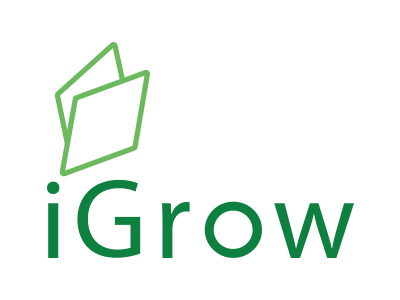
Welcome to iGrow News, Your Source for the World of Indoor Vertical Farming
CANADA: Bringing Local Greens To Ontario Year Round
The state-of-the-art farm is fully automated and equipped to grow microgreens and baby greens 365 days a year, without the use of pesticides, herbicides or fungicides and with dramatically less water consumption
NEWS PROVIDED BY
Sep 15, 2020
Vertical Farm In Guelph Is Now Fully Operational
GUELPH, ON, Sept. 15, 2020,/CNW/ - The revolutionary GoodLeaf Farms' 4,000-square-metre indoor vertical farm is now fully operational.
The state-of-the-art farm is fully automated and equipped to grow microgreens and baby greens 365 days a year, without the use of pesticides, herbicides, or fungicides and with dramatically less water consumption. The result is a safer, more nutrient-dense, and sustainably grown food source, providing a domestic alternative in a produce aisle highly dominated by imports from the southern United States or Mexico.
"Knowing where their food comes from is important to Canadians," says Jacquie Needham, Accounts Manager for GoodLeaf Farms. "Our growing system mimics the spring sun without the use of chemicals, releasing farming from the restrictions of the changing seasons. We can grow local, fresh, nutritious, and healthy leafy greens for the Ontario produce market all year long — we do it safely."
Vertical farming is an innovative growing process that naturally grows plants with hydroponics under specialized LEDs that concentrates the waves from the light spectrum that plants need to maximize photosynthesis. This method of farming is cost-effective, uniquely suited for Canadian climate, and scalable. GoodLeaf Farms is a leader in food safety. Every crop is tested for contaminants before it is shipped, ensuring it is safe for consumers.
GoodLeaf Farms is also sustainable. It uses 95 percent less water than a traditional farm, has no run-off issues or potential contamination of nearby water sources, it is local which eliminates thousands of kilometers of transportation from the supply chain and more food can be grown per acre, reducing land-use pressures.
GoodLeaf currently has four microgreens and two baby greens available in Ontario:
Spicy Mustard Medley — Blend of Asian greens create a spicy touch reminiscent of Wasabi or Dijon Mustard. It makes for a perfect peppery finish.
Pea Shoots — Sweet and crisp with a subtle pea flavour, they add a fresh bite to salads, seafood, and summer rolls.
Micro Asian Blend — Mild peppery flavour with a hint of mustard, this makes a great addition to stir fry, soups, or as a crunchy culinary adventure to any dish.
Micro Arugula — Intense spicy flavour that is both peppery and nutty. Use this to elevate the look and flavour of any meat or seafood dish, as an addition to your salad or to garnish your sandwich.
Baby Kale — Earthy and nutty, it is a calcium-rich dark green to add a nutritional punch to any salad.
Baby Arugula — Excite your taste buds by adding this spicy and peppery green to your salad or as a topping for sandwiches or burgers.
"The pandemic has underscored how important it is to have access to local food sources – food that we know is safe, grown responsibly, and immune to border closures," says Ms. Needham. "Compared to a green that was grown thousands of miles away, packed onto a hot truck and shipped across the continent, our process is far superior. Local food is simply better — better for you, better for the environment and better for our economy."
Follow GoodLeaf Farms on Instagram at @goodleaffarms and like it on Facebook at /GoodLeafFarms.
About GoodLeaf Farms:
With a passion for delicious, nutrient-rich greens, GoodLeaf was founded in Halifax in 2011. Using an innovative technology and leveraging multi-level vertical farming, GoodLeaf has created a controlled and efficient indoor farm that can grow fresh produce anywhere in the world, 365 days of the year. The system combines innovations in LED lighting with leading-edge hydroponic techniques to produce sustainable, safe, pesticide-free, nutrient-dense leafy greens. GoodLeaf has ongoing R&D Programs in collaboration with the University of Guelph, Dalhousie University, and Acadia University.
Learn more at goodleaffarms.com.
SOURCE GoodLeaf Farms
For further information: Jacquie Needham, Accounts Manager at GoodLeaf Farms, jneedham@goodleaffarms.com, 416-579-6117
Netled Partners Up With Agritech Start-Up Vertigo Farms – A Focus On New Kinds of Vertical Farming Applications
Vertigo Farms is the first publicly known European actor to produce natural extracts from plants grown indoors. Mainly herbs are grown and processed in a sustainable manner with no use of chemicals, all-year-round, regardless of weather conditions
26th August 2020 by johannak
Netled and a Polish agritech start-up Vertigo Farms have announced a new technology partnership. Vertigo Farms will use Netled’s Vera® vertical farming technology in its indoor growing projects. The collaboration has already started, and the goal is to have the first plants growing at the beginning of 2021.
Vertigo Farms is the first publicly known European actor to produce natural extracts from plants grown indoors. Mainly herbs are grown and processed in a sustainable manner with no use of chemicals, all-year-round, regardless of weather conditions.
“At Vertigo Farms, we believe that vertical farming serves the future not only for direct consumption purposes, but it may also serve as base for highest quality natural extracts for food, cosmetics and pharma industries”, comments Dawid Drzewiecki, the CEO of Vertigo Farms.
The company works with research laboratories and universities to develop methods for optimal conditions and nutrition of plants to boost their growth. Each type of plant requires a different approach. For start, the company will experiment with Safflower, Lovage, and Opium poppy, but there will be more species along the way.
Niko Kivioja, CEO of Netled, comments the newly formed partnership: “Vertigo Farms has a very interesting approach to produce natural extracts. Netled is proud to be Vertigo’s technology partner. In addition to this, our crop specialist team is especially excited to have insight into the new, more exotic plants growing in a vertical farming environment. Globally, we see massive opportunities to produce crops which have very high-quality standards in vertical farms, alongside the more common leafy greens.”
The mission of Vertigo Farms is to process and deliver the highest quality natural ingredients with the use of state-of-the-art solutions. Thus, the goal is a great fit with Netled, as the company aims to provide the best technology, expertise, and guidance for vertical farming projects and actors all around the globe.
Read more about Netled’s Vera® Vertical Farm: https://netled.fi/vertical-farming-vera/
Read more about Vertigo Farms: http://vertigofarms.eu/
Facebook Twitter LinkedIn Share
Filed Under: NewsTagged With: indoor farming, indoor farming technology, indoor growing, sustainable growing, vertical farm, vertical farming, vertical farming expertise, vertical farming technique, vertical farming technology
“We Are Developing A Sustainable Technology That Uses 75% Less LED Lighting”
Verde Compacto, a Mexican start-up, producer of container farms and indoor farming growing technologies, has seen significant demand for their growing systems during the pandemic
Verde Compacto, a Mexican start-up, producer of container farms and indoor farming growing technologies, has seen significant demand for their growing systems during the pandemic.
"COVID is driving this market forward because people want to know what is behind their food and their diets. Logistic chains in countries like South Korea and Arab countries are really dependent on imports. They are trying to implement urban technologies to strengthen their supply chains. As we’re focusing on growing systems, we are trying to turn this into reality. We are growing food in a more sustainable way where everyone can benefit from it”, Juan Gabriel Succar, Co-Founder and CCO of Verde Compacto says.
The company has an R&D container farm, Huvster, with several labs and small scale systems. The company sells some of its crops locally to better understand the urban business model, as Verde Compacto is educating the future indoor growers.
The Huvster growing container
Succar continues: “We are providing the knowledge to any grower that wants to have an urban farm and we are helping them throughout the process by constructing a farm to their needs.” The company does not only build container farms, which is their standard model but also provides custom made projects such as warehouses or buildings. Or on a smaller scale like supermarkets and restaurants. “We provide the knowledge to install a farm at any size”.
Decreasing LED use
Verde Compacto is looking to improve the electricity use for its growing solutions. “We are developing a sustainable technology that uses 75% less LED lighting, which is part of a sustainable R&D project. The tests are still running but they have delivered positive results. In the end, our technology used for indoor farms allows us to rotate the lamps. Rather than using four lamps at one spot, Verde Compacto can use one light that is constantly rotating. That's why we can make such a big impact on light usage”, Succar affirms.
Lack of quality and water
“Every business model and location has different benefits. As we are one of the largest agricultural countries in the world, we can offer excellent fresh produce quality. The sad story is that all the good fruits and vegetables are exported, thus there is a lack of quality products here in Mexico”, Succar says.
Succar says that Verde Compacto’s technology can build a profitable business model to deliver excellent quality and healthy food to the Mexican society. He notes that the central Mexican region sees a big challenge: a large water shortage. “With our solution, companies still see an opportunity to grow food and maintain their quality by using fewer resources”, Succar notes.
Sustainability
“We always try to give the best options possible regarding our client’s budget, business model, and capabilities. Verde Compacto is cooperating with solar panels to give access to clients for installing these solutions. “Renewable energy, in the end, really depends on the client. Our goal is to make vertical farming as sustainable as we can”, Succar states. At the end of October this year the company will install the first urban farm in Salamanca, Mexico which will be run on 100% solar energy.
Price opportunities
Succar: “In Mexico, we provide our produce at a lower price level than supermarkets. This is done on purpose, to get people to know about vertical farming. Sometimes we are on the same price level.”
Olivier Kappetein, EU representative at Verde Compacto notes: “We have a financial stimulator and we found out that we can bring product prices down. Consumers would pay less compared to supermarket prices as they are unbelievably high. In the United Arab Emirates, locally grown products are unfindable. An iceberg lettuce costs around €7.60 (9 USD) or more. We could get that price down by at least 350% and still make a profit if we were to sell our produce there. We are aiming to sell high-quality food and that’s what they are looking for.”
Pre- and post COVID story
Verde Compacto has a pre- COVID story and a post-COVID story regarding any company expansions. The pre-COVID story was to expand to all Latin American countries, as a priority. They started several alliances and promoted the Verde Compacto technology in Latin America. However, the economy in Latin America was really affected during the pandemic.
“Thus, countries depending on imports saw a great opportunity in our technology for constant production. We didn’t get behind on the expansion actually. Right now, we are working with associations to open different commercial offices in several countries in Latin America. We will be expanding there at the beginning of next year. We are also exploring different options in different parts of the world, expanding globally. One of the regions is Northern Europe because we saw the need for farming technology in those countries. Especially in Luxemburg, where there’s limited fresh produce available.
“The most common problem in vertical farming is the unawareness of the consumer”, Kappetein adds. “They don’t know what it has to offer. It’s still an investment that needs to be made. There is still a greater focus on organic produce as they are aware of the great benefits that come along.”
The Verde Compacto team
Forage
Verde Compacto has been developing its own R&D department, generating knowledge that is also used for new product lines. Succar continues: “We are developing indoor farming systems that are not limited to leafy greens and herbs, but also for forage e.g.. Forage is eaten by grazing cattle mostly. With our hydro system, we can feed cows e.g. with using fewer resources in a more profitable way. The meat and milk industry is impacting the ecosystem significantly. Implementing this technology will help us to make this type of agriculture more sustainable.” The company is also exploring the opportunities of launching indoor strawberries, with the greatest focus on Europe.
For more information:
Verde Compacto
Juan Gabriel Succar, Co-founder, and CCO
juan.gabriel@verdecompacto.com
Olivier Kappetein, EU representative
olivier.kappetein@verdecompacto.com
Phone: +316 14 62 13 10.
www.verdecompacto.com
Publication date: Tue 8 Sep 2020
Author: Rebekka Boekhout
© HortiDaily.com
Nature Fresh Farms Releases NEW 100% Home Compostable Cucumber Wrap
An alternative to traditional polyethylene plastic, this film is an environmentally friendly compostable wrap that breaks down in a household compost without leaving behind microplastics
Leamington, ON (September 8, 2020) – Nature Fresh Farms continue their sustainable initiatives by releasing a new, 100% home compostable wrap for their Long English Cucumbers, a first in the North American market.
An alternative to traditional polyethylene plastic, this film is an environmentally friendly compostable wrap that breaks down in a household compost without leaving behind microplastics. The compostable film will prolong the shelf life of the product; however, it will do so without adding to long term landfill waste. Made from a starch-based PLA that is derived from plant-based resources including non-GMO corn starch, it is 100% compostable, breaking down naturally into CO2 and water.
Each cucumber wrap contains 0.00436 lbs of plastic; this translates to the equivalent of 23-million plastic straws saved from landfills for every 5-million Cucumbers wrapped in the compostable film. Cucumbers are packed in shrink wrap to significantly extend their life by minimizing evaporation. Through the compostable film, Nature Fresh Farms has found a packaging solution that can maintain the shelf life of the Cucumber, while meeting the demands of more sustainable packaging alternatives.
“The launch of the compostable wrap is a demonstration of our commitment to our consumer’s wants of reducing plastic usage. We are excited to be first to market with this initiative in North American and are hopeful this will start a trend with the industry while we continue to lead in sustainable packaging solutions.”
--Matt Quiring, Director of Sales
In addition, the wrap includes a PLU pre-printed on the film in compostable ink. This feature allows the entire wrap to be thrown in with backyard compost or in landfills without harming the environment. PLU stickers are commonly made of vinyl and plastic. This new wrap eliminates the need for the additional application.
“After two years of research & development and a lot of trial & error, it’s so exciting to see this film launch in the market. We are confident in this product’s ability to make a true difference
(in reducing harmful plastic waste)”
---Luci Faas, Product Development Specialist
At Nature Fresh Farms we are driven to accelerate innovation via evidence-informed sustainable packaging solutions that provide a better experience for our customers, while also helping to preserve the vitality of our planet.
-30-
About Nature Fresh Farms -
Continuously expanding, Nature Fresh Farms has become one of the largest independent, vertically integrated greenhouse vegetable farms in North America. As a year-round grower with farms in Leamington ON, Delta OH, and Mexico, Nature Fresh Farms prides itself on consistently delivering exceptional flavor and quality to key retailers throughout North America, while continuing to innovate and introduce more viable and sustainable growing and packaging solutions.
SOURCE: Nature Fresh Farms | info@naturefresh.ca T: 519 326 1111 | www.naturefresh.ca
LIVE Virtual Tour - Inside the Greenery Container Farm with Freight Farms' Lead Designer - Thurs, Sept 10, 2020 - 4:30 PM EST
Explore the technology behind our Greenery container farm that allows farmers to grow food anywhere in the world!
Take a Virtual Tour of the Freight Farms Greenery™
Explore the technology behind our Greenery container farm that allows farmers to grow food anywhere in the world!
Farm expert Derek will explain the ins and outs of the Greenery using a live video stream inside the farm. He’ll cover the basics of controlled environment agriculture, hydroponics, vertical farming, and how all those work together inside the Greenery to create the perfect conditions for crop growth regardless of geographic location.
To Register For This Free Zoom Virtual Live Tour
Thursday, September 10, 2020 - 4:30 PM
Urban Vertical Farming: The Key To A Sustainable Future
By 2050, the forecast is that we will have an extra 2 billion people on the planet. Many of these people will live in urban areas. And we have already used a third of arable farmland in the past 40 years
Living in a dense city population can make you wonder, "where does our food come from?" When you live in urban areas like Houston, New York City, or Seattle, it's rare that you notice farms on your drive to work.
The idea that our food is grown hundreds to thousands of miles away can be worrisome. What if something were to happen to those farms? Our resources would cut off and we would have limited access to foods. This is why vertical farming in urban areas is critical to ensure cities can be sustainable food leaders.
What is vertical farming?
Vertical farming is the practice of growing crops/foods in vertically stacked layers. This is usually done indoors and in a controlled environment. This method optimizes plant growth and allows the use of soilless techniques such as hydroponics.
How does vertical farming work?
Vertical farming needs several things to work. We'll cover each one below:
Physical Layout - The purpose of farming indoors is to maximize volume. We do this by maximizing the output efficiency per square meter. This is why you will see physical layouts in the form of skyscrapers or vertical tower-like structures.
Lighting - To optimize crop growth, a need for artificial and natural lights are essential.
Growing Medium - There are several different growing mediums for vertical farming. These methods include hydroponics, aeroponics, and aquaponics. Coco Coir, Rockwool, ,Biostrate, Vericulite, Perlite, SunShine #4 and Black Gold are great mediums used in indoor farming.
Sustainability Features - Sustainable features often used with vertical farming feature rainwater tanks, wind turbines, and spaces with low energy costs.
Why is urban vertical farming important?
By 2050, the forecast is that we will have an extra 2 billion people on the planet. Many of these people will live in urban areas. And we have already used a third of arable farmland in the past 40 years.
We need to come up with other sustainable ways to grow food to ensure we can feed everyone. Vertical farming allows us to grow healthy, accessible foods within a few acres of land, close to home.
This is critical for urban areas because they will become more populated over time. Instead of relying on faraway food sources, we need to take matters into our own hands. By establishing urban vertical farming settings, we'll be able to control and grow our own food sources.
Vertical farming also uses 95% less water than traditional farming methods. The use of water needed to grow crops traditionally is wasteful. To be able to handle an influx in population, vertical farming is a sustainable solution.
How does vertical farming benefit us?
There are many reasons why vertical farming is the future of farming. By building vertical farms, there will be an increase in job opportunities. There will be easier access to healthier and attainable foods. With food grown close to home, we will always be aware of where our food comes from.
Because of the controlled environment, there is a higher chance of growth success. We will be able to grow crops year-round and have larger yields. Crops will not be exposed to harsh weather conditions since they'll be grown indoors. Urban vertical farming methods should start being adopted right now.
The Takeaway
To prepare for the upcoming increase in food demand, urban areas need to adopt sustainable policies. People should start growing their food indoors as well as increasing the demand for high-tech farming methods.
What Are The Pros And Cons of Hydroponics?
Hydroponics is a type of aquaculture that uses nutrients and water to grow plants without soil. It is an increasingly popular growing method in urban areas and regions with extreme climates
AUGUST 28, 2020
Hydroponics is a type of aquaculture that uses nutrients and water to grow plants without soil. It is an increasingly popular growing method in urban areas and regions with extreme climates. There are many benefits to hydroponics as an alternative form of agriculture, including fewer chemicals, higher yields and greater water efficiency.
However, hydroponics is not a perfect solution. The initial setup is expensive, and the whole growing system is heavily dependent on access to electricity and a clean water source. Here are just a few pros and cons of hydroponics.
Pros
The benefits of hydroponics are myriad and include:
1. More Water Efficient
Growing plants can require a lot of water, and conventional agriculture is historically wasteful of this resource. For example, a single walnut requires almost 5 gallons of water, and an orange uses nearly 14 gallons. Globally, over 70% of freshwater is used for agriculture.
Compared to traditional growing methods, hydroponic systems are much more water-efficient. Growing in a climate-controlled environment allows cultivators to use the exact amount of water required for healthy plants, without any waste. Overall, hydroponics utilizes 10 times less water than conventional agriculture.
2. Higher Yields
Since crops are grown in a climate-controlled environment, hydroponic farmers are not limited by extreme weather or annual rainfall, resulting in higher crop yields. There’s more control over the setup of the system, and crops aren’t limited to a specific growing season.
Additionally, when comparing vegetables grown in soil, hydroponics can sometimes grow plants at up to 16 times higher density. Hydroponics allows growers to do this without using significantly more nutrients or other inputs.
3. Less Space
Some crops require a lot of space, and many conventional forms of agriculture are inefficient when it comes to using land. For example, row crops like soybeans and corn take up most of the arable land in the United States, but the harvest is used mostly for livestock and processed food, not human consumption.
In contrast, hydroponic systems focus on cultivating fruits and vegetables, providing nutrient-dense food for consumers without taking up significant amounts of space. Additionally, researchers at NASA are studying how to incorporate hydroponic systems for longer-duration space missions by providing the right balance of light, carbon dioxide, and water.
4. Community Resilience
Many cities have significant food deserts, and access to quality and affordable items is significantly limited. Urban hydroponic systems enable communities to cultivate their own crops, increasing food security for vulnerable populations.
While hydroponics requires significant operational costs, there is also some proof that it may be a possible solution for countries that struggle with food insecurity or need back-up options during months of extreme drought.
For example, in the United States, many agricultural enterprises grow food in one region but ship it to another for consumption. Many rural communities struggle with access to healthy produce because of this. Hydroponics may help foster community resilience by setting up an accessible system.
5. Fewer Chemicals
Many advocates of hydroponic systems stress that hydroponics reduces the need for synthetic chemicals. Since plants are most often grown in greenhouses with strictly controlled environmental inputs, pest pressure is almost nonexistent. Considering the detrimental impact of pesticides on the environment, using fewer chemicals is a huge advantage for hydroponics compared to traditional growing systems.
However, there is an ongoing debate regarding how to qualify hydroponic crops, and whether they are eligible for organic certification. According to the USDA, this refers to the care and maintenance of soil without chemicals. Since hydroponics do not use earth, many traditional organic growers feel that they are not eligible. Regardless of how crops are labeled, the fact that hydroponics uses fewer chemicals is a definitive advantage compared to conventional agriculture.
Cons
Despite the many positives, hydroponics also has some challenges to overcome.
1. Technology Reliance
Hydroponics is a high-tech process. Most commercial operations utilize specialized equipment that regulates water temperature, as well as acidity and nutrient density. Because plants are cultivated in a completely climate-controlled environment, there is a significant reliance on technology. Hydroponics is considerably more high-tech than other growing methods, and there is an opportunity in agtech to improve yields and decrease inputs. However, the amount of tech also makes it cost-prohibitive for beginning growers.
2. Initial Investment
The hydroponics market is expected to grow from $9 billion to $16 billion in the next five years, so there is certainly an opportunity for investors to consider vertical farming as a viable operation. In traditional agriculture, is it hard for new and beginning farmers to get started, as many face difficulties with land access and infrastructure investments.
However, getting into hydroponics is not necessarily any easier or cheaper. Despite a growing market, the initial investment in hydroponic systems is steep, especially on a commercial scale. For this reason, many of the largest growers are established agriculture corporations that already have capital in place. The initial investment limits profitable hydroponic operations to a few large farms, making it tricky for smaller growers to enter the market.
3. Organic Debate
As mentioned above, there is an ongoing debate in the farming community about whether hydroponic produce can be labeled organic according to USDA standards. Without a clear definition of the nutrient profile of hydroponics, nor stringent guidelines on which fertilizers or chemicals are permissible, many consumers remain cautious about hydroponic produce. This affects the industry’s success, as many consumers don’t know how crops are grown or what’s added to the water.
Without a clear definition from the USDA, there remains some question over self-labeling of hydroponic crops as organic when synthetic chemicals may still be added.
4. Equipment Requirements
While a home gardener can easily utilize some plastic bottles and storage containers to build a small hydroponic system, commercial farmers have significant equipment requirements. In addition to the initial costs of setup for infrastructure, there are also necessary and costly machines to consider. Pumps, tanks, and other controls can be expensive, not to mention electricity and access to filtered water.
5. Waterborne Diseases
While hydroponic systems may reduce or eliminate pest pressure, certain waterborne diseases are more prevalent in hydroponically grown produce. The most common ones affect the plant’s root structure, such as Pythium, which includes several water mold species.
Proper hygiene and cleaning practices can reduce the risk of plant disease, but it is often impossible to avoid completely. Because of this likelihood, many hydroponic growers incorporate bio fungicides to prevent breakouts.
Soil-Free Growing
Hydroponic growing can increase crop yields while reducing water usage. The benefits of hydroponics are significant, and the industry is expected to grow astronomically in the next five years. However, there are also some disadvantages to growing hydroponically. Improving access to infrastructure and making technology more accessible will enable more beginning growers to enter the market.
Swegreen Vertical Farm Goes In-Store in Gothenburg, Sweden
Swegreen's first automated farming unit takes place at ICA Focus in Gothenburg
Swegreen's first automated farming unit takes place at ICA Focus in Gothenburg
Swegreen inks contract with ICA Focus in Gothenburg, to become the exclusive producer of hyper-locally grown vegetables via an automated cultivation system inside the store itself. The agreement is based on Swegreen's subscription-based Farming-as-a-Service, which gives food retailers and restaurants the opportunity to offer their customers fresh crops all year round – harvested directly on-site or in-store.
From left: Andreas Dahlin, CEO at Swegreen. Elsa Adlersson, ICA Focus' responsible for the In-Store greenhouse. Marcus Petersson, chairman at Swegreen.
The contract between Swegreen and ICA Focus concludes that the Gothenburg-based store will be the first in Sweden to offer its customers hyper-locally produced greens grown from seed to fully-grown size inside a store itself. The cultivation facility, which is provided by the Swedish startup company Swegreen, is based on so-called hydroponic cultivation technology that is both resource-efficient and climate-smart. The technical solution also includes the company's special lighting and nutrient recipe, air conditioning system for control of heat, humidity, and CO2 content plus a complete digital monitoring – as well as a data-driven intelligent system for optimization of all cultivation processes.
Through Swegreen's subscription-based business model, Farming-as-a-Service (FaaS), the cooperation between the parties is based on a long-term commitment where Swegreen ensures efficient production at agreed volumes and quality.
- Our FaaS model means that every store and restaurant owner can offer hyper-local, fresh and high-quality crops that are fantastically nutritious and tasty – at very competitive prices, says Swegreen's CEO, Andreas Dahlin.
- We are very proud and happy to start this collaboration with ICA Focus. It is a store that has the will to be at the forefront, and we think there are going to be many who desire to follow their footsteps.
ICA Focus is located in the Gårda district in central Gothenburg, just a stone’s throw away from the famous amusement park, Liseberg, and the Swedish Exhibition and WTC. A flagship store that always has a large assortment of environmental-friendly products.
- Our customers have demanded more locally produced and sustainable greens in our assortment – and it will not be more local and greener than this! Says Daniel Åkerhage, Store Manager at ICA Focus.
- Now we look forward to our first on-site harvest, which we expect to take place later this month.
At full capacity, it is possible to deliver and harvest around 300 units of fresh salad heads and herbs per day in the cultivation facility in the ICA Focus store.
With hydroponic cultivation technology, where the crops grow without soil with lighting from special LED lamps, it is possible to grow vegetables in an urban environment – and thus produce food very close to the consumer. It also removes unnecessary, expensive, and climate-damaging transportations. In addition, the crops do not need to be sprayed by pesticides or herbicides – they are ready to be eaten directly off the growing system. Up to 95% of the irrigation water is reused via the recycling system. Nutrients are also recycled, while the plants receive carbon dioxide through a filtered air intake from the store itself.
Swegreen has developed the cultivation module to be able to create integrated plant environments together with partners in the food and restaurant sector. Therefore, Swegreen has developed a cloud-based control- and monitoring system to make production easy to manage. Through data collection of current factors in the cultivation environment, the system can continuously refine and further optimize the cultivation processes by the use of artificial intelligence.
For more information contact:
Andreas Dahlin, CEO of Swegreen, +46 70-924 00 32, andreas.dahlin@swegreen.se
Daniel Åkerhage, store manager ICA Focus, +46 76-117 16 20, daniel@icafocus.se
Swegreen is a Swedish FoodTech company that combines advanced technology, data science, and agricultural knowledge to be able to efficiently produce high-quality and climate-smart crops in an urban environment. The company offers a subscription-based cultivation service called Farming-as-a-Service (FaaS). It gives food retailers and restaurants the opportunity to offer their customers hyper-locally produced, fresh, nutritious, and tasty greens all year round. www.swegreen.com
ICA Focus is a unique grocery store that has been a rendezvous place for food-loving Gothenburgers for over 25 years. With an assortment of over 35,000 items, you have about twice as much to choose from as in an ordinary ICA store. ICA Focus also has its own bakery, charcuterie and restaurant. The store also has one of Gothenburg's best fish delicate retailers, Fisk i Focus. ICA Focus is located in Focushuset, Gårda, in central Gothenburg.
Publix Grows Hydroponic Produce At Greenwise Store
Publix has partnered with local hydroponics firm Brick Street Farms to grow, pack and harvest hydroponic lettuce in a container farm located outside its Lakeland, Florida Greenwise Market store
Krishna Thakker@krishna_thakker
Aug. 3, 2020
Dive Brief:
Publix has partnered with local hydroponics firm Brick Street Farms to grow, pack and harvest hydroponic lettuce in a container farm located outside its Lakeland, Florida Greenwise Market store.
The 40-foot container farm will grow an equivalent of 2.5 to 3 acres of lettuce and can operate 365 days a year in any weather conditions, Brick Street Farms told Grocery Dive in an emailed announcement. It substitutes soil for mineral-rich water, which means no pesticides are needed. The container farm uses 90% less water than a traditional farm and produces 720 heads of lettuce each week.
Customers can watch the produce grow through a window on the side of the container and purchase heads of lettuce inside the store.
Explore how the current landscape is impacting coffee manufacturers and how organic and fair trade can help ensure long-term success of the industry.
Dive Insight:
Publix has recently stepped up its partnerships in alternative agriculture. Earlier this year, the company began hosting Vertical Roots' interactive mobile hydroponic farm in the parking lots of its grocery stores and Greenwise locations. In March, Publix began selling microgreens from Kalera, a hydroponic farm on top of a Marriott hotel that lost all its business due to coronavirus, at 165 stores.
Hydroponic farming has been plagued by inefficiencies and high costs in the past, but improvements in technology are helping suppliers better meet retailers' demands for pricing and scale. On-site farms also add a bit of theater that can draw curious shoppers to stores.
Publix isn’t the only food retailer exploring this field. Kroger last year installed mini hydroponic farms in a handful of Seattle stores in partnership with Infarm, a start-up based in Germany. Around the same time, Gordon Food Service and indoor farming startup Square Roots opened their first co-located hydroponics farm on Gordon’s headquarters in Wyoming, Michigan. H-E-B and Whole Foods have also experimented with hydroponics in and around their stores.
Having a hydroponic farm at the store removes the need for transportation and storage of lettuce before it hits shelves, according to Brick Street Farms. It also allows Publix to sell the produce in-season all year round, providing some supply stability.
Although omnichannel business is booming for grocers like Publix right now, many are looking for ways to drive traffic to their stores, where they can make the most money per order. Grow farms and other safe, eye-catching attractions could be one way to accomplish this.
Follow Krishna Thakker on Twitter
Lead Photo: Permission granted by Publix
Filed Under: Fresh food Natural/organic
Seeding The Supply Chain
Grocery stores on the cutting edge of providing local produce are nurturing on-site growing spaces to answer consumer demand for locally grown produce. Retailers involved in growing their own hyperlocal produce see benefits
By : Retail Environments Staff
On-site growth of produce benefits enterprising grocers
By Annemarie Mannion
For this Avril store in Laval, Quebec, Canada, on-site growth of produce grew out of a government project that, among other things, sought to find a way to get food to people in northern areas besides having it all shipped by plane. The store’s automated vertical agriculture platform, known as CultiGo, grows organic greens year-round.
Grocery stores on the cutting edge of providing local produce are nurturing on-site growing spaces to answer consumer demand for locally grown produce. Retailers involved in growing their own hyperlocal produce see benefits. They believe that converting cross-country or cross-region shipping miles to mere footsteps makes financial sense because it provides a better-tasting product and reduces shrinkage.
Stores featuring hyperlocal produce are rare, but they reflect a societal trend. According to research firm Packaged Facts, local food sales in the U.S. increased from $5 billion to $12 billion between 2008 and 2014. The study predicted that local food sales would rise to $20 billion in 2019.
Given the demand, Viraj Puri believes more grocery stores will take this approach to provide locally grown produce. Puri is CEO of urban agriculture company Gotham Greens, which operates a 20,000-sq.-ft. greenhouse on the roof of Whole Foods Market’s Gowanus location in Brooklyn, N.Y., U.S. Constructed in 2014, the greenhouse yields produce that is sold and distributed to the market downstairs and to other Whole Foods locations and local restaurants.
“Growing fresh produce in close proximity to city centers means that we can make it available to urban customers within hours of harvest instead of days,” Puri says. He believes grocery stores also benefit when they can provide produce that has superior taste, better shelf life, and fully traceable products.
The superior quality of the hyperlocal produce appeals to both the store and shoppers, agrees Glenn Behrman, founder of CEA Advisors. His company worked with the H-E-B-owned Central Market in Dallas to grow produce on-site in a converted 53-ft.-long shipping container. “It’s in the produce department and on sale 10 minutes after it’s been harvested,” Behrman notes, adding that customers appreciate that it wasn’t trucked over hundreds of miles to get to the store shelves.
The container at Central Market — dubbed a Growtainer — protects the crops from snow, rain, and excessive heat. A 13-ft.-long utility area protects the production area from outside contamination. The 40-ft.-long production area provides environmentally controlled vertical production space, designed for efficiency and food safety compliance, Behrman says. The technology features an ebb-and-flow irrigation system, a water monitoring and dosing system, and “Growracks” equipped with LED systems.
For grocers, on-site growth of produce can reduce shrinkage. “If it takes four days to sell a case of lettuce [produced outside of the store], that last head or two is going to get thrown in the garbage,” says Behrman. Another benefit is the ability to produce small quantities of unique gourmet items. “They can use seeds from France or grow basil with seeds from Italy,” Behrman says.
Behrman believes the most suitable retail stores for on-site produce growth are those in high-income markets where consumers are willing to spend more for fresh, hyperlocal produce.
Are Automated Indoor Growing Facilities The Future For Fresh Produce?
Can growing veg in urban units scale up to meet demand, or is vertical farming a cottage industry focussed on leafy greens? Interest in Controlled Environment Agriculture is increasing internationally. Agri-TechE bring together Controlled Environment Agriculture technologists, producers and investors to discuss the current landscape and promising developments
CEA-Lite is an online debate on precisely that question,
taking place on 10th Sept.
Agri-TechE bring together Controlled Environment Agriculture technologists, producers and investors to discuss the current landscape and promising developments
Can growing veg in urban units scale up to meet demand, or is vertical farming a cottage industry focussed on leafy greens? Interest in Controlled Environment Agriculture is increasing internationally. In the UK autonomous growing systems have attracted funding from the Government’s Transforming Food Production program and tens of millions are being invested in a new training and demonstration facility; but the industry still has many challenges.
Agri-TechE is hosting an event “CEA-lite”, which is discussing the drivers for innovation and investment with leading entrepreneurs, producers, and investors on 10th September 2020.
Are new business models emerging?
Dr Belinda Clarke, Director of Agri-TechE says new models of food production are gaining traction. “Year-round intensive cropping of high-value crops becomes economically viable if the technology can scale. The Transforming Food Production call focussed on big, inspirational projects and this will help de-risk the technology, particularly around automating the monitoring and harvesting, which are so problematic for open field production.”
Jock Richardson of Growpura agrees: “A lot of operators have some great technology but to grow bigger means a linear (or worse) growth in costs. Scale-up is vital but there are operational challenges of how we grow plants at scale and at low cost.”
Could scaled-up vertical farms create economic value in vacant retail units?
“I have seen repurposing of buildings for CEA but location remains vitally important”, says Investor Kiryon Skippen of Capital Agri International, “landlords of these buildings need to be realistic in their rent demands and preferably have a real interest in the vertical farming business and work with it, taking the longer term view.”
Jock has seen uplift in interest in localised crop production, but as their system requires cleanroom conditions, refitting an older building could be too costly. “We’ve been talking to major retailers and its clear there is real interest in the use of hydroponics (growing in water) to fulfil the demand for fresh produce but of course it has to be at a competitive cost and offer a reliable supply,” he says.
The company will announce funding for a large training and demonstration facility in the coming days, which may provide over 200 jobs and internships in the South East Midlands area. “A vibrant hydroponics industry is essential in the UK. On the licensing front there has been interest from a number of countries particularly in the UAE and Asia and also for non-food products which we are progressing keenly,” Jock continues.
Can the industry look beyond leafy greens?
This international interest is a trend David Farquar, of Intelligent Growth Solutions, has also seen. He says; “Interest from NW Europe, the Middle East, and SE Asia is increasing the diversity of the food grown under secure conditions to reflect local diets and cuisine; encouraging the CEA industry to look beyond leafy greens and salads. For example, we have seen more demand for roots and fruits over recent months and interest in re-localizing as much of the food supply chain as possible.”
Phytoponics has recently raised £0.5M to develop its next-generation deep-water culture modules that offer a sustainable more profitable alternative to hydroponics substrates, such as rock wool and coir, and the company has started a series of strawberry trials with Total Produce. CEO Andy Jones, says the funding environment is challenging but that investment is there for companies with the right solutions.
He continues: “For growers, costs remain the big issue and one of the biggest is labor. New approaches need to give growers an economic advantage by reducing those costs.”
Are we swapping a labor shortage for a skills shortage?
However Max McGavillray of Redfox Executive says Brexit, and then COVID-19, has resulted in a marked increase in protected cropping roles as the UK adapts to a new normal: “We’re seeing individuals with plenty of cash establishing vertical farms but with very little experience in agriculture and foods, so there’s a real need for those with growth expertise in controlled environment agriculture.”
CEA Lite is an online event being held
on 10th September 2020 15:00 – 17:00.
Register your interest at bit.ly/ATEeEvents
About Agri-TechE – www.agri-tech-e.co.uk
Agri-TechE is a business-focused membership organization that is supporting the growth of a vibrant agri-tech cluster of innovative farmers, food producers and processors, scientists, technologists, and entrepreneurs.
Agri-TechE brings together organizations and individuals that share a passion for improving the productivity, profitability, and sustainability of agriculture. It aims to help turn challenges into business opportunities and facilitate mutually beneficial collaboration.
Photos:
1 – Credit: Growpura / Caption: Growpura is set to create a hydroponic farm, training and demonstration facility in Bedford, UK
2 – Credit: IGS / Caption: IGS has seen more demand for root vegetables and fruits in recent months as vertically farmed crops diversify
3 – Credit: IGS / Caption: Phytoponics has recently won funding and is undertaking commercial trials of its deep-water hydroponics modules
Feeding The World With Controlled Environments
The fallout from increasing global temperatures, a worldwide pandemic, and political unrest is causing projection reductions for crop yields in some countries as much as 50% this year, and small-scale farmers are the most affected with crop net revenues falling by as much as 90% by 2100
This case study, written by Gene Giacomelli and Eric Roth for Agritecture, takes a look at how CEA has emerged as a viable, contemporary agricultural practice over the past 50 years. Here’s how it happened!
The fallout from increasing global temperatures, a worldwide pandemic, and political unrest is causing projection reductions for crop yields in some countries as much as 50% this year, and small-scale farmers are the most affected with crop net revenues falling by as much as 90% by 2100. The consumer preference for consistent, year-round availability of produce has expanded because of the Controlled Environment Agriculture (CEA) industry, even surviving the recession of 2008. “That indicates to me, that no matter what the next recession brings, CEA food production systems will be firmly entrenched in U.S. agriculture production practices,” says Gene Giacomelli, Professor of Biosystems Engineering and former Director of CEAC at The University of Arizona.
CEA has emerged as a viable, contemporary agricultural practice over the past 50 years. There have been dramatic improvements in efficiency metrics including overall crop yield per square unit and reduction of wastage due to disease, nutrient deficiency, or damage to the product. From Space to Antarctica; from rooftop greenhouses to rural farms worldwide, CEA has proven itself to be not only a complement to open field crop production, but in some instances, a competitive alternative (or in the case of Space and Antarctica the ONLY) approach. Today, more than 60% of all fresh tomatoes consumed in the U.S. are grown in controlled environments and that number approaches 100% during the North American winter. Here’s how it happened...
In the 1990s, the U.S. greenhouse production shifted from its infancy to a steady supplier of fresh produce. While greenhouses use the sun as their main source of light, they can also make use of supplemental lighting for additional growth. This advantage, along with the ability to control and protect the growing environment, encouraged large farming corporations to enter the space in the Northeast, Arizona, Colorado, California, and Texas. Environmental control enabled these early adopters to produce crops like tomatoes, cucumbers, and lettuces year-round. During the same time, small family farms were often adding greenhouses to complement their traditional open-field production.
During the next decade, the major suppliers of field-grown vegetables in Canada and Mexico also began focusing on greenhouse production. The 2000’s firmly established CEA vegetable production as a viable commercial growing method.
In the 2010’s, vertical farming became more mainstream when Dr. Dickson Despommier published the book, The Vertical Farm: Feeding the World in the 21st Century. Vertical farms are essentially plant factories, with multi-level grow systems in insulated buildings using only electrical light instead of sunlight for plant growth. Although there were most likely small scale vertical farms before it, Sky Greens in Singapore was the first vertical farm to begin large scale commercial operations in 2012. Vertical farming became more commercially viable largely because of the advancing technology of Light Emitting Diodes (LED). These distributed light sources are less energy-intensive than the industry standard high-intensity discharge lamps, but more importantly, allow growers to move lights closer to the crop without burning or overheating. This enabled business developers to stack hydroponic grow systems, producing significantly more greens in increasingly smaller spaces. Now confined urban areas where arable land is very limited, could become producers of locally-grown, fresh food.
Protected cultivation has been in America at some level for two centuries, but what technological advancements made feeding the world with controlled environments possible?
Plastics
Polymer plastics such as polyethylene began providing a low-cost, energy-efficient film covering for greenhouses. This lowered the financial barrier to entry by creating more affordable greenhouses, thereby allowing unestablished growers to gain experience with a much lower investment than traditional glass-covered greenhouses. The plastic films dropped the investment cost significantly, while the more rigid, molded plastics improved operational metrics like production capacity, labor efficiency, and biosecurity.
Molded plastics also provided light-weight,easily-sanitized crop handling with trays, pots/flats, and clamshells for the packaging, among other things. Molded plastics further created light-weight structural channels, containers and benches which supported the plant and its root zone within hydroponic nutrient delivery systems, and even provided transport systems for improved labor and logistics management. Fully outfitted climate-controlled CEA plastic film boxes provided lettuce and greens production for the International Space Station.
Microprocessors
The microprocessor with its accuracy, consistency, data storage and simultaneous interpretation of multiple types and number of sensors has allowed the grower to tend more to plant production and much less to environmental control. No longer must the grower walk the greenhouse each morning to adjust the ventilation openings based on a guess of the day to be sunny, rainy or cold. Sensors are available to determine critical environmental plant needs and to make precise responses to air temperature and humidity for VPD (vapor pressure deficit) which affects plant transpiration and photosynthesis; light intensity with quantum sensors to determine DLI (daily light integral) which is directly related to desired growth or production rates; and, pH and EC which affects plant nutrient availability. When all combined, the grower is provided an improved understanding of the plant response to its environment. All this can be obtained on request in real-time by cellphone or within a report upon early morning arrival of the grower to the greenhouse each day.
Even more valuable is the capability of the computer to save data and further process it into useful information, which directs better grower decisions. Expect additional sensor development and implementation in the future to provide higher quality information about the food products, such as its flavor, sweetness, or nutritional quality.
The automation of information, although critically important, may become second in importance to labor-saving automation. Labor is often a farm’s biggest expense and the agricultural talent pool is limited nearly everywhere, but a high-tech farm’s food safety and security are dramatically enhanced when human contact with the edible product is reduced or eliminated. Production system automation that removes the need for people to work in groups on production lines is becoming crucial within this new world of viral pandemics.
There are still many advancements to be made in CEA. Technologies and experiences were transferred from the established greenhouse industry and applied to the developing indoor vertical farming industry. From LED lighting ‘recipes’ to plant nutrition under those recipes; from materials handling and logistics to labor management, years of R&D are required to reach optimal solutions for the plethora of combinations of plant cultivars, stages of growth, and harvest expectations within each type of CEA system.
The challenges remain for educating the people managing and operating the controlled environments. Educated employees working within a production process that is logistically sound, labor efficient, and task friendly are critical considerations for successful CEA businesses. Even with automation, the required work of skilled employees will remain, but at a higher educational level and a lower quantity.
In the future, it’s entirely possible that a CEA system will be able to autonomously program itself, or modify the plant environment without being directed, but for now, the plant production experience of an educated grower or crop manager is still required even in the most high-tech operations. Additional developments for successful CEA businesses include breeding of plant cultivars optimized for CEA production; emphasizing the importance of marketing; valuing employee education and experience; accepting that growing plants is a skill and an art; and, understanding basic physical principles that follow the laws of physics and biology!
CEA is still in such an early stage of commercial viability, but the blueprints for successful ventures continue to be created by intelligent and increasingly well-equipped entrepreneurs. As we look at the timeline of its commercial origins, to the critical technologies that made it work, we can see how far it's come, but also the potential the future holds for feeding the world with controlled environments.
Have you participated in the 2020 Global CEA Census? Autogrow and Agritecture Consulting have launched their 2nd Annual Global CEA Census, focusing on understanding the impact of the COVID-19 pandemic on controlled environment agriculture (CEA) operations around the world. The 2020 Global Census runs from July 7th to August 10th. Those who complete the census are entered to win different prizes from Agritecture and Autogrow.
Publication date: Fri 24 Jul 2020
New Growcer Hydroponic System Will Allow Sheshegwaning to grow Fresh Produce For Residents At Any Time of The Year
It may only be a sea container at this time, but soon Sheshegwaning First Nation (on Manitoulin Island in Ontario, Canada) will be able to grow fresh produce on a year-round basis in this unit and build food security for the community
By Tom Sasvari
July 3, 2020
New Growcer hydroponic system will allow Sheshegwaning to grow fresh produce for residents at any time of the year
SHESHEGWANING – It may only be a sea container at this time, but soon Sheshegwaning First Nation will be able to grow fresh produce on a year-round basis in this unit and build food security for the community.
“We took delivery of the Growcer self-contained hydroponic system,” stated Sheshegwaning Chief Dean Roy last Thursday. “With this project, we will be able to provide some food security as we will be able to produce fresh produce and food year-round here. With COVID-19 there have been times we haven’t been able to get fresh produce as readily as we want from neighboring grocery stores.”
He pointed out, “Growcer is a self-contained modular hydroponic system. We just have to hook up services for hydro and water and will have a representative of Growcer on hand soon to provide training on how to use the system to grow the produce here locally.”
“We should be able to produce 500 heads of fresh produce such as different lettuce weekly, year-round,” said Chief Roy. “I think we will be starting with romaine lettuce and other leaf lettuces, red kale, basil and parsley and we will be able to grow strawberries, for example, in the winter with this system.”
“We took delivery of a sea container last week for the Growcer system,” said April Folz, economic development officer for Sheshegwaning, this past Monday. “The week of July 13 Growcer company representatives will be on hand to provide training. After that, we will be up and running.”
Ms. Folz explained, “we’re going to be growing green products such as romaine lettuce, spinach, bok choy, basil, mint, and dill. And once we get going we will want to get into growing other different greens and produce.” She noted, “we were having a hard time getting fresh greens in local stores, but with this system in place, this will be available at all times. Local residents won’t have to travel to the nearest grocery store.”
Ms. Folz said, “we’re hoping to be able to provide a subscription box for residents, where for say $10 they will be able to get five heads of fresh greens at a time. The hydroponic system will allow for 450 heads of produce to be grown each week.”
“Growcer outfits everything that is needed in the sea containers, and there will be a desk for a systems manager to work at and the actual green area where the seeds are planted and the produce is grown,” said Ms. Folz. With this new system in place, one full-time person will be hired as well as two part-time casual positions will be created.
Chief Roy noted the community currently has a job posting for a systems manager.
Ms. Folz added, “we have a community logo/branding competition for a name for this program here and are hoping to get local input on a name. We will be taking input and submissions until July 15.”