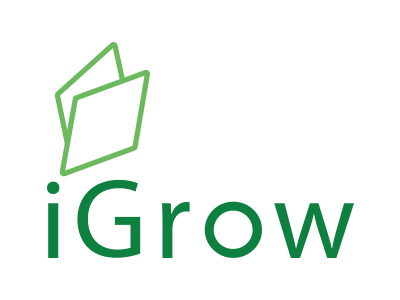
Welcome to iGrow News, Your Source for the World of Indoor Vertical Farming
USA - FLORIDA: Brick Street Farms Was On A Podcast!
What an exciting opportunity we had this week to sit down with Feeding Tampa Bay to record a podcast episode about how we grow our produce and our dedication to sustainability
Farm in a Box with Shannon and Maddy of Brick Street Farms
What an exciting opportunity we had this week to sit down with Feeding Tampa Bay to record a podcast episode about how we grow our produce and our dedication to sustainability.
We also got a chance to discuss how our non-profit organization, Desert Farms, is partnering with them to work towards a hunger-free Tampa Bay. Click below to listen to the full podcast.
Listen
Freight Farm To Teach Youth About Sustainable Agriculture
Beyond School Bells is partnering with the Bay in Lincoln for a new after-school program that will teach students about sustainable ag technology. "We really see Freight Farm as kind of that key, climate-change impervious tool that young people need to know about as we face an uncertain future," said Jeff Cole, Network Lead for Beyond School Bells
by Nicole Weaving
July 24th, 2021
LINCOLN, Neb. — Beyond School Bells is partnering with the Bay in Lincoln for a new after-school program that will teach students about sustainable ag technology.
"We really see Freight Farm as kind of that key, climate-change impervious tool that young people need to know about as we face an uncertain future," said Jeff Cole, Network Lead for Beyond School Bells.
An old shipping container in the parking lot of the Bay has been transformed in a self-contained hydroponic farm.
Using red and blue LED lights, this Freight Farm, known as the Greenery, creates a climate-controlled environment, where the plants grow vertically without a need for soil.
"We enrich the water with nutrients that would normally be in the soil," said Colton Harper, Organizing Manager for The Greenery. "And then in these grow walls, we've got spickets that come right through these foam and it's directly onto the roots of the plants."
Inside of the Greenery with the red and blue LED lights on. (KHGI)
According to Harper, there are currently about 6,000 plants growing in the Freight Farm, but at full capacity, it can hold 13,000 plants between the seeding area and that walls. That would produce the equivalent of a 2.5-acre farm year-round.
"Even in the winter, if there are shortages anywhere, we can turn on a dime, 7-week grow cycle and be able to provide those crops for local markets," said Harper.
The Greenery arrived in Lincoln in April, and Harper has led to two teams to get it up and running. They are currently preparing for their first harvest with items like basil, lettuce, and radishes.
"We're at about Week 7, and in 2-3 weeks, we'll have our produce at a farmer's market," said Harper.
After a few more grow cycles, the program will open to local students to teach them all aspects of sustainable farming.
"From the electrical side, the growing, the programming, computer science to the irrigation, the HVAC system, there's so many elements," said Harper. "And we're particularly well-placed with the Bay and their digital design area of focus, the students will also be able to design the packaging, design the labeling, so it's really a full-circle, interdisciplinary opportunity for the students to get involved."
The Greenery plans to hold a Harvest Party to celebrates the farm's success in the coming weeks
Earth911 Podcast: Freight Farms’ Jake Felser On Hydroponic Agriculture & Container Farming
Earth911 talks with Jake Felser, chief technology officer at Freight Farms, about the company’s “complete farming system inside a box.”
By Earth911
JULY 14, 2021
Earth911 talks with Jake Felser, chief technology officer at Freight Farms, about the company’s “complete farming system inside a box.” It’s a very big box that includes climate controls and monitoring systems to make farming easy for anyone to do. Freight Farms builds and delivers shipping containers converted into highly efficient hydroponic farms that use LED lighting to grow and deliver fresh produce year-round.
Jake discusses the cost of getting started, how many people are needed to run the farm, and how the built-in automation helps farmers plan a profitable business. Grocers, restaurants, communities, and small farms are using Freight Farms installations at 350 farms in 49 states and 32 countries. The company says most of its customers are new to agriculture and operate right in the urban and rural communities they serve.
Jake Felser, CTO at Freight Farms, visits Sustainability in Your Ear to talk about automated hydroponic gardening in shipping containers.
Growing and distributing vegetables locally is one of the most effective ways to lower our society’s carbon footprint. While agriculture contributes about 10% of the U.S. greenhouse gas emissions each year, the majority of that is from raising animals. By increasing our consumption of locally grown vegetables, we can improve local health and reduce overall emissions from transportation. It’s not easy to grow food in most cities using traditional methods. The introduction of container farms and vertical farming inside buildings can reshape food deserts and create economic opportunities.
To learn more, visit FreightFarms.com.
Subscribe to Sustainability in Your Ear on iTunes and Apple Podcasts.
Follow Sustainability in Your Ear on Spreaker, iHeartRadio, or YouTube
Tags: container farming, Freight Farms, hydroponics, reinventing agriculture
Solar Firm To Convert Shipping Containers To Urban Greenhouses
CEO James DiPrima said: “We also felt that inner city urban areas also needed a way to get fresh fruits and vegetables grown right in their own neighborhood. Reimagining old shipping/cargo containers as the structural framework for our soar technology would greatly reduce the costs of building greenhouses
July 9, 2021
New York, New York, July 09, 2021 (GLOBE NEWSWIRE) — Green Stream Holdings Inc. (OTC PINK: GSFI) (“the Company”) (http://www.GreenRainSolar.com), an emerging leader in the solar utility and finance space, which had previously announced that it would be entering the rapidly growing urban gardening sector with solar greenhouses dedicated primarily to rooftop farming, today announced that it is also moving forward with its previously announced project to convert old shipping/cargo containers into inexpensive greenhouses for urban and inner city neighborhoods.
Last year, on October 6, 2020, the Company previously announced that it had entered into a non-binding agreement with Aoki Group Inc. (“Aoki”) and famed restauranter, Kevin Aoki, who wanted to ship his famous mushrooms to his various sites around the world. The mushrooms would grow inside the container while being shipped to their destination.
Blondie’s specializes in custom urban landscapes including roof decks, terraces, courtyards and entry gardens, and is now utilizing that expertise in designing the irrigation systems for our Cargo container Solar Greenhouses. Blondie’s transforms concept and vision into realized functional design.
Blondie’s is experienced in specifying, installing, renovating and maintaining green wall systems. They are famous for their interior and outside Green Walls.
For more information go to: https://blondiestreehouse.com.
CEO James DiPrima said: “We also felt that inner city urban areas also needed a way to get fresh fruits and vegetables grown right in their own neighborhood. Reimagining old shipping/cargo containers as the structural framework for our soar technology would greatly reduce the costs of building greenhouses. Less room, less labor and less panels was a marriage made in heaven for underserved communities. Communities can get one, ten or 100 containers… whatever amount of land is available… and since each container has a small footprint, there is a lot of flex flexibility for each situation.
Using solar energy has two main benefits: Solar energy systems do not produce air pollutants or carbon dioxide, and Solar energy systems on buildings have minimal effects on the environment… OUR Solar Greenhouses combine the two creating a physical structure that produce electricity, with the ability to capture the sun from many different angles.”
About Green Stream Finance, Inc.
Green Stream Finance, Inc., a solar utility and finance company with satellite offices in Malibu, CA and New York, NY, is focused on exploiting currently unmet markets in the solar energy space, and is currently licensed in California, Nevada, Arizona, Washington, New York, New Jersey, Massachusetts, New Mexico, Colorado, Hawaii, and Canada. The Company’s next-generation solar greenhouses constructed and managed by Green Rain Solar, LLC, a Nevada-based division, utilize proprietary greenhouse technology and trademarked design developed by world-renowned architect Mr. Antony Morali. The Company is currently targeting high-growth solar market segments for its advanced solar greenhouse and advanced solar battery products. The Company has a growing footprint in the significantly underserved solar market in New York City where it is targeting 50,000 to 100,000 square feet of rooftop space for the installation of its solar panels. Green Stream is looking to forge key partnership with major investment groups, brokers, and private investors in order to capitalize on a variety of unique investment opportunities in the commercial solar energy markets. The Company is dedicated to becoming a major player in this critical space. Through its innovative solar product offerings and industry partnerships, the Company is well-positioned to become a significant player in the solar space.
SOURCE: Green Stream Holdings Inc.
Tagged indoor farming
Feel Confident In Starting Your Project With This 3-Part Webinar Series!
Even with effortless, turn-key container farms, there are still questions left unanswered for those interested in getting startedThis three-part webinar series will take you step-by-step through what you need to know before you start, how to select the best business model, and your options for financing the project
Even with effortless, turn-key container farms, there are still questions left unanswered for those interested in getting startedThis three-part webinar series will take you step-by-step through what you need to know before you start, how to select the best business model, and your options for financing the project.
By signing up, you will:
Hear and learn from first-hand experiences
Access knowledge and resources from Growcer and Farm Credit Canada
Break down how to get growing year-round into smaller, digestible steps
If you’re interested in growing food for your community but don’t know where to start or are stuck along the way, sign up for the webinar series today!
Register now for all three sessions:
July 13 - Getting Started
July 27 - Choosing a Business Model
August 10 - Financing your Project
Excited for you to join us,
The Growcer Team
BrightBox Farms’ Gideon Saunders Sees Alaska’s Future For Agriculture In Hydroponics
Nestled next to an otherwise ordinary house on Kodiak is a shipping container. It looks out of place, but the garden in it is even more noticeable
July 8, 2021
Nestled next to an otherwise ordinary house on Kodiak is a shipping container. It looks out of place, but the garden in it is even more noticeable. The growing area of the BrightBox Farm looks like a prop from a movie about space exploration – the vertically oriented hydroponic farm has its own perfect microclimate.
The use of this shipping box has enabled Gideon Saunders to conquer the seasons that otherwise rule Kodiak Gardens.
“There we worked with Freight Farms, who build 40-foot containers, high cubes, 2.50 m high, 2.40 m wide, standard containers, only slightly higher, very insulated, highly insulated R-28. So we agreed with them and picked out a unit and then delivered it to us, ”Saunders said.
Freight Farms made the interior of the shipping container. Inside, there are shelves with lettuce and other greens, interspersed with panels of blindingly bright ultraviolet light. A panel filled with nutrients feeds into a water tank on the back, which in turn feeds drips into the hydroponic system. The air is supplemented by a carbon dioxide tank, which ensures that the plants do not lack for anything.
The container is completely controlled by an app. And it even comes with built-in bluetooth speakers. But for the container, function is more than form – Saunders boasts that he could grow 1,000 heads of lettuce a week in less than 30 hours.
It doesn’t just look futuristic. Saunders believes systems like this will revolutionize agriculture.
“I think it’s the future. I mean, we can get into the politics of agriculture and water rights and freshwater use worldwide, and global warming and all these hot topics – 8 billion, 9 billion, 10 billion people, how do you feed them? The population is growing – how do you become more efficient with your food? Well, when it comes to vegetables and leafy greens and what we do, we use 95% less water than traditional farming. We do not use herbicides, pesticides or insecticides. So no glyphosate, no Miracle Grow. Chemically nothing bad. You can control it. So it’s the future of agriculture, ”Saunders said.
This type of production is not cheap. Saunders says the device costs around $ 100,000 with shipping and handling. But as technological advances inevitably push prices down, it becomes more cost-effective for smallholders to invest in such equipment.
And Saunders says it’s already inexpensive, although its container is complemented by a small homemade addition in its garage. He sells microgreens as a subscription service, in which he provides his subscribers with bags of greens for a monthly fee, and through sales at the local farmers’ market. Even on an island known for its horticultural and merchant shipping challenges, herbivores can enjoy fresh, locally grown produce year round.
Contain Inc Announces Finance Arrangement With Edible Beats For FarmBox Foods Container Farm
The container farm is being built and customized for Edible Beats, and will produce ingredients for all of the EB concepts, Linger, Root Down, Vital Root, El Five, and Ophelais
NEWS PROVIDED BY
July 07, 2021
Contain Inc announces a financing agreement arranged between Edible Beats Restaurant Group & a prominent lender for a FarmBox Foods container farm.
Image courtesy of FarmBox Foods
With the FarmBox Food container, we can grow hyper-local, organic, year-round produce that will be featured at all of our restaurants. We feel this is just the beginning of what we can grow”— Justin Cucci of Edible Beats Restaurant Group
RENO, NV, UNITED STATES, July 7, 2021 /EINPresswire.com/ -- Contain Inc is pleased to announce a financing agreement arranged between Edible Beats Restaurant Group and a prominent lender for a controlled-environment container farm, FarmBox Foods. Edible Beats is a locally owned Denver-based restaurant group known for its diverse menus and healthy, plant-based dishes that highlight local and seasonal ingredients. Edible Beats will be able to grow herbs, leafy greens, salad greens, and various produce organically and year-round with the container farm that will be attached to their Vital Root location.
“We have always sought opportunities to be more responsible to the sourcing, growing, and handling of the incredible ingredients that we get,” said Justin Cucci of Edible Beats Restaurant Group. “With the FarmBox Food container, we can grow hyper-local, organic, year-round produce that will be featured at all of our restaurants. We feel this is just the beginning of what we can grow, and we are eager to add the mushroom grow operation in the future”
Image courtesy of Unsplash
Edible Beats purchased the container from FarmBox Foods, a Colorado-based company that builds automated farms that grow gourmet mushrooms, leafy greens, and culinary herbs. To FarmBox, controlled-environment agriculture is the future, and this deal is one of many leading us towards a more decentralized and eco-friendly food system.
“I think we’re going to see a lot more of these types of programs going forward,” said Chris Michlewicz, Chief Public Relations Officer at FarmBox. “Restaurants are realizing that their produce is fresher and has a longer shelf life when they have a container farm on site. It’s a reliable and sustainable source of food, and it’s more eco-friendly because you no longer have to transport food in from elsewhere.”
Image courtesy of Unsplash
Likewise, Contain Inc is thrilled to support Edible Beats as it ventures into indoor ag. “We're delighted to have assisted SemiMojo and FarmBox Foods in this innovative initiative. Contain is always excited to see more fresh food made available to consumers. Customers appreciate freshness and quality produce, year round. Restaurants and container farms make this possible”, said Doug Harding, Head of Leasing & Vendor Relations at Contain Inc. “We are thrilled to have collaborated with Edible Beets and Farm Box Foods on this project. It aligns perfectly with Contain's mission of supporting the controlled environment agriculture industry in its financing needs”.
The container farm is being built and customized for Edible Beats, and will produce ingredients for all of the EB concepts, Linger, Root Down, Vital Root, El Five, and Ophelais.
About Contain Inc
Contain is out to empower the indoor ag industry of tomorrow. Our first and key mission is bringing easier and faster financing to controlled environment agriculture, but we aren't stopping there. We create platforms to move the industry forward, and most importantly, find ways to make indoor ag more accessible to farmers of all stripes.
Contact Contain:
Doug Harding, Leasing & Vendor Relations
doug@contain.ag | 760-330-1199
About Edible Beats
Edible Beats is a locally owned independent restaurant group that operates such diverse concepts as Linger, Root Down, El Five, Ophelais, and Vital Root. “Walking the walk” is important to us and the various aspects of sustainable & local food sourcing, up-cycled design, and authentic Hospitality.
About FarmBox Foods
FarmBox Foods was founded to help provide a sustainable, eco-friendly food source to places where there is a lack of access to farm-fresh produce. The company’s mission is to use container farms to decentralize the food supply chain and empower local communities.
Doug Harding
Contain Inc
doug@contain.ag
Visit us on social media:
Twitter
LinkedIn
Container Farming To Increase Food Security In The Caribbean
As part of our Grow Food Here series, join us for a live conversation with Freight Farmers, Lincoln Deal, and Latesha Gibson from Eeden Farms
Hear How Eeden Farms Is Bringing Fresh,
Local Produce To Their Island.
As part of our Grow Food Here series, join us for a live conversation with Freight Farmers, Lincoln Deal, and Latesha Gibson from Eeden Farms. Throughout the event, we’ll explore how they brought container farming to the Bahamas to reduce the island’s reliance on food imports and serve their local community with the freshest local food available. We’ll also discuss the challenges farmers face in the Bahamas, what they’re currently growing in their three container farms and their plans for the future.
At the end of the event, Lincoln and Latesha will answer your questions through the live q & a
Register Now
Wednesday, July 14th, 2021 12 PM EST
Interested In How To Start Farming?
We take you through the whole journey one step at a time. From finding customers to training to delivery logistics, we’ve got you covered.
Learn more
Get in touch!
Are you interested in learning more about how to become a Freight Farmer? Contact us for additional information on how to get started today.
Vertical Farming For The Future
Beyond providing fresh local produce, vertical agriculture could help increase food production and expand agricultural operations as the world’s population is projected to exceed 9 billion by 2050
Posted by Sarah Federman, AAAS Science and Technology Policy Fellow, Office of the Chief Scientist andPaul M. Zankowski, Senior Advisor for Plant Health and Production and Plant Products, Office of the Chief Scientist in Research and Science
Aug 14, 2018
Indoor And Vertical Farming
May Be Part of The Solution To Rising Demands
For Food And Limited Natural Resources
Imagine walking into your local grocery store on a frigid January day to pick up freshly harvested lettuce, fragrant basil, juicy sweet strawberries, and ripe red tomatoes – all of which were harvested at a local farm only hours before you’d arrived. You might be imagining buying that fresh produce from vertical farms where farmers can grow indoors year-round by controlling light, temperature, water, and oftentimes carbon dioxide levels as well. Generally, fresh produce grown in vertical farms travels only a few miles to reach grocery store shelves compared to conventional produce, which can travel thousands of miles by truck or plane.
Beyond providing fresh local produce, vertical agriculture could help increase food production and expand agricultural operations as the world’s population is projected to exceed 9 billion by 2050. And by that same year, two out of every three people are expected to live in urban areas. Producing fresh greens and vegetables close to these growing urban populations could help meet growing global food demands in an environmentally responsible and sustainable way by reducing distribution chains to offer lower emissions, providing higher-nutrient produce, and drastically reducing water usage and runoff.
Recently, USDA and the Department of Energy held a stakeholder workshop focused on vertical agriculture and sustainable urban ecosystems. At this workshop, field experts shared thought-provoking presentations followed by small group discussions focusing on areas such as plant breeding, pest management, and engineering. Workshop attendees from public and private sectors worked together to identify the challenges, needs, and opportunities for vertical farming. A report on this workshop will be released to help inform Departmental strategic planning efforts for internal research priorities at USDA and external funding opportunities for stakeholders and researchers.
We’re excited about the potential opportunities vertical agriculture presents to address food security. That’s why USDA already has some of these funding and research opportunities in place. The National Institute for Food and Agriculture has funding opportunities (PDF, 1.22 MB) that could support future vertical agriculture conferences and research. Similarly, the Agricultural Research Service is working on a project to increase U.S. tomato production and quality in greenhouses and other protected environments. We look forward to continuing our partnership with our customers, both internal and external.
Lead Photo: Photo credit: Oasis Biotech
Category/Topic: Research and Science
Tags: Office of the Chief Scientist National Institute of Food and Agriculture NIFA Agricultural Research Service ARS Department of Energy vertical farming
Freight Farms And CEO Vanzura Set To Reinvent Container Farming
June 17, 2021
The global pressures exacerbated by COVID-19 and the rippling toll it takes on the international community has made one thing clear: preparedness is everything. The Coronavirus has exposed vulnerabilities in the global health network that no one could have imagined. Food production and distribution must now reset their agendas to prepare for catastrophe.
Freight Farms, a 2011 Agtech company that pioneered hydroponics-based container farming, is committed to preparing the world for the next disaster by reinventing the way we grow food.
“Fill in the blank with the institution, how prepared are you for the emerging trends that are impacting the world,” Freight Farms CEO Rick Vanzura explained. “Sustainability issues, land availability, water availability; those issues obviously preceded COVID-19, but we think there’s going to be a greater sense of urgency around folks expecting us to have an answer and be prepared for these global trends, as opposed to being reactive.”
Vanzura looks to channel his decade of experience as a restaurant executive, growing Wahlburgers from a single restaurant to a $100 million dollar institution, as well as greatly expanding Panera Bread, to redefine food production and distribution as a whole.
Freight Farms uses container-based “vertical farming” to do just that, allowing farmers to produce hundreds of high-quality local crops from a 320 square foot shipping container which automates the farming process for maximum efficiency.
Vanzura plans to expand and distribute these self-contained, sustainable farms to a wide diversity of industry segments. The priority will of course be the global communities that need them the most. “We see the Freight Farm as a perfect fit for countries with food access difficulties, short growing seasons and inherently challenging climates. There’s probably no location where having a hyper-local, highly traceable, always available solution isn’t going to make sense in some way,” he added.
In the name of access to high-quality food, in a sustainable model built to withstand a natural disaster, Freight Farms has now distributed their automated, hydroponic farms to 48 U.S states and across the world to 32 different countries, boasting success and efficiency from the Arctic wilderness, to the desert, and to concrete jungles.
Freight Farms believes that its emphasis on access, preparedness, and sustainability will be more necessary than ever in the wake of COVID-19, as well as global trends of food insecurity and environmental uncertainty. Vanzura explained that the company has already reacted to shifting demands by supporting small-scale farmers as they set up drive-through produce stations to reach customers directly.
Freight Farms CEO Rick Vanzura
“Demand during this time for that hyper-local, fresh product has certainly ramped up,” Vanzura added. “Hopefully, once people get a taste of it, they will understand the difference, and post Covid, our containers will become an industry staple.”
Vanzura sees his role as not only expanding to agriculturally vulnerable countries abroad but also increasing access to high-quality food across institutions in the United States. He wants to specifically target universities and has partnered with foodservice provider Sodexo to ensure local food is available to as many people as possible.
Vanzura says he was forced by his children to move beyond the world of crafting a restaurant chain’s vision and use his knowledge to make the world a better place. Freight Farms, with Vanzura’s leadership, has the ability to change the way we think of farming and change the world.
Freight Farms hopes to combat international uncertainty, face the threats of climate change, and provide people with fresh produce regardless of climatic constraints and difficulties. “Healthy food is a right, not a luxury,” and Freight Farms is helping make this mission statement a reality.
Lead photo: A Freight Farms container has unprecedented environmental control and exceptional ease-of-use to unlock your growing potential.
To learn more about Freight Farms and how they are reinventing container farming, visit their website.
Total Food Service is a monthly B2B foodservice publication and website covering foodservice and hospitality news, industry trends, and exclusive interviews.
CANADA: Thursday, July 8th, 2021 - 12:00 PM EST
Sit back and learn more about Growcer's beginnings, our farm's uses, and essential considerations for starting your own Growcer project. It will be an informal opportunity to ask our team questions and learn more!
Every first Thursday of the month, we'll be hosting a Meet and Eat that anyone can join; however, we're going to have it on the second Thursday in July to accommodate for the statutory holiday on Thursday, July 1st.
Register Now →
Sit back and learn more about Growcer's beginnings, our farm's uses, and essential considerations for starting your own Growcer project. It will be an informal opportunity to ask our team questions and learn more!
SIGN UP TODAY
Thursday, July 8th, 2021
12:00 PM EST
CANADA: The Value of Hyper-Local Produce
At Yellowknife Co-op, produce is grown steps away from the store in a container farm!
The hyper-local food trend is more than just a fad: there’s a reason that hyper-local food is catching on in a big way. If you’re thinking about growing hyper-local food, it’s important to understand the value of the product and its market position.
At Yellowknife Co-op, produce is grown steps away from the store in a container farm!
BUT FIRST, WHAT IS HYPER-LOCAL FOOD?
Where does that ‘local’ head of lettuce you pick up from the grocery store actually come from? The Canadian Food Inspection Agency (CFIA) defines ‘local food’ as being grown in the province where it’s being sold, or within 50km of the border. But hyper-local food is even more local than being from the same province or being Canadian-grown. It is usually grown within the same town or city, or a short distance from where it’s being sold (sometimes even right behind the store!).
BENEFITS OF HYPER-LOCALLY GROWN FOOD
LOWER FOOD MILES
Hyper-local produce is usually grown within the same town or city, or a short distance from where it’s being sold.
As consumers are becoming more and more aware of the environmental impact of our food choices, the demand to lower food miles is also growing. A food mile can be thought of as the distance that food travels from the grower to the consumer. As a metric, it helps to assess the environmental impact of the foods we consume. A 2012 study showed that on average, 30% of food is imported in Canada, leading to annual emissions of 3.3 million metric tonnes of CO2.
Growing food hyper-locally can result in significantly lower food miles (and as few as zero food miles!) in both urban centres and rural communities. This reduces the carbon footprint of what you eat.
SUSTAINABLY GROWN
Growing hyper-locally in a hydroponic farming system has further benefits. Water in a closed hydroponic system is captured and reused, resulting in 90% less water use, and 95% less land than conventional farming.
TRACEABLE FOOD CHAIN
Growing hyper-local is completely traceable. This means you know exactly what’s going into your product. There are no synthetic pest control products, less risk for E.Coli, and a shorter supply chain to manage.
FRESHER PRODUCE WITH A LONGER SHELF LIFE
Growing food hyper-locally also means fresher produce and a longer shelf-life. Instead of wilting in a truck for hundreds of kilometers, hyper-local produce is shelf-ready immediately. This has a marked effect on the quality, as most produce loses 30 percent of nutrients just three days after harvest.
Life Water Gardens, a container garden project in Norway House Cree Nation, sells locally-grown produce at the Northern Store. Click here to learn more about the project and hear from its growers!
“When you get your hands on the fresh produce and taste it, you know it’s a good thing for your community in general. It’s really easy to get excited and pumped about [this project].” - Ian Maxwell from Norway House.
“When you get your hands on the fresh produce and taste it, you know it’s a good thing for your community. It’s really easy to get excited and pumped about [this project].”
— Ian Maxwell, co-manager of Life Water Gardens
WHERE IS HYPER-LOCAL PRODUCE POSITIONED IN THE MARKET?
For growers, it’s important to keep in mind that hyper-local food isn’t competing with foreign produce that you typically find in grocery stores. Between locally-grown vs imported food, the wholesale price for foreign produce is cheaper than local produce.
Keep in mind that grocery stores buy produce at wholesale prices, which means that they may buy produce from you at a certain cost, and then sell it with a 30% margin added to the price. When you walk into a grocery store and see produce being sold for $4.99, the reality is that the grocery store-bought it for $3.50 and added a mark up to the final price to help cover their costs of operations.
To find price-compatible products for market research in your area, look for products that will match your future products, such as living lettuce, other hydroponic greens, and other hyper-local, organic produce. Growcer greens belong in the hyper-local, value-added produce category.
GETTING STARTED WITH HYPER-LOCAL FOOD
Growing hyper-local food has many benefits: not only is it fresher, healthier, and better for the planet, it can also be a profitable investment for growers. When crafting your financial projections, keep in mind the value of hyper-local produce and where it sits in the market.
Interested in learning more about our hyper-local hydroponic growing systems? Find out more.
USA - COLORADO: Sedalia-Based FarmBox Foods Sending Container Farms All Over The World
FarmBox Foods’ short-term goals include partnering with institutions that help provide the biggest possible impact for the most people, including food banks, schools, and hospitals
Posted by Chris Michlewicz
May 28, 2021
With increasingly unpredictable weather patterns impacting crops and a continuing global food crisis affecting millions, a Colorado company is using tech-based indoor farming to make sure no one goes without a reliable, secure source of nutrient-rich food.
FarmBox Foods, based in Sedalia, has spent the last four years developing automated farms in shipping containers to grow organic leafy greens, culinary herbs, tomatoes, and now pine tree seedlings. The company also has a first-of-its-kind gourmet mushroom farm that produces around 400 pounds of mushrooms per week.
The mission-driven company is focused on helping feed those living in food deserts while empowering local communities and providing jobs and educational opportunities. FarmBox Foods’ patented vertical hydroponic watering systems use 90% less water than traditional farms and yield the equivalent of 2 – 2.5 acres of farmland. The repurposed shipping containers that house these systems can be placed virtually anywhere in the world — from island nations to college campuses to the frozen reaches of Alaska — and produce food year-round.
The fully controlled enclosed growing environment is protected from pests and pathogens, which reduces and can eliminate entirely the need for pesticides, allowing people to harvest and eat untainted farm-fresh produce. Setting up containers in or near populated areas also reduces food waste, as the food is able to get to the table more quickly and can better retain its nutritional value.
“The real mission in this whole thing is to be able to feed the world in places that ordinarily wouldn’t be able to grow food,” said Rusty Walker, CEO of FarmBox Foods.
FarmBox Foods’ short-term goals include partnering with institutions that help provide the biggest possible impact for the most people, including food banks, schools, and hospitals.
Learn more at www.farmboxfoods.com.
Posted in Arapahoe County, Douglas County, Douglas County Business, Douglas County Front, Featured, Jefferson County, South Jeffco
Tagged agtech, climatecontrolledfarming, Colorado, coloradobusiness, containerag, containerfarms, eatorganic, farmboxfoods, farmboxfoodscolorado, farming, farmtotable, fooddeserts, foodinequality, foodinsecurity, foodsecurity, growyourownfood, indoorfarming, indoorfarms, mushroomcultivation, mushroomfarm, mushrooms, organic, sedalia, urbanfarming, verticalhydroponicfarm, verticalhydroponics
About the Author: Chris Michlewicz
USA - KENTUCKY: Elliott County High School Receives New Container Farm Through AppHarvest
The curriculum provided by AppHarvest will cover topics such as high-tech growing and an introductory course on local food systems and food resiliency
May. 29, 2021
SANDY HOOK, Ky. (WSAZ) - Some students at Elliott County High School will soon be able to help grow food -- not only for themselves but for the entire region.
The Elliott County High School container farm is the fourth addition to AppHarvest’s program in 2021 and the sixth educational container farm to date.
The container farm program was launched in 2018 and demonstrates AppHarvest’s ongoing commitment to cultivating interest in high-tech farming as it seeks to create America’s AgTech capital from inside Appalachia. Each retrofitted shipping container acts as a hands-on agricultural classroom for students, allowing them to grow and provide fresh leafy greens to their classmates and those in need in their communities.
AppHarvest has opened container farms in Eastern Kentucky at Madison Central High School in Richmond; Breathitt High School in Jackson; Shelby Valley High School in Pikeville; and Rowan County Senior High School and AppHarvest’s flagship farm at Rockcastle County High School in Morehead.
Elliott County High School’s container farm includes space to grow up to 2,760 seedlings and 2,960 mature plants, all at once in a nutrient film technique (NFT) system. NFT is a water-saving system in which plant roots are continuously fed all necessary water and nutrients by a shallow stream, also called “film.” Excess water drains to a holding tank and is then recirculated. This system of high-tech growing sets the Elliott County container apart from AppHarvest’s other educational containers, which have operated hydroponically and vertically.
“One of our goals at AppHarvest is to build an AgTech capital right here in Appalachia,” said Jonathan Webb, AppHarvest Founder, and CEO. “We want to see communities across the region use technology to bring farms to life. And in five years from now, it’ll be leaders from these very programs coming to us with ideas on how we continue to evolve and change agriculture.”
Makayla Rose, Elliott County High School agriculture teacher, will lead the newest container program.
The curriculum provided by AppHarvest will cover topics such as high-tech growing and an introductory course on local food systems and food resiliency.
“This is exciting. Some students who might not like to get in the dirt have a different way of growing vegetables,” said Garret Barker, president of Elliot County’s FFA chapter. “It’s different than my farm at home. It doesn’t depend on outside factors like the rain. It’s all controlled by an app.”
Lead Photo: Elliott County High School receives new container farm through AppHarvest (Kimberly Keagy/ WSAZ)
Brick Street Farms Expands Through Florida and East Coast
“We really wanted to bring food production to the point of consumption, so we’re focused on embedding our farms in urban areas,” says Shannon O’Malley, CEO, and co-founder of Florida-based container farming company, Brick Street Farms
"We Are As Much A
Technology Company
As We Are A Farm Operator”
“We really wanted to bring food production to the point of consumption, so we’re focused on embedding our farms in urban areas,” says Shannon O’Malley, CEO, and co-founder of Florida-based container farming company, Brick Street Farms.
The company was founded by Shannon and her husband Bradley, who combined her expertise in electrical engineering with his background in software development to design their own shipping container farms.
According to Shannon, a major differentiator of Brick Streets Farms is that the company manufactures and operates its own shipping container farms.
Brick Street Farms Hubs
Brick Street Farms has recently secured a significant investment from Lykes Brothers, which is reportedly one of the largest and longest-running private agricultural companies in the United States. During the official announcement last week, the financial investment will be used to aggressively expand Brick Street Farms hubs, which are the combination of container farms with a retail front in densely populated areas.
Click here to Zoom the photo. (Photo courtesy of Brick Street Farms)
According to Shannon, this expansion will begin in west-central Florida then expand to the east coast. From these hubs, Brick Street Farms will also introduce home delivery and will support restaurant partners located within 50-100 miles of the hubs. Already in 272 Publix supermarkets, Brick Street Farms will continue this partnership and plans to expand into additional product categories.
Building a resilient, multi-channel sales strategy
Brick Street Farms was first developed in 2015, and during its early years, the company predominantly sold its products to restaurants and directly to customers. However, the pandemic-induced shutdown in 2020 resulted in the loss of 70% of Brick Street Farms’ clients due to restaurant closures. As Shannon explains, Brick Street Farms was already selling its products in the GreenWise section at Publix supermarkets, which is reportedly the largest employee-owned supermarket chain in the US. This partnership allowed Brick Street Farms to quickly pivot following the mandated closure of restaurants.
“In the same month that Florida went into lockdown, grocery stores saw an incredible jump in demand so we were able to quickly pivot and provide our vegetables to grocery stores within a week. We are currently in 272 Publix stores and are working to expand into west-central Florida,” says Shannon. The state of Florida has since reopened and Brick Street Farms was able to bring back its previous accounts and sign new ones, according to Shannon.
Brick Street Farms also has its own gourmet market located at the farm that is open six days per week. Consumers can shop either on-site or online, with contactless delivery available. Shannon also explains that the company has adopted a unique twist to community-supported agriculture. By subscribing to a farm membership, consumers receive a discount and support the recently approved non-profit, Desert Farms Foundation.
“We established Desert Farms Foundation to help us bring container farms to food deserts within the United States. With a farm membership, 1% of the proceeds go to Desert Farms Foundation to really support community agriculture,” explains Shannon.
Thrive Containers
“Our containers are under the name Thrive Containers, which is wholly owned by Brick Street Farms. Our containers are the equivalent of 2-3 acres of traditional farmland. They use very little water, are energetically efficient, produce very little waste and use no chemicals. Since our products are wash-free, our customers get the benefits of long-lasting produce,” explains Shannon.
According to Shannon, Brick Street Farms is as much an agtech company as it is a farm operator. The company decided to establish Thrive Containers as its own entity within Brick Street Farms in order to differentiate between the food production and manufacturing aspect of the company. “When people see Brick Street Farms, we want them to think of butterhead lettuce, basil and our other vegetables,” notes Shannon.
Thrive Containers does not sell its container farms to third parties, but instead continuously improves the farm design for current and future installations. As Shannon explains, the company focuses on designing intelligent systems that can adjust to indoor and outdoor environmental conditions. Thrive containers have more than 120 sensors in and around the farm to monitor and respond to ambient temperature, humidity, carbon dioxide, vapor pressure deficit, etc.
Brick Street Farms and Thrive Containers work closely, with the engineers and designers having all undergone farmer training to ensure that the systems designed truly respond to the needs of Brick Street Farms’ growers.
Why Florida?
While warm and sunny Florida may seem ideal for outdoor agriculture, Shannon explains that soil conditions make soil-based agriculture somewhat difficult. She says that Florida soils are rather degraded and sandy, lack nutrients and lack natural bacteria, meaning farmers need to spend significant time and effort on rebuilding soils. Also, water sources are highly saline because of our position at level, near the coast, and with a low water table. Finally, the lack of winter makes it difficult to regulate pest cycles.
Lead photo: Co-founders Brad Doyle and Shannon O’Malley
For more information:
Madeline McNaughton, Head of Business Development
Brick Street Farms
madeline@brickstreetfarms.com
www.brickstreetfarms.com
Publication date: Thu 27 May 2021
Author: Rebekka Boekhout
© VerticalFarmDaily.com
USA: Vertical Field Signs Agreement To Provide Vertical Farms of Fresh Vegetables To Senior Living Homes In California
Vertical Field has developed and commercialized unique soil-based, vertical farms that operate in 20 and 40-foot containers that produce freshly harvested and pesticide-free produce
Company To Deliver Unparalleled Produce Quality Via
Freshly-Harvested On-site Vertical Farms in 8 Calson
Management Nursing Homes Across The State
News & Photos by: Vertical Field
May 26, 2021
RA'AANA, Israel, May 26, 2021 /PRNewswire/ -- Vertical Field - ("VF" or the "Company"), a global ag-tech company that develops vertical farming systems, has signed an agreement with Calson Management to supply assisted living homes with on-site vertical farming units. According to the agreement, Vertical Field will provide a demo unit to the Glen Cove senior living lodge in Vallejo, California, and after a successful pilot will expand to seven other centers.
Vertical Field has developed and commercialized unique soil-based, vertical farms that operate in 20 and 40-foot containers that produce freshly harvested and pesticide-free produce. The VF indoor farms are capable of growing a variety of fresh greens and other crops year-round with no seasonality barriers while minimizing supply chain logistics and storage, eliminating the need for transportation, and minimizing inventory losses.
Vertical Field's urban farms use 90% less water and 30 times less land than conventional farming methods. Each portable unit is made up recycled shipping containers that grow produce in controlled conditions. Advanced sensors and monitors, climate control technology, and state-of-the-art lighting create the optimum conditions for crops to grow quickly and efficiently year-round, regardless of the weather.
The Company provides vertical farming for supermarkets, restaurants and multi-site facilities in the United States, Ukraine, United Arab Emirates, Israel, Russia, and others.
"We are very excited to launch our first partnership with an assisted living center, providing senior citizens freshly harvested, high-quality produce grown right outside their residence" says Guy Elitzur, Vertical Field's CEO. "This partnership supports our values of ensuring that nutritious produce reaches the homes of all people- no matter where they live. We look forward to continuing to expand to many other assisted living centers, and to making delicious and quality food accessible to senior citizens and other marginalized communities throughout the world."
About Vertical Field: Vertical Field is an ag-tech company that develops innovative and proprietary vertical growing systems for the urban environment. Our urban farms make efficient use of city space by growing crops vertically and on-site, bringing healthy, fresh, and local produce all the way to the consumer.
About Calson Management:
Calson Management provides a full suite of services and solutions for every aspect of a Senior Living project, and is committed to excellence in providing personal services in a warm, loving, and supportive environment. The Reyes family (partners and managers) have been involved in Senior Living for more than 30 years, and is dedicated to creating unique, specialized communities for seniors throughout California. Our family and our team members work to provide safe, engaging, and comfortable communities.
"Enhancing the health and wellbeing of our seniors is a priority at Calson Management, which is why partnering with Vertical Field to supply senior living homes with fresh, nutritious, and on-site produce was a natural decision. By bringing the farm all the way to our residents, seniors can see where the food grows and enjoy high-quality produce, furthering a living home's ability to create a happy, safe, and comfortable community." – Jason Reyes, Principal, Calson Management
For further information https://www.verticalfield.com
News & Photo Source: Vertical Field
USA - FLORIDA: St. Pete’s Brick Street Farms Gets Multi-Million-Dollar Investment From Lykes Bros
Lykes Bros., one of the oldest and largest agribusinesses in Florida, is putting a big bet on the future of farming as it invests in Brick Street Farms, an urban farm, and market in St. Petersburg
May 20, 2021
Photo credit: Brick Street Farms
Lykes Bros., one of the oldest and largest agribusinesses in Florida, is putting a big bet on the future of farming as it invests in Brick Street Farms, an urban farm and market in St. Petersburg.
Lykes is making a “significant” investment in Brick Street Farms, the two companies announced at a news conference Thursday. The amount of investment was not disclosed, but a news release described it as “multi-million dollar” investment. Lykes will take a 20 percent ownership stake in Brick Street Farms because of the deal, Mallory Dimmitt, vice president of strategic partnerships at Lykes, told the St. Pete Catalyst.
Brick Street Farms will use the investment to accelerate the expansion of Brick Street Farms hubs, an all-inclusive onsite farming and retail shopping experience in urban cores, said Shannon O’Malley, founder and CEO. The company has self-contained, environmentally sustainable THRIVE containers that will be placed in each hub. Each hub will grow between 16 to 20 acres of farmland on one-third acre lots.
Mallory Dimmitt, vice president at Lykes Bros., announces investment in Brick Street Farms while Nikki Fried, Florida Ag Commissioner, looks on.
The first new hub will open in St. Petersburg’s Warehouse Arts District in late 2021, with an expansion to Tampa in early 2022 followed by more hubs on the east coast, O’Malley said.
“We are the future of farming, and our new investors have the perfect expertise to help us take our successful business model in sustainable farming to feed more people healthy food,” O’Malley said.
The two companies first connected in November at the Florida-Israel Agriculture Innovation Summit, hosted by the Florida Department of Agriculture and Consumer Services, said Nikki Fried, Florida Department of Agriculture Commissioner.
The collaboration meets several goals, including feeding people in urban locations, fighting urban food deserts and food insecurity, bringing farm-to-fork produce closer to people and bringing cutting edge agriculture technology to everyone.
From left, Tampa Mayor Jane Castor, St. Petersburg Mayor Rick Kriseman and Shannon O’Malley, founder and CEO, Brick Street Farms
Brick Street Farms is a hub of innovation and creativity and is the only female-founded and led company in the vertical farming industry, said St. Petersburg Mayor Rick Kriseman. He also highlighted the work of the company’s non-profit Desert Farms Foundation.
“Not only is Brick Street Farms working to make us healthier by providing us some of the best and freshest food around, but through its 501c3, Brick Street Farms is working to end food deserts through the Tampa Bay area,” Kriseman said.
Every urban environment struggles with food deserts, said Tampa Mayor Jane Castor.
“The problems that occur from those food deserts are often times for many communities insurmountable. This is a solution to so many problems,” Castor said.
She also praised the company’s business model. It is financially successful by providing produce to a number of restaurants, Castor said.
While an urban focus might seem like an unusual fit for company like Lykes, which owns hundreds of thousands of rural acres throughout the state, “We know from our experience that innovation is what moves the agriculture industry forward,” said Dimmitt, who will join the Brick Street Farms board of directors.
“In addition to innovations in sustainable production and the technology it uses, the job opportunities and related job training and skills are key to Florida’s future and to our health and wellness,” Dimmitt said. “What could be better medicine than high-quality nutrient-dense greens grown close to the consumer where they have direct access, all while creating community.”
Brick Street Farms, at 2233 3rd Ave. S. was founded in 2016 by O’Malley and her husband, Brad Doyle. Read more about O’Malley in St. Pete Catalyst‘s Hustle profile.
CubicFarm Systems Corp. Appoints Technology Industry Executive Janet Wood to the Company’s Board of Directors
Janet Wood is recognized globally as a leader in the technology sector and as a successful executive who retired from a rewarding career with several major technology companies including IBM, Crystal Decisions, Business Objects, and SAP
VANCOUVER, B.C., May 14, 2021 – CubicFarm® Systems Corp. (TSXV:CUB) (“CubicFarms” or the “Company”), a local chain agricultural technology company, announced today that Janet Wood has been appointed to the Company’s Board of Directors.
Janet Wood is recognized globally as a leader in the technology sector and as a successful executive who retired from a rewarding career with several major technology companies including IBM, Crystal Decisions, Business Objects, and SAP. Her success in building global channel partnerships and alliances with leading technology companies will bring invaluable insight to CubicFarms’ Board of Directors.
“It’s clear that the automated indoor growing technologies developed by CubicFarms will empower farmers to grow produce and livestock feed locally, directly addressing critical food security issues,” said Wood. “CubicFarms’ unique patented technologies use less land, less water, and no pesticides or herbicides, using our natural resources respectfully and sustainably.”
“We’re thrilled to welcome Janet Wood, a strong Canadian technology leader, to our Board of Directors. Janet is a trailblazer in the tech industry and an influential leader within every organization fortunate enough to benefit from her vision and expertise,” said Jeff Booth, Chair, CubicFarms. “Her significant experience with large software and technology companies will help CubicFarms continue to grow, innovate, and expand internationally.”
“Janet has been instrumental in contributing to the impressive growth of several large multi-national tech giants like SAP, and her experience will be critical as we enter into the high-growth phase of our business in 2021 and beyond,” said Dave Dinesen, CEO, CubicFarms. “Janet is a proven leader and the exact type of person we need to guide our company as we scale our business globally.”
After joining SAP in 2008, Wood's executive roles included Global Human Resources leader for the Office of the CEO, Global Head of Talent and Leadership, Executive Vice President (EVP) of Global Strategic Partners, and EVP of Global Maintenance Go To Market. At Business Objects, she worked as Senior Vice President of Global Partnerships. Wood also served as Vice President of Business Development at Crystal Decisions and held various management positions during her 16-year tenure at IBM. Wood holds a Bachelor's degree in Business Administration from the University of Alberta, graduating with distinction.
Wood has been recognized with a YWCA Women of Distinction Award and is a past recipient of the Canadian Women's Executive Network Top 100 Women Award.
An active member of the technology community and known for her leadership skills, Wood served for a year as the interim President and CEO of Science World shortly after retiring from SAP in 2019. Science World is a world-class science centre in Vancouver, B.C., that typically welcomes
over 800,000 visitors annually and connects with an additional 140,000 students throughout B.C. to advance STEAM learning for science, technology, engineering, the arts, and mathematics.
Wood is active in her community as a partner in B.C. Social Venture Partners, a not-for-profit organization that supports children and families at risk. She is a Board member of ICBC, Pureweb Technologies, and Junior Achievement of B.C. She sits on the University of Alberta Business School Advisory Committee and is the Canadian Regional Member Engagement Officer for Young Presidents Organization – Gold.
Wood will replace John de Jonge, a founding member of the Company’s Board of Directors. He will continue providing guidance in a different capacity by joining the Company’s newly-formed HydroGreen Business Advisory Board.
“We would like to thank John for his many years of service and contributions to the Board of Directors,” said Dinesen. “The HydroGreen Business Advisory Board will benefit from his significant agriculture and dairy experience with Artex and his commitment to our automated indoor growing technologies for farmers and ranchers to produce fresh, nutritious green livestock feed for their animals.”
About CubicFarms
CubicFarms is a local chain, agricultural technology company developing and deploying technology to feed a changing world. Its proprietary ag-tech solutions enable growers to produce high quality, predictable produce and fresh livestock feed with HydroGreen Nutrition Technology, a division of CubicFarm Systems Corp. The CubicFarmsTM system contains patented technology for growing leafy greens and other crops onsite, indoors, all year round. CubicFarms provides an efficient, localized food supply solution that benefits our people, planet, and economy.
For more information, please visit www.cubicfarms.com
. On behalf of the Board of Directors
“Dave Dinesen”
Dave Dinesen, Chief Executive Officer
Neither the TSX Venture Exchange nor its Regulation Services Provider (as that term is defined in the policies of the TSX Venture Exchange) accepts responsibility for the adequacy or accuracy of this release. Certain statements in this release may constitute “forward-looking statements” or “forward-looking information” within the meaning of applicable securities laws. Forward-looking statements are not guarantees of future performance and actual results may vary materially from those statements. General business conditions are factors that could cause actual results to vary materially from forward-looking statements.
Media Contact:
Andrea Magee
T: 236.885.7608
E: andrea.magee@cubicfarms.com
Investor Contact:
Tom Liston
T: 416.721.9531
E: tom.liston@cubicfarms.com
Squamish Nation Grows Plans For Food Security With A Hydroponic Farm
While the outside of this 40-foot container is rather striking, it’s what’s on the inside that counts. 🌱
While The Outside of This 40-Foot Container Is Rather Striking,
It’s What’s On The Inside That Counts. 🌱
May 19, 2021
By: Elisia Seeber
A big bright orange container has just landed in the Sḵwx̱wú7mesh Úxwumixw (Squamish Nation) community of X̱wemelch'stn in North Vancouver.
While the outside of the 40-foot container is rather striking, it’s what’s on the inside that counts.
The container is a Growcer hydroponic modular farm that will support the community's wellness by allowing them to grow a year-round supply of fresh produce, including leafy greens, herbs and traditional medicinal plants.
Creating a sustainable healthy source of produce and increasing food sovereignty has long been a goal for the Squamish Nation, and the hydroponic farm is another piece of the puzzle, said Kelley McReynolds, director of Squamish Nation’s Ayás Méńmen Child and Family Services.
“Part of the reason that we started to look at ways that we could [provide food] was working from our values as Squamish people and our values around food sharing,” she said.
“Traditionally, we as a community, and as families, would go out and hunt and we would gather out on the lands and the waters and we’d bring it back to our community and people would only take what they need, and the rest of it would be shared.”
Through the launch of a food distribution program about four years ago, McReynolds said the team began breaking down the stigmas and fears around food insecurity and shifting back to their traditional ways, to ensure everyone in the community felt comfortable receiving food.
“We didn't want to look at the food as being a form of charity, or only for those who don’t have food,” she said.
Hydroponic farm idea sprouts
When the COVID-19 pandemic hit, McReynolds said food security worries increased for some members and the team started thinking further outside of the box about how they could address future food scarcity.
That’s when the idea for the hydroponic farm sprouted.
Squamish Nation has looked at more traditional styles of farming, and also has 19 garden boxes set up outside of their office where they grow fruit and vegetables and a traditional medicine garden.
“We plant every year and we harvest that to give to community,” McReynolds said. “We do a lot of training with our youth and our families to help them understand the plants, gardening and harvesting."
She said a thought they always had was, “think what we could do if we had farmland, we could feed so many more people.”
“But, you know, we live in a city and you don't have access to that kind of open space,” McReynolds said.
“So, when we looked at this option of the hydroponic farm and saw that it's the size of a shipping container, we thought, ‘that's pretty cool.’ It comes with all the equipment you need inside there. And, you can get it set up and within five to six weeks you are ready to make your first harvest and it yields approximately 450 heads of produce per week. That's a lot.
“We thought, ‘wow, that's amazing.’”
The founders of the ingenious technology and social enterprise came up with the idea based on their firsthand experience of food insecurity in Nunavut in 2015 and wanted to create a system that allowed communities to grow fresh produce anytime, anywhere, in any climate.
The growing technology was first deployed in food insecure, remote communities, but has since expanded to partner with schools, non-profits, and non-remote communities who see value in growing food locally – like Squamish Nation.
The electronically run hydroponic farms cost around $180,000 to set up and will produce fresh food for around 30 years, according to Growcer.
How does the modular hydroponic farm work?
Hydroponics is a soil-free growing method that uses nutrient-rich water to grow plants using less space, time, and crop inputs.
“The modular farms are automated to provide full environmental control,” Growcer’s website states, adding that plant growth factors such as light, nutrients, temperature, humidity, carbon dioxide, and water are monitored in real-time.
Once set up, a range of 140 leafy green plants can be grown in as little as six weeks.
“It's all brand new to us,” McReynolds said, adding that Growcer would be training staff this week and continue to provide support through their hydroponic farming journey.
“We’re all really excited.”
Squamish Nation to open Food Pantry and Community Kitchen
Produce from the new farm will be shared with families serviced by Ayás Méńmen, the youth centre and the future Smeḵw'ú7ts (Food Sharing) Community Kitchen and S7ílhen (Food) Pantry, which is hoped to be up and running by the summertime.
“We will continue to do monthly food distribution, but we will also have food on our shelves and in the freezers for any of our members who are in need … whatever the situation may be,” McReynolds said.
The hope for the community kitchen is to build a healthy community by providing a safe place for members to learn and improve their food preparation and cooking skills through workshops, which may start on Zoom during the pandemic. Ayás Méńmen also plans to host a six-week program for community members to meet once a week to cook and take a meal home for their families.
“I think what excites me about that is we are such relational people,” McReynolds said. “To be able to come together and learn and share and grow and laugh and tell stories, that's so healthy and therapeutic and it brings joy to your heart just being able to be together.”
While there’s still a bit of work to be done before the hydroponic farm starts producing the goods, McReynolds has more big plans.
“I have this vision of us being able to do a Friday night or Saturday afternoon market where we can have the fresh produce, we can have music, we can maybe have food trucks and we can gather together,” she said.
“I just think it's just a great opportunity for us to celebrate who we are as farmers and come together as a community.”
Elisia Seeber is the North Shore News’ Indigenous and civic affairs reporter. This reporting beat is made possible by the Local Journalism Initiative.
Modular Hydroponic Growing Spaces In Freight Containers For Local Food Production
Freight Farms’ design was the first containerized vertical growing environment using hydroponic technology
May 17, 2021
Southeastern Pennsylvania Correspondent
A Massachusetts company has developed a unique, hydroponic growing environment in closed 40-foot freight containers that are being used world-wide to grow produce in areas with bad soil or weather conditions not conducive to outdoor growing.
Bay State natives Jon Friedman and Brad McNamara were developing rooftop greenhouses in the early 2000s when they realized a modular, hydroponic container might be a more viable solution.
Hydroponics wasn’t something new. Historians believe this soilless gardening can be traced back to hanging gardens of Babylon in Iraq built by King Nebuchadnezzar about 600 BC. Nutrient-rich water was pumped to the gardens from the Euphrates river to sustain its plants. A water-based growing thread continued through history and in the 1930s a University of California scientist, William Gericke, coined the term from the Greek word “hydro” (water) and “ponics” (work).
Friedman and McNamara, who were building outdoor, roof-based gardens on older residential buildings, looked outside the box, and turned their focus to widely available shipping containers.
They thought they could provide the equivalent of 2 acres of growing space in traditional 40-foot-by-8-foot containers and extend growing seasons year-round everywhere — especially in areas that couldn’t support traditional outdoor agriculture or in parts of the world affected most by climate change.
They named their company Freight Farms and placed their first container less than a decade ago. Now the concept is catching on worldwide.
View Photos From Freight Farms
Freight Farms’ design was the first containerized vertical growing environment using hydroponic technology. It was initially funded by a Kickstarter campaign in 2012, where they raised the funds to build a prototype to allow local food production to be available to everyone, anywhere.
The first commercial unit was installed at Boston Latin School, the oldest public school in the U.S., to produce fresh produce for the school cafeteria as well as serving as a teaching classroom for high school students.
“The company has placed 350 units in 48 states and 32 foreign countries,” Friedman said.
The company also introduced proprietary software called “farmhand” to help automate many farm processes, and is manufacturing its 10th generation container, the Greenery S, incorporating the latest technology and automation for vertical, hydroponics growing.
Growing Strong
Hydroponic Operation Supplies High-End Restaurants
Art Petrosemolo, Southeastern Pennsylvania Correspondent
Although the Freight Farms container units are capable of growing a variety of produce, leafy greens are its specialty and the best choice for farmers looking to sell their harvests year-round.
Containers also have been embraced by educational institutions to supply fresh vegetables for cafeterias and serve as learning and teaching space.
St. Joseph College in Standish, Maine, has been operating a Freight Farms unit for years to both supply fresh vegetables to its dining facilities as well as for student employment.
The site also has been a tool for community involvement with St. Joseph students working with a town Institute for Local Food System Innovation utilizing the Freight Farms container in partnership with a large hydroponic farm and commercial processing kitchen for events and agritourism.
With a decade head start in the business, Freight Farms does not have major competition in hydroponics container gardening production, although, in recent years, it has seen significant growth in multiple indoor soil- and water-based farming formats including warehouses, greenhouses and pods that are addressing growing produce year-round.
Climate change has increased concern about food production for growing populations worldwide with extreme weather conditions and higher levels of carbon dioxide in the atmosphere.
Friedman and McNamara have always been aware that the challenge to expansion for stand-alone, container gardening is the cost of power and each new rendition of their growing units has addressed both power consumption and automation to be more efficient.
Their latest Greenery S model uses growing lights that are 50% more efficient than previous models and the technology allows farmers to choose pre-set growing modes to maintain higher yields — 20% higher than earlier models — while prioritizing energy use.
Addressing affordable and clean power for customers, Freight Farms recently partnered with Arcadia, a Washington, D.C., energy company to offer affordable, renewable power options for customers.
Going forward, Friedman said growing container units will continue to become more efficient, allowing owners to increase their growing yield while having more control of their energy use to power the unit.
Slide Show Photos:
Lights and plant arrangements in Freight Farms new Greenery S model container.
Photo provided by Freight Farms
Leafy greens grow in Freight Farms’ own Greenery Farm container.
Photo provided by Freight Farms
This Freight Farms container is ready for shipment.
Photo provided by Freight Farms
Freight Farms' containers under construction in their Vermont facility.
Photo provided by Freight Farms
Lexy Basquette, Freight Farm’s on-site farmer, checks on some of her growing plants.
Photo provided by Freight Farms
Greenhouses, Vertical Farming and Urban Ag: Controlled-Environment Agriculture Has Growth Potential
Paul Post, New York Correspondent