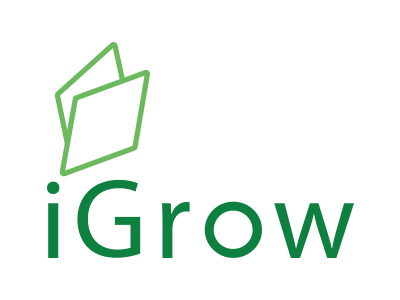
Welcome to iGrow News, Your Source for the World of Indoor Vertical Farming
Agriculture in Space Expert: Deep Horticultural Expertise is Needed for Vertical Farming to Succeed
Dr Gary Stutte is the founder of SyNRGE, a consultancy specializing in Space Agriculture and Controlled Environment Agriculture technology. Stutte, a horticulturalist and university professor, worked at NASA for several years on a program focused on growing crops in space, resulting in some of the first research around vertical farming and LED lighting.
Agriculture in Space Expert: Deep Horticultural Expertise is Needed for Vertical Farming to Succeed
OCTOBER 12, 2017 | LOUISA BURWOOD-TAYLOR
Dr Gary Stutte is the founder of SyNRGE, a consultancy specializing in Space Agriculture and Controlled Environment Agriculture technology. Stutte, a horticulturalist and university professor, worked at NASA for several years on a program focused on growing crops in space, resulting in some of the first research around vertical farming and LED lighting.
Stutte in the Kennedy Space Center growth chamber holding leafy greens grown in self-contained ‘pillows’ (2011)
Today Stutte is actively engaged in developing ground-based applications for space technology in biosciences, protected agriculture, and commercial horticulture. He has published over 150 scientific articles on the effects of growth conditions on crops grown in closed environments, fruit production, space biology, LED lighting systems, and biological life support systems for missions to the Moon and Mars.
We caught up with Stutte ahead of his speaking slot at YFood’s London Food Tech Week at the end of the month (30 October – 3 November), to find out more about his work and thoughts on the development of the indoor agriculture startup scene globally. (Get 20% off tickets with this code! AGFN20.)
How did you come to start working at NASA on indoor agriculture?
It was a bit of luck that allowed me to transition from teaching horticulture and fruit production at a University to working on closed system crop production for NASA. I had been teaching graduate courses in horticulture when I learned of a new program at NASA, which was starting to look growing plants on long-duration space missions. NASA had started the Breadboard project at Kennedy Space Center in Florida as part of the CELSS (Controlled Ecological Life Support System) program that had the objective of demonstrating the feasibility of using higher plants as a renewable life support system for long duration space missions. When the opportunity presented itself to become involved, it was an opportunity I could not pass up.
The Biomass Production Chamber (BPC) at the Kennedy Space Center was the centerpiece of the Breadboard Project in Florida. The BPC was a large (132 m3) closed chamber had been used as a high-altitude test chamber in the Mercury and Gemini programs. The chamber was fitted with lighting, a nutrient delivery system, and air handling systems and provided 20 meters of growing area on four levels. This was one of the first examples of a vertical farm. Incidentally, this design was driven by the constraints of the volume and diminutions of the chamber, not by a desire to design a vertical farm!
Between 1988 and 1996 the chamber operated on a nearly continuous basis — over 1200 days — without any significant failures, and during that time we grew multiple crops of wheat, soybean, rice, lettuce, potatoes and tomatoes in the chamber. Corn was too high for space!
Many other crops were also tested in controlled environment chambers using hydroponic production systems as potential candidate crops for space. Criteria for selection included a short stature, high productivity, short life cycle, nutritional content: criteria nearly identical to those required for successful indoor agriculture operations on Earth.
These tests measured all inputs and outputs including transpiration rates, photosynthetic rates, yield, harvest index and nutrient demand. In addition, the production of volatile organic compounds and ethylene were monitored, as well as the dynamics of the microbial communities associated with each crop.
What were some of the main successes of the program?
The CELSS project in general, and the Breadboard project, in particular, were extremely productive, resulting in over 600 publicly available publications on all aspects of engineering, biochemistry, microbiology, and horticulture associated with controlled environment production. Three area’s I think of great importance were demonstrating the feasibility of the continuous production of crops — not just leafy greens, but tubers like potatoes and staple crops like wheat and soy — hydroponically on a continuous basis, generating detailed data on the nutrient, water, and yield potential of those crops, and pushing the limits of their bioproductivity using electric lighting, nutrient management, and CO2 enrichment.
By the end of the program, we had achieved four-to-five times the world record for field yields of wheat, twice the world record field yields for potatoes in two-thirds of the time, and we exceeded predicted yields from hydroponic lettuce production by 20%.
The data developed by that program on productivity, water use, nutrient demand, and oxygen production are still used as baseline design values for long-duration space missions, including the bases on the Moon and Mars.
What were you using technology-wise?
Lighting was provided by 96 400-W high-pressure sodium lamps in the BPC and crops were grown in recirculating nutrient film hydroponics. The nutrient balance and pH of the solution were controlled, and a number of environmental sensors were installed in the chambers. The BPC itself was designed as a closed system, so the water released by the plants through transpiration was condensed, collected and reused. The atmospheric CO2 was controlled during the day, and all systems were continuously monitored and controlled. There was also a very active resource recovery program in which nutrients from the inedible leaves and stems of crops were recovered and then returned to the plants. By careful management of the nutrient solution and water recovery system, we demonstrated the continuous production of potatoes in the closed system for 418 days in a row; that’s over a year.
There seems to be a lot of development in the lighting space. How did your use of lighting evolve during the project?
The testing began with conventional fluorescent, high-pressure sodium, and metal halide lamps. It was recognized early on that these lighting systems were not suitable for space applications. This was primarily a safety consideration: they are hot to the touch, can explode in low pressure, and contain hazardous gases. Plus, they’re made of glass, that if shattered would mean shards of glass floating around in the vehicle. They are also bulky and have a relatively short lifespan meaning we’d need a lot of replacement bulbs which use up limited storage space and crew mission time.
NASA began funding research on LEDs in the late 1980s, which resulted in the first US patents for growing plants under LEDs in 1991. Subsequently, we used LEDs to examine the effects of light quality on the size, form, and shape of plants, as well as the potential to increase the nutritional content of crops. The use of LEDs is revolutionizing indoor agriculture, and much of the critical research enabling this transformation in horticultural lighting can be clearly tracked to NASA-funded research. I was lucky to be able to participate in some of that work at the Kennedy Space Center in Florida.
LEDs are now being used in all the US plant growth chambers currently on the International Space Station, and the use of LEDs to alter optimize spectral quality through a crops life cycle is becoming a reality.
Do you see any big challenges in how some vertical farms are being developed today?
Controlled environment agriculture faces many challenges, but it is increasing quickly in Asia as well as North America and Europe, and it’s starting to expand into Latin America as well. Vertical farms are driven by the demand for a consistent supply of locally grown, high-quality produce that’s free from pesticides and conserves resources. Much of the growth is enabled by the availability of LED lighting, which can be significantly more efficient electrically than traditional lighting systems, and allows the lamps to be placed close to the plants. However, the challenge remains that it is hard to offset the electrical cost of running LEDs; you often need to sell produce at a big premium, and some early pioneers in the industry have learned that lesson painfully. There are now models for particular crops and markets that I certainly think can succeed. Additional challenges include humidity and temperature control in the facility, as well as excluding pests and achieving sustainability. However, these are all surmountable challenges.
Do you see challenges changing depending on location?
Each site will have its own specific set of challenges, particularly regarding the availability and cost of water, power, and labor. I think the challenge of personnel with training in horticulture is under-appreciated. Vertical farming is an information-intensive enterprise and requires an understanding and appreciation of the fact that you’re growing living things. There is a misconception that using technology to collect data and drive the production of plants makes it relatively easy to automate the production cycle. In theory, it does, but in practice, the biological variables make implementation difficult. The challenge is understanding the environment that each plant species will require; each strain or variety of lettuce, basil, or medicinal plant is a little different.
This understanding of living plants will be the knowledge base that will make or break the next generation of vertical farming facilities; how well the founders pay attention to the selection of species and cultivars and to the horticulture required in the production of plants in an indoor factory.
Have you come across many indoor agriculture operations and startups without horticulture expertise?
Some. Most entrepreneurs are visionaries and have an ideal; they have some information on crops they are growing and some sense of how to grow plants in the field. But once a crop is moved into the control environment of indoor agriculture system, the plant responses can vary greatly depending upon spectral quality, atmospheric composition, and nutrient management. Technology enables indoor agriculture to push the limits of productivity; it becomes far more critical to understand the commodity you’re working with.
Do you think you need a better horticulture understanding growing indoors than outdoors?
In many ways, yes. While indoor agriculture gives you control of the environment, there is less room for error in the decisions that are made.
Why are most vertical farms today purely focused on leafy greens?
Most of the vertical farms focus on leafy greens due to economics. Leafy greens generally have a short production cycle (28-35 days), enabling multiple harvests (9-13 per year per meter squared of production area); short stature maximizing the number of levels that can be grown per m2; have relatively modest lighting density demand (15-17 Moles per m2 day), thus minimizing KW energy required per production cycle, and essentially all of the crop is harvested and sold, minimizing harvesting and processing costs.
It’s hard to do that for wheat; typically the edible grains of wheat makes up less than 20% of a wheat plant. That means you’ve invested all that energy, light and nutrients to grow the inedible roots, leaves, and stems, only to harvest off the seeds that must be processed before they can be sold. In other words, 80% of your investment in the crops not sellable! I anticipate we will start seeing more peppers as shorter season varieties emerge that could be competitive with greenhouse-grown peppers.
I am excited to see that a greater variety of leafy greens, as well as other short cycle vegetables and medically plants produced in indoor farms, are appearing on the market.
We’re not going to feed the world with leafy greens. Are you concerned that there’s not enough research being done on other crops?
I am concerned that there is not enough research being done on other crops. That’s not to say that research is not being done, but it needs to be expanded and conducted in a systematic way to support indoor agriculture. Before I left Kennedy Space Center, our labs had tested over 25 different crops in controlled environments as potential candidate crops for space. It’s imperative to do the research on lighting, nutrient and environmental conditions for new species in vertical farms. While I don’t think that vertical farms will be providing the primary caloric needs for the world, there is certainly potential for it to be a key source of fresh produce that provides critical nutrients and phytochemicals essential to health.
Personally, I’ve yet to see a good business model that would achieve some financial sustainability for a company placing small container type farms in food deserts. That doesn’t mean they don’t exist, but I haven’t seen them. What I can envision is locating a larger scale indoor farm in the economically disadvantaged food desert, in order to stimulate a broader economic impact that could create jobs and generate income for that area. The indoor agriculture model is adaptable to becoming an engine for economic growth and food security in both rural and urban food deserts.
My concern is that many things that indoor agriculture promises are going to be very difficult to deliver, such as the replacement of imported food, fresh food for everybody in large cities, turning food deserts into oases of fresh nutrient vegetables. It is going to be very difficult to do this with the capital and operating costs involved; ultimately you have a perishable product that’s a commodity, and it’s hard to recover the cost of vegetable production unless it is performed at scale.
Philips Lighting Supports MiniCrops’ First Vertical Farm With GreenPower LED Lighting
MiniCrops is the flagship initiative of Vertical Future, a technology start-up aiming to improve health in cities. The MiniCrops initiative provides households, farm shops, catering companies and restaurants with locally distributed boxes of fresh produce, focusing on nutrition, price and sustainability.
October 9, 2017
Philips Lighting Supports MiniCrops’ First Vertical Farm With GreenPower LED Lighting
Eindhoven, The Netherlands – Philips Lighting (Euronext Amsterdam ticker: LIGHT), the global leader in lighting, today announced that it supported MiniCrops, an agriculture technology initiative in the UK, using 200GreenPower LED production modules for its first vertical farm in the center of London. The MiniCrops farm has 65 m2 of production capacity, and triples its growing surface to 195 m2 by rotating crops every 8 hours.
MiniCrops is the flagship initiative of Vertical Future, a technology start-up aiming to improve health in cities. The MiniCrops initiative provides households, farm shops, catering companies and restaurants with locally distributed boxes of fresh produce, focusing on nutrition, price and sustainability. Household customers currently have the choice between boxes totaling either 150 or 300 grams, with each box containing between 6 and 9 different microgreen varieties, such as Rioja Radish, Red Kale, Sorrel, Sweet Genovese Basil and Broccoli. MiniCrops offers fair pricing and free delivery to customers across Greater London, and also recently invested in an electric vehicle fleet, further reducing food miles and environmental impact.
“We see a need for local fresh food with premium quality,” said Udo van Slooten, business leader for Philips Lighting’s horticultural lighting business. “On top of enhancing growth, we now have the ability to influence taste, flavor, nutritional value and shelf life by applying the right growth recipe. This enables our customers to meet the growing demand for fresh consistent quality produce year-round.”
Jamie Burrows, founder of Vertical Future and MiniCrops, realized that with over 70% of people expected to be living in cities by 2050, food sustainability and food security will become bigger and more relevant risk factors. He foresees a significant amount of volatility in food pricing, changes across the farming industry, and temperature variations in food exporting countries. “Consumers expect fresh, locally-sourced, sustainable food – all at the touch of a button. To meet future demands we need to use technology to our benefit, maximizing food production in our own market, close to consumers,” Burrows said, adding that he also thinks that projects like MiniCrops will create local jobs in a new industry.
MiniCrops closely collaborates with Philips Lighting’s horticultural LED lighting partner Cambridge HOK, which supported with the design and build process, resulting in a controlled, uniform, high-quality, maximum yield production facility – minutes from the center of London. MiniCrops is currently in discussions with various parties to develop its second site in London.
For further information, please contact:
Philips Lighting, The Netherlands
Daniela Damoiseaux, Global Marcom Manager Horticulture
Your New Indoor garden Could Be A Tree -- A Living Farming Tree, That Is
Your New Indoor garden Could Be A Tree -- A Living Farming Tree, That Is
Derek Markham (@derekmarkham)
Living / Green Food
October 3, 2017
This aeroponic indoor gardening system from the Italian startup Hexagro is modular, scalable, and automated.
In a bid to help make growing some of your own food at home as easy as possible, without needing prior experience or a green thumb, the latest urban gardening product employs LED lights, a suite of sensors, and an automated aeroponics system to keep maintenance (read: gardening) time to a minimum. There are a number of other indoor and countertop grow units on the market, all of which make similar claims, but what seems to set the Hexagro Living Farming Tree apart is its modular nature, which lends itself well to not only customization, but also to scaling up the size of this vertical gardening system.
The Living Farming Tree uses aeroponics, a soil-less growing method that uses a mist of water and nutrients to feed the plants' roots, which is claimed to use up to 95% less water than conventional soil-based agriculture, while also speeding up growth. The basic setup has four growing modules, each of which can hold 6 plant pots, sitting on a framework consisting of a system of tubes and what the company calls "global connectors" that look like they go together like Tinkertoys. An irrigation network is then threaded throughout the tubing, and LED lighting is connected to the upper section of the framework, which together supply light, water, and nutrients to the plants via an automated control system.
According to the company, as many as 13 growing modules can be connected as a single unit, for a total of 78 plants, making it possible to grow more produce in a small physical footprint than a traditional garden bed. This planting density would allow homes, offices, restaurants, and more to have easy access to some freshly grown foods without taking up a lot of space, and the ability to customize its structure to grow different sized plants could make it a more versatile machine than just lettuce and microgreens, which tend to be the staples of indoor gardening systems.
"The modularity of our system lets you produce any plant you want as long as it can be grown aeroponically. I’m sorry, this means you cannot plant a cherry tree there. However, you can go from micro-greens and sprouts up to aromatic herbs, salads, leafy greens and berries. If you want to produce higher plants, you will just need to configure the system in its 2D configuration, and you will immediately be able to produce plants such as tomatoes, cucumbers, medicinal herbs and many more!" - Hexagro
Hexagro Urban Farming has been working on the Living Farming Tree for several years, and was picked as one of the finalists in the 2015 Biomimicry Global Design Challenge, but now the team is looking to take its system to the public with a crowdfunding campaign. Instead of Kickstarter or Indiegogo, Hexagro is participating in the Katana Reward crowdfunding ecosystem, which is part of the EU-funded business accelerator Katana. Early backers of that campaign at the €549 level (~US$645) will receive a 4-module Living Farming Tree when they ship in June of 2018. More information is available at the Hexagro website.
Melbourne Startup Growing Produce Inside Restaurants
Melbourne Startup Growing Produce Inside Restaurants
September 28, 2017
Melbourne-based startup Farmwall is on a mission to transform cities into “food producing ecosystems” with its edible farms that will live and grow inside Melbourne cafes and restaurants.
Melbourne startup crowdfunds journey to grow produce inside restaurants
The crowdfunded venture will produce vertical farms, called Farmwalls, that are installed inside cafes and restaurants to provide a consistent supply of fresh herbs and microgreens at the fingertips of the chef.
Farmwalls bring “farm to plate in under a minute”.
By growing produce on site, Farmwalls aim to reduce packaging waste and high food miles, with a philosophy to bring “farm to plate in under a minute”.
A rendering of a Farmwall inside a restaurant.
The Farmwall team will make weekly visits to venues with the farms, bringing trays of germinated seeds from the company’s aquaponic farm in Alphington. The farm will act as a base for education, welcoming frequent visits from restaurateurs to test, trial and influence produce.
Meet 10 People Who Are Influencing Different Segments of The Produce Industry
In every industry, there are outstanding individuals who go above and beyond to improve the world around them. Produce is no different. From ag-tech to marketing to urban farming, these people are propelling the industry forward. In this month’s cover story, meet 10 of the leading People in Produce.
People In Produce
Meet 10 People Who Are Influencing Different Segments of The Produce Industry
October 3, 2017
In every industry, there are outstanding individuals who go above and beyond to improve the world around them. Produce is no different. From ag-tech to marketing to urban farming, these people are propelling the industry forward. In this month’s cover story, meet 10 of the leading People in Produce.
Do you know someone you think should be recognized in a future issue? Drop us a line at cmanning@gie.net. We’d love to know who you think is making a difference.
Specialty crops
Andrew Carter, CEO and co-founder, Smallhold
Photo courtesy of Andrew Carter
The authority on New York City mushroom production offers customers hyperlocal subscription-based farms.
graduate of the University of Vermont with a degree in ecological design and environmental sciences, Andrew Carter says that in college he learned a lot about mushroom production — a prime educational example of bioremediation. Following graduation, he worked in greenhouses, growing primarily hydroponic leafy greens and herbs, and consulted for vertical, container and warehouse farmers. A couple years ago, things came full-circle when he saw how he could launch the only operating mushroom farm in New York City.
Along with Adam DeMartino, Carter began Smallhold, which grows mushrooms in a container farm by Brooklyn’s East River and ships subscription-based “Minifarms” to restaurants and grocery stores throughout New York City. “I read a lot,” he says about the research he had to conduct before being able to corner the New York mushroom-growing market. “I went out to a few big farms and spoke with the operators there.”
Although Smallhold is still in its early stages, Carter hopes to expand its markets beyond the five boroughs and also potentially begin growing leafy greens and herbs. “In my opinion, as far as the ag market is concerned, you have to be competitive on freshness and price,” he says.
Smallhold’s roughly six-foot-tall Minifarms include rack row chambers that the company has developed in-house that are equipped with WiFi, LED lights, climate control and irrigation, Carter says. “It’s mostly automated, but when we want to update parameters or we want to change anything, we take care of that,” he says.
Carter calls Smallhold’s nine mushroom varieties gourmet and exotic, and they encompass everything from shiitakes to lion’s mane to oyster to pioppino — a delicacy in Italy. The company sells the mushrooms at a competitive price, and due to their proximity to the end consumer, they are very fresh.
“What we’re really figuring out is a way to bring the freshest produce humanly possible to our customers,” Carter says. “By growing it right there, there’s nothing better than that. We’re really working on ways of streamlining that process, making it affordable and making it easy for everyone to have their food growing right there.” — Patrick Williams
Vertical Farming
Photo courtesy of Henry Gordon-Smith
Henry Gordon-Smith,
Founder and managing director, Agritecture Consulting
Henry Gordon-Smith found his niche in agriculture by chasing new opportunities.
enry Gordon-Smith spent his childhood overseas. He was born in Hong Kong, and lived in Japan, Germany, the Czech Republic and Russia before attending university in Canada. While he was not directly engaged in agriculture while growing up, his international experiences primed him for his current career as the managing director of Agritecture Consulting, a company that helps to plan, design and implement urban agriculture projects around the world.
“I grew up in big cities, and big cities force you to think about how you’re using space,” Gordon-Smith says. “You have the chance to engage with so many different cultures and ways of thinking that it forces you to think in a more diverse approach, which I think is a big part of my philosophy.”
Gordon-Smith was first exposed to urban farming and its benefits while studying at a university in Vancouver, Canada. Involvement in local sustainable farming efforts and his own studies lead him to found a blog focused on vertical and urban farming issues called Agritecture (agritecture.com) while also volunteering at various urban ag operations to obtain hands-on- growing experience. Recently, Agritecture merged with Blue Planet Consulting — where Gordon-Smith served as managing director — to form Agritecture Consulting.
After graduation, he bought a one-way ticket to New York City to become an urban farmer. Despite not landing a job immediately, he stayed there, spent time studying at Columbia University under industry pioneer Dickson Despommier and ultimately found his current niche as a consultant. Now, five years after moving to New York, he wants to help people embark on their own journeys into urban agriculture as he continues his own.
“I want to be known as someone who's excited about this [industry], in it for the long-term and is ready to help people progress,” Gordon-Smith says. — Chris Manning
Technology
Dr. Nate Storey
Co-founder and chief science officer, Plenty
Photo courtesy of Plenty
Storey works to bring local, clean produce to communities around the world.
Dr. Nate Storey first made his mark on the produce industry by developing the ZipGrow Tower, a vertical farming system, at Bright AgroTech, a vertical farming equipment manufacturer he founded. Now, as a co-founder and the chief science officer at Plenty, a high-tech indoor farming company, he’s part of a team that’s trying to give everyone access to local food.
Storey started in agriculture by studying aquaculture-integrated hydroponics at the University of Wyoming, where he earned his bachelor’s degree, master’s degree and Ph.D. There, he was able to pursue research projects specific to his interests — projects that lead him to found Bright AgroTech and develop the ZipGrow Towers over a two-year period while he earned his Ph.D.
“[The university] supported my research,” Storey says. “This wasn’t research other universities were interested in or saw as valuable.”
Now, at Plenty, he’s continuing the work he did at Bright AgroTech — which was recently purchased by Plenty — and taking it further. Plenty’s goal is to bringclean, local food to communities across the world that’s grown in its vertical container farms. And, despite only being a young company, Plenty is already a success story.
According to Storey, Plenty is already competitive with field-grown pricing on different greens and herbs and should eventually be able to replace “a good portion” of what field growers currently produce. Publications such as The Wall Street Journal, Fast Company and Bloomberg say Plenty is a model business in a rapidly evolving industry.
This year, it also received a $200 million investment — the largest ever for an ag-tech company, according to TechCrunch — from a venture capital group that includes Amazon founder Jeff Bezos.
And while Storey understands that it’s not “free money,” he knows and appreciates that his work can make an impact beyond the checkbook.
“I love that I’m impacting the future of humanity,” he says. “I am not powerless to see my ideas come to life.” — Chris Manning
Association leadership
Lauren M. Scott
Photo courtesy of Lauren M. Scott
Chief marketing officer, Produce Marketing Association
A foodie from the beverage industry breaks into a leading produce and floral organization.
Self-proclaimed foodie and experienced marketer Lauren M. Scott appears to have found her dream job. A year ago, she was named chief marketing officer for the Produce Marketing Association (PMA). In her new role, she has the unique opportunity to help all businesses in the produce and floral industry prosper.
“I’ve always been a foodie and I’ve worked in the beverage business at Pepsi and Diageo most of my career,” says Scott. “When the PMA opportunity came my way, it gave me the chance to work with leaders in two of the most popular categories in culture today — produce and floral. I wanted to contribute my talent, energy and skills to help these industries grow and prosper worldwide.”
Scott says she’ll be working with her colleagues at PMA to help members by:
- Examining the landscape: consumer/industry research, including the role culture plays in this space.
- Offering actionable insights on strategic marketing: how it complements existing sales and marketing efforts and can be used as a discipline to grow a business.
- Providing resources companies can use to build their businesses, such as eat brighter! (pma.com/events/eat-brighter) and more.
“Our industry is operating in a highly competitive, dynamic food marketplace,” Scott says. “We have to understand that marketplace and then break through the clutter so that our member companies can perpetually thrive.”
In addition to helping established companies prosper, PMA is working to encourage young people to seek careers in the produce industry. It has set up a foundation called the Center for Growing Talent to “attract and retain the best talent for the industry.”
“PMA is committed to making the produce and floral industries the best place to work,” says Scott. “We have significant programs that target college students and we’ve had great success bringing them into member companies where they are contributing to growth.” — Neil Moran
Marketing
Chris Veillon
Photo courtesy of Chris Veillon
Chief marketing officer, Pure Flavor
In a new role with an expanding grower, this marketer conducts a top-down approach to branding.
Chris Veillon, who recently took the position as chief marketing officer for Pure Flavor, sees exciting times ahead for the company and offers some key insights into the future of the produce industry.
Founded in 2003 in Leamington, Ontario, Pure Flavor grows and markets a variety of greenhouse vegetables, including tomatoes, bell peppers, cucumbers, eggplant and living lettuce grown in the United States, Canada and Mexico. In his new role as CMO, Veillon hopes to take the brand to the next level, in part by taking on specific roles with promotions, advertising, content creation and digital marketing.
“The opportunity to grow with Pure Flavor, not only from a brand and product perspective, but professionally, was something I could not pass up,” Veillon says, citing an upcoming $105 million investment into a 75-acre greenhouse build in Georgia as just one growth opportunity for the brand.
Veillon got his start in marketing in the tourism industry. After 10 years in tourism, he was ready for a change. He says he was contacted “out of the blue” by a produce company that was looking to build a marketing department. Over the last 10 years, he was able to “create, strategize and build” a variety of brands that are developing into household names.
At Pure Flavor, Veillon says he gets to see the company from the 10,000-foot level. He sees opportunities to expand the company’s message, but hasn’t lost sight of the most important thing on consumers’ minds: great taste.
“Flavor drives repeat sales, hands down. Great packaging will attract, but what they bite into is what will determine their next move,” Veillon says. “In a space where there is an S-O-S, or ‘sea of sameness’ as I like to call it, there has to be a unique experience for you to retain that customer.”
As consumers become more savvy, they want to know where their fruits and vegetables come from, Veillon says. “Brands that resonate with consumers are the ones that have a unique value proposition,” he says. “It’s not about smoke and mirrors to get the sale, it is about authenticity to create a customer for life.” — Neil Moran
Sustainability
Photo courtesy of Nathan Kaufman
Nathan Kaufman
Director of living systems, The Perennial
This grower feeds flies to fish to fuel an environmentally friendly farm-to-table experience.
The husband-and-wife restaurateur duo of Karen Leibowitz and Anthony Myint started Mission Chinese Food and Commonwealth before founding The Perennial, a restaurant in San Francisco that sheds light on climate change and practices sustainability. Taking advantage of environmentally friendly food production and service methods such as carbon ranching and offering Kernza, a perennial grain, outdoor farmers and onsite employees do their part. But much of the work takes place across the San Francisco Bay with grower Nathan Kaufman.
As director of living systems, Kaufman runs The Perennial’s roughly 1,000-square-foot greenhouse and 2,000-square-foot outdoor production space in West Oakland. The greenhouse stands out for its highly nontraditional greenhouse crops — everything from turmeric to Australian finger lime to dwarf cardamom to papalo.
“In the year that we had for buildout, there was just so much give and take and discussion,” Kaufman says. “Initially, Anthony and Chris [Kiyuna], the executive chef, hit me with a wish list, and there would be stuff like jackfruit on there. I’m like, ‘Ok, guys. We’re not in Southeast Asia, and that’s going to take like 40 years for me to start getting fruit on it. That’s an 80-foot-tall tree, guys.’”
To boost sustainability efforts, Kaufman takes leftover food prep that the back of house staff has divided into two categories (the first being produce and the second being being meat, dairy and bread) and composts it. He uses worms to break down the produce and black soldier flies to break down the meat, dairy and bread. In turn, he feeds the fly larva to sturgeon and catfish that power aquaponic systems.
Kaufman is also executive director of The Perennial's nonprofit, the Perennial Farming Initiative, which educates others on sustainable efforts. But not every diner wants to hear about environmentalism while eating dinner. “Sometimes if you’re just getting a cocktail after work and you just want a great environment, hey, that’s totally fine by me,” he says. “For us, just by supporting us with your dollar, you’re voting with your buck. In that way, we can really engage with folks wherever they’re at.” — Patrick Williams
Leadership
Dr. Roberta Cook,
Photo courtesy of Dr. Roberta Cook
Director, Village Farms
A longtime academic economist now advises an industry-leading grower.
After 31 years working at University of California, Davis, Dr. Roberta Cook remains as passionate about the produce industry as when she was still a graduate student at Michigan State University.
“In my career at UC Davis, I was tasked with looking at all the key supply and demand trends affecting markets for fresh produce in California,” says Cook, who held the position of extension economist in the Department of Agriculture and Resource Economics. She is now on the board of directors at Village Farms and Ocean Mist Farms.
Her research and consultations have allowed her to gain key insights into the trends affecting the produce industry — information that should be valuable to both growers and retailers. Cook says consumers became very value-conscious during the recession and haven’t reverted to earlier buying practices, making competitive pricing even more important for retailers, which puts pressure on suppliers.
One of the biggest trends she sees affecting the industry, which will most likely continue for years to come is “channel blurring,” or the advent of more and more types of competing retail outlets for fresh produce, beyond the conventional supermarket of old.
“From Walmart Supercenters to club stores, dollar stores, convenience stores, drug stores, online sales and limited assortment stores, such as Aldi and Trader Joe’s, the proliferation of store formats is still expanding,” Cook says. — Neil Moran
Education
Stephen Ritz
Photo courtesy of Stephen Ritz
Founder, Green Bronx Machine
A teacher with a big heart incorporates indoor ag into the classroom.
A teacher with more than 30 years of experience, Stephen Ritz embraced project-based learning decades ago through environmental restoration and community gardening with over-age, under-credited students. Now, the founder of Green Bronx Machine, a native of New York City’s northernmost borough, grows produce in Tower Gardens with primary school age children in the National, Health, Wellness & Learning Center at Community School 55.
In his lessons, Ritz aligns food production with academic standards, and his students are excited to take part. “We took targeted students that had 40 percent attendance and moved them to 93 percent attendance and a 100 percent graduation rate,” Ritz says. “But beyond that — and realize that we are in the poorest congressional district in America, in the least healthy county in New York State, with the highest percentage of homeless and transitional children in New York City — we have record attendance at this school.”
A 2015 Global Teacher Prize Top Ten finalist, Ritz — who is recognizable by his bowties, cheese hat and noticeably trimmer frame than when he carried 300 pounds in the early days of Green Bronx Machine — has visited the White House and worked in his classroom with former White House chef William Yosses. Ritz has also met Pope Francis, former President Bill Clinton, Virgin Group founder Richard Branson and journalist Fareed Zakaria, among other influential public figures and celebrities. Author Michael Pollan featured Ritz in his book “In Defense of Food.” In May 2017, Ritz released his own book, “The Power of a Plant,” which details the path he took to champion for students to become more engaged in learning, make healthier diet decisions and contribute to society in a meaningful way.
When it comes to production output, Ritz and his students don’t skimp. They grow enough food indoors to send 100 bags of groceries home with students weekly. In addition to indoor production, they grow about 5,000 plants outdoors. Their 37 crops include gourmet lettuces, a variety of tomatoes, eggplants, peppers, pickles, collard greens, squash, cucumbers, celery, oregano, basil, nasturtiums, corn, string beans and cilantro. And the food doesn’t go to waste. In partnership with Memorial Sloan Kettering Hospital, Ritz and his students are growing about 5,000 pounds of produce for food-insecure, recovering cancer patients in the Bronx.
As a full-time volunteer, Ritz doesn’t expect payment for his work. This, he says, is to “step apart from” the system in order to fix it. “We need to go from a world that once loved people and used things and now kind of loves things and uses people — we’ve got to get back to our roots, literally,” he says. “Imagine if we refreshed our soil and our farmers the way we took care of our precious laptop screens. The world would be a better place. To me, this is about dignity and respect, growing something greater. Yes, I grow food, but really what we grow is hope and opportunity. I like to say I grow vegetables, but my vegetables grow students, schools and resilient communities and give everybody a chance to sit at the table.” — Patrick Williams
Research
Dr. Kevin Folta,
Professor and chairman, University of Florida’s IFAS Extension
Photo Courtesy of Dr. Kevin Folta
This professor pushes the development of horticultural lighting forward by pursuing unique research projects.
Dr. Kevin Folta grew up knowing that science, in some way, would be part of his career. When he started college at Northern Illinois University, he studied DNA and genetics. But as he interned at different companies as an undergrad, he developed a passion for agriculture and decided to get his graduate degree in biology, and then a Ph.D. in molecular biology, to apply to agriculture research.
In 2002, Folta moved to the University of Florida, where he currently serves as a professor and chairman of the horticultural sciences department. It was at UF where began working on the type of research he’s best known for — LED lighting, and how it can be used to improve plant growth
“That’s where it all came together,” he says.
Folta’s research explores the relationship between lights and plants and specifically how growers can use LED lighting to “talk” to plants. According to his research, a grower can use a specific light color — red, for example — to communicate specific instructions to a plant. This level of precision, in theory, would allow growers to get specific results from each plant in the greenhouse. That could even mean using a specific light color to draw out a specific flavor profile from a crop in the greenhouse.
“You’ve got something people need, something people want and something that makes money for the people who grow it and supply it,” he says.
In addition to his research, Folta also co-hosts podcast called “Talking Biotech” (talkingbiotechpodcast.com) and does it for the same reason he does his research: He loves it. “My one hobby is recording a podcast,” Folta, who records on Saturdays as early as 4 a.m., says. “So that’s why I do it.” — Chris Manning
To hear more from the People in Produce, be sure to check out The Hort Report podcast. Past guests include Dr. Gary Stutte, Dr. Kevin Folta and Dr. Jill Calabro. There is also coverage of industry events attended by the Produce Grower staff such as United Fresh and Indoor Ag-Con. You can find all of the podcasts at bit.ly/2fA8Umr and/or on iTunes at bit.ly/hortreportpodcast
Community Outreach
Photo courtesy of Mario Cambardella
Mario Cambardella
Director of urban agriculture, Atlanta
A career adjustment lead Cambardella towards his current role in shaping urban agriculture in Atlanta.
After graduating college, Mario Cambardella did what most people do after college: look for a job, secure a job and then work towards advancements. For Cambardella, who studied landscape design at the University of Georgia, that meant working at a company called Valley Crest as a designer and project manager for landscape developments in the Atlanta area.
But four years into his career, UGA created a new master’s program called “Environmental Planning and Design,” and the program’s dean recruited him personally for the program. While there, he completed that program, met his future wife, decided to stick around while she finished law school and completed a second master’s in landscape design while starting his own business, Urban Agriculture, which combined his design skills and new interest in sustainable city planning. After graduation, he turned that business into a full-time career for four years.
That business lead him to be hired by the city of Atlanta in 2015, where he now works for the city as the director of urban agriculture. There, he plays a key role in developing “Aglanta,” a digital food hub for Atlanta residents. That also includes the Aglanta Conference, which had 272 attendees in 2017, its first year, and the Aglanta Forum, an annual event where residents can learn about sustainability and healthy eating. (Editor's note: To learn more about the Aglanta Conference, listen to “Previewing Aglanta” here)
“Developing urban agriculture spaces within our city is, I think, a dream job,” Cambardella says. — Chris Manning
Ikea Has Debuted An Indoor Farm That Grows Greens Three Times Faster Than A Garden
In late 2016, Space10 launched a flat-pack spherical garden called the Growroom that grows plants, veggies, and herbs.
Ikea Has Debuted An Indoor Farm That Grows Greens Three Times Faster Than A Garden
- Leanna Garfield | October 2, 2017
Rory Gardiner
Ikea is known for its flat-pack kitchen tables, islands, and cabinets.
Now the home furnishings retailer is experimenting with products that allow people to harvest food at home.
Space10, Ikea's innovation lab, has designed a prototype of a mini-farm that can grow greens and herbs indoors.
Called Lokal, it uses a hydroponic farming system — allowing crops to grow on trays under LEDs in a climate-controlled box. Space10 debuted the device in September at the London Design Festival in Shoreditch.
How To Invest In Leafy-Green Indoor Agriculture
How To Invest In Leafy-Green Indoor Agriculture
Editor’s Note: B. David Vosburg is CFO and SVP Strategy of Crop One Holdings, an indoor farming technology company and producer of high-quality leafy greens in the Boston, MA area of the US under the brand FreshBox Farms. Vosburg is a serial entrepreneur and has an MBA from Yale University.
The lettuce industry in the US is worth just under $6 billion per year. If it follows the tomato industry, 50% of leafy greens will be grown indoors by 2030, a $3 billion opportunity. This transformation is inevitable with the ongoing trend of higher efficiency LEDs.
Indoor farming in cities and suburbs is giving new meaning to the term “local.” These operations are producing crops which had previously been grown only in certain geographies, because of the constraints of available land, water, and weather. This industry is now able to grow anything year-round, anywhere in the world.
In our growing units, we have measured a 99% reduction in water usage, and a 90%+ reduction in land use, compared to Salinas Valley lettuce farms, and since most indoor operations grow locally without any pesticides/herbicides/fungicides and 30 day+ shelf lives, indoor farming is a difficult proposition not to believe in.
And investors are starting to put some big bucks behind it. Indoor farming startups growing fruits and vegetables globally have raised $285 million since the start of 2017, with particularly large rounds for US-based vertical farms pushing the sector to its highest ever investment levels, according to AgFunder data.
The question is, who will win this market in the end?
No doubt you’ve seen several indoor agriculture companies that claim to be the best at growing leafy greens (lettuces, herbs, etc.) indoors. For any number of reasons, they claim to be better than their peers who are also vying for your funding dollars. But how do you tell the difference between them?
Here are seven simple metrics that will tell you if the company is worth your investment dollars.
1. Capital Density (CAPEX/plant site)
Most companies will tell you they grow more capital efficiently than everyone else, but you have to do the math. Calculate the number of plant sites they have per square foot, and the CAPEX required (all-inclusive) to build/buy that square foot of grow space.
Things to look for include companies that grow in vertical channels: the encasement and spacing take up so much space, they’re not able to achieve anything close to market-leading densities. Think cubic feet, not square feet.
If then it appears that that company is growing produce for a fraction of their competition’s Capex per farm, you will know they have a better ability to scale and turn over capital faster. For example, if a company grows for 25% of their competition’s CAPEX/plant site – the farm location — they can scale to four times the size with the same capital and will turn over that capital four times as fast.
2. Form Factor
There are now many players in the space building indoor farms in various formats: Pond greenhouses, Aquaponics, Warehouse growers, and Modular growers; each with its own inherent set of risks, particularly around contamination.
Pond greenhouses grow with sunlight — and at times some LED augmentation — in one, large single pond. They are the most susceptible to contamination as all plants share the same room. From a build-out perspective, it can take over 2.5 years to build one farm!
Aquaponics growers do control for contamination. However, plants are provided nutrients from fish feces, which can lead to contamination. The water temperature at which fish live is in the upper 70s Fahrenheit, several degrees above what is ideal for lettuce, so these growers will be limited in what they can grow and the yields they can achieve.
Warehouse growers can mass produce plants because they can grow them at high density to be some of the most efficient indoor farmers. Contamination can be a risk here as well; if a pest gets into a warehouse, an entire building of produce could be lost or recalled, costing the company tens or hundreds of thousands of dollars. There are several examples of hydroponic warehouse growers that have lost entire operations to a single pest or pathogen.
Modular growers come in many flavors, from divided warehouses to shipping containers. These growers can find a balance between controlling for infestation while growing efficiently. They can also match warehouse growers for density. In whatever shape or size they come, this appears to be the preferred growing approach for indoor farming – assuming that density inside the modular unit can be achieved. However, watch out for modular growers that sub-divide their farms into too many rooms as this will increase labor costs.
Be aware of form factors and decide which style best suits your investment needs.
3. Energy Efficiency (g/KWH)
Energy can be one of the most expensive components, if not the most expensive, of a completely indoor growing operation. This is a large part of the input costs of a labor efficient, completely indoor, growing operation. The common unit of measurement is how many grams of product a company can grow with one KWH of energy input.
What to watch for: many US companies have access to state-level agricultural energy pricing which can be as low as $.015 per KWH. Make sure the company is not ‘efficient’ because they simply have a low energy rate. We’ve all suffered through the end of subsidies in other industries, especially clean-tech!
Identify the number of grams that can be grown on the farm in a given month, then divide this by the number of KWH consumed per month. If the number is south of 40 or 50 – half the peak scientists have achieved in R&D labs– do not proceed unless there is a very clear technology roadmap showing how the company will achieve higher numbers soon.
4. Automation
Hiring is another expensive cost for indoor growers and will only increase in many urban places where indoor agriculture is applied. Automation is, therefore, going to become a critical aspect of reducing costs to increase gross margins. Some of the questions to ask:
1. How many dollars are spent in labor to grow one pound of lettuce?
2. How many hours does it take one person to seed, transplant, harvest, pack, and clean per unit of production?
3. Does the company use automation, and do they own that technology?
4. What is the company doing to find experienced/appropriate labor?
5. Plant Science
Farms grow living organisms. This is not an industry that produces widgets, no matter what anyone tells you. An experienced plant scientist is critical to any successful indoor farm. Identify this person and understand their background, knowledge, experience, and ability to control mold/fungus/pests as well as grow indoors in controlled environment and leverage plant stressors for yield.
The right person will understand every lever that can be pulled to increase yield and reduce costs: light spectrum, humidity, CO2, various micro-nutrients, water oxygenation, micro-pulsing, shadow-less lighting, sunsetting/sunrising, photoperiod and much more. This can contribute to a 50%-75% increase in yield over the competition, something competitors cannot finance their way out of.
Look for companies building competitive advantages around the non-commoditized aspects of growing – lighting, HVAC, and automation have plenty of very clever people around the world focused on improving efficiency in their own industries.
6. Commercial Approach
Brand is King. Those who have the consumer’s mindshare will be the ones to take home the value. Currently, grocery stores in the US are white-labeling many leafy green products so they can switch suppliers at will and reduce retail costs while maintaining margins. The consumer and the grocery store benefit; lettuce growers do not.
If the consumer is unaware of the brand, the company is not worth financing and will never be able to have the leverage to negotiate the price necessary for a venture return — and possibly not even a profitable business.
Ask a company about its consumer-facing products or plans.
7. Speed of Evolution
How quickly can a company change technologies? LEDs, farm management practices, controls and different types of automation are developing exponentially, industry-wide. Can you responsibly invest in a company that takes over two years to build out infrastructure?
The number of lumens/watt an LED produces is projected to quadruple in the next fifteen years, an annual compounded efficiency improvement rate of 10%. This means investing in a two-year project today will result in having lighting technology that is 21% less efficient than new entrants.
Keep track of technological advances and ask companies how they’re planning to stay on top.
IKEA’s Indoor Farm Is Trying To Alter How We Grow Food
IKEA’s Indoor Farm Is Trying To Alter How We Grow Food
The prototype designed by SPACE10 can grow greens three times faster than traditional methods
- 5 OCTOBER 2017
Multinational furniture manufacturer IKEA has introduced an indoor farm with the hopes of giving people the ability to grow their own food at home. The prototype, or Lokal as it’s called, was designed by SPACE10, IKEA’s lab for innovation.
Lokal is the most recent prototype to come from The Farm, a SPACE10 lab seeking to change how we view traditional farming while implementing new food production methods into our cities.
By experimenting with hydroponics, which is the growing of food without soil, SPACE10 says that it’s able to grow food up to three times faster and with 90% less water than traditional methods, according to a blog post with Medium. In addition to being soilless and faster than traditional methods, Lokal is also able to grow greens without any sunlight at all. Instead, the plants survive solely off of LED lighting and mineral nutrient rich water, simulating what Lokal refers to as “The perfect spring day, every day”.
SPACE10 points out that the current global food system is problematic for a few reasons. For starters, our current method of food production is contributing to the changing climate and is also wasteful of resources that we are already running low on, like fresh water. Furthermore, current methods lend themselves to wasting food. The hope is that the benefits of hydroponic farming courtesy of Lokal will go a long way in remedying some of these problems.
People should understand that the benefits of Lokal are not exclusive to the planet. According to its post with Medium, the food also “tastes good, is more nutritious, pesticide-free and fresh all year round”.
While this is all very interesting, simply creating a hydroponic growing apparatus is not even the end goal for Lokal. The Farm seeks to take things further by meshing the agrarian and tech worlds in the future. As it posted in Medium, the lab has hopes of “Introducing sensors and machine learning to the vertical stacks and connecting the data with Google Home — to enable people to ‘talk’ to plants, in effect, and hear how they’re doing, as well as to teach children and adults alike about sustainable food”.
It will be interesting to see just how much of a change Lokal will be able to make on the food growth industry’s ecological footprint, but for now it’s still a prototype.
Vertical Farming Looks To Go Mainstream
Vertical Farming Looks To Go Mainstream
Vertical farming can produce crops with a tiny fraction of the water and nutrients required in traditional outdoor production.
September 29, 2017By: Richard Jones | Email
The University of the District of Columbia is the nation’s only urban land-grant university, so it was a particularly appropriate setting for the Association of Vertical Farming (AVF) to host the AVF Summit 2017 on September 22. The summit was a mix of education, advocacy, and policy discussion about urban agriculture — vertical farming in particular — targeted at finding ways to broaden its adoption in cities around the country and around the world.
You’ve probably heard quite a bit in recent months about vertical farming — systems for growing food in stacked layers in completely controlled environments, applying inputs such as light, water, and fertilizer in precise amounts. While there’s some use of these systems in greenhouse settings, in many cases, urban farmers are repurposing abandoned buildings or even shipping containers. Match the availability of these facilities in most large urban areas with big cities’ limited access to fresh, local produce and you can see why interest — and investment — are growing.
Around 100 people attended the summit, a mix of researchers, suppliers, government employees, and potential growers. The overriding interest of most seemed to be in the potential of vertical farming not just as a business opportunity, but also as technology that can help solve some of the most pressing problems of getting nutritious food to people in areas where there’s limited availability. Techniques such as hydroponics or aeroponics can produce crops with a fraction of the water and nutrient resources required in traditional outdoor production.
“Vertical farming will be one pillar to help tackle these problems,” said Christine Zimmerman-Loessi, Chairwoman of AVF.
That said, the resources required to produce crops in completely enclosed environments where the grower supplies all the inputs — even the light — can be expensive. That’s certainly a limiting factor in adopting vertical systems to this point. A number of people at the conference suggested that as the technology advances and becomes more affordable, vertical farming will become a much more reasonable investment and business.
Sessions throughout the day covered issues from urban zoning and permitting to topics that are more familiar to experienced growers, such as the importance of having a good food safety program.
The concluding session, and possibly the most relevant for the longer-term adoption of urban agriculture and vertical farming, was a discussion of the upcoming farm bill negotiations.
Bob Van Heuvelen, CEO of VH Strategies, a legislative policy and strategic consulting firm, is working with the AVF for recognition of urban ag in the next farm bill through the Agricultural Innovation Alliance.
Van Heuvelen told the group there’s opportunity in a number of areas under the farm bill. For instance, vertical farming could:
- Win explicit recognition in the U.S. Code for promoting activities including urban agriculture, edible gardens, green walls, rooftop agriculture, and indoor vertical farms;
- Gain funding for data collection as part of a census of urban agriculture;
- Create an Office of Urban Agriculture;
- Earn competitive grants to support urban ag and get access to research funding for improving indoor production methods; and
- Fund market access and foreign market development programs.
Van Heuvelen was clear it would be a tough fight to win any of these points. The focus of the current administration in Washington, D.C., is on cutting the budget for farm bill programs, and placing more emphasis on rural agriculture than on urban ag. But, he said, the only way to have a chance to move things forward is to ask for it.
'All Sorts Of Possibilities': Science City Poised To Open In Former Sandwich School
'All Sorts Of Possibilities': Science City Poised To Open In Former Sandwich School
Science centre will have about 40,000 square feet of space and community rooms are also available
By Stacey Janzer, CBC News Posted: Oct 05, 2017 9:28 AM ET Last Updated: Oct 05, 2017 9:28 AM ET
Bill Baylis, the president of Canada South Science City says there are all sorts of possibilities going on in the Forester hub. (Stacey Janzer/CBC)
Stacey Janzer
Stacey Janzer was born and raised in Essex County. Self-described Canadian treasure. She currently works as a video journalist at CBC Windsor. Email her at Stacey.Janzer@cbc.ca.
The closure of J.L. Forster High School in 2014 was a blow to Sandwich, but the century-old building is beginning to blossom once again as a community hub after being purchased by the company that owns the Ambassador Bridge.
Canada South Science City is operating there in a limited capacity and should be fully up and running within a few months. The science centre lost access to its Marion Avenue location in 2015 and was grateful to find a new home on Felix Avenue in the empty school, which opened under another name in 1922.
It has already featured a small exhibit celebrating local black inventor Elijah McCoy, but more renovation work needs to be completed before all of its exhibits can be unpacked and showcased for public visits.
"There's a fair amount to done," said Bill Baylis, president of Canada South Science City. "It's a big, beautiful room with large garage doors. Needs a little fixing up."
Forster has been set up as a co-operative since being purchased by the Canadian Transit Company in 2016. The company wanted the sports fields to make room for a border plaza and buffer area but had no real use for the school building.
'All sorts of possibilities going on'
The science centre will have about 40,000 square feet of space and there are also community rooms available to other non-profit groups in the west end.
"There are all sorts of possibilities going on," said Baylis, who is working with architects to ensure the development of "a really nice science centre."
Bill Baylis, president of Canada South Science City, said Sandwich Towne needs a community centre to thrive. (Stacey Janzer/CBC)
Having more people and groups in the building opens up possibilities like a science store and a cafe, he added.
Baylis hopes to have the centre at least partially ready so he can invite school classes by the end of November. He said the fossil dig and the human bubble and some of the larger exhibits will return.
"We won't be able to to wait until everything is finished before we have to do some opening, because we'll need some income," he said
Baylis is hoping a distinguished guest will attract some attention. Local Grown Salads is a Toronto business that is setting up five of its patent-pending vertical farms in the centre.
"We've grown about 60 different vegetables," said Zale Tabakman, president of Local Grown Salads.
Zale Tabakman, president of Local Grown Salads says each unit is about 32 square feet and grows an equivalent of about an acres worth of food a year. (Stacey Janzer/CBC)
Each unit is about 32 square feet and grows an equivalent of about an acre worth of food a year. Each unit costs about $2,000 to run annually.
"This is patent pending technology that you're seeing here," said Tabakman.
The company has been working with Canada South Science City for about a year. They plan to have displays and classes showing how people can make these on a smaller scale and grow vegetables in their home year round.
"They can set it up in their basement, their kitchen, just using local things they can get in their hardware store," explained Tabakman.
Leafy greens, tomatoes and peppers can be grown using this technology. (Stacey Janzer/CBC)
Plans are in the works for a larger scale social enterprise project that could even create jobs for people tending the vertical farms and packaging the food.
"The production here will be used to fund the Forster building itself," said Tabakman.The food would be sold at markets at normal price, but Tabakman is looking to give back directly to the Sandwich community.
"Another sub section of the farm will be set up to support the people of Sandwich, for people who need a little bit of help with the pricing on the food and this will help."
Ikea Now Has Indoor Vertical Farm, Huge Potential For Solar Partnership
Ikea Now Has Indoor Vertical Farm, Huge Potential For Solar Partnership
Indoor Vertical Farming.chipmunk_1/Flickr
Wednesday, October 4, 2017 5:19 AM UTC
With the world’s climate constantly becoming hotter by the year, industries such as farming are going to experience massive problems such as drought and daylight heat that’s too much for plants to handle. That’s why products like Ikea’s indoor vertical farm are being hailed as great ideas because they can grow food three times faster and with 90 percent less water consumption. What’s more, there’s a huge opportunity to use solar power as a major component.
The new farming implement called Lokal came via Space10, the furniture company’s laboratory researching innovative products, Business Insider recently reported. It’s just a prototype, for now, but it shows great potential. It can grow herbs and greens indoors and is made up of stackable trays so it can go up as high as space would allow.
While the idea of an indoor farm is good, Ikea’s engineers are still working on improving the technology behind Lokal. For example, they want to integrate sensors into the stack so that users can monitor the state of their plants via smartphones.
Even if Ikea is not yet ready to put Lokal on retail, other companies are already looking at indoor vertical farming as a legitimate replacement to traditional tilling and sowing. There’s the indoor vertical farm in Philadelphia, for example, which is the first of its kind to be powered by solar energy.
The entity called Metropolis Farms has apparently constructed a 500KW solar setup on the roof of a building, Clean Technica reports. In the fourth floor of the building, the farm has crops that are reportedly worth 660 acres. More impressive is that they all feet in a space of only 100,000 square feet.
Paired with the news that Ikea could be offering consumer indoor vertical farm constructs in the future, there could be some major investment and startup opportunities in the works. At the very least, it provides hope that humanity might not starve, after all.
"Green Team" Growing Veggies and Fruits at Effingham, IL High School
"Green Team" Growing Veggies and Fruits at Effingham, IL High School
Published on September 29 2017
Written by Greg Sapp
(AVERY LUEKEN DISPLAYS ONE OF THE STRAWBERRY PLANTS BEING GROWN)
Effingham, IL High School's Biology Club, or "Green Team", is busy at work trying to grow a variety of plants as a food source. They are using hydroponics, meaning they are being grown in water, not in soil.
EHS got its first Plant Tower last school year. The program has expanded this year to several Unit 40 buildings..10 at EHS, two at the junior high building, and one each at Central and at South Side.
Three members of the Biology Club...Avery Lueken, Cecelia Castillo and Katie Vahling...were on hand to make a presentation on the project at this week's Effingham Unit 40 School Board meeting, along with EHS instructors Gena McDonald and Melissa Habing.
(FROM LEFT, EHS TEACHERS MELISSA HABING AND GENA McDONALD AND STUDENTS KATIE VAHLING, CECELIA CASTILLO AND AVERY LUEKEN)
Last year, the lettuce grown with the plant tower was sufficient to be used on the salad bar during the lunch hour at EHS. This year, the classes are looking at growing cilantro, basil, sage, banana peppers, bell peppers and hopefully strawberries.
(THE PLANT TOWER CONTAINING STRAWBERRY PLANTS ON DISPLAY AT THE UNIT 40 BOARD MEETING THIS WEEK)
As far as the towers, some assembly is required, but Habing said students watch a video and had one unit put together within 20 minutes.
$200M of Plenty(ful) Capital – The Next Wave of Vertical Farming
$200M of Plenty(ful) Capital – The Next Wave of Vertical Farming
Posted on October 5, 2017by Yoachim Haynes
The $200M raise by Plenty – a pre-revenue company who just one month prior, acquired somebody else’s technology (Bright Agrotech) – is not something you hear about every day. Jeff Bezos, Softbank and Alphabet may have deep pockets, but they are not philanthropic organizations. And for Bezos, this is a follow-on to a 2016 round for Plenty that provided $26M. So, the question is – what are the growth plans for this vertical farming business following the July 2017 investment?
Vertical farming is certainly an area with potential: resource efficient, near consumer demand, and better nutrition – all at competitive costs from current producers of high value leafy greens, herbs and other potential crops. Robotics, sensors, controlled environments, and lots of data combine to create a new level of food production that is a long way from farming. Venture capital has been active in the past several years supporting commercialization of early-stage companies. AeroFarms raised $34M in May 2017, $20M in Dec 2015, and $36M in Nov 2014 and is currently on its 10th (or more) iteration of production facilities. Innovation in controlled-environment farming business models is also sprouting. BrightFarms’ use of long term fixed price purchase agreements helped the company raise $30M in Sept 2016, even though their approach is slightly less controlled due to lighting coming primarily from the sun instead of LEDs. Freight Farms recently increased customer focus on college and commercial campuses as the target for their shipping container-sized farms, following a $7M raise in July 2017. These companies all have operating projects with customers.
Sounds easy, but others have not been doing as well. Past start-ups such as FarmedHere, PodPonics, Alterrus, and Local Gardens have gone bankrupt in attempting to address labor costs, lighting costs, rent, farm productivity, and revenue management. Adapting to the market, Freight Farms laid off some of their work force as part of the shift toward commercializing targeted customers and pulling back on R&D in new areas.
But back to Plenty. The plan, discussed in interviews with us, is all about scale with the underlying belief that customers are ready. No need for market validation – it’s all about infrastructure and scale. Plenty’s proprietary technology subdivides smaller growing environments for flexibility and rapid deployment. The goal is to provide a scalable solution that can be deployed anywhere in the world within a few weeks. The production facilities will be sited near cities with over 1 million people, and product mix will be tailored to the local market. Hence the need for access to substantial capital.
Plenty claims that an essential element of the company’s differentiation comes from its proprietary technology and process, which it acquired from Bright Agrotech. Bright Agrotech’s ZipGrow emerged from the University of Wyoming Entrepreneur Competition in 2011, moving to its own facility in 2015. The two companies have had a close relationship prior to the acquisition: Nate Storey, the founder of Bright Agrotech became Plenty’s full-time chief science officer earlier this year. Physically, one of the unique attributes of the technology are the 15-20-foot growing towers, an alternative approach to the trays often seen in other vertical growing approaches. Like most others in this space, the software, use of machine learning, lighting, nutrient balance, etc. are all proprietary. An area that is still being refined is sourcing of seeds: identifying those that are heirloom-based or clearly stand out in taste.
Monitoring of the continued growth of Plenty, as well as the overall market, should focus on deployment of production facilities –the speed and number of cities, ideally with purchase agreements for the produce. Market saturation of locally grown produce from controlled environments is not an immediate concern; however, first to market in cities might make local expansion easier and create barriers for new entrants. To that end, we might also expect more capital coming into other companies that have demonstrated operating facilities and the need to expand quickly. Probably not a land grab yet, but something to watch. Other areas to monitor should include direct-to-user targeted approaches like Freight Farms’ focus on campuses versus grocery-type markets. The bottom line is that there is ‘plenty’ of competition as the technology moves to commercial deployment, and successfully scaling is now the focus.
This entry was posted in Cleantech News. Bookmark the permalink.
‘Corporate Industrial Food Sucks’: Highlights from NYC AgTech Week 2017
‘Corporate Industrial Food Sucks’: Highlights from NYC AgTech Week 2017
September 29, 2017
Food system's busted. A bunch of people came out last week to discuss solutions — from hydroponic microgreens to the Farm Bill.
By Nina Sparling / CONTRIBUTOR
One of the venues for NYC Agtech Week 2017 | (Photo by Nina Sparling)
How can we grow more food in cities?
That was the seemingly simple question tackled by innovators, developers, investors and thought-leaders in New York last week. And the proposed answers were anything but simple.
Over the course of NYC Agtech Week, attendees from across the globe had the opportunity to attend workshops, learn about investment strategy and share in local food and spirits. There were hands-on experiences with everything from hyper-controlled, in-home grow setups to the sun and soil of area community gardens.
“Six and a half years ago I was just a kid with a blog who was passionate,” said Henry Gordon Smith, founder and managing director of Agritecture Consulting and organizer of the event. “I’m thrilled about the rate of acceleration. Our first year we had seven events; this year we had 31 events and we sold out. We’re focusing on not just talking about urban agriculture, but doing it.”
Conversations during the third-annual agtech week focused on a handful of fundamental questions: What is urban agriculture? Why is interest growing rapidly right now? How can I get involved? The event was hosted by the New York City Agriculture Technology Collective.
NYC Agtech Week 2017. (Photo by Nina Sparling)
Defining urban agriculture and articulating why it matters flowed through many of the presentations and conversations over the course of the week.
In a workshop during Agtech Demo Day, the group offered a handful of impressions about why urban agriculture is hot right now: Density in urban areas, an increased demand for local fresh food, concerns about climate change and, as Diane Hatz, the founder and executive director of Change Food put it, “The food system is broken, and corporate industrial food sucks.”
Among the guests were several young entrepreneurs looking turn ideas into realities. Most of the businesses in the agtech space are venture capital funded, and one panel at the Agritecture Consulting offices featured Andrew Shearer, the founder and CEO of Farmshelf, and Tinia Pina, the founder and CEO of Re-nuble. They addressed strategies for finding investors and building a business from the ground up. “Have a hit list and ask people that know people,” said Shearer. “It’s all networking — a lot of it is pounding the pavement. Fundraising is like dating.”
The tone was straightforward: be transparent, be reliable, and practice your pitch.
NYC Agtech Week 2017. (Photo by Nina Sparling)
The events vibrated with energy and momentum towards building a better food system.
Product designers and farm operators celebrated to how the industry has exploded of late, with Brooklyn leading the way in innovation. “Overall, it’s exciting to see how everything evolves: this event has exploded every year since the beginning,” said Marco Tidona from Heidelberg, Germany, who designed Aponix, a modular vertical farm that accommodates both soil-based and soil-less grow systems. “[Vertical farming] is further developed in New York City than in Europe,” Tidona said. “People are becoming aware — they would rather pay for a safe, clean product.”
I met Tidona at the Locavore Feast, organized by Our Name is Farm, a digital and experiential marketing company for the food system. The evening provided the opportunity for event-goers to network, but also to taste the food produced by New York’s high-tech farmers. A vibrant salad featured greens from Bowery Farms; Edenworks provided microgreens; Catskills Distillerybrought their spirits (including a white whiskey, which is code for moonshine); and the kombucha featured local basil.
Several people had come to the Locavore Feast to learn about the what urban and vertical farming means, looking to get involved in one way or another. “I would love to work in the industry,” said Bronwen Blaney, who won tickets to attend the Locavore Feast and jumped at the opportunity to network with industry leaders. “Be it urban farming or vertical farming, there are so many different ways to approach it. I’m just trying to figure out my way in. So far, it’s full of great people and good food.”
NYC Agtech Week 2017. (Photo by Nina Sparling)
Among the curious observers and invested developers were a handful of people focused on building vertical farming into political and legislative futures.
Mayoral candidate Mike Tolkin — whose campaign is designed around privatizing much of city government — made an appearance at Agtech Demo Day. “Vertical farming is a source of future economic growth that is important for sustainability,” he said in our conversation. “It’s a thrilling integration of private development with public support. We should elevate vertical farming to a new level; everyone eats, it’s crazy that we don’t talk more about this issue.”
And while New York may be a hotbed of sorts for vertical and indoor farming, its future may be much more widespread.
“Right now, vertical farming is a very local activity; to have it implemented on a broader scale we need a policy change,” said Christine Zimmermann, the chairwoman of the Association for Vertical Farming (AVF), who I met at the Locavore Feast. AVF hosted a conference in Washington, D.C., last week, where Zimmermann was looking forward to the opportunity to meet politicians and decision-makers.
“What the United States can do in the Farm Bill has a global significance; everyone will look at what’s going on here,” she said. “The U.S. can take the lead on this.”
Philips Lighting Signs Deal With Glinwell PLC For First 100% LED Installation in The UK to Grow High-Wire Cucumbers
October 3, 2017
Philips Lighting Signs Deal With Glinwell PLC For First 100% LED Installation in The UK to Grow High-Wire Cucumbers
Eindhoven, The Netherlands – Philips Lighting (Euronext: LIGHT), the world leader in lighting, today announced that Glinwell PLC, a leading UK producer of tomatoes, cucumbers, peppers and eggplants, is installing the UK’s first 100% LED grow light system for cultivating high-wire cucumbers. In recent years, high-wire growers have been rapidly adopting LEDs as supplemental lighting systems for their crops and have experienced higher yields, more consistent quality and the ability to move to continuous production. These results convinced Glinwell PLC that a 100% LED system was the best way for them to produce high-quality, British-grown cucumbers all year long to meet growing demand from UK retailers.
The only way is up
“For years, we have seen growers reap the benefits of using our LEDs in the cultivation of high-wire tomatoes. These range from higher yields and better quality fruit to more control over the growing climate and energy costs,” said Udo van Slooten, Business Leader Horticulture at Philips Lighting. “Now we see these benefits also being achieved by high-wire cucumber growers. We expect that the only way is up for LED in high-wire cultivation.”
Shaping the future
“We’re proud to be participating in this ‘first’ for the UK high-wire cucumber market,” said Joe Colletti, Director of Glinwell PLC. “During the winter months, we produce our cucumbers at our own overseas nurseries. We expect that this move will enable us to start growing cucumbers also on British soil, every month of the year. Not only does this greatly reduce our food miles, it allows us to meet the demands of some of Britain’s largest retailers, who want to offer consumers fresh, tasty products that are locally sourced.”
Sam Cannatella and Joe Colletti
Philips Horticulture Partner Cambridge HOK will be installing the 100% LED system which consists of two lines of Philips GreenPower LED interlighting and one line of Philips GreenPower LED toplighting. The project will be undertaken jointly by Eduard Udyanskyy, Growing Manager at Glinwell PLC, and Erik Stappers, Plant Specialist at Philips Lighting.
For further information, please contact:
Philips Lighting, The Netherlands
Daniela Damoiseaux, Global Marcom Manager Horticulture
Tel: +31 6 31 65 29 69
E-mail: daniela.damoiseaux@philips.com
www.philips.com/horti
About Philips Lighting
Philips Lighting (Euronext: LIGHT), the world leader in lighting products, systems and services, delivers innovations that unlock business value, providing rich user experiences that help improve lives. Serving professional and consumer markets, we lead the industry in leveraging the Internet of Things to transform homes, buildings and urban spaces. With 2016 sales of EUR 7.1 billion, we have approximately 34,000 employees in over 70 countries. News from Philips Lighting is located at the Newsroom, Twitter and LinkedIn. Information for investors can be found on the Investor Relations page.
About Glinwell PLC
Glinwell PLC is a second-generation family run business, produce and marketing company growing cucumber, tomato, pepper and eggplants. The company is accredited to BRC, Soil Association and the Farm Assurance Fresh Produce Scheme. Because Glinwell PLC is involved at board level in the Pepper Technology Group, Cucumber Association and Tomato Growers Association – as well as being involved in the Lea Valley Growers Association and Soil Association Working Party – it is part of the voice of the industry. Glinwell PLC is helping to shape the future. Its growing methods keep it as natural as possible from the purchase of high grade seeds, the attention to detail with the growing of the plants and the care taken in harvesting the produce. More information can be found on its website: www.glinwellplc.com
About CambridgeHOK
CambridgeHOK is the UK’s leading Glasshouse, Heating and LED lighting specialist (certified Philips Horticulture LED Partner) with expertise managed by its own inhouse design engineers. It specialises in bespoke turnkey design and installation, adapting every solution to the client’s needs using the very latest in technology. More information can be found on their website: www.cambridgehok.co.uk
Vertical Farming's Best Kept Secret?
A visit to PlantLab:
Vertical Farming's Best Kept Secret?
Stacked layers with leafy greens in fully controlled units; some call it the future of farming. While opinions are divided if all that fancy lettuce will indeed solve world hunger, at PlantLab they are convinced that controlled environment agriculture can introduce groundshaking revolutions to our food system. But how viable is this relatively new industry? And what does a patent have to do with it? Highest time to figure out and pay a visit to PlantLab ourselves.
PlantLab’s indoor growing activities cover a range of various horticultural and agricultural sectors. Partnerships and joint ventures link PlantLab, still fully privately owned, to top international players in agribusiness, breeding, large scale horticultural production and propagating as well as industry leaders in food ingredients, flavours, fragrances and cosmetics.
“Controlled indoor growing changes the way how we approach our food system and enables providing consumers fresh food with distinct taste and nutrient profiles, produced in a complete circular and sustainable system”, according to PlantLab’s Marcel Kers when he welcomed us at their headquarters in ‘s-Hertogenbosch.
“By tweaking the right parameters, crops can be made nutrient dense and become a medicine for example”, adds colleague Ard Reijtenbagh. “We partner with companies from various industries to explore such opportunities and jointly develop and run integrated production solutions with a financially sound business case and a concrete go-to-market strategy. This varies from consumer ready products such as lettuces and herbs to young planting material for growers; and also various crops for specific natural active ingredients for the food industry as well as improved breeding processes.”
HortiDaily was invited to take a look inside their 20,000 square meters facility to witness the PlantLab approach first hand. Here, more than 5,000 square meters of advanced indoor growing facility is currently utilized to develop 'Plant Paradise®’ recipes. The remainder area is used for technology development, production of various crops and there is still space for further expansion.
It is obvious we have entered a facility where it is about more than only R&D and growing leafy greens and were amazed to see so many dedicated indoor vertical farming technologies and production. Without any doubt PlantLab operates one of the largest, if not the largest, most advanced commercial R&D vertical farming facility that we have ever visited.
The PlantLab philosophy is to only introduce its solution with a clear proof of concept from a technology, production and marketing point of view with a sound financial business case. PlantLab says that they are currently the only organization in its sector to guarantee quality and production.
To achieve this, the company works in multi-disciplinary teams with disciplines such as technology, plant science, production, business analysts, supply chain and market experts. This approach in combination with the expertise of its external partners leads to complete new ways of working and products.
The reason that PlantLab and its successes have remained unknown to the broader public? The numerous partnerships and non-disclosure agreements that the company is involved with. "We are working on so many great things and it is often a pity that we can not share it with the outside world. However, we get a lot of satisfaction from our work in the partnerships. To be part of this evolution is very rewarding." Kers said.
Accompanied by large investments, the entire PlantLab team performed dedicated research and development to create what they call 'Plant Paradise’.
"Taking into account the smallest details, we discovered that a fully closed environment enabled maximization of the plant performance by influencing more factors than just temperature and humidity. We need to control more than 80 variables in most cases. It creates new opportunities as a whole, and not just in terms of higher yields or quality."
The method is described by Kers as modifying the complete environment where the plant is growing in. From changing the light spectra to influencing the root zone temperature and humidity at canopy level. "The combination of influencing these parameters in a controlled environment to enhance or influence crop growth is what is covered by our patent”.
And that patent is where PlantLab made headlines with, when the European Patent Office denied the opposition against the PlantLab patent on their method of controlled environment agriculture, which means it remains valid. "Unfortunately the patent has become, for some people, a too loaded topic. We can totally understand that it caused a stir, just like with any patent related to food production. The fact however is that we are open to work together with any company that likes to take advantage of our knowledge and methods", Marcel Kers said. “We do not want this to stop different initiatives around controlled environment growing in the world, on the contrary. All parties can contact us for a licence agreement.” Marcel Kers added.
Kers was eager to explain the background behind their technology and why they filed a patent on it in a period when, according to PlantLab, nobody else was investigating the same opportunities. “We just wanted to protect our investments and hard work that we started in 2005. We have been actively investigating controlled indoor growing methods for more than a decade. Everyone was still convinced that it was not even possible. Nonetheless, we continued our research on the possibilities of fully closed cultivation with the use of new technology such as LEDs. We believed in it more than anyone else at that time.
We are not here to argue or bully the vertical farming and controlled environment agriculture industry, we are here to take the whole industry to the next level".
And that next level is definitely approached at the company's headquarters in ’s-Hertogenbosch. The group invested millions to transform 20,000 square meters of vacant factory and warehouse space into an indoor production unit in combination with an indoor growing research & development centre, which aesthetics could have passed for the biggest Apple store on earth.
Apple or ASML?
"That’s quit the comparison! We have many elements in our business model like ASML in which we enable our partnerships with our solutions, but we have grown over the past years towards a model with a ready go-to-market strategy with consumer products, such as fresh vegetables.” Reijtenbagh commented.
He said that PlantLab always had the vision to develop stand alone closed growing systems that could be applied anywhere in the world and contribute to the challenges of feeding a growing world population. From research, development, production to a consumer ready product; companies that partner with them are offered a solid solution that does what it needs to do; growing a crop with a consistent amount of maximized beneficial properties. "It is our aim to develop indoor cultivation to its fullest and create new opportunities and new profitable business models. Not just in terms of growing leafy greens or other vegetables, but moreover in a broader scope. Think about nutraceuticals, pharmaceuticals, flavours, fragrances, cosmetics and aromas. By innovating in indoor farming we can enhance the development of new production technologies to create unique products that contribute to the environment, health and welfare. Basically, we have grown from a company providing the “next generation of growing” to a situation where it is about “the next generation of food”! When developing new technologies it is so important to interact with your market and the consumer”, according to Reijtenbagh.
Reaching out to consumers?
“Yes, growing crops without daylight in a fully closed environment is no longer a hip trend, but here to stay. We are so convinced of the beneficial properties of the product we produce and that it is the most sustainable way of production; but how to make the consumer familiar and trusted with the product and how it is being produced? This is always a challenge with new technologies.” Reijtenbagh said. “Just showing the purple light in the growing rooms will not work. Consumer panels help us, to test our products. And we also measure the content of our products. In the coming months we will be starting a large-scale program in which we reach out to consumers. We will not do this on our own, but in combination with other companies, universities and experts. We expect a lot of this. In a couple of months we hope to tell you more”.
PlantLab and its partners continue their investments. The group is currently expanding its facilities in ‘s-Hertogenbosch as well as implementing projects on a few spots in the world. Earlier, it opened an office in California to develop and support the North American market. "We have room to double our floor space in ‘s-Hertogenbosch. This illustrates the potential behind our approach", according to Kers. "We did not jump on the indoor farming market too hastily, but wanted to go to market with a proven integrated solution and substantiated decisions. That approach, which started with the first small scale trials in 2005 is still standing. Our playground might be larger, but we still start every experiment with a single plant before we increase scale. This resulted in a successful formula for our partnerships. Before our partnerships invest in a system, it is guaranteed that it works, meets the expectations and that it is commercially and financially feasible. This is exactly where we try to make the difference".
World’s First Solar Powered Indoor Vertical Farm Comes To Philadelphia
World’s First Solar Powered Indoor Vertical Farm Comes To Philadelphia
October 3rd, 2017 by Steve Hanley
It’s always sunny in Philadelphia, according to the title of a popular television show. If so, it’s the perfect place for the world’s first solar powered indoor vertical farm.
Metropolis Farms has constructed a 500 kilowatt solar array made up of 2003 solar panels on the roof of a building in The City of Brotherly Love. On the fourth floor, it is constructing a vertical farm that will be powered entirely by electricity coming from the roof. It plans to grow the equivalent of 660 outdoor acres worth of crops in less than 100,000 sq feet. “The panels are already installed and turned on, now we’re building out the farm. The first crops will be planted in November,” the company says.
Before Metropolis Farms took over the space, the only things growing on the fourth floor were pigeons. But soon, crops of fresh tomatoes, strawberries, lettuce, herbs, and broccoli will flourish there for the benefit of the citizens of Philadelphia and environs. “We feel this inherently demonstrates the wonder of this new industry we’re helping create, the industry of indoor farming.”
The company goes on to say,
“To this point, the city of Philadelphia has only ~8 acres of urban farming, mainly because there’s no available land for growing crops traditionally. By bringing the growing process indoors, in line with our mission of social responsibility, we are revitalizing abandoned spaces and are using them for local food production. We are empowering a new generation of farmers to grow food for cities, in cities.
“This technology democratizes the ability to grow local food in any community, regardless of location or climate. We’re doing this because local food is just better. Local food is more nutritious than food that’s packed in a truck and travels for weeks, it tastes better, and growing food in the communities where it’s eaten helps stimulate the local economy.”
Detractors of indoor farming point out the high cost of powering all the lights and circulation pumps needed, but Metropolis Farms thinks its rooftop solar array will answer the critics.
“The truth is, like any technology, indoor farming is constantly improving upon itself. We have gained efficiencies through innovative lighting (not LEDs), BTU management systems, and other means to dramatically reduce the amount of energy our farms are using.
“And we are on the cusp of a breakthrough in a technology that will reduce our energy usage even further. We hope to demonstrate this new technological advancement at this year’s Indoor Ag-Con, hosted for the first time in Philadelphia. We are pushing the envelope by attempting to build a zero-carbon farm. Through water recapture techniques, renewable energy production, advanced energy systems, and most importantly by farming locally, we are on the right track.”
Another benefit of vertical gardening is a dramatic decrease in the amount of pesticidesneeded to grow fresh food. Not only will the crops not be covered in chemicals, neither will the environment surrounding the vertical garden. That’s a huge benefit that should not be discounted. “We hope others will follow our lead and start building farms of the future, so communities everywhere can benefit from having a quality local food source that grows crops responsibly,” say the leaders of Metropolis Farms.
Schurz Food Science Lab | Episode 01
Schurz Food Science Lab | Episode 01
September 28, 2017
Nick Greens was a co-founder of the first Food Science Lab at Schurz High School. Recently, Nick was invited back to help integrate some donated grow systems and help kick off "Year Three" of the program. Here is an inside look at Nick and the team preparing for Fall semester 2017.
Data Analysis, Tech And Fish Waste Make Urban Farms Viable
Data Analysis, Tech And Fish Waste Make Urban Farms Viable
Brexit boosts business in ex-bomb shelter that controls plants’ every growth variable
Nothing lost: Kate Hofman, chief executive of GrowUp, surrounded by produce nurtured by fish waste
09-25-17 | by Jennifer Thompson
The rows of plants under pinkish lights, tended inside a Dutch warehouse by white-coated workers, bring to mind more a sci-fi film set than a farm. Indeed, the start-up behind the scheme, PlantLab, prefers to describe itself as a “development company” rather than an agricultural business.
Urban farming itself is not new — people have always grown produce or raised livestock in towns and cities, from necessity, as a hobby or to reduce food miles. Now, however, city agriculturalists are harnessing technologies such as light-emitting diode (LED) bulbs, 3D printers and data analysis to speed up growth and create farms virtually anywhere.
In London, in a former bomb shelter underneath Clapham Common, for example, Growing Underground cultivates leafy greens, such as watercress, rocket and coriander.
Built to shelter up to 8,000 people during the second world war, its tunnels now house rows of plants. “It was all [done using] standard agricultural equipment, save for LEDs,” says Steve Dring, co-founder of Growing Underground. LEDs provide the right level of light and heat in an energy efficient manner.
Affordability has proved a big factor for spurring innovation. PlantLab grew out of an older traditional horticultural company, growing greens and soft fruits under glass and greenhouses but was officially launched in 2010 as LED lighting became more affordable. Growing Underground also works on a fast turnround, with a series of ‘mini harvests’.
Tanks of tilapia fish at GrowUp's aquaponics project provide nutrients for plants © Charlie Bibby/FT
Seeds spend three days in a dark, warm and humid environment to fool them into thinking they are surrounded by soil. They then grow for six to 12 days under the light before being harvested for the capital’s restaurants and more recently the London food stores of Marks and Spencer.
A few miles from Clapham, Kate Hofman and her team at GrowUp are also revamping existing equipment and concepts for an ambitious aquaponics project.
Having taken a sabbatical from her career as a management consultant to undertake a masters degree in environmental technology and business, Ms Hofman and co-founder Tom Webster wanted to create an economically viable and environmentally friendly food production system.
Tilapia fish at GrowUp's aquaponics project are reared with a smart monitoring system © Charlie Bibby/FT
The concept of aquaponics, which combines raising fish with growing plants for a mutually beneficial exchange of nutrients, has been around for thousands of years. Technology, however, is bringing a new precision to the process.
GrowUp, established in 2013, operates from a warehouse in east London housing 12 tanks each holding 3,000 litres of water and up to 400 tilapia fish. The waste of the fish nurtures plants growing above — including kale, watercress, and basil — while the plants filter the water, and a smart monitoring system gives complete control over elements such as humidity and temperature.
The impetus from the start was to create something that could succeed as a business.
“We’ve focused on how do you take that technology and make it commercial,” says Ms Hofman. “We were both interested in how hydroponics could be used to grow food commercially. The reality is most of our food production across the world happens on an industrial scale.” GrowUp is currently looking for a location for a second farm, expected to have around ten times the capacity of the original site. This would allow them to begin supplying supermarkets. Ms Hofman says the prospect of Brexit following the UK’s vote last year to leave the EU, has increased interest in the concept of localising food production and technology-driven farming projects have made some inroads into supply chains.
“It was quite obvious there were mathematical patterns in plant growth.” ARD REIJTENBAGH, CHIEF PARTNERSHIP OFFICER AT PLANTLAB
Advances in data analysis are also making these kinds of farms more productive. “It was quite obvious there were mathematical patterns in plant growth,” says Ard Reijtenbagh, chief partnership officer at PlantLab.
Increasing interest in data collection prompted PlantLab’s founders to consider the optimum circumstances in which to grow plants.
They designed and supply so-called ‘plant production units’, as well as software and growing recipes, where growing conditions are tightly controlled: more than 80 potential variables, across the light spectrum, and including humidity and even the movement of air can be altered. The control is so thorough that they can determine the level of iron or zinc in plants.
The combination of technology and farming can also have other benefits.
Nerve Centre, an arts centre in Northern Ireland, runs a ‘digital farm’ project to teach students with learning difficulties entrepreneurship and digital skills.
Students construct aquaponics systems using laser cutters and 3D printers and supply the produce to restaurants. They have just taken delivery of 100 juvenile carp, which may fetch between £60 and £70 each once they are fully grown in two years. John Peto, the centre’s director of education, says: “Some [students] have no interest in growing food but they’re really interested in using computers.” He also expects the cultivation of fish to have a therapeutic effect.
LOKAL is a Prototype of a Salad Bar Whose Ingredients Are Grown Indoors, Locally and Vertically, Using a Hydroponic Farming System
Thanks to hydroponics, microgreens can grow up to three times faster than in fields, using 90 percent less water. This method produces much less spoilage and can be done locally, making it much more sustainable when powered by renewable energy sources.
LOKAL is a Prototype of a Salad Bar Whose Ingredients Are Grown Indoors, Locally and Vertically, Using a Hydroponic Farming System
Linked by Michael Levenston
Photographer: Rory Gardiner and Nicklas Ingemann
SPACE10—IKEA’s external future-living lab—popped up in Shoreditch during last week’s London Design Festival.
By Simon Caspersen
SPACE 10
Director of Communications
Sept 2017
We used the occasion to test a new food concept, we’ve been working on, called LOKAL. It is not fully ready to be implemented in the IKEA business of today, but was received so positively by local Londoners, that we are exploring further.
LOKAL is a prototype of a salad bar whose ingredients are grown indoors, locally and vertically, using a hydroponic farming system, which was on public display throughout the week.
Two thousand salads
The purpose of the prototype was to test how Londoners felt about food grown hydroponically and, more importantly, whether they liked the taste of the microgreens.
SPACE10’s chef-in-residence Simon Perez and his team served more than 2,000 complimentary salads over the course of six days in London. Visitors had a choice of three dishes, each of which came with a salad dressing made with spirulina, a kind of microalgae.
SPACE10 surveyed 100 people about the salads—and the responses were even more positive than expected: 90 people said their salad was “delicious”—the highest possible verdict. Just one person didn’t like it.
Many of the comments received from people also lent strong support to the LOKAL concept:
“Why can’t this be everywhere?”
“A brilliant concept.”
“I love it—make it happen!”
“Really exciting concept—I love it!”
“It’s inspiring to see work being done and people attempting to change the food and restaurant industry.”
“Help me do this at home.”
The perfect spring day, every day
Hydroponic farming allows microgreens to be grown without soil, using nutrient-enriched water, LED lights and computerised automation—ensuring the plants can enjoy a perfect spring day, every day.
Thanks to hydroponics, microgreens can grow up to three times faster than in fields, using 90 percent less water. This method produces much less spoilage and can be done locally, making it much more sustainable when powered by renewable energy sources.
Fresh approach to food
Having trialled its LOKAL prototype in London, SPACE10 will next introduce sensors and machine learning, and connect the data from the microgreens with Google Home. That will enable people to “talk” to the greens and understand their growing conditions and nutrient needs.