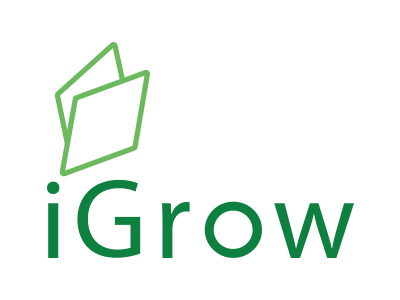
Welcome to iGrow News, Your Source for the World of Indoor Vertical Farming
Vertical Barrels Components "Ready For Vertical Farming Integration"
The aponix vertical barrel system is an alternative vertical NFT solution from Germany that can be used instead of rack systems to use vertical space more efficiently in hydroponic setups and at the same time use natural sunlight better
The aponix vertical barrel system is an alternative vertical NFT solution from Germany that can be used instead of rack systems to use vertical space more efficiently in hydroponic setups and at the same time use natural sunlight better. The system aims to maximize the number of possible grow spaces per level arranged in a given 3D room by increasing the diameter from a ‘Tower’ to a ‘Barrel’.
The whole system is based on lego-like ring segment pieces that serve either as spacers or provide differently organized inserts for standard 2-inch netpots. Assembling multiple of these ring segment pieces will result in stackable ring segments or barrel levels to assemble one or multiple such vertical cylinders. With more ring segments stacked, the height and the number of grow spaces are increased.
By the end of 2020 aponix will have developed the new ‘Version 3’ that will incorporate all collected improvements from the existing global user base from the last 3 years and adding a few more features:
Liquid will be guided more precisely inside. It will also have a new more robust and tight connection mechanism and air traps to keep liquid inside also on high flow rates.
There will be a backwards-compatible and reusable grow plug insert, that is supposed to replace 2-inch one-time use plastic netpots also in other systems. It will also have an optional plant trellis insert to grow larger flowers and fruiting dwarf varieties.
There will be a new lid-base that speeds up setup of lines of vertical barrels and enable rotation of the units if needed.
There will also be a dedicated sprinkler dome lid enabling different sprinkler options including own solutions and also the own existing pressure-less irrigation option using the waterbuffer.
Vertical barrels will be more stable and can be built higher unsing the new V3 part.
There will only be a single ring segment piece in ‘Version 3’ with 2 grow pod inserts that only allow 2 stacking positions instead of 4 in V2. If spaces are unused they can be capped with a nice green cover plug.
As of 2020 aponix also changed their market strategy from looking for distributors to starting to work only with product partners who bring in own engineering and create more specific and distinguishable solutions based on aponix components. Aponix parts are now defined as being mere infrastructure parts that always need to be integrated into a greater individual context involving more or less horticulture engineering depending on the application. Which means product partners create their own unique solutions based on aponix components adding other external even competitive pieces, logic and/or service and market them independently under their own brand and own product name.
For more information:
Aponix
hello@aponix.eu
www.aponix.eu
18 Feb 2021
Overcoming The Challenges of Growing Organically In Soilless Farms - Wednesday, September 23, 2020 @ 12 PM EST
Has your soilless farm ever considered that your food waste could be a source of net income? Join us as we show how Re-Nuble can help soilless farms capture and introduce water solution, organic nutrients from your own production waste as a free supplementary and sterile fertilizer source
Are you a soilless farmer or grower that wants to go organic but keeps facing challenges? Join us as we identify ways for you to work with water-soluble organic hydroponic nutrients in a recirculating system in such a way that voids the risk of introducing food safety-related pathogens, labor inefficiencies and additional costs. Based on seven years of research, Re-Nuble's goal is to guide soilless farms towards a cultivation method that is comparable to the yields of conventional, synthetic mineral salts while increasing a farm’s bottom line using food waste as the mechanism.
In this webinar you will learn:
The main challenges soilless farms face when transitioning to organics
How to overcome these challenges
What soilless farms need to be mindful of when transitioning to ensure profitability
We'll see you there!
Register here
On-Site Waste Management:
An Untapped Income Source
Wednesday, 7 October 2020 @ 12 pm EST
Has your soilless farm ever considered that your food waste could be a source of net income? Join us as we show how Re-Nuble can help soilless farms capture and introduce water solution, organic nutrients from your own production waste as a free supplementary and sterile fertilizer source. We then go on to explain the driving science behind our method, Organic Cycling Science, an approach that allows farms to finally use a fully integrated, closed-loop, and self-sustaining fertilizing system capable of reducing input and disposal costs and increasing efficiencies.
In this webinar you will learn:
How to turn a farm's production waste into a free, renewable source of potable water and (optional) nutrients
Opportunities to improve income by reducing the organic hydroponic nutrient cost
Ways to increase a crop's growth and nutritional content
We'll see you there!
Register here
Speaker Profile: Tinia Pina
Founder & CEO, Re-Nuble
Tinia received her B.S. in Business Information Technology from Virginia Tech and studied briefly at Columbia University's Earth Institute. She has seven years of experience in the financial services industry and ten years as a professional within the sustainability and waste management industry.
Tinia launched Re-Nuble with a mission to “Redefine Waste” within urban communities. Re-Nuble quickly evolved into a social enterprise dedicated to changing wasteful habits around the world with the sole intention to help our farming production and food systems to become more resilient, decarbonized, and with an abundance of accessible organic produce options.
Tinia's pioneering business model has earned her a Huffington Post Millennial Impact Grant, the American Express Emerging Innovator award, and a MillerCoors Urban Entrepreneur grant, among other honors. Her experiences related to food waste, systems and policy have fueled her passion to increase our communities’ resilience, prosperity, and knowledge to help us live more conscious lives.
A High-Yield Indoor Farming System Ideal For The City
According to Pollard, the evolution of new technology, such as LED grow lighting and the Internet of Things (IoT), has complemented the development of indoor soilless cultivation systems
As prolonged droughts occur more frequently in South Africa, some entrepreneurs are investing in and developing new technology and farming methods, such as indoor growing systems, that ensure consistent, high-quality food production. Juan-Griffith Pollard, CEO of Urban Cultivation International, spoke to Pieter Dempsey about his scaleable hydroponic farming system.
More frequent and long-lived droughts. Global warming. Water scarcity. Higher input costs.
These are some of the factors driving the growing interest in new technology that enables a farmer to produce the same quality and yields as conventional farming, but using indoor farming systems instead.
Hydroponics, or indoor soilless cultivation, as Urban Cultivation International (UCI) calls it, is a method of growing plants in a water-based, mineral- and nutrient-rich solution instead of soil, and under artificial LED lights instead of sunshine.
According to Juan-Griffith Pollard, the CEO of UCI, indoor farming uses up to 90% less water than traditional farming practices, and far less space. In addition, plants can be grown pesticide-free and closer to high-consumption areas, such as densely populated cities.
These reasons, and more, explain why an increasing number of growers have begun exploring indoor soilless cultivation.
Precision growing
The system provides the optimal growing conditions for plants, enabling them to develop much faster and be far healthier than is the case with traditional outdoor cultivation.
According to Pollard, the evolution of new technology, such as LED grow lighting and the Internet of Things (IoT), has complemented the development of indoor soilless cultivation systems.
“IoT can be used to automate and regulate indoor farming by monitoring water levels, nutrient levels, pH levels, and temperature and light requirements of plants. “A farmer can be in control of the harvest at all times, wherever he or she is physically present.
“One of the biggest benefits of indoor farming is that produce can be farmed at any time of the year. Thus, a farmer can sell produce at out of season prices, and supermarkets can stock fresh local produce all year around,” says Pollard.
No-soil farming
Pollard started investigating various methods of indoor soilless cultivation in 2016 and fine-tuned them in 2019 to create a healthy, productive indoor farming system.
An entrepreneur by nature, he took note of the various challenges in traditional South African agriculture, including water scarcity and security risks. He also noticed the demand for certain leafy greens and microgreens in cities.
Thereafter, he traveled to the US, Europe and Asia to research systems that could be applied in the South African agricultural environment.
He went on to establish UCI at the N4 Gateway Industrial Park in Pretoria East.
“What makes UCI’s technology different from most other indoor systems is that a farmer can start small and expand by adding additional racks to the system. So there’s no need to commit to a huge capital investment to get started,” Pollard explains.
The UCI model enables the farmer to control the light hours, nutrients and moisture. It is automated to produce rapid harvest cycles with predictable results, and can be used in a small space. Crucially, it is also affordable.
A key advantage is that the plants can be grown without the use of insecticides and herbicides, as the crops are grown in a controlled environment.
Pollard predicts that farms of the future will be urban-based, and crop cultivation will have to become far more sensitive to water and energy usage. There are many cost-effective options for indoor, soilless cultivation, and these allow farmers to move from the fields to the city.
Indoor production is also an easier entry into farming; it can be started by any entrepreneur, or even a retiree, he adds.
A wide range
The options offered by UCI range from small household units to large-scale commercial systems. Regardless of size, they can deliver crop yields of up to 10kg/m2.
The household units are small, with just enough space to service the average household and to plant a variety of crops, such as leafy greens, microgreens and berries.
The household system was also developed for educational purposes and can be used as an entry into indoor soilless cultivation before a large capital investment is made in a commercial unit. UCI has developed a curriculum that explains the A to Z of indoor hydroponic farming.
The company’s industrial units include climate control and a lift system, which makes harvesting easier.
Depending on the type of crop, the return on investment is between two-and-a-half and five years, while high-value crops such as microgreens have a payback period of less than a year on capital investment.
Growing with ease
Plants can be grown from seed to harvest in 28 days, three times faster than that achieved with traditional farming.
“The plants are grown in a controlled environment under 12 to 16 hours of LED lights, giving you optimal harvest and zero wastage,” explains Pollard. In addition, produce grown in UCI’s systems has proved to be of excellent quality and offer good taste.
The entry commercial turnkey solution system contains a 10m-long and 1,9m-wide row, and the buyer can choose to fit between three and 12 levels.
For example, a 10m-row, five-level-high farm enables 100m2 to be planted in a floor space of only 20m2. “The higher you go, the more your yield per square metre,” says Pollard. The grow trays and spacing between plants are designed for optimal growing and yield. No sunlight is needed for this method; all the systems use LED grow lighting.
“LED technology provides the best energy efficiency, which saves you money in the long term,” says Pollard.
Production
A 10m-long unit can handle 54 plants per tray. At 12 trays per level and at five levels, this equates to 3 240 plants per unit.
The lighting is usually kept on for between 12 and 16 hours a day, depending on the requirements of the plants.
“The more light they get, the faster they grow,” says Pollard.
The system can handle a variety of crops such as lettuce, spinach, baby spinach, marog (imfino), cherry tomatoes, strawberries, basil, watercress, sage, zucchini, beans, fodder and a range of microgreens and herbs.
To illustrate potential crop yields, Pollard and his team have used the five-level demonstration system at UCI’s premises to grow 250g lettuce heads in 28 days under optimal growing conditions. A yield of more than 18kg per tray has been achieved.
“Compared with traditional farming, the only major cost drivers are electricity and wages,” he says.
Each tray contains about 20ℓ of constantly recirculated water, and total water use is approximately 1 250ℓ/month. The system is extremely water-friendly, as almost all the water is absorbed by the plant.
“No water is wasted, hence the saving of 90% compared with traditional farming,” says Pollard.
He adds that climate and temperature control is a key factor in the grow room, and even the water temperature is cooled or heated as the plants require.
“We can mimic the controlled growing environment of certain crops as they require. “The system works with any water, and tests are routinely conducted to see what nutrients the plants need, and all variables can be adjusted according to the needs of the plants.
“We have a nursery system that grows the plants from seed to seedlings. After about seven days, the seedlings can be transported into the commercial system; the fully grown plant is then ready to be harvested after another 21 days,” Pollard says.
Due to the way in which the system operates, the chances of a pest infestation are very low.
“Biosecurity is crucial and we prevent any pathogens and pests from entering the facility.”
Harvesting a system that is 10m long and has five levels requires about three hours with two people.
With rapid urbanization increasing the demand for food, UCI’s system offers a number of key advantages.
It brings the farm closer to the people, thereby improving food security, and it reduces transport costs, in turn lowering the carbon footprint of supplying food. The system also offers good potential as a job creator.
“Our aim is to get entrepreneurial farmers to start utilizing the empty spaces in cities, such as empty buildings in city centres. Such spaces can be used to grow food, provide jobs and supply retailers directly,” says Pollard.
Visit urbancultivation.co.za.
By Pieter Dempsey | Farmer’s Weekly | May 6, 2020