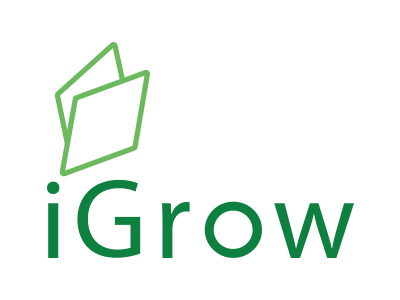
Welcome to iGrow News, Your Source for the World of Indoor Vertical Farming
Eco-Friendly Smart Farms Based On Nutrient Solution Recirculation
UV sterilization and microbial stability analysis used to recycle nutrient solution; proposed method minimizes the use of fertilizers and water by hydroponic farms
15-JUN-2021
UV sterilization and microbial stability analysis used to recycle nutrient solution; proposed method minimizes the use of fertilizers and water by hydroponic farms
NATIONAL RESEARCH COUNCIL OF SCIENCE & TECHNOLOGY
The development of new urban agriculture technologies, such as vertical and smart farms, has accelerated rapidly in recent years. These technologies are based on hydroponic cultivation in which plants are grown using nutrient-rich solutions rather than soil. Approximately 20-30% of the nutrient solutions used during hydroponic cultivation are discharged without being absorbed by the crops, and because most farmers in South Korea do not treat the discharged solutions, hydroponic farms contribute significantly to environmental pollution.
This problem can be reduced if hydroponic farms use a recirculating hydroponic cultivation method that reuses the nutrient solutions after sterilizing them with ultraviolet (UV) light, instead of discharging them. However, two main issues complicate the implantation of such recirculation systems. First, the potential for diseases and nutrient imbalances to develop owing to microbial growth in the recycled nutrient solutions must be eliminated. Second, the initial investment required to set up a recirculating hydroponic cultivation system is often prohibitive, costing hundreds of millions of Korean won per hectare.
However, a new study conducted by researchers at the Korea Institute of Science and Technology (KIST) proposes a method that can stably manage the microbial population in recirculating hydroponic cultivation systems. The research team, led by Drs. Ju Young Lee and Tae In Ahn of the Smart Farm Research Center, KIST Gangneung Institute of Natural Products, conducted an integrated analysis of the microbial growth characteristics by constructing a model that simulates the flow of water and nutrients, and the inflow, growth, and discharge of microorganisms in recirculating and non-circulating hydroponic cultivation systems. Their simulations revealed that the microbial population in recirculating hydroponic cultivation systems can be controlled by adjusting the UV output and the water supply. On the contrary, in non-circulating hydroponic cultivation, the microbial population fluctuates considerably depending on the amount of water used, increasing sharply if there is too little water.
KIST researchers are experimenting with a circulating hydroponic cultivation system. Credit: Korea Institute of Science and Technology (KIST)
High cost has restricted the use of UV sterilization systems in hydroponic farming in Korea And prompted the research team to develop their own UV sterilization system, with further studies underway to commercialize this system as an economical alternative to imported systems.
The results of the study have already received strong interest: the rights to the operation and management software technology for recirculating hydroponic cultivation has been acquired by Dooinbiotech Co., Ltd. for an advance fee of 80 million won (8.5% of the operating revenue), while an agreement is in place with Shinhan A-Tec Co., Ltd. for the advanced recirculating hydroponic cultivation technology for an advance fee of 200 million won (1.5% of the operating revenue). Commercializing the recirculating hydroponic cultivation system is expected to reduce fertilizer costs by approximately 30~40%, which equates to 30 million won per year based on a 1-hectare farm.
Commenting on the envisaged impacts of the study, Dr. Ju Young Lee said, "The developed system makes the transition to eco-friendly recirculating hydroponic cultivation systems an affordable option for many more farmers." Dr. Tae In Ahn added, "We are also developing software and operation manuals to guide farmers in managing the nutrient balance in the solutions to increase the number of farms using the recirculating hydroponic cultivation system."
Lead photo: THE INTEGRATED MODEL DESCRIPTION. view more
CREDIT: KOREA INSTITUTE OF SCIENCE AND TECHNOLOGY(KIST)
###
The study was supported by the Ministry of Agriculture, Food, and Rural Affairs (Institute of Planning and Evaluation for Technology in Food, Agriculture, and Forestry) and the Innovative Smart Farm Technology Development Program of Multi-agency Package. The research results are published in the latest issue of the Journal of Cleaner Production (IF: 7.24, ranked in the top 6.9% by JCR), a highly respected international journal in the field of environmental science.
Disclaimer: AAAS and EurekAlert! are not responsible for the accuracy of news releases posted to EurekAlert! by contributing institutions or for the use of any information through the EurekAlert system.
The New "ModuleX Plant Factory"
On September 9th, 2020, Urban Crop Solutions presented their new “ModuleX Plant Factory” at a launch webinar with 500 registrations from 40 countries, of which 245 attended the event live
The New "ModuleX Plant Factory" Achieves Genovese Basil Full
Production Cost Below 10 EUR/kg (5$/lbs). And
Wins agtechbreakthrough.com
“2020 Vertical Farming Solution of The Year”
The full launch webinar is available at https://urbancropsolutions.com/the-launch-webinar/
On September 9th, 2020, Urban Crop Solutions presented their new “ModuleX Plant Factory” at a launch webinar with 500 registrations from 40 countries, of which 245 attended the event live. The webinar was hosted by Henry Gordon-Smith, CEO of Agritecture, an independent horticultural consulting firm. During the webinar, CEO Tom Debusschere and co-founder/CTO Maarten Vandecruys, showed a demo of the new Grow Module with the BenchCarousel (patent pending).
There was also a guided tour inside of the Indoor Biology Research Center and some in-depth dialogue on the risks and hurdles new entrepreneurs face when starting up a business in Vertical Farming. Other topics covered were the business planning, the 6 months lead time ‘from order to 1st harvest’, and finally the bottom line: an overview of the full production cost (including 10-year depreciation of investment cost) for 3 benchmark crops Romaine Lettuce, Genovese Basil and Red Stem Radish microgreens.
CEO Tom Debusschere: “We couldn’t be happier with the outcome of our launch webinar. In these times of COVID-19 travel restrictions, we have developed the ability to train and start-up new customers completely remotely. I’m glad to see that within the Vertical Farming community, there is such a wide interest in remote presentation and education as well. I am also proud that Agtechbreakthrough.com has awarded us the 2020 Vertical Farming solution of the year".
Timeslots of interesting topics:
· 8’08” Demo video of the Grow Module with BenchCarousel
· 16’01” In-depth conversation on the end-to-end support
· 29’41” Explanation of full lead time ‘from order to 1st harvest’ of 6 months or less
· 39’08” Guided tour inside the Urban Crop Research Center
· 48’10” Full unit production cost, including CAPEX depreciation over 10 years
Urban Crop Solutions is an ag-tech pioneer in the fast-emerging world of ‘Indoor Vertical Farming’. Throughout years of research, 220+ ‘plant growth recipes’ were developed for efficient indoor growing. All drivers for healthy plant growth, such as optimal LED spectrum and intensity, nutrient mix, irrigation strategy, and climate settings are tested and validated daily in the company’s own Indoor Biology Research Center.
To date, Urban Crop Solutions has manufactured container Farms and a Plant Factory for clients throughout Europe, North America, and Asia. Urban Crop Solutions’ commercial farms are being operated for vegetables, herbs, and micro-greens for food retail, foodservice, and industrial applications. Research institutions operate the growing infrastructure of Urban Crop Solutions for scientific research on banana seedlings, flowers, hemp, and many more.
Visit www.urbancropsolutions.com for a full virtual tour.
Brecht Stubbe, Sales Director brst@urbancropsolutions.com
Maarten Vandecruys, CTO mava@urbancropsolutions.com
Tom Debusschere, CEO tode@urbancropsolutions.com
European headquarters: Regional headquarters:
Grote Heerweg 67 800 Brickell Avenue, 1100 Suite
8791 Beveren-Leie (Waregem) Miami (FL 33131)
Belgium Florida
(+32) 56 96 03 06 +1 (727) 601 7158
Facebook: www.facebook.com/urbancropsolutions
Twitter: www.twitter.com/U_C_Solutions
LinkedIn: www.linkedin.com/company/urbancropsolutions
YouTube channel: http://www.youtube.com/c/UrbanCropSolutions
Instagram: https://www.instagram.com/urbancropsolutions/?hl=en
Valentina De Pauw / Marketing & Sales OfficerMobile: +32 487 40 19 56
E-mail: vadp@urbancropsolutions.com