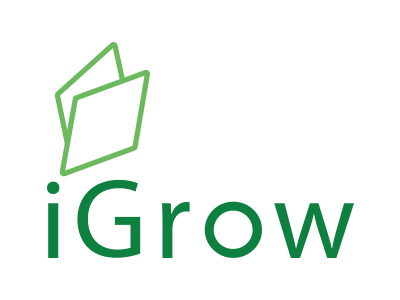
Welcome to iGrow News, Your Source for the World of Indoor Vertical Farming
How Vertical Farming Helps Save Water
In many places around the world, for example in the Middle East, water resources are limited and their price is high. Reducing water consumption on a vertical farm in such regions can have a very positive economic and environmental impact
Generally, vertical farming uses 95% less water than traditional farming. At iFarm we have improved this indicator.
In many places around the world, for example in the Middle East, water resources are limited and their price is high. Reducing water consumption on a vertical farm in such regions can have a very positive economic and environmental impact. iFarm engineers have recently developed and patented a dehumidification system allowing to reuse the water that farm plants evaporate during growth.
How does it work? Let's take a look at a vertical farm with a cultivation area of 1000 m2. It produces 2.5 tons of fresh salads and herbs every month. To get such a yield, you need 2020 liters of water daily, most of which — 1400 liters — is used for plant nutrition. However, the daily actual water consumption is almost three times less. 2020 liters are poured into the system once, and then the "engineering magic" begins.
At iFarm vertical farms, we use flow hydroponics, i.e the roots of plants are constantly placed in the nutrient solution and consume it whenever they need, getting all the macro- and microelements in the right ratio and concentration.
From 1400 liters of the water, plants use only 80 liters for weight gain (consumption of nutrients from a larger volume is a prerequisite). The remaining 1 320 liters the plants simply evaporate. In the process of transpiration, a lettuce leaf can evaporate an amount of water that exceeds its own weight many times. We collect this water with air conditioners and dehumidifiers, purify it and reuse it in production, maintaining the optimal humidity inside at 70%.
The second "source" of water on the farm is the water supply system — another 700 liters are collected from it and then run through a special filtration unit, resulting in 560 liters of purified and 140 liters of untreated water. The latter is collected in a special tank for technical needs (washing hands, pallets, floors, etc.).
Thus in order to save water, we started collecting it from air conditioners and dehumidifiers that were originally designed to maintain optimal moisture on the farm. This approach allows the production to use only 700 liters of tap water per day, which is three times less than growing plants in conventional hydroponic greenhouses.
We are currently improving the automation of the nutrient solution replacement. The system will determine what macro- and microelements are missing in the trays at a given time and adjust them. According to the calculations of engineers, this will reduce the number of times the sewerage has to be drained completely and almost halve its consumption — from 360 liters to 150 liters. The amount of tap water required by a vertical farm to produce delicious and reach yields then will be just 440 liters, which is five times less than what a hydroponic greenhouse needs.
16.10.2020
The Basis, A Homogeneous Climate, Is Already There" Artechno Doing New Cultivation Tests In VF Chamber
Previously, the Artechno industrial hall was mainly the place to build complete water management systems for the greenhouse or harvesting lines and turnkey systems for vertical farms and deep-float systems
"Together with another colleague, I am adding green thumbs to the team that is full of technicians here", Rick van Schie laughs. As the son of a tomato grower and next year's fourth-year horticulture student, he started cultivation research in the industrial hall of Artechno in De Lier. In a AVF+ Junior climate chamber Rick researches irrigation strategies for four different substrates and the effect that far-red light has on the stretching in lettuce.
Previously, the Artechno industrial hall was mainly the place to build complete water management systems for the greenhouse or harvesting lines and turnkey systems for vertical farms and deep-float systems. “The cultivation space with deep-float facility provided insight into growth and also important key figures for the business case. By testing and growing ourselves, we can now also better serve our customers in the vertical farm industry and provide them with better data and growth recipes.”
Rick started growing in the climate chamber in mid-June. "It is often wise for a grower to first do tests in a small chamber and to collect as much information as possible about lighting, climate and irrigation before scaling up to a larger system. That is why we also offer our chambers for rent to growers."
Cameras and LED
The AVF + Junior with which Rick is currently doing tests is equipped with Philips GEN3 LED luminaires, whereby both the spectrum and the light intensity are adjustable. The chamber is also equipped with special hyper-spectral cameras (and sensors), making it possible to monitor the crop and climate without having to enter the chamber.
Homogeneous climate
Anyone who would enter the chamber will notice, according to Rick, that the climate is remarkably homogeneous. "Or actually you do not notice that much and that is positive. To demonstrate that there really is air circulation, I have hung up an A4 sheet, but you do not notice it."
Art, general director: "The aim was to realize a delta T difference of less than 1 degree Celsius difference in a 10-layer climate chamber of about 8 meters high, and we succeeded."
All this is possible thanks to the air treatment units that were developed by Artechno itself. "You want to exclude as many variables as possible in your research, so a homogeneous climate is essential."
Study 1: irrigation strategies
The first study examines the effect of different irrigation strategies on four different substrates (stone wool, foam plug, glue plug, and soil mix with 10% wood fiber). This should become the basis for other studies with various types of lettuce, Rick says.
Study 2: far-red light
The second research is conducted into the addition of far-red light. Lighting is applied with 180 micromoles for a total of 18 hours and in the last hour, far-red light is added with 10%. There is also a control group (DRB LB) without the addition of far-red light.
"The purpose of the addition of far-red light is to achieve more stretching in the leaves so that the plant makes better use of the growing surface after transplanting. This could possibly also influence the bringing forward of the growth curve."
Germination
Rick is very satisfied with the results of the sowing tests in comparison to the tests carried out in the previous two years. "96-98% germination on the various substrates is a good result, but maybe this might be surpassed by an upcoming germination chamber."
Low input, high output
The results of the tests are assessed, among other things, by measurements of fresh and dry weight, growth percentage, quality, and kilo/m2. "From these results, certain trend lines are emerging, from which the crop growth rate can be calculated. This trend line also gives us insight into the smarter use of the LED light (grams of fresh weight per mole). The ultimate aim is to be consistent with the lowest possible input to achieve the highest output (kilo/m2/year)."
Rick knows that kg/m2/year is an important factor for customers to determine the profitability of their business case. "The results of our tests are used for this, among other things. The results and experiences with certain products we always provide feedback to our suppliers and customers, so that they remain up-to-date."
Soft fruit
Meanwhile, Rick and Artechno see that, in addition to demand for research for herbs and leafy crops, there is also an increasing demand for soft fruit. "This includes, for example, growing strawberries indoors and testing with the rooting phase in, for example, the propagation of blueberry plants.
We also want to be proactive in this, so we will certainly carry out tests ourselves. For ourselves, but also for growers or suppliers to whom we rent the chambers. In addition, I can mentor them and, in consultation, help to draw up a good research plan, always with a lot of literature as a foundation, so that you are not wasting time doing research that has already been done."
For more information:
Artechno
www.artechno.nl
info@artechno.nl
Rick van Schie
rick@artechno.nl
Publication date: Fri 24 Jul 2020
© HortiDaily.com
How Leafy Greens Growers Have Turned Food Safety Challenges Into Opportunities
Growing lettuce and other leafy greens in a controlled environment presents its own set of challenges and opportunities
July 30, 2020
Editor’s Note: This article is the second of a three-part series on food safety concerns in the production of leafy greens in a controlled environment.
Click here to check out Part One of the series, which covered the formation of the CEA Food Safety Coalition.
Growing lettuce and other leafy greens in a controlled environment presents its own set of challenges and opportunities. During United Fresh Live in June, Marni Karlin, Executive Director of the CEA Food Safety Coalition, moderated a discussion that outlined how indoor growers who make food safety a priority, rather than dismissing it as a problem unique to field-grown crops, can inadvertently create market opportunities for themselves. The panel featured growers of all types (greenhouses, vertical farms, and warehouses) and sizes. Here are a few insights from the discussion.
Don’t Overlook Irrigation and Growing Media
Jackie Hawkins, Senior Manager of Food Safety at BrightFarms, says irrigation water is likely potable if it comes from municipalities or wells. However, it can still be contaminated, so don’t assume it’s clean and forsake the necessary testing.“Test your incoming water, treat it if necessary, and test it again,” Hawkins says.
Growing media, as well, may not seem like a concern because many leafy greens producers are not growing in soil. “But the seeds might have been grown in media, so it’s important to do routine monitoring of your media as it comes into the greenhouse,” Hawkins says.
From Data Comes Solutions
Michael DeChellis, Co-Founder of Livingston Greens, a small indoor farm in Montana, says it’s critical for greenhouse producers to compile the data they’re able to collect from growing in a controlled environment to create a plan for developing a safer product.“
For small farms, working with other growers in the CEA Food Safety Coalition is a great opportunity,” DeChellis says. “Our members share data, and this culture of collaboration can help us identify ways to overcome challenges.”
For example, DeChellis cites a mold issue at Livingston Greens, which he addressed by using temperature and humidity data to highlight the problem area and the conditions that caused the problem.
Consider Design Upgrades
Simon Yevzelman, Managing Partner and Leader of Biosecurity at Planted Detroit, a vertical farm in the Motor City, says his company saw the concerns of food safety looming, so it opted to temporarily suspend production so it could enhance its production systems with food safety as a guiding principle.“
Thanks to those efforts, we are now in an expansion mode,” Yevzelman says.
Full Company Responsibility
Oscar Camacho, President of Superior Food Safety, a California-based consulting company, says any greenhouse production system should be designed to optimize best food safety practices.“
The system needs to work across the entire company,” Camacho says. “This means communication from one end of the production line to the other is critical.
Retailers and Consumers Care
Chris Livingston, General Counsel at Bowery Farming, a vertical farming company in New York, says the CEA Food Safety Coalition is currently developing a standard specific to controlled-environment production that addresses unique challenges such as water management and infrastructure.“
Our goal is to have a seal that members can use to show their customers they are complying with standards unique to our industry,” Livingston says. “We are also developing a research agenda based on food safety topics.”