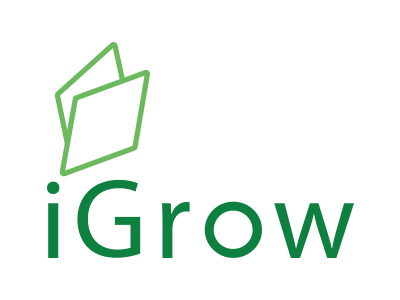
Welcome to iGrow News, Your Source for the World of Indoor Vertical Farming
USA - Minnesota - Based Living Greens Farm Ready For Coast-to-Coast Expansion
The company plans to break ground on a nationwide expansion at the end of this year, or the beginning of 2021, he said
Written By: Noah Fish
September 14, 2020
After spending nearly a decade mastering an aeroponic growing process, Living Greens Farm believes it’s ready to supply consumers nationwide a stronger and healthier form of produce.
Michelle Keller, head grower at Living Greens Farm, and George Pastrana, CEO of the company, stand in the 20,000-square-foot growing site where the company grows its produce. (Noah Fish / Agweek)
FARIBAULT, Minn. — George Pastrana has been the CEO of Living Greens Farm for only a couple of months, and what impressed him first and more than anything was just how green the produce was.
"That color, the thickness and then the taste — it's all what nature intended," said Pastrana, staring at a rack of fresh basil. "It's not what you would expect, because we've been eating stuff for so long that isn't like this."
Freshly harvested basil raised in the 20,000-square-foot growing site in Faribault, Minn. where the Living Greens Farm grows its produce. (Noah Fish / Agweek)
The 20,000-square-foot growing site in Faribault where Pastrana was admiring recently harvested greens is considered to be a "test farm" for the company.
"We believe we've perfected an aeroponic growing process that allows us to create large heads of lettuce at a fantastic yield," said Pastrana.
The company plans to break ground on a nationwide expansion at the end of this year, or the beginning of 2021, he said."That will be the first of multiple phases of expansion," Pastrana said. "To ultimately ship to and supply two-thirds of consumers and households in the United States."
Construction will take place, not in Faribault but somewhere else in the U.S., which will be announced later by the company. The first phase of expansion will be a site that will service the Midwest, and following sites will serve other sections of the U.S. until it's covered.
Pastrana said there's "a lot of excitement amongst the investor community" to fund the expansion efforts. He said most of that interest existed before the pandemic, and the "controlled environment" area of ag-tech has shown a lot of promise over the last decade."
But I think the pandemic really brought to life the need for a better, more consistent supply chain, and controlled agriculture doesn't have all the problems of traditional agriculture, with recalls and so on," said Pastrana. "(The pandemic) has just hyper-exaggerated the need for better farming techniques."
Greens nearing the point of harvest are stacked across from plants on day-one of the growth stage at the 20,000-square-foot growing site in Faribault, Minn. where Living Greens Farm grows its produce. (Noah Fish / Agweek)
True aeroponics
According to Pastrana, what makes Living Greens Farm a "true aeroponic vertical farming business model" is its ability to produce exceptional products.
"We are able to deliver much heavier heads of lettuce than our competitors and more consistent yields in an environment that is herbicide and pesticide-free," he said.
Unlike most of its competitors, the company does its own cutting, washing, and bagging of produce on-site, Pastrana said."So we're going to get our product on the shelves of retailers within 24 hours of harvest," he said. "That makes us pretty unique."Michelle Keller, head grower of the operation in Faribault, has worked at Living Greens Farm for seven years."
Since basically the conception of the project," she said.
She said those years were spent building, reconfiguring, and rebuilding grow systems — all aimed at finding the best way to grow romaine and butter lettuce in a vertical space.
One of the multiple grow rooms at the 20,000-square-foot growing site in Faribault, Minn. where Living Greens Farm grows its produce. (Noah Fish / Agweek)
"We always wanted to go vertical," said Keller of Living Greens.
Traditional vertical farming is "stacked," she said, but the company wanted to incorporate a system that people could work from the floor, without the use of ladders or platform machines.
"So each person can stay on the ground and work the farm completely from the safety of the floor," she said.
It takes a family Keller takes pride in the camaraderie at the farm, with workers leaning into their roles as plant nurturers. She's also not afraid to admit that she and other employees talk to the plants and sometimes give them names.
"We are a small family," said Keller of the different grow groups at the farm. "It's not uncommon to know everyone's name, and to know what they're going through and what they're able to accomplish at the farm."
Patti Guillen, an employee at Living Greens Farm, transplants heads of lettuce in the 20,000-square-foot growing site in Faribault, Minn. where, the company grows its produce. (Noah Fish / Agweek)
Before Living Greens came up with the A-frame technology that it uses now, the company tried four different renditions of a "staircase approach", said Keller.
As head grower, her primary goal is to raise "full-grown heads of lettuce that are robust enough to survive the packaging process," and go on to have a full two-week shelf life.
Living Greens is also committed to being pesticide-free, said Keller, and the farm mandates a high standard of cleanliness to prevent harmful things from getting into its facilities and a protocol for if something does."Every stage of the growth pattern is followed by disinfecting or sanitation," she said.
Keller said the operation at Living Greens is guided by GAP — good agricultural practices — as well as GMP — good manufacturing processes. What makes the operation unique is that it has been conducting both of these processes successfully under the same roof long before the COVID-19 pandemic, Keller said.
When the pandemic broke out in March, Keller called an all-employee meeting where she was straightforward about what was in their control. They now meet every week to discuss what's happened lately with the outbreak.
"We were always just really honest about it," said Keller of the pandemic.
She told them in that original meeting that Living Greens Farm would stay open if employees not only took the on-site precautions seriously but were also "hyper-aware" when they were at home."Making sure that there's no miscommunication about this is what has to be done, to keep ourselves open," Keller said.
Living Greens Farm products can now be found at Whole Foods, HyVee, Walmart, Cub Foods, and more.
Find locations at https://www.livinggreensfarm.com/store-locator.
VIDEO: Urban Fresh Farms Launches New ZipGrow Facility In Dubai
A 1,000 square foot ZipGrowTM ZipFarmTM was recently installed in Urban Fresh Farm’s facility in the Industrial center of Dubai and will soon be producing pesticide-free fresh herbs and leafy greens for the local market
October 8, 2020
ONTARIO, CANADA & DUBAI, UNITED ARAB EMIRATES - With more than 80% of food being imported into the UAE, Urban Fresh Farms, Dubai’s newest indoor vertical hydroponic farm from ZipGrowTM, is doing its part to contribute to a more sustainable local food system.
A 1,000 square foot ZipGrowTM ZipFarmTM was recently installed in Urban Fresh Farm’s facility in the Industrial center of Dubai and will soon be producing pesticide-free fresh herbs and leafy greens for the local market. Urban Fresh Farms is a new company, founded by people who always had an interest in sustainable agriculture but thought they did not have the knowledge or financial backing to get into the industry.
“We, as a group, always found vertical farming really interesting and knew there would be a strong demand for it in the Dubai area”, said Scott Naude, co-founder of Urban Fresh Farms. “We were hesitant to jump in at first, but the combination of ZipGrow’s technology and ongoing training, the increasing demand for higher quality and fresh produce, and the Middle East’s booming tech sector all aligned perfectly for us to begin this venture.”
As with the rest of the world, COVID-19’s impact on the local supply chain has also impacted the Dubai area, with food selections being limited in local grocery stores during the peak of lockdowns.
“Around the world, we are hearing from all our growers that food retailers are actively looking for local food goods to supply”, explains Eric Lang, President of ZipGrow Inc. “We are also hearing from government’s around the world, including in the UAE, who want to actively seek out ways to reduce supply chain lengths to ensure a more consistent and high-quality food stream.”
Hydroponic growing, as an industry, is still recently new to the Middle East region. The UAE government is a leader in the Middle East region, and in 2018 launched a National Food Security Strategy 2051, led by the Minister of State for Food and Water Security, Her Excellency Mariam bint Mohammed Al Mheiri. This strategy aims to increase local food production in the UAE, while simultaneously maximizing the use of modern technologies to bring fresh and sustainable food to the region.
“There's also a demand for healthy eating options and this has given rise to a number of excellent meal plan services and all-in-one meal ingredient boxes which in turn is creating a need for the best, freshest vegetables to be readily available” adds Naude. “We’re planning on starting out growing primarily herbs such as basil, parsley, and coriander, and hope to have our first crop available in December.”
Urban Fresh Farm and ZipGrow Inc. plan to use this new facility to showcase this vertical farming technology to the UAE and the wider Middle East region. Naude adds; “We’re excited about our ongoing partnership with ZipGrow Inc. There is so much educational content available, as well as a fantastic team. So even for someone like myself who is new to all of this, ZipGrow provides all the tools needed to get growing.”
ZipGrow Inc. is an international leader in indoor, vertical farming technology. Our flagship product, the ZipGrowTM Tower, is a core component of many of the world’s most innovative farms; from indoor hydroponic warehouses to vertical aquaponic greenhouses and high-density container farms.
For more information contact:
Gina Scandrett at hello@zipgrow.com or at 1-855-ZIPGROW.
425F Fourth Street West, Cornwall, Ontario K6J 2S7, Canada www.zipgrow.com 1-855-ZIPGROW
Why Kroger And Publix Are Bringing The Farm To The Grocery Store
In March, Publix’s GreenWise market in Lakewood, Florida, added a 40-foot container hydroponic farm in the parking lot
October 8, 2020
By Jesse Klein
Just like every other retailer, grocery stores are focusing on the customer experience to get people back in store. Grocery delivery was already a rising trend, and the pandemic kicked it into the next gear. In May, U.S. online grocery sales had grown to 40 percent. So grocers including Kroger and Publix are looking at onsite vertical farms as one way to attract consumers.
"That experience of going into a grocer and picking something essentially off the vine is compelling from a customer experience standpoint," said Shireen Santosham, head of strategic initiatives at Plenty, a vertical farm company based in San Francisco.
According to Grant Vandenbusschet, chief category officer at Fifth Season, a robotic vertical farm company based in Pittsburgh, fresh produce is keeping a lot of traditional grocery stores alive. It’s the main category still driving traffic into stores, he said, so innovating and investing in this department has been a focus for most retailers.
On-site container farming is not a new idea for grocery stores, but as urban vertical farming has advanced to become a more mainstream part of the supply chain, the idea is becoming more feasible. Some big players have finished their strategic analysis and pilot programs, and are leaning into vertical farming in a bigger way.
That experience of going into a grocer and picking something essentially off the vine is compelling from a customer experience standpoint.
In two Seattle stores, for example, Kroger installed modular vertical farms from German startup Infarm. While the seedlings spend the first few days at Infarm’s centralized nursery, most of the growing happens on-site at the grocery stores.
In March, Publix’s GreenWise market in Lakewood, Florida, added a 40-foot container hydroponic farm in the parking lot. Customers can see the equivalent of three acres of traditional farmland through the container’s windows. It grows about 720 heads of lettuce each week, all sold in the store. But it’s still early days and the process has kinks to work out. At first, Publix wasn’t getting the yields it was expecting.
"It takes time to grow the product and offer consistent quality, flavor, and size," said Curt Epperson, business development director at Publix. "I believe over time, once hydroponic growers refine their processes, and scale-up, we’ll find more efficiencies."
According to Vandenbusschet, one of those efficiencies may be a focus on supporting vertical farms at a large-scale grocer’s distribution center instead of at every single retail location. To get significant business and sustainability impacts from vertical farming, companies will need to get large enough to take true advantage of economies of scale.
"We think a lot of retailers are looking at this format if they are going to have high enough volumes of product to start replacing [traditional] grown products inside of all of their stores," Vandenbusschet said.
Growing is a hard, finicky business. Retailers are experts at retailing, and it’s hard to be good at both retailing and growing, so expect to see key partnerships materialize. Along with the Infarm and Kroger partnership, Publix’s onsite farm is run and managed by Brick Street Farms.
"Finding systems that are not over-encumbering to their operations, things that they can plug-and-play well is really going to be critical," Vandenbusschet said.
If retailers pursue this model, the customer experience might be more akin to going to a farmers’ market than going straight to the farm. But this model has a better chance of scaling well for businesses while also creating sustainability benefits such as cutting freight emissions, lowering water usage, and prolonging shelf life.
Lead photo: Publix is hoping to lure shoppers back to grocery stores with new onsite vertical farms.//Courtesy of Publix
USA - MARYLAND - Father, Daughter Launch Hydroponic Farming Operation In Montgomery County
With lettuce regularly being in the news related to an outbreak of disease, father and daughter Rod Kelly and Alex Armstrong concluded that there has to be a better way to purchase fresh produce
By Sondra Hernandez, Staff writer
September. 28, 2020
With lettuce regularly being in the news related to an outbreak of disease, father and daughter Rod Kelly and Alex Armstrong concluded that there has to be a better way to purchase fresh produce.
“It’s really hard to get fresh produce,” Armstrong said. “About 80 percent of lettuce comes from California. It’s hard to find locally grown produce.”
It was also concerning to her that consumers don’t quite know what they are getting with lettuce brought in from another area. Is it pesticide-free? Was there any contamination from livestock waste runoff?
“People are more aware of what’s in their food and they are more concerned about it,” she said.
To offer a fresh, locally grown option, the two have turned to a climate-controlled, vertical, hydroponic farming operation set up in a shipping container on property in South Montgomery County.“It’s an amazing technology,” Kelly said. “It’s a perfect climate-controlled environment for growing leafy greens.”
Kelly is a petroleum engineer and Armstrong has a marketing background. Kelly also owns several businesses and was looking for a project that he and his daughter could work on together.
They found the technology behind hydroponic farming fascinating.
The farm is contained in a custom-built, insulated shipping container. Kelly and Armstrong worked with Freight Farms in Boston for their operation.
The shipping container came from Boston by 18-wheeler and was delivered in late June. They planted their first crop in late July.
The message of Freight Farms is that fresh produce can be grown anywhere regardless of the climate.
Seedlings begin growth in trays under red and blue LED lights. Once the seedling grows larger, it’s transferred to a vertical tower for growing until its ready to harvest.
Water flows from the top of the container down through the roots and is collected at the bottom of the tower before being recycled to use again. These methods use about 90 percent less water than conventional farming. A panel of red and blue LED lights help the plants to grow into nutrient-rich food.“It’s cool technology and as an engineer, I appreciate that” Kelly said.
Fare House Farms grows a variety of lettuce and herbs.
They offer a wide array of lettuce like butterhead, bibb, romaine, Summer Crisp, and Oakleaf just to name a few. They offer leafy vegetables like arugula, cabbage, collards, kale, mustard greens, spinach, and chard. They also offer a variety of herbs like basil, cilantro, chives, dill, and more.
See their website at farehousefarms.com for a full menu.
Before this experience, Armstrong said she never knew what truly fresh lettuce and herbs tasted like.
She said the hydroponically grown lettuce was sweeter and crunchier. Kelly added the lettuce was prettier too.
The lettuce is sold with the peat moss plug still on so it will stay fresh for longer.
Kelly said they will spend the rest of 2020 experimenting with what grows best and studying the produce preferences of local buyers.
They plan to participate in local farmer’s markets to get their start.
They harvest on Fridays before the Saturday farmer’s markets.“You’re getting the freshest crop that you can get,” Kelly said.
Visit the Fare House Farms page on Facebook for more information and to see the farmer’s markets that they’ll be at.shernandez@hcnonline.com
Photos:
Alex Armstrong left, shares a laugh with Jane Pope after handing her a bag of freshly harvested lettuce at Fare House Farms, a hydroponic farming operation, Wednesday, Sept. 23, 2020, in Oak Ridge. Hydroponic farming is a type of horticulture where indoor crops are grown without soil by using a nutrient-rich and climate-controlled
Photo: Jason Fochtman, Houston Chronicle / Staff photographer
Rod Kelly and Alex Armstrong run Fare House Farms, a hydroponic farming operation in Oak Ridge. Hydroponic farming is a type of horticulture where indoor crops are grown without soil by using a nutrient-rich and climate-controlled environment.
Photo: Jason Fochtman, Houston Chronicle / Staff photographer9of10Alex Armstrong, and Rod Kelly are lit with panels of red and blue lights Alex Armstrong and Rod Kelly at Fare House Farms, a hydroponic farming operation, Wednesday, Sept. 23, 2020, in Oak Ridge. Hydroponic farming is a type of horticulture where indoor crops are grown without soil by using a nutrient-rich and climate-controlled environment.
Alex Armstrong and Rod Kelly make their way past pannels of red and blue lights, which encourage strong plant health and production, at Fare House Farms, a hydroponic farming operation, Wednesday, Sept. 23, 2020, in Oak Ridge. Hydroponic farming is a type of horticulture where indoor crops are grown without soil by using a nutrient-rich and Photo: Jason Fochtman, Houston Chronicle / Staff photographer
Tri-State, EPRI Team To Officially Bring ‘Farm In A Box’ Program To Moffat County School District
Tri-State will install one of EPRI’s cutting-edge indoor agriculture facilities on the grounds of Moffat County High School later this year, according to a press release from Tri-State
09-23-20 | Joshua Carney | Follow
Tri-State Generation and Transmission Association’s decades-long relationship with the Electric Power Research Institute is about to bear fruit for Moffat County School District students and the Craig community as a whole as the “Farm in a Box” project moves forward.
Tri-State will install one of EPRI’s cutting-edge indoor agriculture facilities on the grounds of Moffat County High School later this year, according to a press release from Tri-State.
The “Farm in a Box” is valued at $250,000 – which is covered as part of Tri-State’s EPRI membership – and will provide a new source for fresh produce in the region and educational opportunities for MCSD students. Moffat County High School Business Teacher Krista Schenck presented the project to City Council in early September. The project has the capability to produce various crops, such as lettuce, kale, arugula herbs, flowers, carrots, and radishes, year-round inside the shipping container.
“Tri-State invests in its EPRI membership and is keen to find immediately applicable uses for the remarkable technologies that emerge to benefit the electric sector and society at large,” said Tri-State CEO Duane Highley in a press release. “We also recognize that the transition brought on by our Responsible Energy Plan will have a major impact on coal-dependent communities, so if we can leverage a program to bring new educational, economic, and lifestyle benefits to support Moffat County schools, we are proud and eager to do so.”
An EPRI-led team is constructing the facility – a 40-foot long shipping container equipped with efficient lighting, temperature control, and plumbing infrastructure needed to grow crops inside the container on a year-round basis.
Since 2015, EPRI has been examining the operational, technological, sustainability, and environmental characteristics for indoor agriculture, by installing container farms across the United States and assessing their performance with local electricity providers, academic institutions, and other community organizations.“
As an emerging industry in urban and rural areas throughout the United States, indoor farming can help us use our energy and water resources more efficiently,” said EPRI President Arshad Mansoor. “EPRI’s indoor food production research aims to help electric utilities better understand, plan for, and engage with this novel enterprise while also offering educational opportunities for project collaborators, the local community, and the next generation of farmers to address food availability challenges.”
According to Tri-State, EPRI staff will monitor the container to evaluate nutrient quality of the produce, utility program compatibility, community impacts, sustainability performance, technology trends, market drivers, electricity load profiles, and other broader environmental and economic aspects of indoor food production for the first two years following installation. EPRI will conduct research on the container and MCSD will be the sole owner and operator of the equipment.
“Moffat County School District is excited about the learning potential this program affords its career and technical education students in our community,” said Principal Sarah Hepworth of Moffat County High School.“
Through the collaboration between agricultural, business, marketing, and culinary programs, the opportunities to learn about horticulture, conservation, food regulations, business, and project management, marketing, sales, and food preparation are endless for MCSD students,” said Schenck. “Students and faculty look forward to utilizing this partnership and the technology of ‘Farm in a Box’ to grow crops from microgreens to lettuce and carrots.”
Preparing the container farm will take several weeks and involve manufacturing and a customized graphic treatment of its exterior. School officials are targeting early to mid-November for its arrival in Craig. The EPRI team will consult with the school district on installation and operation.“
This is a true team effort,” added Highley. “One of the seven cooperative principles under which we operate is ‘Concern for Community,’ so we’re excited to see the school district adopt this project and turn it into a real asset for community betterment.”In January, Tri-State announced its Responsible Energy Plan, which will transition the company to more renewable energy production for its members to address changes in the industry and to support new state requirements for clean energy. The effort will result in the closure of the Craig Generation Station by 2030, and Tri-State has been working with state and local officials to support transition efforts in the community.jcarney@craigdailypress.com
Greens Grown In A Warehouse? Vertical Farming A Growing Trend In Ontario
Vertical farming maximizes crop output in a limited space; the seasons don't matter: growing takes place anytime, anywhere
Andrew Coppolino · CBC News
Sep 26, 2020
This photo was taken inside We the Roots vertical farm in Toronto. Wired with LED lights, the hydroponic facility can grow up to 20000 leafy green plants at a time. (Yan Jun Li/CBC)
With vertical farming, seasons don't matter: growing takes place anytime, anywhere
It's a plain building in an industrial complex in Guelph, a few minutes from Highway 401. Inside is 4,000 square metres of high-tech "vertical farm" operated by GoodLeaf Farms, a Halifax-based company.
In the course of 12 months, GoodLeaf grows, harvests and packages 360,000-kilograms of pea shoots, mustard medley, Asian mix and arugula microgreens as well as baby kale and baby arugula. The growing room is a couple of storeys high with trays of microgreens settled into a peat moss-based substrate.
Vertical farming maximizes crop output in a limited space; the seasons don't matter: growing takes place anytime, anywhere.
The facility uses no pesticides, fungicides or herbicides. A blend of red and blue LED lighting casts a pink glow on the produce, which is helped in its growth with computer-controlled hydroponics. Nutrients such as nitrogen are added through the irrigation system.
"A vertical farm is where technology and traditional agriculture come together. We grow leafy greens vertically in stacks in an indoor controlled environment," said Jacquie Needham of GoodLeaf.
There are a lot of computers, so in a way it's farming with data. In this relatively new industry, "controlled environment agriculture" (CEA) uses technology that allows for the precise control of variables such as ventilation, light, heat and humidity to grow fresh greens and get them to market quickly and efficiently and without worrying about variables like drought, flooding, insects and frost.
Would you eat microgreens grown in a warehouse? Many people do. It's from technology called vertical farming. Food columnist Andrew Coppolino visited GoodLeaf Farms' Guelph facility recently to learn about this growing opportunity for farming. (Andrew Coppolino/CBC)
From seed to grocery stores
GoodLeaf, which built its first pilot farm in Truro, NS, in 2015, has been in the commercial market for about a year now. Its microgreens are available at Loblaw stores and Fortino's, and Needham says they hope to be in Longo's and Whole Foods soon.
GoodLeaf employs 70 people, whose goals, aside from producing good flavour, are efficiency and sustainability, which make it a part of the City of Guelph's vision to be Canada's first "circular" food economy.
"In a controlled environment, we can recycle 95% of the water we use," Needham said.
Seeds are planted in trays of peat substrate (later recycled as garden compost) which are loaded onto decks and rolled into a dark germination room, at about 85% humidity, for two days. They then head to the towers of the pink-light growing room, held at 21-degrees C., for a growing cycle between six and 20 days.
At harvest, the microgreen leaves from the miniature plants (these are not "sprouts") are quickly sliced by a machine, packaged and chilled. In the grocery store, they have a shelf-life of over two weeks. As for price, GoodLeaf products are roughly in line with organic greens.
The facility is strictly controlled, in all aspects, to ensure food safety; to protect intellectual property, no photography is allowed. Visitors must remove their jewlery, wear a hairnet, cover their footwear with disposable shoe covers and don a Tyvek anti-microbial lab coat. They then individually enter an air-lock and take an "air shower" before entering the production area.
Predictability in farming
The GoodLeaf facility is one of few state-of-the-art vertical farms in the country and collaborates in research and development with the University of Guelph.
According to Sylvain Charlebois, a professor in food distribution and policy at Dalhousie University, the technology represents a new wave of farming.
"Controlled environment agriculture is part of the future for Canadian agriculture. If we want to grow our food all year round, there is no other way. We need to think about these technologies, which will evolve and become more efficient," Charlebois said.
Predictability and farming do not go together. Charlebois says that CEA could be part of a solution for Canada, a country that imports most of its produce – a fact that makes us vulnerable. "Covid-19 got a lot of provinces and the country to think differently about food and producing food all year round."
He notes that the Agri-Food Analytics Lab at Dalhousie is currently working with Quebec and New Brunswick on food security projects. "A lot of those projects have to do with controlled environment agriculture," he said.
Is it sustainable?
At the other end of the spectrum is traditional outdoor farming, such as that done at Pfenning's Organic Farm in New Hamburg. Jenn Pfenning sees such vertical farms as "a supplement" to our food supply, though she wonders about the input side of such an energy-intensive operation.
"There's nothing wrong with vertical farming with specific crops, but how do you keep them healthy and growing without taking up too many resources in terms of having to heat it and light it? We struggle to produce greenhouse crops year-round as it is," says Pfenning.
She says microgreens are one thing but maturing a head of lettuce or kale, and moreso tomatoes or peppers is quite another. "It requires more than we can provide through artificial light."
GoodLeaf believes they have the technology to make nutrient-dense greens while acknowledging that it does require a lot of energy to keep the plant operating 24/7 and 365 days. They add, though, that their carbon footprint is less than conventional farming with energy emissions significantly reduced by the fact they use no fertilizers and the produce does not require long trips in vehicles in order to get to market.
Proponents of controlled environment agriculture like Charlebois say "it must be part of the future of Canadian agriculture." Around the world, the amount of arable, nutrient-rich land has diminished and demand for healthy foods has increased.
Vertical farms can also coincide with urban renewal planning that includes retrofitting old factories, which could help rejuvenate a city's core — if the capital is there — and be a local source of fresh food.
A worker checks on some microgreens at a GoodLeaf Farms facility. The company has a vertical farming facility near Guelph. (GoodLeaf Farms)
A growth opportunity
While a lot of our produce for much of the year is trucked in many thousands of kilometers from Mexico and the southern United States, these microgreens are local.
Charlebois says that as these technologies evolve, and if a vertical farm can be financially viable and sell its products at a competitive price, it could be a future model for allowing different markets in Canada to grow greens and give retailers an opportunity to sell fresh local produce.
"Think of the north," said Charlebois. "This is the type of technology you need to make sure communities in the north become food secure."
Whether or not vertical farming is a supplement and hybrid-type of farming, and despite the energy and capital required, GoodLeaf has that growth opportunity in their sights, Needham says.
"They're growing fruits and vegetables in other countries, and we will follow suit because we have heightened awareness of food security when it comes to fruit and vegetable production in Canada."
ABOUT THE AUTHOR
Food columnist, CBC Kitchener-Waterloo
Andrew Coppolino is a food columnist for CBC Radio in Waterloo Region. He was formerly restaurant reviewer with The Waterloo Region Record. He also contributes to Culinary Trends and Restaurant Report magazines in the U.S. and is the co-author of Cooking with Shakespeare. A couple of years of cooking as an apprentice chef in a restaurant kitchen helped him decide he wanted to work with food from the other side of the stove.
CBC's Journalistic Standards and Practices|About CBC News
Report Typo or Error
Fresh Hydroponic Produce In A Swedish Ski Resort
ICA Åre, located in one of the leading Scandinavian ski resorts, is the second ICA supermarket store in Sweden to install a hydroponic vertical container farm from Boston-based Freight Farms – providing its customers with just-picked leafy greens grown onsite, year-round
ICA Åre, located in one of the leading Scandinavian ski resorts, is the second ICA supermarket store in Sweden to install a hydroponic vertical container farm from Boston-based Freight Farms – providing its customers with just-picked leafy greens grown onsite, year-round.
Housed inside a 13-meter long shipping container, the onsite Freight Farm will reduce ICA Åre’s reliance on transported produce shipped long-distance into the mountain region, while providing pesticide and herbicide-free greens to customers at the peak of freshness year-round.
The initiative, Åre Byodling, was led by ICA Åre store owner Lars Ocklind and real estate company Diös Fastigheter, who recognized the benefits Freight Farms’ environmentally-controlled technology can have in the Nordic climate, particularly within the resort community hub that’s home to ICA Åre, the main train station, and other surrounding stores and restaurants. Ocklind believes that the store’s ability to grow its own crops is an investment in its future and that of its community.
Freight Farms, founded in 2010, pioneered hydronic vertical container farming and has a large network of IoT-connected farms in the world. The container farms, integrated with IoT data platform, farmhand, creates and maintains the optimal growing conditions to harvest crops year-round using less than 5 gallons of water per day. The technology has empowered ICA Åre and ICA Maxi Högskolan to create closed-loop food systems onsite, eliminating transportation emissions. Harvesting crops onsite also keeps crops fresh and nutrient-dense for longer, significantly reducing food waste for both sellers and consumers.
ICA Åre’s first farm harvest is scheduled for mid-October. The supermarket will begin by selling a selection of lettuce, kale and herbs in-store, and crops will also be used in their own restaurant and sold to other restaurants in the village. The range of crop offerings will continue to develop and expand – there is already great interest in collaboration from local restaurateurs for special lines of locally-grown crops.
For more information:
Freight Farms
www.freightfarms.com
Publication date: Fri 2 Oct 2020
Sodexo Partners With Container Farming Startup Freight Farms To Bring Indoor Ag To College Campuses
The goal of the partnership is to bring fresh, traceable produce to college foodservice year-round that’s pesticide- and insecticide-free with low food miles
January 29, 2020
When a major foodservice player like Sodexo calls up your relatively young startup to ask whether you’d be interested in providing indoor ag services for their university clients, it’s safe to say you’ve arrived.
“Their partnership team reached out to us and said this is a huge problem we are trying to solve and we have been watching you guys from corporate headquarters and we saw you have proven adoption on all these different university campuses,” Brad McNamara, Freight Farms CEO, told AFN. “It’s a surreal moment when the 800-pound gorilla calls you and says we’ve been talking about you internally for six months. Can we work with you?”
The Boston-based container farming company announced today a new partnership to bring Freight Farms’ Greenery container farm setups to the campuses that Sodexo services throughout the US. The goal of the partnership is to bring fresh, traceable produce to college foodservice year-round that’s pesticide- and insecticide-free with low food miles. Sodexo is engaging the company as part of its Better Tomorrow Commitments, developed according to the UN Sustainable Development Goals.
Sodexo is one of the world’s largest multinational corporations serving 80 countries with nearly $17 billion in annual revenue, which means the partnership could go a long way towards demonstrating whether indoor ag systems can provide fresh produce at large-scale. The first Greenery system will be deployed at a college campus this Spring, according to McNamara.
As part of the deal, Sodexo’s campus clients will come under Freight Farms’ ‘farming-as-a-service’ program like any other Greenery user. Freight Farms provides turnkey farming software, training, monitoring, refillables, and support. The number of Greenery machines deployed to each campus will depend on the goal that the university has, which could involve providing as much produce as possible to its foodservice outlets. McNamara describes the units as being able to operate on a commercial scale and to scale up or down quickly depending on the ultimate need.
Invest with Impact. Click here.
More than local lettuce
In 2012, Freight Farms launched a farming system built inside a shipping container dubbed the Leafy Green Machine. Last year, it launched a new model, Greenery, in the same 320-square foot space but with 70% more growing space. It also packs new IoT-driven technology to improve yield, efficiency, and automation, according to the startup.
Today, it claims to have the largest network of connected farms in the world with customers in 25 countries and 44 US states that range from small business farmers to corporate, hospitality, retail, and education entities. So far, 35 educational and corporate campuses are using Freight Farms’ Greenery machine and technology to grow food onsight. The University of Georgia has already purchased two Greenery containers. A group called WhyNot Farm also made a purchase.
What Freight Farms is really trying to achieve is more than just growing lettuce in a shipping container, however. Last time we interviewed the outfit, the goal was to achieve a distributed food system that addresses many of the issues that the conventional produce industry has created: food waste, ugly produce being discarded, and a focus solely on yield maximization to the detriment of ecosystems.
“Schools are a good fit because of the value add that is placed on food and the variety and the quality of food served in cafeterias. There’s not just one customer that schools have to attract. They’re also selling to parents. They have to really be able to give comfort to mom and dad that the student has access to high-quality food and food programming,” McNamara explains.
Students are also hungry for this type of offering, as consumers at large search for ways to get closer to the roots of the food that they consume any way they can. At McNamara’s alma mater, Northeastern, for example, one of its educational programs includes a food co-op where students can work on real-world applications of local food systems.
The indoor ag space is seeing some renewed attention recently, with three of AFN’s top 10 best-read stories in 2019 focusing on the sector.
“I think what’s really exciting now versus just a few years ago is the recognition that this opportunity a lot of us have been talking about is, in fact, big and that there are various markets for us to go after,” McNamara says.
With a freshly inked Sodexo partnership under his belt, it’s hard to say he’s wrong.
Former Shipping Container Maker Uses Them To Farm
Operating on a rented 1,000-square-meter (quarter-acre) patch of wasteland in Hong Kong's rural Yuen Long, Lee's MoVertical Farm utilizes about 30 decommissioned containers, some decades old, to raise red watercress and other local vegetables hydroponically, eliminating the need for soil
September 25, 2020
The bounty is sold to supermarkets in the crowded city
of 7.5 million that is forced to import most of its food
HONG KONG (AP) — After a career-making shipping containers that transport freight around the world, Arthur Lee has stayed with them in retirement, using them to raise crops and fish.
Operating on a rented 1,000-square-meter (quarter-acre) patch of wasteland in Hong Kong's rural Yuen Long, Lee's MoVertical Farm utilizes about 30 decommissioned containers, some decades old, to raise red watercress and other local vegetables hydroponically, eliminating the need for soil. A few are also used as ponds for freshwater fish.
The bounty is sold to supermarkets in the crowded city of 7.5 million that is forced to import most of its food.
As one of the world's great trading hubs, Hong Kong is a rich source of the sturdy 40-foot (12-meter) -long boxes.
Lee uses the latest technology to monitor his crops. The controlled environment inside the boxes uses a hydroponic drip system to deliver nutrients, eliminate the need for herbicides and pesticides, and reduce risks from pests, small animals, and bad weather. Temperature, humidity, carbon dioxide levels, nutrient mixtures, and light can all be monitored and adjusted.
And if Lee loses his lease, he can load his container farm onto trucks and move it elsewhere with minimal disruption.
Shipping container farms have taken off in countries around the world with wildly varying climates, from freezing to tropical, and on scales ranging from single containers to dozens. Many are located in urban areas where fresh produce can easily be delivered to stores or directly to consumers. While vegetables, fruits such as strawberries, and freshwater fish are among the most popular, some growers have turned to raising high-protein insects as a food supplement.
Controlled environment agriculture is just one use for shipping containers, both new and old. In poorer nations, they are often used as shops with the added advantage of locking up tightly at closing time. In more affluent nations, they have been turned into tiny homes, painting studios, coffee shops, backyard sheds for hobbyists, and even swimming pools. Online, containers can be bought for around $4,000, with basic home conversions going for $30,000 or more.
Lead photo (AP Photo/Kin Cheung): Arthur Lee, the owner of MoVertical Farm, feeds his fish inside a shipping container in Yuen Long, Hong Kong's New Territories.
"Vertical Farming Is Not The Answer For All of Humanity's Woes"
When people talk about vertical farming, they often focus on what it gets right: saving water compared to traditional agriculture, providing communities with safe, fresh, healthy and locally-grown food, etc
On the second day of the Vertical Farming World Congress, the speakers really got to the meat of the matter (or should that be to the leafy greens of the matter?). The day was opened with three presentations on market opportunities in the industry, given by Ian Cox of Innovate UK, Christine Zimmermann-Loessl, Chairwoman of the Association for Vertical Farming, and Henry Gordon-Smith, Founder and CEO of Agritecture.
Challenges and opportunities
When people talk about vertical farming, they often focus on what it gets right: saving water compared to traditional agriculture, providing communities with safe, fresh, healthy and locally-grown food, etc. In order to get the complete picture, however, it's also important to look at potential downsides. Ian, in his presentation, didn't shy away from discussing those.
He mentioned the high price of real estate in urban location as one of the potential obstacles to vertical farming. Critics also often argue that vertical farms are energy-intensive; however, Ian notes, there are many different models in vertical farming, and not all of them use lighting. Still, energy is important to the success of a vertical farm, and it is crucial that continuity of power is guaranteed. Finally, not all crops can be grown in vertical farms - the majority is herbs and leafy greens, which grow fast, command a price premium and do not need much light. According to Ian, "more fruits, vegetables, pulses and ground fruits need to be produced in vertical farms."
There are, fortunately, also lots of opportunities in vertical farming - Ian points to innovations in sensors, automation, and new crops being developed as some examples. One of these success stories backed by InnovateUK through CHAP, is GelPonics.
Vertical farming: part of the solution
Christine Zimmermann-Loessl provided an overview of the work of the Association for Vertical Farming. In her presentation, she highlighted the need for agriculture to be more environmentally friendly. In order to achieve this next level, "cooperation of science and industry is important", she said.
With humankind reaching the planetary boundaries, Christine argues, this is particularly important. And while land is scarce, vertical farming alone won't solve this problem. "It will be a part of the solution", she said. For more on Christine's views on vertical farming, check out this HortiDaily interview.
Resilient cities
The last speaker in the day's morning session, Henry Gordon-Smith, spoke about the city of the future, which according to him should be shaped by data-driven scenario planning. He showed how in the past, even a dense urban area like Manhattan had local agriculture. Throughout history, cities always needed to have the resources to make them thrive.
At some point in recent history, that changed, with the focus shifting to heavy urbanization. "One of the cons now is that cities are less resilient". Henry takes Ontario as an example - it used to be an exporter of food, but with unchecked urban development in Toronto, the area actually turned into a net importer of food, making it less resilient. He then went on to highlight some of the solutions Agritecture can offer for these issues.
Image credit: Agritecture
Selecting the best technology and crops
Another session that day focused on choosing the right crops and technology for one's vertical farm, featuring insights from James Lloyd-Jones, Founder and Managing Director of Jones Food Company; David Rosenberg, Founder and CEO of AeroFarms; David Farquhar, CEO of Intelligent Growth Solutions; and Mike Zelkind, Co-founder and CEO of 80 Acres Farms.
James has a background in property and renewable energy - two fields that are related to the vertical farming sector, but not to agriculture as such. Still, James heads one of the largest vertical farms in the world - this fits into a trend that Henry Gordon-Smith also highlighted, where people get into the industry without necessarily having a background in agriculture.
For James, that meant that he had to look for talent to join the team, and he mainly used local, British talent for that. "It's important to build a strong brand to attract strong talent with the right attitude", he emphasized.
An inside view of Jones Food Company
And the growth for Jones Food Company doesn't stop there. At the end of the presentation, James unveiled his plans for the future: by the end of 2021, two new farms will be built in the UK, with an area of 30,000 m2. In addition, the company will continue to scout for talent, and in the first quarter of 2021, they are planning to launch a new retail brand.
"Vertical integration is key"
Next up was David Rosenberg, who introduced his company AeroFarms and the way they work. Having been in business since 2004, they've built ten vertical farms to date, and they're in the process of building one that's twice as large as the biggest one in the world.
David began his presentation by stressing that there's a place for all farms. "Vertical farming is not the answer for all of humanity's woes, not by a long shot. For some crops and for some places in the world, open field or greenhouse farming is the better alternative." For other places and crops, vertical farming is the better alternative. "And those alternatives are going to become more and more as vertical farming reduces capital costs and operating costs," David believes.
AeroFarms
When it comes to choosing new crops, David notes that what works as a small farm doesn't necessarily translate to a big farm. That's why at AeroFarms, they go through three stages when making this decision:
Research & Development: Understand the plant science to improve plant quality and yield
Pilot: Improve how to grow plants mechanically with the right growing system
Commercialization: Solve agricultural problems through collaborations with other industry leaders
This doesn't just apply to crops, by the way - this way of working is just as important when it comes to choosing the right tech. "We pride ourselves in not re-inventing the wheel in automation", David says. "If someone has a better mousetrap, we'll use that. This is a hard business, and to be really good at it, vertical integration is key."
He also stressed the importance of sanitation in the industry, saying it's bad to cut corners there. "I hope we're diligent about that and processes around food safety. After all, we're talking about people's lives here."
And like James, David also had some news to share about the company's future plans. They're currently building what they say is the world's largest R&D indoor vertical farm, as part of an investment of $100 million by the Abu Dhabi Investment Office. Phase 1 of that project is slated to be operational in late Q1 2021.
3-E and 5-D
David Farquhar was up next to talk about the way they do things at Scottish vertical farming company Intelligent Growth Solutions (IGS). "IGS was founded by a farmer, which is why we focus so much on getting crop production perfect", he explains. The way they work is they basically take a traditional open field, cut it up into pieces and stack the pieces on top of each other in towers.
Of course, things do get a bit more complicated with all the tech added into the mix. At IGS, they call it Total Control Environment Agriculture (TCEA). They cultivate their crops 100% IOT-enabled, making use of cloud computing in an Intelligent Grid that was originally for lighting, but can also be used for other links in the chain, including the retail stage.
David then went on to share the philosophy behind all this high tech. First of all, there's the 3-E targets: Excellent quality produce, Economic competitiveness, and Environmentally friendly. In order to achieve these high standards, IGS makes use of the 5-D way of working.
Replicating real weather conditions is an important aspect of the way they work at IGS, and they see weather as three-dimensional (3-D): there's the sun, wind and rain. Of course, David explains, each of these have multiple varieties (between eight and ten each), and each of these variables has almost infinite values. Take light, for instance, which comes in an almost infinite spectrum of colors. David compared it to paying a visit to the hardware store when you want to repaint your bathroom: the array of available colors is dazzling.
Time is also an important factor, it's the fourth dimension in the 5-D equation. At IGS, they give the crop what it needs at each stage in its life cycle, from darker and humid conditions in the germination stage, to a lighter environment later on in the crop life cycle.
And finally, there's the dimension of space: each shelf in an IGS tower is its own microclimate - the temperature can differ quite a bit between two of those microclimates, even though they're only 30 cm apart. That way, they can grow a wide variety of crops in a single tower. "Whatever we're growing, we want to replicate something that's as close to nature as possible."
An IGS facility under construction
"Pay the farmer, not the doctor"
Mike Zelkind of 80 Acres Farms focused less on technology in his presentation - he put the spotlight on the consumer: what do they want? As Mike highlighted, consumers are looking for health and nutrition, flavor and freshness, sustainably-grown products, and trust and transparency.
What they're being offered in the fresh produce market, however, is all about price - it's what Mike calls the '10 cents less mentality'. "There's a race to the bottom, because growers don't believe their produce is worth 10 cents more. The whole category has been commoditized, but produce shouldn't be a commodity." Mike believes that vertical farming can bridge the gap to what the consumer wants, and thus stop this race to the bottom.
To do this, it's important for vertical farmers to understand how to do business. One way to contribute to the advancement of the industry, is by forming true partnerships and ego-less collaboration, Mike argues. "That's why years ago we started looking for partners willing to play by the same rules, so we formed Infinite Acres with Priva and Ocado."
In addition to partnerships, data also plays a big role in vertical farming - both in terms of plant science and predicting customer demand. At 80 Acres Farms, they develop machine learning models to allow them to understand their customers' shopping trends and forecast future demand.
One trend they are looking to reverse is that of increased spending on healthcare and decreased spending on food, as the graph below illustrates. "Your grandparents spent more on food and less on healthcare", Mike says, adding that's it's time to reverse this trend - things like COVID-19 have highlighted the need to focus more on preventative care through healthy eating, like people did in the past. As Mike puts it: "Pay the farmer, not the doctor."
The Vertical Farming World Congress, organized by Zenith Global, is held online September 22-24. We'll post updates from the virtual conference floor in the coming days and weeks, so watch this space for more like this.
Publication date: Thu 24 Sep 2020
Author: Jan Jacob Mekes
© HortiDaily.com
VIDEO: It's A 2-Acre Farm, Packed Into A Shipping Container That Doubles As A Farm Building
The Farm From A Box system is designed to feed 150 people per year and includes drip irrigation, all of the tools, and its own renewable energy setup
The Farm From A Box system is designed to feed 150 people per year and includes drip irrigation, all of the tools, and its own renewable energy setup.
This plug-and-play farming system combines water-smart irrigation, renewable energy, and precision farming technology in a single shipping container that is said to be capable of supporting the cultivation of almost two and a half acres, using regenerative agriculture practices.
We've covered a few different approaches to the "farm in a box" concept, but all of them so far have been built around the idea of growing the crops inside a shipping container, using hydroponics or aeroponics, and artificial lighting. The Farm From A Box is quite a bit different in that the farming takes place outside of the box (or shipping container) and after the contents have been unpacked and deployed, the box itself becomes the hub of the farm infrastructure.
According to the company, this is a "turnkey farm kit" that can be used to build a stronger local food system, especially in food deserts and in the developing world, where infrastructure can be spotty and unreliable at best, and possibly even non-existent. The system is described as being “food sovereignty in a box" that can be a “Swiss Army Knife” for off-grid farming, and while there is a basic template, each unit can be customized to fit the particular situation."
We want to develop this as a rapid response transitional food production system. The box is really infrastructure for places that are struggling with a lack of infrastructure." - Brandi DeCarli, co-founder of Farm from a Box. While the units are designed to be complete systems with all of the core components (minus the land and water rights and labor, of course), the company doesn't just stop there, but also includes a training system to help "new farmers tackle the steep learning curve of permaculture technique." To me, this is one of the critical parts of the venture, because if you've ever tried to grow food on a larger scale than your own backyard, without having any formal training or guidelines to follow, it can be a humbling experience that is full of failures learning opportunities."
Based on extensive field research, we found that rural communities often lack the resources and infrastructure needed to access nutritious food. We developed a toolkit that contains all of the core components needed to grow your own food, on a two-acre plot of land, without the need for an existing grid. Imagine the good it can do by growing local, organic food for a school, or helping jumpstart food production after a disaster. ‘Farm from a Box’ enables and empowers communities to provide for themselves." - DeCarli
Currently, Farm In A Box has a prototype unit operating in Sonoma, California, and a second version is in the works for deployment in the Rift Valley of Ethiopia. Basic units will cost about $50,000, which includes a 3 kW solar PV array, a battery storage system, a drip irrigation system and water pump (which can be fitted to a well or to a municipal water supply), basic farm tools, a sensor package, a seedling house, and a WiFi connectivity package, all packaged into a single shipping container. Other options are available as well, including a water filtration system, an advanced sensor suite, remote monitoring capabilities, and more.
Jake Savageau, COO At FarmBox Foods "There’s A Huge Potential In Helping African Countries Become Self-Reliant And Self-Sufficient”
We offer multiple products that can feed large populations with nutrient-dense food. With mushrooms, we are diversifying that vision because we cannot feed the world with leafy greens alone”, Savageau adds
FarmBox Foods is aiming to scale its production of shipping container farms significantly by the end of 2020. “We have been working with some exciting partners outside the private sector, like Ministries of Agriculture in West Africa. There’s a huge potential in helping African countries become self-reliant and self-sufficient”, Jake Savageau, COO at FarmBox Foods says.
FarmBox Foods holds patents for its vertical hydroponic and mushroom farms. “We are trying to grow the right way, not only in terms of scaling but in separating ourselves from the competition, with logistics as our core tenet. The competition doesn’t focus on logistics like we do, in terms of dealing with governments, and getting our farms deployed all over the world.
We offer multiple products that can feed large populations with nutrient-dense food. With mushrooms, we are diversifying that vision because we cannot feed the world with leafy greens alone”, Savageau adds. “Everyone is growing greens and raising tens or hundreds of millions of dollars, but what I think they are missing is becoming a full-circle food security entity.”
Gourmet mushrooms
Alternative energy solutions
The company is also working on solar power solutions which will eventually be used for running their farms off-grid. Atmospheric water generation technologies are also in the works—a vertical hydroponic farm uses three to five gallons (11.4-19 liters) of water per day. FarmBox Foods has partnered with a Denver company that develops microgrid systems. “As we start working with governments, they won’t be putting just one farm into a warehouse or village. Rather it will be 100 farms or more where there’s limited infrastructure. That’s why we want to ensure that our farms will be fully amenable to off-grid setups.”
It’s not about making money and raising money—it’s about feeding the world. The FarmBox Foods team ultimately offers a solution to a global problem. “We are not the only solution, but I think we are a pretty good one. Our system is very well-thought-out for the end-user. We built the farms to allow for the least amount of labor with the highest yield”, Savageau notes. Currently, FarmBox foods is developing its third product, a root vegetable farm which will allow an entirely new group of crops to be grown in its farms.
Jake Savageau, COO at FarmBox Foods
Savageau continues: “The mushroom farm is a bit different than our previous designs, but we have taken care of everything in just one container. So, from start to finish, we have everything inside that’s needed to produce up to 400 pounds (180kg) of gourmet mushrooms per week. Just like the vertical hydroponic farm, it’s deployable for national disasters or food shortages. There are benefits to small compartmentalized systems because when you have a large greenhouse, it cannot be moved easily. Island nations are particularly well suited for container farming because they can control their food supply in a way that was previously unimaginable”
For more information:
Farmbox Foods
Jake Savageau, COO
jake@farmboxfoods.com
www.farmboxfoods.com
Urban Crop Solutions Launches New "Modulex Plant Factory" on Sept. 9th, 2020
Launch Webinar hosted by Henry Gordon-Smith, CEO of Agritecture, on Sept 9th, 2020 (9 am EDT, 3 pm CEST, 9 pm SGT - 45 minutes)
Register And Get A Sneak Preview on The
New www.urbancropsolutions.com Website
Launch Webinar hosted by Henry Gordon-Smith, CEO of Agritecture,
on Sept 9th, 2020 (9 am EDT, 3 pm CEST, 9 pm SGT - 45 minutes)
Indoor Vertical Farming is a fast-emerging agriculture technology that provides compelling solutions to the United Nation’s Sustainable Development Goals: waste less food and support local farmers (Goal 2), avoid wasting water (Goal 6), and provide decent work (Goal 8).
However, few early adopters are making a profit.
Urban Crop Solutions has worked tirelessly to find a sensible solution to the open issues many investors and growers still face today. The initial Capex or investment cost is high and creates the need for a scalable solution. The unique freshness, taste, and shelf life of the crops go to niche markets with ever-changing needs, which requires a Plant Factory to be extremely adaptable. Also, high labor costs push Indoor Farms to implement more automation and become more efficient.
Based on the experiences and feedback of the customers on the 1st generation products, a new generation Plant Factory was designed from the ground up. The company believes it developed a concept that ‘simply makes sense’.
The ModuleX, the “Sensible Plant Factory” is Scalable, Adaptable, and Efficient.
The ModuleX can be configured between 2 to 64 Grow Modules, which means that the Plant Factory is scalable. One Grow Module contains 86 m² (925 sq.ft) of growing surface, yielding about 6.000 kg/year (13.228 lbs/year) of fresh vegetables. Each separate module features an independent climate and nutrient system, allowing the mix of crops to be adaptable to customers’ needs.
The base price is an industry-low Capex of 1.800 EUR per m² growing surface ex-works (199 USD/sq.ft). The labor costs are reduced by the automated crop-to-person ‘BenchCarousel’. For example, the ModuleX-8 has 8 Grow Modules for a total of 688 m² (7.403 sq.ft). The base price is 1.238.400 EUR (approx. 1.47 mm USD) for an output of 44 ton/year of romaine lettuce (97.000 lbs/year). For mid-sized solutions under 5500 m² growing surface, this is probably the most efficient solution on the market today.
To help people in the long and confusing journey into indoor vertical farming, the company also initiates an end-to-end support program, with a free feasibility calculator, technical support, biological consulting, and contract research. Urban Crop Solutions also developed a Corona-proof support system for training, set-up, startup, and first harvest support of any ModuleX Grow Module, which all can now happen remotely.
Tom Debusschere, CEO of Urban Crop Solutions: “We’ve been listening closely to the feedback of our customers and we found improvements just about everywhere. But the breakthrough invention is the automated BenchCarousel. This new crop-to-person carousel brings any bench of your choice to you within 90 seconds. It also allows us to fit a growing surface of 86m² (925sq.ft) within a 40ft insulated freight container, which we believe is an industry record.
What you really pay for is growing surface, labor, and electricity, and the ModuleX Plant Factory offers a step-change improvement in each. We invite you to take a look at our new website, with the investment cost in full transparency, so you can quickly see which solution is the best fit for you.”
Urban Crop Solutions is an agtech pioneer in the fast-emerging world of ‘Indoor Vertical Farming’. Throughout years of research, 220+ ‘plant growth recipes’ were developed for efficient indoor growing. All drivers for healthy plant growth, such as optimal LED spectrum and intensity, nutrient mix, irrigation strategy, and climate settings are tested and validated daily in the company’s own Indoor Biology Research Center.
To date, Urban Crop Solutions has manufactured container Farms and a Plant Factory for clients throughout Europe, North America, and Asia. Urban Crop Solutions’ commercial farms are being operated for vegetables, herbs, and micro-greens for food retail, foodservice, and industrial applications. Research institutions operate the growing infrastructure of Urban Crop Solutions for scientific research on banana seedlings, flowers, hemp, and many more.
Visit www.urbancropsolutions.com for a full virtual tour.
For more information: www.urbancropsolutions.com
Brecht Stubbe, Sales Director brst@urbancropsolutions.com
Maarten Vandecruys, CTO mava@urbancropsolutions.com
Tom Debusschere, CEO tode@urbancropsolutions.com
European headquarters: Regional headquarters:
Grote Heerweg 67 800 Brickell Avenue, 1100 Suite
8791 Beveren-Leie (Waregem) Miami (FL 33131)
Belgium Florida
(+32) 56 96 03 06 +1 (727) 601 7158
Facebook: www.facebook.com/urbancropsolutions
Twitter: www.twitter.com/U_C_Solutions
LinkedIn: www.linkedin.com/company/urbancropsolutions
YouTube channel: http://www.youtube.com/c/UrbanCropSolutions
Instagram: https://www.instagram.com/urbancropsolutions/?hl=en
45 Years Logiqs: From Container Systems to Vertical Farming and Warehouse Automation
Nowadays Logiqs supports most horticulture crops grown in greenhouses as well as a large variety of hydroponic crops
45 years ago, on July 1st, 1975, the Logiqs journey began, together with the founding of Intransit B.V. (the company’s initial name).
And even though the company name and shareholders may have changed since then, they still look back at this date as the very beginning of the company.
"At the start, the main goal of our company was to design and build innovative and reliable benching systems for potted plant growers, that add true value to the customer’s business.
"This initial focus has held up very well throughout the years and has produced amazing results for our customers, with thousands of acres of Logiqs benching systems operational in greenhouses all over the world.
"This success has allowed us to expand our area of expertise to serve a much wider range of growers as well as a couple of new industries."
Nowadays Logiqs supports most horticulture crops grown in greenhouses as well as a large variety of hydroponic crops.
"Our experience working with some of the most successful growers in the world, encouraged us to also apply our know-how and expertise to the Vertical Farming industry. This amazing collaboration with our customers allowed us to quickly become one of the industry leaders and trendsetters in automated vertical farming.
"Beyond greenhouse cultivation systems and Vertical Farming, we have also made incredible steps in warehouse automation by developing the innovative iCUBE Automated Storage and Retrieval System.
"We are grateful to all of our wonderful customers and partners who have influenced us to get better, and we hope that we can continue to repay their trust in the coming decades.
"We would also like to take this opportunity to thank all Logiqs team members that have devoted their time, energy, and passion to our common goals in the past 45 years.
"Without these devoted and talented individuals, Logiqs could have not evolved into the company it is today.
"We are extremely excited to think of the impact that our talented colleagues will have moving forward on the future of Logiqs, and on the future of horticulture, agriculture, and logistics."
For more information:
Publication date: Thu 2 Jul 2020
SWITZERLAND: Vertical Farming Exclusively For Migros Basel - First Products Available In MParc Dreispitz
After several months of construction, the Vertical Farm on the Wolf site is ready for production. Here, Growcer produces regional foods in a weather-independent, environmentally friendly and water-saving manner exclusively for Migros Basel, delivering them quickly to the branch thanks to the shortest transport routes
After several months of construction, the Vertical Farm on the Wolf site is ready for production. Here, Growcer produces regional foods in a weather-independent, environmentally friendly, and water-saving manner exclusively for Migros Basel, delivering them quickly to the branch thanks to the shortest transport routes. The first six Vertical Farm products will be available from 16 June at the MParc Dreispitz.
Create a cultivated area of more than 1.500m2 on an area of less than 400m2?
This is possible thanks to vertical farming. Last autumn, Growcer, and the Migros Basel cooperative launched a collaboration with the aim of building Switzerland's first "Robotic Vertical Farm" on the Wolf site in Basel. The motivation was not only to build the farm of the future but above all to establish a regional, sustainable, and environmentally friendly concept that would bravely face the challenges of the coming decades.
View into the vertical farming plant in Basel / Picture: Growcer AG
After only six months, the three halls have now been completed and the first products are ready for harvesting. From 16 June, the "Vertical Leaves" product range, consisting of pak choi, wasabi rocket, spring cabbage, chard, and red and green lettuce, will be available exclusively at the MParc Dreispitz. These are primarily products that have not yet been available regionally in this form from Migros Basel and thus complement the range of existing regional producers. The fresh leafy vegetables can be used in the cold kitchen as a salad or salad ingredient, but also in the hot kitchen for wok dishes or as the icing on the cake for other hot dishes. At a later date, it is planned to produce other products all year round and to supply other branches.
Weather-independent and resource-efficient
The plants are grown on the farm from seed to harvest and packaging. Light, temperature, humidity and nutrients are carefully measured and adapted to the requirements of the respective variety. In harmony with modern technology and always up-to-date information, the growers' staff can thus respond to the needs of each individual plant. This special care can almost completely prevent crop failures.
According to recent studies, urban vertical farming uses 90% less water and requires practically no harmful pesticides. In addition, scarce space can be used more efficiently and the proximity to conurbations keeps transport routes, and thus the resulting environmental pollution low. This innovative and future-oriented form of cultivation meets the customers' desire for more regionality, sustainability, and resource efficiency. Those interested in learning more about the products, the cultivation, or the advantages of vertical farming in Basel will soon be able to form their own opinion as farm tours with tastings will soon be offered on the Wolf-site.
For more information:
Growcer AGSt. Jakobs-Strasse 200/Halle 4
4052 Basel
https://growcer.com/
Publication date: Mon 22 Jun 2020
VIETNAM: Shipping Container Farm - Growing Strawberries Indoors in Vietnam
At the 88.17 hectare Agriculture High Tech Park in Ho Chi Minh City, Center for Business Incubation of Agricultural Hi-Tech (AHBI), a first batch is underway with 100% indoor cultivated strawberries. The first batch was planted earlier this year and harvest is expected within 3 months
At the 88.17 hectare Agriculture High Tech Park in Ho Chi Minh City, Center for Business Incubation of Agricultural Hi-Tech (AHBI), a first batch is underway with 100% indoor cultivated strawberries. The first batch was planted earlier this year and harvest is expected within 3 months. The AHBI serves as a testing lab as well as an educational centre to stimulate the development of advanced horticulture in the region.
Meeting the demand for fresh organic produce
Ph.D. Hoang Anh Tuan, Deputy Director of AHBI, talks about how the cultivation is doing and what the challenges and opportunities are. “The demand for fresh and affordable strawberries is increasing across Asia. Our aim is to grow strawberries all year round and near the city”, says Ph.D. Hoang. Until recently, growing strawberries in Ho Chi Minh is not possible due to the local climate. With improvements in climate control, many parameters could be controlled but the right lighting with easy controls was not available until HortiPower launched in Vietnam.
Upgrading yields and more investments
While Vietnam is already known as a significant agricultural producer, its farmers are increasingly looking to upgrade production capacity and increasing yields. PhD Hoang explains: “New generation growers are looking to maximize the yield per square meter with high-value cultivars, to lower the energy use per fruit and affordable solutions to help them start.” There is also a push from private investors, but they are looking to start with technologies and investments that can scale, rather than a large upfront investment with long payback term.
“To support private investors and help them move towards high-tech agriculture we introduced hydroponic container farms. It allows us to control the climate which enables us to grow a high value crop and to grow all year round”.
“The initial investment is reasonable and has only a 2-year payback. They allowed us to do a trial so we would have our own data about potential production results”.
Growing high quality strawberries and producing them year-round has remained a challenge when growing in the field. Growing strawberries in consistent size and quality will require the right lighting, so that the production process becomes more predictable and the yield increases. Consumers indicate that they are prepared to pay more for overseas strawberries that are larger, sweeter and have a softer, smooth skin compared to the local varieties grown normally in the region. Getting the right lighting is very important when growing fully indoor. “We’ve evaluated many different lighting fixtures from other companies. We had the best results with HortiPower since its lighting system allowed us to completely control lighting distribution, the intensity and spectrum. It can also run lighting algorithms without the need for a local onsite computer.”
“Since last year we have actively visited several growers onsite to understand their needs and challenges. We are working closely with a team of our own researchers and several universities to provide suitable lighting solution for many laboratories in the region”, says Katherine Tran - Sales Director of PTP Vietnam which represents HortiPower.
Starting in the spring
This spring, new LEDs from HortiPower were installed. Each shelf has 4 fixtures for an even distribution of light. And with a fully adjustable µmol intensity and spectrum, the strawberries can get exactly what they need at each stage of strawberry cultivation. Supporting plant growth, flowering, and fruiting may require different lighting which affects the nutrient production, quality, taste, and brix. The new lighting also gives better control of harvest times, which is commercially relevant to get ready just before the popular spring festivals and other dates with peak consumer demand.
“With HortiPower we are able to control the exact amount of light intensity, spectrum and ratio. We are now able to control the growing process in a much better way.”
Katherine Tran during A/B testing at AHBI
The right lighting
AHBI evaluated horticultural lighting and chose HortiPower with a spectrum of plant-centric red, green, blue, white, and far-red. This spectrum not only produces the desired stem elongation, but it also makes it possible to achieve a higher yield of strawberries with a low percentage of malformed fruit. The team evaluated various models and chose the linear 20W version with full control on intensity and ratio. “We’re excited and look forward to delivering delicious strawberries all year round”, says the Deputy Director with a smile on his face.
For more information:
HortiPower Asia
Katherine Tran - Sales Director
info@hortipower.com
HortiPower Research
Jille Kuipers – Innovation Manager
info@hortipower.com
www.hortipower.com
Publication date: Mon 8 Jun 2020
Shipping Container Farms Come to London as Growers Ditch Soil
In the era of climate change and Brexit, British farming is facing unprecedented challenges. How to supply environmentally friendly, locally sourced, and competitively priced food?
Vegetables Are Grown Vertically Supplied With Nutrient-Rich Water
20 June 2020
Racks of vegetables grown in a shipping container in London CREDIT: Fiona Hanson
In the era of climate change and Brexit, British farming is facing unprecedented challenges. How to supply environmentally friendly, locally sourced, and competitively priced food?
One part of the answer could lie in a shipping container in an east London car park, just moment’s away from the capital’s business district. Inside are racks of leafy green vegetables, grown vertically using hydroponic technology. Instead of being planted in soil, the vegetables are plugged into a system of nutrient-rich water and kept at the optimal temperature, under specially designed lighting.
The result is flavorsome lettuces, kale, basil, and other leaves, free of pesticides and using up to 95 percent less water than traditional agriculture over a fraction of the space. The shipping containers, which are custom made, mean the produce can be located virtually on the doorstep of its market, effectively eliminating food miles.“
Traditional organic farming is not sustainable if we're going to feed a population,” says Sebastian Sainsbury, the founder of Crate to Plate, which has just had its first harvest.
Not only does Crate to Plate use otherwise wasted space - these three shipping containers can grow the equivalent of an acre’s soil - but the proximity to customers keeps the produce fresh.“ When you harvest the lettuce from the soil, within 48 hours, you've lost 40 percent of the nutritional value. And it goes down every day,”
Indoor farming has boomed in recent years, particularly in the US, where Mr. Sainsbury lived until recently and where he developed his business.
But the UK is yet to fully capitalize on its opportunities, says Dr. Robert Hancock of the James Hutton Institute, which is supporting pioneering vertical farming techniques from its facility in Dundee.“
Even with current technologies and current efficiencies, there's probably a lot more that can be done. And I think that indoor farming can interface a lot more with the broader agricultural picture,” he said.
Lead Farmer of Crate to Plate, a hydroponic vertical farm producing leafy greens and herbs.
CREDIT: Fiona Hanson
Environment Secretary George Eustice this week said vertical farming would have a vital role to play in helping British farming meet the challenges of climate change and post-Brexit food security.
“There are a lot of pressures on land use,” he told the parliamentary environment committee, highlighting “the tricky issue” of repairing biodiversity and soil health in our intensely farmed landscapes.
Mr. Hancock highlighted the UK’s strawberry industry, which relies on imports of propagated plants from the Netherlands, as one example of where indoor farming could boost British production. Britain produces just 7 percent of its fruit and 53 percent of its vegetables. But ultimately, he says, vertical farming can only ever be part of the answer and will likely be limited to salads, berries, and niche crops.
“The replacement for calorie crops I don't think is ever going to happen,” he said.
Crate to Plate is the latest of several hydroponic farming ventures started by those outside of traditional agriculture (Mr. Sainsbury is an ex-banker), many of which haven’t translated to long-term success. The key to seeing vertical farming at scale will be getting more existing farmers on board, says Mr. Hancock.“
They understand the economics of growing.
And they also understand the routes to market,” he said.
The government is hoping that the end of the EU's Common Agricultural Policy could be a chance for new blood to enter the agricultural industry, and will offer older farmers a “golden handshake” if they retire early.
Mr. Sainsbury employs three recent agricultural graduates and says the younger generation are eager to explore new technologies. He has also had interest from farmers keen to locate his shipping containers on their land.
So far, Crate to Plate’s economies of scale and niche produce puts them out of reach of the average supermarket shopper (think £10+ salads marketed to City workers). But they have hopes of moving into residential areas, amid a growing trend for urban farming. The dream, says Mr. Sainsbury, would be a vegetable farm in every urban neighborhood, manned by a dedicated farmer and producing fresh produce for everyone to buy.“
The aim is to make it as local as possible,” he said.
NEW YORK: Vertical Farming Takes Root in Hudson Valley
Vertical Field launched in Israel in 2006 as an agricultural supply solution for the nation’s urban markets. Miner stated the firm began as a “green wall company” that took the horizontal aspect of rooftop gardens and switched it on its side
By Phil Hall
June 20, 2020
Among the more disturbing aspects of the COVID-19 pandemic involved food costs and supplies. The U.S. Department of Agriculture reported a 2.6% increase in food prices nationwide from March to April, marking the largest monthly increase in 46 years. These increases have been fueled by disruptions in the supply chain due to worker illnesses in processing plants.
For restaurants and food retailers, not being able to access materials or being charged higher-than-normal exacerbates an already acute problem of trying to maintain revenue streams during the pandemic.
However, a pair of regional businesses have begun using agricultural technology from the Israeli company Vertical Field that takes the farm-to-table concept and turns it into a container-to-table approach.
“The way it works is that we take a container, just the standard shipping container,” explained Sam Miner, Vertical Field’s U.S. launch manager.
“And the main thing that we do is we put these modules on the wall that have irrigation lines behind it. We simply fill those modules with soil and we put in the right lighting equipment. And once you put plants in there, they just grow fairly simple.”
John Lekic, chef and owner of Poughkeepsie’s Farmers & Chefs restaurant, poses in front of his Vertical Field container used for growing greens and herbs. Photo courtesy Vertical Field.
Vertical Field launched in Israel in 2006 as an agricultural supply solution for the nation’s urban markets. Miner stated the firm began as a “green wall company” that took the horizontal aspect of rooftop gardens and switched it on its side.
The company now has 400 projects around the world, including a massive installation in Vietnam that Miner described as being “tremendous, like a football field.”
This spring, Vertical Field made its way into the U.S. market through a pair of Hudson Valley installations. John Lekic, chef and owner of Poughkeepsie’s Farmers & Chefs restaurant, learned about the technology at a Culinary Institute of America symposium in late 2019 and was intrigued about operating his own food source.
“We were planning to bring in the container in March and we actually brought in a container days after the emergency thing was declared in New York,” he said. “It was a perfect timing. Ten days later, we planted our first crop, mostly salad greens, and in the middle of May we already had to harvest. We are going to have a third one this week.”
Lekic praised the technology for allowing several harvests per week, noting the ability to “harvest them the day of serving.” He also praised the user-friendly aspect of the 20-foot containers.
“It’s super easy to maintain,” he said. “Once the container is set up and the mechanism is in place, you have an app that does the irrigation and controls the temperature and the humidity. It’s not really complicated — after you do it once or twice, the planting and everything else becomes really easy to maintain. It does not require a lot of time.”
Lekic is now growing herbs and leafy vegetables in the containers, adding “it’s still a playground for us.”
Another Hudson Valley business that has Vertical Field’s technology in place is the Evergreen Kosher supermarket in Monsey, which installed its containers at the end of May. Menachem Lubinsky, president of Brooklyn-based Lubicom Business Consulting and marketing director for Evergreen, praised the product for creating a speedy supply of produce.
“If something takes normally three months to grow, the technology can accelerate that to three weeks,” he said. “A restaurant or a supermarket can be in control of their supply.”
Lubinsky said he reached out to Vertical Field following news reports during the pandemic of truckers not being able to deliver goods and farms destroying crops because they suddenly had no outlets for selling. Besides selling the harvested crops, Evergreen is planning to make the containers a visitors’ attraction.
“The customer will be able to see the process of how it grows because one of the walls of the container is glass,” he said. “It’s kind of like an educational experience just for a family to go over to see how this whole process grows. And there’s a very large kosher constituency there who are concerned about consuming insects. This eliminates that concern because of the way it grows — it is insect-free.”
Lubinsky said that Vertical Field is planning to build on its technology to accommodate the growing of a wider variety of items, including strawberries and vegetables.
VIDEO: Top 5 Benefits of Container Farming At Your Co-Op
Are you looking for a fresh addition to your co-op grocery store? Adding a container farm allows your store to be the source of some of the freshest, locally-grown, resource-efficient produce
Stephanie May 26, 2020
The Yellowknife Co-op added a Growcer container farm to their co-op to provide year-round produce to their members.
Are you looking for a fresh addition to your co-op grocery store? Adding a container farm allows your store to be the source of some of the freshest, locally-grown, resource-efficient produce.
Here are five benefits to adding a hydroponic container farm steps away from your store:
1. MORE ROI FOR PRODUCE YEAR-ROUND
Growing your own produce reduces your reliance on suppliers and allows you to avoid supply chain mark-ups. You can sell fresher produce year-round at better margins than what you can with supplied produce.
What can you grow? Lots. Anything from kale, spinach, lettuce, bok-choy, herbs, and more, can be grown within a Growcer system and you can switch it up based on consumer demand.
We’ll help you create a brand that your members will recognize and keep them coming back to your store!
2. MEMBER SATISFACTION AND RETENTION
Container farming allows you to create a unique experience for your customers. Customers can:
request what produce is grown;
purchase store-brand produce or prepared goods; and
at the Yellowknife Co-op, customers can see the produce being grown through a screen - a special experience not typically seen in chain stores.
These special touches build engagement and help with member retention.
3. EMPLOYEE ENGAGEMENT
The Growcer system is made to “plug and play” and it takes one week of on-site training to have employees comfortable with the system. Your co-op’s container farm becomes a source of pride and oasis for employees who enjoy participating in the growing process from beginning to end.
Justin Nelson, general manager of The Yellowknife Co-op, put it best: “On a cold dark day in Yellowknife, there’s no better place to be than inside the Growcer unit. When you’re actually harvesting the product that you’re selling it’s a great feeling”.
For co-ops, Growce’s units can be operated by existing employees who see it as an opportunity to take pride serving their community.
4. REDUCED ENVIRONMENTAL IMPACT
Container farming grows a variety of produce in a controlled environment that is time, space, and resource-efficient. The best part? Your container farm can be located steps away from your store eliminating the need to transport produce long distances.
At the Yellowknife Co-op, produce is harvested immediately before it’s sold and this method eliminates the need for plastic packaging.
Growcer’s container farms are an innovative way to stand out from competitors and provide quality produce to your members.
5. DEMONSTRATE INNOVATION
Embrace efficient growing systems that bring fresher produce to your customers and cement your store as a leader who is embracing agriculture technology.
Your membership invests in you - repay their loyalty by pushing the boundaries of what’s possible. The real value is not only the produce grown, but the ability for a container farm to offer your business a local source of produce, a source of diversified employment, and an additional stream of revenue.
Take the first step and plug in your specifics into our ROI calculator to evaluate the feasibility of a container farm for you.
Indoor Ag-Con Kicks Off New Webinar Series With United Fresh Produce Association Panel
Indoor Ag-Con LLC, producers of the premier event for the indoor|vertical farming industry, is launching a free monthly webinar series to share content originally planned for its May 2020 in-person annual conference that has been postponed due to the Covid-19 pandemic
INDOOR AG-CON KICKS OFF NEW FREE WEBINAR SERIES WITH UNITED FRESH PANEL DISCUSSION ON PRODUCE TRENDS, BUSINESS OPPORTUNITIES FOR INDOOR GROWERS
Free Monthly Virtual Events To Share Content Originally Planned For May 2020 Annual In-Person Conference Postponed Due to Covid-19 Pandemic
LAS VEGAS ( May 20, 2020) – Indoor Ag-Con LLC, producers of the premier event for the indoor|vertical farming industry, is launching a free monthly webinar series to share content originally planned for its May 2020 in-person annual conference that has been postponed due to the Covid-19 pandemic. Titled “Indoor Ag-Conversations,” the new virtual event series kicks off with the United Fresh Produce Association Panel: Produce Trends & Business Opportunities For Indoor Growers Emerging From Covid-19 Pandemic on Wednesday, June 3 at 4 pm EST.
Moderated by United Fresh President and CEO Tom Stenzel, the panel will include Alex DiNovo, President and COO, DNO Produce and Paul Lightfoot, President and Founder, BrightFarms.
“While Covid-19 has temporarily halted our opportunity to gather face-to-face for Indoor Ag-Con, it has not stopped us from sharing the incredible innovations and business-building opportunities our vibrant industry offers,” says Brian Sullivan, co-owner of Indoor Ag-Con. “We’re honored to have the United Fresh Produce Association kick off our first webinar with such a dynamic panel of industry leaders talking about the unprecedented challenges and opportunities we’re facing today.”
“Now more than ever it’s critical that we continue to find new ways to connect with industry peers to share industry ideas and experiences,” adds Tom Stenzel, President & CEO, United Fresh Produce Association. “Indoor growing is an important component of the fresh produce industry, and we’re excited to lead the first Indoor Ag-Con webinar on June 3 as we look ahead to our own new free virtual event, United Fresh Live!, coming the week of June 15.”
With plans to feature one to two sessions each month, the new Indoor Ag-Conversations webinar series will feature content originally planned for the now postponed Indoor Ag-Con 2020 Conference line-up, as well as new sessions designed to help industry members find new ways to grow their business.
Scheduled for June 3 at 4 pm EST, the Indoor Ag-Conversations United Fresh panel will share insights from (pictured clockwise from top left):
Moderator Tom Stenzel, the President and CEO of the United Fresh Produce Association, is a frequent speaker on industry issues and has been recognized for his leadership frequently throughout his career. Tom has testified numerous times before Congress, and works closely with leaders at the White House, USDA, FDA, and other U.S. regulatory agencies. He also leads the United Fresh Start Foundation, the association’s charitable foundation focused on increasing children’s access to fresh fruits and vegetables. The Foundation and its partners have donated more than 5,000 salad bars to schools in all 50 states.
Paul Lightfoot, President and Founder of BrightFarms, is creating the first national brand of locally grown produce. In four years, Lightfoot has led the company from a proof-of-concept to operating four greenhouses in key markets like Washington, D.C., Chicago, Cincinnati, and Philadelphia. BrightFarms was named 235th on the 2017 Inc. 500 list of fastest-growing private companies, ranking 10th among all food companies and the only produce company featured on the list.
Alex DiNovo is President and COO of DNO Produce Group of Companies, a rapidly growing family-owned group of businesses located in Columbus, Ohio. DNO is a fresh fruit and vegetable processor, as well as a distributor, with a distribution network throughout the Midwest, Great Lakes, and the southeastern United States. DNO distributes to customers both directly and indirectly through its network. Alex is a fourth-generation family member who has been involved in the produce business from a young age. He has knowledge and experience in many areas of the produce supply chain.
Indoor Ag-Conversation webinars are free to industry members. To register for the upcoming June 3, 2020 session, visit www.indoor.ag/webinar. In addition, the Indoor Ag-Con team is currently exploring dates and options for its postponed May 2020 in-person event and will be providing updates soon.
ABOUT INDOOR AG-CON LLC
Founded in 2013, Indoor Ag-Con touches all sectors of the business, covering produce, legal cannabis, hemp, alternate protein and non-food crops. In December 2018, three event industry professionals – Nancy Hallberg, Kris Sieradzki and Brian Sullivan – purchased Indoor Ag-Con LLC, setting the stage for further expansion of the events globally. For more information, visit: https://indoor.ag
ABOUT UNITED FRESH PRODUCE ASSOCIATION
United Fresh brings together members across every segment of the supply chain to build relationships that are as solid with a handshake as with a contract. We empower industry leaders to join forces to shape sound government policy. We deliver the resources and expertise companies need to succeed in managing complex business and technical issues. For more information, visit: https://www.unitedfresh.org and to learn more about United Fresh LIVE! Visit www.unitedfreshlive.org
SPECIAL THANKS TO INDOOR AG-CON 2020
SPONSORS, EXHIBITORS MEDIA ALLIES & INDUSTRY PARTNERS
In addition, Indoor Ag-Con is proud to be a member of the Hemp Industries Association.