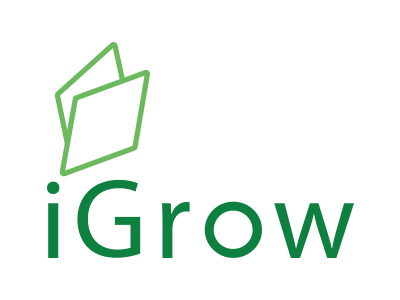
Welcome to iGrow News, Your Source for the World of Indoor Vertical Farming
Step Away From That Screen And On To Our Expanded Expo Floor
There's nothing like an in-person event for getting a first-hand look at the latest product innovations. So step away from that computer screen, step onto our expo floor and see live product demonstrations...Touch new products...Ask questions and gather feedback from company execs and peers in the booth
BIGGER, BETTER EXPO FLOOR OFFERS PERFECT ZOOM FATIGUE FIX!
(And some pretty great solutions for your business, too)
There's nothing like an in-person event for getting a first-hand look at the latest product innovations. So step away from that computer screen, step on to our expo floor and see live product demonstrations...Touch new products...Ask questions and gather feedback from company execs and peers in the booth.
We've significantly expanded our expo floor to bring you even more top names, established best-sellers and promising start-ups. See the latest in lighting, operating, automation and control systems, growth chambers, seed treatments, plant nutrition, greenhouse & hydroponic supplies, substrates, pest control, irrigation, equipment & design resources and so much more from companies like:
LEARN MORE
YOUR TWO-DAY INDOOR AG-CON EXPERIENCE PACKAGE
Indoor Ag-Con is so much more than an event. It's an experience! And one you don't want to miss. Hear from 70+ speakers, network with industry peers, see the latest product innovations. Then, head back to your operation armed with actionable ideas and profitable strategies that promise to grow your business!
Register before our Early Bird Rates end on August 16, 2021 to save up to $300 on our full access pass. And if your plans change, no worries! Passes are completely refundable prior to September 27, 2021, and include:
All Keynotes, Morning Conference Sessions, Afternoon Panels
Expo Floor Access
Welcome Gift Bag
Complimentary On-Demand Access to In-Depth, 2-Day "Financing Indoor Ag Seed To Scale" webinar
White Paper From The Packer & PMG presenting the latest research on indoor growing & sustainability
Lunch Daily
Show Floor Cocktail Receptions
Event App
Access to Indoor Ag-Con Library
REGISTER NOW & SAVE UP TO $300
OUR SAFETY PROMISE
Your health and safety are priority one at Indoor Ag-Con Orlando.
Rest assured that the Indoor Ag-Con team is closely monitoring the
guidelines issued by the CDC, state and local officials. We're working with our venue partner, Hilton Orlando, to provide you with a safe and
productive environment to conduct business.
SPECIAL THANKS TO OUR INDOOR AG-CON SPONSORS,
MEDIA & MARKETING ALLIES
Indoor Ag-Con, 3834 Silvestri Lane, Las Vegas, NV 89120, United States
Optimizing Resource Use Efficiency In CEA System
An important factor affecting the profitability of vertical farming is a grower’s ability to consistently deliver a predictable product
Date: July 29, 2021
Time: 2 p.m. - 3 p.m. EDT
Presented by: Murat Kacira (The University of Arizona)
Click Here To Register
Webinar Description
An important factor affecting the profitability of vertical farming is a grower’s ability to consistently deliver a predictable product. To achieve this, growers must create an environment that supplies all the crop’s needs over its entire growth cycle by identifying and co-optimizing environmental variables such as CO2, light, humidity, airflow, and other parameters. This presentation will focus on real-time sensing, monitoring, and climate control strategies with system designs for environmental uniformity leading to enhanced resource use efficiency in CEA system.
Dr. Murat Kacira (Professor)
Murat Kacira is director of the Controlled Environment Agriculture Center and he is a professor in the Biosystems Engineering Department at the University of Arizona. He received his B.S. degree in Agricultural Engineering in Cukurova University in Turkey and M.Sc. and Ph.D. degrees from Food, Agricultural and Biological Engineering from The Ohio State University in USA. His research involves automation, environmental control, alternative energy integrated CEA systems and resource use optimization in controlled environment agriculture systems including greenhouses and vertical farming-based plant factories with artificial lighting. He is a member of American Society of Agricultural and Biological Engineers (ASABE), American Society of Horticultural Sciences (ASHS), and International Society for Horticultural Science (ISHS). He serves as Chair of the Division Precision Horticulture Engineering under ISHS.
Special thanks to our Industry partners
Join Today
If you have any questions or would like to know more about GLASE, please contact its executive director Erico Mattos at em796@cornell.edu
Designing Future-Proof Substrate for CEA
“I believe that Horticubes® AeroMax will be the most relevant substrate in the industry,” says Dr. Vijay Rapaka, global research manager at OASIS® Grower Solutions, a division of Smithers-Oasis Company, about Horticubes AeroMax. This substrate is engineered for the precision growing of young plants for hydroponic farming of leafy greens and compact plants.
OASIS Grower Solutions Launches Horticubes AeroMax
“I believe that Horticubes® AeroMax will be the most relevant substrate in the industry,” says Dr. Vijay Rapaka, global research manager at OASIS® Grower Solutions, a division of Smithers-Oasis Company, about Horticubes AeroMax. This substrate is engineered for the precision growing of young plants for hydroponic farming of leafy greens and compact plants.
OASIS Grower Solutions was established in the mid-1950s and began with the development of ornamental growing media. Fast forward to the present day and the company has expanded its product offering to meet the demands of the ever-developing horticultural industry, which now includes vertical farms and highly automated greenhouses. OASIS Grower Solutions currently has manufacturing locations in 20 countries and develops new products through in-house research and customer feedback. The company introduced its Horticubes line in the 1980s, then added Horticubes XL in 2011. Now, OASIS Grower Solutions introduces Horticubes AeroMax for the hydroponic production of leafy greens.
The benefits
When designing the Horticubes AeroMax substrate, OASIS Grower Solutions focused on what they consider to be the three cardinal rules of horticultural substrate development. Firstly, a substrate should allow the grower to propagate healthy, uniform, and vigorous young plants. The second rule is that a substrate should support growers in modulating crop growth by facilitating the acceleration or deceleration of growth, or the use of wet and dry cycles. Finally, substrates should be able to withstand automated processes. This, according to Vijay, is especially important in controlled environment agriculture as automation is becoming increasingly used.
“With more LEDs, IoT, and automated processes, we knew that we needed a substrate that allowed us to precise control of young plant growth. We needed a smart substrate exclusively designed for precision hydroponic farming,” says Vijay.
The Horticubes AeroMax is engineered according to these cardinal rules and is unique from other substrates in five main ways. As denoted in its name, AeroMax is a very porous media that enhances the oxygenation of the root zone so that seeds can germinate quickly and uniformly. According to Vijay, more air in the root zone also increases root health and root branching. AeroMax is also different in that the substrate is low-density, low-strength which makes the substrate light and airy. As a result, roots can easily penetrate the substrate and express their full potential without expending much energy.
“With hydroponics, we need the roots to get to the nutrients as soon as possible. We don’t want the substrate to be a barrier,” explains Vijay.
The third advantage of Horticubes AeroMax is the good drainage which virtually eliminates any chance of overwatering because the excess water easily drains out. This also means that growers can achieve maximum nutrient refreshment rates. Fourthly, OASIS Grower Solutions tested multiple substrate colors but eventually selected black as this allows growers to increase the surface temperature of the substrate by a few degrees, thereby accelerating crop growth. A final benefit of Horticubes AeroMax is the reduction in algae growth on the substrate surface as the high drainage rate ensures that the top surface is dry.
According to Vijay, “these five key features weren’t present in our previous substrates. Overall, we achieved in making a substrate that will respond well to controlled growing environments, allowing the precision production of plants.”
The target market for Oasis Horticubes AeroMax
Horticubes AeroMax was primarily developed for leafy green production in vertical farms and was engineered to be future-proof, according to Vijay.
“This industry is progressing with LEDs, IoT, automation, etc. We developed Horticubes AeroMax with all of this in mind and believe it will be the most relevant substrate in the industry.”
OASIS Grower Solutions is currently developing Horticubes AeroMax applications for high-wire products and has another product coming to the floriculture industry.
For more information:
Vijay Rapaka, Global Research Manager
OASIS Grower Solutions
https://oasisgrowersolutions.com/aeromax
Publication date: Wed 16 Jun 2021
Author: Rebekka Boekhout
© HortiDaily.com
Pure Harvest Aims To Change The Face of Fresh Food
Having secured $60 million in funding, Pure Harvest Smart Farms is looking to expand its operations into Saudi Arabia and Kuwait, using advanced technology to bring food security to the arid Middle Eastern climate.
Having secured $60 million in funding, Pure Harvest Smart Farms is looking to expand its operations into Saudi Arabia and Kuwait, using advanced technology to bring food security to the arid Middle Eastern climate.
7 June 2021
Year-round Local Fresh Food
Pure Harvest is a farming startup using hi-tech, fully climate-controlled greenhouses and a coconut shaving hydroponic solution. Their aim is to provide year-round fresh food in a region where nearly 90% of food is imported. Having secured $60 million in funding, with a further $100 million earmarked by Kuwait’s International Investment Company (Wafra), Pure Harvest Smart Farms is looking to expand its operations into Saudi Arabia and Kuwait, using advanced technology to bring food security to the arid Middle Eastern climate. CEO and co-founder Sky Kurtz described their pilot project in Abu Dhabi as showing promising results with the “potential for year-round local production at very high quality and at a very good cost structure.”
Taming the Desert with High Tech Solutions
Farming consumes huge amounts of water, leading to water scarcity even in temperate regions such as Europe and America. In the arid, dry desert wasting even a drop of water is inconceivable, and Pure Harvest Smart Farms claims their self-contained greenhouses offer a level of efficiency 30 times greater than traditional field farms.
This model of controlled-environment agriculture (CEA) uses greenhouses that go far beyond glass walls to isolate plants. A climate chamber removes heat and humidity from the outside air; this humidity is condensed and fed to the plants inside. There is no soil as plants are grown inside a nutrient rich solution and monitored by sensors to keep the plants healthy. Triple-paned smart glass windows and over-pressurized airflow help manage temperatures to within a 1 degree Celsius margin and carbon dioxide is added to optimize plant growth.
Kurtz claims that Pure Harvest is expecting a yield of six to eight times more food per meter than other greenhouse farms, while using only one-seventh the amount of water. It will produce 17 to 23 times more food per meter than a traditional field farm.
A Large Market but Pure Harvest struggles to Gain Funding
Despite the success of the pilot, Pure Harvest has a long way to go. According to Kurtz, once they are producing at a scale of 30,000 square meters the produce should be 20-40% cheaper than imported fresh food giving them a very promising market.
But even with the investment of $60 million, and the $100 million soon to follow, Pure Harvest has struggled to secure the funding to expand. The industry is extremely capital intensive, and the Middle East venture capital market is less developed than in other countries. The company has managed to raise $50 million through bonds known as “Sukuk,” Shariah law compliant Islamic bonds, with a further $10 million investment from a January fundraising round led by Sancta Capital.
With the additional $100 million from Wafra, the total sum might appear to be significant, but compared to comparable ventures it is low. Recently a vertical farming firm in the U.S., Plenty, raised more than $500 million in funding.
A Promising Future for Local Food
With global supply chains heavily disrupted by the Covid-19 pandemic and further shaken by the blockage of the Suez Canal by the Ever Given in March 2021, the UAE region has become increasingly concerned about securing a food supply. If Pure Harvest can deliver on their promises, they stand to benefit handsomely. At the moment there is no reason to suspect otherwise as the company moves forward with expansion plans. Already the Pure Harvest has reached a $35 million agreement with The Sultan Centre in Kuwait to build a farm stretching across 80,000 square meters that can produce millions of kilograms of fresh fruit and vegetables, well past the size that Kurtz marks for profitability.
Photos: findwonder.abudhabi / agfstorage.blob.core.windows.net
USDA Funds Composition of New CEA Market Characterization Report
. “This is the first such supply chain assessment in CEA. We appreciate these leaders for stepping forward to support this important effort.”
Resource Innovation Institute (RII) has assembled a senior level of its Technical Advisory Council to support its USDA-funded project titled Data-driven Market Transformation for Efficient, Sustainable Controlled Environment Agriculture. The new Controlled Environment Agriculture (CEA) Leadership Committee, composed of a range of subject matter experts in CEA, will advise the development of a Market Characterization Report that will analyze the emerging “controlled environment” horticultural supply chain to determine opportunities to increase energy and water efficiency in cultivation.
“Market characterization is a critical first step in a coordinated effort to transform an economic sector toward efficient production,” said Derek Smith, Executive Director of Resource Innovation Institute. “This is the first such supply chain assessment in CEA. We appreciate these leaders for stepping forward to support this important effort.”
The Market Characterization Report represents the first publication that RII will deliver as part of its work on a three-year USDA Conservation Innovation Grant designed to advance resource efficiency in CEA, a diverse, expanding market that includes greenhouses and vertical farms growing a range of crops, from microgreens to tomatoes to berries. RII is partnering with the American Council for an Energy-Efficient Economy (ACEEE) to deploy the grant.
The CEA Leadership Committee is providing input on key market characterization issues such as supply chain: describing key market actors, barriers to energy efficiency and the best leverage points for market interventions; energy use: describing the energy used by producers (including on-site renewable energy, microgrids, and back-up generation); advantages of efficiency; describing the energy and non-energy benefits realized through implementation of efficiency projects; and baseline identification: describing key market baselines to be used in evaluating the impact of the market transformation initiative over time.
The organizations represented on RII’s CEA Leadership Committee include:
American Society of Agricultural and Biological Engineers
American Society of Heating, Refrigerating and Air-Conditioning Engineers
CEA Consultancy
Ceres Greenhouses
Energy Solutions
Fifth Season
Fluence by OSRAM
Grodan
Midwest Energy Efficiency Alliance
Oregon Association of Nurseries
Priva
Resource Innovations
Schneider Electric
Signify
UVM Extension Services
Zartarian Engineering
For a complete roster, see www.ResourceInnovation.org/TAC.
For more information:
Resource Innovation Center
www.resourceinnovation.org
7 June 2021
Controlled Environment Agriculture (CEA) 4.0 - Conference & Exhibition Day 2 - Friday 4th June - Attendee Tickets Still Available - 522 Attendees Registered
By purchasing a ticket for Conference Day 2 you will receive access and instructions on how you can view recording of the below presentations from Conference Day 1
Controlled Environment Agriculture (CEA) 4.0
Day 2 Conference & Exhibition (Virtual)
Friday 4th June 2021
CEA 4.0 Conference & Exhibition Day 2 is this Friday the 4th of June. With 522 industry attendees officially registered, we still have a small number of attendee tickets that have been made available for Conference Day 2 on Friday
Attendee tickets range from £14.99 - £19.99 per attendee.
Day 2 Conference Presenters
Advanced Plant Growth Centre (APGC) - Derek Stewart, Director
Algal Tech - Armando Leon, Founder & CEO
AmplifiedAg - Don Taylor, CEO & Founder
DAG Facilities - Mark Gemignani, CEO
FarmTech Society (FTS) - Nicole Thorpe, Vice-Chair
GlobalG.A.P. - Kristian Moeller, Managing Director
Greens for Good by Farm Urban - Jens Thomas, Technical Director
GroenLeven - Willem de Vries, Business Innovation Manager
Growfoam - Niels Steenvoorden, Chief Commercial Officer
Intelligent Growth Solutions - David Farquhar, CEO
Jungle - Nicolas Seguy, Managing Director
Mycelium - Eric Dargent, Managing Partner
Mycelium - Yishai Nissan, Managing Partner
Natural Resources Institute Finland - Titta Kotilainen, Senior Scientist
Planet Farms - Daniele Benatoff, Co-Founder & Co-CEO
Red Sea Farms - Ryan Lefers, CEO
SolarPower Europe - Miguel Herrero, Policy Advisor
UK Urban AgriTech (UKUAT) - Katia Zacharaki, Communications Director
Urban-Gro - Mark Doherty, Executive Vice President of Operations
Urban Crop Solutions - Tom Debusschere, CEO
Urban Harvest - Alexandre Van Deun, Co-Founder
Urban Harvest - Olivier Paulus, Engineering & Co-Founder
Valoya - Mika Linden, VP Sales
Valoya - Satu Karjalainen, Research Coordinator
Vertical Farm Institute - Daniel Podmirseg, Director
Vertical Future - Jen Bromley, Head of Plant Research & Development
Vertical Harvest - Nona Yehia, Co-Founder & CEO
Würth Elektronik eiSos - Johann Waldherr, Business Development Manager
Day 1 Conference Presenters
By purchasing a ticket for Conference Day 2 you will receive access and instructions on how you can view the recording of the below presentations from Conference Day 1.
AeroFarms - Roger Buelow, Chief Technology Officer
BrightFarms - Paul Lightfoot, President & Founder
CEA Food Safety Coalition - Marni Karlin, Executive Director
Certhon - Martin Veenstra, Consulting Engineer Indoor Farming Systems
Cultinova - Jim Thorpe, Chief Technology Officer (CTO)
Department for Environment, Food and Rural Affairs (Defra) - Caroline Povey, Team Leader – Agri-Innovation Policy
Finnish Glasshouse Growers' Association - Jyrki Jalkanen, CEO
GE Current - Dr. Hans Spalholz, Senior Plant Scientist
Graines Voltz - Solène Voltz, Vertical Farm Sales
Graines Voltz - Wolfgang Fishcer, International Product & Sales Specialist
Heliospectra - Fei Jia, Technical Solutions Manager
HerbanLeaf Farms - Myrianthi Oxtoby, Founder & CEO
Jones Food Company - James Lloyd-Jones, Founder & CEO
LEAF (Linking Environment & Farming) - Caroline Drummond, Chief Executive
Netled - Niko Kurumaa, COO
North Carolina State University - Dr. Ricardo Hernández, Professor
ONO Exponential Farming - Thomas Ambrosi, Director
Planet Farms - Daniele Benatoff, Co-Founder & Co-CEO
Real Leaf Farms - Karen Hennessy, CEO
Signify - Tom Könisser, Business Development Manager City Farming
Singapore Food Agency (SFA) - Poh Bee Ling, Director, Horticulture Technology Department Agri-Food
UK Research & Innovation – Innovate UK - Ian Cox, Innovation Lead
UK Research & Innovation – Innovate UK - Tom Jenkins, Deputy Challenge Director – Transforming Food Production
Urban Crop Solutions - Tom Debusschere, CEO
VEK Adviesgroep - Reinier Donkersloot, Director Business Consultancy
Vertical Future - Jen Bromley, Head of Plant Research & Development
Vitabeam - James Millichap-Merrick, CEO
Wageningen University & Research - Luuk Graamans, Scientist Vertical Farming
CLICK HERE TO BOOK YOUR ATTENDEE TICKET
Click Here To Meet The Current CEA 4.0 Sponsors,
Presenters, Exhibitors & Attendees
VIP Attendee Ticket Includes
Full event access provided to the conference, workshops, exhibition, etc
Personal event attendee profile
Company profile
Ability to arrange up to 36 one-to-one meetings with any attendee during the event
Ability to message and video chat with any attendee
Access to the presentation recordings from Conference Day 1
Company branding on the event website & at the event
CLICK HERE TO BOOK YOUR ATTENDEE TICKET NOW
BEFORE THEY ARE SOLD OUT
TECH 4.0 Ltd
info@tech40.net
https://www.tech40.net/
Polygreens Podcast Episode 28 Jake Emling
Beginning in July 2018 he joined CropKing, Inc. based out of Lodi, Ohio. His experience with hydroponics, aquaculture, and aquaponics was instrumental to his desire to start Root 42 Harvests with his wife Katie
Jake attended Michigan State University where he earned both undergraduate and graduate degrees in horticulture. He has nine years of experience across a variety of specialties including agriculture, agronomy, entomology, and viticulture.
During his early career in Michigan, he worked for Michigan State University, AgroLiquid, and the U.S. Department of Agriculture.
Beginning in July 2018 he joined CropKing, Inc. based out of Lodi, Ohio. His experience with hydroponics, aquaculture, and aquaponics was instrumental to his desire to start Root 42 Harvests with his wife Katie.
Latest Episode
Vertical Farming: Sustainable Food Never Tasted So Good
Vertical farming enables the ability to grow food closer to large population centers and also reduces the “food miles” associated with distribution thus reducing the carbon footprint
Richard Howells | Brand Contributor
May 5, 2021
There’s a lot of good press these days about the potential of vertical farming to help address climate change. The idea is to use hydroponics and other techniques to grow food “soil-lessly” (if that’s a word) in vertically stacked layers.
Vertical farming enables the ability to grow food closer to large population centers and also reduces the “food miles” associated with distribution thus reducing the carbon footprint.
But not so fast.
Mark Korzilius from &ever GmbH – a vertical farming startup with a farm in Kuwait and one coming in Singapore – disagrees with the food miles argument. Here’s why.
Quality first: Iceberg no more!
In a recent interview on the Climate21 podcast with Tom Raftery, Korzilius urges us to “forget about transportation in order to justify vertical farming.” Instead, the focus needs to be on bringing the best product to the consumer. Quality, in this case, means healthy, leafy greens.
“You want to have high nutrients, high in secondary metabolites, everything that is extremely valuable for your body,” said Korzilius.
To most of us, the antithesis of healthy leafy greens is iceberg lettuce. However, as Korzilius explained, it tends to be cut, bagged, and refrigerated for distribution.
“This is where a lot of the carbon footprint comes from,” said Korzilius. “And let’s be honest, iceberg in foul-smelling bags is less than appetizing.”
Instead, &ever follows a “harvest on demand” process. It distributes its leafy greens as potted plants – like you might see with basil or other herbs in your grocery store. Korzilius claims that the customer receives the best-tasting, locally grown leafy greens available, without plastic or refrigeration needed. The chef at the Four Seasons in Kuwait, reportedly, thinks the coriander is the best he’s ever tasted!
Greater control and higher yield, too
&ever’s operations are entirely indoors, where the climate is controlled. This is crucial for successful yields. Growing spinach, for example, is notoriously difficult with vertical farming. But by experimenting with the right seeds, lighting, and temperature, &ever has found the right recipe.
One key advantage is that &ever can grow without pesticides – which, in the end, is just another form of energy. It can also optimize light spectrums to achieve desired results. Many of its crops run on 18 hours of light and six hours of darkness.
The result is higher yields over the course of a year. &ever can grow 18 cycles a year, compared to maybe seven for a traditional greenhouse. And, says Korzilius, it can do it with 85% less water.
Complexity managed
Korzilius also makes the point that tracking all the variables – such as light, temperature, water, production cycles, energy costs, growing recipes, and more – makes for a lot of complexity. SAP is working with &ever to help manage it all. Vertical farming is a high-tech endeavor where control is the key to success. We’re proud to help be part of the solution. Hopefully, this approach to growing food will help minimize carbon output while also delivering delicious food – from (vertical) farm to table.
Listen to the podcast here and be sure to check out the latest research from Oxford Economics on how to “Build a Resilient and Sustainable Supply Chain.”
I've been working in the supply chain management and manufacturing space for over 25 years, and I'm responsible for driving the market direction and positioning of SAP’s Supply Chain Management and IOT solutions. Prior to joining SAP in 2004, I spent 15 years with Marcam Solutions where I was VP of Marketing for the companies Process ERP solutions. I have also implemented ERP and SCM systems at companies such as Nestle, Gillette, Colgate Palmolive, Rohm & Haas, Wyeth, Royal Worcester Spode and Dairy Crest. I hold a Bachelor of Science degree in Computer Science from the University of Mid Glamorgan in the UK. Follow me @howellsrichard
Lead photo: Vertical farm and its employees taking care of plant growth. Plant food production in vertically stacked layers. GETTY
Widespread Investment In CEA Is An Important Piece of The Food Security Puzzle
It has become increasingly clear that traditional agriculture is simply not meeting the food demands of the future
Sky Kurtz, CEO, and Co-Founder, Pure Harvest Smart Farms
There is a commonly quoted statistic estimating that by 2050, we will have nearly 10 billion people on the planet and, in turn, 10 billion hungry mouths to feed. Aside from population factors, the world’s climate is changing in ways human beings have never seen before. Across the globe, our water sources are being diminished and arable landmasses are shrinking. Food security and sustainability is becoming an ever-more pressing issue. There are a number of pioneering companies worldwide working hard to address these critical issues.
The Problem with Traditional Agriculture
It has become increasingly clear that traditional agriculture is simply not meeting the food demands of the future. Food production is heavily driven by significant freshwater consumption and can be both labour intensive and inefficient. Alongside this, changes in climate are negatively impacting yields. This is being witnessed across the board by the food production industry, investors, and governments alike.
The Power of the Consumer
Increased awareness of these issues has led to changes in consumer demands. Consumers have become more discerning about the quality of the products they buy, specifically when it comes to pesticide use, sustainability, freshness, food safety, variety, and brands. They are ever more interested in having knowledge of and creating a relationship with the foods they consume. This is evidenced by the huge organic growth rates of organics over the past 10 years. People care about quality and are voting strongly with their wallets.
Cultural and socio-economic demographics heavily influence what can and should be grown. Some crops such as premium quality leafy greens tend to target more affluent demographics and palates, whereas tomatoes, cucumbers, and a number of other greenhouse vegetables are staples of many diets and can be produced affordably in most places in the world.
The Promise of Controlled-Environment Agriculture
Controlled-Environment Agriculture (CEA) facilitates the growth of sustainable, high-quality produce but not at the expense of the consumer. CEA allows for consistent, high quality production by eliminating the environmental impacts on food production, allowing for more localized production, and reducing, or even eliminating, the use of pesticides.
Reducing Risk
Since early 2020, COVID-19 has woken the world to the risks and fragility of global fresh fruit and vegetable supply chains. Given perishability, the fruit & vegetable market is uniquely vulnerable vs. other crops e.g. the likes of corn, wheat, rice which can be stored & siloed. Controlled-environment agriculture is a solution that addresses these issues facilitating more localized production and supply, offering high output, resource-efficient production capabilities, while meeting the consumer’s changing demands.
In March, the world’s gaze turned to the Suez Canal where a container ship, the Ever Given, became lodged, blocking the canal. On a daily basis, the Suez Canal carries 12% of global trade, around one million barrels of oil and roughly 8% of liquefied natural gas. The cost of the blockage was reportedly $14m-$15m every day!
The Local Promise
The local unique selling point (USP) is now possible pretty much anywhere. Solutions like ours at Pure Harvest Smart Farms have made it possible to affordably produce year-round, even in the harshest climates in the world for example, the UAE, Kuwait, and Malaysia serving Singapore.
Large-scale solutions are necessary for the food to be economic, due to economies of scale in what is ultimately a manufacturing process. Large-scale greenhouses are particularly suitable for dense urban populations, as just 1 or 2 large production sites within 100 – 500 kilometers of the city or town can serve a large group of people affordably.
Unfortunately for more distributed, rural populations, this becomes more challenging. If you scale-down the solutions to hyper-localize, you often lose efficiency (in terms of both capital expenditure/ m2 and operational expenditure/ m2 for production. With more of the world’s population urbanizing, this is another trend that supports widespread investment in CEA as an important piece of the puzzle to serve future food demands.
The Future
The challenge of feeding nearly 10 billion people by 2050 MUST be solved on both the supply side and demand side. From the supply side, adopting technologies that augment output and resource-efficient growing methods. From the demand side, via changing what we consume, reducing waste, and environmental consciousness. Addressing these issues means we can produce more food with less and less resources.
High-tech agriculture presents a multi-decade investment opportunity to contribute to food security, water conservation, economic diversification, and a more sustainable future for all.
Join Sky at the virtual Indoor AgTech Innovation Summit on June 24 and tune into his live panel discussion on ‘Scaling at Speed: Delivering the Promises of a Mission-Led Industry’ at 16.50 EST.
For more information about Pure Harvest Smart Farms, follow them on Facebook, LinkedIn, Instagram and Twitter.
Recent Posts
Indoor AgTech Investment Landscape
Widespread Investment in CEA is an Important Piece of the Food Security Puzzle
Workshop: Food for the Next Frontier
Connecting Retailers, Buyers, and Growers Across Indoor Farming
IGS enters UAE market, signing deal with Madar Farms to enhance food security in the GCC region
Archive
Twitter: @IndoorAgTech
LinkedIn: Indoor AgTech
Hashtag: #IndoorAgTech
Can Vertical Farming Be A Viable Method Of Controlled Environment Production?
Fifth Season is using its fully integrated, automated operating system to crack the economics code for vertical farming with the potential to integrate with greenhouse operations.
Fifth Season is using its fully integrated, automated operating system to crack the economics code for vertical farming with the potential to integrate with greenhouse operations.
To say that controlled environment agriculture is drawing a lot of interest and dollars from the investment world would be an understatement. Austin Webb, co-founder, and CEO at Fifth Season, a vertical farm operation in Pittsburgh, Pa., estimates that over $3 billion has been invested in the CEA industry during the last four years alone, excluding debt and merger and accusations activities for greenhouse operations.
“For indoor ag overall, including both vertical farming and greenhouse, about half that equity investment has been for vertical farming,” Webb said. “There were a lot of dollars that came into this space early on. The unfortunate piece to that is there was a lot of overhype and false promises made in this space. A lot of those dollars came in too early for some of these companies and overall were wasted.
“There has been an industry-wide struggle to make the economics of vertical farming work. All of these companies talk about what they are going to do in the future, but the issue is they have negative unit economics. They lose money for every pound of produce they sell. In many cases, they will say that they will make the economics work in the future, but only after they build more production facilities.”
Webb said negative economics has had a major impact on the vertical farm industry.
“The false promises and the negative economics have held the industry back, overshadowed companies that are building substantial vertical farming solutions that work and pushed additional dollars to incremental greenhouse solutions,” he said. “Moving forward we will continue to see more dollars come into CEA and into vertical farming specifically. This will include public markets and SPAC (special purpose acquisition company) activity.
“Overall, there will be more money invested in CEA. This will include investments that are mediocre. The important element will be investments made into tech platforms designed for scalability and repeatability. This is the only way that volume requirements for wholesale buyers can be met to unlock indoor ag as a material participant in overall market share.”
Need for a mindset change
Even with additional investment dollars coming into the CEA industry, Webb doesn’t expect it to be enough to make traditional vertical farming companies a success.
“Unfortunately, even though significant dollars have been invested in vertical farming, much of it has been wasted,” he said. “The incremental mindset a lot of people in this industry have had is to simply convert farming from outdoors to indoors. In doing so, all they inevitably did was bring people from outdoors and put them indoors. The mindset was to create a growing platform to produce leafy greens and then sprinkle on some technology. The technology was sort of an afterthought.
“There were a lot of companies throwing out buzz words without having actual practicality in regards to robotics, artificial intelligence, and automation. All the money that has been invested has been going toward continued R&D, but at a level which has companies creating technical debt.”
The thing that has helped Fifth Season avoid the technology issues other vertical farms have encountered is the way the company developed and designed its operating system.
Fifth Season has created a manufacturing platform that is fully automated from end-to-end including growing, processing, and packaging.
“We had a completely different mindset,” Webb said. “We took a blank slate to really design this holistically from beginning to end. We think of this as manufacturing a living organism. As a result, we’ve created an IoT–connected smart manufacturing platform that is an industry-first, industry-only, fully end-to-end automated platform—not just growing, but also processing and packaging. There are other operations that have automation here or there, but nothing else truly automated from beginning to end.
“More importantly, we have integrated the system so it is completely run by our proprietary software platform. We don’t have a bunch of automated equipment that runs on its own controls. Instead, we have a combination of our own proprietary tech and some off-the-shelf equipment such as conveyors. All of the electromechanical systems sit within our software skin and are run by our in-house built firmware and software brain. We have a pathfinding algorithm where when we receive an order from a customer, our system is sequencing out the schedule completely on a daily, weekly and monthly basis.”
Fifth Season worked with Hort Americas and GE Current, a Daintree company, to develop its automated grow room.
“Partnering together on our solution helped us validate that there was a path for our vertical farm to have favorable economics,” Webb said. “Being able to bounce ideas and technologies off of the Hort Americas team allowed us to push the boundaries of innovative thinking in terms of our approach and how we wanted to use technology to solve the complex issues that are limiting vertical farming. We were able to think differently, knowing we had the Hort Americas team as both a check and enabler, which ultimately created a successful collaboration.”
Partnering with Hort Americas also gave Fifth Season the opportunity to incorporate Current’s LED technology into its unique growing platform.
“We did a lot of things differently with our proprietary design and in so doing there were certain things that we couldn’t necessarily handle ourselves,” Webb said. “Working with Hort Americas and Current enabled us to move very quickly while making smart, capital-efficient decisions, as opposed to designing the LEDs ourselves or over-paying for unnecessary functionality.
“We worked with Current in key areas that made big differences related to the integration of our design. We leveraged Current’s significant expertise in regards to light spectrum strategy and the corresponding impact on plant science and quality.”
Creating an economic advantage
Webb said Fifth Season’s unique platform has allowed the company to unlock positive unit economics where it can offer a market price that works for wholesalers and consumers.
“We have been able to make money per pound and make vertical farming economically sustainable,” he said. “Our platform has enabled us to make a stepwise function change in labor costs and efficiency and in energy costs. For labor, we have 2x+ less labor costs than other companies in this space. We also measure and track energy down to every individual bot. We have over 60 bots that are all integrated into one robotics system. We measure and track how to optimize energy utilization to all of those bots.
Fifth Season’s unique operating platform has allowed the company to unlock positive unit economics enabling it to offer a market price that works for wholesalers and consumers.
“Finally we have made a stepwise function change in pounds to fixed costs ratio. That’s because we have been able to remove large aisle ways and manual inefficient storage and retrieval. We have created a patent-pending solution around our automated storage retrieval, which ties to the rest of our system. In the end, we are able to remove all human involvement from the grow room and are able to achieve 2x+ the growing capacity.”
Another advantage of the platform Fifth Season has created is the need for raising additional capital compared to some other vertical farms.
“We have raised just over $40 million to date,” Webb said. “There are multiple vertical farm companies that have raised $200 to $400 million+. The reason we haven’t had to raise that much capital is because of our mindset about engineering, grow science, and operations in the same R&D pipeline. It has allowed us to catch up and to surpass the rest of the industry in a fraction of the time with a fraction of the capital.
“As we move forward and look at raising additional capital, what’s different is we don’t have to use our equity capital to build more farms for all the hard costs associated with real estate, equipment and building facilities. We can if we want to and if it makes sense for our equity partners, but it is not required. We have been able to unlock positive unit economics which means we have been able to unlock non-dilutive capital to build additional facilities more capital efficiently. Overall, we have built a scalable, repeatable platform, which is what investors need to see.”
What’s ahead for vertical farming?
Webb said there will be a few select companies that have approached indoor ag and vertical farming with a solution that works and will thrive. There will also be a number of companies that are large and excessive that will eventually disappear.
“There will be some consolidation in this industry,” he said. “Some companies won’t be consolidated because they don’t have a tech platform that is investable in terms of the synergies of wanting to acquire that footprint. Consolidation will be selective in some cases.
“There is a lot of production regardless of footprint and money going into leafy greens. There are companies in this space that have no intention of doing anything different than that. I think that focus will run them into a leafy greens race to the bottom. It all comes down to no sustainable competitive advantage.”
Webb also sees the potential for synergy between vertical farms and greenhouses.
“We have built a scalable system that allows us to do a number of crops and then do asset management across different applications,” he said. “We also have the technology that is applicable from an asset management production operations standpoint that works for greenhouses as well.
“We will be able to unlock with this technology what many others won’t necessarily be able to do. Fifth Season will not only be a company that has vertical farm and greenhouse footprints but also is one that uses those footprints in a collaborative way for specific crops. For example, a crop could be in a vertical farm environment for part of its life and in a greenhouse for another part of its life. This will create cross-category and cross footprint combinations.”
For more: Fifth Season, (412) 899-2268; hello@fifthseasonfresh.com; https://www.fifthseasonfresh.com/
Lead photo: Austin Webb, co-founder, and CEO at Fifth Season, said even though significant dollars have been invested in vertical farming, much of it has been wasted. Photos courtesy of Fifth Season
This article is property of Urban Ag News and was written by David Kuack, a freelance technical writer in Fort Worth, Texas.
Vertical Farming Startup Oishii Raises $50m In Series A Funding
“We aim to be the largest strawberry producer in the world, and this capital allows us to bring the best-tasting, healthiest berry to everyone.”
By Sian Yates
03/11/2021
Oishii, a vertical farming startup based in New Jersey, has raised $50 million during a Series A funding round led by Sparx Group’s Mirai Creation Fund II.
The funds will enable Oishii to open vertical strawberry farms in new markets, expand its flagship farm outside of Manhattan, and accelerate its investment in R&D.
“Our mission is to change the way we grow food. We set out to deliver exceptionally delicious and sustainable produce,” said Oishii CEO Hiroki Koga. “We started with the strawberry – a fruit that routinely tops the dirty dozen of most pesticide-riddled crops – as it has long been considered the ‘holy grail’ of vertical farming.”
“We aim to be the largest strawberry producer in the world, and this capital allows us to bring the best-tasting, healthiest berry to everyone. From there, we’ll quickly expand into new fruits and produce,” he added.
Oishii is already known for its innovative farming techniques that have enabled the company to “perfect the strawberry,” while its proprietary and first-of-its-kind pollination method is conducted naturally with bees.
The company’s vertical farms feature zero pesticides and produce ripe fruit all year round, using less water and land than traditional agricultural methods.
“Oishii is the farm of the future,” said Sparx Group president and Group CEO Shuhei Abe. “The cultivation and pollination techniques the company has developed set them well apart from the industry, positioning Oishii to quickly revolutionise agriculture as we know it.”
The company has raised a total of $55 million since its founding in 2016.
Indoor Agtech: An Evolving Landscape of 1,300+ Startups
Our Indoor AgTech Landscape 2021 provides a snapshot of the technology and innovation ecosystem of the indoor food production value chain
March 17, 2021
Editor’s note: Chris Taylor is a senior consultant on The Mixing Bowl team and has spent more than 20 years on global IT strategy and development innovation in manufacturing, design, and healthcare, focussing most recently on indoor agtech.
Michael Rose is a partner at The Mixing Bowl and Better Food Ventures where he brings more than 25 years immersed in new venture creation and innovation as an operating executive and investor across the internet, mobile, restaurant, food tech and agtech sectors.
The Mixing Bowl released its first Indoor AgTech Landscape in September 2019. This is their first update, which you can download here, and their accompanying commentary.
Since the initial release of our Indoor AgTech Landscape in 2019, the compelling benefits of growing food in a controlled indoor environment have continued to garner tremendous attention and investment.
One of the intriguing aspects of indoor agriculture is that it is a microcosm of our food system. Whether within a greenhouse or a sunless (vertical farm) environment, this method of farming spans production to consumption, with many indoor operators marketing their produce to consumers as branded products. As we explore below, the indoor ag value chain reflects a number of the challenges and opportunities confronting our entire food system today: supply chain, safety, sustainability, and labor. Of course, the Covid-19 pandemic rippled through and impacted each aspect of that system, at times magnifying the challenges, and at others, accelerating change and growth.
Invest with Impact. Click here.
Our Indoor AgTech Landscape 2021 provides a snapshot of the technology and innovation ecosystem of the indoor food production value chain. The landscape spans component technology companies and providers of complete growing systems to actual tech-forward indoor farm operators. As before, the landscape is not meant to be exhaustive. While we track more than 1,300 companies in the sector, this landscape represents a subset and serves to highlight innovative players utilizing digital and information technology to enhance and optimize indoor food production at scale.
Supply chain & safety: Where does my food come from?
The pandemic highlighted the shortcomings of the existing supply chain and heightened consumer desires to know where their food comes from, how safely it was processed and packaged, and how far it has travelled to reach them. A key aspect of indoor farming is its built-in potential to respond to these and other challenges of the current food system.
Indoor farmers can locate their operations near distribution centers and consumers, reduce food miles and touch points, potentially deliver consistently fresher produce and reduce food waste, and claim the coveted “local” distinction. The decentralized system can also add resiliency to supply chains overly dependent on exclusive sources and imports.
Growing local has many forms. Greenhouse growers tend to locate their farms outside the metropolitan area while sunless growers may operate in urban centers, such as Sustenir Agriculture in Singapore and Growing Underground in London. Growers like Square Roots co-locate their indoor farms with their partner’s regional distribution centers, and Babylon deploys its micro-farms solution on site at healthcare and senior living facilities and universities. Recently, Infarm announced it was expanding beyond its growing-in-a-grocery store model, to include decentralized deployments of high-capacity “Growing Centers” across a number of cities. Additionally, the value of “growing local” might take on a much larger meaning if your country imports most of its produce from other countries; a number of the Gulf region countries have announced major indoor growing initiatives and projects with AeroFarms, Pure Harvest, and &ever to address the region’s food dependence on other countries.
Organic produce sales jumped to double digit growth in 2020 as consumers are increasingly mindful of the healthiness of their food. The additional safety concerns due to the pandemic only accelerated this trend. While not typically organic, crops produced in the protection of indoor farms are isolated from external sources of contamination and are often grown with few or no pesticides. Human touch points are reduced as supply chains shorten and production facilities become highly automated. Through the CEA Food Safety Coalition, the industry has recently taken steps to establish production standards with a goal to keep consumers safe from foodborne illness.
Indoor farmers market their products as local, fresh, consistent and clean. This story is resonating with consumers as the growers seem to be selling everything they can produce, with many reporting significant sales growth in 2020. The direct connection to consumer concerns is also a key part of their ability to sell their branded products at a premium, which has been critical to financial viability for some growers. This connection can also enable them to collapse the supply chain further, at least at smaller scales, through direct sales and creative business models, e.g., sunless grower Willo allows subscribers to have their own “personal vertical farm plot” and watch their plants grow online.
Sustainability: Is my food part of the problem or part of the solution?
Farming, as with most industries, has been under increasing pressure to operate more sustainably, and indoor growers, with their efficient use of resources, have rightfully incorporated sustainability prominently into their narratives.
We are well aware of the impacts of climate change, including greater variability in weather patterns and growing seasons. The UN’s Food and Agriculture Organization projects that over the coming decades climate change will cause a decrease in global crop production through traditional farming practices, causing greater food insecurity. Indoor growing, which provides protection from the elements, consistent high yields per land area, and the ability to produce food year-round in diverse locations, including those unsuitable for traditional agriculture, can help mitigate this trend.
Water scarcity is projected to increase globally, presenting a national security issue and serious quality of life concerns. According to the World Bank, 70% of the global freshwater is used for agriculture. Indoor agriculture’s efficient use of water decreases use by more than 90% for the current crops under production. It is also common practice for greenhouses to capture rainwater and reuse drainage as does Agro Care, the Netherlands’ largest greenhouse tomato grower.
On the flip side, energy use, particularly in sunless facilities, is indoor growing’s sustainability challenge. Efficiency will continue to improve, but as recent analysis on indoor soilless farming from The Markets Institute at WWF indicated, there is an industry-wide opportunity to integrate alternative energy sources. Growers recognize this opportunity to decrease impact and improve bottom-line and are already utilizing alternative approaches such as cogeneration, geothermal sources, and waste heat networks. H2Orto tomatoes are grown in greenhouses heated with biogas generated hot water. Gotham Greens’ produce is grown in 100% renewable electricity-powered greenhouses, and Denmark’s Nordic Harvest will be running Europe’s largest indoor farm solely on wind power.
Labor: We’re still hiring!
There are labor challenges and opportunities throughout the food system value chain, and this couldn’t be more acute than on the farm. Farm operators—both in-field and indoor—find it difficult to attract labor for the physically demanding work. Even before the pandemic, the hardening of borders in Europe and the US created a shortage of farmworkers for both field and greenhouse production. In addition, grower and farm manager-level expertise is in short supply, exacerbated by an aging workforce and the rapid addition of new indoor facilities. While operators would like to see more trained candidates coming from university programs, they are also looking to technology and automation to relieve their labor challenges.
Automation of seedling production and post-harvest activities is already well established for most crops in indoor farming. In addition, the short growth cycle and contained habit of leafy greens lends them to mechanization. For example, the fully automated seed-through-harvest leafy green systems from Green Automation and Viscon have been deployed in major greenhouse operations like Pure Green Farms and Mucci. On the sunless side, Urban Crop Solutions has uniquely implemented automation in shipping containers, and Finland’s NetLed has developed a fully automated complete growing system. Note that many of the larger-scale sunless growers have developed their own technology stacks and have designed labor-saving automation into their systems. For example, Fifth Season has robotics deployed throughout the entire production process.
Despite numerous initiatives, the challenging daily crop care tasks and harvesting for certain crops (tomatoes, peppers, cucumbers, and berries) have not yet been automated at scale. However, planned, near-term commercial deployments of de-leafing and harvesting robots offer the promise of significantly altering labor challenges. Software technologies, like those from Nitea and Hortikey address labor management, crop registration, yield prediction, and workflow/process management for the indoor sector and strive to improve operational efficiencies for a smaller workforce.
Technologies that provide, monitor, and control climate, light, water, and nutrients are already deployed in today’s sophisticated indoor growing facilities and are fundamental to maintaining optimal conditions in these complex environments. They also form the base for the next innovation layer, i.e., crop optimization and even autonomous control of the growing environment based on imaging and sensor platforms (like from Ecoation, iUNU, and 30MHz), data analysis, machine learning, digital twins and artificial intelligence. Recent events like the Autonomous Greenhouse Challenge have successfully explored the potential of AI to “drive horticultural productivity while reducing resource use and management complexity”. Emerging commercialized autonomous growing innovations, such as the Blue Radix Crop Controller and Priva’s Plantonomy, promise to extend and enhance the reach of available grower expertise, particularly in large and multi-site operations.
Where do we go from here?
Since we created our initial Indoor AgTech Landscape, there has been positive change and reason to be optimistic about the future. But, as with any evolving market and sector of innovation, it can be a bumpy ride. Some believe CEA is not the answer to our food problems because not everything can be economically grown indoors today. We see indoor ag as just one of the approaches that can help fix our food system and it should be applied when it makes sense. For example, tomatoes sold through retail are already more than likely grown in a greenhouse. Expect more crops to be grown indoors more economically with further advancements.
One aspect of our previous landscape was to increase awareness that, despite the fervor surrounding novel sunless farming, greenhouse growing was already well-established. Dutch greenhouse growers have demonstrated the viability of indoor growing with 50-plus years of experience and more acres “under glass than the size of Manhattan.” The recent public offering and $3 billion market cap of Kentucky-based greenhouse grower AppHarvest also clearly raised awareness! Other high-profile and expanding greenhouse growers, including BrightFarms and Gotham Greens, have also attracted large investments.
The question is often asked, “which is the better growing approach, sunless or greenhouse?”. There is no proverbial “silver bullet” for indoor farming. The answer is dictated by location and the problem you are trying to solve. A solution for the urban centers of Singapore, Hong Kong and Mumbai might not be the same as one deployed on the outskirts of Chicago.
Regardless of approach, starting any type of sizable tech-enabled indoor farm is capital intensive. A recent analysis from Agritecture indicates that it can range from $5 to $11 million dollars to build out a three-acre automated farm. Some of the huge, advanced greenhouse projects being built today can exceed $100 million. Given the capital requirements for these indoor farms, some question the opportunity for venture-level returns in the sector and suggest that it is better suited to investors in real assets. Still, more than $600 million was raised by the top 10 financings in 2020 as existing players vie for leadership and expand to underserved locales while a seemingly endless stream of new companies continue to enter the market.
Looking forward, indoor farming needs to address its energy and labor challenges. In particular, the sunless approach has work to do to bring its operating costs in line and achieve widespread profitability. Additionally, to further accelerate growth and the adoption of new technologies in both greenhouse and sunless environments, the sector needs to implement the sharing of data between systems. Waybeyond is one of the companies promoting open systems and APIs to achieve this goal.
As we stated in the beginning of this piece, the indoor ag value chain reflects some of the challenges and opportunities confronting our entire food system today: supply chain, safety, sustainability, and labor. Indoor agriculture has tremendous opportunity. While it is still early for this market sector overall, it can bring more precision and agility to where and how food is grown and distributed.
US: NORTH CAROLINA: CraftGrown Farms Offers Fresh Microgreens, Lettuce And Herbs
All of the growing is done inside, allowing CraftGrown Farms to produce year-round and the ability to expand its growing capacity
BY JESSICA MAURER
March 10, 2021
CraftGrown Farms involves a hydroponic farm on Castle Street. (Photo courtesy of CraftGrown Farms)
Randall Rhyne’s career has included teaching high school biology and earth science as well as serving in the Army Reserve, with deployments to Iraq and Syria.
After visiting Wilmington last year, he fell in love with the city and decided to relocate from Virginia.
While serving overseas, Rhyne and his unit often had little to no access to fresh food, relying on MREs or snacks like Pop-Tarts. He often longed for fresh produce.
One spring when he was in the Syrian desert, he saw trucks hauling locally grown produce and found himself thinking that if the locals were able to grow their own food in the middle of a civil war, in a desert, there was no reason why he couldn’t do this at home. As soon as he returned to Virginia, Rhyne got to work.
Now, having secured a Castle Street storefront and growing space across from Luna Café on Castle Street last fall, Rhyne has created CraftGrown Farms, an indoor, hydroponic farm selling nutrient-dense microgreens, hydroponic lettuce, and herbs to local restaurants and the public.
All of the growing is done inside, allowing CraftGrown Farms to produce year-round and the ability to expand its growing capacity.
Rhyne said the response so far has been remarkable; in fact, he’s already outgrown his initial vertical grow system.
“It’s a great problem to have,” Rhyne said.
He said new customers are usually so excited about what they’ve tried that they want to take home more than they need.
“I’m an old school believer in the quality of the sale and even though these items have a good shelf life, I try to discourage people from buying too much at once,” Rhyne said.
CraftGrown Farms only harvests what it sells, so the produce is picked right in front of the customer, providing maximum flavor and freshness.
There are currently about a dozen microgreen blends available, as well as leafy greens such as kale, arugula, and tatsoi. The microgreens will keep in a vegetable crisper for two weeks, and all of the lettuce is sold with the root ball intact to preserve flavor and freshness.
“These are not your everyday lettuces,” Rhyne said.
CraftGrown Farms is located at 603 Castle St. and is open from noon to 6 p.m. Monday through Friday and 10 a.m. to 4 p.m. on Saturday.
Have a tip for Restaurant Roundup? Email us at: restaurant@wilmingtonbiz.com.
How Vertical Farms Are Revolutionizing Agribusiness
What is vertical farming and why does it matter?
William Ramstein ・ 1 March 2021 ・ Vertical Farming
Urban planners are tasked with answering some pressing inquiries: how can farming be brought closer to consumers; is digital agriculture an essential ingredient for making cities smarter; and can vertical farming improve socio-economic disparities?
Key Takeaways:
Vertical farming uses LED, Robotics and AI to bring vegetables closer to city dwellers.
The total addressable market for vertical farming is estimated at around $700 billion.
Spread, a Japanese vertical farm is profitable but most firms fail.
Vertical farming is a great way to produce controlled supplies of a customized plant.
Vertical farming struggles with electricity costs despite reducing carbon emissions.
What is vertical farming and why does it matter?
The bedrock characteristic of cryptocurrency technology is called decentralization, a sovereign and flexible organizational system led by a commune, and today other industries like farming are catching the bug. Farming needs to change its practices in order to meet ecological objectives set up by governments and decentralization could open the door to increasing food access and reducing carbon emissions from food transportation. Smart decentralized vertical farming implies using technology like digital platforms, robotics and artificial intelligence to bring food closer to the growing demand seen in cities.
Despite the difficulty of competing against the cost structure of traditional farming, vertical farming offers numerous advantages. It grants more yield per square meter and reduces waste in both carbon and water usage. The production of vegetables is made in large and often times un-used warehouses close to city centers thus cutting transportation costs and middlemen expenses. The supply is more easily controlled, protected, and priced regardless of global weather and plants are customized to local consumer preferences. Consumers are already paying a premium on farmer’s market products, so why not vertical farm products too?
Cases of vertical farming: Nigeria is one of the most promising African nations because of its age pyramid. But with a large young population comes questions around food and water access and today, more than 170 million Nigerians need prolonged and sustainable access to these resources. Nigeria currently imports $3.5 billion worth of food products while exporting only 1/7 of that figure. Fresh Direct is Nigeria’s first Hydroponics Company (growing crops without standard soil) that combines vertical farming to its business model to reduce the distance between cities and rural farming regions.
The firm is able to produce seven to 10 times the yields because of its stackable shipping containers, which use technologies such as drip irrigation, and cold storage. Direct Farming operates with a community mindset, with the goal to inspire more young farmers to set up shop in urban centers and become urban farmers. The company also trains and finances low-skilled workers into urban farmers and increases economic productivity in unemployed youth groups.
In Japan, a company called Spread is one of the world’s most sophisticated examples of vertical farming. Their factory mainly produces lettuce. Large robotic arms transplant lettuce seedlings into pots where they are left to grow under LED lights. Believe it or not, but the factory can produce 30,000 lettuce heads a day. CEO Shinji Inada boasts of being the only large-scale vertical farm that is profitable and hopes that more widespread adoption continues growing.
However, companies like Spread and A-Plus (another similar farm in Fukushima) struggle to lower unit economics because of their low-scale operations, and they find it hard to penetrate the traditional downstream sellers. When producing high-priced lettuce by the tonne, trucking goods to the local wholesaler does not work partly because vertical farming offers customized products for specific local needs, not necessarily for broad demand. These players have thus geared their focus towards international buyers like UAE to export their goods.
Is vertical farming there yet?
Most vertical farms have failed because of the high initial costs and high operational expenses of running robotic equipment. While sunlight is free, the energy cost of running LEDs is not. The solution could be to install renewable energies like solar panels and wind turbines. However, the fixed cost of that installation would inevitably factor into the end-product, or at least on the balance sheet as a liability assuming they keep prices reasonable for consumers.
While Mr. Inada can rightly boast of turning profits, most firms toss lettuce at a loss. The industry should see more growth ahead, however, with research group IDTechEx forecasting that annual sales of $700 million could more than double to $1.5 billion in 2030. There remain technological challenges though. While many competitors boast of successfully leveraging AI and robotics and filtration, new entrants have seen problems with watering automation systems, mold, and infestations (most players do not use pesticides).
Some analysts suggest that while the excitement around vertical farms makes sense, the farming style might just end up becoming just another way of farming amongst greenhouse and open sky farms. More specifically, vertical farming will focus on high-margin crops rather than commodities like bulk grains.
While the challenges of vertical farming are clear, every country has different needs and constraints. There is a large interest from smaller island countries like Singapore or Iceland, rich economies, and countries that have a higher propensity to import due to less arable lands. Britain is a good example of a country that meets the criteria and in the context of Brexit, it makes all the more sense because of import costs and independence constraints. A potential labor crisis could soon loom too assuming seasonal workers are denied entry into the country. Vertical farms only require one-third of the manpower to run and could therefore alleviate the industry.
The market opportunity…According to research by Barclays Investment Bank, the market opportunity for vertical farms is large. Analysts estimate the size of the global fruit and vegetable market to be $1.2 trillion and the total addressable market for vertical farms to be $700 billion. The purchased energy use to produce 1kg of lettuce is 247-kilowatt hours far exceeding Netherland greenhouses’ 70-kilowatt hours consumption. With retailers being asked to meet more carbon-neutral objectives, some vertical farms believe they will be able to overcome their expense through increased demand and scale.
The pandemic has imposed many supply chains disruptions and labor shortages threatening food security in regions around the world relying heavily on imports. Vertical farming is recognized lately and since 2014, has seen a flow of funds equal to $1.8 billion according to data group Dealroom. SoftBank fundraised $140 million into Plenty, a start-up, and countries like Abu Dhabi want to build farms in deserts.
Some of the top players in the global farming market include Vertical Farm Systems (Australia), American Hydroponics (US), Agrilution (Germany), Green Sense Farms (US), Everlight Electronics (Taiwan), Koninklijke Philips (Netherlands), Sky Greens (Singapore), Illumitex (US), Urban Crop (Belgium), Aerofarms (US) and InFarm (Germany).
New York’s Gotham Greens Plans Solano County Indoor Produce Farm
It will be located on 33.6 acres of agricultural land purchased from the university adjacent to Interstate 80.
GARY QUACKENBUSH
FOR THE NORTH BAY BUSINESS JOURNAL
Example of the greenhouse operated by Gotham Greens which announced plans to open in Solano County (Photo courtesy of Gotham Greens)
Gotham Greens Holdings LLC, a firm with indoor agriculture operations across the U.S., Tuesday, announced plans to build a facility next to the University of California, Davis.
The first phase of this 10-acre Solano County facility is expected to open later this year. It will be located on 33.6 acres of agricultural land purchased from the university adjacent to Interstate 80.
The company stated its plans will provide it with the ability to deliver fresh leafy greens, herbs, plant-based dressings, dips and cooking sauces to more retailers, foodservice operators and consumers on the West Coast.
“… We are partnering with one of the highest-ranked agricultural research centers in the world to advance the entire agriculture system,” said Viraj Puri, co-founder and CEO of Gotham Greens. “California is responsible for growing one-third of the country’s vegetables and two-thirds of the nation’s fruit, yet in recent years, issues surrounding drought, food safety and worker welfare have demonstrated the need for continued innovation.”
The greenhouse will generate 60 full-time jobs and provide UC students with the opportunity to learn first-hand how to sustainably grow produce year-round in a safe, clean, climate-controlled environment. The company stated its facilities use 95% less water and 97% less land than conventional farming. Nationwide, Gotham Greens has 500,000 square feet of greenhouse space at five locations staffed by 400 employees.
The UC Division of Agriculture and National Resources and the UC Davis College of Agriculture and Environmental Sciences has entered into a partnership with Gotham Greens to advance research and innovation in the areas of indoor agriculture, greenhouse technology, and urban agriculture to help advance the science, workforce technology, and profitability of indoor agriculture globally.
“We are building a Controlled Environment Agriculture Consortium to support and advance the indoor farming industry, grow more fresh produce on less land and create new jobs for Californians,” said Gabriel Youtsey, the division’s chief innovation officer. “Gotham Greens is an anchoring partner of this research and industry collaboration that we hope will spur innovation, create a new indoor farming workforce and support industry growth.”
Helene Dillard, dean of the college, said, “This partnership will offer our students the chance to learn best practices from leading experts in indoor farming.”
Gotham Greens recently raised $87 million in new equity and debt capital bringing the company’s total financing to $130 million to fuel the next phase of growth.
Founded in 2009 in Brooklyn, New York, Gotham Greens (gothamgreens.com) owns and operates greenhouses in New York, Illinois, Rhode Island, Maryland and Colorado. Its produce is available in more than 40 states and 2,000 retail stores, including Albertsons Companies (Safeway, Jewel-Osco, and Shaw’s), Whole Foods Market, Target, King Soopers, Harris Teeter, and Sprouts.
The company’s products can also be purchased through e-commerce sites including AmazonFresh, FreshDirect and Peapod.
Lead Photo: Gotham Greens
Introducing Vertical Farming To Mexico And Beyond
Above all else, Karma Verde Fresh is a social enterprise whose purpose, according to Tagino, “is to transform the lives of individuals and communities through the creation of accessible food options, that have positive economic and sustainable impacts on the environment.”
Karma Verde Fresh (KVF) is a vertical farm based in Monterrey, Nuevo León (northeastern Mexico), producing a variety of seedlings, leafy greens, strawberries, and beans, and manufacturing its own cultivation systems which can be installed in any urban environment to promote local agriculture.
First established in 2016 by Leo Lobato and Rafael Cuellar, Karma Verde Fresh sought to master vertical agriculture before developing its own system and initially purchased four vertical racks systems from a Dutch company. The company quickly realized that for vertical farming to be successful in Mexico and other developing countries, the technology needs to be both efficient and financially accessible so that any sized growers can participate in the development of their own urban, peri-urban or rural farms.
(F.l.t.r.) Leo Lobato and Rafael Cuellar, co-founders of KVF
According to Tagino, the company’s communications and social media manager, high capital and operating costs are the main barriers to vertical farming.
Technique available to anyone
This has led the company to develop its own technology within Mexico and make it as accessible as possible, all with the goal of providing as many communities with nutritious produce. Today, KVF has increased its cultivation grow racks by more than 89% in the same footprint and their solar LED lights use 21% less energy.
“We know that there are super sophisticated farms across the world, with high automation. That is one way, but in order to impact communities that are left behind, are looking for job opportunities, vertical farming needs to be affordable,” says Tagino.
Once Karma Verde Fresh successfully developed its own cultivation system, the company developed a digital strategy to reach its potential and future customers through various social media platforms which include Facebook, Instagram, and Twitter.
Pushing R&D
Aside from its strong social media presence to attract young customers and entrepreneurs, Karma Verde Fresh also strongly emphasizes the importance for scientific research in the vertical farming industry, publishing their first scientific research report in Cyprus at an international sustainable agriculture conference in March in conjunction with Dr. Gilda Carrasco of the University of Talca.
KVF's salad mix
“Back in 2018, we learned that vertical agriculture really needs the scientific research community to be on board because they can give us the best science for improving growing conditions. In 2019, we started our first laboratories at two UANL campuses (Universidad Autónoma de Nuevo León) and the UAAAN in Coahuila, and in 2021-2023, we’ll be installing cultivation systems at different universities across Mexico, Central America, and as far away as Chile,” says Leo.
By installing cultivation systems at numerous universities, Karma Verde Fresh hopes to attract youth to vertical farming and to develop businesses in the regions where the systems are being established. The company is also immersing itself in the academic world by collaborating on research projects and participating with NCERA-101, a research committee focused on exchanging information about technologies in controlled environment agriculture (CEA).
Expansion plans
Through these research collaborations, the company is creating models that it can replicate across Mexico. Thanks to the American Chamber Mexico, the company met Ken Moskal, now an angel investor and a new corporate structure will allow Karma Verde Fresh to transition out of its start-up phase. While the company hopes to attract investment fund managers, Leo also explained that Karma Verde Fresh is taking its time to grow organically, invest its own money and only bring in outside investments if needed.
Karma Verde Fresh plans to fund its growth mostly through sales of seedlings, produce to restaurants and selling the KVF systems through the national distribution network developed through Mexico’s Industrial Chamber CANACINTRA’s Ag Sector.
Above all else, Karma Verde Fresh is a social enterprise whose purpose, according to Tagino, “is to transform the lives of individuals and communities through the creation of accessible food options, that have positive economic and sustainable impacts on the environment.”
Their purpose garnered the attention of the Inter-American Institute for Cooperation in Agriculture (IICA). The organization asked Karma Verde Fresh to join an alliance, which was signed in 2020 and will work to build cultivation systems in food banks in the country’s most food-insecure regions, as well as the first Vertical Agriculture Tech and Trainer Certification Program in Mexico City.
Sustainable systems
Another interesting initiative of Karma Verde Fresh is its solution called the Rolling Thunder Service. By developing 40-day forecasts over Mexico, the company will be able to better forecast severe meteorological events and begin producing seedlings in its racking systems ahead of such events. When severe storms damage agricultural crops, the company will be able to provide to healthy seedlings to help farmers recover quickly.
The company is guided by three core values: consciousness, innovation and collaboration. With respect to innovation, Tagino explained that it isn’t simply about buying innovation but about actually innovating in the countries seeking to build sustainable agricultural systems. That is ultimately why the company decided to develop its own vertical racks and LEDs. The company’s commitment to collaboration is evidenced by its numerous university partners and research projects.
“Not only are our processes enriched by the different perspectives and knowledge, but it generates a bigger impact among the communities and ecosystems where the collaborations occur,” says Tagino.
For more information:
Karma Verde Fresh
Blvd. Díaz Ordaz #130,
Col. Santa María, Piso 10, Torre 3,
64650, Monterrey, Nuevo León, México
+52 (81) 8851-8261
Leo Lobato, Co-Founder
leo@karmaverdefresh.com
Tagino Lobato, Communication Manager
tagino@karmaverdefresh.com
www.karmaverdefresh.com
Publication date: Thu 25 Feb 2021
Author: Rebekka Boekhout
© VerticalFarmDaily.com
Agritech: Precision Farming With AI, IoT and 5G
For a company that grows and delivers vegetables, Boomgrow Productions Sdn Bhd’s office is nothing like a farm, or even a vertical farm. Where farms are bedecked with wheelbarrows, spades and hoes, Boomgrow’s floor plan is akin to a co-working space with a communal island table, several cubicles, comfortable armchairs, a cosy hanging rattan chair and a glass-walled conference room in the middle
Image from: Photo by Mohd Izwan Mohd Nazam/The Edge
For a company that grows and delivers vegetables, Boomgrow Productions Sdn Bhd’s office is nothing like a farm, or even a vertical farm.
Where farms are bedecked with wheelbarrows, spades and hoes, Boomgrow’s floor plan is akin to a co-working space with a communal island table, several cubicles, comfortable armchairs, a cosy hanging rattan chair and a glass-walled conference room in the middle.
At a corner, propped up along a walkway leading to a rectangular chamber fitted with grow lights, are rows of support stilts with hydroponic planters developed in-house and an agricultural technologist perched on a chair, perusing data. “This is where some of the R&D work happens,” says Jay Dasen, co-founder of the agritech start-up.
But there is a larger farm where most of the work behind this high-tech initiative is executed. Located a stone’s throw from the city centre in Ampang is a 40ft repurposed shipping container outfitted with perception technologies and artificial intelligence (AI) capabilities that mimic the ideal environment to produce more than 50,000kg of vegetables a year.
Stacked in vertical layers, Boomgrow’s vegetables are grown under artificial lights with Internet of Things (IoT) sensors to detect everything from leaf discolouration to nitrate composition. This is coupled with AI and machine learning algorithms.
Boomgrow is the country’s first 5G-connected vertical farm. With the low latency and larger bandwidth technology, the start-up is able to monitor production in real time as well as maintain key parameters, such as temperature and humidity, to ensure optimal growth conditions.
When Jay and her co-founders, K Muralidesan and Shan Palani, embarked on this initiative six years ago, Boomgrow was nowhere near what it is today.
The three founders got together hoping to do their part in building a more sustainable future. “I’ve spent years advising small and large companies on sustainability, environmental and social governance disclosures. I even embarked on a doctorate in sustainability disclosure and governance,” says Jay.
“But I felt a deep sense of disconnect because while I saw companies evolving in terms of policies, processes and procedures towards sustainability, the people in those organisations were not transforming. Sustainability is almost like this white noise in the background. We know it’s important and we know it needs to be done, but we don’t really know how to integrate it into our lives.
“That disconnect really troubled me. When we started Boomgrow, it wasn’t a linear journey. Boomgrow is something that came out of meaningful conversations and many years of research.”
Shan, on the other hand, was an architect who developed a taste for sustainable designs when he was designing modular structures with minimal impact on their surroundings between regular projects. “It was great doing that kind of work. But I was getting very dissatisfied because the projects were customer-driven, which meant I would end up having debates about trivial stuff such as the colour of wall tiles,” he says.
As for Murali, the impetus to start Boomgrow came from having lived overseas — while working in capital markets and financial services — where quality and nutritious produce was easily available.
Ultimately, they concluded that the best way to work towards their shared sustainability goals was to address the imminent problem of food shortage.
“By 2050, the world’s population is expected to grow to 9.7 billion people, two-thirds of whom will be in Asia-Pacific. Feeding all those people will definitely be a huge challenge,” says Jay.
“The current agricultural practice is not built for resilience, but efficiency. So, when you think of farming, you think of vast tracts of land located far away from where you live or shop.
“The only way we could reimagine or rethink that was to make sure the food is located closer to consumers, with a hyperlocal strategy that is traceable and transparent, and also free of pesticides.”
Having little experience in growing anything, it took them a while to figure out the best mechanism to achieve their goal. “After we started working on prototypes, we realised that the tropics are not designed for certain types of farming,” says Jay.
“And then, there is the problem of harmful chemicals and pesticides everywhere, which has become a necessity for farmers to protect their crops because of the unpredictable climate. We went through many iterations … when we started, we used to farm in little boxes, but that didn’t quite work out.”
They explored different methodologies, from hydroponics to aquaponics, and even started growing outdoors. But they lost a lot of crops when a heat wave struck.
That was when they started exploring more effective ways to farm. “How can we protect the farm from terrible torrential rains, plant 365 days a year and keep prices affordable? It took us five years to answer these questions,” says Jay.
Even though farmers all over the world currently produce more than enough food to feed everyone, 820 million people — roughly 11% of the global population — did not have enough to eat in 2018, according to the World Health Organization. Concurrently, food safety and quality concerns are rising, with more consumers opting for organically produced food as well as safe foods, out of fear of harmful synthetic fertilisers, pesticides, herbicides and fungicides.
According to ResearchAndMarkets.com, consumer demand for global organic fruit and vegetables was valued at US$19.16 billion in 2019 and is anticipated to expand at a compound annual growth rate (CAGR) of 6.5% by 2026.
Meanwhile, the precision farming market was estimated to be US$7 billion in 2020 and is projected to reach US$12.8 billion by 2025, at a CAGR of 12.7% between 2020 and 2025, states MarketsandMarkets Research Pte Ltd.
Malaysia currently imports RM1 billion worth of leafy vegetables from countries such as Australia, China and Japan. Sourcing good and safe food from local suppliers not only benefits the country from a food security standpoint but also improves Malaysia’s competitive advantage, says Jay.
Unlike organic farming — which is still a soil-based method — tech-enabled precision farming has the advantage of catering for increasing demand and optimum crop production with the limited resources available. Moreover, changing weather patterns due to global warming encourage the adoption of advanced farming technologies to enhance farm productivity and crop yield.
Boomgrow’s model does not require the acres of land that traditional farms need, Jay emphasises. With indoor farms, the company promises a year-round harvest, undisturbed by climate and which uses 95% less water, land and fuel to operate.
Traditional farming is back-breaking labour. But with precision technology, farmers can spend less time on the farm and more on doing other things to develop their business, she says.
Boomgrow has secured more than RM300,000 in funding via technology and innovation grants from SME Corporation Malaysia, PlaTCOM Ventures and Malaysia Digital Economy Corporation, and is on track to build the country’s largest indoor farms.
Image from: Boomgrow
The company got its chance to showcase the strength of its smart technology when Telekom Malaysia Bhd (TM) approached it to be a part of the telco’s Smart Agriculture cluster in Langkawi last October.
“5G makes it faster for us to process the multiple data streams that we need because we collect data for machine learning, and then AI helps us to make decisions faster,” Jay explains.
“We manage the farm using machines to study inputs like water and electricity and even measure humidity. All the farm’s produce is lab-tested and we can keep our promise that there are no pesticides, herbicides or any preserving chemicals. We follow the food safety standards set by the EU, where nitrate accumulation in plant tissues is a big issue.”
With TM’s 5G technology and Boomgrow’s patent-pending technology, the latter is able to grow vegetables like the staple Asian greens and highland crops such as butterhead and romaine lettuce as well as kale and mint. While the company is able to grow more than 30 varieties of leafy greens, it has decided to stick to a selection of crops that is most in demand to reduce waste, says Jay.
As it stands, shipping containers are the best fit for the company’s current endeavour as containerised modular farms are the simplest means of bringing better food to local communities. However, it is also developing a blueprint to house farms in buildings, she says.
Since the showcase, Boomgrow has started to supply its crops to various hotels in Langkawi. It rolled out its e-commerce platform last year after the Movement Control Order was imposed.
“On our website, we promise to deliver the greens within six hours of harvest. But actually, you could get them way earlier. We harvest the morning after the orders come in and the vegetables are delivered on the same day,” says Jay.
Being mindful of Boomgrow’s carbon footprint, orders are organised and scheduled according to consumers’ localities, she points out. “We don’t want our delivery partners zipping everywhere, so we stagger the orders based on where consumers live.
“For example, all deliveries to Petaling Jaya happen on Thursdays, but the vegetables are harvested that morning. They are not harvested a week before, three days before or the night before. This is what it means to be hyperlocal. We want to deliver produce at its freshest and most nutritious state.”
Plans to expand regionally are also underway, once Boomgrow’s fundraising exercise is complete, says Jay. “Most probably, this will only happen when the Covid-19 pandemic ends.”
To gain the knowledge they have today, the team had to “unlearn” everything they knew and take up new skills to figure what would work best for their business, says Jay. “All this wouldn’t have been possible if we had not experimented with smart cameras to monitor the condition of our produce,” she laughs.
These Buildings Combine Affordable Housing And Vertical Farming
Inside each building, the ground level will offer community access, while the greenhouse fills the second, third, and fourth floors, covering 70,000 square feet and growing around a million pounds of produce a year
A Million Pounds of Produce A Year, Along With Housing And Jobs.
[Image: Harriman/Gyde/courtesy Vertical Harvest]
02-18-21
Some vertical farms grow greens in old warehouses, former steel mills, or other sites set apart from the heart of cities. But a new series of projects will build multistory greenhouses directly inside affordable housing developments.
“Bringing the farm back to the city center can have a lot of benefits,” says Nona Yehia, CEO of Vertical Harvest, a company that will soon break ground on a new building in Westbrook, Maine, that combines a vertical farm with affordable housing. Similar developments will follow in Chicago and in Philadelphia, where a farm-plus-housing will be built in the Tioga District, an opportunity zone.
[Image: Harriman/Gyde/courtesy Vertical Harvest]
“I think what we’ve truly understood in the past year and a half—although we’ve been rooted in it all along—is that we have in this country converging economic, climate, and health crises that are rooted in people’s access to healthy food, resilient, nourishing jobs, and fair housing,” Yehia says. “And we saw this as an urban redevelopment tool that has the potential to address all three.”
Nona Yehia [Image: Harriman/Gyde/courtesy Vertical Harvest]
The company launched in 2015 on a vacant lot in Jackson, Wyoming, aiming in part to create jobs for people with physical and developmental disabilities in the area. In 2019, it got a contract from Fannie Mae to explore how its greenhouses could help with the challenge of food security and nutrition, studying how a farm could be integrated into an existing affordable housing development in Chicago as a model for new projects.
Now, as it moves forward with the Chicago project and expands to other cities, it will also create new jobs for people who might have otherwise had difficulty finding work, working with local stakeholders to identify underserved populations. “Part of this is providing healthy, nutritious food,” Yehia says, “but also jobs at livable wages. We’re positioning all of our firms to address the new minimum wage level of $15 an hour with a path towards career development.”
[Image: Harriman/Gyde/courtesy Vertical Harvest]
Inside each building, the ground level will offer community access, while the greenhouse fills the second, third, and fourth floors, covering 70,000 square feet and growing around a million pounds of produce a year. (The amount of housing varies by site; in Maine, the plan includes 50 unites of housing, and the project will also create 50 new jobs.) In Chicago, there may be a community kitchen on the first level. In each location, residents will be able to buy fresh produce on-site; Vertical Harvest also plans to let others in the neighborhood buy greens directly from the farm. While it will sell to supermarkets, restaurants, hospitals, and other large customers, it also plans to subsidize 10-15% of its harvest for local food pantries and other community organizations. “By creating a large-scale farm in a food desert we are creating a large source of healthy, locally grown food 365 days a year,” she says.
Correction: We’ve updated this article to note that the project in Maine has 50 units of housing, not 15, and the company received a contract—not a grant—from Fannie Mae.
ADELE PETERS
ADELE PETERS IS A STAFF WRITER AT FAST COMPANY WHO FOCUSES ON SOLUTIONS TO SOME OF THE WORLD'S LARGEST PROBLEMS, FROM CLIMATE CHANGE TO HOMELESSNESS. PREVIOUSLY, SHE WORKED WITH GOOD, BIOLITE, AND THE SUSTAINABLE PRODUCTS AND SOLUTIONS PROGRAM AT UC BERKELEY, AND CONTRIBUTED TO THE SECOND EDITION OF THE BESTSELLING BOOK "WORLDCHANGING: A USER'S GUIDE FOR THE 21ST CENTURY."
Vertical Farming ‘At a Crossroads’
Although growing crops all year round with Controlled Environment Agriculture (CEA) has been proposed as a method to localize food production and increase resilience against extreme climate events, the efficiency and limitations of this strategy need to be evaluated for each location
Building the right business model to balance resource usage with socio-economic conditions is crucial to capturing new markets, say speakers ahead of Agri-TechE event
Image from: Fruitnet
Although growing crops all year round with Controlled Environment Agriculture (CEA) has been proposed as a method to localize food production and increase resilience against extreme climate events, the efficiency and limitations of this strategy need to be evaluated for each location.
That is the conclusion of research by Luuk Graamans of Wageningen University & Research, a speaker at the upcoming Agri-TechE event on CEA, which takes place on 25 February.
His research shows that integration with urban energy infrastructure can make vertical farms more viable. Graamans’ research around the modelling of vertical farms shows that these systems are able to achieve higher resource use efficiencies, compared to more traditional food production, except when it comes to electricity.
Vertical farms, therefore, need to offer additional benefits to offset this increased energy use, Graamans said. One example his team has investigated is whether vertical farms could also provide heat.
“We investigated if vertical farms could provide not just food for people living in densely populated areas and also heat their homes using waste heat. We found that CEA can contribute to stabilizing the increasingly complex energy grid.”
Diversification
This balance between complex factors both within the growing environment and wider socio-economic conditions means that the rapidly growing CEA industry is beginning to diversify with different business models emerging.
Jack Farmer is CSO at vertical producer LettUs Grow, which recently launched its Drop & Grow growing units, offering a complete farming solution in a shipping container.
He believes everyone in the vertical farming space is going to hit a crossroads. “Vertical farming, with its focus on higher value and higher density crops, is effectively a subset of the broader horticultural sector,” he said.
"All the players in the vertical farming space are facing a choice – to scale vertically and try to capture as much value in that specific space, or to diversify and take their technology expertise broader.”
LettUs Grow is focussed on being the leading technology provider in containerised farming, and its smaller ‘Drop & Grow: 24’ container is mainly focussed on people entering the horticultural space.
Opportunities in retail
“This year is looking really exciting,” he said. “Supermarkets are investing to ensure a sustainable source of food production in the UK, which is what CEA provides. We’re also seeing a growth in ‘experiential’ food and retail and that’s also where we see our Drop & Grow container farm fitting in.”
Kate Hofman, CEO, GrowUp agrees. The company launched the UK’s first commercial-scale vertical farm in 2014.
“It will be really interesting to see how the foodservice world recovers after lockdown – the rough numbers are that supermarket trade was up at least 11 per cent in the last year – so retail still looks like a really good direction to go in.
“If we want to have an impact on the food system in the UK and change it for the better, we’re committed to partnering with those big retailers to help them deliver on their sustainability and values-driven goals.
“Our focus is very much as a salad grower that grows a fantastic product that everyone will want to buy. And we’re focussed on bringing down the cost of sustainable food, which means doing it at a big enough scale to gain the economies of production that are needed to be able to sell at everyday prices.”
Making the Numbers Add Up
The economics are an important part of the discussion. Recent investment in the sector has come from the Middle East, and other locations, where abundant solar power and scarce resources are driving interest in CEA. Graamans’ research has revealed a number of scenarios where CEA has a strong business case.
For the UK, CEA should be seen as a continuum from glasshouses to vertical farming, he believes. “Greenhouses can incorporate the technologies from vertical farms to increase climate control and to enhance their performance under specific climates."
It is this aspect that is grabbing the attention of conventional fresh produce growers in open field and covered crop production.
A Blended Approach
James Green, director of agriculture at G’s, thinks combining different growing methods is the way forward. “There’s a balance in all of these systems between energy costs for lighting, energy costs for cooling, costs of nutrient supply, and then transportation and the supply and demand. At the end of the day, sunshine is pretty cheap and it comes up every day.
“I think a blended approach, where you’re getting as much benefit as you can from nature but you’re supplementing it and controlling the growth conditions, is what we are aiming for, rather than the fully artificially lit ‘vertical farming’.”
Graamans, Farmer and Hofman will join a discussion with conventional vegetable producers, vertical farmers and technology providers at the Agri-TechE event ‘Controlled Environment Agriculture is growing up’ on 25 February 2021.
Bringing The Future To life In Abu Dhabi
A cluster of shipping containers in a city centre is about the last place you’d expect to find salad growing. Yet for the past year, vertical farming startup Madar Farms has been using this site in Masdar City, Abu Dhabi, to grow leafy green vegetables using 95 per cent less water than traditional agriculture
Amid the deserts of Abu Dhabi, a new wave of entrepreneurs and innovators are sowing the seeds of a more sustainable future.
Image from: Wired
A cluster of shipping containers in a city centre is about the last place you’d expect to find salad growing. Yet for the past year, vertical farming startup Madar Farms has been using this site in Masdar City, Abu Dhabi, to grow leafy green vegetables using 95 per cent less water than traditional agriculture.
Madar Farms is one of a number of agtech startups benefitting from a package of incentives from the Abu Dhabi Investment Office (ADIO) aimed at spurring the development of innovative solutions for sustainable desert farming. The partnership is part of ADIO’s $545 million Innovation Programme dedicated to supporting companies in high-growth areas.
“Abu Dhabi is pressing ahead with our mission to ‘turn the desert green’,” explained H.E. Dr. Tariq Bin Hendi, Director General of ADIO, in November 2020. “We have created an environment where innovative ideas can flourish and the companies we partnered with earlier this year are already propelling the growth of Abu Dhabi’s 24,000 farms.”
The pandemic has made food supply a critical concern across the entire world, combined with the effects of population growth and climate change, which are stretching the capacity of less efficient traditional farming methods. Abu Dhabi’s pioneering efforts to drive agricultural innovation have been gathering pace and look set to produce cutting-edge solutions addressing food security challenges.
Beyond work supporting the application of novel agricultural technologies, Abu Dhabi is also investing in foundational research and development to tackle this growing problem.
In December, the emirate’s recently created Advanced Technology Research Council [ATRC], responsible for defining Abu Dhabi’s R&D strategy and establishing the emirate and the wider UAE as a desired home for advanced technology talent, announced a four-year competition with a $15 million prize for food security research. Launched through ATRC’s project management arm, ASPIRE, in partnership with the XPRIZE Foundation, the award will support the development of environmentally-friendly protein alternatives with the aim to "feed the next billion".
Image from: Madar Farms
Global Challenges, Local Solutions
Food security is far from the only global challenge on the emirate’s R&D menu. In November 2020, the ATRC announced the launch of the Technology Innovation Institute (TII), created to support applied research on the key priorities of quantum research, autonomous robotics, cryptography, advanced materials, digital security, directed energy and secure systems.
“The technologies under development at TII are not randomly selected,” explains the centre’s secretary general Faisal Al Bannai. “This research will complement fields that are of national importance. Quantum technologies and cryptography are crucial for protecting critical infrastructure, for example, while directed energy research has use-cases in healthcare. But beyond this, the technologies and research of TII will have global impact.”
Future research directions will be developed by the ATRC’s ASPIRE pillar, in collaboration with stakeholders from across a diverse range of industry sectors.
“ASPIRE defines the problem, sets milestones, and monitors the progress of the projects,” Al Bannai says. “It will also make impactful decisions related to the selection of research partners and the allocation of funding, to ensure that their R&D priorities align with Abu Dhabi and the UAE's broader development goals.”
Image from: Agritecture
Nurturing Next-Generation Talent
To address these challenges, ATRC’s first initiative is a talent development programme, NexTech, which has begun the recruitment of 125 local researchers, who will work across 31 projects in collaboration with 23 world-leading research centres.
Alongside universities and research institutes from across the US, the UK, Europe and South America, these partners include Abu Dhabi’s own Khalifa University, and Mohamed bin Zayed University of Artificial Intelligence, the world’s first graduate-level institute focused on artificial intelligence.
“Our aim is to up skill the researchers by allowing them to work across various disciplines in collaboration with world-renowned experts,” Al Bannai says.
Beyond academic collaborators, TII is also working with a number of industry partners, such as hyperloop technology company, Virgin Hyperloop. Such industry collaborations, Al Bannai points out, are essential to ensuring that TII research directly tackles relevant problems and has a smooth path to commercial impact in order to fuel job creation across the UAE.
“By engaging with top global talent, universities and research institutions and industry players, TII connects an intellectual community,” he says. “This reinforces Abu Dhabi and the UAE’s status as a global hub for innovation and contributes to the broader development of the knowledge-based economy.”