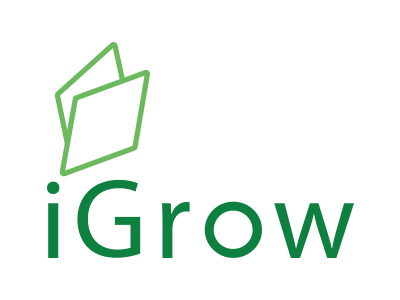
Welcome to iGrow News, Your Source for the World of Indoor Vertical Farming
Vertical Farming Startup Oishii Raises $50m In Series A Funding
“We aim to be the largest strawberry producer in the world, and this capital allows us to bring the best-tasting, healthiest berry to everyone.”
By Sian Yates
03/11/2021
Oishii, a vertical farming startup based in New Jersey, has raised $50 million during a Series A funding round led by Sparx Group’s Mirai Creation Fund II.
The funds will enable Oishii to open vertical strawberry farms in new markets, expand its flagship farm outside of Manhattan, and accelerate its investment in R&D.
“Our mission is to change the way we grow food. We set out to deliver exceptionally delicious and sustainable produce,” said Oishii CEO Hiroki Koga. “We started with the strawberry – a fruit that routinely tops the dirty dozen of most pesticide-riddled crops – as it has long been considered the ‘holy grail’ of vertical farming.”
“We aim to be the largest strawberry producer in the world, and this capital allows us to bring the best-tasting, healthiest berry to everyone. From there, we’ll quickly expand into new fruits and produce,” he added.
Oishii is already known for its innovative farming techniques that have enabled the company to “perfect the strawberry,” while its proprietary and first-of-its-kind pollination method is conducted naturally with bees.
The company’s vertical farms feature zero pesticides and produce ripe fruit all year round, using less water and land than traditional agricultural methods.
“Oishii is the farm of the future,” said Sparx Group president and Group CEO Shuhei Abe. “The cultivation and pollination techniques the company has developed set them well apart from the industry, positioning Oishii to quickly revolutionise agriculture as we know it.”
The company has raised a total of $55 million since its founding in 2016.
The Stock Market Discovers Indoor Ag In A Big Way
Special purpose acquisition companies are a faster cheaper way to raise company funds than the traditional IPO process. What role may they play in our ever growing vertical farming industry?
Robinhood antics aside, there’s no hotter topic in finance right now than SPACs (special purpose acquisition companies), and even indoor agriculture has become caught up in the buzz.
SPACs, or special purpose acquisition corporations, are a shell company that lists itself on a stock exchange and then uses the listing proceeds to acquire or merge with another company. It’s an attractive route to raising funds for companies looking for a faster and cheaper way to list than the rigours of the traditional IPO process.
Though SPACs have been around since the 1990s, they have had a reputation for being “the buyer of last resort”, primarily owing to a spate of failures in the early 2000s. The approach has once more taken off in recent years. There was nearly 8x as much raised in 2020 as in 2018, and 2021’s total has already surpassed last year’s[1]. The approach has become so hot that even Goldman Sachs junior investment bankers recently complained that they were burned out by the sheer volume of SPACs they’re working on[2].
This newfound enthusiasm is generally traced to a combination of tighter SEC regulations, efforts by cash-rich private equity companies to exit portfolio companies and fewer traditional IPO listings. Higher quality sponsors, such as 40-year old private equity firm Thoma Bravo, lead some to believe that things are different this time around. The lustre of famous SPAC participants – such as baseball player A-Rod and basketball legend Shaquille O’Neal – has helped things along.
Detractors point to post-listing underperformance by SPACs, high fees to sponsors and opaqueness around the acquisition of companies. SPAC rules mean that institutional investors sometimes get to see information on potential acquisitions ahead of retail investors.[3] On a recent Clubhouse chat, one investor compared SPACs to the risky no-revenue internet listings of the late 1990s. Another questioned whether retail investors’ appetite for such vehicles would cause greater market volatility[4].
Dan Bienvenue, the interim CEO of mega public pension fund CALPERs, recently described SPACs as “fraught with potential misalignment, potential governance issues”.[5] That said, similar dire warnings have accompanied the rise of many a new approach in finance, most recently equity crowdfunding, and have proven wrong as often as right.
As is so often the case in indoor agriculture, cannabis companies have led the way when it comes to SPACs, generally listing in Canada owing to the US federal prohibition on the crop. One example is Choice Consolidation Corp, which raised $150mm in February, and says that it plans to acquire “existing strong single-state operators”[6].
Historically, food-focused indoor agriculture companies have sourced little of their capital from public markets, preferring instead to work with private equity and strategic investors. To be sure, there is a small cadre of listed CEA firms, such as Canadian greenhouse operator Village Farms (TSE: VFF) and Canadian grow system tech company CubicFarm Systems Corp (TSXV: CUB) are exceptions to this rule.
All of that changed last month when Kentucky-based greenhouse company AppHarvest raised $475mm through NASDAQ listed SPAC Novus Capital. The funds will fuel the expansion of up to a dozen new farms through 2025.
Naturally, the move has led to speculation that vertical farms and greenhouses will follow suit, though it’s worth noting that the rules that govern SPACs aren’t necessarily friendly to CEA companies. They favour large, highly valued companies that easily capture the attention of retail investors, and those are not plentiful in CEA.
Regardless of whether the SPAC trend becomes a permanent feature of the indoor farm fundraising landscape, one more method of accessing capital for CEA can only be a good thing. For the moment at least.
For more information:
Contain
www.contain.ag
Note: None of the above constitutes investment advice.
Sources:
[1] SPACInsider figures
[2] “Goldman’s junior bankers complain of crushing workload amid SPAC-fueled boom in Wall Street deals”, CNBC, March 18, 2021
[3] For instance, where a PIPE is being considered by the SPAC
[4] “SPACS: IPO 2.0 & Agrifoodtech Exits”, March 4, 2021
[5] “CalPERS’ Bienvenue: SPACs are fraught with potential misalignment”, Private Equity International, March 16, 2021
[6] “New cannabis SPAC raises $150 million in IPO for US acquisitions”, Marijuana Business Daily, February 19, 2021
Publication date: Wed 24 Mar 2021
Author: Rebekka Boekhout
© VerticalFarmDaily.com
US-VIRGINIA: Arlington’s Only Commercial Farm To Expand, Double Production
Virginia Gov. Ralph Northam announced this afternoon that Fresh Impact Farms will be getting a $30,000 grant — half from the state, half from the county — that will help it double production and create six jobs.
Believe it or not, Arlington County has a working commercial farm.
The farm, which is located in a commercial building along Lee Highway, uses hydroponic technology to grow a variety of edible plants indoors. And it’s about to expand.
Virginia Gov. Ralph Northam announced this afternoon that Fresh Impact Farms will be getting a $30,000 grant — half from the state, half from the county — that will help it double production and create six jobs.
Fresh Impact, Arlington County’s only commercial farm, is banking on its restaurant customers ramping up purchases as vaccinated customers flock back to the indoor dining. It also launched a direct-to-consumer Community Supported Agriculture program last year.
County Board Chair Matt de Ferranti hailed the business and its expansion.
“Governor Northam’s award to Fresh Impact Farms, Arlington’s only commercial farm, is an innovative way to celebrate unique uses of technology to help a small business pivot during the pandemic,” de Ferranti said in a statement. “I am thrilled that Fresh Impact Farms is growing and looking to the future of a sustainable food supply.”
More on the company’s expansion, below, from a press release issued by the governor’s office.
Governor Ralph Northam today announced that Fresh Impact Farms will invest $137,500, create six new jobs, and more than double production at its Arlington County indoor facility. Operating since 2018 as Arlington’s only commercial farm, Fresh Impact Farms uses proprietary hydroponic technology to grow a variety of specialty herbs, leafy greens, and edible flowers for sale to customers in the Greater Washington, D.C. metro area.
Like many companies, Fresh Impact Farms has pivoted its business model amid the COVID-19 pandemic. Seizing the opportunity created by more people cooking at home, the company initiated a Community Supported Agriculture (CSA) program targeting area residents. The CSA program, which focuses on leafy greens and home kitchen-friendly herbs, has grown steadily since its establishment in April 2020 and now includes smaller wholesale clients. Now, with vaccinations underway and the restaurant industry poised to rebound, Fresh Impact Farms is expanding, which will allow the company to resume supplying their restaurant customers, while also meeting new demand through their CSA program.
“Agriculture continues to be a key driver of our economic recovery in both rural and urban areas of our Commonwealth,” said Governor Northam. “Innovative, dynamic businesses like Fresh Impact Farms are demonstrating how exciting new opportunities can grow out of pandemic-related challenges. I congratulate the company on their success and am thrilled to award the first-ever AFID grant to Arlington County to support this expansion.”
This expansion by Fresh Impact Farms will include a second grow room, larger production facility, and an educational hub where, post-pandemic, customers will be able to see how their food is harvested. Over the next three years, the company expects to grow an additional 10,500 pounds of Virginia-grown leafy greens, herbs, and edible flowers for restaurant and CSA customers.
“Agriculture is Virginia’s largest private sector industry and the Commonwealth continues to be on the forefront of emerging agriculture technologies,” said Secretary of Agriculture and Forestry Bettina Ring. “I am inspired by Fresh Impact Farms’ commitment to not only bringing fresh, local produce to Virginians, but also for its commitment to educate our community about how local food is grown.”
“2020 was undoubtedly one of the hardest years in recent memory for many people and businesses, but I’m heartened by the strength and flexibility the entire Fresh Impact Farms team has shown in our deep pivot to consumers and a CSA model to help us get to the point where we are ready to expand our business,” said Fresh Impact Farms Founder Ryan Pierce. “The support and generosity from the Commonwealth and Arlington County will be valuable as we expand our production and move towards a hybrid model of serving both the needs of restaurants and consumers. As the owner of a local food business, nothing gets me more excited than seeing the community come together in support of local food. The future is bright for urban agriculture and this grant will help us make an even greater impact in our community.”
The Commonwealth is partnering with Arlington County and the Arlington County Industrial Development Authority (IDA) on this project through the Governor’s Agriculture and Forestry Industries Development (AFID) Fund, which is administered by the Virginia Department of Agriculture and Consumer Services (VDACS). Governor Northam approved a $15,000 grant from the AFID Fund to secure the project for Virginia, which Arlington County will match with local funds.
“The Arlington County IDA’s match of the Governor’s AFID grant to Fresh Impact Farms represents an important investment in urban agriculture, sustainability, and technology,” said Arlington County IDA Chair Edwin Fountain. “This project will advance the County’s innovative and forward-thinking approach to developing new sectors of economic activity in Arlington.” […]
“Congratulations to Fresh Impact Farms,” said Senator Janet Howell. “This expansion not only supports our local economy, but also has a significant impact promoting healthy families and vibrant communities as a whole.”
“I am delighted Governor Northam has approved a grant from the AFID Fund to deliver this project for the Commonwealth and Arlington County,” said Delegate Richard Sullivan. “Fresh Impact Farms has been a pivotal resource for providing fresh food to the community. This expansion shows a commitment not only to homegrown produce, but to a healthier community and local economy in Arlington.”
Farmshelf Takes Growers From Seed to Plate
Kitchen gardens are going high-tech as the development of smart, efficient hydroponic grow systems helps both novice and experienced growers from seed to plate
Farmshelf is A Smart, Automated Farm For Hotels,
Restaurants And Corporate Cafes
BY CORRIS LITTLE ON JANUARY 15, 2020
BROOKLYN, NY—Kitchen gardens are going high-tech as the development of smart, efficient hydroponic grow systems helps both novice and experienced growers from seed to plate. One such company is Farmshelf, based here, which builds smart indoor farms that enable people to grow leafy greens, herbs and flowering crops where they live, work and eat.
“Our bookcase-sized smart, indoor farms are small enough to fit into a restaurant and powerful enough to provide pounds of fresh produce every week. Farmshelf brings the outdoors inside and grows food two to three times faster than conventional farming,” said J.P. Kyrillos, co-founder, Farmshelf.
Farmshelf’s bookcase-style growing system was invented by Andrew Shearer, Farmshelf co-founder, and CEO. He found inspiration through his passion for food, technology, engineering, and community.
“He married his years of volunteering experience to fund education in agriculture in Nicaragua’s food-insecure communities, and professional tech experience in Silicon Valley to build a tool that allows people to grow healthful, flavorful food anywhere, any time and know its source,” said Kyrillos.
As a result, the hospitality industry has taken notice. At HX: The Hotel Experience Powered by AAHOA, Farmshelf was the winner of the Best of Show award. Farmshelf has also captured the attention of hotel chefs and high-profile New York restaurateurs like Marcus Samuelsson of Red Rooster and Jose Andres of Mercado Little Spain, who have entered into partnerships with the company.
“They find as much value in the five to six pounds of leafy greens and herbs the units produce weekly as they do the organic marketing value,” Kyrillos said. “Our partners in the hospitality space share with us that the units add beauty to whatever space they are in. We designed Farmshelf to be eye-catching, and we often see hotel guests and diners in the restaurants that house Farmshelf taking time to really look at the unit, discover what it is and admire what it provides.”
Kyrillos also noted that the chefs at the hotels where Farmshelf is stationed regularly praise the accessibility and freshness of the produce.
“We aim to shorten the distance between farm to plate—a journey that’s often hundreds or thousands of miles—and having fresh herbs and greens right at your fingertips not only allows for speedy and easy access, it provides superior freshness,” he said.
Sustainability is a key facet of the Farmshelf business.
“Farmshelf helps minimize food waste because you know exactly how much produce you are able to harvest at any time, and no food expires in transit,” he said. “Nearly 40% or more of the food we grow in the U.S. ends up in a landfill. That equates to millions of dollars and pounds of food that could have otherwise been used. It’s a solvable problem, and we’re working to lay the building blocks to address it in a scalable way. In addition, Farmshelf uses 90% less water in comparison to traditional soil growing. By enabling you to harvest just what’s needed, Farmshelf also eliminates packaging, environmental impacts from transportation, and food waste.”
Kyrillos noted that the Farmshelf leadership team has seen firsthand the devastation that a lack of access to food causes.
“At Farmshelf, we are passionate about ensuring people have access to fresh, healthful food, anywhere and anytime,” he said. “And, while we are still a young company, we are working to scale our technology so that more people can have access to food.”
Andrew Shearer Farmshelf food waste garden Gardening HX: The Hotel Experience Hydroponic J.P. Kyrillos Sustainability
Automated Containers Make Organic Urban Farming Feasible
Commercial containers such as those from Seedo would expand the potential for urban farming to anywhere, anytime. Plants can be cultivated 24/7, regardless of location
The future of agriculture can be found in commercial containers, in which plants can be grown hydroponically.
Hydroponic farming has many benefits, including saving the resources involved in soil cultivation and avoiding the uncertainty of weather conditions, according to Seedo, an innovator in the field of commercial growth containers.
Approximately 40 percent of the costs of produce in large city supermarkets are used to cover logistics and shipping. Commercial containers such as those from Seedo would expand the potential for urban farming to anywhere, anytime. Plants can be cultivated 24/7, regardless of location.
For example, the automated urban farm is ideally suited to the growing market for medical cannabis and medical cannabis products. Seedo is the technology behind the world's first automated medical cannabis farm, which will yield significantly more plants than traditional controlled greenhouses.
Another opportunity for the Seedo technology is to improve the agriculture of at-risk countries, where global warming and other concerns threaten consistent farming and food production.
In some areas, farmers can use Seedo equipment and technology for growing not only medicinal herbs, but also greens such as lettuce, kale, and wheatgrass; herbs such as parsley, dill, and basil; and vegetables such as cherry tomatoes and bell peppers, and even strawberries. In the home, individuals can set up a small unit that grows plants easily and effectively without intervention.
Seedo, a pioneer in agriculture and technology with 20 years of experience, is now delivering indoor growth systems to homes and businesses across the country. Currently, Seedo has sold more than 3,000 home units through pre-orders.
The Seedo products use artificial intelligence software to control and monitor plant development from the moment the seed is planted. The software tracks each plant's development, and responds by taking action to optimize growth. The hermetically sealed systems are designed to yield consistent results regardless of the local climate.
Growers need only to plant seeds or seedlings and monitor the growth process via the Seedo app.
Other features of the Seedo system include a unique lighting system that self-adjusts based on an individual plant's stage of growth, and a smell-proof cover with built-in CO2 cartridges to prevent smell leaks.
Equally important to note is that all produce cultivated with Seedo's technology (both home and commercial) is pesticide-free, of high quality, and has a significantly extended shelf life.
Visit seedo.com for more information about investing in the growth industry of indoor gardening, and to learn more about the Seedo technology and products.
Seedo is a publicly traded company with the ticker symbol OTCQB:SEDO.
A Suffolk Greenhouse The Size of 11 Football Pitches
A company’s multi-million pound investment is about to turn Suffolk into a major producer of vine tomatoes.
Cliff Matthews, a director of Sterling Suffolk Ltd., inside the giant glasshouse being built on land between Great Blakenham and Bramford. The new greenhouse will be used to grow vine tomatoes by hydroponic
A company’s multi-million pound investment is about to turn Suffolk into a major producer of vine tomatoes.
Cliff Matthews, a director of Sterling Suffolk Ltd., inside the giant glasshouse being built on land between Great Blakenham and Bramford. The new greenhouse will be used to grow vine tomatoes by hydroponics
In the first stage of a £30m project, at Great Blakenham near Ipswich, Sterling Suffolk Ltd has built a massive Dutch-style glasshouse with the dimensions of an aircraft hangar - or 11 football pitches.
It is on track for the first tomatoes to be planted in December, and for the first cropping to begin from mid February 2019.
The plan is to produce tomato vines by hydroponics - without soil, but perhaps coconut matting (coir), and fed water and nutrients that are carefully controlled.
This giant greenhouse is similar to those seen in parts of Holland and France, and used to produce a range of salad vegetables, fruit and flowers.
Cliff Matthews, a director of the developers, Sterling Suffolk Ltd, said: “It has been great to start this, seven years ago, and to be here to see it coming to fruition,
“There are some bigger ones in the country of course. This phase one is the size of 11 football pitches.
“It is the most environmentally efficient glasshouse in the UK. The first of its kind here.
“There are a number in France and Holland.
“Real glass is more efficient for this.
“This is agriculture on a industrial scale. There is an art and science to growing tomatoes and we have a very good expert involved, Richard Lewis, one of the best in the UK.”
Vine tomatoes, with clumps of tomatoes still attached to the vine, would be harvested and supplied to supermarkets and the restaurant trade.
“We aim to produce 50,000 vines per week. It is more about the taste than the quantity.” he added. “These will be top of the range quality.”
The 5.6 hectare building is phase one of a three-phase project, costing around £30m in all, over the next three years.
When complete there will be 17 hectares of production glasshouses, plus office, packaging and production on site.
The first giant 8,3 metre tall house has been constructed since March, despite the bad weather.
Now it will be fitted out with blinds and hydroponics equipment ready for the first planting in December.
It would be very environmentlly friendly, he said, with air ciculation systems and the water for the hydroponics collected from the roof and stored in a reservoir.
The tomatoes would grow in natural light, with a season from March through to October, and one hectare of plants would grow under lights at other times.
The site would employ between 40 and 50 people, he said. “And we will employ more when we get growing and expanding.
“We have spent about half a million pounds in the local environment so far, with more to follow.
“Over the years it is gooing to benefit all of the community,”
The project attracted some local opposition during the planning process.
Mr Matthews added: “Personally I don’t think it looks too bad in the countryside. There are trees and we are goiong to plant more for screening.”
This project will not be the largest in the region, at Wissington in Norfolk British Sugar has an 18 hectatre glasshouse - and products there include medicinal cannabis.
Who Cares? Why We Sued Ben & Jerry's
The company’s “Caring Dairy” program sounds like a dream-come-true for Vermont’s dairy farmers and dairy cows. But it’s more like a nightmare
2018
Organic Consumers Association
by Katherine Paul
Splashed across the Ben & Jerry’s website are cartoon-like pictures of happy cows romping in green pastures.
There’s a reason those cows are depicted by drawings, not actual photos—most of the real, live cows whose milk and cream are used in Ben & Jerry’s ice cream products are crammed into dark, filthy barns for most of their short lives.
Ben & Jerry’s goes to great lengths to create the perception that the Unilever-owned company “cares” deeply about the farmers who supply milk and cream for the brand, the cows raised on Vermont dairy farms, and the state of Vermont’s environment.
The company’s “Caring Dairy” program sounds like a dream-come-true for Vermont’s dairy farmers and dairy cows.
But it’s more like a nightmare, for the cows, Vermont’s environment and consumers who care about animal welfare.
As we state in the lawsuit we filed this week against Unilever, Ben & Jerry’s markets its products:
. . . as being made from milk produced by “happy cows” raised in “Caring Dairies,” leading consumers to believe that the products are produced using animal-raising practices that are more humane than those used on regular factory-style, mass production dairy operations.
In contrast to Unilever’s representations, the products include milk that comes from cows raised in regular factory-style, mass-production dairy operations, also known as “Concentrated Animal Feeding Operations” or “Large Farm Operations”—not in the special “Caring Dairies” emphasized in Unilever’s marketing.
As we reported last year, our testing revealed that many samples of popular Ben & Jerry’s ice cream flavors, in the U.S. and in Europe, contain traces of Monsanto’s Roundup weedkiller. We see that as a sign that the brand falls far short of its claims of social and environmental responsibility.
Unilever spends nearly $9 billion a year on advertising, second only to Proctor & Gamble. We think the company should spend less on misleading product claims, and invest more in helping Vermont dairy farmers transition to organic and regenerative practices that actually support those claims.
‘Caring Dairies’ program nothing more than a scam
Like any successful brand, Ben & Jerry’s knows that animal welfare tops the list of issues people care about. Hence, the creation of a program—“Caring Dairy”—intended to make consumers believe that Ben & Jerry’s “cares,” too.
But it’s all smoke and mirrors. Here’s why.
On its “Caring Dairy Standards” website page, the company lists a set of standards it says are required for all dairy farms that supply Ben & Jerry’s.
Thanks to the work of Regeneration Vermont, we know that Ben & Jerry’s sources all of its milk and cream through a cooperative based in St. Albans City, Vermont. Fewer than 25 percent of the approximately 360 farms that deliver milk and cream to the St. Albans co-op meet the “Caring Dairy” standards. But when farmers deliver their milk to the co-op, it’s all mixed together—the co-op doesn’t separate the milk delivered by a “Caring Dairy” program participant from the milk of other dairy farms. So even if some of the milk comes from a farm that actually meets those standards, Ben & Jerry’s can’t truthfully claim that all of their milk and cream come from dairies that meet the company’s “Caring Dairy” standards.
Advertising, even the false kind, pays
So you, the consumer, when you visit the Ben & Jerry’s website and see pretty pictures and a long list of standards the company says all of its farmers meet, are being duped.
All that talk of “Caring Dairies” is there to make consumers feel good about buying Ben & Jerry’s ice cream.
It’s pretty much all a lie. Especially when you consider that over the years, some members of the St. Albans co-op have been fined for violations of environmental laws, including one that illegally expanded its operation near the Missisquoi River Basin, which drains into the already heavily polluted Missisquoi Bay.
In fact, the dairy industry is Vermont’s biggest polluter, according to Regeneration Vermont, in part because the state’s conventional dairy farms feed GMO corn, heavily sprayed with pesticides such as atrazine, metolachlor, and glyphosate, to dairy cows.
So when Ben & Jerry’s says it’s “on a mission to make great ice cream that respects the farmer and their farmworks, the planet and the cow,” don’t believe it.
Ben & Jerry’s is on a mission to spin a false and misleading story about a company that has a lousy track record when it comes to sourcing ingredients from socially and environmentally responsible producers.
Consumers who care about their health, the environment and animal welfare would do better to buy organic brands from companies that don't source glyphosate-sprayed ingredients and that do source from dairies that meet organic standards.
South Korea: Smart Farms Cultivate 'Vegetables of The Future'
South Korea: Smart Farms Cultivate 'Vegetables of The Future'
'We Are Future Vegetables'
May 30, 2018
Plants grow at Miraewon's Fresh Farm III, a factory-style smart farm that grows leafy plants and herbs in an automated environment. / Courtesy of Miraewon
Two South Korean smart farms are leading the way in using a technically advanced agricultural system with a huge future around the world.
By Ko Dong-hwan
They may be farms, but there are no signs of soil or smelly manure. Instead, the sound of water flowing, a breeze, a pleasant temperature and bright artificial lights fill the indoor space of "smart farms" in South Korea. In this environment, countless numbers of different leafy plants thrive in multi-layered beds.
Humans rarely frequent the enclosure, which looks similar to a laboratory. Apart from a cleaner with a vacuum cleaner that sucks water from empty plant beds, not a soul bothers the plants. A closer look at the crops reveals antenna-looking fixtures as small as a human finger installed here and there.
Unlike the quiet space, the real game happens outside the enclosure ― "played" by computers. Reading data transmitted from the antennas, the computers care for the plants, varying temperature, light intensity and water flow amount, and remote-control the enclosures' environment to maintain ideal conditions. The operation goes on round-the-clock, regardless of outside factors like seasonal effects, weather conditions, human error or animal intrusions.
Plants grown in artificial environments, controlled by state-of-the-art artificial technologies, may seem odd to some people. Yet, considering how efficiently smart-farming uses natural resources and energy to produce healthy crops continuously, the concept may well become a reality in a major way.
Plants grow in n.thing's "Planty Square," which can be remotely controlled by a smartphone app to supply water for seeds in each pot. / Courtesy of n.thing
Module pots
The method is being pursued by n.thing, a smart-farm developer based in Jamwon-dong in Seocho-gu, Seoul. Leo Kim, CEO, came up with a plastic pot called "Pickcell." The container, measuring just over five centimeters in width, length and depth and weighing 16 grams, works as a module. Attachable to one another, each hydroponic pot grows a single seed and multiple pots produce plants accordingly.
Pickcells can be linked to make a "Planty Square" or in thousands to make a "Planty Cube," a vertical farm in a shipping container-like space. All the components are Internet of Things inventions, with users controlling them with a dedicated smartphone app that transmits data through the company's firmware.
Leo Kim, right, explains his smart-farm products and software at a SXSW booth in Austin, Texas, in 2016. / Courtesy of n.thing
"Our company is oriented for exports," says Lee, who started the company in 2014. "Because of the module-based design, the farm is easy to install. The Cube's container-concept is convenient in that it allows a faster counter-response to contamination compared to a large-scale factory. We don't have to shut down the entire facility but just isolate containers separately. The module basis also enables easy replacement of hardware parts."
The company started operating the Cubes in practice early this year, installing three in an unused space in Mia-dong in Gangbuk-gu, Seoul. Afterward, Lee searched for spaces to install 100 additional Cubes in three locations that he keeps secret. He said they would be operating within this year.
Lee sold Planty Square to about 30 countries on crowd-funding site Kickstarter. In January, the company exported two Planty Cubes to Poshtel hostel in Copenhagen, Denmark, where smart-farming using artificial lights and conveyor belts began in 1957.
Lee believes that future farming is all about data. Crops' appearance, taste and growth period can all vary depending on different environmental elements that can be adjusted according to data. For example, a cucumber seed, when grown in an African country, can grow several times bigger than in Korea because of the different climate and environment.
Manipulation of the data allows him to customize plants for people who cannot eat fresh plants because of health issues. For people with kidney problems and diabetes, he developed plants without potassium and nitrate, respectively. He has acquired a patent for this.
"We control the data," Lee says, describing the smart-farm maintenance. "Inside the controlled smart-farms, we can grow crops the way we want. People who buy our module farms need our data to grow plants the way they want."
Just as traditional computer servers evolved from a physical box to an online cloud server, Lee describes his smart farm models as "cloud farms" that he operates for customers, charging them an operating fee unrelated to output.
"Because traditional farming is affected by seasons and crops' prices vary accordingly, the supply-and-demand chain is unstable," Lee says. "Smart farms enable stable production and thus stable pricing. It brings down the cost of 100 grams of lettuce as low as a few hundred won retail. It's just like the transition from CDs to online streaming for music listeners."
Lee believes that just as computer engineers need their own working tools to develop programs, farmers need dedicated farming tools to focus on growing crops. He points out that farmers have so far been reluctantly burdened with things other than their main job, from searching for sales routes to managing venues and selling the products.
"The smart farms are a platform for farmers to focus solely on farming," he says.
n.thing's "Planty Cube" is an unmanned smart farm in a space the size of a shipping container. / Courtesy of n.thing.
Veggie factory
Amid wide open farm fields in Pyeongtaek, Gyeonggi Province is a cluster of several manufacturing firms. Next to a dusty road, smart-farm operator Miraewon runs six factories 24/7 with about 200 employees, many of them migrant workers.
At one factory called Fresh Farm III, about 20 different species of plants grow in automated indoor environments. Growing on 98 floors of hydroponic beds spanning more than 1,400 square meters, leafy and herb plants densely pack the enclosure beneath LED lights.
"Every day, we sow and harvest," says Jeong Myeong-hwan, the factory's chief operator. "The tight daily cycle allows us to harvest enough to meet the required demand. Making money in this industry requires a strong, steady pipeline, as well as quality products."
The company produces an average 100 kilograms of leafy vegetables and 50 kilograms of herbs each day. This output would not have been possible without the smart-farming technology that reduces the time taken from sowing to harvesting to 33-37 days. Minimizing the growth cycle and still providing good qualities ― vivid colors and plants weighing at least 150 grams per crop ― is not easy, according to Jeong, who left global corporation Samsung to join the burgeoning smart farm industry years ago.
Miraewon has contracts with South Korea's fried chicken restaurant chain Kyochon and warehouse retailer Costco Korea to provide salad packs containing basil and other greens.
Established in 2004, the company now spearheads domestic smart-farming. Miraewon launched Fresh Farm III in 2014 and built other factories dedicated to making salads, growing herbs, paprika and special vegetables and experimenting with about 60 varieties.
An automated small-scale vertical farm is installed at Hyundai Department Store's Cheonho branch in Gangdong-gu, Seoul, providing vegetables for a restaurant there.
Butterheads grow at Miraewon's Fresh Farm III. / Courtesy of Miraewon
Miraewon's efficient pioneering methods were recognized by the Ministry of Agriculture, Food and Rural Affairs, which loaned the company 1.5 billion won ($1.4 million) to develop a demonstration project for domestic farmers. In 2017, Dutch vegetable farm Enza Zaden, which assesses and grades vegetable factories across the world, rated the company third-highest on a scale of 1-10.
Miraewon's demonstration project, which will be active within this year, will introduce a nutrient film technique (NFT) to replace the old deep-flow technique (DFT). Compared to DFT, which uses potentially hazardous foam in building plant beds and requires five laborers per 300 square meters, NFT uses hazard-free plastic materials and requires as little as two maintenance workers.
"With the demonstration project, we want to surpass Japan," Jeong says, referring to the nation that has long outpaced South Korea in smart farming. "South Koreans, once well organized with ideas and supporting tools, can make miracles happen. I aim to realize another miracle this time."
Miraewon's reputation precedes other domestic smart-farms and motivates it to fulfill its corporate social responsibility. It met members of a disability group and discussed ways to hire physically challenged people as laborers. In this company, age does not really matter. One of the most recent retirees was in his 80s.
The company this year started to teach public servants from other countries about smart-farming. In March, 20 government officials from Laos visited the company. Before this, representatives from 29 countries came to the company to learn South Korea's state-of-the-art agricultural methods.
Prospects for smart farming
By the end of 2020, Seoul plans to build the nation's first smart farm in dedicated buildings. Two structures will be in an outdated section of Mok-dong district in Yangcheong-gu, which will be re-urbanized. The city will contribute about 7.5 billion won to the project.
"We will not erect the farms from scratch but instead renovate existing buildings," said Park Se-hwang from Seoul Metropolitan Government's Urban Agriculture Division, who leads the smart farming project. "We found no laws or regulations that might cause any legal conflict with the project. So it's good to go. It's just a matter of time to secure the site."
Seoul Mayor Park Won-soon is known to be interested in the smart-farm. The city, along with Mok-dong, tried to build another vertical farm near Garak Market in Songpa-gu but the deal fell through.
Because smart-farming requires much more investment ― 10 million won per 3.3 square meters ― compared to vinyl houses or glass houses, and take a painstakingly long time ― up to 10 years ― to offset the cost, starting a smart-farm takes courage. Namyangju in Gyeonggi Province planned the nation's first smart farm in 2009 but decided the investment cost was too high.
"A 30-storey vertical farm can feed 50,000 people," says a Seoul Metropolitan Government official citing a Columbia University's study. "Technological development supporting urban farming and future food businesses are our new perspectives in approaching the (Mok-dong) farm project. No matter how long the project will take, we will get it done."