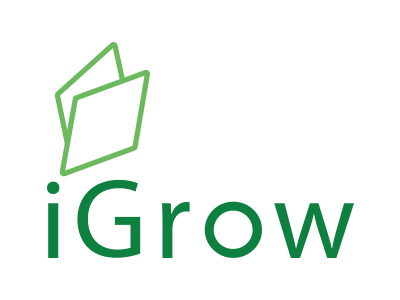
Welcome to iGrow News, Your Source for the World of Indoor Vertical Farming
Farm Tech Investing Is Accelerating Faster Than Ever – New Report
‘Farm tech’ investing soared to $7.9 billion in 2020, topping 2019 investments by $2.3 trillion, or 41%, according to AgFunder’s latest Farm Tech Investment Report.
By Jessica Pothering & Louisa Burwood-Taylor
August 4, 2021
We’ve been watching the surge of investor interest in upstream, close-to-the-farm technologies since the Covid-19 pandemic started. We now have numbers that show just how significant that farm tech investor interest is.
‘Farm tech’ investing soared to $7.9 billion in 2020, topping 2019 investments by $2.3 trillion, or 41%, according to AgFunder’s latest Farm Tech Investment Report. [Disclosure: AgFunder is AFN‘s parent company.]
To put this in perspective, farm tech’s acceleration was about six percentage points greater than agrifoodtech overall — that’s foodtech and farm tech combined — and 37 percentage points higher than global VC’s year-over-year increase in 2020 (which Crunchbase pegged at just 4%.)
Much of the investment activity was led by two sectors: Ag Biotechnology and Novel Farming Systems (mostly the indoor farming of crops and insects). Investors pumped more than $1.5 billion into each category. Ag Biotech companies attracted particular interest from investors: 173 deals closed, representing 58% growth from 2019. Novel Farming Systems deal activity grew by 47% year-over-year.
As difficult as 2020 was globally (2021 hasn’t been pretty in many parts of the world), the pandemic seems to have buoyed farm tech because it “exposed cracks in the industrial agricultural system,” particularly the vulnerability of the food supply chain, Infarm’s CEO Erez Galonza told AFN in an interview featured in the report. The German hyper-local vertical farming venture, whose modular units can be found in grocery stores across Europe, secured $170 million from investors last year.
“[The pandemic] highlighted the need for resilient, localized solutions,” he added.
Farm tech funding 2012-2020
Yellow bar denotes projected total by end of 2021 as more 2020 data come to light. Credit: AgFunder
SPACs for best-funded farm tech categories
Perhaps the biggest winner, in that sense, was US-based high-tech greenhouse operator, AppHarvest. The company announced plans to go public last September via a special purpose acquisition company, or SPAC. It officially listed on the Nasdaq stock exchange in January, just weeks after shipping its first harvest.
AppHarvest recently purchased robotics leader and AgFunder portfolio company Root AI, making founder Josh Lessing the publicly listed company’s new CTO. Read more here.
AppHarvest kicked off a SPAC trend for Farm Tech companies, and Novel Farming ventures specifically. We’ve since seen four other agrifoodtech companies announce plans to go public through SPACs: agbiotech companies Benson Hill and Gingko Bioworks and novel farming ventures AeroFarms and Local Bounti. (Keep up to date with agrifoodtech SPAC news here.)
It is interesting to see public listing activity happening in the two agrifoodtech sectors that surged the most in terms of deal activity last year; it signals that there could be more to come if the process proves successful for these early case studies. For now, it’s certainly providing an exit opportunity to early agtech ventures that bet on deep technologies requiring significant amounts of time (and certainly hefty commitments of resources) to become revenue-generating, much less profitable.
That in and of itself is a significant milestone for a maturing agtech industry.
Pandemic pivots
It isn’t all about Ag Biotech and Novel Farming Systems; the biggest deals of 2020 were in the Agribusiness Marketplace sector. Boston-based Indigo Ag raised two investment rounds, totaling $535 million last year, and San Carlos, Calif.-based Farmers Business Network raised $250 million.
Indigo Ag’s executive team told AFN that because it deals directly with the food supply chain, the company confronted an immediate shock from the pandemic.
“The global pandemic was an external challenge that required our team, like many others, to quickly adapt to ensure that our customers and employees were supported,” they said in a special interview featured in the report. “While we were fortunate that our operations were not significantly impeded by the pandemic, we did have to quickly expand our support services and tap our creativity to enable our farmers, buyers and partners to manage their business with confidence during the early stages of Covid-19.”
The company launched a transport support hotline for grain growers, carriers and shippers to ensure the supply of grain could continue to move as efficiently as possible. It also focused on developing pricing tools, access to grain marketing advisors, and even a podcast to help growers grapple with pandemic-related market volatility.
Indigo Ag isn’t a stranger to unchartered business terrain. The company has put itself in the middle of the evolving but murky carbon markets. “With new players entering the carbon space nearly weekly – many taking less rigorous approaches to verification and measurement – Indigo has remained steadily focused on enabling farmers to make informed decisions about how, when and why to participate in the carbon market,” the Indigo Ag team told AFN.
They added: “By leveraging our scientific insight, technological capabilities, and use of industry-leading carbon accounting protocols, Indigo ensures farmers are supported with the right tools and information to take advantage of the opportunity to raise a new and increasingly valuable crop: carbon.”
Food’s sustainable future
Verification of carbon-capture accounting is indeed getting increased attention and scrutiny. It’s likely to be a key theme in the agriculture industry going forward, and it’s one of AgFunder’s key trends to watch in 2021, alongside overall food system sustainability.
“We can invent a new, sustainable food industry, feeding the planet all the while protecting its biodiversity, and combatting climate change,” the executive team behind French insect farming venture Ynsect told AFN. The company sees insects as a crucial component of food’s sustainable future.
“Insects can aid food security and be a part of the solution to food shortages, given their high nutritional value, low requirements for land and water, low emissions of greenhouse gases, and the high efficiency at which they can convert feed into food,” the Ynsect team argued in an interview featured in the report.
Investors seem to agree: Ynsect scored the largest amount of funding in the novel farming sector in 2020, raising $222 million in 2020, taking its Series C total to $372 million, to build an industrial-sized farm for its Molitor mealworms near the city of Amiens. Ynsect went on to acquire Dutch insect farming company Protifarm in April of this year.
Many of the world’s consumers may as yet be skeptical of insects as a protein source. But consumer consciousness and demand for high-quality, low-environmental impact foods is certainly a trend influencing the evolution of Farm Tech, as evidenced by the range of startups that attracted funding in 2020.
Ag Biotech ventures like Benson Hill, GreenLight Biosciences, and Pivot Bio secured investor backing for helping to diversify crop input technology away from environmentally-harmful synthetic chemicals.
Novel Farming ventures are developing highly efficient and resource-conservative approaches to growing fresh foods.
Farm Management Software, Sensing & IoT companies like ICEYE, Aclima and Cervest are illuminating climate change impacts and helping companies anticipate and forecast climate-related disruptions.
Food preservation technologies like Apeel Sciences’s are helping reduce food waste, as are e-grocery services like Misfits Market and Imperfect Foods, which sell “ugly produce” that would otherwise be wasted among their fresh foods and grocery offerings.
Companies like Celtic Renewables are turning farm waste into a resource through the production of biofuels.
“As companies increasingly make commitments to improve their environmental impact – and governments at all levels enact policies to encourage climate-smart agriculture,” said the Indigo Ag team, “the opportunity for agriculture to act as a climate solution will only become more apparent.”
Sustainably Goals Urges Architect To Build A Greenhouse Around Former Fruit Farm
As decided by the municipality of Gooik, visitors can now see the refurbished agricultural buildings enclosed within a greenhouse-like structure, this way learning more about the countryside of Belgium
Is it a greenhouse, is it an educational center, is it a former fruit farm? It is all in one. A former fruit farm in Gooik, Belgium, is now functioning as an educational center. As decided by the municipality of Gooik, visitors can now see the refurbished agricultural buildings enclosed within a greenhouse-like structure, this way learning more about the countryside of Belgium. Architect Jo Taillieu: "We wanted a generous building that could provide the necessary comfort to all users of the center, even in bad weather, and provide an anchor point for exploring the Pajottenland.”
The old farmhouse had been used as an education center already for years, but the project became to big to be run by volunteers completely. That’s why the municipality bought it and realized further expansion plans.
Interwoven
"Paddenbroek is by no means inconspicuous. In the hilly Pajottenland region, landscape, nature, heritage, and culture have been closely interwoven for centuries. Maintaining that balance was one of the major goals," architect Jo Taillieu explains. "The farmstead and especially the outbuildings were in a bad state and unsuitable for achieving the intended objectives. The link with the context was almost non-existent. The first idea - a classic renovation - was discarded, as was a new building, because it was unrealistic and did not meet the task that could be expected of an educational and tourist center. We, therefore, opted for a roof that would cover the farmstead, the historic baking oven, and the space around it."
Photo courtesy Jo Tailleu
Sustainability was one of the main goals of the construction. The dilapidated outbuildings were dismantled and the farmstead and the baking oven incorporated, restored, and insulated with moisture-regulating wood-wool cement boards and loam. Only these rooms and the offices can be heated. Thus, heating costs are sustainably limited to a few cores in the building and not everything needs to be air-conditioned. Inside the unheated greenhouse, therefore, there is an intermediate climate. Visitors are sheltered from rain and wind and can still enjoy the magnificent view of the surroundings. Upstairs are two more multi-purpose rooms that can be used as meeting rooms.
According to Stefan De Clerq, one of the business managers of the greenhouse construction company, the challenge was mostly the size and complexity of the project, as the features of this construction did not allow for a basic model. We created a unique truss and steel construction where each step was carefully monitored. All steel components were produced in our own workshops. This challenge was brought to a successful conclusion by the close cooperation between our draftsmen, our production team, and the external architects. Our own typical aluminum profiles and glass, applied in the roof and wall, also contribute to the elegant appearance of this nevertheless quite robust realization."
The construction of a complex like that of Paddenbroek in a rural area is not obvious and initially met with the necessary reservations, as could be expected. The fact that the municipality was prepared to go along with the story of architect Jo Taillieu and project manager Dries Deleye, therefore, shows vision and insight. Now that the construction is complete, everyone agrees that Gooik has gained a valuable multipurpose center that responds to ecological sustainability and from which the residents can also derive maximum benefit.
Lead photo: Photo courtesy Jo Tailleu
Publication date: Thu 29 Apr 2021
© HortiDaily.com / Contact
10 Ways Square Roots’ Farm-Tech Platform Empowers The Next Generation of Farmers
Square Roots’ scalable “farmer-first” platform brings fresh, healthy food to urban areas all year-round, while simultaneously training future generations of farmers to maintain sustainability in the future.
Square Roots is building a distributed network of indoor, modular farms, farmed by a new generation of farmers, to grow local food for people in cities all over the world. Here’s why it’s working.
Square Roots Super Farms are scalable, resilient and smart, and can be built fast. (Image: Via Chicago Architects + Diseñadores)
Square Roots’ scalable “farmer-first” platform brings fresh, healthy food to urban areas year-round, while simultaneously training future generations of farmers. With production farms in Brooklyn, New York, and Grand Rapids, Michigan (with more to come in 2020!), Square Roots has a mission to bring local, real food to people in cities across the world while empowering the next generation of leaders in urban farming.
Whether we’re in the farms tweaking CO2 levels, or in a board meeting plotting a pathway for what the company looks like in 2050, every decision we make is guided to help us achieve our mission faster, smarter, and with as much impact as possible.
Choices we’ve made around our technology platform are a good illustration of that. Our platform needs to bring fresh, healthy food to urban areas year-round, consistently, sustainability, and on any continent in the world. At the same time, it must also be a welcoming environment, conducive to training future generations of farmers to be productive, fast.
Central to our platform is the decision we made very early in the company’s life to build a distributed network of modular Climate Containers, as opposed to following the plant factory template.
Inside a Square Roots Climate Container, data-empowered farmers work with optimum growing conditions, all year round.
There are a lot of smart people in this industry, many with different visions for the optimum architecture and model for indoor farming (e.g. plant factories). But all working hard to bring better food to market — which, given our wider vision to bring real food to everyone, is wonderful to see. The more of us working on the real food revolution the better — and we want all of these systems to flourish. But here are 10 reasons why we think container farming rocks:
1. Speed to Market
Today we can enter a new market and open a Square Roots “Super Farm” — with 25 Climate Containers, cold storage, biosecurity infrastructure, and everything else you need to run a food-safe farm at scale — in less than three months, like we did in partnership with Gordon Food Service last Fall. That time period is only coming down. In comparison, building a plant factory can cost tens of millions of dollars, as well as take years to construct. We want to get real food to more people, and fast!
2. Easy to Scale
To meet increasing market demand, we simply add Climate Containers to any existing deployment. This means just-in-time capital deployment, and also just-in-time technology deployment. This is really important in an industry where the technology is improving fast. You don’t want to spend years and millions to open a big farm full of old tech that immediately needs a refresh.
3. Climate Control
I was an early investor in Chicago’s Farmed Here, one of the first and largest plant factories in the US. There, I saw first-hand how much the team struggled to control the climate in a building that size. Plants don’t like it when you get it wrong. And neither do landlords — the humidity can wreak havoc with the underlying infrastructure. In our programmable Climate Containers, each one built inside a 320 square foot shipping container, optimum conditions for a variety of crops can easily be maintained. The perfect climate for each variety can be seamlessly replicated — in any market — to ensure consistent quality every time, at every harvest.
Alyssa Patton, Square Roots Next-Gen Farmer, harvesting fresh, local basil inside a Climate Container in Grand Rapids, Michigan.
4. Diversity of Products
Multiple containers on our Super Farms allow for multiple climates, which lets us grow multiple crops at the same time to satisfy local market demands. For example, basil requires a completely different climate than chives to grow well, so it’s practically impossible to grow these two products together in a way that tastes good if you have a giant farm with one mono climate. The ability to grow multiple quality SKUs is particularly important in the retail market, where product variety is key to getting shelf real estate. Having multiple climates also means we can tackle many niches in any local market (e.g. using one container on a Super Farm to grow something exotic like Shiso or Mustard Greens), giving us a lot of business flexibility while keeping things interesting for our teams of farmers.
5. Sustainable Systems
As with most hydroponic growers, Square Roots uses zero pesticides, and 90% less water than outdoor farms. We can also be clever about energy usage. For example, we make it “daytime” in the farm by turning on our grow lights overnight when there is excess energy in the grid, and the cost per kilowatt-hour is lower. However, if for some reason we need to be in the farms during “daytime,” we can put a Climate Container into “harvest mode” — which dims the lights, and configures the climate to be optimum conditions for people at work — before seamlessly switching back to plant growing mode once we’re done.
6. Location
Our modular architecture means we can be very creative in repurposing existing city infrastructure when we look for locations to build a farm. We can pop up on an empty parking lot like we did in Brooklyn, New York, or build a campus on the headquarters of a major distribution company like we did with Gordon Food Service, or even build into a new development. This flexibility means we can build our Super Farms literally in the same zip code as the end consumer. This means fresher and tastier products for the customer, fewer food miles (most industrial food is shipped in from the other side of the world!), and less food waste. It also helps to get consumers more connected to their food and the people who grow it — they can simply jump on a subway or in their car, and come visit one of our farms!
7. Food Safety and System Resilience
All indoor farms need to be prepared for bad things to happen. While there is way less risk in a controlled environment versus an outdoor farm, it’s inevitable that you will get some sort of pest outbreak, powdery mildew, or some other issue at some point while you’re managing a complex ecosystem full of living, breathing plants. If that ever should happen in one of our Climate Containers, we can quickly shut it down and reboot that single node while the rest of the network keeps going strong. I’ve seen this happen in a plant factory, with one big mono climate, and you lose all your crops.
8. Faster Learning
Our farms are cloud-connected, and we collect millions of data points that we analyze to determine how changes in certain environmental parameters can impact factors like yield, taste, and texture of the final product. More climates in more containers means more feedback loops, which means faster learning. To systematize this learning, we’ve built The Square Roots Farmer Toolbelt — a software which is now the OS for the whole company as we all learn faster together.
9. The Network Gets Smarter as it Scales
Square Roots’ cloud-connected farms and data-empowered farmers learn from each other, enabling us to replicate success from one location to another, seamlessly. Working with Gordon Food Service to build farms across their network of distribution centers and retail stores brings us closer to the vision of a distributed network of indoor farms, bringing local, real food to people in cities across the world—while empowering thousands of next-gen leaders in urban farming through our unique training program.
10. Sense of Responsibility
Perhaps this is unique to Square Roots and our Next-Gen Farmer Training Program, but because we grow in modular Climate Containers, we’re able to give all our young farmers a personalized understanding of their individual impact on the overall business. The Square Roots Farmer Toolbelt provides day-to-day instructions on a per-farmer and per-crop basis, as well as a means for data capture, and real time analysis of both plant health and business metrics. All this information is accessible from the tablets that everyone on our farm team carries everyday. This system also ensures that we track every aspect of production — who does what, when, and how, from seed to sales. This is a goldmine of data, that not only helps us improve operations, but also implicitly provides traceability. In December 2018, we started exposing this data to consumers in the form of our Transparency Timeline. On every package of Square Roots produce, you can simply scan a QR code and get a complete story of where your food comes from — seed to shelf.
Simply scan the QR code on every Square Roots package to see where your food comes from.
Our Super Farm platform is exciting in terms of scalability, resilience, and efficiency, and it’s a really wonderful environment for our farmers to farm in. For urban consumers it means local farmers growing your food with love — which is why it tastes absolutely delicious. And technology enables us to grow a ton of food in a very small area, in ways that make a lot of business sense too. It’s a classic example of “doing well by doing good”.
It has been an exciting journey to our Super Farm platform. When we launched Square Roots back in 2016, we were very focused on figuring out the Farmer Training Program model — as we knew that farmers bring love to the food, the program would create enormous impact over time, and it would also be a long term engine of growth. So we partnered with a number of 3rd parties who could provide parts of the growing system for us, while we got the training program right. (In many ways, that was like Tesla sourcing our chassis from Lotus for the first Roadster). After that initial phase, and finding out what the urban farming world needs — i.e. higher quality yields with much lower costs to drive scalable unit economics, and ultra-high standards of biosecurity to support operations that are first class in food safety—we have developed our own technology specifically tailored to our model. This enables us to grow local food at incredible scale in ways that make sense for people, planet, and profits.
Our partnership with Gordon Food Service was announced at the end of March 2019, and our first co-located farm opened just six months later in Grand Rapids, Michigan — marking our next step of bringing local food to people in cities all across North America while training thousands of future farmers. Which, in a neat and circular way, brings us right back to the mission statement we started this post with.
Of course, we still have lots of work to do and we have a lot of exciting announcements coming this year as we grow! And, we’re always looking to talk with great people — from hardware and software engineers to farmers and plant scientists. So feel free to check our website and get in touch.
This article was originally published on the Indoor Ag-Con blog by Kimbal Musk on March 4, 2020.
Published by Dani Kliegerman for iGrow News
Farm Tech Society, Indoor Ag-Con Partner to Present "Future of Farming | Educating The Next Generation to Make CEA Scalable" | August 19, 2020 - 2 PM EST
New Session Joins Indoor Ag-Conversations Webinar Series, August 19, 2020, From 2:00-3:00 pm EST
New Session Joins Indoor Ag-Conversations Webinar Series,
August 19, 2020, From 2:00 - 3:00 pm EST
(AUGUST 10, 2020) -- As the Controlled Environment Agriculture (CEA) industry grows, companies are facing greater shortages in qualified talent. How can innovation in training and education accelerate the industry to the benefit of all? Hosted by the Farm Tech Society and Indoor Ag-Con, LLC, "The Future of Farming: Educating the Next Generation To Make CEA Scalable," will bring together a panel of top educators to explore viable answers to this pressing challenge.
The latest topic to join the Indoor Ag-Conversations free webinar series, the program will be held on Wednesday, August 19, 2020, from 2:00 - 3:00 pm EST.
Moderated by Farm Tech Society Chairman Ian Kanski, Director, Center for Advanced Agriculture & Sustainability, Harrisburg University of Science & Technology, the panel will include Dr. Laura Vickers, Senior Lecturer in Plant Biology, Harpers Adams University; Sonny Ramaswamy, president, Northwest Commission on Colleges & Universities; and Dr. Marito Garcia, Fellow, Darden School of Business, Center for Global Initiatives (DCGI), University of Virginia.
"We're excited to partner with the Farm Tech Society to foster discussion around this vitally important topic," says Brian Sullivan, co-owner, Indoor Ag-Con, LLC. "The COVID crisis has certainly brought attention and increased awareness to the myriad benefits CEA can offer -- from local food/supply chain solutions to year-round production. Attracting and educating a younger generation are critical to helping CEA reach its full potential."
"Strengthening and securing the future of the CEA industry are key to the Farm Tech Society mission. The new Indoor Ag-Conversations webinar series offers a wonderful platform to exchange ideas and spark new ones. We're looking forward to a great discussion," adds Farm Tech Society Board Chairman and program moderator Ian Kanski. "
During the 60-minute program, the panel will discuss a range of topics, including:
Upskilling and retraining from challenged industry sectors
Skills gaps, labor challenges, and automation
Micro-credentialing and industry certifications
Portability of skills learned in CEA operations
Public-private partnerships for training and education
The program is free and attendees can register at www.indoor.ag/webinar
The Indoor Ag-Conversations panelists will bring a wealth of educational industry experiences and insights to the discussion.
Ian Kanski is a social entrepreneur with a career dedicated to human development and sustainable technology. He is the Director of the Center for Advanced Agriculture and Sustainability at Harrisburg University of Science and Technology, Board Chair for FarmTech Society in Brussels, Belgium and co-founder of INTAG. Ian is also Co-Founder of the STEM Education consultancy B Theory Inc and is the former Chief Product Officer of Zoetic Global.
Dr. Laura Vickers gained her Ph.D. in 2012 from the University of Birmingham before working as a postdoc at Harper Adams University (HAU). She took up her role as Lecturer at HAU in 2014 and was also awarded a NERC Knowledge Exchange Fellowship in Horticulture, where she worked with the Horticulture Innovation Partnership in producing an R&D strategy for the Ornamental industry. She is now a Senior Lecturer at HAU and a leading member of the Urban Farming Group.
Sonny Ramaswamy assumed the presidency of the Northwest Commission on Colleges and Universities in 2018 after six years of service as President Obama's appointee as the Director of the National Institute of Food and Agriculture (NIFA) in Washington, DC. Prior to this position in the federal government, he worked for 30 years at several Land-Grant Universities, rising through the ranks from assistant professor to dean.
Dr. Marito Garcia is a Fellow at the Darden School of Business, University of Virginia, Charlottesville, VA, USA. He is a Board Director at Learning Equality, a non-profit education technology company based in San Diego, CA. He is co-founder of Italpinas Development Corporation, a green-building development company in Asia, based in Manila, Philippines; and Orenko Ltd (Cambridge, UK), an energy development company. He also served as senior staff at the World Bank, Washington, DC in various capacities.
Indoor Ag-Con LLC created the new Indoor Ag-Conversations series to share content originally planned for its May 2020 in-person annual conference that was postponed due to the Covid-19 pandemic. To learn more about this session, as well as other upcoming programs on the schedule, visit www.indoor.ag/webinar
ABOUT INDOOR AG-CON LLC
Founded in 2013, Indoor Ag-Con, LLC produces the premier event for the indoor | vertical farming industry touching all sectors of the business — produce, legal cannabis, hemp, alternate protein and non-food crops. In December 2018, three event industry professionals – Nancy Hallberg, Kris Sieradzki and Brian Sullivan – purchased Indoor Ag-Con LLC, setting the stage for further expansion of the events globally. For more information, visit: https://indoor.ag
ABOUT FARM TECH SOCIETY
The Farm Tech Society (FTS) is an international non-profit industry association that unites and supports the Controlled Environment Agriculture (CEA) industry, seeking to strengthen the sector through the development and implementation of resilient and future proof methods and technologies for indoor growing For more information, visit https://www.farmtechsociety.org
Indoor Ag-Con, 950 Scales Road, Building #200, Suwanee, GA 30024, United States