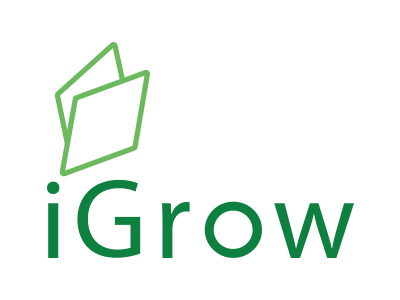
Welcome to iGrow News, Your Source for the World of Indoor Vertical Farming
CANADA: Thursday, July 8th, 2021 - 12:00 PM EST
Sit back and learn more about Growcer's beginnings, our farm's uses, and essential considerations for starting your own Growcer project. It will be an informal opportunity to ask our team questions and learn more!
Every first Thursday of the month, we'll be hosting a Meet and Eat that anyone can join; however, we're going to have it on the second Thursday in July to accommodate for the statutory holiday on Thursday, July 1st.
Register Now →
Sit back and learn more about Growcer's beginnings, our farm's uses, and essential considerations for starting your own Growcer project. It will be an informal opportunity to ask our team questions and learn more!
SIGN UP TODAY
Thursday, July 8th, 2021
12:00 PM EST
For Vertical Farms To Succeed, Sensors Must Take Center Stage
Vertical farming—the process of cultivating produce in stacked, indoor shelves, rather than side-by-side in fields—is a fast-growing industry (pardon the pun)
February 19, 2021
Vertical farming—the process of cultivating produce in stacked, indoor shelves, rather than side-by-side in fields—is a fast-growing industry (pardon the pun). Since it was conjured (or revived, depending who you ask) in a 1999 Columbia University lecture, the technology has grown into a global industry set to be worth $13.5 billion by 2030.
Companies like Plenty, Bowery Farms, and Infarm have innovated vertical farming with a dazzling array of modular, IoT-connected smart devices, which can improve plant “recipes” (the insider term for creating better, more nutritious food) and ramp efficiency alongside vast improvements on water and land usage.
Berlin’s Infarm, for example, claims to have saved over 10m gallons of water and 500,000 square feet of land across its 1,200 farming units, installed in supermarkets in restaurants).
But it is scale and efficiency that proves vertical farming’s bete noir. Leafy greens—low on energy demands and relatively high in price—constitute the lion’s share of output. High-energy food like cereals and potatoes, essential to human survival, remain firmly within the wheelhouse of traditional farms, which already occupy 40% of livable land on Earth, and one of our biggest environmental threats.
“What’s really needed, and that will come with time, is a humanitarian aspect to (vertical farming), which addresses food crises and starvation issues in, say, sub-Saharan Africa where farmers have to put up with horrible things like invasion of locusts,” says Dickson Despommier, the professor who popularized the medium 22 years ago. “Locusts would have a very difficult time invading a vertical farm.”
To feed the world, however, vertical farms need better lights. LED technology has already skyrocketed since its mainstream rollout in the 1960s. “Haitz’s Law” dictates that LED light increases by a factor of 20 and cost drops by a factor of ten every decade.
“The direction is clear: the prices have gone down, the efficiencies have gone up, and I see that continuing,” says Lars Aikala, CEO of Valoya, a leading supplier of LED lights to the vertical farming industry.
But things are getting more complex. Nowadays companies like Valoya can tinker with light spectra to increase growth rates in certain plants while reducing energy costs. “When we started in 2009 this field was pretty much untouched,” says Aikala.
Experts expect Haitz’s Law to tail off in the coming years, as technology becomes smaller, compacter and tougher to scale up. Rather, the next big leaps in LED technology will come via smart sensors, which will help lights replicate night and day, isolate spectra and better tailor themselves to plants’ preferred sunlight.
“If growers want to replicate seasons all year round they have to replicate and control all these parameters in a very narrow window, so plants can survive and grow in a healthy state all year round,” says Fei Jia, technical solutions manager at Heliospectra. “LED lighting allows this because of a high photon efficiency.
“Smart farming is the trend in lighting.”
An added bonus is that around 95% of an LED light is recyclable, helping vertical farmers persuade the public they’re not just a flash in the pan. When sensor technology can lower costs enough to produce carbs and other vital produce, their companies can finally claim to be solving a part of a food crisis that is leaving almost a billion people without adequate access to nutrition each year.
“We’re just at the starting point of (LED) technology, so the price will go down but conversion is going to go up to create more power with less energy,” says Infarm co-founder Erez Galonska. “Now we’re standing on 50-60%, and with the next generation of technology, we easily improve the LEDs. It’s already improved so we’re more energy-efficient already.”
FILED UNDER: CLEAN TECH, CONSUMER, FEATURES, SOFTWARE, STARTUPS, TOP STORY
UNFI Picks Up Living Greens Farm Products in Midwest Expansion
Living Greens Farm (LGF), the largest vertical, indoor aeroponic farm in the US that provides year-round fresh salads, salad kits, microgreens and herbs, announced the addition of significant new retail distribution of its products in the upper Midwest to independent, specialty, and co-op retailers
I|mage from: Living Green Farms
Living Greens Farm (LGF), the largest vertical, indoor aeroponic farm in the US that provides year-round fresh salads, salad kits, microgreens and herbs, announced the addition of significant new retail distribution of its products in the upper Midwest to independent, specialty, and co-op retailers.
Starting February 2021, LGF’s full line of products featuring ready-to-eat bagged salad products (Caesar Salad Kit, Southwest Salad Kit, Harvest Salad Kit, Chopped Romaine, and Chopped Butter Lettuce) will be carried by UNFI Produce Prescott (formerly Alberts Fresh Produce). UNFI Produce Prescott is a division of UNFI, which distributes food products to thousands of stores nationwide. Their focus is on independent, specialty and co-op retailers.
UNFI has eight warehouses nationwide. LGF’s products will be carried by their upper Midwest location, located just across the river from the Twin Cities in Prescott, WI. This distribution center services hundreds of retailers throughout Minnesota, Wisconsin, Illinois, North Dakota, South Dakota, Missouri, Iowa and Nebraska. UNFI is the first national Certified Organic distributor, something they take a lot of pride in. Their produce and floral businesses are rooted in local farms and seasonal import growers.
LGF’s proprietary vertical indoor farming method yields the highest quality and freshest produce available. This is because there are no pesticides or chemicals used in the growing process. And because LGF’s growing, cleaning and bagging process significantly reduces handling and time to the retail shelf, consumers enjoy the freshest product on the market. These benefits continue to attract new users and new retail distribution as UNFI Produce Prescott is the second UNFI location to carry LGF. In December, UNFI’s Hopkins, MN location began offering LGF products.
For more information on why Living Greens Farm products are the cleanest, freshest and healthiest farm salads and greens available, go to www.livinggreensfarm.com.
Fifth Season Takes Vertical Farming to a Whole New Level
Fifth Season’s verdant baby spinach screams farm fresh even though it’s grown nowhere near traditional farmland. The sweet and slightly crunchy greens are grown in a Braddock warehouse on racks stacked 30 feet high. Located just a stone’s throw from U.S. Steel’s Mon Valley Works Edgar Thomson Plant, it is urban farming at its core
Image from: Pittsburgh Post-Gazzette
Fifth Season’s verdant baby spinach screams farm fresh even though it’s grown nowhere near traditional farmland. The sweet and slightly crunchy greens are grown in a Braddock warehouse on racks stacked 30 feet high. Located just a stone’s throw from U.S. Steel’s Mon Valley Works Edgar Thomson Plant, it is urban farming at its core.
What makes the vertical farming operation especially unique is that it is automated and robots call the shots. About 40 to 60 machines are involved in every step of the life of the spinach and other leafy greens, from planting the seed to providing nutrients to the final packing.
Fifth Season does employ local “farm workers” to assist the robots in seeding, harvesting, packaging, quality assurance and control using computer software, but there is no human touch involved through it all.
“The first time someone ever touches the spinach leaf with a finger is when the package is opened,” says Grant Vandenbussche, chief category officer.
Co-founded by brothers Austin and Brac Webb and Austin Lawrence, Fifth Season started a year ago. Within months it was rolling out its baby spinach, leafy greens and salad kits.
“We wanted a name that represents what we are doing,” says Austin Webb, 32, who also is the CEO. “It is a call to the fact we have created an entirely new season. It is 24/7, 365 with the technology we have built.”
None of them planned to become modern farmers, says the Carnegie Mellon University grad, but they turned to vertical farming because it was an efficient, economically sustainable way to solve land and water woes.
Image from: thespoon.tech
‘Fields’ of Greens
Fifth Season grows an equivalent production of 200 acres in 25,000 square feet of grow space. Its “fields” are stacked on top of one another in vertical shelves. When you add up all that surface area of grow space, it is more like 126,000 square feet.
“We also quickly turn crops at the farm,” Mr. Vandenbussche says.
While spinach takes about 40 days to grow outdoors and can be harvested only twice during its peak season, it takes the crop only three or four weeks to grow in the controlled environment and is harvested 19 times. Once the plants are harvested, a new cycle of reseeding begins with fresh media, seeds and nutrients.
“That’s why we get so much more productivity,” he says. “We are immediately reseeding our ‘land.’”
This controlled environment yields quality produce because it is always peak season at Fifth Season, says Chris Cerveny, who heads the Grow R&D division. Greens are grown in the same conditions year-round, getting the exact amount of nutrients and water they need. Because pests and airborne toxins also are kept at bay, crops can be produced without pesticides.
All that TLC comes through in the slightly curled baby spinach, which is sweet and not grassy. The leaf doesn’t wilt or get slimy or lose its slight crunch even after two weeks of refrigeration.
A lot of thought was given even for the curl, which gives the spinach a stronger volume, making it look full and bountiful. The curl also makes the spinach more forkable unlike its flat-leaf counterpart that is hard to stab on a plate.
Other leafy greens such as kale, mustard, Chinese cabbage, green tatsoi and purple pac choi are featured in two blends — Bridge City and Three Rivers. Fifth Season plans to roll out its Romaine lettuce in spring.
The greens also are found in four types of salad kits — Sweet Grains (blended greens, quinoa, chickpeas, corn, feta and poppy seed dressing), Crunchy Sesame (blended greens, farro, sesame sticks, dried cranberries and ginger-mandarin dressing), Toasted Tuscan (spinach, lentils, sun-dried tomatoes, bagel chips and vinaigrette), and Spiced Southwest (blended greens, black beans, pepitas, cotija cheese, corn-salsa sticks and chipotle ranch dressing) — which are available online and in Giant Eagle stores. A fifth salad kit is in the works and is being called “a shakeup of one of the most classic salads.”
While machines are a big part of what Fifth Season does, it seeks to keep human connection alive. It recently launched a recipe blog for those who have an appetite for cooking and writing, The Green Room is devoted to cataloging personal memories, dream meals and recipes via short stories.
Fifth Season also has partnered with the Penguins and is providing greens for the team’s pregame meals for the 2020-21 season.
“We want people in Pittsburgh to be able to eat the exact same delicious blend of greens that Sidney Crosby and company are eating,” Mr. Webb says. “We want people to know that there’s a new way to grow food and to eat and experience it.”
Image from: Next Pittsburgh
It’s All Under Control
Everything from seeding to packaging is done in four rooms. The process starts in the seeding and processing room, where seeds and growing media are placed inside black planter-like boxes called inserts. Each has a unique code that’s traced by a software system. The inserts go on white trays that pass through a photo station, feeding information to the computer system, and then glide into the bio dome.
There are two rooms in the bio dome, each with a grow space of 12,500 square feet. They’re lit up with a pinkish-purplish glow from high-efficiency LED light bulbs that mimic the different seasons of the year.
“They are positioned over the plants at different heights depending on stage of growth,” Mr. Cerveny says. “This is partly how we can provide consistently ideal growing conditions.”
As the plants grow, they are moved by a robot to optimize their growth cycle. Full-grown crops are transferred to the harvesting room by another robot.
“Harvesting is where it becomes like a Willy Wonka factory,” Mr. Vandenbussche says.
Long rows of trays filled with tiny plants are sent on a conveyor system to a station where workers inspect them for quality with surgical tools. After inspection, the plants are harvested by a robot and then immediately ride up a tall conveyor to be packaged and sealed in a 34- to 36-degree room so they remain fresh.
“Every crop we grow gets evaluated for maximum flavor, volume, crunch and color,” he says.
The plants’ intense, dark color is controlled by LED light bulbs, which are dialed up or down to get the correct hue. Although they never see the sun, the greens don’t get into a funk as humans might.
“What humans see in terms of light and how chlorophyll responds during photosynthesis are two different things,” Mr. Cerveny says. “Plants really only need red and blue light to grow effectively. We include some additional colors to help bring out other quality aspects of our crops, but providing the full sunlight spectrum is effectively a waste of energy, especially indoors.
“To the human eye, it looks like the plants live in a land of purple and pink lights, but they are perfectly happy there.”
Even though the environment is controlled and the software system is constantly updated, no two plants are exactly the same. Some fight for light more than others. Some might fail the quality control test and end up in a compost waste facility if their flavor is off or their color is not right.
“That is what is so amazing. We have more control than any other farmer, and yet we have limitations. Every seed is different,” Mr. Vandenbussche says. “They are plants. They are real living organisms.”
Indoor Farming Services Provider Agrify Sets Terms For $25 Million IPO
Agrify was founded in 2016 and booked $9 million in revenue for the 12 months ended September 30, 2020. It plans to list on the Nasdaq under the symbol AGFY. Maxim Group LLC and Roth Capital are the joint bookrunners on the deal
Renaissance Capital Renaissance Capital
January 13, 2021
Agrify, which provides turnkey indoor farming solutions, announced terms for its IPO on Wednesday.
The Burlington, MA-based company plans to raise $25 million by offering 2.8 million shares at a price range of $8 to $10. At the midpoint of the proposed range, Agrify would command a fully diluted market value of $115 million.
The company claims to differentiate itself with a bundled solution of equipment, software, and services that is turnkey, end-to-end, fully integrated, and optimized for precision growing. Revenue mainly comes from core hardware products, the Agrify Vertical Farming Unit, as well as facility build-outs. Agrify provides products to a variety of agricultural segments, citing cannabis as a key market opportunity.
Agrify was founded in 2016 and booked $9 million in revenue for the 12 months ended September 30, 2020. It plans to list on the Nasdaq under the symbol AGFY. Maxim Group LLC and Roth Capital are the joint bookrunners on the deal.
The article Indoor farming services provider Agrify sets terms for $25 million IPO originally appeared on IPO investment manager Renaissance Capital's web site renaissancecapital.com.
Investment Disclosure: The information and opinions expressed herein were prepared by Renaissance Capital's research analysts and do not constitute an offer to buy or sell any security. Renaissance Capital's Renaissance IPO ETF (symbol: IPO), Renaissance International ETF (symbol: IPOS), or separately managed institutional accounts may have investments in securities of companies mentioned.
The views and opinions expressed herein are the views and opinions of the author and do not necessarily reflect those of Nasdaq, Inc.
Derby Vertical Farming Startup Gets £500K Funding to Develop ‘All In One’ Sensor
Derby-based Light Science Technologies delivers lighting, science and research-proven plant monitoring technology and software in partnership with world-leading university research teams
INVESTMENT NEWS / 13 JAN 2021
Derby-based Light Science Technologies delivers lighting, science and research-proven plant monitoring technology and software in partnership with world-leading university research teams. It delivers the right solution across multiple indoor applications such as vertical farming, medicinal plants, and greenhouses. Its full turnkey solution for Controlled Environment Agriculture (CEA) applications for next-generation scalable farming helps customers grow more with less.
Investment to boost agricultural productivity
Light Science Technologies just secured part of the £90M government investment to support the most innovative technology to boost agricultural productivity and set food production systems towards net zero emissions by 2040.
Furthermore, it is one of the 23 feasibility projects that has been awarded up to £500,000 from £4.3M funding that is meant for Science and Technology into Practice feasibility competition, as part of UKRI’s £90 million Transforming Food Production (TFP) program. Innovate UK drives productivity and economic growth by supporting businesses to develop and realize the potential of new ideas. Notably, Innovate UK is part of UK Research and Innovation.
Simon Deacon, CEO of Light Science Technologies added: “This is an especially important boost to our business. To be selected by Innovate UK is confirmation of the urgent need for more sustainable, productive, and cost-effective solutions in farming. Investment in UK technology and innovation in this sector is crucial in achieving a better approach to agricultural production and reducing emissions.”
Innovate UK Executive Chair Dr Ian Campbell said: “There are many innovative projects in our latest feasibility competition showcasing ideas for improving productivity and cutting emissions that range across the whole agricultural sector, from arable, to livestock, to sensor technology and to new biopesticides. Our funding and support for these projects is ongoing.”
Groundbreaking sensor technology
Along with partnership with Nottingham Trent University, the company will lead the project to develop a growing sensor and innovative transmission node for vertical farms over the next six months, which is in synergy with their light and science offering.
The IoT precision data solution for vertical farming will help in boosting 0roductivity and efficiency, thereby reflecting the government’s drive to help the agricultural sector grow economically with less environmental impact.
Light Science Technologies’ ‘all in one’ indoor farm sensor will let farms to monitor and control their environment by measuring key areas such as light, water, air, temperature, humidity, oxygen and soil, thereby ensuring optimal plant productivity and yield. Also, this sensor will form a vital part of its bespoke offering, reducing energy and saving costs using technology and real-time data.
Demand for CEA market!
Of late, there is a growing demand for the Controlled Environment Agricultural (CEA) market, which is growing fast at a CAGR of 21%. The demand is mainly from AgTech CEA farmers looking to install or replace existing indoor farms to achieve a maximum yield on crops for optimum profitability. However, the high startup costs attract investment from stakeholders eyeing the potentially significant ROI opportunity.
Light Science Technologies provides custom-made solution for the CEA market, and works with growers to provide an integrated, cost-effective and low maintenance solution that can be used across different crops to achieve maximum yield. Eventually, it creates the full growing recipe of lighting, nutrients, and the environment.
Notably, Light Science Technologies is focused on becoming a technology-driven trailblazer in vertical farming innovation and technology over the next four years as it eyes to shape up the future of the CEA market.
Autogrow Launches Wireless Smart Sensor Network Into US $40 Billion Global Greenhouse Market
“We’ve advocated for a long time in the industry that you can’t manage what you don’t measure and the decisions you make are only as good as the sensor technology gathering the data
5 February 2020
Leading AgTech expert Autogrow has released a wireless smart sensor giving greenhouse operators high-density microclimate data to improve yield, quality and decision making.
Each Folium sensor gathers environmental data including temperature, humidity, CO2, PAR, RAD and barometric pressure, which growers can view on a heatmap - immediately seeing differences across their grow areas. Folium enables greenhouse operators unlimited depth of environmental analysis, as the number of sensors is completely scalable.
“We’ve advocated for a long time in the industry that you can’t manage what you don’t measure and the decisions you make are only as good as the sensor technology gathering the data. Folium will go a long way to giving growers actionable data using state-of-the-art heat mapping technology. It reveals what the eye can’t see,” explains CEO Darryn Keiller.
“According to market analysts, the global greenhouse market is looking to exceed US$40billion in the next 5 years, so it’s a growth market we are excited to support. With over two years of research and development, and a huge amount of hard work from my team, it’s fantastic to have Folium in the market and offer greenhouse growers new technology that will substantially impact their bottom line.”
Folium’s target customer is large greenhouse growers who, simply by the size of their operations, require high-density climate data to ensure all areas of their facilities are providing the optimal environment for growth. The sensor network reliably scales to any size greenhouse.
Chief Technology Officer Jonathan Morgan notes that sensor technology can be incredibly complex but the experience for the grower should be easy and meaningful.
“We’ve been lucky to work with some fantastic growers throughout the development of Folium who have shared their time, knowledge and grow operations to ensure we are solving some of the pain points they experience when dealing with microclimates,” says Mr. Morgan.
“This is just the beginning of what Folium will be able to do. With the way our technology has been designed, we can easily introduce new features that continually support growers. They can also add more Folium units as their business grows and being connected to our cloud platform gives them access anywhere at any time.”
For more information www.autogrow.com/products/folium
PHOTOS: Folium unit in a greenhouse / Heatmap image showing PAR readings
Kylie Horomia
Head of Brand & Communications
(m) +6421 733 025
About Autogrow
Autogrow leverages the power of technology, data science, and plant biology to provide indoor growers affordable, accessible and easy-to-use innovation – 24/7, anywhere in the world.
Our solutions support growers and resellers in over 40 countries producing over 100 different crop types.
We are the experts in Controlled Environment Agriculture (CEA) and continue to stay ahead of a rapidly evolving landscape.
Autogrow, Level 1, Building 3, 61 Constellation Drive, Mairangi Bay, Auckland 0632, New Zealand
The Role of Sensors And Data Collection In A Successful Vertical Farm
It’s widely recognized that vertical farming has many advantages over traditional crop-growing methods. Simply put, despite relatively high setup and operational costs, the production per unit of growth area in vertical farms easily exceeds that in the most advanced greenhouses
It’s widely recognized that vertical farming has many advantages over traditional crop-growing methods. Simply put, despite relatively high setup and operational costs, the production per unit of growth area in vertical farms easily exceeds that in the most advanced greenhouses. But to consistently hit this level of production, you need to ensure growth conditions are continuously at their best. This is where sensors and data play a pivotal role, and why they’re ready to transform the future of vertical farming.
What data do you need to capture?
To use sensors and data effectively, you first need to know what kind of data is valuable and why. The most important values to measure are the following conditions for growth:
Climate (characterized by a combination of air temperature, humidity levels, CO2 levels and air speed)
Plant temperature
The nutrient composition of the irrigation water
The light level and spectrum (as perceived by the plants)
Plant morphology, deficiencies and growth (phenotyping)
These conditions are significant for different reasons. The difference between plant temperature and air temperature, for example, can tell us whether the leaves’ stomata are open. If they aren’t, the plant cannot absorb CO2 and convert it into biomass. Likewise, we can continually measure the pH (acidity) and EC (electrical conductivity) of the irrigation water to ensure optimal plant growth. We are also cooperating with several companies that are developing sensors to measure other parameters of the irrigation water (such as f.e. iron or magnesium).
You might be surprised to see that we measure the light level and spectrum as perceived by the plants, presuming that we can deduce this already from the type and number of LED lighting modules installed. However, our research has found that the plants’ perceived light level can deviate up to as high as a factor of two from the light level installed depending on the optical properties of the materials used between and above the plants. This value largely depends on the degree to which the plants cover the growth area, and with such a high potential deviation rate, is one we need to measure and track to ensure optimal growth conditions.
The value of monitoring every stage of the growth process
Sensors enable us to monitor these growth conditions, recognize anomalies and identify problems as early as possible. By detecting problems at an early stage, we can respond pro-actively instead of reactively. This holds especially true for system-related problems – such as the temperature deviating from an intended setpoint – which can be rectified almost immediately.
In addition to measuring growth conditions, measuring growth results also provides valuable data – using parameters such as plant size, height, weight and color. We can use cameras to capture images of the plants in the growth layer, for example, following growth development over time and gauging whether growth meets expectations or not by comparing it to data captured in previous growth cycles under similar conditions. Like sensors, cameras can also help to prevent problems early by enabling the detection of early-stage growth deficiencies (such as tip-burn) and diseases.
How our sensor and data platform can help
Our sensor platform allows us to measure the conditions most important for plant growth. These conditions include climate parameters and irrigation parameters (including water supplied/drained in addition to pH and EC). At the GrowWise Center in Eindhoven’s High Tech Campus (HTC), we collect about 1,600 unique setpoint and sensor readings every ten minutes from our eight climate cells – valuable ongoing research that helps us to continuously build on our knowledge base and improve the solutions we can offer.
The sensors can be placed anywhere within a growth layer and wirelessly communicate the data they gather to the system backend. Cloud applications then retrieve this data and visualize the information that is most relevant and useful to plant specialists and growers. The development of the sensor platform is part of Horizon 2020 Internet of Food (H2020 IoF), a European Commission (EC) innovation project, in which we are closely collaborating with Staay Food Group.
The future of vertical farming
The benefits of modern sensor technology and data science are already manifold, but technological advancements in areas such as AI promise to be truly revolutionary. Signify is currently researching AI-based algorithms that can train models to couple realized growth conditions with realized growth results, for example, in a process known as ‘supervised learning’. This will ultimately enable us to predict the precise growth conditions to achieve optimal growth – and meet the most specific grower needs. AI techniques like machine learning can also be used to analyze images of plants’ growth to immediately detect any unexpected deviations or growth deficiencies.
Right now, our sensor and data platform combined with cloud applications adds considerable value for our plant specialists and customers – from monitoring the growth process and detecting problems as early as possible to accelerating the development of new optimized growth recipes. It’s clear that sensors and the data they capture play a pivotal role in the continuing evolution of vertical farms. Signify and our customers will not just be a part of this revolution – we will drive it.
Dr. Marcel Krijn is a principal research scientist at Signify and has over ten years of experience in horticulture. His primary interest is the advancement of vertical farming as a mainstream method of food production that is both energy-efficient and commercially beneficial for Signify’s customers. His research efforts also focus on the development of new options for data-driven growth management.
The Role of Sensors And Data Collection In A Successful Vertical Farm
It’s widely recognized that vertical farming has many advantages over traditional crop-growing methods. Simply put, despite relatively high setup and operational costs, the production per unit of growth area in vertical farms easily exceeds that in the most advanced greenhouses. But to consistently hit this level of production, you need to ensure growth conditions are continuously at their best. This is where sensors and data play a pivotal role, and why they’re ready to transform the future of vertical farming.
What data do you need to capture?
To use sensors and data effectively, you first need to know what kind of data is valuable and why. The most important values to measure are the following conditions for growth:
• Climate (characterized by a combination of air temperature, humidity levels, CO2 levels and air speed)
• Plant temperature
• The nutrient composition of the irrigation water
• The light level and spectrum (as perceived by the plants)
• Plant morphology, deficiencies and growth (phenotyping)
These conditions are significant for different reasons. The difference between plant temperature and air temperature, for example, can tell us whether the leaves’ stomata are open. If they aren’t, the plant cannot absorb CO2 and convert it into biomass. Likewise, we can continually measure the pH (acidity) and EC (electrical conductivity) of the irrigation water to ensure optimal plant growth. We are also cooperating with several companies that are developing sensors to measure other parameters of the irrigation water (such as f.e. iron or magnesium).
You might be surprised to see that we measure the light level and spectrum as perceived by the plants, presuming that we can deduce this already from the type and number of LED lighting modules installed. However, our research has found that the plants’ perceived light level can deviate up to as high as a factor of two from the light level installed depending on the optical properties of the materials used between and above the plants. This value largely depends on the degree to which the plants cover the growth area, and with such a high potential deviation rate, is one we need to measure and track to ensure optimal growth conditions.
The value of monitoring every stage of the growth process
Sensors enable us to monitor these growth conditions, recognize anomalies and identify problems as early as possible. By detecting problems at an early stage, we can respond pro-actively instead of reactively. This holds especially true for system-related problems – such as the temperature deviating from an intended setpoint – which can be rectified almost immediately.
In addition to measuring growth conditions, measuring growth results also provides valuable data – using parameters such as plant size, height, weight and color. We can use cameras to capture images of the plants in the growth layer, for example, following growth development over time and gauging whether growth meets expectations or not by comparing it to data captured in previous growth cycles under similar conditions. Like sensors, cameras can also help to prevent problems early by enabling the detection of early-stage growth deficiencies (such as tip-burn) and diseases.
How our sensor and data platform can help
Our sensor platform allows us to measure the conditions most important for plant growth. These conditions include climate parameters and irrigation parameters (including water supplied/drained in addition to pH and EC). At the GrowWise Center in Eindhoven’s High Tech Campus (HTC), we collect about 1,600 unique setpoint and sensor readings every ten minutes from our eight climate cells – valuable ongoing research that helps us to continuously build on our knowledge base and improve the solutions we can offer.
The sensors can be placed anywhere within a growth layer and wirelessly communicate the data they gather to the system backend. Cloud applications then retrieve this data and visualize the information that is most relevant and useful to plant specialists and growers. The development of the sensor platform is part of Horizon 2020 Internet of Food (H2020 IoF), a European Commission (EC) innovation project, in which we are closely collaborating with Staay Food Group.
The future of vertical farming
The benefits of modern sensor technology and data science are already manifold, but technological advancements in areas such as AI promise to be truly revolutionary. Signify is currently researching AI-based algorithms that can train models to couple realized growth conditions with realized growth results, for example, in a process known as ‘supervised learning’. This will ultimately enable us to predict the precise growth conditions to achieve optimal growth – and meet the most specific grower needs. AI techniques like machine learning can also be used to analyze images of plants’ growth to immediately detect any unexpected deviations or growth deficiencies.
Right now, our sensor and data platform combined with cloud applications adds considerable value for our plant specialists and customers – from monitoring the growth process and detecting problems as early as possible to accelerating the development of new optimized growth recipes. It’s clear that sensors and the data they capture play a pivotal role in the continuing evolution of vertical farms.
Signify and our customers will not just be a part of this revolution – we will drive it.
Smart-Farming Startup Grow Computer Has Just Launched Their First Product - A Digital Growing Platform Called GrowStrip
BROOKLYN, NY, September 26, 2018
GrowStrip offers a user-friendly way for growers of all kinds to make their grows smarter through a simple hardware and software platform. GrowStrip gives any farmer, student, home grower, or researcher the ability to collect environmental and energy data, build automation, remotely monitor, and receive alerts.
The system was designed for usability and takes only minutes to setup, requires no tools, and is totally plug and play.
Indoor farming is an exciting global trend and is empowering anybody to grow almost any plant in their own homes. Hydroponics and other indoor systems conserve water, remove the need for pesticides, and allow a year-round growing cycle. Around the world, hydroponic systems are being used to build amazing indoor farms, empower entrepreneurs, and teach STEAM education in K–12 classrooms.
The company grew out of two communities of agtech startups, one in Brooklyn, NY, and the other in Sacramento, CA. Co-founders Dan Nelson (CEO) and Ian McEachern (CTO) met online through MIT’s Open Agriculture forums, and built out the rest of team at the urban farming co-working space AgTech X in Brooklyn.
McEachern is a medical device engineer with over fifteen years’ experience developing exciting products and, cutting-edge medical devices, including artificial hearts. Nelson is an experienced startup founder and has worked with dozens of companies as a for-hire virtual CFO.
Grow Computer’s vision is to empower people around the world to connect and share plant growing “recipes” and new ideas. They hope this will democratize critical technologies and techniques. In Nelson’s words, Grow Computer may unlock a new urban farming revolution by providing access to better hardware around the world. If we can get a distributed community of growers working together, the potential for scientific, educational, economic, phenotypical, genetic, or operational innovations becomes incredible.”
Grow Computer is proud to launch our crowdfunding campaign in conjunction with Agritecture Xchange, taking place in Brooklyn from September 24–29.
The Xchange conference is a week-long series of events in New York City that will explore agriculture’s role within the sustainable city movement.
GrowStrip will launch exclusively on Indiegogo starting on Wednesday, September 26.
GrowStrip retails for around $600 US and ships with a thermometer and camera, as well as the free, open-source software platform. Indiegogo buyers can purchase GrowStrips at a significant discount.
Why Indoor Growing is Important
Urban populations are growing, bringing with them a growing need for high-quality, sustainably produced food.
To meet global demand, the world needs more farmers, and farms that are more efficient than ever.
We believe that indoor agriculture is the answer. Hydroponics, rooftop greenhouses, and vertical farms are proliferating in major cities and in people’s homes around the world. But, the available technology is still either prohibitively expensive or stuck in the 1980s.
press@growcomputer.com
40 Bushwick Ave
C/O AgTech X
Brooklyn, NY 11206
###
Ikea’s Teaching You How to Use a Hydroponic Vertical Farm
Ikea’s Teaching You How to Use a Hydroponic Vertical Farm
IKEA‘s innovation lab Space10 created a pop-up hydroponic vertical farm during this year’s London Design Festival. The space was created to showcase Space10’s Lokal project, where microgreens are grown indoors, locally and vertically, aims to provide a space-saving and sustainable way for people to grow their own food, as well as testing how Londoners felt about food grown hydroponically and, more importantly, whether they liked the taste of the microgreens.
Agrilyst Raises Another $1.5M For Its Intelligent Indoor Farming Platform
Agrilyst Raises Another $1.5M For Its Intelligent Indoor Farming Platform
February 7, 2018 | Frederic Lardinois (@fredericl)
Agrilyst, a platform that makes it easier for indoor farmers to manage their crops based on sensor data, today announced that it has raised a $1.5 million funding round from iSelect Fund, Argonautic Ventures, Horizons Lab (Horizons Venture’s seed fund) and Onlan Capital Fund. The new investors were joined by existing investors Compound and the New York State Innovation Capital Fund. That’s on top of the $1 million round Agrilyst announced in 2016.
As Agrilyst co-founder and CEO Allison Kopf tells us, the company, which won our Disrupt San Francisco Startup Battlefield in 2015, has been on a bit of a roll lately. It added 100 new customers in 2017 and saw 500 percent growth in both revenue and customers since 2016. Its service is now available in 10 countries and its tools support more than 50 vegetables and 800 crops.
When the company launched, the team was very adamant that it didn’t want to be seen as a tool for indoor cannabis growers, but it recently added support for cannabis, as well as for floriculture and insect productions.
“We see a world where computation cost is driven to zero and we now have the resources to monitor the growth, health, and biology of every single seed,” says Phil Chen, advisor at Horizons Lab. “I see Allison and her team at Agrilyst as the interpreters of this data to secure future food sources.”
As for the team, it’s worth noting that the company recently brought on both a new CTO (to replace co-founder and CTO Jason Camp, who left the company last year) and a VP of Customer Success.
Unsurprisingly, Agrilyst plans to use the new funding to support its growth and expand into new markets and product lines. Having a number of new investors that focus on the large Chinese market (Horizons, Argonautic, and Onland) will surely help the company expand into this market, too.