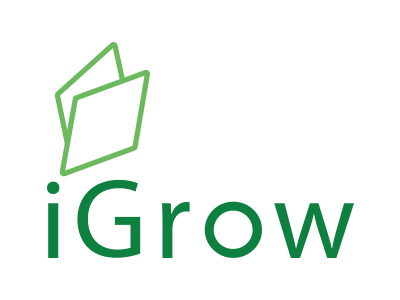
Welcome to iGrow News, Your Source for the World of Indoor Vertical Farming
Smart Farms: Getting To the Heart of The Matter
Labour costs account for up to 50% of the market price of vegetables, berries, and herbs. However, just like the tractor that once transformed agriculture, the new technological revolution greatly reduces the need for manual, skilled and specialist labour
August 3, 2021
Take a look behind the scenes of vertical plant automation and find out what it takes to bring a smart farm to life with exciting exploded-view diagrams.
Labour costs account for up to 50% of the market price of vegetables, berries, and herbs. However, just like the tractor that once transformed agriculture, the new technological revolution greatly reduces the need for manual, skilled and specialist labour. Today, the work is done by a team of robots, sensors, artificial intelligence, and a core team of highly skilled professionals who manage hundreds of farms at once using special software. As a result, we witness the “battle for the harvest” moving into the IT domain.
A vertical farm functions as an organism, and its equipment can be compared to human organ systems. Its sensors and senders are the nervous system, its air conditioners and dehumidifiers act as the respiratory system, while the solution supply pipeline represents the circulatory system. We can compare the nutrient mixing unit to the endocrine system, tray conveyors and lifts to muscles. Naturally, this organism has a “brain” — the Growtune IT platform.
The degree to which the brain can accurately and confidently “take control” determines how ready various systems, nodes, and technologies are to operate without human intervention. Below, we describe all of the tech that lies inside a vertical farm. How, where, and at what production stages does the automation work? For this purpose, we’ll leverage the somewhat forgotten “exploded-view diagram” style. This way, we'll be able to show all the devices the farm uses to take care of the plants.
1. Breathing: ventilation and air conditioning
Let’s remember biology classes. Plants use photosynthesis to turn light, water and CO2 into oxygen and energy. By doing so, they can consume far more CO2 than is normally present in the air. Since the farm, like a space station, uses a closed-loop air exchange system, with no air inflow from the street, creating an optimal environment and climate for plants is purely an engineering challenge. This includes purifying, conditioning, and adding some CO2 to the room to allow plants breathe freely and grow intensively.
“People who walk into a vertical farm for the first time notice how nice and clean the air is. That’s no surprise because it doesn’t contain any dust — there’s nowhere dust can appear from in the closed-loop circuit of the farm.
Alexey Novokreshchenko, Head of Automation at iFarm
The farm has multiple air conditioning units. It’s not just a matter of maintaining a certain temperature and humidity. We need to make sure that the climate is as homogeneous as possible throughout the entire arm, including at different heights. So, instead of one super-powerful unit, we install several medium-sized devices. This provides the right air circulation and creates a failure-proof system.
Hydroponic technologies tend to create a lot of moisture, and the farm air typically needs to be dehumidified (iFarm has developed and patented a dehumidification system that allows you to reuse this water to feed your plants). There are times, though, when you need to do the opposite: for example, you may need to humidify the air, especially at the initial stage of starting a farm when you don’t have a lot of plants.
2. Energy: grow lights
Photosynthesis, that is the conversion of light energy into chemical energy, only occurs when there is light. Agronomists call artificial lighting of plants “supplemental lighting”. It may vary from one area of the farm to another, depending on the crop and its cultivation phase. The light control unit creates “day” and “night” conditions for plants. The most frequent setup resembles a nice summer day: 14–16 hours of light and 8–10 hours of darkness. Darkness is crucial: the night is when cellular respiration occurs and other important processes take place.
“The plant depends on the day-and-night schedule. Its structure and maturation phases vary depending on the light cycle. Keep the microgreen sprouts in the dark a little longer, and they'll stretch out but will become coarser. By changing the lighting, you can experiment with taste. For example, if you keep sunflower microgreens in the dark for 10 days and then expose them to the light for a full day, you’ll get long and very sweet sprouts.”
Nikolai Podvigin, Head of the Agrolaboratory at iFarm
Agronomists at pilot farms refine cultivation flow charts. For example, they are currently experimenting with variable brightness to grow pine strawberries: the lamps are equipped with a dimmer so you can gradually add brightness. It seems that the agronomists’ hypothesis holds true — the berry evidently "enjoys" long dawns. Through smooth, incremental changes in lighting, the osmotic pressure in the stem and leaves grows gradually, whereas its surge upon sudden light exposure can have a tissue-damaging effect.
Sometimes you have to focus not only on what the plants need but also on organisational or purely economic factors. For example, the cost of electricity. True, the lamps we manufacture and install in racks are highly energy-efficient: they convert every watt of electricity into 0.6 watts of photosynthetically active radiation (FAR). Still, energy costs make up a large portion of the costs of growing herbs indoors. Automation can (and should) be leveraged to ensure optimal load distribution. If the farm can use a night rate, we change “days” with “nights” and reschedule the supplemental lighting for the nighttime to minimise operating costs.
3. Nutrition: irrigation and nutrient solution supply
The nutrient solution is made from several components stored in individual containers which can easily be replaced. The solution is prepared in the mixing unit, a sophisticated automated system capable of mixing dozens of litres of stock solutions with high precision and in the right proportions.
The nutrient solution is delivered to the roots of the plants through a tube system. Since the specific recipe depends on the type of the plant and its cultivation stage, the system continuously monitors (and sometimes adjusts) the composition of the solution.
“Plants eat and plants drink. We provide them with both by mixing nutrition with water. This water continuously runs through the rack. To create an individual “menu” for each plant type, we divide the farm into different watering areas and install an additional storage tank in each of them. Each area is equipped with an additional set of sensors that dynamically monitor the changes in the solution. In fact, these sensors control whether the plant “ate well” today and whether they have everything they need.”
Alexey Novokreshchenko, Head of Automation at iFarm
The water used for preparing the solution is added to the system after it is properly treated with a reverse osmosis filter. This removes contaminants, such as minerals, heavy metals, bacteria and viruses, leaving the water virtually pure.
4. Well-being: IoT sensors
The purity of the source water, the ratio of nutrients in the solution, its acidity, the brightness of the light, the amount of carbon dioxide in the air, temperature, and humidity — you need to control all these things with precision. A large farm can have hundreds of sensors.
Based on sensor measurements, the farm's central processing unit controls the equipment and hardware in real-time, always keeping climatic and biochemical parameters within the limits set by the cultivation flow chart.
If these limits are exceeded, it triggers an alarm and remote technicians are alerted. The algorithm helps identify potential human errors, among other things. For example, it will immediately alert you if a technician incorrectly replaces the cans with the source materials for the solution.
“Plants can be extremely sensitive, some may “dislike” even a one-degree deviation from the usual temperature. We covered the racks with sensors and cameras so we could understand what a crop is sensitive to during cultivation. Now we’ve stabilised the process by defining the optimal number of devices to ensure accurate environment control.
Nikolai Podvigin, Head of the Agrolaboratory at iFarm
5. Analytics: computer processing of Big Data
The “head” of the system is a cloud server. It collates and computes data indirectly from the array of actual measurements collected. For example, it calculates the efficiency of air circulation across the farm based on the data from all of the climatic sensors. What’s even more important is the ability of Growtune, the farm management software platform, to process all of the Big Data collected on the farm.
“The algorithms we use to prepare nutrient solutions are based both on recipes and on the processing of collected data. The outcomes of plant nutrition in previous cycles affect future mixing. The controller monitors the plants’ reaction to “dinner” on the previous day and adjusts the solution accordingly. And, after reviewing the combined data from different farms, we gradually optimise the flow charts.”
Alexey Novokreshchenko, Head of Automation at iFarm
Farms are increasingly using machine vision in their “nervous system”. Images from the cameras installed on the racks are analysed by a neural network trained to determine if the plants are healthy. Technicians can also use this neural network by uploading a picture of plants through a chatbot to gain critical information about its health. Another neural network calculates the dynamics of herbage mass accumulation using the same stationary video cameras or drone cameras.
6. Movement: automation of tray movements
Problems usually dealt with by rare and expensive specialists, agronomists, biochemists, and phytopathologists can be solved using artificial intelligence, special equipment, or remote consultants. But, until recently, there hasn’t been a fully automatic farm where electronics also handle routine manual work, such as moving trays.
In February 2021, iFarm engineers implemented and tested a design prototype of a fully automated vertical farm. It features a conveyor belt that moves trays with pots through the planting, germination, growth, ripening, and cutting areas. The farm can also be equipped with individual robot modules for packaging products and preparing trays for the next cycle.
7. A human helping hand
As with any sophisticated modern equipment, an automated farm has special service message protocols. Naturally, these protocols are intended for a person, such as an employee of a certified service provider. Automatic warnings about errors, worn-out nodes, or the need for consumables to be replaced translate into assignments for replenishment or troubleshooting.
The reports of deviations in the growth of herbs are handled by an iFarm agronomist. The first thing this expert does is double-check that the actual conditions match the ones in the flow chart. They then go through a list of tasks almost identical to the sections of this article. So, what’s happening with the air, climate, energy, and nutrition of the plants on the farm? Do the sensors provide correct data? When suspecting a technical failure, the agronomist connects a service employee to the diagnostic interface with one click. They can also connect to the technician’s camera or AR glasses if the employee is already on site.
“We have several continuous operation circuits, millions of second-by-second measurements, sensors, robots, conveyors, drones, cameras, and neural networks. It seems we’ve automated almost everything we can. The only thing you can’t automate is the R&D process itself. This is why people in the company focus on this process. And this is exactly why we are fighting for strategic investments.”
The World’s First “High-Tech Eco Village” Will Reinvent Suburbs
A half-hour commute from Amsterdam, a piece of farmland is slated to become a new kind of neighborhood. Vertical farms, along with traditional fields and orchards surrounding homes, will supply food to people living there. Food waste will turn into fish feed for on-site aquaculture. Houses will filter rainwater, but won’t have driveways. A “village OS” tech platform will use AI to simultaneously manage systems for renewable energy, food production, water supply, and waste.
The 50-acre neighborhood, which will be nearly self-sufficient as it collects and stores water and energy, grows food, and processes much of its own waste, was initially planned for construction in 2017. The developers, called ReGen Villages, struggled with red tape–the area, on a piece of land that used to be underwater but was reclaimed in the 1960s when a seawall was constructed–has regulations that make it difficult for someone other than an individual homeowner to build on land that is mostly used for farming now. But after the project finally got government approval this month, it’s ready to take its next steps.
[Photo: ReGen Villages]
“We can connect a neighborhood the way it’s supposed to be connected, which is around natural resources,” says James Ehrlich, founder of ReGen Villages. If the project raises the final funding needed to begin construction, what is now a simple field will have new canals, wetlands, and ponds that can soak up stormwater (the area is seven meters below sea level, and at risk for flooding) and attract migrating birds. The land will be planted with trees, gardens, and food forests. Vertical gardens inside greenhouses will grow food on a small footprint. The 203 new homes, from tiny houses and row houses to larger villas, will provide needed housing in an area where the population may double in 15 years. The houses range in cost from 200,000 to 850,000 euros.
As cities become increasingly expensive and crowded, Ehrlich believes that this type of development may become more common. “In the last few years, we’ve really seen that the market has shifted and that there’s a hollowing out of cities,” he says. “They are really expensive and the quality of life is going down, and as much as millennials or younger people really want to be in the city, the fact is that they can’t really afford it . . . the trends are really moving toward this kind of neighborhood development outside of cities.”
[Photo: ReGen Villages]
There’s also a need to rethink infrastructure so it works more efficiently, with a lower environmental footprint. The new development considers everything–from electricity to sewage–as an interconnected system, and software links the pieces together. Electric cars, for example, which will be parked on the perimeter of the neighborhood to keep streets walkable, can store some of the extra power from the neighborhood’s solar panels and other renewable energy.
The neighborhood works differently than most. Because of the expected arrival of self-driving cars in coming years, and to encourage walking and biking, the houses aren’t designed with parking; a new bus line along the edge of the neighborhood, with a dedicated bus lane, can take residents to the town of Almere or into Amsterdam. (As in other parts of the Netherlands, separated bike paths also connect to the city.) Water will come primarily from rain collection. The on-site farming, including raising chicken and fish, will supply a large portion of the local food supply. If neighbors volunteer for the community–to garden, or teach a yoga class, or provide elder care, for example–the community will use a blockchain-based time bank to track their hours, and then provide a discount on their HOA fees.
[Photo: ReGen Villages]
A “living machine,” a system that uses plants and trees to filter sewage, and a separate anaerobic digester, can handle the neighborhood’s sewage and provide irrigation or water reused in energy systems. A system for processing food and animal waste will use black soldier flies and aquatic worms to digest the waste and create both chicken and fish feed. Other household waste–like cans and bottles–will be handled by the municipal recycling system, at least initially.
It’s a design that Ehrlich believes is feasible elsewhere, though it may not easily fit into existing regulations, and it would need political support. (Some other “agrihoods,” neighborhoods with built-in farming, do already exist, like Kuwili Lani in Hawaii, which also uses renewable energy and harvests some rainwater.)
“We know that governments around the world are in a desperate situation to build probably over a billion new homes around the world,” he says. “It’s a terrible housing crisis. At the same time, they wrestle with a number of things: the commercial interest of farmers, the commercial interests of traditional real estate developers, material companies who have a way of doing things that they’ve been doing for 100, 150 years. Most of the rules on the books relate to this district-scale thinking–of grid-based electricity, of district-scale water, of district-scale sewage.”
Financing is another challenge: While typical real estate developers look for large rates of return and quick exits, ReGen Villages plans to stay involved in its developments and get long-term, single-digit returns. The company is still raising the last round of money needed for the new development. Because Almere has regulations that don’t allow for high density, the initial development will also be more expensive. But once it’s built–something that Ehrlich expects to happen in 2019–others can follow more quickly. “We have access to a lot of really big money that’s waiting for us to finish the next pilot, and so we need the proof of concept,” he says.
The company has plans to build future developments near cities like Lund, Sweden, and Lejre-Hvalso, Denmark, and it ultimately hopes to bring a low-cost version of the neighborhoods to developing countries. “We can imagine going to rural India, sub-Saharan Africa, where we know the next 2 [billion] to 3 billion people are coming to the planet, and where we know that hundreds of millions of people are moving into the middle class,” he says. “And [we want] to get there as quickly as we can to provide new kinds of suburbs, new kinds of neighborhoods.”
Future of Farming Is Rooting Itself In Central Oregon
A sustainable, shipping container 'vertical farm'
By: Lauren Melink
July 26, 2018
Around the Bend Farms
BEND, Ore. - There’s a new farm in Central Oregon, and it’s a bit different from your standard homestead.
It’s called Around the Bend Farms. And for now, you’ll find it in a laboratory at OSU-Cascades.
Around the Bend Farms CEO, Ben Marsh describes it like this: "It's definitely not your archetypal farmer who is in a field, sweating in 95-degree weather with a big combine. Our combine is a computer or a micro-controller."
Around the Bend, Farms is a non-profit organization that’s partnered with OSU-Cascades to create a personal food computer.
"What that means is that the computer can tell this thing, 'OK, I need you to turn on a light.' And this thing goes 'All right,' and turns on a light," Marsh said.
The farm is a sustainable "vertical farm" that after being programmed with the correct grow recipe, runs on its own.
"We’re controlling the heating, the cooling, the air movement, the lighting, temperature," Marsh said
The goal is to eventually build computer-run, sustainable, vertical farms inside shipping containers.
Lance Porter is an energy systems engineering graduate involved in the project. He thinks the computer farm will attract a different type of farmer.
"The newer generations really want to be more involved in where their food comes from and especially involved in how it’s made and how it’s produced," Porter said
Executive research associate Makena Whitaker said this unique kind of farming will hopefully keep people coming back.
"It’s more fun if you make farming fun and interesting. People will stick around," Whitaker said.
Around the Bend Farms also hopes to create a sense of community around growing food.
"Food was always a family endeavor and a community-based endeavor, and we want to kind of get back to that," Marsh said.
Around the Bend, Farms is in its early stages of development, but already they’ve tripled the size of their crop and hope to have a shipping container farm in Bend within two years.
For more information on the farm, you can visit the website at this link: https://www.aroundthebendfarms.org/
South Korean Government To Create 4,300 Jobs In Smart Farm Industry
Government To Create 4,300 Jobs In Smart Farm Industry
Posted on April 17, 2018 by Korea Bizwire in Agriculture, Business, Industries, Top News
The agriculture ministry is hopeful that the move will help create more than 4,300 jobs over the next few years in the burgeoning smart farming industry. (Image: Yonhap)
SEOUL, April 17 (Korea Bizwire) — The South Korean government has announced plans to create 4,300 jobs in the smart agriculture industry by 2022.
The Ministry of Agriculture, Food and Rural Affairs revealed measures to attract young workers into smart farming by providing training courses and building large-scale smart farm complexes during a meeting with financial officials on Monday.
Smart farming brings information and communications technology to greenhouses and livestock farms and allows farmers to remotely control the growing environment of crops and animals through smartphones and computers.
The latest announcement focuses on creating innovation models, a shift from the previous plan to introduce smart farming at existing farms, under which young entrepreneurs and farmers will be trained and other related businesses will be supported.
Training courses will be available from next year and will last for 20 months, with plans to create 600 professionals by 2022.
In addition, young farmers who complete the courses will be given government subsidies to open a smart farming business on 30 hectares of land that will be allotted to them, while agricultural loans at lower interest rates will be available for both new and experienced farmers.
Plans to build a smart farm test site are also underway where research projects, exhibitions and tests will take place to help enhance the competitiveness of South Korean smart farms.
The South Korean government has announced plans to create 4,300 jobs in the smart agriculture industry by 2022. (Image: Ministry of Agriculture)
Through joint efforts between research institutes and companies, the government is poised to establish South Korea’s own Priva, a Dutch company that produces the world’s highest quality climate control systems.
A total of four smart farming innovation valleys will be built across the country by 2022, multi-purpose venues consisting of a training center, smart farms for rent, and a test site.
The agriculture ministry is hopeful that the move will help create more than 4,300 jobs over the next few years in the burgeoning smart farming industry.
Ashley Song (ashley@koreabizwire.com)