEA emphasizes sustainability in several other areas of its business. In its 2018 sustainability report, IKEA estimated its climate footprint to be 26.9 million tons of carbon dioxide equivalent. Following this, the home furnishings retail giant announced plans to invest over $220 million in efforts to become “climate positive.”
IKEA has also banned all single-use plastic from its cafes to minimize waste and preserve the environment. Instead, the company now uses alternatives such as wooden cutlery and paper straws. The retailer says it sources all materials from sustainable suppliers.
STAFF WRITER | BRISTOL, UNITED KINGDOM | CONTACTABLE VIA: LIAM@LIVEKINDLY.COM
Liam writes about environmental and social sustainability, and the protection of animals. He has a BA Hons in English Literature and Film and also writes for Sustainable Business Magazine. Liam is interested in intersectional politics and DIY music.
Produce Fresh Vegetables In The Comfort of Your Home
BY JAMES HOARE 01/10/2019
When we think of growing plants, phrases such as ‘High maintenance’, ‘Unreliable’ and ‘Time consuming’ spring to mind. But this doesn’t always have to be the case… and Aspara proves this!
Aspara is a smart indoor garden that encourages the growth and consumption of fresh, healthy vegetables and herbs! Remembering to water the plants is a thing of the past; a scaled-down hydroponics farm system has been neatly integrated into the design, allowing for a reduced amount of wasted water, a faster plant growth, and perhaps most importantly, the elimination of the need for regular watering!
It’s not just watering that Aspara simplifies… it removes complexity from the start with its dedicated seed kits; the organic and/or non-GMO capsules plug straight into tray, removing the need for getting your hands dirty! The conditions of the plant’s environment can be monitored remotely from the mobile app, where you can also enter into a community of fellow gardeners, and share tips, tricks and advice on how to get the most out of your indoor garden!
Designer: Julian Bowerman
Click Here to Buy Now: $328 $499 (34% off). Hurry, less than 48 hours left!
The aspara™ smart indoor grow box is a miniaturized hydroponics farm system. Hydroponics is a method of growing plants without soil by using mineral nutrient solutions in a water solvent.
aspara™’s smart built-in sensors monitor, detect, report and record growth conditions based on nutrient concentration, air temperature, humidity, water temperature and overall water content in the system.
The sensors will adjust lighting, water flow and planting modes based on your plant’s needs. Precise monitoring of the growth conditions provides accurate instruction on the amount of water and nutrients required to be refilled into the system.
The adjustable grow light provides a full spectrum of intensity that caters to the needs of different plants at different growth stages, as well as your personal preference. Control growth through specific programs and replicate nature with sunrise and sunset scenery.
The reservoir water system automatically waters your seeds and plants based on their nutrient levels and stage of life. The automatic ebb-and-flow-design circulates the water so that nothing is wasted.
The aspara™ seed kits start with 15+ different organic and/or non-GMO seed capsules (selected) with nutrients that guarantee a 100% germination rate by just plugging the capsules into the specialty grow tray. It’s that simple!
The aspara™ IoT-connected app provides necessities, such as your plant’s light, water, temperature, and nutrient information, and it tracks your plant’s activities and conditions, but it does so much more…
The aspara™ app is a community platform for support, as well as a space to share your plants’ growth with people who share a similar passion. You can even share your progress through photos and videos on social media!
Singapore Changi, The World’s Best Airport To Open A Valoya Lit Indoor Garden
For 8 consecutive years Singapore’s Changi airport has been dubbed the world’s best. It is a hub for 62 million passengers annualy and is known worldwide for its indoor greenery designed to promote Singapore’s reputation as a city of gardens. The extension which is to be opened in the first half of 2019 is a futuristic looking dome of curved glass and steel with the world’s highest waterfall (40 m) placed at its center.
Photo by Jewel Changi Airport
The dome will be populated with flora that consists of 2.000 trees and over 100.000 other plants. These will receive sunlight through the glass of the dome which will be supplemented by Valoya’s luminaires, custom made for the Changi Airport. Valoya is a provider of LED grow lights for the crop science, vertical farming and medicinal plants markets globally, known for their research driven approach and high quality, wide spectra. In addition to the standard product series, Valoya offers custom made solutions developed for large scale projects such as Singapore’s renowned airport. These custom solutions are typically made for projects that are demanding and need a high degree of engineering and photobiology expertise and support.
The form factor of the luminaires resembles a compact box designed to fade into the background and not distract from the plants. Valoya’s powerful LEDs are placed inside with a spectrum optimized for the entire growth cycle of the widest variety of plants. The spectrum’s color is a warm white designed to seamlessly fuse with natural sunlight. It is safe for and pleasant to human eyes.
The construction of this dome is a 1,7 billion dollar project. The order of Valoya luminaires is already delivered to the customer and is in the installation phase. In March 2019 the dome will open its doors to the visitors.
About Valoya Oy
Valoya is a provider of high end, energy efficient LED grow lights for use in crop science, vertical farming and medicinal plants cultivation. Valoya LED grow lights have been developed using Valoya's proprietary LED technology and extensive plant photobiology research. Valoya's customer base includes numerous vertical farms, greenhouses and research institutions all over the world (including 8 out of 10 world’s largest agricultural companies).
Additional information:
Valoya Oy, Finland
Tel: +358 10 2350300
Email: sales@valoya.com
Web: www.valoya.com
Facebook: https://www.facebook.com/valoyafi/
Twitter: https://twitter.com/valoya