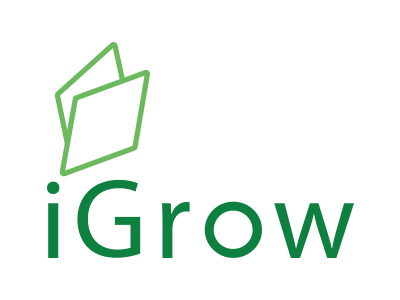
Welcome to iGrow News, Your Source for the World of Indoor Vertical Farming
AUSTRALIA - VIDEO: Shipping Container Farm Teaching TAFE Students More Than Just Agriculture
Nestled beside a building on a TAFE campus in Toowoomba is an ugly metal shipping container, but it's no ordinary storage shed
August 16, 2021
By Lucy Cooper
Nestled beside a building on a TAFE campus in Toowoomba is an ugly metal shipping container, but it's no ordinary storage shed.
Key points:
TAFE is using a shipping container farm to teach students about alternative farming
All features of the farm are controlled by an app
Agriculture, hospitality, and IT students are using the "grow pod" in their studies
Step inside and it's bursting with greenery.
Packed floor to ceiling with vegetables and herbs like basil, kale, mint and mustard, this state-of-the-art modular farm is changing the future of agriculture, all with the push of a button.
TAFE Queensland school manager Elaine Wallace said the "grow pod" aimed to change students' perspectives on traditional farming.
"Often when people think about agriculture, they think, 'Oh, I don't want to go stand in the sun all day picking vegetables, that's a bit too dirty for my liking," Ms. Wallace said.
"This is just one of those technologies that really enables students to get involved in something different and something up and coming."
Student Kallia Stebbins said when she first saw the vertical farm she was amazed by the technology.
"I didn't realise that you can grow crops like this, compared to just out in the middle of a field," she said.
"Now that I've seen this, it's very cool. I'm very interested to learn more about it."
A farm controlled from the palm of a hand
The container farm is controlled remotely with an app.
To switch the lights on inside, Ms Wallace simply whips out her phone.
"If we have a look at our monitors, it tells us that our irrigation cycle has started up, so we can set the cycle to however long or short we need it," she said.
"It's drip irrigation from the top filter through to the bottom and it's caught in the gutter that is at the bottom.
"We have pumps that will feed nutrients into the water and then, of course, we've got our lights, which are LED lights, and they are also set on a timer, so they are grow lights."
'Absolutely no limits'
It's not just agricultural students reaping the benefits of the multidisciplinary project.
Information technology students studied the app controlling the farm, while electrical students looked at how the farm kept running.
Hospitality and cookery teacher Nev Siebenhausen said his students also gained valuable first-hand experience in paddock to plate catering.
"For our students, it's a great opportunity to obviously shorten up the duration and travel on the product," he said.
"It's great for our guys to see different ways it can be grown."
Mr Siebenhausen said the walk up the hill from the grow pod to the hospitality school reduced carbon miles and cut waste by 70 percent for produce like basil, which had a short lifespan.
Any leftover produce is donated to the food relief charity, Oz Harvest.
Talks are also underway to trial sensory herbs for community service students to study the calming effects on people.
"The possibilities are endless," Ms. Wallace said.
USA: VIDEO: Veteran Finds Peace, Purpose In Unique Kind of Farming
John Miller's routine may seem a bit "scaled-down" compared to his former life as a combat soldier. Miller spends much of his time in a 40-foot-long shipping container converted into a hydroponic farm field. Hydroponics involves growing plants without soil.
KENTUCKY
August 2, 2021
LOUISVILLE, Ky. — As John Miller prepared to leave the Air Force, the combat veteran admits he had no idea what he was going to do next.
What You Need To Know
John Miller served 14 years in the Air Force
The Louisville resident is the owner of Falls City Farms
Miller has found peace and purpose in hydroponic farming
In the future, Miller hopes to expand and employ fellow veterans
John Miller's routine may seem a bit "scaled-down" compared to his former life as a combat soldier. Miller spends much of his time in a 40-foot-long shipping container converted into a hydroponic farm field. Hydroponics involves growing plants without soil.
A close-up of Miller's baby kale. (Spectrum News 1/Jonathon Gregg)
“In essence, we sell a lot of things what we would consider baby," Miller explained. Little white turnips is just one crop of many growing inside Falls City Farms. “Right now I’m just pulling off the plug to turnips and then clean up any of the leaves."
The Iraq War combat veteran grows, prunes, packages, and sells a variety of greens to Louisville restaurants, online and at local markets.
“Here is our wasabi arugula, this is one of our fresh herbs, our dill, this would be our romaine trio," Miller said while touring his indoor farm.
Scaled-down? Maybe, but the hydroponic farm has helped Miller overcome what can be a sizable challenge for soldiers adapting to life after service.
“I got into this post-military, trying to find my next thing because I didn’t know what I was going to do when I got out," Miller said.
Miller served 14 years in the Air Force. His wife Amy is still active with 17 years to her credit. In his pursuit to figure out the next chapter of his life, Miller learned about hydroponic farming from a marine veteran in San Diego.
Falls City Farm grows a lot of produce in just 320 square feet. (Spectrum News 1/Jonathon Gregg)
His operation encompasses 320 square feet and boasts 6,600 individual plant spaces. Crops grow thanks to a sophisticated watering system and good-old-fashioned artificial sunlight.
“Because we are in a shipping container, the plants and the crops don’t get any of the big yellow sun outside so we have to create that inside," he said. "So we do LED lighting because it is better from an energy standpoint as well as heat."
Miller has lots of time and enough room to think about his life as a soldier and his new career as a farmer.
“If I am being frank with you, I miss being surrounded by other airmen and folks I used to lead," he said. "But it is calming to be in here with the plants and at the end of the day, that’s one of the reasons I chose this path.”
He was after peace and a purpose, and now his purpose includes bringing other veterans aboard.
“A lot of veterans, as we know, suffer from trying to find that next mission. Hopefully, one day soon be able to bring fellow veterans in here to teach them the art of farming through hydroponics to help them find peace and purpose as well," Miller said.
At first, Falls City Farms may appear to be a small operation, it’s only until you spend time on the inside do you see all the big ideas growing.
“I fell in love with the sense of a day’s accomplishment of work, a sense of comfort of being inside a greenhouse," Miller said.
Crazy Poet Discovers Solution To Vertical Farming Challenges
How on earth are we going to be able to make vertical farming a viable solution without disrupting the cities we live in
August 10, 2021
Lawrence Ip
Facilitating Workforce & Leadership Transformation Through Organisational Governance.
Keep Reading & The House Gets Bulldozed!
Dramatic I know (it's just one of those things). Nope, I won't be making myself homeless as I do actually need a roof over my head. What I also need is to get this crazy idea off my chest before I do actually lose my mind.
You see, I was watching a documentary a while back, about future cities, off the back of a few others that were about farming, global warming and the looming food crisis, and they got me thinking about vertical farming, and the issues the industry sector faces - namely scale.
That was the first thing that struck me.
How on earth are we going to be able to make vertical farming a viable solution without disrupting the cities we live in it, why heck, according to Pew Research world population is pitted to hit 10.9 Billion by 2100, with more and more folks migrating to cities. This begged a flurry of questions such as:
How are we going to feed everyone, and where on earth are we going to put the vertical farms that are supposed to feed them?
Will they really be able to provide the quantity of fruit and vegetables sustainably?
How much will they cost to build?
How much will they cost to run and maintain?
How do we store, pack and deliver the product?
What infrastructure does it require to make it work?
What about the effect on traffic?
What about the load bearing issues of weight on the structure of the farm, the actual building?
How on earth do we face the challenges facing vertical farming?
Don't get me wrong, I see incredible value in vertical farming and it could prove to be the answer to so many of the challenges we face ahead, because as we all know the way in which we produce the food we consume, and waste, is just not sustainable - not in the slightest. The globe's arable land is fast diminishing, and at the current rate the entire globe will be facing starvation soon after 2060 - it's a travesty just waiting to happen (if you haven't watched it yet I can highly recommend watching), Kiss The Ground, it's the documentary that got me started on the quest for answers.
A few weeks ago I woke up in the middle of the night, I had an epiphany.
Prior to going to sleep, I asked myself, what is the single most pressing problem you could solve that would provide the best bang for the buck?
When I woke from that sleep the answer came to me, it came down to answering the last question, which fundamentally is a design question.
Having previously watched a documentary series on super-structures, and thinking about logistics and transportation, it dawned on me that it was not a, how on earth question, but rather a let's go to sea proposition.
I jotted down these two words on the trusty notepad I keep bedside...
"... container ships."
That's right, container ships!
Don't be fooled into thinking that what you see is what you get. What you see on the top deck is just part of the picture, container ships have just as much, if not more storage in their lower decks.
It was like WOW! It makes complete and total sense, well at least to me it does. Let's outline the reasons why container ships could be the perfect vertical farm.
Container ships are designed to bare the types of load required in the design of a vertical farm.
You can move container ships around.
Container ships can have desalination plants built in.
They are freaking massive.
They can be even more massive. Fun fact: when the size of a ship is doubled, it increases the surface area by only 25%.
Transportation logistics is a non-issue.
No need to reinvent the wheel. It wouldn't take much to repurpose container ships that have been decommissioned.
Repurposed ships equals no scrap metal.
Access to the energy required to run them is at hand.
Image Credit: Bernd Dittrich - UnSplash.
That pretty much sums it up, and hey, I'm no expert, but yes, I am a poet, and it really doesn't matter whether I'm certifiable or not, I have at the very least put the idea out there. All I ask of you, is that before you send the men with the straightjacket around, that you consider the idea as a viable solution before discarding it. If anything I hope it provides some inspiration, maybe a spark of some out-of-the-box thinking of your own and I sincerely hope you found the read entertaining too. Thank you for making it this far. I'd love to hear your thoughts and ideas. Do you have a crazy vertical farming solution you'd love to get off your chest? Please feel welcomed and leave your thoughts below. Peace ✌
Image Credit: Bailey Mahon - UnSplash.
#verticalfarmingchallenges #arablelandcrisis #foodcrisis #circulareconomy
Lead photo: Image Credit: Torben - UnSplash.
Published by: Lawrence Ip
Crazy Poet Discovers Solution To Vertical Farming Challenges. hashtag#verticalfarming hashtag#containerships hashtag#crazypoettimes hashtag#sustainability hashtag#agriculture hashtag#environment hashtag#innovation hashtag#climatechange hashtag#circulareconomy hashtag#design hashtag#energy hashtag#arablelandcrisis hashtag#foodcrisis hashtag#kisstheground hashtag#verticalfarmingchallenges
VIDEO: Freight Farm To Teach Youth About Sustainable Agriculture
by Nicole Weaving
July 24th, 2021
To View The Video, Please Click Here
Freight Farm to teach youth about sustainable agriculture (Photo Credit: NTV News)
LINCOLN, Neb. — Beyond School Bells is partnering with the Bay in Lincoln for a new after-school program that will teach students about sustainable ag technology.
"We really see Freight Farm as kind of that key, climate-change impervious tool that young people need to know about as we face an uncertain future," said Jeff Cole, Network Lead for Beyond School Bells.
An old shipping container in the parking lot of the Bay has been transformed in a self-contained hydroponic farm.
Using red and blue LED lights, this Freight Farm, known as the Greenery, creates a climate-controlled environment, where the plants grow vertically without a need for soil.
"We enrich the water with nutrients that would normally be in the soil," said Colton Harper, Organizing Manager for the Greenery. "And then in these grow walls, we've got spickets that come right through these foam and it's directly onto the roots of the plants."
According to Harper, there are currently about 6,000 plants growing in the Freight Farm, but at full capacity, it can hold 13,000 plants between the seeding area and that walls. That would produce the equivalent of a 2.5-acre farm year-round.
"Even in the winter, if there are shortages anywhere, we can turn on a dime, 7-week grow cycle and be able to provide those crops for local markets," said Harper.
The Greenery arrived in Lincoln in April, and Harper has led to two teams to get it up and running. They are currently preparing for their first harvest with items like basil, lettuce and radishes.
"We're at about Week 7, and in 2-3 weeks, we'll have our produce at a farmer's market," said Harper.
After a few more grow cycles, the program will open to local students to teach them all aspects of sustainable farming.
"From the electrical side, the growing, the programming, computer science to the irrigation, the HVAC system, there's so many elements," said Harper. "And we're particularly well-placed with the Bay and their digital design area of focus, the students will also be able to design the packaging, design the labeling, so it's really a full-circle, interdisciplinary opportunity for the students to get involved."
The Greenery plans to hold a Harvest Party to celebrates the farm's success in the coming weeks.
Projected Water Scarcity Prompts Need For Farming Ingenuity
Emerging technologies are quickly trying to find ways to get the most bang for each drop of water. Efficiencies have been identified, including vertical hydroponic farming, which drastically reduces the amount of water needed to grow crops
Posted by chrismichlewicz
July 31, 2021
The common refrain that freshwater is the next gold is ringing true as drastic changes in our climate are resulting in greater competition and a need for more efficient water uses, especially in the agricultural industry.
National Geographic points out that while the amount of fresh water on the planet has remained fairly constant over time — continually recycling through the atmosphere and back into our oceans, lakes, and rivers — the global population has exploded in the last century. This means that competition for a clean supply of water for drinking, cooking, bathing, and sustaining life intensifies every year. There is only so much water to go around.
Essentially, when taking saltwater into account, only about .007 percent of the Earth’s water supply is usable for the planet’s 6.8 billion (and counting) people, National Geographic says.
The vast majority of freshwater — about 70 percent by most estimates — is used for agriculture, and when you consider that feeding a planet of 9 billion people in 2050 will require an estimated 50 percent increase in agricultural production and a corresponding 15 percent increase in water withdrawals, the future becomes a lot clearer, according to World Bank.
Without proper governance, there is likely to be increased competition for water between sectors and an escalation of water crises of various kinds, triggering emergencies in a range of water-dependent sectors, according to a U.N. report.
Emerging technologies are quickly trying to find ways to get the most bang for each drop of water. Efficiencies have been identified, including vertical hydroponic farming, which drastically reduces the amount of water needed to grow crops. FarmBox Foods, a Colorado company that builds automated hydroponic farms inside repurposed shipping containers, has set its sights on creating a tangible shift in the approach to farming.
FarmBox Foods’ innovative, closed-watering system only uses 3-5 gallons of water per day and, almost as important, it does not contribute to groundwater contamination the way that traditional farming does. Furthermore, one farm is able to produce the same yield as 2 – 2.5 acres of farmland on an annual basis.
“Our container farms are built in such a way that it takes only a fraction of the amount of water to grow that same amount of produce,” said Rusty Walker, CEO of FarmBox Foods.
Climate change is projected to increase the number of water-stressed regions and exacerbate shortages in already water-stressed regions. It’s those regions that will realize the most benefit from vertical hydroponic farming and more efficient water usage in general.
An integrated view on water, the biosphere, and environmental flows is necessary to devise sustainable agricultural and economic systems that will allow us to decelerate climate change, protect us from extremes and adapt to the unavoidable at the same time, the U.N. says.
The automated hydroponic farms have a secondary benefit, as they can grow pine trees that contribute to the overall health of the environment by helping reduce the amount of carbon dioxide in the atmosphere. One container farm from FarmBox Foods can grow 35,000 tree saplings per year.
For more information, go to www.UNwater.org or www.FarmBoxFoods.com.
Posted by chrismichlewicz on July 31, 2021 in Arapahoe County Business, Douglas County, Douglas County Business, Featured, Greenwood Village Business
Tagged #farmboxfoods, agriculture, cleanwater, Colorado, containerfarm, containerfarming, environment, farmboxfoods, freshwater, indoorag, indoorfarming, UN, Water, waterscarcity, watershortage, watersupply, waterusage
Central Minnesota Research Project Growing Kale Indoors
The project is a partnership with Todd-Wadena Electric Cooperative, Central Lakes College, Lakewood Health System, Great River Energy and the Electrical Power Research Institute
The project is a partnership with Todd-Wadena Electric Cooperative, Central Lakes College, Lakewood Health System, Great River Energy, and the Electrical Power Research Institute.
Written By: Rebecca Mitchell
July 21, 2021
Central Lakes College research analyst Noah Boetler shows a panel of kale plants in the Sota Grown pod during a virtual tour on July 13, 2021. Rebecca Mitchell/Pioneer Journal
STAPLES, Minn. — A community research project in Staples involving indoor gardens is set to continue growing.
The hydroponics project started in 2020 with Great River Energy, Todd-Wadena Electric Cooperative, and the Electrical Power Research Institute hoping to learn new technology and increase access to fresh produce. And even with kale as the chosen plant, local organizations rooted for the success of the hydroponics pod. The pod, planted at the Central Lakes College Staples campus, is a shipping container with room for 5,820 kale plants.
“I didn’t know how things were going to grow in here, it’s kind of a weird concept with there being no sunlight and things like that, so just seeing it go from a little seed to your big plant and harvesting it, I think that has been the coolest aspect,” CLC research analyst Noah Boelter shared with Minnesota educators in a virtual tour on July 13.
The partnership is called "'Sota Grown" and has helped develop a fully enclosed hydroponic container for growing fresh plants all year long — to supplement existing agriculture practices in communities across the state.
The pod, equivalent to one acre of crops, is a supplement to traditional farming, not a replacement, as TWEC member service manager Allison Uselman said. Although kale is the focus of the two-year project, the team has experimented with growing basil, swiss chard, lemon balm, and chives. Romaine lettuce, butterhead lettuce, and salad mixes are next on the list — and after a year of only kale, Boelter is excited for the new opportunities.
Each kale seed, planted by hand, starts in the nursery before being transplanted to vertical panels. The kale takes 12 weeks to reach maturity. The team of four staff members and interns plant and transplant on Wednesdays and harvest on Mondays.
“Kale is pretty forgiving, which is very fortunate for us,” Boelter said after sharing about a frozen pump during the winter. The kale wilted and bounced back in a matter of days. The team is also learning about flooding and nutrient dosing in the pod.
With the expected growth of indoor agriculture, Uselman said electrical companies will need to prepare for the change. For example, the pod uses the most energy when most other customers could have off-peak rates. The light and water systems run from 4 p.m. to 8 a.m. daily. The kale is watered for five minutes every 45 minutes. The electricity is about $600 a month.
“It’s education with students, it’s giving back and feeding our communities, and Todd-Wadena has the opportunity then to research all the electrical side of things and really understand this industry before it grows to a larger state,” Uselman said.
The pod’s water usage depends on the humidity levels outside, with the most water used in the winter — about 10.5 gallons every day—and about five gallons a day in the summer. The two water tanks deliver water above the panels and water behind the plants. There are also several different nutrients added, such as one to adjust pH levels.
“In the summertime, the pod does not use a whole lot of water because the HVAC unit has a dehumidifier built into it and that’s recirculating around a gallon of water an hour that gets dumped back into the pod, so it’s really efficient in the summer,” Boelter explained. “But when it’s winter, the air is so dry that’s when we use the most water.”
The indoor pod means the ability to regulate the temperature, which is a cool 65-68 degrees and having no pesticides or herbicides used on the plants since most bugs remain outside. There are some drain flies due to the algae.
The red LED lights in the Sota Grown pod at Central Lakes College are the only source of heat. The lights and water run from 4 p.m. to 8 a.m. daily. Rebecca Mitchell/Pioneer Journal, July 2021
As for sunlight, the LED lights are the only heat source in the pod, as Boelter said, though it is also insulated. The red and blue lights support stem growth and leaf density.
The process yields about 20 pounds of kale a week — and on a record week 43 pounds — or over 1,000 pounds as of July 5. All of the kale is donated to Lakewood Health System, who shares the kale through the Food Farmacy and Hilltop Regional Kitchen. The Kitchen uses the kale in specific meals for those who have tested positive for COVID-19 and people being discharged from the hospital. People can also receive free kale at the summer farmer’s market on Thursdays.
As Lakewood’s Community Health Coordinator, Amy Wiese works with about 70-100 bags of kale a week to find where it can best be served. She said the kale lasts about two weeks in the fridge.
People also receive kale recipes for new ways to enjoy the vegetable. Wiese enjoys massaging the kale to break down the bitterness and then eating it in a salad. Other favorites are kale chips and soups.
“We just see the benefits of this project and recognize the positive impact that healthy food can have on individuals and in the community,” Wiese said. The organizations also hope to address local food deserts. “It’s really amazing that we are able to provide fresh produce all year with this pod” even with snow on the ground for six months of the year.
The seeds grown and sown in the community have finished their process with new seeds set to germinate, grow to maturity, and be harvested and packaged in four to eight hours for their short drive up the road.
Photo: 1 - The kale seeds are planted in peat moss plugs and stored in the nursey for three weeks before being transplanted to the indoor panels. The planting process takes about an hour. Submitted photo
Photo: 2 - The shipping container contains an acre of kale growing hydroponically with LED lights. Photo courtesy Todd-Wadena Electric Coop
Photo: 3 - Each section has 22 panels with space for 5,820 kale plants or the resemblance of one acre of crops. Rebecca Mitchell/Pioneer Journal, July 2021
Malaysian, Smart Farm That Grows And Delivers Organic Vegetables
“The pandemic has underscored the urgency of building better food production, including fresh vegetables. Customers are increasingly aware that food choices influence both the health and the health of the planet,” the team concluded
July 15, 2021
7 years. It’s how long the farm lasts with 5G BoomGrow it has existed, but it has not always been so efficient. Founders Jay, Murali, and Shan had initially explored different cultivation methods, from simple hydroponics to aquaponics.
Image Credit: Founders of BoomGrow
“We grew our greens in small boxes. We even tried to grow them outdoors. Nothing worked, ”Jay recalled in an interview with Vulcan Post.
This trial and error lasted for five years until the co-founders discovered AI-driven vertical agriculture. With this method, they realized that they could also grow their greens in a controlled indoor environment that would make harmful chemicals such as pesticides unnecessary.
Finally, they had found it the method that allowed them to properly achieve their goals of producing clean, tasty greens.
Using 95% less resources to get the same performance
“Our systems detect how diverse contributions like the light, the water, and the pH affect the quality and the flavor of our plants. That’s what we call our plant recipes, ”said Shan.
“We then rely on machine learning and data analysis to tailor each entry to the respective plant, producing tastier greens.”
The team says its system equipped with technology is Machine Farm. It is used in all reused BoomGrow shipping containers where crops are grown on modular plant racks.
According to the team, five piles of crops on a 360-square-foot plot can produce a yield that is the equivalent of the traditional harvests of a 1-acre outdoor farm.
With this technology and efficient use of space, they can grow 20 varieties of leafy vegetables and herbs in a residential neighborhood of Ampang.
At the same time, Jay said Machine Farm uses 95% less land, water, and fuel than traditional outdoor farms.
Its technology-based agricultural approach has seen BoomGrow achieve multiple milestones, from being the country’s first 5G showcase farm to receiving benefits from government grants from SME Corp, PlaTCOM Ventures, and MDEC.
One of his most proud moments was the validation of renowned chefs working in 5-star hotels, who placed an order for their greens and have since been loyal followers.
Dedicated to clean processes and products
Clearly, there are already several agents in the precision and vertical farming industry with more union, but few are as gung-ho about clean produce as BoomGrow is.
Cleaning doesn’t just mean pesticide-free vegetables; the team decided that value should be reflected in the overall operation of their business.
Inside a Container / Image Credit: BoomGrow
As a former national athlete, Murali wanted to start BoomGrow because he knew the difference a good diet could make.
Meanwhile, Shan is a trained architect who had developed an interest in sustainable design throughout his career. Fascinated by the way modular structures had minimal impact on their environment, he wanted to explore other avenues for incorporating sustainability into everyday life.
He is the director of innovation at BoomGrow, designing and bringing its plant systems to life. On the other hand, Jay was inspired to co-found BoomGrow after many years in sustainability consulting.
He told Vulcan Post: “Throughout my career, I have had consulting experience for various agricultural and F&B manufacturing companies. This allowed me to evaluate the data around some of the practices, as well as the disconnection that people from these organizations had about sustainability. ”
Bringing the head together led the team to arrive at the current solution that is committed to implementing the 12th Sustainable Development Goal, responsible consumption, and production.
Organic vegetable packages at competitive prices
With all the investment in technology growing their organic greens, it looks like a purchase of them should cost a bomb.
But because they are able to eliminate the need for extensive land located in remote areas and a long cold chain, they can offer their vegetables at a competitive price.
BoomGrow sells 5 to 6 varieties of vegetables depending on the package you want, priced between 45 and 65 RM per package. Free delivery is offered to subscribers of weekly or fortnightly plans. Otherwise, deliveries to the Klang Valley would cost 10 RMS for purchases over 45 RM or 15 RM for those under 45 RMS.
Young Greens Growing on Modular Racks / Image Credit: BoomGrow
Compared to another vegetable delivery service with a subscription model, Plant B, BoomGrow prices are reasonable.
Floor B offers 6 types of vegetables in a box and a two-week subscription would be RM37 / week, while a 4-week subscription would be RM34 / week. Shipping costs are offered at fixed rates of RM6-RM8 depending on where you are in the Klang Valley.
For both BoomGrow and Plant B, people may not be able to choose exactly what goes into their box, but Plant B customers will be informed of the variety they can expect depending on the season and availability. You can also contact the team for exclusions.
On the other hand, BoomGrow clearly lists each variety of vegetables in a package with the assigned weight, so you’ll know exactly what you’ll get. To add, plant B does not claim that its product is organic.
Improve your B2C services during the pandemic
When the pandemic first hit in 2020, BoomGrow saw a sharp drop in overall sales as hotels and restaurants had to cut back on their orders.
Conversely, their e-commerce orders increased as more people subscribed to their vegetable packages.
“The pandemic has underscored the urgency of building better food production, including fresh vegetables. Customers are increasingly aware that food choices influence both the health and the health of the planet,” the team concluded.
They were able to meet this demand thanks to the support of MaGIC, particularly as part of cohort 4 al Global Accelerator Program.
Through it, their technology pipelines became more focused and were able to expand their digital footprints, refine e-commerce offerings, and improve their automation. Now, BoomGrow is preparing a launch of its machine factories outside of Klang Valley to reach more customers.
Outside, they will come face to face with more players in the vegetable delivery space, but perhaps their technology and mission will differentiate them in the long run and attract a segment of customers with whom their mission resonates.
Earth911 Podcast: Freight Farms’ Jake Felser On Hydroponic Agriculture & Container Farming
Earth911 talks with Jake Felser, chief technology officer at Freight Farms, about the company’s “complete farming system inside a box.”
By Earth911
JULY 14, 2021
Earth911 talks with Jake Felser, chief technology officer at Freight Farms, about the company’s “complete farming system inside a box.” It’s a very big box that includes climate controls and monitoring systems to make farming easy for anyone to do. Freight Farms builds and delivers shipping containers converted into highly efficient hydroponic farms that use LED lighting to grow and deliver fresh produce year-round.
Jake discusses the cost of getting started, how many people are needed to run the farm, and how the built-in automation helps farmers plan a profitable business. Grocers, restaurants, communities, and small farms are using Freight Farms installations at 350 farms in 49 states and 32 countries. The company says most of its customers are new to agriculture and operate right in the urban and rural communities they serve.
Jake Felser, CTO at Freight Farms, visits Sustainability in Your Ear to talk about automated hydroponic gardening in shipping containers.
Growing and distributing vegetables locally is one of the most effective ways to lower our society’s carbon footprint. While agriculture contributes about 10% of the U.S. greenhouse gas emissions each year, the majority of that is from raising animals. By increasing our consumption of locally grown vegetables, we can improve local health and reduce overall emissions from transportation. It’s not easy to grow food in most cities using traditional methods. The introduction of container farms and vertical farming inside buildings can reshape food deserts and create economic opportunities.
To learn more, visit FreightFarms.com.
Subscribe to Sustainability in Your Ear on iTunes and Apple Podcasts.
Follow Sustainability in Your Ear on Spreaker, iHeartRadio, or YouTube
Tags: container farming, Freight Farms, hydroponics, reinventing agriculture
Solar Firm To Convert Shipping Containers To Urban Greenhouses
CEO James DiPrima said: “We also felt that inner city urban areas also needed a way to get fresh fruits and vegetables grown right in their own neighborhood. Reimagining old shipping/cargo containers as the structural framework for our soar technology would greatly reduce the costs of building greenhouses
July 9, 2021
New York, New York, July 09, 2021 (GLOBE NEWSWIRE) — Green Stream Holdings Inc. (OTC PINK: GSFI) (“the Company”) (http://www.GreenRainSolar.com), an emerging leader in the solar utility and finance space, which had previously announced that it would be entering the rapidly growing urban gardening sector with solar greenhouses dedicated primarily to rooftop farming, today announced that it is also moving forward with its previously announced project to convert old shipping/cargo containers into inexpensive greenhouses for urban and inner city neighborhoods.
Last year, on October 6, 2020, the Company previously announced that it had entered into a non-binding agreement with Aoki Group Inc. (“Aoki”) and famed restauranter, Kevin Aoki, who wanted to ship his famous mushrooms to his various sites around the world. The mushrooms would grow inside the container while being shipped to their destination.
Blondie’s specializes in custom urban landscapes including roof decks, terraces, courtyards and entry gardens, and is now utilizing that expertise in designing the irrigation systems for our Cargo container Solar Greenhouses. Blondie’s transforms concept and vision into realized functional design.
Blondie’s is experienced in specifying, installing, renovating and maintaining green wall systems. They are famous for their interior and outside Green Walls.
For more information go to: https://blondiestreehouse.com.
CEO James DiPrima said: “We also felt that inner city urban areas also needed a way to get fresh fruits and vegetables grown right in their own neighborhood. Reimagining old shipping/cargo containers as the structural framework for our soar technology would greatly reduce the costs of building greenhouses. Less room, less labor and less panels was a marriage made in heaven for underserved communities. Communities can get one, ten or 100 containers… whatever amount of land is available… and since each container has a small footprint, there is a lot of flex flexibility for each situation.
Using solar energy has two main benefits: Solar energy systems do not produce air pollutants or carbon dioxide, and Solar energy systems on buildings have minimal effects on the environment… OUR Solar Greenhouses combine the two creating a physical structure that produce electricity, with the ability to capture the sun from many different angles.”
About Green Stream Finance, Inc.
Green Stream Finance, Inc., a solar utility and finance company with satellite offices in Malibu, CA and New York, NY, is focused on exploiting currently unmet markets in the solar energy space, and is currently licensed in California, Nevada, Arizona, Washington, New York, New Jersey, Massachusetts, New Mexico, Colorado, Hawaii, and Canada. The Company’s next-generation solar greenhouses constructed and managed by Green Rain Solar, LLC, a Nevada-based division, utilize proprietary greenhouse technology and trademarked design developed by world-renowned architect Mr. Antony Morali. The Company is currently targeting high-growth solar market segments for its advanced solar greenhouse and advanced solar battery products. The Company has a growing footprint in the significantly underserved solar market in New York City where it is targeting 50,000 to 100,000 square feet of rooftop space for the installation of its solar panels. Green Stream is looking to forge key partnership with major investment groups, brokers, and private investors in order to capitalize on a variety of unique investment opportunities in the commercial solar energy markets. The Company is dedicated to becoming a major player in this critical space. Through its innovative solar product offerings and industry partnerships, the Company is well-positioned to become a significant player in the solar space.
SOURCE: Green Stream Holdings Inc.
Tagged indoor farming
Feel Confident In Starting Your Project With This 3-Part Webinar Series!
Even with effortless, turn-key container farms, there are still questions left unanswered for those interested in getting startedThis three-part webinar series will take you step-by-step through what you need to know before you start, how to select the best business model, and your options for financing the project
Even with effortless, turn-key container farms, there are still questions left unanswered for those interested in getting startedThis three-part webinar series will take you step-by-step through what you need to know before you start, how to select the best business model, and your options for financing the project.
By signing up, you will:
Hear and learn from first-hand experiences
Access knowledge and resources from Growcer and Farm Credit Canada
Break down how to get growing year-round into smaller, digestible steps
If you’re interested in growing food for your community but don’t know where to start or are stuck along the way, sign up for the webinar series today!
Register now for all three sessions:
July 13 - Getting Started
July 27 - Choosing a Business Model
August 10 - Financing your Project
Excited for you to join us,
The Growcer Team
Contain Inc Announces Finance Arrangement With Edible Beats For FarmBox Foods Container Farm
The container farm is being built and customized for Edible Beats, and will produce ingredients for all of the EB concepts, Linger, Root Down, Vital Root, El Five, and Ophelais
NEWS PROVIDED BY
July 07, 2021
Contain Inc announces a financing agreement arranged between Edible Beats Restaurant Group & a prominent lender for a FarmBox Foods container farm.
Image courtesy of FarmBox Foods
With the FarmBox Food container, we can grow hyper-local, organic, year-round produce that will be featured at all of our restaurants. We feel this is just the beginning of what we can grow”— Justin Cucci of Edible Beats Restaurant Group
RENO, NV, UNITED STATES, July 7, 2021 /EINPresswire.com/ -- Contain Inc is pleased to announce a financing agreement arranged between Edible Beats Restaurant Group and a prominent lender for a controlled-environment container farm, FarmBox Foods. Edible Beats is a locally owned Denver-based restaurant group known for its diverse menus and healthy, plant-based dishes that highlight local and seasonal ingredients. Edible Beats will be able to grow herbs, leafy greens, salad greens, and various produce organically and year-round with the container farm that will be attached to their Vital Root location.
“We have always sought opportunities to be more responsible to the sourcing, growing, and handling of the incredible ingredients that we get,” said Justin Cucci of Edible Beats Restaurant Group. “With the FarmBox Food container, we can grow hyper-local, organic, year-round produce that will be featured at all of our restaurants. We feel this is just the beginning of what we can grow, and we are eager to add the mushroom grow operation in the future”
Image courtesy of Unsplash
Edible Beats purchased the container from FarmBox Foods, a Colorado-based company that builds automated farms that grow gourmet mushrooms, leafy greens, and culinary herbs. To FarmBox, controlled-environment agriculture is the future, and this deal is one of many leading us towards a more decentralized and eco-friendly food system.
“I think we’re going to see a lot more of these types of programs going forward,” said Chris Michlewicz, Chief Public Relations Officer at FarmBox. “Restaurants are realizing that their produce is fresher and has a longer shelf life when they have a container farm on site. It’s a reliable and sustainable source of food, and it’s more eco-friendly because you no longer have to transport food in from elsewhere.”
Image courtesy of Unsplash
Likewise, Contain Inc is thrilled to support Edible Beats as it ventures into indoor ag. “We're delighted to have assisted SemiMojo and FarmBox Foods in this innovative initiative. Contain is always excited to see more fresh food made available to consumers. Customers appreciate freshness and quality produce, year round. Restaurants and container farms make this possible”, said Doug Harding, Head of Leasing & Vendor Relations at Contain Inc. “We are thrilled to have collaborated with Edible Beets and Farm Box Foods on this project. It aligns perfectly with Contain's mission of supporting the controlled environment agriculture industry in its financing needs”.
The container farm is being built and customized for Edible Beats, and will produce ingredients for all of the EB concepts, Linger, Root Down, Vital Root, El Five, and Ophelais.
About Contain Inc
Contain is out to empower the indoor ag industry of tomorrow. Our first and key mission is bringing easier and faster financing to controlled environment agriculture, but we aren't stopping there. We create platforms to move the industry forward, and most importantly, find ways to make indoor ag more accessible to farmers of all stripes.
Contact Contain:
Doug Harding, Leasing & Vendor Relations
doug@contain.ag | 760-330-1199
About Edible Beats
Edible Beats is a locally owned independent restaurant group that operates such diverse concepts as Linger, Root Down, El Five, Ophelais, and Vital Root. “Walking the walk” is important to us and the various aspects of sustainable & local food sourcing, up-cycled design, and authentic Hospitality.
About FarmBox Foods
FarmBox Foods was founded to help provide a sustainable, eco-friendly food source to places where there is a lack of access to farm-fresh produce. The company’s mission is to use container farms to decentralize the food supply chain and empower local communities.
Doug Harding
Contain Inc
doug@contain.ag
Visit us on social media:
Twitter
LinkedIn
USA - Pennsylvania: Container Farm To Be Delivered To School In Oakmont
CEA Advisors announced today that they have delivered another custom-built 40’ Growtainer® Vertical Farm to the Riverview School District in Oakmont, PA. Unlike other school’s container farms that can only teach one method of production, this farm is specifically designed to teach the students about multiple growing methods
CEA Advisors announced today that they have delivered another custom-built 40’ Growtainer® Vertical Farm to the Riverview School District in Oakmont, PA. Unlike other school’s container farms that can only teach one method of production, this farm is specifically designed to teach the students about multiple growing methods.
The Oakmont Growtainer has three distinct chambers to provide a real hands-on experience for the students, including a classroom/lab/germination area, an LED-lit multi-level soil chamber, and an LED-lit multi-level hydroponic system.
Glenn Behrman, President, and founder of CEA Advisors, a global controlled environment consulting firm and the manufacturer of Growtainers worked with the school’s staff to design a cost-effective system that could provide various levels of a learning experience as well as providing fresh leafy greens for the cafeteria for their students of all ages.
“Due to Corona virus supply chain issues, the school couldn’t wait for our Growracks to arrive from our manufacturing partner in Holland. So we designed and built a custom multi-level racking system for the ebb and flood hydroponic installation including automatic irrigation and water monitoring and dosing.”
The soil side is also a multi-level design with LED lighting and an irrigation system. The climate is independently controlled in each chamber including de-humidification. In the next month or so the entire campus, including the Growtainer will be powered by solar.
For more information:
CEA Advisors LLC
Glenn Behrman, Founder, and President
gb@cea-advisors.com
www.cea-advisors.com
23 June 2021
Freight Farms And CEO Vanzura Set To Reinvent Container Farming
June 17, 2021
The global pressures exacerbated by COVID-19 and the rippling toll it takes on the international community has made one thing clear: preparedness is everything. The Coronavirus has exposed vulnerabilities in the global health network that no one could have imagined. Food production and distribution must now reset their agendas to prepare for catastrophe.
Freight Farms, a 2011 Agtech company that pioneered hydroponics-based container farming, is committed to preparing the world for the next disaster by reinventing the way we grow food.
“Fill in the blank with the institution, how prepared are you for the emerging trends that are impacting the world,” Freight Farms CEO Rick Vanzura explained. “Sustainability issues, land availability, water availability; those issues obviously preceded COVID-19, but we think there’s going to be a greater sense of urgency around folks expecting us to have an answer and be prepared for these global trends, as opposed to being reactive.”
Vanzura looks to channel his decade of experience as a restaurant executive, growing Wahlburgers from a single restaurant to a $100 million dollar institution, as well as greatly expanding Panera Bread, to redefine food production and distribution as a whole.
Freight Farms uses container-based “vertical farming” to do just that, allowing farmers to produce hundreds of high-quality local crops from a 320 square foot shipping container which automates the farming process for maximum efficiency.
Vanzura plans to expand and distribute these self-contained, sustainable farms to a wide diversity of industry segments. The priority will of course be the global communities that need them the most. “We see the Freight Farm as a perfect fit for countries with food access difficulties, short growing seasons and inherently challenging climates. There’s probably no location where having a hyper-local, highly traceable, always available solution isn’t going to make sense in some way,” he added.
In the name of access to high-quality food, in a sustainable model built to withstand a natural disaster, Freight Farms has now distributed their automated, hydroponic farms to 48 U.S states and across the world to 32 different countries, boasting success and efficiency from the Arctic wilderness, to the desert, and to concrete jungles.
Freight Farms believes that its emphasis on access, preparedness, and sustainability will be more necessary than ever in the wake of COVID-19, as well as global trends of food insecurity and environmental uncertainty. Vanzura explained that the company has already reacted to shifting demands by supporting small-scale farmers as they set up drive-through produce stations to reach customers directly.
Freight Farms CEO Rick Vanzura
“Demand during this time for that hyper-local, fresh product has certainly ramped up,” Vanzura added. “Hopefully, once people get a taste of it, they will understand the difference, and post Covid, our containers will become an industry staple.”
Vanzura sees his role as not only expanding to agriculturally vulnerable countries abroad but also increasing access to high-quality food across institutions in the United States. He wants to specifically target universities and has partnered with foodservice provider Sodexo to ensure local food is available to as many people as possible.
Vanzura says he was forced by his children to move beyond the world of crafting a restaurant chain’s vision and use his knowledge to make the world a better place. Freight Farms, with Vanzura’s leadership, has the ability to change the way we think of farming and change the world.
Freight Farms hopes to combat international uncertainty, face the threats of climate change, and provide people with fresh produce regardless of climatic constraints and difficulties. “Healthy food is a right, not a luxury,” and Freight Farms is helping make this mission statement a reality.
Lead photo: A Freight Farms container has unprecedented environmental control and exceptional ease-of-use to unlock your growing potential.
To learn more about Freight Farms and how they are reinventing container farming, visit their website.
Total Food Service is a monthly B2B foodservice publication and website covering foodservice and hospitality news, industry trends, and exclusive interviews.
CANADA: The Value of Hyper-Local Produce
At Yellowknife Co-op, produce is grown steps away from the store in a container farm!
The hyper-local food trend is more than just a fad: there’s a reason that hyper-local food is catching on in a big way. If you’re thinking about growing hyper-local food, it’s important to understand the value of the product and its market position.
At Yellowknife Co-op, produce is grown steps away from the store in a container farm!
BUT FIRST, WHAT IS HYPER-LOCAL FOOD?
Where does that ‘local’ head of lettuce you pick up from the grocery store actually come from? The Canadian Food Inspection Agency (CFIA) defines ‘local food’ as being grown in the province where it’s being sold, or within 50km of the border. But hyper-local food is even more local than being from the same province or being Canadian-grown. It is usually grown within the same town or city, or a short distance from where it’s being sold (sometimes even right behind the store!).
BENEFITS OF HYPER-LOCALLY GROWN FOOD
LOWER FOOD MILES
Hyper-local produce is usually grown within the same town or city, or a short distance from where it’s being sold.
As consumers are becoming more and more aware of the environmental impact of our food choices, the demand to lower food miles is also growing. A food mile can be thought of as the distance that food travels from the grower to the consumer. As a metric, it helps to assess the environmental impact of the foods we consume. A 2012 study showed that on average, 30% of food is imported in Canada, leading to annual emissions of 3.3 million metric tonnes of CO2.
Growing food hyper-locally can result in significantly lower food miles (and as few as zero food miles!) in both urban centres and rural communities. This reduces the carbon footprint of what you eat.
SUSTAINABLY GROWN
Growing hyper-locally in a hydroponic farming system has further benefits. Water in a closed hydroponic system is captured and reused, resulting in 90% less water use, and 95% less land than conventional farming.
TRACEABLE FOOD CHAIN
Growing hyper-local is completely traceable. This means you know exactly what’s going into your product. There are no synthetic pest control products, less risk for E.Coli, and a shorter supply chain to manage.
FRESHER PRODUCE WITH A LONGER SHELF LIFE
Growing food hyper-locally also means fresher produce and a longer shelf-life. Instead of wilting in a truck for hundreds of kilometers, hyper-local produce is shelf-ready immediately. This has a marked effect on the quality, as most produce loses 30 percent of nutrients just three days after harvest.
Life Water Gardens, a container garden project in Norway House Cree Nation, sells locally-grown produce at the Northern Store. Click here to learn more about the project and hear from its growers!
“When you get your hands on the fresh produce and taste it, you know it’s a good thing for your community in general. It’s really easy to get excited and pumped about [this project].” - Ian Maxwell from Norway House.
“When you get your hands on the fresh produce and taste it, you know it’s a good thing for your community. It’s really easy to get excited and pumped about [this project].”
— Ian Maxwell, co-manager of Life Water Gardens
WHERE IS HYPER-LOCAL PRODUCE POSITIONED IN THE MARKET?
For growers, it’s important to keep in mind that hyper-local food isn’t competing with foreign produce that you typically find in grocery stores. Between locally-grown vs imported food, the wholesale price for foreign produce is cheaper than local produce.
Keep in mind that grocery stores buy produce at wholesale prices, which means that they may buy produce from you at a certain cost, and then sell it with a 30% margin added to the price. When you walk into a grocery store and see produce being sold for $4.99, the reality is that the grocery store-bought it for $3.50 and added a mark up to the final price to help cover their costs of operations.
To find price-compatible products for market research in your area, look for products that will match your future products, such as living lettuce, other hydroponic greens, and other hyper-local, organic produce. Growcer greens belong in the hyper-local, value-added produce category.
GETTING STARTED WITH HYPER-LOCAL FOOD
Growing hyper-local food has many benefits: not only is it fresher, healthier, and better for the planet, it can also be a profitable investment for growers. When crafting your financial projections, keep in mind the value of hyper-local produce and where it sits in the market.
Interested in learning more about our hyper-local hydroponic growing systems? Find out more.
Vertical Roots Expands To Atlanta, Partners With Two Wholesalers
The company partnered with two of the leading Southeastern produce suppliers, Collins Brothers Produce BB #:128652 and Phoenix Wholesale Foodservice BB #:134241, to place the farm directly at their facilities
June 11, 2021
CHARLESTON, S.C., June 10, 2021 /PRNewswire/ — Vertical Roots, the largest hydroponic container farm in the U.S. sustainably growing fresh leafy greens year-round, opened its third indoor farm in Atlanta, Georgia this June.
The company partnered with two of the leading Southeastern produce suppliers, Collins Brothers Produce BB #:128652 and Phoenix Wholesale Foodservice BB #:134241, to place the farm directly at their facilities.
The new Atlanta farm site will eliminate the need for produce transportation to the distributor and allow Vertical Roots lettuce to be delivered to local customers the same day it’s harvested.
Located within the Atlanta State Farmers Market, this is phase one of the company’s Atlanta expansion. With farm production underway, Vertical Roots Georgia Grown™ lettuce will be available in grocery stores in July 2021.
Crisp, sweet, tender, or buttery, Vertical Roots lettuces are nutritious, pesticide-free, and come in a wide variety of flavors, colors, and textures for culinary masterpieces and everyday meals. With long lasting freshness, produce is in the hands of consumers within one to three days of being harvested and has up to a 21-day shelf life.
Vertical Roots’ mission is to revolutionize the ways communities grow, distribute, and consume food. Farming directly at distribution hubs is a part of Vertical Roots’ distinctive strategy to eliminate a massive leg of produce transportation in order to reduce emissions and provide communities with fresh, locally-grown produce.
The new Atlanta farmsite will reduce produce transportation by an estimated 300 miles per delivery and will help meet the company’s retail demand that services thousands of grocery stores across the Southeast and Mid-Atlantic, as well as restaurants, universities, and schools.
“A large part of our mission is to grow food as close to the point of consumption as possible, and this farmsite accomplishes just that,” said Andrew Hare, co-founder, and general manager of Vertical Roots. “The Collins family are esteemed produce industry leaders for three generations, and we’re ecstatic about the unique grower-supplier partnership that we’ve cultivated.”
David Collins, President of Collins Brothers & Phoenix Wholesale Foodservice, said, “At Collins Brothers and Phoenix Wholesale, we’ve had the privilege to work with dedicated farmers across the country for decades. We’re thrilled to partner with Vertical Roots as they bring an innovative way of farming to the agriculture industry. We look forward to this relationship as we share a like-minded mission in providing our customers with high quality, fresh, local produce.”
Vertical Roots’ state-of-the-art indoor farms are manufactured from upcycled shipping containers at the company’s headquarters in Charleston, SC. The farm containers made their way to Atlanta on June 8, where farmers started seeding and transplanting to produce Vertical Roots lettuce within weeks.
A small footprint with a large output, the new farm will produce half a million heads of lettuce this year. Each 320-square-foot container maximizes the growing space with 3,400 plants per harvest, and up to 17 harvests per year.
Vertical Roots farms operate with the highest globally recognized food safety standards, eliminating the need for pesticides of any kind.
An AmplifiedAg, Inc.® company, Vertical Roots operates farms with proprietary software and technology. The farms don’t rely on soil, use up to 95% less water and grow crops 25% faster, compared to traditional farming methods.
About Vertical Roots:
An AmplifiedAg, Inc. company, Vertical Roots is the country’s largest hydroponic container farm and is revolutionizing the ways communities grow, distribute and consume food. Sustainably-grown indoors and pesticide-free, Vertical Roots leafy greens are fresh, clean, nutritious, and delivered to your local grocery store within one to three days of being harvested. Vertical Roots produce is available at thousands of leading grocery stores in 12 Southeastern states, educational institutions, restaurants, and other food service organizations. Vertical Roots operates farms in Charleston, S.C., Columbia, S.C. and Atlanta, Ga.
Tagged greenhouse, lettuce, vertical farming
CubicFarms Announces Closing of $25.3 Million Equity Financing
This financing allows us to fully capitalize on our accelerating sale pipeline growth and market-leading R&D program.”
CubicFarm Systems announced today the closing of its previously announced bought deal equity offering of common shares of the company. The net proceeds from the offering of approximately C$23.8 million will be used to support CubicFarms’ continued global growth, research, and development efforts to optimize machine yields, automation, and functionality, expand addressable crop varieties, and for working capital and other general corporate purposes.
Pursuant to the offering, the company issued a total of 18,740,742 common shares at a price of C$1.35 per common share for gross proceeds to the company of C$25,300,001, which includes the exercise, in full, by the underwriters of the over-allotment option granted by the company to purchase an additional 2,444,445 common shares at a price of C$1.35 per common share.
“We are thrilled by the overwhelming support by our global institutional shareholders, like Handelsbanken, and their confidence in our vision,” said Dave Dinesen, Chief Executive Officer, CubicFarms. “The strong demand for this bought deal financing allowed us to upsize and fully allocate the over-allotment option with the closing of $25.3 million. This financing allows us to fully capitalize on our accelerating sale pipeline growth and market-leading R&D program.”
CubicFarms completes previously announced debt reduction
CubicFarms also announced that further to its news release dated May 3, 2021, the company has completed its previously announced issuance to Business Development Bank of Canada of 128,205 common shares of the company at a deemed price of $1.56 per common share.
“We’re pleased to work with our long-term lending partner on reducing the debt associated with our C$2.5 million growth capital loan with more favorable terms for the Company,” said Dave Dinesen, CEO, CubicFarms. “This demonstrates continued confidence in our ongoing development and the growth of the Company.”
CubicFarms approves grant of options
The Company also announced today that its board of directors has approved the grant of 700,000 stock options to certain directors and officers of the company pursuant to the company’s stock option plan. The options have an exercise price of $1.47 per share, vest as to one-third n each of 12, 24, and 36 months from the date of grant, and have a 5-year term. The grant of the options is subject to the approval of the TSX Venture Exchange.
For more information:
CubicFarms
1-888-280-9076
info@cubicfarms.com
www.cubicfarms.com
Publication date: Fri 4 Jun 2021
VIDEO: World Food Prices Rise At Fastest Pace In A Decade As Inflation Concerns Continue In U.S.
What's driving the increase? Drought in key growing regions including the western U,S. and Brazil, slowing vegetable oil production in Southeast Asia along with increasing costs for livestock producers and soaring Chinese demand
AgDay 06/04/21 - Food Prices
By AGDAY TV June 4, 2021
The United Nations issued a warning this week as world food prices are rising at their fastest pace in a decade.
The data comes from the UN's Food and Agriculture Organization (FAO)'s Food Price Index for May. The Index surged in May with prices rising at their fastest monthly pace since October of 2010. Global food prices have risen for 12 consecutive months and now sit at their highest level since September of 2011.
What's driving the increase? Drought in key growing regions including the western U,S. and Brazil, slowing vegetable oil production in Southeast Asia along with increasing costs for livestock producers and soaring Chinese demand.
Arlan Suderman of StoneX Group says inflation is also part of the equation.
"It definitely is a factor," says Suderman. "And we saw after the Beige Book report [Federal Reserve] came out this past week talking about inflation pressures, how money came into the commodity sector in the overnight trade following that report's release, and it's a hedge against inflation. However, whenever that causes the dollar to rise sharply because interest rates start to go up, then they start to pull back because the fear factor takes hold, we're not going to compete. Longer-term, though, the trend is inflation tends to be positive for the commodity sector, particularly those with a story."
Suderman says data indicates wage inflation is also having an impact. He says wage inflation is increasing at rates the U.S. hasn't seen since the 12th Federal Reserve Chair Jimmy Volcker held his position from 1979 to 1987, under U.S. presidents Jimmy Carter and Ronald Reagan.
"I still see momentum building on the flip inflation pressures right now," Suderman adds. "And a lot of people talk about it being transitory, the Fed talks a lot about that supply lines refilling, that's not what we're seeing in ag, this is a build up a demand that's been building up over time. And then when you look at wage inflation, the last four quarters in a row combined, the strongest wage inflation we've seen in four decades going back to the Paul Volcker era."
FAO says the world food price surge comes with a warning as it echoes similar moves in 2008 and 2011, when high costs led to food riots across some 30 nations.
USA - COLORADO: Sedalia-Based FarmBox Foods Sending Container Farms All Over The World
FarmBox Foods’ short-term goals include partnering with institutions that help provide the biggest possible impact for the most people, including food banks, schools, and hospitals
Posted by Chris Michlewicz
May 28, 2021
With increasingly unpredictable weather patterns impacting crops and a continuing global food crisis affecting millions, a Colorado company is using tech-based indoor farming to make sure no one goes without a reliable, secure source of nutrient-rich food.
FarmBox Foods, based in Sedalia, has spent the last four years developing automated farms in shipping containers to grow organic leafy greens, culinary herbs, tomatoes, and now pine tree seedlings. The company also has a first-of-its-kind gourmet mushroom farm that produces around 400 pounds of mushrooms per week.
The mission-driven company is focused on helping feed those living in food deserts while empowering local communities and providing jobs and educational opportunities. FarmBox Foods’ patented vertical hydroponic watering systems use 90% less water than traditional farms and yield the equivalent of 2 – 2.5 acres of farmland. The repurposed shipping containers that house these systems can be placed virtually anywhere in the world — from island nations to college campuses to the frozen reaches of Alaska — and produce food year-round.
The fully controlled enclosed growing environment is protected from pests and pathogens, which reduces and can eliminate entirely the need for pesticides, allowing people to harvest and eat untainted farm-fresh produce. Setting up containers in or near populated areas also reduces food waste, as the food is able to get to the table more quickly and can better retain its nutritional value.
“The real mission in this whole thing is to be able to feed the world in places that ordinarily wouldn’t be able to grow food,” said Rusty Walker, CEO of FarmBox Foods.
FarmBox Foods’ short-term goals include partnering with institutions that help provide the biggest possible impact for the most people, including food banks, schools, and hospitals.
Learn more at www.farmboxfoods.com.
Posted in Arapahoe County, Douglas County, Douglas County Business, Douglas County Front, Featured, Jefferson County, South Jeffco
Tagged agtech, climatecontrolledfarming, Colorado, coloradobusiness, containerag, containerfarms, eatorganic, farmboxfoods, farmboxfoodscolorado, farming, farmtotable, fooddeserts, foodinequality, foodinsecurity, foodsecurity, growyourownfood, indoorfarming, indoorfarms, mushroomcultivation, mushroomfarm, mushrooms, organic, sedalia, urbanfarming, verticalhydroponicfarm, verticalhydroponics
About the Author: Chris Michlewicz
USA - KENTUCKY: Elliott County High School Receives New Container Farm Through AppHarvest
The curriculum provided by AppHarvest will cover topics such as high-tech growing and an introductory course on local food systems and food resiliency
May. 29, 2021
SANDY HOOK, Ky. (WSAZ) - Some students at Elliott County High School will soon be able to help grow food -- not only for themselves but for the entire region.
The Elliott County High School container farm is the fourth addition to AppHarvest’s program in 2021 and the sixth educational container farm to date.
The container farm program was launched in 2018 and demonstrates AppHarvest’s ongoing commitment to cultivating interest in high-tech farming as it seeks to create America’s AgTech capital from inside Appalachia. Each retrofitted shipping container acts as a hands-on agricultural classroom for students, allowing them to grow and provide fresh leafy greens to their classmates and those in need in their communities.
AppHarvest has opened container farms in Eastern Kentucky at Madison Central High School in Richmond; Breathitt High School in Jackson; Shelby Valley High School in Pikeville; and Rowan County Senior High School and AppHarvest’s flagship farm at Rockcastle County High School in Morehead.
Elliott County High School’s container farm includes space to grow up to 2,760 seedlings and 2,960 mature plants, all at once in a nutrient film technique (NFT) system. NFT is a water-saving system in which plant roots are continuously fed all necessary water and nutrients by a shallow stream, also called “film.” Excess water drains to a holding tank and is then recirculated. This system of high-tech growing sets the Elliott County container apart from AppHarvest’s other educational containers, which have operated hydroponically and vertically.
“One of our goals at AppHarvest is to build an AgTech capital right here in Appalachia,” said Jonathan Webb, AppHarvest Founder, and CEO. “We want to see communities across the region use technology to bring farms to life. And in five years from now, it’ll be leaders from these very programs coming to us with ideas on how we continue to evolve and change agriculture.”
Makayla Rose, Elliott County High School agriculture teacher, will lead the newest container program.
The curriculum provided by AppHarvest will cover topics such as high-tech growing and an introductory course on local food systems and food resiliency.
“This is exciting. Some students who might not like to get in the dirt have a different way of growing vegetables,” said Garret Barker, president of Elliot County’s FFA chapter. “It’s different than my farm at home. It doesn’t depend on outside factors like the rain. It’s all controlled by an app.”
Lead Photo: Elliott County High School receives new container farm through AppHarvest (Kimberly Keagy/ WSAZ)
Brick Street Farms Expands Through Florida and East Coast
“We really wanted to bring food production to the point of consumption, so we’re focused on embedding our farms in urban areas,” says Shannon O’Malley, CEO, and co-founder of Florida-based container farming company, Brick Street Farms
"We Are As Much A
Technology Company
As We Are A Farm Operator”
“We really wanted to bring food production to the point of consumption, so we’re focused on embedding our farms in urban areas,” says Shannon O’Malley, CEO, and co-founder of Florida-based container farming company, Brick Street Farms.
The company was founded by Shannon and her husband Bradley, who combined her expertise in electrical engineering with his background in software development to design their own shipping container farms.
According to Shannon, a major differentiator of Brick Streets Farms is that the company manufactures and operates its own shipping container farms.
Brick Street Farms Hubs
Brick Street Farms has recently secured a significant investment from Lykes Brothers, which is reportedly one of the largest and longest-running private agricultural companies in the United States. During the official announcement last week, the financial investment will be used to aggressively expand Brick Street Farms hubs, which are the combination of container farms with a retail front in densely populated areas.
Click here to Zoom the photo. (Photo courtesy of Brick Street Farms)
According to Shannon, this expansion will begin in west-central Florida then expand to the east coast. From these hubs, Brick Street Farms will also introduce home delivery and will support restaurant partners located within 50-100 miles of the hubs. Already in 272 Publix supermarkets, Brick Street Farms will continue this partnership and plans to expand into additional product categories.
Building a resilient, multi-channel sales strategy
Brick Street Farms was first developed in 2015, and during its early years, the company predominantly sold its products to restaurants and directly to customers. However, the pandemic-induced shutdown in 2020 resulted in the loss of 70% of Brick Street Farms’ clients due to restaurant closures. As Shannon explains, Brick Street Farms was already selling its products in the GreenWise section at Publix supermarkets, which is reportedly the largest employee-owned supermarket chain in the US. This partnership allowed Brick Street Farms to quickly pivot following the mandated closure of restaurants.
“In the same month that Florida went into lockdown, grocery stores saw an incredible jump in demand so we were able to quickly pivot and provide our vegetables to grocery stores within a week. We are currently in 272 Publix stores and are working to expand into west-central Florida,” says Shannon. The state of Florida has since reopened and Brick Street Farms was able to bring back its previous accounts and sign new ones, according to Shannon.
Brick Street Farms also has its own gourmet market located at the farm that is open six days per week. Consumers can shop either on-site or online, with contactless delivery available. Shannon also explains that the company has adopted a unique twist to community-supported agriculture. By subscribing to a farm membership, consumers receive a discount and support the recently approved non-profit, Desert Farms Foundation.
“We established Desert Farms Foundation to help us bring container farms to food deserts within the United States. With a farm membership, 1% of the proceeds go to Desert Farms Foundation to really support community agriculture,” explains Shannon.
Thrive Containers
“Our containers are under the name Thrive Containers, which is wholly owned by Brick Street Farms. Our containers are the equivalent of 2-3 acres of traditional farmland. They use very little water, are energetically efficient, produce very little waste and use no chemicals. Since our products are wash-free, our customers get the benefits of long-lasting produce,” explains Shannon.
According to Shannon, Brick Street Farms is as much an agtech company as it is a farm operator. The company decided to establish Thrive Containers as its own entity within Brick Street Farms in order to differentiate between the food production and manufacturing aspect of the company. “When people see Brick Street Farms, we want them to think of butterhead lettuce, basil and our other vegetables,” notes Shannon.
Thrive Containers does not sell its container farms to third parties, but instead continuously improves the farm design for current and future installations. As Shannon explains, the company focuses on designing intelligent systems that can adjust to indoor and outdoor environmental conditions. Thrive containers have more than 120 sensors in and around the farm to monitor and respond to ambient temperature, humidity, carbon dioxide, vapor pressure deficit, etc.
Brick Street Farms and Thrive Containers work closely, with the engineers and designers having all undergone farmer training to ensure that the systems designed truly respond to the needs of Brick Street Farms’ growers.
Why Florida?
While warm and sunny Florida may seem ideal for outdoor agriculture, Shannon explains that soil conditions make soil-based agriculture somewhat difficult. She says that Florida soils are rather degraded and sandy, lack nutrients and lack natural bacteria, meaning farmers need to spend significant time and effort on rebuilding soils. Also, water sources are highly saline because of our position at level, near the coast, and with a low water table. Finally, the lack of winter makes it difficult to regulate pest cycles.
Lead photo: Co-founders Brad Doyle and Shannon O’Malley
For more information:
Madeline McNaughton, Head of Business Development
Brick Street Farms
madeline@brickstreetfarms.com
www.brickstreetfarms.com
Publication date: Thu 27 May 2021
Author: Rebekka Boekhout
© VerticalFarmDaily.com