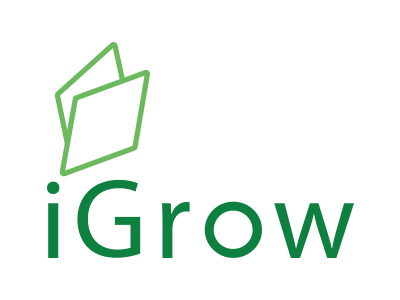
Welcome to iGrow News, Your Source for the World of Indoor Vertical Farming
"Spend Less Time On Your Controls, But More Quality Time With Your Plants"
Practical insights from the Autonomous Greenhouse Challenge
When your team wins the Autonomous Greenhouse Challenge, you may safely call yourself an expert on autonomous cultivation. René Beerkens, who's been with Hoogendoorn Growth Management for twenty years, and Evripidis Papadopoulos, who worked as a Data & Algorithm specialist for Hoogendoorn during the challenge and is now back to LetsGrow.com as a Researcher & Data Analyst, were both involved with winning team AuTomatoes, and from the Hoogendoorn headquarters, they shared some of their insights with growers.
Plant Empowerment
At the heart of Hoogendoorn's holistic approach, René explains, is the concept of Plant Empowerment, which evolved from Next Generation Growing. "We're not only a technical supplier, but also spend an awful lot of time on research and development", René introduces his company.
"The Dutch have a vast history of experience growing plants, mostly by trial and error", he continues. Having learned the laws of physics and completed a lot of research on plant development, growers have moved on from trial and error to a data-driven approach.
Data-driven
This begs the question: why data-driven growing? "We lack experts in the field", René says, "investors want a quick return on investment (they want to invest in something that works from the start), but the main thing is, we want to leave planet Earth in a better way than we found it, using less resources."
The Autonomous Greenhouse Challenge was a perfect opportunity to put this data-driven approach to the test. Using a variety of sensors that measured things like air temperature, humidity, CO2, EC and root temperature, plant temperature, and light levels, a range of data was collected, which was all gathered in one central place so the team could access it wherever they were.
This team featured members from various disciplines, who met once a week. The dashboard, built on the LetsGrow.com platform and customized for Hoogendoorn, helped them analyze data and make the appropriate decisions. As Evripidis puts it, this allows you to "save time for yourself, and due to the holistic approach you find space for further optimization."
Results
The main attraction of the webinar was, of course, the results that participation in the challenge yielded. Using a data-driven strategic approach, the team built their strategies based on historical data from outside conditions. During the challenge, the AI system made adjustments to accommodate the changing circumstances, as can be seen in the below graph showing the ratio temperature radiation (RTR).
"You can't be at your computer daily," Evripidis explains, "so the algorithm made changes automatically, based on feedback from the crop."
It may sound scary to give your precious crops into the hands of an autonomous computer, but the holistic approach taken by team AuTomatoes at least provides the grower with the peace of mind that they can actually see the crop, even when they're not in the greenhouse. The slide below shows how that looks in the dashboard.
René explains that you can also make time-lapses with the dashboard and compare day by day development with the pictures, which is arguably better comparing than just looking at the plants in the greenhouse, because changes in the crop become more noticeable.
Data Driven Operational approach
The next graph shows two identical days with the outside temperature and wind speed the same. In the first day (on the left), the temperature fluctuates a lot, as Evripidis points out. On the second day, the temperature doesn't fluctuate so much, thanks to an intervention in ventilation from the autonomous system, which is of course more favorable to the crop.
While growers are fully focused on ventilation or temperature, Evripidis explains how they came up with VO control. "We keep the windows as closed as possible to trap humidity, so that the temperature is not too high, stomata will remain open, and photosynthesis is maximized. If you trap humidity, you also trap CO2, so it's a win-win situation." With VO control it's not necessary to work with P-band anymore. Growers can set five setpoints, the rest will be done automatically.
René and Evripidis also discussed how the autonomous cultivation system dealt with irrigation and assimilates during the challenge. More about the former can be found in this article from Godfrey Dol on HortiDaily, and Hoogendoorn shared some information on realizing an optimized assimilates balance in this article.
Quality time
In conclusion, it can be said that a grower can do much more based on data. "We had a grower who had never grown tomatoes in the Netherlands, and he did quite well using just data", René shares, telling growers that they can "spend less time on your controls, but more quality time with your plants."
As Evripidis puts it: "We're trying to assist, not take over - we make the car, you drive the car." Or to use another metaphor, as René did: "A plane can fly itself, but the pilot still has to know what happens in the background. We can do a lot with data, but we're still dealing with organisms that are much cleverer than us - they've evolved for millions of years, we are just catching up in the last few years."
For more information:
Hoogendoorn Growth Management
info@hoogendoorn.nl
www.hoogendoorn.nl
Publication date: Mon 7 Sep 2020
Author: Jan Jacob Mekes
© HortiDaily.com
Doctor Grows Vegetables For Antarctic Team
Dr. Hu Miao, from Shanghai East Hospital, has been working at China’s Great Wall Station in the Antarctic since December 4. As this year’s doctor in the polar region, Hu not only treats scientific investigation team members if they get sick but also grows vegetables. Vegetables contain vitamins that are necessary for health, he says
By Tian Shengjie
2020-08-28
Dr. Hu Miao, from Shanghai East Hospital, has been working at China’s Great Wall Station in the Antarctic since December 4.
As this year’s doctor in the polar region, Hu not only treats scientific investigation team members if they get sick but also grows vegetables.
Vegetables contain vitamins that are necessary for health, he says.
Various types of vegetables are grown in the greenhouse in the Antarctic. | Ti Gong
However, due to the extreme climate, it is rare to see the natural development of plants.
Hu said: “The weather is terrible with heavy snow and high winds even if it is summer in the Antarctic.”
Eating fresh vegetables was just a dream of the team members.
However, that dream became reality after a greenhouse was established at the Great Wall Station in 2015.
Several types of vegetables are grown in the greenhouse now, such as squashes, pumpkins, and pak choi, or Chinese cabbage, Hu said.
He added: “There are over 10 people at the station and everyone can eat a cucumber every two days.”
Plants thrive in the ideal environment of the greenhouse. | Ti Gong
The 36-square-meter greenhouse is made of transparent plastic sheets of the type usually for aircraft windows. It can allow 90 percent light to pass through.
There’s artificial lighting, automatic irrigation, and heating to provide the best environment for the plants to grow, said Shu Yu, one of its developers.
Because of aged circuits, the greenhouse burst into flames in 2018. This year, it has been repaired and renovated with more areas to grow and purple lights to strengthen photosynthesis.
The hospital has sent eight medical workers to the Antarctic and Arctic since 2015.
Source: SHINE Editor: Yang Meiping
Lead photo: Hu Miao harvests vegetables grown in the Antarctic greenhouse.
Technician Theo Builds High-Tech Greenhouse As a Hobby
How great would it be to have a small greenhouse in your own garden where you can grow vegetables, fruit, and herbs in an environmentally-friendly, clean, and energy-neutral way?
How great would it be to have a small greenhouse in your own garden where you can grow vegetables, fruit, and herbs in an environmentally-friendly, clean, and energy-neutral way? That is what the recently retired Theo van Lieshout of Wognum (Netherlands), thought. He did not want to sit at home, staring out of the window, and decided to take up a challenge, after he had previously made his home energy neutral.
Now he can also cross the construction of a high-tech greenhouse off his list, and the greenhouse is almost ready for the first crops. Hydroponically grown, that is, and for this, Theo relies on the advice of experts.
Theo in his greenhouse
IKEA
The greenhouse is 5 meters long, 2 meters wide and 2 meters high. The rainwater is collected and stored in stackable IKEA trays. "In the greenhouse, I make use of 4 layers with tubes which, for example, transport water with nutrients according to the ebb-and-flow system once per hour. A pond has been installed on the ground level on which the floats sit. The tube has numerous cutouts for pots with compressed soil as substrate. Put a seed in it, and it grows."
Tinkering with LED lighting
It sounds easy, but of course, it is not, as Theo knows full well. A lot more is required, such as lighting.
"I have purchased customized Chinese LED lights. Adjusted, because the reliability and safety were not up to scratch. Depending on the application, the various layers have different colors, such as mainly blue for seedlings, mainly red for leafy vegetables, and broad spectrum for blossom setting. All groups can be separately controlled in two intensities."
LED lamps from China
Own CO2
Although LED lighting is very efficient (40 - 50%), the lamps are still getting hot, Theo notices during testing. "For this reason, each layer has two fans to provide a calm airflow for the plants, so it is a double-edged sword."
During testing, the tubes first became too hot
"A nice feature is that the CO2, which we breathe out at home, is measured, and when concentration increases (> 700 ppm), a fan will suck the air out of the house. It is then made available for the greenhouse plants."
Tubes wrapped in aluminum tape
Aluminum tape
Every greenhouse owner knows the problem of heating by the sun. In March, the greenhouse was already 20 degrees warmer than the surroundings. Theo has solved this in two ways. "All tubes and trays are wrapped in aluminum tape. The light is no longer absorbed and reflected, and thus available for other plants. That already makes a lot of difference."
On top of that, Theo came up with another 'interesting solution'. "That is using semi-transparent solar panels on the roof. Around 5 percent of the light is let through to be used by the plants, but the rest is used for generation of electricity, an estimated 1500 kWh per year. The sides have been shielded by plants, partially blocking the sun light. The result is that the greenhouse is now no more than five degrees higher than the surroundings."
Partially transparent solar panels on the greenhouse roof
Water pump
Another interesting feature which Theo has applied is the coupling to a heat pump. "A year and a half ago, I completely made my house completely energy neutral with heat pump, solar panels, and heat generation. I also have written books about this, by the way.
"Residual heat is then used to heat the greenhouse but cold from the ground. I also call this ground cold, which can be used to cool the greenhouse, both with a radiator and heat exchanger (hose) in the pond."
Tablet
On balance, the energy use approaches energy neutral, in combination with the solar panels on the greenhouse, Theo notes. "A tablet or PC can be used for control, anywhere. As a technician, I am/was an electrotechnician, I have much experience with technical projects, and at the University of Amsterdam, I worked on projects such as the design of LED lighting for plants and a photospectometer."
Grain of salt
Now Theo is ready to grow, he runs into the fact he does not know very much about the effects of light and nutrients on the plants. Except for what can be found on the internet, but you should take that with a grain of salt. Luckily, there is also some common sense. "Now, I have to mainly focus on the possibilities and demands of the plants."
Cultivation + parallel project
Theo would like to get in touch with people who are as crazy as he is, in his words. "I will never break even, that much is clear to me. I will start with a diversity of seeds (vegetables, fruit, and herbs) and try to optimize with nutrients and light colors.
"A project running parallel to this is the making of a photospectometer to measure the color shift/intensity so you can see whether a plant is saturated with light. This is an extension of the work I have done before. But that is something for winter."
Curious about Theo's progress? Take a look at his website: www.hobbyvantheo.nl.
Theo can be contacted at: info@hobbyvantheo.nl
Publication date: Tue 1 Sep 2020
Spill the Greens - Mucci Farms Launches Podcast
Canadian Mucci Farms is launching a podcast called Spill the Greens
To connect the dots between greenhouse operations and their customers, Canadian Mucci Farms is launching a podcast called Spill the Greens. “We think it’s important for people to know who we are, and see this platform as an opportunity to introduce retailers and consumers to our amazing team through education and information about the greenhouse industry,” says Ajit Saxena with Mucci Farms.
“To many people, we are a brand or a product, but behind the logos and packaging there is a team of 1400 people dedicated to growing, packing, shipping and marketing high quality fresh produce. We hope to provide transparency through this platform, with an aim to increase awareness and consumer loyalty,” Saxena added. After months of research and preparation, the official launch is today, August 18.
How did the idea for a podcast start off? Saxena explained that Mucci Farms is always looking for new ways to enhance its online presence and marketing. “As a forward-thinking company, we regularly consider new digital opportunities to reach people, and given the current circumstances, that effort has undoubtedly increased,” Saxena shared. “Prior to working in produce, I worked in Radio Broadcasting for 6 years so the podcast space was naturally intriguing, but I wasn’t sure if we could create enough content for an engaging show worthy of a regular listenership.”
In February of this year, some of Mucci Farms’ marketing team members attended United Fresh’ Brandstorm event. One of the sessions at the event was called the Power of Podcasting which highlighted the benefits of the platform. “As we listened to the panelists, it became clear that we needed to take a deeper dive into the opportunity and really take a look at how much content we could create. It was obvious that this was a rising platform. After the event, we went home to Kingsville, did our research and then presented our findings to our team.”
Podcast host Ajit Saxena and Mucci's CEO Bert Mucci.
Research was convincing
Nielsen had a lot of real-time data on podcasts available. “There were a surprising amount of statistics that pointed to our general target demographic as big consumers of podcasts,” said Emily Murracas, Director of Marketing at Mucci Farms. “It was eye-opening to learn that the podcast platform is growing more rapidly than YouTube,” she added. “We were convinced it was a good idea and without hesitation, green lit the effort to begin its development.”
Today, earlier than planned, Mucci Farms launches its very first episode. “Originally, we were going to launch closer to PMA Fresh Summit,” said Murracas. “However, when circumstances changed in mid-March, and much of the world shifted online, it made sense for us to move up the date.”
Bridging the gap between grower and consumer
The main purpose of the podcast series is to bridge the gap between greenhouse operations and their customers, including retail buyers and end consumers. “More than ever before, consumers want to know where their food comes from and a podcast will allow us to provide detailed information in full context without time constraints,” commented Saxena. “With Spill the Greens, our goal is to educate retail staff and consumers on what we do, how we do it, and what the benefits are of greenhouse-grown produce.”
The first three episodes will feature Mucci Farms owners, starting with CEO Bert Mucci in today’s first episode. Spill the Greens can be found on Spotify, Apple, Google, and Stitcher, but also by going to a dedicated website: www.spillthegreens.com.
For more information:
Ajit Saxena
Mucci Farms
Tel: (+1) 519-326-8881
asaxena@muccifarms.com
www.muccifarms.com
By Marieke Hemmes | Tue 18 Aug 2020 | HortiDaily
Gotham Greens Produces Sustainably Farmed Lettuce In Stapleton
What was once the Stapleton Airport runway is now sprouting sustainably grown greens. Brooklyn, New York-based Gotham Greens has opened its high-tech urban greenhouse
Look for the urban greenhouse’s lettuces, basil, salad dressings, and pesto at Alfalfa’s, Safeway, and Whole Foods locations in the Denver metro area.
By Allyson Reedy • 5280 | July 20, 2020
What was once the Stapleton Airport runway is now sprouting sustainably grown greens. Brooklyn, New York-based Gotham Greens has opened its high-tech urban greenhouse next to Aurora’s Stanley Marketplace, and is out to woo Front Rangers with local basil, greens, salad dressings, and pesto.
Gotham Greens’ aim is to provide high-quality local product on a national scale, bolstering the food supply chain by stocking cities with fresh greens grown right there in the area. The company started in Brooklyn in 2011 and has slowly expanded, with the Aurora greenhouse marking its eighth—and furthest west—location. The 30,000-square-foot facility will provide two million heads of lettuce to the Rocky Mountain region each year, as well as serve as the company’s flagship site on this side of the country. Because the greens are grown and sold locally, the products are fresher when they get to your kitchen, and because the plants are grown hydroponically, Gotham Greens’ produce uses 95 percent less water and 97 percent less land than traditional soil-based produce.
“The technology enables us to have perfect conditions for our plants,” says director of community and partnership marketing Nicole Baum. “Our plants are very spoiled. They’re very coddled.”
That technology includes curtains to create a natural SPF for the plants, as well as to shade them from the sun or lock in heat in the winter. The temperature-controlled space, which is typically set at 75 degrees with 70 percent humidity, can even create different climates depending on where you are in the greenhouse. Basil, for example, likes it a couple degrees warmer than the lettuces. The misting system works overtime in Colorado’s dry climate to inject moisture into the air.
Unique to this Centennial State location are two new-to-Gotham varieties of lettuce: the crispy green leaf, a hardier and more nutrient-dense alternative to romaine, and Rocky Mountain Crunch, a toothsome green whose leaves grow in a rose-like pattern.
You can buy both of those lettuces, along with eight other types of lettuce, basil, salad dressings (don’t miss the Vegan Goddess), and pesto, at Alfalfa’s, Safeway, and Whole Foods locations in the Denver metro area, but you’ll also find Gotham Greens products at an increasing number of local restaurants. At neighboring Stanley Marketplace, Annette and Comida use the greens, and owner Tommy Lee nabbed the crispy green leaf lettuce for his menus at Uncle and Hop Alley.
“We like working with chefs who care about where the food comes from, and luckily in Colorado there’s a lot of them,” Baum says.
Thanks to the greenhouse’s ideal year-round growing conditions, it takes only about a month for seeds to metamorpihize into those verdant, leafy greens. Which means you’ll probably be seeing a lot more of Gotham Greens’ locally-grown produce in grocers and restaurants around town—even through winter.
Lead Photo: by Allyson Reedy
The World's Largest Indoor Farm Is Creating 300 Jobs In Kentucky
The 2.76-million square foot controlled environment agriculture facility is based in Morehead, Eastern Kentucky. A region where unemployment is 44 percent higher than the national average. AppHarvest aims to develop this area into an agricultural technology hub
AppHarvest's new indoor farm in Kentucky is creating jobs and shows an alternative, sustainable form of agriculture and farming.
The world's largest indoor farm just created 300 jobs in Kentucky. | AppHarvest/Instagram
August 21, 2020
High-tech greenhouse developer AppHarvest just opened the world’s largest indoor farm in Kentucky, creating 300 full-time permanent jobs.
The 2.76-million square foot controlled environment agriculture facility is based in Morehead, Eastern Kentucky. A region where unemployment is 44 percent higher than the national average. AppHarvest aims to develop this area into an agricultural technology hub.
“Eastern Kentucky, with its central U.S. location, provides the perfect place to build AppHarvest’s indoor farms,” said Johnathan Webb, the founder, and CEO of AppHarvest. “While also providing much-needed jobs to a ready workforce.”
AppHarvest combines agriculture with cutting edge technology to promote sustainable change within the industry. The new indoor farm drastically reduces the land needed to increase food production. It uses no pesticides and no GMO products.
All water needs are met exclusively by a closed-loop, recycled rainwater system. This also minimizes the water runoff unavoidable with traditional agricultural methods. Overall, AppHarvest’s sustainable greenhouses use 90 percent less water than other farming.
“It’s time for agriculture in America to change,” continued Webb. “The pandemic has demonstrated the need to establish more resilient food systems, and our work is on the forefront of that effort.”
The transportation of fresh produce can have significant carbon emissions.
The Future Of Farming
In addition to job creation, the new farm’s location will also reduce production costs and carbon emissions.
Morehead is less than one day’s drive from 70 percent of the U.S. population. This means a reduction in diesel fuel costs by 80 percent and allows for more competitive pricing against low-cost foreign imports.
AppHarvest recently closed on its $28 million Series C round of fundraising, making a total of over $150 million in just two years. The company has also expanded its board to include investor and author J.D. Vance, Rise of the Rest Seed Fund partner Anna Mason, and AOL co-founder Steve Case.
Impossible Foods CEO and plant-based food proponent David Lee and lifestyle icon and keen vegetable gardener Martha Stewart also sit on the AppHarvest board. Stewart said: “The future of food will be, has to be, growing nutrient-rich and delicious produce closer to where we eat.”
“That means food that tastes better and food that we feel better about consuming,” she added. “AppHarvest is driving us towards that future and working from within Appalachia to elevate the region.”
STAFF WRITER | BRISTOL, UNITED KINGDOM | CONTACTABLE VIA: LIAM@LIVEKINDLY.COM
Liam writes about environmental and social sustainability and the protection of animals. He has a BA Hons in English Literature and Film and also writes for Sustainable Business Magazine. Liam is interested in intersectional politics and DIY music.
The Underwater Habitat With A Greenhouse
Swiss designer Yves Behar has unveiled his design for French ocean conservationist Fabien Cousteau's underwater pressurised research station that will be "the ocean's equivalent to the International Space Station".
29-07-2020 | Msn News/ India Block
Swiss designer Yves Behar has unveiled his design for French ocean conservationist Fabien Cousteau's underwater pressurised research station that will be "the ocean's equivalent to the International Space Station".
Behar designed the station, which is called Proteus, for the Fabien Cousteau Ocean Learning Center. It will have its own greenhouse to allow scientists to grow their own food 18 metres under the sea near Curaçao, an island in the Caribbean.
Up to 12 researchers and aquanauts – scientists who remain underwater breathing pressurised air for over 24 hours – will be able to live in Proteus at a time.
Like the International Space Station, Proteus will allow scientists to collaborate and make new discoveries in an inhospitable environment.
"The research station will enable the discovery of new species of marine life, create a better understanding of how climate change affects the ocean, and allow for the testing of advanced technologies for green power, aquaculture, and robotic exploration," Behar told Dezeen.
Living underwater in a pressurised environment, rather than just diving in, allows scientists to spend far more time in the water and only decompress at the end of their assignment.
Proteus is the result of Behar's studio Fuseproject being commissioned by Cousteau, and his non-profit the Fabien Cousteau Ocean Learning Center (FCOLC).
"We needed to understand the constraints that come from building underwater and the challenges of living in an underwater structure," Behar said.
"The social isolation, the humidity, the lack of light and lack of exercise all needed to be addressed," he explained. "I learned about these challenges from Fabien, who had the record as the person who lived longest in an underwater habitat."
© Provided by Dezeen Proteus by Yves Behar
Cousteau broke the record, previously set by his grandfather, with a 31-day-long stay in an underwater laboratory off the coast of Florida called Aquarius.
Behar used Cousteau's experience to inform the design of Proteus, which has two levels connected by a curving ramp with pods set around the edges.
Circular-shaped main spaces are designed to encourage teamwork and social interaction for the scientists. Pods around the perimeter are designed to hold specific laboratories, bathrooms and areas for sleeping.
"Both circular floors are offset to allow as much natural light as possible through skylights and portholes, and are connected by a sloping ramp which creates the opportunity for physical activity," said Behar.
Social spaces will be kept separate from the more humid areas of the wet labs and the moon pool – the space in an underwater habitat where occupants can access the water directly in a protected environment.
© Provided by Dezeen Proteus by Yves Behar
An underwater greenhouse will allow occupants to grow their own food, allowing them to stay underwater for longer and cope more comfortably with the confines of a pressurised environment where no open flames for cooking are allowed.
Behar deliberately gave the underwater habitat a retrofuturist vibe in keeping with the way science fiction has traditionally imagined underwater living.
"Fabien and I looked at many exploratory designs from the 60s and 70s, a golden era of interest for the oceans pioneered by the Cousteau family history," Behar told Dezeen.
"We felt that Proteus could incorporate a new visual language based on modern hull and composite building technology, as well as be a state-of-the-art scientific environment while delivering a comfortable social interior space."
In keeping with the Cousteau dynasty's ocean conservation goals, Proteus will be powered by renewable energy. The habitat will use a mixture of wind, solar, and Ocean Thermal Energy Conversion (OTEC), a process that produces electricity using the difference in temperature between warm water on the surface and cold water from the deep ocean.
Cousteau will head to Curaçao to map the site as soon the borders shut due to the coronavirus pandemic open, hopefully in September. Behar estimates it will then take 36 months to build and lower Proteus to the ocean floor.
Behar hopes Proteus will be one of a series of marine habitats dedicated to research and conservation. As well as scientists, the designer hopes the facility will be able to welcome civilian visitors.
"Proteus is designed to be a scientific environment, but also to create that desire in people to want to visit," he said.
"For me, it’s a lot more exciting to visit Proteus than going to Mars."
Behar embraces technology with his designs, which include plans for 3D-printed houses for impoverished farmers and a wearable UV sensor to protect against skin cancer.
The post Proteus is an underwater habitat with a greenhouse designed by Yves Behar appeared first on Dezeen.
Source: Msn News/ India Block
Photo Provided by Dezeen
US: MAINE - Vertical Greenhouse Coming to Westbrook
The City of Westbrook will soon be growing produce a little differently. Starting in the spring of 2021, a company called Vertical Harvest will begin building a vertical greenhouse on Mechanic Street
29-07-2020 | News Center Maine
US- A 70,000 square-ft vertical greenhouse will produce 1 million pounds of produce per year to the city and surrounding areas.
The City of Westbrook will soon be growing produce a little differently. Starting in the spring of 2021, a company called Vertical Harvest will begin building a vertical greenhouse on Mechanic Street.
The planned 70,000 square ft facility will initially grow a variety of microgreens and lettuce. The company estimates the greenhouse will produce 1 million pounds of produce per year to the city and surrounding areas.
Westbrook will be the company’s second location in the United States. The co-founder said she came up with the vertical idea after realizing the need for fresh produce year-round in an urban setting.
“We want to grow as much food as possible. We want to employ as many people as possible. We want to do both year-round. That’s what gave us the idea to go up. So at its heart, we want to be able for these farms to serve the community in which it sits, so that means being in the heart of our urban centers,” said co-founder Nona Yehia.
Yehia said the greenhouse will bring 50 full-time equivalent jobs to the city. The mayor of Westbrook said the greenhouse is part of a larger project, which will include a parking garage and new apartments.
A documentary about Vertical Harvest called Hearts of Glass was recently released.
Here’s an excerpt from the film.
Source and Photo Courtesy of News Center Maine
Controlled Environment Agriculture Open Data (CEAOD) Project
The use of Machine Learning and Artificial Intelligence techniques could provide CEA researchers and commercial growers an opportunity to optimize crop production efficiency and unveil new methods to improve production yield
Date: August 4, 2020
Time: 2 p.m. - 3 p.m. EDT
Presented by: Erico Mattos, GLASE Director, and Kenneth Tran, Koidra
Click Here to Register
Controlled Environment Agriculture (CEA) is a data-driven scientific discipline. In CEA operations all the environmental parameters are monitored and controlled to provide optimal conditions for crop growth. Recent technological advancements made the use of sensors and controls more accessible to CEA growers allowing them to precisely adjust these parameters.
The use of Machine Learning and Artificial Intelligence techniques could provide CEA researchers and commercial growers an opportunity to optimize crop production efficiency and unveil new methods to improve production yield. However, there is a lack of a centralized repository and a standard methodology for data sharing.
Join GLASE Director Erico Mattos and Koidra CEO Kenneth Tran on this GLASE Webinar to learn about the Controlled Environment Agriculture Open Data (CEAOD) project. This initiative aims to promote data sharing to accelerate Controlled Environment Agriculture (CEA) research through the establishment of a free centralized platform for the CEA community. Researchers and commercial growers are welcome to join and learn more about it.
Kenneth Tran was part of the winning team at the first International Autonomous Greenhouse Challenge held at Wageningen University in 2018. The team defeated four other international teams, consisting of experts in the field of Artificial Intelligence (AI) and horticulture. Erico Mattos is working with Cornell University and Rensselaer Polytechnic Institute Researchers to develop a guideline for data collection and upload to the CEAOD project.
Indian Grower Capitalizes On Market Opportunities With AI
Things are looking up for the greenhouse produce market in India. "We see an increase in demand in the Indian market, especially in many cities where we supply", says Sachin Darbarwar, founder of Simply Fresh
Sachin Darbarwar, Simply Fresh
Things are looking up for the greenhouse produce market in India. "We see an increase in demand in the Indian market, especially in many cities where we supply", says Sachin Darbarwar, founder of Simply Fresh. Last year, the grower invested $30 million in expanding the greenhouse operation, and that investment appears to be paying off.
"With more awareness on hydroponic farming and more emphasis on food safety, consumers today are selective in their buying and prefer produce, which is clean, safe, and traceable", Sachin tells us. "With the current global scenario and special focus on health and immunity, we only see this demand increasing in future."
Sachin and Shweta Darbarwar, founders of Simply Fresh
Simply Fresh not only supplies its produce to the local market, however: "We have exported our produce to the UAE, and will shortly resume our exports to countries like the UK, USA, and South East Asia."
So they look across the border, and not just when it comes to exporting their produce. "Our greenhouse structure was designed and delivered to us by Cravo, a Canadian company that specializes in retractable greenhouses", Sachin tells us. They source their seeds from various domestic and international suppliers as well, like Rijk Zwaan. "Depending on crop type we reach out to different vendors to get the best variety of seeds to have high-quality produce for our consumers."
Nutraceuticals
Under their nutraceutical vertical, Simply Fresh grows varieties of medicinal plants. "These have three times more alkaloid content than field grown plants, and serve as raw material for nutraceutical companies", Sachin explains. "The choice to grow these has been a successful move as we are able to provide medicinal plants which are traceable and with higher alkaloid content, which reduces the cost of extraction. Also, all our fresh produce and medicinal plants are safe, traceable and grown using sustainable farming techniques without any use of pesticides."
It's been a bit of a pioneering project to grow those "non-traditional" greenhouse crops: "They are very challenging as globally there are not many growers who have grown this and can share best practices/knowledge on how to grow them and how they behave without soil", Sachin tells us.
Farm in A Box
Like any modern grower, Simply Fresh also makes use of AI, having implemented it in creating data points and making decisions on data points. "For example, we use AI in forecasting yield, predicting seeding charts, space utilisation, traceability, managing crop workflows and knowledge line."
The Farm in A Box (FiAB) platform, developed by the grower, plays a central role in this strategy. "It helps us track everything from the very initial stage of sending, plant profiling, monitoring plant health and nutrient level requirement at each stage of the plant growth.
"We also use the same FiAB platform to plan and forecast the yield required for future and for our internal CRM management, to collect and process orders received from different vendors from various cities."
The company is constantly developing the platform, and in future FiAB may become available for other growers to use as well.
That's not the only thing they have in store for the future: Simply Fresh will be further expanding, growing to 40 acres on their current site in Phase 2 of the expansion.
For more information:
Simply Fresh
www.simplyfresh.co.in
Publication date: Wed 22 Jul 2020
Author: Jan Jacob Mekes
© HortiDaily.com
Larry Ellison's Indoor Greenhouse Farm In Hawaii Undergoes Business Changes
The initial farm on Lanai island was separated from Sensei, formerly Sensei Retreats, and Sensei Lanai, a wellness resort operated by hotel management firm Four Seasons
April 12, 2011: Lanai, Hawaii. The long red dirt road of Munrow Trail. (Image: Jenna Szerlag/Design Pics via ZUMA Wire)
HONOLULU - The owner of a hydroponic greenhouse operation in Hawaii has announced changes to the farm operation in Lanai, including a new leader and severance from resort operations.
Owner Larry Ellison and partner David Agus said earlier this week that Sensei Farms has been rebranded as Sensei Ag as part of the change, the Honolulu Star-Advertiser reported.
Sensei Ag began producing vegetables earlier this year on Lanai and is currently supplying hotels, retailers, and chefs on the island. The operation aims to produce more than a million pounds of food annually for distribution beyond Lanai using 90% less water than traditional farming, company officials said.
The initial farm on Lanai island was separated from Sensei, formerly Sensei Retreats, and Sensei Lanai, a wellness resort operated by hotel management firm Four Seasons.
The farm and the resort were previously part of Sensei Holdings, Inc.
Sonia Lo was also named CEO of Sensei Ag, officials said. Lo has more than 30 years of experience in finance and most recently was CEO of Crop One Holdings, a California-based indoor farm operator.
“We are incredibly well-positioned with Larry and David’s guidance, knowledge, and networks to become the leader in our space,” Lo said. “There has never been a better time to rebuild our global food and agriculture supply chains.”
Ellison, the co-founder of Oracle Corp., was ranked by Forbes as the fifth-richest person in the world, with a net worth of $73 billion. He bought 98% of Lanai in 2012, the Star-Advertiser reported.
His partner Agus is a doctor and renowned cancer specialist.
Feeding The World With Controlled Environments
The fallout from increasing global temperatures, a worldwide pandemic, and political unrest is causing projection reductions for crop yields in some countries as much as 50% this year, and small-scale farmers are the most affected with crop net revenues falling by as much as 90% by 2100
This case study, written by Gene Giacomelli and Eric Roth for Agritecture, takes a look at how CEA has emerged as a viable, contemporary agricultural practice over the past 50 years. Here’s how it happened!
The fallout from increasing global temperatures, a worldwide pandemic, and political unrest is causing projection reductions for crop yields in some countries as much as 50% this year, and small-scale farmers are the most affected with crop net revenues falling by as much as 90% by 2100. The consumer preference for consistent, year-round availability of produce has expanded because of the Controlled Environment Agriculture (CEA) industry, even surviving the recession of 2008. “That indicates to me, that no matter what the next recession brings, CEA food production systems will be firmly entrenched in U.S. agriculture production practices,” says Gene Giacomelli, Professor of Biosystems Engineering and former Director of CEAC at The University of Arizona.
CEA has emerged as a viable, contemporary agricultural practice over the past 50 years. There have been dramatic improvements in efficiency metrics including overall crop yield per square unit and reduction of wastage due to disease, nutrient deficiency, or damage to the product. From Space to Antarctica; from rooftop greenhouses to rural farms worldwide, CEA has proven itself to be not only a complement to open field crop production, but in some instances, a competitive alternative (or in the case of Space and Antarctica the ONLY) approach. Today, more than 60% of all fresh tomatoes consumed in the U.S. are grown in controlled environments and that number approaches 100% during the North American winter. Here’s how it happened...
In the 1990s, the U.S. greenhouse production shifted from its infancy to a steady supplier of fresh produce. While greenhouses use the sun as their main source of light, they can also make use of supplemental lighting for additional growth. This advantage, along with the ability to control and protect the growing environment, encouraged large farming corporations to enter the space in the Northeast, Arizona, Colorado, California, and Texas. Environmental control enabled these early adopters to produce crops like tomatoes, cucumbers, and lettuces year-round. During the same time, small family farms were often adding greenhouses to complement their traditional open-field production.
During the next decade, the major suppliers of field-grown vegetables in Canada and Mexico also began focusing on greenhouse production. The 2000’s firmly established CEA vegetable production as a viable commercial growing method.
In the 2010’s, vertical farming became more mainstream when Dr. Dickson Despommier published the book, The Vertical Farm: Feeding the World in the 21st Century. Vertical farms are essentially plant factories, with multi-level grow systems in insulated buildings using only electrical light instead of sunlight for plant growth. Although there were most likely small scale vertical farms before it, Sky Greens in Singapore was the first vertical farm to begin large scale commercial operations in 2012. Vertical farming became more commercially viable largely because of the advancing technology of Light Emitting Diodes (LED). These distributed light sources are less energy-intensive than the industry standard high-intensity discharge lamps, but more importantly, allow growers to move lights closer to the crop without burning or overheating. This enabled business developers to stack hydroponic grow systems, producing significantly more greens in increasingly smaller spaces. Now confined urban areas where arable land is very limited, could become producers of locally-grown, fresh food.
Protected cultivation has been in America at some level for two centuries, but what technological advancements made feeding the world with controlled environments possible?
Plastics
Polymer plastics such as polyethylene began providing a low-cost, energy-efficient film covering for greenhouses. This lowered the financial barrier to entry by creating more affordable greenhouses, thereby allowing unestablished growers to gain experience with a much lower investment than traditional glass-covered greenhouses. The plastic films dropped the investment cost significantly, while the more rigid, molded plastics improved operational metrics like production capacity, labor efficiency, and biosecurity.
Molded plastics also provided light-weight,easily-sanitized crop handling with trays, pots/flats, and clamshells for the packaging, among other things. Molded plastics further created light-weight structural channels, containers and benches which supported the plant and its root zone within hydroponic nutrient delivery systems, and even provided transport systems for improved labor and logistics management. Fully outfitted climate-controlled CEA plastic film boxes provided lettuce and greens production for the International Space Station.
Microprocessors
The microprocessor with its accuracy, consistency, data storage and simultaneous interpretation of multiple types and number of sensors has allowed the grower to tend more to plant production and much less to environmental control. No longer must the grower walk the greenhouse each morning to adjust the ventilation openings based on a guess of the day to be sunny, rainy or cold. Sensors are available to determine critical environmental plant needs and to make precise responses to air temperature and humidity for VPD (vapor pressure deficit) which affects plant transpiration and photosynthesis; light intensity with quantum sensors to determine DLI (daily light integral) which is directly related to desired growth or production rates; and, pH and EC which affects plant nutrient availability. When all combined, the grower is provided an improved understanding of the plant response to its environment. All this can be obtained on request in real-time by cellphone or within a report upon early morning arrival of the grower to the greenhouse each day.
Even more valuable is the capability of the computer to save data and further process it into useful information, which directs better grower decisions. Expect additional sensor development and implementation in the future to provide higher quality information about the food products, such as its flavor, sweetness, or nutritional quality.
The automation of information, although critically important, may become second in importance to labor-saving automation. Labor is often a farm’s biggest expense and the agricultural talent pool is limited nearly everywhere, but a high-tech farm’s food safety and security are dramatically enhanced when human contact with the edible product is reduced or eliminated. Production system automation that removes the need for people to work in groups on production lines is becoming crucial within this new world of viral pandemics.
There are still many advancements to be made in CEA. Technologies and experiences were transferred from the established greenhouse industry and applied to the developing indoor vertical farming industry. From LED lighting ‘recipes’ to plant nutrition under those recipes; from materials handling and logistics to labor management, years of R&D are required to reach optimal solutions for the plethora of combinations of plant cultivars, stages of growth, and harvest expectations within each type of CEA system.
The challenges remain for educating the people managing and operating the controlled environments. Educated employees working within a production process that is logistically sound, labor efficient, and task friendly are critical considerations for successful CEA businesses. Even with automation, the required work of skilled employees will remain, but at a higher educational level and a lower quantity.
In the future, it’s entirely possible that a CEA system will be able to autonomously program itself, or modify the plant environment without being directed, but for now, the plant production experience of an educated grower or crop manager is still required even in the most high-tech operations. Additional developments for successful CEA businesses include breeding of plant cultivars optimized for CEA production; emphasizing the importance of marketing; valuing employee education and experience; accepting that growing plants is a skill and an art; and, understanding basic physical principles that follow the laws of physics and biology!
CEA is still in such an early stage of commercial viability, but the blueprints for successful ventures continue to be created by intelligent and increasingly well-equipped entrepreneurs. As we look at the timeline of its commercial origins, to the critical technologies that made it work, we can see how far it's come, but also the potential the future holds for feeding the world with controlled environments.
Have you participated in the 2020 Global CEA Census? Autogrow and Agritecture Consulting have launched their 2nd Annual Global CEA Census, focusing on understanding the impact of the COVID-19 pandemic on controlled environment agriculture (CEA) operations around the world. The 2020 Global Census runs from July 7th to August 10th. Those who complete the census are entered to win different prizes from Agritecture and Autogrow.
Publication date: Fri 24 Jul 2020
Calculating Optimal Equipment And a Settings, Before The Greenhouse is Built
“Our software calculates the best configuration of a closed greenhouse for any crop all over the world,” says Vincent Stauffer, director of Hortinergy, a French technology company
“Our software calculates the best configuration of a closed greenhouse for any crop all over the world,” says Vincent Stauffer, director of Hortinergy, a French technology company. It’s mostly used before the construction of a closed greenhouse to select and size the equipment. It helps to make sure that the right choices for energy-efficient equipment are made to reach the optimal climate with the lowest energy expenditures.
The greenhouse simulation software calculates energy consumption and expenditures (cooling, dehumidification, heating, and lighting). It models the inner climate like a virtual greenhouse, with specific parameters, and allows users to compare different technical solutions. Growers, consultants, and greenhouse designers use the software to know what the best settings and equipment are.
Orange Climate
Orange Climate, a Dutch supplier of climate technique, uses Hortinergy software to calculate the demands for the installation. Jeroen Verhagen, Business Unit Manager at the company talks about how the product works for them. “We have to know how many kiloWatts of heating and cooling we need, to have the requested greenhouse conditions, and we can calculate that with Hortinergy.”
When the company first started using the software, there were some issues and questions. “Vincent really cooperated with us on this, we discussed via Teams. He is very involved in the process.” Sustainable climate solutions for greenhouses and special concepts can be a big save in energy. “With Hortinergy, we can calculate what can be saved.”
For more information:
Hortinergy
contact@hortinergy.com
www.hortinergy.com
Publication date: Fri 3 Jul 2020
Author: Marlies Guiljam
© HortiDaily.com
Why Locate In Appalachia?
Kentucky native Jonathan Webb is turning his dream of a high-tech farming hub in Appalachia into reality with AppHarvest
Kentucky native Jonathan Webb is turning his dream of a high-tech farming hub in Appalachia into reality with AppHarvest.
The company is building some of the largest indoor farms in the world, combining conventional agricultural techniques with today’s technology to grow non- GMO, chemical-free produce. The company’s first greenhouse will span 60 acres and open in the second half of 2020 in Morehead, Ky.
Like many Kentuckians, Jonathan grew up knowing of the devastating job losses in the region. His grandmother was raised in Whitley County, where a coal mining accident killed his great-grandfather. Jonathan strives to work alongside the hard-working men and women of Eastern Kentucky and build a resilient economy for the future.
Before founding AppHarvest, Jonathan worked with the U.S. Department of Defense on what was then the largest solar project in the Southeastern United States. The project aimed to help achieve a White House goal of ensuring the military receives 20% of their electricity from renewable sources by 2025.
- Kentucky native and University of Kentucky graduate
- Before starting AppHarvest, Jonathan helped build some of the largest solar projects in the Southeast, seeking to help the military generate 20% of their electricity from renewable sources.
- While working on renewable energy farms, Jonathan discovered the high-tech controlled environment agriculture farms of the Netherlands and returned home to Kentucky in 2017 with the dream of building AppHarvest and creating America’s AgTech capital in Eastern Kentucky.
- Named Emerging Entrepreneur by the Kentucky Entrepreneur Hall of Fame in 2019
- Selected to be a member by worldwide entrepreneurship network Endeavor.
The organization seeks out the best high-impact entrepreneurs around the world, and, to date, has screened more than 60,000 individuals and selected around 2,000.
Talking points for agreement
- 17 organizations signed an agreement committing to create America’s AgTech capital in Eastern Kentucky
- Calls for opening a Dutch representative office in Kentucky, creation of a series of research programs at universities, construction of a center of excellence, and the building of additional controlled environment agriculture farms like AppHarvest’s, which is under construction in Morehead.
- Dutch are widely recognized as the world’s leaders in AgTech. Even with a landmass just roughly the size of Eastern Kentucky, the Netherlands has become the world’s second-largest agricultural exporter. How? They utilize controlled environment agriculture facilities to grow up to 30 times more fruits and vegetables on an indoor acre compared to a traditionally farmed outdoor acre. And they do it using 90% less water.
- Why Kentucky? Our central geographic location, which has attracted the likes of Amazon and UPS, allows fresh fruits and vegetables to reach nearly 70% of Americans in a day's drive. That means fresher food and far less food waste as grocers benefit from the extended shelf life. Eastern Kentucky is also home to a strong workforce that long powered the country and exhibits the faith and grit needed to build a more resilient economy.
VIDEO: The Produce Industry Podcast With Patrick Kelly. We Chat With Nick Greens, Horticulturist/Consultant at Nick Greens, LLC
In this episode of The Produce Industry Podcast with Patrick Kelly we chat with Nick Greens, Horticulturist/Consultant at Nick Greens, LLC
THE PRODUCE INDUSTRY PODCAST
In this episode of The Produce Industry Podcast with Patrick Kelly we chat with Nick Greens, Horticulturist/Consultant at Nick Greens, LLC. Nick Greens started his growing career in 2002. From 2007-2014 Nick made big moves in the industry with vertical and greenhouse farming along with leading new generations for success! Nick and Patrick dive into vertical farming during the COVID-19 pandemic and how teaming up with a greenhouse / vertical farm to create consistent food for your business.
Vertical Farming vs. Greenhouse Farming: Which is More Efficient?
When starting a farming operation, the first choice you face is what type of farm to start. The options are many: indoor vs. outdoor; arable vs pastoral; intensive vs. extensive. For farmers going the indoor route, one of the biggest decisions is between vertical farms and greenhouses
June 1, 2019
When starting a farming operation, the first choice you face is what type of farm to start. The options are many: indoor vs. outdoor; arable vs pastoral; intensive vs. extensive. For farmers going the indoor route, one of the biggest decisions is between vertical farms and greenhouses. Both vertical farms and greenhouses operate indoors, which means they enjoy benefits like climate control and year-round growing.
While there are differences and similarities between the two, they are best compared in terms of efficiency. For a long time, it was thought that greenhouses were more efficient and profitable than vertical farms, as they do not require artificial lighting. However, a 2018 study out of Quebec (Eaves & Eaves, 2018) showed that vertical farms enjoy a number of benefits over greenhouses, especially if the farm is operating for commercial purposes.
To understand what those benefits are, we first need to understand the reasons for farming indoors.
Why grow indoors?
For most of human history, farming has been an outdoor activity. Plants need sunlight to live, and soil to get water and nutrients from, so it is no surprise that traditional farming is done outdoors.
But as agriculture developed, farmers gradually realized that there were benefits to indoor farming. For one, it keeps pests and diseases at bay, as well as allowing certain crops to be grown all year long. Furthermore, indoor farming in ‘hot’ greenhouses can allow plants to grow faster than they would outdoors. By the late Roman Empire, greenhouse-like methods were already being used for these and other reasons. In the 1800s, Greenhouses hit their stride, as European farmers started using them to grow tropical plants that otherwise would not grow naturally on their continent.
The differences between vertical farms and greenhouses
While vertical farms and greenhouses both practice indoor farming, the similarities end there. Greenhouses rely on sunlight and have their plants arranged on one horizontal plane. This means that they require a large amount of space and are therefore best suited for rural or suburban areas. In comparison, vertical farms can operate in urban areas as they need far less space than greenhouses to operate. This is because vertical farms have plants stacked in layers and rely on artificial light.
Many people have argued that because vertical farms require artificial light, they are less efficient than greenhouses. While artificial lighting is a major cost at vertical farms, it is not necessarily a barrier to profitability. The 2018 study “Comparing the Profitability of a Greenhouse to a Vertical Farm in Quebec” showed that growing lettuce in a vertical farm can actually be more profitable than growing it in a greenhouse. They attributed this to two factors: increased yield per square meter, and centralized distribution.
Yield
The main advantage that vertical farms have over greenhouses is a greater yield per square meter. Although vertical farms have higher light and heat costs, they have the benefit of more produce grown per unit of soil. This means that even though vertical farms cost more to operate, they produce more crops, with the end result being higher revenue.
The 2018 study supports this through the results of a simulation, which showed that lettuce grown in a vertical farm has a slightly higher yield than that grown in a greenhouse.
Distribution
Another major advantage of vertical farms is centralized distribution. Because these farms can be run in almost any kind of building (ex. warehouses), they can be located in urban areas. This puts them right at the heart of major distribution hubs, in the middle of a big local customer base. Therefore, compared to a rural greenhouse, a vertical farm has less distance to travel to get to customers, and when it does have to ship over a distance, it has better transportation options.
As a result, vertical farm crops can be sold more quickly and at higher margins than greenhouse crops. According to the Quebec paper, this creates a perception of freshness that helps the vertical farm produce sell quicker than the greenhouse equivalent.
Gross profits
Due to centralized distribution, vertical farms may enjoy higher gross profits than greenhouses. The Quebec paper showed this to be the case specifically for lettuce grown in the Quebec area. Although the wholesale price of lettuce produced at greenhouses and vertical farms is usually the same, the vertical farm’s lettuce may enjoy a premium when sold in its local market due to the perception of freshness. Additionally, because the vertical farm is located in an urban area, it can ship more fresh produce to more customers, without high transportation costs.
A second reason for the higher gross profits at vertical farms is winter heating costs. It is widely assumed that vertical farms use more electricity than greenhouses. But that’s not necessarily the case. It really depends on the specific farm(s) in question. As the Quebec paper showed, in areas that get extremely cold in the winter, Greenhouses can be very expensive to heat. Depending on how rural their location is, they may need to be heated by a generator; and depending on their size, they may consume quite a bit of electricity. So while the vertical farm needs to be heated year-round, the greenhouse can actually be more expensive to heat in the crucial winter season.
Growth potential
One area where vertical farms really shine is the potential for growth. While sales from greenhouses are growing at 8% year-over-year, sales from vertical farms are growing at a full 30% annually. That means that vertical farms are growing more than three times as quickly as greenhouses. While part of this can be explained by the fact that vertical farms are newer than greenhouses, it also has to do with centralized distribution. Since vertical farms have access to urban distribution centers, they can get more product out, more quickly, than greenhouses can. The greater yield per square meter of vertical farm space also contributes to this fast growth.
Putting it all together
Vertical farming is the cutting edge of agriculture. Offering the ability to grow more crops, in a controlled environment, inside major distributions hubs (i.e. cities), it takes advantage of economies of scale in a way no other farming operation can. In the past, many critics have cited lighting costs as a stumbling block to profitability for vertical farms. But as the Quebec paper showed, vertical farming can actually be more profitable than a conventional greenhouse operation. Especially when situated in major urban centers, and taking full advantage of the distribution benefits that come with that, vertical farms can be highly profitable. And when you add the benefits of automated labor into the equation, the benefits can be greater still.
We see vertical farming as the evolution of the greenhouse.
Latest developments in LED (less consumption) and solar energy (higher efficiency) will reduce the biggest remaining cost factor (energy) during the next years.
Automation will increase the benefits of vertical farming even further
Source: Growcer
Florida Indoor Farming Firm Turns Pandemic Disruption Into Opportunity
Orlando, Fla.-based Kalera had to give away an entire harvest in March when the company's commercial customers closed amid stay-at-home orders. But, like some other greenhouse operations around the country, Kalera found other customers and avoided layoffs or going out of business
JULY 9, 2020
A large greenhouse operated by Brooklyn, N.Y.-based Gotham Greens helped produce food as the coronavirus pandemic cut supply chains in March.
Photo courtesy of Gotham Greens
ORLANDO, Fla., July 9 (UPI) -- A Florida company that grows lettuce in greenhouses turned a desperate situation during the coronavirus pandemic into new opportunities, thanks to a nationwide upswing in produce purchases from indoor farms.
Orlando, Fla.-based Kalera had to give away an entire harvest in March when the company's commercial customers closed amid stay-at-home orders. But, like some other greenhouse operations around the country, Kalera found other customers and avoided layoffs or going out of business. Indoor farms like Kalera produce food close to their customers, in clean, hygienic facilities. The process also is called vertical farming because produce is grown on racks, using hydroponics -- raising crops with water and nutrients, but without soil.
Good hygiene and a local supply are more important than ever during supply chain disruptions and waves of panic buying during the pandemic, said Daniel Malechuk, Kalera's chief executive officer.
RELATED NASA advances food-in-space technology"
It was literally the day of our first harvest at a new facility when the state announced stay-at-home orders and many of our food-service customers closed overnight," Malechuk said about what the company faced in March."
My reaction at first was massive disappointment. That would be an understatement. But we rolled up our sleeves and were determined to make the best of it," he said.
Kalera has developed its farm technology over the past 10 years and had built a demonstration farm and production facility in Orlando. To the CEO's dismay, the crops in the new greenhouse became ready for harvest just as Gov. Ron Desantis ordered all restaurants closed to indoor dining.
RELATED USDA announces another $470 million in purchases for food banks
That meant Kalera -- and other farmers who faced similar closures around the nation -- had nowhere to sell their crops. Some growers buried their produce rather than shoulder the expense of harvesting crops without having buyers waiting.
Among the customers Kalera lost were Marriott Orlando World Center, the Orlando Magic basketball team, and area theme parks, Malechuk said.
Kalera had built a large grow house on the grounds of the Marriott resort to supply fresh lettuce and micro-greens to the kitchens there. But the resort has been closed for months and does not plan to reopen until Aug. 1.
RELATED Florida team studies hydroponic hemp as toxic algae remedy
Instead of destroying the food, Malechuk donated his crop directly to local residents and food banks. That's also when he reached out to Florida-based Publix, one of the nation's largest grocery chains with more than 1,200 stores in the Southeast and Mid-Atlantic regions.
At first, Publix paid Kalera for some crops and donated the produce to food banks.
Worried about possibly laying off his workforce of about 100, Malechuk wrote a heartfelt email to a Publix executive with whom he previously corresponded. His subject line was "Humble Plea."
The email asked Publix to make Kalera a permanent supplier. It worked, and Kalera produce now is sold in hundreds of Publix stores."
I knew Publix wasn't accepting new suppliers at that point, and I didn't think it would work," Malechuk said. "But I had to try, and I told Publix that.
"Unexpectedly, Publix expedited its process for accepting new products because of Kalera's crisis, said Curt Epperson, the company's business development manager for produce and floral.
“We were not only able to help their business -- and all the people who depend on them -- but our customers and our community," Epperson said in an email to UPI.
Kalera was not alone in turning a dismal outlook to a brighter future. Other indoor farm companies overcame difficulties during the pandemic and saw new opportunities.
Brooklyn, N.Y.-based Gotham Greens opened new greenhouses in several states as the pandemic spread around the world, CEO and co-founder Viraj Puri said.
His employees already had been wearing masks in growing areas before the pandemic struck. As coronavirus advanced, management added more levels of safety. "We started detailed health screening calls, temperature checks, increased distancing. It was a hard time for everyone. We all knew people who tested positive, and we saw people lose their jobs," Puri said.
Gotham Greens soon saw increased demand from retail merchants for its greenhouse produce as other farmers around the country struggled to find labor for harvests and had difficulties shipping food across the country during the pandemic, the CEO said."
The pandemic altered life around us, unfortunately, but it also showed that we can help ensure food security with indoor farming in controlled environments," Puri said. "These local supplies for growing produce are going to be important."
A number of other indoor farming operations found new customers -- and appreciation for their products -- during the pandemic, said Joel Cuello, a professor of agricultural and biosystems engineering at the University of Arizona and vice-chair of the Association for Vertical Farming, based in Munich, Germany.
“In the future, customers want to make sure they have reliable access to food nearby. Vertical farming can be hyper-local, with a facility next to your restaurant or inside your grocery market if wanted," Cuello said.
As people value their health more during a global pandemic, nutrient-packed leafy greens are the most likely food that will be produced indoors, especially in remote areas with harsh environments, said Krishna Nemali, assistant professor of controlled environment agriculture at Purdue University in Indiana. "In northern places, like Iceland or Alaska, or in desert regions, like the Middle East, they struggle to grow food outdoors, so they are turning more to hydroponics," Nemali said. "That's where we will see more demand."
Another vertical farm company, Indiana-based Green Sense Farms, also reported an increase in calls and inquiries to its sales staff from potential customers about its technology, said Robert Colangelo, a founder, and CEO.
Colangelo's company provides contract research, design, and construction of indoor, controlled-environment agriculture facilities. Green Sense charges a little under $1 million to provide a system that includes an automated germination room, grow room, equipment room, and cooled packinghouse room."
What we found is the COVID virus caused people to look at the length of their supply chains. Long complex supply chains can really be disrupted," Colangelo said.
He said he has spoken to officials in various cities who want to learn more about setting up vertical farms."
If you have a food desert [an area with few grocery stores] or a school or hospital in a remote area, you could produce greens right on your property or right next door for that," he said.
Chicago-Area Greenhouse BrightFarms Expands As Pandemic Fuels Demand For Local Lettuce, Spinach and Other Greens
BrightFarms’ Rochelle greenhouse, which annually supplies 1 million pounds of lettuce, spinach, arugula, basil and other greens to Mariano’s and other regional grocery stores, is increasing production by 40% by adding more hydroponic ponds to the two-acre facility, CEO Steve Platt said
CHICAGO TRIBUNE | JULY 07, 2020
Silvia Penaran grabs a handful of spring mix to pack in a container at BrightFarms on July 1, 2020, in Rochelle. (Stacey Wescott / Chicago Tribune)
BrightFarms is boosting capacity at its Chicago-area greenhouse as the pandemic-driven rise in cooking at home fuels demand for locally grown greens.
BrightFarms’ Rochelle greenhouse, which annually supplies 1 million pounds of lettuce, spinach, arugula, basil and other greens to Mariano’s and other regional grocery stores, is increasing production by 40% by adding more hydroponic ponds to the two-acre facility, CEO Steve Platt said.
BrightFarms was seeing year-over-year sales growth of about 20% before the COVID-19 pandemic hit the U.S., but in March and April growth jumped to 40% as stay-at-home orders set in and customers flocked to grocery stores, Platt said. The at-home cooking trend has remained steady, with growth now leveled out above 30%.
“We’re seeing really great demand,” said Platt, whose company, based in Irvington, New York, has other greenhouses in Northern Virginia, Ohio, and Pennsylvania and is building one in North Carolina. “The pandemic has supercharged that.”
Baby romaine lettuce fills sections of the greenhouse at BrightFarms on July 1, 2020, in Rochelle. (Stacey Wescott / Chicago Tribune)
Greens grown indoors, either in sprawling sunlit greenhouses or under artificial lights in vertical farms, occupy a tiny niche of the market. But they have been gaining popularity in recent years in the Midwest as consumers opt for more local, pesticide-free produce that doesn’t travel thousands of miles from California or Arizona farms to reach their dinner plates.
In addition to addressing environmental and freshness concerns, growing year-round in a controlled environment guards against bacterial contamination that lead to illness and recalls.
Local greenhouses had an advantage as demand from grocery stores surged during the rush to stockpile food during the pandemic because they could pivot quickly while some of the large operators of field-grown produce couldn’t get enough product to stores shelves quickly enough, Platt said.
“When the customers needed product we were able to deliver it,” Platt said. BrightFarms added 800 stores to its distribution this year and now has 2,000 customers nationwide, he said.
Angelica Vasquez cleans the floors at BrightFarms in Rochelle on July 1, 2020. (Stacey Wescott / Chicago Tribune)
In Chicago, locally grown greens represented 11.5% of the tender leaf packaged salad market during the first half of this year, up from 9.4% last year and 7.9% in 2018, according to data from the market research firm SPINS provided by Bright Farms. Nationally the share is much lower, at 3.2%.
The growing interest fits with a broader trend toward more premium foods, with people willing to pay more for products they perceive as healthier. A clamshell of BrightFarms romaine or spinach is $2.99, twice the cost of the cheapest option though on par with field-grown organic produce, Platt said.
But Platt attributes the growth not only to consumer demand but also retailer demand, as stores try to avoid the disruption of recalls. Last month certain bagged garden salads from Jewel-Osco, Aldi, Hy-Vee, and Walmart were recalled due to suspected contamination of cyclospora, a bacteria found in human feces, and E. coli illnesses have prompted mass recalls of romaine lettuce in recent years.
Other indoor growers also are expanding in response to increased demand.
Gotham Greens last year more than doubled its capacity to serve the Chicago area when it opened a new 100,000-square-foot greenhouse in Pullman, a stone’s throw from its existing 75,000-square-foot greenhouse on the roof of the Method soap manufacturing plant.
MightyVine, which grows hydroponic tomatoes in a greenhouse in Rochelle, is doubling its footprint to 30 acres.
Alexia Elejalde-Ruiz
Alexia Elejalde-Ruiz covers the food industry for the Chicago Tribune's business section. Prior beats include workplace issues, the retail sector and lifestyle features, plus stints at RedEye, the Daily Herald and the City News Service. Alexia grew up in Washington, D.C., and has her degree in international relations from Brown University.
Focusing On The French Market With Turnkey Greenhouse Projects
"Sustainability is really a theme in France," says Richard van Dijk with HortiNed. The company is focused on the French market, although they do projects in other countries as well.
"Sustainability is really a theme in France," says Richard van Dijk with HortiNed. The company is focused on the French market, although they do projects in other countries as well. Just before the COVID-19 pandemic outbreak, the concrete was poured at a 4-hectare project in Nîmes. Hortined prefers to do the whole project, from greenhouse and heating to screening and gutters.
French market
In the beginning of the COVID-19 pandemic, the pricing in France was under a lot of pressure. There was a great deal of uncertainty on the market for, among others, vegetables, flowers and plants. "France always needs some import to meet the demand, and little goes abroad."
"The French appreciate the French product more than the Dutch appreciate the Dutch product," explains Richard. "French people like to eat food from their own country." The country tries to keep its own market up, by putting only French products in the supermarkets. The pricing is influenced positively by this, and most vegetable growers have been able to have decent results. The flower and ornamental industry has been hit pretty hard, though.
The projects were allowed to continue during the corona crisis, luckily. With the necessary adjustments, forms were required, for instance, and extra obligations had to be met. "Fortunately we were in regions where the virus didn't hit as hard as in other regions." In the cafeteria, everyone had to sit a bit further apart and cleaning was done more often. The projects are large and spacious, and everything is outside, which makes it easier to work further apart. "We did let the local security officer check everything."
Projects
A good example of sustainability in the French projects is also the project which HortiNed did in Égletons. HortiNed took care of the greenhouse, the heating and the screening here, in cooperation with French company Divatec. The project is run by two young growers and an experienced one who already runs a project nearby. Tomatoes are grown here, and at the end of 2019, it was time for the first harvest. "At least one, probably two seasons will be grown here, and then the next 4 hectares will be built." There's air treatment units in the greenhouse, that ensure that the customer can efficiently manage the climate and dehumidify.
Residual heat
The greenhouse in Égletons is connected to a waste incineration plant. "Up until now, most of the heat from the plant was not used, but now we can heat the greenhouse with it." There still is a boiler room at the company, but that's only used as a back-up, or when the incineration plant is in maintenance. In France, it's quite common to connect greenhouse projects to residual heat, for instance geothermal, waste heat, or wood boilers. A project like this, with a waste incineration plant, is also not uncommon. "With our heating experts, we can determine what the best way of using the heat is, and prepare and execute this technically. With this, we help clients as much as possible."
Brittany
HortiNed also recently started with a new project in Brittany. "That wasn't easy, the labor inspection didn't allow the start of the work due to the COVID-19 outbreak. We sat around the table with them and explained the situation, upon which they allowed us to start. That is the advantage of focusing on a certain market, we know the people and where we have to go, which enables us to take care of these kinds of cases more easily. That is good for the customer and for us."
The project in Brittany is also four hectares in size. It is an existing nursery of eight hectares, of which half will be removed by greenhouse demolishing company Olsthoorn. This will be recycled, and four hectares will be built back.
For more information:
HortiNedJogchem van der Houtweg 5
2678 AG De Lier
The Netherlands
info@hortined.nl
www.hortined.com
Publication date: Mon 29 Jun 2020
Author: Marlies Guiljam
© HortiDaily.com
Food Insecurity Rates Vary Across States
USDA monitors the extent of food insecurity in U.S. households at the national and State levels through an annual U.S. Census Bureau survey
USDA monitors the extent of food insecurity in U.S. households at the national and State levels through an annual U.S. Census Bureau survey. Food-insecure households are defined as those that had difficulty at some time during the year providing enough food for all of their members due to a lack of resources.
Food insecurity rates vary across States because of differing characteristics of the population, State-level policies, and economic conditions. Data for 2016-18 were combined to provide more reliable State statistics than one year alone would provide.
The estimated prevalence of food insecurity during 2016-18 ranged from 7.8 percent of the households in New Hampshire to 16.8 percent in New Mexico with a national average of 11.7 percent. In 12 States, the prevalence of food insecurity was higher than the 2016-18 national average, and in 16 States, it was lower than the national average. In the remaining 22 States and the District of Columbia, differences from the national average were not statistically significant.
This map appears in the Food Security and Nutrition Assistance section of the Economic Research Service’s Ag and Food Statistics: Charting the Essentials.
Horti Daily | Tuesday, May 12, 2020