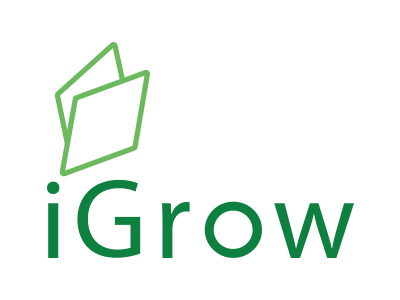
Welcome to iGrow News, Your Source for the World of Indoor Vertical Farming
Important Tips For Designing A Hydroponic Production Facility
Growers should always choose a properly sized and engineered system. The reality is that the budget will drive many of the growers’ decisions
Why Do You Keep Saying Buffer Capacity?
For anyone that has called me to discuss the design of their new vertical farm or greenhouse, they have probably grown quickly tired of me using the term buffer capacity. But, of everything I have learned over the past 25 years, the understanding of “buffer capacity” might possibly be the most important. It makes your production system easier to manage, more predictable and more stable. All traits that can be found in all successful farming and commercial horticulture production facilities. (You might remember my recent article on simplicity, well this goes right back to that.)
Let’s start by agreeing that I am not properly using the term buffer capacity which is normally defined as the moles of an acid or base necessary to change the pH of a solution by 1, divided by the pH change and the volume of buffer in liters; it is a unitless number. A buffer resists changes in pH due to the addition of an acid or base though consumption of the buffer.
Now let us focus on how we can manipulate that definition to fit the needs of designing a greenhouse or an indoor farm. When referring to buffer capacity in our production environment we are referring to our system’s ability to keep key elements (temperature, humidity, wind, nutrients, light, CO2, oxygen, water) from fluctuating unless we as the grower determine that we want it to and have the ability to manipulate these key variables while keeping the others in balance.
The ability to keep key elements from fluctuating unless the grower determines that the variables should be adjusted to produce a crop response. Adjustments should be met with the abilities to keep all other elements in balance.
For this article I am going to use (3) examples of how designing “buffer capacity” into your farm will lead to better production and more consistency.
Greenhouse Structure.
For those starting to investigate different greenhouse types and designs or for those that have already gone through the process, I think we can all agree that the choices are limitless, and for the most part the look of the greenhouse has not changed much of the years with one major exception. They have gotten much taller. Taller greenhouses provide a more uniform, stable and ultimately superior growing environment for the crop. During hot weather (as an example), the additional space creates a buffer that avoids trapping heat and humid air around the plants.
Water holding tanks and nutrient solutions reservoirs
For beginning growers this is the area where the right decisions might provide the biggest advantages. Experienced growers may choose to size their systems differently depending on their budget, crop and space but one thing is for sure, they will make sure that they have ample water availability as well as on demand storage to respond to changing crop needs.
Larger tanks and reservoirs (as compared to the amount of plants in the system) have a considerable buffer before they will run out or need to be dumped. The most obvious benefit is that of ensuring the tanks don’t run dry and cause extensive damage to the pump(s) or loss of crops and production. The most important benefit might be a properly sized system’s ability to keep the nutrient solution from having big erratic swings in EC and pH.
Substrates
Hydroponic substrates provide an (additional) reservoir for water, a place for plants to take up nutrients, an area for the plant to develop a sufficient root system as well as location for gaseous exchanges. A good grower will consider all the other decisions that he or she has made in building the greenhouse and designing the irrigation system then decide how much buffer capacity their substrate needs to provide. If the buffer capacity of the irrigation system is limited, the grower may choose to use more substrate with a higher water holding capacity so the total system is more durable on hot summer days. If the grower has a tremendous amount of confidence in their access to water, the responsiveness of their irrigation system and their ability to fix the system if they have problems then the grower might choose a substrate that they can steer thereby providing them more control in the greenhouse.
Growers should always choose a properly sized and engineered system. The reality is that the budget will drive many of the growers’ decisions. Understanding buffer capacity in the system will allow growers to get the most out of their investment while still focusing on consistent and uniformed crop production.
To continue the conversation, email us and schedule some time with either Chris Higgins or our newest grower consultant Tyler Baras (aka The Farmer Tyler.)
Next article. Can indoor farming be profitable?. Simple answer: of course. Complexed answer it all depends.
Share this:
Tagged GreenhouseHydroponic Production SystemsHydroponicsVertical Farming
Vertical Farming Robot Wins Design Challenge
The winners of the 2018 Valtra Design Challenge were announced at the EIMA Show in Bologna, Italy. The competition which started in April and ended on September 23rd was targeted globally to designers, academic design students, design studios and automotive suppliers. This year’s challenge was to design the multi-purpose vehicle of the future: a machine that can handle multiple tasks to meet future needs and that is more efficient than today’s highly specialized machines.
The first place of the competition was awarded to the work “VERTICAL” by Austrian design team Benjamin Miller, Jack Morris, and Alireza Saeedi. The jury praised the concept as being a very creative interpretation of the challenge theme. “At first glance it looks very specialized, but if you judge the complete system instead of only the tractor, a versatile and holistic concept for the future emerges. The concept takes care of everything from seeding to distribution of food”, comments member of the jury Hans Philip Zachau.
“Valtra has been widely recognized for ground-breaking and visionary industrial design. We started the Design Challenge in order to raise awareness of future challenges in the agricultural community and society at large. It is also a platform for designers to showcase their innovations.” comments head of the jury and industrial design & user experience manager at Valtra, Kimmo Wihinen. “The Valtra Design Challenge is the world´s largest design contest in agricultural machinery and one of the biggest in the off-road vehicle industry. The high number of innovative and high-class entries shows us that there is a demand for this type of competition, and we are already working on the theme for the next edition”, he adds.
The Valtra Design Challenge 2018 Jury members were Kimmo Wihinen from Valtra, Brandon Montgomery and Sam Freesmeyer from AGCO, Hans Philip Zachau from Lighthouse Industrial Design and Paolo Grazioli Frozen Design Tokyo.
The Valtra Design Challenge was organised for the second time in 2018. This year the competition has received 107 entries from 32 different countries and six continents. The first prize of the Valtra Design Challenge is a €10,000 cheque.
For more information:
www.valtra.com/designchallenge