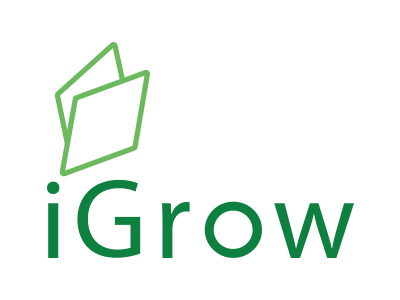
Welcome to iGrow News, Your Source for the World of Indoor Vertical Farming
Bringing Energy Management And Automation Opportunities To Indoor Farming
“We can’t be the most sustainable company in the world if we don’t work on the world’s biggest sustainability challenges,” says Travis Graham, international account manager at Schneider Electric. Schneider provides a vast array of digital technologies to multiple sectors, including horticulture
By Rebekka Boekhout
July 14, 2021
“We can’t be the most sustainable company in the world if we don’t work on the world’s biggest sustainability challenges,” says Travis Graham, international account manager at Schneider Electric. Schneider provides a vast array of digital technologies to multiple sectors, including horticulture. However, the company recently decided to strategically address the indoor farming segment and partner with growers to improve energy efficiencies within the sector.
As a global specialist in energy management and automation, Schneider’s goal is to empower the global population to improve their energy and resource use efficiency. This purpose, coined “Life is On”, aligns strongly with the spirit of indoor agriculture whose goal is to produce food and medicinal crops in an environmentally sustainable manner.
Named the world’s most sustainable company in 2021 by Corporate Knights, Schneider holds sustainability at its core and uses its century-long experience in energy management to help growers improve the energy efficiency of their facilities.
Read the rest of the article here
For more information:
Schneider Electric
www.se.com
Ontario Greenhouse Installs Combined Heat Power
"We look forward to expanding our energy-efficient and sustainable system"
With the demand for greenhouse-grown produce continuing to increase, DelFrescoPure is consistently looking for ways to become more sustainable. "Ensuring high-quality produce is available year-round. Implementing a Cogeneration power plant is the most efficient way to achieve that goal," they say. As of fall 2021, DelFrescoPure will be increasing their pre-existing Cogen system by 6.5 MW, for a total of 10+ MW across their facilities.
Cogeneration or combined heat and power (CHP) is the onsite generation of electricity from the use of natural gas. The byproducts of CHP are the heat that can be stored and used to create the desired microclimate within the greenhouse and CO2 that is used to fertilize the crops. The CHP units will additionally produce the electricity required to power the grow lights as well as the mechanical load of the facility. While electricity generation alone is typically 40% efficient in converting fuel to power, adding heat recovery to the equation can bring that efficiency to 90%, a reality that suits greenhouses well.
Year-round production
DelFrescoPure intends to use the electricity to power the lights at Via Verde Hydroponics. These grow lights allow for an extended growing season, making produce that would originally be grown in the summer available all year round. The heat harnessed by CHP will also be recycled to heat the greenhouses and meet all daily power needs. Being able to produce electricity more cost-effectively onsite also means DelFrescoPure does not have to worry about voltage fluctuation from the area maxing out the local grid. With electricity no longer being a concern DelFrescoPure is primed and ready for the 25-acre expansion currently underway.
“DelFrescoPure is excited to increase our Cogeneration Power units. We are very pleased to be working with Martin Energy again to install the new CHP technology and solutions they offer. The results from using the Cogeneration technology over the past three years have been great. We look forward to expanding the system so we can continue to provide fresh produce all year long.” said Carl Mastronardi, President of Del Fresco Produce.
Along with the financial benefits, CHP power is better for the environment. This method ensures that fewer resources are wasted and required to produce electricity. The extended growing season also reduces our carbon footprint by decreasing the need for local retailers to import high milage commodities. DelFrescoPure is taking a sustainable approach to providing consumers with the freshest items possible. CHP is perfectly suited for the greenhouse environment since it is able to harness all three attributes of the technology (electricity, heat & CO2). DelFrescoPure® will never have to worry about where their energy is coming from and can continue to expand as market demand increases.
For more information:
DelFresco Pure
www.delfrescopure.com
CANADA: Quebec AI Processing Centers To Heat Gigantic Greenhouse Complex
A Quebec City entrepreneur, well known in the field of technology, is piloting a pharaonic project. Workers are working quietly on a large plot of land in Saint-Nicolas. The value of the total investment is in the billions of dollars
A Quebec City entrepreneur, well known in the field of technology, is piloting a pharaonic project. Workers are working quietly on a large plot of land in Saint-Nicolas. The value of the total investment is in the billions of dollars. And it would be only the first of a series of "campuses" at the cutting edge to be built on Quebec soil. And, there's greenhouses in it.
Developer Martin Bouchard, founder of the Copernic search engine and then of the 4Degree data centers, wants to build at least three high-intensity data processing complexes with thermal waste recovery, to which would be added a pole of applied innovation in artificial intelligence. The total estimated cost is close to 5 billion euros. Why that could be relevant for the horticultural industry? The business plan calls for the recovered heat being used to heat greenhouses. "We want to contribute to the province's food autonomy with a potential of 400 hectares of greenhouses for the first campus alone," he tells in an article on LaPresse.
Put the words artificial intelligence, innovation, circular economy, high-capacity computer servers, clean energy, greenhouse production, food autonomy; stir calmly and you will obtain the "Baiejamésienne" project on which Mr. Bouchard and his associates Vincent Thibault and Dany Perron have been working for three years on the QScale project.
QScale is a high-density data processing campus. The campuses seek to meet the needs of machine learning, which is in growing demand with the arrival of artificial intelligence in businesses. Consider the data calculations required to safely drive autonomous vehicles. Bouchard cites Tesla, Volkswagen, Pfizer and Goldman Sachs as potential clients.
The serial entrepreneur, along with private investors, has invested $30 million to start the project. The rest of the financial package will be revealed at the time of the official announcement. "We are working very hard to ensure that the ownership of the company remains entirely Quebec-based. "
The Quebec government is receptive to the project, La Presse has learned. Hydro-Quebec would have already said yes, assures Mr. Bouchard. The imprimatur of the monopoly of electricity distribution is essential because such a data center dedicated to artificial intelligence consumes twice as much power in a year as a city the size of Drummondville.
Construction has begun on the first campus located in Levis. Delivery is scheduled for November 2022. The daily newspaper Le Soleil recently outlined the project. QScale is planning a second branch in the Écoparc de Saint-Bruno-de-Montarville, on Montreal's South Shore, just behind the commuter train station.
With the heat, greenhouses are to be heated. "We want to contribute to the province's food autonomy with a potential of 400 hectares of greenhouses for the first campus alone," he insists. However, all the vegetable production in greenhouses is currently grown on 123 hectares. "We are in discussion with several players for this part of the project," says Bouchard. André Michaud, a consultant for Savoura, says he has never been contacted by QScale. He said he was puzzled when he saw the project outline.
We have a greenhouse robotization project using artificial intelligence to eventually automate physically demanding jobs," says Mr. Bouchard. In Levis, we have the adjacent farmland that corresponds to the equivalent of 80 soccer fields, enough to produce 2880 tons of raspberries and 83,200 tons of tomatoes. "
4 Jun 2021
Joined Up Thinking: Food & Energy Grids
This article, written by our CEO and co-founder Charlie Guy, about the connection between our energy grid and food networks, originally appeared in Volume 35 of the Journal for Food Science and Technology.
It may not always feel like it at this time of year, but on our planet we are blessed to bathe in a constant and abundant stream of energy and warmth. Effectively, all of this energy comes from the sun before being transformed, stored or used in some way. From the organic matter that once formed our fossil fuel sources, to the climatic differences that drive our weather systems and the solar panels you might have on your roof.
Food is our fundamental energy source as individuals - it powers everything that we do in our daily lives. For almost all food types, the energy used to produce it is derived from the sun (ok, mushroom-heads may argue against this, but they are still feeding on organic matter). Because of this simple concept, our food and energy systems are intrinsically intertwined. Bizarrely though, this fact is often overlooked in the food supply chain, from producers, all the way through the distribution and cold chain, right up to ourselves, the end consumers. Our current food system separates out different energy types. Heat, electricity, fuel and light often end up as mere balance sheet inputs to the production of food and many energy inputs don’t get recorded at all.
This simplified way of thinking leads to us cutting corners for the sake of cost and not considering the absolute energy impact of our food production. There are no individuals at fault here, our economic system has lined us up to think in a linear fashion for the past few centuries and this has muddied the long-held practices of stewardship for the land. Effectively, our understanding of what we give and take from nature and the sun to produce our food is no longer in balance.
If we look at the inputs and flows of energy that make up global food production, we see many areas that we may not consider when we buy food products in our local supermarkets or greengrocers. Berners-Lee et al (2018) produced a high-level analysis of the global energy flows in food production, shown in Figure 1, ultimately showing that we grow enough calories to feed everyone on our planet, but we do not use or distribute them efficiently.
Figure SEQ Figure \* ARABIC 1 - The flows of global food energy (kcal/person/day) from the amount grown to the amount eaten. For crops fed to animals, the units are based on the global human population, not animal population. The left-hand bar divides the crops grown into those that are directly edible by humans and the grass, pasture & stover that is only edible by animals. The right-hand bar divides the nutrients eaten into that required for healthy human living and net excess consumption. Animal losses include all the losses inherent in animal husbandry, such as energy used for respiration, growth, movement, and reproduction and the wastage of animal parts not used as food. DOI: https://doi.org/10.1525/elementa.310.f1
When you consider the journey of a simple soil-grown lettuce, you must consider the following energy inputs and flows as a minimum:
- Preparation – soil, seed production, transportation of seeds, drying and storage of seeds, farming infrastructure, fertilizer/pesticide production
- Growing - the sun, soil, fertilizer/pesticide application, and waste, machinery, human labor, energy use if in a greenhouse/vertical farm
- Harvesting and storage – farm machinery, fuel, refrigeration and spoilage
- Processing and packaging – transforming raw materials into products
- Transportation - cold chain refrigeration, freight by lorry, boat or long haul air travel
- Consumption - home energy usage including storage and cooking
- Waste - throughout the chain and in the home
Through each of these processes, we are either adding energy to our food on its journey to our plates or we’re losing energy through losses along the way. This is why the impact of wasting food in the home is so severe, as we are not only wasting the energy that went into producing the food, but we are also wasting the energy that was used in the supply chain along the way too. Each of these losses, even if they seem small at each stage, adds up. Taking Berners-Lee’s analysis and comparing this to electrical energy usage, the average food wasted per person is equivalent to all 7.8 billion people on our planet leaving a reasonably-sized LED TV (64W) on for 24 hours a day, 365 days a year.
Ever more work is being done in the field of lifecycle analyses to understand and bring to light the impact of our foods. These individual losses need to be understood, quantified and then reduced in our vision of a more efficient combined food and energy system.
There is a clear comparison that can be made between our current food systems and the journey that our energy systems have been on over the last few centuries. Through the various energy revolutions, we have transitioned from distributed to centralized energy and food systems. Centuries ago, we were required to balance the use of wood and food, to heat and fuel ourselves, to sustain our communities, and avoid overconsumption of either energy source. Food and fuel tended to be distributed locally to fulfill the energy needs of the community and we had a better understanding of the link between the sun, our food, our energy and the need to prevent over-consumption to remain in balance.
Fast-forward to the 21st Century and the current paradigm of large power stations that distribute electricity through grids to people, whose only connection is the vibration of their phone when they plug it in to charge. There is zero connection to how or where the energy was produced. The equivalent analogy in food production sees swathes of industrialized monocropping, focused in certain areas of the globe. Products and ingredients are shipped halfway around the world and our only connection is to open the packet and experience their flavors. Arguably there are substantial “efficiencies” and economies of scale in this kind of production model, but at what cost? Is this what we want the next chapter of our food and energy systems to look like?
Renewable energy has a huge opportunity to bring us back to a more decentralized system. In simplistic terms, the fact that the wind and sun are well distributed around the world gives the potential for much more equitable access to energy production. Renewables also bring us much closer to the only real source of energy that we have, the sun, whilst revealing our true reliance upon it as well. There are some known issues regarding renewable energy storage, but the humble chloroplasts in plants long-ago worked out how to capture this energy and store it for use later on. We can learn from this and begin to look forward with a more joined-up view of our food and energy systems. Putting our farmers and stewards at the heart of this system, ensures that links can be rebuilt between food and energy production.
So how do we link our food and energy systems back together in a way that can provide enough food for all of us in the most sustainable way? Firstly, this challenge needs to be undertaken with the concepts of sustainable intensification and circular economy principles in mind. If these are new to you, do check out the Ellen Macarthur Foundation. Secondly, we need a diversity of thinking and solutions, including both technical and business innovations. There is no silver bullet here for such a complex problem.
Many solutions in both energy and food supply are coming to the fore already, albeit independently at the moment – local energy schemes and community-supported agriculture schemes (CSAs) both enable communities to benefit from locally produced energy and food. Can we imagine a future where we bring these together into combined food and energy schemes?
Controlled environment agriculture (CEA) is one emerging practice that allows us to do things in ways that previously we have not been able to do in open-field agriculture. Using CEA, indoor farms such as greenhouses and vertical farms, enable the inputs to the growth of fresh produce to be understood, controlled and optimised. Water, nutrients, light energy and environmental conditions can all be tweaked to optimise the output of the crop and to reduce the use of resources.
These farms allow us to understand the system of growing without impacting the local environment, by ensuring efficient energy and resource flows along with recapture technologies. They enable us to build farms anywhere in the world, to grow produce in a more decentralized, resource-efficient way that can help build resilience into our food system.
Opponents of CEA will point to the increased use of energy, but this is offset by the reduced energy requirements in transportation, processing, storage, fertiliser and pesticide usage. If you understand and match your local energy and food production, this is no longer such an issue. There are still challenges for the CEA industry, but the winds are blowing in the right direction.
Increasing the renewable energy mix on the grid will reduce the cost of energy over time and is the perfect power source for indoor farms. Spiky supply and storage may appear to present an issue, but the energy profile of an indoor farm can be tuned to the supply of the grid. Plants are great at storing energy and have inherent redundancy too, hence the possibility of using plants as a new form of battery becomes very real when we see our food and energy systems as one.
There are numerous flagship examples of CEA projects implementing many of these principles worldwide. From the advanced Dutch greenhouse networks, to Sundrop Farms in Australia, to new combined heat, power and greenhouse projects in the UK such as Beeswax Dyson’s new strawberry growing facility. From Growing Underground’s vision of circular farms, to LettUs Grow’s partnership with Octopus Energy and the many projects in the pipeline with farmers around the UK looking to incorporate indoor vertical farms with existing anaerobic digestion plants. These projects show that things are moving rapidly in the right direction to bring our food and energy systems back together again.
There are still big questions to answer and challenges ahead when looking at the sustainable future of our combined food and energy systems, but we are on a very exciting journey as part of a new industry and a whole new way to look at food and energy. Joined up thinking is needed and bridges need to be rebuilt - energy and food producers will be working much closer together. To address climate change we know that we need to seriously address our energy system. And to address our energy system in full, we need to include food as a fundamental part of it.
Charlie is co-founder & Chief Executive Officer at LettUs Grow. With a background in renewable energy consultancy & engineering design, Charlie is a proponent of tech for good & passionate about all manners of sustainability, whether in food, energy, resource efficiency or waste valorisation. Charlie is also on the UKUAT (UK Urban AgriTech collective) advisory board.
Pilot Project To Recycle Crypto Mining Farm Energy Waste Into Energy For Greenhouses
The pilot project's objective is to address concerns about the excess energy waste generated by crypto mining facilities while also supporting the government's objective to become more self-sufficient in food production, rather than relying on imports
Genesis Mining has announced the launch of a new pilot project that will focus on recycling excess energy waste from crypto mining facilities into sustainable heat and energy to power greenhouses.
The pilot project's objective is to address concerns about the excess energy waste generated by crypto mining facilities while also supporting the government's objective to become more self-sufficient in food production, rather than relying on imports.
Commenting on this potential, Mattias Vesterlund, Senior Researcher at RISE (Research Institutes of Sweden), said, "A 1 MW data center would have the ability to strengthen the local self-sufficiency up to 8% with products that are competitive on the market."
The project is a private-public partnership between Systemair, Lulea Technical University, RISE (Research Institutes of Sweden), Boden Business Agency, the local Boden municipality, and Genesis Mining's philanthropic arm, Hashpower For Science. It's located in Boden, Sweden, and has been in development for over one year.
Boden Business Agency's Nils Lindh, said, "This project is exciting because there is an opportunity to contribute in scaling up the food industry and at the same time meet the national energy efficiency targets. It's the first of many projects within the Energy Symbiosis, and hopefully, the results will show that it's very possible to scale up into large commercial production."
For the initial pilot project, one of Genesis Mining's custom-built crypto mining storage containers will be placed near the greenhouse. The greenhouse and container are connected via a custom-built air duct system that carries the excess energy directly from the crypto mining storage container into the greenhouse.
Andreas Johansson, a Senior Lecturer from Lulea Technical University, who is making the calculations for designing the system for air flow from the datacenter to the greenhouse, said, "For the cold climate in the north of Sweden, our calculations show that a 300 m2 greenhouse can easily be heated with a 550 kW container, even with outdoor temperatures reaching almost -30℃. But the potential is much bigger than that. The temperature difference over the greenhouse is in this calculation only 10 degrees since we assume a DC output temp of 35℃ and a GH temp of 25℃. If the DC output is increased to 55℃, then the GH area can be tripled to 900 m2."
Genesis Mining's CEO and co-founder Marco Streng said, "Crypto mining is the backbone that makes decentralized cryptocurrencies and applications possible, and we strongly believe the benefits of this decentralization will transform the world, but all those benefits can't come at the cost of the environment."
As one of the world's largest crypto mining companies with over a dozen data centers spread across the globe, Genesis Mining's R&D team has been actively working on different solutions and collaborations to enable more sustainable crypto mining facilities.
"Genesis Mining has always preferred locations that offered 100% renewable energy sources, that's why we've focused so much on the Nordics. But as the industry leader, we view it as our moral and ethical responsibility to push the industry forward, and finding a way to convert our excess energy has been a major priority. We look forward to scaling this project and bringing it to not only more of our own datacenters — but to others as well."
A Monster Wind Turbine Is Upending An Industry
Twirling above a strip of land at the mouth of Rotterdam’s harbor is a wind turbine so large it is difficult to photograph. The turning diameter of its rotor is longer than two American football fields end to end
G.E.’s Giant Machine, Which
Can Light Up A Small Town,
Is Stoking A Renewable-Energy Arms Race
By Stanley Reed
January 1, 2021
Twirling above a strip of land at the mouth of Rotterdam’s harbor is a wind turbine so large it is difficult to photograph. The turning diameter of its rotor is longer than two American football fields end to end. Later models will be taller than any building on the mainland of Western Europe.
Packed with sensors gathering data on wind speeds, electricity output and stresses on its components, the giant whirling machine in the Netherlands is a test model for a new series of giant offshore wind turbines planned by General Electric. When assembled in arrays, the wind machines have the potential to power cities, supplanting the emissions-spewing coal- or natural gas-fired plants that form the backbones of many electric systems today.
G.E. has yet to install one of these machines in ocean water. As a relative newcomer to the offshore wind business, the company faces questions about how quickly and efficiently it can scale up production to build and install hundreds of the turbines.
But already the giant turbines have turned heads in the industry. A top executive at the world’s leading wind farm developer called it a “bit of a leapfrog over the latest technology.” And an analyst said the machine’s size and advance sales had “shaken the industry.”
A New Generation of Wind Turbines
General Electric’s prototype for a new offshore wind turbine, the Haliade-X, is the largest ever built.
London Eye - Ferris wheel GE Haliade-X 13MW - wind turbine Empire State Building
HEIGHT: 443 feet HEIGHT: 853 feet HEIGHT: 1,050 feet
Source: General Electric
The prototype is the first of a generation of new machines that are about a third more powerful than the largest already in commercial service. As such, it is changing the business calculations of wind equipment makers, developers, and investors.
The turning diameter of the Haliade-X’s rotor is longer than two American football fields.Credit...Ilvy Njiokiktjien for The New York Times
The G.E. machines will have a generating capacity that would have been almost unimaginable a decade ago. A single one will be able to turn out 13 megawatts of power, enough to light up a town of roughly 12,000 homes.
The turbine, which is capable of producing as much thrust as the four engines of a Boeing 747 jet, according to G.E., will be deployed at sea, where developers have learned that they can plant larger and more numerous turbines than on land to capture breezes that are stronger and more reliable.
The race to build bigger turbines has moved faster than many industry figures foresaw. G.E.’s Haliade-X generates almost 30 times more electricity than the first offshore machines installed off Denmark in 1991.
In coming years, customers are likely to demand even bigger machines, industry executives say. On the other hand, they predict that, just as commercial airliners peaked with the Airbus A380, turbines will reach a point where greater size no longer makes economic sense.
“We will also reach a plateau; we just don’t know where it is yet,” said Morten Pilgaard Rasmussen, chief technology officer of the offshore wind unit of Siemens Gamesa Renewable Energy, the leading maker of offshore turbines.
The turbine is so large that it will be able to generate enough power to light up a town of 12,000 homes. Credit...Ilvy Njiokiktjien for The New York Times
Although offshore turbines now account for only about 5 percent of the generating capacity of the overall wind industry, this part of the business has taken on an identity of its own and is expected to grow faster in the coming years than land-based wind.
Offshore technology took hold in Northern Europe in the last three decades and is now spreading to the East Coast of the United States as well as Asia, including Taiwan, China and South Korea. The big-ticket projects costing billions of dollars that are possible at sea are attracting large investors, including oil companies like BP and Royal Dutch Shell, that want to quickly enhance their green energy offerings. Capital investment in offshore wind has more than tripled over the last decade to $26 billion, according to the International Energy Agency, the Paris-based forecasting group.
G.E. began making inroads in wind power in 2002 when it bought Enron’s land-based turbine business — a successful unit in a company brought down in a spectacular accounting scandal — at a bankruptcy auction. It was a marginal force in the offshore industry when its executives decided to try to crack it about four years ago. They saw a growing market with only a couple of serious Western competitors.
Still, G.E.’s bosses figured that to become a leader in the more challenging marine environment, they needed to be audacious. They proceeded to more than double the size of their existing offshore machine, which came to G.E. through its acquisition of the power business of France’s Alstom in 2015. The idea was to gain a lead on key competitors like Siemens Gamesa and Vestas Wind Systems, the Danish-based turbine maker.
A larger turbine produces more electricity and, thus, more revenue than a smaller machine. Size also helps reduce the costs of building and maintaining a wind farm because fewer turbines are required to produce a given amount of power.
These qualities create a powerful incentive for developers to go for the largest machine available to aid their efforts to win the auctions for offshore power supply deals that many countries have adopted. These auctions vary in format, but developers compete to provide power over a number of years for the lowest price.
The prototype is on a piece of land in Rotterdam Harbor, but the Haliade-X is designed as an offshore turbine, to be planted in relatively shallow sea water. Credit...Ilvy Njiokiktjien for The New York Times
“What they are looking for is a turbine that allows them to win these auctions,” said Vincent Schellings, who has headed design and production of the G.E. turbine. “That is where turbine size plays a very important role.”
Among the early customers is Orsted, a Danish company that is the world’s largest developer of offshore wind farms. It has a preliminary agreement to buy about 90 of the Haliade-X machines for a project called Ocean Wind off Atlantic City, N.J.
“I think they surprised everybody when they came out with that machine,” said David Hardy, chief executive of Orsted’s offshore business in North America.
As a huge buyer of turbines, Orsted wants to help “establish this new platform and create some volume for G.E.” so as to promote competition and innovation, Mr. Hardy said.
The G.E. turbine is selling better than its competitors may have expected, analysts say.
On Dec. 1, G.E. reached another preliminary agreement to provide turbines for Vineyard Wind, a large wind farm off Massachusetts, and it has deals to supply 276 turbines to what is likely to be the world’s largest wind farm at Dogger Bank off Britain.
One day turbines will reach a size limit, but “we just don’t know where it is yet,” said Morten Pilgaard Rasmussen of Siemens Gamesa Renewable Energy. Credit...Carsten Snejbjerg for The New York Times
These deals, with accompanying maintenance contracts, could add up to $13 billion, estimates Shashi Barla, principal wind analyst at Wood Mackenzie, a market research firm.
The waves made by the G.E. machine have pushed Siemens Gamesa to announce a series of competing turbines. Vestas, which until recently had the industry’s biggest machine in its stable, is also expected to unveil a new entry soon.
“We didn’t move as the first one, and that of course we have to address today,” said Henrik Andersen, the chief executive of Vestas.
To pull off its gambit, G.E. had to start “pretty much from scratch,” Mr. Schellings said. The business unit called G.E. Renewable Energy is spending about $400 million on design, hiring engineers and retooling factories at St. Nazaire and Cherbourg in France.
To make a blade of such extraordinary length that doesn’t buckle from its own weight, G.E. called on designers at LM Wind Power, a blade maker in Denmark that the company bought in 2016 for $1.7 billion. Among their innovations: a material combining carbon fiber and glass fiber that is lightweight yet strong and flexible.
Offshore turbines account for only about 5 percent of the generating capacity of the overall wind industry, but that number is expected to grow. Credit...Ilvy Njiokiktjien for The New York Times
G.E. still must work out how to manufacture large numbers of the machines efficiently, initially at the plants in France and, possibly later, in Britain and the United States. With a skimpy offshore track record, G.E. also needs to show that it can reliably install and maintain the big machines at sea, using specialized ships and dealing with rough weather.
“G.E. has to prove a lot to asset owners for them to procure G.E. turbines,” Mr. Barla said.
Bringing out bigger machines has been easier and cheaper for Siemens Gamesa, G.E.’s key rival, which is already building a prototype for a new and more powerful machine at its offshore complex at Brande on Denmark’s Jutland peninsula. The secret: The company’s ever-larger new models have not strayed far from a decade-old template.
“The fundamentals of the machine and how it works remain the same,” said Mr. Rasmussen, the unit’s chief technology officer, leading to a “starting point that was a little better” than G.E.’s.
There seems to be plenty of room for competition. John Lavelle, the chief executive of G.E.’s offshore business, said the outlook for the market “gets bigger each year.”
Stanley Reed has been writing from London for The Times since 2012 on energy, the environment and the Middle East. Prior to that, he was London bureau chief for BusinessWeek magazine. @stanleyreed12 • Facebook
A version of this article appears in print on Jan. 2, 2021, Section B, Page 1 of the New York edition with the headline: A Monster Wind Turbine Is Upending an Industry. Order Reprints | Today’s Paper | Subscribe
Micro-Naps For Plants: Flicking The Lights On And Off Can Save Energy Without Hurting Indoor Agriculture Harvests
A nighttime arrival at Amsterdam’s Schiphol Airport flies you over the bright pink glow of vegetable production greenhouses. Growing crops under artificial light is gaining momentum, particularly in regions where produce prices can be high during seasons when sunlight is sparse.
The Netherlands is just one country that has rapidly adopted controlled-environment agriculture, where high-value specialty crops like herbs, fancy lettuces and tomatoes are produced in year-round illuminated greenhouses. Advocates suggest these completely enclosed buildings – or plant factories – could be a way to repurpose urban space, decrease food miles and provide local produce to city dwellers.
One of the central problems of this process is the high monetary cost of providing artificial light, usually via a combination of red and blue light-emitting diodes. Energy costs sometimes exceed 25% of the operational outlay. How can growers, particularly in the developing world, compete when the sun is free? Higher energy use also translates to more carbon emissions, rather than the decreased carbon footprint sustainably farmed plants can provide.
I’ve studied how light affects plant growth and development for over 30 years. I recently found myself wondering: Rather than growing plants under a repeating cycle of one day of light and one night of darkness, what if the same daylight was split into pulses lasting only hours, minutes or seconds?
Short bursts of light and dark
So my colleagues and I designed an experiment. We’d apply the normal amount of light in total, just break it up over different chunks of time.
Of course plants depend on light for photosynthesis, the process that in nature uses the sun’s energy to merge carbon dioxide and water into sugars that fuel plant metabolism. Light also directs growth and development through its signals about day and night, and monkeying with that information stream might have disastrous results.
That’s because breaking something good into smaller bits sometimes creates new problems. Imagine how happy you’d be to receive a US$100 bill – but not as thrilled with the equivalent 10,000 pennies. We suspected a plant’s internal clock wouldn’t accept the same luminous currency when broken into smaller denominations.
And that’s exactly what we demonstrated in our experiments. Kale, turnip or beet seedlings exposed to cycles of 12 hours of light, 12 hours dark for four days grew normally, accumulating pigments and growing larger. When we decreased the frequency of light-dark cycles to 6 hours, 3 hours, 1 hour or 30 minutes, the plants revolted. We delivered the same amount of light, just applied in different-sized chunks, and the seedlings did not appreciate the treatment.
The same amount of light applied in shorter intervals over the day caused plants to grow more like they were in darkness. We suspect the light pulses conflicted with a plant’s internal clock, and the seedlings had no idea what time of day it was. Stems stretched taller in an attempt to find more light, and processes like pigment production were put on hold.
But when we applied light in much, much shorter bursts, something remarkable happened. Plants grown under five-second on/off cycles appeared to be almost identical to those grown under the normal light/dark period. It’s almost like the internal clock can’t get started properly when sunrise comes every five seconds, so the plants don’t seem to mind a day that is a few seconds long.
Just as we prepared to publish, undergraduate collaborator Paul Kusuma found that our discovery was not so novel. We soon realized we’d actually rediscovered something already known for 88 years. Scientists at the U.S. Department of Agriculture saw this same phenomenon in 1931 when they grew plants under light pulses of various durations. Their work in mature plants matches what we observed in seedlings with remarkable similarity.
A 1931 study by Garner and Allard tracked the growth of Yellow Cosmos flowers under light pulses of various durations. J. Agri. Res. 42: National Agricultural Library, Agricultural Research Service, U.S. Department of Agriculture., CC BY-ND
Not only was all of this a retread of an old idea, but pulses of light do not save any energy. Five seconds on and off uses the same amount of energy as the lights being on for 12 hours; the lights are still on for half the day.
But what would happen if we extended the dark period? Five seconds on. Six seconds off. Or 10 seconds off. Or 20 seconds off. Maybe 80 seconds off? They didn’t try that in 1931.
Building in extra downtime
It turns out that the plants don’t mind a little downtime. After applying light for five seconds to activate photosynthesis and biological processes like pigment accumulation, we turned the light off for 10, or sometimes 20 seconds. Under these extended dark periods, the seedlings grew just as well as they had when the light and dark periods were equal. If this could be done on the scale of an indoor farm, it might translate to a significant energy savings, at least 30% and maybe more.
Recent yet-to-be published work in our lab has shown that the same concept works in leaf lettuces; they also don’t mind an extended dark time between pulses. In some cases, the lettuces are green instead of purple and have larger leaves. That means a grower can produce a diversity of products, and with higher marketable product weight, by turning the lights off.
One variety of lettuce grew purple when given a 10-second dark period. They look similar to those grown with a five-second dark period, yet use 33% less energy. Extending the dark period to 20 seconds yielded green plants with more biomass. J. Feng, K. Folta
Learning that plants can be grown under bursts of light rather than continuous illumination provides a way to potentially trim the expensive energy budget of indoor agriculture. More fresh vegetables could be grown with less energy, making the process more sustainable. My colleagues and I think this innovation could ultimately help drive new business and feed more people – and do so with less environmental impact.
July 22, 2019 6.58am EDT Updated July 22, 2019 2.40pm EDT
This article was updated with a corrected legend on the photograph of the plants grown in 1931.
Future of Indoor Vertical Farming With Microgrids
Schneider Electric’s Don Wingate discusses how microgrids can help the indoor vertical farming movement realize its full potential
09-07-2020 | Microgrid Knowledge
Schneider Electric’s Don Wingate discusses how microgrids can help the indoor vertical farming movement realize its full potential.
While indoor agriculture has steadily gained traction in recent years as the world seeks alternative ways to feed growing populations, the uncertainty of today’s global pandemic has accelerated a rethinking of the way we obtain our food. In the last few months, modern supply chains experienced volatility like never before and it wasn’t long before we started to see the impact beyond medical gear and personal protective equipment and began to affect food production. According to the Institute of Supply Chain Management, 75% of companies reported some kind of supply chain disruption due to COVID-19.
Indoor vertical farming is emerging as an alternative to conventional farming because it both requires lower land-use and introduces the opportunity to bring agricultural production closer to consumers — shortening supply chains and increasing footprint productivity. This is especially important during times of turmoil, which is broader than the current pandemic as weather events and changing climate patterns continue to put constant strain on traditional farming practices. In addition to shortening supply chains, indoor farming has many other advantages in comparison to traditional agriculture such as using zero pesticides, employing 95% less water, and reducing food waste. Health benefits also include fresher food, increased urban availability, and pollution reduction.
Despite the major advantages, there is one looming barrier to mainstream adoption: the process is very energy-intensive.
Solving for the energy intensity problem
Vertical farming presents a unique opportunity to grow food on already developed land and increase domestic food production, but the energy demand required to power these facilities is much higher than other methods of food production. In fact, we’ve identified indoor agriculture as one of the four major drivers that will increase electricity consumption in the next decade, along with electric vehicles, data centers, and the electrification of heat. This is why more of today’s modern farming companies are turning to microgrids as a possible solution to ease their energy challenges.
Although most of today’s facilities are not equipped to meet the electricity needs of an indoor agriculture operation, microgrids can provide dynamic energy management and the resources required to support maximum productivity, sustainability, and energy efficiency. They can provide localized power generation and utilize renewable distributed energy resources to help deliver power and reach clean energy goals, while also allowing users more control and reliability. Additionally, microgrids can capture and repurpose CO2 emissions to help in crop production.
Moreover, microgrids provide resilience from unexpected outages that could result in a loss in production. A key advantage of vertical farms is their ability to allow crops to grow year-round, and communities rely on their ability to deliver on this promise. Microgrids not only have several clean energy benefits, but they also increase business continuity that maximizes output. Given their ability to operate either in conjunction with or as an island from the utility grid, they can keep the farm producing even when the grid goes down.
The case for investment: Securing an affordable solution
Building and operating a vertical farm requires various technologies that can translate to high startup cost and design complex processes. At the same time, it is more expensive to maintain a vertical farming operation than traditional field farming. Microgrids offer a compelling value proposition, but they’re inherently complex machines and not many companies have the upfront capital or in-house expertise needed to make the investment. Fortunately, innovative business models such as energy-as-a-service (EaaS) help provide price certainty and make the investment attainable.
For example, a modern farming company, Bowery Farming, created a facility wherein crop production is 100 times more efficient than traditional farmland. This generated a need for a greater need for reliable, efficient power. Thus, the company made the decision to integrate a hybrid microgrid system that would feature a rooftop solar array, natural gas generator, and a lithium-ion battery energy storage system through an EaaS business model. Through EaaS, Bowery Farming saved upfront capital that can be used toward additional operational investments.
By 2050, the world’s population is expected to grow by another 2 billion people, and feeding it will be a major challenge. According to the projections of the Food and Agriculture Organization, we have to increase overall food production by 70% by this timeline. Coupled with new concerns that have surfaced as a result of today’s global pandemic and unstable weather, vertical farming will play a key role in future food production and institutions will take notice. However, the technology that will help ease some of the industry’s ongoing energy challenges will be just as important to aid the transition.
Don Wingate is the VP of utility and microgrid solutions at Schneider Electric.
Source: Microgrids Knowledge
Photo Courtesy of Microsoft News