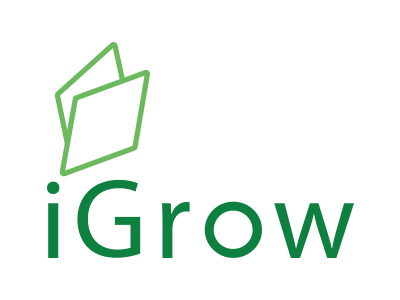
Welcome to iGrow News, Your Source for the World of Indoor Vertical Farming
H-E-B-Owned Central Market Partners With CEA Advisors and Growtainer® For Store Grown Initiative
H-E-B-Owned Central Market Partners With CEA Advisors and Growtainer® For Store Grown Initiative
Friday, May. 19th, 2017
DALLAS, TX – After more than a year of planning between Central Market’s Produce Marketing team and CEA Advisors, the two companies have announced the completing of the first custom built onsite production Growtainer®. Central Market’s new Store Grown Produce program is in effect and turning out fresh leafy greens, herbs, and spices for Central Market customers in Dallas.
Glenn Behrman, Founder, Greentech Agro LLC and CEA Advisors LLC.
“We spent over a year discussing [Central Market’s] concerns and objectives, and when I was sure we were all on the same page, we began the design and manufacturing process” said Glenn Behrman, Founder of Greentech Agro LLC and CEA Advisors LLC.
The state-of-the-art 53-foot custom-built Growtainer provides 480-square-feet of climate-controlled vertical production space designed for maximum efficiency and food safety compliance. The miniature production facility features a dedicated proprietary technology for ebb and flow irrigation and a state-of-the-art water monitoring system, and its Growracks® are equipped with energy efficient LED production modules specifically designed for multilayer cultivation.
Growtainer
According to a press release, Central Market—the Texas-based upscale grocery banner owned by H-E-B—is currently using its Growtainer setup in an effort to “produce the freshest, unique, gourmet leafy greens and herbs for Central Market customers at the retail level.” The release noted that Central Market and CEA Advisors have worked closely with Chris Higgins and Tyler Baras of premier horticultural supplier Hort Americas to train the Central Market associates to operate a food safety compliant, climate controlled, LED-lit, multi-layer vertical indoor production environment.
Central Market storefront
“CEA Advisors is proud to be working with the Produce Team at Central Market, all committed to innovation and focused on food safety, unique products, and the customer experience” said Behrman.
GreenGro Technologies, Inc. (GRNH: OTC Pink Current) | Greengro Technologies, Inc. Retains Investor Relations Partners to Support Company's Strategic IR Program
GreenGro Technologies, Inc. (GRNH: OTC Pink Current) | Greengro Technologies, Inc. Retains Investor Relations Partners to Support Company's Strategic IR Program
May 25, 2017
OTC Disclosure & News Service
ANAHEIM, Calif., May 25, 2017 (GLOBE NEWSWIRE) — Greengro Technologies, Inc. (OTC:GRNH), a leader in the indoor agriculture technology market, today announced that it has retained Investor Relations Partners (IRP), one of the fastest growth investor and public relations firms in the nation, to expand the Company’s strategic investor relations program.
“GreenGro Technologies is at the forefront of the burgeoning indoor agriculture technology market. Our business units cover the entire indoor agriculture supply chain from developing growing technology to growing structures, plant processing, distribution and sales,” said Jim Haas, Chief Executive Officer of GreenGro Technologies, Inc. “In the past few months we have made a number of strategic acquisitions and partnerships and built what we believe is a solid pipeline of significant deals. However, the market has yet to grasp our unique strategy and the enormous role we expect to play in the indoor agriculture market. We have retained IRP to help communicate the series of expected positive developments to the investment community in an effort to significantly increase our exposure as well as support our overriding goal of building shareholder value,” concluded Mr. Haas.
To be added to the Company’s investor lists, please contact Bill Miller at Investor Relations Partners at 844-565-5665 or via email at bmiller@irpartnersinc.com.
About Greengro Technologies
Greengro Technologies (OTC:GRNH) is a world class provider of eco-friendly green technologies with specific domain expertise in indoor and outdoor agricultural science systems serving both the consumer and commercial farming markets. It brings together community and commerce through the growth and distribution of healthy, nutritious foods and vital medicines backed by science and technology. Customers include restaurants, community gardens, small and large scale commercial clients. Greengro Technologies also provides design, construction and maintenance services to large grow and cultivation operations and collectives in the medical and recreational marijuana sectors.
The company’s websites: www.greengrotech.com, offer regular updates including educational videos, projects updates, recipes and nutritional information, and where to find the company’s products. https://www.facebook.com/GreengroTechnologiesInc.
About Investor Relations Partners
Investor Relations Partners, Inc. (IRP) is a full-service investor relations firm serving a global client base. The principals of IRP have received top industry awards for their investor relations programs for a number of high-profile companies, including, but not limited to, Starwood Hotels & Resorts Worldwide, ValueVision Media, Taro Pharmaceuticals, and LJ International. The firm’s principals have executed effective investor relations programs for dozens of public companies, ranging from emerging micro-cap companies to multinational corporations with market capitalizations in excess of $15 billion. For further information on IRP, please visit the firm’s Website at www.irpartnersinc.com.
Forward Looking Statements
This release may contain forward-looking statements. Actual results may differ from those projected due to a number of risks and uncertainties, including, but not limited to, the possibility that some or all of the matters and transactions considered by the Company may not proceed as contemplated, and by all other matters specified in the Company’s filings with the Securities and Exchange Commission. These statements are made based upon current expectations that are subject to risk and uncertainty. The Company does not undertake to update forward-looking statements in this news release to reflect actual results, changes in assumptions or changes in other factors affecting such forward-looking information. Assumptions and other information that could cause results to differ from those set forth in the forward-looking information can be found in the Company’s filings with the Securities and Exchange Commission (www.sec.gov), including its recent periodic reports.
Investor/Media Contact: Bill Miller Investor Relations Partners Phone: 844-565-5665 bmiller@irpartnersinc.com
Copyright © 2017 GlobeNewswire. All Rights Reserved
This Texas Supermarket Is Growing Its Own Veggies In A Shipping Container Farm
This Texas Supermarket Is Growing Its Own Veggies In A Shipping Container Farm
Agriculture, Carousel Showcase, News, Sustainable Food, Urban Farming
A Texas chain of supermarkets isn’t just in the business of selling vegetables; it’s growing them, too. Based in Dallas, the H-E-B-owned Central Market has joined forces with Controlled Environment Agriculture Advisors, a self-described “horticulture disrupting” firm, to raise some of its produce in a custom-built onsite shipping container—a first for an American food retailer.
The 53-foot-long “Growtainer” features 480 square feet of climate-controlled and food-compliant vertical space designed to achieve a higher yield in a shorter time than conventional methods, according to GreenTech Agro, the system’s manufacturer.
Related: Belgian supermarket unveils plan to sell food grown on their own rooftop garden
“We spent over a year discussing [Central Market’s] concerns and objectives, and when I was sure we were all on the same page, we began the design and manufacturing process,” said Glenn Behrman, founder of GreenTech Agro and CEA Advisors, in a statement.
The miniature farm comes with a modular, self-contained series of LED-lit aluminum “GrowRacks” that supports any number of cultivation levels.
Related: Pop-up shipping container farm puts a full acre of lettuce in your backyard
It also offers an intelligent water-monitoring system, as well a zoned irrigation system that meets the needs of different varieties of produce at different stages of growth.
The Growtainer is part of Central Market’s efforts to “produce the freshest, unique, gourmet leafy greens and herbs for Central Market customers at the retail level,” the supermarket said. The hyper-local vegetables are marketed under the label “Store-Grown Produce.”
Related: Freight Farms are super efficient hydroponic farms built inside shipping containers
“CEA Advisors is proud to be working with the Produce Team at Central Market, all committed to innovation and focused on food safety, unique products, and the customer experience,” Behrman added.
Sustainable Indoor Farm Aims To Grow The Most Delicious Produce
Sustainable Indoor Farm Aims To Grow The Most Delicious Produce
A San Francisco startup is creating an indoor vertical farm that aspires to produce crops more efficiently and sustainably than traditional farms
- 25 MAY 2017
Indoor vertical farming startup Plenty wants to transform the way greens are produced. The company, headquartered in San Francisco, has created 20-foot towers of rare herbs and greens—including special kinds of basil, chives, mizuna, red leaf lettuce and Siberian kale—that are not frequently available at the average grocery store because of their high production costs.
“When you’re not outside and you’re no longer constrained by the sun, you can do things that make it easier for humans to do work and work faster, and for machines to work faster,” Plenty CEO and co-founder Matt Barnard told Fast Company. The company claims it can grow crops up to 350 times more effectively than conventional farms in a given area. Indoor vertical farms are more energy- and space-efficient, Barnard says, producing the same output as fairly large farms in a far smaller space. He believes that the indoor farming process, once perfected, may become more sustainable than traditional farms.
Plenty is attempting to put ever-improving technology toward its success and plans to build farms near large cities so it can fit into existing supply chains that deliver to city limits. Faster delivery means better food, preserving both flavor and nutrients. Indoor farming also has the potential to be more sustainable by using solar energy and cutting down on the costs and pollutants of traditional supply chains.
The Spacepot Hydroponic Planter Brings NASA Grade Farming To Your Kitchen
The Spacepot Hydroponic Planter Brings NASA Grade Farming To Your Kitchen
May 20, 2017
Qhilst cooking with fresh herbs is a simple pleasure, most novice urban farmers have never known a basil pot to last more than a few months. that’s why futurefarms have turned to NASA’s hydroponic farming techniques to revolutionize herb growing for the not-so-green-thumbed. reforming space-grade science into an elegant kitchen planter called a ‘spacepot’, futurefarms have set out to downsize the extraterrestrial farming technique into an elegant tabletop planter that grows perfect herbs in just 5 weeks, with almost zero maintenance.
hydroponic farming—that’s the art of growing plants without soil—was first popularized by NASA. widely associated with futuristic space gardens, by cutting out the soil from the equation hydroponic farms provide their plants directly with nutrients, cutting out the middle man to create bigger, healthier shrubs that grow much faster than their soil-situated counterparts. maybe it’s the their extraterrestrial connotoations, or the fact they always seem to be kitted out with endless complicated pumps and tubes, but when it comes to hydroponic farming, until now it’s been widely accepted that you do, indeed, need to be a rocket scientist to master the technique. and that’s a stigmatism futurefarms set out to change with their ‘spacepots’—elegant, hydroponic planters that bring the benefits of soil-free farming to the masses.
branded ‘hydroponics beautifully simplified’ the spacepot required no pumps, no electricity, and no extra parts to maintain. by mixing space-age technology with cutting edge design, futurefarms have crafted a planted that delivers all the benefits of hydroponics without any of the maintenence. by using the kratky method—the simplest, most hands-off way for gardening—all the spacepot requires from you is to fill the reservoir with water and nutrients, plant a seed, and watch your beautiful plant flourish in just five weeks. fashioned of high-clarity acrylic and food-grade PET,the planter’s aesthetic is designed to represent its functionality—easy and simple.
futurefarms–the LA based startup behind the futuristic and fashionable approach to gardening–comprises a team of designers, creators, and researches leading the field of personal hydroponics. ‘on a macro scale,’ they explain, ‘our mission is to have hydroponics be a part of everyone’s lives because we believe it makes us smarter, and more conscious of our health and well-being.’
beatrice murray-nag I designboom
may 20, 2017
Japan’s New Approach To Farming Without Soil
Japan’s New Approach To Farming Without Soil
By Siyanda Sishuba
May 22, 2017 12:05 pm
Japanese experts have made a breakthrough in agricultural technology, using polymer film to grow food.
Yuichi Mori, the chemical physicist who founded Mebiol in 1995. He spent most of his career developing polymer technologies for the medical industry.
Photo: Drop Farm
Dubbed Imec, the innovation, developed by Mebiol’s Dr Yuichi Mori, makes it possible to grow crops ‘virtually anywhere’, according to a report from the Japanese government. Mebiol is a technology corporation based in Tokyo.
The report describes ‘film farming’ as using “waterproof sheets to separate the crops being cultivated from the ground underneath”.
It continues, outlining the basics of what it says is a ‘simple system’: “The special features of the new technology are to be found in the film, which is made of hydrogel, a hydrophilic polymer gel used in disposable diapers and other products. The film’s design incorporates nano-sized (one millionth of a millimetre) pores, which absorb water and nutrients but block germs and viruses. This means only small amounts of agricultural chemicals are needed, ensuring the crops are safe to eat.”
“As the film holds on to water, it also makes the plants work harder to get it by increasing osmotic pressure; the plants create more amino acids and sugar, and so they taste better and have higher nutritional value.”
Ali Adnan, senior adviser at Mebiol, said 150 farms around Japan have introduced the technology, with “over 10 already deployed in China”.
He added that “future projects within the next 12 months are forecasted to be installed in Germany, Saudi Arabia, Qatar, and several other countries are in the pipeline for approval”.
Imec is already being used to grow tomatoes around Japan and at overseas locations, including Shanghai, Singapore, and Dubai.
More than 50% of the farmers in Japan come from a non-farming background, and, according to Adnan, “they say that the system is easy to use and enables them to produce high-quality produce”.
With its ‘easy-to-use’ aspect, Imec may prove a boon to small-scale and even urban farmers in South Africa, and Adnan says that, “Farmers in South Africa can access our technology. We will first need to export the simple system and film from Japan.”
For more information about Imec, visit www.mebiol.co.jp/en
Urban Agriculture: Growing Network Wants to Make City Farming Easier
Urban Agriculture: Growing Network Wants to Make City Farming Easier
Courtesy photo This photo from Grow Pittsburgh shows an urban agriculture area in the city.
MAY 24, 2017
CHERIE HICKS - Staff Writer - chicks@altoonamirror.com
Living in the city doesn’t mean you can’t raise a wide variety of your own food. And a growing network of urban agricultural interests in Blair County is trying to make it easier.
Kick-started by a grant last year and joining a nationwide movement, the Blair County Urban Ag Program already has pulled together more than 100 members from different groups — schools, churches, governmental organizations, nonprofit agencies, homeowners, farming interests and more. They are sharing how-to information from raising backyard chickens to gardening with organic practices, and they’re taking lessons from Pittsburgh.
“We’re surrounded by all these big farms, but people living in the city of Altoona are going hungry … because they live in a food desert,” said Beth Futrick, an ombudsman with the Blair County Conservation District and recipient of a $46,000 grant last year to start the urban ag program.
“Food deserts” are large pockets of residences at least a mile from a supermarket or large grocery store where fresh food can be purchased, she said.
“Too many poor people lack transportation to get to Weis so they walk to the closest convenience store” and purchase prepared, processed food, according to Futrick.
Last year, she enlisted the Healthy Blair County Coalition and organized the network’s first event, a tour of a community garden in State College. More than 30 people in the medical field, schools, WIC and other social programs showed up, Futrick said, with one common goal: How to get healthier foods to their customers, their clients, their patients, their students.
“We are trying to reach out to as many people as we can and build a network.”
The grant helps pay for her salary, as well as a consultant, speakers and other education programs, especially to get the word out about the programs, she said.
Tyrone Milling, for example, held a seminar on how to raise backyard chickens, and the network promoted the idea. It is legal to raise chickens in your backyard in Altoona, said Planning Director Lee Slusser, who noted that goats, chickens and rabbits are “great urban animals.”
The City of Altoona mulled an animal husbandry ordinance similar to Pittsburgh’s, but there haven’t been very many complaints so it got shelved for the time being, said Slusser, who is an active member of the urban ag network.
But it still would be unwise, Futrick said, for city residents to have a rooster.
“My dad had a rooster that at 3 o’clock in the morning would go ‘cockadoodle doo’,” she said. “Don’t make your neighbors upset.”
Futrick noted that Pennsylvania has a right-to-farm law that prevents municipalities from getting too strict, though.
“We can regulate how many animals you can own,” such as one cow per acre, Slusser said. “But we can’t ban it outright.”
Another major component of the urban ag network is the Society of St. Vincent DePaul, which has operated the nonprofit Monastery Community Gardens south of Hollidaysburg since 2008. In addition to growing produce for local food banks, the society rents out garden plots and a few are still available this season for $25 or $40. (Contact Kathy Saller at ksaller@netzero.com).
It also sponsors regular gardening classes in conjunction with the urban ag network.
The next education event, a workshop sponsored by the National Association of Conservation Districts, will discuss indoor farming techniques from 9 a.m. to 2:30 p.m. on June 12 at the Logan Valley Mall Community Room. The deadline to register is June 1. Area experts will discuss hydroponics (growing plants without soil); aquaponics (dealing with the relationship between aquaculture, or farming fish, and hydroponics); Bokashi composting (an anaerobic composting method for kitchen scraps, including dairy and meat); and growing microgreens, the immature shoots of edible plants. A $15 fee to attend includes lunch and education credits are available.
A bus trip to Pittsburgh on June 28 ($30 per person) will include visits to several programs of the Grow Pittsburgh program, which formally organized in 2008 and today has 18 full-time staff members.
“We really think about growing food across the city, among all different ages and in all different kinds of communities,” said Jake Seltman, executive director.
Its programs include urban gardens and school gardens, and it provides resources for community gardens throughout Pittsburgh, having started more than 60 of them before turning over their sustainable operations to the communities in which they’re located, he said.
“We provide a lot of resources,” Seltman continued. “We share best practices and make it easier for people to grow their own food.”
Its website (www .GrowPittsburgh.org) is full of resources for urban dwellers.
The Blair urban ag program specifically will visit the Grow Pittsburgh’s Braddock Urban Farm, as well as the Allegheny County Courthouse’s rooftop garden, the Phipps Conserva-tory and Botanical Gardens’ Center for Sustainable Landscapes and the Phipps’ Homegrown program at the Homewood YMCA.
Among the lessons Futrick said she hopes the network can teach to consumers is an understanding of growing seasons and which crops are available here and when.
“They want corn in April,” she said. “We just need to do some customer education. We shouldn’t buy so much from California. There it’s picked to travel, not for good taste.
“We can grow really nice stuff here in Pennsylvania.”
Mirror Staff Writer Cherie Hicks is at 949-7030.
Indoor Farming: On To Pastures New
Indoor Farming: On To Pastures New
24 May 2017 | By Mia Hunt
In the drive for sustainability, new operators are looking to indoor farming to bring food closer to consumers.
Indoor farming - a low-energy, low-water-use way of growing food - Source: Mandy Zammit
Asked to imagine a farm, most people will think of vast green fields filled with neat lines of crops, grazing animals and a tractor trundling along in the distance.
It’s an idyllic visualisation that would be shattered if you were told that the farm were, in fact, on an industrial estate on the edge of a major conurbation.
Say hello to indoor - or vertical - farming, an emerging sector that aims to produce food sustainably, without sunlight or soil and, crucially, close to the retailers that will sell it and the consumers who will eat it.
It is a concept still very much in its infancy, but if this new farming method takes hold, warehouse space will be high on the shopping lists of these new operators. So what is indoor farming? And what are operators’ requirements?
Indoor farming is sustainable and uses less transport. Those who are doing it now are the forward-thinking food producers - David Binks, Cushman & Wakefield
“This is very much a new, emerging sector,” says David Binks, a partner in the industrial team at Cushman & Wakefield.
“The thinking driving this trend is to move food production closer to the source of customers. It’s sustainable and uses less transport, which is a very positive thing. Those who are doing it now are the forward-thinking food producers.”
GrowUp Urban Farms is one such operator.
A year ago it opened Unit84, an indoor farm in an industrial warehouse in Beckton, east London, that had previously lain vacant for 18 months. It claims it is the UK’s first aquaponic, vertical farm.
The farm combines two well-established farming practices: aquaculture, a method of farming fish, and hydroponics, whereby plants are grown in a nutrient solution without soil. It is a low-energy, low-water-use way of growing food that is especially suited to high-density urban agriculture.
The farm’s 6,000 sq ft of growing space produces more than 20,000kg of salads and herbs - enough to fill 200,000 salad bags - and 4,000kg of fish each year. And according to chief executive and co-founder Kate Hofman, GrowUp’s next project will be “10 times bigger”.
“I set up GrowUp with COO and co-founder Tom Webster four years ago,” Hofman explains. “We have different career backgrounds - he was a sustainability consultant for an engineering firm and I was a strategy consultant - but we were both interested in making sustainable urban food production commercially viable.”
Food For Thought
The pair took over the warehouse at London Industrial Park in May 2015 and launched after a comprehensive six-month fit-out process.
“Our 600 sq m [6,500 sq ft] hydro room alone provides 8,000 sq m of growing space because we’re able to grow up as well as along,” says Hofman. “And because it isn’t dependent on environmental and climate factors, we can produce salads of consistent quality 365 days a year.”
Now that Unit84 is fully up and running, Hofman and Webster are looking ahead to their next project - a considerably larger farm for which the firm will soon work up a design that will enable it to make even more efficient use of space. This next farm will be the blueprint for a model that can be rolled out to many different locations on a franchise basis.
Indoor farming uses hydroponics, whereby plants are grown in a nutrient solution without soil - Source: Mandy Zammit
Hofman says a standard warehouse is the ideal place for vertical farming and lists requirements similar to those of light industry, including locations within easy reach of customers - GrowUp distributes all of its produce itself using electric vehicles - and with good access and packing space.
“From what I’ve seen, read and heard, these operators need decent utility access - predominantly renewable energy to power the artificial lights that are used in place of sunlight - although they require very little water, significantly less than a traditional farm,” says Binks. “They need to be heated and cooled efficiently. And because they use a degree of technology to support the growing methods, that may be a consideration in their requirements.”
Looking Up
Binks believes old multi-level industrial buildings are well suited to vertical farming. “Former textile factories and other such buildings built in the early 1900s on the outskirts of towns and therefore in close proximity to the customer base would probably work well,” he says. “If they are at a cost base that is affordable for these operators, they could potentially bring very old, dilapidated buildings that have been redundant for years back into use.”
However, he highlights that residential developers are often at the front of the queue for these types of buildings and, as such, indoor farming operators could struggle to secure buildings.
“It’s a challenge and it could be a barrier to entry,” he says. “But where they find the right building in the right location that hasn’t been earmarked for residential use, I don’t see why they couldn’t bring it forward. They might also occupy fairly new industrial buildings with mezzanines.”
Source: Mandy Zammit
New buildings are a consideration for GrowUp. Hofman explains that they could convert an old warehouse, depending on the age and quality of the building, but the retrofitting costs are huge, so it could look to partner with developers to create the right space for its specific needs from scratch. And it isn’t only industrial space that is on GrowUp’s shopping list. It could also operate from big-box units on retail parks.
“At a time when businesses are becoming increasingly streamlined operationally and focusing on last-mile delivery, huge out-of-town retail spaces could become vacant,” says Hofman. “Landlords are already looking for alternative uses - we could be it.”
We are utilising ways of growing food that make sense commercially and environmentally - Kate Hofman, GrowUp
When it comes to planning, the sustainability and community benefits of indoor farming are such that Binks believes local authorities would be in favour of vertical farming uses. However, there is a caveat.
“There is some debate as to how employment generative they are,” he says.
“If they use automatic feeding systems, there might only be a need for a handful of year-round on-site staff and a short-term need for extra staff during the picking season. Operators may have to persuade councils that it’s a good thing for their boroughs.”
Question Marks
Planning isn’t the only potential hurdle that may need to be overcome. While it can be done profitably, Binks says this new farming technique is so innovative that thus far it is only private investors who are investing in it.
Aquaculture is a method of farming fish -Source: Mandy Zammit
“There is a question mark over the covenant strength of these types of occupiers,” he explains. “For now, the sector is so new that landlords and developers aren’t considering this to be a new or potential major occupier category. But perhaps they ought to be - indoor farming is flying under the radar.” He adds that the landed estates might pursue these tenants in a bid to showcase a forward-thinking approach.
As for the future, a number of factors could accelerate the growth of these types of farm, as Hofman explains: “Brexit could have an impact on imported foods and imported labour. Couple that with climate changes affecting farming in countries that supply the UK with much of its produce, including floods in Spain and droughts in California, and a growing desire by retailers to sell and consumers to eat locally produced food, and I see this [indoor farming] as the answer. We are utilising ways of growing food that make sense environmentally and commercially - it is an attractive investment.”
There may be questions over the viability of indoor farming but, in a changing world, its future could well be bright. This new method of food production has not yet piqued the interest of industrial landlords or institutional investors - but perhaps now is the time to take notice of a trend that is likely to grow.
Mucci Farms Gears Up For Growth With New Private Equity Partnership
Mucci Farms Gears Up For Growth With New Private Equity Partnership
Mucci Farms has announced a partnership with NOVACAP, one of Canada’s leading private equity firms.
“We are very excited to be partnering with NOVACAP who, with its resources and expertise, will provide invaluable support to our company as we enter this next phase of growth", said Bert Mucci, President of Mucci. “This partnership will allow us to focus on operations and growth as we aim to become the preferred quality supplier of our industry”.
Located in Kingsville, Ontario, Mucci grows its own produce and is involved in marketing over 700 acres of greenhouse produce from growers throughout North America. The company also operates warehouse and distribution facilities in Ontario and Michigan. Mucci is Kingsville’s largest employer with more than 1,200 full-time employees.
“This partnership is a great opportunity for NOVACAP to support a highly qualified management team and to partner with a leader in the industry’’, said Domenic Mancini, Senior Partner at NOVACAP. "The company has an established track record and strong customer relationships and we are looking forward to working with the team and take the business to the next level.”
For more information:
www.muccifarms.com
www.novacap.ca
The World’s Smallest Garden is Created in New York City
The World’s Smallest Garden is Created in New York City
Nate Littlewood and Rob Elliott have created The World’s Smallest Garden, a device which turns an empty bottle into a hydroponic garden.
After meeting at Columbia University in early 2016, the co-founders combined their skills in business and food growing systems to launch this first product, which is intended for beginning growers to use in their home. Setup for the product should only take about 60 seconds, by placing the small, biodegradable plastic device into the top of a bottle—such as a whiskey or wine bottle.
With UrbanLeaf, Littlewood and Elliott hope to create an experience which helps people reconnect with their food. Food Tank had a chance to speak with Nate Littlewood about the inspiration behind UrbanLeaf and challenges he and his partner have faced along the way.
Food Tank (FT): What was the inspiration that led to creating the UrbanLeaf product?
Nathan Littlewood (NL): We wanted to show people that growing food at home could be fun, easy, and accessible. Through over 200 customer interviews, we feel we’ve developed a pretty good handle on the sorts of challenges and obstacles that amateur urban farmers face.
Nine times out of ten, home gardens fail because people forget to water them. The World’s Smallest Garden solves this problem in the simplest, most elegant, and cost-effective way we could imagine. It provides a way for plants to water themselves. We also like that it repurposes something that is available locally (an empty bottle) to create the hydroponic reservoir. In doing so, we eliminate the need to make an injection molded plastic reservoir and import it from overseas. The small amount of plastic we do use in our product is biodegradable. It costs us a bit more, but we feel this is money well spent.
FT: What has been your biggest challenge in developing UrbanLeaf?
NL: It’s been really hard finding hardware know-how and expertise here in New York. There’s a ton of people that understand tech and services based businesses, but widget producers are few and far between! We were recently accepted into FutureWorks, which is a hardware-specific Incubator Program. It seems like an amazing community and we’re looking forward to getting more involved!
FT: How do hydroponics contribute to a more sustainable food system?
NL: Hydroponics opens up new possibilities for food-system design. It doesn’t rely on clearing land, soil quality, large open spaces, and the right season. Hydroponics is very well suited to growing food in urban environments. It’s stackable, it can go vertical, and it can be modular. It allows us to conceive food system designs that involve shorter supply chains, fewer food miles, less weather vulnerability, less wastage, and less packaging.
UrbanLeaf co-founders Nate Littlewood and Rob Elliott. | Photo courtesy of UrbanLeaf
FT: What piece of advice would you give to early entrepreneurs trying to make an impact in the food system?
NL: Emily, you’d know better than most about the level of interest growing around food and sustainability—and I’m sure you’ll agree that this is a good thing. Whilst it’s encouraging to see so many bright, talented, and motivated people entering this space, coming from a business background, I do worry that food businesses generally have low barriers to entry. I fear that a lot of people are going to burn a lot of capital over the next 5 to 10 years learning hard lessons about the importance of competitive advantage. As a producer of consumer hydroponics products, this is something I worry about more than most! My advice is to remember that you can’t pay your rent with passion—most landlords require dollars.
FT: What inspires you to keep working towards food system change every day?
NL: When I’m an old man, and I tell my grandchildren what I’ve done with my life, I want them to be so excited about the answer that they go to school the next day and tell all their friends about it. I’m only in my 30s, so the grandkids are some way off, but the quality of the environmental legacy that I leave behind for them is why I’m doing this. I want them to be able to enjoy the great outdoors in the same way I have. I’m also 100-percent confident that we can improve the quality of thousands of peoples’ lives along the way by providing an experience that helps them reconnect with food.
FT: You’ve mentioned that The World’s Smallest Garden is only a first step towards building a future where food is fresh, local, and personal. What is your vision for UrbanLeaf down the road?
NL: Our goal is to make our customers happy, and to show people that growing their own food can be fun, easy, and accessible. The World’s Smallest Garden is the perfect product to start with both for us as a company and for consumers who are new to this space. Ultimately we want to grow with our customers, and we have a really exciting pipeline of new products that we’ll be releasing over the next few years. I’ll tell you more about that in our next interview!
Techno Farm Keihanna, World’s First and Largest Automated Vertical Farm to Break Ground
Techno Farm Keihanna, World’s First and Largest Automated Vertical Farm to Break Ground
Kyoto, Japan - May 22, 2017 - SPREAD Co., Ltd. (www.spread.co.jp/en) announces the groundbreaking of its next-generation vertical farm, Techno Farm Keihanna in Kizugawa, Kyoto.
Expected to be completed by the end of 2017, Techno Farm Keihanna will employ an automated cultivation system, and achieve the largest output of any indoor vertical lettuce farm in the world at 30,000 heads (3 tons) daily.
SPREAD has operated its current indoor vertical farm, Kameoka Plant (Kameoka, Kyoto) since 2007, which produces 21,000 heads (2 tons) of lettuce every day. Its lettuce is sold under the brand VegetusTM at more than 2,200 supermarkets and retail stores all over Japan. By March of 2013, SPREAD achieved profitability, which is said to be very difficult for the indoor vertical farming business. In 2014, SPREAD started developing its next-generation vertical farming system, Techno FarmTM, based on its accumulated know-how with the aim of global expansion.
Innovation at Techno FarmTM centers around three themes: reduced cost, limited environmental impact, and global adaptability. To achieve each of these goals, SPREAD has cooperated with Japanese equipment manufacturers to develop innovative technologies for water recycling, environmental controls, automated cultivation, and LED lighting. Moreover, the farm will also include specialized research and development facilities.
Scheduled for completion at the end of 2017, Techno Farm Keihanna will be the first of its kind, with shipping expected to start in 2018. The farm’s daily output of 3 tons will be shipped to supermarkets all over Japan under the VegetusTM brand name.
SPREAD will continue to collaborate with innovative business partners from a variety of backgrounds as it works to produce ever greater technological innovation and make sustainable agriculture a reality.
Conceptual image of Techno Farm Keihanna
Representing the next generation of vertical farming, Techno FarmTM builds on SPREAD’s original indoor vertical farming technology to provide a further improved model for stable production in any climate. With its innovation centered around the themes of reduced cost, limited environmental impact, and global adaptability, Techno FarmTM aims to realize sustainable farming by enabling cultivation in locations experiencing agricultural challenges. The system’s original name Vegetable FactoryTM has been changed to the more universally appealing Techno FarmTM as part of SPREAD’s overseas business expansion.
Reduced Environmental Impact And Operating Costs
1. Automated Cultivation
Reduces labor costs by 50%1 by automating the labor intensive cultivation process (from seedling to harvesting)
2. Water Recycling Technology
Improves the recycling rate of water used for cultivation to 98%1 through water filtration and recycling.
3. Environmental Control Technology
Restricts variance in temperature, humidity, wind velocity, and lighting intensity
4. Specialized LED Lighting
Reduces the energy consumption by 30%2 by using LED lighting developed inhouse and tailored to vegetables cultivated in indoor vertical farms.
5. IoT Technology
Enables centralized remote collection and analysis of big data related to cultivation and operations
1: Compared to SPREAD’s Kameoka Plant, 2: Compared to existing LED lighting
SPREAD will partner with companies and organizations both domestically and globally to bring Techno FarmTM to numerous locations around the world. Domestically,
SPREAD will aim for a 10% share of the Japanese lettuce market by utilizing a franchise/ownership model to establish 20 facilities and a daily production capacity of 500,000 lettuce heads (50 tons). Globally, SPREAD will cooperate with local companies in each country and provide technology and support for distribution and sales. SPREAD will develop and propose business schemes applicable to each area.
Rice University Students Create Indoor Farming Device
A group of mechanical engineering students at Rice University have come up with a way to cultivate vegetables without needing a large plot of land outdoors.
Rice University Students Create Indoor Farming Device
By Rebecca Hazen, rebecca.hazen@chron.com
Photo: Lettuce Turnip The Beet
Published 4:11 pm, Tuesday, May 23, 2017
A group of mechanical engineering students at Rice University, called the Lettuce Turnip the Beet team, have come up with a way to cultivate vegetables indoors.
A group of mechanical engineering students at Rice University have come up with a way to cultivate vegetables without needing a large plot of land outdoors.
The Senior Capstone Design project, made up of students Jared Broadman, George Dawson, Sanjiv Gopalkrishnan and Dominique Schaefer Pipps, aptly named their group "Lettuce Turnip the Beet." (LTTB)
According to group member Gopalkrishnan, the mechanical engineering department pitched different projects to the senior students, including a vegetable cultivation machine, and the four choose to work on that particular project.
The main goal of team LTTB, through the vegetable cultivation machine, was to produce one salad per week, for a year.
"Other goals were to make the project sustainable, easy to build and operate, and able to be used in an apartment setting. We have achieved all of our goals - our most recent harvest yielded eleven salads after four weeks of growth," Gopalkrishnan said.
The team has been working on the project since August, and created two versions, both with vegetables growing hydroponically - without soil. The first prototype is in an enclosed area outside. It is based on a triangular frame, has three circular grow tubes, and two pumps with inputs into each of the tubes. It is about 6 feet tall. The second prototype is inside. It is eight feet tall, hosts six square grow tubes, and one pump with an input to the top of the tube arrangement.
"The wooden frame of the second prototype is modular, in that it is composed of four two foot tall sections of two-by-fours, held together by dowel rods. The frame was designed this way to facilitate customization and easy transport. The pipes are square because they are easier to fit into the framework, and have a larger bottom area for the roots to lay upon as the nutrient solution flows across them," Golpalkrishnan explained. "The one input was chosen for ease of operation, as the pipes are all connected in a gravity fed cascade. It is vertical for easy user access. The triangular shape of the first prototype made it hard to access plants at the top. We use a Platinum P900 LED to feed plants at the top of the device, with two smaller fluorescent lights to supplement the bottom plants. The entire device draws about the same amount of power as a microwave."
Golpalkrishnan continued, "We learned quite a bit from the first iteration that we implemented into the second, final prototype. We built the first prototype in November 2016 and the second prototype in February 2017."
It may seem complicated, but the reality is that growing plants is straightforward. They just need light, water, nutrients and a place to grow.
"If the system is set up properly (which is easy to do, and takes about an hour per week to maintain), the plants grow on their own. The biggest key to being able to grow indoors is a good grow light. Plants will grow without light, but one cannot harvest a salad per week without a good light. As far as anyone being able to do this - the answer is yes. Three of the four of our team had no gardening experience, and we have learned as we go," Golpalkrishnan said.
Tomatoes are currently being grown in the outdoor prototype, because there is easy access to pollinators. The LTTB team found that it was easy to grow leafy greens indoors because they do not require pollination. The indoor prototype is currently growing lettuce, kale, Swiss chard and spinach. There are also herbs like basil and parsley, and the team even managed to grow a carrot and radish.
"It is amazing to see the whole plant cycle, from seedling, to adolescent plant, to being able to harvest them. The device has made it easy for us to grow our own vegetables, and our hope is that the device can combat the negative practices utilized by industrial agriculture," Golpalkrishnan said.
Recently, the team showed off their work at the Engineering Design Showcase, which is an event for all Rice engineering teams. Lettuce Turnip the Beet won the Best Environment and Sustainability Design Award.
As the last part of the project, the team will travel to Gothenburg, Sweden, at the end of this month. There, the device will be implanted at the HSB Living Lab at Chalmers University.
"That trip will be the culmination of our efforts as a team, as we are going our separate ways after graduation. However, at least two of us will be building our own versions of the device for personal use," Gopalkrishnan said.
Indoor Farms of America Sales Exceed 2016 Total in First Four Months of 2017 as Growth Escalates
Indoor Farms of America Sales Exceed 2016 Total in First Four Months of 2017 as Growth Escalates
LAS VEGAS, May 23, 2017 /PRNewswire/ -- Indoor Farms of America is pleased to announce that sales through the first four months of 2017 have exceeded the entire year of 2016, when the company first sold its patented vertical aeroponic indoor farm equipment.
According to company CEO David Martin, "During 2016, our first year selling our equipment, we enjoyed what we consider a very solid year for launching our unique vertical farming equipment, and 2017 has already eclipsed that in dollar volume and diversity of farms being sold, built and delivered."
Indoor Farms of America two story display at 2017 Indoor AgCon Las Vegas
GrowTruck Container Farm Display at 2017 Indoor AgCon Las Vegas
The company sold numerous smaller farm packages and container farms during 2016, many of which were considered "pilot farms," to allow potentially large warehouse farm operators to get a feel for this amazing vertical equipment, prior to making larger commitments.
"We knew when we introduced the equipment throughout the previous year, it would somewhat be a year of "tire kickers," and we were overwhelmed at the positive response to our total farm solutions. Those tire kickers are now converting into sold larger farms, as we continue to see positive crop growing results by folks across the U.S. and in key international markets."
Indoor Farms of America spent several years designing and developing its patented ultra high yield vertical aeroponic equipment. The firm manufactures a robust line of aeroponic products, including the world's most productive containerized farms, for deployment in any area of the world that has real need for such a unique small farm platform that produces commercial quantities of fresh produce in an manner superior to any other container farm manufacturer.
Other "turn-key" complete farm packages were specifically developed for fully scalable indoor farm applications to drive down initial capital costs as well as the ongoing operational costs. This focus combines to provide the operator with the single most cost-effective indoor agriculture equipment available in the world.
Ron Evans, company President, stated it this way: "We received numerous affirmations throughout 2016 from third party growers using our farm technology that it delivers on what we promise in overall farm performance. We are committed to the concept that if you are going to own and operate an indoor farm, it should provide you a very sound financial return."
"So many farm platforms that Ron and I analyzed in the early R&D phase back in 2013 and 2014, we believed were doomed to financial failure due to poor design with off the shelf 30 year old growing technology that was not innovative. We recognized that if those marginally profitable operators made errors in execution, they would not survive. It was our mandate internally to develop a complete farming solution that would transcend anything on the market, and we achieved that", stated Martin.
New sales by the company for 2017 to date include numerous locations around the U.S., as well as other countries, as the company continues on a path of rolling out the products in key markets that will benefit dramatically from truly locally grown fresh produce.
"We have sold our first farm for Alaska, destined for Juneau in the next couple months. As well, we have sold our first farm for the GCC region, destined for Dubai. This farm will change the landscape for food production in the Middle East." stated Martin. "Further developments include complete farms sold for multiple regions of Canada, including Alberta, Manitoba and Ontario provinces, and that region is about to explode with growth in the use of our farm solution."
Martin added, "We have sold our first large scale farm for Africa, destined for the country of Botswana. We have had a farm in operation in Johannesburg for many months, and our distributor there reports how amazed potential customers are with the robust growing they experience with our vertical aeroponics platform."
The company has spent thousands of hours developing new crops beyond leafy greens. Evans stated: "Leafy greens were the easy part, and ours does that better than anything else. We have proven out growing of certain varieties of cherry tomatoes, strawberries, peppers, peas and beans for proteins, and we are now working on specialty root crops like heirloom carrots and baby potatoes. We know a well-rounded garden approach is what many folks want to see, not just leafy greens, and we are rapidly developing those for commercial scale."
Indoor Farms of America has a showroom with demonstration farms operating in Las Vegas, Nevada and in multiple locations in Canada, and in South Africa, where their patented vertical aeroponic equipment is on display and receiving amazing reviews by industry leaders.
CONTACT:
David W. Martin, CEO • 161290@email4pr.com • IndoorFarmsAmerica.com
4000 W. Ali Baba Lane, Ste. F Las Vegas, NV 89118
(702) 664-1236or (702) 606-2691
SOURCE Indoor Farms of America
Related Links
Emil Radkov Brings Proven Track Record of Industry Innovation to VividGro
Emil Radkov Brings Proven Track Record of Industry Innovation to VividGro
May 23, 2017 09:00 AM Eastern Daylight Time
WEST WARWICK, R.I.--(BUSINESS WIRE)--Lighting Science® today announced the appointment of noted horticultural and SSL technology expert Emil Radkov as Senior Agronomist and Director of VividGro, a division of Lighting Science Group focused on advanced agricultural and horticultural LED solutions. Lighting Science’s mission is to bring life-changing products in human health, agriculture, and infrastructure to market. Their extensive technology and intellectual property portfolio includes nearly 400 LED technology patents, from biological circadian LED technology solutions to VividGro’s expanding range of products for cannabis and indoor agriculture. Radkov himself has authored over 40 technology patents on the subject of LED technology and horticultural innovation, making his addition to the company’s leadership a clear reinforcement of VividGro’s commitment to continually pushing the industry forward.
VIVIDGRO® ANNOUNCES NEW DIRECTOR AND SENIOR AGRONOMIST
“It’s thrilling to join a company that prioritizes scientific innovation as part of their mission,” said Radkov. “It is my hope that my particular experience in driving LED grow-light technology will aid in the development of even greater products while accelerating consumer awareness of sustainable, future-conscious options in the agricultural and horticultural industries around the world.”
Radkov comes to VividGro following positions at Soraa, Dow Corning and Illumitex. An innovative expert with proven ability of creating new IP for LED technology, Radkov has set industry records for performance and light quality. His key areas of expertise include extensive knowledge of LED phosphors and encapsulants, spectral design for general and specialty lighting applications, reliability and SSL standards.
Lighting Science has long been investing in the research and development of urban agriculture, including working with NASA, Harvard University and the U.S. Scientific Research Station at the South Pole to establish indoor food production. Since launching VividGro in 2014, Lighting Science’s products have consistently been one of the most popular brands in cannabis and large-scale indoor farming production. LSG was one of the first LED companies to offer an energy efficient alternative to high pressure sodium (HPS) lighting. Their patented VividGro LED lamp is proven to increase yields by up to 20% while using 45% less energy. In addition, unlike many other LED grow solutions, VividGro differentiates itself by creating a “white light” working environment for grow house employees. These commercial LED solutions are highly adaptable to both urban and agricultural environments, including greenhouses of any scale.
The VividGro division will be led by recently-appointed President David Friedman and Radkov, and supported by a team of engineers, scientists and sales and marketing executives who all have extensive LED lighting and cannabis industry experience.
About VividGro
Tailored to the indoor agriculture and horticultural markets, the state-of-the-art VividGro product line delivers optimized photosynthetically active radiation (PAR) to maximize plant growth and PAR efficacy, while also providing light suitable for the human visual system and excellent color penetration. VividGro’s patented light spectrum has been proven to speed crop development and increase crop yield. In addition, unlike other LED grow lights, VividGro distinguishes itself from its industry peers by creating a “white light” working environment for grow house employees. These commercial LED solutions are highly adaptable to both urban and agricultural environments, including greenhouses of any scale. Lighting Science continues to experiment with the technology and spectrum to enhance the plant growth at different stages and has plans to launch its next generation VividGro 3 in 2017.
About Lighting Science
Lighting Science (OTCQB:LSCG) is a global leader in innovative LED lighting solutions that designs, manufactures and brings to market advanced, intelligent products for consumer and commercial applications. We are committed to using the science of light to improve the lives and health of people and our planet by inventing breakthrough, biologically-friendly LED lamps and lighting fixtures. Lighting Science is headquartered in West Warwick, RI, with research and development facilities in Cocoa Beach, Florida, and offices in Shenzhen, China. Find out more about us and our products at www.lsgc.com and join us on Facebook, Twitter, LinkedIn and the Lighting Science Blog.
Contacts
Lighting Science
Dustin O’Neal or Alexandra Polier
917-693-2768
press@lsgc.com
How Millennials Will Forever Change America’s Farmlands
How Millennials Will Forever Change America’s Farmlands
[This article originally appeared in Fortune on March 21, 2017]
Square Roots co-founders Kimbal Musk and Tobias Peggs with the first cohort of urban farmer entrepreneurs on the Brooklyn- based Square Roots vertical farming campus.
As Americans increasingly reject cheap, processed food and embrace high-quality, responsibly-sourced nutrition, hyper-local farming is having a moment.
Tiny plots on rooftops and small backyards are popping up all across America, particularly in urban areas that have never been associated with food production. These micro-farms aren’t meant to earn a profit or feed vast numbers of people, but they reflect the Millennial generation’s desire to forge a direct connection with the food they consume.
These efforts are an admirable manifestation of the mantra to think globally and act locally, but they miss the opportunity that is going on right now: the economics of branded local farms have changed, and technology in agriculture has led to a renaissance of independent American farming. Whether this means farming the traditional acreage of the Heartland or adapting to cutting-edge indoor farming methods, the result is the same: demand for real food is far outstripping supply. Highly-educated, entrepreneurial, and socially conscious young people have a great opportunity to think seriously about agriculture as a career.
On the surface, this advice sounds dubious, given the well-documented, decades-long decline of independent farming in America. Between 2007 and 2012, the number of active farmers in America dropped by 100,000 and the number of new farmers fell by more than 20%. Ironically, however, the titanic, faceless factory farms are barely eking out a profit. That often means that an independent 100-acre farm growing high-demand crops can be far more profitable than a 10,000-acre commodity farm growing corn that may end up getting wasted as ethanol.
The key to reviving America’s agricultural economy is casting aside the sentimental images we associate with farming — starting with what a farmer looks like. In recent years, many of the same technologies that have revolutionized the consumer world have fundamentally altered and improved the way we farm. Drones, satellites, autonomous tractors and robotics are now all at home on farms. As a result, tomorrow’s farms won’t just be part of the agricultural sector, they’ll also be part of the tech sector — and tomorrow’s farmers will look a whole lot like the coders who populate Silicon Valley…except with better tans.
The next assumption about farming we need to cast aside is what a farm looks like and where it will be found. The vast planting fields of America’s heartland are going to change by adjusting to grow real food with 21st century technology, but tomorrow’s farms will also be vertical and in or near our urban centers. By 2050, 70 percent of the global population will live in cities. As both a social imperative and a practical matter, it makes sense to grow food near these cities, rather than to waste time and resources delivering products from hundreds or even thousands of miles away.
Square Roots urban farming campus in Brooklyn, NY.
This will require innovative new technology that will create even more flexibility in the way we farm. With this in mind, I recently co-founded Square Roots, a social enterprise that aims to accelerate urban farming by empowering thousands of young Americans to become real food entrepreneurs. We create campuses of climate-controlled, indoor hydroponic farms in the heart of our biggest cities and train entrepreneurs how to grow and sell their food year-round. After their training, these young entrepreneurial farmers, in partnership with the U.S. Department of Agriculture, can qualify for larger loan programs as a next step to owning their own farm — either soil-based or indoor. Whether they move on to their own farm or another business, they are prepared to build forward-thinking companies that will become profitable and create good jobs.
Greens growing vertically with a Square Roots farmer entrepreneur in the background. Photo Courtesy Square Roots
We are investing in this initiative not only because it’s the right thing to do, but also because we are confident that agriculture is poised for explosive growth, and that technology and the power of locally branded farms will be the keystone to success. Just ask self-described “AgTech nerds” like Sarah Mock, who is a leader in the growing movement of Millennial entrepreneurs who see an opportunity in farming to achieve the double bottom line — value and values — that is key to solving our planet’s toughest challenges.
Private enterprise will lead this revolution, but the federal government must help fuel its growth. The 2018 farm bill is a critical opportunity. This massive legislation, renegotiated by Congress every five years, establishes the blueprint and funding priorities across America’s agricultural sector. Last year, Democratic U.S. Senator Debbie Stabenow of Michigan introduced forward-looking legislation called the Urban Agriculture Act that would offer protections and loan options that are currently available only to traditional rural farmers. Ideas like these are essential.
A future in which our food is safer, healthier and environmentally sustainable can exist alongside one in which our agricultural economy grows and creates good jobs for millions of American workers. The technologies and business practices of modern farming is spreading rapidly. The opportunity for a young farmer has never been better — and it’s a future we can all get behind.
This Veggie Garden Is Basically An Organic Server Farm Of Kale
This Veggie Garden Is Basically An Organic Server Farm Of Kale
Commentary: Sustenir's vertical garden is literally a concrete food jungle, and it's one of the coolest things I've seen all year.
by Aloysius Low May 22, 2017 5:00 AM PDT @longadin
Surrounded by concrete walls that were until recently home to industrial tooling machines, thousands of kale plants are stacked in a vertical hydroponic garden. It is literally an organic server farm of kale.
I plucked a leaf from the wall of green and popped it in my mouth.
Absolutely delicious. And I'm not what you'd call a salad guy.
This is Sustenir, a 668 square meter farm located in a concrete estate, in an industrial suburb of Singapore that wants to grow hydroponic (the method of growing plants without soil) food crops in the land-scarce country to feed more people and keep import costs down.
Trust me, this all-grey temple of manufacturing is the last place you'd expect to find a thriving farm, let alone anything living and green. That contrast is exactly how Sustenir's founders, construction manager Benjamin Swan and accountant Martin Lavoo, like it.
Sustenir's founders Martin Lavoo (left) and Benjamin Swan.
Aloysius Low/CNET
Before you can appreciate the scale of the project, you have to understand Singapore's relationship to farming.
An island nation about half the size of Los Angeles, Singapore imports 90 percent of its food from around the world.
In 2015, local farms produced about 13 percent of the vegetables consumed locally (PDF), using about 1 percent of the island to grow crops. Most of Singapore's produce comes from Malaysia and China, but some is flown in from as far as the US or Australia -- like Tuscan kale and curly kale, two varieties that Sustenir grows.
Singapore currently has 10 indoor vertical vegetable farms.
As Sustenir doesn't want to compete with the few local farmers, it works on non-native produce instead. By growing the crop here, Sustenir's imported, organic kale can stay fresh for two weeks longer compared to imported kale, which loses part of its freshness in the shipping process.
Given Singapore's smaller land size, the ingenious use of space and hydroponics could set an example for urban farmers everywhere to produce clean, pesticide-free vegetables faster and more abundantly than in the ground.
Starting fresh
Starting in a basement, Sustenir's initial setup cost $150, but the company went through 18 lighting vendors and numerous indoor configurations before deciding on the right recipe to grow kale efficiently in such land-strapped space.
"The way we wanted to look at technology was [from] a value-engineering standpoint," said Lavoo, the engineer. "We wanted to take all the ideas around vertical farming, and boil it down to the basics."
In this case "the basics" include a combination of red and blue LED grow lights (sprouting kale and growing kale use different spectrums), and hydroponics, a nutrient solution, instead of soil, as some indoor farms do.
Consumers tend to prefer soil-grown produce, said Fadhlina Suhaimi, a senior scientist at Singapore's Agri-Food and Veterinary Authority (AVA), and it's easier to grow a wider range of vegetables and herbs in soil.
But the old-fashioned way using soil requires more manpower and planting materials, and kale can take longer to grow, so yield is lower.
Grow Sustenir's kale did. It takes this concrete jungle kale garden two weeks to go from seed to harvest, compared to about a month for outdoor farms, according to Lavoo.
"We [don't] think we can grow a plant in our environment that would compete with the best of what nature is able to provide," said Lavoo. "But what the best nature is able to provide is becoming more a constricted reality for mankind."
Room to grow
A healthy harvest is one thing, but what really sets Sustenir apart from other hydroponic farmers is a patent-pending system that lets it store more growing racks in a smaller enclosed space, while still giving workers enough room to harvest and replant.
Harvested kale at Sustenir's farm.
Aloysius Low/CNET
Remember when I compared Sustenir's farming operations to an organic server farm? With racks and racks of kale stacked next to each other, that's a pretty close description.
Because Sustenir uses hydroponics and an air-conditioned indoor facility, the company says it doesn't need to use pesticides to keep the plants bug-free. There's no soil harboring little bugs and no stretches of open air for their migration.
However, this kale farm takes precautions anyway. I did have to endure an air shower and put on a sterile jumpsuit before heading inside the facility.
The company currently takes up about half of its rented space, with plans to expand to its other half in the coming months. Besides kale, the company is also looking into cherry tomatoes, having successfully cultivated a test crop so far, and strawberries.
Growth-wise, Sustenir is looking to spread its gospel to other land-scarce urban environments, such as Hong Kong or even Colombo, Sri Lanka, where its already-established model of locally growing high-end, high-value crops could also work.
In Singapore and elsewhere, Sustenir's LED lights and server farm-style plantings would help keep the cost of imported produce down.
With access to tasty, locally-grown produce like this, I might even learn to become a salad guy after all...
Confusion Over Hydroponics Grows at National Organic Standards Board Meeting
Proponents of organic certification being exclusive to soil-based agriculture, as opposed to hydroponics and aquaponics, were left frustrated by the National Organic Standard Board (NOSB) meeting in Denver last week when the board decided not to vote on the eligibility of hydroponic farming for at least another six months
Confusion Over Hydroponics Grows at National Organic Standards Board Meeting
APRIL 25, 2017 by JILL ETTINGER
Proponents of organic certification being exclusive to soil-based agriculture, as opposed to hydroponics and aquaponics, were left frustrated by the National Organic Standard Board (NOSB) meeting in Denver last week when the board decided not to vote on the eligibility of hydroponic farming for at least another six months.
“The NOSB decided this was something so fundamental to the organics industry, they want everyone participating in the policy developing process for how to handle container and hydroponic growing systems,” Lee Frankel, executive director for the Coalition for Sustainable Organics told the Packer.
Currently, hydroponic and aquaponic farming methods are eligible for the USDA organic certification despite using no soil—a point many members of the organic industry say is significant because soil plays a huge part of the process of becoming an organic producer. Not only is cleaning up soil and ensuring that it’s free from agricultural runoff, banned pesticides, herbicides, fungicides, and fertilizers, critical to the quality of the food, but it’s also vital to the environment and ecosystems connected to it.
“Soilless, hydroponic/container growing is not necessarily ‘bad,’ it simply isn’t organic, by law,” says The Cornucopia Institute, the organic industry’s leading watchdog group. “Allowing year-round imports from countries where hydroponic/container growing is illegal, then labeling and selling them as organic in this country, undercuts legitimate US organic farmers. It is dead wrong—and patently illegal under the Organic Foods Production Act and the current regulations.”
Much of the confusion lies in the National Organic Program’s definitions of organic, and more specifically, the definitions of both hydroponic and aquaponics farming methods that don’t involve soil. While some water-based growing methods rely on liquid fertilizers and rocks, soil is otherwise absent from the process. Hydroponics and aquaponics have been certified through the program since the USDA developed the standards in 2002. They make growing in soil-less environments possible, such as urban areas. The water-based growing methods also reduce the risk of pests and weeds, common issues with soil-based growing methods that increase the needs of pesticides and herbicides.
But there are so many types of aquaponic and hydroponic growing that the NOSB is requesting more information on the specific growing mechanisms of these systems in order to determine whether or not the methods can continue to qualify as organic.
“The NOP should adopt the European standard that requires that organic crops be grown in the soil in the ground, except for edible sprouts, aquatic plants growing outdoors in their native ecosystems, and transplants sold in their containers,” The Cornucopia Institute noted in its public comments to the NOSB.
“Soilless systems are not organic systems,” Cornucopia explains, “because they are removed from the regenerative organic practices that capture carbon and nitrogen from the atmosphere into the soil.”
“[O]rganics should be about more than soil,” Marianne Cufone, executive director of the Recirculating Farms Coalition and proponent of soil-less farming, told FoodNavigator-USA. “It should be about the whole picture. We should be looking to improve our planet and these types of farms at their very core are eco-efficient.”
Frankel says the organic industry shouldn’t expect a decision in October, either, citing significant turnover in the board earlier this year adding to the decision-making processes.
“NOSB has not yet achieved consensus among its members regarding definitions, and without definitions a vote on prohibition cannot occur,” he said.
iStock/LouisHiemstra
The Power of a Plant – Green Bronx Machine
Globally acclaimed teacher, Stephen Ritz, author of “The Power of a Plant” shows how in one of the nation’s poorest communities, his students thrive in school and in life by growing, cooking, eating, and sharing the bounty of their green classroom
The Power of a Plant – Green Bronx Machine
Globally acclaimed teacher, Stephen Ritz, author of “The Power of a Plant” shows how in one of the nation’s poorest communities, his students thrive in school and in life by growing, cooking, eating, and sharing the bounty of their green classroom. His innovative program began by accident. When a flower broke up a brawl among burly teenagers at a tough South Bronx high school, Stephen saw a teachable moment to connect students with nature.
By using plants as an entry point for all learning, he witnessed nothing short of a transformation. Attendance soared from 40 to 93 percent. Disciplinary issues plummeted. In a school with a 17 percent graduation rate and high crime rate, every one of his students finished school and stayed out of jail. More than 50,000 pounds of vegetables later, he has figured out how to bring the magic of gardening into the heart of the school day for students of all ages.
Affinor Growers Signs an "On-Site Test License Agreement" with BC Company to Develop Vertical Farming with Coniferous Tree Seedlings
Affinor Growers Signs an "On-Site Test License Agreement" with BC Company to Develop Vertical Farming with Coniferous Tree Seedlings
Vancouver (Canada), May 22, 2017 - Affinor Growers Inc. (CSE:AFI, OTC:RSSFF, Frankfurt:1AF) (“Affinor” or the “Corporation), is pleased to announce the signing of a research and development On-Site License Agreement with a BC company to use Affinor's vertical growing equipment to mass produce high quality coniferous seedlings.
The test agreement is a collaboration of Affinor’s vertical farming tower technology, proprietary owned BC registered Tree Seeds by D.K Helicropper Ltd. and Vertical Designs Ltd. Under the terms of the agreement, specific coniferous seeds potentially more resistant to the Pine Beetle (MPB), will be propagated and mass produced with Affinor's growing technology on the Vertical Designs Ltd. farm located in Abbotsford BC. In the agreement, Vertical Designs will be able to purchase four 10 level towers with no license fee or royalty. In return, Vertical Designs will share the testing and production results with Affinor.
Forestry is a major economic resource for BC resulting in a high demand for high quality MPB stress resistance seedlings. In 2016, 259 million trees were planted and for 2017, 266 million trees are planned to be planted.
Jarrett Malnarick, President and CEO said that "This is another great opportunity for Affinor to expand our growing technology into other markets. Reforestation through tree planting and Silviculture is a large market not just in BC, but the entire world. We are excited to develop new cultivation systems using vertical growing technology to produce next generation seedling."
For More Information, please contact:
Jarrett Malnarick, President and CEO
604.837.8688
jarrett@affinorgrowers.com
About Affinor Growers Inc.
Affinor Growers is a publicly traded company on the Canadian Securities Exchange under the symbol ("AFI"). Affinor is focused on growing high quality crops such as romaine lettuce, spinach and strawberries using its vertical farming techniques. Affinor is committed to becoming a pre-eminent supplier and grower, using exclusive vertical farming techniques.
On Behalf of the Board of Directors
AFFINOR GROWERS INC.
"Jarrett Malnarick"
President & CEO
The CSE has not reviewed and does not accept responsibility for the adequacy or accuracy of this release.
FORWARD LOOKING INFORMATION
This News Release contains forward-looking statements. The use of any of the words "anticipate", "continue", "estimate", "expect", "may", "will", "project", "should", "believe" and similar expressions are intended to identify forward-looking statements. Although the Company believes that the expectations and assumptions on which the forward-looking statements are based are reasonable, undue reliance should not be placed on the forward-looking statements because the Company can give no assurance that they will prove to be correct. Since forward-looking statements address future events and conditions, by their very nature they involve inherent risks and uncertainties. These statements speak only as of the date of this News Release. Actual results could differ materially from those currently anticipated due to a number of factors and risks including various risk factors discussed in the Company's disclosure documents which can be found under the Company's profile on www.sedar.com. This News Release contains "forward-looking statements" within the meaning of Section 27A of the Securities Act of 1933, as amended, and Section 21E the Securities Exchange Act of 1934, as amended and such forward-looking statements are made pursuant to the safe harbor provisions of the Private Securities Litigation Reform Act of 1995.
Japan Plant Factories Are Providing A Safe, Reliable Food Source
Japan’s plant factories are expanding to meet the increasing demand for safe, pesticide-free, locally-grown food
Japan Plant Factories Are Providing A Safe, Reliable Food Source
Japan’s plant factories are expanding to meet the increasing demand for safe, pesticide-free, locally-grown food.
Japan has more plant factories (PFs) than any other country. The largest number of plant factories are located in Okinawa Prefecture near Taiwan. The rapid commercialization and financial subsidization by the Japanese government of PFs, which began in 2010, are helping to drive interest in their development.
Another reason for the increase in PFs in Japan is that the country has been importing a large amount of fresh, sliced salad vegetables from China. The Japanese are concerned about the amount of pesticides being used for Chinese vegetable production and looking for alternative sources of fresh vegetables and herbs.
Hort Americas spoke with Dr. Toyoki Kozai, professor emeritus at Chiba University and chief director of Japan Plant Factory Association, about Japan’s expanding plant factory industry. Chiba University researchers are studying various aspects of indoor farming. A PF on the university campus, which is operated by a private company, is selling around 3,000 heads of lettuce daily to a variety of customers, including Japanese grocery store chain Tokyo Stores.
The number of Japanese plant factories producing more than 10,000 heads of lettuce daily is estimated to be around 10.
Photos courtesy of Dr. Toyoki Kozai.
How large is the average plant factory in Japan and can you describe what type of equipment is used in one of these operations?
As of March 2014 there were about 170 plant factories (PFs) in Japan. Of these, 70 are producing more than 1,000 lettuce heads (50-100 grams per head) or other leafy greens daily. The number of PFs producing more than 10,000 heads of lettuce daily is estimated to be around 10.
The average floor area of a PF with 10-15 tiers for producing 10,000 lettuce heads daily is 1,500 square meters. The main components of a PF are:
- A thermally well-insulated and airtight warehouse-like structure with no windows.
- Tiers/shelves with a light source and culture beds.
- A carbon dioxide supply unit.
- Nutrient supply units.
- Air conditioners.
- An environment control unit.
- Other equipment includes nutrient solution sterilization units, air circulation units and seeders.
Are most of Japan’s plant factories located in renovated buildings (i.e. old warehouses, abandoned factories, etc.) or are the buildings housing these operations constructed specifically for use as plant factories?
Sixty percent of the PFs in Japan are located in new buildings.
Why has Japan been one of the leaders in the development of plant factories?
Citizens’ concerns for and interest in health, pesticide-free products, freshness and high-tech are high. There are many researchers who have been doing research on PFs for more than 10 years. e Japanese government started subsidizing R&D and doing extension related to PFs in 2010.
Are most of the Japan’s plant factories operated by private companies and/or corporations or are there some operated as family farms?
Thirty percent of PFs are operated by families with ve to 15 part-time workers. Half of these PFs are for vegetable production. Ten percent of the PFs are operated by agricultural unions or similar organizations. The rest are operated by private companies.
What are the most common crops grown in the plant factories?
Primarily green leaf lettuce, romaine lettuce, frill lettuce, spinach, basil and arugula.
Are there any limits (i.e. space restrictions, plant size, light requirements, etc.) to the types of crops that can be grown in plant factories?
Plant height is 30-40 centimeters or less, grow well at a photosynthetic photon ux (PPF) of 150-250 micro-mol per meter squared per second (umol/ m2/s) and at high planting density. Plants can be harvested within two months after seeding and respond well to controlled environments.
How are most of the crops grown in plant factories marketed to consumers?
The produce is sold to diverse markets. Forty percent to large- and medium-size supermarkets, 30 percent to restaurant chain stores, 20 percent to meal delivery service companies and the rest to department stores, convenience stores and Internet shopping.
Is there any type of marketing on television, radio, online, newspaper, etc., done for the crops grown in the plant factories?
Most marketing is done on PF websites for ordering via the Internet. The PFs also do many interviews for articles and TV news without spending money for advertisement. PF sales personnel visit supermarkets, restaurants and department stores frequently.
In regards to the production system set ups currently being used in plant factories, where could the greatest improvements be made?
Automation for transplanting, harvesting, packing and cost and production management systems.
What are the benefits/advantages of plant factories over greenhouse production and traditional field crop production?
Ten- to 100-fold annual productivity per unit land area regardless of weather, clean and no need to wash before cooking and a long lifetime. Consumers are now interested in its nutrition for humans, taste, functional and medicinal components in leaves, beauty color and mouth feeling
Japan’s plant factories are used for the production of leafy greens, herbaceous medicinal plants, herbs and miniature root crops such as micro carrots and turnips.
What are the benefits/advantages of greenhouse production and traditional field crop production over plant factories?
PFs produce vegetables with high quality (small, delicate looking and flavorful) which cannot be produced in greenhouses or in the fields. The PF vegetables are 1/3 to 1/100 the size of greenhouse- or field-grown vegetables. PFs enable consumers living alone to eat fresh vegetables daily.
Do you think that plant factories will be able to overcome their current limitations to compete with greenhouse and field production? If so, how many years do you think it will take for the production costs to be comparable?
PFs are useful only for the production of leafy greens, herbaceous medicinal plants, herbs, and miniature root crops such as micro carrots and turnips. These root crops must have edible tasty leaves.
PF vegetables are not replacements for greenhouse- and field- grown vegetables. They are new products and create a new market. It will take about 10 years in Japan, less than 10 years in China.
What aspects of plant factory production are being studied at Chiba University?
Research includes:
- The production of low potassium lettuce for persons who have kidney-related problems.
- Development of production and cost management systems.
- Lighting system using LEDs.
- Reduction in electricity costs.
- The physiological disorder of tip burn.
For more: Dr. Toyoki Kozai, Japan Plant Factory Association, Chiba University, Center for Environment, Health and Field Sciences, Kashiwa-no-ha, Kashiwa, Chiba, 277-0882, Japan; kozai@faculty. chiba-u.jp.
Additional articles on Japan’s plant factories are available at:
http://www.japan-acad.go.jp/en/publishing/pja_b/ contents/89/89_10.html; http://www.meti.go.jp/english/policy/ sme_chiiki/plantfactory/about.html
David Kuack is a freelance technical writer in Fort Worth, Texas; dkuack@gmail.com.