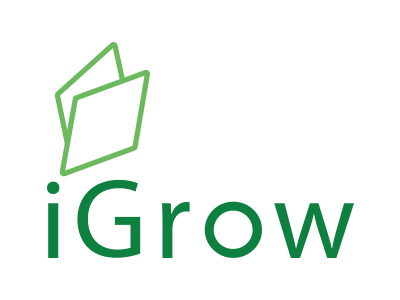
Welcome to iGrow News, Your Source for the World of Indoor Vertical Farming
AI Is Learning To Understand How Vegetables Taste
With the global demand for food escalating, vertical farms are becoming a critical component of agriculture's future. They use robotics, machine learning and artificial intelligence (AI) to automate farming and perfect the growing of greens and vegetables.
By Jennifer Kite-Powell
July 20, 2021
With the global demand for food escalating, vertical farms are becoming a critical component of agriculture's future. They use robotics, machine learning and artificial intelligence (AI) to automate farming and perfect the growing of greens and vegetables. With steady growth, the vertical farming market was had an estimated value of $4.4 billion in 2019 and is expected to reach $15.7 billion by 2025.
Fifth Season is a vertical farm in Pittsburgh that uses super-stack software and robotics to run their fully automated farming systems. And, by combining big data and AI, they have created the optimal grow recipe that determines the best flavor for the plants they grow.
"The role of AI in determining flavor is to leverage big data and AI to ensure you achieve the target flavor — sweetness, spiciness, bitterness, total degree of flavor and texture," said Austin Webb, CEO of Fifth Season.
"Our plant's individualized grow recipe is the unique mix of the different LED lights," said Webb. "The plants go through the grow room with a QR code that communicates that plant's route and tells the automated system where each plant needs to be throughout the process."
Webb says their super stack system, which serves as 'the brain' of the vertical farm maps, maps out each plant's route through the grow room based on its grow recipe and then moves the plants where they need to go.
"We use AI and data to find improvements in all aspects of crop quality, even beyond what humans think they know about flavor profiles. We call this proactive, deterministic growing compared to traditional farming, including greenhouse growing, where you have to be reactive based on weather and sunlight conditions," said Webb. "We then leverage human/chef feedback on what tastes the best and what texture is best and [..] combine that qualitative data with the 26K quantitative data points for every tray of greens per lifecycle."
"From there, we tweak our grow recipes to build the best flavor. For some vegetables, like tomatoes, experts have leveraged Brix scores, but [..] we measure flavor quality based on these factors: sweetness, spiciness, bitterness, the total degree of flavor, texture and color," said Webb. "Humans don't need to guess what iron content or Brix score is best; the brain in our farms can do that. Humans tell the grain what tastes best, and the brain will compute and tweak the grow recipes from there."
Darryn Keiller, CEO and founder of WayBeyond, says that to impact flavor, you either have to change the genetics of the crop or alter the existing biochemical profile.
"For example, growers can impact flavor by adjusting light and nutrients, which can then enhance the texture (crunch, thickness) or flavor (increased sweetness or bitterness)," said Keiller. "Once you determine the key characteristics you want in a crop, you then use machine learning or AI to automate and optimize the production process for consistent growth and be responsive to changing consumer preferences."
"Currently, vertical farms utilize seed stock bred for outdoor farming. Using AI technology, they can create their breeding stock (or lines) better suited for indoor environments. It's about refining your research and development and creating genetics perfect for your environment and management practices while ensuring continuous improvement of commercial production. The potential is huge."
Webb adds that many indoor growers sought to build an outdoor farming system that can thrive indoors; however, Fifth Season chose to apply smart manufacturing principles to agriculture that would enable them to grow food in a new way.
"We grow more than 15K pounds a week of fresh food with 90% less water than what would be required to grow that amount of fresh food on a traditional outdoor farm - and that is done on a footprint of just 25,000 square feet," added Webb.
Webb believes that scaling viable vertical farming operations that can crack code on both the technology and the consumer experience to deliver consistently fresh, nutritious and clean produce changes the consumer shopping significantly.
"It changes our entire definition of what fresh can and should taste like; it changes the ease of access and availability and convenience to fresh food, which brings so much value to consumers," said Webb. "It's another avenue for shoppers to access the freshest, highest-quality food at retail with produce that has a much longer shelf life than we're accustomed.”
Lead Photo: Greens leaving the grow environment on route to harvesting and packaging in Fifth Season's vertical farm in Pittsburgh.
Robots Take Vertical Farming To New Heights
Braddock, Pa., is where Andrew Carnegie first mass-produced steel. The city, now one-tenth its former size, is home to a new kind of industry: robotic farms that grow greens inside buildings
Braddock, Pa., Is Where Andrew Carnegie First Mass-Produced Steel. The City, Now One-Tenth Its Former size, Is Home To A New Kind Of Industry: Robotic Farms That Grow Greens Inside Buildings.
June 28, 2021
A decades-long decline of industry in Braddock has left the western Pennsylvania town in ruins. Ten miles upriver from Pittsburgh in the Mon (Monongahela) Valley, most of the city’s factories, businesses and homes were abandoned long ago and leveled. Among the ruins, a sprawling steel mill, built by Andrew Carnegie in 1874, is still producing slabs of steel, 24 hours a day, seven days a week. It’s stained blue walls and maze of giant, rust-colored pipes and vents stand in contrast to the brand-new, block-long, gleaming white structure directly across the street. The mill’s neighbor is Fifth Season, a vertical farm growing greens indoors by stacking racks of plants on top of each other.
Fifth Season is the brainchild of brothers Austin and Brac Webb, and co-founder Austin Lawrence. “We view vertical farming as really a smart manufacturing system,” says Austin Webb. “We just happen to manufacture living organisms.”
The partners consider their fledgling enterprise as more than a means to feed people, but also a chance to work with a community in need. Almost none of the old steel plant’s employees live in Braddock. Conversely, everyone hired to work at Fifth Season lives close by and in the surrounding communities. “We’re creating a workforce of the future,” Webb says. “It’s an entirely new ag-manufacturing job that hasn’t existed before.”
Since the collapse of the steel industry in Braddock, the borough has struggled to attract new business and residents.(David Kidd/Governing)
Automated City Farming
Two shifts of 20 people oversee operations at the vertical farm. And like the steel maker across the road, the work never stops. Dressed in blue scrubs and lab coats, with heads covered and gloves on their hands, workers inside the plant look more like medical research professionals than farmers. The entire process, from seed to harvest, is controlled robotically. “What we have built is the industry first, and industry only, end-to-end automated platform,” says Webb.
Fifth Season’s proprietary software allows efficiencies otherwise not attainable. Spinach, arugula and other greens move around the 60,000-square-foot facility in plastic trays, each with its own unique ID. Sensors are constantly monitoring everything from nutrient mix, carbon dioxide levels and light spectrum, in order to ensure that the greens follow their prescribed grow recipe. Every plant can be traced from any point in the process, at any time.
Webb is quick to tout the advantages of vertical farming. Fifth Season uses up to 95 percent less water and 98 percent less land than conventional farming. Water from the municipal system is filtered and proprietary nutrients added before getting to the plants directly through their roots. “It means you can replicate any form of soil environment,” he says. Whatever water is not used by the plants is retreated and recirculated, with nutrients added as needed. A peat mix is used to support the roots, but all the nutrients are in the water, not the “soil.”
“We use no herbicides and no pesticides,” Webb says. “And that’s because we have hermetically sealed environments.” The possibility of contamination is all but eliminated. Fifth Season recently received a perfect score from the Safe Quality Food (SQF) program, an international, independent body that certifies food safety management. “The second time in 25 years they gave 100 percent,” he says.
With only their faces exposed, employees work among the various conveyor belts that crisscross the high, white-walled rooms of Fifth Season’s production floor. But there are no humans in the adjacent grow room, where tightly spaced racks, supporting trays of plants, are stacked 30 feet high, bathed in an otherworldly purple-magenta glow. The dramatic color comes from the LEDs that replicate the most useful parts of the spectrum of sunlight. “You can’t control the sun,” Says Webb. “But what you can control are LEDs.”
Fifth Season’s proprietary systems allow more plants to be grown in less space. The purple-magenta LED lighting replicates the most useful parts of the spectrum of sunlight, improving growth of the greens.(Fifth Season)
Every few minutes, a robot glides forward and back along a raised guideway that runs down the center of the room, dividing the stacks in half. The machine is not much more than a plain box, just a few feet tall. A metal beam rises from its back, extending to the ceiling. Its task is to place and remove trays of plants, taking its instructions from the all-knowing software. Because they are so tightly spaced, more trays can be stacked on top of each other, resulting in greater production.
“Compared to some other vertical farms out there, we have a lot more density,” says Webb. “We’re able to have more racks that grow inside the same space.” Moving trays is a task well-suited to a machine. Not only does the robot fit into places no human could, it always knows where every tray of greens should be, and for how long.
Vertical Farming Comes to Braddock
After a five-year career in finance, Austin Webb enrolled in an MBA program at Carnegie Mellon University in Pittsburgh. “I believe that robotics will possibly disrupt every industry in the world,” he says. “And so I went to C.M.U., specifically because it’s the No. 1 school in computers, science and robotics.”
There he met Austin Lawrence, who shared his interest in controlled environment agriculture. Together they visited a few vertical farms, coming to the conclusion that what was needed was an entire robotic platform, something the two of them could not accomplish on their own. Webb’s brother Brac, a self-described engineer and entrepreneur, was soon recruited to help. Their new business was incorporated in 2016, initially as RoBotany, which later morphed into Fifth Season.
With financial backing in hand, the partners looked for a place to build, quickly settling on nearby Braddock. They broke ground in May of 2019, were installing equipment less than a year later and were at full production before the end of 2020. “I think there’s a lot of opportunity for resurgence in a place like this,” says Webb. “A lot of folks that stayed are passionate around Braddock being able to grow and thrive and we want to be a part of that.”
In the foreground, Fifth Season’s new structure stands in contrast to the steel plant behind it that still dominates the town.(David KIDD/Governing)
Andrew Carnegie’s mill was the first of many that would proliferate in the Mon Valley, making it the nation’s steel capital. The churches, schools, stores and restaurants that served the town’s 20,000 inhabitants are mostly gone now. Shops and services are few and far between for the 2,000 that remain. “The nearest grocery store is up the hill, two towns over,” says Braddock Mayor Chardae Jones. “And most people don’t have cars.” It’s a hot day in June when a few of the locals gather in a brand-new park along Braddock Avenue. Everyone agrees the park is nice, but it’s no consolation for the hospital that used to stand on the site.
Many years ago, steelworkers and their families lived close to the mill.(David Kidd/Governing)
A few blocks away, an ever-present din still emanates from Carnegie’s steel mill, and a parade of trucks continues to roll past the boarded-up stores and empty lots that line the borough’s main thoroughfare. “We have a lot of vacant buildings,” says Mayor Jones. “That’s our biggest issue.” But there are signs of a revival among the ruins.
Present Day Braddock
Against the backdrop of empty and dilapidated storefronts, “The Ohringer,” a former furniture store built in the streamline moderne style of the 1940s, has recently been completely rebuilt and modernized as apartments and studio space for artists. Applicants are expected to present their work for review and answer a few questions, one of which is “why are you interested in becoming part of Braddock’s resurgence?”
Not only does Braddock lay claim to Andrew Carnegie’s first steel mill, but also the first Carnegie library, dedicated in 1889. Narrowly escaping demolition in the 1970s, the impressive stone structure is today undergoing a comprehensive restoration and modernization. Bright yellow notices of this year’s street sweeping schedule are affixed to telephone poles near the library and all over town, an indication that the local government is still functioning.
A repurposed furniture store now provides updated living and studio space to area artists.(David Kidd/Governing)
Further up the avenue, more official-looking signs are attached to random telephone poles. “NOTICE, WRITE MORE LOVE LETTERS” says one. “NOTICE, LOVE IS FREE,” says another. The signs were placed there, unofficially, by Gisele Fetterman, wife of former mayor and current Lt. Governor John Fetterman. Among her many initiatives to improve the lives of people in Braddock, she founded the Free Store nine years ago, a place where “surplus and donated goods are received and redistributed to neighbors in need.”
Fifth Season is a regular contributor to the Free Store, having recently given them a new refrigerator and donating 100 pre-packaged salads every Thursday. “We’re treated like we’re a customer,” says Gisele Fetterman. “We’re not getting things that didn’t sell, or surplus. Our families get to come in and choose. They can feel like they are at a grocery store. There is great dignity in the process of being able to choose.”
Offering “produce grown in soil by humans in Braddock,” workers at Braddock Farms do it the old-fashioned way.(David Kidd/Governing)
There are more signs along Braddock Avenue. “BE ALERT: VEGETABLES AHEAD.” Another simply says “TURNIPS.” Back in 2007, when John Fetterman was the mayor, he encouraged a nonprofit group of community gardeners to establish a farm in Braddock. Bisected by a side street, the organic farm has expanded to a little less than an acre in size, growing greens, tomatoes, onions, peppers and eggplant. This is Nick Lubecki’s fourth year as manager of the farm. “We’re here in Braddock, so the people in Braddock are our main focus,” he says. “We want to be useful.”
At best, the little farm on Braddock Avenue can produce 13 plantings of greens in a year. It is entirely different from the computer-controlled, machine-driven, non-stop production that takes place a few blocks away at Fifth Season, where a half-acre indoors can produce the equivalent of nearly 100 acres of farmland. But higher yields don’t matter as much if a significant portion is ultimately lost in transit to the table.
Serving a Market
Localized food production means less spoilage and waste. “If it takes anywhere from five to eight days to go from California to Pittsburgh, you’ve just lost five to eight days of shelf life,” says Austin Webb. Most of what Fifth Season produces is consumed in the Pittsburgh area. “The day after it was cut, not 10 days later.” Their ready-to-eat salads can be purchased at a local supermarket chain, or delivered directly to the consumer at home, a direct response to the pandemic. Local restaurants, hospitals and universities are also customers.
Convinced they have successfully demonstrated the viability of their proprietary technology, the three partners are looking to expand beyond western Pennsylvania. “We can build these anywhere… even larger than what we have here today,” says Austin Webb. “And we don’t have to re-create the wheel. It’s not like it would take us another five years.”
Conversations are already taking place about licensing the technology, proceeding in partnership with someone else, or going it alone. “That will allow us to build a facility just like we built in Braddock, in other parts of the U.S., and other parts of the world, even faster.”
A Job You Can Walk to
Andrew Carnegie built his steel mill in the Mon Valley because he needed the river, the raw materials, and access to labor. His plant was expressly designed to use the Bessemer Process, the first method to inexpensively mass-produce steel. Nearly 150 years later, the Webb brothers and their partner Austin Lawrence chose the exact same location to showcase their own new manufacturing technology and to fill a need in the community. “Knowing that we could build these anywhere, we wanted to build in Braddock because we knew that we could create jobs,” says Austin Webb. “That we could create this new workforce of the future.”
Employed since January, John Davis lives less than a block away from Fifth Season. “I have family in Braddock. They’re very happy I’ve got a job.”(David Kidd/Governing)
Braddock resident John Davis may or may not think of himself as part of the workforce of the future. But he’s happy to have a good job. Covered head to toe in his surgical outfit, he works in the seeding department at Fifth Season, a job he’s held since January. He’s lived here for 20 years, and this is the first job he’s had that didn’t involve a commute. He walks to work from his house, half a block away.
Davis is 32 years old and anxious to put the past behind him. “To have a job that you like, where you live, it’s comfortable,” he says. “And you can see that this is going to change Braddock for the better because it gives the residents jobs and new innovations. It’s going to bring life.”
While awaiting their fate, many of Braddock’s empty buildings provide space for murals and artwork.(David Kidd/Governing)
Lead photo: Greens leave the grow room at robot farm Fifth Season, ready for harvest. (Fifth Season)
Tags: Economic DevelopmentFood AssistanceTechnology
David Kidd is a photojournalist and storyteller for Governing. He can be reached at dkidd@governing.com.
Farm Tech Startup Iron Ox Appoints Impossible Foods and Tesla Veteran Rachel Konrad as First Independent Board Member
Iron Ox growing facilities use advanced robotics to precisely cultivate perfect, nutritious produce by giving each plant the specific attention it needs, and then getting it on a store shelf nearby within about a day of harvest
-- Konrad, who spent the past five years at Impossible Foods, joins the board of Iron Ox during a period of rapid manufacturing scale-up and retail expansion.
-- Iron Ox growing facilities use advanced robotics to precisely cultivate perfect, nutritious produce by giving each plant the specific attention it needs, and then getting it on a store shelf nearby within about a day of harvest.
-- The Series B-stage company, whose products are already a breakout seller in California, is also hiring plant scientists, engineers, greenhouse operators, and roboticists.
SAN CARLOS, Calif., June 10, 2021 /PRNewswire/ -- Iron Ox, a farming innovation company with deep expertise in robotics and artificial intelligence, has appointed former Impossible Foods and Tesla executive Rachel Konrad as its first independent board member. This appointment further demonstrates the food tech startup's growth trajectory as they scale up operations and expand their commercial footprint.
Iron Ox, which launched the world's first autonomous farm, has an industry-leading intellectual property portfolio to automate farming and produce that's fresher, cleaner, and locally grown. Thanks to the company's groundbreaking robotics, Iron Ox farms require 90% less water than traditional farms — generating 30 times more produce per acre of land.
Konrad joins Iron Ox after spending the past five years as Chief Communications Officer and a member of the senior leadership team at Impossible Foods, reporting directly to CEO Pat Brown. She previously held senior management roles at Renault-Nissan-Mitsubishi and Tesla, where she reported directly to Elon Musk as the company scaled up operations.
"We can't solve our planet's climate crisis without radical changes to the way we make food," said Konrad, who lives in the San Francisco Bay Area and enjoys cooking for her family and hiking with her rescue German Shepherd. "Iron Ox's intellectual property portfolio can usher in a new era of farming that produces food sustainably and ethically. But honestly, I was sold after my first whiff of Iron Ox basil."
"Rachel understands the unique power of disruptive startups to shift entire industries and force even the most entrenched incumbents to do the right thing for people and the planet," said Brandon Alexander, Iron Ox CEO and Co-Founder. "Her unique perspective will help Iron Ox refine and execute our ambitious strategy. As our first independent board member, we expect Rachel to help us set a new standard for inclusive governance in corporate America."
The Series B-stage company operates farms in Northern California and recently broke ground on a new 535,000 sq. ft. indoor farm in Lockhart, Texas. Today, California consumers can buy Iron Ox food throughout California at Whole Foods and at San Francisco Bay Area's upscale Biancchini's markets. Sales in Texas are expected to begin in late 2021.
The company is also hiring plant scientists, engineers, greenhouse operators and roboticists who are passionate about solving food insecurity, which is at the root of our environmental and public health crises.
For more information, and to view the job openings, visit the Iron Ox jobs page.
About Iron Ox:
Iron Ox is a farming innovation company with deep expertise in robotics and artificial intelligence, and a vision to solve global climate through food. Their approach redesigns every step of the farming process, achieving levels of precision that are impossible through traditional farming. Iron Ox produce is both local and sustainable by design, greatly reducing systemic food waste and minimizing the ecological impact of farming. For more information, visit www.ironox.com.
SOURCE: Iron Ox
USA: TEXAS - Iron Ox Breaks Ground On New Robotic Growing Facility In Lockhart
The state-of-the-art indoor facility will be fully dedicated to growing techniques harnessing the power of robotics and intelligence, enabling Iron Ox to grow sustainable, local produce to serve the Texas community
By FOX 7 Austin Digital Team
April 22, 2021
California-based company Iron Ox held a groundbreaking ceremony for its new Lockhart facility in partnership with the Economic Development Corporation of Lockhart. (City of Lockhart)
LOCKHART, Texas - A new robotic growing facility is expected to bring over 100 jobs to the city of Lockhart.
Iron Ox, a California-based company that specialized in robotics and AI-enabled farming with a mission to solve food insecurity, has begun construction on a 535,000 square-foot indoor hydroponic farm in the city.
Once completed, the farm, which sits on 25 acres of agricultural land, will significantly increase Iron Ox’s growing capacity for fresh, clean, and healthy herbs, leafy greens, berries, and vine crops, says the company. The state-of-the-art indoor facility will be fully dedicated to growing techniques harnessing the power of robotics and intelligence, enabling Iron Ox to grow sustainable, local produce to serve the Texas community.
Iron Ox, a California-based company that specialized in robotics and AI-enabled farming with a mission to solve food insecurity, has begun construction on a 535,000-square-foot indoor hydroponic farm in the city. (City of Lockhart)
The company says that Lockhart is an ideal location for greenhouse agriculture given its ample sunlight, central location near many cities, and it’s proximity to several great universities.
The indoor farm is expected to cost over $10 million to develop, says Iron Ox, with 275,000 square feet of the project anticipated to be completed by the end of this year and 260,000 square feet of the project anticipated to complete by the beginning of 2022. In total, the project will create over 100 jobs.
"The addition of Iron Ox to the Lockhart business community represents synergy between our city’s storied history in agriculture and our growing technology sector," said Lockhart Mayor Lew White in a release. "The food and beverage processing industry is one of four business sectors Lockhart has targeted in its 5-year economic growth plan. Our city’s unique advantages align perfectly with the needs of companies like Iron Ox."
Lockhart Mayor Lew White (left) and Iron Ox co-founder and CEO Brandon Alexander stand next to a concept drawing of the new Iron Ox facility being built in Lockhart. (City of Lockhart)
Iron Ox expects to complete their first harvest and to begin delivering sustainable, local produce to select chefs and retailers throughout Texas by the end of this year. It is anticipated that Lockhart’s hydroponic facility will grow thousands of pounds of fresh fruits and vegetables. Each crop type is cared for by Iron Ox’s expert growers and empowered by a robotic growing process ensuring year-round consistency, quality, and flavor says the company.
"We have made it our mission to address food security by developing autonomous greenhouses that grow a variety of local and consistently delicious food for everyone", said Iron Ox CEO and co-founder Brandon Alexander. "We’re excited to begin development of our newest indoor farm here in Lockhart—our first out-of-state facility. We look forward to further developing ties to the local community and to expanding our partnerships and distribution channels throughout the state of Texas."
Iron Ox co-founder and CEO Brandon Alexander addresses people at the groundbreaking ceremony of the new Iron Ox facility in Lockhart. (City of Lockhart)
Focused on sustainable, scalable food production for a changing climate and an ever-growing population, the Iron Ox process eases the growing pressure of food waste and labor scarcity by providing a stable supply of fresh, nutritious food for local communities, says the company.
Iron Ox says it designed its growing system around the sun, an approach that uses less energy than other modern forms of farming. Their hydroponic growing system uses 90% less water over traditional farming while growing 30 times the amount of crops per acre of land, allowing Iron Ox to deliver on its mission to increase access to premium produce for everyone.
Iron Ox currently operates two hydroponic farms located in Gilroy and San Carlos, California.
VIDEO: Indoor Farming Powered By Robotics And Technology - Plenty
Indoor farming powered by robotics and technology is enabling one California company to grow 'Plenty' of flavorful nutrient-rich and pesticide-free produce
Author: abc10.com
April 6, 2021
UNFI Picks Up Living Greens Farm Products in Midwest Expansion
Living Greens Farm (LGF), the largest vertical, indoor aeroponic farm in the US that provides year-round fresh salads, salad kits, microgreens and herbs, announced the addition of significant new retail distribution of its products in the upper Midwest to independent, specialty, and co-op retailers
I|mage from: Living Green Farms
Living Greens Farm (LGF), the largest vertical, indoor aeroponic farm in the US that provides year-round fresh salads, salad kits, microgreens and herbs, announced the addition of significant new retail distribution of its products in the upper Midwest to independent, specialty, and co-op retailers.
Starting February 2021, LGF’s full line of products featuring ready-to-eat bagged salad products (Caesar Salad Kit, Southwest Salad Kit, Harvest Salad Kit, Chopped Romaine, and Chopped Butter Lettuce) will be carried by UNFI Produce Prescott (formerly Alberts Fresh Produce). UNFI Produce Prescott is a division of UNFI, which distributes food products to thousands of stores nationwide. Their focus is on independent, specialty and co-op retailers.
UNFI has eight warehouses nationwide. LGF’s products will be carried by their upper Midwest location, located just across the river from the Twin Cities in Prescott, WI. This distribution center services hundreds of retailers throughout Minnesota, Wisconsin, Illinois, North Dakota, South Dakota, Missouri, Iowa and Nebraska. UNFI is the first national Certified Organic distributor, something they take a lot of pride in. Their produce and floral businesses are rooted in local farms and seasonal import growers.
LGF’s proprietary vertical indoor farming method yields the highest quality and freshest produce available. This is because there are no pesticides or chemicals used in the growing process. And because LGF’s growing, cleaning and bagging process significantly reduces handling and time to the retail shelf, consumers enjoy the freshest product on the market. These benefits continue to attract new users and new retail distribution as UNFI Produce Prescott is the second UNFI location to carry LGF. In December, UNFI’s Hopkins, MN location began offering LGF products.
For more information on why Living Greens Farm products are the cleanest, freshest and healthiest farm salads and greens available, go to www.livinggreensfarm.com.
This Startup Wants Vertical Farmers To Hire A Robot Gardener
“By automating the production with robotics and remote monitoring, we can lower labor costs and offer solutions for food producers that are economically viable and environmentally sustainable,” the company claims on their website.
Arugula micro greens are grown at AeroFarms on February 19, 2019, in Newark, New Jersey.
Photo: Photo by Angela Weiss (Getty Images)
In recent years, vertical farming has emerged as a futurist’s solution to the world’s agricultural problems. The growing trend seeks to use controlled environments to boost food production, leveraging indoor labs where temperature, light, and nutrients can be mechanically controlled.
Yet while vertical farms have gained in popularity, they are also still very expensive. When compared to conventional farming, these farms necessitate the purchase of pricey equipment to aid human labor—a fact that, when paired with other economic pressures, has apparently led to an industry “littered with bankruptcies.”
One company hopes to change this dire picture. Enter Watney the robot.
Watney was designed by start-up Seasony. The company, which was featured today at this year’s Alchemist Accelerator’s Demo Day, has sought to make the tech-farming trend more accessible by automating away some of the more difficult labor involved.
Image: Screenshot: Youtube/TV2LORRY
“By automating the production with robotics and remote monitoring, we can lower labor costs and offer solutions for food producers that is economically viable and environmentally sustainable,” the company claims on their website.
Indeed, Watney is designed to augment (and, in many ways, replace) a human labor force—currently one of the biggest expenditures for vertical farms. Essentially an intelligent, automated cart, the robot was designed to “move and transport plant trays” within a farming hub. In techno-jargon, it is an autonomous mobile manipulation robot (AMMR), a type of machine known for moving and manipulating items on its own. It is also equipped with a camera that captures image data and sends it back to farm management software for human analysis. Watney also gathers valuable horticultural data to help farmers optimize yields, said Christopher Weis Thomasen, Seasony’s CEO and Co-Founder, in an email.
From left to right: Erkan Tosti Taskiran, Servet Coskun and Christopher Weis Thomasen.
Photo: Photo from Seasony.
“We are doing for vertical farming what the integration of autonomous mobile robots did to amazon. We are able to decrease the costs of growing food in a vertical farm by alleviating the logistics pains of working from scissor lifts,” said Thomasen.
Thomasen, a mechanical engineer, and his two co-founders electrical engineer Servet Coskun and business specialist Erkan Tosti Taskiran, were inspired to create the business while brainstorming what it would take to sustain life in outer space (Watney the robot is named after Mark Watney, the astronaut in the movie The Martian, who, after being stranded on the Red Planet, fertilizes potatoes with his own poop to survive).
“It quickly evolved to Seasony setting up a vertical farming lab and exploring the technical challenges facing the new industry. Reducing the costs related to labor is key in order to scale vertical farming and make agriculture more sustainable,” Thomasen said.
There is, of course, some debate in the farming community about the social costs incurred through the large-scale displacement of human labor.
Presumably, we will have to wait to see what that cost-saving process looks like. Seasony, which is still getting off the ground, plans to do a pilot trial with the largest vertical farm in Europe in April. It has plans to conduct further testing with several smaller vertical farms, as well, Thomasen said.
Lucas Ropek
Staff writer at Gizmodo
VIDEO: How 2 Hong Kong Pioneers’ Hi-Tech Robotic Arms Can Transform Traditional Industries And Research
Technology created at Jonathan Cheung’s Inovo Robotics performs repetitive tasks that can cultivate sustainable crops and process foods in automated kitchens
Technology created at Jonathan Cheung’s Inovo Robotics performs repetitive tasks that can cultivate sustainable crops and process foods in automated kitchens
Eric Wong has transformed lab experiments with Nikyang’s automated tools that allow researchers to carry out a more reliable and systematic analysis
7 January 2021
While robotic technology has been widely used by big manufacturing companies to increase productivity, the high cost of getting started means many smaller businesses have yet to take advantage of its huge potential.
However, Inovo Robotics, a Hong Kong-based technology start-up, is working to solve this problem.
Since it was founded in 2016, the robotics company has been developing solutions for small- and medium-sized enterprises to help them adapt to automation in their everyday business practices.
Jonathan Cheung, the co-founder of the start-up, says his goal is to “democratize robots” and develop tools for all businesses to help them improve efficiency and remain competitive.
By submitting, you consent to receiving marketing emails from SCMP. If you don't want these, tick here
“We found that there is such a big disconnect to the market for small businesses to be able to benefit from affordable and flexible robots,” he says.
“There are a lot of businesses that are struggling to get staff to do monotonous tasks, so what we’re developing is really a tool that enables them to take away repetitive work.”
Jonathan Cheung, the co-founder of Inovo Robotics, says high entry costs mean that many small businesses have yet to take full advantage of automation’s full potential.
Disrupting traditional industries
One of the applications of the robotic arms has seen them used around the clock to carry out repetitive tasks that help grow high-quality, pollution-free vegetables at a futuristic farm in Hong Kong’s Tai Po district.
The farm, operated by indoor farming company Farm66 since 2018, is located inside a 20,000-square-foot (1,860-square-metre) factory building.
The use of the robotic arms to automatically sow seeds and harvest plants helps the farm to produce up to 200 tonnes of organic fresh produce, including cherry tomatoes, cabbage and basil, which is sold online and delivered to the city’s supermarkets and restaurants.
“Robots really improve the efficiency and speed of the products that are being made,” Cheung says. “In this competitive world, there is always a desire to drive costs down.”
In the case of vertical farming, the technology means minimal space and manpower are needed for the farming process, offering a glimpse of how technology will be able to transform farming in future.
Besides the vertical farm, the technology has also been used in an automated kitchen, where it helps with food processing to ensure cooking consistency. Inovo Robotics is also teaming up with a programming company to develop a system for high-resolution 3D scanning.
Inovo Robotics’ technology is being used to cultivate fresh organic produce at Farm66’s futuristic indoor farm inside an industrial factory building in Hong Kong. Photo: Farm66
Popularising robots for everyday use
Before setting up his own venture, Cheung spent more than a decade working as an engineer, when he witnessed first-hand how robots can help businesses scale their operations.
In 2016, Cheung and a colleague co-founded Inovo Robotics to popularise the everyday use of robot technology by businesses.
Its launch product, Modular Arm, with an adjustable system of six fully rotatable joints, gives the robot the flexibility to reach different positions. The robot’s modularity also gives customers an easy mechanism to choose longer or shorter arms, depending on their configurations.
Cheung says while large manufacturing companies often require tools that can automate a repetitive task, smaller businesses look for collaborative robots that can work alongside staff to complete different jobs at the same time.
“Smaller businesses tend to have smaller batch sizes and tighter spaces,” he says. “That is where a collaborative robot really comes into its own.”
Jonathan Cheung says Inovo Robotics’ modular robot technology offers small businesses a variety of options thanks to its adjustable flexible joints and the choice of using shorter or longer arms.
Inovo Robotics currently has two offices at Hong Kong Science Park, a government-run start-up incubator, and London, in the United Kingdom, as it seeks to tap into both the Asia-Pacific and European markets.
Cheung says Hong Kong has proved an ideal location to scale up his business because of its proximity to hi-tech research and an abundance of talent.
“[We can] be close to our supply chain, which allows us to manage it closely and deliver the best product to our customers,” he says.
“At any point in Hong Kong, you are probably within 25km to five or 10 great universities,” he adds. “There is a wealth of talent to be able to tap into – there are only a few countries with that level of accessibility.”
Revolutionizing academic research
Another Hong Kong start-up, Nikyang, has also developed fully automated laboratory equipment to help academic researchers increase the reliability of data collected in experiments.
Today, its automation technology has been applied in many settings, such as research institutes and pharmaceutical and biotechnology companies.
The venture was founded by Hongkonger Eric Wong in 1999 with the initial goal of helping researchers in traditional Chinese medicine (TCM) to conduct analysis in a more systematic way.
“The basic dream of Nikyang was originally to pursue TCM research to gain a better understanding,” says Wong, who graduated with a master’s degree in biochemistry in Canada.
“I thought we needed a more standardized way of doing analysis in TCM to collect valid and precise information.”
Eric Wong, the founder of automation company Nikyang, says the use of robotic technology allows researchers to conduct more systematic analysis.
When he started his business journey by reaching out to laboratories in Hong Kong and mainland China, he realized that researchers wanted to use machines to help them follow the correct procedure as closely as possible while carrying out repetitive work.
However, many automated instruments available then lacked the ability to carry out different steps in lab research, he says, rendering them error-prone when applied in studies.
To solve the problem, Wong collaborated with Chemspeed, a Switzerland-based provider of lab equipment, in developing specific instruments for TCM research.
His team has integrated Chemspeed’s tools with robotic arms and wearables to increase collaboration between researchers and machines in conducting the analysis.
However, he realized the company would not be sustainable if it focused solely on serving the TCM industry, so he later diversified the business and began developing solutions for different settings.
In 2008, Nikyang began receiving orders from petrochemical companies in China, which gave Wong a lifeline to sustain his business and pursue his dream in TCM research.
The venture now places an emphasis on boosting effectiveness by providing an immerse lab experience.
Its SmartLab product, which is still under development, is set to integrate sensor technology, smart wearables, and cloud data management to help researchers work more efficiently with machines.
Nikyang’s SmartLab, which is still under development, will integrate sensor technology, smart wearables, and cloud data management so researchers can work more efficiently with machines. Photo: Nikyang
Nikyang has its headquarters at Hong Kong Science Park, where it carries out most of its research and development work. To tap into the China market, it has also opened branches in Beijing, Shanghai, and Guangzhou to sell its products.
Wong says Hong Kong has served as an ideal location to grow his company because of its connectivity with China and different parts of the world.
“Hong Kong is definitely unique in terms of being a super-connector between the East and the West,” he says.
The city’s world-class financial market and sound legal system have also helped start-ups in raising capital and developing ideas as they embark on their journey.
Pioneering spirit
Both Wong and Cheung believe it is important for aspiring innovators to be passionate about their business vision to help them overcome challenges when developing and selling the products.
Wong, who spent a decade before he found a way to make his business sustainable, says it was vital to remain dedicated because many innovators experience failures before they can get their businesses on track.
“You need to have passion and a big heart to accept failure, and [an] even bigger heart to think and take risks,” he says.
Eric Wong, who spent a decade before finding a way to make Nikyang sustainable, says aspiring innovators should be passionate about their business vision – and not focus only on profits.
Wong also advises young entrepreneurs not to look only at making profits if they want to make a difference in the world.
“Money is only a by-product,” he says, adding that many successful pioneers often have to make substantial investments before they are able to disrupt the industry.
Cheung agrees that innovators must feel empowered to turn ideas into reality.
“My advice is to really focus on the business model,” he says. “It’s a very, very difficult journey to go on, and it’s very, very rewarding as well. And it’s very important to make sure you stay true to what you believe in.
“Having an idea that you believe in wholeheartedly, that you are willing to give your time and commitment to, is a good validation that you are on the right track.”
Morning Studio is the commercial content team of the South China Morning Post (SCMP). It aims to engage readers through storytelling while enabling the brand behind the content to achieve its marketing objectives. The Morning Studio team consists of specialists in various areas such as journalism, multimedia graphics, video production, digital technology, and marketing.
100% Robotization Allows Constant Quality Produce
"One of the biggest bottlenecks for most vertical farms is labor-intensity and associated costs. Our first focus was to reduce manual handling," says Ard van de Kreeke, Growx's CEO and founder
"One of the biggest bottlenecks for most vertical farms is labor-intensity and associated costs. Our first focus was to reduce manual handling," says Ard van de Kreeke, Growx's CEO and founder.
Growx has recently been featured in the 75th edition of RuMoer Magazine by BOUT, a master student association program in Building Technology at TU Delft, the Netherlands. The 75th issue is dedicated to urban farming as a solution for reconnecting the urban population to their food sources.
Ard continues, "Not only to reduce cost but also to ensure a constant quality of produce. The implementation of 100% robotization was successfully introduced in 2020. This not only makes a huge difference in labor costs and produce quality but also keeps the cell extremely clean. Human interfaces are only needed for malfunctions and checks. Another additional advantage is that there is no need to keep aisles and room for personnel to move around."
Each plant (gutters) continuously records broad water and nutrients, exposure, and air quality. But also a photographic representation in visible and infra-red light. This data stream is centrally stored and analyzed with the aim of developing optimal cultivation profiles.
Growx's robots pick up the entire process from start to finish, in other words, from seeds to harvest. "As soon as the plant moves on to the next phase of the growing cycle, the robot can respond automatically. Think of different light- or water composition," says Ard.
The company created a closed-loop system, where 100% of their waste is recycled to produce energy, CO2, water, and nutrients. They use an anaerobic digester for all the waste, which results in biogas that can be used for heat pumps and CO2 for the plants to use.
The complete article can be found here.
For more information:
Growx
info@growx.co
www.growx.co
Autonomous Delivery Startup Nuro Hits $5 Billion Valuation On Fresh Funding of $500 Million
Nuro, the autonomous delivery startup founded by two former Google engineers, has raised $500 million, suggesting that investors still have an appetite for long-term pursuits such as robotics and automated vehicle technology
Kirsten Korosec@kirstenkorosec / November 9, 2020
Image Credits: Nuro
Nuro, the autonomous delivery startup founded by two former Google engineers, has raised $500 million, suggesting that investors still have an appetite for long-term pursuits such as robotics and automated vehicle technology. Nuro now has a post-money valuation of $5 billion.
The Series C round was led by funds and accounts advised by T. Rowe Price Associates, Inc., with participation from new investors including Fidelity Management & Research Company and Baillie Gifford. The round also includes existing investors such as SoftBank Vision Fund 1 and Greylock.
Nuro was founded in June 2016 by former Google engineers Dave Ferguson and Jiajun Zhu. While the startup was initially bootstrapped by Ferguson and Zhu, it has never struggled to attract investors. Nuro completed its first Series A funding round in China in 2016, a deal that gave NetEase founder Ding Lei (aka William Ding) a seat on Nuro’s board. A second, U.S.-based, round in June 2017 raised Nuro’s total Series A funding to $92 million. But it was the monster $940 million investment made by the SoftBank Vision Fund in February 2019 that catapulted Nuro ahead of numerous other startups attempting to commercialize autonomous vehicle technology. Nuro had a $2.7 billion valuation following the SoftBank investment, meaning its value doubled in about 18 months. That money has helped it grow to more than 650 employees.
Unlike many other startups in the AV industry, Nuro has focused its effort on designing a low-speed electric self-driving vehicle that transports packages, not people. Some of Nuro’s first tests and pilots were with Toyota Prius vehicles equipped with its self-driving system. Nuro partnered in 2018 with Kroger to pilot a delivery service in Arizona. The pilot, which initially used Toyota Prius vehicles, transitioned to its R1 delivery bot. Nuro has also partnered with companies like CVS, Domino’s, and Walmart.
The company has since developed a second-generation vehicle, known as the R2. This delivery bot, which is designed for local delivery service for restaurants, grocery stores, and other businesses, received an exemption from the federal government earlier this year that allows it to operate as a driverless vehicle.
“We are witnessing an unprecedented shift in consumer demand for safe and affordable local delivery services,” Zhu, CEO, and co-founder of Nuro said in a statement. “This funding, which brings us together with many of the world’s top investors, positions Nuro confidently toward a future where our world-class technology is adopted into people’s everyday lives.”
The company, which is testing and operating R2 on public roads in Arizona, California, and Texas, told TechCrunch that the new funding will allow it to “confidently grow for years to come, with multi-year runway to build in multiple cities and scale across multiple markets.” Nuro’s near-term focus is on scaling its service in Houston and implementing R2 into commercial service.
The Farm Of The Future Might Be In Compton. Inside A Warehouse. And Run Partly By Robots
Plenty wants to build at least 500 of these vertical farms around the planet, especially in densely populated cities of at least 1 million people
BY STEFAN A. SLATER IN FOOD
OCTOBER 6, 2020
Lettuce grows in a vertical farm at Urban Crop Solutions in Waregem, Belgium, on September 20, 2016. (JOHN THYS/AFP via Getty Images)
From the outside, the gray and white warehouse near the corner of Oris Street and Mona Boulevard seems like a thousand other mundane Southern California buildings. But the interior, once completed, will resemble a sketch from a futurist's daydreams. If all goes well, the 95,000-square-foot Compton facility will house rows of hydroponic towers organized into emerald walls of non-GMO, pesticide-free leafy greens. These plants won't rely on sunlight in order to grow. Gleaming LED lamps will provide all the light the crops could ever want. Robots will transport seedlings while other machines move the towers as part of an orchestrated production process. Picture a grow room in a futuristic Martian colony and you're probably on the right track.
The exterior of Plenty's vertical farming facility in Compton. (Stefan Slater for LAist)
The operation is run by Plenty, a San Francisco-based startup that uses vertical farming to create high-quality, nutritious plants "you'd actually want to eat" (their words). Stated another way, they grow crops, often without natural light or soil, in vertically stacked beds in enclosed and controlled environments.
Plenty wants to build at least 500 of these vertical farms around the planet, especially in densely populated cities of at least 1 million people.
The first Plenty farm, in South San Francisco, went into production in 2018 and was upgraded in the summer of 2019 to increase production. For its agricultural second act, the company chose Compton.
A farm operations associate in front of leafy greens growing in vertical towers at Plenty's vertical farming facility in South San Francisco. (Spencer Lowell/Courtesy of Plenty)
Plenty's long-term goals go beyond tasty salad greens. It wants to combat food apartheid by bringing healthy, locally-grown crops to communities that lack access to nutritious produce.
"We want to invest in places where we can serve a large number of people," says Shireen Santosham, the company's head of strategic initiatives. "Compton can help us better serve Los Angeles while also allowing us to invest in a community with a long history of farming."
The goal for Plenty's Compton outpost, once it's running at full capacity, will be to create enough produce to make regular deliveries to hundreds of grocery stores. In early August, the company reached an agreement with Albertsons to provide 430 of its California stores with assorted leafy greens.
Company reps say the Compton site will initially focus on producing kale, arugula, fennel, and bok choy before adding strawberries to its repertoire. They expect prices to be similar to organic leafy greens currently on grocery store shelves.
The company was hoping its Compton farm would be able to bring produce to market by the end of 2020 but the coronavirus pandemic altered that timeline. Plenty now hopes to start its first customer deliveries sometime in 2021.
A view of the grow space at Plenty's vertical farming facility in South San Francisco as seen through the vestibule window. (Spencer Lowell/Courtesy of Plenty)
WHY COMPTON?
Los Angeles has for centuries been a land of citrus groves, peaches, olives, and even vineyards, and Compton was no exception. In the late 1860s, Reverend Griffith Dickenson Compton led roughly 30 people from Stockton to settle in and cultivate the area. Rough weather and tremendous floods nearly destroyed their dreams, but they persisted, and their agricultural efforts eventually began to thrive.
A drawing of the Compton farm and Star Cheese Dairy of Omri J. Bullis in 1880. It was located on Alameda Street, north of El Segundo Blvd. (Security Pacific National Bank Collection/Los Angeles Public Library Collection)
In 1888, Compton donated his land and the area was incorporated as the city of Compton under the condition that a swath of it be zoned for agriculture. That particular area — a 10-block neighborhood sandwiched between downtown Compton and what's now the 91 Freeway — became Richland Farms, known for a variety of crops including pumpkins, sugar beets, and cauliflower. By the 1940s and '50s, Compton had become a working-class suburb. African American families, many of whom had moved to the West Coast to work in military production during World War II, settled there and were drawn to the Richland Farms neighborhood. With its large lots and agricultural zoning, residents could grow crops and raise livestock to provide for their families and their community.
Richland Farms — home of the Compton Cowboys — remains a living link to Compton's agricultural past. Drawing on that history, Plenty began designing and developing its Compton vertical farm (located a few miles north of Richland) in the summer of 2019.
"There is just a rich tradition of farming in Compton, and to have Plenty come back in an innovative way is exciting for our community," Compton Mayor Aja Brown says.
City officials are working with the company to connect its facility with nearby schools so kids can learn about vertical farming and the technologies associated with it.
A farm operations associate tends to plants in the grow space at Plenty's vertical farming facility in South San Francisco. (Spencer Lowell/Courtesy of Plenty)
OK, BUT WHAT EXACTLY IS A VERTICAL FARM?
Compared to traditional field agriculture, which humanity first started tinkering with approximately 12,000 years ago, vertical farming is in its infancy.
One of the first vertical farms was a hydroponic system built-in Armenia sometime before the early 1950s, although there's not much information about it.
The modern vertical farm, at least in the way we think of it, was popularized two decades ago by Dickson Despommier, an emeritus professor of public and environmental health at Columbia University.
Baby kale is grown at AeroFarms on February 19, 2019, in Newark, New Jersey. (ANGELA WEISS/AFP via Getty Images)
In 1999, he wanted students in his medical ecology class to explore ways they could feed New York's residents on crops grown entirely within the city. They started with rooftop gardens but those barely made a dent in the amount of food they needed. Then, Despommier remembered the city's abandoned buildings. "What if you could fill up those buildings with the grow system that you've instituted on the rooftop and just increase food production?" he says.
The result was a multi-level, urban farm featuring layers of crops stacked on top of one another.
Greens growing at Bowery Farming, a vertical farm in Kearny, New Jersey, on January 28, 2019. (DON EMMERT/AFP via Getty Images)
Until the 21st century, commercial vertical farming seemed like the stuff of utopias, a grand if impractical dream evangelized by a handful of futurists and agricultural techies. But the last few years have seen a jump in interest — and venture capital. Between 2016 and 2017, investments in vertical farming grew nearly eightfold.
In 2017, Plenty received $200 million from several high-profile investors including Alphabet chairman Eric Schmidt and Amazon founder Jeff Bezos. One of its East Coast competitors, Bowery Farming, received a $90 million investment from Google Ventures.
The UAE's Badia Farms in Dubai, seen on August 4, 2020, uses hydroponic technology and vertical growing towers to produce fruits and vegetables year-round. (KARIM SAHIB/AFP via Getty Images)
AeroFarms, which uses aeroponics to grow produce, scored $40 million from IKEA and Sheikh Mohammed bin Rashid of Dubai. The United Arab Emirates is also hoping vertical farming will boost the country's limited domestic food production. The Abu Dhabi Investment Office sunk $100 million into four ag-tech companies, including Aerofarms, which plans to build a new vertical farm and R&D center in Abu Dhabi.
Two farm operations associates tend to plants in the grow space at Plenty's vertical farming facility in South San Francisco. (Spencer Lowell/Courtesy of Plenty)
WHY DO WE NEED THEM?
Vertical farming is all about efficiency. The process allows growers to control and monitor light, oxygen, nutrients, temperature, humidity, and carbon dioxide levels. In a vertical farm, you don't need to wait for the right season. Growth and harvesting can occur year-round.
Plenty's approach relies on automation, intricate sensors, machine learning and hydroponic grow towers where plants are cultivated in a nutrient-rich water solution instead of soil. With this method, the company claims it can grow 350 times as much produce, per square foot, as a conventional, outdoor farm — all while consuming a fraction of the water.
"[Vertical farms] are much more water-use efficient than field production," Neil Mattson, associate professor of plant science at Cornell University, says.
Santosham claims Plenty's vertical farms will use "about 1% of the land and 5% of the water" required by a comparable traditional farm.
Producing more food with less land is a must if we want to keep humanity fed.
A worker tends to basilicum plants at an indoor vertical farm at Colruyt Group in Halle, Belgium on March 3, 2020. (THIERRY ROGE/BELGA MAG/AFP via Getty Images)
By 2050, Earth will have 9.8 billion residents and two-thirds of them will probably live in a city. In places like Los Angeles or New York, where real estate doesn't come cheap, vertical farms could be installed without taking up much space.
Produce from vertical farms would also be less likely to spoil since it would, in theory, only travel a few miles to the nearest grocery store, market or restaurant, instead of sitting on a plane or cargo ship for hundreds or thousands of miles.
Plus, vertical farms could help make our food supply chain more resilient.
Since March, the pandemic has impacted everything from beans to strawberries. When the hospitality industry shut down, some farmers had buyers for only half of their crops, so they had to let them rot or plow them back into the soil. Dairy farmers dumped millions of gallons of milk. Meat plants have had to shut down due to COVID-19 outbreaks. Plus, the workers who pick the crops, raise the cows and run the slaughterhouses have been ravaged by the virus. And all of this has been happening while hunger skyrockets. In the last six months, food banks have seen a surge in demand, in some cases by as much as 600% percent.
"I don't think all of our food is going to come from urban production," Mattson says. "It does add diversity to our food supply chain to have some of our produce — the nutrient-dense foods — come from close to where they're consumed."
With COVID-19 exposing the weaknesses in our food supply chain, Mattson believes indoor growing (which includes vertical farming and greenhouses) and more localized production might get their moment in the high-intensity LED spotlight: "We're going to see these trends happen even quicker than if we hadn't encountered COVID."
The central processing area at Plenty's vertical farming facility in South San Francisco. (Spencer Lowell/Courtesy of Plenty)
A PEEK INSIDE
The Compton farm is still under construction but the company is using its existing South San Francisco facility as a template.
That facility, which started in 2015 as a container farm, features 50,000 square feet of production space and a roughly 10,000-square foot grow room. It provides produce to approximately 40 grocery stores and runs entirely on solar and wind power.
The Compton farm will feature a similar grow system. Employees, referred to as growers, will oversee the process of cultivating seeds into seedlings. Robotics will transfer the seedlings to large vertical grow towers, arranged to form what looks like a vast, green wall.
The amount of time produce spends in the grow room depends on the crop. Nate Storey, chief science officer and co-founder of Plenty, explains that one leafy green crop might go through the entire process from seedling production to harvesting in two to three weeks. That's significantly less time than if those crops were grown via traditional agriculture.
Laborers harvest romaine lettuce using a machine with heavy plastic dividers that separate them from each other on April 27, 2020, in Greenfield, Monterey County, California. (Brent Stirton/Getty Images)
On a large, outdoor farm in the Salinas Valley, baby kale would typically require 35 to 50 days, depending on the time of year, before it was ready for harvest, according to Richard Smith, a University of California Cooperative Extension vegetable advisor for the Central Coast.
"For something like lettuce, where you might be waiting for several weeks in the field, we're carving a significant amount of time off that production schedule," Storey says.
A post-harvest associate inspects produce for packaging at Plenty's vertical farming facility in South San Francisco. (Spencer Lowell/Courtesy of Plenty)
Once the plants spend some time in Plenty's grow room, robots pick up the towers and retrieve the produce, which is moved to a processing area where it's packaged. Through it all, human hands never touch the food.
"We're able to create an environment that's so favorable to plants and not pathogens or pests that we can deliver a product without ever applying pesticides, which is a big win," says Nick Kalayjian, senior vice president of engineering at Plenty.
In fact, without bugs or human contact, he claims Plenty's produce doesn't need to be washed. Kalayjian also says the small adjustments in temperature, water, nutrients and light result in produce that's at the peak of flavor.
Plenty sent me samples of their baby kale, baby arugula and Sweet Sunrise mix, a combo of fennel, beet leaves and other greens. Did visions of tree stars seize me and shatter all perception of space and time? No. But they did taste exceptionally fresh. The flavors were strong, clean and... just good. I found myself snacking on the Sunrise mix straight from the package, something I never do with greens.
A farm operations associate tends to plants in the grow space at Plenty's vertical farming facility in South San Francisco. (Spencer Lowell/Courtesy of Plenty)
WHERE DO WE GROW FROM HERE?
Vertical farms aren't cheap to build. They also require a lot of energy to run, much more than conventional field agriculture or greenhouses. "That, to me, is one of the big sticking points," Mattson says.
In a 2020 study, Mattson and other Cornell University researchers studied the economic and environmental impacts of bringing leaf lettuce to U.S. cities via field-based agriculture vs. CEA (controlled environmental agriculture) supply chains such as greenhouses and vertical farms.
"We had almost the same carbon footprint of growing in a greenhouse in New York City as compared to field growing and shipping 3,000 miles. The vertical farm had about twice the carbon footprint of either of those," Mattson says.
In Plenty's case, making sure their farms operate on sustainable, renewable power is a priority. The South San Francisco facility has a power purchase agreement in place with a renewable provider to supply the farm with sustainable energy. Plenty wants its Compton farm to run entirely on clean energy but that won't happen until some undetermined point in the future. Company reps couldn't offer a more precise timeline on when that might happen.
Various leafy greens grow in vertical towers at Plenty's vertical farming facility in South San Francisco. (Spencer Lowell/Courtesy of Plenty)
Warehouse-sized vertical farms may someday be common sights in major cities but it'll take time to scale up to that level. No one, except maybe the most optimistic futurists, thinks vertical farming is going to overtake field agriculture anytime soon.
"We're an additive technology, not a replacement technology. We simplify the supply chain and allow domestic production in places that don't currently have it," Kalayjian says.
A worker tends to lettuce under artificial lights at the Pink Farms warehouse in Sao Paulo, Brazil, on August 28, 2020. (JONNE RORIZ/AFP via Getty Images)
Although vertical farming is still in its earliest stages, Despommier urges us to imagine how it might work in 50 years. "We're looking at a sort of Stanley Steamer [car], not even a Ford Model T," he says, "We're looking at the early trials and tribulations of an industry that wants to supply all of your food. Look how fast it took America to go from no cars to two cars per person."
Maybe by the time humanity has figured out how to colonize other planets and build Star Trek-style replicators, the urban dwellers of earth will rely on skyscraper-style vertical farms. Maybe thousand-acre fields of fruit and vegetables will someday look as obsolete as rotary phones. Until then, we'll be playing in the dirt, just as we've done for thousands of years.
Fresh Produce, Brought To You By Robots
IN SAN CARLOS, CALIFORNIA, UNDER LED lighting in a controlled, 8,000-square-foot environment, a team of autonomous robots is whirring night and day between rows of leafy greens
A Family-Owned Market In California
Is Now Selling Robot-Reared Leafy Greens
BY LUKE FATER AUGUST 08, 2019
An industrial robotic arm with custom gripper and sensors constantly reorganizes plants as they grow. IRON OX
IN SAN CARLOS, CALIFORNIA, UNDER LED lighting in a controlled, 8,000-square-foot environment, a team of autonomous robots is whirring night and day between rows of leafy greens. There is no dirt, there are no pesticides, and on this indoor farm, the only humans work behind screens. This is one of the world’s first autonomously operated commercial farms, and their produce is now flying off the shelves.
As a child, roboticist Brandon Alexander spent summers in Oklahoma helping his grandfather grow potatoes, peanuts, and cotton on a 6,000-acre farm. But as CEO of Iron Ox, the start-up company behind the automated farm, he says traditional farming is now his biggest competition—and granddad understands. “He knows that for farming to survive, this is almost inevitable,” says Alexander.
At Bianchini’s Market, a family-owned grocery in the San Francisco Bay Area, the two worlds are competing for the first time. As it stands, the robots are holding their own: Between retail buyers and several local restaurants, including San Francisco’s Trace, Iron Ox saw sales more than double last quarter.
Compact spacing techniques unique to hydroponic farms allow Iron Ox to grow 30 times the yield per acre compared to outdoor farming, according to Alexander. IRON OX
The San Carlos operation is not completely automated just yet. Human staff still plant the initial seed and handle post-harvest packaging. But the rest is left to robots.
Angus, a half-ton aluminum porter, roams the “field” of trays, or pallets, 24/7 with an overhead camera. On traditional farms, plants need space for their roots to absorb nutrients; on hydroponic farms, however, seeds can be planted in their trays mere inches apart. As they grow and begin crowding each other, though, this does require more attention from, say, a sleepless robot. Angus carries the 800-pound pallets in need of rearranging to a separate, industrial robotic arm that gently re-shuffles the growing pods into new compact rows. Angus is also responsible for IPM (integrated pest management) and scanning for aphids, mildew, and browning.
The robotic arm’s stereo-camera (“two cameras that kind of mimic your eyes,” Alexander casually explains) creates a 3-D model of at-risk produce that’s run through a machine algorithm to diagnose the issue and quarantine or prune accordingly. “The Brain,” a cloud-based AI software, coordinates all these autonomous functions while monitoring light, nitrogen, and water levels. “It’s a neighborhood farm,” says Alexander.
A 1,000-pound aluminum porter named Angus scans for crowding, carrying plant pallets to a separate robotic arm for rearranging. IRON OX
He’s not wrong. Produce from Iron Ox travels less than a mile to reach Bianchini’s—itself a mere 25 miles from downtown San Francisco. In fact, evening shoppers at Bianchini can buy produce robo-picked that morning, and at price points that compete with outdoor farms: A bunch of basil sells for $2.99; four heads of baby lettuce for $4.99; and a bunch of red-veined sorrel for $2.99.
Typically, the cost of human labor required for indoor hydroponic farms has made their produce inaccessibly expensive. Jake Counne of Backyard Fresh Farms, a similarly autonomously assisted farm in Chicago, told the Chicago Tribune that employing robotics reduced his labor costs by 80 percent. For this reason, building a farm around robotics and A.I. could crack the code of making indoor farms feasible. And while Alexander’s leafy greens remain local, the consequences of Iron Ox’s success may not.
Using robotics to make indoor hydroponic farms practical could alleviate a host of agricultural problems. In 2016, World Water Forum cited farming as a major contributor to global water scarcity. But farms like Iron Ox use 90 percent less water than outdoor farms. In a 2019 report on the challenges of feeding 10 billion people by 2050, The World Resources Institute cites concern over “the difference between global agricultural land area in 2010 and the area required in 2050 … if crop yields continue to grow at past rates.” According to Alexander, Iron Ox yields 30 times more produce per acre over the course of a year than conventional farms, and without using any arable land. A 2016 report from the National Center for Biotechnology on Chemical Pesticides urged a “drastic reduction in the use of agrochemicals,” and indoor farms alleviate the need for herbicides and pesticides.
This vision-enabled robot runs 3-D scanned models of the plants through a machine learning algorithm for quality control. IRON OX
For now, Iron Ox’s goals are more pointed. “How can we make your salad pop? We try to prioritize that,” Alexander says. Following the success of the San Carlos location, he does plan to set up robotic farms near other U.S. cities, though he’s not announcing anything yet. Iron Ox is, however, hiring humans for plant science and growing teams.
Gastro Obscura covers the world’s most wondrous food and drink.
Sign up for our email, delivered twice a week
Indoor Farmers Bet On Robots, AI
While the first versions of modern vertical farms sprouted about a decade ago, in recent years the introduction of automation and the tracking of data to regulating light and water has allowed them to get out of lab mode and into stores. Now they are trying to scale up
Erik Groszyk, 30, used to spend his day as an investment banker working on spreadsheets. Now, he blasts rapper Kendrick Lamar while harvesting crops from his own urban farm out of a shipping container in a parking lot in Brooklyn, New York, US. REUTERS/Mike Segar/Files
Leafy salad greens grown under banks of LED lights, with mist or drips of water are having their day in the sun. Several top US indoor farms, stacked with plants from floor to ceiling, tell Reuters they are boosting production to a level where they can now supply hundreds of grocery stores.
Plenty, Bowery, Aerofarms, and 80 Acres Farms are among young companies that see a future in salad greens and other produce grown in what are called vertical farms that rely on robotics and artificial intelligence, along with LED lights.
While the first versions of modern vertical farms sprouted about a decade ago, in recent years the introduction of automation and the tracking of data to regulating light and water has allowed them to get out of lab mode and into stores. Now they are trying to scale up.
Plenty and others say their customized, controlled lighting — some more blue light here, some more red light there — makes for tastier plants compared to sun-grown leaves and that they use 95 percent less water than conventional farms, require very little land, and use no pesticides, making them competitive with organic farms.
And because vertical farms exist in windowless buildings that can be located in the heart of urban areas, produce does not have to travel far by fossil-fuel-guzzling trucks to reach stores.
The companies’ expansion comes as plant-based burger makers Beyond Meat Inc and Impossible Foods captivate investors and make inroads in high-end restaurants and fast-food chains.
But whether the sunless farms can compete financially with their field-grown brethren, given big upfront investments and electric bills, remains a question.
“We’re competitive with organic today and we’re working very hard to continue to make more and more crops grocery store competitive,” said Matt Barnard, chief executive and co-founder of Plenty, which is based in Silicon Valley.
Plenty’s salads sell on organic grocery delivery site Good Eggs for 99 cents an ounce, while a leading brand, Organic Girl, on grocery chain Safeway’s online site was priced at 80 cents an ounce.
Plenty said its new farm, dubbed “Tigris,” can produce enough leafy greens to supply over 100 stores, compared with its previous farm that could only supply three stores and some restaurants.
The technology world is paying attention. In its last round in 2017 Plenty raised about $200 million from investors including Japan’s Softbank, Amazon founder and CEO Jeff Bezos and former Alphabet Chairman Eric Schmidt. New York City-based Bowery raised $95 million in a fund-raising round led by Google Ventures and Temasek last year.
LED lights glow from a cluster of 10 hydroponic climate-controlled farms housed in repurposed 320-square-foot metal shipping containers where entrepreneur farmers enrolled in the "Square Roots" farming program are growing and selling a variety of organic greens in the parking lot of a former Pfizer factory in Brooklyn, New York, US. REUTERS/Mike Segar/Files
Bowery said its third farm coming online soon will help it supply hundreds of stores from dozens today, and Aerofarms, in New Jersey, said it is doubling its space to meet demand.
None of the three companies would give details about costs.
Former Vertical Farm CEO Matt Matros is sceptical that sunless farms can make economic sense. He invested in and ran Chicago-based FarmedHere in 2015, but changed its business into food processing.
“The issue with indoor farming was that you could really only grow a couple things efficiently — namely basil and micro greens. But the problem is the world just doesn’t need that much basil and micro greens,” Matros said.
80 Acres Farms in Cincinnati says it already grows and sells tomatoes and cucumbers, and Plenty is testing cherry tomatoes and strawberries in the lab.
Agriculture technology investor Michael Rose says vertical sunless farms are more expensive to run than modern greenhouses that rely on sunlight, supplemented by LED lights. He sees limited areas where it makes sense, such as the Middle East, where much of the food is imported, or China’s mega-cities where pollution and urban sprawl limit the availability of premium fresh food.
At Plenty’s new farm, robots put seedlings in tall, vertically hung planters. The planters move along a wall of LED lights for 10 days and are then put through a harvesting machine that shaves off the leafy greens.
The machines minimize labour needs, and Plenty says the speed of production also helps control pests.
“We use no pesticides,” said Nate Storey, co-founder and chief scientist at Plenty. “We don’t even have to use things like ladybugs, because we go so fast in our production that we out-race the pests themselves.”
Robots Are Already Farming Crops Inside This Silicon Valley Warehouse
Indoor farming company Plenty’s new, bigger operation wants to deliver fresh greens, any time of year. And its robot farm workers help it optimize growing conditions to make the most delicious produce
06.20.19
Indoor farming company Plenty’s new, bigger operation wants to deliver fresh greens, any time of year. And its robot farm workers help it optimize growing conditions to make the most delicious produce.
1/7 [Photo: Spencer Lowell/courtesy Plenty Farms]
Inside a cavernous warehouse in South San Francisco, 16-foot-tall walls of kale and other greens stretch down aisles twice the length of a bowling lane. Matt Barnard, CEO and cofounder of Plenty, the startup that designed and built the indoor farm, points to two types of mustard greens called mizuna and tatsoi. “This is one of the blends that we are working to position against junk food,” he says.
Barnard wants to change how the world eats by changing how food is grown. The new farm, which will begin selling produce to San Franciscans later this year, is the latest iteration of its indoor growing system, designed to grow food as efficiently as possible in any space, so cities anywhere can have access to locally grown vegetables—optimized for flavor—at any time of year. When I first visited the company’s headquarters in 2017, it used only a small amount of the space, a former electronics distribution center in an industrial neighborhood. A few months later, Softbank led a $200 million investment round in the startup. The new version of Plenty’s farm now sprawls over a much larger part of its headquarters, and the company plans to eventually replicate it near large cities globally.
[Photo: Spencer Lowell/courtesy Plenty Farms]
Each step in the process is now automated. In one corner of the massive warehouse, a bright yellow robot picks up a tower filled with kale that was growing, minutes earlier, in one of the aisles of greens next door. Gently turning the tower on its side, the robot sets it on a conveyor belt where a spinning wheel neatly trims the greens to harvest them. When the farm opens, this will be one of the last steps before produce is delivered to grocery stores or directly to consumers (the company already sells greens from its earlier, smaller farm through a local food delivery service called Good Eggs, along with some independent groceries). In another corner, robots pack trays with soil and seeds and deliver them to another room to germinate. Along another wall, four robots inside glass boxes carefully lift seedlings out of trays and plant them into the tall white growing towers. Back in the growing room, infrared cameras and sensors monitor the indoor climate, and software adjusts details like the precise “recipe” for light or water to create the best flavor in the plants.
“We essentially coax a different flavor profile out of the plants by giving them the right recipe,” says Barnard. Each day, the company runs harvested crops through its “sensory” department, evaluating factors like size and flavor and tweaking the growing environment as needed for the next crop. “We take those plants and analyze what’s in them, and then we work to give subsequent crops exactly the right recipe so that these things are lovable. And that’s critical. That’s how we get to 10-year-olds asking their mothers for our kale.”
[Photo: courtesy Plenty Farms]
Right now, only around 1 in 10 Americans eat as many fruits and vegetables each day as federal guidelines recommend. If it’s possible to buy local, freshly harvested produce in Minneapolis in February—rather than wilted greens that spent a week on a truck from Arizona or California—Plenty believes that people will be more likely to want to eat them. Because the company can control the growing environment, it says that it can achieve flavors that aren’t consistently possible in fields. It can also sell varieties of produce that are too delicate to survive current supply chains. Consumers don’t really want to buy iceberg lettuce, Barnard says. But it’s a huge crop because it can survive both difficult growing conditions on farms and then travel thousands of miles. With a local journey, Plenty can sell crops that don’t exist in typical supermarkets now. I tasted wasabi arugula, a spicy wild green that mimics the heat of the Japanese condiment.
The company wouldn’t comment on the cost of its system. But it says that it’s still possible to sell greens at the same cost as those grown on a traditional farm. One of the largest costs for indoor farms is energy use, especially from lighting; in the last year, Plenty cut energy consumption by 80% per kilogram of plants grown, and it expects to cut that further. Roughly a third of the value of vegetables sold in the eastern U.S., it says, comes from transportation from farms in places like California or Mexico. Indoor farms can also avoid the cost of days in distribution centers and other parts of those long supply chains. There’s also intrinsic value for consumers in the fact that greens grown in food safety-certified facilities can avoid the contamination that sometimes happens outdoors. In 2018, in three outbreaks, romaine lettuce grown on traditional farms caused 300 infections and hospitalized 128 people; six died. Water contamination from nearby livestock was the culprit. Plenty uses purified tap water inside a space so pristine that it doesn’t have to treat its greens for them to be safe to eat (“prewashed” greens from farms are often washed in bleach in an attempt to kill germs).
Indoor farming still hasn’t proven itself at scale. Aerofarms, another startup with a massive indoor farm at its headquarters in Newark, New Jersey, said in 2015 that it expected to build 25 farms over the next five years; to date, it has built one large farm in addition to its headquarters. FarmedHere, which said in 2015 that it planned to build 18 farms near major cities. Two years later, the company shut down. Bowery, a New York-based, Alphabet-backed startup that also uses robotics, has two farms so far, though it raised a $90 million round of investment in late 2018 and plans to expand. Plenty itself had planned to open a farm near Seattle by this point, but decided to focus on building its tech platform. Still, it can move quickly: The company completed the design for its new automated Bay Area farm last November, began construction in December, and was operational by March.
To begin with, like other companies in this space, Plenty is growing greens, because they are particularly economical to grow in this way. But at another location in Wyoming, where it tests new varieties of crops—700 over the last year—it is also perfecting the “recipes” to grow foods like strawberries and tomatoes. Indoor growing is unlikely to ever replace growing in fields, both because some crops are better suited for outdoor growing and because of the scale required. But as available space for farmland shrinks and the global population grows, indoor farming could help fill some of the gap. Plenty declined to share the exact size of its new farm or expected annual production, but depending on the crop, the company’s indoor growing system can produce between 150 and 350 times as much produce as the same crop in a field. It could also become more necessary in some areas as outdoor farms struggle with drought, heat waves, flooding, and other impacts from climate change. Indoor farms use a small fraction of the water required in places like California.
Barnard believes that the company can grow quickly. “I think people are going to be stunned at the speed with which a lot of what’s available in the fruit and vegetable aisle is from a Plenty farm or from an indoor farm,” he says.
ABOUT THE AUTHOR
Adele Peters is a staff writer at Fast Company who focuses on solutions to some of the world's largest problems, from climate change to homelessness. Previously, she worked with GOOD, BioLite, and the Sustainable Products and Solutions program at UC Berkeley.
Robot Farming Startup Iron Ox Sells First Produce In California
Robot farming startup Iron Ox has announced that it’s selling robot-reared leafy greens in a single location in California. The firm, which launched last October, is offering three varieties of greens at the San Carlos branch of Bianchini’s Market, a family-owned grocery store that specializes in local and organic produce.
Iron Ox is one of a number of companies trying to automate the human-intensive work of agriculture. It uses a combination of robotic picking arms, hydroponic vats, and self-driving porters to grow vegetables. But despite its repeated claims that its farming is “autonomous,” humans are still needed for a lot of the work. Laborers plant seedlings and package plants when they’re ready to eat: robots just tend them while they’re growing.
One benefit is that robot farms can be located nearer to customers because of their smaller physical footprint. Iron Ox says the greens it’s producing for Bianchini’s travel just 0.6 miles to get there, which is half the distance traveled by a typical head of lettuce. This means lower transportation costs and fewer food miles, a big factor when it comes to the environmental impact of what you put on your plate.
But the scale of Iron Ox’s operation is limited. It’s selling just three varieties of leafy greens and delivering them to Bianchini’s just once a week. The prices aren’t exorbitant, but they are on the expensive side. A two-ounce box of red-veined sorrel will go for $2.49, a two-ounce box of Genevieve basil will cost $2.99, and four heads of baby lettuce will be $4.99.
Source: www.theverge.com
Publication date: 5/3/2019
Does AI Hold The Key To A New And Improved “Green Revolution” In Agriculture?
Producing enough healthy food to feed the world—on a changing planet—is going to be a steep challenge. These researchers are giving farmers AI-driven techniques and tools to find solutions
Producing enough healthy food to feed the world—on a changing planet—is going to be a steep challenge. These researchers are giving farmers AI-driven techniques and tools to find solutions.
BYJACKIE SNOW FEBRUARY 19, 2019 NOVA NEXT
Automation in agriculture may soon make robots as common in greenhouses as they are on factory floors. Photo credit: Shutterstock
On a stretch of highway in the Netherlands not far outside of Amsterdam, a row of greenhouses at Wageningen University & Research (WUR) poke up like knuckles along the flat landscape. The Dutch university is known for its cutting-edge agricultural research, but some of these greenhouses recently ran an experiment that’s novel even for them: autonomous growing.
Stepping into a humid box from a brisk autumn day, you hear the noises of machines adjusting themselves mixing with the sounds of leaves rustling. The amount of light, water, fertilizers, and carbon dioxide—along with the temperature of the greenhouse—are all set by deep learning algorithms and executed by machines. Humans are still responsible for moving vines up the lattices as they grow, as well as pruning and harvesting.
But it’s pretty clear who—or rather, what—is calling the shots.
The Future of Farming?
By 2050, we’ll need to feed nine billion people with about a third less arable land than we had in the 1970s, experts estimate. Farmers will need all the help they can get, including insights gleaned from artificial intelligence, or AI. Developed carefully—and with the people who will be using it taken into account—AI can be part of the solution to feeding a growing world, according to the Refresh report, a document put together by researchers from Google, university professors, nonprofits, and farmers. And as an added bonus, some of the unsustainable practices developed over the past 70 years could be reversed with more efficient, AI-driven technology.
The Green Revolution was a set of advances that started in the 1950s in areas like high-yield crops, synthetic fertilizers, and irrigation technology that greatly increased food production, especially in developing countries—saving an estimated one billion people from starvation. But it left in its wake a culture of pesticides, reduced agricultural biodiversity, and overuse of chemical fertilizers that deplete the soil and poison waterways.
“It was never meant to be used in the long term,” says Danielle Nierenberg, the president of Food Tank, a non-profit working to build a better food system that also worked on the Refresh document. Farmers were supposed to transition back to organic, Nierenberg adds: It just never happened because increased yields generated by industrial-scale farming put pressure on smaller farms to follow suit.
One of the main ways AI could help agriculture transition out of practices forged in the Green Revolution and into a more sustainable future is with precision farming. Until now, there hasn’t been an easy way for farmers to learn from historical or real-time data. But AI-powered programs can combine data on weather patterns, crop yields, market prices, and more to guide farmers to planting at the right time, adding the appropriate level of fertilizers, and harvesting at peak ripeness.
WUR is one of the places where big data approaches to growing food are being tested. Last fall, five teams of AI researchers and biologists from around the world competed in growing cucumbers in separate 96-square-meter greenhouses, with a sixth grown manually as a reference. Each team trained its own algorithm, although the teams had the ability to decide how closely to follow the solutions that their AI models came up with. The teams kept an eye on their crops with sensors and cameras, and could feed the algorithms new data and tweak them as needed. To win, teams had to maximize total yield and net profits while minimizing the use of resources.
The winner was a team called Sonoma, made up of Microsoft Research employees and students from Danish and Dutch universities. According to Silke Hemming, head of the scientific research team for greenhouse technology at WUR, Sonoma’s plan used more artificial light earlier and kept carbon dioxide levels higher than a typical gardener might. But other teams also discovered counterintuitive ways to increase yield, such as pruning smaller cucumbers close to harvest or letting bigger ones have a chance to grow a little more.
Like all problems in AI, growing cucumbers and other crops by algorithm demands a food source of its own: data—and lots of it. The cucumber contest was a start at putting information together that other researchers can build on with future projects.
“You have a dataset you would never have,” Hemming says. “You can learn so much from that.”
The researchers organizing the competition chose cucumbers because they are a fast-growing crop cultivated worldwide, and problems like blight show up in them immediately. But this project could transform how other indoor crops are grown. It’s a first step in finding ways to combine humans and AI technology to produce more food, more efficiently.
“It’s not all about winning.” Hemming says. “It’s also about learning.”
FARMWAVE Founder and CEO Craig Ganssle uses its smartphone app with an automated kernel count feature to assess corn yield. Photo credit: FARMWAVE
AI on the Farm
“Farming is a lot more complicated than other industries,” says Joshua Woodard, an agricultural business and finance professor at Cornell and founder of the farming data company Ag-Analytics. “It’s a really complex system of environment and management practices."
Ag-Analytics’s wants to bridge that gap with easy-to-use data analysis tools to help farmers plan and monitor their fields. Their farm management platform takes data from sensors in John Deere farm equipment and combines it with other datasets, like satellite imagery and weather forecasts, to develop predictions for individual farms.
Algorithms working from afar could make a huge impact for less tech-heavy farms, too. Farmers in the developing world are working with minimal data and stand to make leaps in productivity with algorithms in the cloud instead of expensive machinery in their fields. According to the United Nations, 20 to 40 percent of crop yields are lost each year due to pests and diseases. AI tools like Plant Village and FARMWAVE allow farmers to take photos with their phones of sickly plants, bugs, and weeds, and then have computer vision-powered algorithms diagnose the problem from afar in seconds. FARMWAVE is already working with farmers in countries across the world, who, despite their distance, are all dealing with similar problems that AI can spot.
"Army worm in corn looks the same in Africa versus the U.S.,” says Craig Ganssle, the founder and CEO of FARMWAVE.
In India, a team at the International Crops Research Institute for the Semi-Arid Tropics (ICRISAT) is working on providing real-time pest predictions to help Indian farmers take specific actions to protect their crops. ICRISAT uses cloud computing, machine learning, and data from IoT (short for the “Internet of Things”) sensors to come up with personalized predictions about pest risks.
Dr Avijit Tarafdar of ICRISAT converses with chickpea farmer Mr Srinivasa Boreddy in Adilabad District, Telangana. Photo credit: D Chobe, ICRISAT
“Whenever [farmers] see the pests in the field, they simply go for pesticides,” says Dr. Mamta Sharma, a principal scientist at ICRISAT. “It will help them reduce the amount of sprays that farmers are applying."
ISCRISAT has offices in Africa that could eventually use the tool, with interest coming from South America as well. As these offices collect more data, Sharma says, it could be used to spot new risks due to climate change.
“It helps us recognize emerging threats,” she says.
Robot Green Thumbs
Indoor farming currently occupies around 2.3 million square feet worldwide. But based on information from growers, the analysis firm Agrilyst predicts this number will balloon to 22 million square feet over the next five years. Despite the expense of setting up these spaces and the limited types of produce that can currently be profitably grown, much of AI research is being done in greenhouses and other indoor spaces because, with the reduction of arable land, these production methods will become more critical. Indoor farming can also produce up to 20 times as much fruit and vegetables per square foot as outdoor farming, while using up to 92 percent less water, according to one study, with one company claiming it needs 99 percent less water.
In San Carlos, California, two robots cruise within a hydroponic farm developed by the start-up Iron Ox. These robots, which plan, care for, and harvest produce, are overseen by a computer program affectionately nicknamed “the Brain.” Even before the advent of AI, hydroponic systems were known to use less water, need fewer pesticides, grow faster, and produce more plants in less space. However, hydroponics are notoriously labor-intensive, requiring plants to be moved to different vats throughout the growing phase. Training robots for this monotonous task could make razor-thin profit margins a little less tight.
“A lot of things that weren’t feasible outside of a lab five years ago are possible now,” says Brandon Alexander, the CEO of Iron OX.
In the end, improved agricultural processes lead to better food options. And making small indoor farms more efficient could open up the possibilities of food grown closer to city centers. Most produce travels an average of 2,000 miles from farm to shelf in the U.S., which forces farmers to plant fruits and vegetables that can handle being transported—not necessarily those that taste good.
“Fresh produce isn’t that fresh,” Alexander says.
After improving its robotic systems, Alexander says, Iron OX’s long-term plans include breeding plants using data currently being gathered on its farm. Algorithms crunching this data and other local information, like what sells best, could replace tasteless, homogenized tomatoes and lettuce with more varieties suited to different communities’ tastes.
“We could make delicious, extra healthy things that people want to eat,” Alexander says.
Robots, Hydroponics, 'Hands In The Dirt': A Look At Who — Or What — Will Feed Us In The Future
Play
November 19, 2018
This is the first in our series "Lab to Table: The Future of Our Food" exploring the future of food. Stories will publish every Monday from now until Dec. 17. In the spring, the series will continue with another week of stories.
Lettuce grows vertically in a controlled environment using LED lights and a hydroponic growth system in the Freight Farm Leafy Green Machine. (Jesse Costa/WBUR)
When you picture a dinner plate 20 or 30 years from now, what do you see? Lab-grown meat? Gene-edited crops? Superfoods? Or, something like Soylent?
Will fresh produce be part of that imagined future, or could agriculture end up forgotten, like in the movie "WALL-E" where a human character in 2805 thinks farmers once grew crops of pizza in the ground?
That scenario might not seem like science fiction if you consider the growing body of research on the threats of climate change. A recent U.N. report predicts temperature increases will cause extreme flooding, fires and drought that would impair our global food systems. Innovators across the food industry, including here in Massachusetts, are working hard on high and low tech solutions for feeding the planet.
Robot Farming
“We are building robots that care for crops and harvest their fruits,” Joshua Lessing, founder of Root AI, explains as he buzzes us through a set of doors at Greentown Labs in Somerville. It’s a “clean tech” incubator — the largest in the U.S. — that supports entrepreneurs focused on solving environmental problems.
“People are predicting CO2 levels are going to rise faster than we ever thought, ice melt is going to happen faster than we ever imagined,” Lessing says, echoing studies and conversations happening across the food industry. “The needs for food are larger than we ever conceived.”
There will be a lot of mouths to feed in the future. The world’s population is expected to reach 9.8 billion by 2050.
“I think a lot about what we can do here in Boston with all the talent we have,” Lessing says, “looking outward into the world: 'Are these problems that I myself can sit in my lab and fix?' ”
He hopes so, and he thinks his robots can help.
Lessing shows me a video of a Root AI prototype “bot” in action. It’s a buzzing, mobile, white metal box with a 3D-mapping camera and a unique arm. It’s got a gripper designed to delicately pluck fruits and veggies — like cherry tomatoes and strawberries — off vines without damaging their delicate flesh. The bot’s robust artificial intelligence can collect and analyze crop data to determine ripeness and reduce waste.
“Its nutrition, its disease, its yield forecasting, its harvesting,” he says. “Instead of having artificial intelligence figure out if there's an adorable cat in your friend's photo, it can see food that you want to eat.”
Lessing foresees robots like his working 24/7 — year-round — rolling along tracks in huge, indoor farms made of glass and polycarbonate. He points to vast greenhouse complexes in the Netherlands as models for the future. Dutch innovators have been wildly successful in carrying forward that country’s commitment to increasing agricultural production with advanced, sustainable growing systems.
Co-founder and CEO of Root AI Joshua Lessing holds his robot’s gripper. (Andrea Shea/WBUR)
Indoor farms are scattered throughout Canada and the U.S., too. Lessing thinks all metro areas should have versions of them.
They're climate-controlled and impervious to weather, AI would make them smarter, and they’d supply regional distribution centers that he says would help reduce CO2 emissions on a massive scale.
But talk of robots raises the inevitable question: Will robots replace humans?
Lessing says no, they'll help alleviate agricultural labor shortages. He cites the worker crisis California farms have been experiencing because of immigration policy. Lessing’s robots have been tested in that state, and he says Root AI will deploy its first wave of full-time AI workers next year.
It’s not the only Boston-area company bringing high tech to farming.
Hydroponic Farming
Two Freight Farms Leafy Green Machines sit stacked in a parking lot near their headquarters in the South End of Boston. (Jesse/CostaWBUR)
As you drive on Route 93 adjacent to Boston's South End you can spot two white and green shipping containers in a parking lot, one stacked on the other. The top box has the words, “THIS IS A FARM,” in capital letters painted on its exterior. Brad McNamara, CEO of Freight Farms, acknowledges it makes a novel, 40-foot-long billboard for his South End operation.
As he pulls open the door we are met with a chilly blast of ventilated air.
“This is a Leafy Green Machine,” McNamara says, “you step through the door and all of a sudden you smell it, you feel it, you taste it — you're in a farm growing acres’ worth of produce.”
The hydroponic farm is filled with rows of vertical columns packed with vibrant, edible greens – kale, arugula, Swiss chard. McNamara and his partner launched Freight Farms in 2010 to connect more people with farming on a micro-level, year-round.
“What we saw was an opportunity to allow more people to grow food locally, and reinvent or recreate the food system for the future,” McNamara recalls.
Everything can be managed within the turn-key farm’s four walls — from seeding to harvesting to feeding.
Leafy greens grow vertically in a controlled environment using LED lights and a hydroponic system in the Freight Farm Leafy Green Machine. (Jesse Costa/WBUR)
Containers of colorful, liquid nutrients flow through tubes to plants growing in polymer mesh, not soil. Energy-efficient LED light strips hang from the ceiling and water is recirculated through a drip irrigation system that can feed up to 5,000 plants with less than 5 gallons of water a day.
And there are growing “recipes” that Freight Farms COO Jon Friedman says can be custom-designed to perfection.
“Say you wanted a more purple color in your lettuce, you would have the blue lights on for longer. If you wanted them to grow faster you might put the red lights on for longer,” he says. “There's a lot of tuning you can do to get a desired effect.”
Then Friedman opens an app on his phone called “farmhand.” It controls the system remotely.
“Right away you'll see cameras that are placed in certain spots of the farm,” he points out. “So if you wanted to just see a quick view of how the lettuce is doing you could just pop in and see, ‘Do I need to transplant today or could I wait ‘til tomorrow?' ”
The "farmhand" app allows farmers to monitor and manage their farm from their phone. (Jesse Costa/WBUR)
So you could monitor crops from, say, the couch on a snowy day. With the app, farmers — be they citizens or professionals — can adjust settings and crunch data. It even offers a Spotify playlist with nature sounds and stimulating music.
The founders say their mission is to educate and get people excited about farming. But it’s also to help small, commercial farmers evolve into the future by adding hydroponic greens to their existing soil-based operations — like Karma Farms did in Maryland.
More than 210 Leafy Green Machines can be found around the world in 14 countries — in places like a farm in Guam that sells its greens to a couple of Wendy’s on the island; a pioneering urban farm in Brooklyn; Google’s campus in California; and at schools in Boston, Salem and elsewhere in Massachusetts. And this year, the company launched a program called "Grown By Freight Farms" that even adds a farmer to help with daily maintenance 20 hours a week.
Watercress seedlings sprout beneath LED lights inside the Leafy Green Machine. (Jesse Costa/WBUR)
The cost of the shipping containers, like other farming equipment, is tax-deductible, but you’d need about $85,000 to buy one. Even so, Friedman sees a future where every workplace, urban neighborhood and farm could have one.
“In our earlier phase of agriculture, as a society, we built everything around it, but now we've gotten so distant from it at the same time,” he muses. “It’s going to be interesting to see how technology helps bring it closer to us and make that more of our experience.”
But technology is only part of the solution for Jennifer Hashley.
“To what end are we going to have all this great technology if we don't have people that can afford to start these businesses?” she asks.
Soil Farming
Jennifer Hashley, director of the New Entry Sustainable Farming Project, grabs a handful of peppers for farm share orders in Lowell. (Jesse Costa/WBUR)
Hashley runs the New Entry Sustainable Farming Project at Tufts University where future farmers learn all aspects of the business of local agriculture.
“We still need people to have their hands in the dirt," she says. "As much as we want to rely on technology for advances in productivity and knowledge and data and efficiencies and to save labor — all those things are wonderful — but we're still going to need people to understand natural ecosystems."
Standing in a warehouse on the outskirts of Lowell, some of the students in the program, alongside volunteers, box up all kinds of fresh veggies, from carrots to jalapeños. They were grown on incubator farms the students manage. Some are for CSAs (Community Supported Agriculture farm shares) and others are being packed to go to homes for the elderly and other partner institutions.
Daniela Marzuca, left, and Dalia Rosas of Whitemars Farm in Dracut weigh 1 lb bags of carrots at the New Entry Sustainable Farming Project in Lowell. (Jesse Costa/WBUR)
The 20-year-old New Entry program teaches students — many of them immigrants — about the realities of a career in sustainable farming. They also learn about soil management and being stewards of the earth’s fragile ecosystem.
Hashley says there's a long list of barriers to getting into farming – everything from high estate taxes that prevent farming families from passing down land, to over-development, to a lack of agricultural policy. She points to the stat that about 1 percent of workers in the U.S. are involved in agriculture. Hashley believes people have lost reverence for where our food comes from.
New Entry student Jorge Marzuca feels farming is one of the noblest professions.
“We think the future of farming is small farms, CSAs,” he says, adding that farmers should diversify their crops and rotate their fields.
As Marzuca sorts and weighs peppers, he explains that he and his wife, Daniela, moved to the U.S. from Mexico where they worked on a 200-acre broccoli farm.
“Mexican farmers are used to just doing one crop,” he says, speaking of the practice that’s known as monoculture. “You stick with broccoli, you stick with strawberries. And now we're seeing the side effects of that. More erosion, less products and you have to put more fertilizer in.”
Jorge Marzuca is eligible to lease land on a training farm in Dracut through the New Entry program. (Jesse Costa/WBUR)
Now Marzuca wants to farm differently by growing a wide variety of crops and selling them locally and directly to people in his community. This, he says, will help open more people’s eyes to the benefits of sustainable agriculture. Still, the 34-year-old farmer sees tech in his future.
“We have to combine and find the balance between labor and technology because a lot of people need jobs,” Marzuca says, “but we also need technology to be better farmers.”
Industrial agriculture is one of the world's largest polluters. Everyone interviewed for this story agrees: The more sustainable farming there is — in fields, shipping containers, greenhouses, backyards and even on balconies — the better off we, and the planet, will be.
(Jesse Costa/WBUR)
Correction: A previous version of this article misstated the number of Leafy Green Machines that exist in the world. The story has been updated. We regret the error.
This segment aired on November 20, 2018.
Andrea Shea Senior Arts Reporter
Andrea Shea is WBUR's arts reporter.
New Autonomous Farm Wants To Produce Food Without Human Workers
To View Video Please Click Here | COURTESY OF IRON OX
Down on a new robot farm, machines tend rows of leafy greens under the watch of software called “The Brain.”
by Erin Winick
October 3, 2018
Iron Ox isn’t like most robotics companies. Instead of trying to flog you its technology, it wants to sell you food.
As the firm’s cofounder Brandon Alexander puts it: “We are a farm and will always be a farm.”
But it’s no ordinary farm. For starters, the company’s 15 human employees share their work space with robots who quietly go about the business of tending rows and rows of leafy greens.
Today Iron Ox is opening its first production facility in San Carlos, near San Francisco. The 8,000-square-foot indoor hydroponic facility—which is attached to the startup’s offices—will be producing leafy greens at a rate of roughly 26,000 heads a year. That’s the production level of a typical outdoor farm that might be five times bigger. The opening is the next big step toward fulfilling the company’s grand vision: a fully autonomous farm where software and robotics fill the place of human agricultural workers, which are currently in short supply.
COURTESY OF IRON OX
Iron Ox isn’t selling any of the food it produces just yet (it is still in talks with a number of local restaurants and grocers). So for now, those tens of thousands of heads of lettuce are going to a local food bank and to the company salad bar. Its employees had better love eating lettuce.
The farm’s non-lettuce-consuming staff consists of a series of robotic arms and movers. The arms individually pluck the plants from their hydroponic trays and transfer them to new trays as they increase in size, maximizing their health and output—a luxury most outdoor farms don’t have. Big white mechanical movers carry the 800-pound water-filled trays around the facility.
COURTESY OF IRON OX
At first, making sure these different machines worked together was tricky. “We had different robots doing different tasks, but they weren’t integrated together into a production environment,” says Alexander.
So Iron Ox has developed software—nicknamed “The Brain”—to get them to collaborate. Like an all-seeing eye, it keeps watch over the farm, monitoring things like nitrogen levels, temperature, and robot location. It orchestrates both robot and human attention wherever it is needed.
Yes, although most of the operation is automated, it still does require a bit of human input. Currently, workers help with seeding and processing of crops, but Alexander says he hopes to automate these steps.
But why go to the trouble of automating farming at all?
Alexander sees it as solving two problems in one: the shortage of agricultural workers and the distances that fresh produce currently has to be shipped.
Rather than eliminating jobs, the company hopes, the robots will fill the gaps in the industry’s workforce. And he believes that by making it possible to grow crops close to urban areas without paying city-level salaries, the automated farms will enable stores to chose vegetables fresher than those that had to travel thousands of miles to get there. That is, assuming the startup can get its prices to match those of traditional competitors.
COURTESY OF IRON OX
“The problem with the indoor [farm] is the initial investment in the system,” says Yiannis Ampatzidis, an assistant professor of agricultural engineering at the University of Florida. “You have to invest a lot up front. A lot of small growers can’t do that.” This could risk creating a gap between the big farming institutions and smaller family-owned operations, in terms of gaining access to new technology.
To View Video Please Click Here | COURTESY OF IRON OX
Despite this, Ampatzidis says that bringing automation to both indoor and outdoor farming is necessary to help a wider swath of the agricultural industry solve the long-standing labor shortage.
“If we don’t find another way to bring people [to the US] for labor, automation is the only way to survive,” he says.
Erin Winick Associate Editor
I am the associate editor of the future of work at MIT Technology Review. I am particularly interested in automation and advanced manufacturing, spurring from my background in mechanical engineering. I produce our future of work e-mail… More
Vertical Farms Tended By Robots To Make Harvesting More Efficient
- MARK BLUNDEN August 17, 2018
Clapham underground is home to 'Growing Underground', the UKs first underground farm. ( Getty Images )
Vertical urban farms tended by robots that grow vegetables — and even rear chickens, fish, and lobsters — in hundreds of stacked boxes have been designed by online grocer Ocado.
It has drawn up plans for a “mechanized growing system” to rival existing projects by London salad farmers, such as one at Clapham North Tube station.
According to a European patent, Ocado’s intensive warehouse system could grow plants using LED lights, and its stacking concept would do away with “large areas of land” normally needed for crops such as herbs.
The patent even suggests that in addition to fruits and vegetables, Ocado’s system could battery-farm “living organisms” such as poultry and fish.
The firm believes “vertical farming” will be cheaper, more efficient, higher-yielding and need fewer people than traditional methods. Produce would be grown in trays inside stacked boxes tended by wheeled, wifi-connected robo-pickers on rails, which winch up the trays when the produce is ripe and dispatch them to another robot for picking and packing.
Robots would also be used for planting, pruning, and spraying pesticides. The patent shows two levels of about 300 growing containers, each about 1m wide by 1.4m high, which would be supplied with water, fertilizer, light, and heat.
Each tray would be tall enough to “allow the plants to grow to their natural harvesting height”, the patent says, and the boxes could be stacked 20m high or more. The patent says growing the plants upside-down, lit from below, “would reduce the energy expended by the plant to move water and nutrients against gravity and may make some species grow faster”.
The idea is based on an automated system used in Ocado’s warehouses.
Dr Nick Palmer, of Compassion in World Farming, said he was “extremely worried” that Ocado envisaged raising fish, chickens, oysters, and lobsters in the system. He said: “A factory farming system where animals are likely to be crammed together with little space, natural light or stimuli would be a step backwards.”
Why You Should Hope Your Next Tomato’s Grown Indoors by Robots
Why You Should Hope Your Next Tomato’s Grown Indoors by Robots
Kevin Maney is a journalist, author, and advisor. His most recent book, written with Hemant Taneja, is Unscaled: How AI and a New Generation of Upstarts Are Creating the Economy of the Future.
If you were inventing the farm today, why would you put it outside, on a giant plot of land?
OK, there’s the sunlight thing, but then you get droughts and frosts and plant-munching insects that have to be battled with harmful pesticides. And because outdoor farms need so much acreage, they’re usually far from most of their customers — which means that by the time a tomato gets to you in a city, it tastes like a baseball.
But now, upstarts such as Bowery farming, AeroFarms, and Lettuce Networks are doing something different. They’re growing food indoors. They’re using data and artificial intelligence to operate more efficiently than traditional farms. And they’re staying small and close to population centers. The new generation of farming promises to feed more people while doing less environmental damage.
Photograph by AeroFarms
This kind of distributed farming fits with a larger 21st-century movement that venture capitalist Hemant Taneja and I call “unscaling.” We document the economic trend in our book, Unscaled: How AI and a New Generation of Upstarts Are Creating the Economy of the Future.
Massive scale was the goal throughout the 20th century. Mechanization and technologies such as the truck and telephone made it possible. Mass production, mass markets, and economies of scale ruled in every sector. So we ended up with giant companies, huge hospitals, big universities — and corporate mega-farms.
Today, industry after industry is unscaling. The cloud, mobile devices, big data, AI, and new technologies such as blockchain and 3D printing are making it possible to profitably customize products for smaller and smaller niches. Netflix is an unscaled version of mass-market cable networks like HBO, using data to make programs that appeal to specific types of viewers. Airbnb is a distributed hotel company. In an unscaled era, businesses can operate at smaller, more focused levels and beat giant enterprises.
So farms are unscaling, too. Bowery and AeroFarms both operate inside old industrial buildings in New Jersey and are a short drive from New York City. Inside these buildings, LED lights mimic natural sunlight. The crops grow in nutrient-rich water beds on trays stacked floor to ceiling. And sensors constantly monitor the plants and send data back to AI-driven software, which can learn what’s best for the plants and tweak lighting, water, and fertilizer to improve yields. Much of the “farming” is done by robots. “We get productivity hundreds of times greater than a traditional farm,” says AeroFarms CEO David Rosenberg. “And we use less water and no pesticides — because we’re indoors — and can grow 365 days a year.”
These unscaled farms can give consumers a better product than mega-farms, too. Food grown nearby doesn’t need to endure shipping — so it can ripen the way it’s supposed to. In the middle of winter, indoor-grown, local tomatoes will taste like tomatoes. As you can imagine, that’s what consumers prefer.
Photograph by AeroFarms
Since 2013, about US$2 billion has been invested in hundreds of agricultural technology startups, according to CB Insights senior analyst Zoe Leavitt, who spoke about the future of food at a recent Techonomy conference in New York. AeroFarms has raised more than $100 million and sells to Whole Foods and FreshDirect.
Boston-based Freight Farms is growing food in container cargo vessels, often selling to restaurants, hotels, and college campus eateries. New York-based BrightFarms says it “finances, designs, builds, and operates” indoor farms close to food retailers and has raised $11 million in funding. Edenworks is operating rooftop greenhouses that grow produce fertilized by ground tilapia and prawns, which are also grown at the mini-farm.
Lettuce Networks is trying another approach. It is using cloud and mobile technology to create a network of urban farms. Founder Yogesh Sharma calls it an Airbnb for farming. The company contracts with owners of small plots throughout a city and installs sensors that can monitor crops and the surrounding environment. Nearby residents can subscribe to the Lettuce service to get food delivered. The system knows what’s being grown all around the city and, from that network, assembles a basket of local produce for delivery. Owners of the plots make some money off their harvest, while subscribers get an assortment of fresh food grown nearby.
In an unscaled era, businesses can operate at smaller, more focused levels and beat giant enterprises. Distributed, indoor, AI-assisted farming should be good news for the environment. Scaled-up farming was the right answer for the past century, feeding a burgeoning population while making food relatively cheap. The percentage of disposable income used for food is lower today than it was in the 1970s, according to Pew Research Center. But by 2050, the planet is projected to have 2.2 billion more people to feed, just as global warming is expected to make weather less predictable and dry up previously fertile regions. If food can be grown indoors, in a cost-effective way, in or near cities, climate will be less of a concern, and far less carbon will be burned moving food thousands of miles via trucks, trains, and ships.
Whether unscaled farming is a net economic benefit remains to be seen. It’s a new industry, with techniques and business models that are works in progress. Analyst firm Market Research Future notes that urban farms cost a lot to start (a warehouse in New Jersey is more expensive than a plot of land in Saskatchewan) and don’t yet work for a lot of crops, such as corn or bananas. Sunlight is free and sustainable; LED lights require energy. But proponents believe that because these indoor farms are far more productive and are closer to consumers, once there are a lot of them and the techniques and technology get honed, more people will be fed for less cost than ever before.
As investment pours in and environmental conditions drive a need for new solutions, unscaled farming looks a lot more like the future of food than does a massive field baking under the sun.
Topics: agriculture, artificial intelligence, carbon, green technology, startups, sustainability, technology