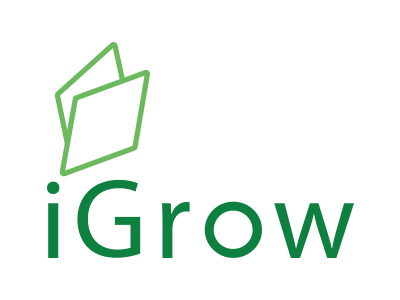
Welcome to iGrow News, Your Source for the World of Indoor Vertical Farming
BrightFarms’ Indoor Farming System Lands $30M to Grow
Leafy greens and tomatoes don’t have to travel hundreds of miles to reach salad plates anymore.
Consumers can easily make garden salads year round because grocery stores get their greens from farms across the country where items like lettuce are always in season. But those leafy greens and tomatoes don’t necessarily have to travel hundreds of miles to reach salad plates.
Agtech startup BrightFarms uses indoor farming to try to shorten grocery store supply chains, and also lower costs by using less land, water, transportation fuel, and pesticides than traditional farming. The New York-based company announced last week that it raised $30.1 million from investors to take this greenhouse model to new markets across the country.
The BrightFarms investment eclipses the $18 million raised by Harrisonburg, VA-based Shenandoah Growers earlier this year. That company, which sells herbs and herb plants grown in its greenhouses, raised funds from S2G Ventures and Middleland Capital, according to AgFunder. Despite those deals, indoor agriculture remains a small part of overall agtech investment.
The technologies claiming most of the $1.8 billion in global agtech investments in the first half of the year were food e-commerce, biomaterials and biochemicals, soil and crop technology, and precision agriculture, according to AgFunder. That six-month total marked a 20 percent decline compared to the same period in 2015. Indoor agriculture accounted for $21 million across 10 deals in the first half of 2016—just 1 percent of all agtech funding raised and just 3 percent of all deal flow, according to AgFunder. Still, a number of startups, including BrightFarms, are betting on consumer and investor interest in indoor farming.
The indoor farming market is shaking out into several segments. BrightFarms is a food supplier, distributing the food it grows to contracted retailers, who in turn sell the produce to consumers. That’s the same approach taken by Brooklyn, NY-based startup Edenworks, which grows produce inside a warehouse and supplies stores in New York. Other companies are providing businesses with the hardware to do their own indoor farming. Atlanta-based PodPonics, for example, sells shipping containers and software to manage food-growing operations inside them. Boston-based Freight Farms also sells refashioned shipping containers outfitted with LED lights and climate controls.
Some startups are bringing indoor growing options directly to consumers. Somerville, MA-based Grove sells high-tech growing cabinets that consumers can place in their homes. And Cambridge, MA-based SproutsIO, which like Grove shares MIT roots, has developed a microfarming system that fits on a kitchen countertop.
All of these startups pledge to provide locally grown food that reduces water use and eliminates pesticides. For its part, BrightFarms claims its greenhouses use 80 percent less water, 90 percent less land, and 95 percent less shipping fuel compared with crops grown outdoors and shipped to market via conventional supply chains.
BrightFarms currently operates greenhouses near Chicago, Philadelphia, and Washington, DC. It says it has long-term, fixed price contracts to provide produce to several supermarket companies including Mariano’s, a Chicago-area grocery retailer owned by Kroger (NYSE: KR); ShopRite, whose footprint includes New York and New Jersey; and Giant Foods, which has stores in the central Atlantic states.
When BrightFarms opened its newest greenhouse in Illinois, CEO Paul Lightfoot told the Chicago Tribune that the 160,000 square-foot facility cost about $10 million, which included land acquisition and construction. In the funding announcement, the company did not say where it will use the fresh capital to expand.
Frank Vinluan is a contributing editor at Xconomy, based in Research Triangle Park. You can reach him at fvinluan@xconomy.com Follow @frankvinluan
High Times: Vertical Farming Is On the Rise — But Can It Save the Planet?
Farming as we know it is failing.
Farming as we know it is failing. Mom-and-pop operations are struggling to survive and Big Ag cares far more about its bottom line than about your health, or the health of the planet. Ecologists, anti-GMO activists, even sticker-shocked soccer moms in the produce aisle agree: It’s time for a revolution. Now, some experts are saying, this revolution may come via vertical farming, in which produce is grown indoors, in stacked layers. After years of technological trial and error, the practice is primed for blastoff.
The basic idea is not new. For centuries, indigenous people in South America pioneered layered farming techniques, and the term “vertical farming” was coined by geologist Gilbert Ellis Bailey in 1915. But the need for its large-scale implementation has never been greater. Under our current system, U.S. retail food prices are rising faster than inflation rates, and the number of “food insecure” people in the country — those without reliable access to affordable, nutritious options — is greater than it was before the era of agricultural industrialization began in the 1960s. And we’re only looking at more mouths to feed; according to the UN, the world’s population will skyrocket to 9.7 billion by 2050, an increase of more than 2.5 billion people.
Additionally, climate change is threatening the sustainability of our current food production system. Rising temperatures will reduce crop yields, while creating ideal conditions for weeds, pests and fungi to thrive. More frequent floods and droughts are expected, and decreases in the water supply will result in estimated losses of $1,700 an acre in California alone. Because the agricultural industry is responsible for one-third of climate-changing carbon emissions, at least until Tesla reimagines the tractor, we’re trapped in a vicious cycle.
So how do we break out?
“We have to extinct outdoor farming,” Dickson Despommier, PhD, emeritus professor of microbiology and public health at Columbia University and author of “The Vertical Farm: Feeding the World in the 21st Century,” told Salon. “We have to put the earth back to the way it was when trees were the most abundant crop. If we paid farmers to plant carbon-sucking trees instead of corn — what’s called carbon farming — the earth’s atmospheric makeup could be completely different in 20 years’ time. But this means looking elsewhere for a food source.”
In vertical farming, that food source starts with a building – any building – usually comprising more than one floor. On every level are flat racks of plants taking root not in soil, which is unnecessary for growth, but instead in a solid, sustainable, and pesticide-free substrate, like mashed-up coconut husk. In these hydroponic systems, plants are fed a nutrient solution from one of a variety of devices, including a misting nozzle, a slow-feed drip, and a wicking tool (like the volcanic glass called perlite) that carries nutrients from an in-house reservoir directly to the roots.
CA Farmers Use Advanced Drone Tech to Save Water http://videos.tout.com/dry/mp4/7ef39d7e62d9b298.mp4
The buildings are equipped with artificial lighting in place of sun, and they’re temperature and humidity controlled. Unlike in the great outdoors — where wind, precipitation, and season are out of a farmer’s hands — growing conditions are controlled and plants are able to reach maturity twice as fast. Often, the spaces are hermetically sealed to prevent common plant diseases, like wheat rust, from blowing through. And the final product? It tastes the same as crops grown outside, even better if those outside crops came from degraded soil. While leafy greens have traditionally been the most cost-effective crop to grow indoors, improved technology is also allowing for a broader range of options (think tomatoes, berries and ramps).
Vertical farming operations are sprouting in the U.S. and around the globe. Earlier this year, the $39 million AeroFarms, comprising 12 layers spread over 3.5 acres, opened in an old steel mill in Newark, New Jersey. Production yields the equivalent of 13,000 acres of farmland in the region. It also utilizes 95 percent less water than traditional vegetable farms since the H2O is recirculated.
In Philadelphia, Metropolis Farms, which already operates the world’s first vegan-certified vertical farm in North America, is planning a network of 10 vertical projects throughout the city, including the world’s first solar-powered vertical farm. Because the technology has advanced so much in recent months, according to president Jack Griffin, this network will cost 5 percent of what AeroFarms did, require 80 percent less real estate, and allow for a greater yield. Similar projects are seeing success in Japan and Berlin —and in Sweden, a plantagon, or plantscraper, 16 stories tall is in the works.
The goal, in addition to creating green-collar jobs, is to bring nutritious produce to urban areas where high-quality, fresh food is hard to come by. With 70 percent of the world’s population expected to reside in cities by 2050, utilizing agritecture to eliminate these food deserts is an increasingly attractive option. In the U.S., $32 million in venture capital was invested in indoor agriculture in 2014, and proponents say the industry has a revenue potential of $9 billion.
But not everyone is convinced the idea won’t go to seed. Early this year, in an article for Alternet, environmental writer Stan Cox argued against growing food in high-rises because of the method’s large energy requirement — specifically, the need for LED lighting in lieu of sunshine. Louis Albright, PhD, emeritus professor of biological and environmental engineering at Cornell University, called vertical farming “pie in the sky” for the same reason.
“The sun is equivalent to $400,000 worth of electricity per acre when growing outdoors,” Albright told Salon. “What vertical farming can save in transportation costs is quite small comparatively. It’s not viable.”
But proponents of vertical farming say such rebukes are based on outdated information — the efficiency of LED lighting has increased dramatically, by 50 percent between 2012 and 2014. Progress is expected to continue — the U.S. Department of Energy has recently adopted new LED efficiency standards, set to be finalized by January 2017. Meanwhile, vertical farms are hiring engineers and ergonomists to reduce the footprint even further.
“We designed our own LED lights to dial into wavelength spectrums,” Allison Towle, director of community engagement at the Los Angeles vertical farm Local Roots, told Salon. “We control them to emit only red or only blue or only white light, whichever helps a specific plant grow, which reduces energy output. Our R&D phase was two years long, because we developed these specific recipes, meaning for each plant we determined the right kind of lighting, the right nutrient makeup in the water, and the right amounts of each. This has brought outdoor growth times down by 40 percent.”
Robert Colangelo of the Indiana-based Green Sense Farms, which has 10 new projects in the deal pipeline, says improvements in LED efficiency are largely responsible for his current expansion, which involves building a network of vertical farms throughout the U.S., Canada, Scandinavia and China. The plan is to launch at points of consumption — grocery stores, hospitals, colleges and military bases — for direct-to-consumer sales. The food will be fresh, and the distribution-related carbon emissions, nonexistent.
“Comparing the energy requirement of growing outdoors versus growing inside is like comparing apples and oranges,” Colangelo told Salon. “We use LED lighting and they use sunlight. But they need tractors and other mechanical equipment, more water, fertilizer. It’s two different growing processes. Instead of comparing them, look at the crops and evaluate the most sustainable way to grow each one. Commodity crops, like soybeans, will likely always be grown outdoors. Leafy greens are better inside. What vertical farming has done is stratified the industry.”
In the future, some vertical farmers, like Colangelo, are looking to incorporate biopharmaceuticals into their growing rosters. And NASA, which counts itself as a vertical farming pioneer, may end up using the method for growing food on other planets, in a more sophisticated version of the techniques used in “The Martian.” But for now, the industry is still in its infancy.
“It’s like the beginning of the Internet, or even the Internet 10 years ago,” Despommier told Salon. “Look how far that’s come. There are people who looked at the airplane and thought: ‘That will never fly.’ But people are going to continue innovating. In 10 years’ time, we’ll all be getting our food this way.”
Bay View Grows Mushrooms
Mushrooms don’t require as much light as vegetables, making them a good fit with indoor urban farming.
Three urban farmers are growing mushrooms in an old industrial building on Milwaukee’s south side, using coffee grounds from local coffee shops as mushroom food, and selling the finished fungi to restaurants.
Grow Local, a natural-foods business from Neenah in the Fox Valley has the 6,000 square-foot mushroom operation in the old W.B. Bottle Co. building at 822 E. Bay St. in Milwaukee's Bay View neighborhood.
Grow Local owners Steve Catlin, Calvin Andersen and Alex Fehrenbach share the building with other businesses, including a furniture store and a carpentry shop. They grow about 100 pounds of mushrooms a week for restaurants, with plans to boost that to 500 pounds a week over the next year.
By Rick Barrett
“We are in full production mode, but we are still investing more in this space, building out our system and network,” Catlin said.
Mushrooms get their nutrition by metabolizing nonliving organic matter. The Grow Local mushrooms’ food includes coffee grounds from Stone Creek and Kickapoo coffee shops.
The fungi are grown in a big, open room that’s essentially a humidity and light-controlled greenhouse.
Catlin developed a system for growing the gourmet mushrooms, including the shiitake and oyster varieties, that uses coffee grounds, sawdust and wood chips as the substrate.
Mushrooms don’t require as much light as vegetables, making them a good fit with indoor urban farming.
“I am kind of an evangelist for getting people to grow mushrooms. You can grow them on your own if you can maintain a semimoist mulch bed,” Catlin said.
Catlin is a 2011 Marquette University graduate, with a degree in psychology and philosophy. Andersen and Fehrenbach are University of Wisconsin-Madison graduates with degrees in biological systems engineering and geography.
Their business produces greens, herbs and fish in Neenah, and the mushrooms in Milwaukee.
Most of Grow Local’s products are sold in the Fox Valley, but it also sells to some Milwaukee-area restaurants. The business aims to develop a direct-to-consumer market that would partner with other farmers and would provide customers with information on how their food was produced.
Catlin said he wants to offer people year-round the experience they get at farmers markets. "You look the farmer in the eye, and that person tells you the reasons why their product is good,” Catlin said.
The Bay View neighborhood — with its young, health-conscious residents — could be a prime location for that.
“One of our niches is year-round production of chemical-free products,” Catlin said. “There are a lot of organic farmers quietly doing an awesome job.”
The trio wrote their business plan while they were in college. They started with the 2,000-square-foot greenhouse in Neenah, using a system in which the waste produced by farmed fish supplies nutrients for plants grown hydroponically. The Neenah location also has a herb garden.
The large, open space in the former bottling plant in Bay View was perfect for growing mushrooms.
“And we don’t see this as our last space, for sure,” Catlin said.
Milwaukee has been a leader in urban farming, whether it’s growing mushrooms indoors or fruits and vegetables on vacant lots.
“We were getting excited about all of the changes in local foods in Wisconsin, especially in Milwaukee. We were inspired by Will Allen and some other farms in the area,” Catlin said.
Allen is the founder and CEO of Growing Power, a nonprofit focused on urban farming and creating sustainable food systems. He started with 3 acres of land on Milwaukee’s north side in 1993 and now has locations in Milwaukee, Chicago, Detroit and other places throughout the world.
“We have the largest urban farm in the world, but we need more folks who really want to scale it up,” Allen said.
“There are going to be people who do this on a small scale, and that’s great … but we need to scale up to the point where we can grow some jobs and put people to work,” he said.
Allen, named one of the 100 World’s Most Influential People by Time Magazine, believes that urban farming can help address poverty and related social issues.
“The answer to end poverty and violence is to give people living-wage jobs, and this is an industry that can do that. We don’t see other industries moving into troubled communities,” Allen said.
Growing Power has trained mushroom farmers from all over the world. It also has greenhouses for year-round production of fruits and vegetables in cold climates.
Increasingly, consumers have sought locally-grown foods.
“The market is there. The problem is there’s not enough production. We have to grow some farmers,” Allen said.
Indoor Farms: Where Venture Capital Doesn’t Always Make Sense
So where should startup indoor farms look for early stage funding?
This week I took part in NYC AgTech Week, a week-long event that attracted indoor agriculture enthusiasts from across the globe for a series of presentations, tours, and panel discussions. On Tuesday evening, indoor ag software startup Agrilyst hosted a panel discussion on funding for indoor farms and other agtech startups.
For an area of agtech that gets so much hype, if AgFunderNews click rates are anything to go by, we are always amazed at the relatively low volumes of funding that go into it. In 2015, indoor agriculture startups — encompassing physical indoor farms and any hardware or software products serving them — raised $77 million, and during the first half of this year that figure was just $21 million. That’s from a total $4.6 billion in agtech investment in 2015 and $1.8 billion in the first half of 2016.
Having said that, the subsector has captured some of agtech’s largest deals, and this week’s $30 million Series C from BrightFarms is no exception. BrightFarms says this is the largest equity funding round for a US indoor ag company. The largest deal on record was 2014’s $100 million investment from private equity behemoth KKR into Sundrop Farms, the Australian greenhouse project. New Jersey-based vertical farming group AeroFarms has also raised big money, with Goldman Sachs and Prudential contributing $40 million to a $70 million debt financing for a specific farm project last year and the company has raised more in equity funding for the business too.
These deals are so big because scaling an indoor farming business is no small feat. The time it takes to do so is a big question for venture capital firms and has kept many away, argued James Smits from Beta Bridge Capital, who was speaking on the panel. Venture capital investors typically want to hold investments for around five years, but scaling an indoor farming company could take at least that time.
Beta Bridge, which focuses on seed stage investments, is instead accessing the indoor ag market through software and invested in Agrilyst’s seed round earlier this year. Agrilyst is likely to behave a lot like any other SaaS platforms in Smits’ portfolio and very different from asset-heavy indoor farming businesses.
There are of course some VCs that have invested in indoor farming startups, and the main players all have VCs in their investor line-up. It’s particularly suitable at the growth stage, such as Catalyst Investors in BrightFarms’ latest round. In this case, BrightFarms has de-risked its business model with proven technology in existing facilities and long-term produce purchase agreements with grocery making it a very different proposition to investing in a startup indoor farm with little operating history.
So where should startup indoor farms look for early stage funding? If you look at the investor base of indoor farms so far, you’ll notice there’s actually a very broad range of investors available to the sector, including family offices and impact investors. They may have longer investment time horizons and missions than a typical VC, and so can stick with the business through the early stages and into growth.
Regional investors are another potential source of funding such as NYS Innovation Venture Capital Fund, a New York state-funded vehicle, which is looking closely at the agtech space. Speaking on the panel from the fund, Lindsay Freeman Avagliano said that the fund’s mission was to make a positive impact on communities in New York through funding local innovation. The relatively new fund, which has $100 million to deploy, will reserve follow-on funding for the majority of investments it makes, she told the audience.
Then there are other routes altogether, namely project financing and debt for specific initiatives like the Goldman Sachs deal. This funding can be longer term and support the construction of facilities and purchase of equipment — instead of providing equity funding for a startup’s general overheads.
Speaking to this on the panel was Angela Ferrante from SparkFund, which offers loans to businesses to purchase energy efficient tools for their businesses, and has loaned to indoor farms to purchase LED lighting. This is a novel way of getting access to the equipment you need without giving away equity.
There’s also the crowdfunding route, which is a great way to find mission-oriented individual investors, who are passionate about the space.
So while venture capital might not always make sense for indoor ag startups, there are other options for startups to consider.
By Louisa Burwood-Taylor
What do you think? Where do you think indoor farming startups should seek funding? Get in touch Media@AgFunderNews.com.
Indoor Farming Opportunity
If you’re in Dallas and interested in operating two Growtainer™ farms, please contact me by email
Indoor Farming Opportunity
If you’re in Dallas and interested in operating two Growtainer™ farms, please contact me by email. Very interesting opportunity for a couple of people that want to run their own business growing gourmet greens and supplying local restaurants. Includes all LED lighting, Climate Control, Ebb and flood system and fully equipped NFT system. Completely plug and play, just bring seeds and substrate and you’re in business. These are the original Growtainer™ prototypes at Agrilife Research Center in Dallas, available for a couple of entrepreneurs that want to run their own business. Plus you get to hang out with me….gb@greentech-agro.com
Glenn Behrman, President of GreenTech Agro announced today that the Growtainer™ version 2.0 is officially just weeks away from launch. Offered at a very competitive price with a dramatically increased potential yield, Growtainer™ 2.0 has been completely re-designed to be more affordable for a quick ROI and more efficient in every way. It’s easier to operate and comes with a maximum yield, moveable and adjustable Growrack™ system. The proprietary Growrack™ system was designed by GTA and manufactured in Holland. Growtainers™ are available in a 40’ or 45’ version and can be custom designed for any climate. Developed for food production, horticulture or floraculture, they are available with complete climate control or refrigeration for vertical vernalization.
An operator can now produce 2 to 3 times as much produce in the patent pending Growtainer™ compared to other container based products in the market today. For example: Growing in 50’s = 12,000 plants per cycle, 72’s = 17,280 plants per cycle, 98’s = 23,520 plants per cycle. You do the math, very easy to calculate the ROI.
Glenn announced that GTA is finally ready to talk to investors and to choose two or three distributors. He said at Indoor Ag that he wouldn’t sell a Growtainer™ unless it was perfect and version 2.0 is perfect.
For more information, email: gb@greentech-agro.com
www.growtainers.com
Edible Learning Lab – A Year In Growth
“Our mission is to bring edible education to all kids K through 12, and it’s something we think about all the time”
Edible Learning Lab – A Year In Growt
Nick Spanos, nick@buffalobulletin.com
On most afternoons, a magenta glow can be seen reflecting out from the eastside stairwell of the Bomber Mountain Civic Center. If you follow the light down the stairs and through the side door, you’ll find yourself in what was once the middle school’s music room, but in place of scattered music stands and an upright piano collecting dust, you’ll find a room budding with life, literally.
The converted space houses a fully functional edible learning lab complete with raised planting beds, a fully equipped teaching kitchen and a vertical hydroponic system with red and blue LED grow lights to stimulate plant growth – the source of the magenta glow.
The Edible Learning Lab program is the brainchild of admitted foodies and entrepreneurs Tim Miner and Dave Creech.
They launched the program in Buffalo last September, and in the lab’s first year of operation it has prospered, producing well over 100 pounds of food and educating hundreds of Johnson County students in the process.
“Our mission is to bring edible education to all kids K through 12, and it’s something we think about all the time,” Miner said.
Edible education means giving students hands on experience growing their own food, but it also means teaching them the biological processes that bring food from a seed to a family’s table.
Educating the kids and introducing students to healthy eating practices is something that Miner sees as invaluable.
“We think it’s important because this is one of the solutions or one of the processes that can lead to health changes,” he said.
Miner also mentioned the staggering number of health problems caused by dietary related issues in the U.S.
“We feel that educating kids at an early age is going to set them on the right trajectory. It’s going to give them understanding and love for the relationship they have with food,” Miner said. “It’s going to create a more sound foundation for that relationship, and over time kids are going to be making healthier choices and they’ll be exposed to things they wouldn’t otherwise be exposed to, and we feel that’s our way to plant the seed for change going forward.”
The strong vision that Miner has for the learning lab wasn’t always set in stone. He’ll be the first to tell you it’s been an evolving journey from day one to now.
“I would love to tell you that we had this crystal clear idea of what an edible learning lab would be, what it would look like and how it would be organized, but the reality is this has been kind of a snaking back and forth approach. When we first started working on the rough outline of the curriculum we had intended it to be for adults,” Miner said. “I was on the board of the BDTA at the time, and I was serving with Lisa (Mueller) who was the CEO of the Boys & Girls Club, and we were talking about the curriculum and I was telling her how surprised I was by the number of kids who couldn’t pick broccoli out of a line up of vegetables, and she said, ‘You’re working on the course, do you think you could apply that to kids?’”
Miner responded with an immediate yes, and when Mueller came back a week later and said she might be able to secure grant money for the project, Miner was fully on board.
Miner and Mueller worked together to prepare the grant application just before the deadline and were approved for the maximum award of $125,000 a year for five years, and after Miner and Creech reworked the curriculum and ordered the equipment for the lab, everything began to fall into place.
A year later, Miner is just putting the finishing touches on the project.
“We’re placing our last orders for equipment, we’ve fully equipped the kitchen and are working on the rain harvesting system, which will allow us to capture over 200 gallons of rainwater from the downspouts to be used in the lab,” Miner said.
The concept of the edible learning lab has always been something that Miner and Creech wanted to be applicable and repeatable on a national scale.
“The plan has always been to open as many of these labs around the ounty as possible. Right now we’re talking to about 100 schools. We’re really interested in having this information being presented to all schools around the country,” Miner said.
Vertical Farming Market worth 3.88 Billion USD by 2020, at a CAGR of 30.7%
Lighting functional device expected to lead the vertical farming market
Arshad Singh
Vertical Farming Corporate Communicator at MarketsandMarkets
Vertical Farming Market worth 3.88 Billion USD by 2020, at a CAGR of 30.7%
Sep 21, 2016
The factors which are driving the vertical farming market include need for high quality food with no use of pesticides, less dependency on the weather, increasing urban population, and need for year round production. The largest market in the functional device segment is lighting market owing to the high acceptance of LEDs to replace traditional lighting. LEDs have been developed which provide optimum electromagnetic spectrum for photosynthesis, consume less energy, and have minimal heat signatures which keeps the energy requirement for temperature maintenance at a minimum.
Download Free PDF Brochure @http://www.marketsandmarkets.com/pdfdownload.asp?id=221795343
The vertical farming market is estimated to reach USD 3.88 billion by 2020, at a CAGR of 30.7% between 2015 and 2020.
Lighting functional device expected to lead the vertical farming market
Lighting as a functional device, in terms of value, is expected to hold the largest share of the vertical farming market by 2020. The traditional lighting system is being replaced by LED lighting system which is more efficient, emits electromagnetic spectrum ideal for photosynthesis and generates low heat. The increased acceptance of LED lighting system by end users is driving the growth of this market.
Hydroponics as a growth mechanism segment dominates the vertical farming market
The market for hydroponics as a growth mechanism is expected to be the largest between 2015 and 2020. This is mainly because of the benefits associated with it such as quicker growth, faster harvest, higher yield, and low nutrient wastage as mineral nutrients are dissolved in water and are fed directly to a plant’s root system without any involvement of soil.
APAC expected to hold the largest market share and grow during the forecast period
The APAC vertical farming market is expected to hold the largest share by 2020 owing to major driving forces such as growth in urban population, less availability of cultivable land, government initiatives, and demand for food with low impact on environment, the vertical farming market is growing in this region.
Global Vertical Farming Market, by Functional Device
- Lighting
- Hydroponic Components
- Climate Control
- Sensors
Global Vertical Farming Market, by Growth Mechanism
- Aeroponics
- Hydroponics
- Others
This research report categorizes the global vertical farming market based on functional devices, growth mechanism, and regions. This report describes the drivers, restraints, opportunities, and challenges with respect to the vertical farming market. The Porter’s five forces analysis has been included in the report with a description of each of its forces and their respective impact on the vertical farming market.
Major players involved in the development of vertical farming market Aerofarms (U.S.), FarmedHere (U.S.) Koninklijke Philips N.V (The Netherlands), Illumitex Inc. (U.S.), Sky Greens (Singapore), and others.
Independence LED Lighting
LED Grow Light Plant Growth Time Lapse For Basil With Aquaponics.
Inside Look: Independence LED Lighting Creates Better Produce!
Next-Generation Food Supply! See this time-lapse video showing 30 days growth in the controlled environment under Independence LED lighting. The LED Grow lighting creates a heavier and leafier product, which in this case is basil.
To view state-of-the art Horticulture LED Lighting for advanced Agriculture learn more here: http://independenceled.com/led-grow-lights/
LED Grow Lights can dramatically change the economics of indoor framing for warehouse and greenhouse facilities. Independence LED Lighting is ideal for Horticulture LED Lighting that advanced Agriculture LED Lighting for Indoor Farming such as the production of cost-effective Indoor Vegetables at Grow Operations.
Since LED lighting for commercial farming is “green” and on the rise, we welcome content submission such as LED grow light videos, LED grow lights photographs, and LED grow light production case studies.
Submit LED horticulture and LED agriculture content here via: Contact GREENandSAVE
Programming Sun and Rain: Students Run an Indoor Farm at School by Computer or Mobile App
High-school students grow an acre’s worth of vegetables in an old shipping container that’s been transformed into a computer-controlled hydroponic farm.
Green beans and other vegetables growing in the computer-controlled climate of a hydroponic farm in an old shipping container at Boston Latin School. Students monitor and control it all, on site or with a mobile app.
BOSTON – On the cramped urban campus of Boston Latin School, high-school students grow an acre’s worth of vegetables in an old shipping container that’s been transformed into a computer-controlled hydroponic farm. Using a wall-mounted keyboard or a mobile app, the student farmers can monitor their crops, tweak the climate, make it rain and schedule every ultraviolet sunrise.
In a few decades, nine billion people will crowd our planet, and the challenge of sustainably feeding everybody has sparked a boom in high-tech farming that is now budding up in schools. These farms offer hands-on learning about everything from plant physiology to computer science, along with insights into the complexities and controversies of sustainability. The school farms are also incubators, joining a larger online community of farm hackers.
“We are constantly experimenting,” said Catherine Arnold, a Boston Latin history teacher who oversees the environmental club that runs the farm as an extracurricular activity. It was built by a Boston startup called Freight Farms, which “upcycles” discarded shipping containers into “Leafy Green Machines” for small-scale growers and restaurants, as well as a dozen schools and colleges.
“My students can collect data on the farm from anywhere, whenever they want to.”
Graeme Marcoux, of Salem, Mass., who teaches a high school vocational course in hydroponics and aquaculture
The latest version of a freight farm costs $82,000. Boston Latin has a cheaper, earlier version, paid for with a green-schools grant. The students have been giving their food away but plan to sell produce to parents and neighbors this year, to cover the annual cost of seeds, nutrients and other supplies.
On a recent morning, Arnold showed off rows of spinach, peppers, tomatoes, lettuces, green beans and herbs hanging below drip irrigation that was bathing the roots in a recirculating mix of water and nutrients. The plants grew out of a recycled plastic mesh rather than soil and were lit by thin strips of LED lights.
When the school’s farm opened in 2014, Freight Farms staffers taught students about crops that have a proven hydroponic track record and their preferred mixes of temperature, nutrients, moisture and other factors. But Arnold said the real learning comes from trying new things.
“They never said you can grow green beans, but we have two varieties,” Arnold said. “This year, we’re going to try carrots and turnips. Anything the students want to try, we’re going see what happens.”
A video camera and sensors send real-time data about the growing environment to a computer that triggers farm systems set to schedules and thresholds (such as carbon dioxide or nitrogen levels). Students monitor and control it all, on site or with a mobile app. According to Graeme Marcoux, a high-school environmental and marine science teacher in Salem, Massachusetts, whose school set up a freight farm last spring, the remote access is essential, because only so many students can work inside a 320-square-foot box, and because farming doesn’t stop when the bell rings.
“My students can collect data on the farm from anywhere, whenever they want to,” said Marcoux, who teaches a vocational course (worth one science credit) in hydroponics and aquaculture.
Besides passing on technical knowhow, Marcoux encourages class debates about food sustainability. The many high-tech automated “vertical farms” popping up in cities around the world have a shared mission of growing more food locally, while using a lot less land and water than conventional farms. Being indoors means no pesticides, and their closed systems mean they don’t poison waterways with fertilizer runoff.
“To imagine you could help feed people with this computer was amazing to these kids. Most of them don’t think about technology and food going together, when clearly they do, even in traditional farming.”
Will Borden, director of academic technology, Shady Hill School, Cambridge, Massachusetts
But critics say that indoor farms are energy hogs. A farm like the one at Boston Latin, for instance, uses enough energy to power about two and a half American households. Of course, conventional agriculture also has many hidden energy costs, from shipping food, refrigerating storage facilities, manufacturing and operating massive farm equipment, and moving and treating all that irrigation water. Plus, rapid gains in LED efficiency and renewable energy will help shrink the carbon footprint of indoor farms.
“It’s a great debate to have with the students, because by the end of that debate everybody has a much deeper sense of what actually makes something sustainable,” said Marcoux.
The Freight Farm app links to a repository of articles about everything from crop scheduling to food safety. There’s also a Facebook group of freight farmers who are a ready source of ideas and advice on topics such as how to deal with tiny spots on your lettuce or how best to keep the humidity under control.
The potential of networked farmers swapping expertise and experimental results – call it crowdsourcing crops – is also at the heart of OpenAg, an initiative of MIT’s Media Lab, led by research scientist Caleb Harper. In 2015, the OpenAg group gave a handful of local schools prototypes of their “personal food computers,” which are tabletop hydroponic farms that users program with “climate recipes.” Every recipe, as well as the user-interface code, is open-source and posted online for use by a global community of green-thumbed hackers.
One of the early food-computer recipients was the Shady Hill School, a private preK-8 academy not far from MIT in Cambridge, where students grew basil, sage and various leafy greens.
Every grade had some access to the food computer. The first-graders, for instance, featured it in their “farm to table” unit, alongside food grown in an outdoor garden.
James O’Brien, a Connecticut high school senior, built and programmed his own “food computer” after watching a TED talk on YouTube; then he demonstrated the computer and the lettuce he grew with it to middle schoolers at a local summer camp. Photo: Eileen O’Brien
“They could not only measure the plants, they could see and measure the growing roots,” said Will Borden, Shady Hill’s director of academic technology.
“To imagine you could help feed people with this computer was amazing to these kids,” he added. “Most of them don’t think about technology and food going together, when clearly they do, even in traditional farming.”
The food computers for the pilot schools came pre-assembled. But for everyone else, they were totally DIY, using downloadable step-by-step instructions. For example, James O’Brien, a senior at Staples High School in Westport, Connecticut, was inspired to build a food computer after watching a Caleb Harper TED talk on YouTube last summer.
On his own, O’Brien machined and assembled the parts, bought the sensors, wired them into a circuit board, and programmed the computer’s brain. He demonstrated his food computer and the lettuce he grew with it to middle school kids at a summer camp run at a local farm. In August, he started a nonprofit called Workshop Garden Technologies to create after-school programs for middle-school students using food computers.
OpenAg is now readying a more refined and user-friendly kit version of the food computer for a second round of school pilots planned for the spring. It will also be possible to program the “climate recipes” with a simpler, block-based coding language, such as Scratch (another Media Lab creation).
There will still be a strong DIY element, however. The idea is that lesson plans, like climate recipes, will be created, shared and improved upon by the community of school food-computer users.
“We want to include kids in a co-creation process, to let them play with the food computer and help us improve the engagement and experience of growing with it,” said Hildreth England, OpenAg’s program coordinator. “Kids are natural tinkerers. It’s a perfect fit.”
This story was produced by The Hechinger Report, a nonprofit, independent news organization focused on inequality and innovation in education. Read more about Blended Learning.
By Chris Berdick
BrightFarms Raises $30.1 Million to Set Up Futuristic Greenhouses Across the U.S.
On a mission to make all fresh fruit and vegetables locally!
Agriculture tech startup BrightFarms has raised $30.1 million in Series C funding to bring its high-tech greenhouses, and fresh produce, across the U.S.
The company is on a mission to make all fresh fruit and vegetables locally, rather than require them to be hauled from long distances or imported from overseas before they are sold at groceries.
Taking a page from the playbook of solar power providers in the U.S., BrightFarms offers customers a long-term, fixed rate on the salad greens and tomatoes it grows in its greenhouses to grocers.
BrightFarms-raised produce.
The startup’s CEO Paul Lightfoot explained that after BrightFarms locks in a “produce purchasing agreement,” it raises funds from various sources including economic development programs and different banks or equity firms to build a new greenhouse.
In effect, a big chunk of the company’s cost of goods is already committed revenue before they open up a greenhouse’s doors and start growing.
The new round of funding was led by Catalyst Investors, and joined by BrightFarms earlier backers WP Global Partners and NGEN.
Catalyst’s Tyler Newton said his firm backed BrightFarms largely due to its business model innovation and ability to “out-execute” other food producers in the U.S.
Consumers definitely want to buy groceries made by local businesses, and to help support jobs that pay a local living wage in their own back yard. According to research by the U.S. Department of Agriculture, local food sales totaled $12 billion in 2014 and are expected to grow to $20 billion by 2019.
A BrightFarms greenhouse that grows tomatoes and salad greens.
“Where the seasons don’t cooperate, we just didn’t have the option to buy local before. So that feels good. But when you taste a tomato or some arugula from BrightFarms, and compare it to something that’s been shipped from out West, there is an obvious taste advantage, too. That’s what grocers want,” Newton said.
BrightFarms is going after a huge market that doesn’t have a lot of competition outside of the states of California and Arizona, today.
America’s farms contribute $177.2 billion, or about 1 percent of the nation’s gross domestic product each year according to the most recent available calculations also from the U.S. Department of Agriculture.
And 90% of the salad greens consumed in the U.S. are produced in California and Arizona, then shipped across the country or exported out of it.
Other agriculture tech startups like AeroFarms or FreightFarms are building out indoor and container-based farms, in urban areas to meet rising consumer demands for locally-produced, and delicious fresh foods.
BrightFarms CEO Paul Lightfoot
But Lightfoot believes that his company’s greenhouses – which take advantage of natural sunlight, obviously—can prove more environmentally sustainable and cost-efficient than indoor farms, and produce more supply than container-based and rooftop farms.
He says that’s because BrightFarms controlled environment greenhouses don’t need to use as much electricity for grow lights and temperature controls as indoor farms. Both are significantly more water efficient than traditional farms, even those using precise irrigation systems.
So far, BrightFarms operates three greenhouses, each employing 25 full-time workers, in the greater Philadelphia, Washington D.C. and Chicago metro areas.
If drought conditions continue, Lightfoot said, the company could someday move into the “salad bowl” state of California, or other agricultural hubs, displacing traditional, and often water-intensive, farms.
But for now it will focus on metro areas where demand for fresh produce is high but there isn’t a lot of arable land or weather to support traditional farms.
BrightFarms’ customers and partners have so far included grocers like Kroger, Ahold USA, Wegmans and ShopRite.
Besides using the new Series C capital to build out additional greenhouses, Lightfoot says the company will explore new crops and is likely to start growing peppers and strawberries in the near future.
Featured Image: BrightFarms Inc.
By Lora Kolodny
Elon Musk’s Brother Aims to Revolutionize Urban Farming with Square Roots
Kimbal Musk, Elon Musk’s younger brother has launched a new accelerator and company in Brooklyn called Square Roots that will invest in startups, growing fresh produce in cities.
By opening an urban farm in Brooklyn, New York, Square Roots aims to revolutionise the way Americans think about food and produce.
The accelerator will also provide mentorship and resources to millennial urban farmers, using shipping containers with hydroponic growing towers.
What is Square Roots?
Square Roots is a new agriculture venture that is located in the old Pfizer factory, Brooklyn, New York that holds 10 farms and young farmers who tend to the fresh produce.
Along with Tobias Peggs he two entrepreneurs will use 10 steel, 320 square foot shipping containers full of organic greens and herbs to make vertical farms inside the Pfizer building.
The young millennial farmers “Will get hands-on experience running a vertical farming business with us- but we’re here to help them become future leaders in food, wherever that journey leads,” said co-founder Tobias Peggs.
The incubator program that starts this this fall will give food-tech entrepreneurs space to develop and increase farming startups.
They will use technology developed by startups freight Farms and Zip Grow using climate controlled LED lights and a hydroponic system.
Who is Kimbal Musk?
Photo was taken of Musk outside The Kitchen in Boulder
Kimbal Musk is the younger brother of Elon Musk, the CEO of Tesla, who has invested in SolarCity and SpaceX.
Originally from South Africa the brothers worked together to found Zip2, a startup in 1995 that allowed newspapers to build their own city guides.
After selling the company for $300 million in 1999 to Compaq, Elon Musk founded PayPal, the online payments platform, Tesla and his other space ventures.
Kimbal took a different route, moving to New York to take French cooking classes at international Culinary Center.
When he volunteered to feed firefighters after the terror attacks on September 11 2001, Musk had an epiphany, citing “That sense of community that I felt was just profound to me,” opening a restaurant soon after.
Kimal Musk then opened the restaurant The Kitchen Upstairs and taking an executive job at social networking startup, OneRiot, before launching Next Door, to merge community and fresh food, and quality burgers together. There are five restaurants in Colorado at present with plans to expand.
What is Urban Farming?
Photo Credit: Freight Farms
Urban farming or agriculture is producing food in cities or heavily populated areas where space is scarce.
The difference between urban farming and community gardening is the commercial aspect involved. The former is based on selling produce rather than for personal needs.
Food can be sold to restaurants, farmers markets or community enterprises.
Why Choose Urban Farming?
Many advocates of urban farming point to the fact that vertical farms expend 80 percent less water than outdoor farms and require much less space, which is significant in urban areas.
With seven billion people earth, the planet is under massive strain with pollution, habitat damage and climate change.
Urban farming decreases the ‘food miles’ linked to long-distance transportation, making it a more sustainable way to grow food.
By increasing greenery in cities, this increases shading, and reduces toxic emissions. Urban farming also helps people reconnect to their food, understanding how it is grown.
Why is Urban Farming So Important for Americans?
Photo Credit: Square Roots
Tobias Peggs noted that he is often approached by young people who are frustrated with the industrial food system but don’t know what to do about it.
Peggs said, “Seeing this frustration, and pent up energy, was a big part of the original inspiration for founding Square Roots.”
Musk said in a Medium article that people want real food:
“Young people especially are turning away from McDonald’s towards healthy, locally-sourced options like Next Door and Sweetgreen.”
According to thestateofobesity.org, in 2016 adult obesity rates now exceed 35 percent in four states, 30 percent in 25 states and are above 20 percent in all states.
What Impact will Square Roots Have on Urban Farming?
Square Roots aims to help young urban farmers to start thinking about innovative food production.
With investors such as food tech VCs Powerplant Ventures, Lightbank, GroundUp, FoodTech Angels and The Kitchen, there is plenty of scope for this venture to work.
If successful, Musk will be able to build more farms similar to the Square Roots in Brooklyn, within New York and expand to other US cities.
By Tanya Geddes
Containers Could Hold The Future of Farming
Containers could hold the future of farming
Containers could hold the future of farming
by: Wolf Depner - Saanich News
- posted Sep 20, 2016 at 3:00 PM
Tamara Knott looks over some of the plants growing in her Leafy Green Machine, inside a refurbished shipping container on her West Saanich Road property.— Image Credit: Wolf Depner/News Staff
The future of farming might be found inside the 40 x 8 x 9.5 feet dimensions of the Leafy Green Machine.
Those are the dimensions of a refurbished shipping container that stands on an agricultural lot in the 6000 block of West Saanich Road.
From the outside, the green-and-metallic box underwhelms. Step inside it though and you enter a world that evokes the agricultural wizardry of Matt Damon’s character in The Martian.
Tamara and Bruce Knott, who own the container, burst out in approving laughter when they hear this comparison.
“Except,” says Tamara, “he was growing those potatoes with a particular type of material with which we have nothing to do. I keep my vegans very happy.”
Differences in fertilizers aside, the Knotts also grow different crops, mainly lettuce as of now. Yet even the most cursory survey of the container underscores the technological sophistication of the Knotts’ business.
“Yeah, we are kind of nerds,” says Tamara.
Developed by the Boston-based company Freight Farms, the container houses an automated lighting and irrigation system that can roughly produce the yield of 1.5 acres of farmland.
Its heart consists of 256 vertically suspended cuboids (rectangular prisms). Each of these narrow “towers”, as the Knotts call them, can hold anywhere between 14 to 17 heads of various types of salad greens.
Each head begins life as a granular seed planted inside what Bruce calls a “peat plug” about the size of a pinky finger.
After growing in horizontally placed trays that receive a steady supply of nutrient-enhanced water, the plants are then planted several inches apart in the towers, each lined with a growing medium completely free of dirt and of a texture that Bruce compares to a “coarse brush.”
The towers are then hung between two horizontal metal cuboids.
The upper supplies each of the towers and the produce within them with nutrient-enriched water; the lower catches the run-off and sends it back into the irrigation system, where sensors continuously monitor the nutrient content, ph level and temperature of the water running through the system to ensure optimal growth.
“We don’t discharge any of that [water],” says Bruce. “We use it all. It just continues [to circulate through the system] and we just keep adding water at a rate of about five gallons a day, as the plants use it.”
This volume of water use marks a drastically reduced rate. “In terms of a conventional farming operation for these types of crops, the estimate is that the water use is 90 per cent less,” says Tamara.
Narrow ropes of energy-efficient LED lights, which Bruce says “look a little bit like disco lights,” add to the futuristic atmosphere.
Cascading off the container’s ceiling like party streamers, they emit blue and red light following a specialized schedule that ensures the plants receive optimal energy and rest. “For photosynthesis, plants predominately use light in the red and the blue spectrum, so we just give them that, because that is what they need to thrive,” says Tamara.
“They actually reflect the yellow and green back at our eyes, because they are not using it for photosynthesis.”
Aside from using far less water than outdoor farming, this type of indoor farming also foregoes pesticides and herbicides and requires far less land.
“You can put this unit on almost two parking spots downtown ... and you can feed a lot of people,” he says.
Finally, it can provide fresh produce year-around.
As such, it offers itself as a solution to a future marked by water shortages, declining supplies of arable land and growing urban populations facing various food security issues.
“The water, the lack of waste, the proximity to the people who are actually going to consume the food — we like all those things,” says Bruce. “That is why we sort of thought, this is the way of the future and we just want to be part of that future.”
With 85 million discarded sea containers available, others may follow the Knotts’ example.
If so, foodies might be in for a treat as well.
The Knotts, who describe themselves as “salad snobs,” say they “are pretty pleased with the quality of products.”
After spending three to four months to get their operation off the ground, the Knotts have been on the market for about a month now, selling to three local restaurants and customers at the local farmers’ markets. The Knotts are also organizing a network of pick-up points across Greater Victoria, where customers can pick up prepaid weekly produce baskets. “So folks are able to get their fresh produce, particularly at a time of year when none of the farmers’ markets are operating,” says Tamara.
So how do people react when the Knotts tell them where their lettuce comes from?
“Mostly, they say, ‘Cool! You can do that?’” says Tamara. “It has been really positively received and people are really excited about it. They think it is just a really, really neat idea.”
Garden going up: Work begins to turn old MFA mill into high-tech indoor farm
For decades, the landmark MFA logo towered over downtown. The colorful sign on the tall white grain elevator served as a nod to our farming heritage. This week, workers rolled out a new banner highlighting the building's new tenant, Vertical Innovations, LLC.
SPRINGFIELD, Mo. For decades, the landmark MFA logo towered over downtown. The colorful sign on the tall white grain elevator served as a nod to our farming heritage. Now, after 65 years, it is gone. In its place is a sign announcing something new to come.
This week, workers rolled out a new banner highlighting the building's new tenant, Vertical Innovations, LLC.
"It was about a six hour project," stated David Geisler, Manager and General Counsel of Vertical Innovations. "That is a lot of work to fasten a banner 200 feet in the air," he laughed.
Vertical Innovations is turning the long-vacant Missouri Farmers Association grain silo complex into a massive indoor vegetable farm. The structure, which has been vacant for years, is owned by Missouri State University, and is being leased to Vertical Innovations for the project.
Geisler explained, "If it works, we are going to be able to supply a large amount of food for the people of Springfield that we know is safe, it is traceable. They are going to be able to say, this is hours old. It is going to be fresh."
There's obviously no sunlight in the tall tubes. So, artificial light and other technologies will help the garden grow. Several new employees will be brought on board to tend the crops and facility.
"Essentially, we are going to be a true vertical farm. We will be a farm using some new ideas we have that nobody else has done before," Geisler said.
As you can imagine, there are not a lot of companies left that build grain elevators. So, for this project, the developer had to hire the modern incarnation of the company that built this place back in 1955. Borton Contractors & Engineers, based in South Hutchinson, KS, is now busy retrofitting the structure for its new purpose.
Geisler said, "I think that is part of the beauty of the project is it allows us to take these icons of our agricultural heritage and reuse them in the 21st century environment. It is refreshing."
Developers and supporters have high hopes for the future of farming in urban environments. Though a grand opening is still months away, Geisler believes this project could be the first of many.
"I think we will provide a model, a blueprint if you will, for how we can use abandoned grain elevators in other cities. But, Springfield will always be first."
As for the old MFA signs, Geisler says the one removed from the north side of the headhouse has been saved for preservation. The emblem facing south, which remains in place, will likely also be taken down and preserved.
By Michael Landis
Startup That Grows Crops in Shipping Containers Unveils Sleek, New Design
At first glance, the tall metal box on the Greenway looks somewhat innocuous. But open the doors and there’s a salad disco happening inside
At first glance, the tall metal box on the Greenway looks somewhat innocuous. But open the doors and there’s a salad disco happening inside.
The large white container, which will be situated in the park all day Friday at the corner of High and Purchase streets, is the latest product from Freight Farms, the local startup that enables would-be farmers to grow produce anywhere using its tricked-out shipping containers.
The company, which has raised nearly $5 million in funding, has become somewhat of a darling to the startup set. Google is using one of its hydroponic containers to feed its 20,000 employees in Palo Alto, and last month Freight Farms partnered with Elon Musk’s chef brother, Kimbal, to help launch his urban farming accelerator, Square Roots.
Since launching in 2010, the company has sold 100 of its signature device, the Leafy Green Machine, said its president, Jon Friedman.
The prototype is a slightly smaller version of the modular growing system. He dubbed it the Leafy Green C (the C stands for community, or compact ... they haven’t decided yet). It’s about one quarter the size of a typical shipping container, clocking in at about 10 feet long, 9 feet high, and 8 feet wide. And it can grow 200 heads of lettuce each week.
Inside is where the fun starts.
Farmers plug their seedlings into six-foot tall, gutter-like “towers” that act as a growing medium for the young shoots. Each tower is then hung from the ceiling and lit with blue and red LED lights, which can be tweaked to emulate the sun as it cycles through the day.
Imagine dozens of vertical spinning towers of lettuce. The entire system gives off a very disco-like feel.
The original containers, which each cost $85,000, are now in nine countries, six islands, 25 states, and 12 schools. But Friedman said the system’s new design has a different customer in mind. It will be half as expensive as the original model (the exact price is not yet set, he said). He’s hoping to attract restaurants, communities and perhaps even individuals who are excited about the idea of container farming but don’t necessarily need nearly an acres worth of produce a week. The company will begin taking preorders in November.
Part of the draw, said Kyle Seaman, the company’s farm technology director, is the newly-designed app called Farmhand that allows the owner of the unit to control all aspects of the container from a smartphone, adjusting the light, heat, nutrients, and water.
“The app informs the farmer if something goes wrong,” said Seamen.
Should their lettuce need some love, they’ll get a ping on their phone. Now, if they can just make it connect to Spotify, they’ll be in business.
Janelle Nanos can be reached at janelle.nanos@globe.com. Follow her on Twitter @janellenanos.
IES Launched Full Range Of LED Horticulture Grow Lighting Products
IES is one of the leading global developers of greenhouse and indoor farming and gardening LED lights solution.
IES is one of the leading global developers of greenhouse and indoor farming and gardening LED lights solution. With an international team of agriculture experts and researchers, IES focuses on driving innovation and development in their industry which has earned them the status of being a global leading light in the field of supplemental lighting. Recently,
Technological advancements have paved the way to more unconventional methods of cultivating plants, growing and caring for them which include indoor farming and gardening. IES is directed by their desire to generate and cultivate innovative and hi-tech LED Horticulture Lighting technology. Their main point of focus is to satisfy their customers through their high standards of quality in both their products and their customer services. The company spokesperson said: Our Horticulture LED Solutions develops light systems to condition any crop in growth. We do not only provide mere lighting, but we provide the best possible care to increase profit for the grower, we call this custom made plan a ‘light recipe’.”
The range of products has been created to cater to the needs of contemporary indoor and greenhouse farming and gardening lighting needs, the comprehensive range of products includes LED lights specially designed for a greenhouse, hydroponics, aeroponics, home garden, farm, vegetable shed, botanic garden, flower exhibitions, horticulture, hydroponics, hemp cultivations, medical plants cultivations, etc. the spokesperson continued: “Our light recipes are suitable for different segments within horticulture, e.g. vegetable production, tissue culture and young plant production, cut flowers, seedlings and nurseries. Horticulture LED Solutions is offering knowledge of LED Plant lighting around the world to you.”
Consistent global standards of quality and various certifications are the testament to the company's commitment towards maintaining the highest levels of superiority. The company takes a lot of pride in the fact that they maintain a large worldwide customer based with clients in every part of the world including Europe, America, the Middle East and Southeast Asia, their product are available for sale on all major online marketplaces and the complete details of each product is available on the IES horticulture lighting website.
The company looks forward to expanding their global customer base to become a major LED grow lighting manufacturer globally and continue serving their esteemed clients with top of the range products.
About:
IES Lighting Co., Ltd is a horticulture and agriculture LED light producer based in China.
For more information please visit: http://www.grow-lighting.com/
Contact: Jessie
info@grow-lighting.com
Shenzhen,China
Media Contact
Company Name: IES Lighting Co., Ltd
Contact Person: Jessie
Email: info@grow-lighting.com
Country: China
Website: http://www.grow-lighting.com/
Four Key Takeaways from Agrilyst’s Indoor Farming Report
The 2016 State of Indoor Farming report by Agrilyst is now available.
The 2016 State of Indoor Farming report by Agrilyst is now available. The full results are at the bottom so just scroll past my rapid-fire take aways if you’re only interested in a deep data dive.
1. Scaling up vine crops is an enormous opportunity.
The crop that jumps out at me on this chart is vine crops. They make a whopping $175 per sq ft in the small scale farms. With that kind of revenue, one would think building a large scale facility would be akin to winning the lottery.
But alas, scaling up Vine crops is harder than winning the lottery, which is why vine crop earn 1/6th the amount of revenue per sq foot in large farms.
Take away: Figuring out how to scale Vine Crops is like winning the lottery
2. Operating costs are an industry pain point.
You might be sitting there wondering, “What are the top two challenges indoor farmers say they are facing right now?” Well if you are, you’re in luck because that’s exactly what I’m about to answer:
Top Problem: Keeping operating costs down
Second to Top Problem: Predictability/stability of operating costs
Why are these the top problems? Because we are in a new industry where best practices are still in TBD.
Take away: Hire a Consultant. Only 38% of those surveyed hired a consultant to help them develop best practices.
3. Something is wrong with organic certification.
More than half of indoor growers aren’t interested in USDA organic certification. Of course, you already knew that USDA organic and indoor growing aren’t exactly jelling if you read the recent AgFunder article that quotes me talking about this rift.
Take away: Join a trade Association like the AVF, NYC Ag Collective, Israeli Ag Collective, California Urban Ag Collective, the FDCEA, or the Aquaponics Association to team up and affect policy.
4. Collaboration Works
Isn’t it great that we have all of this data to work with? Isn’t it great that Agrilyst, Association for Vertical Farming, Urban Ag News, Foodshed.io, FarmersWeb and Cornell University all teamed up to do this work for the industry for free?
Take Away: Join a trade Association like the AVF, NYC Ag Collective, Israeli Ag Collective, California Urban Ag Collective, the FDCEA, or the Aquaponics Association to team up and be a part of something bigger than your own company. (Hey that sounds familiar)
State of Indoor Farming
There are many unknowns and misconceptions about the indoor farming market. We wanted to provide detailed insight into what indoor growers are doing, what they’re challenged by, and how they see the indoor farming industry changing over the next few years. So, we teamed up with Cornell University, Urban Ag News, foodshed.io, the Association for Vertical Farming, and FarmersWeb to survey growers from around the world, receiving over 150 responses. Data from the survey is supplemented by research conducted by our team and others (as linked). The results are below.
The Landscape
Responses came from growers around the world, including the United States, Canada, the Caribbean, Slovakia, Taiwan, Bahrain, Dubai, Tunisia, Finland, Belgium, China, and Japan.
Indoor vertical farms and hydroponic greenhouses were the most prominent primary facility type of survey respondents. Small farms primarily consisted of indoor vertical farms while larger farms primarily consisted of hydroponic greenhouses.
Any crop can be grown indoors. The more common crops grown indoors are greens, microgreens and herbs, vine crops, cannabis, some fruits, and flowers or nursery crops. Survey respondents also reported growing tubers, mushrooms, insects, hops, algae, and commodity crops (corn and wheat).
Survey respondents are growing greens, microgreens, and cannabis in greenhouses, vertical farms, and container farms, while they are growing vine crops and flowers predominantly in greenhouses.
For the most part, indoor farmers believe that the products they’ve chosen to grow are the most profitable and they plan to continue growing those crops in the future. Cannabis and microgreens top the list of crops growers believe are most profitable to grow.
Though many growers agree that cannabis is the most profitable crop, most do not plan to grow it in the next five years.
When asked about annual production and revenue capacity, cannabis topped the list of highest revenue generating crops at about $112 per square foot or about $4,800,000 per acre. Greens were the next highest revenue generating crop at $64 per square foot or about $2,800,000 per acre. The lowest revenue generating crops reported were strawberries at about $22 per square foot or $1,000,000 per acre.
Production & Operations
One of the reasons indoor farming is gaining significant traction in the United States is the ability to produce more while using less resources. According to the United States Department of Agriculture’s (UDSA) July projection for the 2016 - 2017 growing year, corn prices range from $3.10 - $3.70 per bushel and farms are producing an average of 168 bushels per acre; conventional lettuce and tomatoes are between 23 and 25x more productive at about $12,000 and $13,000 per acre respectively. In comparison, on a revenue basis alone, indoor horticulture is about 4,000x more productive than conventional outdoor commodity farming; indoor cannabis is about 9,000x more productive.
The higher revenues realized by indoor farming are driven by three factors: (a) year round production capability, (b) higher yield, and © higher retail pricing.
Year Round Production
In a given year, assuming there are no weather-related incidents, outdoor conventional lettuce farmers will be able to harvest their entire farm 4–5 times. In comparison, indoor farmers will be able to harvest their entire farm an average of 18 times in a given year.
Yield
According to the USDA, the average yield for outdoor conventional lettuce production in 2015 was about 30,000 pounds per acre. Indoor greens growers reported growing an average of 340,000 pounds per acre annually. The 11x increase in yield over conventionally grown lettuce is partially due to faster growth times and additional crop turns. After removing the benefit from cyclical advantages, the increase due to indoor productivity alone is 2.8x.
Higher Retail Prices
According to the USDA, the average price per pound of conventionally grown head lettuce was $0.29 in 2015. In the same year, the price of leaf lettuce was $0.58, the price of romaine lettuce was $0.39, and the price of tomatoes for the fresh market was $0.46 per pound.
In comparison, indoor greens growers reported revenues of $6.00 per pound and indoor vine crops growers reported revenues of $1.13 per pound. Even compared to the highest priced conventional lettuce crops, indoor greens farmers are seeing 10x increases in pricing and indoor tomato growers are seeing 2.5x increases in pricing.
Organic Certification And Local Production
Half of survey respondents reported growing organically though only 8% of growers answered that they were certified as USDA Organic. When asked if growers who weren’t certified wanted to achieve the certification, 47% of growers indicated interest in the certification.
Operating Costs
When asked about their biggest challenges, growers reported managing operating costs as the most difficult - their highest priorities were both reducing and predicting/stabilizing operating costs.
Labor is one of the most costly components of indoor farming operations. Large farms reported employing an average of 24 full time and 12 part time employees. Small farms reported an average of two full time and two part time employees.
On average, data collection and analysis account for about 9% of a farm workforce’s weekly labor hours and 27% of respondents spend 20 or more hours per week on data collection and analysis.
Cannabis growers, whether small or large, spend the most time working with data (about 30 hours per week on average). Large cannabis growers also have the largest reported workforce, and growers of greens and microgreens/herbs have the smallest, comparatively.
Technology
A climate control system is one of the most critical pieces of technology for an indoor farm. This system comprises of sensors (typically recording light, temperature, humidity, CO2) and some level of control for HVAC and lighting equipment.
Of those surveyed, 54% of farms have climate controls systems and 74% of those systems are connected to the internet. There are a handful of leaders in the climate controls market, including Priva, Argus, Link4, Hortimax, and Hoogendoorn; 45% of respondents have one of these systems. Of respondents, 29% have a custom system, ranging from HVAC systems on timers to proprietary sensor and controls systems developed in partnership with universities.
On average, growers have an annual budget of $12 per square foot to invest in technology for both increasing plant yields and managing operations more efficiently. Growers have an annual budget of $15 per square foot to invest in technology to improve crop quality.
Topping a list of new technologies of interest to farmers, 39% of growers are interested in purchasing a farm management system in the next year; 28% of growers are interested in purchasing post-harvest automation systems, 28% are interested in purchasing LED lighting, and 27% are interested in purchasing climate control systems. The lowest priority item listed was organic nutrients. (Note that respondents could select more than one item.)
Farm management systems help growers cut down on the time spent collecting and analyzing data as well as the cost of hiring a growing consultant. Of the 38% of respondents who reported hiring a growing consultant, about half spend between $5,000 to $20,000 in a given year on such consulting.
With farm management systems, growers have access to data and insights into their operations, and they see the value in such analytics. Of those surveyed, 90% of growers believe they can increase crop yields with data analytics.
When asked to rank the operational processes on which data would have the largest impact, growers ranked crop quality and energy/climate control first. Impact is defined here as cutting costs and/or increasing yields.
Growers recognize the amount they could save with both hardware and software upgrades. Small vertical indoor farms report large savings expectations — on average, microgreen/herb farmers reported possible software savings of $71 per square foot. Larger farms show a range of $0.05 up to $7.00 in savings per square foot with software and hardware improvements. Cannabis growers estimate the largest benefit from technology improvements. As yield efficiency increases, so does the impact of technological improvements.
Market & Future
The vast majority of growers, 86% of survey respondents, are planning to expand their facilities in the next five years and they’re planning on growing significantly. The minimum planned expansion is 4.7x larger than current farm size.
Small farms have big plans — farms less than 1,500 square feet have a planned minimum expansion of 179x the sum of their current square footage. For large farms, the minimum planned expansion is 2.7x the sum of current square footage.
Based on current reported revenue and the expected expansion area, these farms will add to the market between $336 million and $610 million in revenue in the next five years. From all existing indoor farms then, this means a market expansion of between $3.7 billion and $6.8 billion during the same period.
Based on current reported revenue and expected expansion area, reporting cannabis growers will add between $102 million and $153 million in expansion revenue to the market in the next five years.
2 Acres of Farming In A Shipping Container
With the increasing demand for agricultural products, it has become necessary to practice alternative methods for bringing up the supply levels
2 Acres of Farming in a Shipping Container
Anna Domanska , September 13, 2016 / 2153 0
With the increasing demand for agricultural products, it has become necessary to practice alternative methods for bringing up the supply levels. It has to be taken into consideration that land simply cannot be cleared off to make space for more farms. With this in mind, the technique of vertical farming proves to be beneficial. To explain this further, vertical farming is a technique in which plant cultivation will take place inside skyscraper greenhouses. A specific environment is created using solar or wind turbine energy which is suitable to the plant growth. Furthermore, this type of farming can be done year-round.
The Vertical Farming Accelerator called Square Roots
In order to take this technique further into the agricultural market, entrepreneur Kimbal Musk along with Tobias Peggs is planning to launch a new urban farming incubator program, called Square Roots. Under this program, vertical farming will take place in the Pfizer factory situated in Brooklyn, New York. These vertical farms will be created inside 10 steel containers 320-square-foot each. Each of these containers will be managed by a young agricultural entrepreneur for one year. These entrepreneurs will be given hands-on training in running a vertical farm business by Square Roots. They will have full access to their respective farms at any time they want. In this case, the entrepreneurs can choose to grow anything they like. The entrepreneurs who are interested are supposed to pitch their start-up concept in front of Square Roots.
Such containers will contain rows of organic herbs and these plants will be monitored for watering and proper nutrient content. Due to constant monitoring, many plant diseases and spoilage could be discovered before it starts spreading further. Such farms are located in or around the city. Due to this, the consumer will acquire fresh food products which are a major benefit of vertical farming. The technology used will be developed by vertical farming start-ups Freight Farms and ZipGrow. The plants grown in such containers will be rooted in water instead of soil and cultivated under LED lights. The team of experts has decided to grow green crops inside these containers. This is because such crops are small enough for the entrepreneurs to understand vertical farming thoroughly. One such container is efficient enough to grow crops equivalent to 2 acres of farmland.
Benefits of Vertical Farming
Musk and Peggs strongly believe that urban farming has a number of advantages over traditional farming. Significantly, vertical farms expend 80% less water than outdoor farms and require much less space. On the other hand, Square Roots aims to help young farmers understand this technology better so that it can be implemented efficiently. Such entrepreneurs will be trained under the best mentors provided by Square Roots. The most important advantage of vertical farming is that it’s healthier than the products of industrial farming. The food produced through industrial farming is high-calorie, low nutrient and processed thousands of miles away. Whereas vertical farming does not compromise with the nutritional value.
Kimbal Musk and his ventures within the Agricultural Industry
Kimbal Musk is an American entrepreneur, known for his investments in several technology and food companies. He is an environmentalist who has introduced technological ideas which help in the sustainable growth of society. Musk co-founded The Kitchen which is a chain of restaurants which stocks up its food sources from local farmers. He has also co-founded a venture called The Kitchen Community, which is a non-profit organization. The Kitchen Community builds learning garden in schools around the USA. This organization has already planted vegetable gardens at more than 200 schools nationwide.
The technique of vertical farming is a progressive step towards the sustainable development on a global scale. As this technique requires minimum resources, it gives an output as good as the traditional farming method. Also, it helps in solving the problem of cutting down vegetation to meet the increasing demand of food.
Hydroponic Grower Creates Digital Greenhouse Tour
A Los Angeles-based builder of hydroponic vertical farms has unveiled a digital tour of one of its greenhouses.
A Los Angeles-based builder of hydroponic vertical farms has unveiled a digital tour of one of its greenhouses.
Local Roots Farms converts 40-foot shipping containers into hydroponic farms. The company began commercial production of lettuce in September 2015.
Each container produces the equivalent of four acres of outdoor production, according to the company.
In the digital tour, available on Local Roots’ website, users can navigate through one of the containers in which lettuce is being grown.
Local Roots crops are sold 100 miles or less from they’re produced. They use 97% less water than conventionally grown crops, according to the company.
Local Roots lettuce is currently being sold at Mendocino Farms and Tender Greens restaurants in Southern California and at severalarea farmers markets.
In July, the company exhibited for the first time at the Produce Marketing Association’s Foodservice conference and expo in Monterey, Calif.
Growing in the Air
A Newark-based AeroFarms seeks to transform agriculture through aeroponics technology that grows greens soil-free and indoors.
Forget sunshine and soil to grow leafy greens and fresh vegetables for health-conscious consumers. A US venture firm is leading a new wave of future agriculture by adopting the latest technology to produce something more fresh, safe and environmentally conscious at the heart of urban spaces.
Instead of growing crops on land with the use of pesticide and water, a Newark-based AeroFarms is running high-tech greenhouses to produce high quantities of nutritious and quality fresh food all year round. Indoor vertical farming -- a concept invented by Dickson Despommier, an ecologist and an emeritus professor of Columbia University -- is what the firm has been promoting.
The firm grows massive amounts of edible greens in stacked rows that reach to the ceiling in a controlled-environment where the temperature, nutrients and lighting are constantly monitored and adjusted. At AeroFarms, plants grow under light-emitting diodes on permeable micro fleece cloth irrigated with a nutrient-infused mist. It uses 95 percent less water, about 50 percent less fertilizers and zero pesticides.
An illustrated image of AeroFarms' vertical farming (AeroFarms)
The US firm is also working on turning an old steel mill in Newark, New Jersey into the world’s largest indoor vertical farm.
In the 6,503 square-meter space, the firm aims to produce up to 907,184 kilograms of baby greens per year, said Marc Oshima, the co-founder and chief marketng officer of AeroFarms in an email interview with The Korea Herald.
Indoor farming can ease growing concerns about climate change, population growth and fast urbanization, he said. Not only is vertical farming sustainable and socially responsible, it is a promising business as it produces greens that are tasty, rich and more nutritious, he added.
Vertical farming, in particular, can be a solution for tech-savvy South Korea that has millions of people living in congested city areas, as it offers a greater level of control to consistently grow high quality food, he said. Korean municipalities have been investing in local startups to conduct research and development in indoor farming. But there has not been many local companies involved in such business so far, according to local experts, citing the lack of economic feasibility and efforts in securing the market.
The following are the questions and answers of the interview.
1. What inspired you to start a high-tech farming business?
We are committed to building, owning, and operating indoor vertical farms that grow delicious, safe, healthy food in a sustainable and socially responsible way all over the world.
We build our farms in repurposed spaces benefitting communities and creating local jobs. Our R&D facility was once a night club and one of our farms is a former paintball/laser tag arena. We are currently building the world’s largest indoor vertical farm in an old steel mill in Newark, New Jersey. It will be 70,000 square feet (6,503 square meters) and have the capacity up to 2 million pounds (907,184 kilograms) of produce per year.
2. What are the benefits of vertical farming for customers, businesses and communities?
Our way of farming mitigates food safety risks: no soil, completely insulated from neighboring operations, no pesticides ever, and we can track a package of greens down to the exact square foot of growing. Most of the common food safety risks simply are not an issue with our system. In addition, all of our farmers and staff go through rigorous food safety training, and we are certified with United States Department of Agriculture Good Agricultural Practices.
Food-borne illnesses from vegetables are mainly a product of the practices needed to sustain large-scale commercial agriculture. Overuse of antibiotics in factory farming of livestock have created resistant bacteria, which are then sold to farmers in the form of manure or fertilizer.
Also, all of our farms have been in repurposed spaces. Our technology can really fit anywhere, but we have been focusing on dormant warehouse space that is close to existing retailers and food service distributors. A big part of our mission is to decrease food miles and travel time so that our greens are as fresh as possible when you eat them. That is why we focus on urban warehouse space specifically. But also, it’s gratifying to breathe some new life into areas that may have lost manufacturing businesses decades ago. The communities we enter are so ready for us to come in and start growing and hiring.
3. What differentiates AeroFarms’ greens from other greens produced through conventional farming methods and mass production?
Just because the supermarket shelves are stocked doesn’t mean that all is well. Food in the US travels thousands of miles and is often up to two weeks old when it reaches consumers.
That’s why distribution is a huge part of our thought process when opening new facilities. AeroFarms builds farms on major routes and near distribution centers so that our greens spend minimal time in transit. That means longer a shelf life, less shrink, better taste and also better nutrition. The second a leaf is harvested the nutrition starts to degrade, so when we can cut transit time down by growing locally we give consumers an even healthier product. So not only do our greens reach the store with more of their original nutrition, our precise control of every aspect of the nutrients, water and environment our plants use to grow means we can create the perfect conditions to optimize for flavor, taste, color, and yield to have a truly sustainable business. Our products are available to the consumer at the exact same price as field grown produce while delivering superior value.
4. Will high-tech vertical farming be the future of farming?
Vertical Farming is growing as quickly as it is because the relief of pressure on our natural resources currently caused by industrial farming is striking a chord. Traditional farming will always be an important part of the food supply, but we would like to see vertical farming become a substantial percentage of overall production. From a food security point of view it’s just smart, but also from a biodiversity and flavor point of view.
5. Who does your business mainly target?
Our greens are incredibly tasty and tend to convert even people who don’t think they like to eat leafy greens -- so there’s really no one in America who is not a potential customer. Our goal is to democratize access to good, healthy food that is responsibly grown.
6. Do you think that vertical farming could be a good business opportunity in Korea?
Absolutely. Vertical Farming is a great solution for dense urban areas because fresh food often has to travel long distances from rural areas to these cities. More importantly, vertical farming offers a far greater level of control to be able to consistently high quality food.
7. What are the challenges you have faced so far? Has there been any opposition from local farmers?
The biggest challenge for us so far has been getting to market fast enough. We have more demand from retailers than we can supply, which is why we’re working hard to bring new farms on line as quickly as possible. We don’t really see ourselves in competition with local farmers. What we’re looking to disrupt is the giant industrial farms in California and Arizona, which have energy and water needs that are vast and generally unreported. Plus, with 20 crop turns a year, we can provide fresh local green in February, when we’re really not competing with anyone.
Marc Oshima, co-founder and chief marking officer of AeroFarms
8. What kind of advice do you have for Korean start-ups or government-funded entities interested in vertical farming?
Growing indoors is not easy to do and we really want to underscore the importance of food safety. At the end, we recommend that experts like AeroFarms get engaged to help in the process.
9. What are your future strategies?
We are looking to build 25 farms over the next five years, and that is a very conservative number given the demand. We currently have farms in development in four different continents including Asia.
By Cho Chung-un (christory@heraldcorp.com)
Green Sense Farm Crowdfunding Offer Quickly Hits Goal on StartEngine
Green Sense Farm, raising capital under Reg CF on StartEngine, quickly hit its goal within the first 24 hours of listing.
Green Sense Farm, raising capital under Reg CF on StartEngine, quickly hit its goal within the first 24 hours of listing.
Green Sense Farms is a “vertical farm”. The company has established a vision of building a network of indoor vertical farms, and locate them at perishable food distribution centers owned by large grocery stores. The company also intends on creating locations at institutional campuses or wherever large volumes of food are served. If you think about it, a vertical farm makes sense. Grow the food close to where it is going to be consumed and you save on transportation (no lettuce from 3000 miles away), minimize associated pollution and harvest only when ripe. Green Sense says it is the market leader in the emerging indoor vertical farming market. The company first launched in Portage, Indiana in a 20,000 square foot facility. They now have ten development farms in their pipeline in the US, China, Canada and Scandinavia. They formed a Hong Kong company to help build out China operations. The first farm opened in China last month.
The concept is easy the practice is hard.
Green Sense Farm says it can harvest year round using the fraction of resources necessary in a traditional farm. No pesticides, herbicides, GMO seeds necessary.
Watch the video below published last year about the company.
Have a crowdfunding offering you'd like to share? Submit an offering for consideration using our Submit a Tip form and we may share it on our site!
By JD Alois