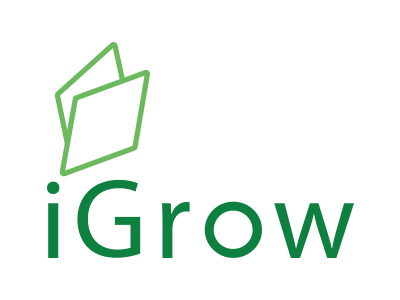
Welcome to iGrow News, Your Source for the World of Indoor Vertical Farming
Pontus Submits Building Permit Application for Surrey Aquaponics Facility
The Company has submitted a construction application to the City of Surrey for its 20,570 square foot aquaponics facility. The approval process is estimated to be completed within 6 weeks and is expected to be followed by the immediate commencement of construction of the Facility's leasehold improvements. Accordingly, the leasehold improvements are to consist of a complete retrofit of the Facility to establish Pontus' solar-powered, water recycling CEVASTM aquaponic system
VANCOUVER, BC, Feb. 3, 2021 /CNW/ - Pontus Protein Ltd. ("Pontus" or the "Company"), is pleased to announce it has made significant progress towards the development of its state of the art, integrated aquaponics facility located in Surrey, British Columbia, Canada (the "Facility").
Image from: CNW Group/Pontus Protein Ltd
The Company has submitted a construction application to the City of Surrey for its 20,570 square foot aquaponics facility. The approval process is estimated to be completed within 6 weeks and is expected to be followed by the immediate commencement of construction of the Facility's leasehold improvements. Accordingly, the leasehold improvements are to consist of a complete retrofit of the Facility to establish Pontus' solar-powered, water recycling CEVASTM aquaponic system.
The installation of all required equipment for the growth and production is forecasted to take between four and six months to complete. Upon completion, the Facility will be approximately 20 times the size of Pontus' prior prototype facility. The prototype facility has been used to test and develop the technology for the Company's proprietary growing process.
The Facility, as seen in the image above and video below, will utilize an array of additional technologies to create a clean and sustainable aquaponics ecosystem. Solar energy panels will be installed to capture renewable energy and power the closed-loop water system, which recycles up to 95% of all water inputs. The implementation of the Facility's unique, sustainable technology in conjunction with Pontus' proprietary CEVAS™ automated growth technology will allow the Company to emphasize biosecurity in its agricultural production processes, removing the need for additional chemicals, pesticides, and other non-native components.
Pontus CEO, Conner Yuen states: "Entering the construction application process is a major milestone for the Company as we move toward the commissioning of the Facility. Our aim is to create a state of the art process that will incorporate the latest in sustainable agriculture technology. The ability to implement this highly efficient technology solves many issues we see with current methods of food production such as land scarcity and low yields and contamination.
Pontus' biosecurity and renewable food sources are intended to create a proactive solution to these issues by reducing the potential for contamination and the need for pesticides. Pontus hopes the Facility will revolutionize how traditional agriculture is conducted and show the power of technological food advancements."
Plant-based Protein Powder Market
The Company's plant-based protein powder is a premium entry into the global protein and supplements market, which is currently valued at USD$15 Billion and is expected to grow to USD$20 Billion by 2025 according to Grand View Research. This growth is expected to be fuelled by many North Americans reducing or eliminating the regular consumption of animal products. The North American plant-based protein market is also anticipated to grow at a compound annual growth rate of 14% from 2019 through 2025.
About Pontus Protein Ltd
Pontus Protein Ltd. makes pure plant-based protein powder sourced from nutritious water lentils, farm-grown in Vancouver, BC, with development plans to expand to Surrey, B.C.. Not only does Pontus Protein Powder exceed certified organic standards, but it's also gluten-free, pure and allergen safe. It's jam-packed full of antioxidants, minerals, vitamins and ALL the essential amino acids.
This is not your average lentil, these are water lentils; a crop that can be harvested every 24 hours in an indoor aquaponic farm that uses 95% less water than traditional agriculture, using Pontus' proprietary Closed Environment Vertical Aquaponics System (or CEVAS™) aquaponic agritech technology. This is wonderful news for a planet populated with us hungry and health-conscious humans.
NASA's Challenge To Grow Food In Space Can Win You Up To $500,000
There are thousands of bizarre challenges doing the rounds on the internet. These unique challenges soon go viral on the internet, with countless participants hopping on board. A number of these challenges also involve some form of food. If you're a food innovator who's looking for the next interesting challenge to take up, NASA (National Aeronautics and Space Administration) may have something for you. The NASA, in collaboration with Canada's CSA (Central Space Agency), has launched a 'Deep Space Food Challenge'. The one-of-a-kind competition seeks to find food production technologies which are sustainable in long duration missions to outer space.
NASA has launched a 'Deep Space Food Challenge' to prompt innovation of food production techniques and technologies viable in outer space.
Image from: Deep Space Food
There are thousands of bizarre challenges doing the rounds on the internet. These unique challenges soon go viral on the internet, with countless participants hopping on board. A number of these challenges also involve some form of food. If you're a food innovator who's looking for the next interesting challenge to take up, NASA (National Aeronautics and Space Administration) may have something for you.
The NASA, in collaboration with Canada's CSA (Central Space Agency), has launched a 'Deep Space Food Challenge'. The one-of-a-kind competition seeks to find food production technologies which are sustainable in long duration missions to outer space.
Our cargo resupply missions can only go so far! That's why we need your help to design a food system to keep our astronauts feed during long duration space exploration.
— NASA Wallops (@NASA_Wallops) January 30, 2021
Check out the @NASAPrize Deep Space Food Challenge: https://t.co/9mxtZXbwaC pic.twitter.com/izU8nSqPDc
A short video explaining the purpose behind the challenge was shared by the official handle. The 56-second clip elaborated on how astronauts embarking on lunar space exploration missions usually rely on pre-packaged meals or resupply of food through shuttles from Earth.
Thus, creating a brand, new food production system with minimal input and nutritious output with minimal wastage can go a long way in fuelling longer duration space explorations. The challenge's focus is on identifying food production technologies that can help feed a crew of four astronauts and help fill food gaps for a three-year round-trip mission with no resupply required from Earth.
These innovative food production methods may also help communities on Earth living in harsh conditions and extreme climates. This could also help tackle food insecurity in the future, which is one of the biggest issues that loom large today. "Solutions identified through this Challenge could support these harsh environments, and also support greater food production in other milder environments, including major urban centres where vertical farming, urban agriculture and other novel food production techniques can play a more significant role," stated the Deep Space Food Challenge's official website.
.@NASA & @csa_asc are launching a Deep Space Food Challenge to develop food production tech in space.
— NASA STI Program (@NASA_STI) January 28, 2021
Hey @GuyFieri, how about Diners, Drive-Ins, Dives & Deep Space? #STIdocs #Flavortown 🚀🥘
Read about it: https://t.co/fnz80uwpJT
See research: https://t.co/18q6RG3L2G pic.twitter.com/lSRTiiAFes
Registrations for the challenge close on 28th May, and submissions are due 30th July, 2021. Winners of Phase 1 of the challenge will be announced in the month of September this year. The prize money for winners of Phase 1 can go up to USD 500,000 (Rs. 3.64 crores approximately). So, if you have an exciting idea to produce food which could help future space missions - you know what to do!
Challenges With Airflow Strategies In Vertical Applications
As the industry continues to search for ways to maximize efficiencies, the utilization of LED lighting is becoming increasingly common. Aside from energy efficiency gains, one of the many benefits of migrating to LED’s is the ability to also maximize space utilization
As the industry continues to search for ways to maximize efficiencies, the utilization of LED lighting is becoming increasingly common. Aside from energy efficiency gains, one of the many benefits of migrating to LED’s is the ability to also maximize space utilization.
With less radiant heat and more consistent PPFD, cultivators are able to move lighting much closer to the plant canopy (in some cases less than 6”), which makes vertical, or multi-tier, cultivation far more feasible than with HID lighting.
The obvious benefit to tiered applications is the ability to increase canopy square footage without additional building square footage. Although there are some drawbacks to multi-tier growing, there can also be great reward, and so we’re seeing more and more of our clients choose to go this route in their facilities.
From an HVAC perspective
The challenge with multi-tier cultivation is twofold: first, we must ensure homogeneity to the entire canopy at multiple heights (that all plants at all levels are seeing the same conditions), and second, we must ensure that the HVAC system is getting adequate access to the hot, humid canopy air to ensure that it operates at full capacity.
When standalone dehumidifiers are in use (as opposed to integrated dehumidification systems), it’s doubly important. Dehumidifiers are typically ceiling-mounted and getting the humidity from the lower tier all the way to the ceiling is both difficult and absolutely vital to the proper operation of the dehumidification system. These requirements can be challenging even in single tier applications, so when the complication of airflow obstructions associated with multiple tiers of canopy are added into the mix, the need for specialized expertise becomes even more evident.
Unfortunately, it can be exceptionally difficult for cultivators to find and incorporate a well-designed airflow system for their racking design. While something is certainly better than nothing, one-size-fits-all strategies without the proper engineering can be difficult to dial in, often resulting in improper air speed over the canopy, uneven temperatures, higher than necessary cost or higher than necessary energy use in both HVAC and the air distribution system itself.
The variables must be considered
Various lengths of ductwork, various canopy heights, and various distances from the lighting source will all result in variances in airflow requirements. The speed of the airflow, the diffusion of the airflow, and the temperature of the air will all impact VPD and plant transpiration. As even LED lights vary in wattage and sensible heat output, so should the amount of air being displaced over the canopy to ensure that temperature goals are met.
While certain components of racking airflow systems can be utilized in multiple applications, some care must be taken in each application to ensure that the components being applied are appropriate—from duct diameter to static pressure and fan selection to diffusion strategies. And this is only contemplating what is required to deliver cooler, dryer air to the canopy. Delivering the hot, humid air to the air conditioning and dehumidification system must also be considered. Luckily, these are all challenges that can be addressed with the right experience and engineering expertise, and it doesn’t have to cost an arm and a leg.
The racking airflow design should be an integral part of the HVAC design
We are very happy to help any cultivator retrofit their existing racking systems with a well-designed airflow system, regardless of the HVAC system in use. With the proper engineering behind them, these retrofits can solve homogeneity and airflow challenges quite nicely and at a reasonable cost.
By the same token, what we find is that the most cost-effective and energy efficient multi-tier airflow strategies are those incorporated from the get-go as part of the HVAC design. Looking at it objectively, of course these systems should be incorporated at the HVAC design level when possible. Incorporating airflow over the canopy is a natural extension of the HVAC system. However, historically the industry has seen it as a separate challenge, or as a component of the racking systems themselves, and has largely considered only canopy air movement without considering how to ensure the HVAC system impacts the design.
Consistent airflow is achievable if designed right
The fact of the matter is, integrating the airflow systems with the racking systems is the easiest part. The hard part is making sure the airflow systems themselves are correctly designed to achieve their actual purpose: helping provide a cultivation environment that is consistently perfect.
When the multi-tiered airflow strategies within a room are considered as part of the HVAC design, all of the various airflow systems in the room are working in harmony instead of competing and interfering with each other, ensuring that everything operates as it was intended. This approach also minimizes the amount of equipment being utilized to achieve air distribution goals, which minimizes capital costs, overall connected electrical load, and energy use. It can even boost the energy efficiency of the HVAC system itself, by ensuring that air handlers have greater access to the hot, humid air at the canopy.
In any multi-tier application, a well-engineered racking airflow system design is an absolute requirement. However, we must stop thinking of these systems as components of racking, or as a design afterthought, and start thinking of them as an important part of the overall HVAC strategy.
Whether designing the system at the beginning of the room HVAC design or incorporating it after the fact, engineering and expertise that implements the racking airflow system as a vital component of the overall HVAC strategy will always yield the best results.
For more information:
Surna
Tel. +1 303 993 5271
www.surna.com