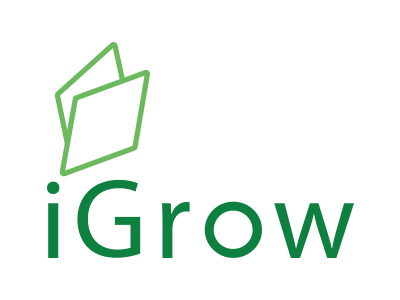
Welcome to iGrow News, Your Source for the World of Indoor Vertical Farming
Vertical Farming Comes to Edinburgh
Scotland’s Rural College is to be the first higher education institute in Scotland to open its own vertical farm for research and education.
By Gordon Davidson
August 10, 2021
Scotland’s Rural College is to be the first higher education institute in Scotland to open its own vertical farm for research and education.
The half million-pound facility is to be built at the SRUC's King’s Buildings campus in Edinburgh next year, with the backing of a £200,000 grant from the Scottish Government. It will enable key research into plant and crop science, growing nutrient-dense fruit and vegetables with specific human health qualities, while analysing crop yield and growth rates – with all inputs recorded in the closed environment – to compare their carbon footprint to other production systems.
SRUC's vertical farm will operate on renewable energy sources from the national grid, supported by battery technology to manage peaks in energy demand.
With only a handful of commercial vertical farms in Scotland so far, it is envisaged that the facility will be important for demonstration and knowledge exchange with farmers, growers and small businesses. It will also be used by SRUC students as part of their educational activities, looking to a future when such systems will be far more common places of work.
Cabinet Secretary for Rural Affairs and Islands, Mairi Gougeon, said: “As we look to produce more fruits and vegetables locally, vertical farming could provide us with a way to make better use of our land. It’s an exciting and innovative field that could bring us real benefits and it is important that we have the skills in Scotland to take advantage of this technology.
“By supporting the industry at an early stage, we can assess these benefits and help to focus our long-term strategy. We will also be reaching out to the wider industry to explore in further detail the opportunities low-carbon vertical farming offers. We will work together to establish the future of vertical farming in Scotland.”
Principal and chief executive of SRUC, Professor Wayne Powell, said: “One of the most critical challenges we face is how to feed a growing global population. We have been teaching farmers for generations but, as the population increases, it is important that we look at growing different, more nutritious crops to support healthy diets and local access to food.
“Not only will this vertical farming unit be a valuable asset to our students, but it will also provide us with important data to help optimise and promote innovation into this expanding industry.”
Lead Photo: A new vertical farm at SRUC will be used for education and research.
"Using Variable Spectrum Luminaries Allows us to Grow a Wide Range of Plants"
Bringing food closer to consumers is no longer an option but rather a necessity, given the strain traditional agriculture and transportation place on the environment.
August 11, 2021
Bringing food closer to consumers is no longer an option but rather a necessity, given the strain traditional agriculture and transportation place on the environment. Czech grow tech company GreeenTech teamed up with Hungary’s Tungsram to provide vertical farming solutions that pave the way for sustainable crop production.
Prague-based GreeenTech was born out of this realization. The company specializes in the research and development of hydroponic technologies to be used in container farms and vertical farms set up in buildings. Established in 2000, the business aims to enable people to grow agricultural crops anytime and anywhere in the world.
They are involved in developing innovative solutions for the local production of leafy vegetables, herbs, and small fruits through their own hydroponic cultivation technology complete with an IOT control system created in cooperation with Siemens. The uniqueness of the solution provided by GreeenTech lies in the development of tailor-made hydroponic farming technology.
Finding the perfect lighting solution
"Hydroponic systems are soil-less, water-based farming processes. The technology is based on growing plants in a controlled environment where crops are fed nutrient-rich water. Crop cultivation takes place in an enclosed growing space, where sensors control conditions such as humidity, temperature, or light cycle. The result is quality crops that have not been subjected to treatment with pesticides and herbicides and the farm uses about 90% less water than conventional agriculture," the GreeenTech team explains.
Given that crops are not exposed to natural light, selecting the right lighting solution in these farms is of utmost importance. GreeenTech’s quest for the best lighting solution provider-led them to Tungsram, whose variable spectrum LED luminaries proved to be the perfect match as the light sources have been designed and created only for the purposes of a growing container.
“We were searching for a lighting solution and we realized that Tungsram’s luminaries and the automation solutions provided by them are ideal for our needs because they are well suited for research purpose. Using variable spectrum luminaries allows us to grow a wide range of plants. In addition, customers have a high degree of flexibility in deciding what kind of plants they want to grow or in switching from one crop to the other,” said Karolína Pumprová, CGO at GreeenTech.
LED lights
"Our four-channel LED lights offer the highest performance in their category and are extremely easy to install," the Tungsram team says. "The luminaries are controlled remotely and allow users to adjust the color spectrum and light intensity independently for each growing rack, which is a game-changer for large-scale urban farms."
In addition to the lights, Tungsram also provided a tailor-made lighting design with the help of the company’s engineers and designers. "Variable spectrum luminaries are a powerful tool for growers in terms of adopting a “dynamic light recipe approach,” which is a rather unique offering in the market."
Compatible with software
“Another factor that weighed heavily in favor of Tunsgram was the fact that the lighting solution developed together with them was compatible with the software and system we already had in place,” said Milan Souček, CTO at GreeenTech.
GreeenTech will use the Tungsram luminaries at the expo in Dubai, which will run from September through March. The cultivation container will be set up in a restaurant and the plants will be used in the restaurant. As part of a cooperation with the Technical University in Prague, Tungsram lights will be installed at a small hydroponic farm set up by GreeenTech where students will be conducting research and testing.
For more information:
Tungsram
Keith Thomas, Commercial Leader
keith.thomas2@tungsram.com
agritech.tungsram.com
Vertical Farming: Turning Deserts Into Fresh Food Hubs
Deserts and arid lands are commonly perceived as worthless. Because of this image of the world’s drylands, agricultural investments and development initiatives pass these regions by. Moreover, with the new NASA food challenge, it seems like AgriTech enthusiasts would rather attempt to cultivate plants in space than in desert environments on their native planet.
August 10, 2021
Vertical farming technologies allow for collecting the humidity produced by plants. With recirculating and recycling techniques, hydroponic and aquaponic systems can reuse 98% of water, which makes vertical farms feasible in deserts.
Deserts and arid lands are commonly perceived as worthless. Because of this image of the world’s drylands, agricultural investments and development initiatives pass these regions by. Moreover, with the new NASA food challenge, it seems like AgriTech enthusiasts would rather attempt to cultivate plants in space than in desert environments on their native planet.
Taking up 41% of our planet’s landmass, arid zones have always been seen as marginal for agriculture. But thanks to technological advancements, they can produce fresh food and compete on the global market. How? By adopting next-generation technologies like vertical farming.
How vertical farming enables agriculture in deserts
The most fascinating thing about vertical farming technology is that it brings food production to regions with no arable land. Crops grow indoors, stacked in layers under LED lights. Most vertical farms rely on hydroponic, aeroponic, or aquaponic methods, as they don’t require soil. Anything “hydro” and “aqua” may seem inappropriate for arid lands, but these methods are extremely water efficient.
And here’s what thrills me a lot: While most barren lands suffer from aridity, agriculturally developed regions waste tons of water. Even though modern smart irrigation systems do help reduce water use on traditional farms, water is still lost because of wind and evaporation. On the contrary, vertical farming technologies allow for collecting the humidity produced by plants. With recirculating and recycling techniques, hydroponic and aquaponic systems can reuse 98% of water, which makes vertical farms feasible in deserts.
Vertical farms ensure plants have exactly what they need
The ultimate goal of vertical farming technology is to get the highest possible yield by precisely meeting plants’ needs. One can believe me or not, but it works like magic.
After the vertical farming facility is built and all equipment is installed, a complex network of IoT and analog sensors comes to life. They measure gases and nutrients, humidity, light, and temperature inside and outside the farm. Additionally, the monitoring system takes photos and videos of plant growth. Then, all this data is transferred to secure cloud storage via edge gateways.
This provides a huge volume of raw data that can be integrated into AI-based software and analytics platforms. Built-in machine learning algorithms can match plant images against a huge database and learn to recognize plant types as well as deviations in their growth. The analytical algorithms can process plants’ growth data and correlate it with microclimate measurements to find the perfect combination of environmental factors for particular crops.
The final flourish is data visualization. User-friendly dashboards present calculations, analytics, and prediction results in meaningful histograms and neat reports. Having vertical farming software installed on any device, owners can get real-time insights into farm health and make data-driven decisions.
Basically, a vertical farm is a premium luxury ultra-all-inclusive spa resort for plants.
The vertical farming market has huge potential
An ever-changing climate along with the depletion of soil nutrients and groundwater have accelerated the adoption of vertical farming technology. The coronavirus pandemic has also contributed. The risk of supply chain disruptions has underscored the need to locate vertical farms near distribution routes and intended markets.
With many drivers igniting the industry, the global vertical farming market will reach USD 11.71 billion by 2027, growing at a CAGR of 20.1% according to Emergen Research. But we’re only at the advent of vertical farming in terms of technology. Innovative advancements are expected to reduce costs and improve the efficiency of plant growth in vertical farms, giving us high hopes for the future.
Desert reality: vertical farming or nothing
Some skeptics may consider vertical farming advantages controversial. But with temperatures reaching +40 degrees Celsius (over 100 degrees Fahrenheit), just a few days of rain a year, and barren sands, deserts don’t seem like suitable places for any other agricultural practices. In addition, climate change promises to make these lands even drier, hotter, and less valuable. Being land-agnostic and capable of conserving water, vertical farming is a reasonable option for arid lands. This ingenious method of producing food in deserts might be a springboard to economic development of arid regions.
Boosts the local economy
Local economies have attracted a lot of attention recently. And guess what I consider to be a remarkable contribution to developing local economies? Right, vertical farms near desert cities. The more often and the faster a dollar circulates in a region, the more income it creates. Studies also show that the most prosperous communities gain and sustain their wealth because they have the highest percentage of jobs in local businesses. Such communities still engage in global trade, but they import only things they can’t supply themselves.
Reinforces food security
The coronavirus pandemic has spotlighted local food production, making it more of a necessity than a luxury. Countries that heavily rely on food imports are now striving to achieve food security and resilience more than ever. And the risk of food supply chain disruptions is less imminent with several vertical farms near megalopolises. Because indoor environments are independent of outside weather conditions, vertical farms ensure reliable harvests to meet delivery schedules and supply contracts.
Decreases prices for fresh food
Besides ending dependence on imported food, vertical farming in close proximity to cities lowers the cost of products. Since food prices are linked to oil prices, delivery distance is an influential factor in food costs. The shorter the distance food travels, the less it costs. Additionally, local produce is fresher, as it isn’t stored in fridges for long during delivery. On top of that, vertically farmed crops are healthier than field-grown crops and are naturally flavorful, as strict biosecurity procedures in indoor farms eliminate plant diseases and the need for pesticides.
Creates new jobs
Among other vertical farming advantages are the job opportunities the technology provides. Yes, an indoor farm doesn’t require much manual labor due to automated growing systems and robotics. Nevertheless, it creates a lot of new jobs in farm construction and management, plant cultivation, technology development and support, distribution control, and personnel management.
Uses energy sustainably
Although a 30-story vertical farm needs 26 million kWh of electricity, it can generate 56 million kWh through biogas digesters and solar panels. The excess energy can be transferred back to the grid and bring additional income.
Given the technical opportunities, market potential, and benefits for communities, I struggle to find a rational explanation as to why large desert areas still lie unused. Fortunately, some early adopters have already recognized the potential of arid lands.
The challengers who have already succeeded
However challenging the idea of growing crops in hostile climates may seem, some daring companies are already leveraging high-tech techniques of vertical agriculture and running successful businesses, boosting food production in their countries.
The Al-Badia market garden farm is among these pioneers. The daily harvest of the Middle East’s first commercial vertical farm is two hundred boxes of greens, including radishes, kale, mustard, basil, and arugula. The multi-story setup is on an 800-square-meter plot of land in one of Dubai’s main industrial areas. Al-Badia serves nearly 70 local caterers and restaurants, providing fresh and pesticide-free products that wouldn’t be available otherwise.
The driest state in the USA, Nevada, has become home to a 20,000-square-meter hydroponic vertical farm built by Oasis Biotech. Besides catering to the needs of the Las Vegas restaurant industry, the company has created its first consumer-facing brand, which is currently sold through a local distributor. While most US produce travels between 1,500 and 2,500 miles before reaching the consumer, Oasis Biotech ensures its goods are delivered within an average of four miles and go from harvest to plate within 36 hours.
In Australia — a country that is 53% deserts and drylands by landmass —vertical farming technology is also being adopted. Stacked Farm’s two locations (200 and 4000 square meters) focus on salad greens, leafy vegetables, and livestock feed. But what’s more exciting about these farms is that they’re fully automated, from planting the seeds to harvesting and packaging the produce. Nevertheless, Stacked Farm doesn’t intend to take work away from farmers but rather to support farming communities that are suffering through drought or during off seasons.
Deserts are no longer deadlands
Vertical farming technology is certainly a game changer for regions with severely hot climates. Once a dryland gets a vertical farm, it stops being a deadland and becomes an advanced hub of fresh food. Vertical farming pioneers will be remembered as the kick-starters of thriving desert economies. The first to build a vertical farm in a desert will most likely be the first to start getting profits from desert farming and eventually become a frontrunner in the industry.
Source: Agritech Tomorrow
Things Are Looking Up For New Vertical Farming Students
Building work on the £500,000 facility is expected to begin next year with the £200,000 grant from the Scottish Government helping key research to be carried out in this growing area of plant and crop science – and being the first such facility to be directly connected with an educational establishment, it will also give students hands-on experience of this new field of technology.
By The Newsroom
August 10, 2021
Building work on the £500,000 facility is expected to begin next year with the £200,000 grant from the Scottish Government helping key research to be carried out in this growing area of plant and crop science – and being the first such facility to be directly connected with an educational establishment, it will also give students hands-on experience of this new field of technology.
The new building and associated technologies will focus on growing nutrient-dense fruit and vegetables with a specific focus on human health qualities. The site will also analyse crop yield and growth rates along with all resource inputs - allowing the true overall carbon footprint of the latest in growing techniques to be compared with more traditional production systems.
Vertical farming systems focus on controlling all inputs into the growing system, with light levels and frequencies carefully controlled along with temperature and CO2 levels on top of water provision and all other nutrients and substrates.
The SRUC said the facility would operate on renewable energy sources from the national grid, with new battery technology being used to help manage peaks in energy demand.
“With only a handful of commercial vertical farms in Scotland, the facility will be important for demonstration and knowledge exchange with farmers, growers and small businesses, giving vital support and promoting innovation,” said Professor Wayne Powell, Principal and Chief Executive of SRUC.
“One of the most critical challenges we face is how to feed a growing global population,” he continued.
“We have been teaching farmers for generations but, as the population increases, it is important that we look at growing different, more nutritious crops to support healthy diets and local access to food.”
But he said that the vertical farming unit would also be a valuable asset to students studying at the site, while also providing important data which would help optimise and promote innovation into what was becoming a fast-expanding area of the industry.
The Scottish Government’s cabinet secretary for Rural Affairs and Islands, Mairi Gougeon said:
“As we look to produce more fruits and vegetables locally, vertical farming could provide us with a way to make better use of our land. It’s an exciting and innovative field that could bring us real benefits and it is important that we have the skills in Scotland to take advantage of this technology.
She said that by supporting the industry at an early stage, policy makers would be better able to assess the benefits and help to focus on long-term strategy.
“We will also be reaching out to the wider industry to explore in further detail the opportunities low-carbon vertical farming offers. We will work together to establish the future of vertical farming in Scotland.”
The project will be going out to tender in the coming weeks.
AeroFarms Is Trying To Cultivate The Future of Vertical Farming
2021 is turning out to be quite the year for Newark, New Jersey-based vertical farming pioneer AeroFarms.
By Jesse Klein
August 10, 2021
2021 is turning out to be quite the year for Newark, New Jersey-based vertical farming pioneer AeroFarms.
The biggest news is that the company is going public. In March, it announced a merger with a blank-check firm, Spring Valley Acquisition Corp., that will see the company traded publicly later this year under the ticker ARFM. Also in March, AeroFarms announced a research and development partnership with Hortifrut to push vertical farming technology into the lucrative $39.8 billion berry market, reducing its dependency on revenue from leafy greens. And in July, AeroFarms rebranded its Dream Greens produce line to AeroFarms to capitalize on its name recognition. At the same time, it expanded into five new leafy green products: Baby Bok Choy, The New Spinach, Micro Arugula, Micro Broccoli, Micro Kale and Micro Rainbow Mix. And in August, AeroFarms announced another partnership with Nokia Bell Labs, the New Jersey-based historic scientific research firm, to take its technology to the next level with increased networking, advanced autonomous systems, machine vision and machine learning technologies.
The company is obviously picking up steam. The public market offering and the capital gained during the process will be crucial for AeroFarms to reach the next level of its growth and to achieve several strategic expansions, including improving operational and energy efficiency, adding into new products (right now it’s focusing on berries), and maintaining its social impact.
"We told investors, we view this as a long-term industry," CEO David Rosenberg said. "It is going to be massive. We feel we have a strong leadership position in the industry from a technology standpoint. So how do we build upon that and really double down on the tech producing [capital expenditures], reducing [operating expenses] and improving quality as well as new varieties of plants on this platform."
AeroFarms was founded in 2004, and its products are sold in 200 grocery stores across the Northeast including Whole Foods. It operates one vertical farm in New Jersey, with more on the way. AeroFarms is breaking ground on a facility in Abu Dhabi, pitched as the world’s largest vertical farm, as well as one in Danville, Virginia. Along with the publicly announced farms in Abu Dhabi and Danville, AeroFarms plans to build 16 more farms with the capital it’s raising, using a slightly different strategy than the company’s previous build locations.
"It’s not where the mouths are, but where the produce distribution centers are," Rosenberg said. "So we can sell to a surrounding number of cities. We’ve gone from a lens of hyper local to a more looser definition of local."
AeroFarms uses aeroponics, a soilless way of growing produce that uses mist to cut down on water usage by 95 percent; it plants seeds in cloth made from recycled plastic bottles. Using LED lights, the vertical farms draw on specific wavelengths to maximize efficiency of the plants’ photosynthesis.
The vertical farming industry, already an important part of the food supply chain, is poised to explode. According to a 2020 report by the World Wildlife Fund, indoor farming is projected to have a combined annual growth rate of more than 24 percent between 2018 and 2024, hitting $3 billion in revenues worldwide in 2024. The challenges and opportunities faced by AeroFarms over the next few years will inform the vertical farming playbook for its followers.
Energy is the next big hurdle
The SPAC merger is expected to bring AeroFarms $317 million in cash, on top of the $80 million the company already has, to scale and expand into new geographies. According to Rosenberg, the company focused most of the last 15 years on innovating its technology, seeds and plants. He is confident its technology can support a massive jump in demand and commercialization.
Energy stands out as one of the bigger hurdles facing the [vertical farming] industry.
But the process of scaling up vertical farming isn’t without controversy. A World Wildlife study that compared the life cycle assessment of lettuce grown traditionally in California and transported to St. Louis against indoor farming solutions based in St. Louis — including greenhouse hydroponically grown lettuce, greenhouse aquaponically grown lettuce, indoor vertically farmed lettuce, hydroponically grown lettuce and indoor vertically farmed, aquaponically grown lettuce — found that the energy required to run the lights, irrigation and automation for all the indoor solutions resulted in an overall higher climate impact than the traditional farming method.
"Energy stands out as one of the bigger hurdles facing the [vertical farming] industry," said Julia Kurnik, director of innovation startups at WWF and author of the study. "Because it already is making great gains around things like water use, pesticide use, food loss and food waste. So it’s doing wonderful things there."
According to Kurnik, hydroponics and aeroponic farming use less water and don’t degrade soil like traditional farming, but for vertical farming to become environmentally sustainable on a carbon emissions level, these systems need to source electricity from renewables such as solar, wind or hydro.
But simply hooking up a vertical farm to solar or wind power won't solve the problem. Manufacturing solar panels is also an environmental strain due to the materials mined and energy used to make the solar panels. Like Kurnik said, everything that produces energy has to be built. And on the business side, AeroFarms said it’s very difficult for the company to find locations that have access to 100 percent renewable energy.
According to Rosenberg, access to a greener grid is part of AeroFarms’ weighting process for picking new locations for farms, but it can’t be a dealbreaker. For example, Danville relies heavily on nuclear and natural gas for energy, which is one reason AeroFarms decided to build there. Rosenberg also hopes AeroFarms will start to focus on places and cities that have access to hydropower.
But both Kurnik and AeroFarms CTO Roger Buelow agreed that one of the main goals for both the industry and AeroFarms specifically should be reducing the energy intensity of vertical farm growing.
"Let’s be more efficient," Buelow said. "Let’s make sure we are getting the most pounds per square meter per photon we can get. So that we’re really being good stewards with that energy. And we’re making sure that every photon gets to do its job."
One way AeroFarms does this, according to Buelow, is to put a lot of effort into making sure it uses the most efficient LED lights. But Rosenberg emphasizes that there is more to the environmental picture than just energy usage. He notes that aeroponic farming doesn’t use pesticides, herbicides or fungicides, which all have embodied energy in their production and produce degradation effects on the environment.
"There’s the environmental picture. There’s the energy side. There’s the pollution side. There’s the soil degradation side. There’s the water usage side. The water contamination side. There’s the food waste side," he said. "It’s part of a much broader narrative in assessing what’s good or what’s not as smart for the environment."
Working on expanding crop offerings
According to the WWF study, energy represents about 25 percent of the operating costs for vertical farms, and those costs have limited what is profitable to grow in contained-environment agriculture.
"I’ve seen pretty much anything, even fruit trees growing in these systems," Kurnik said. "But it isn’t cost-effective or energy-effective. You would spend so much energy growing them, it would bring a large environmental footprint, and it would become too expensive for the farms to sell that produce. So to see the entire industry scale and be able to grow a much greater variety of things and therefore capture all the benefits that these farms do bring, we need to figure out how to lower and/or green that energy footprint."
Berries are a high-value crop that could make the investment on the vertical farming side worthwhile for businesses such as AeroFarms.
AeroFarms is working on breaking out of the leafy green market and making some of those more energy-intensive crops profitable. The company has grown 550 varieties of plants in at least the research phase and is participating in a trial of growing a pharmaceutical ingredient for a drug. But the most likely success story will be the berries it hopes to cultivate working alongside Hortifrut.
"[The partnership] is a great example of how we really think of ourselves as a platform," Rosenberg said. "And how we work on this platform to solve broader problems in agriculture."
Berries are a fickle fruit in the agriculture world. Berries are part of the Dirty Dozen, a list of 12 produce types created by nonprofit The Environmental Working Group that use a lot of pesticides. They are also a high-demand product that people want year-round but that only grow best in summer months, leading to massive transportation costs (both financially and environmentally) as the industry ships berries from farther away places to meet this demand. With that in mind, berries are a high-value crop that could make the investment on the vertical farming side worthwhile for businesses such as AeroFarms.
"It’s local. It’s perishable. There’s a reliable demand. There’s a need for consistency. There’s a need for pesticide-free, herbicide-free," said AeroFarms CFO Guy Blanchard. "There’s many, many markets that look like they could very well make sense [for vertical farming]. We’re at the forefront of looking for those types of crops and markets and finding ways to deploy the technology to address those markets."
One example of that initiative: AeroFarms is also a founding member of Precision Indoor Plants (PIP), a joint venture between The Foundation for Food and Agriculture Research and other participants including BASF, Benson Hill, FFAR, Fluence, GreenVenus and Priva. The consortium is working on genetically adapting seeds for optimized indoor growing, improving light recipes, advancing speed breeding technology and altering the chemical makeup of plants to improve flavor, nutrition and medical efficacy.
"The broader world of vertical farming will have access to all those genetics, and we’ll all be able to grow stronger plants that really make the best use of the features of vertical farms," Buelow said.
PIP and AeroFarms plan to share their findings and innovations with the broader vertical farming community so every business in the industry can operate as efficiently as possible.
"I do think there is a lack of knowledge sharing and best practices across the industry," Kurnik said. "Because it is a bunch of startups. It is very nascent. I think the entire industry could benefit from sharing and establishing metrics and a baseline to figure out how to improve."
Balancing automation alongside social goals
The sustainability of farming and food are huge social issues as much as they are environmental ones. According to Rosenberg, one reason AeroFarms chose to locate a farm in Danville was because of the social impact it could make there. The city is 51 percent African American and has a relatively higher poverty rate than its neighbors.
By entering an economically depressed city, AeroFarms can address food deserts and help alleviate them by providing locally sourced food and creating jobs. The Danville operation will employ about 100 people from the community, according to Rosenberg. "We want to go into those communities and inspire those communities," he said.
AeroFarms also supports a past offenders program that started in 2016 and provides employment for 15 formerly incarcerated people so far.
Automation is coming, and it is one way AeroFarms will decrease costs. But that could undermine the jobs added by the company in the future. Right now, the company automates the seeding process, but the seedlings are placed in trays manually. The loading, unloading, harvesting and packaging is automated but pockets of manual work are needed as well. AeroFarms wants to use the best technology while still providing jobs, according to executives.
Vertical farms are often a collision of education levels; highly educated engineers working alongside farm labor.
"Obviously, our next farms are going to be more automated, much more automated and that innovation is something we are proud of," said Diego Rivera, Aerofarms’ master grower. "But even with automation, nothing is going to replace the human eye. Some key positions are going to be still there."
So it’s going to be about retraining. According to Rivera, Aerofarms has programs in place that create conditions for people to stay at the company by promoting people from within.
"Our approach is going to innovate and continue to work to bring our workforce along with us," Rosenberg added. "How do we train for those next skills? How do we get them to understand how to use those controls so they could apply their contribution in a higher level way? We’re constantly training them to be ready for the next challenges."
To provide employees with the opportunity for upward mobility, AeroFarms offers computer literacy programs and financial literacy workshops. According to Rosenberg, vertical farms are often a collision of education levels; highly educated engineers working alongside farm labor.
"So how can we get the highly educated workforce to work with our frontline workers to teach them these skills and help form that sense of community," Rosenberg added.
It’s clear vertical farming sits right in the middle of many of the largest issues facing our economy and our planet. AeroFarms is trying to tackle a lot of them; everything from food insecurity to energy usage to job sustainability. Succeeding could create a path leading others towards a sustainable and equitable economy of the future for others to follow, while failing will offer a parable of trying to be all things to all people and biting off more than you can chew.
Opening Large Vertical Farming Facilities in Europe
Infarm has signed a contract for a new Growing Centre in Bedford which will measure 9,760 sqm in size, offering more than 5500 sqm of growing space in Infarm’s cloud-connected farming units.
August 9, 2021
Infarm has signed a contract for a new Growing Centre in Bedford which will measure 9,760 sqm in size, offering more than 5500 sqm of growing space in Infarm’s cloud-connected farming units.
Jeremy Byfleet, UK Country Director at Infarm, said: “Infarm has a clear goal to expand in the UK market. Our second UK Growing Centre located in the “golden triangle” allows us to significantly increase the amount of fresh produce grown year-round in the UK.
When fully equipped, the units - each occupying 25 sqm of ground space and 10 metres in height - are able to produce up to 18 million plants per year and generate the crop equivalent of 360,000 sqm of farmland. The Growing Centre is currently in construction and on track for a first harvest in Q4 of 2021.
Each Infarm Growing Centre can save up to ten million liters of water per year, reducing water consumption by 95% versus traditional agricultural methods. Pentadel, appointed by Infarm to select a site as well as design and manage the construction of the new Growing Centre, has also integrated rainwater harvesting into the design of Infarm's new facility. Implementing rainwater harvesting is expected to capture a further 2.5 million litres of water per year, which will be used for conditioning plants.
Infarm will continue to operate its existing Growing Centre in Edmonton, North London and is currently hiring. “We have already opened up new positions for our locations in London and Bedford and will continue to do so as we expand our Bedford operation,” said Byfleet. To establish this large vertical farming facility, Infarm has partnered with Pentadel Project Management.
The location of the facility enables us to serve 90% of the UK population within four hours, bringing the freshest plants just on time to our clients. Consequently, food mileage is substantially reduced. One of the largest indoor vertical farming facilities in Europe to date is going to deliver millions of plants and provide fresh and locally grown produce to even more consumers via our retail partners, restaurants and online food retailers.”
James Kemp, Managing Director of Pentadel, said: “We are thrilled to be supporting Infarm with the delivery of this innovative facility that we believe represents the future of sustainable, scalable and resilient farming. We are passionate about delivering projects just like this – projects that place the future of people and the planet at their heart – and I know the whole team is proud to play a part in Infarm's revolutionary story.” Pentadel has identified a suitable UK site, negotiated terms and is now designing and managing the construction of the facility.
In the UK, Infarm’s herbs and leafy greens are currently found at Whole Foods Market, Selfridges, Marks & Spencer, Fortnum & Mason and Budgens as well at online retailers Weezy and Farmdrop. The new Growing Centre will join Infarm’s expanding global network of vertical farms that all connect to a central farming brain that gathers data constantly to improve plant yield, taste, and nutritional value, while further reducing the use of natural resources. By the end of 2025, Infarm plans to expand to 100 locations worldwide.
For more information:
Infarm
press@infarm.com
www.infarm.com
2021 Virtual Plant Lighting Short Course
In each sequential module, attendees will use interactive tools to define their specific lighting requirements, hear from industry experts about available horticultural lighting systems, and learn how to compare different lighting strategies
Now Open For Registration!
Working in partnership, GLASE, OptimIA, and LAMP are excited to announce the first annual Plant Lighting Short Course! This 6-week modular short course is designed to provide participants the opportunity to learn about all aspects related to the selection, implementation, and benefits of plant lighting systems.
In each sequential module, attendees will use interactive tools to define their specific lighting requirements, hear from industry experts about available horticultural lighting systems, and learn how to compare different lighting strategies. By the end of the course, participants will be equipped to make informed decisions about the best options to meet their lighting needs.
More Info & Registration
Media Partners
Recordings Now Available
Optimizing Resource Use Efficiency in CEA Systems - July Webinar
New CEA Research Programs in the U.S. - June Webinar
"We’re Hoping For A More Domestic Type of Farming”
“Whilst living in a 9-square meter student residence, the idea of being able to use this really small space to sustain myself with well packed nutritious food was what sparked the idea of Vita” Walid Brahim, CEO with Élever Group explains.
By Jenneken Schouten
August 9, 2021
“Whilst living in a 9-square meter student residence, the idea of being able to use this really small space to sustain myself with well packed nutritious food was what sparked the idea of Vita” Walid Brahim, CEO with Élever Group explains.
A small personal farm for everyone, a revolutionary product that combines aesthetic looks and the implementation of the most advanced technologies to date. That is the idea behind Vita that Élever Group recently launched.
The main aim of creating Vita was to bring a new level of transparency to food production, powered by blockchain technology, permitting users to safely buy and sell their harvest within small-scale communities. “We noticed that France, despite being a nation known for its agricultural scene, has experienced somewhat of a downfall regarding the people’s confidence when buying or consuming the goods grown in their own country. With Vita, we aim to rebuild this confidence,” Walid explains.
Read the rest of the article here
“We Can Put 90 Strawberry Plants Per m2 Where A Greenhouse Would Put Only 10-12”
“I spent my first 25 years on a farm and the next 25 years in technology. Vertical farming is the bridge between those worlds,” says Yves Daoust, chief operating officer and founder of Ferme d’Hiver. The company was founded in 2018 and aims to develop a network of indoor farms and become a global hub for vertical farming.
By Rebekka Boekhout
August 9, 2021
“I spent my first 25 years on a farm and the next 25 years in technology. Vertical farming is the bridge between those worlds,” says Yves Daoust, chief operating officer and founder of Ferme d’Hiver. The company was founded in 2018 and aims to develop a network of indoor farms and become a global hub for vertical farming.
In May 2021, Ferme d’Hiver announced that it had secured $5 million in funding from Investissement Québec, Haystack and Mavrik during its most recent funding. This funding will help Ferme d’Hiver build its first commercial indoor strawberry farm, which will cover roughly 1000 square meters and be located in Vaudreuil, Québec. Winterberry production is expected to begin in October 2021.
Read the rest of the article here
80 Acres Farms Secures $160 Million In Series B Led by General Atlantic To Accelerate Global Farm Expansion & Product Development
80 Acres Farms' vertical farm systems grow the widest variety of produce commercially sold at scale by any vertical farm to-date, including leafy greens, herbs, tomatoes, cucumbers, and microgreens
August 9, 2021
HAMILTON, OH / ACCESSWIRE / 80 Acres Farms, the industry-leading vertical farming company, has secured $160 million in additional funding in a round led by General Atlantic and joined by Siemens Financial Services, Inc. (the U.S. financing arm of global technology company Siemens). The company intends to utilize the capital for continued expansion and product development, building from its current footprint of vertical farms that yield a diverse offering of high-quality produce.
The funding round also included Blue Earth (formerly PG Impact Investments) and General Atlantic's Beyond Net Zero team, in addition to participation from existing investors including Barclays and Taurus.
80 Acres Farms' vertical farm systems grow the widest variety of produce commercially sold at scale by any vertical farm to-date, including leafy greens, herbs, tomatoes, cucumbers, and microgreens. The company's breakthrough growing technologies and advanced data analytics capabilities have enabled this industry-leading product breadth, driving over 450% revenue growth since the end of 2020. 80 Acres Farms now services over 600 retail and food service locations, including its recent expansion with Kroger, announced earlier this year to 316 stores in the U.S. Midwest and to the e-commerce channel powered by Kroger - Ocado Solutions' partnership. With farms co-located near customers, 80 Acres Farms' produce travels significantly fewer food miles, shortening the farm-to-table footprint and reducing overall food waste. Growing methods at 80 Acres Farms use 97% less water than traditional farming practices and are powered by renewable energy.
- ADVERTISEMENT -
To date, 80 Acres Farms operates eight indoor farms and is committed to supporting and building high-tech production facilities close to regions where fresh produce is consumed. The company has transformed a former factory in Hamilton, Ohio, to a world-class tomato indoor farm, and in 2020, 80 Acres Farms completed construction on a new, 64,000-square-foot, state-of-the art farm with 10 levels of cultivating space. 80 Acres Farms is currently engaged in identifying new farm locations for additional commercial farms to operate at similar scale.
Shaw Joseph, Managing Director of General Atlantic, said: "80 Acres Farms is building an incredibly exciting vertical farming business that provides high-quality produce through innovative practices. With global food consumption increasing and growing threats impacting supply chains and food security, there is a pressing need for healthy, fresh and local foods that are grown in more sustainable and cost-effective ways. We look forward to working closely with Mike, Tisha and the broader 80 Acres Farms' team as they scale."
Jason Thompson, Vice President of Sustainability and Growth Equity at Siemens Financial Services, said, "We are committed to help scale sustainable vertical farming technology. 80 Acres has demonstrated their ability to build and operate profitable farms, and Siemens is enthusiastic about the opportunity to support its global expansion with both our capital and technical know-how, including our recently established Center of Competence dedicated to supporting companies in realizing their digital transformation."
Kayode Akinola, Head of Private Equity Directs at Blue Earth Capital, said, "We are excited to be partnering with General Atlantic and Siemens to provide growth capital and support to Mike, Tisha and the entire 80 Acres team to help scale their operations within existing and new markets."
Mike Zelkind, CEO of 80 Acres Farms, said: "We are proud of what our team has been able to accomplish and enthusiastic about the road ahead. We are also honored to be supported by such a high caliber group of strategic investors who are enabling us to continue to lead this evolving and fast-growing industry. The investment is a quantum leap for the business to build more farms both nationally and globally.
Tisha Livingston, CEO of Infinite Acres, and Co-founder of 80 Acres Farms, said: "The new investment positions the company as the leading proven and profitable technology provider prepared for rapid expansion. In addition, this enables 80 Acres to focus on their operational expertise and deep research and development capabilities beyond leafy greens."
As part of this funding round, Shaw Joseph will join the 80 Acres Farms board. Eli Aheto, former 80 Acres Farms board member, led BeyondNetZero's contributions to this round. "I am pleased to be able to continue and grow my support of 80 Acres with this contribution from the BeyondNetZero team. 80 Acres has proven a farm design that is poised to reduce food miles, food waste and the resulting negative carbon emissions that exist within our food supply chain," said Eli Aheto.
Barclays acted as sole placement agent to 80 Acres on the capital raise.
About 80 Acres Farms
80 Acres Farms is a vertical farming leader providing customers with the freshest, and most nutritious fruits and vegetables at affordable prices. Utilizing world-class technology and analytics, the Company offers customers a wide variety of pesticide-free food with a longer shelf-life that exceeds the highest standards in food safety. Consumers can find 80 Acres' products of just-picked salads, tomatoes, cucumbers, herbs, and microgreens at Kroger, Whole Foods, The Fresh Market, Dorothy Lane Markets, Jungle Jim's Markets, and key National Foodservice Distributors including Sysco and US Foods.
Media Contact
Rebecca Haders / rebecca.haders@eafarms.com / +1 513-910-9089
About General Atlantic
General Atlantic is a leading global growth equity firm with more than four decades of experience providing capital and strategic support for over 400 growth companies throughout its history. Established in 1980 to partner with visionary entrepreneurs and deliver lasting impact, the firm combines a collaborative global approach, sector specific expertise, a long-term investment horizon and a deep understanding of growth drivers to partner with great entrepreneurs and management teams to scale innovative businesses around the world. General Atlantic currently has over $65 billion in assets under management and more than 175 investment professionals based in New York, Amsterdam, Beijing, Hong Kong, Jakarta, London, Mexico City, Mumbai, Munich, Palo Alto, São Paulo, Shanghai, Singapore and Stamford. For more information on General Atlantic, please visit the website: www.generalatlantic.com
General Atlantic also recently formed its BeyondNetZero (BnZ) team to seek out growth companies delivering innovative climate solutions. BnZ looks to identify entrepreneurs with technologies that enable companies to meet and exceed Net Zero emissions targets, with a focus on de-carbonization, energy efficiency, resource conservation and emissions management.
Media Contacts
Mary Armstrong & Emily Japlon / General Atlantic media@generalatlantic.com
Faustine Rohr-Lacoste / Spendesk faustine@spendesk.com
About Siemens Financial Services
Siemens Financial Services (SFS) - the financing arm of Siemens - provides business-to-business financial solutions. A unique combination of financial expertise, risk management and industry know-how enable SFS to create tailored innovative financial solutions. With these, SFS facilitates growth, creates value, enhances competitiveness and helps customers access new technologies. SFS supports investments with equipment and technology financing and leasing, corporate lending, equity investments and project and structured financing. Trade and receivable financing solutions complete the SFS portfolio. With an international network, SFS is well adapted to country-specific legal requirements and able to provide financial solutions globally. Within Siemens, SFS is an expert adviser for financial risks. Siemens Financial Services has its global headquarters in Munich, Germany, and has around 2,800 employees worldwide. www.siemens.com/finance.
About Blue Earth Capital
Blue Earth Capital is a global investment firm focused on sustainability and impact investing. Headquartered in Zug, Switzerland, with operations in New York, London, Singapore, Luxembourg and Guernsey, Blue Earth Capital seeks to invest in businesses that address pressing environmental and social challenges, whilst generating market-rate financial returns. Initiated in 2015 by Urs Wietlisbach, one of the founders of Partners Group, and backed by the Wietlisbach Foundation, Blue Earth Capital was incubated and built up with the support of Partners Group.
Media Contacts
Urs Baumann / CEO Blue Earth Capital urs.baumann@blueearth.capital
80 Acres CEO Reflects on Vertical Farming Post $160m Raise: ‘There Will Be Losers With Very Big Names’
For Mike Zelkind, CEO at Ohio-based vertical ag operation 80 Acres Farms, not everyone will make it to the finish line.
By Lauren Manning
August 11, 2021
The indoor farming sector is dazzling investors and attracting its fair share of nine-figure deals. But as the space grows more crowded and competitive, questions are sprouting up regarding market saturation, the right business models, and whether indoor mega-farms like the one Minnesota’s Revol Greens is planning are the way to go.
For Mike Zelkind, CEO at Ohio-based vertical ag operation 80 Acres Farms, not everyone will make it to the finish line.
“This is the way the market works. There will be winners and losers and there will be losers with very big names,” he tells AFN.
“But the world needs this and even the losers [will have been] very well-intentioned. My heart will go out to everyone who does not win because I know they fought the good fight.”
80 Acres just announced the close of a $160 million Series B round led by US growth equity firm General Atlantic.
Other investors in the round included Siemens Financial Services — the US financing arm of German tech giant Siemens — as well as Barclays, Blue Earth, Taurus Investment Holdings, and General Atlantic’s impact-focused BeyondNetZero team.
Although Zelkind views the indoor farming space as big enough for many players to do well, he thinks some recent valuations are exaggerated.
In his opinion, 80 Acres sets itself apart through its partnerships, like its joint venture with e-grocer Ocado and tech provider Priva. The trio formed the venture, Infinite Acres, in 2019 to help growers enter the tech-enabled indoor farming space.
Staying close to the consumer
80 Acres takes a decentralized approach to getting its produce on consumers’ tables, building its farms close to areas where its customers are located. The startup runs eight farms, and sells its products in around 600 retail and foodservice locations. Without sharing specific figures, it claims to have posted 450% growth in revenue since the end of last year.
Building close to its customer base has also been a foundational aspect of 80 Acres’ business model, Zelkind suggests.
“I don’t think there are any other farming operations today that have built a farm as close to the distribution center of their customer,” he says. “Just getting a little closer to the customer is not good enough.”
Zelkind claims that 80 Acres had a lot of options when it came to choosing investors for its Series B round but that funders with strategic angles were the winning choice. General Atlantic focuses on world-changing technologies, including foodtech, while Siemens can assist with continued industrialization of the startup’s capabilities, he adds.
80 Acres will use the new funding to expand its footprint while supporting product development. Based on his own observations of rival startups’ activities and claims, Zelkind argues that his company offers the widest variety of produce in the vertical farming industry, selling leafy greens, herbs, tomatoes, cucumbers, and microgreens, among others.
“I’m not aware of anybody even making a claim that they are commercially growing these items, and we’ve had the product in the marketplace for the last four years,” he says. “It’s not a claim – it’s a fact.”
Lead Photo: Mike Zelkind, CEO, 80 Acres Farms. Photo credit: 80 Acres Farms Facebook page.
Strengthening Ties With Qatar To Grow In The Middle East
At iFarm, we will remember June 2021 as the month of Qatar! We announced an agreement to build a vertical farm based on our technology in Doha, hosted two high-profile delegations from Qatar at a lettuce farm, and held a series of important discussions regarding cooperation in the country
August 3, 2021
At iFarm, we will remember June 2021 as the month of Qatar! We announced an agreement to build a vertical farm based on our technology in Doha, hosted two high-profile delegations from Qatar at a lettuce farm, and held a series of important discussions regarding cooperation in the country.
Background information on the Middle East region
The Arabian Peninsula has an extremely hot and arid climate (it’s one of the hottest places on the planet), and Qatar is no exception. There are sands and dunes in the north, sandy hills in the south — with a rocky desert in the middle. In the summer months, temperatures can reach 50 °C. The country has no rivers and obtains most of its freshwater by desalinating seawater. As a result, Qatar has extremely unfavourable conditions for growing edible plants such as vegetables, berries, and herbs. However, where tomato plants wither, date palms thrive. The “Queen of the Oasis” has been bearing excellent fruit throughout the entire Middle East region for thousands of years. It’s just, you can’t live on dates alone.
99,1 %
Qatar’s urbanisation rate
(one of the highest in the world)
90 %
of food in Qatar is imported
Although Qatar ranks among the richest countries in the world in terms of per capita income, it relies heavily on imports to feed its population. Local agriculture only covers 10% of the country’s needs, and food security remains high on Qatar’s agenda. With its abundant financial resources, the country can use state-of-the-art technology to grow crops. Due to this, we believe local, year-round cultivation of vegetables, berries, and herbs on vertical farms is one of the best solutions for this region.
“By working with iFarm, Qatar increases its share of locally grown products, and we can showcase how our technology can be used in a region with extreme climatic conditions. The use of translucent greenhouses can be a problem given the hot climate: they need to be shaded and cooled. Vertical farming, on the other hand, is a perfect match. This is an excellent tool that can help Qatar achieve its ambitious food security goals.”
Alex Lyskovsky
president of iFarm
As you may recall, Qatar has adopted a National Food Security Strategy under which the country aims to reach 70% self-sufficiency in food production by 2023.
Cooperation with Agrico
Our first talks about building vertical farms powered by iFarm technology in Qatar go back to 2019. The Qataris are very cautious in choosing partners, but once they get involved, you can be sure it’s going to be serious and long-lasting. We recently announced a joint project with Sadarah that includes building a commercial pilot farm based on the Agrico Farm in Al Khor, 50 km from Doha. iFarm supplies hardware and software, and will oversee the farm once it goes live and help the partners manage the technology. The second phase of this joint effort involves the commercial distribution of products to the local market and the extension of vertical cultivation technology to other farms in Qatar and neighboring countries. Contractors are currently erecting a purpose-built environment specifically for this vertical “plant factory” project.
Cooperation with Lulu Group International
LuLu Group International is iFarm’s signature partner in the Middle East. It is a multinational corporation that operates one of the largest retail chains in Asia and the Persian Gulf. LuLu is among the fastest-growing chains in the world and employs more than 57,000 people around the world. We are in talks with LuLu Group’s representative office in Qatar regarding building vertical farms right in the supermarkets. At least one side of the pilot farm is designed using transparent material, so that customers can see the process of growing and harvesting plants from “smart” beds. In early June 2021, the project was discussed at the International Economic Forum in St. Petersburg. It is of great importance to us because it can be scaled up throughout the entire chain, covering more than 200 stores in 22 countries.
Qatari delegations visit farms powered by iFarm technology
Indoor cultivation in a fully controlled environment still attracts a lot of attention and investment due to its obvious benefits, including land and water conservation, reduction of CO2 emissions, absence of pesticides, etc. Vertical farming is a sustainable method of farming, and although it won’t replace conventional farming everywhere, in many regions it is, perhaps, the only way to harvest high-quality fresh vegetables, berries, and herbs locally throughout the whole year.
Two delegations from Qatar visited a farm powered by iFarm technology in June. The head of the country’s investment promotion agency (IPA Qatar), Sheikh Ali Al-Walid Al-Thani, was one of our guests. The agency aims to attract direct investment in Qatar and assists entrepreneurs throughout the entire investment process providing services on a ‘one-stop shop’ basis.
We also had the pleasure of welcoming Masoud Jarallah al-Marri, Director of the Food Security Department at the Ministry of Municipality and Environment. He is responsible for the national certification of agricultural products and takes special care to verify the performance of any technology that is going to be introduced in Qatar.
Both guests inspected all of the production areas at the vertical farm, saw how the engineering equipment and software work, tasted a range of products grown on the farm, and left satisfied!
“Qatar is developing rapidly, and I am amazed at the pace of change in this country, which is literally turning into a huge beautiful oasis in the middle of the desert. Doha, for example, has a state-of-the-art, fully automated subway running under the city’s skyscrapers. Qatar has welcomed many foreign investors and businesses in recent years, thanks to its national vision, efforts to diversify the economy and the country’s role as hosts of the FIFA World Cup in 2022. We are happy that iFarm technology will provide guests and locals with delicious greens, vegetables and berries, and will enhance the country’s food security in the long term.”
Alex Lyskovsky, president of iFarm
Source and All Photo Courtesy of iFarm
Smart Farms: Getting To the Heart of The Matter
Labour costs account for up to 50% of the market price of vegetables, berries, and herbs. However, just like the tractor that once transformed agriculture, the new technological revolution greatly reduces the need for manual, skilled and specialist labour
August 3, 2021
Take a look behind the scenes of vertical plant automation and find out what it takes to bring a smart farm to life with exciting exploded-view diagrams.
Labour costs account for up to 50% of the market price of vegetables, berries, and herbs. However, just like the tractor that once transformed agriculture, the new technological revolution greatly reduces the need for manual, skilled and specialist labour. Today, the work is done by a team of robots, sensors, artificial intelligence, and a core team of highly skilled professionals who manage hundreds of farms at once using special software. As a result, we witness the “battle for the harvest” moving into the IT domain.
A vertical farm functions as an organism, and its equipment can be compared to human organ systems. Its sensors and senders are the nervous system, its air conditioners and dehumidifiers act as the respiratory system, while the solution supply pipeline represents the circulatory system. We can compare the nutrient mixing unit to the endocrine system, tray conveyors and lifts to muscles. Naturally, this organism has a “brain” — the Growtune IT platform.
The degree to which the brain can accurately and confidently “take control” determines how ready various systems, nodes, and technologies are to operate without human intervention. Below, we describe all of the tech that lies inside a vertical farm. How, where, and at what production stages does the automation work? For this purpose, we’ll leverage the somewhat forgotten “exploded-view diagram” style. This way, we'll be able to show all the devices the farm uses to take care of the plants.
1. Breathing: ventilation and air conditioning
Let’s remember biology classes. Plants use photosynthesis to turn light, water and CO2 into oxygen and energy. By doing so, they can consume far more CO2 than is normally present in the air. Since the farm, like a space station, uses a closed-loop air exchange system, with no air inflow from the street, creating an optimal environment and climate for plants is purely an engineering challenge. This includes purifying, conditioning, and adding some CO2 to the room to allow plants breathe freely and grow intensively.
“People who walk into a vertical farm for the first time notice how nice and clean the air is. That’s no surprise because it doesn’t contain any dust — there’s nowhere dust can appear from in the closed-loop circuit of the farm.
Alexey Novokreshchenko, Head of Automation at iFarm
The farm has multiple air conditioning units. It’s not just a matter of maintaining a certain temperature and humidity. We need to make sure that the climate is as homogeneous as possible throughout the entire arm, including at different heights. So, instead of one super-powerful unit, we install several medium-sized devices. This provides the right air circulation and creates a failure-proof system.
Hydroponic technologies tend to create a lot of moisture, and the farm air typically needs to be dehumidified (iFarm has developed and patented a dehumidification system that allows you to reuse this water to feed your plants). There are times, though, when you need to do the opposite: for example, you may need to humidify the air, especially at the initial stage of starting a farm when you don’t have a lot of plants.
2. Energy: grow lights
Photosynthesis, that is the conversion of light energy into chemical energy, only occurs when there is light. Agronomists call artificial lighting of plants “supplemental lighting”. It may vary from one area of the farm to another, depending on the crop and its cultivation phase. The light control unit creates “day” and “night” conditions for plants. The most frequent setup resembles a nice summer day: 14–16 hours of light and 8–10 hours of darkness. Darkness is crucial: the night is when cellular respiration occurs and other important processes take place.
“The plant depends on the day-and-night schedule. Its structure and maturation phases vary depending on the light cycle. Keep the microgreen sprouts in the dark a little longer, and they'll stretch out but will become coarser. By changing the lighting, you can experiment with taste. For example, if you keep sunflower microgreens in the dark for 10 days and then expose them to the light for a full day, you’ll get long and very sweet sprouts.”
Nikolai Podvigin, Head of the Agrolaboratory at iFarm
Agronomists at pilot farms refine cultivation flow charts. For example, they are currently experimenting with variable brightness to grow pine strawberries: the lamps are equipped with a dimmer so you can gradually add brightness. It seems that the agronomists’ hypothesis holds true — the berry evidently "enjoys" long dawns. Through smooth, incremental changes in lighting, the osmotic pressure in the stem and leaves grows gradually, whereas its surge upon sudden light exposure can have a tissue-damaging effect.
Sometimes you have to focus not only on what the plants need but also on organisational or purely economic factors. For example, the cost of electricity. True, the lamps we manufacture and install in racks are highly energy-efficient: they convert every watt of electricity into 0.6 watts of photosynthetically active radiation (FAR). Still, energy costs make up a large portion of the costs of growing herbs indoors. Automation can (and should) be leveraged to ensure optimal load distribution. If the farm can use a night rate, we change “days” with “nights” and reschedule the supplemental lighting for the nighttime to minimise operating costs.
3. Nutrition: irrigation and nutrient solution supply
The nutrient solution is made from several components stored in individual containers which can easily be replaced. The solution is prepared in the mixing unit, a sophisticated automated system capable of mixing dozens of litres of stock solutions with high precision and in the right proportions.
The nutrient solution is delivered to the roots of the plants through a tube system. Since the specific recipe depends on the type of the plant and its cultivation stage, the system continuously monitors (and sometimes adjusts) the composition of the solution.
“Plants eat and plants drink. We provide them with both by mixing nutrition with water. This water continuously runs through the rack. To create an individual “menu” for each plant type, we divide the farm into different watering areas and install an additional storage tank in each of them. Each area is equipped with an additional set of sensors that dynamically monitor the changes in the solution. In fact, these sensors control whether the plant “ate well” today and whether they have everything they need.”
Alexey Novokreshchenko, Head of Automation at iFarm
The water used for preparing the solution is added to the system after it is properly treated with a reverse osmosis filter. This removes contaminants, such as minerals, heavy metals, bacteria and viruses, leaving the water virtually pure.
4. Well-being: IoT sensors
The purity of the source water, the ratio of nutrients in the solution, its acidity, the brightness of the light, the amount of carbon dioxide in the air, temperature, and humidity — you need to control all these things with precision. A large farm can have hundreds of sensors.
Based on sensor measurements, the farm's central processing unit controls the equipment and hardware in real-time, always keeping climatic and biochemical parameters within the limits set by the cultivation flow chart.
If these limits are exceeded, it triggers an alarm and remote technicians are alerted. The algorithm helps identify potential human errors, among other things. For example, it will immediately alert you if a technician incorrectly replaces the cans with the source materials for the solution.
“Plants can be extremely sensitive, some may “dislike” even a one-degree deviation from the usual temperature. We covered the racks with sensors and cameras so we could understand what a crop is sensitive to during cultivation. Now we’ve stabilised the process by defining the optimal number of devices to ensure accurate environment control.
Nikolai Podvigin, Head of the Agrolaboratory at iFarm
5. Analytics: computer processing of Big Data
The “head” of the system is a cloud server. It collates and computes data indirectly from the array of actual measurements collected. For example, it calculates the efficiency of air circulation across the farm based on the data from all of the climatic sensors. What’s even more important is the ability of Growtune, the farm management software platform, to process all of the Big Data collected on the farm.
“The algorithms we use to prepare nutrient solutions are based both on recipes and on the processing of collected data. The outcomes of plant nutrition in previous cycles affect future mixing. The controller monitors the plants’ reaction to “dinner” on the previous day and adjusts the solution accordingly. And, after reviewing the combined data from different farms, we gradually optimise the flow charts.”
Alexey Novokreshchenko, Head of Automation at iFarm
Farms are increasingly using machine vision in their “nervous system”. Images from the cameras installed on the racks are analysed by a neural network trained to determine if the plants are healthy. Technicians can also use this neural network by uploading a picture of plants through a chatbot to gain critical information about its health. Another neural network calculates the dynamics of herbage mass accumulation using the same stationary video cameras or drone cameras.
6. Movement: automation of tray movements
Problems usually dealt with by rare and expensive specialists, agronomists, biochemists, and phytopathologists can be solved using artificial intelligence, special equipment, or remote consultants. But, until recently, there hasn’t been a fully automatic farm where electronics also handle routine manual work, such as moving trays.
In February 2021, iFarm engineers implemented and tested a design prototype of a fully automated vertical farm. It features a conveyor belt that moves trays with pots through the planting, germination, growth, ripening, and cutting areas. The farm can also be equipped with individual robot modules for packaging products and preparing trays for the next cycle.
7. A human helping hand
As with any sophisticated modern equipment, an automated farm has special service message protocols. Naturally, these protocols are intended for a person, such as an employee of a certified service provider. Automatic warnings about errors, worn-out nodes, or the need for consumables to be replaced translate into assignments for replenishment or troubleshooting.
The reports of deviations in the growth of herbs are handled by an iFarm agronomist. The first thing this expert does is double-check that the actual conditions match the ones in the flow chart. They then go through a list of tasks almost identical to the sections of this article. So, what’s happening with the air, climate, energy, and nutrition of the plants on the farm? Do the sensors provide correct data? When suspecting a technical failure, the agronomist connects a service employee to the diagnostic interface with one click. They can also connect to the technician’s camera or AR glasses if the employee is already on site.
“We have several continuous operation circuits, millions of second-by-second measurements, sensors, robots, conveyors, drones, cameras, and neural networks. It seems we’ve automated almost everything we can. The only thing you can’t automate is the R&D process itself. This is why people in the company focus on this process. And this is exactly why we are fighting for strategic investments.”
Vertical Gardening: A Modern Farming Method
Many of our communities are transforming into industrial and urban centres as the earth’s population increases. This growth, coupled with climate change, poses new challenges to the human populace to produce enough food as farmland acreage decreases and consumers’ demands increase.
July 25, 2021
Many of our communities are transforming into industrial and urban centres as the earth’s population increases. This growth, coupled with climate change, poses new challenges to the human populace to produce enough food as farmland acreage decreases and consumers’ demands increase.
Over the past decade, scientists and agronomists have been developing methods to produce double or triple the amount of food, using the same scale of land or less a farmer may cultivate. One of these approaches currently gaining much attention and adaptation is the vertical gardening or farming method.
NAREI staff harvesting and inspecting various crops planted in the vertical stack stand model, using PVC gutters
The notion of farming indoors is not strange to us, since greenhouse agricultural systems have been widely adopted for some time now. These houses have been used for years, providing conditions for numerous commercial crops (such as tomatoes, strawberries, peppers, and cucumbers) to thrive at its maximum production index. Cultivating under shaded facilities compared to outdoor farming fields can aid in year-round production, but few or none of these greenhouses have been constructed as multi-storey facilities.
Vertical farming is a method that uses vertically inclined surfaces to produce food, instead of the traditional method of growing vegetables on a single level in a greenhouse or open field. The National Agricultural Research and Extension Institute (NAREI) is currently evaluating the cost and productivity of various vertical-farming models. The experiment is being conducted at NAREI’s compound, Mon Repos, ECD.
NAREI staff harvesting and inspecting various crops planted in the vertical stack stand model, using PVC gutters
The vertical models installed under the tunnel house are: vertical stack stand using PVC gutters, vertical trellis made of nylon, barrel model using recycled plastic drums, and vertical wall using recycled plastic bottles.
Using vertical farming techniques have numerous advantages, such as: year-round production; reducing soil erosion and runoffs; maximising the use of abandoned structures or unused spaces; minimising crop failures due to harsh weather conditions and reduces the use of fossil fuels, since less farm mechanisation is needed. It also creates new urban employment openings; adds energy back to the grid via methane generation; returns farmlands to nature, aiding in restoring ecosystem functions; reduces pest and disease indices; reduces the need for abundant use of pesticides and herbicides, and offers the possibility of a sustainable food-production engine for our communities.
The experiment is being done to ascertain yields of a wide variety of crops needed to sustain large populations, without exhausting existing resources. With the success of this study, local households in Guyana can better utilise yard space to produce their foods at a cheaper cost and local farmers can increase productivity to reach consumer demand. In addition to that, this method can be utilised to combat major challenges faced due to climate variation in Guyana, such as flooding.
FI Report Preview: Vertical Farming Concept Experiencing Immense Growth
Vertical farming is growing by leaps and bounds. In fact, the evolving form of agriculture has become a multibillion-dollar industry and is expected to reach $12.77 by 2026, growing at a compound annual growth rate of nearly 25%, according to Allied Market Research.
By Kelly Beaton
July 19, 2021
Vertical farming is growing by leaps and bounds. In fact, the evolving form of agriculture has become a multibillion-dollar industry and is expected to reach $12.77 by 2026, growing at a compound annual growth rate of nearly 25%, according to Allied Market Research.
Quite simply, the concept “has gone viral,” said Dr. Dickson Despommier, a professor at Columbia University.
And Despommier should know. After all, he’s credited with conceiving the concept, back in 1999, during an especially spirited Medical Ecology course.
The Food Institute recently interviewed Despommier at length, in advance of its in-depth report on vertical farming, which is set to be published Tuesday (you can eventually download the report here). Here’s some exclusive content from that interview, which discussed numerous aspects of indoor farming, also known as controlled-environment agriculture (or CEA):
HOW WOULD YOU PERSONALLY DEFINE INDOOR FARMING AND VERTICAL FARMING?
Despommier: “Indoor farming includes all indoor farms, including vertical farms, and it also includes greenhouses. The only difference between a vertical farm and a greenhouse is height, because you can’t just set greenhouses on top of each other.
“Vertical farms have grow lights. If you use grow lights … you get more nutritious plants as a result of that, because you can tweak those lights to cause the plants to produce more things that we need, like vitamins.”
IN YOUR OPINION, WHAT’S A KEY BENEFIT PROVIDED BY VERTICAL FARMING?
Despommier: “By manipulating the indoor lighting systems … you can create plants that you could never grow outside. That’s one of the advantages.”
WHICH COUNTRIES ARE EMBRACING VERTICAL FARMING THE MOST?
Despommier: “The country that’s really got the most [vertical farming facilities] is Japan – Japan now has hundreds of vertical farms throughout the country, and they’re doing quite well. Taiwan has about 150, last I heard. Singapore has countrywide demand for locally produced food. The United States has a fair number, I would say in the neighborhood of 100, to 150.
HOW DO YOU ENVISION VERTICAL FARMING GROWING IN THE NEXT 5-10 YEARS?
Despommier: “I think the next issue will be, how can we franchise ourselves into a complete grocery store. And I know companies that are already doing that, so that’s in the wings. And, I think in another 5 years you’re going to see a versatility of crop selection that will force everything else into competition, and therefore [vertical farming] will succeed. That’s in the next 5 to 10 years.”
Vertical Harvest, MedRhythms Get FAME Financing to Advance Growth Plans
The Finance Authority of Maine has approved a total of nearly $50 million in financing for two startups — Vertical Harvest L3C, which plans to launch a hydroponic greenhouse in Westbrook, and a Portland provider of "digital therapeutics," MedRhythms Inc.
By Catie Joyce-Bulay
July 19, 2021
The Finance Authority of Maine has approved a total of nearly $50 million in financing for two startups — Vertical Harvest L3C, which plans to launch a hydroponic greenhouse in Westbrook, and a Portland provider of "digital therapeutics," MedRhythms Inc.
Vertical Harvest will receive $45 million in conduit bond financing. The company plans to produce over 1 million pounds of produce annually, and FAME's funds will be used to finance a portion of the construction costs to build 70,000-square-foot Westbrook farming facility. The project ultimately is expected to create approximately 50 full- and part-time jobs, many of which are expected to be performed by individuals with disabilities.
The project is part of a larger master-planned development that is expected to include affordable housing and parking in downtown Westbrook. Because the project will treat wastewater as an exempt facility, all or a portion of the bonds will be eligible for tax-exempt treatment under federal tax law.
“We appreciate FAME’s support for the agricultural component of this project,” said Greg Day, president of TDB LLC, developer of the project. “This master-planned program establishes a compelling business model for food production in an urban core that our firm is expanding to other communities throughout New England and the nation.”
Vertical Harvest plans to break ground on the facility in the fall. It's expected to be Maine’s first vertical farm, and the country’s second. The company’s first location in Jackson Hole, Wyo., was the first of its kind and has been operating for five years.
MedRhythms, Inc. will receive tax credit certificates related to approximately $2.8 million in investments through the Maine New Markets Capital Investment Program to help with the costs of a commercialization strategy of its device and software for stroke rehabilitation. The certificates authorize the issuance by the state of approximately $1.1 million in tax credits through the program.
“We are pleased to support MedRhythms’ plans to advance their digital therapeutic for stroke rehabilitation, as well as additional research and development,” said David Daigler, chair of the FAME board. “Digital therapeutics are a cutting-edge field that can help to improve the everyday lives of Mainers and other patients who will benefit from the company’s technology.”
MedRhythms uses sensors, music, and software to build solutions that measure and improve walking. The company, which currently employs 18 individuals, with 13 full-time employees in Maine, hopes to triple its workforce in the next few years.
“Digital therapeutics are the future of health care, and we appreciate the support of FAME,” said Brian Harris, CEO and founder of MedRhythms.
FAME uses tax-exempt private activity bonds, or “conduit bonds,” which are authorized by the Internal Revenue Code in order to stimulate economic development in certain targeted industries. The projects financed in recent years range from nonprofit health and higher education projects to solid waste improvements, public infrastructure and manufacturing.
Lead Photo: A 300,000-square-foot Westbrook building, shown in this rendering, is expected to house the Vertical Harvest indoor farm, as well as apartments, parking and commercial space.
Four Vertical Growers Collaborating To Deliver Social-Impact Projects in Wales
Four UK vertical farming companies, LettUs Grow, Digital Farming, Farm Urban and GrowStack, are collaborating to bring the benefits of CEA to Welsh communities
July 9, 2021
Four UK vertical farming companies, LettUs Grow, Digital Farming, Farm Urban, and GrowStack, are collaborating to bring the benefits of CEA to Welsh communities. This is one of the widest collaborations between leading CEA tech providers in the UK to date, with a focus on delivering vertical farms across different locations in Wales as part of a social impact and community-focused project called Crop Cycle.
Crop Cycle is looking to bring the benefits of vertical farming directly to communities that could benefit most and is being funded by the Welsh Government through the Foundational Economy Challenge Fund. The project is being led by Social Farms and Gardens, supported by Welsh Government's NutriWales CEA Special Interest Group and BIC Innovation.
The project enables multiple different CEA systems to be tailored to fit different community settings, whilst also allowing them to be assessed in coordination across the pilot sites. This approach is unique, facilitating the testing of new socially focused business models, the engagement of the local communities and businesses with CEA and the development of new technical solutions. LettUs Grow, Digital Farming, GrowStack and Farm Urban are working together to share their specialisms and apply different technologies to where they are best suited within four sites in Wales, two of which are in the Valleys.
This project will introduce year-round food growing right into the heart of Welsh communities, where they’ll be connected to the particular dynamics of the local area. Activities will test new community-based engagement models, focusing on social well-being, local entrepreneurship and environmental impact. In this way, the project will be bringing together community, businesses and local public sector organizations.
Gary Mitchell, the Wales Manager for Social Farms and Gardens who is leading the project team stated, "we are excited to be running the pilot project across a diverse set of sites to gain insight and further knowledge into how new agricultural systems can successfully support communities in delivering local, fresh and nutritious foods as well as important social benefits in a sustainable manner."
Read the complete article at: Vertical Farm Daily
For more information:
LettUs Grow
info@lettusgrow.com
lettusgrow.com
GrowStack
www.growstack.co.uk
Digital Farming
www.digitalfarming.io
Farm Urban
www.farmurban.co.uk
Ocado To Fund New Vertical Farm Near Bristol As Sales Leap
Ocado is planning to “assist” with the building of a vertical farm near Bristol, it has announced. The online grocer said it had invested £5 million in Lincolnshire-based Jones Food Company (JFC) as part of a wider £25 million raise
By Holly Williams, Hannah Baker, David Laister
July 6, 2021
Ocado is planning to “assist” with the building of a vertical farm near Bristol, it has announced.
The online grocer said it had invested £5 million in Lincolnshire-based Jones Food Company (JFC) as part of a wider £25 million raise.
The funding will be used to help JFC - Europe’s largest vertical farm - to build a second site outside the South West city.
Ocado said its original stake in the Scunthorpe business, which uses hydroponics and renewable energy to grow herbs and leafy greens, was now worth “more than double” its initial investment, made in mid 2019.
JFC launched in early 2018 with a 5,000 sq m farm in an adapted coldstore, with an entrepreneur and expert agronomist at the helm.
Initial harvests saw enough produce grown for 11 million sandwiches.
The announcement was made as Ocado posted its half-year results on Tuesday. The company said in the six months to May 30, losses narrowed sharply as sales surged.
But the company said shoppers had begun returning to some pre-pandemic habits due to easing restrictions.
Jones Food Company is an energy intensive business, and has partnered with Flexitricity to participate in demand side response for the National Grid. (Image: HLC Creative)
Ocado posted a £23.6m loss before tax over the period - down from losses of £40.6m a year earlier. Underlying earnings – the company’s preferred measure – rose 41% to £61m.
Ocado said revenues for its retail joint venture with Marks & Spencer jumped 19.8% higher in the first half to £1.2bn
This comes as a marked slowdown on the 39.7% sales rise notched up in the first quarter to February
The online grocer also said its first UK mini Customer Fulfilment Centre (CFC) in Avonmouth, near Bristol, was “ramping faster” than any facility before it.
Lead Photo: Ocado has invested millions into Scunthorpe vertical farming start-up Jones Food Company
Grōv Technologies Signs Definitive Agreement With Superior Farms
Agtech and indoor farming company, Grōv Technologies, today announced a definitive agreement with California-based Superior Farms for the purchase of 10 Olympus Tower Farms that will produce fresh year-round feed for Superior’s upcoming Sheep Discovery Center™ in Central Utah
July 12, 2021
Vineyard — Agtech and indoor farming company, Grōv Technologies, today announced a definitive agreement with California-based Superior Farms for the purchase of 10 Olympus Tower Farms that will produce fresh year-round feed for Superior’s upcoming Sheep Discovery Center™ in Central Utah. Grōv is part of Superior Farms’ efforts to dramatically improve the sustainability and growth of US lamb production.
The ten Olympus Tower Farms will produce 60,000 pounds of Grōv’s fresh High-Density Nutrient (HDN) Superfeed wheatgrass a day using less than 5 percent of the water needed for field-grown fodder, without the use of pesticides or herbicides.
The Sheep Discovery Center is a new venture of Superior Farms. The goal of the Discovery Center is to showcase how sustainably focused science and technology can help farmers increase their flocks and consistently produce high-quality lamb.
“Our collaboration with Superior showcases how Grōv indoor ag technology can benefit farmers who want to improve production and sustainability, and minimize risk, especially as it relates to drought conditions that plague regions across the world,” says Steve Lindsley, president of Grōv Technologies. “The innovative thinking of Superior Farms is right in line with our efforts to provide feed security for animals and food security for growing populations.”
Leveraging Grōv’s indoor Olympus Tower Farms to grow fresh HDN feed, Superior Farms intends to optimize nutrition and environmental conditions to help support animal health during the lambing cycle. Superior Farms will also implement Grōv’s seasonal lighting technology as part of Superior’s efforts to improve the productivity of their sheep and provide a more consistent lamb supply throughout the year.
“The current Western U.S. megadrought is pushing farmers to ration their natural resources and find innovative ways to give their animals a more sustainable and nutrient-rich environment,” says Rick Stott, CEO of Superior Farms. “Feeding sheep with Grōv HDN opens up new opportunities for sheep farmers and gives them a way to overcome the water issues affecting their flocks.”
During the Covid pandemic, more consumers tried lamb for the first time and continued to purchase it throughout the year. The US lamb industry expects demand to keep rising as the number of new consumers who are more familiar with lamb continues to grow.
For more information about Grōv Technologies please visit www.Grōvtech.com.
About Grōv Technologies, LLC
Grōv Technologies is pioneering next-generation indoor agriculture technology and science to help meet the demand for global food and animal feed security. The company has developed enterprise-scale, automated controlled environment agriculture (CEA) systems to grow high-density nutrient animal feed and other crops using significantly less water and resources than traditional farming. These systems utilize patented low-heat LED technology, seed-to-harvest robotics, and data-driven scientifically proven indoor growing protocols. Grōv also operates an LED lighting and power management subsidiary, Stellar Smart Energy Solutions, using proprietary Wave Power Transformation and power management networking technology for commercial and agricultural facilities. Grōv is wholly owned by Nu Skin Enterprises, Inc. (NYSE: NUS), which develops and distributes a comprehensive line of premium-quality beauty and wellness solutions through a global network of sales leaders.
About Superior Farms
Superior Farms, the leading purveyor of sustainably raised, ranch-to-table American lamb. Proudly providing the highest quality natural lamb for a variety of recipes from weeknight dinners to Sunday brunch, lunches, and more, Superior Farms offers a range of premium cuts. From the mountains of Utah, the brisk winters of Minnesota, and the shores of California, Superior Farms prides itself on working exclusively with family ranchers who raise lambs with the best care and commitment to quality wellbeing and stable environment. Respecting a nutrient-rich land, maintaining a sustainable footprint, and working with dedicated family ranchers who raise flocks with the highest level of care, all are core values that make Superior Farms the leader in American lamb. From the plant floor to the corner office, Superior Farms is also proud to be 100 percent owned by its dedicated and talented employees. For more information, visit www.superiorfarms.com, order home delivery at www.superior-farms.com, or follow the brand on Instagram (@SuperiorFarms) and Facebook (@SuperiorFarms).
An Action Plan To Ensure Food Security In Kashmir
In Kashmir valley, where most farmers own less than an acre of land, any Government policy related to land acquisition, especially for “development projects”, needs to take into account the fragile mountainous environment and climatic conditions as well. At a time when the agricultural land is shrinking day by day and population on rise, what is the future of agriculture in Jammu & Kashmir especially the Kashmir valley?
By Dr Raja Muzaffar Bhat
July 9, 2021
The majority of the farmers in Jammu and Kashmir are officially recognized as marginal farmers because of very small land holdings. The agricultural landholdings in J&K was estimated at 0.55 hectares during the agriculture census 2015-16, but unofficially this is much smaller (around 0.45 hectares ). In Kashmir valley, the size is even smaller. During the 2010-2011 agriculture census, the average size of operational land holdings in India was 1.15 hectares. This figure was lower, at 0.62 hectares in Jammu and Kashmir. Districts in Kashmir valley had even lower landholding sizes than the state as a whole. Kulgam 0.39 hectares Anantnag 0.39 , Shopian 0.56, Pulwama 0.48, Srinagar 0.31, Budgam 0.43, Baramulla 0.51, Ganderbal 0.37, Kupwara 0.51, Bandipora 0.48. These figures again came down during the 2015-16 census. I have written in detail about it in past.
In Kashmir valley, where most farmers own less than an acre of land, any Government policy related to land acquisition, especially for “development projects”, needs to take into account the fragile mountainous environment and climatic conditions as well. At a time when the agricultural land is shrinking day by day and population on rise, what is the future of agriculture in Jammu & Kashmir especially the Kashmir valley?
World population by 2040
The world's overall population is expected to increase by another 2 billion by 2040. Feeding such a large population will be the most challenging task ? Scientific studies show earth has lost one- fourth of its arable lands over the last
50 years only? India has a huge population. Urbanization and industrialization is shrinking its agricultural land. The Vertical farming is the solution to these challenges. This type of farming is an innovative way of maintaining our agricultural practices. In India, vertical farming is mostly polyhouse-based farming. Poly-house farming is a protected way that gives higher productivity and yield of vegetables and fruits across India. Increasing food demand due to a growing population along with ever decreasing arable lands poses one of the greatest challenges for us. Many believe that vertical farming can be the answer to this challenge. It is believed that vertical farming is the future of agriculture. For a place like Kashmir it is indeed the solution to ensure food security in future
What Is Vertical Farming ?
Vertical farming is the practice of producing food on vertically inclined surfaces. Instead of farming vegetables and other foods on a single level, such as in a field or a greenhouse, this method produces foods in vertically stacked layers commonly integrated into other structures like a skyscraper, shipping container or repurposed warehouse. Using Controlled Environment Agriculture (CEA) technology. This modern idea uses indoor farming techniques. The artificial control of temperature, light, humidity, and gases makes producing foods and medicine indoor possible. In many ways, vertical farming is similar to greenhouses where metal reflectors and artificial lighting augment natural sunlight. The primary goal of vertical farming is maximizing crops output in a limited space.
Firstly, the primary goal of vertical farming is producing more foods per square meter. To accomplish this goal, crops are cultivated in stacked layers in a tower life structure. Secondly, a perfect combination of natural and artificial lights is used to maintain the perfect light level in the room. Technologies such as rotating beds are used to improve lighting efficiency. Thirdly, instead of soil, aeroponic, aquaponic or hydroponic growing mediums are used. Peat moss or coconut husks and similar non-soil mediums are very common in vertical farming. Finally, the vertical farming method uses various sustainability features to offset the energy cost of farming. In fact, vertical farming uses 95% less water.
Vertical farming in J&K
As discussed above the agricultural land holding in Jammu & Kashmir is very less. The government is in the process of acquiring more and more agricultural land for highways and transmission lines. More than than 800 acres of highly fertile agriculture land is being acquired for the Srinagar Ring Semi Road project. Budgam alone is loosing more than 600 acres of vegetable, paddy and orchard land (4800 kanals). Right to Fair compensation act which is applicable in J&K post article 370 abrogation is not applied as the 2017 notification has become null and void due to efflux of time. Dozens of villages in Pulwama, Budgam, Srinagar and Ganderbal are affected by the land acquisition process for this project. We already lost a lot of agricultural land during construction of Qazigund – Baramulla railway line. Due to urbanization a lot of paddy fields were converted into housing colonies around Srinagar, Budgam and Ganderbal districts. Shopping malls, hospitals, schools have come up on agricultural land. Have we ever thought about our future generation ? Will people in Kashmir valley be able to grow vegetables or paddy in 2050 ? No not at all. What is the solution? Why are our agri –scientists and researchers not coming forward and guiding people on vertical farming?
Advantages of Vertical farming
Vertical farming has a lot of advantages. However, there are some challenges as well. The advantages are listed below :
Preparation for the Future:
In the next 30 to 35 years around 70 % of the world population is expected to live in urban areas, and the population growth will demand more food. The efficient use of vertical farming may perhaps play a significant role in facing such challenges.Year-Round Crop Production:
The vertical farming ensures to produce more crops from the same square footage of growing area. In fact, 1 acre (8 kanals) of an indoor area offers equivalent production to at least 4-6 acres of outdoor capacity. According to an estimate, a 30-story building with a base area of 5 acres can potentially produce an equivalent of 2,400 acres of conventional horizontal farming. Additionally, year-round crop production is possible in a controlled indoor environment which is completely controlled by vertical farming technologies. This is indeed a very useful technique for a place like Kashmir in view of shrinking farm lands and harsh winter months. Vertical farming allows us to produce crops with 70% to 95% less water than required for normal cultivation.
Production of Organic Crops:
As crops are produced in a well-controlled indoor environment without the use of chemical pesticides, vertical farming allows us to grow pesticide-free and organic crops. Indoor vertical farming can significantly lessen the occupational hazards associated with traditional farming. Farmers are not exposed to hazards related to heavy farming equipment, diseases like malaria, poisonous chemicals and so on. As it does not disturb animals and trees inland areas, it is good for biodiversity as well
Challenges
Difficulties with Pollination
Vertical farming takes place in a controlled environment without the presence of insects. As such, the pollination process needs to be done manually, which will be labor intensive and costly.
Labor Costs
As high as energy costs are in vertical farming, labour costs can be even higher due to their concentration in urban centers where wages are higher, as well as the need for more skilled labor. Automation in vertical farms, however, may lead to the need for fewer workers. Manual pollination may become one of the more labor-intensive functions in vertical farms.
Conclusion
The constant shrinking of agriculture land is a big challenge at global level as discussed above. For a place like Kashmir valley the shrinking of agricultural land due to urbanization and population growth will lead to food crises in future. Vertical farming is the only hope now and our agriculture scientists, universities and research institutions need to shift their focus on vertical farming....
Disclaimer: The views and opinions expressed in this article are the personal opinions of the author. The facts, analysis, assumptions and perspective appearing in the article do not reflect the views of GK.
Lead Photo: Why are our agri-scientists not coming forward, and guiding people on vertical farming?