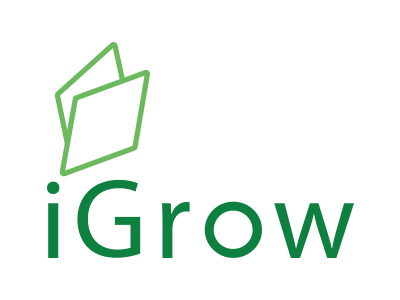
Welcome to iGrow News, Your Source for the World of Indoor Vertical Farming
NatureFresh™ Farms Introduces the 2018 Greenhouse Education Center Team!
NatureFresh™ Farms Introduces the 2018 Greenhouse Education Center Team!
Leamington, ON (May 7th, 2018) – The Greenhouse Education Center is a greenhouse on wheels – and it may be coming to a city near you! NatureFresh™ Farms is on the road again with the Greenhouse Education Center program, taking part in events at retail stores, schools, and fairs all summer long. A brand-new crew of passionate student leaders have also joined the ranks to spread the word about greenhouse-grown produce and share why eating fresh every day is so important!
The NatureFresh™ Farms team created the Greenhouse Education Center in 2015 to show consumers exactly how they grow in their greenhouses. Many people don’t fully understand their food’s journey from the farm to their table, and this lack of knowledge can often lead to unhealthy eating choices. The NatureFresh™ Farms team recognized this disconnect, and the Greenhouse Education Center was born.
The Greenhouse Education Center is a 38-foot-long mobile greenhouse unit equipped with vibrant plants, innovative growing technology, and a busy Bumble Bee ecosystem. Visitors to the unit can physically touch the plants and see exactly how they are grown in NatureFresh™ Farms greenhouses. They can see the drippers, the ventilation system, the heating rails – everything! This behind-the-scenes look at greenhouse growing allows consumers to gain a greater understanding about how their food is grown and get enthusiastic about healthy eating.
A brand-new team of passionate students will also be traveling with the mobile greenhouse all summer long to answer questions about NatureFresh™ Farms, greenhouse growing, and all things fresh. This year’s students have backgrounds ranging from Business to Agriculture to Health Sciences, which means that they bring a diverse set of perspectives to the greenhouse farming industry. Although they come from different life experiences, they are all passionate about the future of fresh!
This year, the Greenhouse Education Center will be taking part in over 70 different events across eastern North America. The team will be visiting retail locations, schools, and fairs across Ontario and throughout states including Ohio, New York, and Pennsylvania.
The NatureFresh™ Farms team encourages all those interested in attending an event to visit their website for further details about dates and locations: http://www.natureefresh.ca/gec.
Family Harvest: Hydroponic Farming Provides A New Job And A New Life On The Northern Neck
Family Harvest: Hydroponic Farming Provides A New Job And A New Life On The Northern Neck
April 16, 2018
Farnham, Virginia
As snow fell on the fields of the Northern Neck last month, Justin McKenney was in his tomato greenhouse tending to his plants with his young assistants: daughters Josslyn, 5, and Joely, 2.
Last week, he was back in the greenhouse, and the plants were about 4 feet tall with plump, green tomatoes forming on the vines. He expects to pick the first ripe tomatoes by the end of April. He will harvest until December, with each of his 1,050 plants — growing to about 40 feet in length by then — producing upwards of 50 pounds of tomatoes for the year.
Hydroponic farming has its advantages.
Before they launched Sion House Farm in 2015, McKenney and his father, Jack Mc- Kenney, had no connection to farming, except for cousins who farmed land along the Rappahannock River that has been in the family for more than a century. Justin McKenney, 32, worked for an oil-field services company in Pennsylvania; Jack McKenney, 64, had retired from a career in banking.
“I’d never grown anything,” said Justin. “I don’t think I’d even grown grass seed.”
But they were looking for a joint business venture so Justin could start a new career, his old job having worn him down with the night shifts and long hours that kept him away from his wife and young daughters. They also wanted to do something that might bring them together on the Northern Neck, where neither had lived full-time but both had spent summers and many weekends during their youth visiting grandparents and cousins.
Scouting around for an opportunity, Jack came upon hydroponic farming — essentially growing plants without benefit of soil — and looked into it. The men were further intrigued after attending a two-day orientation in Ohio held by a company that manufactures hydroponic supplies. After a particularly unhappy night on the job in Pennsylvania, Justin called his father: “I’m tired of this. Let’s do it.”
Justin and his wife, Jamie, decided to make the move, and they relocated to the Northern Neck, near the Farnham community. Justin acquired 12 acres of family land that had been in grain production and set up four greenhouses.
Justin has taught himself about hydroponic farming, becoming a voracious reader on the subject and making Google and YouTube his personal online classrooms, while his dad is generally more involved with sales and deliveries and that side of the business. Both McKenneys live nearby. Justin and Jamie’s home, just beyond the greenhouses, is in the approximate footprint of where his great-grandparents’ home stood.
Besides tomatoes, they raise bibb lettuce and bok choy year-round, selling to supermarkets (including Tom Leonard’s in Richmond), wholesalers, home-delivery services and roadside stands. They have added two greenhouses, and Justin has branched out into field-farming, where he will grow several acres of sweet potatoes, potatoes, and tomatoes this summer. For someone who had never even grown grass, Justin has embraced his new profession and lifestyle.
“Absolutely, I love it,” he said. “My days haven’t gotten any shorter. They’re just in daylight now instead of in the dark.”
***
Jack McKenney’s great-grandfather, Carter Mothers- head, acquired a stretch of land along the Rappahannock, between Sharps and Morattico, about 1906. Four of his sons farmed the land and made their homes along what is now known as Mothershead Neck Road, where Sion House Farm occupies about a dozen acres. (The farm takes its name from a former plantation house on the property, thought to be the childhood home of Cyrus Griffin, who served as the last president of the Continental Congress prior to ratification of the U.S. Constitution.)
“This was called ‘coming to the country,’ ” said Jack, who grew up outside Philadelphia. “I was the oldest grandchild, and I got to hang around with my grandfather. I felt pretty lucky.”
In high school, Jack’s family moved first to Tampa, Fla., and then to Richmond, where he was in the first class to graduate from what was then the “new” Hermitage High in the spring of 1972. After attending the University of Virginia, he went into banking, working mostly in Northern Virginia, where Justin and his two siblings grew up.
Justin also grew up with a long-distance affection for the Northern Neck and liked the notion of making his home there, though job prospects seemed limited until he and his father struck upon the idea of hydroponic farming.
Hydroponic farming is not an inexpensive venture — with its infrastructure and internal systems controlled by computers, propane to warm the greenhouses in winter, electricity to operate pumps and fans around the clock, and the labor necessary for frequent planting and transferring (in the case of lettuce and bok choy), and pruning and trellising (in the case of tomatoes) and regular harvesting of everything. But it also doesn’t require the capital investment of expensive machinery for conventional farming and is not at the mercy of variables such as weather.
High wind or hail storms can destroy field crops in a matter of seconds, and heat and drought are always serious possibilities. Not so in greenhouses. A run of cloudy days can slow the growth of plants coming up indoors, and extreme cold can raise heating costs, but an indoor crop is generally safe from outside disasters. Pests and disease also can be managed somewhat more easily in a greenhouse’s climate-controlled environment, though plants grown indoors are certainly not immune.
Production in a hydroponic operation also is more predictable, Justin said, and there is little waste: he sells almost everything he grows. What he doesn’t sell he gives to a local food bank, and if he has some particularly unsightly produce that has hung around the greenhouse a little too long, he’ll drop it off at a buddy’s pigpen.
And his operation becomes particularly lucrative when he can attract a premium price for his fresh produce when other local growers don’t have it to sell — vine-ripened tomatoes in May or November and lettuce in the heat of the summer.
“I’m definitely sold on [hydroponic farming],” he said. “We can make the plants do what we want them to do.”
The lettuce and bok choy grow in long trays, roots dangling in a closed-circuit stream of ever-moving water that is constantly refreshed and replenished with nutrients. In the case of each, it’s about 48-62 days from seed to harvest, depending on the time of year and the availability of daylight, Justin said. The tomatoes grow in Perlite, a lightweight soil substitute, and are fed by drip irrigation every half-hour. Hives of bumblebees pollinate the tomatoes.
How much land would be required to produce the same amount of food?
“I don’t know the answer to that,” Justin said, “but I know it’s way higher than what we are doing here.”
Last year, he said, Sion produced 42,000 pounds of tomatoes in a 4,200-square-foot greenhouse, the equivalent of about one-tenth of an acre.
Jack McKenney said the future of hydroponic farming is promising because “you’re able to produce so much more in smaller acreage, you’re able to go year-round, and you don’t use as much water.”
Elaine Lidholm, director of communications for the Virginia Department of Agriculture and Consumer Services, agreed.
“It is safe to say that hydroponics is a very small part of the overall industry of agriculture, but it is growing, and I believe it will continue to grow,” she said in an email.
“This is just my opinion, but I wouldn’t be surprised if we saw a real burst of new companies in the very near future. I think it has advantages for new farmers or urban farmers, although it can occur on farms, too. It is a good fit for urban agriculture, and the world is becoming more urbanized every year. I don’t think it’s going to feed the world by itself, but it can help, and we are going to have to explore every avenue for food production in order to feed the burgeoning world population.”
(804) 649-6639
‘Greenhouse Of The Future’ With Special Solar Glass Coming To Netherlands
‘Greenhouse Of The Future’ With Special Solar Glass Coming To Netherlands
A ‘Greenhouse of the Future’ will soon be built on the Floriade site in Venlo. The greenhouse, made possible with various subsidies, will be energy and CO2 neutral and can even generate energy. To achieve this, the latest technological innovations in the field of Het Nieuwe Telen (Next Generation Cultivation) such as Air & Energy and LED systems are combined with Dye-Sensitized Solar Cells (DSSC) nanotechnology.
The greenhouse, a prototype covering a total of 1200 m2, will be built by Maurice Kassenbouw. Michel La Crois, director at Maurice Kassenbouw: "All designs are ready, and we only have to wait for the special glass in the right dimensions."
Solar panel
The special glass has been developed by Brite Solar Technologies from Greece. Nick Kanopoulos, the man behind Brite Solar Technologies: "The glass we make has a special, transparent coating that transmits 70 to 75 percent of light in the frequencies that are important for photosynthesis. The glass also features special stripes, similar to what you seen in the rear window of a car. These are solar cells that generate energy from sunlight, so the glass actually functions as a solar panel. An additional advantage is that the glass also has improved insulating properties, so less energy is needed to heat the greenhouse. "
Energy gain
In Greece the glass has already been tested on a small scale on a 100 m2 greenhouse. Many growers feared that the glass letting through less light would have a negative effect on crop yield, but this turned out to not be true in those tests. There were as many kilograms from the test greenhouse in Greece as from comparable greenhouses without special glass. In addition, the glass also generated an energy gain of 5,400 kilowatt hours per year during the test.
The glass will larger on the Dutch prototype greenhouse. Where the glass panels in Greece measured 50 x 50 cm, they will now be 1 x 1.2 m. The results of the project will be closely monitored by Brite Solar Technologies, both remotely and by people on the ground. Nick: "All kinds of sensors will be placed in the greenhouse, so that we can monitor the results from anywhere in the world."
Self-sufficient
Although the first prototype has not even been built yet, Maurice Kassenbouw already has a second project lined up for another two hectares. However, they need to wait on the results of the first greenhouse. "In the south of Europe in particular, I expect a high energy yield. There is already interest in this type of greenhouse in Dubai, and we expect that we will soon be able to build these types of greenhouses on a large scale."
The glass is now 6 mm thick, but in order to be able to replace existing glass in existing greenhouses, they are working on glass with the conventional thickness of 4 mm.
Ultimately, the goal is for these greenhouses to be self-sufficient in terms of energy and to be a solution to the problem of food scarcity. Michel: "The question that we are jointly facing is: how are we going to feed nine billion people by 2050?"
European innovation program
The construction of the greenhouse is part of the European Innovation Program Southern Netherlands (PROJ-01061).
For more information:
Brite Solar Technologies
www.britesolar.com
info@britesolar.com
Maurice Kassenbouw
www.kassenbouw.com
maurice@kassenbouw.com
Publication date: 5/2/2018
Europe’s Largest City Farm Built On Rooftop In Brussels
Europe’s Largest City Farm Built On Rooftop In Brussels
BIGH “Ferme Abattoir” in Anderlecht
The "Ferme Abattoir", the first city farm built by Building Integrated GreenHouses (BIGH), has opened on the roof of Foodmet, the new food hall of the Abattoir site in Anderlecht, Brussels. With around 2000 m2 of greenhouses for horticulture and aquaponics, and 2000 m2 open-field vegetable cultivation, they claim to be the largest city farm in Europe situated on the roof of a building.
Aquaponics
BIGH is based on an 'aquaponics' production model, which means that fish and plant breeding are linked by a biological filter that continuously purifies the water for the fish. The waste from the fish is converted into natural fertilizers for the plants. The water is used to irrigate the plants and is replenished daily. Aquaponics is the combination of hydroponics (cultivation without soil) and aquaculture or fish farming. It’s an example of circular economic principles in which waste and water from fish are used for the cultivation of crops.
Reusing CO2
In 2015 BIGH was established to optimize urban real estate and to make the city more productive by, for example, installing greenhouses on roofs. To this end, BIGH integrates the reuse of surplus C02 and energy emissions and using rainwater in the production process to better utilize the value and space of buildings, focusing on sustainable and circular urban agriculture. This will reduce the ecological footprint and improve nutrition, urban quality of life, employment, aesthetics, climate, and biodiversity.
Together with a number of economic and social partners, BIGH's entrepreneurs play an active role in the pursuit of a sustainable food model. For them, urban agriculture is a link between urban consumers and rural production, between experts and producers and other actors in the food sector.
Short chain
Since a few years, consumers demand products that are healthy, local and traceable. In that respect, aquaponics and urban agriculture can offer high-quality, tasty and healthy products according to the short-chain principle. Urban agriculture refers to agricultural activities in an urban environment, which are based on a more ecological, social, sustainable and circular food system. With this approach the city can provide for a part of its own needs and turns it into a non-polluting production centre.
Network of urban farms
BIGH wants to create a network of urban farms in major European cities for the benefit of the inhabitants of those cities. "These are innovative examples of a circular economy that are cost-effective, transparent, high-quality and ecologically and socially driven. Their shape and content are created in symbiosis with the urban environment."
For more information:
BIGH
www.bigh.farm
contact@bigh.tech
The Decades-Long Quest To End Drought (And Feed Millions) By Taking The Salt Out of Seawater
Paton is the founder of Seawater Greenhouse, a company that transforms two abundant resources – sunshine and seawater – into freshwater for growing crops in arid, coastal regions such as Africa’s horn.
The Decades-Long Quest To End Drought (And Feed Millions) By Taking The Salt Out of Seawater
“The world isn’t short of water, it’s just in the wrong place, and too salty," says Charlie Paton – so he's spent the past 24 years building the technology to prove it.
Sundrop Farms now produces 15 per cent of the Australian tomato market – all of it grown using seawater. Credit: Sundrop Farms
By EMMA BRYCE
20 March 2018
In October 2017, Charlie Paton was driving across the parched plains of northwestern Somaliland when he passed a seemingly endless queue of rumbling trucks. Each was piled high with containers of grain – 47,000 tonnes in all – to be distributed as food aid across Somalia and Ethiopia. Paton was struck by the irony: it was the region’s harvest season, and yet here were trucks delivering industrial quantities of grain that would surely strip whatever meager business there was away from local producers. “Suddenly, the place is awash with food,” he recalls thinking. “Who’s going to buy food from a farmer when it’s free?”
Huge drops of food aid are common in the drought- and famine-plagued Horn of Africa. This year alone, the United Nations is appealing for $1.6 billion in aid just for Somalia – a fact that unsettles Paton. “That $1.6 billion could probably make the place self-sufficient, not just in 2018, but forever,” he says. And he thinks his invention could help make that a reality.
Paton is the founder of Seawater Greenhouse, a company that transforms two abundant resources – sunshine and seawater – into freshwater for growing crops in arid, coastal regions such as Africa’s horn. The drought-stricken landscape that cloaks this region doesn’t exactly inspire visions of lush agriculture – but then, Paton sees things differently: “The world isn’t short of water, it’s just in the wrong place, and too salty,” he says.
His latest project in Somaliland (an autonomous but internationally unrecognised republic in Somalia) takes that bullish optimism to the extreme. On a 25-hectare plot of desert land close to the coastline, he’s building the region’s first sustainable, drought-resistant greenhouse. Using solar power to pump in seawater from the coastline and desalinate it on site, Paton is generating freshwater to irrigate plants, and water vapor to cool and humidify the greenhouse interior. In January – less than a year after its launch – this improbable desert oasis produced its first harvest of lettuce, cucumbers, and tomatoes. “The idea is so simple that it’s rather insulting,” Paton says. “People say, ‘If that’s going to work then somebody would have done it before.’”
The prevalence of this attitude might explain why Paton’s invention is the first of its kind in the Horn of Africa. That – and the overwhelming challenges of investing there. “The main problem is drought. Somalia was hit by serious water shortage in 2016 and 2017,” says Amsale Shibeshi, who works with the NGO Pastoral and Environmental Network in the Horn of Africa, a partner on the greenhouse project. Though Somaliland has maintained relative peace since the 1990s, in neighboring Somalia the drought has fuelled persistent famine, which underlies disease outbreaks and ongoing political instability – with the militant fundamentalist group al-Shabab still influential there.
Today, only a fraction of Somalia’s overall land area is cultivated, and half the population is food insecure (data for Somaliland itself is scant, because it’s not internationally recognised.) Regular aid shipments bring products like rice, sorghum, sugar, and cooking oil to the region. Somaliland relies on these to a lesser degree than Somalia – in good years its pastoral farmers produce plenty of meat and milk from livestock – but it still has to import most fruits and vegetables from neighbouring countries, Shibeshi says. “It’s the centre of world water insecurity, which makes it the centre of food insecurity,” Paton says. “But if we could crack it here it would be a really big prize, because it’s not just Somaliland. Then it would work in Somalia, Eritrea, Sudan, Mali, and Mauritania.”
Charlie Paton, founder of Seawater Greenhouse, built desert greenhouses in Abu Dhabi and Australia. Now he's taking on his biggest challenge yet.
Christopher Andreou
February 2018. At his suburban East London office, Paton – a lanky, blue-eyed figure with a head of closely-cropped silver hair – opens the front door, letting in a flurry of snow. To the left is a garage, an experimental workshop filled with pieces of metal and wood, where he and his son tinker around with designs for greenhouses in much warmer countries. Up a narrow flight of stairs Paton’s two young colleagues – Karl Fletcher and Chris Rothera – clack away on keyboards in a bright, clean-lined, airy interior that looks more like a trendy coffee shop than the birthplace of rugged desert greenhouses.
In this building, Paton has been developing his concept for more than 20 years – and his ideas have unusual origins. Back in school, he was neither sporty, nor academic, and he struggled with dyslexia. “If you don’t fit in, you rebel,” he says, settling into a chair at a long trestle table, adorned with a large sample of the latticed cardboard structure he uses to filter freshwater vapor into his greenhouses. By age 16, he’d been expelled. But then, Paton found an unexpected refuge in theatre, after taking his first job as a stage electrician for the London Festival Ballet. That became the springboard for a career in theatre lighting design, which many years later would fuel his curiosity in something completely different: the effect of light and heat on plants.
“It was this conflict between photosynthesis and transpiration – that was the kernel of the idea,” Paton says. He started by pondering an age-old conundrum: while sunlight is essential for photosynthesis and growth, the heat that accompanies it makes plants transpire and lose water. In arid places, the benefits of boundless sunshine are overwhelmed by the extreme heat and dryness, meaning farming becomes too water-intensive for it to make any sense.
Paton began drawing up an invention that could capitalize on the desert’s abundant sun, while simultaneously creating a freshwater-fuelled habitat for plants. He thought it could work. But without tests, it was hard to be sure. Paton asked his colleague, Philip Davies, a mechanical engineer with experience in climate modeling, to examine his greenhouse virtually. Davies looked at elements like temperature, humidity, and airspeed, using Tenerife in the Canary Islands – a region marred by decades of low rainfall and groundwater extraction – as an example. The tests were encouraging. Constructed in 1994, Paton’s Tenerife prototype became the basis for his company, Light Works Ltd., the ancestor to Seawater Greenhouse.
The structure’s double-layered fiberglass roof transmitted sunlight but captured heat, diverting it through ducts into a compartment at the building’s rear. There, the heat was used to distill fresh water out of seawater for irrigation. The rest was vaporized and sucked through the growing space by fans to cool and humidify the plants, reducing transpiration. Paton calculated that a square metre of crops adjacent to the greenhouse would have required eight litres of water per day to offset what they lost in transpiration. “But inside we were using closer to one litre per square metre per day, and we were growing a better crop.”
In 2000, Seawater Greenhouse launched another project in Abu Dhabi, and then in 2004 one in Oman. Today, these are used mainly as research sites for academics. But then Paton’s ideas caught the attention of businessman Philipp Saumweber, an ex-Goldman Sachs investment banker who had moved into the agricultural sector. By 2010, they had joined forces and were moving into the deserts of South Australia for the company’s first overtly commercial venture. At a site near the city of Port Augusta, they built a gigantic solar plant, designed to create enough heat to evaporate several thousand litres of freshwater a day from seawater that had been piped in from the Southern Ocean.
But, after disagreements about the precise aims of the project, Paton ultimately split with Saumweber, who now runs it under the auspices of Sundrop Farms. The greenhouse has since expanded to 20 hectares and supplies 15 percent of the Australian tomato market.
Somalian expats in the UK noticed the project’s huge success. But when they asked Paton if he could take it to the Horn of Africa, the designer hesitated. “It was just too expensive,” he says. The vast solar plant and huge workforce that made the Australian project work wouldn’t translate to the Horn’s harsh and often insecure territory. “But then I went back to the drawing board, and realized it could – if I made it really simple, and stripped it back to the basics.”
Philipp Saumweber with Sundrop Farms' desert-grown tomatoes. Saumweber and Paton split after disagreements about the aims of the project. Sundrop Farms
Paton, Rothera and Fletcher started work in Somaliland in early 2017, with a £518,000 grant from Innovate UK. It wasn’t easy. As a condition of their presence, the group had to be ushered everywhere by a team of armed guards. At one point the fierce desert winds became so hot that they had to halt construction entirely. But, at length, they began building on some land leased by the Somaliland government, which conveniently lay just 200 metres from the shimmering Gulf of Aden, an abundant source of free saltwater.
The location was perfect, but almost everything else brought a major challenge: the greenhouse had to be cheaper, and able to withstand the 42°C temperature extremes and searing desert winds. For Davies, the modeller – who now works at Aston University – these conditions made life extremely difficult. “It was reduced down to its bare bones. As the design became simpler the modelling actually became more challenging.”
Davies joined forces with Sotos Generalis and Takeshi Akinaga in the University’s mathematics department to build a climate modelthat would simulate the ideal growing conditions for crops. They factored in regional data on wind speed and direction, orientation, humidity, solar radiation, air temperature, and satellite readings of ground temperature.
The result is what Paton calls “a grown-up Bedouin tent”, a solar-powered one-hectare greenhouse made of lightweight, photoselective shade netting that reflects hot infrared light to shield the plants below. Cued by the model, Paton decided to take advantage of the desert’s prevailing summer and winter winds to push water vapour through the internal space – instead of using the standard fans, which would have doubled the cost.
Each day, Sundrop Farms turns one million litres of seawater into fresh water – and then uses that water to grow food. Sundrop Farms
At each end of the tent, the team built a 1.5 metre wall from layers of porous, resilient cardboard – a feature at other sites – which is designed to be soaked regularly with seawater pumped in from a beach well. As the hot, dry desert winds waft through the wall, they evaporate freshwater and vaporize it into the growing space, which cools and humidifies the interior. That reduces temperatures by 10 to 15 °C. As a result, crops are losing only one to two litres of water per square metre per day through transpiration, compared to the 15 they’d lose outside, Paton says.
A solar-powered desalination machine makes freshwater for irrigation. “[It’s] the size of a washing machine, costs about £6,000, and it’s the first one in the Horn of Africa. That’s completely nuts!” Paton says. Of every litre of seawater it processes, 30 percent is transformed into fresh liquid. The leftover super-salty brine is then evaporated in trays, leaving behind a crust of salt – the plant’s first product, being developed for sale in Somaliland and Ethiopia. (This is a bid to avoid the ecologically damaging process of pumping unused brine back into the sea, as most desalination plants do.)
Many hurdles lie ahead. Seawater Greenhouse is still working out how to supply vegetables to the local market, and Paton says the plant will likely produce only half the yield per square metre compared to the Australian project. He’s encountered academics who fear the high humidity conditions inside seawater greenhouses may even be damaging for crops. Others have enduring scepticism about the economic validity of the project.
“It belongs to an ‘alternative tech’ era and mindset – whereas closed environment agriculture has now moved in to the stage of big corporate investment and large-scale urban fresh veges supply,” says John Mathews, a professor of management at Maquarie University in Australia, and author of a book about the rise of new green industries. “This is the key to generating successful enterprises and avoiding bankruptcy – something that the seawater greenhouse concept has never grappled with.”
Mathews points out the commercial chasm between Paton’s idea and the spread of larger agritech ventures worldwide – especially those providing vast amounts of food for growing urban populations. But Paton doesn’t necessarily see himself in competition with the likes of Sundrop Farms. Rather, he seems to be driven by the challenge of enabling agricultural self-sufficiency in places where it was once deemed impossible. And, he wants to leave the task of scaling up in the hands of local pastoral farmers – who make up between 55 and 60 per cent of Somalia’s population. “I am confident that output, quality and profitability will all go up as experience is acquired. For that reason, my primary focus, now that we have a fully functional site, is to arrange scale-up and training in parallel,” Paton says.
This year he plans to build an on-site training centre to teach local farmers how to grow greenhouse vegetables. The structure’s modular design will enable farmers to adopt their own one- to five-hectare plots – the dream being a network of connected, drought-resistant farms running across the country.
“One of the exciting things is that it can work all the way along our long Red Sea coastline, bringing new sources of income in arid, pastoral areas,” Shibeshi says. “If you have a greenhouse, you aren’t worried about whether there’s rain or no rain.”
Paton is also interested in the long term restorative benefits of his invention. Davies’ model predicted that the greenhouse’s cooling and humidifying effect would seep into the surrounding environment: “You can see there would be a plume of cool air coming off the greenhouse,” he says. And since the region hasn’t always been barren, Paton thinks greenhouses could return parts of it to the naturally vegetated state it was in before overgrazing and drought took hold. “I believe that when you get to, say, 20 years, you’d have enough vegetation to do the job of the greenhouses because they’re creating shade and shared humidity – changing the climate.” Because vegetation sequesters carbon, that also has broader ramifications for mitigating the effects of climate change.
The notion of a seawater-fuelled greenhouse – let alone the idea of reforesting a desert – remains too risky for some organisations, like the UK’s Department for International Development, which has rejected Paton’s funding applications multiple times. But for his doubters, Paton offers a rough calculation. He estimates that the $1.6 billion aid target for Somalia would be enough to finance 16,000 hectares of seawater greenhouses across the landscape, which could grow an astounding 4.8 million tonnes of fresh produce a year.
Many would say that’s a pipe dream, but Paton is used to incredulous reactions to his work. “Have you heard of the Shirky Principle? It’s that institutions exist to preserve the problem to which they have a solution,” he says. “Sending food to starving countries is this knee-jerk reaction. How much have we sent to Somalia and Ethiopia, and what dent has it really made? If some of that humanitarian aid could instead be directed towards encouraging self-sufficiency, everyone would win.”
Pittsburgh Farmer Takes The Highway To Hydroponics
Pittsburgh Farmer Takes The Highway To Hydroponics
- Eric Hurlock, Digital Editor
- Apr 13, 2018
BALLY, Pa. — Three hundred miles may seem like a long way to go for lettuce, but Tuesday’s trip to Butter Valley Harvest Farm was well worth the extra gas for Henry Wilde.
The Pittsburgh farmer is relatively new to hydroponics, and Butter Valley was offering some veteran tips during a teaching session organized by the Pennsylvania Association for Sustainable Agriculture and Penn State Extension.
“I’ve been running my own (hydroponics) farm since August, and I’ve never been to a working farm, so I’m working through every learning curve as it comes up,” said Wilde, who farms butterhead lettuce. “I wanted to come here and talk to someone who’s been doing it for 10 years.”
Seeing Ryan Ehst’s hydroponic operation was an eye-opening experience.
“He’s got all these channels right up next to one another because he’s got these small crops,” Wilde said. “And that surprises me because I could be growing a lot more stuff in the same number of square feet.”
Wilde was one of about 20 people in attendance at the session. And while he may have traveled the farthest, his reason for attending was similar to everyone else’s: curiosity.
Chelsea Mackie is in a farmer apprenticeship program at Pennypack Farm in Horsham and had never seen a hydroponic farm. She was surprised that the growing environment was less controlled than she thought it would be.
“It sounds like you still deal with a lot of the same issues you would if you were growing in the field,” she said. “It’s probably easier in some ways and harder in others.”
Changing perceptions and expanding knowledge was a main goal of the event for Ehst, who led the group on a tour of his Butter Valley Greenhouses. The growing facilities consist of four 22-by-128 foot bays, three of which are connected and used for growing herbs and greens, and the fourth for growing tomatoes and cucumbers.
Ehst grew up on the farm, which traces its roots back to a land grant from Pennsylvania founder William Penn.
Looking for a way to expand operations, he and his father, who had just retired from teaching, formed a partnership, drew up a business plan, and went forward with hydroponics.
They broke ground in 2008 and started growing a year later, but didn’t reach capacity until well into 2010, “because you can’t just plant your greenhouse full and get rid of it unless you want to give stuff away.”
They originally planned for three tomato houses, but realized pretty quickly that was too risky, so they scaled back and expanded into greens.
“The business plan we wrote was for three bays of tomatoes, and we would have never made it,” he said. “Tomatoes are a lot of risk/reward scenario. After the first risky year, we said that’s enough, and got into more greens.”
In their third year, they added a fourth house and reconfigured the original greenhouses to better accommodate growing greens.
Along the way, they added a geothermal heating system that allowed the farm to heat the greenhouse with a sustainable source: the earth itself.
The only time the farm uses its propane heaters is when the outside temperature dips into the 20s.
The farm’s main crops are cherry and beefsteak tomatoes, cucumbers, basil, butterhead lettuce, salad blend lettuce, arugula, and watercress. To a smaller degree, they grow baby kale, baby bok choy, romaine lettuce, and spinach.
Ehst started out selling to a few area chefs and grocery stores and has been adding customers ever since. His largest buyer now is Lafayette College in Easton, which features his produce in its dining halls. Ehst also manages an on-farm market.
The process of growing hydroponically is pretty simple, he explained. Instead of growing in soil, the plants grow in water that has been supplemented with nutrients.
The system Ehst uses for his greens is a closed system, where the nutrient-rich water is circulated by a pump. But for his tomatoes and cucumbers, it’s an open system where gravity controls the flow of the nutrients.
Ehst uses rock wool to start tomatoes from seed in January. Once the seedlings are established, they are transferred into a system of interconnected buckets, two plants per bucket, and set in the greenhouse.
There are 360 buckets growing 720 tomato vines suspended by spools of string, which will be moved throughout the greenhouses as the vines grow, letting the plants climb up to 50 feet by the end of the season, from March to October.
“The hope is that each plant gets a minimum of 30 to 35 pounds (of fruit). If everything goes well, it should be over 40,” Ehst said.
The air in the tomato house was thick and warm and had the smell of a backyard garden in August. The plants were already towering nearly 6 feet high, heavy with blossoms and fruit. Big fans kept the air circulating.
But there was another, smaller buzzing sound in the air too: Bumblebees.
The farm brings in hives of bees to do the pollination work throughout the growing season.
The biggest challenges the farm faces in the greenhouses are downy mildew on the basil and powdery mildew on the lettuces. Ehst says it’s easier for him to prevent these problems than it is to get rid of them once they appear on his crops. Diligent, methodical surveying of his plants is necessary, as is inspection of their nutrient delivery system, where algae will occasionally start to grow and cause the system to clog.
By the end of the tour, the finer points of farming in water started to soak in, giving Wilde a lot to think about on his long journey back to the Steel City.
What impressed him most was the geothermal system that heats the greenhouses.
“He doesn’t use any propane until it gets to 28 degrees,” Wilde said. “My gas bill in January was $5,500. You have to grow a lot of lettuce to overcome $5,500 gas bills.”
French Engineering Office Is Marketing The First Online Software To Facilitate The Construction Of Energy Efficient Greenhouses.
After 5 years of Research & Development, Agrithermic a French engineering office is marketing the first online software to facilitate the construction of energy efficient greenhouses.
Called Hortinergy, this decision-making tool enables producers and agricultural consultants to compare and size different equipment in order to reduce energy costs.
Savoie Technolac April 26th, 2018 - Energy is a major expense in greenhouse productions and with energy prices volatility we have not heard the last of this.
Technical solutions currently exist on the market to help reduce energy costs: curtains, etc. For growers, consultants or suppliers the dilemma is how to choose an optimal configuration adapted to the climate, crop(s), and yields and to determine the investment payback.
Hortinergy is the first online software that can simulate energy consumptions of an existing or planned greenhouse anywhere worldwide.
The library includes the major equipment available on the market: glass, plastic films, climate screens, etc. Equipment manufacturers can spotlight their branded products for select pre-set parameters to simplify the user experience.
As decision-making tool to evaluate energy-saving options Hortinergy helps to calculate the required dimensions of equipment and to optimize the investment: users compare economical and technical scenarios with a simple online interface. A detailed report is sent for each scenario. Outputs include heating consumptions, dehumidification needs, photosynthetically active radiation (PAR) reaching canopy, etc. for hourly, monthly or annual periods.
Hortinergy allows users to determine optimal configurations for investment and energy savings which can be up to 50% for renovations and more than 70% for innovative greenhouse concepts.
Innovative algorithms take into account greenhouse-specific parameters, such as: light transmission through the transparent cover, external and inner climate regulation (screens, VPD, etc.), canopy evapotranspiration, crop types, etc.
Result reliability was validated with measurement campaign in classic and semi-closed greenhouses. For example, the comparison with the Wageningen University & Research (WUR) greenhouses showed an accuracy with less than 10 percent margin error.
In partnership with leading companies in the horticulture industry and research centers, multiple add-ons will complete the software.
Hortinergy competes for the 2018 GreenTech Innovation Awards and will be part of the AgTech innovations presented at VivaTechnology Paris 2018.
About Agrithermic:
Agrithermic is an engineering office specializing in energy efficiency of horticultural greenhouses.
Based in the French Alps, this small company is now recognized among European specialists in this specific issue. Its regular customers include leading companies.
Whole Foods Local Producer Program Helps Microgreens Producer
Whole Foods Market will award an $80,000 loan to Greenbelt Microgreens as part of the grocer's Local Producer Loan Program, which grants low-interest loans to growing local artisans, farmers, and producers.
Whole Foods Local Producer Program Helps Microgreens Producer
APRIL 05, 2018
Whole Foods Market will award an $80,000 loan to Greenbelt Microgreens as part of the grocer's Local Producer Loan Program, which grants low-interest loans to growing local artisans, farmers, and producers.
Greenbelt Microgreens, a certified organic greenhouse grower of soil-based microgreens, grows year-round locally in British Columbia, Ontario and New York state, and plans to utilize the loan to expand its packing and cold storage space at its greenhouse in Maple Ridge, BC.
The organic microgreens, which include arugula, pea shoots, sunflowers, broccoli, and radishes, are early-stage vegetables that have a delicious flavor profile and a very high nutrient density because of their young age (10-14 days).
“Our commitment to local farms and artisan producers drives our ability to offer new and interesting products to our customers that are local to their region,” said Denise Breyley, local forager for the Pacific Northwest and western Canada. “These relationships give us the opportunity to seek out the best products, while also giving local farmers and food artisans the tools and guidance to help them grow their business.”
Whole Foods Market North Vancouver, opening on April 26, will also feature a strong selection of local and regional products.
Whole Foods Market is committed to the concept of fresh, healthy, local foods, and supporting both local products and the people who supply them. Loan recipients must meet Whole Foods Market’s quality standards, use the funds for expansion and have a viable business plan. Typical loans range from $1,000 to $100,000 and have fixed low-interest rates.
Previous recipients have used their loans for purchasing more livestock, investing in new equipment, expanding production facilities, adapting to more sustainable practices or converting to organic production. The Greenbelt Microgreens loan will be the sixth for small business owners in British Columbia, for a total of over $400,000. Overall, more than $2 million has been distributed to recipients in the Pacific Northwest.
56 Turbines And A 20 MW Battery To Supply 10 ha Greenhouse With Renewable Energy
The LED lamps of the 10-hectare Australian agribusiness Nectar Farms are to be powered with wind and battery storaged energy. The greenhouse will share its site with a power renewable power company Neoen.
56 Turbines And A 20 MW Battery To Supply 10 ha Greenhouse With Renewable Energy
The LED lamps of the 10-hectare Australian agribusiness Nectar Farms are to be powered with wind and battery storaged energy. The greenhouse will share its site with a power renewable power company Neoen. They ordered the building of a pioneering wind complex. A wind farm will be installed by Siemens Gamesa Renewable Energy with 56 of the firm's SG 3.4-132 turbines (for total capacity of 194 MW) and a battery energy storage system.
Stawell
According to the Victorian government, this project will make the advanced agriculture facility the world’s first ever crop farm to be completely powered by renewable energy. “This is an exciting initiative which illustrates how renewable energy can unlock opportunities for large, energy-intensive businesses to create jobs and build a better future for regional communities", says Lily D’Ambrosio, Minister for Energy, Environment and Climate Change.
The whole project is to be realised at the Bulgana Green Energy Hub, located in the Australian town of Stawell, in the state of Victoria. The whole facility will comprise a 194 MW wind farm as well as a 20 MW / 34 MWh lithium-ion (Li-ion) battery. Construction is set to begin right away and the commissioning of the facility is expected by August 2019.
The power of the complex is to be purchased by two partners: the government of the state of Victoria has agreed to buy the power for the next 15 years, and the Nectar Farms has agreed to do so for the next 10 years.
LED light technology
Nectar Farms will use LED light technology to grow tomatoes in glasshouses. In total, they plan a 40-hectare facility.
It is estimated that 97% of Nectar Farms needs will be supplied by 15% of all of the electricity generated at the wind plus storage facility, with the rest going directly to the local grid. Only 3 percent of Nectar Farms' energy demand cannot be supplied with wind energy when longer no-wind-periods occur.
Nectar Farms will also receive the power stored in the batteries during low wind periods. The energy supplied directly from the wind farm, at a lower cost than available from the grid, helped its business case to proceed.
Bulgana Green Energy Huby
Under the terms of the contract entered into with the renewable energy IPP, Neoen, Siemens Gamesa will build the entire complex on an EPC basis and then maintain it for 25 years.
For more information:
Siemens Gamesa
www.siemensgamesa.com
Publication date: 4/12/2018
The Russian-Japanese Company Will Produce up to 6,000 Tons of Vegetables A Year
Up to 6 thousand tons of greenhouse production per year will increase the production capacity of the resident of TOR "Khabarovsk", agrofirm JGC Evergreen.
April 3rd, 2018
The Russian-Japanese Company Will Produce up to 6,000 Tons of Vegetables A Year
The third phase of innovative greenhouses, the resident of the TOP Khabarovsk will be put into operation in 2021
AmurMedia. Up to 6 thousand tons of greenhouse production per year will increase the production capacity of the resident of TOR "Khabarovsk", agro firm JGC Evergreen. As a result of the introduction of the third phase of innovative greenhouses, the Russian-Japanese company will fully satisfy the demand of the inhabitants of the regional center for organic vegetables.
Today cucumbers, tomatoes, sweet pepper, leaf lettuce, radish, green cultures under the brand name "New Day" are sold in four branded points of the agricultural firm and several shops in Khabarovsk.
According to the general director of the enterprise Tomoyuki Igarasi , agro firm has a plan to compete with analogs from China for quality and price. "The close location to the points of sale allows us to deliver fresh vegetables to the store as soon as they are ripe, this is the difference from remote suppliers whose product matures en route.Our mission is to give customers the joy of enjoying a quality product," the general director of the company said.
According to the chief agronomist JGC Evergreen Svetlana Gudkova , the main quality control is carried out in the laboratory, and the goal is to make sure that the vegetables do not contain nitrates and heavy metals.
The townspeople pay tribute to the crops from the Russian-Japanese greenhouses. "A couple of weeks of cucumbers with the" New Day "logo were not on sale," said Olga Koval, a Khabarovsk resident, who was brought from the Amur Region, from Sakhalin, from China . "By the way, many times the sellers have tried to give out the goods for "Evergreen".
The manufacturer has protected its brand from counterfeits: the packaging of vegetables contains a bar code and a label indicating the variety that is damaged at the dissection. Re-paste it is impossible.
A few years ago, local manufacturers provided the need for fresh greenery only by 10%, said Oleg Fomin , head of the food and food resources department of the Khabarovsk administration . Since 2015, a real greenhouse boom has started, and the city's self-sufficiency in vegetables has risen to 60%. The main role in this was played by the company JGC Evergreen, which became the first foreign resident of the territory of the leading socio-economic development "Khabarovsk".
"The main reason for our entry into the TOP is significant tax and other preferences granted to residents, which made it possible to significantly reduce the cost of production and make it more affordable for the consumer," said Tomoyuki Igarasi.
"The anchor investor of the territory - JGC Evergreen Ltd. - is located in the" Industrial Park Avangard ", in addition to which there are three other residents. The site is well located and attracts investors focused on financing projects related to agriculture, "said Denis Tikhonov, General Director of the Corporation for Development of the Far East .
The peculiarity of this site is the complete provision of the necessary engineering infrastructure at the expense of the federal and regional budgets. Water, electricity and gas supply networks are connected to the territory. Also, at the moment, about 5 km of road infrastructure has been repaired, and in July 2019 the repair of the route leading to the boundaries of the land plot of the Avangard site will be completed. The customer of all the works was the administration of Khabarovsk.
Using the advantages of the resident of the TOP, JGC Evergreen (82.2% owned by the Japanese holding company JGC, the rest of the stake is owned by the Russian company Energo-Imuls-Plus) began construction of the greenhouse complex simultaneously with the creation of the Khabarovsk TOR in June 2015. Investments in the first place of the project amounted to 556 million rubles. For five months, greenhouses with an area of 2.5 hectares with a capacity of up to 400 tons of vegetables per year were built and put into operation.
"This is the first agricultural project for us in Russia, we believe that the experience is successful, and we will continue the development of greenhouse complexes," said Honorary Chairman of JGC Group Yoshihira Sigahisa .
At the end of 2017, during the "Days of the Far East" in Moscow, the construction of the second stage was officially completed, to which 480 million were invested.
"With the introduction of the second phase, we will increase the volume of vegetable deliveries to 1.3 thousand tons per year," Tomoyuki Igarashi said during a teleconference with Prime Minister Dmitry Medvedev .
"There is no doubt that we are very interested in developing the production of a wide range of products - both industrial and agricultural - in the Far East, which is why I, and my colleagues, are really engaged in this on a permanent basis," the prime minister replied.
Thanks to the introduction of the second stage of production, the assortment of hothouse vegetables has significantly expanded. "The townspeople appreciated our radish Donar," said Ekaterina Panova, assistant to the general director of the enterprise , "he has a short, but edible top-up." In turn, the production of eggplants. " In addition to tomatoes and cucumbers, leaf lettuce and rukola are grown here. The experimental batch of sweet pepper of the cultivar Tequilo has already been sold - it has an unusual rich violet color and a bright aroma.
The Russian-Japanese resident of the TOP in the near future plans to expand the range of Japanese strawberries, and is also working on the possibility of growing a number of crops in the open ground, such as potatoes, carrots and onions. This will allow not to stop production even in the summer months, when the greenhouses are closed for sterilization.
The agro-company intends to proceed with the construction of the third stage of greenhouses and increase their area to 10.3 hectares. The total investment is estimated at 2.3 billion rubles. There will be 150 new jobs.
"Today, many Japanese companies, knowing about this successful experience, are constantly consulting with us about how quickly to get started in Russia." In our view, the secret of success is the constant attention of federal and regional authorities to our project, "said the senior executive director of the corporation JGC Masanori Suzuki.
ТОР "Хабаровск", created on June 25, 2015, consists of three sites: "Airport", "Rakitnoe" and "Avangard".
According to calculations by the Agency for Investment and Development of the Khabarovsk Territory, by the year 2025, 9,706 jobs will be created by the residents of the territory. The volume of taxes paid to the budgets of all levels will reach 10.475 billion rubles (6% of total taxes to the regional budget). The attracted investments will amount to 5.05 rubles for each ruble invested by the state, or 60 million rubles per 1 ha of a resident land plot.
The material was prepared by the Far Eastern United Editorial Board (DOR).
Подробнее: https://amurmedia.ru/news/681922/
Joe Spano With Mucci Farms On The Company’s Expansion Into The US
Mucci Farms has completed the first phase (24 acres) of greenhouse expansion in Huron, Ohio, and harvest will begin in May.
Joe Spano With Mucci Farms On The Company’s Expansion Into The US
“We want to be close to the customer”
Mucci Farms has completed the first phase (24 acres) of greenhouse expansion in Huron, Ohio, and harvest will begin in May. “For the first phase, we chose Tomatoes On-The-Vine (TOV) because it is amongst the commodities with the highest demand from consumers,” says Joe Spano with Mucci Farms. The new facility is equipped with HPS grow lights, making it important to choose a product that sees high demand during the winter months. TOV’s will be grown in Huron year-round and a 70,000 square foot warehouse has been built on site for packing and distribution.
This is the company’s first expansion outside of Canada. “A majority of our product is currently sold in the US, so proximity to market was an important decision-making factor,” said Spano. “Having a US location also helps us reduce travel miles, save travel time by being able to avoid a border crossing as well as accommodating US consumers that prefer locally-grown product.”
From a farming standpoint, it is ideal as the geographic location is right across from Kingsville, on the opposite side of Lake Erie. “Weather patterns and growing conditions are almost identical, preventing us from having to learn alternative processes,” Spano mentioned.
By 2020, construction of phase two and three should be finalized, covering a total of 60 acres under grow lights. “Phase two and three will also be heavily dominated by TOV’s, but we may grow a small amount of specialty tomatoes as well,” shared Spano.
Unveiling new cucumber product at CPMA
Mucci Farms will be exhibiting and once again sponsoring the relaxation lounge at CPMA. Inspired by the western Canadian boho theme, this year’s lounge has been rebranded as the “Core Meeting Space.” Located just before the entrance to the show floor, attendees can get off their feet to relax or find a quiet place to meet away from the busy atmosphere. “This show is very important to us,” said Ajit Saxena with Mucci Farms. “It’s in our home country and offers a great opportunity to showcase Canadian farmers. We’ve worked closely with CPMA throughout the years and in a way, we feel like hosts as people travel from all over to attend this show.”
In addition to Natural Organics and Veggies To GoTM that will be showcased, the company will also unveil a fresh new look for its SmucciesTM Sweet Strawberries. In addition, a brand-new item called CuteCumberTM Poppers will be unveiled. “These one-bite Poppers are a unique variety in that they only grow to about half the size of our CuteCumbers and we’ve decided to remain focused on value-added consumer convenience by including a dip inside the package,” Saxena said.
To get a closer look at all Colors of Flavor, Mucci Farms is inviting attendees to “pop in” to booth #921 on April 25 or 26 in the Vancouver Convention Centre.
For more information:
Ajit Saxena
Mucci Farms
Tel: (+1) 519-326-8881
Publication date: 4/19/2018
Author: Marieke Hemmes
Copyright: www.freshplaza.com
1mn sqm of Land For Indoor Farming To Boost Qatar’s Agri Sector
Al-Khalaf said the 1mn sqm project will involve more than four local farms, and could operate by the end of 2019 or early 2020 if plans pushed through as scheduled.
1mn sqm of Land For Indoor Farming To Boost Qatar’s Agri Sector
April 02 2018
Nasser Ahmed al-Khalaf.
Qatar agriculture sector's self-sufficiency efforts will get a further boost with a plan to develop 1mn sqm of land for indoor farming, prominent Qatari agriculturist Nasser Ahmed al-Khalaf told Gulf Times.
“Now we are developing other farms and we have under study some other projects, which can reach 1mn sqm in total,” said al-Khalaf, the owner and managing director of Agrico.
A private Qatari agricultural development company, Agrico was established in 2011 with the aim of helping the country achieve food security. Agrico operates a 120,000sqm (12 hectare) organic farm in Al Khor.
Al-Khalaf said the 1mn sqm project will involve more than four local farms, and could operate by the end of 2019 or early 2020 if plans pushed through as scheduled.
“Currently we are putting the feasibility study and the drawings,” he noted, adding that such initiative can significantly increase the country’s fresh produce and help efforts for self-sufficiency.
Al-Khalaf said Agrico invested in research and development, trying to develop indoor farming in the past two and a half years to produce fresh vegetables all year long in Qatar.
“We have modified technology developed in the Western World, and adapted it even further to have a very unique system anywhere in the world,” he stressed.
The Qatari agriculturist cited a significant increase in the production of fresh vegetables this winter, covering more than 20% of the country’s total consumption.
“The final figures will not be known until the season is finished,” he said. “Some farms will finish by end of April, the remaining will finish by end of June but some other farms are producing all year long.”
Agrico built an additional 120,000sqm of “seasonal greenhouses” to grow more fresh vegetables during the winter season amid the blockade on Qatar, in addition to its 120,000sqm facility, which operates year-round.
According to al-Khalaf, these seasonal greenhouses will stop operating during the summer but actual greenhouses (using 120,000sqm of land) will continue to produce, about five tonnes of fresh vegetables daily.
He added that Agrico and other local farms are producing more herbs now such now as coriander, spinach and parsley, among others, to meet the growing demand in the country.
Fruit production may take more time since it will require more land unlike vegetables.
Al-Khalaf added most of the farm owners in the country are continuously expanding their cultivation area and growing more varieties of vegetables.
The Netherlands: Hands-On Mentality At Bom Group Suits John Meijer Well
The Netherlands: Hands-On Mentality At Bom Group Suits John Meijer Well
John Meijer has been working at Bom Group for less than a year. In mid-2017, there was a vacancy for a Commercial Manager at a greenhouse construction company in greenhouse horticulture. This function also included joining the Management Team within Bom. John already worked for a greenhouse construction company. His ambitious considerations were decisive. At Bom he could advance his career. Furthermore, it also suited his résumé perfectly. Mike Vermeij is general manager at Bom and the gentlemen knew each other well from their previous employer. John: "We have a good business relationship. We have a good understanding. Trust is important in order to perform this function properly so that Bom Group can continue to flourish and grow. "
In terms of staff, the Bom Group is smaller than his previous employer. This requires an even greater hands-on mentality (for which horticulture is already known for). A lot of initiative is demanded, but also more room for initiative is given. John: "I like that. I can easily share my ideas here. Furthermore, it strikes me that on the one hand the existing management is and remains involved and on the other hand gives the ‘new’ management room for new ideas. That's great, right? We learn a lot from each other and together we arrive at new insights and solutions, and complement each other well and that is beneficial for the company."
These are good times for the greenhouse builders. There is every reason to be positive. Of course they are also aware of this at Bom. On the other hand, they have not forgotten that there also were less flourishing times. John: "The management is well aware of that. That awareness has resulted in a down-to-earth mentality. We are now mainly busy to make the whole process even more efficient, so that the turnover can continue to grow. We actually see growth separate from growth of the number of employees. That does not necessarily have to go hand-in-hand. At the moment we have a labor force of 43 people and that number may go up to 50 to realize an optimal process. "At Bom Group there is room for work planners, quantity surveyors and warehouse staff. Current vacancies can be found here (and interested persons may contact Rob Grootscholten).
For more information:
Bom Group
John Meijer
Kulkweg 60
3151 XE Hoek van Holland
T:+31(0)174 629 441
E: j.meijer@bomgroup.nl
www.bomgroup.nl
NatureFresh™ Farms Kicks Off 2018 Growing Season With Wide Variety
It is an exciting time of year at NatureFresh™ Farms – the company’s Leamington, ON greenhouses have started full production for the 2018 growing season!
NatureFresh™ Farms Kicks Off 2018 Growing Season With Wide Variety
Leamington, ON (April 13th, 2018) – It is an exciting time of year at NatureFresh™ Farms – the company’s Leamington, ON greenhouses have started full production for the 2018 growing season! In addition to greenhouse-grown Peppers, Tomatoes, and Cucumbers, NatureFresh™ Farms is now offering Organic Sweet Bell and Mini Sweet Peppers. There is plenty of fresh news to celebrate in Ontario this season!
As one of the largest Bell Pepper growers in North America, NatureFresh™ Farms continues to offer Red, Orange, and Yellow Sweet Bell Peppers for North American consumers. The 2018 season is especially exciting for Bell Pepper growing at NatureFresh™ Farms because of their recent expansion of organically-grown offerings. Along with Organic Sweet Bell Peppers, NatureFresh™ Farms is now growing Organic Sweet Mini Peppers for North American consumers.
With production now beginning in Ontario, the popular TOMZ® Snacking Tomato line will be grown in both Ontario and Ohio greenhouses. Using the same growing processes and methods at both facilities, NatureFresh™ Farms is committed to providing the same exceptional flavor and great quality that consumers expect from TOMZ® grown in both Ontario and Ohio. The TOMZ® Snacking Tomato line includes Red Grape, Orange Grape, Yellow Grape, Cocktail, and Red Cherry Tomatoes, as well as the exciting new Tomberry® Tomatoes! The TOMZ® line is sold in vibrant, convenient packaging, which will be easy to spot as products hit store shelves this season.
NatureFresh™ Farms also provides consumers with high-quality, consistently fresh Long English and Mini Cucumbers. With a recent expansion to boost production, Cucumbers from NatureFresh™ Farms will be available year-round!
Produce grown in NatureFresh™ Farms Ontario greenhouses will consistently be shipped to North American retailers starting in April 2018. But what Niels Klapwijk, the company’s Retail Account/Procurement Manager, is most excited about this season is the wide variety of Ontario-grown produce options now being offered by NatureFresh™ Farms: “By increasing the variety of commodities grown at our farm, NatureFresh™ is further defining itself as a leader within the fresh produce industry. This form of growth for the company is very exciting.”
With a diverse range of commodities now being grown in Leamington, ON, NatureFresh™ Farms continues to develop its greenhouse operations to successfully serve retail partners and respond to the evolving needs of the consumer
"Radiant Heat SON-T Reaches Deeper Than Convection Heat LED"
Dutch grower Lans Zeeland has the first large greenhouse where tomatoes are cultivated under full LED. The ClimaLED3 system from QWestland provides white light and is equipped with a small fan that aids the lamp in reducing heat.
Full LED at Lans Zeeland:
"Radiant Heat SON-T Reaches Deeper Than Convection Heat LED"
Dutch grower Lans Zeeland has the first large greenhouse where tomatoes are cultivated under full LED. The ClimaLED3 system from QWestland provides white light and is equipped with a small fan that aids the lamp in reducing heat. In terms of design, the lights look more like SON-T luminaires than the red / blue bars used in most LED experiments. In the context of the monitoring project, which is financed by Kas als Energiebron (Greenhouse as Source of Energy), Wageningen University & Research, Business Unit Greenhouse Horticulture, follows this cultivation at Lans and additional measurements have been carried out into the temperature and light distribution in the greenhouse.
By means of a thermal imaging camera and ventilated temperature sensors, it turned out that the fan blowing down which reduces lamp heat would indeed result in a higher head temperature under the lamps. The smoke tests also showed that the air movement from the lamps does not extend beyond the head of the crop. This makes the temperature of the head under LED lighting higher than at the bottom of the crop. This difference is even higher than with SON-T and that is contrary to expectations. Apparently, the radiant heat of SON-T lamps reaches deeper into the crop than the convection heat of the LED lamps. In itself, this does not have to be a problem, but it is important to take this into account in the heating strategy.
Heat usage
Furthermore, the greenhouse with LED lamps has, in comparison with a nearby greenhouse with an almost equal consumption of electricity, realized a 1 °C higher greenhouse temperature and a 6% lower RH with 10% less heat usage. This is striking because it is usually assumed that LED lighting actually leads to more heat consumption.
All lamps are suspended below the girder. This way they have to bridge a distance of 5 meters. And since the LED lights shine a bit more down than the wider-beam SON-T lighting, this gives a less even light distribution at head height (1.9 m below the light). Deeper in the crop the light distribution of the lamps is more or less the same. Whether the uneven light distribution is a disadvantage for production has not been established yet. Over time, all the crop heads will be straight under the light once. Moreover, it has been found that the temperature right below the lamps is ± 1 °C warmer than between the lamps. This can be an advantage when the crop gets more light.
This project is funded from the Kas als Energiebron program, the innovation and action program of LTO Glaskracht Nederland and the Ministry of Agriculture, Nature and Food Quality.
Read more about this project at this link. (In Dutch)
For more information:
Kas Als Energiebron
www.kasalsenergiebron.nl
Publication date: 3/29/2018
Pure Flavor® - IFCO Partnership Ensures Year-Round Delivery of Quality Fresh Produce Across North America
Pure Flavor® - IFCO Partnership Ensures Year-Round Delivery of Quality Fresh Produce Across North America
Use of Shared and Reusable “Smart Packaging” Maximizes Operational Efficiency
Tampa, Florida (February 27, 2018) - Pure Flavor®’s use of IFCO Reusable Plastic Containers (RPCs) has had a positive impact for the Leamington, Ontario-based, a vertically integrated provider of a wide variety of fresh produce products year-round to retailers across North America. After six years of collaboration, Pure Flavor®’s use of IFCO RPCs has continued to grow rapidly to include packaging for a wide range of products, including tomatoes, peppers, cucumbers, and eggplants.
“IFCO is a valuable partner,” said Jason Veno, Packaging Operations Manager for Pure Flavor®. “Not only do they provide us with ‘smart packaging’ that protects and cools our products extremely well, they maximize our operational efficiency by ensuring we have an adequate supply of RPCs year-round, even during peak growing seasons. That predictability means we can continue to serve our customers and their shoppers efficiently, effectively and on time”, said Veno.
IFCO now provides Pure Flavor® with over one million RPCs annually. They are used to package fresh produce at locations in San Antonio, Texas, Romulus, Michigan, and Leamington, Ontario, and are then shipped to retailers throughout the U.S. and Canada.
“IFCO’s partnership with Pure Flavor® is based on thoughtful collaboration and the shared goal of providing consumers with a constant supply of high quality, safe, nutritious and affordable produce each- and every- day,” said Daniel Walsh, President, IFCO North America. “Our RPCs are tailor-made for growers like Pure Flavor® that want the best possible efficiency and sustainability for their packaging, and we are proud to work side-by-side with such a visionary company. We are also proud of our presence and expansion in the Canadian marketplace, as well as the supporting infrastructure we have established there to better serve our many Canadian customers.”
IFCO and Pure Flavor® have developed a forecasting model that tracks the company’s produce orders and growing seasons and ensures on-time delivery of the right number and type of RPCs throughout the year. In addition, some RPCs are stored on-site, providing the Pure Flavor® operations group with greater flexibility to manage its product flow.
Ongoing collaboration between Pure Flavor® and IFCO will continue to optimize supply chain operations, as well as reduce the companies’ environmental footprint in the months and years ahead.
IFCO and Pure Flavor® will be exhibiting at the upcoming Southern Exposure Convention & Trade Show in Tampa, FL on March 3rd. IFCO will be located at Booth #120. Pure Flavor® will be located at Booth #605. Retail partners are encouraged to stop by the Pure Flavor® booth to learn more about the company’s greenhouse vegetable products as well as the expansion to Georgia with a new 75-acre high tech greenhouse facility.
Additional information -
Pure Flavor® is a family of greenhouse vegetable growers who share a commitment to bringing A Life of Pure Flavor™ to communities everywhere. Our passion for sustainable greenhouse growing, strong support for our retail & foodservice customers, and focus on engaging consumers is built on a foundation drawn from generations of growing expertise. We are the next generation of vegetable growers, inspired to put quality, flavor, and customers first by providing greenhouse-grown vegetables from our farms that are strategically located throughout North America. http://www.pure-flavor.com/
IFCO is the leading global provider of reusable packaging solutions for fresh foods, serving customers in 50+ countries. IFCO operates a pool of over 290 million Reusable Plastic Containers (RPCs) globally, which are used for over 1.4 billion shipments of fresh fruits and vegetables, meat, poultry, seafood, eggs, bread, and other items from suppliers to grocery retailers every year. IFCO RPCs ensure a better fresh food supply chain by protecting freshness and quality and lowering costs, food waste and environmental impact compared to single-use packaging. IFCO is a Brambles Company. www.ifco.com.
Saint Lucia Launches Climate-Smart Greenhouse Project
Saint Lucia Launches Climate-Smart Greenhouse Project
The SLCSI has received grant funding in the amount of USD$50,000 under the Global Environment Facility (GEF) program for the implementation of the first-ever “Climate Smart Greenhouse” project.
The two-year project is aimed at using technology to create a sustainable climate-smart system which can be used by farmers in Saint Lucia.
The experimental project is the first of its nature in the Caribbean. It is an integration of agriculture and technology that will demonstrate effective protected organic farming practices, using a specially-designed greenhouse to cushion plants from weather elements and provide an environment that can be easily manipulated.
The project utilizes an integrated, automated farm management system that gives insight into production and the farm business.
The first instalment of the grant is in the amount of USD$50,000. A further grant of USD$150,000 is contingent on the success of the project.
Publication date: 3/28/2018
Creating The Climate Needed To Provide Produce
Creating The Climate Needed To Provide Produce
The GrowHaus, located in Denver, Colorado is a non-profit greenhouse operation that has successfully established a program designed to create a community-driven, neighborhood-based food supply system that serves as a hub for food distribution and provides educational and economic opportunities. Svensson's reflective Solaro shade screen allows the inspiring operation to create the greenhouse environment needed to provide healthy, equitable and resident-driven produce.
The non-profit food hub operates out of Denver’s Elyria-Swansea neighborhood, an area not only described as a ‘food desert’ but also identified as being the most polluted zip code in the country due to its industrial processing heritage which dates back to the 1800’s. Residents in this environmentally wounded area have historically lacked access to healthy, affordable food and therefore suffer from high rates of diet-related challenges. The GrowHaus is working to change these conditions by addressing the community’s access to fresh and healthy food options. The organization focuses on food- production, distribution and education, with the vision to catalyze a neighborhood-based food system that is equally healthy, equitable and resident-driven. “At the root of agriculture is culture and GrowHaus is really trying to build a strong culture by using food as the lens,” describes Co-Founder, Coby Goul.
The food production facilities at GrowHaus include a variety of innovative, sustainable and community-oriented urban farm techniques, including hydroponic and aquaponic greenhouses, a mushroom farm, seedling start nursery and a permaculture farm. Bib lettuce and other leafy greens such as chard, kale, arugula, spinach, and cilantro are all produced in the 5,000 square foot hydroponic greenhouse. The crops are harvested every 1-2 weeks and are then distributed at cost to the residents of the Elyria-Swansea neighborhood through a food box program. The remaining greens are sold to local restaurants, grocery stores and specialty markets in Denver, including Whole Foods and King Soopers. The organization also operates a commercial-scale aquaponics system which occupies over 3,200 square feet.
In search of the right screen solution
Although Denver is surrounded by the Rocky Mountains, production during the warmer spring and summer months has always been challenging for GrowHaus due to the high temperatures in the greenhouses. The Aluminet shade screen they were using at the time was not providing the adequate shade or ideal conditions they needed for their plants or employees working in the greenhouse. In search of a more efficient shade solution that would enable them to meet the yields required for produce distribution within the community, they turned to Svensson. The operation needed a screen solution proven to lower temperatures, but being a non-profit the funding was limited and required a cost-effective solution that wouldn’t break the bank or put them over budget.
After taking into consideration the climate challenges, the crops they were growing and budget constraints, Svensson recommended Solaro 5120 O E, an open structure reflective shade screen. The reflective white Solaro screen had been proven to lower temperatures while also allowing more light in, giving the non-profit organization the ability to vastly improve their growing climate.
Crops no longer suffer from heat stress
Since installing the reflective Solaro shade in September of 2016, the GrowHaus team has been extremely pleased with the screen’s ability to better manage their greenhouse climate. After using the shade for a full spring and summer cycle last year, their lettuce crops no longer suffered from heat stress and the working conditions for the employees has been much more manageable thanks to the cooler climate.
Following these positive results, GrowHaus has started a fundraising initiative to raise the funds needed to purchase Solaro for their second greenhouse, with hopes to stay ahead of the spring and summer heat in all their greenhouses. To support these inspiring initiatives, donations to the GrowHaus fundraiser can be made by clicking here.For more information:
Ludvig Svensson
BrightFarms To Invest Up To 17 Million In Texas Green
180,000 Square Foot
BrightFarms To Invest Up To 17 Million In Texas Greenhouse
BrightFarms has selected Abilene as the site of its first hydroponic greenhouse farm in Texas. Construction is slated to begin this summer, and shoppers will find their greens and herbs in area grocery stores by early 2019.
The company will receive approximately 21 acres in Access Business Park in Texas, valued at $632,700, to construct the 180,000 square foot greenhouse. The project aims to begin construction in summer 2018 and be fully operational by early 2019.
The state-of-the-art hydroponic greenhouse will be constructed at an estimated cost of up to $17 million and create as many as 30 “green-collar” jobs for local residents, each paying a living wage and offering health benefits. The incentive requires the company to meet minimum performance criteria for jobs and investment over the next five years.
BrightFarms
Operating greenhouse farms to help meet the growing demand for year-round local produce, BrightFarms’s sustainable growing methods use 80 percent less water, 90 percent less land and 95 percent less shipping fuel than conventional agriculture. As the future of scalable, sustainable local farming, this model eliminates time, distance, and costs from the food supply chain.
Founded in 2011 in New York, New York, the company currently has facilities in Rochelle, Illinois; Culpeper County, Virginia; Bucks County, Pennsylvania and is in the process of opening a new location in Wilmington, Ohio.
By constructing greenhouse farms near major metros, the company’s produce is grown locally and picked at the height of freshness, delivering to supermarkets within 24 hours of harvest. By comparison, the majority of produce found on grocery shelves travel 5-7 days and thousands of miles.
Brand for retailers
BrightFarms has established a successful brand that has gained the attention of major grocery retailers, with current partners representing more than 60 percent of the U.S. grocery market. As a result, the company has put forth a plan to phase its growth over the next few years to serve customers across the U.S.
In October 2017, The Governor’s Office of EDT (Economic Development and Tourism) contacted the Abilene Industrial Foundation (AIF), on behalf of BrightFarms, to identify an ideal site as part of its efforts to expand into the southern market. The AIF works on behalf of the DCOA to promote the growth, development, and diversification of the economy in Abilene by attracting new industries.
Texas
BrightFarms asked targeted Texas communities for greenfield sites to construct its next greenhouse operation. The AIF worked with the DCOA to formulate a response, highlighting the land that was recently made available next to the Abilene Regional Airport. This area, Access Business Park, is being developed as Abilene's next-generation business park that aims to be the home for new industry in the coming years.
"Abilene's central location, available land and incentive program plays an influential role in attracting this project to the city," said Justin Jaworski, Executive Director for the Abilene Industrial Foundation.
Spin-off businesses
It is estimated that BrightFarms will generate $23.1 million in direct economic output over the next 10 years. Spin-off businesses in the community will produce $12.9 million in economic output in this same time frame, as a result of local operations. In total, the company will support $36 million in new economic output over this time. Economic output is the value of goods and services produced in the economy and can be thought of as revenues for businesses.
Kent Sharp, CEO of the Development Corporation of Abilene, said the company will contribute approximately $12.5 million in payroll to the local economy in its first 10 years. "The project itself will generate an additional $3 million in revenues to local taxing entities over this period of time, with $1.5 million accruing to the City of Abilene," he added.
As a result, the DCOA approved a 10 percent match of the investment, up to $1,700,000, leaving the remaining 90 percent to be provided by the company. "The involvement from the DCOA to incentivize this company to locate in Abilene is a testament to all the great things our city has to offer businesses," said DCOA Board President John Beckham.
For more information:
BrightFarms
Using Space-Age Technology For Down-to-Earth Agriculture
Astronauts and polar explorers can grow fresh foods in space and Antarctica. Now, it’s time for rural communities to get into the greenhouse game. Similar to what Matt Damon portrayed in the movie The Martian, astronauts can successfully grow enough food to sustain themselves in orbit or on another planet.
Using Space-Age Technology For Down-to-Earth Agriculture
Posted by Scott Elliott, National Institute of Food and Agriculture in Research and Science
Mar 30, 2018
University of Arizona students work in the University of Arizona’s Controlled Environment Agriculture Center vertical farming facility for research, education and outreach. (Photo courtesy of Austin Smith)
Astronauts and polar explorers can grow fresh foods in space and Antarctica. Now, it’s time for rural communities to get into the greenhouse game.
Similar to what Matt Damon portrayed in the movie The Martian, astronauts can successfully grow enough food to sustain themselves in orbit or on another planet. Researchers in Antarctica have been doing the same since 2004 in an environment where the average yearly temperature is minus 56 F. One of the researchers involved in these extreme environment success stories says that local communities can also benefit from controlled environment agriculture (CEA).
Dr. Gene Giacomelli, professor of agricultural and biosystems engineering at the University of Arizona, leads an internationally recognized, one-of-a-kind research and education program at the university’s Controlled Environment Agriculture Center (CEAC). Their studies and applications focus on the technical, and practical and business development aspects of designing, monitoring, managing, modeling and optimizing crop production.
Giacomelli and other researchers at CEAC have received grants from USDA’s National Institute of Food and Agriculture to study sustainable indoor growing systems (click on the video’s “Dr. Giacomelli” tab).
“We recognize the momentous historical change that CEA promotes for a non-famer without land who may now become a significant producer of food as never before possible,” he said. “This is a renaissance time for production agriculture.”
According to Giacomelli, the renaissance began in 2006 with increased use of “high tunnels” – low-cost, uncontrolled environments that extend growing seasons and produce more, high-quality crops. “The market brought demand, which created new businesses, or renovated older farm businesses,” he said.
In addition to growing food, greenhouses have the potential to become a social magnet for communities by bringing people together for planting and harvesting activities. More advanced greenhouses create a need for non-seasonal jobs that require knowledge-based training in biology and engineering.
Giacomelli said greenhouses can become the center of commerce for rural communities or communities that have fallen on hard economic times.
“Greenhouses production can be as diverse as the local user desires, extending beyond simple edible plant crops to include fish (aquaculture), fish and plants (aquaponics), or other tradable products, including flowers, seedling starter transplants, medicinal crops, oil crops, animal feed and pharmaceuticals.”
Developing an environment that can support growth in space or Antarctica may be beyond the reach of most folks, but advancing from backyard gardener to creating a sustainable CEA or hydroponics system need not be. Giacomelli says education is the key – he recommends taking classes and workshops and working with Master Gardeners and local county Cooperative Extension offices to get hands-on experience.
Category/Topic: Research and Science
Tags: National Institute of Food and Agriculture NIFA Arizona greenhouse Controlled Environment Agriculture aquaculture hydroponics rural communities University of Arizona