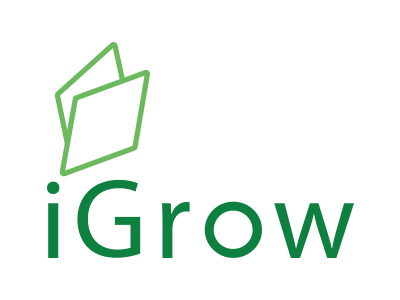
Welcome to iGrow News, Your Source for the World of Indoor Vertical Farming
BONAFIDE Will Continue To Develop It's Concept On Decentralized Agriculture And Food Supply Systems
The trend for decentralization is growing all the time and we trust that agricultural policies will follow suit to support local farmers and a new generation of young entrepreneurs that find their ideology in creating new markets
Over the last 6 years, we have seen technology advance to facilitate urban vertical farming embracing entrepreneurial opportunities, the supply of fresh food daily, and secure cultural kitchens requirements for raw materials anytime anywhere.
At the same time conflicts, natural resource competition, and climate change have had adverse effects on food security that local production using new technology can alleviate.
The trend for decentralization is growing all the time and we trust that agricultural policies will follow suit to support local farmers and a new generation of young entrepreneurs that find their ideology in creating new markets.
thomas.tapio@gmail.com
Thomas Tapio (LION) • Consultant (retired)
Strasbourg 27th February 2021, 🇫🇷🇪🇺
Little Leaf Farms Raises $90M to Grow Its Greenhouse Network
Massachusetts-based Little Leaf Farms has raised $90 million in a debt and equity financing round to expand its network of hydroponic greenhouses on the East Coast. The round was led by Equilibrium Capital as well as founding investors Bill Helman and Pilot House Associates. Bank of America also participated.
by Jennifer Marston
Image from: Little Leaf Farms
Massachusetts-based Little Leaf Farms has raised $90 million in a debt and equity financing round to expand its network of hydroponic greenhouses on the East Coast. The round was led by Equilibrium Capital as well as founding investors Bill Helman and Pilot House Associates. Bank of America also participated.
Little Leaf Farms says the capital is “earmarked” to build new greenhouse sites along the East Coast, where its lettuce is currently available in about 2,500 stores.
The company already operates one 10-acre greenhouse in Devins, Massachusetts. Its facility grows leafy greens using hydroponics and a mixture of sunlight supplemented by LED-powered grow lights. Rainwater captured from the facility’s roof provides most of the water used on the farm.
According to a press release, Little Leaf Farms has doubled its retail sales to $38 million since 2019. And last year, the company bought180 acres of land in Pennsylvania on which to build an additional facility. Still another greenhouse, slated for North Carolina, will serve the Southeast region of the U.S.
Little Leaf Farms joins the likes of Revol Greens, Gotham Greens, AppHarvest, and others in bringing local(ish) greens to a greater percentage of the population. These facilities generally pack and ship their greens on the day of or day after harvesting, and only supply retailers within a certain radius. Little Leaf Farms, for example, currently servers only parts of Massachusetts, Pennsylvania, New York, and New Jersey.
The list of regions the company serves will no doubt lengthen as the company builds up its greenhouse network in the coming months.
Vertical Farming ‘At a Crossroads’
Although growing crops all year round with Controlled Environment Agriculture (CEA) has been proposed as a method to localize food production and increase resilience against extreme climate events, the efficiency and limitations of this strategy need to be evaluated for each location
Building the right business model to balance resource usage with socio-economic conditions is crucial to capturing new markets, say speakers ahead of Agri-TechE event
Image from: Fruitnet
Although growing crops all year round with Controlled Environment Agriculture (CEA) has been proposed as a method to localize food production and increase resilience against extreme climate events, the efficiency and limitations of this strategy need to be evaluated for each location.
That is the conclusion of research by Luuk Graamans of Wageningen University & Research, a speaker at the upcoming Agri-TechE event on CEA, which takes place on 25 February.
His research shows that integration with urban energy infrastructure can make vertical farms more viable. Graamans’ research around the modelling of vertical farms shows that these systems are able to achieve higher resource use efficiencies, compared to more traditional food production, except when it comes to electricity.
Vertical farms, therefore, need to offer additional benefits to offset this increased energy use, Graamans said. One example his team has investigated is whether vertical farms could also provide heat.
“We investigated if vertical farms could provide not just food for people living in densely populated areas and also heat their homes using waste heat. We found that CEA can contribute to stabilizing the increasingly complex energy grid.”
Diversification
This balance between complex factors both within the growing environment and wider socio-economic conditions means that the rapidly growing CEA industry is beginning to diversify with different business models emerging.
Jack Farmer is CSO at vertical producer LettUs Grow, which recently launched its Drop & Grow growing units, offering a complete farming solution in a shipping container.
He believes everyone in the vertical farming space is going to hit a crossroads. “Vertical farming, with its focus on higher value and higher density crops, is effectively a subset of the broader horticultural sector,” he said.
"All the players in the vertical farming space are facing a choice – to scale vertically and try to capture as much value in that specific space, or to diversify and take their technology expertise broader.”
LettUs Grow is focussed on being the leading technology provider in containerised farming, and its smaller ‘Drop & Grow: 24’ container is mainly focussed on people entering the horticultural space.
Opportunities in retail
“This year is looking really exciting,” he said. “Supermarkets are investing to ensure a sustainable source of food production in the UK, which is what CEA provides. We’re also seeing a growth in ‘experiential’ food and retail and that’s also where we see our Drop & Grow container farm fitting in.”
Kate Hofman, CEO, GrowUp agrees. The company launched the UK’s first commercial-scale vertical farm in 2014.
“It will be really interesting to see how the foodservice world recovers after lockdown – the rough numbers are that supermarket trade was up at least 11 per cent in the last year – so retail still looks like a really good direction to go in.
“If we want to have an impact on the food system in the UK and change it for the better, we’re committed to partnering with those big retailers to help them deliver on their sustainability and values-driven goals.
“Our focus is very much as a salad grower that grows a fantastic product that everyone will want to buy. And we’re focussed on bringing down the cost of sustainable food, which means doing it at a big enough scale to gain the economies of production that are needed to be able to sell at everyday prices.”
Making the Numbers Add Up
The economics are an important part of the discussion. Recent investment in the sector has come from the Middle East, and other locations, where abundant solar power and scarce resources are driving interest in CEA. Graamans’ research has revealed a number of scenarios where CEA has a strong business case.
For the UK, CEA should be seen as a continuum from glasshouses to vertical farming, he believes. “Greenhouses can incorporate the technologies from vertical farms to increase climate control and to enhance their performance under specific climates."
It is this aspect that is grabbing the attention of conventional fresh produce growers in open field and covered crop production.
A Blended Approach
James Green, director of agriculture at G’s, thinks combining different growing methods is the way forward. “There’s a balance in all of these systems between energy costs for lighting, energy costs for cooling, costs of nutrient supply, and then transportation and the supply and demand. At the end of the day, sunshine is pretty cheap and it comes up every day.
“I think a blended approach, where you’re getting as much benefit as you can from nature but you’re supplementing it and controlling the growth conditions, is what we are aiming for, rather than the fully artificially lit ‘vertical farming’.”
Graamans, Farmer and Hofman will join a discussion with conventional vegetable producers, vertical farmers and technology providers at the Agri-TechE event ‘Controlled Environment Agriculture is growing up’ on 25 February 2021.
Bowery’s Founder, Irving Fain, On The Future of Vertical Farming
At one point in the not-so-distant past, vertical farming’s role in our future agricultural system was far from certain. Growing leafy greens in warehouse-like environments controlled by tech seemed like a compelling business, but one that had yet to prove itself either economically or as an important source of food for a growing world population
Image from: The Spoon
At one point in the not-so-distant past, vertical farming’s role in our future agricultural system was far from certain. Growing leafy greens in warehouse-like environments controlled by tech seemed like a compelling business, but one that had yet to prove itself either economically or as an important source of food for a growing world population.
That, at least, was a common sentiment Irving Fain, CEO and founder of Bowery, met with when he started his vertical farming company five years ago. “There was a bit of skepticism around it,” he told me over a call recently, suggesting that five years ago, there were a lot more “ifs” than “whens” in terms of vertical farming’s future.
Fain, Bowery, and the entire vertical farming industry get a much warmer reception nowadays. Investment dollars are pouring into the space. Around the world, companies, scientists, and food producers are using the method to not just supply upscale grocery stores with greens but experiment with breeds of produce, feed underserved populations, and grow food in non-arable regions. As Fain suggested when we spoke, the last 12 months seem to have turned those “ifs” into definite “whens.”
Bowery’s last 12 months also illustrate this change. Fain said that Bowery went from under 100 retail locations about a year ago to nearly 700 right now, and will be in more than 1,000 “in the coming months.” Its produce is in a number of food retailers around the Mid-Atlantic and Northeast, including Whole Foods Market, Giant Food, Stop & Shop, Walmart, and Weis Markets. And in 2020, the company experienced “more than 4x growth” with e-commerce partners.
While the pandemic is responsible for some of this popularity, Fain insists it is not the only reason for the eventful year. “It’s definitely bigger than the pandemic,” he said. “What you’re seeing is a food system that’s evolving and [people have a desire] to see transparency and traceability in the food system.” These, he says, are issues the traditional food supply chain isn’t really able to address right now, hence the opportunity for companies like Bowery, which effectively cut multiple steps out of the supply chain.
Bowery grows its greens (lettuces, herbs, and some custom blends) inside industrial spaces where crops are stacked vertically in trays and fed nutrients and water via a hydroponic system. Technology controls all elements of the farm, from the temperature inside to how much light each plants get. The company currently operates two farms, one in New Jersey and the other in Maryland. A third is planned for Pennsylvania.
Technology, in particular, is something Bowery has big plans for. On top of a retail expansion, Bowery also added some notable personnel to its staff, including Injong Rhee, formerly the Internet of Things VP at Google as well a chief technologist at Samsung. Having such technology chops onboard will be vital in order for Bowery to realize many of its ambitions around advanced automation, which has the potential to optimize many parts of the seed-to-store process for vertically grown greens.
For example, Bowery’s farms are equipped with sensors and cameras that are constantly collecting data — “billions” of points, according to the company — that can be used to not just observe the current state of plant health but also predict the most optimal growing conditions for each crop. Elements like temperature, humidity levels, nutrient levels, and light intensity can all be adjusted, via the BoweryOS software, to create those optimal conditions. The end result is more consistent crop production, better yields, more flavorful food, and, ideally, a better nutritional profile for the greens compared to what conventional produce offers.
The system can also, through automation and AI, detect problems with plants. In a recent interview with Venture Beat, Bowery Chief Science Officer Henry Sztul used the example of butterhead lettuce yellowing at the edges during growth. Bowery’s system is technologically advanced enough at this point that it is starting to understand the conditions that create those yellowing edges. That foreknowledge, in turn, will allow growers to adjust the crop “recipe” (see above mixture of lights, temperature, etc.) to avoid the problem.
It took Bowery years to get to this point in terms of what its technology is capable of doing. “The system [for] indoor farming that you choose has a direct impact on the crops you’ll be able to grow, on the margins you’ll be able to generate, and on the return profile of the business itself,” said Fain. “And so being incredibly intentional and thoughtful about what technology you use is something we spent a lot of time on because it has an extraordinarily important economic impact.”
On a less technically complex note, controlled ag from Bowery and others also goes some way towards reinventing the supply food chain. Rather than greens being harvested in, say, Mexico and shipped via a complex distribution process all the way to Baltimore, they are packaged up at the farm and distributed to nearby retailers, usually those within a day’s drive “It is much more sustainable. It is much more efficient, and it’s more reliable, and those things have been important to consumers long before COVID,” said Fain.
Bowery will continue to innovate on both the technology and supply side of its business, as well as with the food itself. The company just launched a new specialty product line that will experiment with different flavors of greens and change frequently.
In terms of tech, Bowery’s latest farm, currently being built in Bethlehem, Pennsylvania, will incorporate even more automation than the company’s two existing farms. That location is slated to open later in 2021. When it does, Bowery will be capable of serving nearly 50 million people within a 200-mile radius.
The company hopes to expand its geographic reach much wider some day, building farms near most major U.S. cities and beyond. Given the increased confidence in the vertical farming sector as a whole, now looks to be the optimal time to move towards those ambitions.
by Jennifer Marston, The Spoon
These 2 Companies Are Putting Big Money Into Hawaii’s Agricultural Future. Will Their Bets Pay Off?
A pair of companies backed by a billionaire and a pension fund are trying to revitalize fallow farmland in the state
A pair of companies backed by a billionaire and a pension fund are trying to revitalize fallow farmland in the state.
02-15-21
On Lanai, where shreds of black plastic in the soil are the last vestiges of the island’s defunct pineapple fields, a sliver of long-abandoned farmland is getting an encore — and a reinvention.
In six high-tech greenhouses, a futuristic vision of food-growing is underway — one in which nutrient density and flavor are automated.
It doesn’t matter that the red dirt below the greenhouse is eroded or peppered with plastic that once served as Dole pineapple plantation’s weed control. In fact, the hydroponic tomatoes and leafy greens grown here by Sensei Ag don’t depend on soil at all.
The ag-tech company founded by Larry Ellison, the Oracle founder who owns nearly all of Lanai’s acreage, and Dr. David Agus, a physician, and medical researcher, is pioneering tools to produce affordable food in places like Lanai that — despite its history as an agricultural plantation — lack traditional farming essentials like water and fertile soil.
Sensei Farms Lanai, a two-acre indoor farming pilot project by Larry Ellison’s Sensei Ag, produced 35,000 pounds of produce in less than three months last year. Sensei Ag
In doing so, the company is redeploying a scrap of neglected farmland into active agriculture in an attempt to buck an unsettling trend: Hawaii imports more than 85% of its food.
Hawaii has tens of thousands of acres of fallow former sugar and pineapple plantation lands. There are many reasons why this land isn’t being used for farming — inadequate infrastructure, soil erosion, the sky-high price of agricultural real estate. All of these challenges and more make growing food on old plantation acreage unaffordable for most farming operations.
Putting more of this stagnant acreage into food production, however, is a worthwhile goal, experts say, because it could help the state wean itself off of a reliance on the cargo ships and planes that deliver food supplies to the islands.
“When you bring up Hawaii to anyone anywhere on earth, what they think of is paradise on earth,” said Vincent Mina, president of the Maui Farmers Union United. “But what paradise do you know of that brings in 85% of its food?”
State Efforts Have Fallen Short
Re-fashioning former sugar and pineapple plantations into viable food farms is what the Hawaii Agribusiness Development Corp. was designed to do.
However, a scathing state audit in January said that the 25-year-old state agency has so far failed its mission because “the economic void created when plantations ceased production remains mostly unfilled.”
Larry Jefts, one of the state’s largest produce producers, recently expanded his farm footprint with access to ADC lands in Central Oahu that had lain fallow since Del Monte stopped pineapple production nearly two decades ago.
The problem, according to Jefts, is not that the ADC is inert. It’s the state’s poor land use policy that has allowed some farmland to be developed, as well as society’s lack of commitment to local agriculture.
The Agribusiness Development Corp. has failed in its mission to reinvent Hawaii’s agricultural sector, two recent reports say. Office of the Auditor
“The problem is there’s no will here,” Jefts said. “Good farm ground is coming out to go into solar energy farms because the people who own it can make more money in solar. If they charged that much money to the farmers, the farmers would fail and imported foods would take over.”
Yet while Jefts is farming on a portion of the 1,200-acre Whitmore Project — land left vacant by Del Monte in 2004 and then acquired by the ADC for local agriculture in 2012 — hundreds of acres attached to the project remain fallow almost 10 years later.
That’s in part due to the time-intensive, bureaucratic process of securing money, permits, and contracts to build and repair the infrastructure required to make more of the acreage farmable, said Sen. Donovan Dela Cruz, a champion of the project.
It’s one thing to acquire the land, he said. But it’s another challenge entirely to ready it for farmers who need water, roads, electricity for refrigeration, and food safety-compliant facilities in order to make their businesses financially viable.
“With our state, there’s so many good intentions but just no money to put through to implementation,” said Kirsten Oleson, associate professor of ecological economics at the University of Hawaii College of Tropical Agriculture and Human Resources.
“If we’re serious about doubling production of food that is grown and eaten here, it would take some time to rethink policy and some pretty large and potentially risky investment that the state’s coffers don’t have.”
While state efforts flounder, a pair of new agriculture companies backed by a billionaire and a pension fund are stepping in with lofty goals to revitalize fallow farmland with diversified agriculture operations that aim to help Hawaii wean itself off of imported foods.
A Billionaire’s Bid To Boost Food Security
On Lanai, Sensei Ag is sidestepping many of the traditional high-yield farming requirements: lots of land, lots of water, lots of hard manual labor.
Founded by Oracle billionaire Larry Ellison, left, and medical researcher David Agus, Sensei Ag’s goal is to grow food that is more sustainable and nourishing than if it were farmed traditionally.
Sensei Ag
Although the company’s two-acre greenhouse farm is just a scrap of the 20,000 farmed acres that earned Lanai the moniker of the world’s largest pineapple plantation, yields from hydroponics can be far greater than those from conventional soil farming.
Sensei Ag CEO Sonia Lo projects the company will harvest 500,000 pounds of food for statewide consumption in 2021, including Swiss chard, basil, tomatoes, cucumber and eggplant.
“What we’re doing is we’re competing against the likes of Organic Girl that’s coming in from California or Earthbound Farms,” Lo said. “It’s pretty straightforward given that our stuff is a day old or two days old by the time it gets on a shelf as opposed to two weeks or three weeks old.”
Hydroponic growing is capital-intensive, however. Sensei Ag’s approach benefits from the fact that it’s bankrolled by Ellison, one of the richest people in the world.
Lo declined to reveal the amount of financial investment it took for the Lanai pilot project to achieve its inaugural harvest last October, but she acknowledged the role of Ellison’s wealth.
Yet while the cost to build a state-of-the-art greenhouse is out-of-reach for most farmers, indoor farming offers growers a chance to capture significant long-term financial savings since producing food this way requires significantly less land and water than traditional outdoor farming.
According to Lo, Sensei Farms Lanai requires about 10% of the amount of water it would take to produce a similar harvest in the dirt.
With this in mind, Sensei Ag’s mission includes efforts to make greenhouse farming more accessible. The company is aggregating risk assessment data in hopes that it will encourage banks to finance indoor growing mechanisms such as greenhouses and vertical farms. The company is also writing a playbook for people who want to build a successful indoor farm business, Lo said.
The rise of this kind of high-tech, high-yield farming could be a key to making Hawaii-farmed foods more competitive, according to Jesse Cooke, vice president of investments and analytics at the Ulupono Initiative.
“Using a hydroponic system, you could guarantee that every week you would have the same amount of quantity and the same quality (of produce) — and that’s what you need to sell to a large grocer,” Cooke said. “A lot of outdoor operations can’t guarantee that because they’re at the whim of nature itself.”
Brian Miyamoto, executive director of the Hawaii Farm Bureau Federation, agrees that indoor farming could be a game-changer — if Hawaii farmers can figure out how to raise enough capital to build the infrastructure without sabotaging future profits.
“We can grow a lot of things here in Hawaii as far as food products,” Miyamoto said. “What we struggle with is doing it competitively — that’s why we import so much.”
Hawaii can’t rely on billionaires to make the upfront investment in high-tech indoor farming, Oleson said. Rather, the state needs to follow in the footsteps of other countries that enacted public policies to encourage this kind of agriculture.
In places like Israel and the Netherlands, high-tech greenhouses are important food production tools, Oleson said.
Beyond policy and economics, Oleson said there are aesthetic and cultural considerations associated with scaling up indoor farming in the islands.
“You’re not looking across rolling green landscapes, you’re looking at lands with big infrastructure on it so there’s sometimes social pushback,” Oleson said. “I’m not a Native Hawaiian, but I would be very curious to know the response of the local community to that kind of agriculture because it’s very divorced from the earth.”
Will Mahi Pono’s ‘Serious Amount Of Money’ Pay Off?
On Maui, a partnership between a California farm management company and a Canadian pension fund is producing food on fallow land resulting from the 2016 closure of the state’s last sugar grower.
Since Mahi Pono bought 41,000 acres of Hawaiian Commercial & Sugar Co.’s former sugar cane fields in 2019, the company has begun growing some of Hawaii’s top food imports — potatoes and onions — in hopes of winning over some of that market share.
Mahi Pono’s mission to produce foods that Hawaii imports heavily and that are agriculturally possible to grow here is a smart one, according to Oleson. But she said it could be difficult for the company to compete with the price point for potatoes and onions imported from the mainland.
In 2016, Hawaii’s last remaining sugar grower shut down an operation that had run for 146 years. Now the 40,000 acres are owned by Mahi Pono, the marriage of a California farm management company and a Canadian pension fund. The company is growing produce with plans to reduce the state’s reliance on imports. Courtesy: Mahi Pono
It might also prove hard to convince consumers to pay more for locally grown potatoes and onions as opposed to more perishable produce.
“Potatoes and onions can sit on a boat and the quality doesn’t decline quite as fast, but all of us know what happens when you buy a box of spinach from Costco and if you don’t eat it that night it turns to slime,” Oleson said. “So the concern is growing foods locally where the freshness really matters.”
But Mahi Pono is growing more than just root vegetables. The company planted over a half million avocado and breadfruit trees, as well as rows of trees to shelter crops from the wind. The company plans to plant its 1 millionth tree by the end of June, according to community relations director Tiare Lawrence.
The company is also growing produce ranging from tangelos and finger limes to broccoli and eggplants, and it’s leasing affordable land and water to small farmers for an annual fee of $150 per acre.
Ultimately, Mahi Pono’s staple crops will be citrus, papaya, macadamia nuts, and coffee, Lawrence said.
And while the company is exporting papayas to Canada, and eventually plans to export coffee, macadamia nuts, and citrus to markets outside the state, the majority of the food produced by Mahi Pono will feed Hawaii’s people, Lawrence said.
“I personally think these lands can be brought into production,” Lawrence said. “We’ve seen it across Hawaii where farmers have been able to take former sugar and pineapple lands and turn it into a thriving farm and I refuse to entertain doomsday scenarios.”
Mahi Pono is growing red, yellow, and white potatoes with the goal of stealing away some of the Hawaii market share from mainland-grown potatoes. Courtesy: Mahi Pono
But the farm enterprise faces many challenges.
With an average wind speed of 30 miles per hour in the Central Maui plains, there are erosion issues, as well as crop damage from pests, deer, and pigs.
“We really can’t plant a field unless we fence it in, so that adds to our costs,” Lawrence said.
There’s also the problem of the former plantation’s aging, outdated infrastructure.
“Mahi Pono has spent a serious amount of money in updating the irrigation systems and making repairs to wells,” Lawrence said.
If Mahi Pono can surmount these challenges and find success, Cooke of Ulupono said the operation will be an example to follow.
“If they can get it up and running, that could be one of the hugest transformations that Hawaii has seen, especially going towards local food for local consumption,” Cooke said. “The worry is that it doesn’t work and somehow the land gets zoned residential and a housing development goes up.”
“Hawaii Grown” is funded in part by grants from the Ulupono Fund at the Hawaii Community Foundation, the Marisla Fund at the Hawaii Community Foundation, and the Frost Family Foundation.
Brittany Lyte is a reporter for Civil Beat. You can reach her by email at blyte@civilbeat.org or follow on Twitter at @blyte
Use the RSS feed to subscribe to Brittany Lyte's posts today
Bringing The Future To life In Abu Dhabi
A cluster of shipping containers in a city centre is about the last place you’d expect to find salad growing. Yet for the past year, vertical farming startup Madar Farms has been using this site in Masdar City, Abu Dhabi, to grow leafy green vegetables using 95 per cent less water than traditional agriculture
Amid the deserts of Abu Dhabi, a new wave of entrepreneurs and innovators are sowing the seeds of a more sustainable future.
Image from: Wired
A cluster of shipping containers in a city centre is about the last place you’d expect to find salad growing. Yet for the past year, vertical farming startup Madar Farms has been using this site in Masdar City, Abu Dhabi, to grow leafy green vegetables using 95 per cent less water than traditional agriculture.
Madar Farms is one of a number of agtech startups benefitting from a package of incentives from the Abu Dhabi Investment Office (ADIO) aimed at spurring the development of innovative solutions for sustainable desert farming. The partnership is part of ADIO’s $545 million Innovation Programme dedicated to supporting companies in high-growth areas.
“Abu Dhabi is pressing ahead with our mission to ‘turn the desert green’,” explained H.E. Dr. Tariq Bin Hendi, Director General of ADIO, in November 2020. “We have created an environment where innovative ideas can flourish and the companies we partnered with earlier this year are already propelling the growth of Abu Dhabi’s 24,000 farms.”
The pandemic has made food supply a critical concern across the entire world, combined with the effects of population growth and climate change, which are stretching the capacity of less efficient traditional farming methods. Abu Dhabi’s pioneering efforts to drive agricultural innovation have been gathering pace and look set to produce cutting-edge solutions addressing food security challenges.
Beyond work supporting the application of novel agricultural technologies, Abu Dhabi is also investing in foundational research and development to tackle this growing problem.
In December, the emirate’s recently created Advanced Technology Research Council [ATRC], responsible for defining Abu Dhabi’s R&D strategy and establishing the emirate and the wider UAE as a desired home for advanced technology talent, announced a four-year competition with a $15 million prize for food security research. Launched through ATRC’s project management arm, ASPIRE, in partnership with the XPRIZE Foundation, the award will support the development of environmentally-friendly protein alternatives with the aim to "feed the next billion".
Image from: Madar Farms
Global Challenges, Local Solutions
Food security is far from the only global challenge on the emirate’s R&D menu. In November 2020, the ATRC announced the launch of the Technology Innovation Institute (TII), created to support applied research on the key priorities of quantum research, autonomous robotics, cryptography, advanced materials, digital security, directed energy and secure systems.
“The technologies under development at TII are not randomly selected,” explains the centre’s secretary general Faisal Al Bannai. “This research will complement fields that are of national importance. Quantum technologies and cryptography are crucial for protecting critical infrastructure, for example, while directed energy research has use-cases in healthcare. But beyond this, the technologies and research of TII will have global impact.”
Future research directions will be developed by the ATRC’s ASPIRE pillar, in collaboration with stakeholders from across a diverse range of industry sectors.
“ASPIRE defines the problem, sets milestones, and monitors the progress of the projects,” Al Bannai says. “It will also make impactful decisions related to the selection of research partners and the allocation of funding, to ensure that their R&D priorities align with Abu Dhabi and the UAE's broader development goals.”
Image from: Agritecture
Nurturing Next-Generation Talent
To address these challenges, ATRC’s first initiative is a talent development programme, NexTech, which has begun the recruitment of 125 local researchers, who will work across 31 projects in collaboration with 23 world-leading research centres.
Alongside universities and research institutes from across the US, the UK, Europe and South America, these partners include Abu Dhabi’s own Khalifa University, and Mohamed bin Zayed University of Artificial Intelligence, the world’s first graduate-level institute focused on artificial intelligence.
“Our aim is to up skill the researchers by allowing them to work across various disciplines in collaboration with world-renowned experts,” Al Bannai says.
Beyond academic collaborators, TII is also working with a number of industry partners, such as hyperloop technology company, Virgin Hyperloop. Such industry collaborations, Al Bannai points out, are essential to ensuring that TII research directly tackles relevant problems and has a smooth path to commercial impact in order to fuel job creation across the UAE.
“By engaging with top global talent, universities and research institutions and industry players, TII connects an intellectual community,” he says. “This reinforces Abu Dhabi and the UAE’s status as a global hub for innovation and contributes to the broader development of the knowledge-based economy.”
US - OHIO: Thinking And Growing Inside The Box
A brother-sister team has taken the mechanics of farming out of the field and into a freight container. “We are growing beautiful plants without the sun; there’s no soil, and so it’s all a closed-loop water system,” Britt Decker, co-owner of Fifth Season FARM, said
A brother-sister team has taken the mechanics of farming out of the field and into a freight container.
“We are growing beautiful plants without the sun; there’s no soil, and so it’s all a closed-loop water system,” Britt Decker, co-owner of Fifth Season FARM, said. “We use non-GMO seeds, completely free of herbicides and pesticides, so the product is really, really clean. In fact, we recommend people don’t even wash it, because there’s no reason to.”
Fifth Season FARM is unique in many ways; the 3-acre hydroponic farm is contained in a 320-square-foot freight container that sits along 120 S. Main St. in Piqua, with everything from varying varities of lettuce, to radishes, to kale and even flowers in a climate-controlled smart farm that allows Decker and his sister, Laura Jackson, to turn crops in a six- to eight-week cycle. The crops spend 18 hours in “daytime” every day, and the farm uses 90% less water than traditional farming.
“It’s tricky because we’re completely controlling the environment in here. It’s kind of a laboratory more than a farm,” Decker said. “I think there’s about 50 of them around the world right now. These are really international, and they’re perfect for places that are food deserts where they can’t grow food because of climate or other reasons. It gives them a way to grow food in the middle of nowhere.”
Image from: Sidney Daily News
Decker and Jackson, along with their brother Bill Decker, also do traditional farming and grow corn, wheat and soybeans, but Decker said they were looking for a new venture that would help lead them to a healthier lifestyle and learn something new.
“Just with the whole local food movement becoming more and more important and food traceability, we just thought it would be a great thing to bring to our community to help everyone have a healthier lifestyle,” Decker said. “People love food that’s grown right in their hometown and the shelf-life on it, when you get it home, is remarkable. It’ll keep for two weeks.”
Image from: AgFunder News
Currently, Decker and Jackson are growing a half-dozen variety of specialty lettuces that include arugula, butterhead and romaine, as well as specialty greens like kale and Swiss chard, and even radishes and flowers. They received their freight container at the end of July and set up their indoor farm over two weeks; while the farm has been in operation for less than six months, Decker says that they’re growing beautiful product.
They have also started growing micro-greens, said Decker. Micro-greens are immature plants which are 1 to 3 inches tall and are in a 5-inch by 5-inch container.
“People will use them as garnishments and in smoothies,” said Decker. “Since they are immature plants, they have an intense flavor.”
Decker said they are growing wheat germ, broccoli and spicy salad mixes.
They’ve also started moving forward with sales and marketing. Fifth Season FARM has partnered with the Miami County Locally Grown Virtual Market to sell their products to the community. They also take orders through their website, customers can opt to pick up their orders between 4 and 6 p.m. on Wednesdays, or Decker and Jackson will deliver products up to five miles from the farm. Decker said that Fifth Season FARM is also in discussions with three restaurants in the area about including their specialty greens on their menus.
Decker said they also plan to attend the Sidney Farmers Market when it opens for the spring/summer season.
“We’re really just getting going,” Decker said. “While we were learning to grow products, we didn’t want to overcommit to a restaurant or grocery store before we knew we could really grow beautiful product, so we’ve been donating product every week to the food pantry at the Presbyterian Church. It feels good to plant the seeds and watch them grow, and it feels good to make sure that people who aren’t getting the proper nutrition are getting some.”
Is AppHarvest the Future of Farming?
In this video from Motley Fool Live, recorded on Jan. 28, Industry Focus host Nick Sciple and Motley Fool contributor Lou Whiteman discuss AppHarvest, one such SPAC that is looking to disrupt the agriculture industry. Here are the details on what AppHarvest wants to do, and a look at whether the company represents the future of farming.
Special purpose acquisition companies, or SPACs, are red-hot right now, with investors clamoring to get into promising young companies.
In this video from Motley Fool Live, recorded on Jan. 28, Industry Focus host Nick Sciple and Motley Fool contributor Lou Whiteman discuss AppHarvest, one such SPAC that is looking to disrupt the agriculture industry. Here are the details on what AppHarvest wants to do, and a look at whether the company represents the future of farming.
Nick Sciple: One last company I wanted to talk about, Lou, and this is one I think it's -- you pay attention to, but not one I'm super excited to run in and buy. It was a company called AppHarvest. It's coming public via a [SPAC] this year. This vertical farming space. We talked about Gladstone Land buying traditional farmland. AppHarvest is taking a very different approach, trying to lean into some of the ESG-type movements.
Lou Whiteman: Yeah. Let's look at this. It probably wouldn't surprise you that the U.S. is the biggest global farm exporter as we said, but it might surprise you that the Netherlands, the tiny little country, is No. 2. The way they do that is tech: Greenhouse farm structure. AppHarvest has taken that model and brought it to the U.S. They have, I believe, three farms in Appalachia. The pitches can produce 30x the yields using 90% less water. Right now, it's mostly tomatoes and it is early-stage. I don't own this stock either. I love this idea. There's some reasons that I'm not buying in right now that we can get into. But this is fascinating to me. We talked about making the world a better place. This is the company that we need to be successful to make the world a better place. The warning on it is that it is a SPAC. So it's not public yet. Right now, I believe N-O-V-S. That deal should close soon. [Editor's note: The deal has since closed.] I'm not the only one excited about it. I tend not to like to buy IPOs and new companies anyway. I think the caution around buying into the excitement applies here. There is a Martha Stewart video on their website talking up the company, which I love Martha Stewart, but that's a hype level that makes me want to just watch and see what they produce. This is just three little farms in Appalachia right now and a great idea. This was all over my watchlist. I would imagine I would love to hold it at some point, but just be careful because this is, as we saw SPACs last year in other areas, people are very excited about this.
Sciple: Yeah. I think, like we've said, for a lot of these companies, the prospects are great. I think when you look at the reduced water usage, better, environmentally friendly, all those sorts of things. I like that they are in Appalachia. As someone who is from the South, I like it when more rural areas get some people actually investing money there. But again, there's a lot of execution between now and really getting to a place where this is the future of farming and they're going to reach scale and all those sorts of things. But this is a company I'm definitely going to have my radar on and pay attention to as they continue to report earnings. Because you can tell yourself a story about how this type of vertical farming, indoor farming disrupts this traditional model, can be more efficient, cleaner, etc. Something to continue paying attention to as we have more information, because this company, like you said, Lou, isn't all the way public yet. We still got to have this SPAC deal finalized and then we get all our fun SEC filings and quarterly calls and all those sorts of things. Once we have that, I will be very much looking forward to seeing what the company has to say.
Whiteman: Right. Just to finish up along too, the interesting thing here is that it is a proven concept because it has worked elsewhere. The downside of that is that it needed to work there. Netherlands just doesn't have -- and this is an expensive proposition to get started, to get going. There's potential there, but in a country blessed with almost seemingly unlimited farmland for now, for long term it makes sense. But in the short term, it could be a hard thing to really get up and running. I think you're right, just one to watch.
(Assistant) Professor Crop Modelling In Greenhouses And Vertical Farms (Tenure Track)
Are you keen to contribute to the sustainable production of healthy fresh vegetables? We have a vacancy for an Assistant professor of Crop modelling in Greenhouses and vertical farms. Do you like to supervise students? Do you want to combine modelling and data analytics with plant experimentations? Then this position could be a perfect fit for you!
The chair group Horticulture and Product Physiology of Wageningen University & Research (WUR) is keen to hire an Assistant Professor (0.7-1.0 ft). As an Assistant Professor, you will take a leading role in developing research and education and the opportunity to establish your own research and education in crop modeling in greenhouses and vertical farms.
This position also involves experimental physiological work at the plant organ, whole plant or whole crop level, which is necessary to build, calibrate and validate models.
In this challenging career trajectory:
You will perform research on modeling, combined with experimentation, of growth, development, and quality of horticultural crops and products (vegetables, fruits, cut flowers, and/or pot plants).
You acquire, lead and implement together with the chair holder and other staff members innovative and creative (inter-)national research projects for our group. Once acquired you also implement and lead these projects.
You supervise Ph.D., MSc, and BSc students, and you will develop and teach courses (lectures, practicals) on the modeling of key plant processes in greenhouses and vertical farms.
Your work will focus on the development of models, which are a combination of multiscale Spatio-temporal data-driven, as well as knowledge-based models. Model applications may include predictions of yield, plant development and growth, quality, post-harvest behavior, resource use and running costs for crops grown in greenhouses and vertical farms
You collaborate with colleagues and establish a personal research portfolio that is embedded in the Horticulture and Product Physiology group
You undertake research on modeling and data analytics, combined with experimentation, that leads to high-quality research output.
You will perform research on modeling, combined with experimentation, of growth, development, and quality of horticultural crops and products (vegetables, fruits, cut flowers, and/or pot plants).
Tenure Track is a career path for scientists who pursue to excel in education and research. We seek to attract scientific talent and to stimulate and support their development.
Requirements:
You hold a Ph.D. degree in plant science, mathematical science, biological science, data science, or similar.
You have experience in modeling and data analytics, as well as a keen interest in combining these activities with experimentation with plants.
You have published research in high-quality journals and are willing to develop your skills in teaching and grant proposal acquisition.
You are strong in stakeholder management because you need to communicate the importance and significance of your research.
This position requires excellent English language proficiency (a minimum of CEFR C2 level). For more information about this proficiency level, please visit our special language page.
The chair group Horticulture & Product Physiology
The chair group Horticulture and Product Physiology conduct high impact research and educate students providing the scientific basis required to answer questions that are of utmost importance for sustainable crop production and product quality in horticulture.
The research focus is on how physiological processes in crops, plants, and plant organs interact with the abiotic environment and how this affects crop production and product quality. Questions arising from horticultural practice are translated into fundamental research topics, aiming to explain mechanisms. The research and education contribute to sustainably feeding the World with healthy high-quality products.
The chair group is an international team consisting of 15 permanent staff members, about 25 Ph.D. candidates and postdocs, and a number of guest researchers. Each year about 40 MSc students conduct their thesis study (6-month research) at our group. We organize and participate in a variety of courses for BSc and MSc students to transfer knowledge on horticulture (pre-and post-harvest), environmental physiology, and product quality.
More info about the chair group can be found at www.hpp.wur.nl or see the video below:
Salary Benefits:
Wageningen University & Research offers excellent terms of employment. A few highlights from our Collective Labour Agreement:
sabbatical leave, study leave, and paid parental leave;
working hours that can be discussed and arranged so that they allow for the best possible work-life balance;
the option to accrue additional flexible hours by working more, up to 40 hours per week;
there is a strong focus on vitality and you can make use of the sports facilities available on campus for a small fee;
a fixed December bonus of 8.3%;
excellent ABP pension regulations.
In addition to these first-rate employee benefits, you will be offered a fixed-term, 7-year contract which, upon positive evaluation based on criteria elaborated in the University's Tenure Track policy, can lead to a permanent employment contract as a professor. Depending on your experience, we offer a competitive salary of between € 3.746,- and € 5.127,- (assistant professor position) for a full-time working week of 38 hours in accordance with the Collective Labour Agreements for Dutch Universities (CAO-NU) (scale 11). The position can be part-time or full-time (0.7-1.0 ft).
Wageningen University & Research encourages internal advancement opportunities and mobility with an internal recruitment policy. There are plenty of options for personal initiative in a learning environment, and we provide excellent training opportunities. We are offering a unique position in an international environment with a pleasant and open working atmosphere.
You are going to work at the greenest and most innovative campus in Holland, and at a university that has been chosen as the "Best University" in the Netherlands for the 16th consecutive time.
Coming from abroad
Wageningen University & Research is the university and research center for life sciences. The themes we deal with are relevant to everyone around the world and Wageningen, therefore, has a large international community and a lot to offer to international employees. Applicants from abroad moving to the Netherlands may qualify for special tax relief, known as the 30% ruling. Our team of advisors on Dutch immigration procedures will help you with the visa application procedures for yourself and, if applicable, for your family.
Feeling welcome also has everything to do with being well informed. Wageningen University & Research's International Community page contains practical information about what we can do to support international employees and students coming to Wageningen. Furthermore, we can assist you with any additional advice and information about helping your partner to find a job, housing, schooling, and other issues.
Work Hours: 38 hours per week
Address: Droevendaalsesteeg
This Startup Wants Vertical Farmers To Hire A Robot Gardener
“By automating the production with robotics and remote monitoring, we can lower labor costs and offer solutions for food producers that are economically viable and environmentally sustainable,” the company claims on their website.
Arugula micro greens are grown at AeroFarms on February 19, 2019, in Newark, New Jersey.
Photo: Photo by Angela Weiss (Getty Images)
In recent years, vertical farming has emerged as a futurist’s solution to the world’s agricultural problems. The growing trend seeks to use controlled environments to boost food production, leveraging indoor labs where temperature, light, and nutrients can be mechanically controlled.
Yet while vertical farms have gained in popularity, they are also still very expensive. When compared to conventional farming, these farms necessitate the purchase of pricey equipment to aid human labor—a fact that, when paired with other economic pressures, has apparently led to an industry “littered with bankruptcies.”
One company hopes to change this dire picture. Enter Watney the robot.
Watney was designed by start-up Seasony. The company, which was featured today at this year’s Alchemist Accelerator’s Demo Day, has sought to make the tech-farming trend more accessible by automating away some of the more difficult labor involved.
Image: Screenshot: Youtube/TV2LORRY
“By automating the production with robotics and remote monitoring, we can lower labor costs and offer solutions for food producers that is economically viable and environmentally sustainable,” the company claims on their website.
Indeed, Watney is designed to augment (and, in many ways, replace) a human labor force—currently one of the biggest expenditures for vertical farms. Essentially an intelligent, automated cart, the robot was designed to “move and transport plant trays” within a farming hub. In techno-jargon, it is an autonomous mobile manipulation robot (AMMR), a type of machine known for moving and manipulating items on its own. It is also equipped with a camera that captures image data and sends it back to farm management software for human analysis. Watney also gathers valuable horticultural data to help farmers optimize yields, said Christopher Weis Thomasen, Seasony’s CEO and Co-Founder, in an email.
From left to right: Erkan Tosti Taskiran, Servet Coskun and Christopher Weis Thomasen.
Photo: Photo from Seasony.
“We are doing for vertical farming what the integration of autonomous mobile robots did to amazon. We are able to decrease the costs of growing food in a vertical farm by alleviating the logistics pains of working from scissor lifts,” said Thomasen.
Thomasen, a mechanical engineer, and his two co-founders electrical engineer Servet Coskun and business specialist Erkan Tosti Taskiran, were inspired to create the business while brainstorming what it would take to sustain life in outer space (Watney the robot is named after Mark Watney, the astronaut in the movie The Martian, who, after being stranded on the Red Planet, fertilizes potatoes with his own poop to survive).
“It quickly evolved to Seasony setting up a vertical farming lab and exploring the technical challenges facing the new industry. Reducing the costs related to labor is key in order to scale vertical farming and make agriculture more sustainable,” Thomasen said.
There is, of course, some debate in the farming community about the social costs incurred through the large-scale displacement of human labor.
Presumably, we will have to wait to see what that cost-saving process looks like. Seasony, which is still getting off the ground, plans to do a pilot trial with the largest vertical farm in Europe in April. It has plans to conduct further testing with several smaller vertical farms, as well, Thomasen said.
Lucas Ropek
Staff writer at Gizmodo
VIDEO: Potato Seeds Made Without Soil With Little Help From Peru
Scientists say that in aeroponics technique, potato seeds are grown in mist environment. Potato seeds grown through this technology are free from soil-borne diseases. Potato Technology Centre has established three units which have the capacity to grow 10 lakh minitubers
Parveen Arora
Potato Technology Centre, (PTC) Shamgarh, in the district in collaboration with Central Potato Research Institute (CPRI) in Shimla and International Potato Centre (CIP), Peru, has started producing potato seeds in the air with the help of aeroponic technique.
Scientists show a potato breed at Potato Technology Centre at Shamgarh village in Karnal district. Sayeed Ahmed
In this technique, there is no need for soil and other growing media like coco-peat for production. The scientists say that in aeroponics technique, potato seeds are grown in mist environment. They claim potato seeds grown through this technology are free from soil-borne diseases.
“We have started the process of growing minituber (potato seed) plants with the help of aeroponic technique. It is the latest technique for growing plants and potato seed production in an air or mist environment. There is no need for soil and this technology is free from soil-borne diseases,” said Dr Prem Chand Sindhu, Deputy Director, PTC, Shamgarh.
He maintained that they have established three units which have the capacity to grow 10 lakh minitubers in one crop cycle which is for three months. The scientists claimed that the production of seeds through this technique is much higher than conventional methods.
Dr Manish Sainger, the senior consultant at PTC, said that on an average, 30 minitubers and maximum 50-60 minitubers can be obtained from each plant. He said that through this technique, 7-10 times more minitubers can be obtained in comparison to conventional methods like net-house or open field.
About the technology, Dr Sainger said they planted tissue culture plants in the grow chambers which have pipes and nozzles for mist spray on the roots of the plant. “The roots of the plant hang in the air in the chamber and all the nutrients are provided through the mist, which consists of all the required elements for plant growth and tuberisation, periodically. The upper part of plant remains at the top of the chamber,” he added. He said that the size of minitubers is uniform at 3-4 gm.
Dr Sainger said it is easy to transport minitubers at minimal cost. “These seeds will be given to growers at subsidised rates by the Department of Horticulture. Later, seed growers will cultivate these seeds in the soil for the multiplication of seeds.”
WayBeyond Appoints Head of Industry Transformation to Drive Sustainability Agenda
“…ensuring we deliver on the United Nations Sustainable Development Goals and formalizing and extending the work we have been doing on industry education, connecting the eco-system and our own graduate and internship program,” says CEO & Founder Darryn Keiller.
WayBeyond’s vision is to transform the agricultural industry. This is a declaration of intent and to give this intent focus and leadership, Kylie Horomia has been appointed into a new role as Head of Industry Transformation. Ms. Horomia holds a Masters in International Communications, 20 years in communications and almost 10 years in the Horticulture industry, most notably with T&G Global and recently with Autogrow where she was Head of Brand & Communications.
“Kylie is a passionate and respected communications specialist and industry advocate, who has provided the next level of thinking around our story and will begin working on our long-term global sustainability strategy. This includes ensuring we deliver on the United Nations Sustainable Development Goals and formalizing and extending the work we have been doing on industry education, connecting the eco-system and our own graduate and internship program,” says CEO & Founder Darryn Keiller.
The key to the transformation of anything is the transformation from the inside. In the context of agtech, this means ushering in a new generation of farmers, scientists, and technologists. Addressing Zero Hunger (including reduction of waste), Clean Water & Sanitation, Sustainable Cities, and the evolution of Industry, Innovation, and Infrastructure; will take creativity and collaboration.
“With our WayBeyond team based in New Zealand, the Netherlands, and United States and employees from 15 cultures; we celebrate our diversity, which critically includes the diversity of thinking required to solve the world’s greatest food production challenges," explains Mr. Keiller.
Ms. Horomia is also on the Executive Board of the NZ Guild of Agricultural Journalists and Communicators and worked to develop the Global CEA Census alongside New York-based industry partner Agritecture Consulting.
“I’m very excited about this new opportunity. AgTech is an amazingly fast-paced industry to be in and the work we are doing to grow food sustainably using science and technology is something of which I am incredibly proud. I will continue to promote the inclusion of STEM disciplines to reduce food waste, increase the efficiency of natural resources, and make a positive impact on growers, the environment and communities we operate within,” says Ms Horomia.
Ms Horomia will take up the role effective immediately.
To learn more about WayBeyond and follow Kylie’s transformation of the brand, please go to www.waybeyond.io
For further information, interviews and images, please contact
Kathy Cunningham
(e) kathy@empirepr.co.nz
(m) +6421 743 378
About WayBeyond
The WayBeyond Vision is to transform the agricultural industry to produce food sustainably for everyone on the planet.
The Mission is to break boundaries to explore new ways of farming so our solutions benefit every farm in the world (and beyond). This includes sharing knowledge and expertise with data, artificial intelligence, and plant science to transform the way growers farm. www.waybeyond.io
Which Type Of Hydroponic System Is Better?
So why do I answer, “it all depends”?
Hint: They are all just irrigation systems.
One of the questions that I get most frequently is, “Which hydroponic system is the best?”
I am fairly sure that my standard answer of, “it all depends” annoys most of the people I am speaking to. From suppliers to growers and from researchers to hobbyists there is always a desire to know and understand which system is the best.
So why do I answer, “it all depends”?
Whether we are talking about nutrient film technique (NFT), deep water culture (DWC), drip irrigation systems, aeroponics systems, ebb and flow systems, or any other system we should agree that these are all just variations of irrigation systems.
Buffer capacity means security. Buffer capacity means you can leave for a day without fear of losing the crop.
Next let’s talk about the systems suppliers and their sales representatives. Suppliers of hydroponic systems will all tell you why theirs is better, but the conversation should really revolve around what factors cause their systems to fail. Every system has a weakness. Your crop, your budget, your facility and your geographic location will likely quickly highlight these weaknesses.
A large variety of hydroponic systems all at once – Big Tex Urban Farms
So, how do you determine what system is best for you?
Here are the things you should know, think about and research thoroughly before you invest.
What crop are you going to grow? If you are planning to grow tomatoes, it’s very unlikely that you will want to invest in a nft system or a dwc system. The needs of your crop will help direct you into the right direction. Likewise, a closed loop drip irrigation system is unlikely to be the answer for lettuce production.
Know your budget. Your budget will play a major role in this decision making process. Do not only think about the upfront costs of the system. Make sure to include the operational and labor costs associated with running the system 7 days a week 365 days per year.
Know your environment. Each crop type will respond to these 9 environmental variables (see diagram) in different ways. As a grower your ability to manage these variables will be a primary indicator of your ability to achieve your target yields. The irrigation systems primary function is to help you control the 4 variables surrounding the root zone (see diagram 0.0 to understand the variables.) Your geographic location and crop will determine which of these variables are most important.
Truly understand the design. In the recent Urban Ag News article, “Important Tips For Designing A Hydroponic Production Facility” I discussed the importance of buffer capacity. Buffer capacity in your irrigation system plays some very important roles. First, it will help you manage your nutrients. Second, it will help your crop deal with variations in temperature. Third and most importantly, it will be a primary indicator of how much time you can spend away from your farm.
Figure out your maintenance and spare parts plan. Irrigation systems break. Irrigation systems get clogged. Irrigation systems need to be serviced and fixed. Make sure you understand everything from how to access the most vulnerable and weak parts of the system to how long it will take you to get replacement parts and what parts you should plan to carry in case of an emergency. Think about redundancy!
Labor is KEY! Consider every aspect of labor. From the education requirements of running the labor, to the amount of labor needed to operate and maintain the system to the importance of labor needed to check on the system on a regular basis.
Budget • Scale • Access
Which brings me back to where we started. Which hydroponic system is the best? It truly all depends. All we know for sure is that if a supplier tells you, “you can grow every crop in our system”, be concerned. It might be true, but I can almost guarantee you that you cannot grow every crop profitably in their system. If a supplier struggles to help you clearly understand and answer the questions posed in this article, look for a new supplier. There are plenty that will.
Finally, focus on building a professional network with experience in the commercial hydroponics industries. Ask lots of questions and understand the full benefits and limitations of any system you choose.
Final hint: Aquaponics growers use one of these systems as well.
“Sharing Technology Is The Only Way The Industry Will Grow”
Lack of this might lead to farmers being susceptible to misleading information, using ineffective technologies, which I’ve seen many people suffering from.
“There is a lack of know-how amongst farmers to apply those techniques in a successful way,” says Joe Swartz, Vice president and Lead horticulturalists at AmHydro. In every situation, according to Joe, from geography to the skill of the grower or climate control, all play into what types of technology should be used. This requires a lot of experience and knowledge. Lack of this might lead to farmers being susceptible to misleading information, using ineffective technologies, which I’ve seen many people suffering from.
Joe adds, “Watching many good growers that have been led down a bad path in the industry, while investing so much into technologies that are not really effective, really breaks my heart. While providers know that they aren’t effective in this particular situation. With many years of industry experience, Joe is well aware of the challenges that the industry faces these days. Within the aquaponics sector there is not one singular technology, just as in conventional farming, rather various unique technologies can be combined for different outcomes.
Lack of know-how
When asked about the kind of growers that Joe educates, he notes that there are two kinds of growers contacting him. “We have two types of growers: either growers facing challenges or new growers wanting equipment and knowledge. Both of those approaches are interesting and it’s great to be able to help them become successful. It is great to see our system helping companies to grow and develop and become a worldwide provider. Growers like that keep coming back to us. They are the ones that move the industry”.
Joe Swartz, Vice president
An essential part of being a vertical farmer, in Joe’s opinion, is having experience with working on the ground floor. Only this will teach you what it takes to manage the equipment, crops and technology. “The best growers have started in the greenhouse. Hydro-experts will get nowhere with their college degree alone,” Joe states. For that reason, AmHydro offers grower seminars and even possesses a commercial greenhouse where growers can work in order to gain experience. “Some growers don’t think that they need it as they rely on technology, but my experience is exactly the opposite.”
Fake promises
Joe observes similar trends as in the 1980s when certain technologies were promoted as ‘the farming of the future’. People talked about automatic farming, in which no farmer would be needed, new techniques and new lightings. All things we hear today were said back then. What happened afterward, according to Joe, was that some techniques turned out disappointing. Millions of dollars invested were lost, leading to the industry losing its credibility.
“As a result, investors only valid projects that already have a positive cash flow, as they have become more cautious. Some growers struggled to get funding, even though they had a viable business model. In a certain way, negative events have closed off some appetite for investments in CEA, which is a shame. It is a good investment in general, but every time we see a less than a reputable company or a technology that fails, it holds the industry back.”
Misconception
Related to that, Joe says that vertical farming still has to overcome a somewhat negative public image. “The traditional consumer, at least in the USA, have an image of farmers working on the land using sustainable methods. Now, being a conventional farmer using hydroponics I know that it is a sustainable and safe way to produce food, but there’s a public perception of automatization, as robotic food. Some people even call it “Frankenfood”. In my opinion, the more we can promote CEA as what it is, sustainable growing techniques, people will be more accepting and investors will invest more easily”.
Joe strongly senses that the vertical farming industry needs more skilled farmers and growers to meet the demand. “A lot of my work is actually training people. We want to help especially young people, new to the industry, by giving them skills, experience and knowledge. I have been blessed to have mentors when I was young and I try my best to pass that knowledge as this will help the industry along. That’s one of the reasons why we now see some consultancy firms who see economic opportunities. Sharing technology is the only way in which the industry will grow,” says Joe.
“Despite the diversity amongst growers that I meet in over 66 countries, all growers face similar problems. Funny tech flitches, pipes that break and spray water all over the greenhouse, or water pumps that break down. It doesn’t matter whether it’s a technologically advanced greenhouse or a small low-tech one. It kind of goes across the board,” says Joe laughing.
For more information:
AmHydro
Joe Swartz, Vice president and Lead horticulturalist
joe@amhydro.com
www.amhydro.com
Author: Rebekka Boekhout
© VerticalFarmDaily.com
Join Us For Global G.A.P. World Consultation Tour - Focused On Controlled Environment Agriculture (CEA)
Join the upcoming virtual meeting on January 25, 2021 13:00-14:30 EST
The GLOBAL G.A.P. World Consultation Tour goes into its second round! Join the upcoming virtual meeting on January 25, 2021 13:00-14:30 EST in collaboration with the Farm Tech Society. Together, we aim to deliver an impactful standard in line with producers’ practices. The unique challenges presented by vertical farming or produce grown in controlled environments will be addressed to ensure an appropriate user experience.
High-tech monitoring and control systems in commercial controlled environment agriculture farms and their supply chains enable the opportunity to capture automated measurements, support assessment and analyze a wide range of variables including water to energy to inputs, reducing costs and adding value for individual farms and across the industry. The ultimate goal of the partnership is the development and implementation of an impactful standard and certification process.
Participants will meet the expert working group behind the standard revision, and will have the opportunity to join the ongoing discussion and process.
About FTS:
The Farm Tech Society (FTS) is an international non-profit industry association that unites and supports the Controlled Environment Agriculture (CEA) industry, seeking to strengthen the sector through the development and implementation of resilient and future proof methods and technologies for indoor growing. The FarmTech Society is enlisted in the EU Transparency Register with #469686733585-87
About GLOBAL G.A.P.:
GLOBAL G.A.P. is a leading global certification program whose mission is to bring farmers and retailers together to produce and market safe food, to protect scarce resources, and to build a sustainable future.
Join the FarmTech Society in 2021
The Farm Tech Society (FTS) is an international non-profit industry association that unites and supports the Controlled Environment Agriculture (CEA) industry, seeking to strengthen the sector through the development and implementation of resilient and future proof methods and technologies for indoor growing. We look forward to continuing to grow and drive #CEA4CriticalChallenges with members like you.
Growing Smart And Sustainable
The industry has received much more attention this year, which has motivated the interest in sustainability. There is more focus on the sustainability of a farm, alongside its profitability and the validity of a system.
“The industry has received much more attention this year, which has motivated the interest in sustainability. There is more focus on the sustainability of a farm, alongside with its profitability and the validity of a system,” Michael says.
Michael Martin is a researcher at the IVL Swedish Environmental Research Institute and KTH Royal Institute of Technology, focusing on sustainability and industrial ecology. Michael has been researching the sustainability of vertical farming systems for a few years now. Currently, he leads a number of projects on the subject, collaborating with many of the Swedish system developers.
Michael Martin
“I think that there’s a discourse used to promote or motivate why vertical farms are there. They’re often related to the reduction of water, transport, and so on, but there are also a large number of critics cherry-picking some of the more obvious potential drawbacks of the systems,” Michael affirms.
Carbon footprint and energy
For impacts related to energy, Michael states that it really depends on where a grower is located. Where energy use is key, for e.g. LED lighting, Northern European countries have great preconditions, with lower carbon energy sources and a supply of district heating. A large share of [district] heating in Northern European countries derives from the incineration of waste and biomass.
Most vertical farms are found in, or in close proximity to, urban areas, in residual spaces, meaning that they have access to heat. However, as these farms have stable ambient temperatures they don’t need much heat, and options for cooling are sometimes more important.
However, sometimes there’s too much excess heat in the building, which then needs cooling. “We have been looking into the interplay of the building and the farming system, plus the synergy of it. ‘What are the possibilities of heating a building with LEDs waste heat?’ There is potential for integrating the systems to the neighborhood so that the residuals, biofertilizers, waste heat and so can all be used to reduce wastes and improve resource efficiency through symbiotic development."
Smart growing and automation
Taking lighting conditions, for instance, by creating the optimal conditions for plants to grow. Typically one recipe is used for lighting and nutrients. But when allowing different optimizations through smart technology, everything can be monitored in terms of nutrients and water, etc. By being hands-on with the growing processes, resource consumption can be reduced.
There are new types of systems that are coming with a greater focus on product-service systems such as FAAS, i.e. selling functions and services instead of products. "I think that in terms of technology we can really make farms more sustainable. Automation and optimization of growing conditions can create large potential resource consumption improvements and optimize growing conditions."
For more information:
IVL Swedish Environmental Research Institute and KTH Royal Institute of Technology
Michael Martin
michael.martin@ivl.se
Publication date: Tue 15 Dec 2020
Author: Rebekka Boekhout
© VerticalFarmDaily.com
Hydroponic Farms Use Less Land, Water To Grow Vegetables
Growing lettuce and other leafy greens indoors is gaining traction nationwide, as such big players as New Jersey-based Aero Farms and Bowery, are producing huge quantities in giant warehouses fueled by millions of dollars in investment
By Susan Salisbury For The Palm Beach Post
August 12, 2019
Green Life Farms’ hydroponic greenhouse occupies nearly 3 acres. It expects to yield 750,000 pounds of premium leaf green produce throughout the year, said Mike Ferree, vice president. The greens are grown, harvested and packaged onsite. [CONTRIBUTED BY HYDRONOV}
Greenhouses Allow Year-Round Growing
And Protection From Freezes And Extreme Rainfall.
Growing lettuce and other leafy greens indoors is gaining traction nationwide, as such big players as New Jersey-based Aero Farms and Bowery, are producing huge quantities in giant warehouses fueled by millions of dollars in investment.
The push comes as farmland becomes increasingly expensive and in short supply, and consumers demand locally grown produce that’s fresher because it hasn’t been transported hundreds of miles.
In Palm Beach County two new hydroponic farms—Green Life Farms and Patagonia Green Leaf— are being launched in greenhouses off U.S. 441 west of the Lake Worth Beach/Boynton Beach area. Hydroponic farming uses no soil. Instead, crops are grown in perlite, coconut fiber or nutrient-rich water in a controlled and enclosed environment.
Art Kirstein, agricultural economic development coordinator with the Palm Beach County Cooperative Extension Service, said that hydroponic farming offers advantages such as year-round growing, increased capacity on a smaller amount of land and protection from freezes and weather events such as extreme rainfall.
Green Life Farms harvested its first crop of baby arugula, baby romaine and baby spinach in mid-July. Its greenhouse occupies nearly 3 acres and will yield approximately 750,000 pounds of premium leaf green produce throughout the year, said Mike Ferree, vice president.
Baby romaine lettuce grows in the Green Life Farms hydroponic greenhouse off U.S. 441 west of Lake Worth Beach. The company has spent $15 million on the facility.
The greens are grown, harvested and packaged onsite, then picked up or shipped directly from the farm. They are also GMO and pesticide-free.
Green Life’s head grower, Greg Graft, said the produce is mechanically harvested using an automated system.
The first crop is not available for sale. Once Green Life begins official commercial production, products will be available at local grocery stores, restaurants and other locations, Graft said.
Green Life chose Palm Beach County for its large consumer market, proximity to sales partners and an agriculture-friendly environment, Graft said. It has invested $15 million so far.
Green Life uses a deep-water floating raft technology from Hydronov, an Ashley, Ind.-based leader in the hydroponic industry with more than 30 years of experience.
The floating raft system helps to conserve water, using the oxygenated clean water in which the plants grow as a conveyor system. Green Life will be able to produce 18 harvests each year and use 90 percent less water than conventional farming.
Patagonia Green Leaf, about a mile south of Green Life, is a hydroponic farm on a former plant nursery. It’s owned by the Canosa family. They’ve farmed in the traditional way in Argentina for 10 years.
The first phase of 10 greenhouses totaling 30,000 square feet is completed. The initial crop of baby greens will be planted soon, with harvesting expected by late September.
“The idea is to harvest and deliver the product within 24 hours,” said Juan Ignacio Canosa, who lives in Boca Raton.
After visiting Miami and Fort Lauderdale on vacations, the family started coming to Boca Raton. Last year they bought 5 acres from Boynton Botanicals, whose owner was retiring.
Plants will be grown pesticide-free using a system known as NFT, (nutrient film technique) from Arcata, Calif.-based AmHydro. A pump delivers fertilized water to the growing trays, flows over the plants’ roots, then drains back into the reservoir and is recycled.
Robert Hochmuth, regional extension agent with the University of Florida’s North Florida Research and Education Center, said since the early 2000s, the number of acres of produce grown in greenhouses and other structures in Florida has increased five-fold to more than 500 acres.
Producing in protected structures extends the season and reduces insects and diseases, Hochmuth said.
“You can be a consistent supplier in the marketplace over a long period of time,” Hochmuth said.
Most of the hydroponic farms in Florida are less than an acre and tend to cater to local markets.
Hochmuth said hydroponic growing is attracting people who are new to farming.
“Because they are going with high-value specialty crops, the likelihood of profitability makes sense,” Hochmuth said.
Of course, greenhouses and other facilities are at risk of being destroyed during hurricanes or high winds. Hochmuth advises removing the plastic from the structures prior to storms because it acts as a sail.
Hydroponic farming isn’t new to Palm Beach County. Walter Ross founded Farmhouse Tomatoes west of Lake Worth in 1996 and grows heirloom tomatoes in 160,000-square-feet of greenhouses from Nov. 1 through June 30.
Plant Factory With Artificial Lighting: Toyoki Kozai's Brilliant Research On An Interesting Practice
According to AgriGarden, 'Plant factory is a highly efficient agriculture system which uses high precision control facilities in the continuous production of crops."
1/9/2019 9:16:19 AM
(MENAFN - GetNews) Dr. Toyoki Kozai's research work is on ' Opportunities and Challenges for Plant Factory with Artificial Lighting (PFAL) (or vertical/indoor farming). Dr Kozai graduated from Chiba University, Japan in 1967. He obtained a Master's degree in 1969, and a PhD degree of Agricultural Engineering in 1972 from the University of Tokyo in 1972. He served as Dean of Faculty of Horticulture and Director of Center for Environment, Health and Field Sciences of Chiba University. He was inaugurated as the President of the prestigious Chiba University in 2005. He resumed his career in research as a professor emeritus in an endowed chair position at the Center for Environment, Health and Field Sciences during 2009-2012. He established Japan Plant Factory Association (non-profit organization) in 2010 together with his colleague, and served as the president until 2018, and is serving as the honorary president to date.
Furthermore, Kozai's academic excellence and his scientific interest can be gauged from the multiple books he has written, namely, 'Smart Plant Factory: The next generation indoor vertical farms (2018), 'LED Lighting for Urban Agriculture (2016), 'Plant Factory: An indoor vertical farm for efficient quality food production (2015), and 'Photoautotrophic (Sugar-free) Micropropagation as a New Micropropagation and Transplant Production System (2005).
His early work on greenhouse light environments, energy savings, ventilation, computer control, knowledge engineering, integrative environment control using a heat pump, fogging and null-balance CO2 enrichment systems, and closed systems with artificial lighting for transplant production in the fields of greenhouse horticulture earned him great recognition in his field.
Kozai has recently been working on 'plant factory with artificial lighting (PFAL) and has been leading the R & D of PFAL. His continuous quest in this field allowed him to dive deeper into this subject. He has been invited as a keynote speaker on the PFAL to more than 20 international symposia during 2015-2018.
According to AgriGarden, 'Plant factory is a highly efficient agriculture system which uses high precision control facilities in the continuous production of crops."
According to Kozai, it is believed that PFAL is expected to contribute to solving the food-environment-resource-health issues concurrently. Kozai has further described the six major components of the PFAL viz., thermally well-insulated, almost closed structure, multi-tier unit with lighting and hydroponic cultivation devices, air conditioners and fans, CO2 supply unit, nutrient solution supply unit and environmental control unit. Furthermore, he has mentioned that relatively large automated PFALs have been built in Japan in the year 2018, and the number of profit-making PFALs has been increasing in Japan since 2016. Besides, there are ongoing large-scale projects in the world hence stressing the fact that this concept is gaining prominence not only in Japan but globally as well.
In addition to the above, Kozai's study throws light on the essential benefits of PFAL as well. First, that PFAL offers a high degree of freedom of environment control and that any environment can be created at minimal costs, thereby making it highly cost-effective. Second, all rates of resource supply, plant production and waste production can be measured and controlled. Then, Resource Use Efficiency (RUE) (amount ratio of resource fixed or kept in plants to the resource supplied to the PFAL) can be estimated online for each resource element including electricity, water, CO2, fertilizer and seeds. This shows the convenience and the hassle-free process.
Currently, compared to the greenhouse, the PFAL can save water consumption for irrigation per kg of produce by 95% by recycling use of transpired water vapor from plants (The transpired water vapor is condensed and collected at the cooling coil of air conditioners and returned to nutrient solution tank). The productivity of leafy lettuce per unit land area is more than 100 times higher in the PFAL than in the open field. Thanks to this high productivity per unit land area, the PFAL can be built in urban areas with non-fertile or contaminated soil, resulting in the reductions of CO2 footprint, loss of produce during transportation, and delivery time of fresh vegetables to citizens.
However amongst all the benefits, there is one issue which still remains unresolved i.e., a methodology to find an optimal set of environmental factors automatically to maximize the CP (or productivity) under given conditions is yet to be developed. To maximize the CP, unit economic value, plant growth rate, percent marketable portion, cost of each resource element, consumption and RUE of each resource element needs to be measured or estimated online, and be integrated to calculate the CP.
Kozai's excellent research suggests how the CP can be more than doubled and the impact and the expected increase this will have on the PFAL market. He has therefore proposed the reduction in cost per kg of produce, an increase in sales per m2 of cultivation space by introducing recent advanced technologies such as artificial intelligence. Currently, costs for electricity, labour and depreciation for the initial investment account for about 20%, 20% and 30%, respectively. The rest (about 20%) is for seeds, fertilizer, water, containers, maintenance, etc.
Further, Kozai has the discussed the idea of next-generation PFAL (n-PFAL) and the associated requirements, scheme for R & D, challenges and opportunities. According to him, n-PFAL needs to create unique environments for plant production to produce high-quality plants with high yields using minimum resources and minimum emission of waste by introducing advanced but inexpensive technologies. He has suggested different technologies, which can be of great use in the same. However, he has submitted some challenges and opportunities, for example, smart LED lighting, phenotyping (plant trait measurement), production management including seed processing and circadian rhythm, efficient use of resources with minimum waste, breeding using DNA markers of plants suited to PFALs, et cetera. He has defined plant phenotyping and has given a detailed account of its usage in n-PFAL. Plant traits include plant architecture, chemical components, physiological status and response, etc.
In the n-PFAL, a huge time-series dataset of plant phenotype (traits), environment and management (human and machine interventions including seed processing) is automatically accumulated in a data warehouse. The data warehouse is connected with a related genome database and other n-PFALs' data warehouse via Internet. This global and local network of n-PFALs each with semi-open database will bring about a paradigm shift of plant/food/agricultural production and breeding of plants suited to PFALs. For example, breeding of plants suited to PFALs can be speeded up using the n-PFAL. Kozai has further recommended four types of models to be implemented in the PFAL: 1) mechanistic models for photosynthesis, respiration, transpiration and growth, and for substance, energy and monetary balance, 2) multi-variate statistic models, 3) behaviour (or surrogate) models, and 4) AI (or deep learning) models.
Kozai's study has won great acclaim amongst the researchers and his brilliant research on PFAL, an upcoming innovation will be of great use not only nationally but internationally as well.
At This High-Tech Farm, The Boss Is An AI-Powered Algorithm
Bowery Farming Says Its Proprietary Software Can Top The Intuition Of A Seasoned Farmer.
By Aki Ito
September 20, 2018
This High-Tech Farmer Grows Kale in a Factory
Each morning when she gets to work at Bowery Farming Inc., Katie Morich changes into a clean uniform, puts on a hairnet and cleans her hands with sanitizer. Then she consults a computer monitor displaying all the tasks she needs to accomplish that day. The to-do list’s author isn’t human; it’s a piece of proprietary software that uses reams of data collected at the indoor farm to make important decisions: how much to water each plant, the intensity of light required, when to harvest and so forth. In short, Morich and her fellow human farmers do what the computer tells them to do.
Morich, 25, doesn’t mind taking orders from a computer. “I guess I do kind of report to the Bowery Operating System,” she laughs, referring to the software her employer developed to run the so-called vertical farm in a New Jersey industrial park. Bowery says the machines are constantly learning how to grow crops more effectively and are more than a match for the intuition of a seasoned farmer. “We don’t really have to double-guess ourselves,” says Morich, who is the subject of the latest episode of Bloomberg’s mini-documentary series Next Jobs, which profiles people in careers that didn’t exist a generation ago.
Katie Morich, a farmer at indoor vertical farm startup Bowery Farming.
Photographer: David Williams/Bloomberg
Bowery is part of an emerging industry promising to bring new efficiencies to the millennia-old science of agriculture, focusing for now on greens such as lettuce, arugula and kale. The startup, based in New York and backed by leading Silicon Valley investors, including Alphabet Inc.’s venture arm, says automation, space-saving, vertically stacked crops and a year-round growing season make its operations 100-plus times more productive per square foot than traditional farms.
Morich and Bowery declined to disclose her salary, but the company says she earns more than the median $23,380 annual salary pulled down by a traditional American farm worker. This is how economists hope technology will help the economy: by raising workers’ productivity and bolstering their wages over time. It’s also worth noting that Morich’s job is far safer and less strenuous than tending the acreage of a conventional farm.
Trays of vegetables growing at Bowery Farming.
Photographer: David Williams/Bloomberg
Of course, artificial intelligence also has the potential to kill jobs, and Morich’s role, however new, is not immune. Bowery hasn’t yet figured out how to automate everything that needs to get done in the farm, but since she was hired less than two years ago, the company has made progress:
Such processes as seeding, once done by hand, are now completed by machines. Morich says she doesn’t worry about job security, but economist Erik Brynjolfsson is more skeptical. “If a task doesn’t draw on human creativity or other human strengths like interpersonal skills, then it’s a candidate for automation,” says Brynjolfsson, a professor at the MIT Sloan School of Management and co-author of “The Second Machine Age: Work, Progress and Prosperity in a Time of Brilliant Technologies.” “This could be profitable in the short and medium term,” he says, but as robots become more mobile and dexterous, “I would not count on having a job like that in 10 or 15 years.”
Nor should the rest of us. Machines and automated software may displace 75 million workers by 2022, the World Economic Forum forecast in a report this week. “Technology has always been destroying jobs, and it has always been creating jobs,” says Brynjolfsson. “The answer is not to freeze in any particular set of jobs or skills. It’s to be flexible and be ready for the new jobs, many of which haven’t been invented yet.”
Morich, for one, isn’t standing still: In May, she was promoted to lead a team of farmers, which left her confronting a whole new set of challenges. She’s been working long hours ahead of the opening of Bowery’s second facility. Once things settle down, she plans to read “Managing For Dummies.”
Can Artificial Intelligence Do As Well As Farmers In The Future?
Cucumber plants to enter autonomous greenhouse of Wageningen University & Research
Tuesday 14 August marked the start of the Autonomous Greenhouses Challenge as five international teams try to grow cucumbers at a distance with the use of artificial intelligence at the facilities of Wageningen University & Research (WUR). “The goal is to convert knowledge about cultivation into algorithms that can enable computers to regulate cultivation automatically in the future, even in places where such knowledge is lacking. So the question is: can computers do as well as farmers?”
The five international teams will have four months to produce a cucumber yield remotely and without human intervention, using as little water, nutrition and energy as possible while achieving the highest possible output (i.e. production). Each team has been allocated 96 square metres in the facilities of WUR’s business unit Greenhouse Horticulture in Bleiswijk.
“The teams have partly developed their own algorithms and used them to determine output settings such as temperature, light quantity, CO2 concentration, fertilisation and several cultivation-related parameters such as plant and stem density,” says the head of the Horticulture Technology research team Silke Hemming. “The sensors and cameras – which they will be installing themselves in the week of 20 August – measure some of these cultivation data. The sensors send the information to the computer systems, allowing them to control the climate and fertilization in the greenhouse. The teams will not be allowed to enter the greenhouses apart from to install the equipment.”
The teams will collect all data remotely and be able to continuously adjust their algorithms for the software. Hemming: “The software itself will adjust the output settings like temperature where necessary. The goal is that the self-teaching software gradually takes over human decision-making.”
The challenge was organized by Wageningen University & Research Greenhouse Horticulture and the internet company Tencent. “We think we can further improve food production in greenhouse horticulture by introducing artificial intelligence,” Hemming continues. “This unique challenge lets us connect with international partners and make major strides forward. Although they are already global leaders in cultivation expertise, we believe even Dutch breeders will benefit from results of the challenge, as it will enable them to make decisions based on more carefully considered information.”
According to Hemming, the use of artificial intelligence will have an even greater impact globally. “In many countries, there is very little knowledge about complex plant production. Artificial intelligence can help people make complicated decisions, so they can locally produce vegetables and fruit with fewer means. The higher yield and production are especially important in view of the growing global population.”
Cucumber, the crop of choiceIn addition to the autonomously controlled greenhouses, the challenge will comprise a reference greenhouse where the chief grower of WUR Greenhouse Horticulture and several Dutch growers will cultivate cucumbers in an authentic way. “We settled on cucumbers as our crop of choice because they grow fast,” says Hemming. “This will enable us to obtain lots of information in four months. Cucumber plants are also very quickly affected if something is done incorrectly during cultivation. A breeding company cultivated the plants for the teams, and people from the test company of WUR Greenhouse Horticulture will put the plants in the greenhouses. The yields, their value and the associated costs and sustainability factors will be compared to the reference greenhouse.”
Supervisors from WUR Greenhouse Horticulture will provide the teams with the required digital information. Information will be shared with and output settings received from the teams via an interface produced by LetsGrow.com, one of WUR’s tech partners. WUR employees will be responsible for harvesting and communicating standard crop information, including yield weight, to the teams. An international jury will oversee the process and award points.
“Most of the points will be awarded for maximization of net profit,” Hemming explains. “Another criterion will be sustainability: energy & water consumption, CO2 levels and the use of crop protection agents.” Teams will also receive points for the use of artificial intelligence. Questions such as ‘how autonomous was the teams’ actual approach?’ and ‘how realistically could this system be applied on a large scale?’ will be the main issues evaluated by the jury in the final stage.
An exciting competition
“We expect an exciting competition in which the teams – deep_greens, AiCU, The Croperators, Sonoma, and iGrow – apply different approaches,” Hemming concludes. “For one team, for instance, the focus will be on artificial intelligence, while another team will highlight cultivation expertise.” The winner will be announced in the second week of December during the AgriFoodTech trade exhibition. “We will gain lots of new knowledge for a new cultivation method for the future.”
For more information:
Publication date: 8/15/2018