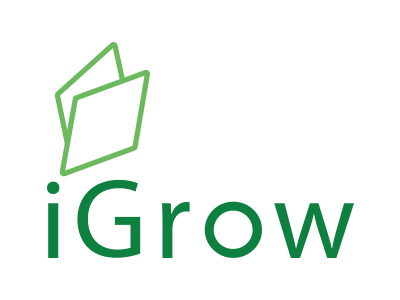
Welcome to iGrow News, Your Source for the World of Indoor Vertical Farming
The Promise And Peril of Vertical Farming
The indoor agriculture industry spans centuries-old growing methodologies and high-tech, computerized urban farms
August 10th, 2018
MARIYA KHANDROS
As part of the Anchor Procurement Initiative, Economy League staff investigate new and emerging industries that could yield opportunities to localize institutional spend. Over the last 4 months, Mariya Khandros, Economy League’s Director of Shared Solutions, has been investigating the current state and future promise of the indoor, vertical farming industry. Conceptually, vertical farming can meet the institutional demand for produce via high-tech, indoor, commercial-scale urban farms. Mariya attended the Aglanta Conference, Indoor AgTech Innovation convening, and participated in working sessions at USDA’s Innovation and Design in Vertical Agriculture & Sustainable Urban Ecosystems conference to help define USDA's research agenda on the subject of indoor agriculture. The following article is a summary of her findings.
The indoor agriculture industry spans centuries-old growing methodologies and high-tech, computerized urban farms.
For most people, the concept of indoor farming typically conjures images of neat rows of greens in futuristic self-contained boxes under violet LED lights. But indoor farming – known as Controlled Environment Agriculture (CEA) among those in the industry – has been a reality in Pennsylvania since 1885. Kennett Square mushroom farms produce half of America’s mushrooms, primarily indoors. CEA encompasses a wide range of farms, ranging from lower-tech plastic hoop houses to greenhouses, to high-tech vertical farms. While great advances have been made across the spectrum, significant media and investor attention have homed in on high-tech vertical farms – large plant factories that grow vegetation indoors primarily using LED lights, and relying on sophisticated computer systems to track, measure and, often, harvest crops.
The rest of this article investigates the newest addition to the CEA family - the vertical farm.
As the population grows, arable land shrinks and water becomes scarce, the world faces a looming food crisis.
The growth of the global population, combined with a looming water crisis is moving the Earth towards a global food crisis. Feeding the projected population of 2050 (9.7B) requires an additional 109 million arable hectares, a landmass larger than Brazil. Given that 80% of arable land is already in use, absent major changes to traditional agriculture practices the world faces a significant food shortage.
Water scarcity, likely to be made worse by climate change, is another threat to the global food system. According to the United Nations, by 2025, two-thirds of the world's population will live in water-stressed regions as a result of use, growth, and climate change. Currently, 70% of the world’s freshwater is used for traditional agriculture, so a water crisis will inevitably reinforce the food crisis.
The impact of climate change will be variable and unpredictable, which will also add pressure on the food system. For example, higher CO2 levels will increase some plant yields, but will reduce their nutritional values. Warmer temperatures may lead to the growth of many new pests and weeds. Extreme temperatures may lead to droughts or extreme rainfall, both of which can prevent crops from growing.
Vertical farming could be part of the solution because it uses less water and allows farmers to control the growing climate
Dr. Dickson Despommier, who popularized the idea of vertical farming in the US, has estimated that a 30-story building covering one city block (5 acres) could have the productivity of a 2,400 acre traditional farm, because of the year-round growing season and the ability to use vertical space to stack vegetables. Because a controlled environment allows easier water recapture and reduces evaporation, vertical farming is estimated to use 70-95% less water than traditional agriculture. For this reason, areas with limited water supplies are early adopters of vertical farming. The United Arab Emirates is building the world's largest indoor farm, as the country's arid climate, poor soil quality and occasional locust plagues make indoor farming a more financially viable alternative.
However, the industry is young and grappling with many open questions.
The vertical farming industry today can be compared to the home video industry when VHS was still competing with Betamax. There are no standards around technology or growing processes. Data on growing efficiency and financial sustainability is just starting to emerge.
Most vertical farms are struggling financially. According to an Agrilyst survey, only 27% of indoor vertical farms are profitable, as compared to 67% of greenhouse farms and 50% of container farms. Despite a year-round growing cycle, vertical farms can only profitably grow a limited number of crops. Excluding cannabis, the most lucrative crops in 2016 were reported to be tomatoes and other vine crops, strawberries, herbs, and microgreens, salad greens and edible flowers. The single biggest reason for low profitability are the massive start-up costs – an estimated $4 million of up-front investment is needed for a 30,000 square-foot farm, and that does not include the sizeable electricity bills associated with farm operations.
Critics are also concerned with the environmental impact of indoor farms, pointing to the inefficiency of replacing natural light with fossil fuel-powered lights. A study completed by Cornell suggested that vertical farms have a much higher carbon footprint than greenhouses. Critics see vertical farming as an over-engineered solution to the problems plaguing the food system and suggest that improving crop diversity, reducing food waste and maintaining soil integrity in traditional agriculture will address the long-term nutritional needs of the planet.
As a city, Philadelphia has seen first-hand the ‘over-promise and under-deliver’ downside of the indoor farming industry, with the recent revelations about the legal and operating troubles of the much-hyped Metropolis Farms. It also saw the rise and fall of a once-promising aquaponics endeavor in the early 2000s.
Despite early struggles, the industry may be reaching a tipping point; rapidly falling cost of LEDs, artificial intelligence and the global water crisis may tilt the scale in favor of vertical farms.
In the United States, there are an estimated 40,000 CEA farms producing $14.1B of market value each year; when compared to 2.1 million farms overall, with $395 billion in agricultural products, the number of vertical farms seems negligible. However, despite comprising a small portion of farming, indoor farms seem to take the lion’s share of investor attention. In 2016, investment in vertical farming grew from $36 million to $271 million (+653%), driven primarily by Plenty Farms. Several technological and environmental developments are driving this trend.
Despite murky profitability prospects associated with vertical farms, investors see potential because of rapid development in two technologies – LED lights and artificial intelligence. Many companies made their fortunes on the falling cost of a technology: Google on the cost of data storage, CRISPR on the reduced price in DNA sequencing. This is what ultimately convinced prominent investors, including Amazon’s Jeff Bezos, to give $200M to Plenty, a fledgling, but ambitious vertical farm company.
The second development driving down the cost of indoor farms is the leaps and bounds being made in the realm of artificial intelligence. Labor is one of a cost that indoor farmers are open about seeking to minimize. A familiar debate tends to emerge around the question of job destruction; with vertical farmers saying that they are replacing hard, back-breaking labor of harvesting with family-sustaining technician jobs, while critics allege that the new jobs will not benefit individuals who are losing the low-end job. However, by and large, vertical farmers are not aiming to replace traditional farming, but capture untapped demand generated by a growing population and an increased appetite for greens and other produce. Anecdotal evidence demonstrates that so far, the job creation story aligns with this vision. Vertical farming is creating entirely new jobs and drawing from a young, urban, highly-educated population that would be unlikely to pursue traditional farming jobs.
The third economic lever is related to environmental change. Historically, water has been highly subsidized in the US. However, as water becomes scarce, and in regions such as the Middle East, where it already has, the cost of traditional agriculture will rise, compared to the more-water efficient vertical farms.
Aquaponics Bed, CC Image courtesy of Plant Chicago on Flickr
In the US, vertical farming has the potential to provide numerous benefits to cities, including the revitalization of vacant spaces, job training programs and an innovative approach to nutritional education.
Around the country, cities have employed vertical agriculture as a tool for education, food system resiliency, job training, and community-building by incorporating vertical farms into broader community initiatives and building deep connections with neighborhoods in which farms are located.
For example, in Washington DC, Urban Food Hubs are small scale systems centered on high-efficiency urban food production (traditional urban farming methods combined with hydroponic and aquaponic systems), co-located with commercial kitchens and community spaces for education. These centers provide nutritional education, vocational training in vertical farming and food processing, and help address nutritional deficiencies in neighborhoods by growing food for local distribution.
In 2017, a Baltimore company, Urban Pastoral, partnered with workforce training organization Humanim, a nonprofit that creates sustainable social enterprises, to build a vertical farm that will train workers in “new generation farming.” This year they are slated to open another farm on the grounds of a high school to teach students about farming and running a business.
In Chicago, Plant Chicago is a collective of businesses with a mission to cultivate ‘circular economies’ (systems where waste from one process is repurposed as inputs for another to create a closed-loop model of material reuse). An aquaponic vertical farm is one of the components of the system, interchanging CO2 and oxygen with a co-located kombucha producer and beer brewer.
Atlanta sees vertical farming as a puzzle piece in their urban agriculture landscape and another way of increasing the resiliency of their food system, under the Smart Cities initiative. Additionally, their policymakers work to attract farms to vacant lots and buildings in order to help increase surrounding property values.
It should be noted that although the initial pitch of a vertical farmer to a city typically starts with the promise of job creation, this is not a benefit most cities seek from vertical farms. By design, vertical farms are not very labor-intensive. One of the most successful indoor growing operations, Gotham Greens, is building the world’s largest rooftop farm (140,000 sf) in Chicago’s 9th Ward. It will create 60 permanent jobs. Despite this limited workforce development potential, policy makers see value in vertical farms as a tool for community engagement and education, at least while the industry is in its early stages.
Philadelphia should be positioning itself to capitalize on the vertical farming opportunity while implementing policies to mitigate risks associated with the industry.
Vertical farming can benefit Philadelphia’s economy in a variety of ways: indoor farms can help improve the utilization of abandoned warehouses and buildings, provide another means of nutritional education and help a new generation become enthusiastic about farming through workforce development initiatives. At the same time, vertical farming is an industry in flux, making it difficult for policymakers to predict the success or failure of any given venture. In order to mitigate risk, rather than picking winners for large tax incentives, policymakers should create an ecosystem that allows many vertical farms to thrive.
The following are policy areas that Philadelphia should consider to encourage the growth of vertical farming while limiting the city's exposure to the industry's downside.
Including Vertical Agriculture in City Planning Efforts
Rather than seeing vertical farming as a stand-alone industry, policymakers should consider it in the broader context of the regional food system. Not only does Pennsylvania have a robust farming industry, Philadelphia’s traditional urban farms have been a vehicles for lot beautification, food justice, and income generation for decades. Consequently, any urban farming plans or zoning policies should take existing urban and regional farms into account. Atlanta offers a great example of comprehensive planning. Atlanta included urban food policy into its Resilient Atlanta Strategy and promotes every type of agriculture, from lot farming to high tech indoor farming through Aglanta, a program under the umbrella of the Mayor’s Office of Resilience. Aglanta, in turn, cooperates with the state-wide Georgia Grown program.
Tax Incentives
Both Philadelphia and the Commonwealth of Pennsylvania offer extensive tax incentives and grants to new companies for job creation, investment in disinvested neighborhoods, property renovation, and environmental sustainability. Additionally, there are programs at the state and federal levels specifically targeted to farmers. Rather than adding new incentives, Philadelphia policymakers should assemble relevant tax breaks into a package that entrepreneurs can use to identify applicable incentives and navigate the process of applying for each program.
Defining the Market
A market study that quantifies the demand for locally grown produce, identifies distribution centers, institutional buyers and other potential clients can catalyze the creation or expansion of farms by demonstrating the opportunities available in the Philadelphia market. The Economy League’s assessment of the Philadelphia food economy can serve as the foundation for such a study. Beyond a report, actively making connections between farmers and institutional food buyers can support fledgling ventures by providing a stable source of revenue.
Due Diligence
Because vertical agriculture is a new and evolving industry, few investors and clients have the skillset to assess the technological capabilities, revenue projections and growth forecasts of vertical farms. Policymakers can help build credibility with both set of parties by identifying organizations or companies that provide due diligence. For example, Eric Stein is developing a Center of Excellence for Indoor Agriculture in Pennsylvania. Nationally, Agrictecture specializes in helping municipalities develop policies and foster the creation of vertical farming economies. By identifying a skilled and neutral party to help investors and buyers distinguish between promising and floundering ventures, policymakers will help build a local knowledge base and reduce risk.
Industry Networking Opportunities
Many entrepreneurs in the vertical farming space are not focused on building and managing farms, but on producing different parts of a whole (lighting, fertilizer, irrigation system). For this reason, creating a space to bring together technology companies, farmers, customers and funders will be critical to the success of the industry. However, limiting these events to vertical farmers would be a mistake. Rather, these events should provide an opportunity to create linkages between urban and rural farmers, as well as Philadelphia's traditional and high-tech farms, to facilitate knowledge and technology transfer.
Education and Workforce Training
Building out a workforce requires breaking down siloes between technology and agriculture, working with universities (such as Philadelphia’s two nearest land grant universities – Rutgers and Penn State) to create opportunities for training and knowledge transfer. When it comes to equity, vertical farming is in danger of repeating the mistakes of Silicon Valley – creating opportunities almost exclusively for an ethnically homogenous group of wealthy individuals. Placing growing towers in public schools and community centers, creating multi-functional food hubs and developing job training program are ways that cities have worked to distribute opportunities more equitably. Working with vertical farms to ensure they are growing culturally appropriate products for their neighborhoods will deepen linkages to surrounding neighborhoods and, consequently, a more diverse workforce.
The Economy League's Anchor Procurement Initiative team will remain attentive to developments within the industry.
Vertical farming alone will not solve food deserts, nor eliminate unemployment. However, it is an exciting new industry that promises to revolutionize many aspects of agriculture, while redefining local by bringing farming into our most intimate spaces: homes, offices, and schools. If Philadelphia approaches this new industry with discipline and intention, our city will be poised to reap the benefits for many years to come.
Although the vertical farming industry is currently in too early of a stage to be able to provide a stable supply of produce to anchor institutions, it is developing very rapidly. The API team will keep track of the developments within the industry, in order to identify viable opportunities as they appear in our city.
Old MacDonald Had A Carpark? The Urban Farms Growing In Unlikely Places
Demand in cities for locally sourced food is growing, but space is at a premium. No wonder urban farms are flourishing everywhere from carparks to air-raid shelters
Tue 17 Dec 2019
Growing Underground in Clapham, south London, an urban farm in former air-raid shelters.
Photograph: Dan Kitwood/Getty Images
Demand in cities for locally sourced food is growing, but space is at a premium. No wonder urban farms are flourishing everywhere from carparks to air-raid shelters.
The delivery man arrives back at the farm, his produce drop-offs for the day complete. He’s greeted by ecstatic barking from his three dogs, one of which leaps into his arms, licking his face enthusiastically.
It’s a familiar scene from any farm, anywhere in the world. But this delivery man didn’t drive through muddy fields or down country roads to get here. He freewheeled his bicycle down the blue-striped spiraling entrance of an underground car park.
This is La Caverne, the only subterranean agricultural operation in Paris. It is housed within 9,000 sq m of a disused multistorey parking facility beneath a social housing complex. Since 2017, Jean-Noël Gertz, a thermal engineer and founder of agricultural start-up Cycloponics has used this space to grow mushrooms and endives and deliver them to the organic shops of the city’s inner north.
Cycloponics co-founders Jean-Noël Gertz (left) and Theo Champagnat with some of their subterranean produce. Photograph: Kasia Wandycz/Paris Match via Getty Images
Gertz shows me around the facility, which winds deeper and deeper. One level down, a conveyor belt runs across several numbered parking bays, along which staff separate endives from their gnarly roots and pack them into crates for delivery. Endives, grown entirely without sunlight, are a perfect crop for a below-ground venture like this. Reportedly discovered by a Belgian farmer who tried to hide chicory roots from the taxman in his cellar only to find they grew delicious, tender leaves while they were down there, endives are now the fourth most popular vegetable in France
As we descend even further, Gertz has the straightforward air of someone who thinks running a farm out of an underground car park is a perfectly normal thing to do. He says he doesn’t mind spending most of his time below ground. “We have a lot of space here and we walk a lot, we’re all in very good health,” he says. With limited land, the only idea is to grow food underground and leave the land above for peopleSaffa Riffat, World Society of Sustainable Energy Technologies
Odd as it seems in the heart of the city, this kind of agriculture may soon become widespread as demand for organic, locally produced food grows and car use declines. Underground farms have sprung up in other major capitals such as London and New York.
This particular one runs three storeys deep below a public housing complex in Porte de La Chapelle. Built-in the autocentric 1970s, by the time Cycloponics moved in there were just 40 vehicles left. The area has double the poverty rate of the Paris average, and 30% of residents under 25. Owning a car is simply no longer an option for many people.
Indeed, across Paris, 58% of working households do not own a car. As mayor Anne Hidalgo continues to discourage driving and encourage public transport, the city is looking for new uses for these vast subterranean spaces.
Endives, which grow without light, are the perfect crop for an underground farm.
Photograph: Kasia Wandycz/Paris Match via Getty Images
Since 2016, the town hall’s Pariculteurs programme has offered up spaces like this – as well as rooftops and courtyards – to businesses willing to turn them green. Businesses like Cycloponics can bid for these spaces in a public call. Parisculteurs estimates that by 2022, there will be 1,240 tonnes of fruit, vegetables, mushrooms, herbs and 1.3m plants grown in Paris every year.
Saffa Riffat, the president of the World Society of Sustainable Energy Technologies, says that if the world is going to feed 9 billion people by 2050 agriculture will have to move underground. Riffat is leading a project at Nottingham University on how to convert the 12.5 sq km of abandoned mines in the UK into farms.
Anything that’s local in provenance and sustainable is going to pay a larger and larger role in people’s purchasing decisions Steven Dring, Growing Underground
“With limited land, the only idea is to grow food underground and leave the land above for people,” he says.
He gives the example of China, where vast swathes of land are too contaminated to farm and many people are being sent to the big cities to live.“
People are moving from the countryside to the city so there’s [fewer and fewer] farmers to grow food. So, we have to move the overall infrastructure of growing food from the countryside to cities,” he says.
Clapham, south London, is home to Growing Underground, a massive hydroponic operation in a second world war air-raid shelter. While La Caverne specializes in vegetables that don’t require sunlight, Growing Underground uses LED lighting to grow herbs, microgreens, and salad leaves – something that’s only become possible in recent years with advances in technology, says co-founder Steven Dring. Eight to ten years ago, the lighting available would have made the tunnel too hot to grow anything down there, he says.
An employee carries boxes of micro-green salad from the elevator Growing Underground. The farm’s clients include Tesco, Marks & Spencer and Ocado. Photograph: Daniel Leal-Olivas/AFP/Getty Images
Growing Underground supplies restaurants and supermarkets with 15 different product lines and has deals with Tesco, Marks & Spencer and Ocado, among others.
“Anything that’s local in provenance and sustainable is just going to pay a larger and larger role in people’s purchasing decisions,” Dring says.
Most of what we eat in Paris is cultivated, raised or produced 600km from where we live Julien Roudil, Le Producteur Local
Back at La Caverne, Gertz takes me to see the mushrooms. Neat rectangular bales are suspended from the ceiling in rows, small clusters of mushrooms sprouting out of each. Steam pours out of overhead pipes and the floor is under a centimeter of water in parts. “We have to recreate autumn in here,” he says.
Unlike the familiar carpark sound of footsteps echoing in concrete, the air here smells like a fusty forest floor. It is thicker, damper and warmer than the crisp early winter day above ground.
Controlling the temperature year-round is one of the major advantages of underground farming.
Suspended bales grow champignons de Paris in artificially autumnal conditions.
Photograph: Kasia Wandycz/Paris Match via Getty Images
The disadvantages, Gertz says, involve frequent water leaks and having to haul the farm’s waste up to ground level to dispose of it – not to mention the Herculean effort required to clean the polluted space to the standards required for organic certification.
If hyperlocal city produce seems like the ultimate 21st century demand, there is actually a surprising precedent for growing mushrooms under the streets of Paris. Throughout the 19th century, farmers grew champignons de Paris – button mushrooms – in the abandoned quarries below the city. Stones taken from these underground caverns gave the Hausmann buildings of the capital their distinctive rose-grey hue, and left behind a perfect environment for the fungus to thrive.
The mushrooms were pushed out of the city that gave them their name with the construction of the Métro at the turn of the 20th century. Now, the popularity of the Métro and the decline in car use is what’s bringing them back.
In 2020, with the opening of Cycloponics’ second Paris location, and alongside their shiitake and oyster brethren, champignons de Paris will be grown within city limits once more, 90 years after they disappeared. La Caverne already produces 100-200kg of mushrooms a day, selling to places like Le Producteur Local, an organic supermarket and non-profit cooperative of 45 producers that stocks meat, cheese and vegetables all grown within 150km.
A rooftop farm in Paris run by Agripolis, an urban farming company. Photograph: Agripolis
“You have to realise that most of what we eat in Paris is cultivated, raised or produced 600km from where we live,” says director Julien Roudil, pointing out that much of what a Parisian household regularly consumes is in fact readily available within just 60km.
Although he’s a champion of local produce, Roudil says Paris will probably never be able to feed itself entirely, no matter how many rooftops or carparks are converted into farms. The popularity of locally grown produce already outstrips the local land available for farming, he says, and there’s not enough space available in Paris to supplement that at a reasonable price.
Dring is more optimistic about the prospects of greater London becoming self-sufficient, whether by growing on rooftops, on barges on the Thames or in bunkers. “All these different technologies will be complementary to each other. I think London will certainly be sufficient within 100 miles,” he says
Dubai Industrial City Home To Badia Farms’ New Large-Scale Vertical Farm
Dubai Industrial City, a TECOM Group member and one of the largest industrial hubs in the region, will be home to Badia Farms’ upcoming new large-scale high-tech vertical farm
December 17, 2019
Dubai Industrial City, a TECOM Group member and one of the largest industrial hubs in the region, will be home to Badia Farms’ upcoming new large-scale high-tech vertical farm. Badia Farms is a regional AgTech leader that was selected by Financial Times in September 2019 as one of the top 25 most innovative companies in the Middle East that are disrupting their sectors.
The signing ceremony drew the participation of His Excellency Dr. Thani bin Ahmed Al Zeyoudi, Minister of Climate Change and Environment, and Abdulla Belhoul, Chief Commercial Officer of TECOM Group. Saud Abu Al-Shawareb, Managing Director of Dubai Industrial City, and Omar Al Jundi, Founder and CEO of Badia Farms, signed the agreement formalizing the partnership.
Spanning an area of 50,000 sq ft, the state-of-the-art facility is expected to start operations in Q2 2020. The vertical farm will have the capacity to produce 3,500 kg of high-quality fruits and vegetables on a daily basis. From Dubai Industrial City, Badia Farms will grow more than 30 varieties of fruits and vegetables sustainably.
Considered as the future of farming, vertical farming uses high-tech methods to produce crops in a controlled environment leveraging vertical space, without pesticides, and using fewer resources compared to traditional farming. The Badia Farms facility in Dubai Industrial City, in particular, is a game-changer, as combining fruits and vegetables in vertical farming is uncommon on a commercial large-scale basis.
This pioneering farm aligns with Dubai’s and the UAE’s efforts to promote the AgTech industry and implement progressive policies nurturing innovation that contributes to national food security in a country where more than 80 percent of fruits and vegetables are imported. The UAE expects to become a food producer in the near future, owing to technological transformations, especially in vertical farming. As a key stakeholder of the Dubai Industrial Strategy 2030 tasked with priority subsectors that include the food industry due to its importance to national food security, Dubai Industrial City offers diverse solutions that cater to the requirements needed for such operations.
His Excellency Dr. Al Zeyoudi said: “Badia Farms is an exceptional example of how the UAE’s agricultural industry can thrive while protecting our environment for future generations. This new high-tech vertical farm will contribute to the UAE’s commitment to becoming more sustainable. Hydroponic technology is a major contributor to agricultural sustainability and food diversity, as it improves crop production and lowers its cost. This is evident in the successful production achieved by Badia Farms in the very short time since its inception. Sustaining food diversity relies heavily on innovation and the employment of cutting-edge technologies.
“The Ministry supports all efforts in this field and works on strengthening its ties with the private sector to explore more potential opportunities. We commend the successful endeavor of Badia Farms, which reaffirms the UAE’s position as a leading incubator for innovation.”
Her Excellency Mariam bint Mohammed Saeed Hareb Almheiri, Minister of State for Food Security, said: “The UAE has set clear plans to enhance its food security, relying on an integrated ecosystem to produce and manage food – a system that employs advanced modern technologies to develop solutions to the challenges the UAE faces, most notably water scarcity and lack of arable land. Controlled-environment agriculture systems are an important solution for producing food in the UAE and the world. The UAE is now home to several vertical farms equipped with hydroponics and soilless farming technologies.”
Her Excellency applauded the announcement to establish a vertical farm as part of Badia Farms that will begin operations next year. She added that the UAE is working to create a conducive environment to promote investment in agriculture in strategic partnership with the private sector, noting that the objective is to ensure sufficient supply of produce to the local markets while driving progress in the food security sector to establish the UAE as one of the top 10 countries on the Global Food Security Index by 2021.
Abdulla Belhoul said: “In line with the UAE’s efforts to lead in innovation and technology, our focus at TECOM Group is on providing an enabling environment for companies across our communities in order to support the growth of our business partners and to attract the most innovative organizations and the best talent that can contribute to Dubai’s knowledge- and innovation-based economy.”
Saud Abu Al-Shawareb said: “As a task force leader of the Dubai Industrial Strategy 2030, our mission is to contribute to the advancement of the industrial sector in the UAE and the sub-sectors identified as priority areas, including the food industry. A main focus for us is on supporting the development of an advanced and sustainable food industry that contributes to national food security. We are proud to have Badia Farms as part of our business community and we are committed to supporting its endeavors to achieve sustainable food production using modern technologies in a state-of-the-art warehouse in line with the National Food Security Strategy 2051.”
Omar Al Jundi said: “In continuation of our efforts to solve the food security challenges in the UAE and the region, we are proud to announce our partnership with Dubai Industrial City to launch a large-scale high-tech vertical farm that will produce gourmet-quality fruits and vegetables all year round. This partnership is key to achieving our objectives and ensuring alignment with the UAE Vision 2021 to provide sustainable solutions to growing food. As founders of the first vertical farm in the region back in 2016, we are committed to innovation in the AgTech space to achieve our ultimate goal of elevating the UAE and the region from importers to exporters of fruits and vegetables.”
Dubai Industrial City provides intelligent infrastructure and integrated solutions for businesses. It is a key stakeholder of the Dubai Industrial Strategy 2030, tasked with developing priority areas, including the food and beverage industry. The hub is home to over 280 factories and more than 750 business partners in sector-specific zones, including major local and multinational organizations.
Based in Dubai, Badia Farms is the AgTech leader in the region that uses innovative hydroponic technology to grow fruits and vegetables all year round. The farm’s ground-breaking methods produce crops without sunlight, soil or pesticides, using 90 percent less water compared to open field farming. The company’s vision is to revolutionize the agricultural sector to provide practical solutions for food security.
Tags: Dubai Industrial City
Take A Look Into The Plant Production Units of Dutch Wholesaler Van Gelder
Man and machine in perfect harmony - that is Japanese car manufacturer, Mazda's, slogan. Looking at Dutch wholesaler, Van Gelder's, new head office gives one the same impression. In the facility two Plant Production Units (PPUs) are realised, to offer inspiration in the field of vertical farming. Earlier this year Van Gelder entered a partnership with indoor farming specialist PlantLab to realise this facility.
New Van Gelder building
This new building in Ridderkerk, the Netherlands, is still in its test phase and includes features such as the High Care kitchen, processing, and packaging divisions, and kitchen. These have all been further optimized and enlarged. The warehouse process has been almost entirely mechanized too. All this in a 32,000m2. The whole company will move over at the end of the first quarter of 2020. Our editors were given a sneak peek of the new facilities.
Meeting place for healthy eating"We have grown tremendously in recent years," says Van Gelder's General Director, Gerrit van Gelder. "Last year, we again realized a healthy growth in revenue. This new location was, therefore, desperately needed."
It will not be merely a fruit and vegetable warehouse. "We are helping to meet the demand for tasty, healthy, sustainable products. We have noticed that chefs are open to having more vegetables in their dishes."
"The hospitality industry is moving more toward 80% vegetables, 20% meat. We are responding to that with this building. It will become a meeting place for healthy food. A place where all your senses will be stimulated," explains Gerrit.
Gerrit van Gelder in front of the banana plants in the new building's entrance.
Healthy meals
Come to Van Gelder in a few months, and you will have your choice of healthy meals. There will be 30 serving counters. People will be able to enjoy a fruit salad, smoothie, or healthy sandwich from the refrigerated counter. There is also a good chance the lettuce and herbs will come from the company's own vertical farm. This cultivation is done in their PlantLab's fully controlled Plant Production Units.
"We were looking for tastier, more nutritious products. We discovered the possibilities vertical farming has to offer. We can grow lettuce and herbs in just 18 days. And we can do so in the most sustainable manner."
"In the future, we will go in search of more new, special tasting products. We will do this in consultation with our clients. Seed breeders are getting the opportunity to bring new crops onto the market. These are based on increasingly renewed techniques and plant knowledge," Van Gelder continues.
Indoor farming
Vertical cultivation units
The vertical cultivation units are located on the third floor of the Experience Center. In this building, there is also room to hold events for as many as 500 people. Some of Van Gelder's suppliers have made these consultation areas uniquely their own.
These suppliers include Zespri, Greenco, Fruit Masters, and Deli-Jack. Then there are, Fruity-Pack, Koppert Cress, Schaap Holland, and Peka Kroef. Beekers Berries, Fruity-Line, and BVP packaging are included too.
These areas showcase the Dutch food sector to every visitor to Van Gelder's new home. From 1 March 2020, these spaces will be up for hire for meetings and such. Outside the new building, no fewer than 540 fruit trees have been planted. Roelof Tree Nursery and fruit farmer, De Jong provided these trees. In this way, visitors will be able to compare many of the fruit varieties with each other.
"At this location, we can further explain our tale for healthier eating. Van Gelder will soon share our growers' personal stories with both international and local visitors. This will happen in the Experience Center as well as outside in the orchard," says Gerrit. ‘’It is literally our source-to-plate story."
Advanced shuttle systemMoving on to the warehouse. "Our assortment is expanding rapidly. The market also has ever-shorter turnaround times. As a result, we focused strongly on innovation in the new warehouse. This has been done thanks to the automation and mechanization of all processes."
Vanderlande largely provided the warehouse's automation. This company is very active in baggage logistics at airports. The warehouse boasts an advanced shuttle system. It is good for 52,000 tray storage locations served by 92 ADAPTOs.
This system sends products to order pickers, in crates, at their work stations. Prepared orders are then immediately refrigerated. When needed, these orders are automatically placed on the loading docks, ready to be delivered.
"We bring the products to the people, rather than having the people fetch the products. For this market segment, this type of technology is truly innovative," says Gerrit. Far fewer order pickers are, therefore, needed. More staff is, however, required in the company's technical division.
The washing of the crates is also fully automated. As many as 3,000 crates are washed per hour. This is thanks to a Viscon-designed crate washing line. There is not only a shuttle warehouse for crate storage. There is also a pallet warehouse with different temperature zones.
Ripe fruitWorkspaces, each with its own unique function, have been set up. An example of this is the building's ripening cells. Visitors can get an idea of the added value Van Gelder provides. They can also taste it later.
‘’We are getting more and more of our products directly from the source. Ripening in our building is done in a controlled, even manner. In this way, the fruit is always tasty. You may as well have picked it from the tree yourself."
’Fruit is picked long before it naturally ripens. This practice is due to large-scale food distribution to, for example, supermarkets. This fruit can then be easily transported and stored for an extended period," the General Director goes on to say.
"The fruit in our orchard may only be picked once it is sufficiently ripe. Each piece of fruit is, therefore, much tastier when you eat it. Whether it comes from a tree on our doorstep or from our warehouse."
Van Gelder believes in minimal risk of loss and the highest possible yields. For this reason, they have a processing area in a 12.000m2+ space. It has 35 product lines. They also have a packaging room and various production kitchens. "We want to add more value to everything we do. We want to give something back," concludes Gerrit.
For those who want to have a look at the building - after its official opening, there will be tours twice a week. The public at large is welcome to join. For now, we have compiled an extensive photo report.
For more information:
Gerrit van Gelder
Van Gelder Groente en Fruit
70 Handelsweg
2988 DB Ridderkerk, NL
Tel: +31 (0) 180 618 599
Email: gvangelder@vangeldernederland.nl
Website: www.vangeldernederland.nl
Publication date: Mon 16 Dec 2019
© HortiDaily.com
Is Vertical Farming Here to Stay?
Almost two decades after vertical farming pioneer Dickson Despommier first introduced the idea of growing food in buildings, not fields—and later published his seminal book, The Vertical Farm—indoor farms are in more cities than ever before
Posted on April 11, 2019, by Jodi Helmer - Story
Unprecedented investments in indoor agriculture are no guarantee the high tech plant factories will be key players in the future of food.
Almost two decades after vertical farming pioneer Dickson Despommier first introduced the idea of growing food in buildings, not fields—and later published his seminal book, The Vertical Farm—indoor farms are in more cities than ever before.
Vertical farming—so-named because the produce sprouts in floor-to-ceiling racks to grow more food in less space—uses less water and fertilizer than conventional “soil” farming and the climate-controlled environments allow growers to harvest crops regardless of the temperatures outside.
Technologies like LED lights, micro-sensors and data analytics help maximize growing conditions and improve yields. Most vertical farms are located in urban areas, minimizing the environmental impacts of shipping produce thousands of miles from farm to plate.
With a global population expected to hit 9 billion in 2050—and 74 percent of the residents of developed nations living in cities—proponents of vertical farming argue that agriculture requires high-tech reinvention. Record numbers of vertical farms are sprouting up to address the perceived need. In cities from Singapore to San Francisco, startups are growing food in shipping containers and warehouses that know no seasons.
The industry has a number of cheerleaders, including the venture capitalists bankrolling the promise of vertical farms. Investments in indoor agriculture increased by 653 percent between 2016 and 2017.
Despite significant investments, Stan Cox, research coordinator for The Land Institute, a nonprofit agriculture research organization, and vocal opponent of vertical farming believes the model is doomed to fail.
“[Despommier’s] original version of growing food in buildings 30 stories tall has never come close to happening,” he explains.
The mismatch between concept and execution, according to Cox, can be attributed to limitations on the crops that can be grown indoors; ongoing investments in infrastructure and technology; and high costs of energy.
Powering Plant Growth
On conventional farms, crops depend on sunlight to grow. Without the energy from the sun, farmers must use huge amounts of electricity to provide enough light to trigger growth.
In a recorded seminar, Louis Albright, emeritus professor of biological and environmental engineering at Cornell University and pioneer of controlled-environment agriculture ran the numbers: Growing wheat in a vertical farm would generate 20 cents per square foot in annual income and growers would need to charge $23 per loaf of bread just to cover the power bills, he estimated.
In a 2016 TED Talk, Astro Teller, head of research for Google, admitted that the tech giant started—and later shuttered—its vertical farm because it was impossible to grow staple crops like grains and rice via indoor agriculture.
Limited crop production is one of the major criticisms of vertical farming.
Most vertical farms grow leafy greens such as arugula, kale and watercress because the crops require less light than other fruits or vegetables. But even with the most efficient LED bulbs, Albright found that it took 2.72 kWh per head of lettuce to grow the crop in a vertical farm—more than three times the energy required to grow lettuce in a greenhouse.
Last fall, Metropolis Farms constructed a 500-kilowatt solar array on the rooftop above its fourth floor vertical farm in Philadelphia that is reported to generate enough power for its 100,000 square foot indoor farm. (Albright questioned whether solar powered indoor agriculture was feasible, explaining that a one-acre crop of lettuce would require 9.3 acres of solar panels).
“The more technology is involved in something, the more fascinated we seem to be with it but the products produced in these high-tech operations have to be pretty expensive to cover energy and other costs,” Cox says.
A panel discussion at the Agritecture conference in Atlanta called An Examination of Shuttered Vertical Farming Facilities led Chris Michael, co-founder of Bright Agrotech, to pen a post, 9 Reasons Vertical Farms Fail. Competing with retail pricing was among them.
In the article Michael notes, “Your pricing should match the quality of your product, not the status quo. With the right system and distribution strategy, the local product you produce should be better than anything else on the shelves and it should be priced to reflect the increase in value.”
Fresh Direct sells 4.5-ounce clamshells of Dream Greens from AeroFarms for $3.99. The price is on par with other packaged organic greens but more than two times the price of Fresh Express brand romaine lettuce sold at Safeway stores.
Despite promises that vertical farming can address food deserts, the premium prices for the leafy greens grown in these high-tech environments often mean those who struggle with food insecurity won’t be able to afford to buy the fresh vegetables growing in their urban neighborhoods.
Cox notes that indoor agriculture makes sense for a high-value crop like cannabis that commands upwards of $8 per gram, but it’s not feasible for a lower value crop like lettuce, which clocks in at one cent per gram.
“Indoor leafy green production can survive if growers sell to more affluent areas of big cities,” he says. “But we’re not going to see [crops from vertical farms] expand into larger segments of the food market.”
Cultivating Job Opportunities
The proliferation of vertical farms has led to a bumper crop of job opportunities.
A CivilEats article declares, “Millennials look to high-tech farms for careers,” noting that Gotham Greens had seen 400 percent growth in its team from 2015 to 2016, creating jobs in the historic African-American Pullman neighborhood of Chicago; and BrightFarms planned to double its staff in 2016 with future expansions potentially creating up to 500 new job openings.
Vertical Harvest in Jackson, Wyoming, employs 15 staff with developmental disabilities to manage tasks ranging from growing and harvesting to retail sales and deliveries.
Unlike conventional agriculture, which depends on a seasonal labor pool, the 24/7 nature of vertical farms can provide regular, long-term employment—and the opportunities extend beyond cultivating and harvesting leafy greens.
The job openings at AeroFarms include mechanical design engineer, plant scientist, research associate and commercial grower with experience in vertical controlled environment agriculture.
Assessing the Impact
Vertical farms have captured the collective interest of investors, academics and foodies alike but will these high-tech plant factories contribute significant volumes of fresh, local foods to our diets? Cox says no.
“There are not enough warehouses and shipping containers to grow that volume of produce indoors,” he explains. “Vertical farming will never be able to supply a significant percentage of our food.”
The challenges haven’t prevented startups from pushing forward or stopped investors from writing checks to back the potential promise of large-scale indoor food production.
In July, San Francisco-based startup Plenty raised $200 million in Series B funding to expand its operations with a goal of “[producing] Whole Foods quality at Wal-Mart prices.” It was the largest agriculture technology investment in history.
Concerns about climate change and farm labor shortages coupled with the need to figure out how to feed nine billion people have helped drive investments. Venture capitalists know we need solutions and see vertical farming as a potential change-maker. Investors also see opportunities related to the technologies used in vertical farms. One investor cited the high-tech indoor farms (and associated advances in robotics, sensors, and software) to be massive opportunities to disrupt conventional farming methods as his reasons for investing in vertical farms.
But significant cash infusions are no guarantee of success.
FarmedHere was considered a national leader in indoor farming when it launched in 2011 but the commercial-scale hydroponic farm in Chicago declared bankruptcy last year, citing unsustainable labor and energy costs. Atlanta-based PodPonics raised $15 million in startup capital but liquidated its assets and shuttered operations in 2016. Labor costs were a factor.
The high-profile failures don’t surprise Cox. Rather than investing millions in vertical farming, he advocates looking to vacant lots and rooftops where sunshine and water can turn seedlings in raised beds into fresh produce for a fraction of the cost of powering indoor agriculture.
“The closer we can produce fresh produce to densely populated urban areas, the better,” Cox says. “Agricultural production has plenty of problems but we’re not going to solve them by growing food indoors.”
Photo: Marcus Spiske Unsplash
Tags: startups, vertical farming
AeroFarms Plans Largest Indoor Vertical Farm of Its Kind
Governor Ralph Northam today announced that AeroFarms will invest $42 million to build their largest, most sophisticated indoor vertical farm to date in the Cane Creek Centre, a joint industrial park for the City of Danville and Pittsylvania County
At 150,000 square feet, the new farm more than doubles the size of AeroFarms’ last major commercial farm in New Jersey.
RICHMOND—Governor Ralph Northam today announced that AeroFarms will invest $42 million to build their largest, most sophisticated indoor vertical farm to date in the Cane Creek Centre, a joint industrial park for the City of Danville and Pittsylvania County.
Just recognized by Time Magazine as one of the Best Inventions of 2019 for Food & Beverage, AeroFarms is an award-winning farming company with proprietary aeroponic growing technology, enabling year-round local commercial production with over 390-times more productivity for leafy greens on a per-acre basis vs. field farming, while using up to 95% less water and no pesticides, herbicides, or fungicides. Virginia successfully competed with North Carolina for the project, which will create 92 new jobs.
“AeroFarms is a leader in agricultural innovation with farming technologies that make high-quality, local produce available to more communities,” said Governor Northam. “We are bringing capital investment and economic opportunity to rural Virginia by recruiting innovative companies like AeroFarms. I thank the company for choosing Virginia for this important venture and commend Danville-Pittsylvania County for helping to secure this project.”
With global headquarters in Newark, New Jersey, AeroFarms is a Certified B Corporation on a mission to grow the best plants possible for the better of humanity. Hiring locally and creating year-round employment, AeroFarms is able to disrupt traditional supply chains to nourish its communities with locally-grown, sustainably-sourced, pesticide-free produce that delivers peak nutrition and flavor, all year round. Proud to be named one of the World’s Most Innovative Companies by Fast Company two years in a row, AeroFarms has grown over 800 different varieties by creating the perfect conditions for healthy plants to thrive, taking agriculture to a new level of precision and productivity with minimal environmental impact and virtually zero risk. AeroFarms indoor vertical farms use specialized growing algorithms leveraging custom LED lights and precision plant nutrition, calibrated to the needs of each plant, to produce baby leafy greens and microgreens that can be grown in up to a third of the time that it takes out in the field by giving the plants exactly what they need when they need it.
“Agriculture is Virginia’s largest private sector industry, and the Commonwealth continues to be on the forefront of agricultural advancements,” said Secretary of Agriculture and Forestry Bettina Ring. “I look forward to working with AeroFarms as they expand the use of agriculture technology to strengthen Virginia’s food system and provide increased access to healthy foods.”
“AeroFarms has an important objective to ensure our growing population has year-round access to healthy food, and we are proud to support its first Virginia operation in Danville-Pittsylvania County,” said Secretary of Commerce and Trade Brian Ball. “The company’s decision to establish a vertically integrated facility in the Commonwealth is a strong testament to the advantages of our location and transportation and logistics infrastructure, which attract industry-leading companies from around the world seeking expansion into new markets. We welcome AeroFarms to Virginia and look forward to our future corporate partnership.”
“We are excited to expand to Virginia, an incredible state with a strong farming tradition, and we have been honored by the amazing reception at all levels,” commented David Rosenberg, Co-Founder & CEO of AeroFarms. “We want to thank everyone for helping bring our 10th farm to life to create new jobs and increase access to healthier foods with better flavor that top chefs like native Virginian David Chang have embraced. With the property developer RealtyLink, we are building out the largest, most advanced indoor vertical farm of its kind with our next generation of growing technology. Locating in the Danville area also specifically highlights how our innovative indoor growing approach works in both rural and urban environments. At 150,000 square feet, our new farm more than doubles the size of our last major commercial farm in New Jersey that will help us meet the strong consumer demand for safely grown produce that delivers peak flavor always. We are also excited about the future collaboration opportunities with The Institute for Advanced Learning and Research (IALR) to build on our Strategic Partnership work with Fortune 100 companies to solve broader ag-related supply chain issues.”
The Virginia Economic Development Partnership worked with the Virginia Department of Agriculture and Consumer Services, Pittsylvania County, the City of Danville, and the Southern Virginia Regional Alliance to secure the project for Virginia. Governor Northam approved a $200,000 grant from the Commonwealth’s Opportunity Fund, as well as a $200,000 grant from the Governor’s Agriculture and Forestry Industries Development (AFID) Fund, to assist Danville-Pittsylvania County with the project.
The Virginia Tobacco Region Revitalization Commission has approved a grant for $190,000 from the Tobacco Regional Opportunity Fund for the project. AeroFarms qualifies for state benefits from the Virginia Enterprise Zone Program, administered by the Virginia Department of Housing and Community Development. Funding and services to support the company’s job creation will be provided through the Virginia Jobs Investment Program (VJIP).
“We’re pleased that AeroFarms has selected the Cane Creek Centre for their new mid-Atlantic facility”, said Robert “Bob” Warren, Vice-Chairman of the Danville-Pittsylvania Regional Industrial Facility Authority and member of the Pittsylvania County Board of Supervisors. “It is only appropriate that the largest county in the Commonwealth by land area will soon be home to the world’s largest and most advanced vertical farm. The region has placed a heavy emphasis on attracting technology-based agribusiness firms through strategic investments in our workforce, and we thank AeroFarms for their commitment to Southern Virginia and its people.”
“AeroFarms is a perfect example of how blending technology with agriculture can provide an environmentally responsible solution to growing nutritious food,” said Fred Shanks, Chair of the Danville Pittsylvania Regional Industrial Facility Authority. “Given the history and importance of agriculture to this region, I cannot think of a better place for AeroFarms to locate. We are delighted to welcome them to this great community.”
“The Tobacco Commission has always supported Virginia’s agriculture industry, the backbone of our state’s economy, and attracting AeroFarms to Danville-Pittsylvania County is a big win,” said Senator Frank Ruff, Tobacco Commission Vice-Chairman. “AeroFarms’ technologically advanced approach to farming is an example of how the industry is adapting to meet the demands of modern consumers and I am pleased that they chose to grow their business here in Southside Virginia.”
“It is exciting to see an innovative company like AeroFarms open their first Virginia location here in Southside,” said Delegate Danny Marshall, a Tobacco Commission member. “Attracting a company like this to our region shows that the effort we have put into developing a top-notch business climate is paying off. I welcome AeroFarms and their team to Danville-Pittsylvania County and wish them the best as they get hiring underway.”
Tagged greenhouse, indoor farming, vertical farm
This Farm Is Growing Food Deep Beneath South Korean Mountains
Once a functioning highway in the province of North Chungcheong, the tunnel's sharp curve was deemed dangerous, so in 2002 it was closed and a more gently curved road was constructed nearby. Now this 2,000-feet-long (600 meters) tunnel is being used to grow salads, leafy greens, and strawberries
By Temujin Doran and Katie Pisa, CNN
December 09, 2019
North Chungcheong, South Korea(CNN) It might seem an unlikely place to be growing fruit, but deep beneath a South Korean mountain, a high-tech farm has been built inside an abandoned tunnel.
Once a functioning highway in the province of North Chungcheong, the tunnel's sharp curve was deemed dangerous, so in 2002 it was closed and a more gently curved road was constructed nearby. Now this 2,000-feet-long (600 meter) tunnel is being used to grow salads, leafy greens, and strawberries.
It's an example of "vertical farming" -- a method of growing food without soil or natural light, in vertically stacked beds in a controlled environment. With no natural sunlight, here, LED lights are used to grow crops all year round.
They're also what give the farm its pink glow -- they emit only the spectrum of light that plants use to photosynthesize. More unusually, the music of Beethoven and Schubert is piped into the tunnel, because it encourages the produce to grow, according to Choi Jae-bin, CEO of NextOn, the company that created the farm.
Are vertical farms the future of food?
In Dubai, a joint venture from agri-tech firm Crop One and Emirates Flight Catering plans to build the largest vertical farm in the world.
An appealing concept
With the world's populations predicted to reach 9.7 billion by 2050, and cities predicted to become more crowded, hyperproductive indoor vertical farming built-in unused spaces, or close to the consumer, has become an appealing concept.
Global warming, increasing soil erosion and water shortages are leading to declining yields in crops, but it's hoped new methods of farming can help tackle the challenge of food production.
Traditional farms can take up a huge amount of space, often requiring forests to be cleared, and the vehicles that harvest crops burn even more fossil fuels. Traditional farms also use much more water than vertical farms.
"The world's population is only going to grow but the environment is only getting worse to grow various vegetables, so I think it [vertical farms] will be the only alternative to provide healthy food to our table in the future," said Choi.
Outside the innovative tunnel farm.
Dickson Despommier -- professor emeritus of public and environmental health at Columbia University, and a pioneer of vertical farming -- agrees.
Find out more about Call to Earth and the extraordinary people working for a more sustainable future
Food derived from indoor farming is more nutritious and safer, he told CNN, as there isn't the same risk of foodborne illnesses, pollution, allergens, and pesticides. Plus, if a traditional farmer were to lose a crop they would often have to wait until the following year for a new harvest. With indoor farming, it's the next week, he said. "The long-term loss is much less."
Challenges for vertical farms
Critics say one of the biggest drawbacks of vertical farming is that maintaining a controlled environment and providing artificial light uses a lot of energy, which can mean a big carbon footprint. But that can be reduced by powering farms using renewable energy, and by increasing the efficiency of their LED lights.
Choi says his underground tunnel system has a naturally steady temperature, which means it needs less energy for cooling or heating.
Another criticism of vertical farming is that it's mostly used to produce leafy greens, rather than higher calorie vegetables or crops. But Despommier says that will change, as more people acquire the expertise to grow different foods.
He says training and education is becoming available at institutions in Rotterdam, Shanghai, and in the US. "As soon as universities catch onto this (teaching indoor farming), they can fill it up with applicants faster than you can sit down to eat dinner," said Despommier.
Other high-profile vertical farms include Berlin-based InFarm, which builds hydroponic modular systems that can be used in supermarkets. California-based Plenty claims for certain crops, it can grow 350-times as much as a field of the same size, while in June, online grocer Ocado announced that it had invested £17 million ($21.5 million) in the nascent industry.
As for NextOn, Choi says his company has plans to build many more farms using the same technology, in urban locations -- reducing the cost and carbon footprint of transporting food to shops.
"Plants easily grown at home, at nearby stores, at hamburger restaurants, or even at metro stations," said Choi. "I think the system to grow crops far away from a city and transporting it will disappear."
Farmshelf Gets Angel Investment From Singapore’s she1K, Liberty Produce Launches UK Vertical Farming Project
Angel network she1K has syndicated an early-stage investment in Farmshelf, according to an article published today on AgFunder News
Angel network she1K has syndicated an early-stage investment in Farmshelf, according to an article published today on AgFunder News. Singapore-based she1K, which is known for its global female executive leadership, did not disclose financial terms of the deal. Farmshelf is the third company to join its portfolio
Whereas many companies in the vertical farming space right now have massive indoor facilities aiming to produce millions of heads of leafy greens, Farmshelf differentiates itself by staying focused on smaller spaces like supermarkets, offices, hotels, and restaurants. Its bookcase-sized farm grows leafy greens and herbs using a combination of custom LEDs, sensors, and software that deliver water, nutrients, and the optimal amount of light needed for each crop. The system, which can simply be plugged into a wall and connected to WiFi, is already at a number of restaurants, hotels, and other spaces, including NYC chain Tender Greens, Marriott Marquis Times Square, and the Condé Nast offices.
The Farmshelf system is currently available to businesses in parts of Texas and California and will be available to customers “in most major markets” in 2020.
Farmshelf isn’t the only indoor farming initiative kicking off December with big news. Across the Atlantic, agtech company Liberty Produce has finally launched its vertical farming project that looks to improve both crop yield and operational costs for vertical farming through improved, more automated tech.
According to a press release sent to The Spoon, Liberty Produce has partnered with several entities for the project. While most were not disclosed, a major one is Crop Health and Protection (CHAP), a network of scientists, farmers, researchers, academics, and businesses developing new ways to use technology to improve the farming system in the UK. Work on the Liberty Produce project is being done at CHAP’s Fine Phenotyping Lab at Rothamsted Research in the UK, with experts experimenting with plants’ responses to different light intensities and studying the best LED “recipes” for crops.
“There’s lots we don’t know about growing plants in this artificial environment and we’re not giving them optimal conditions,” Liberty Produce founder Zeina Chapman told The Spoon earlier this year. “With lighting, there isn’t an option to control it in a way that maximizes plant growth. So we might be putting plants under stress.”
Liberty also wants to use more automation to make the concept of vertical farming easier for anyone, something Farmshelf also appears to be striving for with its plug-in-and-go system.
It’s an admirable goal to strive for, especially if it can get more locally grown produce into the hands of more cafeterias, universities, local businesses, and, eventually, individual homes.
The test — and something we’ll hear more about in 2020 — will be whether the vertical farming industry can find a way to do this cost-effectively. There’s plenty of hype right now around the promises of vertical farming. As to whether it can actually become an everyday reality for the everyman, the jury is still out.
FILED UNDER: AG TECH BUSINESS OF FOOD FEATURED FOODTECH FUNDING MODERN FARMER
Autogrow Appoints Two Product Specialists For Growing Market
Autogrow has appointed Steve Gardner - Head of Product and Sophie Stanley - Head of Product Marketing, to support the company’s continued global growth. Both are members of the Senior Leadership Team
4 December 2019: Autogrow has appointed Steve Gardner - Head of Product and Sophie Stanley - Head of Product Marketing, to support the company’s continued global growth. Both are members of the Senior Leadership Team.
“It’s great to have someone with Steve’s experience joining us. He will lead customer conversations and engagement to shape the value our products provide to growers and the industry,” says Darryn Keiller, CEO.
“Sophie’s experience within agriculture is fantastic. Combined with her passion for the industry, we are lucky to have her on board.”
Steve previously lead product development involving machine learning, IOT and augmented reality products covering web, mobile, APIs and embedded systems in South Africa and New Zealand.
Sophie, a Nuffield Scholar and previous Vice President of Figured – USA, will lead Autogrow’s go-to-market strategy. Having previously built a successful partnership with one of the largest farm lending institutions in the American Midwest, Sophie will drive market adoption and commercial growth.
Autogrow has increased their team over the past 12 months with new employees in Malaysia, the United States, and New Zealand. This growth will continue through 2020 as new innovations are launched into the market.
PHOTO: Sophie Stanley and Steve Gardner
MEDIA QUERIES
Kylie Horomia, Head of Communications
(e) Kylie.horomia@autogrow.com
(m) +6421 733 025
(w) www.autogrow.com www.farmroad.io www.cropsonmars.com
Sales queries – Sales@autogrow.com
About Autogrow
Autogrow leverages the power of technology, data science and plant biology to provide indoor growers affordable, accessible and easy-to-use innovation – 24/7, anywhere in the world.
Our hardware, software and data solutions support growers and resellers in over 40 countries producing over 100 different crop types.
We are the experts in Controlled Environment Agriculture (CEA) and continue to stay ahead of a rapidly evolving landscape.
Denmark: Grown And Harvested In Stores Now In Copenhagen
This is the beginning of a new partnership between Infarm and the Danish retailer Irma. Infarm is planning to bring their fresh produce to more Irma locations across Sjælland in the next few months
Starting Nov. 21st fresh Infarm produce will be available to Danish consumers for the first time at Copenhagen’s Irma Østerport (Oslo Pl. 2, 2100 København, Denmark). Local shoppers (and perhaps even local chefs) will be able to choose from a selection of living Italian Basil, Greek Basil, Parsley, and Coriander Confetti, grown and harvested right in the store.
This is the beginning of a new partnership between Infarm and the Danish retailer Irma. Infarm is planning to bring their fresh produce to more Irma locations across Sjælland in the next few months.
Infarm
Glogauerstr. 6 10999 Berlin
+49 30 58846540
infarm.de
Publication date: Fri 22 Nov 2019
THE NETHERLANDS: "Container Offers Flexible Research Solutions"
On the outside it's 'just' a container. But when the doors open, a good deal of high-tech reveals itself. A climate container to be precise
on their way to USA
On the outside it's 'just' a container. But when the doors open, a good deal of high-tech reveals itself. A climate container to be precise. In Aalsmeer in the Bosman Van Zaal production hall, two are ready to be transported to a large American herb grower who wants to use the container to work out the optimum cultivation recipe for basil.
Carlo Castelijn inside of the container in which three 'Danish carts' fit next to each other. If desired, both sides can also be provided with a Grow&Roll-system with Danish carts.
Container over climate chamber
But why a container and not a climate chamber? "Simple", says Carlo Castelijn of Bosman Van Zaal. "These containers can then be clicked onto the back of a trailer. This makes it possible, after a research project, to sell the container or transport it to another location of the company. A lot cheaper than demolishing an entire climate chamber and rebuilding it elsewhere."
Recently, numbers three and four were built, after the first container had already been built two years ago at the request of another customer.
Three Danish cars
A total of three extra wide 'Danish' cars fit in one half of the container. These can be used to create a small-scale multilayer cultivation system with LED and all the bells and whistles that come with it. On the other hand, a growing table has been mounted for research into 'normal', non-multi-layer cultivation.
The only thing needed to get the climate container up and running is electricity, water and CO2. Electricity to keep the LED lights on and the climate computer running. The latter then takes care of the rest, including the water and CO2 dosing.
The side containing the grow table, a request from the customer who wanted the table as low as possible. In addition, gutters are hung in the container so that the customer can experiment with strawberry cultivation.
Over the past few weeks, the finishing touches have been put to the containers, which will be transported in December.
Finishing off with the numbers:
-Container outer dimensions: 6058x2500x2896 mm LxWxH
-Grow&Roll cultivation area: 9x0.9 square meters
-Cultivation surface table: 2 square meters
For more information:
Bosman Van Zaal
info@bosmanvanzaal.com
www.bosmanvanzaal.com
Publication date: Tue 26 Nov 2019
© HortiDaily.com
OUTLOOK 2019: Global Entrepreneurs Eye Pitt Meadows Vertical Farm
Traditional farming practices have many variables that come into play when growing consistent crops, and with climate change being a rife issue around the globe, what does the future of farming look like? It looks like a Greenhouse 2.0, according to Dave Dinesen, CEO of Cubic Farm Systems
Commercial-Style Crops Growing At Cubic Farm Systems
November 28, 2019
Traditional farming practices have many variables that come into play when growing consistent crops, and with climate change being a rife issue around the globe, what does the future of farming look like?
It looks like a Greenhouse 2.0, according to Dave Dinesen, CEO of Cubic Farm Systems.
“It’s an automated commercial-scale vertical farming system that allows you to grow commercial-scale quantities of leafy green vegetables, herbs, animal feed, lots of different sorts of leafy green products, 12 months a year anywhere on earth,” Dinesen explained about the pesticide-free operation.
Pitt Meadows is home to the sole corporate-owned and operated cubic farm facility that produces commercial-scale crops locally that can be found at some IGA and Fresh Street Market locations. Dinesen says the facility is their test kitchen and production site. The company is in business to sell, install and train their farmer customers on how to operate the system.
“Our smallest system is about a 17 machine set up which would grow almost two million heads of lettuce per year or thousands of pounds of microgreens or other crops like that,” he said.
But the company is hearing from retailers that the crop is not what they have come to expect from traditional farms.
“Believe it or not when it comes to our lettuce, the two consistent feedbacks are, best we’ve ever tasted and this stuff lasts forever, which are two comments that you rarely hear… and the difference is, its how we grow, harvest, and package,” Dinesen explained. “And because we’re able to harvest produce and leave the root on and leave it living, it lasts a long time, stays health, stays crispy, retains its nutritional value.”
So what are the benefits of this technology-enabled farming?
“Traditional farming uses an enormous amount of freshwater and we have to preserve that commodity,” explained Dinesen. “We have to be able to grow locally, we can’t keep shipping so much food for so many miles. Technology-enabled farming or indoor automated vertical farming enables all that. It facilitates automation in a way that is challenging otherwise.”
The company has also found the system produces consistent crop yields when environmental factors are eliminated, something that remains a major factor is traditional farming practices.
“Probably the biggest difference between our system and anyone else is that we have a machine that significantly increases the amount of crop you can grow per cubic foot because we can go high as opposed to just one layer which would be a traditional Greenhouse or a traditional field crop.”
The local corporate facility received its GAP (good agricultural practices) certification almost a year ago and has been in operation since.
“I think Pitt Meadows can be proud it’s had one of the largest vertical farms in Canada operating now for a year. People from all over the world fly in, almost every week to see it, so it is generating a significant amount of economic benefit for the city,” said Dinesen.
The company has sold several units in Canada and some in the U.S. Dinesen said there are a few deals in the works for the new year as well.
“We have a very large farm that will be going into another municipality nearby, early in 2020. The system will be a 26 machine system, they will be growing a wide variety of leafy green vegetables, Asian vegetables, Asian herbs… it’s going to be grown for the local market,” he said. “And we have two other deals pending in B.C. that we expect to close early in 2020 for a similar size facility.”
The company is also looking to expand the Pitt Meadows site on the same site or nearby.
Cubic Farm System is created by founders of Langley-based Bevo Farms’ Jack and Leo Benne when the pair were invited to solve growing challenges in Puerto Rico.
Bevo Farms operates 39 acres of Greenhouses in Langley and five acres in Pitt Meadows, according to their website. Last year, the company entered the cannabis industry when they signed a deal with medical marijuana producer Sun Pharm Investments Ltd.
Does Farming’s Greener Future Mean A Return To Tradition, or New Technology That Heralds ‘The End of Sustainable Agriculture As We Know It’?
With the UK committed to becoming carbon-neutral by 2050, agri-tech — technology applied to farming — is increasingly playing a crucial role in reconciling food production with sustainability
Carla Passino November 24, 2019
Indoor farming could pave the way for the UK to move towards net-zero, say experts Credit: Getty Images/iStockphoto
With the climate emergency and biodiversity crisis becoming increasingly pressing, we could see a shift away from conventional agriculture towards indoor food production, say some experts.
With the UK committed to becoming carbon-neutral by 2050, agri-tech — technology applied to farming — is increasingly playing a crucial role in reconciling food production with sustainability. But rapidly advancing innovation, together with the growing interest in the natural capital of land to combat climate change and halt the decline in biodiversity, could change agriculture as we know it, with vertical farming replacing, at least in part, field-grown crops.
Emily Norton, head of rural research at Savills, told a meeting of rural professionals this week that the future may not look anything like they’ve envisioned.
‘Pursuing carbon efficiency in agriculture is going to be transformational,’ she said at a meeting in Norwich.
‘Farmers have naturally been adopting a wait-and-see approach to accessing ELMS, but the climate debate could fast-track disruptive agricultural innovation and signal the end of sustainable agriculture as we recognize it here in Norfolk.’
That’s a stark warning: we think of sustainable farming as a return to traditional methods, and while this will be part of the solution there will be a role for technology such as indoor growing.
‘If agriculture as an industry accepts the net-zero challenge we need to be prepared to adapt accordingly… Indoor production is inevitable for a variety of crops’
‘The Committee on Climate Change Land Use Change report recommended the release of around half of all UK arable land to environmental adaptation,’ she explained.
‘If we’re to produce the same amount of food, this signals a major shift to innovations like controlled environment agriculture — removing food production from the soil. However controversial it might feel, if agriculture as an industry accepts the net-zero challenge we need to be prepared to adapt accordingly. Net-zero, climate change, and technological innovation all suggest that more indoor production is inevitable for a variety of crops.’
There is no doubt that, with the climate emergency at the forefront of people’s minds, there’s a growing demand for land to deliver environmental benefits, whether through planting trees, generating green energy or restoring habitats for fast-disappearing wildlife.
Likewise, the technology to deliver sustainable, indoor-farmed produce has quickly advanced. ‘For many years, we have grown produce in glasshouses and vertical farming is another step forward,’ says Charlie Yorke, technology specialist at rural insurers NFU Mutual, which earlier this month published a report on agri-tech.
‘Crops can essentially be grown anywhere as long as there is water and electricity’
The term, he continues, broadly covers ‘a variety of farming methods that stack multiple layers of crops on top of one another — fully utilizing 3D space.’ Farm designs can be entirely tailored to suit each crop type and space constraints, whether this means having racks of micro-green pallets in a shipping container, or tall spires of lettuces in a bespoke glasshouse. Because of this flexibility, ‘crops can essentially be grown anywhere as long as there is water and electricity.’
But the system’s key advantage, according to Mr. Yorke, is that farmers ‘can control the environment completely,’ targeting it to the specific requirements of the crops they are growing to optimize growth and yields. ‘They can control the humidity, the temperature, the light and they can really start to tailor these crops just by using light and different nutrients.’
Essentially, this means people can ‘consistently produce perfect crops all year round’. And because everything is closely controlled, ‘there is minimal use of pesticides and petrochemical fertilizers’. Vertical farms also ‘hardly use any water and a lot of what they use is recycled — it might be from rain, it might be filtered.’ Mr. Yorke mentions Intelligent Growth Solutions, a vertical farm system in Edinburgh, as an example of a company that recycles rainwater.
All this, together with the ability to make the best possible use of available space, results in ‘higher yields per area of land with much lower waste’.
‘Leafy greens work well but cereals and fruits are a challenge’
Nonetheless, the National Farmers’ Union, which earlier this year stated that agriculture should strive and become carbon neutral by 2040, ten years earlier than the government’s own deadline, believe that it’s yet early days for soil-less farming to supplant more traditional practices.‘Vertical farming is very much in the early stages of being researched to test how feasible it is for the future,’ said a spokesperson. ‘Currently, the high costs of implementation will limit its uptake and therefore its impact on the wider food supply chain.’
Instead, with British growers at the forefront of technological developments that improve quality, yield, environmental protection and energy use, according to the NFU, ‘it is crucial that retailers ensure they also invest and support the farmers that supply them with large, field-scale crops such as root vegetables, where vertical farming is not realistic.’
The NFU Mutual’s Mr. Yorke agrees it’s early days and that, ‘at present, the technology is not suited to all crops; leafy greens work well but cereals and fruits are a challenge.’
Overall, however, he believes the future of sustainable food production lies very much in integrating vertical farming into a wider mix that also includes other ground-breaking tools, such as digital soil mapping systems, robotic micro-sprayers or livestock sensors, that support land-based agriculture and help make it more productive and eco-friendly at the same time.
‘We don’t see vertical farming replacing traditional farming methods — rather we see it complementing farming and maximizing spaces which may have previously been seen as non-agricultural,’ he says, quoting, as an example, Growing Underground, a micro-green and salad producer operating 108 feet below the streets of Clapham, in London. ‘It is one of a number of innovations which are already demonstrating alternatives to conventional field-based production.’
INDIA: This MeitY-Backed Startup Has Built An Automated Farming Device To Grow Plants And Veggies Indoors
This MeitY-backed startup has built an automated farming device to grow plants and veggies indoors Delhi-based startup Agro2o is marrying hydroponics (soilless farming) and automation to bring a cool new gadget and a whole lot of good vibes to millennial households
This MeitY-backed startup has built an automated farming device to grow plants and veggies indoors Delhi-based startup Agro2o is marrying hydroponics (soilless farming) and automation to bring a cool new gadget and a whole lot of good vibes to millennial households.
Yash Vyas was working in a retail store in Dubai when he stumbled upon the concept of hydroponics in a newspaper.
Hydroponics (also known as ‘soilless farming’) is a practice where plants are grown indoors using mineral nutrient solutions in water solvents. It fascinated Yash instantly and also made him realize that Dubai’s harsh desert climate had made it difficult to grow farms.
“There was inefficiency of land and water, and almost no greenery either at home or outside. That formed my belief that hydroponics could be a fix. It is a clean and sustainable solution, unlike current farming techniques,” Yash tells YourStory. He then returned to India at the end of 2017 and started Agro2o in early 2018.
Yash Vyas, Founder & CEO, Agro2o (centre) with Ashish Goel, CTO, Agro2o (right)
Growing an indoor smart garden
The Delhi-based startup operates at the intersection of agritech and IoT. Agro2o has developed a proprietary smart garden using a fully automated indoor hydroponics system.
The plug-and-play solution allows anyone to grow fresh herbs, veggies, medicinal plants, and even flowers inside their homes. Because it is an IoT-enabled product, it requires little human attention on a daily basis. The Founder-CEO explains, “We call it automated hydroponics. Depending on the plant type, the system can intelligently judge and provide the level of light, water, and nutrients required, and create an ideal growing condition for the plant.
There are microcontrollers fitted into it. All you have to do is insert a nutrient cartridge depending on the plant you want to grow.” The smart garden is also enabled with a touchscreen and WiFi connectivity. It sends out alerts to users whenever the water has to be topped up. In the future, the system could even come with Alexa integrations, Yash shares.
Intersection of hydroponics and automation
He explains that this unique marriage between hydroponics and automation is a result of the startup’s two years of extensive R&D in plant science, for which it collaborated with the Delhi University’s Department of Plant Molecular Biology.
“We also acquired expertise in automation and AI to be able to perfect the technology and apply for design patents,” Yash reveals. While the product is yet to see a commercial launch (planned for early 2020), Agro2o showcased its technology at the Startup Expo held in September.
“It attracted a lot of interest from investors and general buyers,” claims the Founder. Agro2o has even opened pre-orders on its website.
It has also been incubated by Electropreneur Park, an initiative of the Ministry of Electronics and Information Technology (MeitY). The currently bootstrapped startup might even look to raise a seed round of Rs 1.5 crore to Rs 2 crore in 2020. Agro2o’s current device allows you to grow 10-12 crops at a time. These are categorized into Herbs, Greens, Veggies, and Ornamentals.
“Categories of crops cannot be mixed because the nutrients and conditions required for each are different,” Yash says. He adds that a 24-crop device is in the pipeline. The plan is to have three products for varying crop capacities in the price range of Rs 8,000 to Rs 18,000. “It is like any other consumer durable device that can last you for 4-5 years,” Yash adds. Also Read How DST-backed agritech incubator Indigram Labs is ushering in a new green revolution ‘
Key markets and growth plans
As could be expected, the demand for indoor hydroponics systems is much higher in the Gulf countries than in India.
The founder attributes this to severe climatic conditions and higher disposable incomes in these regions. Hence, to tap into this growing demand, Agro2o will launch in the Middle East along with its rollout in Delhi, Mumbai, Bengaluru, and Chennai. By 2025, the startup plans to sell two lakh units in India, and clock revenue of Rs 300 crore - Rs 350 crore. In the GCC countries, meanwhile, it hopes to sell about five lakh units in five years.
Yash observes, “I see two user profiles for our products. One is the value-conscious customer who wants something positive in their space.
The second is urban millennials who like cool gadgets and also love cooking with fresh veggies and herbs.” While smart homes is Agro2o’s immediate focus, the startup also has ambitions to venture into the smart farm segment. “Technology-enabled commercial soilless agriculture will soon become a reality,” says Yash. Also Read Stanford Seed startup Future Farms is out to solve India’s food crisis with clean, soil-less farming
Tech a facilitator for soilless agriculture
Hydroponics is a nascent sector in India. But globally, the market is expected to be worth $12.1 billion by 2025, with the Asia Pacific being the growth driver, according to Transparency Market Research.
Agro2o claims to be the first in Asia to launch a smart hydroponics product. “So, building awareness is both an opportunity and a challenge,” says the founder.
“Our nearest [undisclosed] competitor in the West is valued at only $120 million. This is a relatively new sector, but there is a large potential to be realized,” he explains. Does Agro2o want to be seen as an agritech or an IoT company? A bit of both perhaps. Or, as Yash puts it: an innovation company in the smart hydroponics sector. “Tech is just a facilitator to make soilless farming more accessible,” he signs off. (Edited by Evelyn Ratnakumar)
Read more at: https://yourstory.com/2019/12/meity-agritech-startup-hydroponics-smart-garden-automation-iot
Stacked Farm, Australia's First Fully Robotic End-to-End Vertical Farm
Australia may have one of the world's lowest population densities and plentiful farmland, but as farmers know all too well, water is and will continue to be a great challenge for the country's food supply
Written on the 3 December 2019 by Matt Ogg
Whether it be Bowery Farming backed by Google's parent company Alphabet, Square Roots which was founded by Elon Musk's brother Kimbal, or the innovative startup InFarm with leafy green-growing modules installed in supermarkets, vertical farming is a fertile space for development right now.
Australia may have one of the world's lowest population densities and plentiful farmland, but as farmers know all too well, water is and will continue to be a great challenge for the country's food supply.
Innovations abound in the sector, most notably Sundrop Farms in South Australia which has become a global leader in sustainable agriculture by powering its greenhouse with solar power and sourcing irrigation from desalinated seawater.
Now another Australian company Stacked Farm is set to join the ranks of innovators pioneering food solutions for the future.
After four years of research and development, the Gold Coast-based group's fully automated end-to-end vertical farm will soon be supplying leafy greens to national wholesalers including Sumo Salad, QSR, Dnata, Crown Resorts and Morco Fresh.
This means Stacked Farm's urban-grown produce from Burleigh Heads will be supplied to casinos, in-flight airline catering and retail outlets around the country, with plans for expansion with new facilities in 2020.
A spokesperson for the company says the facility is likely the first of its kind in the world to be fully automated.
"Other vertical farms might have a component of automation but one or two components are done by hand whether that's seeding, cutting or packing," she says.
Stacked Farm CEO Conrad Smith (pictured) says the farm is commercially viable, scalable and competitive, from seedling through to packaging with leading-edge technology.
"A good crop is not weather dependent and can be grown using up to 95 percent less water than conventional farming. It eliminates the use of pesticides and other climate-related hazardous processes as the growing is fully contained and controlled," says Smith.
"We also take sustainability very seriously and renewable power is already contributing up to 30 percent of what it takes to power the farm."
"Drought has wiped out so many primary producers in the country. Water is always going to be an issue in Australia it's our most valuable commodity. Vertical farming can help support our farmers in times of drought or crisis."
Efficient water usage is just one of the sustainable aspects that makes this operation appealing to food wholesalers in Australia. Produce growth is fast and shelf-life longer, with the entire process from seed to bag taking only 16-21 days.
"Produce life is increased due to the controlled growing environment, the technology and the fact it's packed within seconds of harvest and there's no need to wash it - which can be a big degrader of product quality," he says.
"It's great for growing in the city, as we can deliver within kilometres of the produce being grown, not like most farms who rely heavily on lengthy transport distances."
While the current facility can produce a couple of tons of produce a week equating to a 20-acre farm in output. Smith doesn't see this as working against traditional agriculture but rather as a means to complement it.
It's a game-changer for the cattle industry. We have identified that we can grow livestock feed en masse very quickly, and again using up to 95 percent less water. A 1000sqm vertical farm will have enough output to feed hundreds of cattle daily."
"The impact that this could have on farming communities that are suffering through the drought is enormous."
While the production is currently focused on leafy greens, herbs and livestock feed, Stacked Farm is also working with the CSIRO to develop additional products suited for indoor vertical farm growth.
Discussions are also underway with property owners in Victoria and Queensland to build farms suitable for produce growing, as well as a major farming operator in NSW to grow livestock feed.
Roto-Gro on track for Freshero JV and first facility
In other recent horticultural news, ASX-listed Roto-Gro International announced Friday that it had made significant progress in negotiations for a joint venture with Freshero, an aspiring organic produce grower with longstanding relationships across the wholesale, retail and foodservice space in Australia, Southeast Asia and the Middle East.
The company expects to execute the terms of an agreement by the end of 2019, in a move that will see the construction of a fully automated state-of-the-art facility Roto-Gro's patented and proprietary cultivation technology with standard agricultural seeding and harvesting equipment.
This technology includes rotational garden systems, fertigation units, the company's iGrow Software as well as material management systems.
Roto-Gro said Freshero CEO Tony Mahoney had strategically positioned Freshero to lead the development of organic urban vertical farming and distribution centres for fresh organic produce grown in proximity to large urban centres.
Despite the positive news, the RGI share price is currently less than half of what it was a year ago, most likely due to the collapse of cannabis stocks to which its growing technology is also closely aligned.
"Montreal Will Be The Home of The World's Largest Rooftop Greenhouse"
Lufa Farms has announced the construction of their fourth commercial rooftop greenhouse, soon to be completed in the borough of Saint-Laurent, Montreal
Lufa Farms Announces Expansion
Lufa Farms has announced the construction of their fourth commercial rooftop greenhouse, soon to be completed in the borough of Saint-Laurent, Montreal. The greenhouse will measure 163,800 square feet (about 3 football fields), making it the largest rooftop farm in the world. Construction began in September of this year and is expected to be finished by March 2020. This milestone also coincides with the tenth anniversary of Lufa Farms' founding in 2009.
This greenhouse repurposes an existing industrial rooftop to further Lufa's vision of growing food where people live and doing so sustainably. "With each greenhouse, we hold ourselves to an ever-higher standard for sustainable design. Our new farm will be the most energy-efficient to-date and integrate all our learnings from the last ten years to responsibly grow more vegetables year-round," says Lauren Rathmell, Co-Founder and Greenhouse Director.
Responsible agriculture meets innovative greenhouse technology
The greenhouse will feature double-paned glass and two sets of energy-saving screens for improved insulation, and its integration with the building below provides additional thermal benefit to both structures. The greenhouse will also capture rainwater to be used in the closed-loop irrigation system, as well as offset waste with an on-site composting system. At this fourth and largest site, Lufa Farms will be growing eggplants and more than ten unique tomato varieties without the use of synthetic crop protection.
Scaling urban agriculture to feed Montreal
Lufa Farms' most recent greenhouse will have a greater surface area than their three current greenhouses combined. "This rooftop greenhouse will double our growing capacity and allow us to feed 2% of Montreal with fresh, local vegetables. It's an unbelievable step forward for hyper-local, sustainable urban farming," says Mohamed Hage, Co-Founder, and CEO.
Saint-Laurent's Mayor, Alan DeSousa, further stated that "as a sustainable municipal territory, Saint-Laurent is proud to welcome the fourth greenhouse for Lufa Farms. Located in the heart of Saint-Laurent's biodiversity corridor, this greenhouse will facilitate residents' access to local, sustainably-grown products and further promote healthy habits. It will also make it possible to fight against heat islands in our district, where more than 70% of the surface area is devoted to industrial and commercial activities. And lastly, it confirms Saint-Laurent's position at the forefront of the new 4.0, particularly innovative green technologies."
Lufa Farms' mission is to create a better food system by growing food sustainably on city rooftops and partnering with hundreds of farmers and food makers, to provide customers with fresh, local, responsible food via their online Marketplace.
See one of Lufa Farms' other rooftop greenhouses in action in the video below.
Lufa Farms
(514) 669-3559
info@lufa.com
montreal.lufa.com
Publication date: Mon 25 Nov 2019
West Village Farms’ Indoor, Vertical Style A Growing Success
Inside the old Hewlett-Packard printer factory in east Vancouver, Ken Kaneko walks among towering rows of scaffolding that hold sprouted plants growing under LED lights
East Vancouver Company Sells Lettuce, Microgreens
To Chuck's, New Seasons, High-End Grocers
By Will Campbell, Columbian Assistant Metro Editor
November 10, 2019
Inside the old Hewlett-Packard printer factory in east Vancouver, Ken Kaneko walks among towering rows of scaffolding that hold sprouted plants growing under LED lights.
Kaneko is the co-owner and CEO of West Village Farms, a company harnessing a new type of agriculture called “vertical farming,” and it’s among the first in Clark County that’s growing food indoors using marijuana-industry methods.
Every factor of the farm can be controlled because the operation is indoors: the temperature, the amount of light and what touches the plants — never bugs or pesticides. Growing the plants in dirt trays stacked eight rows high allows the farm to conserve space.
West Village is about a year into selling its lettuce and microgreens at high-end grocers in Oregon and Washington, including New Seasons and Chuck’s Produce, where a plastic container retails for $4.99. The young company is in a state of rapid growth as it works its way into more stores on the West Coast.
In October, the farm began harvesting three times a week, up from twice, to get fresher products to customers. It’s also seeing double or triple revenue growth each month, Kaneko said.
“Compared to last year, we made 80 times more,” he said of the revenue. “But we’re still in the infant stages of the company.”
Kaneko expects to expand operations inside West Village Farm‘s rented space at 18110 S.E. 34th St. It’s using a little more than half its 25,000-square-foot space and plans to be at full capacity by the first quarter of 2020.
Unlike any outdoor farm, West Village also plans to expand operations upward by adding at least four more rows, which are bundled into a “pod” reaching nearly to the ceiling.
Kaneko touts both health and environmental benefits of consuming indoor-grown plants. Even outdoor-grown food labeled organic can sometimes be exposed to herbicides or pesticides, he said.
Another advantage is having a short farm-to-table time. Compared with plants harvested on outdoor farms and trucked long distances to the grocer, harvesting plants in Vancouver means putting them on shelves in one or two days.
“A lot of microgreens are shipped here from (California), but it takes two weeks before they hit the shelves,” he said. “With West Village Farms, the product arrives at grocery stores a day or two after it’s harvested. That’s how we provide quality to our customers.”
West Village Farm’s method uses 95 percent less water compared with an outdoor farm, Kaneko said. Part of that is due to the company’s patented irrigation system.
Technology company
Before Kaneko co-founded West Village, he worked for Apple in California and often traveled for work. He recalls a business trip to Japan, where he saw a vertical farm operating out of a defunct semiconductor factory.
“I thought it was an interesting idea,” he said. “It was a thing in Japan, especially after the Fukushima disaster, to secure the supply chains of food.”
The vertical farms also reminded Kaneko of his time at Stanford University studying computer hardware manufacturing. At Stanford, where Kaneko earned a degree in materials science and engineering, he learned about two of the legends to come out of the department: Craig Barrett, former CEO of Intel, and Ko Nishimura. Nishimura fell victim to American internment during World War II but eventually became CEO of Solectron, one of the world’s largest electronics manufacturing companies.
“I idolized both those people,” Kaneko said.
After Kaneko toured the vertical farm in Japan, he learned that Nishimura owned one in California called Ecopia, so he reached out to him via email.
The two met for lunch, and Kaneko began to materialize his interest in starting his own vertical farm in the Pacific Northwest, where Kaneko held his first job after college at Intel’s Hillsboro, Ore., complex.
Over the next year, Nishimura “probably was vetting me out,” Kaneko said. “Afterward, when we felt comfortable with each other, we decided to create this new company.”
Kaneko, Nishimura and some other investors eventually decided to name the company after Nishimura, which in Japanese translates to “West Village.”
US: Wisconsin - From Groceries to Growing: Ernessi Farms Aiming to Buy Market Fresh Site, Turn It into ‘Vertical Farm’
Ernessi Farms grows plants indoors hydroponically. According to its website, “In vertical farming our growing levels are stacked on top of each other in unused urban spaces. With our space saving design and proprietary technology, our vertical farm allows us to grow 80% more produce while using 90% less water.”
Bryan Ernst shows how the roots of the plant extend below the growing bed into the water tray during a February 2017 tour of Ernessi Farms in downtown Ripon.
Ian Stepleton, Editor
11/27/2019
Bryan Ernst speaks with the Ripon Common Council, including Ald. Doug Iverson, seen in the background.
Ripon’s downtown grocery store has been for sale for some time.
Soon, it may have a new owner — but the building will be used to grow food, not sell it.
Ernessi Farms, which first opened in the lower level of the Bluemke’s building downtown, is planning to purchase the Market Fresh building at 111 E. Fond du Lac St. There, it’s expected to greatly expand its ability to grow produce, increase its market share and hire new employees.
“With this expansion, this will make us the largest vertical farm in the state by far,” said Bryan Ernst, owner and founder of Ernessi Farms. “The only other vertical farms that are getting close to the size by the time we’re done would be found in cities like Chicago, New York, and Minneapolis.”
A closing date has not yet been set for the proposed sale.
“We’re a little further past the negotiation process right now; we’re finalizing some final details,” Ernst told the Commonwealth Tuesday, noting negotiations have been ongoing for a few months. “I’d like to be able to close by a little after the first of the year, but it’s looking like it should be relatively soon, assuming all things go well between the attorneys.”
Ernessi Farms grows plants indoors hydroponically. According to its website, “In vertical farming, our growing levels are stacked on top of each other in unused urban spaces. With our space-saving design and proprietary technology, our vertical farm allows us to grow 80% more produce while using 90% less water.”
Meanwhile, specifics about what will happen to Market Fresh, such as when it is expected to close, are unclear.
When called by the Commonwealth Tuesday, owner John Maczuzak declined to comment.
Read the full story in the Nov. 28, 2019 edition of the Ripon Commonwealth Press.
These Vertical Hydroponics Systems Are Growing Fresh Lettuce Anywhere With An Outlet
Tyink was an opera singer then and like the arias he performed onstage, the process of growing food captivated him. So Tyink started doing it, too — growing food in the middle of the city for friends and family. Any extra went to a food pantry
Sarah Hauer Milwaukee Journal Sentinel
November 29, 2019
Alex Tyink, a partner in Fork Farms, is shown looking down at a vertical hydroponics unit on Tuesday, November 26, 2019 at Butte des Morts Elementary School in Menasha, Wis. Fork Farms LLC has expanded a lot in the last year going from just selling in Wisconsin to 18 states. Three of these goods are harvested each week, producing about 60 pounds of fresh Romaine lettuce, which is used by the food service at Menasha High School. MARK HOFFMAN/MILWAUKEE JOURNAL SENTINEL
Mark Hoffman/Milwaukee Journal Sentinel
Years ago, Alex Tyink met a guy who was farming on a rooftop in New York City.
Tyink was an opera singer then and like the arias he performed onstage, the process of growing food captivated him. So Tyink started doing it, too — growing food in the middle of the city for friends and family. Any extra went to a food pantry.
Tyink helped start more rooftop gardens around New York. But he found the farms difficult to scale.
Five years, 30 prototypes and a move back to Wisconsin later, Tyink is the founder of Appleton-based Fork Farms LLC. With his product, dubbed a Flex Farm, food can be grown nearly anywhere with an outlet. The company produces a vertical hydroponics system for indoor agriculture, requiring lower energy and labor resources than other systems Tyink used.
The Flex Farm is catching on and growth is ramping up. Fork Farms is set to double its revenue this year, Tyink said. Fork Farms' systems are now in schools, restaurants, private clubs and in health care systems in nearly 20 states.
"Everyone is tired of paying for food to go bad," he said.
The Flex Farms are best for highly perishable foods like lettuces and tomatoes. One four-foot-tall system can grow more than 150 pounds of leafy greens a year, according to the company. The Flex Farm starts at $2,995.
Hydroponics is a method of growing plants that deliver nutrients through water, rather than soil. The Flex Farm system requires water and electricity to run, light is reflected throughout the system so the plants will grow.
"Sometimes people think about it as being unnatural and I don’t think about it that way," said Neil Mattson, associate professor of plant science at Cornell University. "Roots take up nitrogen in the same molecular form if it's in soil or a water solution and photosynthesis takes the same form if its sunlight or another beam."
Hydroponics takes up less space and uses less water than traditional agriculture. It can be done indoors, allowing for year-round food production. Highly perishable crops are among the most common to grow using hydroponics, Mattson said.
While Tyink's initial vision was to sell to schools, all sorts of would-be hydroponics farmers are buying the units. Fork Farms has installed its system in almost 300 locations, Tyink said. Some of those installations are one Flex Farm while others have a dozen or more.
The Marshfield Clinic's community health center purchased 17 farms to be placed in Rusk County to see if the increase in fresh food available affects public health, he said. Medinah Country Club outside Chicago is using Flex Farms to ensure fresh produce year-round.
The Oak Creek-Franklin Joint School District has four Flex Farms kept in the 9th Grade Center's cafeteria at Oak Creek High School. The farms supply fresh lettuces and herbs daily to around 2,000 students a day who eat lunch served by the district.
"I don't have a green thumb," said Jill Fehler who serves as the district's hydroponic farmer. " I had a fear of failure, but it's not hard to grow the lettuce and things. Cucumbers and strawberries are a little harder."
Fehler said she spends less than 15 minutes a day on the farm. The ph levels need to be checked and water added to the tanks, said Fehler, a food service director for Teher Inc., the school district's food management company.
"I also sing to them," she said. "They like Sinatra."
It takes about four weeks for the plant to grow from a seed to something to harvest. She's looking to start growing jalapenos next.
Six full-time employees comprise Fork Farms' core team. Nearly every component that goes into one of the units is produced within 50 miles of Fork Farms headquarters in Appleton. All of the plastics work, gasketing, and metal fabrication is done in Wisconsin.
It's the social mission that keeps the team going, Tyink said. Fork Farms developed a curriculum with FIRST Educational Resources LLC in Oshkosh for kindergarten through grade 12 students to accompany the hydroponics system, covering science, arts, health and other disciplines.
"We have to keep selling stuff to stay alive but that’s not really why we’re here," Tyink said.
Sarah Hauer can be reached at shauer@journalsentinel.com or on Instagram @HauerSarah and Twitter @SarahHauer. Subscribe to her weekly newsletter Be MKE at jsonline.com/bemke.
Watch: 5 Acres of Greens In 55m²? No Imports…Hyper-Local Food
Two re-purposed shipping containers, fitted with a ‘Farmony’ – 55m² in size, can produce 55,000 heads of lettuce per year or 408 trays of micro greens per week
November 20, 2019
Two re-purposed shipping containers, fitted with a ‘Farmony’ – 55m² in size, can produce 55,000 heads of lettuce per year or 408 trays of microgreens per week.
John Paul Prior sees these “5ac farms” as a way to compliment an existing farming enterprise.
His vision is to have as many Farmony models across the country as possible, complementing an existing beef enterprise for example and providing another income, all while replacing food imports into this country.
These salads, herbs and microgreens will be grown using hydroponic technology – no soil involved – and will be highly nutritious and free of pesticides.
That IT input into the farm provides a controlled environment.
Anyone who owns a Farmony solution can control it from anywhere in the world with a mobile device. The controlled environment means no pesticides are used and growth cycles are efficient.
Salads and microgreens are grown inside this controlled environment
“The growing season in Ireland is obviously from May to September. In a Farmony, a producer can grow all year round – 365 days a year,” John Paul explained.
This provides a whole new window of opportunity for Irish growers to have a continuous supply of fresh and local produce.
The business model allows for crops to be grown in small spaces. Restaurants could have their own source of salads and herbs all year round for example.
A restaurant’s beef supplier could provide the beef, the herbs to season it and the salad to accompany it.
“With microgreens your grow cycle is just six-to-seven days, so in terms of output one module can grow 24 trays of micro-greens per week and multiply that by 17 and you’re at 408 trays of micro-greens every week, so it’s an impressive output.”
Replacing Imports
At present, Ireland is heavily dependent on imports in this sector, which can be clearly seen on the supermarket shelves.
“We’re encouraging people to apply for the horticultural grant in 2020,” John Paul noted.
“The country imports about €300 million worth of produce, so we’re trying to basically offer a solution for producers to replace those imports.
You’re talking about hyper-local produce. These farms could be placed in urban centres or farmyards.
John Paul noted that while there are some farming sectors struggling at the minute, one of his company’s solutions could fit into a current farm business.
John Paul estimates a total workload of 25-30 hours/week and noted that there is a 40% grant available to set up the farm.
The system can also be used in an existing farm building. Mushroom houses, which are no longer in use for example, are ideal for these modules.
How Does It Work?
John Paul explained a small bit about how the farm works. The modules – which from the outside look like shelves – are basically flat-packs and can each be assembled in 45 minutes.
Water and nutrients flow through these modules feeding the plants. The gallery below shows the root structures of some of the plants and the water in the trays which is filled with artificial fertilisers.
“We use hydroponic technology so there’s a constant water flow throughout the module.
First of all the process is you seed sow. Then you transplant and the roots take the nutrients from the water solution that’s ebbing and flowing throughout the module.
Once the initial work of sowing and transplanting is carried out, the remainder of the work can be completed from a mobile device until harvest.
Lighting and temperature, as well as electrical conductivity and pH levels in the water, are all monitored and used to decide on the different “plant recipes”. The information is all sent to the master controller and sends nutrients to the plants accordingly.
Lights go on and off automatically, nutrients go in and out.
The irrigation system and lighting can all be changed from anywhere in the world. The amount of light hours can be changed for example, depending on the different plants.
Some plants like basil might require more white lights, while mustard or chard will have more blue lights.
As well as plant recipes, John Paul thinks he has the recipe to “supplement and compliment” current farming businesses, which he thinks can be made more sustainable and profitable by building a Farmony on site.