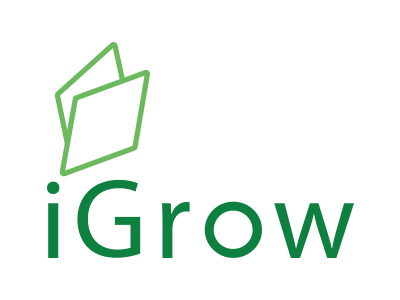
Welcome to iGrow News, Your Source for the World of Indoor Vertical Farming
No Changes to Organic Standards For Containers, Hydroponics and Aquaponics
No Changes to Organic Standards For Containers, Hydroponics and Aquaponics
NOVEMBER 2, 2017 URBAN AG NEWS
National Organic Standards Board Rejects Recommendation to Remove Container, Hydroponic and Aquaponic Production Methods from Eligibility for USDA Organic Certification.
The members of the NOSB voted on Wednesday by a margin of 8 to 7 to reject the proposals to make Hydroponic and Aquaponic production methods prohibited practices under the USDA organic standards. In addition, the NOSB rejected the proposal by a vote of 8 to 7 to create prescriptive nitrogen ratio requirements and to limit delivery of nutrients through irrigation systems in other container production systems. The proposed definition of hydroponics was any system in a container (roots of a plant not in the outer crust of the Earth) that does not have at least 50 percent of the nitrogen needs of the plant in the container before planting and that no more than 20 percent of nitrogen needs are delivered through the irrigation system, watering cans or in a liquid form.
The NOSB did vote to make aeroponics a prohibited practice by a vote of 14 in favor of the ban with 1 member abstaining from the vote. This recommendation will now go to the U.S. Department of Agriculture. Given that the NOSB is technically a Federal Advisory Committee, the staff of the National Organic Program and other USDA officials will determine if the USDA will begin formal rulemaking to modify the existing USDA organic standards. The USDA typically will move forward with rule making or return the proposal for additional clarification. Only after a public comment period and regulatory review would the proposal convert into a regulation.
Greenhouse production practices to be discussed on Thursday by NOSB
The NOSB will begin discussions on the need to create modifications to the standards regarding the use of artificial light, the composting and disposal of green waste and substrate after a production cycle, requirements to recycle containers, and the use of plastic mulches and weed cloth in greenhouse and container operations. No votes are scheduled for these topics.
CSO thanks all growers who contributed their views through written or oral testimony
The CSO wishes to express its gratitude to the roughly 70 producers from all sides of the issue who delivered oral comments and the hundreds of individuals that submitted written comments. The Coalition especially appreciates the time of the many growers who volunteered their time to help educate members of the NOSB and the organic community. Ultimately, both the quantity and quality of the voices explaining the importance of preserving the rights of growers to determine the most appropriate growing method for their site-specific conditions led to this mostly positive outcome.
What happens next?
The vote did not resolve the long-standing issue of the lack of consistency in how accredited auditors review the farms and production facilities of growers that incorporate containers in their systems. The members of the NOSB and the USDA NOP staff will determine in the coming hours, days and weeks if there is value in continuing work on proposed regulations that would impact other aspects of greenhouse and container production systems. The CSO will be there to protect your interests.
Everyone deserves organics
The most viable option to achieve this goal is to use all certified systems and scales of production, not to kick certain growing practices out of the industry. The organic industry should embrace and promote diversity rather than stifle it. Organic production should not be limited to annual crops grown in temperate climates with high rainfall and killing freezes in the winter. The NOSB should be ensuring that organic rules do not arbitrarily discriminate against production in urban, desert, or tropical areas, nor should they exclude other systems that use containers and greenhouses. We should trust growers to make their own determination to know when growing in the soil or in containers make the most sense for the protection of the consumer and the ecology we all share.
Kimball Musk: “Food Production is Facing Unprecedented Innovation”
“Food is a wonderful gift we give each other three times a day, he says. — But it’s hard to imagine a more horrible system than the one we have today”. He says that food space — the so called food industry in Silicon valley — inspires him now exactly like the Internet in 1995. “We’ve never seen around food innovation today’s scale,” he says.
Kimball Musk: “Food Production is Facing Unprecedented Innovation”
By: paradox | 18.10.2017
Speaking of Kimble Musk, it will be difficult to avoid comparisons with his older brother because Kimball wants to do agriculture the same as Elan did with space exploration and electric vehicles. Kimball plans to feed the world in the style of Silicon valley.
Kimball prospered, working together with his brother. Now he’s 45 years old and he is buying up land across America. He believes in environmentally friendly “real food”, which in direct and figurative sense of the word and to feed consumers, and farmers, and the United States, and the planet as a whole. In his business, as in business brother, comes to the fore strategy, idea and marketing. He doesn’t just want to spread innovative vertical farms across the country. Kimball plans to establish a whole infrastructure: training centres, promotion of new food philosophy, venture capital programs, special accelerators. His system is, he believes, needs to completely change today’s American agriculture, and in General, American eating habits.
“Food is a wonderful gift we give each other three times a day, he says. — But it’s hard to imagine a more horrible system than the one we have today”. He says that food space — the so called food industry in Silicon valley — inspires him now exactly like the Internet in 1995. “We’ve never seen around food innovation today’s scale,” he says.
Musk-younger, like a politician or a missionary who travels the States with his idea about the food industry of the future. This year he visited the 50 major conference related to food and business. However, he spends millions on their portfolio companies and support other projects. His non-profit organization has installed 425 of educational vegetable gardens in kindergartens and schools, so that children from a young age understand how there is a “real food”. Musk says that for any business the important scale. The previous company who tried to promote the idea of proper food, did not receive sufficient result, because they could not scale their model, and it is certain that you can.
His model, there are critics. They say they work with farmers, 100% different from working with dotcom, which you didn’t have to get your hands dirty on the ground. Michelle Nischan, founder and chief Executive officer of the company Wolesome Wave, trying to make fruits and vegetables more accessible for people with low incomes, says that the Mask is the right ideas. But to understand the breakthrough technology and scale, is not equal to the ability to negotiate with the target farmers and to get their hands dirty. According to her, the Mask does not have enough practical experience on the farm.
In October was the first release of the accelerator Kimball Musk's Square Roots, which develops urban farming. During the year, 10 businessmen learned how to work with container farms and to market products. Each participant in the accelerator receive from the company a cargo container with a vertical system for growing plants, irrigation systems and a set of blue and red LEDs, and learned to extract from this yield. According to Kimball Musk, such containers will fill the city and are an important source of food.
© 2017, micetimes.asia. All rights reserved
Ashley Ridge High School’s Farm Container Program is Growing Local Leafy Greens for Students
Ashley Ridge High School’s Farm Container Program is Growing Local Leafy Greens for Students
By Stetson Miller Published: October 27, 2017
SUMMERVILLE, S.C. (WCBD) – Ashley Ridge High School’s farm to school program in Summerville is delivering fresh local vegetables to six Dorchester District Two schools.
A container farm on the school’s campus provides fresh lettuce to students at Ashley Ridge, Summerville High School, DuBose Middle School, Beech Hill Elementary, Sand Hill elementary and Gregg Middle School.
The farms grow European-style head lettuce inside a shipping container at a faster rate than traditional farming and use less space. The farming method also allows for vegetables to grow in a controlled environment that can be monitored and adjusted remotely using a computer or smartphone.
The container farm is part of a College of Charleston study to examine how nutritious the leafy greens are compared to traditional school food and to see if there is a change in consumption of salad at the schools.
Dorchester District Two teamed up with local companies. Summerville-based Tiger Corner Farms manufactured the container farm, Vertical Roots grows the produce inside, and Boxcar Central created the technology.
“Our goal and mission now is teach the kids about sustainable farming,” said Andrew Hare, General manager of Vertical Roots. “Get an educational piece going to this in addition to having them eating better. No one is going to argue that our country has an issue with obesity and if we can teach kids from an early age, start them the right way on what’s good to eat and the nutritional value of something that is grown properly, that’s something that can last them a lifetime.”
By the end of 2017 the school district will evaluate the farm container program and decide if it will expand it.
Freight Farms Expands Into International Markets And Business and Education ChannelI
"Local food is in high demand, and schools and businesses are prioritizing health, wellness, and engagement now more than ever. The LGM™ fits seamlessly in with their goals, and we are re-focusing to meet the demands of a new market -- it's a very dynamic time to be in ag tech," said Brad McNamara, CEO and co-founder, Freight Farms.
Company Moves to New Corporate Headquarters Due to Accelerated Growth in 2017
NEWS PROVIDED BY Freight Farms
BOSTON, Oct. 31, 2017 /PRNewswire/ -- Freight Farms, the leading manufacturer of commercial-grade hydroponic farms built inside of shipping containers, today reported company growth to accommodate the increasing demand from new business sectors and international markets. As the company continues to thrive, Freight Farms also announced a corporate expansion to the South End Exchange neighborhood of Boston.
With the new office, comes a new company direction. Small business farmers have historically shown the most interest in the company's flagship product, the Leafy Green Machine™ (LGM™), to start or expand their business. However, over the past several months, Freight Farms has experienced widespread interest from larger entities. Restaurants, schools, universities, corporations, municipalities, and non-profits are all buying LGMs™. In the past year, sixteen businesses and campuses launched Leafy Green Machines™. Additionally, Freight Farms has been working with major institutional food service providers Compass Group and Sodexo. By focusing on this channel, Freight Farms hopes to bring the LGM™ to many more communities, spreading sustainable farming methods to a broader audience.
"Local food is in high demand, and schools and businesses are prioritizing health, wellness, and engagement now more than ever. The LGM™ fits seamlessly in with their goals, and we are re-focusing to meet the demands of a new market -- it's a very dynamic time to be in ag tech," said Brad McNamara, CEO and co-founder, Freight Farms.
"An important piece for Sodexo is our 'Better Tomorrow Plan,' which specifically focuses on individuals, our communities, and our environment. Freight Farms has given us a great opportunity to have that engagement with students on a higher level, especially with sustainability," said Heather Vaillette, district manager of campus services and independent schools, Sodexo.
As Freight Farms continues to grow, it will not turn its back on the small business farmers who gave it its start. This channel is still growing as traditional farmers adopt Freight Farm's technology. With an LGM™, farmers can extend their business year-round and provide crop protection in the face of increasingly extreme weather patterns.
"There are significant environmental benefits to farming in a hydroponic system, which allows farms to use 90 percent less water than traditional methods," said Jon Freidman, President, and co-founder, Freight Farms. "The contained environment also eliminates the need for herbicides or pesticides, and the ability to farm anywhere reduces the impact of food transportation. As our user base expands to larger organizations, we look forward to seeing sustainable produce spread to new markets."
Notable moments 2016 – 2017:
April 2016 – Partnered with Clemson University and NASA to explore Self-Sustaining Crop Production Units (SSCPU) as a new way of growing food in extreme climates and outer space.
September 2016 – Kimbal Musk purchased 10 Leafy Green Machines™ to launch Square Roots – an urban farming accelerator – in Brooklyn, NY.
November 2016 – Freight Farms partnered with a major agricultural supplier located in the Netherlands to service Europe. To date, six Leafy Green Machines™ have been sold.
January 2017 – Introduced The 2017 Leafy Green Machine™ which contains all the components needed for commercial food production. It is equipped with the most advanced growing technology and engineered for easy operation, allowing users of all backgrounds to immediately start growing fresh food produce year-round.
March 2017 – Freight Farms partnered with Federal Realty Investment Trust. Leafy Green Machines™ will occupy unused parking areas to bring urban farming to shopping centers throughout the U.S.
November 2017 – The first federal farmer within the program, Nate Brown, launched his Leafy Green Machine™.
April 2017 – Freight Farms placed three farms in Dubai, marking an expansion into the Middle Eastern market. This mirrors similar expansion made in April 2016, when Freight Farms placed containers in the Caribbean.
2017 Leafy Green Machine Stats:
The 40-foot container can produce 2-4 tons of produce a year.
The LGM™ comes equipped with 256 vertical growing towers to maximize space and production.
The LGM™ has 3,600 seedling sites and 4,300 growing sites.
LGM™s are currently operating in climates between -40 degrees and 120 degrees Fahrenheit.
Freight Farmers can harvest 365 days a year.
The LGM™ automates temperature, water, nutrient levels, pH, CO2, and humidity to maximize growth.
Users can schedule, track, and control all farming components remotely using the farmhand® platform.
About Freight Farms
Founded in 2010 in Boston, Freight Farms has established itself a leader in the agriculture technology industry. The company was the first to bring farming into a shipping container to create their flagship product: The Leafy Green Machine™. The "LGM™" is a complete vertical hydroponic growing facility built inside a repurposed container. It enables Freight Farmers to grow fresh food year-round, regardless of prior experience or environment. The LGM™ is outfitted with environmental controls and indoor growing technology, which can be monitored and controlled using Freight Farm's complimentary technology platform- farmhand®. To date, there are over 150 farms in operation in the U.S.,Canada, Europe, Dubai and the Caribbean. For more information about Freight Farms, visit www.freightfarms.com.
Media Contact
Elizabeth Yekhtikian
InkHouse for Freight Farms
elizabeth@inkhokuse.com
SOURCE Freight Farms
Related Links - http://www.freightfarms.com
National Organic Standards Board Decrees That Hydroponic Can Be Organic
National Organic Standards Board Decrees That Hydroponic Can Be Organic
By Dan Nosowitz on November 2, 2017
A row of hydroponic greens | Aqua Mechanical onFlickr
On November 1st, the National Organic Standards Board finally made a decision on one of the most divisive issues in the organic world: should crops grown in water, containers, or otherwise not in the ground be allowed to call themselves organic?
The decision is thus: hydroponic and container gardens will remain eligible for organic certification.
This is a debate that’s much more complicated than it seems. Hydroponics and other types of high-tech farming get a lot of attention, most of it positive, for utilizing spaces that previously couldn’t house farms (abandoned factories, shipping containers, that kind of thing). They can potentially be very energy-efficient and reduce water usage. And there’s rarely a need for pesticides at all, since many of these operations are indoors.
Among those pleased with the decision is the Recirculating Farms Coalition, a group of eco-conscious high-tech farmers and innovators. “By siding with current science and recognizing that existing law purposely leaves the door open for various farming methods, the NOSB is sending a critical message that sustainability and innovation are valuable in U.S. agriculture,” wrote RFC executive director Marianne Cufone in a release.
But many of the farmers who were behind the original push for an organic certification program are vehemently opposed, and it’s not because of groups like the RFC. Two main groups benefit from hydroponic farms being able to get organic certification (and thus charge much more for their wares): techie farmers, like those Cufone represents, and large agribusiness firms. Those firms, which include Driscoll’s and Wholesum Harvest, operate gigantic hydroponic operations for their organic food, and many organic activists, like the Cornucopia Institute, see those as a cheap and easy way to charge a premium without actually doing any of the stuff the organic program is really about.
At its core, say those activists, organic food is about an entire ecosystem: taking care of the soil, recharging nutrients with crop rotation, providing for natural pollinators and pest control. It is a way for farming, which can often be ecologically destructive, to work with the planet. And massive hydroponic and container operations like Driscoll’s do not do that: they are willfully separate from the environment. They do not contribute to soil health (partly because they don’t use soil) nor to the overall health of the natural world. For their part, those companies say that they follow the rules in terms of pesticide use and therefore should be allowed to use the label. Organic activists say this is a loophole—a way to get the big bucks an organic label can secure by following the letter, rather than the spirit, of the law.
In some ways, it’s an unfortunate debate, because it pits people against each other who have many of the same goals in mind. Organic activists and small hydroponic farmers both want to grow food sustainably, at their core. But, as with most of the agricultural developments during the current administration, this decision isn’t about small farmers.
It may seem like a small thing, allowing hydroponics to call themselves organic. But to many organic farmers, this is a total perversion of what the term is supposed to mean and achieve. What’s the point of following all of these expensive and difficult planet-saving rules if a huge corporation can just build a factory and undercut your prices with a product that doesn’t work toward the same goals?
Little Box Farms Turns Vacant Crown Heights Lot into Container-Farming Facility
October 31, 2017
Little Box Farms Turns Vacant Crown Heights Lot into Container-Farming Facility
The operation can grow up to an acre's worth of produce in vertically stacked shipping containers
Photo: Little Box Farms
Your next serving of fresh greens could come from the back of a shipping container.
Tech investor Travis Ally has leased a plot of vacant land at 827 Bergen Street in Crown Heights for an urban farm concept called Little Box Farms, housed in repurposed freight containers that have been converted in growing pods.
While greenhouses and rooftop farms operate throughout the city, Little Box Farms uses the containers, which are equipped with LED lights and hydroponic technology, to cultivate microgreens, such as sprouts and baby chard, as well as larger leafy vegetables like kale. The plants are rooted in burlap sacks and placed on shelves that run the entire height of each container.
"These shipping containers can each produce an acre of farming land while using 90% less water," Ally said. "Plus we're producing as close as possible to the consumer so we can cut super fresh and organic produce, and deliver it for consumption the same day."
The urban farm is designed to scale easily—two containers are currently in operation at the site, but Ally envisions bringing in more and stacking them vertically up to five containers high. Ally procured the growing containers from two companies, Growtainer and CropBox—two players in an expanding urban farming industry.
Ally, who has invested $150,000 into launching the venture, admits it's not yet profitable due to the large start-up costs. He said he hopes the vertical concept will help him maximize revenue and beat the costs of the land he is now leasing, which is pricey relative to the economics of farming.
Little Box Farms leased the 5,400 square foot site for five years. Asking rents for the space were around $7 per square foot.
"In the future consumers will care more about how and where their food is grown and water will become more scarce," Ally said. "We don't have the transit costs because we're growing for the local market and we don't have to pay for fertilizers or fighting insects or worry about weather because we're growing organically in a controlled environment."
So far, Ally has been selling his produce to restaurants. He eventually plans to reach more consumers through stocking stores such as Whole Foods.
Peter Schubert, a leasing broker at TerraCRG, arranged the deal on behalf of the property owner, Saeed Fakir.
"There are other urban farm sites in the city but this concept was something unique and an amenity for the neighborhood," Schubert said. "On the weekends, Little Box Farms plans to host a greenmarket, which is something Crown Heights hasn't had."
Kimbal Musk Defends His Container Farming Accelerator
Musk’s solution is simple, if a tad controversial: The accelerator’s first yearlong field experiment did away with the need for a field entirely. Instead, its 10 farming containers are located in a Brooklyn-based parking lot. “So far, we’ve seen a lot of enthusiasm if you can bring the farm to the farmer,” Musk added.
Kimbal Musk Defends His Container Farming Accelerator
Dan Barber of Blue Hill fame took Musk’s Square Roots project to task during Fast Company’s Innovation Festival.
In 2016, Kimbal Musk cofounded Square Roots, an accelerator that teaches farmers how to raise crops with LED lighting in climate-controlled shipping containers. He quickly received more than 500 applications for 10 spots.
This year, that number more than doubled to 1,100.
“It’s extraordinary how much interest there is in farming among young people,” the food-tech entrepreneur said during a Fast Company Innovation Festival panel about remaking the U.S.’s food system. “But I can’t get them to go to Iowa.”
Musk’s solution is simple, if a tad controversial: The accelerator’s first yearlong field experiment did away with the need for a field entirely. Instead, its 10 farming containers are located in a Brooklyn-based parking lot. “So far, we’ve seen a lot of enthusiasm if you can bring the farm to the farmer,” Musk added.
Kimbal Musk
Square Roots’s vertical farms prize the idea of growing locally in small but incredibly bountiful little biodomes as a way to cut food miles and production costs–and encourage year-round access to healthier food. That’s something he has championed in a different way at his upscale Colorado restaurant, The Kitchen, and in his growing base of Next Doorrestaurants, which are more affordable. Both of these restaurants source their ingredients heavily from local farmers.
There’s no silver bullet to fix America’s food production problem, which involves agricultural, manufacturing, and even restaurant systems designed to create cheap, calorie-dense, and highly processed stuff to eat. But Musk can afford to take risks and stray from conventional models: He made millions in the late ’90s by selling an online city guide service that he cofounded alongside his brother, Elon.
As the New York Times recently reported, however, Kimbal Musk’s swashbuckling entrance into hydroponics has upset some farm-to-table chefs and sustainable farming advocates, who see his approach as Silicon Valley-style industrialization. Growing plants in a sci-fi-like way–in Musk’s method, there’s no soil required–might scale quickly, delivering certain foods more cheaply to grocery stores, restaurants, and people in need. At the same time, the container method doesn’t address rising concerns from environmentalists about how to fix the U.S.’s reliance on resource-intensive and pollution-causing commodity cropland. Or how to create farms with the sort of wide-variety of offerings that can remain resilient if weather shifts, or more apocalyptically, the power cuts out.
At the Innovation Festival, Musk’s fellow panelist, Dan Barber, one of the food world’s most prominent local and sustainable eating advocates, echoed those concerns. “The future of produce from a container, whether or not it’s next door to Jay-Z, doesn’t make me [excited],” countered Barber, after Musk playfully noted that Square Roots was located in the rapper’s old Brooklyn neighborhood of Bedford-Stuyvesant.
Barber is concerned that the rise of container farming could lead to new-age produce with inferior flavor and potentially lower nutrient content, depending on what seeds and conditions future farmers simulate to grow their compartment-based foods. At the same time, Barber told the crowd, he worries that Musk’s smart sales pitch might steal both funding and mindshare from other viable agricultural options. There are plenty of nonprofit farmer training programs that offer education to encourage more back-to-the-landers to just get started and adopt more holistic farming methods.
Dan Barber (right)
“[Take] your whatever square footage of kale,” Barber said to Musk. “On a half acre, we could do the same thing, but we could also grow a cover crop, we could grow tomatoes, we could grow a series of grains from which to make bread and porridge, and probably run some cattle over to graze, and have a whole cuisine on that half acre versus just producing the kale.”
Musk, defending his practice, talked about solving the “salad in January” problem. Currently, Next Door restaurants located in cold-winter climates have to source greens from as far off as California or even Australia, which results in a higher carbon footprint for the meals he serves in his establishments. That might change if Square Roots graduates–or others entering the container farming space, and there are many–can create closer, more available substitutions.
Of course, his restaurants could also just stop serving salad in January, but Musk isn’t into that idea. At Next Door, he argued, having a salad consistently on the menu is important–it’s a gateway to healthier eating in general. “I also don’t know if not eating a salad in January is the right answer, because I like a salad in January,” he said.
That get-it-when-I-want it mentality is widespread among consumers, at the expense of a variety of seasonal alternatives like Brussels sprouts or winter squashes. Meanwhile, container farming operations are increasingly efficient. A year ago, it was possible to grow about 50 pounds of kale per week in a shipping container, Musk noted. Today, with upgraded lighting and the right light recipe, he suspects you could theoretically produce 300 pounds of kale in the same time period. “Or you could say, I’m going to really make this super delicious and make 150 pounds of kale,” he said, an acknowledgement that at scale, there are always trade-offs when it comes to food quality.
Ultimately, it will be up to the next wave of farmers to help decide what kind of harvest they’re supplying to their customers.
As Fast Company has reported, Square Roots has already received $5.4 million in seed funding to take their concept to other cities. That’s not a lot of money for a hot startup backed by an established entrepreneur, but each entrant represents a future business owner. And Musk is already planting his own potential vendors in those places. Musk announced, on Medium in January, plans to open 50 Next Door eateries across the country by 2020.
ABOUT THE AUTHOR
Ben Paynter is a senior writer at Fast Company covering social impact, the future of philanthropy, and innovative food companies. His work has appeared in Wired, Bloomberg Businessweek, and the New York Times, among other places.
Kimbal Musk Has a Silicon Valley-Style Plan to Feed America
Kimbal Musk Has a Silicon Valley-Style Plan to Feed America
Kimbal Musk, Elon Musk's brother, is aiming to foment an agricultural revolution in America. With scalable projects that include healthy low-cost fast food and urban farms in parks and shipping containers, he's made an impressive start.
“REAL FOOD” PHILOSOPHY
Kimbal Musk is Elon’s younger brother, who made his first money working in tech and went on to invest in his brother’s other businesses. He serves on the board of both Tesla and SpaceX today. However, Kimbal Musk’s first love is food, cooking, and how we eat. He opened his first restaurant, The Kitchen, in Colorado in 2004. But after a skiing accident into 2010 left him temporarily paralyzed, he had an epiphany: he would devote his life’s work to changing the way we eat in America.
Musk recently opened a satellite to his upscale Kitchen restaurant inside Shelby Farms, a 4,500-acre park in the urban center of Memphis, Tennessee. He is currently testing a small takeout spot there, offering well-prepared, locally-grown meals for around $5—an antidote to fast food. He also made 300 nearby acres, formerly used to grow cotton, part of that deal, and is now transforming that land into an organic farm.
Kimbal Musk’s food philosophy —that “real food” should sustain not just the human body, but also the planet and the food producer—is actually very similar to the community garden or farmers’ market philosophy. Musk’s difference, promoted by him under The Kitchen brand, is that he wants to bring Silicon Valley scalability and innovation to the food system.
“My way of working is very practical,” Musk said to the New York Times. “There are many wonderful solutions to real food, but I focus on what we can scale. The Slow Food guys were right, but what they didn’t know was how to scale. If you can’t scale, it doesn’t matter.”
For example: Musk is interested in school gardens, but criticizes the traditional school garden model—because it doesn’t scale. Although he purports to care most about cooking and eating food, and says he does not place scalability above those concerns. In several areas, this isn’t clear.
The nonprofit arm of the company, The Kitchen Community, has installed learning gardens along with materials and staff in 100 Memphis schools. They also exist in Chicago, Los Angeles, and Pittsburgh, and Musk aims to have them in at least 1,000 schools by 2020.
CRITICS AND CHALLENGES
Not everyone working in food is a fan of Kimbal Musk’s food philosophy, or the way he acts on it. His remarks have often been called tone-deaf, or lacking in broader knowledge about food systems.
After Musk suggested in an interview that food hadn’t yet seen the benefits afforded by technology, Ontario farmer Lawrence McLachlan tweeted in response: “You might want to visit a Farm Progress show. Or even a farm. I think you might have missed 70 years of Ag history. It’s Hi-Tech stuff bud.”
"Food is one of the final frontiers that technology hasn't tackled yet. If we do it well, it will mean good food for all." @kimbal#foodtank pic.twitter.com/6cyv0VsW8Q
Lawrence McLachlan @LMcLachlan60
You might want to visit a Farm Progress show. Or even a farm. I think you might have missed 70 years of Ag history. It's Hi-Tech stuff bud
Musk has, mostly by happenstance, become symbolic of a divide between people working in the modern American food justice movement, where largely “old school” values such as growing food in soil take precedence, and those with “new school” values that emphasize business and tech-focused practices.
“It’s the divide between the technophile cornucopians and the techno-skeptic redistributors,” Krishnendu Ray, New York University nutrition and food studies department chairman, said to the New York Times. For some, like Bay Area chef and and school garden activist Alice Waters, Musk is a Johnny-come-lately who simply doesn’t have enough information.
“I don’t want to hear another word about scaling,” Waters told the Times. “He doesn’t know what he doesn’t know. He’s very earnest about what he’s doing, but he doesn’t know enough about farming and about the soil. He wants to do the right thing, but he just hasn’t done his homework. Not everything has to be scalable.”
That won’t stop Musk, however. His Square Roots project, which trains young farmers to grow greens for sale with nothing but LEDs and enhanced water in Brooklyn shipping containers, yields about as much produce per box as two acres of soil. Musk wants to start a similar program in every major American city.
While the program has its critics, it is part of a larger vertical farming trend. Other programs like Musk’s, which grow faster than soil in less space, are flourishing, even in warehouses. Big cities like Shanghai are creating vertical farming districts, and even Antarctica is getting in on the action.
Philosophy aside, in a time of need and changing climate, even food staples we depend on may grow short; growing more food in less space might be the winning strategy.
References: NYTimes - Tech, TedxTalks, Square Roots
Layoffs Hit Freight Farms As It Shifts Focus To College Campuses
By: Dylan Martin
September 28, 2017
Freight Farms, the Boston startup that makes automated farms in shipping containers, laid off seven employees Monday to focus on its growing segment of college campus customers as some other initiatives foundered.
Brad McNamara, Freight Farms’ CEO and co-founder, confirmed the layoffs to BostInno Thursday. Axios’ Pro Rata newsletter first reported on the layoffs earlier this week, but McNamara said there were some inaccuracies in the initial report. He said there were no executive departures, as Axios had reported, and that the only recent departure was Austin Coffin, a sales manager who left to pursue a larger role at another startup.
Freight Farms raised a $7.3 million Series B led by Spark Capital in July, which brought total funding to $12 million. The company has now deployed more than 150 of its Leafy Green Machines, which costs $85,000 and can produce 1,000 heads of lettuce a week.
The layoffs, which amounted to roughly 18 percent of the company’s 38-person staff, were the result of the company’s decision to shift its focus from some research and development efforts that weren’t panning out to its growing segment of college campus customers, an area that started seeing more traction by the end of last year. College campuses are using Freight Farms’ containers to supply their dining operations.
“THE REAL OPPORTUNITY THAT IS GROWING FAST IS THIS SPACE IN THE INSTITUTIONAL AREA.”
The first deal seemed like an outlier, McNamara said, but then the company eventually landed five deals within a five-month period, which showed promise. The company now has containers deployed at 15 or 16 campuses, in addition to roughly three corporate campuses. Freight Farms’ base of small farm customers, which is now around 75, remains a focus, but McNamara said the traction with college campuses has more growth potential.
“The real opportunity that is growing fast is this space in the institutional area,” he said. “As a team, we have to make a choice for what’s best for the company.”
McNamara said the research and development efforts that weren’t moving the needle were some product and software projects. One of the products the company has adjusted expectations for is its smaller “LGM” container that was revealed last year and aimed at attracting restaurant customers. The CEO said the company has deployed a few units with early customers to get more feedback, with a commercial launch planned next year.
Taos Youth Shelter Grows Steady Funding With Sustainable Agriculture
Taos Youth Shelter Grows Steady Funding With Sustainable Agriculture
PHOTOS COURTESY FREIGHT FARMS
Posted Friday, October 20, 2017 | By Cody Hooks | chooks@taosnews.com
DreamTree Project, a local nonprofit that operates a youth shelter, is buying a retrofitted shipping container that comes fully stocked and installed with all the technology and equipment necessary to do vertical hydroponic farming in any weather. The “social enterprise” will fund the shelter and other programing.
While most farmers in Northern New Mexico have put their gardens to bed for the season, one local nonprofit is looking to harvest its first bundles of lettuce, kale and basil just after the start of the new year.
DreamTree Project announced earlier this month that the organization is branching into agriculture to cultivate a new source of much-needed revenue for the high costs of running a temporary shelter and transitional housing program for young people.
"It's simple," said DreamTree Project Executive Director Catherine Hummel. "We will grow, package and distribute produce to local markets and in return create jobs and revenue for DreamTree Project."
But how are nonprofit-do-gooders-turned-first-time-farmers going to raise a crop that's ready in the dead of winter?
The answer is a retrofitted shipping container that comes fully stocked and installed with all the technology and equipment necessary to do vertical hydroponic farming in temperatures as hot as 120 degrees and cold as 20 degrees below zero, said Hummel.
DreamTree Project is purchasing the 40-foot-by-9-foot shipping container from Freight Farms, a company based in Austin, Texas.
Once fully operational, the relatively small growing space inside the shipping container can produce 1 acre's worth of leafy greens, lettuce and similar crops with little more than 10 gallons of water a day, Hummel said. Many of the hydroponic monitoring and distribution systems are automated and can be controlled through a mobile app.
While the shipping container farms were designed for in-fill spaces in densely packed cities that have a chronic shortage of fresh food, Hummel said the vertical farm offers the opportunity to "link in with the Taos agricultural tradition," but with an "innovative, high-tech approach."
Hummel said the crops grown in the new vertical farm, which will be located near the nonprofit's main space in Taos, will be sold to restaurants that have confirmed their need for a consistent supply of greens in the winter months. A weekly farm stand supplied by the DreamTree Project farm is also in the works.
Hummel estimates the new farm will bring in at least $25,000 a year - a significant chunk of money in a cash-strapped community full of nonprofits that inevitably compete for resources.
As a social enterprise, the farm isn't about netting a profit for investors, but meant to put money directly toward housing and counseling services for young people without a home.
Lisa O'Brien, director of the Taos Community Foundation, told The Taos News that DreamTree's project is bold.
While "grant funding, gala events and individual gifts have been the anchors of traditional fundraising strategies," O'Brien said, "there are great demands on nonprofit organizations to meet the ever-growing needs in community, and creating diversity in funding streams is critical to their long-term health."
Ironically enough, DreamTree Project has made a down payment on the pop-up farm, but seeks grants and donations to buy it outright instead of taking on loan payments. The vertical gardens typically have a three-year return on investment, according to the Freight Farms website.
But finding the right type of social enterprise can be tricky. Online business are a viable option for making money, but are often disconnected from the community, Hummel said. One nonprofit in Albuquerque started growing wheatgrass for the many smoothie stores in the metro area to pick up extra cash while another organization coordinates vehicle donations to fund its mission.
DreamTree Project screened at least 50 potential ideas and went through market research for about six. "This one really fit our criteria: It's a small business we have the capacity to run, meets a need and can be sustainable in our community."
DreamTree Project's youth shelter can house up to eight residents who are between 12 and 17 years old for up to 90 days, while the transitional living program can help more than a dozen young people ages 16 to 24 for up to two years.
"Once it's fully up and running, generating money for our programs, there'll be other opportunities - making prepared foods like salads and pesto we can sell through local markets," she said.
DreamTree Project is hiring a part-time farm manager and part-time sales manager to jump-start the operations. Hummel said that once the farm is running smoothly, it could offer opportunities for youth employment - in harvesting, sales and deliveries.
Houston’s Urban Container Farm Unfazed By Harvey
A 320-square-foot container just north of downtown Houston is not where you would expect to find a farm, but that’s exactly where is located at. Acre in a Box consists of two shipping containers retrofitted to grow leafy greens.
Houston’s Urban Container Farm Unfazed By Harvey
While many Texas crops got flooded, one unconventional Houston farm was able to supply restaurants with fresh lettuce after Harvey
POSTED ONOCTOBER 16, 2017, 10:15 AM
A 320-square-foot container just north of downtown Houston is not where you would expect to find a farm, but that’s exactly where is located at.
Acre in a Box consists of two shipping containers retrofitted to grow leafy greens.
“All of our seeding goes through a germination process,” the young company’s CEO, Andrew Abendshein, explained.
After that, the seeds are planted into 256 hanging towers where they grow – vertically – to lettuce, kale or mustard greens.
Abendshein and his team then distribute them to local restaurants and farmers markets. The container is manufactured by Boston-based Freight Farms.
Besides the convenience of having this more or less mobile farm in an urban setting, the concept proved useful during Harvey because the water didn’t get to it. So they were able to provide a restaurant that was open with fresh lettuce.
“We were the only salads on their menu that day,” Abendshein said. “And it was great because people, I think it was the first real day people could kind of get out, and we had fresh produce for everybody.”
Abendshein hopes to expand and eventually serve markets and grocery stores in Houston’s food deserts.
These Cold-Weather Container Farms Let Produce Grow In The Arctic
In the subarctic town of Churchill, Manitoba–unreachable by paved roads and best known for its population of polar bears–a head of romaine lettuce can cost as much as $8 without subsidies. Shipments of produce can take weeks from distant farms, and when vegetables arrive, it’s an event. But the town will soon have another option: a shipping container farm growing greens on site.
- 10.12.17
- Fast Company | WORLD CHANGING IDEAS
These Cold-Weather Container Farms Let Produce Grow In The Arctic
As traditional Inuit diets change, they’re being replaced with processed food because it’s so difficult to stock markets with fresh produce. Now, they can grow it themselves, even in sub-zero temperatures.
“The impetus for the whole project was the high cost of food and lack of opportunities for employment in Inuit communities.” [Photo: Vertical Harvest Hydroponics/The Growcer]
In the subarctic town of Churchill, Manitoba–unreachable by paved roads and best known for its population of polar bears–a head of romaine lettuce can cost as much as $8 without subsidies. Shipments of produce can take weeks from distant farms, and when vegetables arrive, it’s an event. But the town will soon have another option: a shipping container farm growing greens on site.
A 40-foot shipping container was repurposed into a hydroponic greenhouse in Spokane, Washington, then shipped to Montreal, where a cargo ship has taken it through the St. Lawrence River, around the coast of Newfoundland, and is now traveling through the Hudson Bay. When the delivery arrives on October 19, Churchill will be the seventh community in the Far North to begin using this type of farm, called the Arctic Growing System.
“If you’re in a community in Northern Canada where it already takes a week for produce to get to an urban center, and another week or two for it to fly to three different communities . . . everything that was fresh is no longer really edible.” [Photo: Vertical Harvest Hydroponics/The Growcer]
“The impetus for the whole project was the high cost of food and lack of opportunities for employment in Inuit communities,” says Corey Ellis, cofounder and CEO of The Growcer, the startup that makes the shipping container farms and works with the small communities that operate the farms.
The company was born out of a project called the Northern Innovation Hub, which aims to find solutions to local problems like food security, housing, and employment. Ellis and others worked with remote communities to brainstorm potential solutions, and landed on local food production as a way both to spur economic development and improve health.
Right now, many people in the area struggle to afford food. Even when grocery stores get subsidies from the Canadian government to offset high produce prices, the cost of shipping extremely long distances and the rates of spoilage on the journey means fruits and vegetables are still quite expensive. That cost means that consumers are more likely to pick unhealthy packaged foods, which have pushed up the rate of diabetes.
And the fresh options that do make it often aren’t very appealing. “If you’re in a community in Northern Canada where it already takes a week for produce to get to an urban center, and another week or two for it to fly to three different communities and kind of bunny hop over to yours, everything that was fresh is no longer really edible,” Ellis says.
The container farms can also create new jobs. “I think they saw an opportunity: Hey, why are we spending money down south to buy food when we could keep it in our community and pay someone local to harvest it?” he says.
“Why are we spending money down south to buy food when we could keep it in our community and pay someone local to harvest it?” [Photo: Vertical Harvest Hydroponics/The Growcer]
Shipping container farms aren’t new, but the startup realized that current options–typically developed for cities in milder climates–wouldn’t work in the region. The farm they designed is insulated enough to withstand days at 60 degrees below zero and blizzards. By splurging on more expensive parts than a typical indoor farm kit, such as the highest-quality lights, the Arctic Growing System can actually be more productive than a similar farm in Boston or New York.
“We ended up with a system that has probably twice the cost but very similar ROI to a unit like Freight Farms, because we were able to basically triple the yields that a Freight Farm unit would get,” says Ellis. (Beyond using more expensive parts, the yield was improved by a unique advantage of farming in the Arctic: The cold, dry air helps make it easier to expel humidity from the greenhouse, which helps plants grow faster.)
“Somebody has to make money for this to grow sustainably, so that’s at the root of everything we do.” [Photo: Vertical Harvest Hydroponics/The Growcer]
The system arrives with everything needed to start the farm, including 14 months’ worth of growing material, seeds, cleaning solution, and multiple spare parts for every major part in the system. The community plugs it in, connects it to water, and it’s ready. The farm managers don’t need prior experience farming; the startup works very closely with customers, helping develop custom business models and monitoring the greenhouses by satellite to help managers troubleshoot any issues. “Somebody has to make money for this to grow sustainably, so that’s at the root of everything we do,” he says.
Six communities in Alaska have started using the farms, some for as long as 18 months, and all have broken even. Even with the relatively high energy bills required to keep the farms warm, the system is far less expensive than shipping produce thousands of kilometers. In one community, for example, growing the produce is roughly 25% of its retail cost. The growers and the grocery store can add margins and customers still pay 30% less than they would have otherwise.
Notably, produce was not traditionally part of the diet of Inuit or other indigenous people. But, then again, neither was soda, candy, or other junk food that has become common. As diets evolve, Ellis says that there’s a growing interest in fresh produce. The startup is also working to develop plans for ready-made meals that combine traditional ingredients with produce, which greenhouse owners will be able to offer as another product.
“What we’re doing is basically creating an environment where the healthy alternative is just as convenient and affordable as the unhealthy one,” he says.
ABOUT THE AUTHOR
Adele Peters is a staff writer at Fast Company who focuses on solutions to some of the world's largest problems, from climate change to homelessness. Previously, she worked with GOOD, BioLite, and the Sustainable Products and Solutions program at UC Berkeley.
Start-up Furthers The Cause of Urban Farming From a Shipping Container
Start-up Furthers The Cause of Urban Farming From a Shipping Container
by Christina Anthony
Thursday, October 12th 2017
GRAND RAPIDS, Mich. (NEWSCHANNEL 3)
A farm on wheels is growing crops from a Grand Rapids parking lot.
Meteorologist Christina Anthony reports on a start-up company furthering the cause of urban farming.
When white-collar technology meets blue-collar labor it gives birth to the very interesting Green Collar Farms, where plants can grow without the help of soil or natural sunlight, and where size truly doesn't matter.
Brian Harris, Former President and CEO of H&H Metal Source, spent twenty years employing science against the elements of steel.
Now, he's using his scientific background to harvest crops for his new company, Green Collar Farms, all from the inside of a shipping container.
Harris said, "It's 350 square foot inside, but because we're growing hydroponically without soil in a vertical form factor, we're able to yield about an acre in a half to two acres of crop every seven weeks, 365 days a year."
By growing crops in a controlled environment, Harris can weed Mother Nature out of the equation.
He can adjust the temperature, humidity, lights, and carbon dioxide levels manually from within the container, or with an application on his iPhone.
Harris can even feed crops nutrients through a computer system wired to vertically stacked columns of greens.
He said, "The food all comes to them. Their root ball is about 10 percent the size of a normal root ball. So they taste really, really good."
Green Collar crops, like lettuce, kale, and arugula, are harvested alive with the tiny root attached, and distributed within 24 hours. No matter the season, which means the leafy greens have a longer shelf life than those trans-plants.
Harris said, "This container farm is simply the first expression of what indoor agriculture can be."
Harris's mission for Green Collar Farms runs deeper than his scientific roots.
He said, “Once we get down the road another twelve months or so, we will have an idea about how to bring in the whole 10,000 square foot facility in the urban core that provides stem education opportunities, employment, health, and wellness benefits, jobs. So that's the journey."
Harris hopes his container farm will grow on Grand Rapids, and kids interested in science.
If you want to learn more about his blossoming business head to http://www.greencollarfoods.com/
Indoor Farming Grows In Greater Boston
Credit: Cristina Quinn/WGBH News
Indoor Farming Grows In Greater Boston
October 11, 2017
Indoor farming is an industry that continues to grow — and not just your greenhouse variety, either — but a close cousin that uses no sunlight or pesticides, little water, and a whole lot of technology.
Inside an old ginger ale factory in Millis, Freshbox Farms has 8-by-40 foot containers lined up, each connected to a water purification and air filtration system. Inside every container is a hydroponic farm growing an acre’s worth of leafy greens. But, before we can even enter one, the company’s senior vice-president of plant science and product development, Deane Falcone, and I suit up in lab coats and hair nets so we don’t bring in insects that can damage the plants.
Inside, rows of lustrous, leafy green romaine lettuce greet us from trays of water. Each section is in a different stage of growth ranging from two weeks to harvest time, which occurs at five weeks. The company also monitors the soil and air conditions, which is captured every 30 seconds with software created in-house
This romaine lettuce receives 16 hours of fake sunshine from LED lights and uses about 18,000 gallons of water in an entire year, a fraction of what traditional lettuce farms use. Hydroponic farming has long been regarded for its water efficiency but critics of indoor farming like this say the cost to power the LED lights is hard to justify. Falcone agrees that it’s costly but cites Haitz’s Law, which predicts the efficiency of LED lights to increase exponentially every decade.
“So we're paying for a lot of electricity to power up a lot of the LED lights,” he said. “The thing that we always point to is the fact that the efficiency of the LEDs is increasing every couple of years.”
The cost factor is something the founders of Freight Farms, a local startup, considered when they started turning shipping containers into pre-fabricated vertical farms that require only one layer of lighting on each side. They’re called Leafy Green Machines.
It was one of the draws for Bobby Zuker and Chris Mutty, who bought one of these containers. Together they launched Greenline Growers, right out of a former taxi depot in Coolidge Corner, Brookline.
“We started in December of 2015,” Zuker said. “That was when we got our first Freight Farm. And then by March we were actually selling to restaurants.”
Greenline Growers now has three vertical farms. Freight Farms sells these Leafy Green Machines to budding farmers like Zuker and Mutty for $85,000. They also provide training and now an app that allows users to control settings remotely.
“They've taken a lot of different technologies and aggregated it and made it fairly simple to automate it and then we just do the farming part.” Zuker said.
Tim Griffin of the Friedman School of Nutrition Science and Policy at Tufts, said this latest iteration of urban agriculture could diversify the food supply as weather becomes more erratic.
“I see it as being it's another way that we grow food and if it works really well with particular foods, then we should be thinking about how we should be thinking in a positive way,” he added. “And then [we should] also always [be] thinking about who has access to what and who does not.”
Even though we won’t be seeing corn or wheat grown in these things, that doesn’t rule out strawberries and even someday rice and grapes to go with the ever-growing varieties of lettuce.
Lego For Social Entrepreneurs: An Ode To The Shipping Container
Lego For Social Entrepreneurs: An Ode To The Shipping Container
Craig Kielburger, Contributor | Co-Founder of WE, social entrepreneur, author and speaker
o-authored by Marc Kielburger
10/03/2017
As Hurricane Harvey loomed on the horizon, Andrew Abendshein filled the water tanks and “battened down the hatches” on his small farm in Houston, Texas. All he could do was hope.
In Harvey’s aftermath, it was three days before Abendshein could get back to his farm.
Despite the storm’s massive disruption of local agriculture, he found his crops intact: the lettuce was hearty and the kale was hale, not a leaf out of place. The greens were safe in their sturdy, hydroponically-enabled shipping containers. Thanks to the repurposed metal crates, Abendshein’s Acre in a Box business was soon making deliveries to local restaurants, providing the only fresh veggies on the menu following the storm.
Abendshein is an oil industry worker turned urban farmer, thanks to Freight Farms. This Boston-based business takes old shipping containers, retrofits them with hydroponic equipment, and turns them into portable gardens. Using 90 per cent less water than traditional farming, shipping crate farmers like Abendshein can produce as much food as a football stadium-sized field in an area smaller than the end zone.
Freight Farms offers a creative new lease on life for these ubiquitous giants that would otherwise have gone to waste.
There are more than 17 million shipping containers around the world, bringing us bananas from the Dominican Republic and smartphones from China. Unfortunately, these prodigal crates rarely return home. It’s cheaper for manufacturers to build new containers for their goods than to send back old ones. Megatons of metal wind up rusting in dockyards. But savvy entrepreneurs are using shipping containers like huge Lego blocks—they can become anything.
Retired from the sea, these crates have found new life as libraries and computer labs in developing communities, and classrooms in refugee camps.
Container homes have been a fad for years now, and not just for eccentric hipsters. American Family Housing, a California non-profit, has made shipping containers into housing for homeless veterans.
Clinic in a Can, in Wichita, Kansas, turns old containers into mobile doctors’ offices, medical labs, and even fully-equipped surgical units. The pods can be quickly deployed to natural disaster zones. Stick a bunch together and you have an instant hospital.
In Toronto, a community center has built a pop-up marketout of 15 shipping containers. Local entrepreneurs can rent vending space for far less than a brick-and-mortar store, creating economic opportunity and a thriving neighborhood hub.
Now, aspiring container entrepreneurs beware: it’s not as easy buying one and moving in.
Many containers have been treated with lead paint or harmful chemicals and must be cleaned. You’ll need doors, windows, insulation, and special equipment for uses like hydroponic farming. Up-cycling a crate to use for housing or a storefront can cost upwards of $20,000. A hydroponic-enabled container from Freight Farms costs around $80,000.
But it’s worth the investment.
Abendshein estimates his two farm containers will pay for themselves within four years. And he’s producing environmentally sustainable fresh veggies in a city notorious for its extensive “food deserts.”
Mountains of old, rusted shipping containers are a monument to our insatiable desire for consumer goods and foods from abroad. Reincarnation means these metal boxes don’t go to waste.
Craig and Marc Kielburger are the co-founders of the WE movement, which includes WE Charity, ME to WE Social Enterprise and WE Day. For more dispatches from WE, check out WE Stories.
DD2 Participates In Farm-to School Pilot Program
DD2 Participates In Farm-to School Pilot Program
Inside the container, plants do not have to contend with weather, pests or soil depletion and can grow year round
A new container farm is providing leafy greens to Ashley Ridge High.
The container farm is the result of a partnership working to make sure healthy food is going into students’ mouths – not in the trashcan.
Dorchester District Two, Ashley Ridge High’s agriculture program, Vertical Roots, Tiger Corner Containers and Boxcar Central have joined forces to start a farm-to-school program in the district.
Deb Filomarino, director of nutrition and food services for the district, said the partnership started with Olivia Thompson, public health professor at the College of Charleston. Through Thompson, Filomarino was introduced to Stefanie Swackhamer, general manager of Tiger Corner Farms, and a partnership grew to start the farm-to-school program.
Boxcar, Vertical Roots and Tiger Corner Farms are sister companies. The farm-to-school implementation started at the beginning of the school year.
All the partners celebrated with a kickoff party Oct. 3. Filomarino said she is “over the moon” with the turnout and the number of students and community members who participated.
Thompson said they are going to start collecting data now and look at production costs, the economic impact at schools and a nutritional analysis.
“Ultimately, how do we get the food into students' mouth and not in the trash cans?” she said.
Tiger Corner Containers manufactures the container farm, which is just that – a mobile aeroponic farm system customized with an innovative cloud-based control system that allows growers 24-hour, 365-day monitoring of each plant from seed to sale and the ability to adjust the farm system setting from any computer or mobile device. Tiger Corner Farms Manufacturing is locally-owned and operated in Summerville.
Inside the container, plants do not have to contend with weather, pests or soil depletion and can grow year-round.
Right now the container grows 4,450 heads of lettuce a week. Vertical Roots is growing the produce inside. Boxcar Central builds the technology system that goes into the container.
Ashley Ridge provides the lettuce in the school lunches and also provides it to five other schools; Filomarino said they are reaching potentially 12,000 students.
“This is a model for other districts to adopt,” she said.
Vertical Roots officials said they use no pesticides in the farming, and the whole system uses about eight gallons of water a day. Co-owner Matt Daniels said they can grow anything within reason – right now the container has the proper setup for leafy greens, and every aspect of the indoor environment is controlled by the technology Boxcar set up.
The lettuce is harvested on Monday nights.
The kickoff party consisted of tours of the container farm and catering by GoGo Greens, which offered samplings of two types of salad, a kale smoothie and chocolate pudding – all made with sustainable, organic ingredients.
Eleventh-graders Dalton Mitchum and Colton Matthew try out the kale smoothie.
Ashley Ridge students were also invited to check out the container farm and food samplings – the kale smoothie and chocolate pudding were a big hit; the latter was made from cacao powder, strawberry, avocado and agave.
Eleventh-grade horticulture student Amandadell Mills tried out the pudding.
“It’s actually pretty good. I don’t like avocado but you can’t really taste it,” she said.
Ben Gibson, one of the agriculture teachers at the school, called the partnership an “excellent opportunity” for the school to bring in an outside horticulture business whose goals are similar to the school’s education goals.
Gibson said they are hoping one day they can provide these groups with students who want to work in the business.
“It’s another way to show our kids, 'Hey, this is also horticulture,'” he said.
Heading Off To The Eternal Ice
Heading Off To The Eternal Ice
EDEN ISS Greenhouse En Route to Antarctica
10 October 2017 | Credit: DLR (CC-BY 3.0).
The loading at the port of Hamburg begins
- DLR scientist Paul Zabel moves to the Antarctic for one year with the EDEN ISS greenhouse
- Test run in Bremen produces more than 40 kilograms of fresh vegetables
- Plant cultivation without soil, with optimised light, carbon dioxide content and closed water cycle
- Focus: Space, biosystems
The venture to cultivate plants in the Antarctic is gathering momentum: on 8 October 2017 the special EDEN ISS greenhouse container, packed safely away on a cargo ship, left the Port of Hamburg en route to the Ekström ice shelf in the Antarctic. The journey will last approximately 11 weeks. The EDEN ISS team is expected to receive the high-tech greenhouse at the German Neumayer Station III of the Alfred Wegener Institute (AWI) shortly before Christmas. In this project, the German Aerospace Center (Deutsches Zentrum für Luft- und Raumfahrt; DLR) is collaborating with international partners to investigate the fully self-sufficient cultivation of vegetables to supply food in harsh climatic environments and for future manned missions to the Moon and Mars.
Rich harvest in the trial run
Cucumbers, tomatoes, radishes, peppers, lettuce and herbs flourished in the 12-metre container greenhouse during the trial run from late June until August 2017. "The trial run at the DLR site in Bremen yielded a rich harvest," says Project Coordinator Daniel Schubert from the DLR Institute of Space Systems. "We are confident that everything will proceed smoothly in the harsh environment of the Antarctic as well."
In total, the researchers produced over 40 kilograms of fresh vegetables over the course of the test phase. What makes it so fascinating? There is no loss of water. The only water that leaves the self-sufficient greenhouse system is in the harvested fruits. The rest is recycled and reintroduced into the plants. Under special artificial light, in a temperature-controlled environment without soil and supplied with selected nutrient solutions, the plants can grow faster and more productively than in their natural environment.
Vegetables #MadeinAntarctica
The actual crop cultivation experiment in Antarctica will begin at the end of December 2017. DLR scientist Paul Zabel will move to the Antarctic, where he will live for one year at the Neumayer III research station and work at the EDEN ISS greenhouse. He will be part of the winter crew staffing the Neumayer III Antarctic station operated by the Alfred Wegener Institute (AWI). "Scientists live and working all year round in the research station, despite the harsh Antarctic. During the summer, there are up to 50 people at the station. In the winter, however, only nine people remain there: one cook, three engineers, one doctor and four scientists," says the long-time Station Manager Eberhard Kohlberg. This is the winter team that Zabel will join as the tenth member.
Team colleagues from the EDEN ISS project will help Zabel with the construction and commissioning of the greenhouse, before leaving him in charge of running the greenhouse and cultivating the crops. The harvest during the months of darkness will enrich the diet of the people at the Neumayer III station. At the same time, the project will imitate the supply scenario for a manned mission to Mars.
"The preparations for the winter sojourn are exciting and already account for much of my day's work," says Zabel. “It gives you an idea of just how painstaking the preparations for a space mission are, when every eventuality has to be considered and one must be prepared for everything." Zabel has already completed survival training in the Alps as a member of the Neumayer III winter team. He has also attended a number of seminars on the technical systems at the station and a one-week fire-fighting training course. And there is still a lot of preparatory work ahead before his departure in December.
Food production of the future
Global food production is among the key societal challenges of the 21st century. The world's rising population, coupled with the simultaneous upheaval associated with climate change, demand new methods to cultivate crops, even in climatically inhospitable regions. A closed greenhouse system will enable crop growth independent of the weather, Sun and season in deserts and low-temperature regions – as well as for future manned missions to the Moon and Mars – while also reducing water consumption and eliminating the need for pesticides and insecticides. The EDEN ISS project will put this model for a future greenhouse through its paces for one year during a long-term trial in the extreme conditions of the Antarctic. System assembly is planned for late December 2017 to February 2018. Research operations will follow and are scheduled to run through the Antarctic winter and until December 2018.
International cooperation in EDEN ISS
The EDEN ISS project will be conducted during an overwintering mission at the German Antarctic station Neumayer III, in collaboration with the Alfred Wegener Institute, Helmholtz Center for Polar and Marine Research (AWI). A large number of other international partners are contributing to a research consortium under the auspices of DLR, ensuring that the greenhouse will work smoothly in the Antarctic: Wageningen University and Research (Netherlands), Airbus Defence and Space (Germany), LIQUIFER (Austria), the National Research Council (Italy), the University of Guelph (Canada), Enginsoft (Italy), Thales Alenia Space (Italy), Arescosmo (Italy), Heliospectra (Sweden), the Limerick Institute of Technology (Ireland) and Telespazio (Italy) all form part of the consortium of the EDEN ISS project. The project is financed with funds from the EU Framework Programme for Research and Innovation under project number 636501.
Last modified:
10/10/2017 13:28:37
Contacts
Falk Dambowsky
German Aerospace Centre (DLR)
Media Relations, Aeronautics
Tel.: +49 2203 601-3959
Daniel Schubert
German Aerospace Center (DLR)
DLR Institute of Space Systems
Tel.: +49 421 24420-1136
Paul Zabel
German Aerospace Center (DLR)
DLR Institute of Space Systems
Tel.: +49 421 24420-1273
Dr. Eberhard Kohlberg
Alfred Wegener Institut (AWI)
Tel.: +49 471 4831-1422
How To Invest In Leafy-Green Indoor Agriculture
How To Invest In Leafy-Green Indoor Agriculture
Editor’s Note: B. David Vosburg is CFO and SVP Strategy of Crop One Holdings, an indoor farming technology company and producer of high-quality leafy greens in the Boston, MA area of the US under the brand FreshBox Farms. Vosburg is a serial entrepreneur and has an MBA from Yale University.
The lettuce industry in the US is worth just under $6 billion per year. If it follows the tomato industry, 50% of leafy greens will be grown indoors by 2030, a $3 billion opportunity. This transformation is inevitable with the ongoing trend of higher efficiency LEDs.
Indoor farming in cities and suburbs is giving new meaning to the term “local.” These operations are producing crops which had previously been grown only in certain geographies, because of the constraints of available land, water, and weather. This industry is now able to grow anything year-round, anywhere in the world.
In our growing units, we have measured a 99% reduction in water usage, and a 90%+ reduction in land use, compared to Salinas Valley lettuce farms, and since most indoor operations grow locally without any pesticides/herbicides/fungicides and 30 day+ shelf lives, indoor farming is a difficult proposition not to believe in.
And investors are starting to put some big bucks behind it. Indoor farming startups growing fruits and vegetables globally have raised $285 million since the start of 2017, with particularly large rounds for US-based vertical farms pushing the sector to its highest ever investment levels, according to AgFunder data.
The question is, who will win this market in the end?
No doubt you’ve seen several indoor agriculture companies that claim to be the best at growing leafy greens (lettuces, herbs, etc.) indoors. For any number of reasons, they claim to be better than their peers who are also vying for your funding dollars. But how do you tell the difference between them?
Here are seven simple metrics that will tell you if the company is worth your investment dollars.
1. Capital Density (CAPEX/plant site)
Most companies will tell you they grow more capital efficiently than everyone else, but you have to do the math. Calculate the number of plant sites they have per square foot, and the CAPEX required (all-inclusive) to build/buy that square foot of grow space.
Things to look for include companies that grow in vertical channels: the encasement and spacing take up so much space, they’re not able to achieve anything close to market-leading densities. Think cubic feet, not square feet.
If then it appears that that company is growing produce for a fraction of their competition’s Capex per farm, you will know they have a better ability to scale and turn over capital faster. For example, if a company grows for 25% of their competition’s CAPEX/plant site – the farm location — they can scale to four times the size with the same capital and will turn over that capital four times as fast.
2. Form Factor
There are now many players in the space building indoor farms in various formats: Pond greenhouses, Aquaponics, Warehouse growers, and Modular growers; each with its own inherent set of risks, particularly around contamination.
Pond greenhouses grow with sunlight — and at times some LED augmentation — in one, large single pond. They are the most susceptible to contamination as all plants share the same room. From a build-out perspective, it can take over 2.5 years to build one farm!
Aquaponics growers do control for contamination. However, plants are provided nutrients from fish feces, which can lead to contamination. The water temperature at which fish live is in the upper 70s Fahrenheit, several degrees above what is ideal for lettuce, so these growers will be limited in what they can grow and the yields they can achieve.
Warehouse growers can mass produce plants because they can grow them at high density to be some of the most efficient indoor farmers. Contamination can be a risk here as well; if a pest gets into a warehouse, an entire building of produce could be lost or recalled, costing the company tens or hundreds of thousands of dollars. There are several examples of hydroponic warehouse growers that have lost entire operations to a single pest or pathogen.
Modular growers come in many flavors, from divided warehouses to shipping containers. These growers can find a balance between controlling for infestation while growing efficiently. They can also match warehouse growers for density. In whatever shape or size they come, this appears to be the preferred growing approach for indoor farming – assuming that density inside the modular unit can be achieved. However, watch out for modular growers that sub-divide their farms into too many rooms as this will increase labor costs.
Be aware of form factors and decide which style best suits your investment needs.
3. Energy Efficiency (g/KWH)
Energy can be one of the most expensive components, if not the most expensive, of a completely indoor growing operation. This is a large part of the input costs of a labor efficient, completely indoor, growing operation. The common unit of measurement is how many grams of product a company can grow with one KWH of energy input.
What to watch for: many US companies have access to state-level agricultural energy pricing which can be as low as $.015 per KWH. Make sure the company is not ‘efficient’ because they simply have a low energy rate. We’ve all suffered through the end of subsidies in other industries, especially clean-tech!
Identify the number of grams that can be grown on the farm in a given month, then divide this by the number of KWH consumed per month. If the number is south of 40 or 50 – half the peak scientists have achieved in R&D labs– do not proceed unless there is a very clear technology roadmap showing how the company will achieve higher numbers soon.
4. Automation
Hiring is another expensive cost for indoor growers and will only increase in many urban places where indoor agriculture is applied. Automation is, therefore, going to become a critical aspect of reducing costs to increase gross margins. Some of the questions to ask:
1. How many dollars are spent in labor to grow one pound of lettuce?
2. How many hours does it take one person to seed, transplant, harvest, pack, and clean per unit of production?
3. Does the company use automation, and do they own that technology?
4. What is the company doing to find experienced/appropriate labor?
5. Plant Science
Farms grow living organisms. This is not an industry that produces widgets, no matter what anyone tells you. An experienced plant scientist is critical to any successful indoor farm. Identify this person and understand their background, knowledge, experience, and ability to control mold/fungus/pests as well as grow indoors in controlled environment and leverage plant stressors for yield.
The right person will understand every lever that can be pulled to increase yield and reduce costs: light spectrum, humidity, CO2, various micro-nutrients, water oxygenation, micro-pulsing, shadow-less lighting, sunsetting/sunrising, photoperiod and much more. This can contribute to a 50%-75% increase in yield over the competition, something competitors cannot finance their way out of.
Look for companies building competitive advantages around the non-commoditized aspects of growing – lighting, HVAC, and automation have plenty of very clever people around the world focused on improving efficiency in their own industries.
6. Commercial Approach
Brand is King. Those who have the consumer’s mindshare will be the ones to take home the value. Currently, grocery stores in the US are white-labeling many leafy green products so they can switch suppliers at will and reduce retail costs while maintaining margins. The consumer and the grocery store benefit; lettuce growers do not.
If the consumer is unaware of the brand, the company is not worth financing and will never be able to have the leverage to negotiate the price necessary for a venture return — and possibly not even a profitable business.
Ask a company about its consumer-facing products or plans.
7. Speed of Evolution
How quickly can a company change technologies? LEDs, farm management practices, controls and different types of automation are developing exponentially, industry-wide. Can you responsibly invest in a company that takes over two years to build out infrastructure?
The number of lumens/watt an LED produces is projected to quadruple in the next fifteen years, an annual compounded efficiency improvement rate of 10%. This means investing in a two-year project today will result in having lighting technology that is 21% less efficient than new entrants.
Keep track of technological advances and ask companies how they’re planning to stay on top.
Leafy Green Machine Growing Garden-Fresh Veggies At CHS
Leafy Green Machine Growing Garden-Fresh Veggies At CHS
Vegetables grow in verticle towers, maximizing space in the growing unit.
9/27/2017
Indoor facility first in state at public school
By ETHAN SHOREY, Valley Breeze Managing Editor
CUMBERLAND – A modified shipping container capable of producing a football field’s worth of vegetables every seven weeks now stands outside the kitchen door at Cumberland High School.
The Leafy Green Machine, as it’s called, will bring fresh vegetables to the plates of students at CHS and across the school district, making Cumberland the first public school district in Rhode Island to boast such a facility, according to those who will run it.
Shauna Spillane, food service director for local provider Sodexo, said the hydroponic growing facility is essentially like a “smart home” for food, a “really awesome” facility that keeps vegetables in ideal growing conditions at all times. When it gets too hot in the growing container, the LED lights shut off and the AC comes on. Only the amount of light needed for photosynthesis is used. Air quality is constantly monitored and controlled.
The money to purchase the grow box from Boston-based Freight Farms came out of the food service budget.
Sodexo will manage the growing and picking of vegetables for daily use, but students will be invited to participate in the process. CHS administrators eventually hope to have an agriculture pathway at the school, teaching students about sustainable growing and horticulture.
The Leafy Green Machine, or LGM, allows a variety of crops to be grown regardless of weather conditions, providing students with year-round access to local and fresh produce. Vegetables are grown in vertical rows, requiring minimal water and electricity to flourish. Water drips from overhead spouts onto strips, going down vertical columns to give vegetables exactly the amount that they need. The water then falls into a trough, where it is pumped out.
Gina Rodriguez, food service manager for Sodexo, said employees have typically struggled a bit to put fresh vegetables on the table all winter. Last year was particularly bad, as vegetables often had to be thrown out because they didn’t last, she said.
With the LGM, workers will “pick today for tomorrow,” said Rodriguez. Vegetables typically start losing nutrients the moment they’re picked, she said. The difference will be noticeable in the vegetables picked from the LGM, as they’ll taste better, be a brighter green, and provide more nutrition for students. Because the container is insulated and climate-controlled (about 65 degrees), the entire system uses just five gallons of water a week.
Sodexo currently uses about 200 pounds of leafy greens, mostly for salads, across all schools in Cumberland, including at Blackstone Valley Prep charter school, said Rodriguez. The vegetables harvested from the LGM will be used to supplement the supply.
The entire plant-to-harvest process takes about seven weeks, meaning it can be done several times in a year.
Optimized to grow lettuce, herbs or greens such as kale or Swiss chard, the LGM will initially grow kale and Romaine lettuce at CHS. Spillane said adding something like basil changes the dynamics inside the LGM, because growing the herb calls for slightly different conditions.
The Farmhand App makes farming easier by monitoring, controlling and tracking the indoor farm remotely. Rolling racks allow workers to move the plants for easier access.
Though the LGM is a rarity at public high schools, a number of colleges in New England, including Clark University in Worcester, Mass., have them.
Over the course of a year, the 320-square-foot LGM can grow the same amount of food as about 2 acres of land. Freight Farms, which produces the LGM, promotes its product as a way to grow food in almost any condition all around the world.
The inside of a Leafy Green Machine shows the full operation of vertical gardens, bathed in LED light.
Shauna Spillane, left, and Gina Rodriguez, of Sodexo Food Service, show off the new Green Leafy Machine outside the door of the kitchen at Cumberland High School. The former storage container will be used to grow vegetables for the school’s food service. (Breeze photo by Ethan Shorey)
Antarctica Is Getting A Farm That Can Grow Produce Even When It's -100 Degrees Fahrenheit Outside — Take A Look
But engineers at the German Aerospace Center (GAC) will soon build a high-tech farm that will allow Antarcticans to harvest produce.
Antarctica Is Getting A Farm That Can Grow Produce Even When It's -100 Degrees Fahrenheit Outside — Take A Look
German Aerospace Center scientist Paul Zabel inside Eden-ISS.DLR German Aerospace Center
Antarctica's nonstop winters make it impossible to grow food outdoors. Fruits and vegetables are instead shipped long distances from overseas, just a few times per year.
But engineers at the German Aerospace Center (GAC) will soon build a high-tech farm that will allow Antarcticans to harvest produce.
The farm will feature a year-round greenhouse that can grow food for researchers at the Neumayer III polar station on the Ekstrom Ice Shelf.
Called the Eden-ISS, the farm exists inside a climate-controlled shipping container. The greenhouse relies ona technique called vertical farming, in which food grows on trays or hanging modules under LEDs instead of natural sunlight.
Take a look at the farm, which will come to Antarctica in October, below.
Before the Eden-ISS shipping container farm debuts in Antarctica, the GAC is testing growing fruits and vegetables at its headquarters in Bremen, Germany.
The Eden-ISS in Bremen, Germany.DLR German Aerospace Center
The 135-square-foot farm can grow all sorts of produce indoors. Harvesting food outdoors is impossible in Antarctica due to its endless winters.
DLR German Aerospace Center
The only way to get produce to McMurdo, the US station where the majority of Antarctic researchers stay, is by ship or plane. In January, a shipment of dried and frozen food is delivered, and during summer, planes come with fresh food around once a week, according to Atlas Obscura.
GAC scientist Paul Zabel will move with the farm to Antarctica, where he will grow fruits and vegetables under 42 LED lamps.
German Aerospace Center scientist Paul Zabel.DLR German Aerospace Center
Since the farm is climate-controlled, it can grow crops year-round in a place where temperatures can plummet as low as -100 degrees Fahrenheit.
DLR German Aerospace Center
As Modern Farmer notes, some sub-Arctic regions are experiencing somewhat of an agricultural boom, due partly to climate change.
Over the past 100 years, Arctic temperatures have increased at nearly twice the global average, making it possible to grow crops in once-desolate places like Yellowknife in Canada and Greenland.
In order to help the plants thrive, the researchers pump in extra carbon dioxide and set the temperature at 75 degrees Fahrenheit.
DLR German Aerospace Center
The LEDs are tuned to red and blue wavelengths — the optimal light frequencies for growing produce.
DLR German Aerospace Center
The crops are stacked on trays. Every few minutes, they receive a spritz of nutrient-rich mist.
DLR German Aerospace Center
The researchers plan to grow between 30 and 50 different species, including leafy greens, peppers, strawberries, radishes, and tomatoes, as well as herbs like basil and parsley.
DLR German Aerospace Center
In July, the team grew its first cucumber, which measured 96 grams and 14 centimeters long, inside Eden-ISS.
DLR German Aerospace Center
In February, the GAC built the farm's platform by crane in Antarctica. Everything else will arrive next month.
DLR German Aerospace Center
The larger goal of the Eden-ISS project is to create a system that allows GAC astronauts to harvest food in space.
DLR German Aerospace Center
If the researchers can perfect a growing process for Antarctica's harsh climate, they may stand a chance at growing on Mars or the moon.
DLR German Aerospace Center