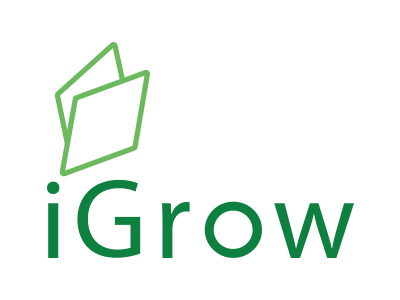
Welcome to iGrow News, Your Source for the World of Indoor Vertical Farming
USDA Funds Composition of New CEA Market Characterization Report
. “This is the first such supply chain assessment in CEA. We appreciate these leaders for stepping forward to support this important effort.”
Resource Innovation Institute (RII) has assembled a senior level of its Technical Advisory Council to support its USDA-funded project titled Data-driven Market Transformation for Efficient, Sustainable Controlled Environment Agriculture. The new Controlled Environment Agriculture (CEA) Leadership Committee, composed of a range of subject matter experts in CEA, will advise the development of a Market Characterization Report that will analyze the emerging “controlled environment” horticultural supply chain to determine opportunities to increase energy and water efficiency in cultivation.
“Market characterization is a critical first step in a coordinated effort to transform an economic sector toward efficient production,” said Derek Smith, Executive Director of Resource Innovation Institute. “This is the first such supply chain assessment in CEA. We appreciate these leaders for stepping forward to support this important effort.”
The Market Characterization Report represents the first publication that RII will deliver as part of its work on a three-year USDA Conservation Innovation Grant designed to advance resource efficiency in CEA, a diverse, expanding market that includes greenhouses and vertical farms growing a range of crops, from microgreens to tomatoes to berries. RII is partnering with the American Council for an Energy-Efficient Economy (ACEEE) to deploy the grant.
The CEA Leadership Committee is providing input on key market characterization issues such as supply chain: describing key market actors, barriers to energy efficiency and the best leverage points for market interventions; energy use: describing the energy used by producers (including on-site renewable energy, microgrids, and back-up generation); advantages of efficiency; describing the energy and non-energy benefits realized through implementation of efficiency projects; and baseline identification: describing key market baselines to be used in evaluating the impact of the market transformation initiative over time.
The organizations represented on RII’s CEA Leadership Committee include:
American Society of Agricultural and Biological Engineers
American Society of Heating, Refrigerating and Air-Conditioning Engineers
CEA Consultancy
Ceres Greenhouses
Energy Solutions
Fifth Season
Fluence by OSRAM
Grodan
Midwest Energy Efficiency Alliance
Oregon Association of Nurseries
Priva
Resource Innovations
Schneider Electric
Signify
UVM Extension Services
Zartarian Engineering
For a complete roster, see www.ResourceInnovation.org/TAC.
For more information:
Resource Innovation Center
www.resourceinnovation.org
7 June 2021
Glase Provides Analysis of CEA Market Growth To Industry Members
Using the results of the USDA’s 2007, 2012 and 2017 censuses, Mattos discussed the national market growth of food crops produced under protection with detailed analyses of the top producing states
During GLASE’s Industry Talks series presentation, executive director Erico Mattos discussed changes to the CEA market based on USDA Census of Agriculture data.
By David Kuack
One of the benefits offered by the Greenhouse Lighting and Systems Engineering (GLASE) consortium to its industry members is its Industry Talks series. This series of informal conversations are presented by academics and field experts who focus on topics suggested by the consortium’s industry members.
During the consortium’s Industry Talks presentation in August, GLASE executive director Erico Mattos reviewed controlled environment production market growth based on the results of the USDA’s Census of Agriculture. Using the results of the USDA’s 2007, 2012 and 2017 censuses, Mattos discussed the national market growth of food crops produced under protection with detailed analyses of the top producing states. The full video can be accessed by GLASE members at the GLASE.org
Increasing value of protected food crops
Total market value for all protected food crops, including tomatoes, vegetables, berries, and fresh herbs, increased 17.9 percent from 2012 to 2017. Market growth for sales of all protected food crops increased 20 percent from $634 million in 2012 to $748 million in 2017. Greenhouse tomato sales increased 4.7 percent from $400 million in 2012 to $419 million in 2017. Other greenhouse vegetable sales increased 40.6 percent from $234 million in 2012 to $329 million in 2017. Fruit and berries sales decreased 13.5 percent from $29 million to $25.1 million even though production area for these crops rose from 7.9 million square feet to 11.7 million square feet.
Greenhouse tomato production area expanded from 55.1 million square feet in 2012 to 63.9 million square feet in 2017, a 16 percent increase. For other greenhouse vegetables, production area rose from 42.8 million square feet in 2012 to 48.6 million square feet in 2017, a 13.6 percent increase.
Only other greenhouse vegetables and fresh-cut herbs saw an increase in market share from 2012 to 2017, rising from 35 percent to 43 percent. Both greenhouse tomatoes and fruit and berries saw a decline in market share between 2012 and 2017. Tomatoes fell 6 percent from 60 percent in 2012 to 54 percent in 2017. The decrease for fruit and berries was only a 1 percent drop from 4 percent in 2012 to 3 percent in 2017.
Increase in protected food crop operations, production area
The number of protected growing operations increased for all crop categories between 2012 and 2017. The number of farms producing greenhouse tomatoes rose 26 percent, up from 6,323 operations in 2012 to 7,974 operations in 2017.
The number of farms producing other greenhouse vegetables rose 36.6 percent between 2102 with 5,268 operations to 7,198 operations in 2017.
Farms producing greenhouse fruit and berries also saw a double digit increase (25.7 percent), up from 673 operations in 2012 to 846 operations in 2017.
Number of small farms increasing
Mattos said the increase in the number of protected crop operations is driven by the establishment of smaller farms.
“There are a lot of smaller farms producing greenhouse vegetables, but they represent a very small part of the market share,’ he said. “In general, as the size of the farms increases the value of sales increases until the size of operations reaches 40,000 square feet or more where there is a dramatic jump in the value of sales.”
Small size farms from 1-999 square feet represent 31.6 percent of the number of farms in the United States. These small operations only cover 1.1 percent of the square foot production area for the total industry. These farms also only represent 1 percent of total sales. They are receiving a net rate of $5.74 per square foot for what they are selling.
Operations from 1,000 to 2,999 square feet account for 32.8 percent of U.S. farms. The net rate sales are the lowest for operations from 2,000 to 2,999 square feet at $4.42.
Those greenhouse vegetable operations with 20,000 to 39,999 square feet in size are earning the most money per square foot at $11.23 per square foot. Mattos said this size category might be a good mix of technology and greenhouse management and are definitely doing something right.
Mattos said there are fewer large farms producing greenhouse vegetables, but they dominate a big part of the market. The largest operations in the U.S. with 40,000 or more square feet represent 2.7 percent of the number of farms. However, they account for 67.6 percent of the square footage (76.1 million square feet) in the U.S. These large operations also have the highest value of sales per square foot at 67.8 percent. These farms are making $6.67 per square foot.
For greenhouse tomatoes, the largest operations are the most efficient, accounting for 74.5 percent of sales and having the largest return per square foot at $7.28.
Major protected-environment producing states
On a state-by-state basis for all greenhouse vegetable categories, the top state in regards to market share value was California with 46 percent, which had a market value increase of 26 percent from 2012 to 2017. Even though the number of farms decreased from 427 to 409, the amount of square footage grew 24 percent from 28.3 million to 35.2 million square feet.
Other leading states with market share included Texas (14 percent), Ohio (10 percent), New York (9 percent), Maine (8 percent), Virginia (7 percent) and Minnesota (6 percent). Ohio had the largest rise in sales, increasing from $10.5 million in 2012 to $43.8 million in 2017, accounting for an increase of 317 percent in just five years. Virginia also experienced a large sales increase (270 percent), going from $8.5 million in 2012 to $31.5 million in 2017.
While California still had the largest market share (33 percent) for greenhouse tomatoes, it wasn’t as dominant as it was for total greenhouse production. Other states which accounted for greenhouse tomato market share included Texas (21 percent), Ohio (13 percent), New York (12 percent), Minnesota (10 percent), Arizona (6 percent) and Illinois (4 percent).
States with the largest increase in tomato share included Ohio (908 percent increase), going from $3.2 million in 2012 to $32.1 million in 2017. Illinois also saw a major rise in greenhouse tomato sales going from $1.7 million in 2012 to $10.7 million in 2017, a 517 percent increase.
For other greenhouse vegetables and fresh-cut herbs, California dominates sales ($126. 2 million) with 60 percent of the market. Virginia followed with 11 percent of the market and Illinois had a 7 percent market share. These two states had the largest growth in this crop category with sales in Illinois rising 565.8 percent from $2.2 million in 2012 to $14.3 million in 2017. Virginia saw sales grow 245 percent from $6.7 million in 2012 to $23 million in 2017.
For more: Erico Mattos, Greenhouse Lighting and Systems Engineering (GLASE), (302) 290-1560; em796@cornell.edu; https://glase.org.
David Kuack is a freelance technical writer in Fort Worth, Texas; dkuack@gmail.com.
Posted in News
Inside Indoor AgTech
In order to better foster thought leadership through The Mixing Bowl and gain a deeper perspective for investment opportunities at Better Food Ventures, we have created a landscape of Indoor AgTech (Download Landscape Here)
Chris Taylor and Michael Rose provide a deep-dive analysis of Indoor Agriculture, tracking more than 1,000 companies to capture the technology ecosystem of controlled-environment agriculture: vertical farms, greenhouses, urban farms, plant factories, and container farms...
Understanding the Landscape
Controlled Environment Agriculture (CEA) or, Indoor Ag, as it is more commonly known, has been garnering tremendous attention because of the compelling benefits of growing indoors in a controlled environment. In order to better foster thought leadership through The Mixing Bowl and gain a deeper perspective for investment opportunities at Better Food Ventures, we have created a landscape of Indoor AgTech (Download Landscape Here). As with our partners’ landscape maps from Brita Rosenheim and Seana Day on FoodTech and AgTech (field production), this landscape focuses on the technology of the Indoor Ag market.
With the first release of this Indoor AgTech Landscape, we believed it was important to start with an ecosystem of the market as opposed to an investment heat map. As part of this effort, we are tracking more than 1,000 companies in the indoor space. This landscape is a subset of those companies, and others, that are active in the space. While some market assessments, including the notable AgFunder AgriFood Tech Investment Report, include cannabis, algae, and insect production, this landscape is limited to traditional food crop production, from seed to immediate post-harvest activities, and utilizes a lens focused on digital and information technology.
The landscape is segmented into broad categories of component technologies, production growing systems, and actual growers. Some other important components of indoor operations, such as the structures themselves, energy systems, and traditional or tangential equipment and supplies are not part of the map. Additionally, many companies in this space, particularly established vendors, offer products in multiple categories but are only represented once. Also, tools that are often shared with field farmers, such as supply-chain platforms and other downstream applications, are captured on the AgTech Landscape created by our colleague Seana Day.
Greenhouses as part of the Indoor Ag Landscape
While there has been much media attention on growing indoors with artificial lights in “Sunless” environments (sometimes referred to urban, vertical, indoor, plant factory,…), greenhouses, as an indoor farming approach, need to be included in the discussion and we have made a point to include them in this landscape. Greenhouses provide similar compelling benefits as a complete Sunless approach and have been utilized to enhance crop production for decades. They have evolved to become technically sophisticated, large in scale and widely deployed while incorporating a broad range of innovations in energy, sustainability, lighting, environmental control, irrigation, monitoring and automation. There are a number of greenhouse operations where production is already fully automated such as Little Leaf Farms in Massachusetts.
Component Technology
Indoor AgTech component technologies are represented on the left half of the landscape map segmented into environment, monitoring, management, and automation. In general, these technologies may be applicable to both sunless and greenhouse environments.
The landscape includes vendors of systems that are used to maintain an optimal growing environment, namely environmental control, irrigation/fertigation, and lighting. Environmental control and fertigation are not new technologies, but as they encapsulate and effectuate a grower’s decisions, they have enabled greater precision and scale in operations. Lighting, the third component, has seen more change in recent years as LEDs have emerged as a viable alternative to traditional lighting technologies. Lighting systems, most obvious in sunless environments, are also applied in greenhouse operations.
Companies offering monitoring solutions, including sensors and imaging systems to gather data on the environment, crop health and pests and disease pressure are also included. Environmental Monitoring companies measure conditions such as indoor and outdoor weather, soil moisture, and nutrient, CO2 and light levels; data that has been used historically to drive decisions and control at a relatively macro level. Newer innovations in Pest/Disease and Crop Monitoring like automated scouting, stress detection, and growth monitoring can shift focus from maintaining external conditions to a plant’s real-time response to a grower’s decisions.
The Management and Analytics segment, including crop and farm management solutions, may hold the most promise of all the component technologies. With more extensive deployment of sensors and associated big-data analytics, the growth environment will be increasingly managed by predictive, proactive, real-time, and autonomous optimization by AI that can recognize complex interactions beyond a grower’s capabilities. However, as with field farming, maximizing yield does not necessarily equate to maximizing the success of the overall operation. Forecasting, labor and overall farm management solutions address that greater requirement.
Production Growing Systems
In addition to individual component technologies being marketed to the Indoor Ag market, companies are also selling production growing systems in various formats and configurations: appliances, containers, and sunless and greenhouse production systems. These systems extend almost linearly in size and features from countertop consumer units to acres-scale installations, many being provided as complete growing environments. While one can find countless consumer and hobbyist growing systems on Amazon, Alibaba, and Walmart.com, the landscape does not capture them due to our commercial growing focus.
Industrial Appliances
A step up from the consumer growing systems are Industrial Appliances. These standalone units, intended for restaurants, grocery stores or corporate/school foodservice, are designed for volume production and can be located in the front of the store and in the “back of the house”. While primarily focused on greens and herbs, they provide retailers and foodservice with the freshest produce available, virtually eliminating the carbon footprint of distribution. Some questions do arise around food safety and challenges of adding new operational roles to this labor impacted sector. These appliances not only contain all the requisite elements of a growing environment and operating software, but many are offered with a service/supply program that included seeds, nutrient inputs, grow recipes and even remote monitoring and operation, i.e., remote growing by the appliance vendor.
Container Systems
Like the Industrial Appliances, Container Systems offer a complete growing environment but typically enclosed in a shipping-like container. In general, these units provide a significant increase in production volume and great flexibility in location, including and typically outdoors. Available for a moderate investment (roughly $100,000) they can produce tons of greens and herbs annually. This combination of benefits has made this approach appealing to a broad range of customers from retailers or food service locating units at their distribution centers to rural field farmers wanting to try their hand at indoor growing on a yearly basis.
Sunless and Greenhouse Production Systems
Manufacturers can deploy production systems at industrial scale. They are usually modular and allow purchasers to expand a system footprint as needed. Typically these systems are complete growing environments that include all the necessary components for production, often configured to be site-specific. These systems are specifically designed to reduce labor and maximize yield for the space allocated, often through the use of automation. As with other segments of the landscape, many of these system manufacturers are building products for both the sunless and greenhouse markets.
The growing environment of Sunless Production Systems is vertically oriented and typically configured as stacked horizontal trays or vertical growing panels/walls. Most of these systems deliver nutrients utilizing hydroponics though some providers are offering aeroponics approaches such as the Mobile Aeroponics system from the CombaGroup in Switzerland. Currently, most systems deployed are producing leafy greens and herbs, and in some cases strawberries. While generally smaller in footprint compared to greenhouses, they are capable of large production per floor area due to the system’s vertical orientation, such as at the Jones Food Company facility with its 17 levels stacked to a height of 36 feet. In some instances though, Sunless Production Systems have been deployed with larger footprints such as SananBio’s Chinese installation covering more than two acres and producing 1.5 tons of leafy greens a day. These systems are being offered with various business models. This can range from a simple equipment sale to a turnkey offering where a provider such as Infinite Acres will partner with the purchaser and provide operational expertise.
Greenhouse Production Systems are typically horizontally oriented with nutrients delivered through various approaches such as deep water with floating rafts, Nutrient Film Technique, or drip irrigation. The systems will operate in environments with ambient light, and supplemental lighting purchased separately. They are available for a range of crops from leafy greens and herbs to vining crops such as tomatoes, cucumbers and peppers and increasingly, strawberries. The footprint of a typical Greenhouse Production System is quite large with installation increments characterized in acres, or even tens of acres. Automation within systems varies and is usually crop dependent with a minimal amount in systems for vining crops and an extensive level in leafy greens and herbs. A number of providers such as Hortiplan and Viscon have extensive deployments of fully automated systems that handle seeding to harvest.
Growers
As mentioned above, we thought it was important to highlight indoor growers in addition to Indoor Ag technologies in this year’s landscape. While it is still farming at its core, technology is the essence of modern Indoor Ag and its operations. Not only do indoor producers leverage technology to farm, in many instances growers such Plenty, Bowery and aquaponics grower, Edenworks, are developing their own technology.
The landscape captures as a subset of the growers operating in the market today. Those represented are noted for the respective scale and scope of technology used in their operations, innovative systems integration, novel approaches, or that they are currently pioneering technical growing practices in their country or region.
Modern Sunless Growers, catching the spotlight in the last few years, are standing on the shoulders of early Plant Factories built in Asia where they began over 25 years ago. While most of the publicly identified funding for Sunless Growers over the last few years has been in the U.S., there are now more than 500 Plant Factories in operation throughout Asia according to New Bean Capital. Operating economics remains a key challenge and criticism for these facilities and sunless operations in general, although the Japanese grower Spread, which opened their second facility in late 2018, claims that through the use of technology, scale, and automation they are not only profitable but can be cost-competitive with field farming.
Greenhouses are the larger and more developed growing method. Cuesta Roble Consulting estimates that there are more than one million acres of vegetable production inside permanent structures worldwide. Though, most of the technically advanced and greatest concentration can be found in the Netherlands where there are more acres “under glass” than the size of Manhattan. While already well established as an indoor-growing approach, it appears the recent attention on Sunless farming and cannabis has stimulated additional activity in the sector. Since the beginning of 2018 more than $500 million has been invested in Sunless growers. During that same time period, the Greenhouse sector has seen the likes of Equilibrium raise and deploy its new Controlled Environment Foods Fund of $336 million, Gotham Greens and Bright Farms raise $84 million and investors such as ValueAct Capital Management and Revolution invest in AppHarvest, which is building one of the country’s largest greenhouse in Eastern Kentucky.
There are many impressive and much needed community-based and social impact organizations focused on indoor growing. These efforts range from Teens for Food Justice working on urban access of fresh produce to increasing employment opportunities for veterans by Veterans to Farmers. These are important entities but are not captured on the landscape as it focuses on commercial-scale businesses and production.
The Changing Landscape
For the purpose of this first Indoor AgTech Landscape, we make the distinction of Greenhouse and Sunless as a growing approach or market. This segmentation is done only to raise awareness, to ensure the entire market and various approaches are represented.
Too often we hear declarative statements that “this” is the “right” approach for Indoor Ag or is “the” future of farming. It is more appropriate to start with the question “what problem are you trying to solve?” The unique environmental, climate, economic, and market factors will inform the growing approach. It is doubtful that a one-size-fits-all solution will dominate, but rather utilization of the most appropriate growing structures, systems, and technologies for the desired crop, location and business goal. The challenges, needs, and parameters in Singapore are not going to be the same as St Louis, or Dubai. It is not always an either-or question.
Not only are we seeing vendors and technology providers offering products and systems for both the Sunless and Greenhouse segments, some growers are now utilizing or combining the two approaches. Veteran indoor grower Green Sense Farms is now designing combined facilities and Shenadoah Growers, a long time field and greenhouse grower, has added Sunless production to their operations. Deliscious, a Dutch lettuce grower has seamlessly integrated sunless seeding and propagation into the automation workflow before plants are transported and finished in a greenhouse mobile gutter system. Even on the financing front, start-up Contain is providing a leasing and insurance platform for all indoor farming approaches from “container farms and warehouse farms to the most sophisticated greenhouses and plant factories.”
Moving Forward
To meet its promise and continued expansion, particularly to those locations underserved by traditional production methods, Indoor Ag needs to drive down its cost of operations. Sunless production, especially, has further to go on this front mainly due to a lack of efficiencies from scale and energy use. While indoor costs need to be closer to field production, no one will benefit from a race to the bottom on cost. Indoor and field production are both working on some of the same challenges including labor, sustainability, safety, traceability, and profitability. Technology has an important role in meeting those challenges and we look forward to seeing further advances, innovations, and implementations in data capture and analytics, automation, and predictive and autonomous control.
We welcome your thoughts and reactions and look forward to following the Indoor AgTech landscape together for the coming years.
Bios:
Chris Taylor, a Senior Consultant on The Mixing Bowl team, has spent more than 20 years on global IT strategy and development innovation in manufacturing, design and healthcare, focusing most recently on Indoor AgTech.
Michael Rose is a Partner at The Mixing Bowl and Better Food Ventures where he brings more than 25 years immersed in new venture creation and innovation as an operating executive and investor across the Internet, mobile, restaurant, and Food Tech and AgTech sectors.
Tradeoffs In Aquaponics Vs Hydroponics, By The Numbers
Enhanced flavor and higher consumer preference for ecologically grown products make aquaponics better aligned with consumer and operator interests
Part two in our “Lean manufacturing for indoor agriculture” series
Nov 26, 2017
In our previous blog post, we made the case that aquaponics enables better capacity management for indoor agriculture than hydroponics. The basis of our argument is that aquaponics is a “just-in-time” manufacturing system — multiple SKUs with different nutrient requirements can be produced in the same aquaponic system simultaneously without sacrificing quality or yield, whereas multiple hydroponic systems with different nutrient recipes would be required to achieve similar quality and yield.
This is one of the key reasons that we believe aquaponics is the future of indoor farming.
But what if you stripped away all the benefits of aquaponics? Is aquaponics still competitive with hydroponics on cost if you assumed the same yield, quality, and breadth of product with no fish sales? Unwinding this is the purpose of this blog post, and we find that aquaponics is slightly more expensive with costs 2% higher than those in hydroponics as a percentage of revenue. To compensate for this, aquaponic operators will need to utilize the capacity management methods discussed in our previous blog post to achieve throughputs ~2% higher than their hydroponic counterparts. Below, we break down how we got to these numbers.
But first, there are trade offs besides cost in choosing aquaponics over hydroponics. Let’s start with aquaponics’ unique barriers to entry.
Nonstarters
The first two tradeoffs with aquaponics are existential. The inability to overcome these first two tradeoffs will make it highly unlikely the aquaponic farm will get off the ground.
Lack of off-the-shelf systems and expertise. If you want to be a commercial hydroponics operator, there are dozens of top-notch hydroponic design and consulting firms who can construct turnkey, state-of-the-art hydroponic farms anywhere in the world and even bring in an experienced grower to run the operation. If you’re a hobbyist, you can buy an off the shelf hydroponic system, along with the hydroponic bible, Howard Resh’s Hydroponic Food Production, and get yourself 80% of the way there (it’s great — aquaponic hobbyists should buy it too and get themselves 50% of the way there). In short, hydroponic education and expertise is accessible.
In aquaponics, while there are experts who have designed large scale commercial operations, these experts are few and far between. Scaling an aquaponic farm relies on finding these people, most of whom are not in the US. On the education front, while there are books on aquaponics, the true leaders of the movement are PhD-level researchers who have published narrowly focused academic papers as opposed to accessible, comprehensive, authoritative guidebooks. It’s on operators to find the right people, design a stable system, and implement a comprehensive operating plan.
Keeping the fish and plants healthy, at the same time. This is a big one. Each piece of the aquaponic ecosystem — the fish that supply manure, the bacteria that break down the manure into nutrients that are bioavailable to the plants, and the plants that absorb those nutrients and drive revenue — requires slightly different environmental conditions. Optimizing for plant health, as a result, requires monitoring three different systems as opposed to one.
Even if you were to install a well-designed aquaponic system and manage the operational tradeoffs, black swan events happen. If the fish develop an infection, if you develop a fly infestation, or if pythium (a common fungus that wreaks havoc on plants) takes root, the standard remedies of antibiotics for fish or toxic pesticides for crops won’t cut it in a traditional aquaponic design.
Your production is entirely dependent on maintaining a healthy ecosystem and plant microbiome. When you kill the bad microbes through antibiotics or pesticides, they tend to kill the good microbes too. Most pesticides, even organic ones, are not “fish safe” — fish are particularly chemical sensitive. For aquaponic farmers, the ecological approach to farming doesn’t just apply when yields are steady. It applies 24/7, 365 days a year, barring traditional, toxic, pesticidal approaches to solving these problems.
All that said, hydroponic and aquaponic operations are converging towards similar operating constraints due to technology improvements and consumer demand. One of the most sought after labels in produce is “pesticide free”. As a result, many of the latest generation of hydroponic operators have taken up the label, limiting themselves to the same biological and ecological remedies aquaponic operators are inherently restricted too. At the same time, “decoupled” aquaponic systems, where water only flows in one direction — from the fish to the plants (and not back again) — are growing in popularity due to their ability to treat the plants without worrying about the effect on fish. The result is the ability to use the same plant treatments as a traditional hydroponic facility.
Luckily for all camps, there are plenty of ways to remedy these issues in pesticide free facilities that are more cost effective than traditional approaches. In indoor farms especially, the incidence of most issues can be reduced through rigorous standard operating procedures for both day to day practices and early detection of and response to ecological stress.
If you’re confident that you have the expertise to design a stable aquaponic system and to handle both the operating basics and ecological considerations during black swan events, then it’s worth digging into the operating costs of aquaponics and hydroponics.
Comparing operating costs
There are certain added costs associated with aquaponics — there’s no free lunch, so growing all those fish has to be accounted for somewhere. For aquaponics to be a better business than hydroponics, the added costs must be compensated for by either higher throughput of salad greens or fish. In our previous blog post, we showed how aquaponics can achieve higher throughput than hydroponics. In this analysis, assuming fish are never sold, we show that throughput needs to be ~2% higher in order for aquaponics to beat hydroponics on cost, which is well within aquaponics’ potential.
We have put these tradeoffs in a spreadsheet for a more convenient comparison. You can see the spreadsheet here, while reading below for context. The numbers here are not reflective of Edenworks’ designs and projections. We’re basically asking “if we ran our competitor’s farms aquaponically instead of hydroponically, what would the business look like?” For example, Gotham Greens projected an EBITDA for their first facility at “greater than 15%,” and so we’ve targeted a 15% EBITDA margin for the hydroponic facility, then made a few changes based on industry-standard assumptions to back out the aquaponic cost analysis.
source: Edenworks spreadsheet analysis
The following line items are the largest cost differences:
Added expense of fish feed. While hydroponic fertilizer is most often composed of mined mineral salts, fish feed for aquaponics has the fat and protein that the fish need along with the minerals that both plants and fish need. For aquaponics in a recirculating shallow water culture system, we calculate¹ the expense of fish feed to be about 9 cents per pound of harvested greens, a 7 cent premium over synthetic hydroponic fertilizer. Assuming best in class yields for both systems, this comes out to a 1.4% difference in nutrient costs between the two systems, as a percentage of revenue. However, with the world farming more fish than ever before, new technologies are coming online that are expected to substantially lower the price of fish feed, while also making the feed more sustainable.
Added labor. Most indoor farming facilities have a long way to go until they can be considered highly automated. Despite incorporating automation and machine learning techniques for things like climate control and disease detection, modern indoor farms still complete many tasks, such as harvesting, by hand. The biggest labor efficiency gains are fertilizer (i.e. hydroponic / aquaponic) agnostic. Those gains come from automating the movement of plants through the production system, along with the unit tasks of seeding, transplanting, harvesting, packaging, and cleaning. This is where Edenworks has invested substantially in IP, but that’s a story for another post.
All that said, raising fish does require someone who knows how to spot potential health issues, how to harvest fish, and how to maintain aquaculture equipment. None of this is time intensive, but it does require hiring an aquaculture specialist at each facility.
Space for the fish. Aquaponic fish tanks and hydroponic nutrient reservoirs require similar space. However, aquaponic systems require a bit more space overall for the extra pumps, sumps, and biofilters for converting fish waste into nutrition for the plants — an additional 1.7% more space in our analysis of an approximately 70,000 square foot hydroponic facility. Assuming rent for warehouse space is $10 per square foot, this comes out to a difference of 0.1% of revenue.
Quantifying the total trade-off.
Assumptions are based on commonly used designs, equipment, and raw material suppliers, which are noted in the spreadsheet. Furthermore, in order to get close to an apples to apples comparison, we assumed the following:
Both systems sell baby greens for the same price.
Revenue from fish, and the associated costs of selling fish are not included.
Both systems are vertically stacked, indoor farms.
Yields for both hydroponic and aquaponic systems are the same. For the purpose of this study, we use our yield estimate for AeroFarms. AeroFarms has projected yields of 2 million lbs of greens at their Newark facility. Looking at the size of their facility (69,000 s.f.) and their geometry, we estimate their growing space is ~160,000 s.f.² in vertically stacked beds. This gives AeroFarms 12.5 lbs yield / s.f. / year, which is in line with other best-in-class yields for hydroponic and aquaponic indoor leafy greens farm.
Both systems have similar needs, and therefore costs, for the following line items: energy, packaging, growing medium, seeds, delivery, rent, cleaning and other general farm supplies, and merchandising.
This leaves just three significant differences between the costs of the two systems: nutrients (fish feed vs synthetic fertilizer), labor (employing an aquaculture specialist vs. having one less employee), and rent (extra space needed to break down organic nutrients vs. not needing extra space).
Given the assumptions behind these hypothetical facilities, we estimate aquaponic systems’ costs as a percentage of revenue are 2 percentage points higher than hydroponics’. In order to compensate for these added costs, aquaponic facilities need to sell 2% more of their capacity than hydroponic facilities. As explained in our previous post, with typical per-SKU sales swings in packaged salad of up to 20% week on week, hydroponic farms that cannot grow different crops in the same production system suffer from significant capacity constraints. Aquaponics, on the other hand, can grow wide varieties of crops in the same production system, enabling them to sell higher percentage of their capacity (certainly higher than 2% more).
To top it all off, enhanced flavor and higher consumer preference for ecologically grown products make aquaponics better aligned with consumer and operator interests. It is for these reasons, in addition to its competitiveness with hydroponics on cost, that we believe aquaponics will become the primary fertilization technology for indoor operators as the market continues to grow.
¹ This calculation is based on standard aquaponic feed ratios from Dr. James Rakocy and hydroponic feed ratios from Howard Resh’s book Hydroponic Food Production. These calculations are in the third tab of the spreadsheet and are what we used in this analysis. Comparing one “standard” feed rate to another “standard” feed rate seemed apples to oranges to us though, so we also compared feed costs based on nitrogen content of each feed, and came up with very similar cost ratios. These are presented in the fourth tab of the spreadsheet.
² Aerofarms’ bedspace estimation comes from public websites. For bed width and length, see (a) and (b). For number of beds, see (b) and (c).
(a) https://patentimages.storage.googleapis.com/pdfs/US8533992.pdf
(b) http://www.foxbusiness.com/features/2015/07/28/farming-in-sky-inside-wall-street-backed-vertical-farm.html
(c) https://www.nytimes.com/2015/04/08/realestate/commercial/in-newark-a-vertical-indoor-farm-helps-anchor-an-areas-revival.html
Is The United States "Under Greenhoused"?
Peter Tasgal: The author is a consultant focused on the agriculture space with previous experience as CFO and board member of a $100 million CPG business headquartered in Montreal, Canada prior to which he was an investment banker for over 10 years.
US Greenhouse Trends - Comparison to Netherlands and Finland
May 28,2019
Peter Tasgal: The author is a consultant focused on the agriculture space with previous experience as CFO and board member of a $100 million CPG business headquartered in Montreal, Canada prior to which he was an investment banker for over 10 years.
His contact information is as follows: Peter Tasgal, ptasgal1@gmail.com, 617-794-4058.
The United States has over 10,000 vegetable and herb growing greenhouses according to the 2017 US Census of Agriculture. However, the majority of production occurs in only a small slice of these. A mere 296 of these greenhouses (2.7% of the category), make up what is termed as the “Large Commercial Greenhouses” category - characterized as being 40,000 square feet or larger. However, the Large Commercial Greenhouse category represents 68% of total square footage and sales. United States production is highly concentrated and much of the growth in vegetable greenhouses has been in “Small Greenhouses” – characterized as being less than 10,000 square feet. As of 2017, there are 9,658 greenhouses of less than 10,000 square feet, a 3.5x increase from 2002, when there were just 2,726.
The United States is “under-greenhoused” when it comes to vegetable production. Below is a comparison of the United States, The Netherlands, and Finland’s greenhouse vegetable production on a per capita basis:
United States: 0.35 square feet of greenhouse per capita
Finland: 4.12 square feet of greenhouse per capita
Netherlands: 31.4 square feet of greenhouse per capita
The reasons for the significant discrepancies among countries include Finland’s climate being much less conducive to outdoor farming than the US, and in the case of The Netherlands, it is a significant exporter around the world. However, these discrepancies are massive. Finland has 12x the production of the US per capita and The Netherlands has 90x the production of the US per capita. Why is this and more importantly how do we increase US production in a significant way?
Commercial Greenhouses – US
The focus of this document is commercial greenhouses, which I classify as those 10,000 square feet or greater. 10,000 square feet was chosen as the US Census shows an average sales figure of just over $6 per square foot for greenhouses of 10 to 20 thousand square feet, implying a minimum $60,000 revenue per greenhouse in the category. Please note this is a minimum and there are farmers doing hundreds of thousands of dollars in revenue in greenhouses less than 10,000 square feet. For analytic purposes it is useful to delineate those greenhouses which are 10 to 40 thousand square feet (“Medium Commercial Greenhouses”) as compared to Large Commercial Greenhouses, those over 40 thousand square feet. The following table summarizes data from the 2017 Census of Agriculture for:
“Total greenhouse vegetables and fresh cut herbs”:
The 1,191 commercial greenhouses represent 81% of greenhouse vegetable production. Within commercial greenhouses, those defined as medium sized are quite small, averaging less than 17 thousand square feet. A 17 thousand square foot greenhouse selling product at a rate of $6 per square foot is generating in the range of $100,000 in revenue per annum. As in any analysis, these figures are averages, and many greenhouses are doing far more in revenue on a per square foot basis. Like anything else, greenhouses are not all the same. Revenues are dependent on crop types, cycles per annum, efficiency of farm, location and sales method.
Benchmarking “Best of Breed”
Finland
Given that Finland is one of the world’s northernmost countries, outdoor vegetable growth is limited. This makes Finland ideally suited for greenhouse production, as well as imported products. Finland imports significant amounts of outdoor grown produce from the likes of Spain, Italy, Greece and other parts of the world. However, there is a significant concern from the Finnish people regarding pesticide levels of imported fruits and vegetables. According to the Luke Natural Resources Institute of Finland, the country is more independent in terms of greenhouse vegetables than it was 10 to 15 years ago.
According to the Natural Resources Institute of Finland, as of 2018, there were 484 enterprises involved in greenhouse vegetable production. This represents 2.1 million m2 of production. 2.1 million m2 equates to 22.8 million square feet of production and an average of over 47 thousand square feet per enterprise. As a comparison, the average vegetable producing greenhouse in the US is just over 10 thousand square feet.
The Netherlands
The Netherlands has been the leader in greenhouse production for decades. In a September 2017 article in the National Geographic it was noted that The Netherlands is the “globe’s number two exporter of food as measured by value, second only to the United States, which has 270 times its landmass.” Comparing US greenhouse production to The Netherlands’ is difficult as the Dutch made a national commitment toward sustainable agriculture in the early 2000’s. However, it does give the US direction as to production and methodologies for the future.
According to Statistics Netherlands, there were 4,990 hectares (approximately 537 million square feet) of vegetable production under glass in 2018 across 1,180 greenhouses. This represents an average of over 455 thousand square feet per greenhouse. For comparison purposes, the average size of a Large Commercial Greenhouse in the US is about 257,000 square feet, just over half the size of the average of all vegetable greenhouses in The Netherlands.
Trends in the US Compared to Best of Breed Countries
When analyzing 10 and 20-year trends in the US vegetable greenhouse industry, findings show them to be in almost direct contrast to the trends for a similar period in Finland and The Netherlands. In the US there has been a rapid increase in the number of greenhouses and total production space, but the average size of each greenhouse has gotten smaller. Similar trends exist relating to commercial vegetable greenhouses in the US, those 10,000 square feet and greater. The number of greenhouses and production space has increased, but the average size of each greenhouse is smaller. In 2007 the average size of a commercial vegetable greenhouse was 118 thousand square feet and in 2017 averaged 76 thousand square feet, a 35% decrease over the decade.
In Finland and The Netherlands the number of enterprises have decreased dramatically. There is a slight discrepancy in terms of average production space. In the Netherlands average production space has increased nominally and in Finland it has decreased, but these trends are much more moderate than those trends in the US. In both the Netherlands and Finland the average size of each greenhouse has risen dramatically over the period. The tables on the following page highlight the long-term trends:
Table 1. US Vegetable Greenhouse Industry
The contrast between countries is quite staggering. The Dutch are the clear industry leaders, distantly followed by the Finnish, and even more distantly followed by the US. Additionally, the trends in each of Finland and the Netherlands are highly consistent on a year-over-year basis over the long-term. Looking to the future of the US commercial vegetable greenhouse industry, similar trends are expected to those that Finland and The Netherlands have experienced over the past 10 to 20 years. Looking forward 10 years from now, I would expect the average commercial greenhouse in the US to be significantly larger than 76 thousand square feet.
Basis for Trends in The Netherlands and Finland
Some of the underlying reasons for the trends outlined above for the Finnish and Netherlands greenhouse industries are outlined below:
Aging Farmers – The farmer population is aging. Those next generation farmers who have chosen to remain farmers have invested in larger greenhouses with more modern cultivation technology which will allow them to compete on a global scale.
Professionalism – Maintaining a competitive presence requires professional operations, especially in the highly competitive export market.
Mergers / Alliances – Given that economies of scale are reached through larger facilities; there has been significant merger / alliance activity. In Finland, for example, there are currently 3 to 4 entities representing 70 to 80% of the production of lettuce and herbs.
Desire for Local – In Finland there is less dependence on imported produce than 10 to 15 years ago. People want local produce. At those times when local is not accessible, consumers still want to know the origin of their produce. There is a major concern in Europe regarding levels of pesticide use by outdoor farmers in the major European growing areas - Spain, Italy, Greece.
Renewable Energy Sources – The latest technology in greenhouses is expected to utilize “renewable energy resources”, potentially making greenhouse production carbon neutral. This would quell a lot of the discussion regarding the balancing act between greenhouses using less water than outdoor growing; but using more energy resources for lighting and temperature maintenance.
The basis for trends in The Netherlands and Finland are directly relevant to the United States applying to:
Aging farmers
Desire for locally grown food
Concerns as to farming practices of food exporters
Pesticides
Energy usage / Ability to use renewable energy
Environmental volatility
Population growth
Water scarcity
A significant number of these could be mitigated through the building of technologically advanced greenhouses and other forms of CEA within the United States. There are highly experienced commercial greenhouse manufacturers in the United States, The Netherlands and around the world who can bring the latest technology to the US market (See Appendix A – Overview of Greenhouse Manufacturers).
Summary:
Currently the United States is “under-greenhoused”. There are many reasons why it is important and possible for the United States to have more greenhouses over the near and long-term. The United States can be an efficient operator of greenhouses, similar to best of breed countries - The Netherlands and Finland, if some trends over the past two decades are steadily reversed. Growth in vegetable greenhouses will need to be focused on Large Commercial Greenhouses as compared to Small Greenhouses. The technology and capital needed to build large greenhouses is expensive. However, the end result of building such greenhouses will help mitigate some of the biggest issues of our time – energy usage, water scarcity, consumer knowledge of food origin, and growth inputs.
© 2019 - The Under-Greenhoused U.S. - Peter Tasgal
The Urban Farming ‘Revolution’ Has A Fatal Flaw
Commercial urban agriculture in New York City has provided questionable environmental gains, and has not significantly improved urban food security
By Emma Bryce
April 15, 2019
Commercial urban agriculture in New York City has provided questionable environmental gains, and has not significantly improved urban food security.
These are the findings of a recent case study of New York City which shows that, despite the fanfare over commercial urban farming, it will need a careful re-evaluation if it’s going to play a sustainable role in our future food systems.
The rise of commercial controlled-environment agriculture (CEA)—comprised of large scale rooftop farms, vertical, and indoor farms—is a bid to re-envision cities as places where we could produce food more sustainably in the future. Proponents see CEA as a way to bring agriculture closer to urban populations, thereby increasing food security, and improving agriculture’s environmental footprint by reducing the emissions associated with the production and transport of food.
But the researchers on the new paper wanted to explore whether these theoretical benefits are occurring in reality.
They focused on New York City, where CEA has dramatically increased in the last decade. Looking at 10 farms that produce roof- and indoor-grown vegetables at commercial scales, they investigated how much food the farms are producing, who it’s reaching, and how much space is available to expand CEA into.
They found that the biggest of these 10 commercial farms is around a third of an acre in size. Most are on roofs spread across New York City, and some are inside buildings and shipping containers. Mainly, these farms are producing impressive amounts of leafy greens such as lettuce, and herbs; some also produce fish.
But while rooftop farms rely on natural sunlight to feed the crops, indoor farms use artificial lights. These farms potentially have a greater energy footprint even than conventional outdoors farms, the researchers say–challenging the assumption that urban farms are less impactful than conventional ones.
Some farms also embraced high-tech systems, such as wind, rain, temperature, and humidity detectors and indoor heating, to enhance growing conditions in environments that aren’t naturally suited to agriculture. These elevate the energy costs of the food produced, and may be giving CEA an unexpectedly high carbon footprint, the researchers say.
Furthermore, the predominantly grown foods—such as lettuce—aren’t of great nutritional value for the urban population, especially those threatened by food insecurity. Most produce from CEAs is sold at a premium, something that partly reflects the cost of the real estate used to grow the food. Consequently, that produce is typically grown for high-end food stores and restaurants, meaning it’s unlikely to reach low-income urban populations who need it most.
The researchers also think it’s unlikely that CEA—which currently occupies just 3.09 acres in New York City—could expand into the roughly 1,864 acres they estimate is still suitable for urban farming in New York City.
The rising cost of real estate might put these urban acres beyond the reach of new farming start ups, they think. These companies also face increasing competition from a growing number of farms springing up on the outskirts of cities—where land is cheaper and there’s space to produce more food, while also benefiting from urban proximity.
With its one-city focus, the research isn’t representative of what might be unfolding in other places around the world. Other cities may be having more success—for instance, Tokyo has gained global attention for its large scale vertical farming efforts. Yet as a case study, it does reveal useful lessons—especially for cities wanting to meet the original twin goals of urban agriculture: equitably increasing access to food, at a lower environmental cost.
The researchers note first of all that CEA is optimal in places where less supplemental heat and light is needed to grow food. More thought might also be given to the nutritional value and cost of foods grown, to generate benefits for all the city’s residents, not just high-income ones. The researchers question whether smaller, community-driven plots of urban agriculture—like community gardens, school, and prison farms—might actually do a better job of providing food to at-risk city residents, compared to commercial urban farms that inevitably have to focus on profits.
Based on the study of New York, the researchers caution: “CEA may be touted as an exciting set of technologies with great promise, but it is unlikely to offer a panacea for social problems or an unqualified urban agricultural revolution.”
It’s easy to be drawn in by the dystopian allure of vertical farms and underground greens nestled into our cities. But until we’ve streamlined its role, we should perhaps not overstate what commercial urban agriculture can do—or, instead be guided by cities where there are stronger signs of social and environmental success.
Source: Goodman et. al. “Will the urban agricultural revolution be vertical and soilless? A case study of controlled environment agriculture in New York City.”Land Use Policy. 2019.
This piece was originally published on Anthropocene Magazine, a publication of Future Earth dedicated to creating a Human Age we actually want to live in.
The Future of Container Farming & Controlled-Environment Agriculture
There are positives and negatives of growing produce far from the end consumer, but most would agree that all else being equal, local is better
Peter Tasgal: The author is a consultant focused on the agriculture space with previous experience as CFO and board member of a $100 million CPG business headquartered in Montreal, Canada prior to which he was an investment banker for over 10 years.
His contact information is as follows: Peter Tasgal, ptasgal1@gmail.com, 617-794-4058.
Over the past two decades many industries including the auto industry and the retail environment have seen drastic evolutions. At first glance, the agricultural space seems to be lagging behind. Produce at your local grocery store largely comes from seasonally favorable climates. For example, tomatoes from Canada during summer and peppers from Mexico during winter. Increasingly, produce is coming from areas of the world in close proximity of the equator to limit seasonality. Today, more than half of the fresh fruit and over one-third of the fresh vegetables that Americans buy is grown outside of the United States. This share has been growing steadily for decades and is expected to continue to grow over the future decade and beyond. 1
There are positives and negatives of growing produce far from the end consumer, but most would agree that all else being equal, local is better. Chilean grapes stored in refrigerated containers for 1 to 5 months at a temperature of 30 to 32 degrees Fahrenheit and which have traveled 5000 miles are not going to taste as good as freshly picked grapes from your local farmers market.
Community desire for local produce, combined with improvements in hydroponic, lighting and other technologies, have attracted participants looking to grow in controlled environments. Controlled environments include greenhouses – both ground level and rooftop, buildings, and 40 to 53-foot shipping containers re-purposed for growing.
The table below provides a high-level comparison of some prominent forms of farming today:
Please click on the above to enlarge
The fundamental reliance on rain and sun makes traditional farming the most efficient and environmentally friendly form of agriculture. However, generally it is furthest from the end consumer. Shipping containers on the other hand can be located at or are very close to the consumer but are the least efficient in terms of cost per delivered pound. Greenhouses and contained structures are in the middle of the two. Depending on their locations, greenhouses and other contained structures can be close to the consumer. Also, they can deliver produce at a competitive price for certain items.
1 https://www.nytimes.com/2018/03/13/dining/fruit-vegetables-imports.html
Technological innovation is happening in all areas of agriculture. The biggest evolutions are happening in environmental control systems, data collection, material handling/logistics , traceability/food safety and crop management.
Examples of innovators in the agricultural space include:
2 companies founded out of Boston based Flagship Pioneering, Indigo Ag, Inc. and Inari have raised $600 million and $40 million respectively. Indigo Ag is using natural microbiology and digital technologies to improve grower profitability, environmental sustainability and consumer health. Inari is building the world’s first seed foundry to reintroduce genetic diversity to achieve desired field experiences.
New Zealand based BioLumic is introducing Ultraviolet light to transplant crops at nursery stage to increase crop yield.
Philips recently introduced its GreenPower LED production module, optimized for closed, climate- controlled cultivation facilities. The module allows for a dedicated combination of spectrum, intensity, timing, uniformity and positioning of light to optimize production.
Let’s make the assumption that assumption that the consumer prefers locally grown produce, and that locally grown produce tastes best. The question I am then posing is: Can produce grown in a shipping container be priced competitively with traditional farm grown produce? Or, alternatively, does the consumers’ mindset need to be changed for them to be willing to pay a large premium for local products to enable container farming to work? Essentially, does the industry need a “Starbucks model” to motivate people to pay a premium price for a premium product when lower cost, albeit less quality product is available?
The University of California Cooperative Extension Agricultural and Natural Resources – Agricultural Issues Center did a complete analysis in 2015 of a range of crops. One of these crops was romaine hearts from the Central Coast Region (Monterey, Santa Cruz & San Benito Counties). They determined that based on a range of assumptions it costs an average of $0.65 to deliver a pound of romaine hearts to a blend of regions across the United States (See Appendix A for Cost Analysis – Conventional Farming). Traditional retailers in the United States look for 40 to 45% gross margins in their produce departments. This allows retailers to sell a pound of romaine hearts for just over a dollar to meet their return targets.
Grown in a container farm, the cost to deliver a similar product as described above is at best 3.6x the cost of conventional farming ($2.38 per pound), and more realistically 10.9x ($7.14 per pound - See Appendix B for Cost Analysis – Container Farming). This is impressive for container farming, especially given the square footage of a container is equal to approximately 1% of the square footage of an acre of land.
To determine the viability of selling container grown produce at the retail store level, I did a store check on a range of greens at a local supermarket. Greens were chosen as they are the easiest to grow in a container because they stay at a vegetative stage and do not go to a flowering stage. The flowering stage requires additional lighting of different color for optimum growth.
The chart below depicts pricing for a range of greens at a recent store check of a Whole Foods Market in Newton, Massachusetts. A 40% store level gross margin is assumed for the analysis below:
Please click on the above to enlarge
As shown above, container farming can provide a competitively priced source for many of the locally grown items, as well as small packages of specialized herbs. The items for which container farming can be competitive are largely niche products. Examples of this are products sold in low volumes at a Whole Foods Market in an affluent Boston suburb. For example, there were 30 small boxes of organic herbs on the shelf during my visit, equating to less than 2 total pounds of herbs.
Where are likely efficiencies to be found in container farms?
There are 4 high-level variables that determine the efficiency of a container farm:
Product yield
Cost of the container
Labor
Power
Product Yield
According to American Hydroponics (“AmHydro”) the maximum number of plants per year that can be grown in a container are 46,592. This is based on the assumption of 3,584 plant sites are turned 13x per year. This case assumes a 2oz plant, which equates to 5,824 pounds of annual production. This is the most aggressive yield case and assumes each of the following: (i) 4-week grow time; (ii) No loss; and (iii) no downtime. A much more realistic yet still aggressive yield case would be closer to 4,000 pounds of production. This is based on a 5 to 6 week grow period, 10 turns per year, and some downtime for container maintenance and cleaning. After discussions with container farmers, their estimation of actual yields are closer to 3,000 pounds per year. Efficiency improvements are likely to be limited in terms of yield, given the size constraints of a container.Container Cost
Freight Farms is listing its containers at $85,000 prior to delivery and set-up. AmHydro projects a delivered figure of $87,000. Each of these figures assume use of a container typically purchased from shipping lines and/or container lessors once determined the containers are no longer seaworthy, retrofit for hydroponic farming. CAI International, a major container lessor, published in its 2017 annual report a 3-year average residual price for a 40-foot standard dry van container of $1,101 and $4,045 for a 40-foot high cube refrigerated container. Therefore, the vast majority of the cost of a container ready for farming lies in its retrofitting and profit margin to the container farm seller / lessor.
Determining the true cost of retrofit for a container is difficult. Dan Backhaus, the number 2 person at now defunct PodPonics, a company which had raised $14 million in funding, estimated the cost of retrofit at approximately $20,000. Additionally, a Google search of container farms for sale depicted several Freight Farm units originally purchased in 2016 and now being listed for sale between $55,000 and $68,000.
Efficiencyimprovementsarelikelytobegreatestintheareaofcontainercosts. Ifthemarketgrowsthere will be additional container farm suppliers which will bring prices down. In Appendix B, under the likely scenario, the amortization of the cost of the container represents $2.25 per pound of production.
Labor
The amount and cost of labor is a function of several variables:
Proximity – For example, if one person is going to be responsible for several containers which are far
apart, this will require more staffing hours than if containers are clustered together;
Product type (s) being grown – Certain crops require more care than others and growing multiple crops
will require more labor;
Singular vs multiple cycles – One consistent cycle where an entire containers’ crop is ready at one time
will be more efficient compared to staggering the cycle so that product is being harvested on a more
frequent basis.;
Container layout – More efficient container layout could optimize labor efficiency, although the
efficiency may come with the cost of lower production levels; and
Cost of labor in the region.
Improvements in labor efficiencies are likely to be a function of what is trying to be achieved in the container farm. As the popularity of container farming increases, labor is likely to become more skilled and containers will be in closer proximity. Technological advancements have been very effective in reducing labor costs (eg. viewing plants and monitoring pH levels and other internal variables from a distance). However, most of these technological advancements are what has made container farming viable today. Most of these technological enhancements are not since but rather prior to the advent of the container farm. There has been limited research on the use of robotics to improve harvesting and seeding in container farms. This could potentially have a great impact on labor efficiency but will be very expensive.
Power
Based on my discussions, the item that farmers underestimate the most is the cost to provide heating and cooling to the container farm. The containers themselves are solid steel masses but then are being modified for an alternate function. Modifications are frequently made to provide multiple entrances and exits. Additionally, provisions for ventilation, heating and cooling are needed to achieve optimal temperatures and humidity levels for plant growth. Each of these modifications reduces the solidity of the container and can require further power. Additionally, as high levels of lighting are required for growth, these lights can generate significant levels of heat.If the container is expected to be mobile, there may be limitations to types of power which can be used. Copious work has been done on the use of solar, with limited benefits to date. The limiting factor largely is the square footage of the container (typically 8ft x 40ft). Increased lighting efficiency, predominantly within LED, has improved power efficiency. These improvements are likely to increase steadily.
Summary of Efficiencies
The greatest cost improvement will be the pricing of the retrofit container. In a blog posting in March of 2018 by the Indoor-Ag Conference, it was estimated that branded containers cost in the range of $50,000 and $120,000 to purchase (our analysis uses $85,000 to $87,000) and those which were “homegrown” cost between $15,000 and $20,000. The cost of the branded containers should come closer to those which are homegrown. In the same blog, it was estimated that the cost of LED lighting, representing 25% of the fixed cost of a container, is expected to fall 40% from 2017 to 2020.
Labor is a second area where efficiencies will likely occur. However, gaining short term efficiencies in labor will likely be capital intensive. Given there are an estimated 500 container farms in the world, the incentive to infuse large amounts of dollars into container farms by R&D focused entities, is likely limited. The efficiencies will likely initially come to greenhouses and other contained environments; then the technology will be transferred to container farms.
Container Farms vs. Other Types of Controlled Environments
One of the many benefits of a container farm is related to being close to the customer. Another is that production is occurring in a fully contained environment. However, what are the benefits of container farming as compared to other forms of farming in controlled environments? The Indoor-Ag Conference Blog from March 2018 described the 5 most important benefits of container farms (paraphrased below):
The typical farmer is aging and 80% of container farmers are new to growing – Therefore, this brings new farmers into industry.
Investors have shown interest in providing funding to the industry.
Container can be in place and ready to grow in a few months, versus many months to over a year for
a fixed structure.
Containers can be placed almost anywhere due to size and having been retrofit offsite.
Comparatively low priced to set-up.
However, the question still remains, why choose a container instead of other forms of controlled environment farming facilities. This is a complex question because the constraints of the container footprint can impact the efficiencies of the container. I outlined 2 major reasons that could spur the growth of the container farm industry, as outlined below.
Reason 1: The primary reason that I can see for growth in container farms is that new farmers want to get into the industry with a limited investment. In no other form can one own a farm and all the necessary equipment for less than $100,000, and be up and running within a few months. This is an enticing motivator for an individual interested in going into farming. However, why the need for container farming. If a product can be grown in an alternative contained environment at a location within a day’s transport from the end consumer, at a cost that is far below that of produce grown in an on-site container farm; then there seems limited need for the container form for farming. Potentially container farming would be practical in an extremely cold location, where building a solid structure would be problematic.
Reason 2: Marketing! Wouldn’t it be a great marketing tool for a high-end restaurant or other type of food establishment to tell customers that the food they are eating was grown on-site and picked just prior to serving. An interesting example is the Boston based Cultivar restaurant, that touted on their homepage “Chef Dumont’s menu is informed by the restaurant’s on-site Freight Farm hydroponic garden, enabling fresh food production year-round, along with seasonal market produce, foraged ingredients, sustainable seafood and dry-aged meats”. In this example and others, the container was a great marketing tool and provided a premium product. However, it required great amounts of time and expense. I visited Cultivar l
to see the container and noted that it was covered in a fine wood exterior (see picture below) and was seeming less than a 20-foot container (less than 160 square feet). The container was located in a very public and expensive location and has a singular entrance point outside of the restaurant requiring an individual to go outside of the restaurant to harvest. Per Cultivar’s website, the container produced 225 heads of lettuce, brassicas and herbs a week.2
Summary:
Following a full analysis herein, my conclusion is that container farming is and will continue to be a niche product. It appears that fewer new farmers will buy container farms as they learn the results others have experienced. I believe container farming will become an increasingly niche product focusing on area’s that cannot get recently harvested produce at a reasonable price as well as niche restaurants and other food establishments that are willing to invest their resources to tout the growth of produce on-site.
The benefits of growing in a container, versus growing in an alternative contained environment are largely supply-side benefits: (i) Need for more farmers in the market; (ii) Investors seeking returns in the space; (iii) Entry into market with limited capital; (iv) Time to market; and (v) Limited footprint. It is on the demand side that the viability of the business comes into question. What do you get by growing right next to your location, versus, growing within a short distance of your location? The answer lies in the marketing of the container farm. It is my belief that the entities whom are willing to invest time and money to gain this marketing appeal will be very limited.
2 Please note that in January of 2019 it was announced that Cultivar was closing after being opened for less than 2 years. Speaking to Cultivar’s owner, Mary Dumont, she stated that the farm would be for sale in the near future.
Please click on the above to enlarge
Please click on the above to enlarge
Please click on the above to enlarge
USDA Vertical Ag Workshop Report
On June 27 and 28, 2018 the U.S. Departments of Agriculture and Energy co-hosted a workshop in Washington, D.C.
By urbanagnews
March 1, 2019
On June 27 and 28, 2018 the U.S. Departments of Agriculture and Energy co-hosted a workshop in Washington, D.C. The workshop engaged stakeholders, experts, and researchers from across the United States in interdisciplinary discussions on the potential for indoor agriculture (IA), in the context of sustainable urban ecosystems, to address global environmental challenges. Participants collaborated to identify Research and Development (R&D) challenges, opportunities, and needs relating to six major areas:
Community Services
Economics 5.
Ecosystem Services
Plant Breeding
Pest Management
Systems Engineering
Discussions relating to each of these six major themes are summarized in the body of this report.
USDA Vertical Ag workshop report Download
Get The Free Report On The Investment Potential Of Greenhouse Business In Russia 2018
Last year was one of the most successful years for Russia’s greenhouse industry. Over 250 ha new commercial greenhouses were commissioned, the number of 5-gen greenhouses increased. Further expansion of greenhouse area is expected – new projects are set to be launched in different regions across the country.
Last year was one of the most successful years for Russia’s greenhouse industry. Over 250 ha new commercial greenhouses were commissioned, the number of 5-gen greenhouses increased. Further expansion of greenhouse area is expected – new projects are set to be launched in different regions across the country.
Prior to the International Investment Forum and Exhibition “Greenhouse Complexes Russia 2018”, Vostock Capital team of analysts has conducted a research on the investment potential of Russian greenhouse industry, which covers:
the information about the prospects for the development of Russian greenhouse industry
new investment greenhouse projects (construction and modernisation)
criteria for the selection of technology and equipment by the decision-makers of greenhouse companies and agriholdings and many other important results.
Request the report:
The research involved over 250 respondents, including the C-suite of agroindustrial holdings and greenhouse complexes, suppliers of latest technologies and equipment, regulators, project operators, representatives of financial institutions and investors, independent market experts.
The international Forum and Exhibition “Greenhouse Complexes Russia 2018” is the high-class professional platform to unlock investment in Russian greenhouse industry, discuss industry development strategy, share experiences between key market players and conclude new lucrative contracts.
The Event spans investors from the CIS, Europe, and Asia, initiators of investment projects from across Russia, decision-makers of federal and regional agriholdings, dedicated ministries and agencies, heads of regions, retail chain executives, service providers, presidents of national unions and associations.
Contact: Elvira Sakhabutdinova, Project Director
ESakhabutdinova@vostockcapital.com Tel. +7 499 505 1 505
Website: http://www.greenhousesforum.com/en/