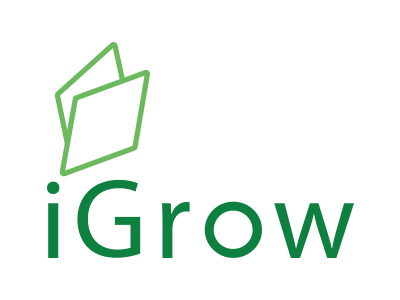
Welcome to iGrow News, Your Source for the World of Indoor Vertical Farming
Why Lettuce Greenhouse Sector's Growth Is Focused In The U.S.
Greenhouses for lettuce and leafy greens are being built at a rapid pace across the U.S. In contrast, in neighboring Mexico there is no similar greenhouse production and in Canada there is very little — the primary exception being 11-acre Whole Leaf Farms located in Coaldale, Alberta.
By Peter Tasgal
August 10, 2021
Greenhouses for lettuce and leafy greens are being built at a rapid pace across the U.S. In contrast, in neighboring Mexico there is no similar greenhouse production and in Canada there is very little — the primary exception being 11-acre Whole Leaf Farms located in Coaldale, Alberta.
Based on my research, the primary driver for this U.S. phenomenon is investor comfort in making U.S.-based investments in leafy greens greenhouses, which are more expensive to build compared to tomato, cucumber and pepper greenhouses.
For example, AppHarvest’s latest tomato greenhouse is expected to be 63 acres and valued at $139 million — just over $50 per square foot. In contrast, Bright Farms’ 280,000-square-foot leafy greens greenhouse in North Carolina cost $21 million, or $75 per square foot. Gotham Greens built a 100,000-square-foot leafy greens greenhouse in Providence, Rhode Island, that cost $12.2 million, or $122 per square foot.
In addition to investor interest in the U.S. market, other potential factors affecting this phenomenon include:
Temperature variance;
Pricing certainty;
Equilibrium capital leading the charge; and
Generational knowledge in Canada.
Temperature variance
Lettuce and leafy greens perform best at cooler temperatures, up to 70 degrees Fahrenheit. Tomatoes, cucumbers and peppers, in comparison, grow best at temperatures in excess of 70 degrees Fahrenheit.
As the U.S. has a more moderate climate than either Canada or Mexico, a band of greenhouses across the U.S. takes advantage of the more temperate climate. Historically, leafy greens greenhouses have been built in the middle and upper sections of the U.S. However, boundaries have moved. Revol Greens, for example, has a 10-acre greenhouse in Minnesota and is expected to build a 20-acre greenhouse in Austin, Texas, to be completed in 2022.
Historically it has been more costly to keep a greenhouse cool rather than to heat it. However, alternative sources of energy and energy pricing incentives in parts of the southern U.S. have made it increasingly cost competitive to build greenhouses in this area.
Pricing certainty
The cost to build a leafy greens greenhouse is more than a tomato, pepper or cucumber greenhouse on a per square foot basis and on a per pound basis. As a reference, the cost of AppHarvest’s tomato greenhouse is approximately $3 per one year’s production of pounds of tomatoes. In comparison, Bright Farms’ recent leafy greens greenhouse is over $10 per one year’s production of pounds of lettuce and leafy greens.
This large cost structure variance requires greenhouse-grown lettuce to be priced at a premium. In contrast, greenhouse-grown tomatoes can and are priced directly with field-grown tomatoes. In the U.S. today, greenhouse-grown tomatoes make up the majority of fresh tomato sales.
The risk for an investor in a premium product is demand fluctuation. Economic and other market conditions will have a greater effect on premium product demand compared to product with more commodity-like traits.
Equilibrium Capital leading the charge
Equilibrium Capital is a leading investor in the North American controlled environment agriculture sector. It closed its second fund (CEFF II) this past month, with a capacity of $1.022 billion. Its first fund, CEFF I, had a capacity of $336 million. Recent investments made by Equilibrium include:
AppHarvest: $91 million non-dilutive investment to support the building of its second tomato greenhouse in Kentucky.
FINKA: Expansion capital for the Mexican greenhouse company, which operates tomato, pepper and cucumber greenhouses, the product of which is primarily sold into the U.S. and Canada. This was Equilibrium’s first investment outside of the U.S.
Little Leaf Farms: $90 million of debt and equity financing for the company, which is currently building a lettuce and leafy greens facility in Pennsylvania and is expected to follow with a facility in North Carolina.
Revol Greens: $110 million of debt and equity capital to support its building of a large lettuce and leafy greens greenhouse in Texas.
FINKA is Equilibrium’s only investment outside of the U.S. to-date.
Generational knowledge in Canada
According to the Ontario Greenhouse Vegetable Growers’ website, the organization formed in 1967 has “220 members who grow greenhouse tomatoes, cucumbers and peppers on over 3,000 acres.”
Two of the largest growers in Canada, Mastronardi Produce and Mucci Farms, have invested primarily in building their current greenhouses. To the extent each has branched out, it has been primarily to berries and eggplants. Mastronardi and Mucci have little to no owned lettuce and leafy greens production across North America.
Of note, in 2019 AppHarvest entered into a Purchase and Marketing Agreement with Mastronardi, under which “Mastronardi will be the sole and exclusive marketer and distributor of all tomatoes, cucumbers, peppers, berries and leafy greens” at its Morehead, Ky., facility (currently producing only tomatoes).
Per the 10-year agreement, Mastronardi has a right of first refusal for any additional facilities established in Kentucky or West Virginia. The take-away is Mastronardi is willing to distribute and market greenhouse-grown leafy greens, venturing a reputational risk, but has not yet chosen the investment risk of operating its own greenhouses.
Speaking to the OGVG, most greenhouse operators in Ontario have chosen to put their resources into products they already know. When asked specifically about lettuce and leafy greens, OGVG said the cost to build this type of greenhouse is very expensive per unit of output.
Recap
Some of the most seasoned greenhouse operators in North America are growing a range of produce types in the Ontario, Canada, area largely focused on tomatoes, cucumbers and peppers.
Each of these products grows best at higher temperatures than lettuce and leafy greens. Canadian operators who have been in the business for generations are potentially willing to distribute and market leafy greens, yet they have not been willing to make significant investments in the area.
While leafy greens were once only grown in the Northern parts of the U.S., Revol Greens, backed by Equilibrium Capital, is building one of the largest greenhouses in Texas. Equilibrium Capital, the “smart money,” has only invested in U.S. CEA companies to-date. The exception is FINKA, which operates in Mexico but sells exclusively to the U.S. and Canada.
Based on my research, until lettuce and leafy greens greenhouse production can be priced competitively with field-grown product, it will continue to be a U.S. phenomenon. At least until that time, Canadian and Mexican operators will leave greenhouse lettuce and leafy greens production to U.S. operators.
Peter Tasgal is a Boston-area food agriculture consultant focused on controlled environment agriculture.
Lettuce: Meet The Salad Kings of SA
Back home in East London in 1978, he made the decision to become a farmer, an option that was met with criticism from family and peers who did not have farming backgrounds.
By Glenneis Kriel
August 6, 2021
Not knowing what to do after finishing his military service back in the 1970s, Michael Kaplan set off to work on a kibbutz in Israel, where he was exposed to banana, dairy and chicken production.
From there, he backpacked through Europe, and was particularly impressed by the new technologies that farmers in the Netherlands were using to protect their crops and improve production efficiencies.
Back home in East London in 1978, he made the decision to become a farmer, an option that was met with criticism from family and peers who did not have farming backgrounds.
“My mother, Ethel, was a doctor and my father, Lewis, a lawyer, so they thought I was completely bonkers when I told them I wanted to farm,” recalls Kaplan.
In pursuit of his dream, he wanted to study agriculture at the Elsenburg Agricultural
Training Institute in the Western Cape, but entries had already closed by the time he applied. So he began working at what was then the English Trust Company farm in Stellenbosch, thanks to an introduction from his childhood friend, Bruce Glazer, who already worked there.
Dew Crisp was co-founded by childhood friends Michael Kaplan (left) and Bruce Glazer.
“It really was a case of being in the right place at the right time, as the English Trust Company was one of the first to introduce farming tunnels in South Africa.
“They produced tomatoes using the nutrient film technique [NFT] and experimented with the gravel flow technique [GFT] to grow butter lettuce and celery,” says Kaplan.
These hydroponic techniques, he explains, are similar in that both entail the circulation of a nutrient solution in a closed system. The difference is that with GFT, gravel is used as a growth medium, whereas, with NFT, plants are suspended and their roots exposed.
Early days
Kaplan worked at the English Trust Company for two years. He then learnt that the Joburg Market sold up to three times more vegetables than its Cape Town equivalent.
Deciding it was time to spread his wings, he drove up to Johannesburg, where he began looking for a business partner and land on which to grow his own produce.
“My mother lent me R10 000, which I used to rent land near Heidelberg [about 50km south-east of Johannesburg] and produce celery under 2 000m² of nets using GFT,” says Kaplan.
In 1981, Heidelberg was hit by a severe snowstorm. It destroyed almost all of Kaplan’s infrastructure, but he managed to save most of the crop and used the income from the sale to rebuild his operation.
“I kept costs low by doing almost everything myself, and using the income to grow the operation, reaching 8 000m² by the third year of production,” recalls Kaplan.
In his fourth year of operation, he started looking for land closer to the Joburg Market and with more favourable production conditions.
“These are actually two of the most important prerequisites for farming success; you need to be close to the market, and farm in a region where the climatic and production conditions are suited to the crop you want to grow. I learnt the hard way that the Highveld is unsuited to salad production in winter,” he says.
Financing
With a clearer idea of what he required, Kaplan bought land near Nooitgedacht and applied to the Land Bank for a loan.
Being unfamiliar with hydroponic production, the bank declined his application, but Kaplan managed to secure a loan from First National Bank at an interest rate of 26%. Fortunately, the market was far less competitive and demanding in those days, which enabled him to repay the loan quickly.
“It would be almost impossible to accomplish the same today; land, labour, infrastructure and production costs are exorbitant. And you buy everything in dollars and euros but get paid in rands,” he says.
Costs are driven up even further by international production standards and auditing programmes such as GlobalGAP and HACCP, which are required to supply most markets today, while market access is complicated by retailers and big buyers demanding huge supply volumes all year round.
An impressive growth path
In the intervening years, Glazer had studied agriculture at Elsenburg and thereafter also worked on a kibbutz in Israel. On his return in 1984 he bought a farm near Kaplan’s, and two years later the two decided to amalgamate their businesses to create better economies of scale.
The new company was called Dew Crisp. To add value to their produce, they sold ready-to-eat lettuce in pillow packs, a market they dominated for over six years.
Since then, Dew Crisp has grown into one of the largest value-added salad suppliers in South Africa, expanding their geographical footprint over time to lengthen their production season and mitigate climate and production risks.
Today, they have 10ha under production in Muldersdrift, 200ha near Bapsfontein and 140ha near Philippi, as well as processing plants in the West and East Rand of Gauteng and in Franschhoek in the Western Cape.
Dew Crisp also sources produce from between 15 and 20 selected farmers across geographically diverse regions, some of whom have been supplying the business for over 25 years.
The company’s empowerment arm, Rural Farms, supports and sources produce from five previously disadvantaged smallholder farmers.
In 2009, Agri-Vie, the Africa Food & Agribusiness Investment Fund, bought a 49% share in Dew Crisp, which enabled Kaplan and Glazer to grow the business and place greater emphasis on financial administration and corporate governance.
“We realised that it wasn’t enough to simply follow the market; we had to create our own destiny by becoming market leaders.
“To achieve this, we needed to be innovative and have a really good understanding of consumer trends. We’ve introduced many firsts on the market,” says Kaplan.
Glazer and Kaplan have also drastically diversified their market risks by supplying all the major retailers, various prepared-meal manufacturers such as the Rhodes Food Group, and food service companies such as KFC, McDonald’s, Nando’s and Burger King.
Production
Dew Crisp’s produce is grown under nets, in plastic tunnels and in open fields.
“Tomatoes, English cucumbers and peppers don’t like water or cold [air] on their leaves, so we generally produce them under plastic,” says Kaplan.
Shade nets are used in the production of salad vegetables, as these are sensitive to sunlight, heat and wind. The nets also protect against hail and bird damage while reducing the impact of rain by breaking up the droplets. In addition, they help to absorb heat and keep the production area cool.
Open-field production is highly seasonal and limited to hardier vegetables such as sweetcorn, onions and cabbage.
Most of the produce is grown in hydroponic systems, where the plants are supplied with nutrients via a nutrient solution. In most cases, Dew Crisp uses closed hydroponics (recycled water).
“Closed hydroponics is used for salad production in GFT, whereas open hydroponics is used in the production of tomatoes and cucumbers, as they are really sensitive to diseases that might spread with the water. For this reason, each of these plants has access to its own dripper,” explains Kaplan.
Sawdust and coco peat are used as growth mediums in the open hydroponic systems.
“Some farmers sterilise these mediums to reuse them, but I prefer using them only once to prevent disease outbreaks. We do, however, reuse the gravel in the open gravel system, after cleaning it with a chlorine solution at the end of each production cycle.”
In the same way, the crops that are planted in the soil are rotated to prevent a build-up of diseases.
Water quality largely determines the success of a hydroponic system, so a farmer should not even think of using it if the irrigation water is of poor quality or has high levels of chlorine or sodium. Water can be pretreated to rectify mineral imbalances, but this drives up costs. Water should, in any case, be filtered before use.
Dew Crisp has worked with scientists for years to refine its plant feeding programmes based on the nutritional requirements of various crops during different development phases.
“The trick is to supply exactly what the plant needs. An undersupply leads to plant deficiencies, while an oversupply is wasteful and might result in damage to the system and plants. To prevent this, we constantly monitor the recycled solution, plant growth and climatic conditions, and tweak the nutritional programme accordingly,” says Kaplan.
Achieving this with open-field crops is even more challenging due to soil differences. Soil, nonetheless, has a higher buffering capacity and is thus more forgiving.
The farm does not employ any climate-control technology because of its high capital and running costs. Instead, tunnel windows are opened and closed to augment ventilation and reduce the interior temperature.
Even without climate-control technology, production is energy-intensive, as the water has to be recycled continuously. Back-up generators are a necessity, as most of the salads will die within hours if water flow is interrupted.
Advice
Farming, and especially farming under protection, has become highly specialised over the years, with low profit margins leaving little room for error.
“In the past, when a buyer ordered a hundred frilly lettuces, we could plant 150 and it didn’t really have an impact on the bottom line. These days, production costs are so high that we plant to order and programme,” says Kaplan.
The shift has also made it increasingly important for farmers to make use of consultants to fill their knowledge gaps.
“If you want to be successful today, you need to surround yourself with people who are better skilled than you are in their respective jobs.”
Email Michael Kaplan at mkaplan@dewcrisp.com.
Lead Photo: Shade nets are used in the production of salad vegetables, as these are sensitive to sunlight, heat and wind. Photo: Dew Crisp
Kalera Announces The First Harvest For Atlanta Vertical Farming Facility That Will Produce Over 10 Million Heads of Lettuce Per Year
The new facility will supply schools, restaurants, grocery stores, hospitals, retailers, and more with safe, fresh, nutrient-dense, locally-grown greens
The new facility will supply schools, restaurants, grocery stores, hospitals, retailers, and more with safe, fresh, nutrient-dense, locally-grown greens
April 27, 2021
Source: Kalera
ATLANTA, April 27, 2021 (GLOBE NEWSWIRE) -- Kalera (Euronext Growth Oslo ticker KAL, Bloomberg: KSLLF), one of the fastest-growing US vertical farming companies in the world and a leader in plant science for producing high-quality produce in controlled environments, today celebrated their first harvest in their Atlanta-area facility. Its largest farm to date — and the largest vertical farm in the Southeastern United States — the facility is 77 thousand square-feet and has the capability of producing over 10 million heads of lettuce per year. Located in Forest Park, GA, the farm was built in just eleven months thanks in large part to the company’s modular building approach and has created dozens of new jobs in the Atlanta area.
“Our new Atlanta facility is open and performing in line with our expectations and we are eager to begin offering our local, fresh, safe, sustainable greens to the Georgia market,” said Daniel Malechuk, CEO of Kalera. “Our customers are telling us that there has never been a better time to ensure supply continuity, locally, than now and we are grateful Kalera can provide this.”
Kalera’s optimized nutrient and light recipes allow them to grow high-quality, pesticide-free, non-GMO produce at accelerated growth cycles. Planting at the Atlanta facility began in early March, and the first harvest began successfully last week. Kalera has so far experienced optimal operating efficiencies in Atlanta, particularly in terms of lighting productivity. All growth systems, environmental equipment, and technology have operated effectively since opening the facility on March 11. Due to strong sales indications in the region from both retail and foodservice customers, Kalera is implementing a faster ramp-up schedule than originally planned.
The facility’s location near the urban center of Atlanta cuts down on travel times for retailers, restaurants, and other customers who want access to the freshest, non-GMO, clean living lettuces and microgreens. Royal Food Service, a leading produce distributor in the state, is one of Kalera’s top partners bringing “pick-to-plate” greens to restaurants, hotels, schools, and other businesses including Ansley Golf Club, The Ritz-Carlton at Reynolds, Lake Oconee, The Georgia World Congress Center, several restaurants and many others. The lettuce is also available on the shelves of Publix Supermarkets.
“As the former Governor of Georgia, I could not be more excited that Kalera’s delicious greens are now available in the Atlanta area,” said Sonny Perdue, former U.S. Secretary of Agriculture, who joined Kalera’s Board of Directors earlier this year. “Kalera is leading the pack in a booming vertical farming industry. It’s a perfect example of the power of American innovation, creativity, and entrepreneurship to develop different, innovative ways to grow and provide food at home and around the globe.”
Kalera currently operates three growing facilities – two in Orlando and one in Atlanta and is building facilities in Houston, Denver, Columbus, Seattle, Minnesota, and Hawaii. Kalera is the only controlled environment agriculture company with coast-to-coast facilities being constructed, offering grocers, restaurants, theme parks, airports, and other businesses nationwide reliable access to locally grown clean, safe, nutritious, price-stable, long-lasting greens. Once all of these farms are operational, the total projected yield is several tens of millions of heads of lettuce per year. Kalera uses a closed-loop irrigation system which enables its plants to grow while consuming 95% less water compared to field farming.
Recently, Kalera also acquired Vindara, a seed company that uses genomics, machine learning, and computational biology along with traditional breeding methods to meet the market need for produce that is non-GMO, nutritious, high-yielding, and delicious. Explicitly intended for the new high-tech indoor growing environments, Vindara seeds offer growers the opportunity to capitalize on significantly higher yield potential, production efficiencies, and product customization — in a fraction of the time through reducing the grow cycle.
ABOUT KALERA
Kalera is a technology-driven vertical farming company with unique growing methods combining optimized nutrients and light recipes, precise environmental controls, and cleanroom standards to produce safe, highly nutritious, pesticide-free, non-GMO vegetables with consistently high quality and longer shelf life year-round. The company’s high-yield, automated, data-driven hydroponic production facilities have been designed for rapid rollout with industry-leading payback times to grow vegetables faster, cleaner, at a lower cost, and with less environmental impact.
Media Contact
Molly Antos
Phone: (847) 848-2090
Email: molly@dadascope.com
BrightFarms Founder And CEO Reflect On 10 Years of Growing Leafy Greens Indoors And Talk Future Plans
Valued at $6.8bn in the US alone (according to Research&Markets), the market for hydroponically-grown produce is no longer niche
31-Mar-2021 By Mary Ellen Shoup
Valued at $6.8bn in the US alone (according to Research&Markets), the market for hydroponically-grown produce is no longer niche and poised for strong growth over the next several years, predicts BrightFarms, a company growing a variety of leafy greens hydroponically in massive indoor greenhouses.
Please Click Here To Read The Full Article
New Research by Edith Cowan University: ‘Green Leafy Vegetables Are Essential For Muscle Strength’
Researchers examined data from 3,759 Australians taking part in Melbourne’s Baker Heart and Diabetes Institute AusDiab study over a 12-year period
According to new Edith Cowan University (ECU) research, eating just one cup of leafy green vegetables every day could boost muscle function. The study was published in the Journal of Nutrition; it found that people who consumed a nitrate-rich diet, predominantly from vegetables, had significantly better muscle function of their lower limbs.
Researchers examined data from 3,759 Australians taking part in Melbourne’s Baker Heart and Diabetes Institute AusDiab study over a 12-year period. They found those with the highest regular nitrate consumption had 11 percent stronger lower limb strength than those with the lowest nitrate intake.
According to scitechdaily.com, Lead researcher Dr. Marc Sim from ECU’s Institute for Nutrition Research said the findings reveal important evidence for the role diet plays in overall health. “Our study has shown that diets high in nitrate-rich vegetables may bolster your muscle strength independently of any physical activity,” he said. “Nevertheless, to optimize muscle function we propose that a balanced diet rich in green leafy vegetables in combination with regular exercise, including weight training, is ideal.”
Lead photo: mage: Dreamstime.com
26 Mar 2021
VIDEOS: How To Design A Successful Vertical Farm
Vertical farming provides a practical and cost-effective way to bring food production to congested spaces. Getting a vertical farm off the ground requires more than just a green thumb and some warehouse space, though
March 26, 2021
Vertical farming provides a practical and cost-effective way to bring food production to congested spaces. Getting a vertical farm off the ground requires more than just a green thumb and some warehouse space, though. Read on to find out how to design a successful vertical farm and start harvesting crops indoors in city environments.
What Is Vertical Farming?
Vertical farming is an indoor cultivation technique that maximizes the use of space for plant production. It involves layering multiple crops or types of crops in a highly controlled vertical hydroponic or container-based system. Those who are already familiar with indoor growing can think of it like a traditional hydroponic or container garden but on multiple levels.
The Four Key Design Factors
There are four key design factors that future vertical farmers must keep in mind if they want to bring down large, high-quality yields. They mimic processes that occur in nature but would otherwise be absent in a man-made system. The four factors are:
Lighting
Climate control
Nutrient control
Vertical integration
There’s little sense in purchasing seeds or rootstock until future farmers know exactly how they will provide for all the plants’ needs, so this is a good place to start. Let’s take a look at what factors farmers need to take into account before they start the design phase.
Adequate Lighting
All indoor farms and gardens require some form of artificial lighting. Farmers and growers who are still in the beginning stages of taking their operations indoors can get the basics down by visiting Agron and reading through their educational materials. However, vertical farming is a little more complicated than a normal hydroponic or container-based garden.Since plants will be grown on multiple levels, hanging lights from the ceiling isn’t always the best solution. Most vertical farmers purchase specialized ballasts and use LED lights that emit very little heat so they can keep their lighting as close to the plants’ canopies as possible. Some modern farmers also go in for more advanced options like installing rotating beds or utilizing smart lights, but they won’t make up for inadequate lighting for all levels of the vertical farm.
Climate Control
Plants can only grow and thrive under the right climate conditions. Vertical farms need good temperature, humidity, and air handling systems. In most cases, the building’s HVAC system will be able to handle heating and cooling demands. Without adequate ventilation and air handling systems in place, though, high humidity can negatively impact plants’ cellular respiration processes and create a perfect environment for the spread of fungal diseases. It’s worth taking the time to investigate options like dehumidification systems, exhaust fans, or specialized HVAC systems that manage humidity and airflow as well as temperature control.
Nutrient Control
Plants don’t get all the energy they need from photosynthesis alone. They require nutrients as well as light and water. Every species has a different set of requirements, but all terrestrial plants need macronutrients like nitrogen (N), phosphorous (P), and potassium (K) along with a smaller amount of micronutrients to fuel healthy growth and crop production. How they get those nutrients is largely a matter of farmers’ preferences.
There are four types of systems that are appropriate for vertical farming. On a small scale, container farming using soil, amendments, and fertilizers can work. However, most large-scale vertical farms eschew this traditional practice in favor of hydroponic or aeroponic systems. Hydroponic and aeroponic setups remove soil from the equation entirely. They’re similar systems, but while hydroponics gives plants access to nutrients via a water-based solution, aeroponics involves leaving the roots exposed and spraying them with nutrients.
Finally, some more sustainability-minded vertical farmers introduce elements of aquaponics into their farms. Aquaponics involves cultivating both plants and fish. The fish provide beneficial nutrients via a hydroponic system, while the plants filter the water so the fish can thrive. The benefits of vertical aquaponics systems include improved sustainability, water conservation, and added crop value.
Vertical Integration
Not all indoor farms are vertical farms. To qualify as a vertical farm, the plants must be cultivated on multiple levels in the same room. Warehouses are perfect for this approach since they have high ceilings that can accommodate tall towers of plants and all the equipment required to maintain optimal temperatures, humidity levels, light, and nutrient delivery. The key in designing a vertically integrated farm is to maximize crop production by ensuring that the plants have just enough space to grow and thrive and receive as much light as possible.
Crop Selection for Vertical Farming
It may be tempting to assume that since vertical farming occurs indoors in a highly controlled environment, that means it’s suitable for all crops. While it’s true that vertical farmers can grow almost any kind of annual plants, and even some perennials, that doesn’t mean they should. Farmers need to consider these factors when selecting crops:
Local demand
Time to harvest
Climate requirements
Revenue margins
If the idea is to get crops out to market as fast as possible, farmers may want to stick with fast-turn crops like lettuce, potherbs, and other greens. Most of these crops will be ready for harvest in six weeks or less. Slow turn crops have higher revenue margins but require more inputs and time to grow than leafy greens. It’s also perfectly fine to plant a combination of crops as long as they all have similar climate requirements.
Vertical Farming Is the Future
With climate change poised to wreak havoc on agricultural lands across the globe and the costs associated with water scarcity on the rise, vertical farming poses a viable solution. A well-designed system can help to conserve water, avoid the impacts of inclement weather, and provide reliable, year-long access to fresh food.
The best part is, designing sustainability features like LED lighting, aquaponic systems, or even wind turbines into the vertical farm from the beginning can help to offset both the financial and environmental costs of producing food for city-dwellers, often right in their backyards. It takes a large initial investment to get started, but the payoffs will be worth it.
Related Videos about How to Design a Successful Vertical Farm :
Vertical Farms | Design, and Innovation
Growing Up: How Vertical Farming Works
Designing the vertical farm
Vertical Farming
Tags: vertical farming design pdf, vertical farming business plan, vertical farming technology, vertical farm for home, vertical farming in india, hydroponic vertical farming, vertical farming equipment, how to start vertical farming,
Elevate Farms To Expand In New Zealand And New Jersey By Late 2021
Other than building high-tech production facilities and growing leafy greens, Elevate is also in the business of proving its detractors wrong as the company is on track to produce 1 million pounds of leafy greens in one of its 5,000-square foot facilities in Niagara, Ontario
Producing 1 million lbs of Leafy Greens Per Year
Other than building high-tech production facilities and growing leafy greens, Elevate is also in the business of proving its detractors wrong as the company is on track to produce 1 million pounds of leafy greens in one of its 5,000-square foot facilities in Niagara, Ontario.
Elevate is a vertical farming company located in Toronto, Ontario and
producing leafy greens in state-of-the-art facilities. With its Niagara facility spanning 20,000 square feet with a cultivation area spanning 5,000 square feet, it can produce as much food as 100 acres of land-based agriculture. This, according to chief strategy officer Travis Kanellos, is critical to people’s understanding of vertical agriculture and its benefits over other conservation agriculture methods. While organic agriculture strives to improve soil health and conserve biodiversity, the global agricultural land base still cannot support the growing population.
Travis Kanellos, Chief Strategy Officer
Further, organic certifications do not necessarily prohibit the use of any and all chemicals, but instead, greatly restrict the list of certified agrochemicals. Organic agriculture is thus only part of a global agricultural solution, while vertical farming should also play an increasingly important role as it does not use any agrochemicals and demonstrates unparalleled planting density.
Elevate primarily produces leafy greens but has also successfully grown tomatoes, strawberries, beans, and various plant proteins during research trials. With many vertical farms producing crops with low caloric value, such as microgreens and herbs, Elevate is eager to broaden this range and include higher value, higher calorie crops. Nevertheless, Elevate has had significant success producing leafy greens and is reportedly one of few profitable vertical farming facilities that is actually delivering its forecasted yields, which Kanellos attributes to the company’s diligent approach and scientific partnerships.
“Typically we’ve seen the industry of indoor farming; secure funding, build the farms and expect everything to come to them. But building it then trying to figure it out is backwards to us. We’ve spent years of research and commercialized production with intellectual property. When you build a company through 15 years of R&D, along with our core team’s execution track record and all of the experience from our academic partners, we feel that is a pretty good recipe for success.”
The company’s most important partnership is with Intravision, a Norwegian agtech company with additional offices in Toronto and Shanghai. The company’s products include controlled environment systems, LED lighting, and research tools. However, Intravision does not limit itself to simply supplying products; the company also develops partnerships to continuously research and improve production methods in indoor agriculture. So while Intravision does supply much of the hardware for Elevate farms, the two companies have a strong partnership and collaborate throughout project implementation, crop production and aligned business interests.
Looking ahead, Elevate aims to have its pilot facility operating at 100% capacity in the coming months. Also, the company plans to build and begin operating facilities in New Zealand and New Jersey by late 2021.
“Our pilot facility in Toronto allowed us to reach out and develop global relationships. What started in Canada with the 1,000 square foot pilot facility in Toronto has led to agreements across Canada and New Zealand for the construction of more than 10 facilities, with each slated to produce 1 million pounds of produce annually,” says Kanellos.
Elevate is currently deeply entrenched in implementing artificial intelligence to optimize its production systems as well as vision systems to generate actual predictive outcomes. Kanellos is keen on Elevates future stating “we believe the next step for Elevate, aside from global scale, is to deepen the ability for our facilities to become autonomous. Our field-grown yields, profitability at wholesale market prices are great first steps but true AI and facility optimization sets the groundwork for years to come.”
Lead photo: Panoramic view of the pilot facility
For more information:
Elevate Farm
Travis Kanellos, Chief Strategy Officer
+1 905-580-2388
Tkanellos@elevate.farm
www.elevate.farm
For more information:
Intravision Canada
www.intravisiongroup.com
Publication date: Fri 26 Feb 2021
Author: Rebekka Boekhout
© VerticalFarmDaily.com
TURKEY: The Goal Is To Establish a Million Square Meters of Agriculture Factory
Vertical farming practice is a method of soil-free farming, unlike traditional methods. Agriculture can be done completely with water without using any soil
The rapidly increasing world population causes an increase in the demand for food. People expect to consume fresh fruits and vegetables throughout their lives. It is getting harder every year to meet the fresh food demand of people due to the declining fertile lands due to the increasing urbanization and industrialization, the climate changes, and the inadequate irrigation of agricultural lands. While more production is made with the hormone drugs and other pesticides used to meet this demand, the yield and quality of the fresh foods produced decrease.
HGT Tarım, a Pimtaş establishment, started the works to establish an agricultural factory of 1 million square meters in order to prevent all these problems and to meet the increasing demand for fresh and organic food. All necessary work is underway for the Vertical Agriculture project, which is carried out jointly with PİMARGE and Gebze Technical University.
Smart Agricultural Investment
Vertical farming practice is a method of soil-free farming, unlike traditional methods. Agriculture can be done completely with water without using any soil. Thanks to the Vertical Farming system, there is no need for agricultural land, and the water used is used continuously by using the recirculation system. It allows us to obtain more efficiency with less water usage.
The products that meet our mineral needs in water will be made efficient by lighting with special LEDs without using any fertilizer drugs. While lettuce soil yields 60 crops in 1 day in our latest works, this period is reduced to 15 in 1 day with the Smart Agriculture system.
Products that are constantly working and controlled by automation with special software are indispensable for customers who want to buy fresh products at affordable prices, apart from being 100% organic.
Our project will stimulate the economy
The arable land requirements of traditional farming are too large and invasive to remain sustainable for future generations. With rapid population growth rates, arable land per capita is expected to decrease by approximately 2050% in 1970 compared to 66. Vertical farming allows more than ten times the crop yield per acre compared to traditional methods. Unlike traditional farming in non-tropical areas, indoor farming can produce crops year-round. All seasonal farming increases the productivity of the field surface 4 to 6 times depending on the crop.
All processes are environmentally friendly
All products that will be used in the system are completely recycled. Environmental problems are becoming less dangerous for the agricultural industry with vertical farming. Farmers do not use chemicals such as pesticides, so the whole process runs environmentally friendly. Vertical farming has an important role in a sustainable environment. In addition, it enables the production of fresh and healthy products and production for 365 days without the need for agricultural knowledge.
Speaking about the project, our Chairman of the Board of Directors Şamil Tahmaz said, 'Thanks to this project, which we will implement with 100% domestic and national means, we will protect our country's natural resources and ensure that our nation can access the food products they need most whenever they want. He said to produce what our country needs most and to produce more. ''
CDC Updates E. coli Outbreak Numbers
The Centers for Disease Control and Prevention has added 16 more people to an E. coli outbreak investigation of unknown origin
By CHRIS KOGER
November 25, 2020
The Centers for Disease Control and Prevention has added 16 more people to an E. coli outbreak investigation of unknown origin.
There are now 39 cases in the E. coli O157:H7 outbreak, according to a CDC notice on Nov. 23. The previous number of ill people as 16, according to the CDC. Cases have been reported in 18 states; there have been no deaths.
The CDC and Food and Drug Administration are not advising people to avoid any particular food at this time.
“State and local public health officials are interviewing ill people to determine what they ate and other exposures in the week before they got sick,” according to the CDC’s Nov. 23 update. “Of the 22 ill people interviewed to date, all reported eating a variety of leafy greens, like spinach (16), romaine lettuce (15), iceberg lettuce (12), and mixed bag lettuce (8). No single type or brand of leafy greens or other food item has been identified as the source of this outbreak. CDC is not advising people to avoid any particular food at this time.
Lead photo: (Courtesy CDC)
Vera Vertical Farming Technology Introduced in Finland’s Largest Retail Group
Finland’s largest retailer is now carrying produce farmed in vertical-farming centers to provide ultra-fresh produce year round.
Netled And Pirkanmaan Osuuskauppa Sign A New Long-Term Cooperation Agreement
In the photo: Ville Jylhä, COO of Pirkanmaan Osuuskauppa
Netled has entered into a significant long-term cooperation agreement with Pirkanmaan Osuuskauppa, a regional operator of S-Group, the largest retail chain in Finland.
Netled’s Vera Instore Premium Growing Cabinets, offering a range of herbs and salads, will now be a regular feature in Prisma retail stores in the Pirkanmaa area. Herbs and some of the leafy greens are grown in-store in the cabinets, and are harvested directly off the shelf. The growing conditions are fully automated and controlled remotely.
The newly opened Prisma Pirkkala is Finland’s first hypermarket to launch the new Vera Instore Cabinets. In addition, Netled will deliver to the hypermarket salads and herbs grown on its own vertical farm nearby, thereby allowing customers to get same-day harvested herbs and salads all year round.
”With this newly formed collaboration we can offer consumers fresh, ultra-locally produced products and at the same time introduce them to vertical farming as a method of ecological, urban farming”, says Ville Jylhä, COO of Pirkanmaan Osuuskauppa.
S-Group is a customer-owned Finnish network of companies in the retail and service sectors, with more than 1 800 outlets in Finland. The group offers services in areas such as, supermarket trade, department store, and speciality store trade. As the largest retail group in Finland, S-Group’s main focus is also on sustainable food and innovative ways it can offer healthy and responsibly produced food to its customers.
Netled Ltd. is Finland’s leading provider of turn-key vertical farming systems and innovative greenhouse lighting solutions.
”As the leading vertical farming technology provider in Finland, we have developed an extensive range of products for all segments of vertical farming. Instore growing systems are a rapid-growth segment, and our cutting-edge Vera technology puts us at the forefront of the instore space”, says Niko Kivioja, CEO of Netled Ltd.
“The agreement with Pirkanmaan Osuuskauppa is just the latest proof of concept, and is also a clear signal to potential customers, investors and other global partners that Vera technology is a game changer.”
18th December 2020 by johannak
More information:
Niko Kivioja
CEO, Netled Ltd
+358 50 360 8121
Robert Brooks, Investor Relations and Communications Manager
+358 50 484 0003
Hi-Tech Vertical Farm Could Produce A Third of Leafy Greens And Create 30 Jobs
Wayne Furbert, the Cabinet Office minister, said the state-of-the-art farm could also reduce the cost of food production and create up to 30 jobs
November 13, 2020
Wayne Furbert, the Minister for the Cabinet Office (Photograph by Blaire Simmons)
A vertical farm could produce almost one-third of Bermuda’s demand for leafy greens – the equivalent of 200 acres of farmland, it was revealed today.
Wayne Furbert, the Cabinet Office minister, said the state-of-the-art farm could also reduce the cost of food production and create up to 30 jobs.
Mr. Furbert added the Government was close to finalizing plans for the development and finance for the project.
He said: “Vertical farming will utilize the latest technology to grow leafy greens in a controlled environment.”
“The aim of this venture is to reduce the cost of food to the general public, reduce the reliance on imported leafy greens, and boost employment in Bermuda.”
Vertical farming involves the production of crops in a controlled environment, usually indoors.
It also uses techniques such as hydroponics instead of soil and the crops grow in stacked layers.
Mr. Furbert said the hi-tech farm would be “environmentally sound”, use 95 percent less water than conventional production, and no pesticides.
He added: “A key component of this project, and in line with the Government’s vision to create a nation of owners, will be to allow Bermudians to invest in this entity so that they can enjoy the benefits of ownership of local food production.”
According to environmental studies, there are about 760 acres of land available for farming in Bermuda, although only 365 were being actively worked.
The plans will be presented to the Cabinet Committee for Economic Development next week.
Mr. Furbert also fleshed out plans for a proposed fish processing center, a drive to attract technology companies to the island, and a bid to expand the intellectual property industry.
He said: “The shoreside fisheries complex will be the operational center of a new, long-anticipated enterprise that will transform and reposition Bermuda’s commercial fisheries sector.
“It will be a purpose-built facility where fish will be cleaned and processed for sale to the Bermuda market.
“This facility is just the start of our ambitions and while targeted towards local consumption, it has the potential to grow into international exports.”
Mr. Furbert said that the aim of technology companies was to “create a hub wherein technology companies can set up and conduct their business right here in Bermuda in a business-friendly environment”.
He added: “We have recently been engaged in very fruitful discussions with global tech companies about relocating to Bermuda.”
Mr. Furbert said that Government was examining how to overhaul legislation “to remove bureaucracy and red tape”.
He highlighted that changes had already meant the arrival of 58 technology workers from Pakistan.
Mr. Furbert said: “They are part of a very large and successful technology company and it is our hope that this will be the genesis of their setting up business long-term in Bermuda and training and hiring Bermudians.”
He added further amendments to legislation would make Bermuda an attractive location for international companies that wanted to register trademarks and copyrights.
Mr. Furbert said: “We have adopted a phased approach to overhauling our intellectual property legislation and by the Spring of 2021 we shall have achieved significant enhancements in this realm.
“These are just a few of the major initiatives the Cabinet Ministry is forging ahead with in the next year or so, and I am very optimistic that we shall succeed in generating positive economic activity as a result.”
New Smart Urban Farm Takes Root
Using New Tech, it Can Grow Up to 100 Tonnes
or About 1% of Leafy Vegetables Grown Here
October 23, 2020
An urban farm that aims to produce high-yield greens without sacrificing any flavour by leveraging Internet of Things technology was officially launched yesterday.
Commonwealth Greens took root in Jurong in May. The forest-like farm consists of over 6,200 pillars, each of them 2.4m tall, that are reminiscent of the foliage of trees.
Positioned in six different rooms the size of Housing Board flats, the pillars in each room support one type of leafy green: lettuce, kale, chard or herbs. Hydroponics is used to grow the plants.
The farm can grow up to 100 tonnes of vegetables a year, which is close to 1 per cent of leafy vegetables grown locally.
Minister for Sustainability and the Environment Grace Fu (centre) viewing Just Harvest, the latest farm to table solution which will be announced soon for potential clients such as hotels, restaurants and cafes. ST PHOTO: TIMOTHY DAVID
During the launch yesterday, Minister for Sustainability and the Environment Grace Fu visited the farm as well as Archisen, the agri-tech firm that set up and manages Commonwealth Greens.
Archisen's co-founder and chief technology officer Sven Yeo said Commonwealth Greens is one of the highest-yielding indoor farms in Singapore and that it will support and contribute to the country's goal to self-produce 30 per cent of its nutritional needs by 2030.
The farm's leafy greens are currently sold on online supermarkets such as RedMart and PandaMart, under the brand Just Produce. Each 100g salad mix that costs between $4 and $4.50 comprises a variety of lettuce and kale, along with either mustard greens, sorrel or mizuna.
From the middle of next month, the farm will start selling speciality herbs - mustard greens, ice plant and sorrel - in 20g boxes which will cost between $4 and $5.
Archisen has also developed a mini version of its farming system.
Shorter pillars brimming with full-grown veggies are stored in a glass cabinet and can be sent to restaurants for direct harvesting. From next month, the company will deploy those cabinets to five hotels, restaurants and food service companies.
Walls of edible greens: This forest-like area is one of six grow rooms in a new urban farm called Commonwealth Greens. Leafy greens such as lettuce, kale, chard and sorrel are grown hydroponically along each 2.4m white pillar. ST PHOTO: TIMOTHY DAVID
It is not just its aesthetic that makes Commonwealth Greens unique.
To ensure optimal yield, fast growth and highly nutritious and flavourful greens, the vertical systems are powered by a smart cockpit that heavily leverages Internet of Things technology, data analytics and sensors.Culinary uses for speciality herbs
ICE PLANT
The edible succulent is coated with tiny, crystal-like beads that give the unique vegetable a frosty, magical appearance.It typically grows in saline environments and its beads trap salt - hence its salty taste.
Archisen grew different sets of ice plant using nutrient solutions filled with either table salt, sea salt or Himalayan pink salt. It was discovered that table and sea salt made the taste too sharp for comfort but Himalayan pink salt was easier on the palate. The mildly salty succulent has a crunchy texture, and is juicy and refreshing.
MUSTARD GREENS
The dainty-looking leaf with the frilly edges can be a healthier substitute for wasabi.
The fierce wasabi heat hits you immediately, spreading down the throat and up the nose. You may tear up a little too.R&D was used to intensify the wasabi flavour.
RED-VEINED SORREL
The leaves can replace lemon juice or dressing in salads. On second bite, the citrusy flavour explodes, giving a sour surprise.Data is continually stored in the cloud, in real time, for the scientists to analyse and to drive automation. For example, if the pH of the nutrient for lettuce reaches unhealthy levels, sensors will alert a device to automatically restore the acidity level."
As we have more growth cycles over time, our data sets increase, and that enables us to construct mathematical models to predict the outcome of how we grow," said Mr Yeo.
Tenders awarded to turn 9 HDB carpark rooftops into urban farming sitesWild teen to urban farmer: He wants to make Singapore a more sustainable and liveable city
Archisen's office, which is one level above Commonwealth Greens, also houses a research lab for conducting experiments and testing new solutions.In the near future, the company plans to build indoor fruit orchards or vineyards.
Parliament: Encourage growth of urban farming to secure Singapore's food supplies, says Ang Wei NengFeeding cities of the future
Scientists in the lab are now growing black, red and green grapes in a controlled environment. In 10 months, the vines have started to bear clusters of grapes, each fruit about the size of a chickpea. Through traditional farming, it takes about three years to fully grow grapes.Although immature and smaller grapes tend to be sour, the black grapes from the lab taste sweet.
A version of this article appeared in the print edition of The Straits Times on October 23, 2020, with the headline 'New smart urban farm takes root'.
Lead photo: Archisen co-founder and chief executive Vincent Wei (left) and chief technology officer and fellow co-founder Sven Yeo seen here with full-grown veggies from the mini version of its farming system, which will be deployed to restaurants and hotels.ST PHOTO: TIMOTHY DAVID
Can Vertically-Grown Leafy Greens Make Your Salad Fresher And More Sustainable?
As indoor farms can control everything from temperature to humidity to airflow and even lighting schedules, their products are often marketed as more sustainable than outdoor agriculture
Courtesy of Forward Greens
A warehouse may seem like an odd place for a farm, but it's one of the places you'll find arugula, kale, and other leafy greens growing in Vancouver, Washington. The 25,000 square foot warehouse is home to Forward Greens, one of several indoor vertical farms attempting to use technology to make our lunch salads taste better and be better for the planet.
"We're trying to grow the cleanest healthiest greens we can while preserving the earth's resources," said Ken Kaneko, the founder of Forward Greens. Even if you haven't yet had greens from an indoor farm, chances are more and more of the greens in your salad are going to come from farms like Forward Greens, Gotham Greens, Bowery Farming, and others.
Related: Young Farmers Need Land and These Organizations Are Helping Them
What Exactly Is a Vertical Farm?
Simply put, it's a farm where rows of produce are stacked. "We grow up instead of out," Kaneko said. In the late 1990s and early 2000s, Columbia University professor and microbiologist Dickson Despommier and his graduate students began popularizing the idea of vertical indoor farms as one answer to some of the world's biggest problems: how to feed a growing worldwide population, especially with more and more people, centered around cities, and how to produce that food more efficiently and sustainably.
Today most indoor farms use soilless farming techniques. Some like, New York-based Gotham Greens, one of the early pioneers of indoor farms and whose products you'll find in Safeway, Meijer, and Harris Teeter, among others, use a hydroponics system. Other soilless systems include aeroponics and aquaponics.
Does Arugula Grown on an Indoor Farm Taste Better Than Arugula Grown Outside?
While outdoor farms rely on water, sun, and sometimes luck to produce leafy greens, most vertical indoor farms use technology and constant data monitoring to grow their crops. That data means that indoor farms can tweak everything from how your arugula tastes to how it feels to the nutrients it contains.
But beyond the tech, depending on where you live, leafy greens grown indoors might be fresher. Most of the salad greens you find in the supermarket likely came from Salinas, California, or Yuma, Arizona. According to Kaneko, Forward Greens delivers its products to markets in the Pacific Northwest within 48 hours of harvest. As vertical farms aren't dependent on weather, you can buy the same arugula from the same farm year-round. "We can provide a consistent year-round supply," said Gotham Greens CEO Viraj Puri. And that supply is also fully traceable, possibly making it safer.
Are Leafy Greens from an Indoor Farm More Sustainable?
As indoor farms can control everything from temperature to humidity to airflow and even lighting schedules, their products are often marketed as more sustainable than outdoor agriculture. According to Bowery Farming, whose leafy greens are available in the Mid-Atlantic and Northeast at Whole Foods Market, Giant Food, Stop & Shop, Walmart, and Weis Markets, their indoor farms are more "productive on the same footprint of land than traditional agriculture."
Similarly, Forward Greens says through its technology; it can use 95 percent less water, 99 percent less land, and 100 percent less pesticides compared to outdoor agriculture. But there's not much data on how vertical farms compare to their conventional counterparts. Researchers from Cornell University are in the middle of a three-year grant looking at not only how controlled-environment agriculture compares to traditional field agriculture in terms of energy, carbon and water footprints, profitability, workforce development, and scalability but what if any educational and psychological benefits local systems can offer by connecting urban people to their food. However, it's not clear if that study will also account for food waste, which has been found to be as high as one-third on traditional farms, and which both Puri and Kaneko say their farms can reduce.
While indoor farming likely isn't going to save the planet it may be one part of the puzzle and will make it easier to get fresh, locally grown salad greens year-round.
Albertsons To Bring Plenty Leafy Greens To 400-Plus Stores
Plenty products are already available in some Safeway and Andronico’s locations in the Bay Area, and the plan is for more of the company’s stores in California — Albertsons, Vons and Pavilions locations — to also carry Plenty products as supply increases
August 12, 2020
Boise, Idaho-based Albertsons has entered into an agreement with South San Francisco, Calif.-based Plenty Unlimited to bring its leafy greens to more than 430 California stores.
Plenty products are already available in some Safeway and Andronico’s locations in the Bay Area, and the plan is for more of the company’s stores in California — Albertsons, Vons and Pavilions locations — to also carry Plenty products as supply increases, according to a news release.
Stores plan to carry four Plenty products to start: baby arugula, baby kale, crispy lettuce and mizuna mix.
“We pride ourselves on offering fresh, quality products that surprise and delight our customers,” Geoff White, executive vice president of merchandising for Albertsons, said in the release. “Plenty’s data-driven and sustainable methods are truly innovative, and we look forward to bringing their unique and exciting products to more customers in California as they scale their operations.”
The company’s indoor vertical farm is powered by wind and solar energy, and its operation leverages customized lighting, machine learning and data analytics, per the release. The farm can grow a million plants at a time and process 200 plants per minute.
Lead Photo: Albertsons and Plenty announced a new partnership. ( Albertsons and Plenty )
Related Topics: Produce Retail Sustainability Lettuce
Improving The Profitability and Sustainability of Indoor Leafy-greens Production
A multi-university team of horticulturists, engineers and agricultural economists led by Michigan State University (MSU) has received a four-year, $2.7 million grant from the U.S. Department of Agriculture (USDA) to study indoor production of leafy greens. Industry partners have matched funding, bringing the project total to $5.4 million
February 11, 2020
By urbanagnews
A multi-university team of horticulturists, engineers and agricultural economists led by Michigan State University (MSU) has received a four-year, $2.7 million grant from the U.S. Department of Agriculture (USDA) to study indoor production of leafy greens. Industry partners have matched funding, bringing the project total to $5.4 million. The investigators on the grant include Erik Runkle, Roberto Lopez and Simone Valle de Souza of Michigan State University, Chieri Kubota of Ohio State University, Cary Mitchell of Purdue University and Murat Kacira of University of Arizona.
Leafy greens include commonly consumed vegetables such as lettuce, kale, and microgreens. Production challenges outdoors have led to interest in growing these specialty crops hydroponically in controlled environments, such as indoor farms. However, there is little information on whether this is economically viable. Capital and operating costs can be significant for startups, especially as it relates to light-emitting diodes (LEDs) and cooling systems. Leafy greens are a good candidate for indoor farming because they can be grown rapidly and in relatively small spaces. Indoor environments are heavily controlled, so growers aren’t constrained to a small geographic area within the U.S. There are, however, other geographic concerns.
The team and its collaborators have three major goals:
Define optimal profitability based on yield and other high-value attributes of the plants, such as nutrition content
Optimize indoor environmental conditions, such as humidity, air movement, temperature, light and carbon dioxide concentration, to increase yield and high-value attributes
Encourage indoor farming stakeholders to collaborate with academic and industry groups that are working in controlled-environment agriculture.
The long-term project goals are to help integrate indoor farming into the specialty-crop segment of agriculture in the U.S.; to increase the sustainability and hence profitability of this rapidly emerging sector, and to locally produce leafy greens that have higher quality attributes. To this end, our economists will better understand operating and capital expenditures (capex), and define risk and production scenarios that are most profitable. Our horticulturists and engineers will improve production efficiency, product quality, and value-added attributes of leafy greens for reliable, consistent, year-round production. In addition, the team will design and test more effective localized air-distribution methods suitable for indoor production systems, as well as develop strategies to better manage humidity around plants to reduce tip burn. While the project focuses on leafy greens, the results will also inform a wide range of controlled-environment growers through the development of growth recipes, strategies for nutritional content and anthocyanin enhancement, environmental management recommendations, and insights for economic sustainability as well as market and consumer perception of locally produced crops.
For more information, visit the project website at scri-optimia.org.
Direct Delivery
With its fresh delivery service and strategic retail partnerships, Great Lakes Growers is building a business for the modern consumer.
May 28, 2019
Chris Manning | Photos by Allison Krieg
Great Lakes Growers, based in Burton, Ohio, produces leafy greens and herbs hydroponically in glass greenhouses.
Great Lakes Growers wants to change the way people buy and think about salad. The hydroponic greens and herbs operation is capitalizing on changing consumer tastes and sending its products straight to customers’ doorsteps with a new initiative called Great Lakes Growers Express.
Located in Burton, Ohio — a village with a total population of less than 1,500 — the operation was founded in 2011. But through relationships with restaurants and regional grocery store chains such as Buehler’s, Giant Eagle and Heinen’s, the business can reach a customer base in Ohio and neighboring states that would make up several dozen Burtons. And if its home delivery service goes according to plan, the company’s reach will extend even further.
“There’s about 80 million people we can reach,” says John Bonner, owner and founder.
“There are home delivery services out there for food, but we’ve always heard the complaints about, well it’s the produce that is really bad,” says Tim Ward, who does marketing for Great Lakes Growers and helped develop the Great Lakes Growers Express concept. “The other food is fine; the produce doesn’t hold up because they’re really packaging it and shipping it in traditional methods, the way you might find in a traditional grocery store. They’re getting it from out West. Everything’s being shipped directly from the source here.”
Through Great Lakes Growers Express, which officially launched in March, consumers can order combinations of living lettuce, fresh-cut herbs and other leafy greens from the grower online, and have them shipped directly to their home via UPS. Currently, there are four different combinations to pick from and each is available for delivery weekly or every other week for $29.99 per delivery.
According to Bonner, the logic behind the delivery service is two-fold. First, it opens new markets in urban and rural communities that don’t have grocery stores nearby — like inner-city Cleveland or a small town in Pennsylvania.
Second, Bonner believes that by shipping fresh greens directly to the consumer, he can tap into a younger customer base that seeks out instant gratification and is already ordering other goods like pet food, razors and toothbrushes online with pre-determined shipping (and payment) dates. It’s also a customer base, Bonner says, that wants fresh produce and worries about the quality of food they are consuming.
“Even if you’re getting it from a local guy like me, it’s still three or four days old at the store, which there’s probably not much difference in freshness,” Bonner says. “So it had to be fresh, had to be good, and the cost had to be no more money than they’re going to pay when they go the grocery store.”
John Bonner, left, and Tim Ward
Bonner’s beginnings
Bonner grew up in Burton, where his entire family is connected to the horticulture industry. On his father’s side, the main family profession has been traditional field farming. On his mother’s side, his grandfather founded BFG Supply, a greenhouse supply company based in Burton. Additionally, his father founded Dillen Products (later renamed HC Companies), a manufacturer of injected molded pots whose clients included many members of the Van Wingerden family, several of whom own large-scale ornamental operations.
“That’s how I got into farming,” Bonner says.
Additionally, his sister owns Eagle Creek Nursery, a wholesale ornamental producer. Originally, though, horticulture was not the path Bonner pursued. After graduating high school, Bonner attended Capital University in Columbus and earned a bachelor’s degree in finance. From there, he took a job at Merrill Lynch. But according to Bonner, it wasn’t work that fit him.
Bonner worked at Eagle Creek Nursery for a time after leaving Merrill Lynch, gaining notoriety in the industry for implementing sustainable business practices. In 2011, he left the family business and founded Great Lakes Growers.
The business started out small. He tested out his concept with 300 square feet of poly greenhouses and a basic hydroponic system constructed from supplies at Home Depot — but expansion came quick. From there, he was able to get his greens into local restaurants and eventually local grocery chains.
Today, Great Lakes Growers has 80,000 square feet of production space and is currently in the middle of an expansion that will double its size. Down the line, Bonner sees a need to hire growers. (Currently, he’s hands-on with the plants seven days a week.) But he can’t envision a future where he doesn’t spend at least some time in the greenhouse working directly with the crops.
“I cannot see myself not coming in here at least one day a week and watering everything and taking care of everything,” he says. “I can call everybody up in an hour and find out, ‘Hey, where do we want to do this, do that?’ But it’s just got to have more structure as we get bigger. And that’s what we’re doing. We’re expanding as an organization; we’re broadening out. So it’s fun. It’s challenging.”
Great Lakes Growers is in the midst of an expansion but it's already mapping out its next building project.
Fresh deliveries
Bonner and Ward, another Burton native and someone Bonner has known for years, started working on the delivery service about a year ago. According to Bonner, Great Lakes Growers Express and has been rolled out slowly on purpose in order to solve any potential logistical issues. The idea appealed to Bonner as a way to diversify outside of traditional retail methods.
“We told our retail partners we were doing it and they said, ‘Spot on man.’ Because they’re seeing it, too,” he says. “We’re doing meal kits and things for them, but their product development, this whole convenience thing, is what I was seeing when I started. This whole feeling of instant gratification — well it’s getting on steroids now. And I think we see it in all these subscription services and things like that. It’s not going to stop.”
To start, the company sent out greens and herbs via UPS and FedEx to friends and family. When the packages arrived, those friends and family sent back pictures of the greens to see how they held up. Bonner says that they sent out packages in a variety of weather conditions from extreme heat to extreme cold to make sure the greens would remain fresher than what they could buy at the store.
“We were testing so many things and looking at the variables,” Ward says. “I think we got it down to where anything within basically 24 hours is doable. So in any place that UPS can ship within a day is perfect.”
A key to the service is that Great Lakes Growers offers living lettuce with the roots still attached — allowing the lettuce to last longer once its in the customer’s fridge. Each order is also checked by hand in Burton to ensure that the greens are fresh and the order is correct. According to Ward, word-of-mouth and rave reviews from customers on social media are the driving factor as the business continues to grow organically and expand into new areas.
“We want to make sure that we can check every single box and we’ve had zero complaints so far of anything that we’ve shipped out to consumers,” Ward says. “And frankly I expect that to continue.”
Offering fresher products than the local grocery store is the main selling point for Great Lakes Growers Express. Say a customer orders greens on a Sunday. On Tuesday of that week, the greens are harvested, packaged and shipped out. The next day, the greens arrive at the customer’s doorstep via UPS. That’s even faster than the same greens, harvested the same day, would arrive at the local grocery store.
“It’s more units than you might find on a trip on a Monday to a grocery store, but it’s also got a shelf life that’s two weeks plus,” Bonner says. “So that whole process of training people that say, ‘Hey wow, got five heads of lettuce or six heads of lettuce, whatever it is, I can’t eat all that.’ But then if you leave it in your fridge for a week, two weeks, and you look at it, you’re going to go, ‘Damn, that still looks better than anything I’ve put in there.’”
Great Lakes Growers Express launched in April 2019 as part of Bonner's effort to better engage with modern consumers.
A key part of Great Lakes Growers' labor force is workers from the neighboring Amish communities.
Growing into the future
Right next door to the greenhouses filled with greens and herbs in Burton, Great Lakes Growers is in the process of expanding. Walk through one door and instead of greens, you’ll find construction crews building glass greenhouses and setting up the space for a concrete floor to be poured. Each greenhouse will be outfitted with LED lighting, environmental control systems, boom irrigation and other technologies since Bonner believes embracing technology and its possible benefits is key to keeping the business moving forward.
“I’m a big believer that ultimately, we have to get the cost inside the greenhouse down in the space or an area where we’re competitive with the field-grown stuff,” he says.
The plan, Bonner says, is to have enough growing space that products shipped via Great Lakes Growers Express have their own production area. He adds that the additional space is already “sold out” — meaning he already knows what will be grown there. And another expansion in the near future isn’t out of the question either.
There are also plans to continue diversifying the business. In addition to the delivery service — which Bonner and Ward hope to expand to new areas in the coming months — Great Lakes Growers products are now sold at Giant Eagle under the grocery store’s Market District branding. And other retailers are selling the product with the Great Lakes Growers logo on the package.
Outside of that, Bonner says selling greens to the food service sector is the business’ largest growing market share.
The key for whatever comes next, however, is still freshness. Regardless of what is next for Great Lakes Growers, and for Bonner, he says that must remain the core principle of the business.
“I look at it as we need to have stuff there that tastes better, looks better, grows better,” he says. “We need to give our customers the best price, so they can compete with their competitors. But ultimately, we’ve got to give the consumer the best price and the best quality.”
To learn about Great Lakes Growers' Amish workforce, search 'Amish' at producegrower.com
Hydroponics Leafy greens Herbs Grocery Harvesting
Brooklyn, New York: Spinach Ice Cream: Made With Leafy Greens, Olive Oil And Salt
Spinach, packed as it is with vitamins and fibers, is one of the most popular veggies that's recognized as a superfood. Added to pasta or simply sautéed with garlic, spinach is also an incredibly versatile green.
Now, Van Leeuwen Ice Cream, an artisanal frozen treats shop based in Brooklyn, New York, has launched a spinach-flavored ice cream in honor of cartoon sailor Popeye’s 90th birthday and the annual Fleet Week.
This spinach ice cream doesn't just contain the leafy green, however. It's also a dairy-free ice cream, perfect for vegans to enjoy it as well.
"When we were presented with the opportunity to collaborate with an icon like Popeye, we wanted to make a special flavor that was plant-based since everyone knows he gets his strength from eating lots and lots of spinach," Ellie Zitsman, head of research and development at Van Leeuwen Ice Cream, told TODAY Food via email. "Our vegan ice cream base is rich in nutrients and packed with protein since it’s made with house-made raw cashew milk, coconut cream, raw organic coconut oil, pure cocoa butter and organic cane sugar."