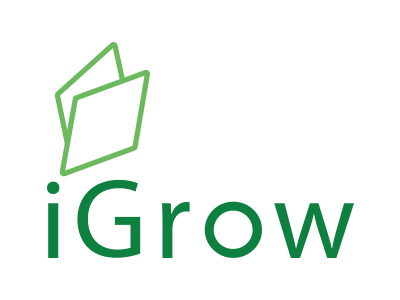
Welcome to iGrow News, Your Source for the World of Indoor Vertical Farming
VIDEO: Will This Y Combinator-Backed Startup’s Urban Home Farms Take Root In India?
UrbanKisaan leverages hydroponic technology for home growing kits, as well as a network of urban farms for online delivery and retail channels
Inc42 Staff
27 Aug'20
UrbanKisaan leverages hydroponic technology for home growing kits, as well as a network of urban farms for online delivery and retail channels
During the lockdown phase, the company claimed to have seen 10x growth in terms of demand for its fresh produce, compared to pre-Covid times.
Based in Hyderabad, UrbanKisaan has installed close to 30+ vertical farms and plans to expand to Bengaluru, Chennai among other cities
There’s a minor revolution underway in many of India’s biggest cities. We are talking about hydroponic farming and this soil-less method is fast becoming the answer to solving the problem of carbon footprint in food. Call it hydroponic farming, soilless farming, vertical farming or anything else — for many it is the long-awaited answer to responsible eating.
In this backdrop, agritech and hydroponics startups are quickly finding niches in various produce categories and cities. Despite their shared ethos for sustainable food production, the likes of UrbanKisaan, Barton Breeze, Hydrilla, Simply Fresh, Acqua Farms, Letcetra Agritech, BitMantis Innovations, Future Farms, Ela Sustainable Solutions, Agro2o, Junga FreshnGreen, Pindfresh are working in this field through different models and targeting different niches — from large-scale hydroponics farming in rural areas to small home farms for the cities.
Working on the philosophy of bringing farms closer to home is Hyderabad-based UrbanKisaan. With the vision of making hydroponic technology more affordable and accessible for the masses, UrbanKisaan offers home-grow kits or vertical hydroponic farms. And by creating mini-farms in cities and revitalizing farmlands with hydroponic technology, the startup also supplies fresh produce to customers through Swiggy, Zomato, Dunzo, and other retail channels as well as in the D2C model on subscription and on-demand basis.
“We are the only startup in the hydroponic landscape to have taken a hybrid approach, where we have 20,000 sq. ft. research and development facility, along with 15+ in-house scientists working on newer innovations and products,” claimed cofounder and CEO Vihari Kanukollu elaborating on how the company is looking to differentiate itself in the burgeoning hydroponic market.
However, UrbanKisaan is not alone in the game, Simply Fresh, another Hyderabad based agritech startup, also grows and supplies a line of medicinal plants and fresh produce from its greenhouses. Similarly, Chennai-based Future Farms works on hydroponic technology at a commercial level, where it designs integrated full-stack solutions for alternative farming in the country. The vibrancy of the hydroponic models and the large ground area that needs to be covered across cities and villages has made it possible for multiple startups to thrive in this space.
Needless to say, the market opportunity is huge, as ‘urban farming’ is catching up at a rapid pace globally. According to MarketsandMarkets, the global hydroponics market is expected to reach $16.6 Bn by 2025, growing at a compound annual growth rate of 11.9% from $9.5 Bn in 2020. The growth of the sector is said to be driven by the increase in population and the need for food security through alternative high-yield farming techniques, given the depletion of water across the globe.
Plus, the rise in awareness and demand for a healthier lifestyle is said to have opened doors for a plethora of possibilities for hydroponic startups to reap the benefits in the long run.
UrbanKisaan earns revenue from its multiple channels which allow it to reach all kinds of consumers — from those who want a taste of the hydroponic produce to those who want to grow it themselves. Its urban farms are strategically located next to retail stores to facilitate hyperlocal deliveries and its DIY home kits are for the latter set. Additionally, it is also supplying its technology to local farmers to reutilise farmland.
The startup was founded in 2017 by Kanukollu, Srinivas Chaganti, Dr Hari, Shiva Prasad and Dr Sai Ram, a scientist who has been instrumental in developing the nutrient solution for their state-of-the-art vertical farming technique. In March 2020, the company also raised $1.5 Mn in seed funding from Y Combinator.
Home Farming In The Times Of Covid
During the lockdown phase, the company claimed to have witnessed 10x growth in terms of demand for its fresh produce, compared to pre-Covid levels. Further, cofounder Kanukollu said that the disruption in the supply chain and consumers leveraging on the hyperlocal delivery modes, along with the change in consumer lifestyle, for the consumption of fresh, organic produce has resulted in the surge in demand.
The Covid-19 pandemic temporarily halted the movement of produce across India and highlighted the gap in the food supply chain. This allowed agritech startups such as UrbanKisaan that specialise in hydroponic farming to tap a tremendous opportunity and bring efficiency in the supply chain.
With its hyperlocal urban farms model, Kanukollu claimed UrbanKisaan is not only bringing transparency to the vegetable supply chain but also lowering the carbon footprint, reducing food waste. Most importantly, their farming technique also claimed to save 95% water, and grow the produce 30x compared to traditional farms.
Its home kits are priced anywhere between INR 9,900 and INR 19,900 with about 50+ varieties of leafy vegetables and exotic vegetables supported by these kits, including spinach, coriander, mint, basil, bok choy, lettuce, parsley, fenugreek, capsicum, tomato and kale among others.
Further, the company claimed to have semi-automated the entire process and has designed the kits in such a way that it requires limited resources to manage it. “Once installed, it requires 15 min/week of effort to take care of the plants, thereby making it seamless for consumers to grow their own fresh produce,” said Kanukollu.
A Tech Upgrade For Rural Farmers
In addition to this, UrbanKisaan also works with local farmers who own greenhouses, where it helps them in setting up vertical farms from scratch to producing and supplying fresh fruits and vegetables.
Cost-wise, the poly house or greenhouse setup would typically cost farmers anywhere between INR 35 to INR 50 Lakhs per acre, of which, the government may subsidise up to 80%. Once this is installed, which is a fixed cost, for setting up of hydroponic setup, it would cost the farmer additionally INR 50 Lakhs. But, UrbanKisaan told Inc42 that it looks to reduce this cost at INR 15 to INR 20 Lakhs.
UrbanKisaan claims to have installed close to 30+ hydroponics farms in the state, across its various offerings. In the coming days, it plans to expand into other cities, including Bengaluru, Chennai among others, along with growing its team, adding newer varieties of hydroponic seeds, fruits and vegetables, and enhancing its technology capabilities.
Kanukollu is looking at creating a centralised monitoring system through UrbanKisaan for these various hubs and farms. “We are heavily investing in artificial and machine learning tools, where once the network of the urban farm increases, we will be able to monitor and control their farms remotely and provide a real-time update to customers.”
Micro-Naps For Plants: Flicking The Lights On And Off Can Save Energy Without Hurting Indoor Agriculture Harvests
A nighttime arrival at Amsterdam’s Schiphol Airport flies you over the bright pink glow of vegetable production greenhouses. Growing crops under artificial light is gaining momentum, particularly in regions where produce prices can be high during seasons when sunlight is sparse.
The Netherlands is just one country that has rapidly adopted controlled-environment agriculture, where high-value specialty crops like herbs, fancy lettuces and tomatoes are produced in year-round illuminated greenhouses. Advocates suggest these completely enclosed buildings – or plant factories – could be a way to repurpose urban space, decrease food miles and provide local produce to city dwellers.
One of the central problems of this process is the high monetary cost of providing artificial light, usually via a combination of red and blue light-emitting diodes. Energy costs sometimes exceed 25% of the operational outlay. How can growers, particularly in the developing world, compete when the sun is free? Higher energy use also translates to more carbon emissions, rather than the decreased carbon footprint sustainably farmed plants can provide.
I’ve studied how light affects plant growth and development for over 30 years. I recently found myself wondering: Rather than growing plants under a repeating cycle of one day of light and one night of darkness, what if the same daylight was split into pulses lasting only hours, minutes or seconds?
Short bursts of light and dark
So my colleagues and I designed an experiment. We’d apply the normal amount of light in total, just break it up over different chunks of time.
Of course plants depend on light for photosynthesis, the process that in nature uses the sun’s energy to merge carbon dioxide and water into sugars that fuel plant metabolism. Light also directs growth and development through its signals about day and night, and monkeying with that information stream might have disastrous results.
That’s because breaking something good into smaller bits sometimes creates new problems. Imagine how happy you’d be to receive a US$100 bill – but not as thrilled with the equivalent 10,000 pennies. We suspected a plant’s internal clock wouldn’t accept the same luminous currency when broken into smaller denominations.
And that’s exactly what we demonstrated in our experiments. Kale, turnip or beet seedlings exposed to cycles of 12 hours of light, 12 hours dark for four days grew normally, accumulating pigments and growing larger. When we decreased the frequency of light-dark cycles to 6 hours, 3 hours, 1 hour or 30 minutes, the plants revolted. We delivered the same amount of light, just applied in different-sized chunks, and the seedlings did not appreciate the treatment.
The same amount of light applied in shorter intervals over the day caused plants to grow more like they were in darkness. We suspect the light pulses conflicted with a plant’s internal clock, and the seedlings had no idea what time of day it was. Stems stretched taller in an attempt to find more light, and processes like pigment production were put on hold.
But when we applied light in much, much shorter bursts, something remarkable happened. Plants grown under five-second on/off cycles appeared to be almost identical to those grown under the normal light/dark period. It’s almost like the internal clock can’t get started properly when sunrise comes every five seconds, so the plants don’t seem to mind a day that is a few seconds long.
Just as we prepared to publish, undergraduate collaborator Paul Kusuma found that our discovery was not so novel. We soon realized we’d actually rediscovered something already known for 88 years. Scientists at the U.S. Department of Agriculture saw this same phenomenon in 1931 when they grew plants under light pulses of various durations. Their work in mature plants matches what we observed in seedlings with remarkable similarity.
A 1931 study by Garner and Allard tracked the growth of Yellow Cosmos flowers under light pulses of various durations. J. Agri. Res. 42: National Agricultural Library, Agricultural Research Service, U.S. Department of Agriculture., CC BY-ND
Not only was all of this a retread of an old idea, but pulses of light do not save any energy. Five seconds on and off uses the same amount of energy as the lights being on for 12 hours; the lights are still on for half the day.
But what would happen if we extended the dark period? Five seconds on. Six seconds off. Or 10 seconds off. Or 20 seconds off. Maybe 80 seconds off? They didn’t try that in 1931.
Building in extra downtime
It turns out that the plants don’t mind a little downtime. After applying light for five seconds to activate photosynthesis and biological processes like pigment accumulation, we turned the light off for 10, or sometimes 20 seconds. Under these extended dark periods, the seedlings grew just as well as they had when the light and dark periods were equal. If this could be done on the scale of an indoor farm, it might translate to a significant energy savings, at least 30% and maybe more.
Recent yet-to-be published work in our lab has shown that the same concept works in leaf lettuces; they also don’t mind an extended dark time between pulses. In some cases, the lettuces are green instead of purple and have larger leaves. That means a grower can produce a diversity of products, and with higher marketable product weight, by turning the lights off.
One variety of lettuce grew purple when given a 10-second dark period. They look similar to those grown with a five-second dark period, yet use 33% less energy. Extending the dark period to 20 seconds yielded green plants with more biomass. J. Feng, K. Folta
Learning that plants can be grown under bursts of light rather than continuous illumination provides a way to potentially trim the expensive energy budget of indoor agriculture. More fresh vegetables could be grown with less energy, making the process more sustainable. My colleagues and I think this innovation could ultimately help drive new business and feed more people – and do so with less environmental impact.
July 22, 2019 6.58am EDT Updated July 22, 2019 2.40pm EDT
This article was updated with a corrected legend on the photograph of the plants grown in 1931.
VIDEO: Vertical Farming Offers Solutions
Vertical farming has long been seen as a solution to rising populations and increasing urbanisation, but its efficiency may make it key to sustainability in general
BY TOM JOYCE
23rd June 2020
Vertical farming has long been seen as a solution to rising populations and increasing urbanization, but its efficiency may make it key to sustainability in general
Finland-based Novarbo, part of the Biolan Group, is helping growers to adapt to the concept of vertical farming and all the benefits that come with it, according to project engineer Arttu Lammensalo.
A specialist in greenhouse technology, Novarbo’s Vertical Farming Concept is able to solve the challenges of various operations, he said.
According to Lammensalo, a facility equipped with climate control and heat re-use systems is an extremely energy-efficient way of cultivating high-quality plants indoors.
Any surplus heat energy is stored for reuse, while food transportation is decreased by moving production closer to the consumer, reducing the carbon footprint. A large amount of transpiration from the crop is captured from the air and returned to the irrigation system.
In addition, with Novarbo Growisor software, the grower is able to optimise the plant growth factors of the fully automated facility, Lammensalo said, enabling long-term production planning and wireless tracking.
“Our first vertical farm serves as our laboratory for climate control experiments,” he explained. “We want to help people to adapt to vertical farming. We have collected data for over a year and a half, working on more than ten products, determining the effect of LED lights at different times and for different periods of time. The climate control system allows us to improve irrigation efficiency by 90 per cent.”
According to Lammensalo, vertical farming is quite expensive initially, but after five years, you can expect to get your investment back. “Some are a little afraid of this technology,” he said. “If there is a power cut, for example, you need a backup energy source. Herbs and salads can be quite expensive in the winter, though, so the costs can sometimes balance out.”
Vertical farming is also gaining considerable attention as a solution to feeding the large numbers currently crowded into the world’s cities.
“Vertical farming will be useful anywhere there isn’t much growing area,” Lammensalo stated. “In Singapore, they import most of their herbs and vegetables from abroad, so they are very keen on vertical farming to avoid any supply issues. It also significantly reduces the carbon footprint, as well as the water footprint, so it’s a good solution in countries that suffer from water shortages.”
Aquaponics Firm Eyes A Green Future, With Water Lentils In A Starring Role
After a year of research and development on Vancouver Island, and a crowdfunding campaign that reached $750,000, a new agri-tech company is preparing to significantly expand its footprint and hit the market with a plant protein
Andrew Duffy / Times Colonist
MAY 30, 2020
Steve McArthur, CEO of Pontus Water Lentils, at the company's research and development site.
Photograph By ADRIAN LAM, TIMES COLONIST
After a year of research and development on Vancouver Island, and a crowdfunding campaign that reached $750,000, a new agri-tech company is preparing to significantly expand its footprint and hit the market with a plant protein.
Pontus Water Lentils, which has been doing research and development at a test farm run by Victoria’s Garden City Aquaponics, has developed an aquaponics system — a hybrid of aquaculture and hydroponics — to produce water lentils. It says those lentils pack an unrivaled protein punch.
Chief technology officer and co-founder Steve McArthur said Pontus has developed a grow and harvest system which, when installed in a new facility, will be capable of producing 100 metric tonnes of water lentils.
McArthur, who also founded Garden City Aquaponics, said the plan is to build a new 10,000 square foot facility for the closed-cycle system. It will also grow and nurture rainbow trout — the fish waste is converted by microbes into fertilizer for water plants, which in turn filter the water for the fish.“
It’s a grown-in-Victoria business,” said McArthur. They are considering sites for the facility in Langford or on the Lower Mainland.
He said the water lentils grown in the facility would be dried and turned into about 6.4 metric tonnes of protein powder that can be used as a supplement for protein shakes, a partial ingredient replacement in foods such as pasta, or to be used in manufacturing food such as protein bars and beverages.
The company intends to package the powder for sale to grocery stores and find partners to produce a line of products packed with the protein-rich powder, while the fish will be sold to local grocery stores and restaurants.
McArthur noted they have already had some success in producing fish and leafy greens at Garden City, as they sold fish to local restaurants and small-scale production of leafy greens to Red Barn Market and other grocers as well as local chefs.
Currently, Garden City, which produces two types of tilapia and the water lentils, is being used entirely for research and development for Pontus, but it may revert to producing small-scale food for local stores and restaurants when Pontus opens its facility.
McArthur said the high-protein water lentils add a protein boost to various products.“The final product is 42.1 percent protein by weight, that’s pretty significant,” he said, noting that is higher than both pea and pumpkin protein. “In terms of plant-based protein that’s one of the highest and we would be growing it aquaponically on a commercial scale.”
The next step for Pontus is the larger facility, which McArthur said they now have the money to build.
Pontus started a crowdfunding campaign on Frontfundr.com. It had hoped to raise at least $750,000 and as much as $1.25 million to build its first production farm. To date, it has raised just over $766,000; they are also raising private capital.
When built, the facility will be capable of producing 6.4 metric tonnes of dried and powdered lentils and about 11,000 trout every year.
McArthur said the market opportunity is big as the product ticks a lot of boxes in terms of its sustainable production, the massive demand for plant-based protein, and food security.
The facility is scalable, moveable could be built almost anywhere, and has a small environmental footprint, he said.
The company says the farm uses less than five percent of the water used in field farming and has none of the carbon footprint.