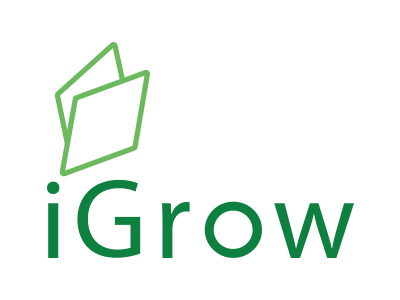
Welcome to iGrow News, Your Source for the World of Indoor Vertical Farming
Roto-Gro Set To Blast Into Space With Food Production System
Roto-Gro is capitalizing on the space exploration boom, as it applies to a NASA challenge developing novel food production technologies to feed astronauts on long-term missions
Advanced Agritech Company Roto-Gro International (ASX: RGI) Is Aiming To Feed The World’s Astronauts.
August 9, 2021
Roto-Gro is capitalizing on the space exploration boom, as it applies to a NASA challenge developing novel food production technologies to feed astronauts on long-term missions.
Advanced agritech company Roto-Gro International (ASX:RGI) is aiming to feed the world’s astronauts as it capitalizes on innovations in food production systems and a boom in space exploration.
Roto-Gro World Wide (Canada), a wholly-owned subsidiary of Roto-Gro International, has applied to the Deep Space Food Challenge as part of its first step into the space agriculture sector.
Administered under an international collaboration between National Aeronautics and the Space Administration (NASA) and the Canadian Space Agency (CSA), the international competition aims to incentivize the development of novel food production technologies needed for long-development space missions and terrestrial applications.
Roto-Gro’s application highlight’s the technological diversification and adaptability of its patented proprietary indoor vertical farming technology.
Astronauts’ food needs changing as missions evolve
Astronauts currently receive food from spacecrafts regularly launching from Earth, for example to the International Space Station.
However, NASA and the CSA recognize that as the distance and duration of space exploration missions increase, the current method of feeding astronauts will no longer be sustainable.
Future astronauts will be required to use food production systems on their voyages and be self-sustaining. The challenge aims to inspire the agricultural industry to help bring innovative food production technologies to space, reducing the need for resupply from earth and ensuring astronauts have continuous safe and nutritious food supplies.
The ability to develop sustainable food production is considered the crucial next step for longer-term human presence on the lunar surface and the future missions to Mars.
The challenge is not only about space exploration but also missions in extreme arid and resource-scarce environments on Earth. Like space, input efficiency will be key, including the efficient use of water and electricity to reduce resources needed for food production here on Earth.
Adapting Roto-Gro’s existing models key to space success
A new Roto-Gro rotational garden system — branded Roto-Gro Beyond Earth — will be designed with engineering adapted-off components from its existing Model 420 and Model 710 rotational garden systems.
Roto-Gro Beyond Earth will be a smaller, more portable version of the Model 420 but feature the injection feed system from the Model 710, significantly reducing the required resource inputs while maximizing nutritional outputs when compared to other indoor farming technologies.
Roto-Gro CEO Michael Di Tommaso said Roto-Gro Beyond Earth will enhance the already existing, unique benefits of its rotational garden systems, optimizing both the operational efficiencies and yield per m2, which is crucial to the development and prospective use of food production systems in space.
“The technology developed to form the application to the challenge is astoundingly demonstrating the vast applicability and sheer innovation of the company’s technology,” Di Tommaso said.
He said the company had developed several key relationships with organizations currently providing food system solutions for long-duration space voyages, along with others focused on using space to solve problems we are experiencing on earth.
“We look to develop and foster these relationships moving forward, further strengthening our position in the sector,” Di Tommaso said.
He said entering the space agricultural sector was a natural progression for Roto-Gro, supporting its vision to provide sustainable technological solutions for agricultural cultivation, critical to ensuring global food security.
“Food system innovation is crucial to our progression in space, and we are excited with the prospect of moving to the next phase of the Deep Space Food Challenge, while also generating other opportunities to develop and implement Roto-Gro’s technology in the industry,” Di Tommaso said.
Roto-Gro global forecasts international growth
Established in 2015, Roto-Gro is continuing to attract interest on a global scale.
The company recently partnered with agriculture company Verity Greens Inc. who has signed a binding $10M Technology License to purchase 624 RotoGro Model 710 rotational garden systems, with the first, flagship indoor vertical farming facility to be built in Canada.
The deal is expected to generate long-term, sustained recurring revenue with Di Tommaso hailing it as not only a “win-win” for both companies but a venture that works on a socially responsible level by helping tackle global food shortages.
“RotoGro will introduce our revolutionary technology into the booming indoor vertical farming space, while Verity Greens, utilizing the RotoGro Garden Systems and supporting technology, will operate with a viable and cost-effective competitive advantage,” he said.
“Verity Green’s first facility also serves to further its objectives – to roll out indoor vertical farming facilities globally utilizing RotoGro’s technology, not only to generate substantial revenue for both companies but also to provide a truly sustainable solution to address the issues caused by food insecurity.”
Lead photo: Pic: Giphy
This article was developed in collaboration with Roto-Gro International, a Stockhead advertiser at the time of publishing.
This article does not constitute financial product advice. You should consider obtaining independent advice before making any financial decisions.
What’s Real And What’s Hype With Controlled Environment Agriculture?
The flourishing development of Controlled Environment Agriculture and how retailers and consumers view this emerging segment of fresh produce production will be the topic of an educational session at Organic Produce Summit 2021.
July 27, 2021
The flourishing development of Controlled Environment Agriculture and how retailers and consumers view this emerging segment of fresh produce production will be the topic of an educational session at Organic Produce Summit 2021. The Growth of CEA—What’s Real and What’s Hype from a Retail and Consumer Perspective will feature leadership from a pair of recognized retailers and one of the fresh produce industry’s most progressive grower-shippers, offering their insight on how indoor-grown fresh produce items come to market, pricing and marketing challenges, and how consumers are reacting to them.
Moderated by Walter Robb, former CEO of Whole Foods, the session is the second of a two-part educational series at OPS offering a retailer and consumer perspective on the growth of indoor growing. Among the topics to be discussed in the session are the impact of indoor-grown products on the supply chain, the messaging and labeling of these various items, and the ramifications of what CEA production means for the organic fresh produce industry.
Panelists for the session include Frances Dillard, vice president of brand and product marketing at Driscoll’s; Victor Savanello, vice president produce and floral at Spartan Nash; and Shawn Peery, vice president produce and floral at Albertsons.
Production of fresh produce in CEA has become a $100 billion-plus industry, showcasing how growing indoors uses less water and no pesticides, while incorporating innovative and efficient technologies to provide fresher produce to consumers. “CEA is changing the landscape of food production and providing consumers a variety of new items that will continue to evolve in the years ahead,” said Susan Canales, president of Organic Produce Summit. “OPS attendees will have the chance to hear from retail leadership on how these products are marketed and learn about the challenges and opportunities these new items offer consumers.”
This second educational workshop follows a session exploring the growth of CEA from leaders actively involved in the production of indoor growing. The panelists for the first session include Philip Karp, president of Shenandoah Growers; Marc Oshima, co-founder of AeroFarms; and Caitlin Tierney, director of business development for Mastronardi Produce.
“Indoor agriculture is increasingly playing a more meaningful role in our fresh produce supply, in terms of volume, variety, and geographical footprint,” said Robb. “The ability of indoor ag to provide predictability and resiliency for supply, coupled with its lower impact on both the environment and resource use, is drawing substantial interest from both investors and consumers. Clearly, the future will be a hybrid one and our panels will explore how quickly and responsibly this will happen.”
Organic Produce Summit 2021 is a live and in-person two-day event specifically designed to bring together organic fresh produce growers, shippers, and processors with retailer and buying organizations from across North America. Over 1,000 attendees will meet Sept. 15-16 in Monterey, CA, to exchange ideas, information and insights into the organic fresh produce industry.
In addition to the educational sessions focused on CEA, a session looking at the organic industry in a post-COVID-19 environment and a keynote presentation by Jim Donald, co-chairman of Albertsons, have also been announced. OPS 2021 also includes a selection of field tours for retailers and buyers, a gala opening night reception, and a sold-out trade show floor featuring over 150 producers and processors of organic fresh produce from across North America and the globe.
iUNU Meets U.S. House Agriculture Committee & Highlights Importance of CEA To U.S. Food Supply
Chairman David Scott (GA) held a Congressional Hearing Thursday morning to increase public awareness of the critical importance of the CEA (Controlled Environment Agriculture) industry to promote food safety, nutritious produce, and food security for the American people
Chairman David Scott (GA) held a Congressional Hearing Thursday morning to increase public awareness of the critical importance of the CEA (Controlled Environment Agriculture) industry to promote food safety, nutritious produce, and food security for the American people.
Adam Greenberg | CEO | IUNU LLC
“While a global pandemic certainly magnified our food supply chain issues, one of the issues we can cover today is how to ensure a supply of fresh fruits and vegetables from all sources,” Chairman Scott asserted in his opening statement. “Controlled environment agriculture has the ability to fill in gaps where there are food deserts, reduce emissions from transportation of produce, and very importantly, limit our reliance on imports to fill our needs for fresh produce. We have an opportunity today to be on the cutting edge of technologies and the ability to provide affordable food to more households that need it.”
iUNU, an AI and computer vision-based technology platform that is employed by large commercial growers to enhance productivity is working with Congress and the USDA to ensure nutritious produce is available to all Americans.
“iUNU is an integral part of the solution to these issues as the leading provider of Artificial Intelligence and machine learning to help indoor growers rapidly expand their operations,” stated CEO Adam Greenberg at the Hearing. “The fact that 87% of the imported tomatoes come from one country, Mexico, leaves the U.S. population highly susceptible to food insecurity whether it is from a pandemic or other forces we can’t control. The CEA industry can significantly reduce these risks.”
Representative Jim McGovern (MA) expressed deep concerns about the need to recognize that food security is a national security issue in terms of ensuring the availability of healthy, nutritious produce for all Americans. “Every child in America deserves fresh, nutritious, contaminant-free fruits and vegetables they can trust.”
iUNU provides indoor growers with an AI and machine learning technology that gives growers the ability to see a plant from the time it sprouts until the time it is harvested in real-time.
“Our LUNA system can see where a problem is when it is happening and what is causing it, which significantly reduces the time it takes to identify any potential outbreak,” Mr. Greenberg said. “By catching a pest or pathogen issue as early as possible, we help growers reduce the need for pesticides. In short, we help reduce a grower’s risks and increase their productivity.”
Representative Jim Costa (CA) reiterated his concern with the nation’s food supply. “The sustainability of our food supply is critical,” he stated. “Focusing on protecting America's food supply chain is a national security issue. We need to focus on innovation as we move forward.”
Later in the afternoon, both Chairman Scott (GA) and Ranking Member Thompson (PA) issued a joint statement urging Congress to address the expansion of Broadband Internet so Americans living in rural areas and food deserts will have the same access as those living in urban areas. The lack of access hampers the ability of businesses such as growers to optimize their facilities through the use of AI and computer vision.
How To Maximize Resource Efficiency In Controlled Environment Ag Operations
Join Meena Sankara, KETOS CEO, and Tinia Pina, Re-Nuble CEO, for a discussion about the most significant challenges and opportunities facing Controlled Environment Agriculture operations
Tuesday, August 3 @ 12:30 pm ET / 9:30 am PT
Wednesday, August 4 @ 9:00 am ET / 1 pm GMT
Meena Sankara, KETOS CEO
Join Meena Sankara, KETOS CEO, and Tinia Pina, Re-Nuble CEO, for a discussion about the most significant challenges and opportunities facing Controlled Environment Agriculture operations. In this webinar you will learn:
Tinia Pina, Re-Nuble CEO
Why water management is important in the CEA industry
Challenges soilless/indoor farms face when improving water management efficiency
How soilless operations (including vertical farms and greenhouses) can be more resource-efficient
Strategies for the nutrient wastewater recovery
Which waste recovery solutions are best for your operation
August 3rd Webinar Registration
August 4th Webinar Registration
Optimizing Resource Use Efficiency In CEA System
An important factor affecting the profitability of vertical farming is a grower’s ability to consistently deliver a predictable product
Date: July 29, 2021
Time: 2 p.m. - 3 p.m. EDT
Presented by: Murat Kacira (The University of Arizona)
Click Here To Register
Webinar Description
An important factor affecting the profitability of vertical farming is a grower’s ability to consistently deliver a predictable product. To achieve this, growers must create an environment that supplies all the crop’s needs over its entire growth cycle by identifying and co-optimizing environmental variables such as CO2, light, humidity, airflow, and other parameters. This presentation will focus on real-time sensing, monitoring, and climate control strategies with system designs for environmental uniformity leading to enhanced resource use efficiency in CEA system.
Dr. Murat Kacira (Professor)
Murat Kacira is director of the Controlled Environment Agriculture Center and he is a professor in the Biosystems Engineering Department at the University of Arizona. He received his B.S. degree in Agricultural Engineering in Cukurova University in Turkey and M.Sc. and Ph.D. degrees from Food, Agricultural and Biological Engineering from The Ohio State University in USA. His research involves automation, environmental control, alternative energy integrated CEA systems and resource use optimization in controlled environment agriculture systems including greenhouses and vertical farming-based plant factories with artificial lighting. He is a member of American Society of Agricultural and Biological Engineers (ASABE), American Society of Horticultural Sciences (ASHS), and International Society for Horticultural Science (ISHS). He serves as Chair of the Division Precision Horticulture Engineering under ISHS.
Special thanks to our Industry partners
Join Today
If you have any questions or would like to know more about GLASE, please contact its executive director Erico Mattos at em796@cornell.edu
Contain Inc Announces Finance Arrangement With Edible Beats For FarmBox Foods Container Farm
The container farm is being built and customized for Edible Beats, and will produce ingredients for all of the EB concepts, Linger, Root Down, Vital Root, El Five, and Ophelais
NEWS PROVIDED BY
July 07, 2021
Contain Inc announces a financing agreement arranged between Edible Beats Restaurant Group & a prominent lender for a FarmBox Foods container farm.
Image courtesy of FarmBox Foods
With the FarmBox Food container, we can grow hyper-local, organic, year-round produce that will be featured at all of our restaurants. We feel this is just the beginning of what we can grow”— Justin Cucci of Edible Beats Restaurant Group
RENO, NV, UNITED STATES, July 7, 2021 /EINPresswire.com/ -- Contain Inc is pleased to announce a financing agreement arranged between Edible Beats Restaurant Group and a prominent lender for a controlled-environment container farm, FarmBox Foods. Edible Beats is a locally owned Denver-based restaurant group known for its diverse menus and healthy, plant-based dishes that highlight local and seasonal ingredients. Edible Beats will be able to grow herbs, leafy greens, salad greens, and various produce organically and year-round with the container farm that will be attached to their Vital Root location.
“We have always sought opportunities to be more responsible to the sourcing, growing, and handling of the incredible ingredients that we get,” said Justin Cucci of Edible Beats Restaurant Group. “With the FarmBox Food container, we can grow hyper-local, organic, year-round produce that will be featured at all of our restaurants. We feel this is just the beginning of what we can grow, and we are eager to add the mushroom grow operation in the future”
Image courtesy of Unsplash
Edible Beats purchased the container from FarmBox Foods, a Colorado-based company that builds automated farms that grow gourmet mushrooms, leafy greens, and culinary herbs. To FarmBox, controlled-environment agriculture is the future, and this deal is one of many leading us towards a more decentralized and eco-friendly food system.
“I think we’re going to see a lot more of these types of programs going forward,” said Chris Michlewicz, Chief Public Relations Officer at FarmBox. “Restaurants are realizing that their produce is fresher and has a longer shelf life when they have a container farm on site. It’s a reliable and sustainable source of food, and it’s more eco-friendly because you no longer have to transport food in from elsewhere.”
Image courtesy of Unsplash
Likewise, Contain Inc is thrilled to support Edible Beats as it ventures into indoor ag. “We're delighted to have assisted SemiMojo and FarmBox Foods in this innovative initiative. Contain is always excited to see more fresh food made available to consumers. Customers appreciate freshness and quality produce, year round. Restaurants and container farms make this possible”, said Doug Harding, Head of Leasing & Vendor Relations at Contain Inc. “We are thrilled to have collaborated with Edible Beets and Farm Box Foods on this project. It aligns perfectly with Contain's mission of supporting the controlled environment agriculture industry in its financing needs”.
The container farm is being built and customized for Edible Beats, and will produce ingredients for all of the EB concepts, Linger, Root Down, Vital Root, El Five, and Ophelais.
About Contain Inc
Contain is out to empower the indoor ag industry of tomorrow. Our first and key mission is bringing easier and faster financing to controlled environment agriculture, but we aren't stopping there. We create platforms to move the industry forward, and most importantly, find ways to make indoor ag more accessible to farmers of all stripes.
Contact Contain:
Doug Harding, Leasing & Vendor Relations
doug@contain.ag | 760-330-1199
About Edible Beats
Edible Beats is a locally owned independent restaurant group that operates such diverse concepts as Linger, Root Down, El Five, Ophelais, and Vital Root. “Walking the walk” is important to us and the various aspects of sustainable & local food sourcing, up-cycled design, and authentic Hospitality.
About FarmBox Foods
FarmBox Foods was founded to help provide a sustainable, eco-friendly food source to places where there is a lack of access to farm-fresh produce. The company’s mission is to use container farms to decentralize the food supply chain and empower local communities.
Doug Harding
Contain Inc
doug@contain.ag
Visit us on social media:
Twitter
LinkedIn
Vertical Farming World To Meet In September
With the theme of ‘Raising Expectations’, the 2nd Vertical Farming World Congress will host industry members, from global leaders to new start-ups, on 20-22 September at a hybrid event online as well as in-person
With the theme of ‘Raising Expectations’, the 2nd Vertical Farming World Congress will host industry members, from global leaders to new start-ups, on 20-22 September at a hybrid event online as well as in person.
“This will be the most substantial dedicated event of the year, featuring many of the world’s leading companies and technologies, offering unparalleled networking opportunities as well as training for new entrants,” commented Richard Hall, Chairman of event organiser Zenith Global.
“We’re hoping as many people as possible will attend in person, so we’ve selected a hotel within the London Heathrow airport complex. Many others will wish to join us online, using a platform that allows for full participation including networking and questions. One advantage for everyone is that all sessions will be recorded and available for review later,” he concluded.
Congress sessions and speakers include:
Industry leadership panel with InFarm, Kalera, Plenty and YesHealth
Market opportunity and strategy with HortAmericas, Rabobank, VeggiTech and Vertical Future
Crop and technology innovation with 80 Acres, Bowery, Fork Farms, Grow Group IFS, Swegreen
and Vertical Field
Science briefing from NASA on vegetable production at the International Space Station
Industry policy forum with industry associations from Africa, Japan, UK and US alongside
Association for Vertical Farming and Farm Tech Society
Regional pioneers AgroUrbana from Chile, UrbanKisaan from India and 808 Factory from Japan
Customer and investor panels.
Other highlights include:
Agritecture workshops on planning an urban farming business
Vertical Future farm visit and fresh produce tasting
Presentation of 2021 Vertical Farming World Awards
Welcome and networking receptions.
The event is supported by Platinum sponsors Vertical Future and Intelligent Growth Solutions, and Gold sponsor CubicFarms. The awards are supported by Headline sponsor Cutlivatd.
Full programme and booking details are available on www.zenithglobal.com/events/vfwc2021.
For further information, email events@zenithglobal.com
No Soil. No Growing Seasons. Just Add Water And Technology
A New Breed of Hydroponic Farm, Huge And High-tech, is Popping Up in Indoor Spaces All Over America, Drawing Celebrity Investors And Critics
A New Breed of Hydroponic Farm, Huge And High-tech, is Popping Up in Indoor Spaces All Over America, Drawing Celebrity Investors And Critics.
By Kim Severson
July 6, 2021
MOREHEAD, Ky. — In this pretty town on the edge of coal country, a high-tech greenhouse so large it could cover 50 football fields glows with the pinks and yellows of 30,600 LED and high-pressure sodium lights.
Inside, without a teaspoon of soil, nearly 3 million pounds of beefsteak tomatoes grow on 45-feet-high vines whose roots are bathed in nutrient-enhanced rainwater. Other vines hold thousands of small, juicy snacking tomatoes with enough tang to impress Martha Stewart, who is on the board of AppHarvest, a start-up that harvested its first crop here in January and plans to open 11 more indoor farms in Appalachia by 2025.
In a much more industrial setting near the Hackensack River in Kearny, N.J., trays filled with sweet baby butterhead lettuce and sorrel that tastes of lemon and green apple are stacked high in a windowless warehouse — what is known as a vertical farm. Bowery, the largest vertical-farming company in the United States, manipulates light, humidity, temperature, and other conditions to grow produce, bankrolled by investors like Justin Timberlake, Natalie Portman, and the chefs José Andrés and Tom Colicchio.
“Once I tasted the arugula, I was sold,” said Mr. Colicchio, who for years rolled his eyes at people who claimed to grow delicious hydroponic produce. “It was so spicy and so vibrant, it just blew me away.”
The tomatoes at AppHarvest were delicious enough to attract an investment from Martha Stewart.Credit...Luke Sharrett for The New York Times
The two operations are part of a new generation of hydroponic farms that create precise growing conditions using technological advances like machine-learning algorithms, data analytics and proprietary software systems to coax customized flavors and textures from fruits and vegetables. And they can do it almost anywhere.
These farms arrive at a pivotal moment, as swaths of the country wither in the heat and drought of climate change, abetted in part by certain forms of agriculture. The demand for locally grown food has never been stronger, and the pandemic has shown many people that the food supply chain isn’t as resilient as they thought.
But not everyone is on board. These huge farms grow produce in nutrient-rich water, not the healthy soil that many people believe is at the heart of both deliciousness and nutrition. They can consume vast amounts of electricity. Their most ardent opponents say the claims being made for hydroponics are misleading and even dangerous.
“At the moment, I would say the bad guys are winning,” said Dave Chapman, a Vermont farmer and the executive director of the Real Organic Project. “Hydroponic production is not growing because it produces healthier food. It’s growing because of the money. Anyone who frames this as food for the people or the environment is just lying.”
The sprawling Kentucky farm is one of a dozen that AppHarvest hopes to open across Appalachia.Credit...Luke Sharrett for The New York Times
The technical term for hydroponic farming is controlled environmental agriculture, but people in the business refer to it as indoor farming. What used to be simply called farms are now referred to as land-based farms or open-field agriculture.
“We’ve perfected mother nature indoors through that perfect combination of science and technology married with farming,” said Daniel Malechuk, the chief executive of Kalera, a company that sells whole lettuces, with the roots intact, in plastic clamshells for about the same price as other prewashed lettuce.
In March, the company opened a 77,000-square-foot facility south of Atlanta that can produce more than 10 million heads of lettuce a year. Similar indoor farms are coming to Houston, Denver, Seattle, Honolulu, and St. Paul, Minn.
The beauty of the process, Mr. Malechuk, and other executives say, is that it isn’t limited by seasons. The cost and growing period for a crop can be predicted precisely and farms can be built wherever people need fresh produce.
“We can grow in the Antarctic,” he said. “We can be on an island. We can be on the moon or in the space station.”
That’s easy to picture: The farms are staffed by a new breed of young farmers who wear lab coats instead of overalls and prefer computers to tractors.
Today, the more than 2,300 farms growing hydroponic crops in the United States make up only a sliver of the country’s $5.2 billion fruit and vegetable market. But investors enamored of smart agriculture are betting heavily on them.
Lettuces at a Kalera vertical farm destined for nutrient-filled water begin in small plugs of growing medium.
Credit...Courtesy of Kalera
In 2020, $929 million poured into U.S. indoor-farming ventures, more than double the investments in 2019, according to PitchBook data. Grocery chains and California’s biggest berry growers are partnering with vertical farms, too.
“There is no question we are reinventing farming, but what we are doing is reinventing the fresh-food supply chain,” said Irving Fain, the founder, and chief executive of Bowery, which is based in Manhattan and has the indoor farm in New Jersey and one in Maryland, another under construction in Pennsylvania, and two research farms in New Jersey.
Mr. Fain said his farms are 100 times as productive as traditional ones and use 95 percent less water. Other companies claim they can grow as much food on a single acre as a traditional farm can grow on 390.
Vertical farms can be built next to urban centers, so lettuce, for example, doesn’t have to sit inside a truck for days as it makes its way from California to the East Coast, losing both quality and nutritional value. Vegetables can be bred for flavor rather than storage and yield.
The new systems are designed to produce a sanitary crop, grown without pesticides in hygienic buildings monitored by computers, so there is little risk of contamination from bacteria like E. coli, which forced large recalls of romaine lettuce in 2019 and 2020.
Bowery, the largest vertical-farm company in the United States, is growing hydroponic vegetables that have attracted the attention of chefs. Credit...Brian Fraser for The New York Times
Still, many farmers and scientists remain unpersuaded. Mr. Chapman, of the Real Organic Project, served on a U.S. Department of Agriculture hydroponics task force five years ago, and is leading an effort to get the agency to stop allowing hydroponic farmers to certify their produce as organic. The very definition of organic farming, he and others say, rests on building healthy soil. In May, the Center for Food Safety, an environmental advocacy group, led an appeal of a federal court ruling that upheld the agency’s policy.
Although the nutritional profile of hydroponic produce continues to improve, no one yet knows what kind of long-term health impact fruits and vegetables grown without soil will have. No matter how many nutrients indoor farmers put into the water, critics insist that indoor farms can never match the taste and nutritional value, or provide the environmental advantages, that come from the marriage of sun, a healthy soil microbiome, and plant biology found on well-run organic farms.
“What will the health outcomes be in two generations?” Mr. Chapman asked. “It’s a huge live experiment, and we are the rats.”
The divide between soil loyalists and ag-tech futurists is playing out on a much more intimate scale between two influential brothers: Dan and David Barber, who founded and own the organic farm Blue Hill and its restaurants in Greenwich Village and at Stone Barns in Pocantico Hills, N.Y.
In 2018, David Barber created an investment fund to support new food tech companies, including Bowery. But Dan Barber, a chef whose 2014 book “The Third Plate: Field Notes on the Future of Food” devotes an entire section to soil, believes that truly delicious food can come only from the earth.
“I am not buying any of it,” Dan Barber said of the hydroponic fever.
The chef Dan Barber, a soil loyalist, is skeptical of the claims made for hydroponic farms.
Credit...James Estrin/The New York Times
Trying to enhance water with nutrients to mimic what soil does is virtually impossible, he said, in part because no one really knows how the soil microbiome works.
“We know more about the stars and the sky than we do about soil,” he said. “We don’t know a lot about nutrition, actually.”
There is a cultural cost, too. For centuries, cuisines have been developed based on what the land and the plants demanded, he said. Regional Mexican diets built on corn and beans came about because farmers realized that beans fixed nitrogen in soil, and corn used it to grow strong.
“The tech-farming revolution is turning this equation on its head,” Mr. Barber said. It aids efficiency in the name of feeding more people but divorces food from nature.
His brother, David, had long been skeptical of hydroponics, too. “Most of my career was about good soil leads to good agriculture and good systems and ultimately good flavor,” David Barber said.
But the environmental advantages of next-generation hydroponic food production can’t be ignored, he said. Nor can the improvements in taste over earlier hydroponic produce. “They are combining outdoor and indoor thinking, and science and history, to create something special,” he said. “There are not going to be many winners in this space, but it is going to be a part of our food system.”
At Bowery, “there is no question we are reinventing farming, but what we are doing is reinventing the fresh-food supply chain,” said Irving Fain, its founder, and chief executive. Credit...Brian Fraser for The New York Times
Indoor farm companies view their competition as the large, industrial growers that produce fruits and vegetables bred to withstand processing and shipping — not smaller farmers using more natural growing techniques. The battle, they say, is against monoculture, not farmers who maintain healthy soil and feed their communities. Hydroponic farms can help develop new and more diverse plants, and reduce overall pesticide use.
“The only thing we are trying to do is get as good as farmers were 100 years ago,” said Mr. Malechuk, the hydroponic lettuce grower.
Indoor farming is a bet on the nation's agriculture, said Jonathan Webb, the Kentucky-born founder and chief executive of AppHarvest.
“The American farmer is already obsolete,” he said, pointing out that the United States imports four billion pounds of tomatoes from Mexico every year. “Our hope is we can get farmers back on U.S. shelves.”
Even Mr. Colicchio, who led a campaign against genetically modified food and has long been a champion of small farmers, said the two styles of farming can coexist. “We’re going to need a lot of tools in the toolbox,” he said.
Ouita Michel, a chef in Kentucky, likes AppHarvest because the company is creating jobs and growing tomatoes she is happy to use in her restaurants.
But technology, she said, will never trump the magic of soil. “Nothing will ever replace my summer Kentucky tomatoes.”
Lead photo: AppHarvest, the nation’s largest hydroponic greenhouse, opened in January in Morehead, Ky. — one in a new breed of huge indoor produce farms that use technology to fine-tune flavor, texture, and other attributes. Credit...Luke Sharrett for The New York Times
Sweden: Opening of New In-Store Vertical Farm At ICA Maxi
The opening event of the in-store vertical farm, a service provided and managed by Swedish technology company Swegreen, gained lots of traction from surprised and sometimes confused shoppers.
“We are actually making a difference here, because we grow next to the consumer, literally,” says Andreas Dahlin, CEO of Swegreen. “There are still many vertical farms that claim to produce sustainable, located close to the consumer, but they don’t mention the last mile. If logistics are needed to get the product to the consumer, they can still make a much bigger difference. That’s why we think this hyper-local model really makes an impact in the supply chain.”
It was all laughs and surprised faces during the opening at the ICA Maxi supermarket in Linköping this week. The opening event of the in-store vertical farm, a service provided and managed by Swedish technology company Swegreen, gained lots of traction from surprised and sometimes confused shoppers. Andreas opened the event by giving a toast to invitees. After explaining the concept, the crowd was allowed a visit to the farm.
Andreas leading the tour. Photo credit: Vertical farm daily.
Click here to view the photo report.
Biggest in Sweden
After successfully launching an in-store farm at ICA Focus, Gothenburg late 2020, the Swedish, fast-growing vertical farming enterprise Swegreen is now rolling out its Farming-as-a-Service concept in Scandinavia. First to get the installation in place is Ica Maxi in Linköping. The 60m2 farm supplies 10 different lettuces and herbs to the store – and more sorts are coming up – which makes this in-store growing facility the biggest in Sweden. Another share of the crops will be used in the store's own kitchen. Every day, several hundreds of crops are harvested that will end up on the shelves very soon after that.
Andreas adds, “The excessive heat from the farm is brought into the supermarket to optimally use all energy of the farm. We’re constantly looking at how we can optimize the cultivation processes up to energy use.”
Andreas explaining on vertical technologies. Photo credit: Verticalfarmdaily.
Full control
All technology is supplied and developed by Swegreen, such as the cultivation room and the AI-based control system which controls and optimizes the environment remotely. The farm is fully equipped with sensors, taking a huge relief off the farm operator who normally visits the facility 3-4 hours a day. Robot arms enable the gutters to be automatically moved from the beginning to the end-stage.
All processes are done on the farm, from seeding, breeding, cultivation and harvesting to packing the products. Everything in the farm is visible to the naked eye of store visitors.
Sepehr Mousavi, Chief Innovation Officer, and Innovation Lead at Swegreen explains that all technology is automated. “We can prevent any kind of error in the farm because the sensors will notify our technical services team immediately if something goes wrong to prevent any downtime.”
Click here to view the photo report.
Lead photo: Photo report: Swegreen launches event to celebrate project launch
For more information:
Swegreen
Andreas Dahlin, CEO of Swegreen
andreas.dahlin@swegreen.se
www.swegreen.se
Publication date: Wed 16 Jun 2021
Author: Rebekka Boekhout
© FreshPlaza.com
Certhon Wraps Up 7th Raspberry Trial Successfully
After successfully growing strawberries in the Certhon Innovation Centre (CIC), the company has decided to take on another trial of growing fruits indoors.
“Raspberry isn’t the first crop that comes to mind when figuring out which crops to grow indoors,” Andrea Huegler, R&D Engineer and Agronomist at Certhon said. “However, we accepted the challenge and decided to go for it as there are a lot of benefits to growing it in a controlled environment.”
After successfully growing strawberries in the Certhon Innovation Centre (CIC), the company has decided to take on another trial of growing fruits indoors. Certhon has been doing lots of research on indoor farming for a long time now. This has allowed them to investigate how to grow more complex crops in a controlled environment without daylight.
Andrea Huegler
Trial results
The main advantage of growing this crop indoors is having higher yields and consistent quality year-round. Certhon sees great opportunities ahead for the crop, due to its premium status and short shelf life. “It makes it a perfect candidate to be grown indoors.” During this trial, common raspberry cultivars were chosen. Certhon used chilled raspberry canes from a propagator, pollination by bumblebees and top and interlighting was used to flourish the crops. The harvesting period comprises 10 weeks, out of a total cultivation cycle of 21 weeks and is expected to end in July 2021.
Cultivation risks
The research was mainly about investigating the right transition of the vegetative state of the crop to the generative state. Andrea says that balancing the climate and light with energy consumption is the trickiest part here. “Ever since the first raspberry trial we’ve been trying to balance out the reduction of energy use, having an X amount of yield at a great quality and extending the harvesting period. Throughout the trials, we have obtained nearly twice as much yield compared to the traditional Dutch polytunnel producers in the summer,” Andrea notes.
However, raspberry cultivation isn’t without challenges. “One of the risks that could come up is growing grey mold,” explains Andrea. “If nectar isn’t removed well from the flower, the fruit can grow mold or have a grey undertone. However, if you manage your humidity wisely, the incidence is severely reduced. That’s the idea behind the CIC, optimizing growing recipes and eventually expanding the product portfolio because we want to provide a wide selection of product options to our clients.”
Greenhouse application
The knowledge that is generated in the CIC can also be applied to the cultivation of raspberries in greenhouses. Growing these crops indoors allows Certhon to generate ideal growing conditions and maximum potential for raspberry cultivation. With this knowledge, Certhon generates a blueprint that growers can follow in greenhouse cultivation as well.
Andrea explains, “For instance, the blueprint can be followed when growers want to know when to: provide extra lighting, shading, or adjust the humidity. In this way, ideal growing conditions can be mimicked to achieve the highest quality and yield possible in a greenhouse.”
Cane risk
Another, very important aspect is the quality of the raspberry canes. In order to have good production, your raspberry canes need to be of good quality and pest-free. “This cannot always be guaranteed, '' says Andrea, “since they are propagated outdoors and therefore bound to the pressures of external influences, such as climate. Although we have not tried it ourselves yet, we think the next step is to also propagate raspberry canes in a controlled environment without daylight.”
For more information:
Andrea Huegler, R&D Engineer and Agronomist
Certhon
andrea.huegler@certhon.com
ABC Westland 555
P.O. Box 90
2685 ZH Poeldijk
The Netherlands
Tel: +31 174 22 50 80
www.certhon.com
Publication date: Mon 7 Jun 2021
Author: Rebekka Boekhout
© HortiDaily.com
CEA Food Safety Coalition Details First Indoor-Farming Standards
Inspired by rising food safety concerns after the 2018 Thanksgiving romaine recalls, the CEA Food Safety Coalition is launching the first-ever food safety certification program specifically designed for indoor-grown leafy greens.
By AMY SOWDER June 2, 2021
(Photos courtesy CEA Food Safety Coalition)
Inspired by rising food safety concerns after the 2018 Thanksgiving romaine recalls, the CEA Food Safety Coalition is launching the first-ever food safety certification program specifically designed for indoor-grown leafy greens.
“The new standard champions CEA-grown produce as a critical component of safe and secure domestic food supply, especially in times of business disruption as experienced during the COVID-19 pandemic,” Marni Karlin, executive director of the CEA Food Safety Coalition, said in a news release.
Controlled Environment Agriculture, or CEA, has exploded with investment and sales the last few years, as more urban, indoor farms crop up to meet demand.
Soon after organizing in 2019, the coalition educated the Centers for Disease Control and Prevention and Food and Drug Administration about the limited risk of contamination from indoor-produced leafy greens, Karlin said.
“During the Thanksgiving 2019 romaine recall, those government agencies were transparent that CEA leafy greens were safe and did not extend the recall to them. This enabled retailers to keep CEA-produced greens on the shelves and consumers to safely buy CEA leafy greens for their families,” she said in the release.
The team had to create a standard that made sense across the board for the variety of production processes included in CEA — from greenhouses and vertical farming to aeroponic, hydroponic and aquaponic.
“Current food safety standards were written for the field, and many don't adequately address the unique attributes of controlled indoor environments,” Karlin said in the release. “Traditional food-safety risk profiles associated with conventional farming include examining the physical hazards and microbial hazards from water use, herbicide, and pesticide use, and impact from animals and animal byproducts. These do not impact CEA growers in the same way, if at all.”
As a result, a separate set of guidelines is needed.
This new certification process and the accompanying on-pack seal will spread awareness about CEA and unify these growers while differentiating them from traditional field growers, she said.
“It will allow producers to adhere to a standard tailored to indoor production and give incoming entrepreneurs guidance on the measures they'll need to meet to align with the existing industry,” Karlin said in the release.
The certification program is available to all CEA food safety coalition members for a small fee, and an external audit to the standard must be completed on an annual basis.
Growers are assessed across four key areas:
Hazard analysis: All potential hazards associated with a producer’s practices, including use of water, nutrients, growing media, seeds, inputs, and site control;
Water: Often used by CEA producers, recirculated water requires a continuing hazard analysis throughout its life cycle and zone-based environmental monitoring based on company-specific risk assessment, she said;
Site control: All food contact surfaces and adjacent food contact surfaces, including plant containers, must be considered and associated with potential farm physical hazards, including lighting, robotics, sensors, equipment, and utensils; and
Pesticide and herbicide use: Even though CEA-produced greens generally don’t use pesticides or herbicides, this module evaluates the potential risk of pesticide contamination and addresses if residue testing is required, she said.
“Consumer interest in food labels is high and shows a genuine desire to shop smarter,” Karlin said. “For consumers to truly make informed purchasing decisions, we need to explain what the labels mean, the process of certification and which labels they can trust.”
Controlled Environment Agriculture (CEA) 4.0 - Conference & Exhibition Day 2 - Friday 4th June - Attendee Tickets Still Available - 522 Attendees Registered
By purchasing a ticket for Conference Day 2 you will receive access and instructions on how you can view recording of the below presentations from Conference Day 1
Controlled Environment Agriculture (CEA) 4.0
Day 2 Conference & Exhibition (Virtual)
Friday 4th June 2021
CEA 4.0 Conference & Exhibition Day 2 is this Friday the 4th of June. With 522 industry attendees officially registered, we still have a small number of attendee tickets that have been made available for Conference Day 2 on Friday
Attendee tickets range from £14.99 - £19.99 per attendee.
Day 2 Conference Presenters
Advanced Plant Growth Centre (APGC) - Derek Stewart, Director
Algal Tech - Armando Leon, Founder & CEO
AmplifiedAg - Don Taylor, CEO & Founder
DAG Facilities - Mark Gemignani, CEO
FarmTech Society (FTS) - Nicole Thorpe, Vice-Chair
GlobalG.A.P. - Kristian Moeller, Managing Director
Greens for Good by Farm Urban - Jens Thomas, Technical Director
GroenLeven - Willem de Vries, Business Innovation Manager
Growfoam - Niels Steenvoorden, Chief Commercial Officer
Intelligent Growth Solutions - David Farquhar, CEO
Jungle - Nicolas Seguy, Managing Director
Mycelium - Eric Dargent, Managing Partner
Mycelium - Yishai Nissan, Managing Partner
Natural Resources Institute Finland - Titta Kotilainen, Senior Scientist
Planet Farms - Daniele Benatoff, Co-Founder & Co-CEO
Red Sea Farms - Ryan Lefers, CEO
SolarPower Europe - Miguel Herrero, Policy Advisor
UK Urban AgriTech (UKUAT) - Katia Zacharaki, Communications Director
Urban-Gro - Mark Doherty, Executive Vice President of Operations
Urban Crop Solutions - Tom Debusschere, CEO
Urban Harvest - Alexandre Van Deun, Co-Founder
Urban Harvest - Olivier Paulus, Engineering & Co-Founder
Valoya - Mika Linden, VP Sales
Valoya - Satu Karjalainen, Research Coordinator
Vertical Farm Institute - Daniel Podmirseg, Director
Vertical Future - Jen Bromley, Head of Plant Research & Development
Vertical Harvest - Nona Yehia, Co-Founder & CEO
Würth Elektronik eiSos - Johann Waldherr, Business Development Manager
Day 1 Conference Presenters
By purchasing a ticket for Conference Day 2 you will receive access and instructions on how you can view the recording of the below presentations from Conference Day 1.
AeroFarms - Roger Buelow, Chief Technology Officer
BrightFarms - Paul Lightfoot, President & Founder
CEA Food Safety Coalition - Marni Karlin, Executive Director
Certhon - Martin Veenstra, Consulting Engineer Indoor Farming Systems
Cultinova - Jim Thorpe, Chief Technology Officer (CTO)
Department for Environment, Food and Rural Affairs (Defra) - Caroline Povey, Team Leader – Agri-Innovation Policy
Finnish Glasshouse Growers' Association - Jyrki Jalkanen, CEO
GE Current - Dr. Hans Spalholz, Senior Plant Scientist
Graines Voltz - Solène Voltz, Vertical Farm Sales
Graines Voltz - Wolfgang Fishcer, International Product & Sales Specialist
Heliospectra - Fei Jia, Technical Solutions Manager
HerbanLeaf Farms - Myrianthi Oxtoby, Founder & CEO
Jones Food Company - James Lloyd-Jones, Founder & CEO
LEAF (Linking Environment & Farming) - Caroline Drummond, Chief Executive
Netled - Niko Kurumaa, COO
North Carolina State University - Dr. Ricardo Hernández, Professor
ONO Exponential Farming - Thomas Ambrosi, Director
Planet Farms - Daniele Benatoff, Co-Founder & Co-CEO
Real Leaf Farms - Karen Hennessy, CEO
Signify - Tom Könisser, Business Development Manager City Farming
Singapore Food Agency (SFA) - Poh Bee Ling, Director, Horticulture Technology Department Agri-Food
UK Research & Innovation – Innovate UK - Ian Cox, Innovation Lead
UK Research & Innovation – Innovate UK - Tom Jenkins, Deputy Challenge Director – Transforming Food Production
Urban Crop Solutions - Tom Debusschere, CEO
VEK Adviesgroep - Reinier Donkersloot, Director Business Consultancy
Vertical Future - Jen Bromley, Head of Plant Research & Development
Vitabeam - James Millichap-Merrick, CEO
Wageningen University & Research - Luuk Graamans, Scientist Vertical Farming
CLICK HERE TO BOOK YOUR ATTENDEE TICKET
Click Here To Meet The Current CEA 4.0 Sponsors,
Presenters, Exhibitors & Attendees
VIP Attendee Ticket Includes
Full event access provided to the conference, workshops, exhibition, etc
Personal event attendee profile
Company profile
Ability to arrange up to 36 one-to-one meetings with any attendee during the event
Ability to message and video chat with any attendee
Access to the presentation recordings from Conference Day 1
Company branding on the event website & at the event
CLICK HERE TO BOOK YOUR ATTENDEE TICKET NOW
BEFORE THEY ARE SOLD OUT
TECH 4.0 Ltd
info@tech40.net
https://www.tech40.net/
Raleigh Shipping Container Farm Using Hydroponic Technology
The technology that Nanue’s Farm uses was created by Boston-based company, Freight Farms. Each container has thousands of LED grow lights, temperature controls and uses between five and ten gallons of water each day
BY KYLEIGH PANETTA RALEIGH
MAY 10, 2021
RALEIGH, N.C. — Summer is one of the busiest and most profitable times for farmers across the state but what if they could grow produce year-round?
Nanue’s Farm in Raleigh is using some advanced technology to do just that.
What You Need To Know
Nanue's Farm is located in downtown Raleigh and uses hydroponic technology
The "container farm" is about 320-square feet and can hold 5,000 heads of lettuce
The technology is being used in dozens of countries and may help eliminate "food deserts"
Nanue’s Farm is on S. West Street, what some may say is a pretty strange place for a farm.
“This is in downtown Raleigh. You can see the great skyline we have here,” said Trevor Spear, the owner of Nanue’s Farm. “I walk to work when I can. I don’t have to drive.”
Spear admits that a seemingly empty parking lot with a shipping container is not what most people expect to see when they arrive at a farm.
“It’s funny because people don’t understand what it is. They think it’s just a shipping container and people are storing stuff inside it,” said Spear.
Nanue’s probably looks more like a science experiment than a farm.
“It’s 65 degrees, 60% humidity. Co2 runs at night, so we’re like 2,000 parts of Co2 in there. It’s optimal growing conditions for lettuce and that’s how we do it in seven weeks’ time,” said Spear.
Spear specializes in leafy, crunchy greens. Something else you can hear inside the farm, from time to time, is classical music.
“We play classical music at night and I think it makes a difference. They like it. Sometimes we play a little Van Halen but usually Bach or Beethoven,” said Spear who knows that a little TLC goes a long way and said every lettuce has a name.
It’s not your typical lettuce but Spear is also not your typical farmer. He named the farm after his grandmother, Lydie Cox.
"When I was a kid I would go have summers at Nanue’s house and she had a huge garden, an acre size garden. I would go up and down the rows with her as a kid. That’s where I probably got the bug because once it bites you, you live with the sting," said Spear.
Nanue’s Farm is getting a second container in June and hopefully a third by the end of the year. They currently offer home delivery to a few areas and are looking into creating a farm stand. The majority of the produce is sold to local restaurants in the area.
"When chefs come and tour the farm, they open the door and they’re like, 'Wow.' We can hold 5,000 heads of lettuce. We harvest 60 cases a week, so when they walk in and see that much lettuce growing and looking as good as it does, it’s a take-back," said Spear.
If you’re interested in trying some of their lettuce, you can also find a Nanue’s salad at Hummingbird, a restaurant in Raleigh.
The technology that Nanue’s Farm uses was created by Boston-based company, Freight Farms. Each container has thousands of LED grow lights, temperature controls and uses between five and ten gallons of water each day.
The containers also have cameras and connect to Wi-Fi so it can be monitored from an app or website. Freight Farms said the goal is to replicate an ideal farming environment so that more people have access to fresh produce.
“In the U.S., food moves 500 to 1,000 miles, predominantly from California. If you can move the farm then you can put a farm in a food desert and then you can grow the food and the hyperlocal food and the high nutritional values of that food. Either food deserts or even urban areas,” said James Woolard, the chief marketing officer for Freight Farms. “You might not think it’s a food desert but it is from a socio-economic point of view and an access point of view.”
Robotic Warehouse Farms Will Save The World
CEA technology is just getting started. Like the Tesla Cybertruck, we have a working concept that promises a more-than-Jetson’s-level future many of us can see the benefits of and actively want―it’s just not quite available to the masses yet
by Elle Griffin
Four years ago, Ritch Wood was looking for a better way to grow plants. As the CEO of global skincare company Nu Skin, he ran into ingredient shortages every winter when fields went dormant―and when he moved grow operations to the equator he ran into water and land shortages, along with a host of quality control issues.
Nu Skin needed reliable, quality ingredients for their skincare products. But farming was too unpredictable an industry. “If there was a way to grow indoors,” he thought, “and be able to do that 24 hours a day, 365 days a year―if we could guarantee that it was grown without any herbicides or pesticides and in a sustainable way that uses less water and land―that would be really helpful.”
At the time, controlled-environment agriculture (CEA) was in its infancy and grow-light technology had yet to take a turn for the more affordable. When he learned of an agricultural system that promised to use a fraction of the land and water used by traditional agriculture methods and had the potential to make it more affordable, Wood made an investment.
Nu Skin paid $3 million for 70 percent of the company and rights to its IP―and Grōv Technologies was born.
Grōv grass grown in the Olympus machine at the Bateman Mosida Farms. Photo from Grōv Technologies
Controlled-environment agriculture is on the rise
The theory behind CEA is that by controlling the environment in which it grows, we can control everything about a plant and what it grows into by micro-tweaking one of a thousand different characteristics―including temperature, humidity, light duration, light wavelength, dissolved oxygen in the water, and carbon dioxide saturation in the air. By tweaking the growing cycle, we can control the caloric content as well as the nutrient content and density of the plant.
“What we’ve learned through controlled-environment agriculture,” Benjamin Swan, co-founder and CEO at Sustenir in Singapore, once told National Geographic, “[is] we can actually emphasize certain characteristics of the plants. So, without using GMO, we can make our kale softer, we can actually make it sweet.”
The theoretical use cases for this technology are endless―from being able to grow in places where water is scarce (like in much of Africa), or where water is overly abundant (like Hawaii), or in places where labor is scarce (like in parts of Asia), or even in places that have long winters (like Northern Europe). Theoretically, we could have grow towers in every town and feed the whole of it no matter its natural environment.
We could even grow those foods to those cities’ exact nutritional needs―more vitamin D-rich foods in wintery places, for example. Dr. Lee Mun Wei, a senior manager at the Food Innovation and Resource Centre (FIRC) in Singapore aims to predict and prevent illness in a given population by tracking their biometric data using Apple watch-like wearables, then 3D printing nutrient-specific foods that could mitigate imbalances.
Though these technologies exist, they are still in their infancy. Singapore leads much of the research and development out of necessity. With limited land and water resources, the county is forced to import 90 percent of their food and 40 percent of their water from outside the country. As a result, they have no option but to grow vertically and desalinate water from the ocean.
Elsewhere, the industry has been slow to catch on, largely due to exorbitant startup costs, low returns, and lack of urgent need. According to a 2017 State of Farming report by L.E.K., only 27 percent of indoor, vertical farms are profitable compared with 50 percent of container farms and 75 percent of greenhouses. But one thing has spurred the industry on in recent years: cannabis.
Legalized in 39 states, demand for cannabis has created a $13.6 billion industry and enough capital to fund CEA-enabled grow operations. “When you have a crop that fetches up to $2,400 or $2,500 a pound, you need to be able to dial everything in and make it consistent and repeatable,” says Dashiel Kulander, co-founder and CEO at Boojum Group. “If the temperature swings five to 10 degrees on a cannabis plant, that will change the plant’s various cannabinoids. The goal is to create a medicine that is consistent batch after batch.”
It’s only recently that there has been some financial incentive to use CEA technologies for food use―largely driven by Big Ag players hoping to hedge out the competition. Berry farming giant Driscoll’s, for one, led a $500 million round to fund Plenty, a 2.2-acre vertical farm in California they hope will help them fulfill a contract with Albertsons. The Ingka Group, for another, led a $100 million round to fund AeroFarms, a 2.4-acre vertical farm in New Jersey that will help them fulfill a contract with Singapore Airlines.
Grōv tent at the Bateman Mosida Farms. Photo from Grōv Technologies
Grōv Tech is building CEA prototypes in Utah
By investing in Grōv Tech, Nu Skin hopes to do something similar, getting ahead of the supply chain that fuels their skincare products before the competition can beat them to it, or before climate change makes traditional methods more difficult, all while shoring up technology that could provide a farming model that is more sustainable―if only it were more economical.
“The purpose was always, can we build a better product for Nu Skin?” Wood says. “We think there’s a huge story around the ingredient sustainability, and there were a lot of ingredients we felt we could grow, but the challenge was: could we do it in an economical way?”
Grōv Tech started out with a prototype: a tower that pairs hydroponic growing technology with grow lights. But like all CEA startups, a lot of the growing process was manual and the technology was prohibitively expensive. To make something that was scalable and profitable the whole thing needed to be automated and it needed to be cheap.
With this goal in mind, Wood decided they would start by growing animal feed for Bateman’s Dairy farm. Having grown up on a dairy farm himself, Wood figured this would allow the company to scale the product while refining and automating the technology to the point that it could be replicated. And all of this would have a fortuitous effect on Nu Skin’s bottom line.
“One of our bestselling products is a weight-loss protein powder which uses whey protein,” Wood says. “So again, a very nice connection there is if the animal is eating a more sustainable product and producing better milk with better protein and it’s being done in a sustainable way―certainly that can be a benefit to Nu Skin down the road.”
One year into feeding the 20,000 animals at Bateman, the company has learned a lot. For instance: cows need a lot of magnesium, but they don’t like eating it. Now, Grōv Tech puts magnesium in the water so it’s directly absorbed into the plant and then becomes bioavailable to the cow upon eating it. And because the growing process only takes seven days, data scientists can analyze the results in real-time and adjust the components to optimize production for the next batch of feed.
According to Grōv Tech president Steven Lindsley, it’s not far off that we’ll be looking at milk production (butter, fats, and proteins) and optimizing a herd’s diet for taste, quality, and nutritional value―not to mention the wellbeing of the animal. We’ll be able to look at how many trips from the veterinarian an animal gets when they’re fed certain nutrients in their diet, and whether they can have more calves and produce the same amount of dairy on less, better quality feed. (So far, the answer to this last question is yes. When animals are fed better quality food they need less of it―just like humans.)
And if we hook all of the cows up to robotic milking equipment and connect everything to artificial intelligence, machine learning, and the Internet of Things―Lindsley’s far-flung goal―then we might be able to collect enough data to not only feed cows to their optimum health and performance ability, but humans too. And that could have ramifications not only for feeding the world, but nourishing it― just like Dr. Wei hopes to do in Singapore.
“Last year was about starting to feed animals and get data and prove out the hypothesis we have while continuing to perfect the technology and get confidence there,” Wood says. “And now we’re really to a point where we’ve got data that proves that it works and that financially it’ll be a good thing for a farmer. So now we can really take that proposition to farmers and start to scale.”
Olympus Tower Farm at Bateman Farms in Mosida, UT. Photo from Grōv Technologies
CEA technology could feed the world
Right now, Grōv Tech is focused on refining its technology right here in our own backyard. But once they do that, the plan is to expand internationally.
“Saudi Arabia has actually passed a law where you cannot use water to grow fodder or feed for animals, so all of that now has to be imported. China imports one-third of their alfalfa feed for their dairy animals because they don’t have the capability of growing it,” Wood says. “So there are countries that will probably benefit more than the US would. But we’ve got to refine the technology and get that built to where it’s ready to scale before we start spreading ourselves all around the globe.”
CEA technology is just getting started. Like the Tesla Cybertruck, we have a working concept that promises a more-than-Jetson’s-level future many of us can see the benefits of and actively want―it’s just not quite available to the masses yet. But with more than a billion dollars invested in the technology in just the past few years alone―we’re getting there. And the “there” we are heading toward is rosy indeed.
“To put it in perspective, one tower that is about 875 square feet on the ground will replace 35 to 50 acres of land,” says Lindsley. “And that will feed the animals on roughly five percent of the amount of water. The UN says that that the world will add about 2.5 billion people in the next 30 years. And we have to find a way to feed them on arguably less arable land and water. The good news is the technology is coming along to help solve that equation.”
If COVID-19 taught us anything, it’s that our food supply chain is fragile. But that’s only because our supply chain was built to grow food in California, refrigerate it so it stays fresh, then transport it 1,500 miles so we can eat a salad in the winter in Chicago. In the future, that might not be a thing. “We’re having a dry year now,” Lindsley tells me in February. “But a year ago we were in a blizzard, and even in the middle of a blizzard in February in Utah, we’re pumping out fresh, beautiful, safe green grass for animals. It’s a paradigm shift.”
“Four years ago it was a good idea,” Wood tells me of his company’s investment in CEA technology, “But four years from now it’s going to be required.”
Elle Griffin
Elle is the editor-in-chief of Utah Business and a freelance writer for Forbes, The Muse, and The Startup. She is also a literary novelist and the author of a weekly newsletter called The Novelleist. Learn more at ellegriffin.com.
2020 Sustainability Report Highlights AppHarvest’s Impact
“Resiliency is at the core of our beliefs at AppHarvest because farming as we’ve known it is broken and not sustainable for the planet,” said Founder & CEO Jonathan Webb
On A Mission To Redefine Agriculture
Titled “Feed the Future,” our 2020 Sustainability Report is now available for view and outlines our efforts to create positive environmental change in agriculture, empower employees and improve the communities in which we operate.
“Resiliency is at the core of our beliefs at AppHarvest because farming as we’ve known it is broken and not sustainable for the planet,” said Founder & CEO Jonathan Webb. “We’re solving for the variables that make our food system unreliable, such as extreme weather, droughts, fire or contamination. Our team built one of the world’s largest facilities in the midst of a global pandemic.”
This Earth Day, we’re detailing our progress toward three distinct impact goals as we work to establish a reliable, climate-resilient domestic food supply:
Drive positive environmental change in agriculture: Our first high-tech indoor farm grows more with fewer resources and contributes to a climate-resilient, domestic food supply. With our strategic location in Central Appalachia, we can reach 70% of the U.S. population within a day’s drive. The location reduces diesel used for transportation as much as 80% compared to produce trucked from Mexico or the Southwest of the U.S. Our operations are also designed to use 90% less water than open-field agriculture with 100% recycled rainwater, zero chemical pesticides, and zero agricultural runoff.
Empower individuals in Appalachia: To us, ‘empowering individuals’ means creating a life-changing experience for employees and their families. As of March 31, 2021, we have created 500 jobs with 100% of employees verified to be paid a living wage plus a comprehensive benefits package that is considered best-in-class in the agriculture sector. We also make each employee a stakeholder in the company’s success by providing equity-based incentives.
Improve the communities in which we operate: Our plans call for more than tripling our investment in Appalachia to reach almost $1 billion in capital invested by 2025. We're also working with Eastern Kentucky high schools to incorporate AgTech curriculum and provide high-tech container farms that offer students a hands-on opportunity to grow their own food and learn about nutrition. In fact, we opened another container farm today. Read more below.
“Consumers are more educated than ever, and they use that knowledge to support organizations, like AppHarvest, that have the best interests of all stakeholders in mind by putting people and planet first,” said AppHarvest President David Lee.
The complete Sustainability Report can be downloaded here.
“I’m Opting For Localized Franchised Farming”
Natalie, an 18-year-old engineering student, is determined to run her own farm in the future. It all started with finding a research project . . .
Engineering student wants to start her own farm in New Jersey
“In the States, the food system is so inefficient both in the way it’s produced, at a massive scale and in terms of quality,” says Natalie Radu. "The problem is that consumers are left in the dark. They don’t know what pesticide is used on the food they’re eating. GM foods are not labeled. Let aside the waste this industry has.” Natalie says that many don’t have access to healthy food. When walking around in the Bronx for instance, on the lookout for a grocery store, it’s so much easier to buy a pack of soda for half the price of fresh produce.
‘Localized franchised farming’
“McDonald's is known for real estate. If only we could do a Wholefoods / McDonalds franchise where customers could walk in and snip off lettuce, directly available to consumers. I’m opting for localized franchised farming. I have been trying to figure out a location in terms of real estate, but, from the perspective of a small business, New Jersey and New York prices are very high. I would have to start out in a place that’s cheaper on average. However, I would definitely apply for grants to fund the initial infrastructure for the farms."
Natalie Radu in action on her channel
Natalie has her passion for writing and her engineering study to her advantage when starting a farm. “I think because of this intersection I will be able to work with the science and also have the ability to convey that science. I can make the lettuce we’ll be growing feel personal for someone that’s in their own house, miles away or even across the world. That’s the biggest thing, you have to get people excited about vertical farming, at least as excited as you are. However, when it comes down to engineering I’m going to need some help.”
“My family immigrated from Moldova to the US around the collapse of the Soviet Union,” says Natalie. “My grandparents used to grow several fruits in the backyards and my affection for farming started right about there, it’s in my blood.” Natalie, an 18-year-old engineering student has been determined to run her own farm in the future. It all started with finding a proper research topic, which turned into her biggest passion nowadays.
As Natalie’s based in New Jersey, she is surrounded by several vertical farms. She wanted to pass by some farms near her to visit and stumbled upon Good Feeling Farms. Eventually, Natalie was able to do an internship at Good Feeling Farms to get a better understanding of every aspect of a vertical farm, from seeding to growing to harvesting. Good Feeling Farms is a New Jersey-based wholesale micro greenery that specializes in microgreens and hydro lettuce. The farm is run by a team of three, taking care of the cultivation and harvesting process.
Inside Good Feeling Farms' growing facility
Ever since her internship, Natalie is determined to run her own farm in the future. She currently runs a YouTube channel, where she experiments with indoor hydroponics. She recently spoke at a local TEDx event about the inefficacies in traditional food production and distribution systems.
Natalie says: “I’ve tried many growing conditions for plants and I think you can grow them under many different conditions. You have to work with your circumstances. Ideally, your indoor garden would be sustainable. The growth mediums could be sanitized and reused to lessen waste. Besides being water-efficient, vertical farming really shines in the areas of automation and data science. The ability to collect and analyze plant data constantly and instantly modify environmental factors has massive potential for produce cultivation as we know it.”
For more information:
Natalie Radu
natlydrad@gmail.com
Publication date: Fri 15 Jan 2021
Author: Rebekka Boekhout
© VerticalFarmDaily.com
USA: New Farm Brings Sustainable Farming To Northern Michigan
There's a new farm in northern Michigan that provides fresh and local produce all-year-round using environmentally friendly practices and high-tech resources. The container is home to Pine Hill Farms, a farm that uses a controlled environment agriculture system to grow produce
by Miya Ingle
April 16, 2021
To View The Video, Please Click Here:
Pine Hill Farms uses a controlled environment agriculture system to grow produce. (Miya Ingle/ WPBN)
KALKASKA COUNTY, Mich., (WPBN/WGTU) -- There's a new farm in northern Michigan that provides fresh and local produce all-year-round using environmentally friendly practices and high-tech resources.
If you're driving down Tower Road in Kalkaska, you might notice a big container.
The container is home to Pine Hill Farms, a farm that uses a controlled environment agriculture system to grow produce.
The produce is grown hydroponically instead of in the ground.
Staff at Pine Hill Farms say this growing method uses 95% fewer resources than traditional farming.
"Some of the biggest benefits to growing hydroponically versus in a traditional manner is number one; we can grow year-round, 365 days a year," Pine Hill Farms Founder Jeff Bickley said. "Number two, we're hyperlocal. Local is a really big deal. People want to support local businesses. They also benefit from the difference in freshness."
Pine Hill Farms is currently growing nine different kinds of lettuce but plans to expand its products in the future.
The farm is connecting with local restaurants to sell its produce to.
Entrepreneurs See Hydroponics As Farming Solution In Libya
Conventional Agriculture Struggles In Mostly-Desert North African Country
Conventional Agriculture Struggles
In Mostly-Desert North African Country.
11/04/2021
TRIPOLI--Under a yellow tarpaulin stretched over an arched metal frame, Siraj Bechiya and his partner inspect their hydroponically-grown lettuce, pioneers of the method in mostly-desert Libya where conventional agriculture struggles.
Zip ties, punctured plastic cups as pots and PVC tubing bought in DIY shops hold the precious crops at “Green Paradise” — so dubbed by the two young Libyan entrepreneurs spearheading the project.
But the ad hoc nature of the materials hasn’t stopped the plants from thriving, their long white roots nourished by water rich with nutrients and oxygen.
Bechiya and his partner, Mounir, have been working tirelessly on their project for months in the small town of Qouwea, 40 kilometres east of the capital Tripoli, erecting a tunnel-shaped greenhouse surrounded by breeze-block walls on a semi-arid site.
Their hope is to demystify hydroponic farming, which “guarantees a good yield in small spaces”, uses little water and doesn’t need pesticides, 20-year-old Bechiya said.
Soilless farming has gained ground in many countries but is still in its infancy in Libya.
But in a country whose territory is 90 percent arid desert, the method could offer a path toward more food self-sufficiency, Bechiya believes.
Challenges to farming
Agriculture remains a marginal sector in Libya, where the economy is dominated by hydrocarbons, the country boasting the most abundant oil reserves in Africa.
Arable land barely makes up three percent of Libya’s territory and is under threat, as rapid urbanisation eats up the fertile strip along the Mediterranean coast.
Another major challenge to farming in Libya is the lack of water where agriculture needs it most.
The Great Man-Made River — a pharaonic project realised by the toppled long-time ruler Muammar Gadhafi more than 30 years ago — carries drinking water pumped from groundwater tables in the south to the northern cities where most Libyans live.
But this resource is not infinite, and the GMMR’s network has been heavily damaged in the decade of conflict that has ravaged Libya since Kadhafi’s ouster in a 2011 NATO-backed uprising.
In the face of these challenges, Bechiya and Mounir set out to train in hydroponics two years ago in neighbouring Tunisia.
“When we came back, it was imperative that we move from theory to practice,” Bechiya said.
“We started with some vegetables in the house and we were surprised by people’s enthusiasm.”
New Techniques
In theory, hydroponics can guarantee higher yields and profits than conventional farming, which is at risk from weather, water shortages, and pollution from unregulated pesticide use.
“With more space in the greenhouse, the idea was able to take off. We will continue to develop it… and improve quality,” said Bechiya, as he measured the acidity of the water feeding his young lettuce.
“Libyan consumers don’t want produce full of pesticides anymore, but organic produce,” he added.
While not saturated with pesticides, hydroponic products, poo-pooed as bland by detractors, generally are not labeled organic.
Agronomist Abdelkafi al-Amrouni said the method “paves the way toward the introduction of new agricultural techniques in Libya” to compensate for water shortages.
There are still obstacles to widespread hydroponic use, however.
“It’s complicated and very expensive to get supplies in Libya,” even as the country tries to turn the page on a decade of chaos, Amrouni said.
Such costs could make the products ultimately prohibitively pricey.
But Bechiya is not deterred.
“You have to be patient and believe in your idea,” he said.
Lead photo: Project manager checks a plantation of hydroponically grown lettuce, in a greenhouse in the small town of Qouwea, about 40 kilometres east of Libya’s capital Tripoli. (AFP)
Can Vertical Farming Be A Viable Method Of Controlled Environment Production?
Fifth Season is using its fully integrated, automated operating system to crack the economics code for vertical farming with the potential to integrate with greenhouse operations.
Fifth Season is using its fully integrated, automated operating system to crack the economics code for vertical farming with the potential to integrate with greenhouse operations.
To say that controlled environment agriculture is drawing a lot of interest and dollars from the investment world would be an understatement. Austin Webb, co-founder, and CEO at Fifth Season, a vertical farm operation in Pittsburgh, Pa., estimates that over $3 billion has been invested in the CEA industry during the last four years alone, excluding debt and merger and accusations activities for greenhouse operations.
“For indoor ag overall, including both vertical farming and greenhouse, about half that equity investment has been for vertical farming,” Webb said. “There were a lot of dollars that came into this space early on. The unfortunate piece to that is there was a lot of overhype and false promises made in this space. A lot of those dollars came in too early for some of these companies and overall were wasted.
“There has been an industry-wide struggle to make the economics of vertical farming work. All of these companies talk about what they are going to do in the future, but the issue is they have negative unit economics. They lose money for every pound of produce they sell. In many cases, they will say that they will make the economics work in the future, but only after they build more production facilities.”
Webb said negative economics has had a major impact on the vertical farm industry.
“The false promises and the negative economics have held the industry back, overshadowed companies that are building substantial vertical farming solutions that work and pushed additional dollars to incremental greenhouse solutions,” he said. “Moving forward we will continue to see more dollars come into CEA and into vertical farming specifically. This will include public markets and SPAC (special purpose acquisition company) activity.
“Overall, there will be more money invested in CEA. This will include investments that are mediocre. The important element will be investments made into tech platforms designed for scalability and repeatability. This is the only way that volume requirements for wholesale buyers can be met to unlock indoor ag as a material participant in overall market share.”
Need for a mindset change
Even with additional investment dollars coming into the CEA industry, Webb doesn’t expect it to be enough to make traditional vertical farming companies a success.
“Unfortunately, even though significant dollars have been invested in vertical farming, much of it has been wasted,” he said. “The incremental mindset a lot of people in this industry have had is to simply convert farming from outdoors to indoors. In doing so, all they inevitably did was bring people from outdoors and put them indoors. The mindset was to create a growing platform to produce leafy greens and then sprinkle on some technology. The technology was sort of an afterthought.
“There were a lot of companies throwing out buzz words without having actual practicality in regards to robotics, artificial intelligence, and automation. All the money that has been invested has been going toward continued R&D, but at a level which has companies creating technical debt.”
The thing that has helped Fifth Season avoid the technology issues other vertical farms have encountered is the way the company developed and designed its operating system.
Fifth Season has created a manufacturing platform that is fully automated from end-to-end including growing, processing, and packaging.
“We had a completely different mindset,” Webb said. “We took a blank slate to really design this holistically from beginning to end. We think of this as manufacturing a living organism. As a result, we’ve created an IoT–connected smart manufacturing platform that is an industry-first, industry-only, fully end-to-end automated platform—not just growing, but also processing and packaging. There are other operations that have automation here or there, but nothing else truly automated from beginning to end.
“More importantly, we have integrated the system so it is completely run by our proprietary software platform. We don’t have a bunch of automated equipment that runs on its own controls. Instead, we have a combination of our own proprietary tech and some off-the-shelf equipment such as conveyors. All of the electromechanical systems sit within our software skin and are run by our in-house built firmware and software brain. We have a pathfinding algorithm where when we receive an order from a customer, our system is sequencing out the schedule completely on a daily, weekly and monthly basis.”
Fifth Season worked with Hort Americas and GE Current, a Daintree company, to develop its automated grow room.
“Partnering together on our solution helped us validate that there was a path for our vertical farm to have favorable economics,” Webb said. “Being able to bounce ideas and technologies off of the Hort Americas team allowed us to push the boundaries of innovative thinking in terms of our approach and how we wanted to use technology to solve the complex issues that are limiting vertical farming. We were able to think differently, knowing we had the Hort Americas team as both a check and enabler, which ultimately created a successful collaboration.”
Partnering with Hort Americas also gave Fifth Season the opportunity to incorporate Current’s LED technology into its unique growing platform.
“We did a lot of things differently with our proprietary design and in so doing there were certain things that we couldn’t necessarily handle ourselves,” Webb said. “Working with Hort Americas and Current enabled us to move very quickly while making smart, capital-efficient decisions, as opposed to designing the LEDs ourselves or over-paying for unnecessary functionality.
“We worked with Current in key areas that made big differences related to the integration of our design. We leveraged Current’s significant expertise in regards to light spectrum strategy and the corresponding impact on plant science and quality.”
Creating an economic advantage
Webb said Fifth Season’s unique platform has allowed the company to unlock positive unit economics where it can offer a market price that works for wholesalers and consumers.
“We have been able to make money per pound and make vertical farming economically sustainable,” he said. “Our platform has enabled us to make a stepwise function change in labor costs and efficiency and in energy costs. For labor, we have 2x+ less labor costs than other companies in this space. We also measure and track energy down to every individual bot. We have over 60 bots that are all integrated into one robotics system. We measure and track how to optimize energy utilization to all of those bots.
Fifth Season’s unique operating platform has allowed the company to unlock positive unit economics enabling it to offer a market price that works for wholesalers and consumers.
“Finally we have made a stepwise function change in pounds to fixed costs ratio. That’s because we have been able to remove large aisle ways and manual inefficient storage and retrieval. We have created a patent-pending solution around our automated storage retrieval, which ties to the rest of our system. In the end, we are able to remove all human involvement from the grow room and are able to achieve 2x+ the growing capacity.”
Another advantage of the platform Fifth Season has created is the need for raising additional capital compared to some other vertical farms.
“We have raised just over $40 million to date,” Webb said. “There are multiple vertical farm companies that have raised $200 to $400 million+. The reason we haven’t had to raise that much capital is because of our mindset about engineering, grow science, and operations in the same R&D pipeline. It has allowed us to catch up and to surpass the rest of the industry in a fraction of the time with a fraction of the capital.
“As we move forward and look at raising additional capital, what’s different is we don’t have to use our equity capital to build more farms for all the hard costs associated with real estate, equipment and building facilities. We can if we want to and if it makes sense for our equity partners, but it is not required. We have been able to unlock positive unit economics which means we have been able to unlock non-dilutive capital to build additional facilities more capital efficiently. Overall, we have built a scalable, repeatable platform, which is what investors need to see.”
What’s ahead for vertical farming?
Webb said there will be a few select companies that have approached indoor ag and vertical farming with a solution that works and will thrive. There will also be a number of companies that are large and excessive that will eventually disappear.
“There will be some consolidation in this industry,” he said. “Some companies won’t be consolidated because they don’t have a tech platform that is investable in terms of the synergies of wanting to acquire that footprint. Consolidation will be selective in some cases.
“There is a lot of production regardless of footprint and money going into leafy greens. There are companies in this space that have no intention of doing anything different than that. I think that focus will run them into a leafy greens race to the bottom. It all comes down to no sustainable competitive advantage.”
Webb also sees the potential for synergy between vertical farms and greenhouses.
“We have built a scalable system that allows us to do a number of crops and then do asset management across different applications,” he said. “We also have the technology that is applicable from an asset management production operations standpoint that works for greenhouses as well.
“We will be able to unlock with this technology what many others won’t necessarily be able to do. Fifth Season will not only be a company that has vertical farm and greenhouse footprints but also is one that uses those footprints in a collaborative way for specific crops. For example, a crop could be in a vertical farm environment for part of its life and in a greenhouse for another part of its life. This will create cross-category and cross footprint combinations.”
For more: Fifth Season, (412) 899-2268; hello@fifthseasonfresh.com; https://www.fifthseasonfresh.com/
Lead photo: Austin Webb, co-founder, and CEO at Fifth Season, said even though significant dollars have been invested in vertical farming, much of it has been wasted. Photos courtesy of Fifth Season
This article is property of Urban Ag News and was written by David Kuack, a freelance technical writer in Fort Worth, Texas.
CHINA: $500 Billion To Bring All World Crop Farming Indoors
China will build 2 Million hectares (20 billion square meters) of controlled environment greenhouses by 2025 and this will produce half of their vegetables and crop needs
Brian Wang | April 3, 2021
China will build 2 Million hectares (20 billion square meters) of controlled environment greenhouses by 2025 and this will produce half of their vegetables and crop needs. Temperature, humidity, lighting would all be under controlled conditions. It would not matter if there were new extreme temperature swings outside or if there was drought. The needed food and water would be immune to any projected climate change over the next 500-1000 years.
Alibaba sells greenhouses for as little as 70 cents per square meter. The bulk, high volume cost to the manufacturer is about 50 cents per square meter. If installation labor costs are 50% of the 2 million hectare project then it would cost about $20 billion for the 2 million hectare project. $40 billion would be sufficient for China to make 40 billion square meters of climate-controlled greenhouses which could produce all vegetables and crops. It would cost $260 billion to make greenhouses for the food production of the entire world.
Indoor climate-controlled agriculture has almost no need for pesticides and uses 7% of the water. This would take up 3-5% of the total land area of open-air farming.
Additional funds could be provided for higher demand from population growth and for some level of automation, sensors and other systems.
There is an economic analysis of smaller scale greenhouse and vertical farming. The all-in delivered cost of a pound of greens grown in a commercial greenhouse is estimated to be $2.33 per pound. It cost $18.3 million to build 280,000 square feet (2.6 hectares) of commercial greenhouse in the USA. The total cost to grow would be just over $3.0 million per year for 2 million pounds of greens or $1.52 per pound. BrightFarms employs 165 people for the three greenhouses. $1.10 per pound consists of employee costs.
The cost estimates for greenhouses could be brought down to $1 per pound or less with large-scale construction. Below are costs for 2.8 hectare systems in the USA.
There is value to having national food security and not having to depend on imported food. Ten billion to twenty billion dollars per year in indoor farm subsidies closes the cost gap with open-air farming.
China’s controlled environment system will have a lot of automation and lower construction costs because of the massive scale and lower costs in China.
PNAS – Wheat yield potential in controlled-environment vertical farms
Wheat growing is vastly more land and water-efficient but costs are not yet competitive with open-air farming.
Wheat is the most important food crop worldwide, grown across millions of hectares. Wheat yields in the field are usually low and vary with weather, soil, and crop management practices. We show that yields for wheat grown in indoor vertical farms under optimized growing conditions would be several hundred times higher than yields in the field due to higher yields, several harvests per year, and vertically stacked layers. Wheat grown indoors would use less land than field-grown wheat, be independent of climate, reuse most water, exclude pests and diseases, and have no nutrient losses to the environment. However, given the high energy costs for artificial lighting and capital costs, it is unlikely to be economically competitive with current market prices. Wheat grown on a single hectare of land in a 10-layer indoor vertical facility could produce from 700 ± 40 t/ha (measured) to a maximum of 1,940 ± 230 t/ha (estimated) of grain annually under optimized temperature, intensive artificial light, high CO2 levels, and a maximum attainable harvest index. Such yields would be 220 to 600 times the current world average annual wheat yield of 3.2 t/ha. Independent of climate, season, and region, indoor wheat farming could be environmentally superior, as less land area is needed along with reuse of most water, minimal use of pesticides and herbicides, and no nutrient losses.
Meat production could also be brought under climate control. The feed for cows, pigs, chicken and fish could be either brought into greenhouses or converted to insects. Insect feed can be twenty to one hundred times more space and water-efficient.
Meat can be converted into cell-based production in large vats. This would be similar to the industrial production of beer.
There would be zero risk of mass starvation caused by temperature or drought-induced crop failure.
There may not be a need to bring all crops indoors. But if China brings half of all of their crops indoors in five years it clearly shows that civilization can bring all crops and farming indoors at any time. The cost as I have shown is less than 0.5% of global GDP for the crops and a few percent to deal with the meat and feed as well.
It is likely only truly economical (even with China’s mass production) to bring vegetable and fruit farming indoors. If China has indoor vegetable and fruit production at $1 per pound then other countries could follow at different levels based upon how cost-competitive indoor farming is against open-air farming for a particular crop. There is also the question if people will pay more for greenhouse crops. Greenhouses allow for year-round crop production. This means consistent prices and availability for fruits and vegetable year round. It also means indoor farms can be inside of cities for fruit and vegetables that are fresh from the tree and vine. The greenhouse crops would also be mostly or completely free of pesticides. Indoor farming share will grow as efficiency and costs are improved.
I think 20-60% of all crops (mainly higher-value fruits and vegetables) globally will go indoors by 2030 and gradually more as indoor becomes a lower cost and superior product to outdoor farming. Greenhouse farmed fruits and vegetables can have a higher quality versus outdoor grown fruits and vegetables.
Some of the advantages of protected culture greenhouse crops are:
Season extension is just one of the advantages gained from greenhouse growing. Protected crops are less apt to be damaged by wind, rain, and hail so the percentage of marketable products is higher. Yield is often higher as well, if you can provide optimum growing conditions for each crop. Greenhouses protect crops from many diseases, particularly those that are soilborne and splash onto plants in the rain. And greenhouse crops may be protected from common field pests. Of course, greenhouse crops have their own particular problems such as foliar disease, aphids, and whiteflies, so vigilance is still required.
SOURCES- Alibaba, PNAS, agfunder news