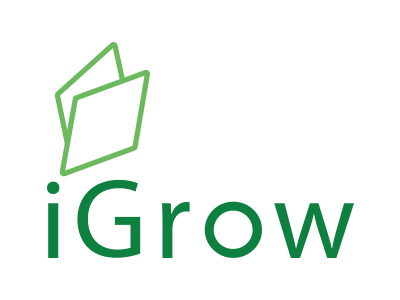
Welcome to iGrow News, Your Source for the World of Indoor Vertical Farming
Can Vertically-Grown Leafy Greens Make Your Salad Fresher And More Sustainable?
As indoor farms can control everything from temperature to humidity to airflow and even lighting schedules, their products are often marketed as more sustainable than outdoor agriculture
Courtesy of Forward Greens
A warehouse may seem like an odd place for a farm, but it's one of the places you'll find arugula, kale, and other leafy greens growing in Vancouver, Washington. The 25,000 square foot warehouse is home to Forward Greens, one of several indoor vertical farms attempting to use technology to make our lunch salads taste better and be better for the planet.
"We're trying to grow the cleanest healthiest greens we can while preserving the earth's resources," said Ken Kaneko, the founder of Forward Greens. Even if you haven't yet had greens from an indoor farm, chances are more and more of the greens in your salad are going to come from farms like Forward Greens, Gotham Greens, Bowery Farming, and others.
Related: Young Farmers Need Land and These Organizations Are Helping Them
What Exactly Is a Vertical Farm?
Simply put, it's a farm where rows of produce are stacked. "We grow up instead of out," Kaneko said. In the late 1990s and early 2000s, Columbia University professor and microbiologist Dickson Despommier and his graduate students began popularizing the idea of vertical indoor farms as one answer to some of the world's biggest problems: how to feed a growing worldwide population, especially with more and more people, centered around cities, and how to produce that food more efficiently and sustainably.
Today most indoor farms use soilless farming techniques. Some like, New York-based Gotham Greens, one of the early pioneers of indoor farms and whose products you'll find in Safeway, Meijer, and Harris Teeter, among others, use a hydroponics system. Other soilless systems include aeroponics and aquaponics.
Does Arugula Grown on an Indoor Farm Taste Better Than Arugula Grown Outside?
While outdoor farms rely on water, sun, and sometimes luck to produce leafy greens, most vertical indoor farms use technology and constant data monitoring to grow their crops. That data means that indoor farms can tweak everything from how your arugula tastes to how it feels to the nutrients it contains.
But beyond the tech, depending on where you live, leafy greens grown indoors might be fresher. Most of the salad greens you find in the supermarket likely came from Salinas, California, or Yuma, Arizona. According to Kaneko, Forward Greens delivers its products to markets in the Pacific Northwest within 48 hours of harvest. As vertical farms aren't dependent on weather, you can buy the same arugula from the same farm year-round. "We can provide a consistent year-round supply," said Gotham Greens CEO Viraj Puri. And that supply is also fully traceable, possibly making it safer.
Are Leafy Greens from an Indoor Farm More Sustainable?
As indoor farms can control everything from temperature to humidity to airflow and even lighting schedules, their products are often marketed as more sustainable than outdoor agriculture. According to Bowery Farming, whose leafy greens are available in the Mid-Atlantic and Northeast at Whole Foods Market, Giant Food, Stop & Shop, Walmart, and Weis Markets, their indoor farms are more "productive on the same footprint of land than traditional agriculture."
Similarly, Forward Greens says through its technology; it can use 95 percent less water, 99 percent less land, and 100 percent less pesticides compared to outdoor agriculture. But there's not much data on how vertical farms compare to their conventional counterparts. Researchers from Cornell University are in the middle of a three-year grant looking at not only how controlled-environment agriculture compares to traditional field agriculture in terms of energy, carbon and water footprints, profitability, workforce development, and scalability but what if any educational and psychological benefits local systems can offer by connecting urban people to their food. However, it's not clear if that study will also account for food waste, which has been found to be as high as one-third on traditional farms, and which both Puri and Kaneko say their farms can reduce.
While indoor farming likely isn't going to save the planet it may be one part of the puzzle and will make it easier to get fresh, locally grown salad greens year-round.
Producing Seedlings In An Off-Grid LED Lit Vertical Farming Facility
Plant Raisers Ltd, the largest propagator of glasshouse salad crops in the UK, has in addition to a recent expansion of its conventional glasshouse facility, partnered with sister company IGrowing Ltd to develop a system to produce seedlings using an off-grid LED lit vertical farming facility
How Plant Raisers Ltd Are Taking Propagation ‘Off Grid’
Plant Raisers Ltd, the largest propagator of glasshouse salad crops in the UK, has in addition to a recent expansion of its conventional glasshouse facility, partnered with sister company IGrowing Ltd to develop a system to produce seedlings using an off-grid LED lit vertical farming facility.
Eliminating carbon footprint
The concept has been designed to eliminate the carbon footprint associated with vertical farming and maximize the yield of seedlings per unit of electricity. To achieve this, every aspect of power demand for urban farming systems was analyzed and optimized. A key focus in developing a sustainable and efficient vertical plant production system targeted the excess heat created by the inefficiency of existing systems. Eliminating this waste energy has allowed the parasitic loads associated with heat management to be negated saving energy and unnecessary capital cost and making off-grid operation a reality.
LED fixture and power infrastructure producing negligible heat
The first task for the designers was to produce an LED fixture and power infrastructure which produced negligible heat. Collaboration with Extreme Low Energy, a UK company with knowledge and expertise in DC infrastructures provided the electrical solution and the APP-based control system that delivered crop-specific lighting recipes. Several iterations of light unit design were required before the targeted level of energy efficiency and lighting performance was achieved. The end result is a bespoke fixture that has excellent light uniformity, full spectral and intensity control and emits virtually no waste heat. The control of spectral lighting recipe and duration allows for further energy gains building on Plant Raiser’s horticultural understanding of crop requirements at each stage of growth. Additionally, as the luminaires are only 8 mm thick there is an opportunity to maximize the number of growing levels in any given space maximizing space utilization.
With no surplus heat load from the installation, controlling the environment required a different approach to the conventional HVAC systems. Instead, environmental control is provided by fans and sensors. These are switched by the App-based program which allows for remote control at any time of day or night. The app also has the ability to continuously record data to aid management decisions on the most appropriate climate and lighting settings.
Container system with low energy demand
The total energy demand of the container system is now so low that it can support off-grid production with power provided by locally mounted solar panels and/or a small scale wind turbine with a stand by gas generator available as an optional extra. Battery technology allows storage and control of the power generation. These aspects are also controlled and monitored using the app-based program.
The resulting system is the culmination of over three years' research at Plant Raisers Ltd focussed on containerized growing seedlings with the minimum energy input. The project is now fully operational and will be further developed by iGrowing Ltd for customer-specific applications. The system components can also be fitted into larger vertical farm developments looking to take advantage of the energy savings and design methodology.
For more information:
Nick Denham
iGrowing Ltd
nick@igrowing.co.uk